Assembly tooling
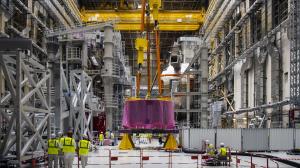
Assembling ITER requires tools to lift, tools to suspend, tools to transport, tools to assemble, tools to adjust ... over 100 custom devices have been designed for the assembly phases of the ITER machine.
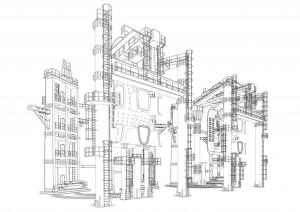
A broad array of large, purpose-built assembly tools are required for ITER. These mainly motor-driven or hydraulic-powered tools are designed to accomplish specific tasks—lifting, adjusting, supporting, transporting, aligning—during assembly of the ITER Tokamak device.
The tools have loading capacities that vary from 500 tonnes for the "upending" tool that turns vacuum vessel sectors from horizontal to vertical, to 1,500 tonnes for the heavy lift cranes overhead in the assembly theatre.
In addition to the large, specialized tools, more standard tooling, generally for lifting and handling, has been designed and procured either by the ITER Organization or by assembly works contractors with specific tasks to carry out.
For major components weighing hundreds of tonnes—and with linear dimensions of up to 24 metres—the positioning tolerances are in the low-millimetre range. This subset of components includes the vacuum vessel sector