ITER NEWSLINE
-
The first 60 metres
Inside the Poloidal Field Coils Winding Facility, around 60 metres of conductor length have already been submitted to the series of operations that will ultimately turn cable-in-conduit (CICC) conductor into the "double pancake windings" for the ring-shaped magnets of the ITER Tokamak.
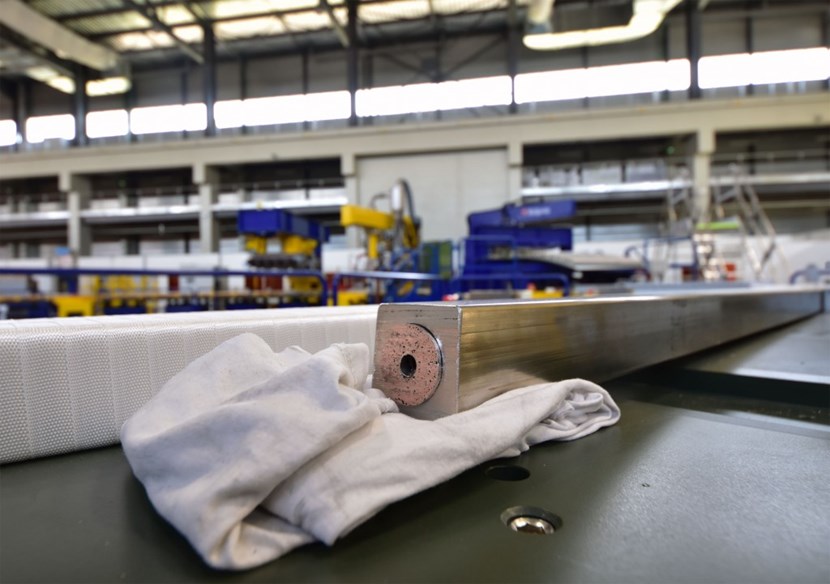
Some 60 metres of conductor length have already been submitted to the de-spooling, straightening, cleaning, bending, re-cleaning, drying and taping operations that mark the first stage of coil fabrication.
The process—from conductor de-spooling to tape and fiberglass wrapping—represents only the first stage of fabrication (the "winding" stage) and just a fraction of the material that will go into making the
double pancakes of an actual poloidal field coil.
Depending on their size, the four poloidal field coils manufactured on site by Europe will require from 6 to 14 km of conductor.
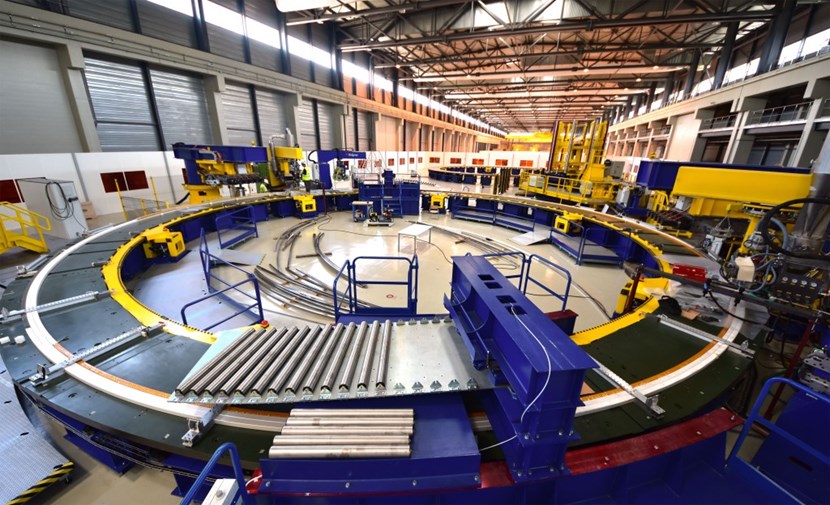
With the winding table now commissionned, fabrication for a ''pre-dummy'' and a real-size dummy, using copper conductor in lieu of the actual niobium-titanium (NbTi) alloy, will begin in late June.
With the winding machine now commissioned, the fabrication of a pre-dummy (a few more turns than the present sample) followed by an actual dummy for poloidal field coil #5 (17 metres in diameter) will begin in late June.
However, before dummy fabrication can start one last operation needs to be performed: the cleaning, from top to bottom, of all the surfaces inside the 12,000 square metres building to ensure the required clean atmosphere—a task that has just begun and will take about four weeks to complete.
Click here to view a video, produced by the European agency for ITER, on the manufacturing process of the ITER poloidal field coils.
return to the latest published articles