assemblies, the poloidal field magnets, the central solenoid, and the cryostat.
After core machine assembly and the closure of the cryostat, in-vessel component installation will take place through the port openings of the vacuum vessel. The ITER Organization is procuring a set of specifically engineered tools for these challenging operations.
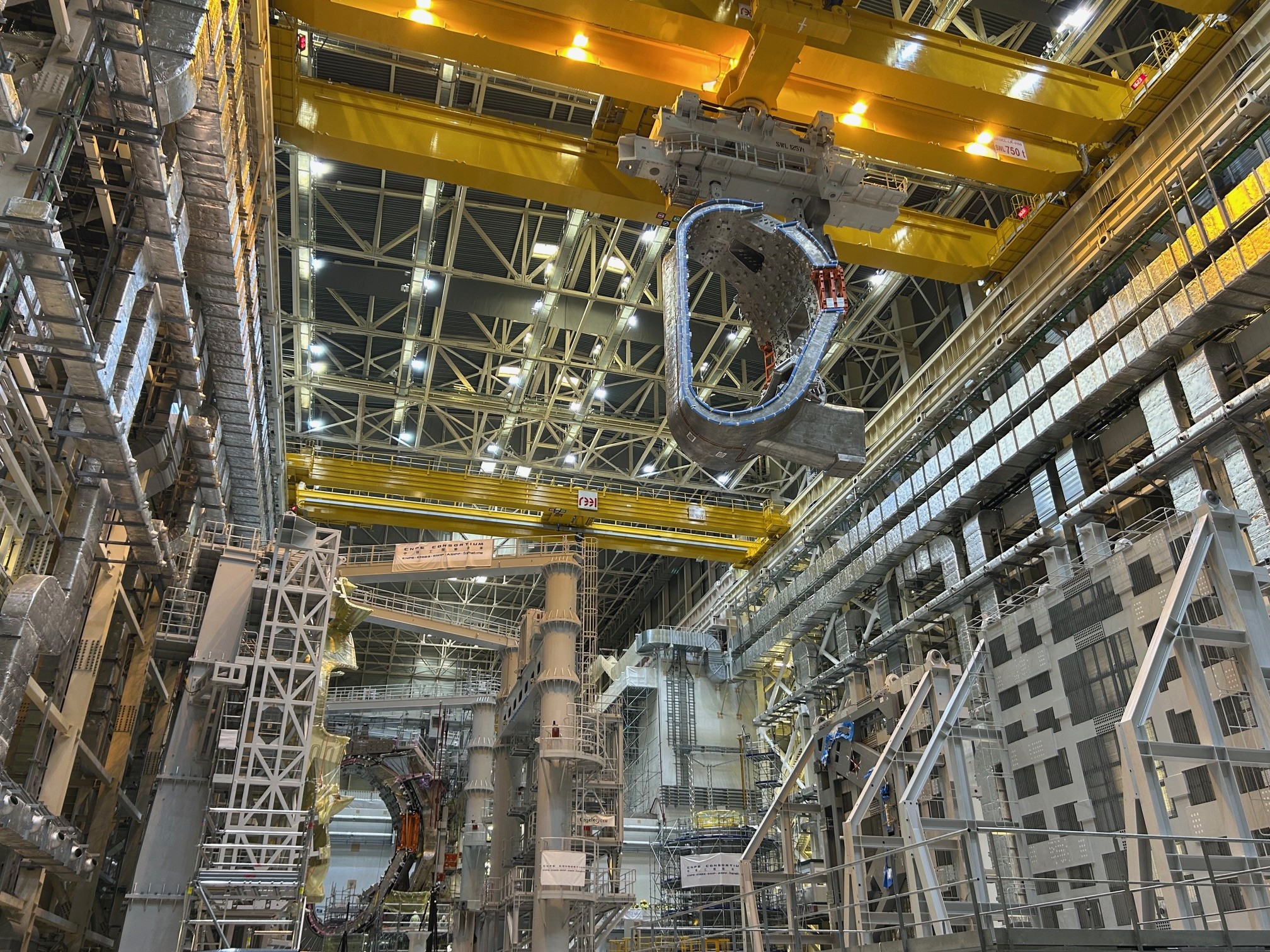
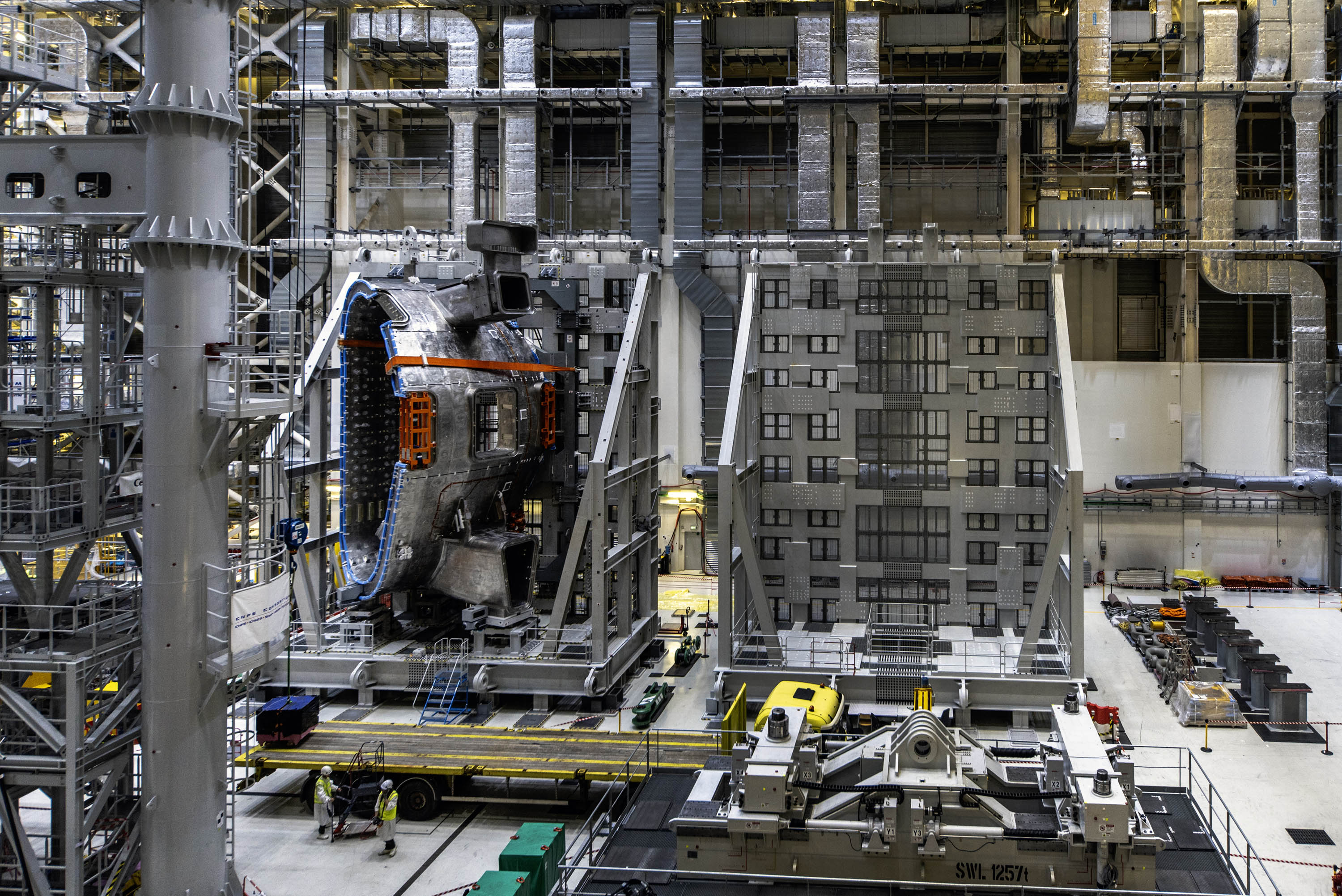
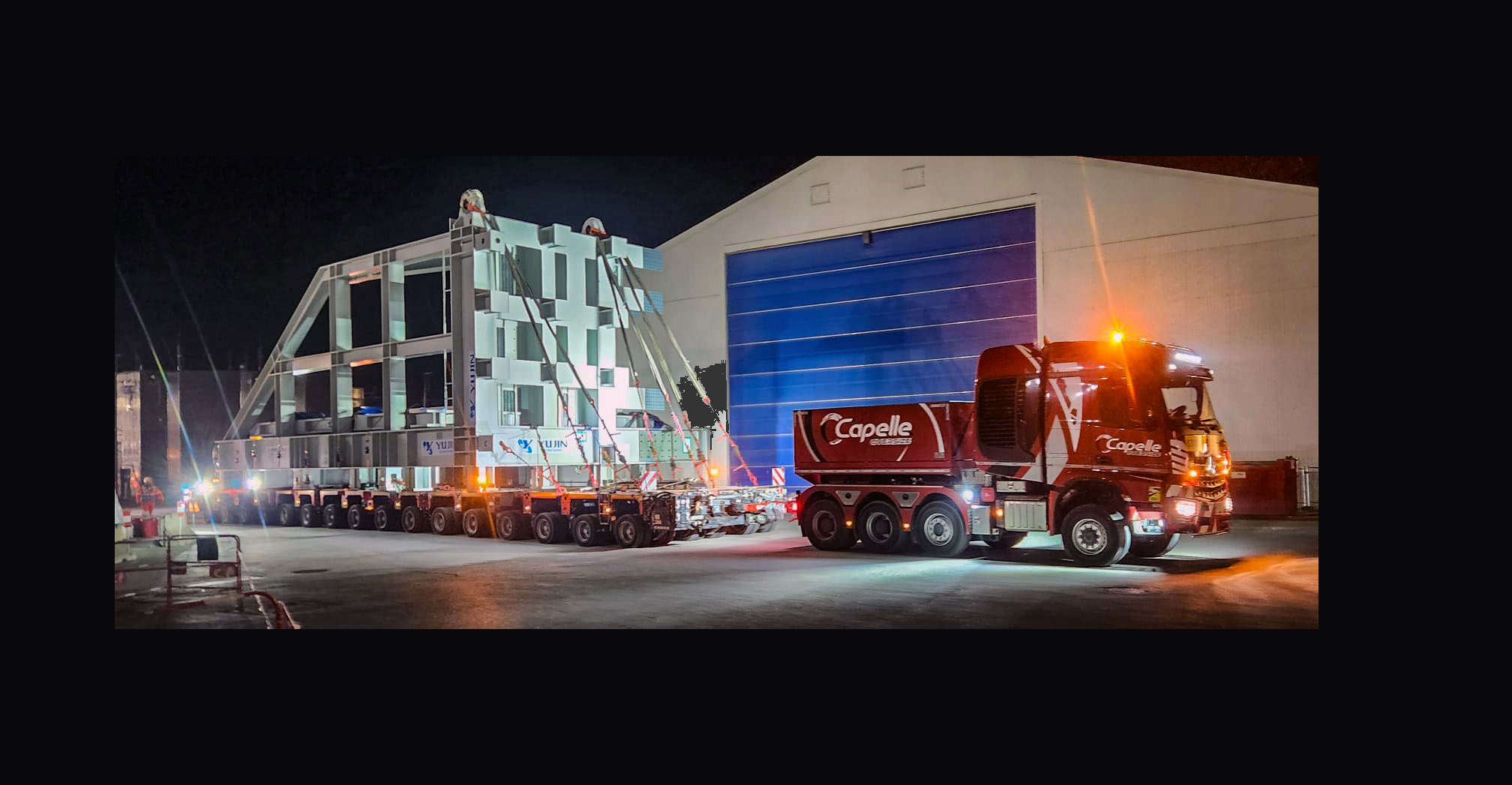
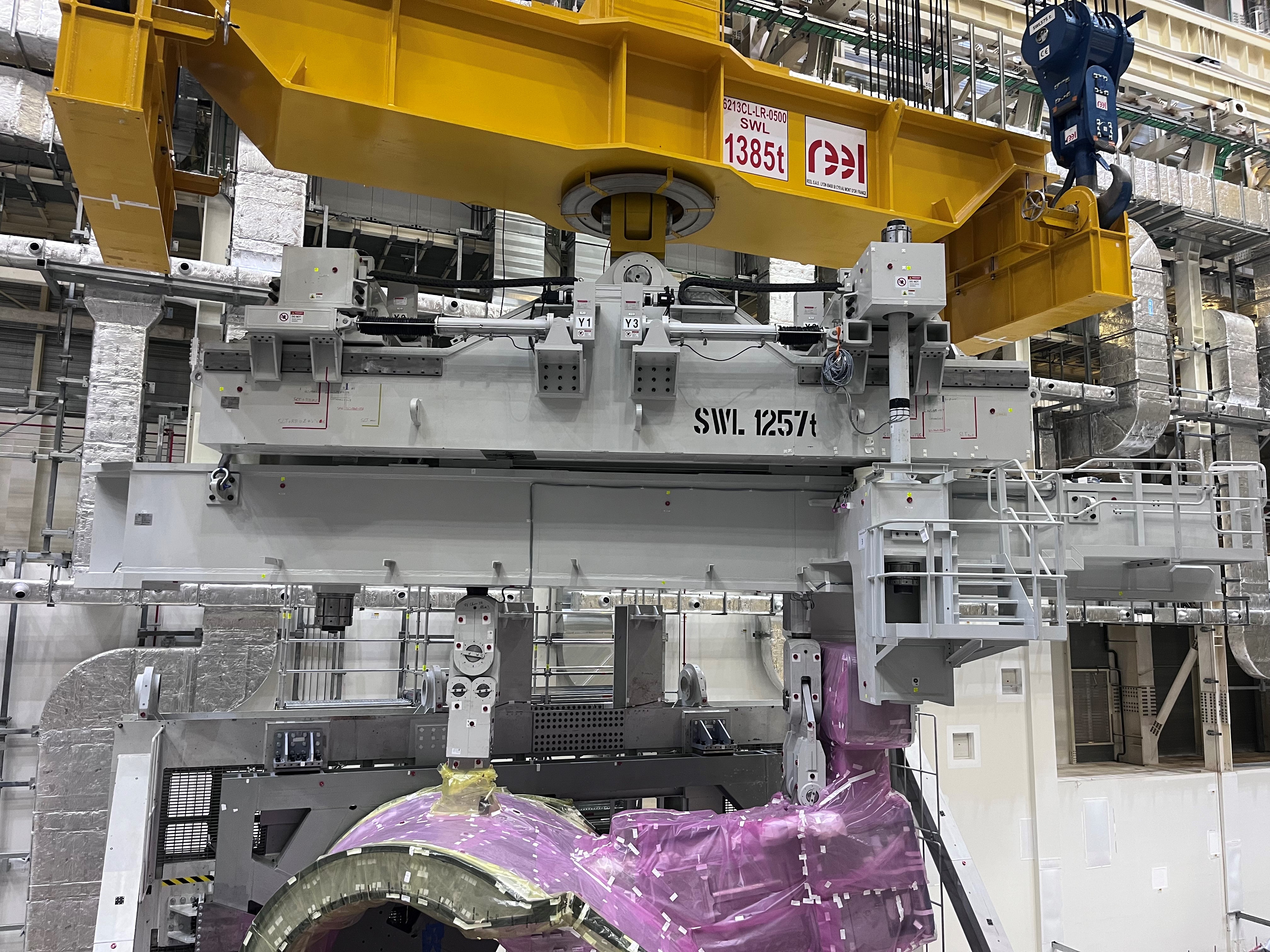
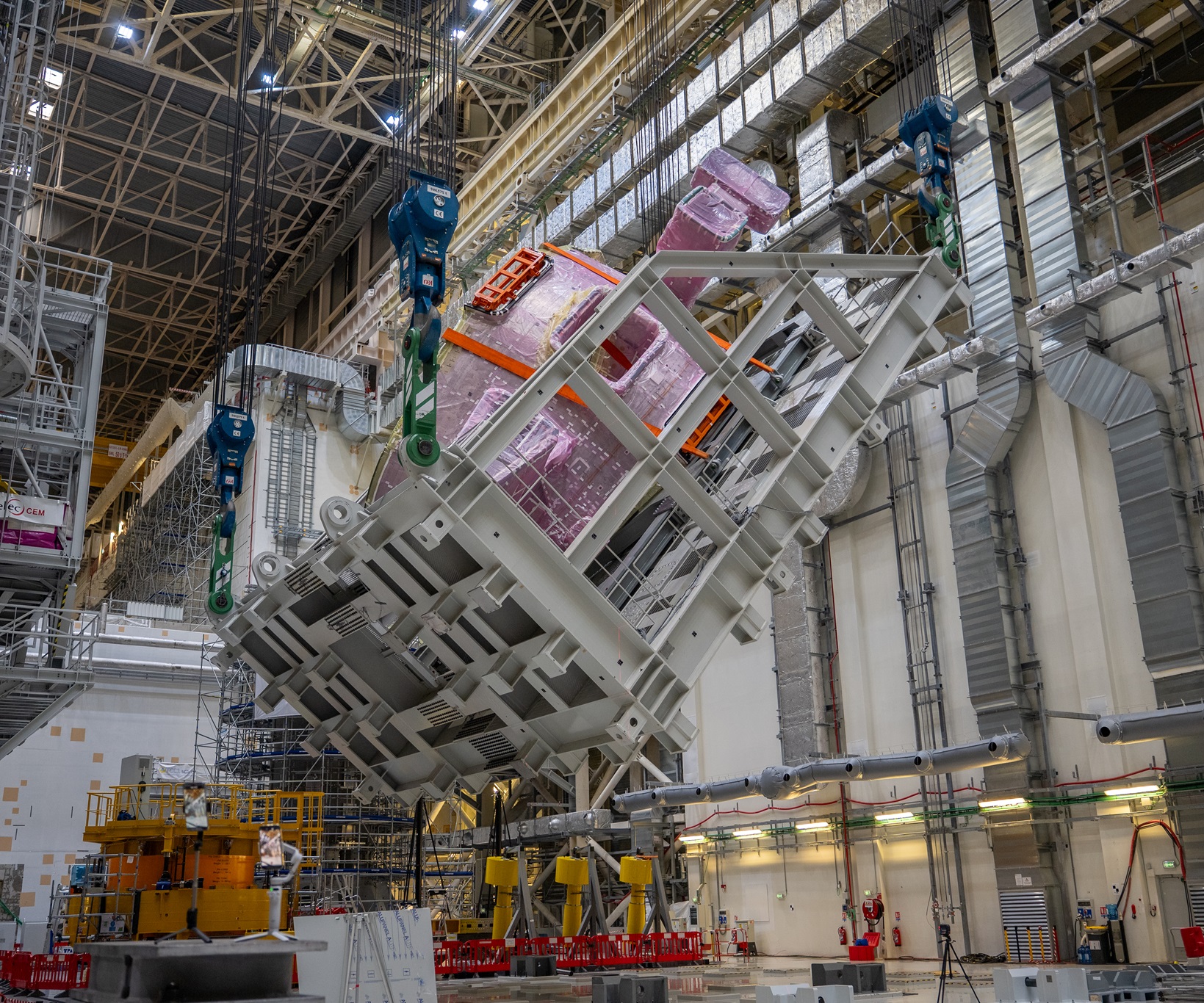
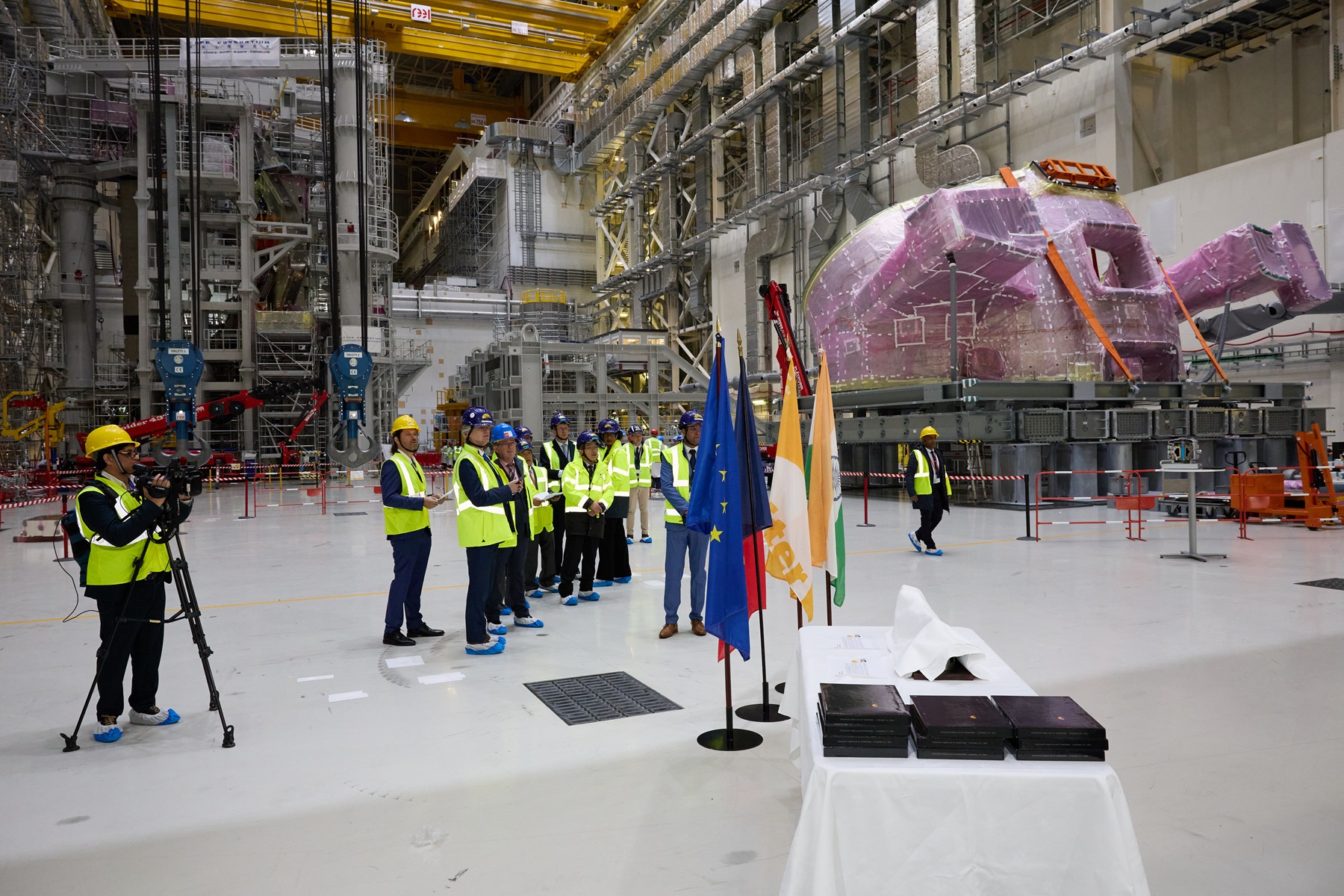
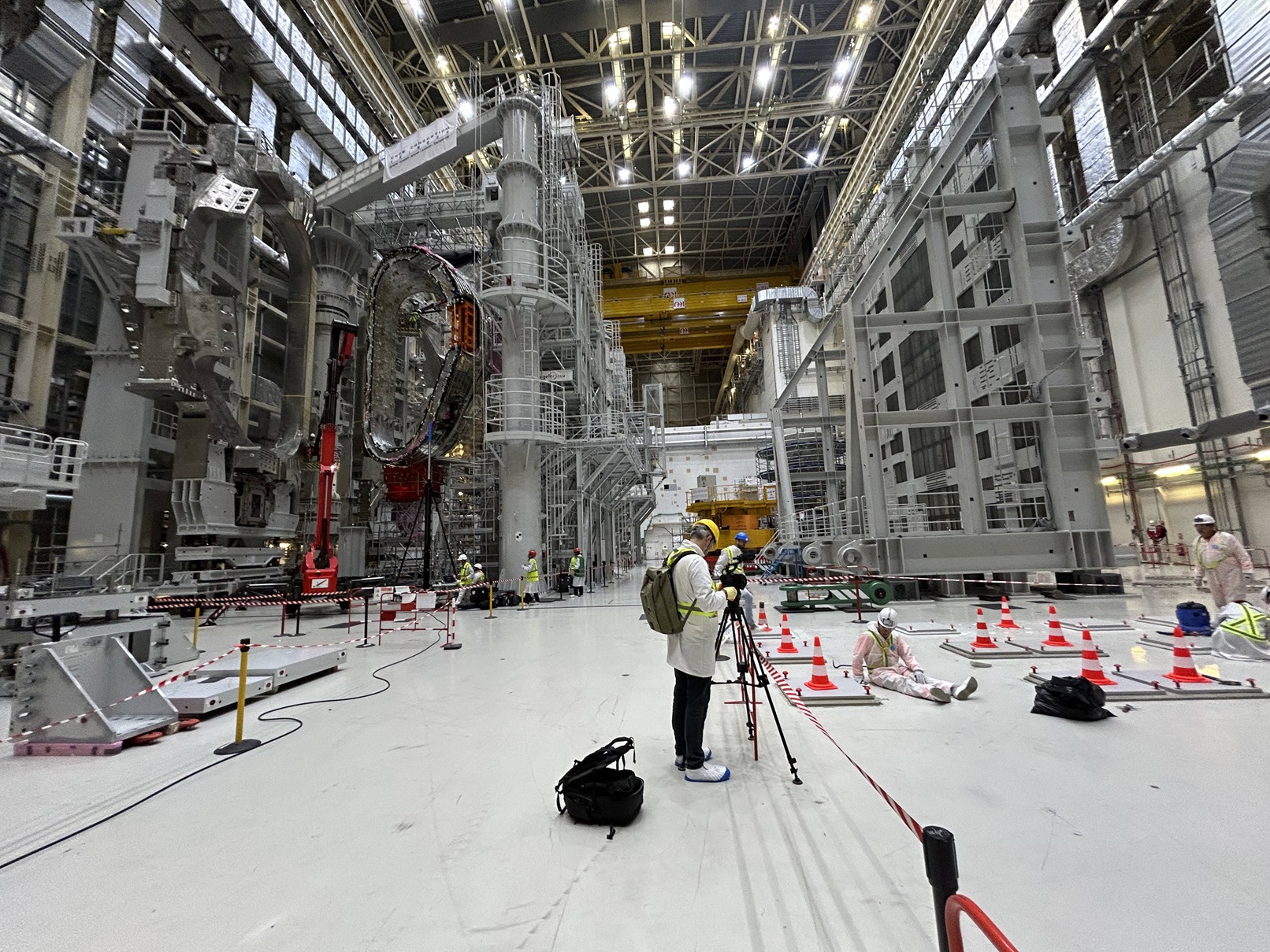
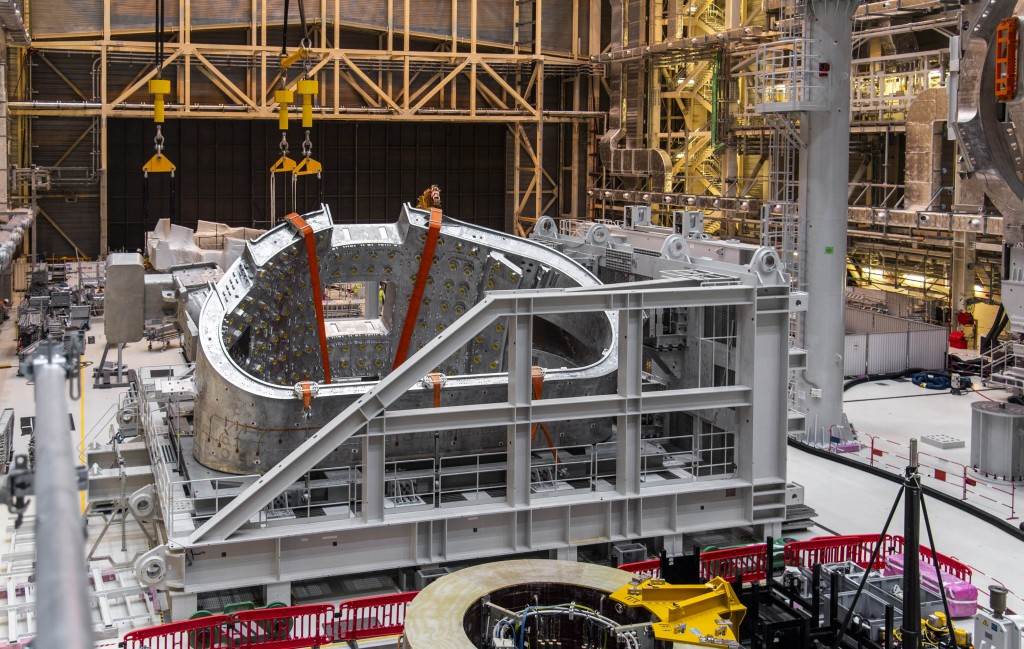
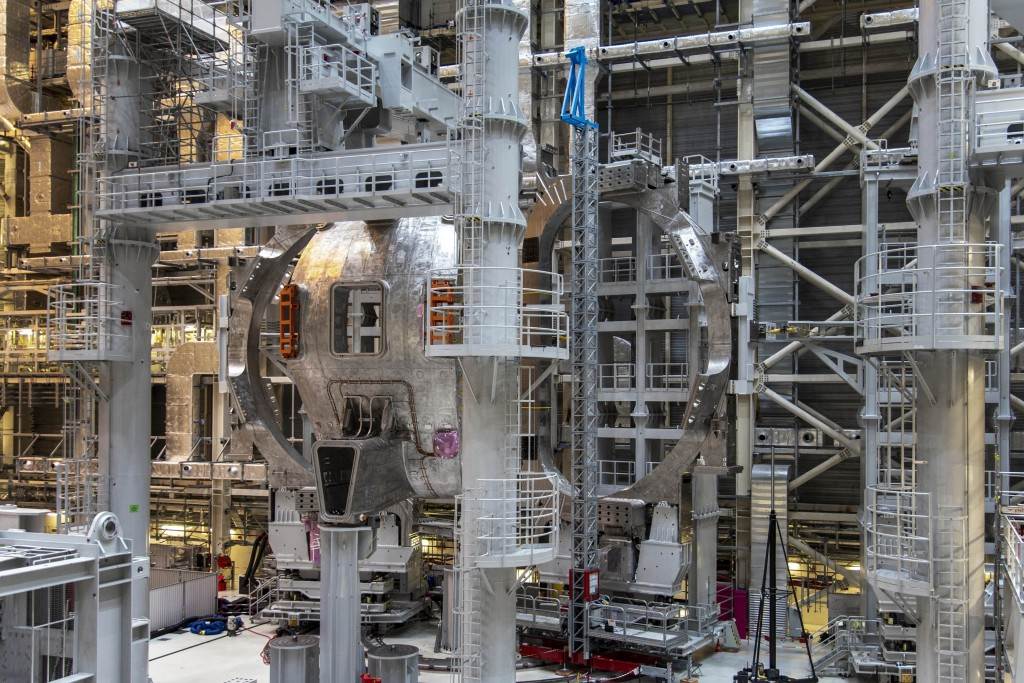
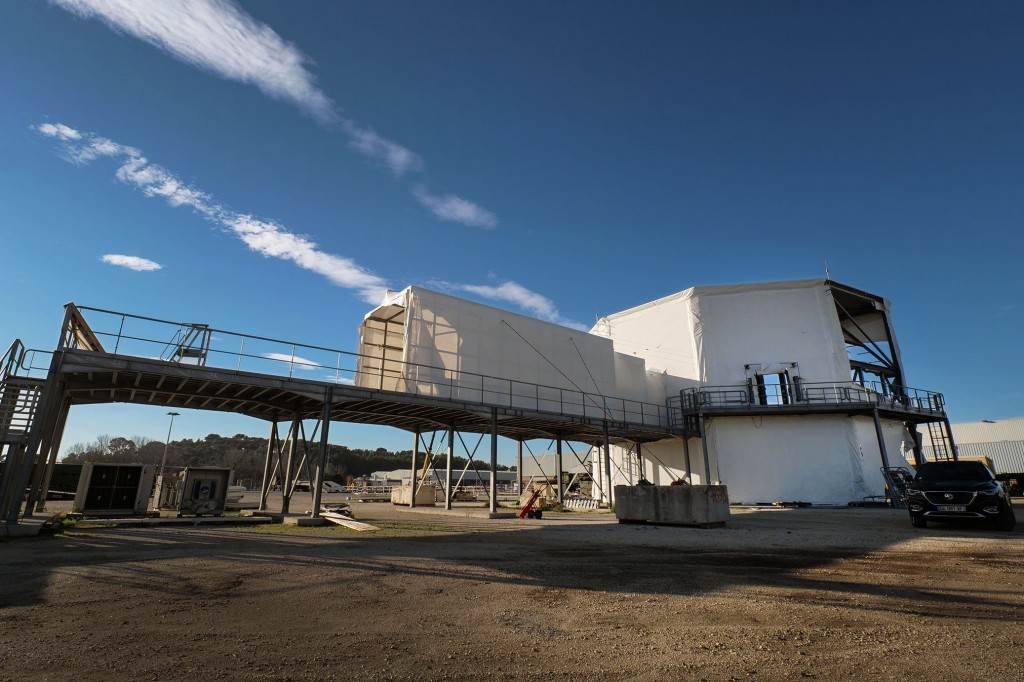
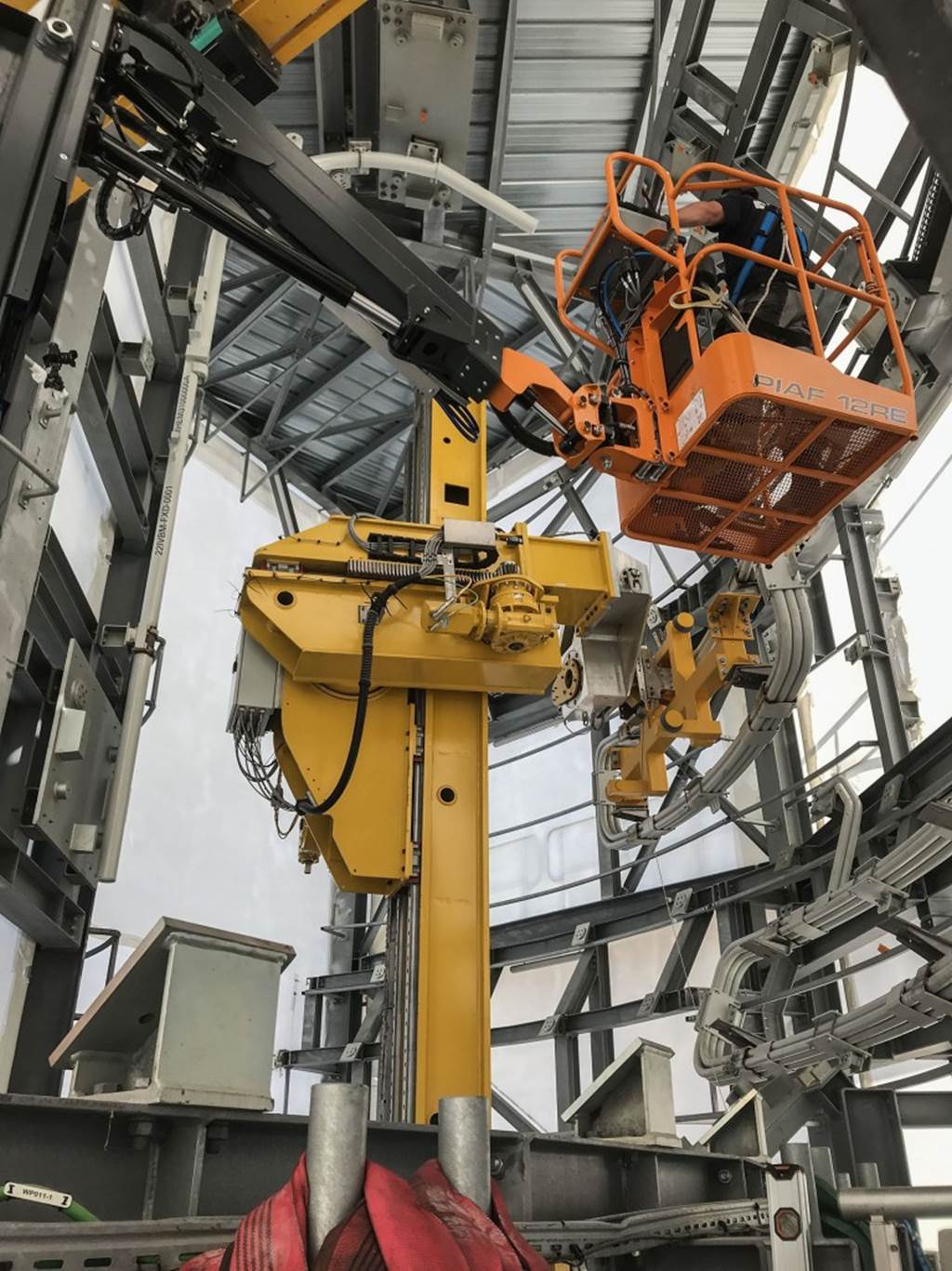
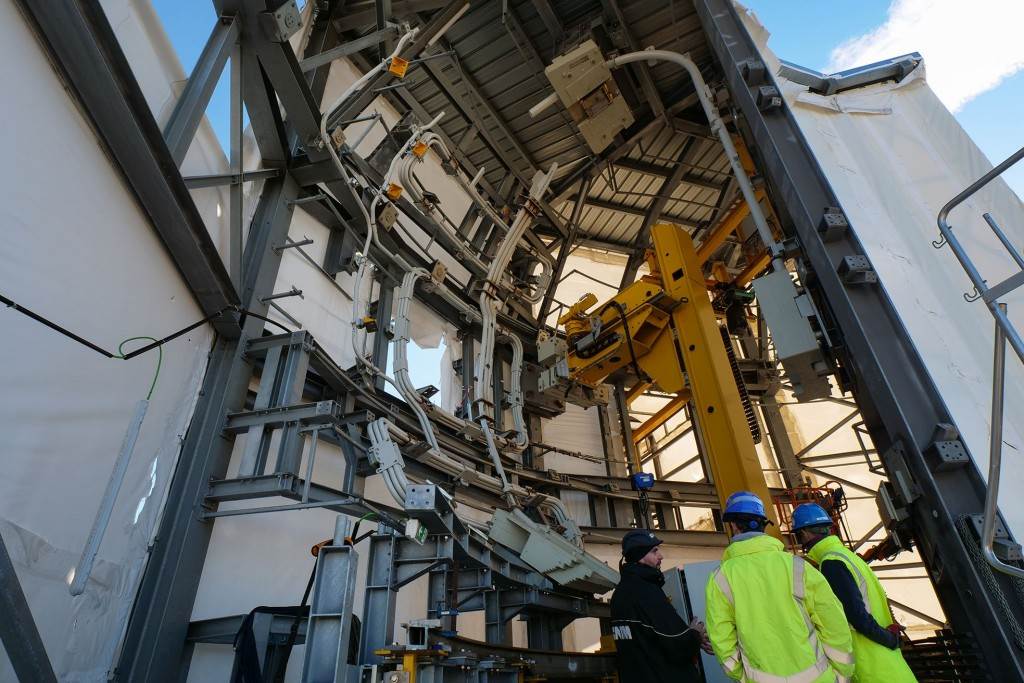
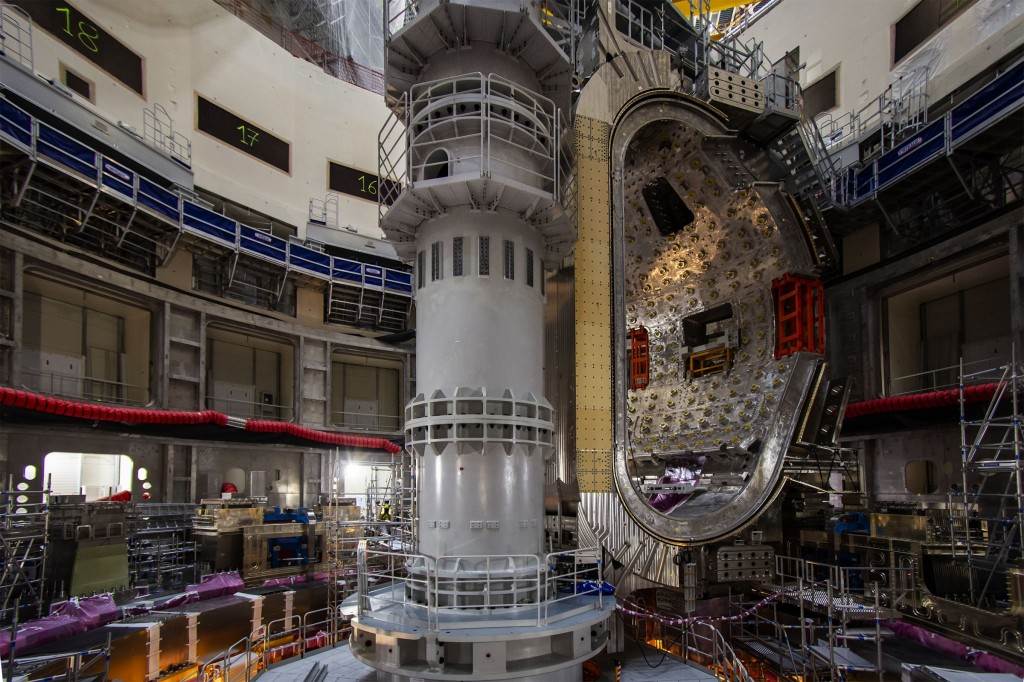
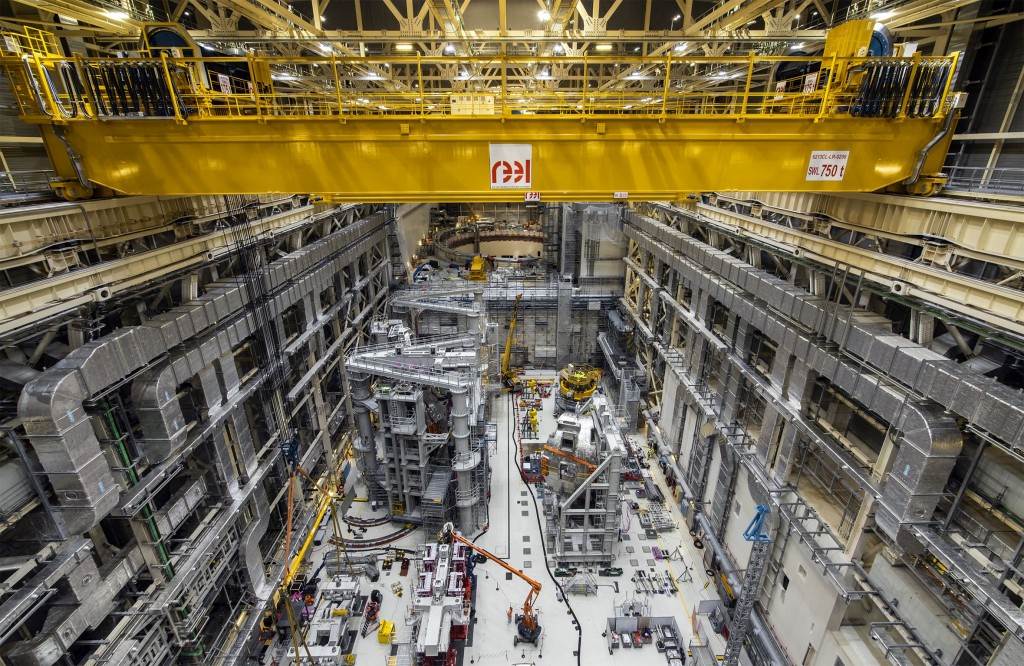
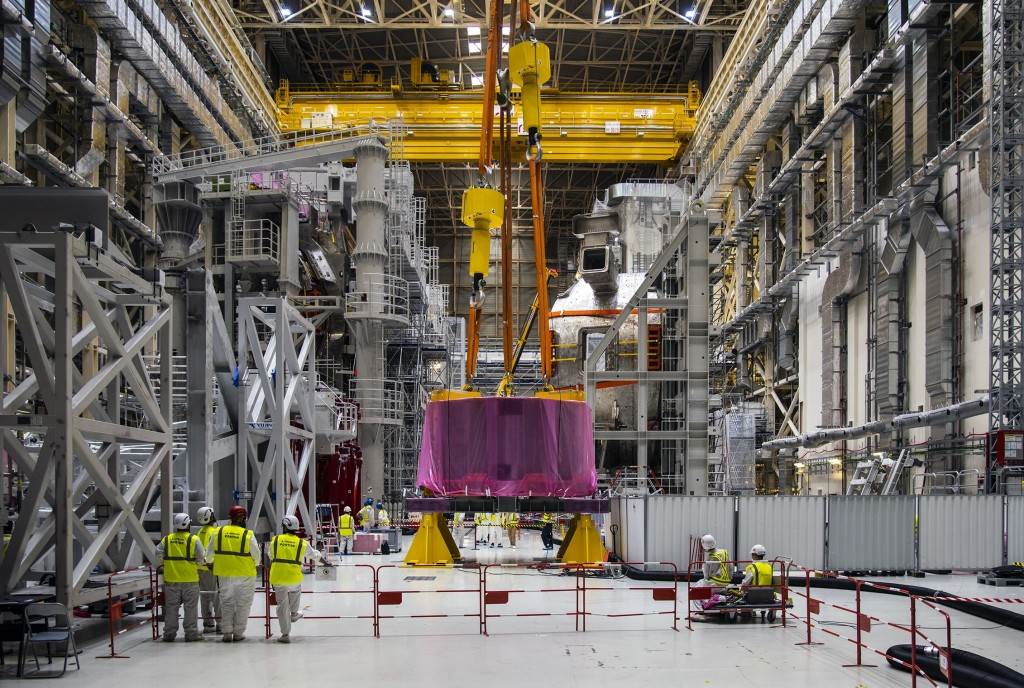
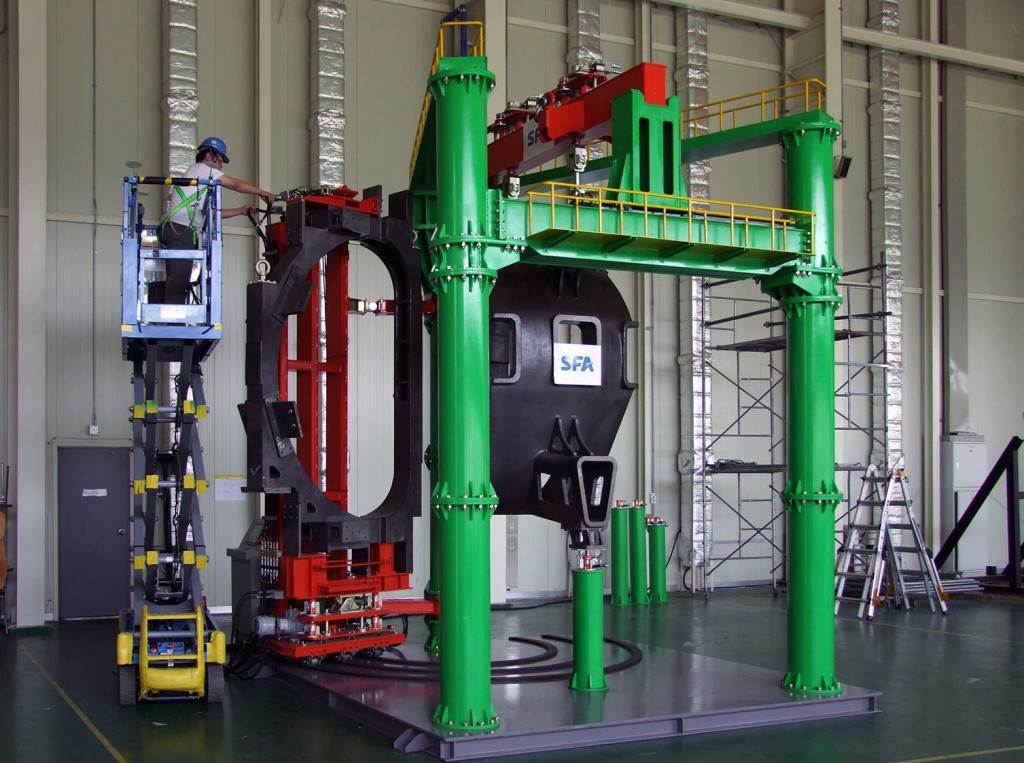
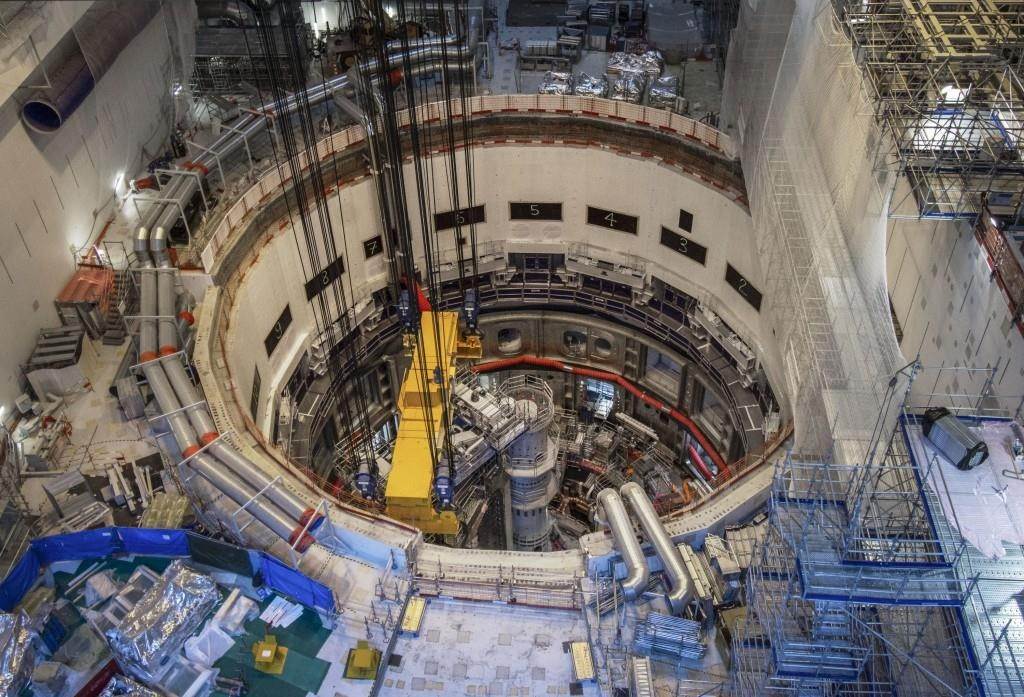
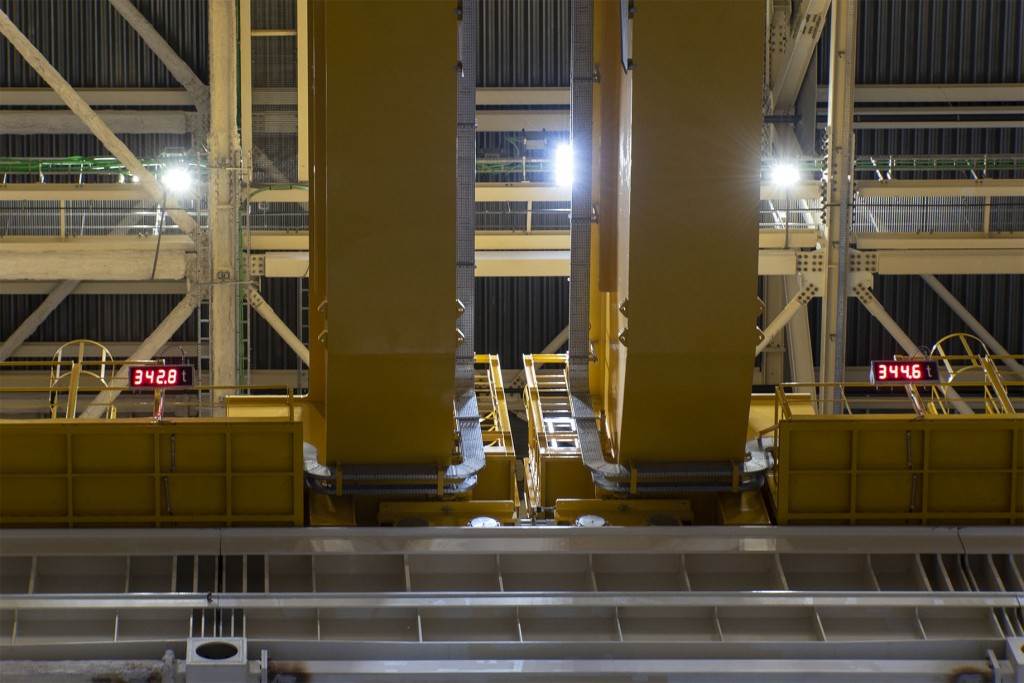
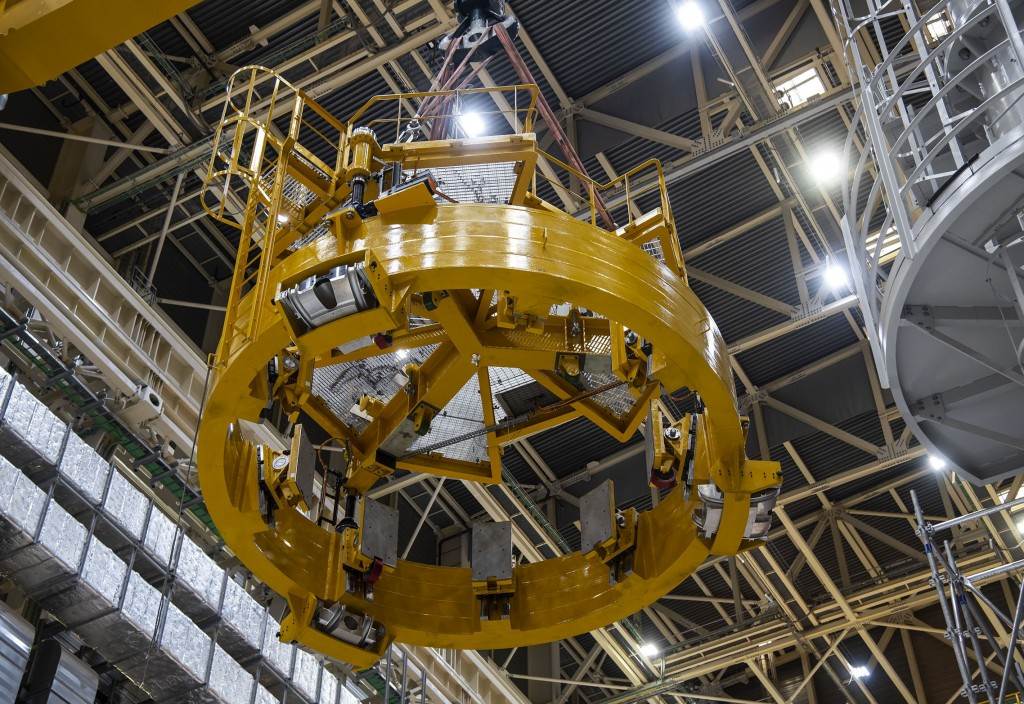
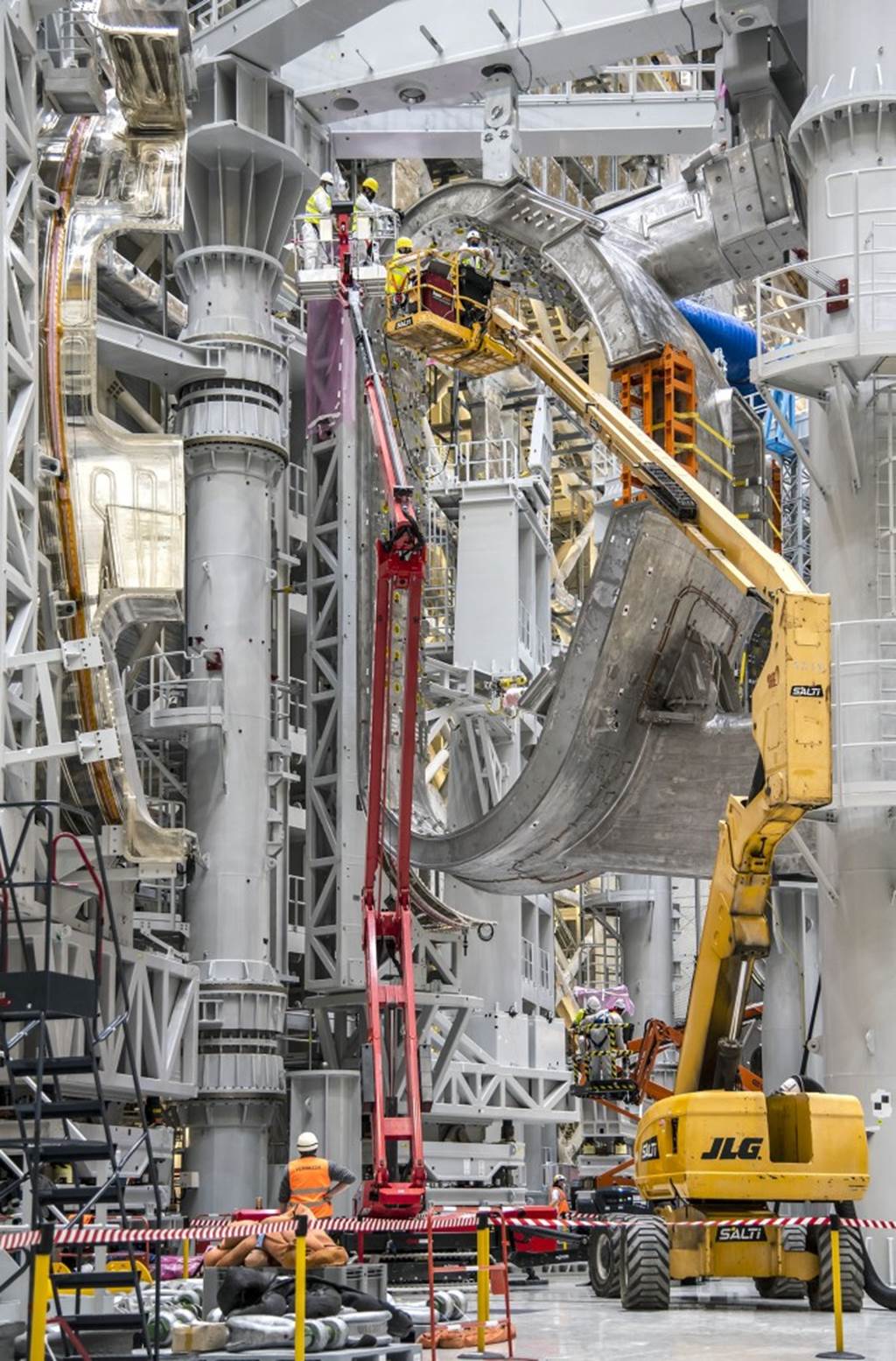
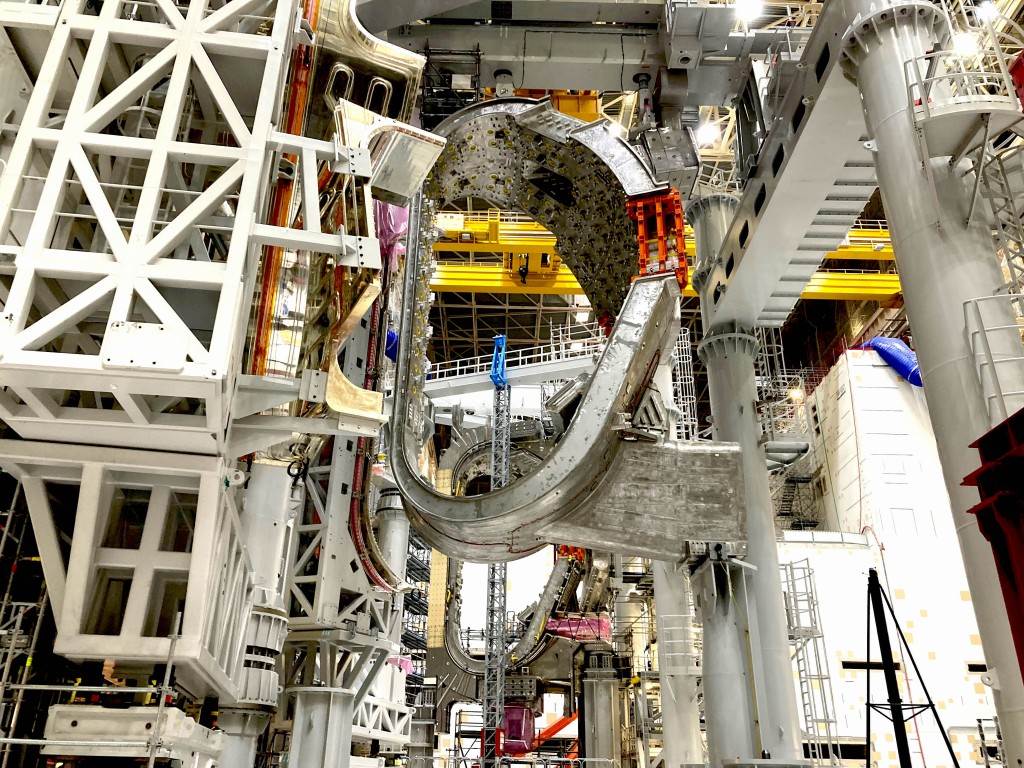
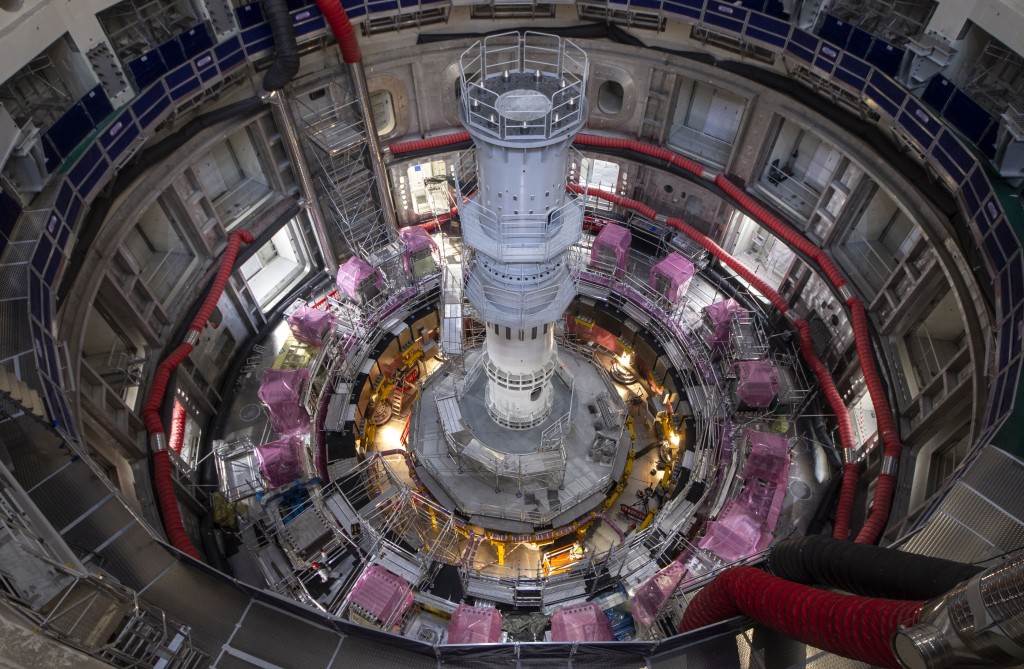
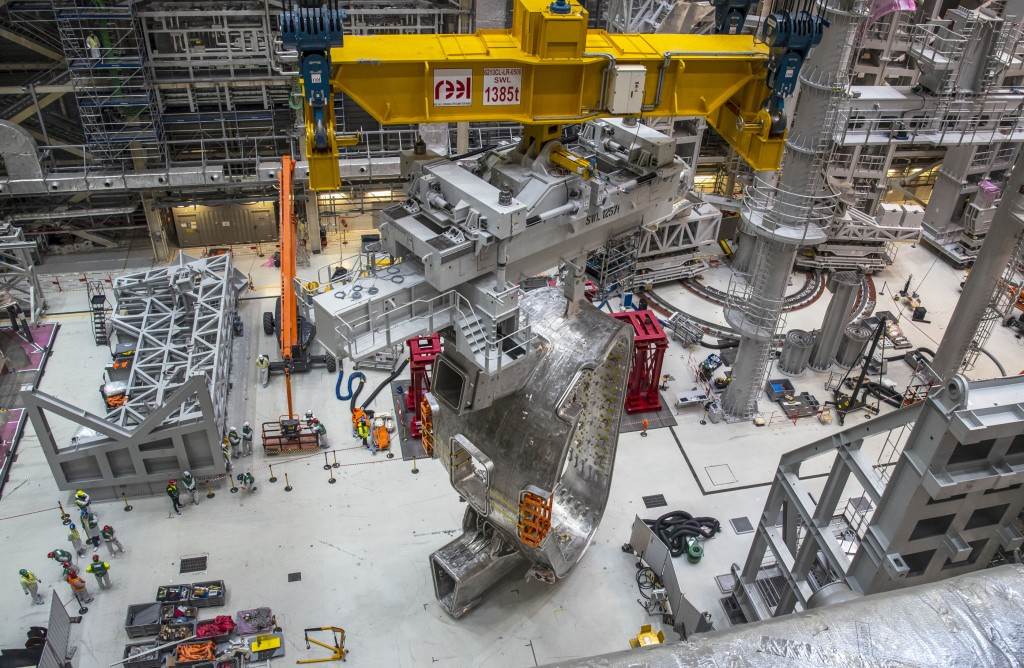
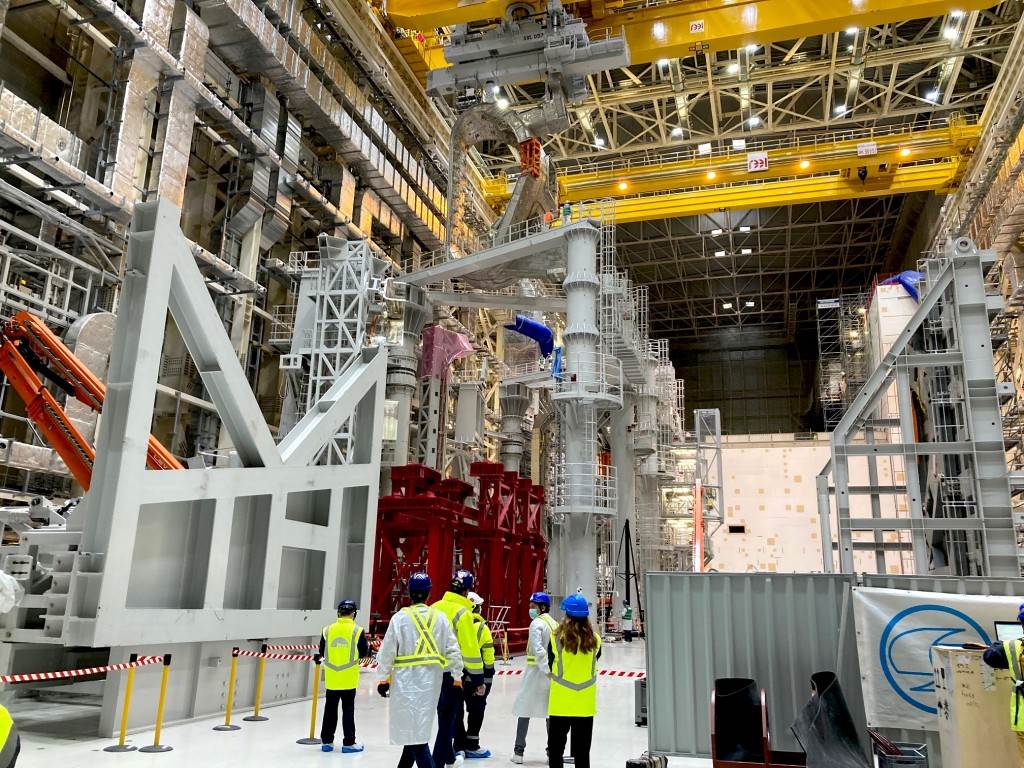
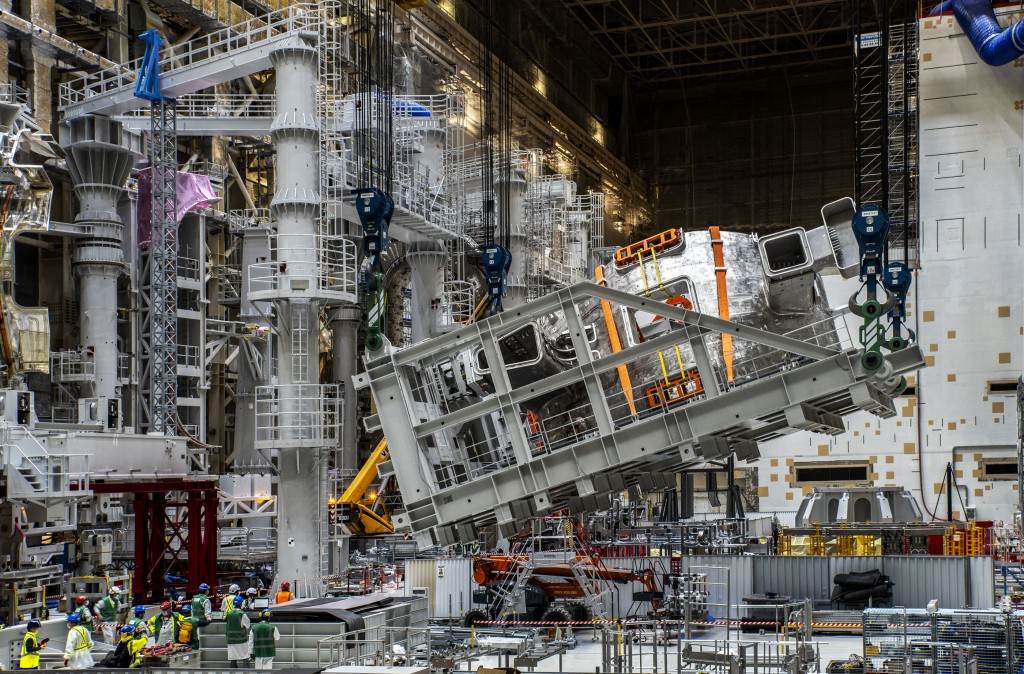
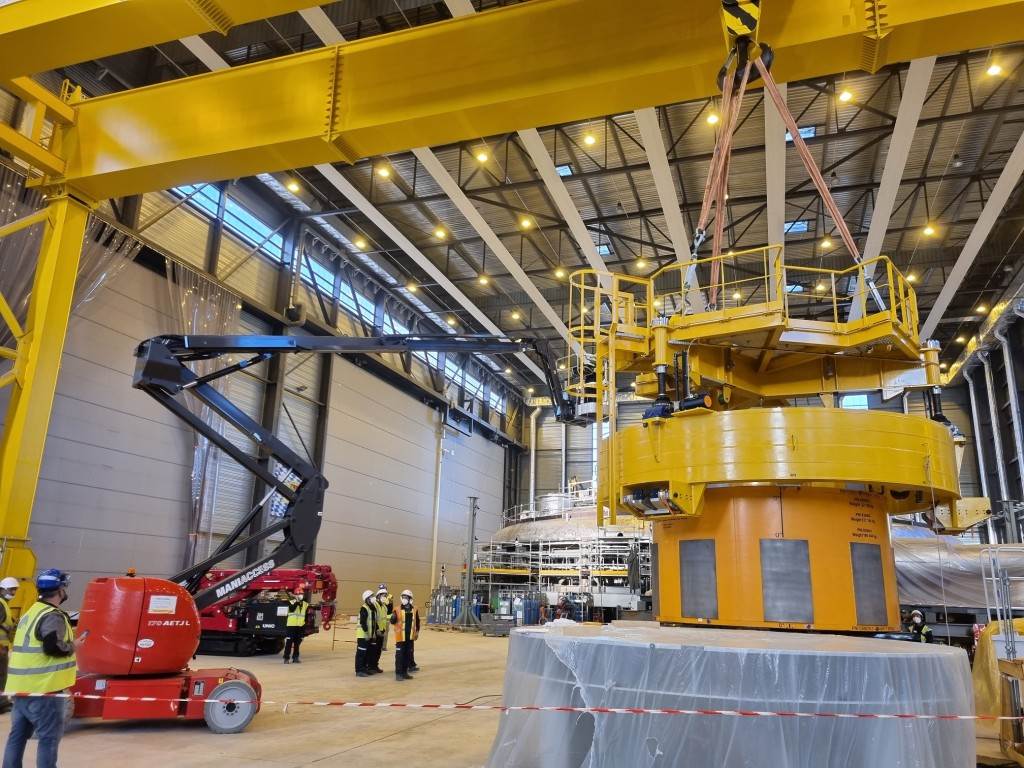
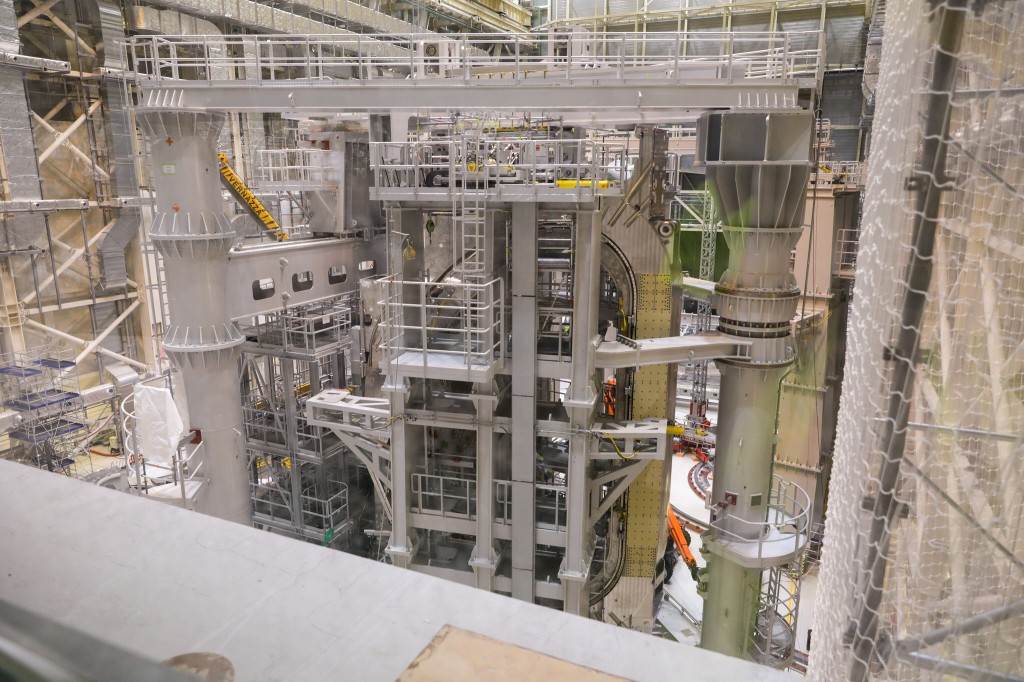
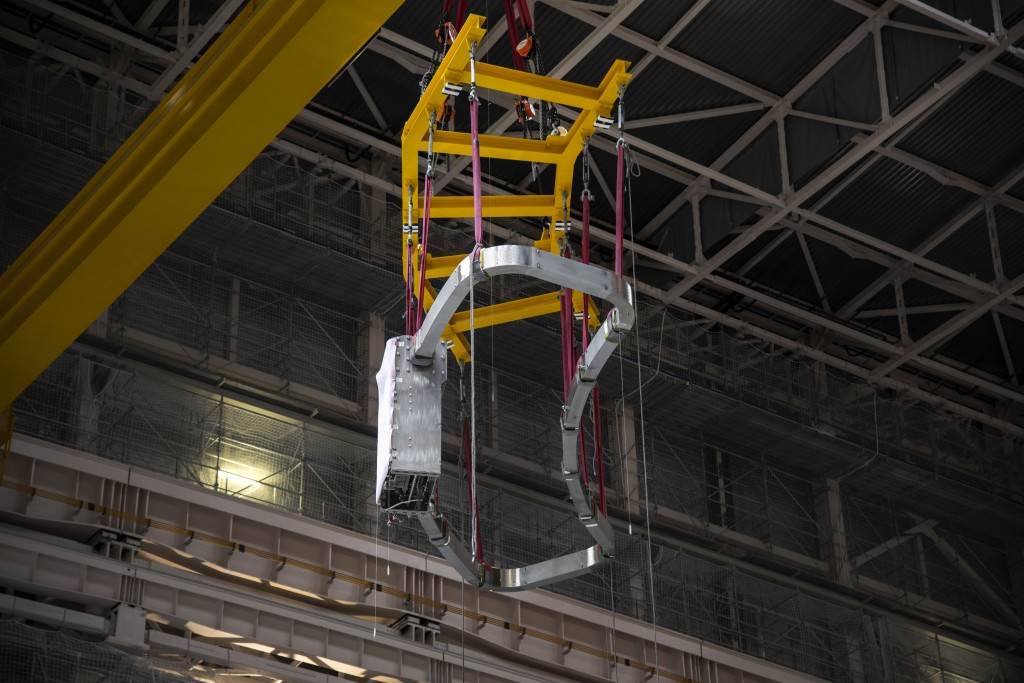

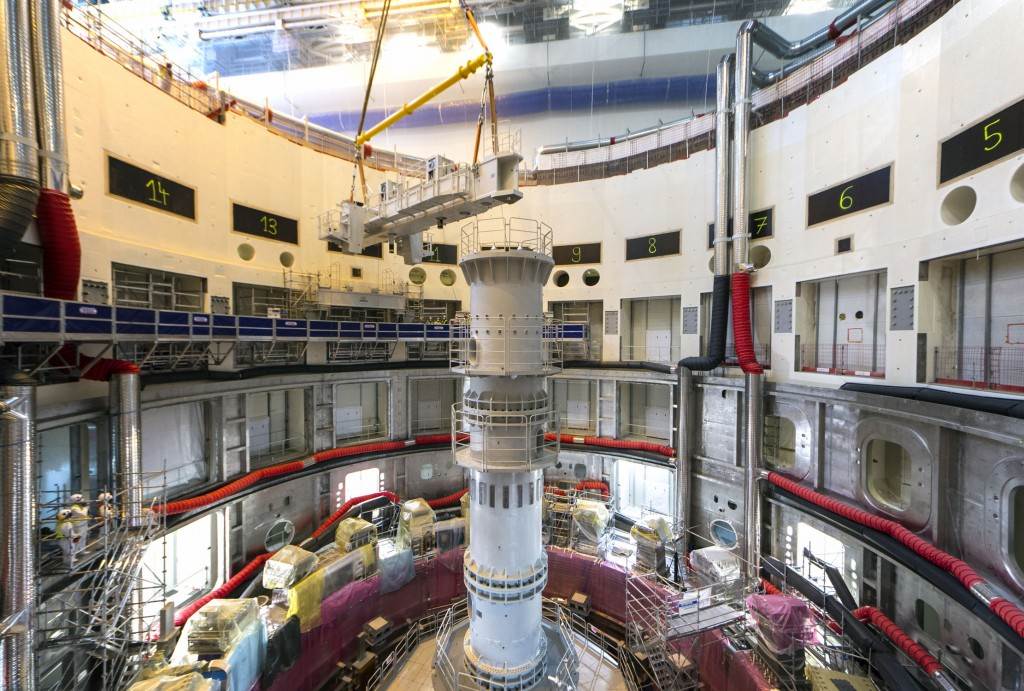
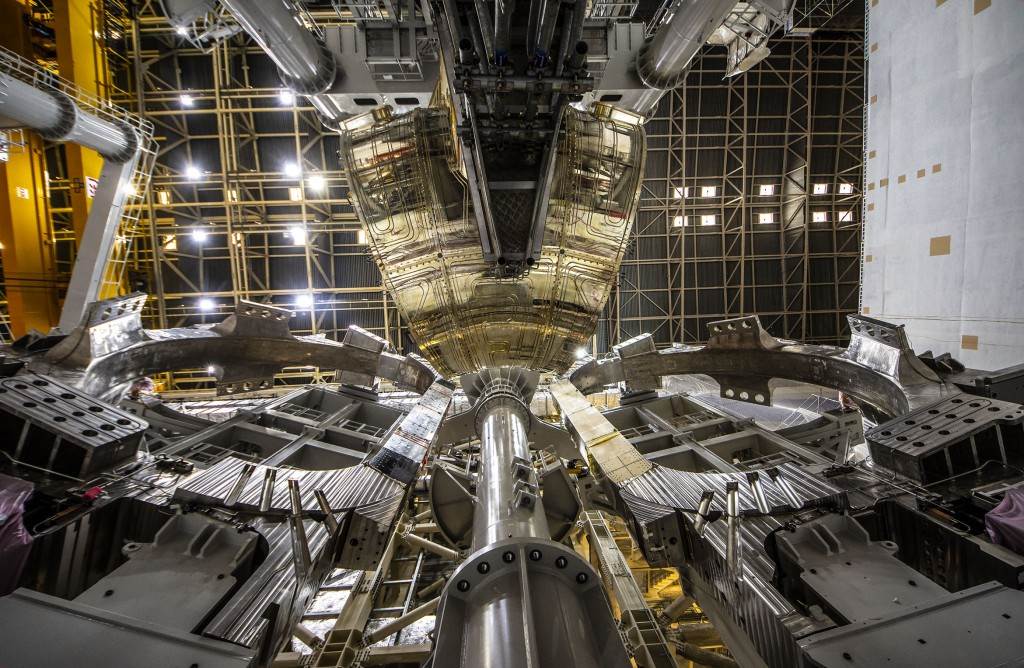
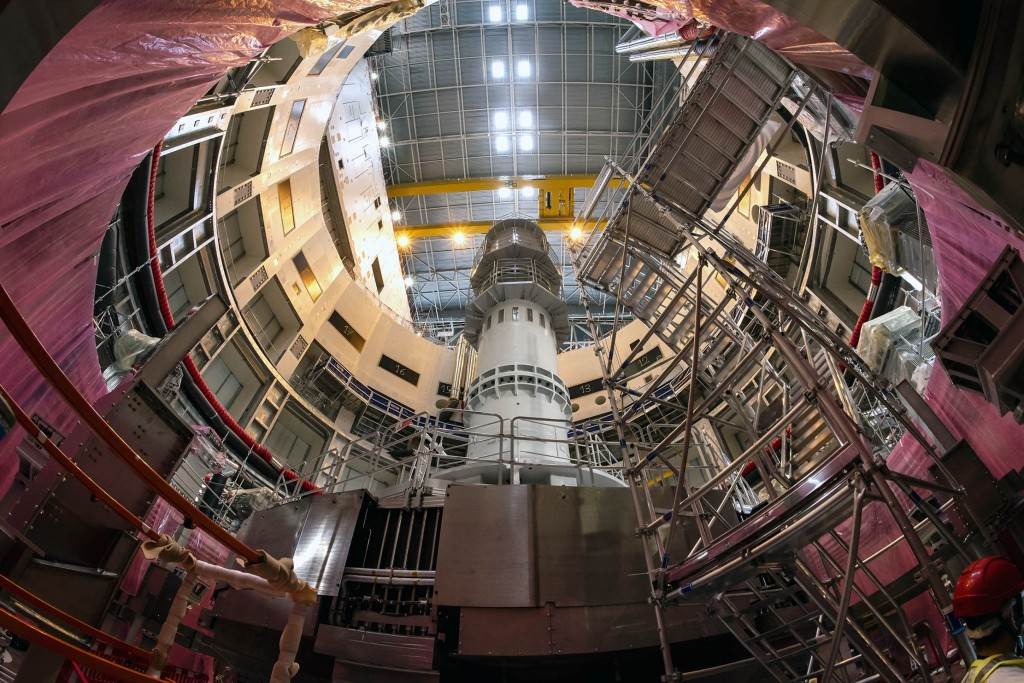
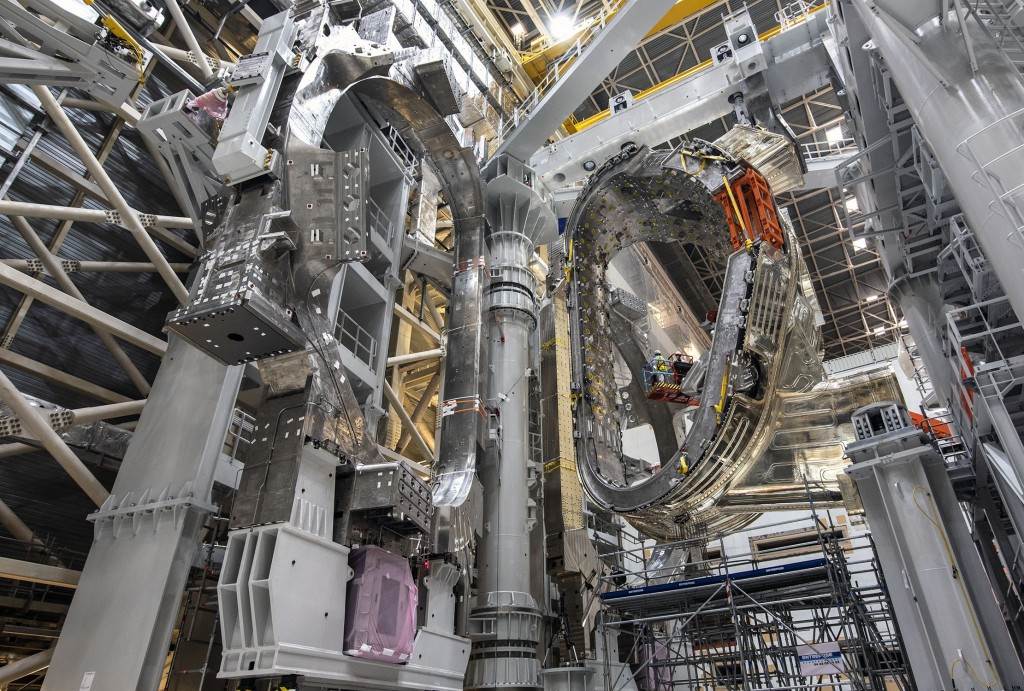
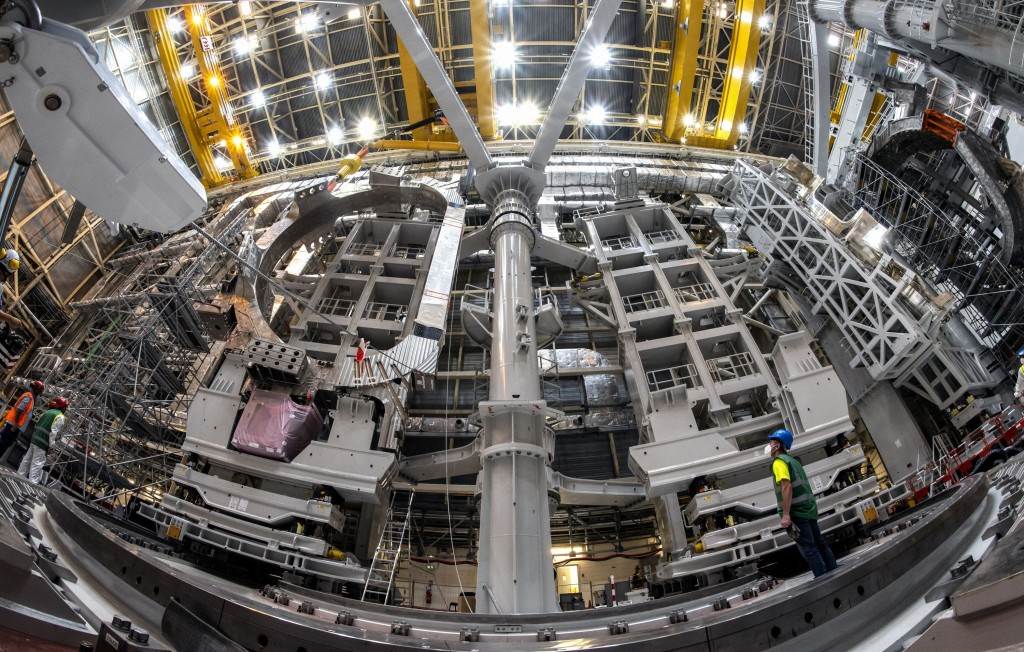
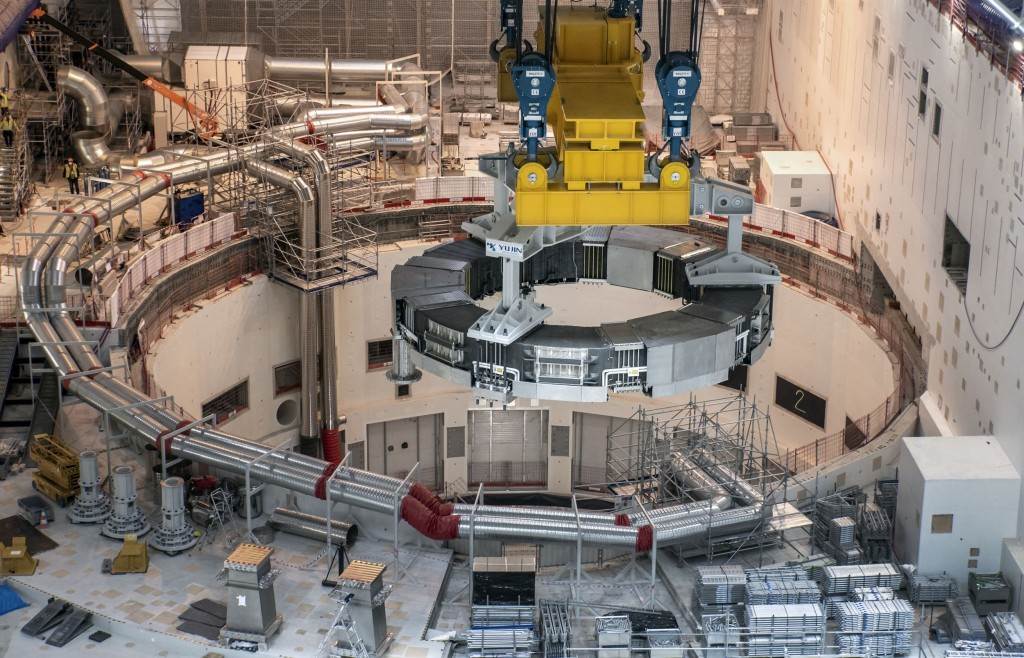
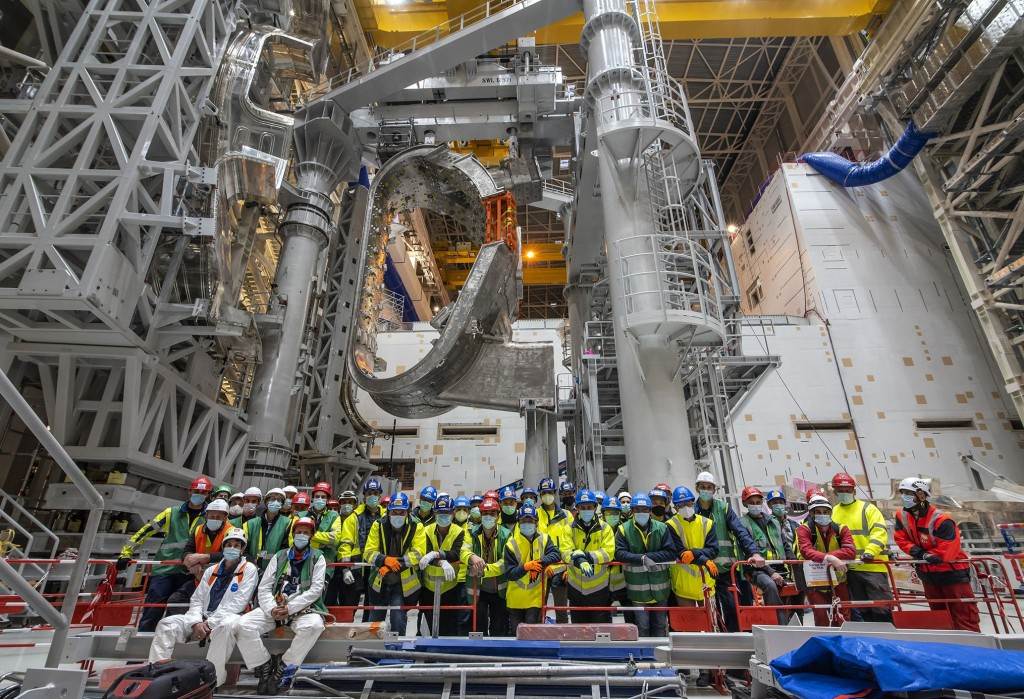
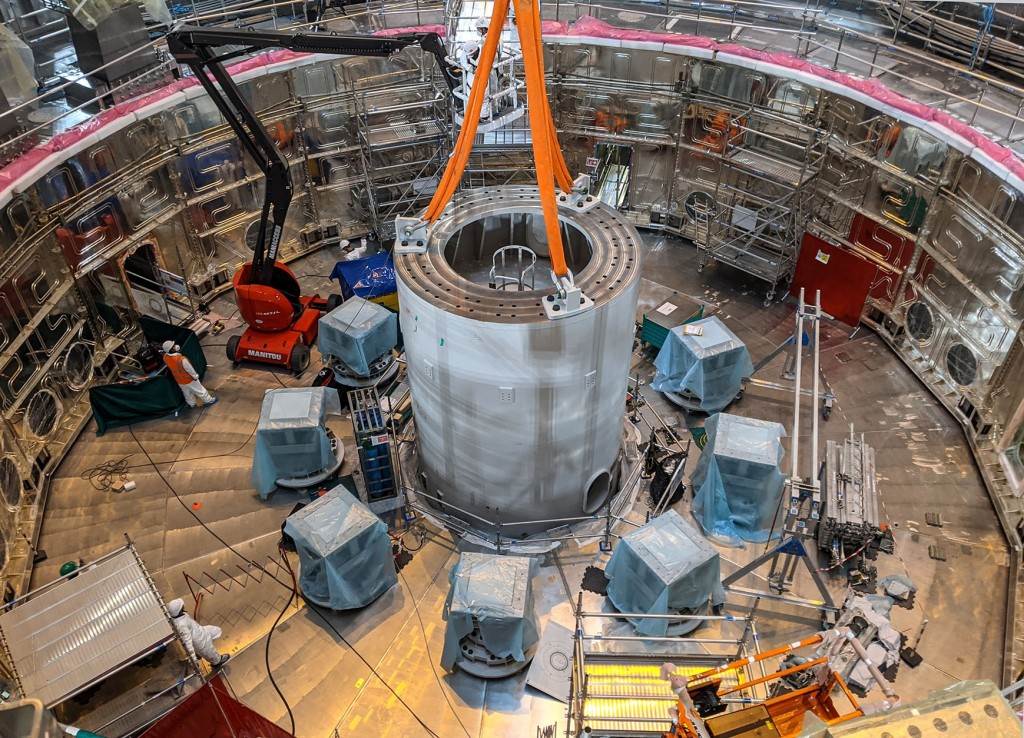
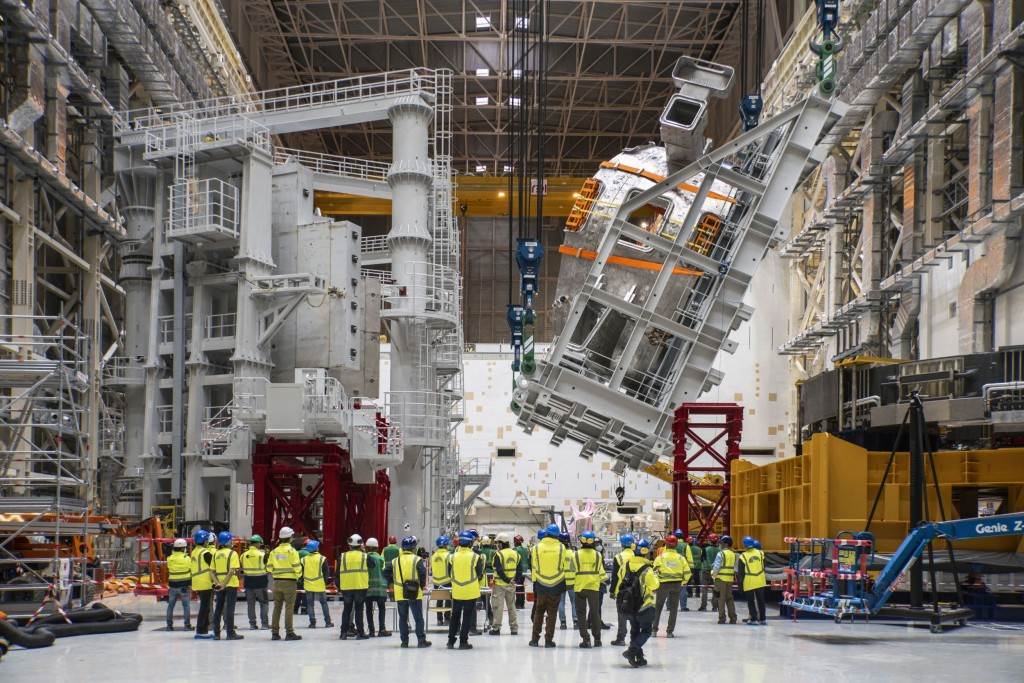
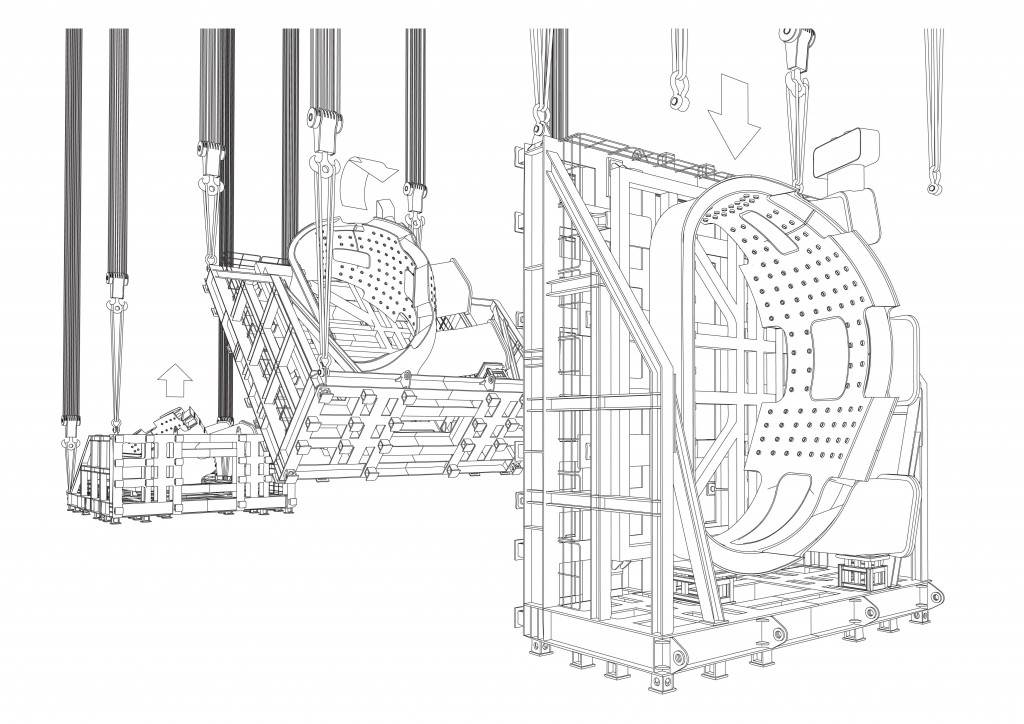
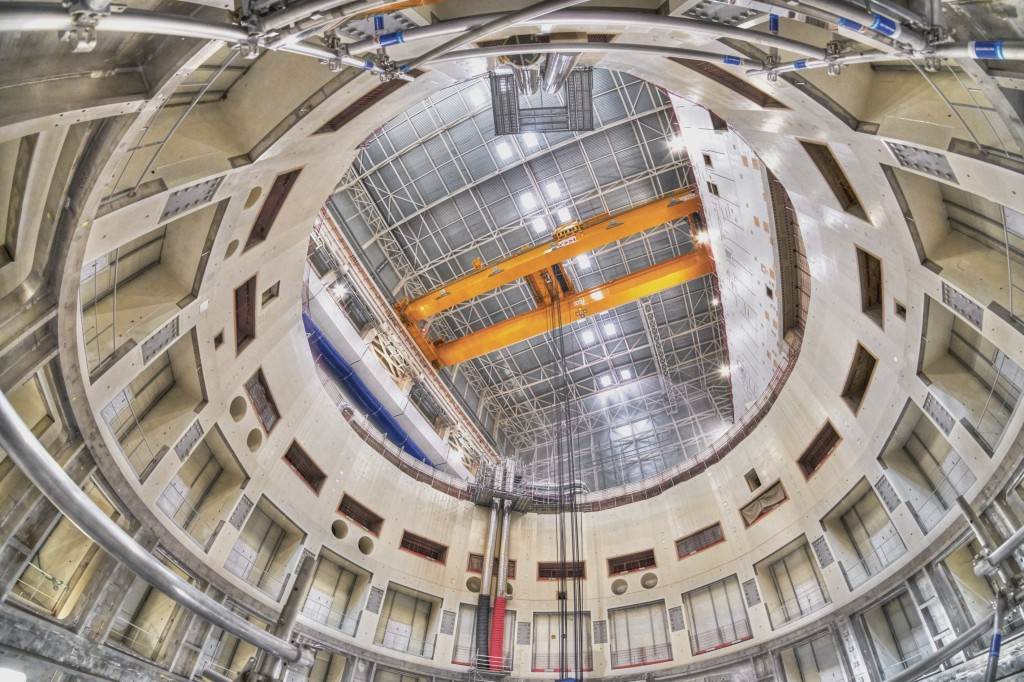
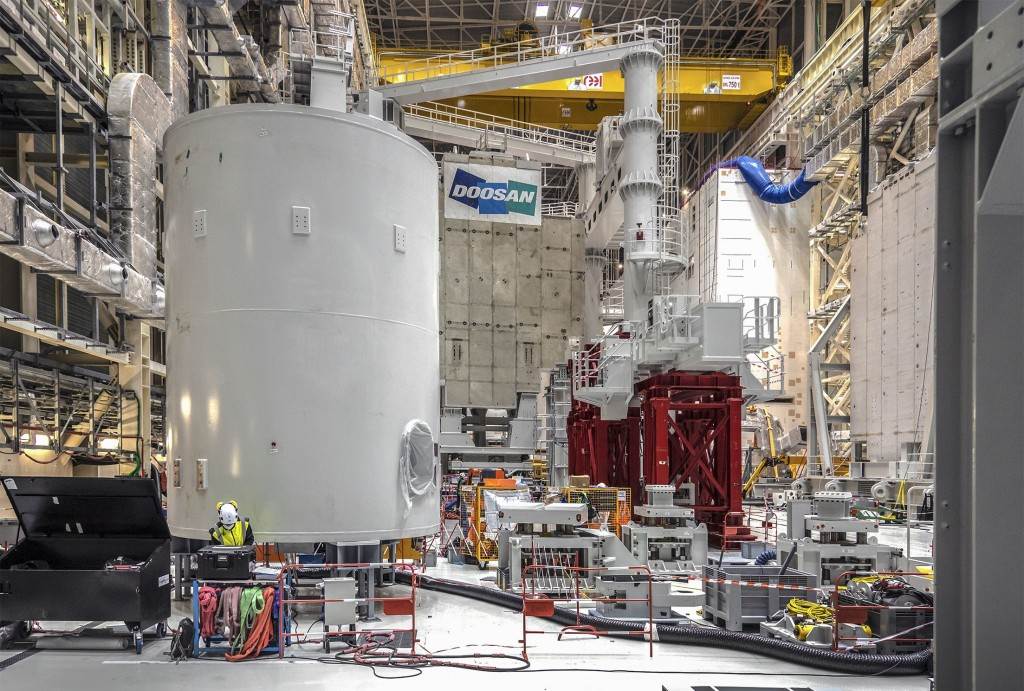
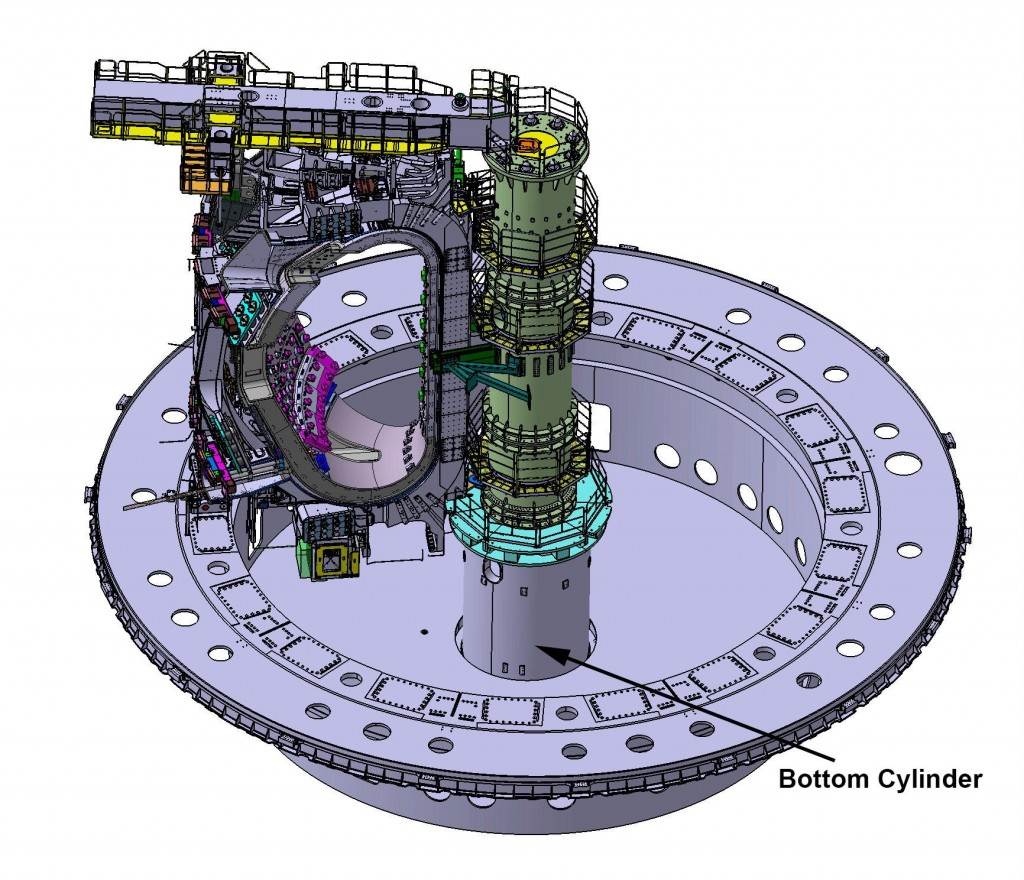
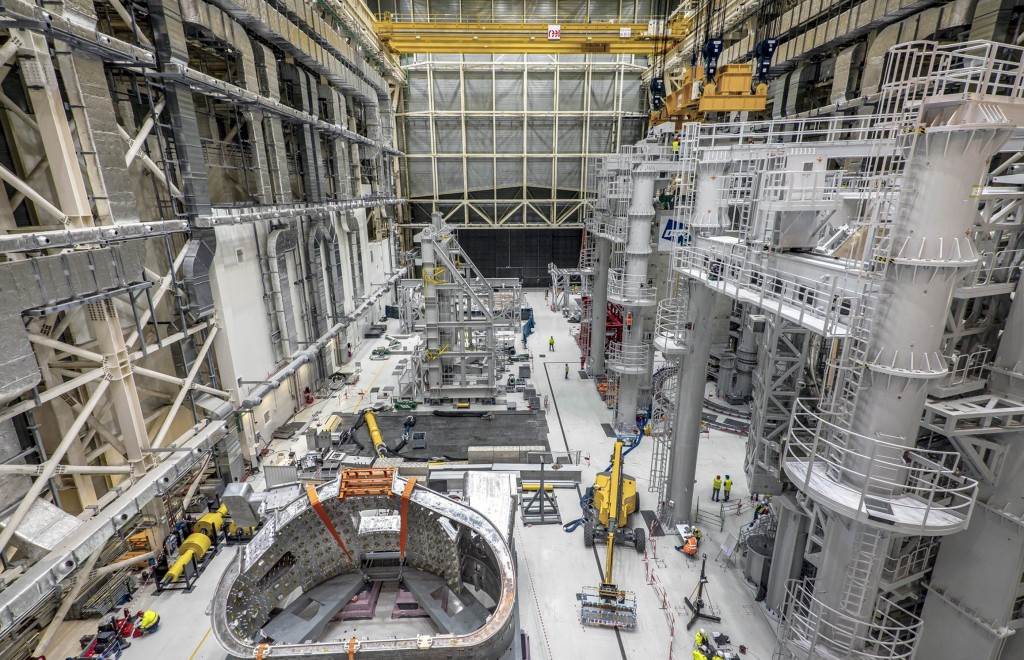
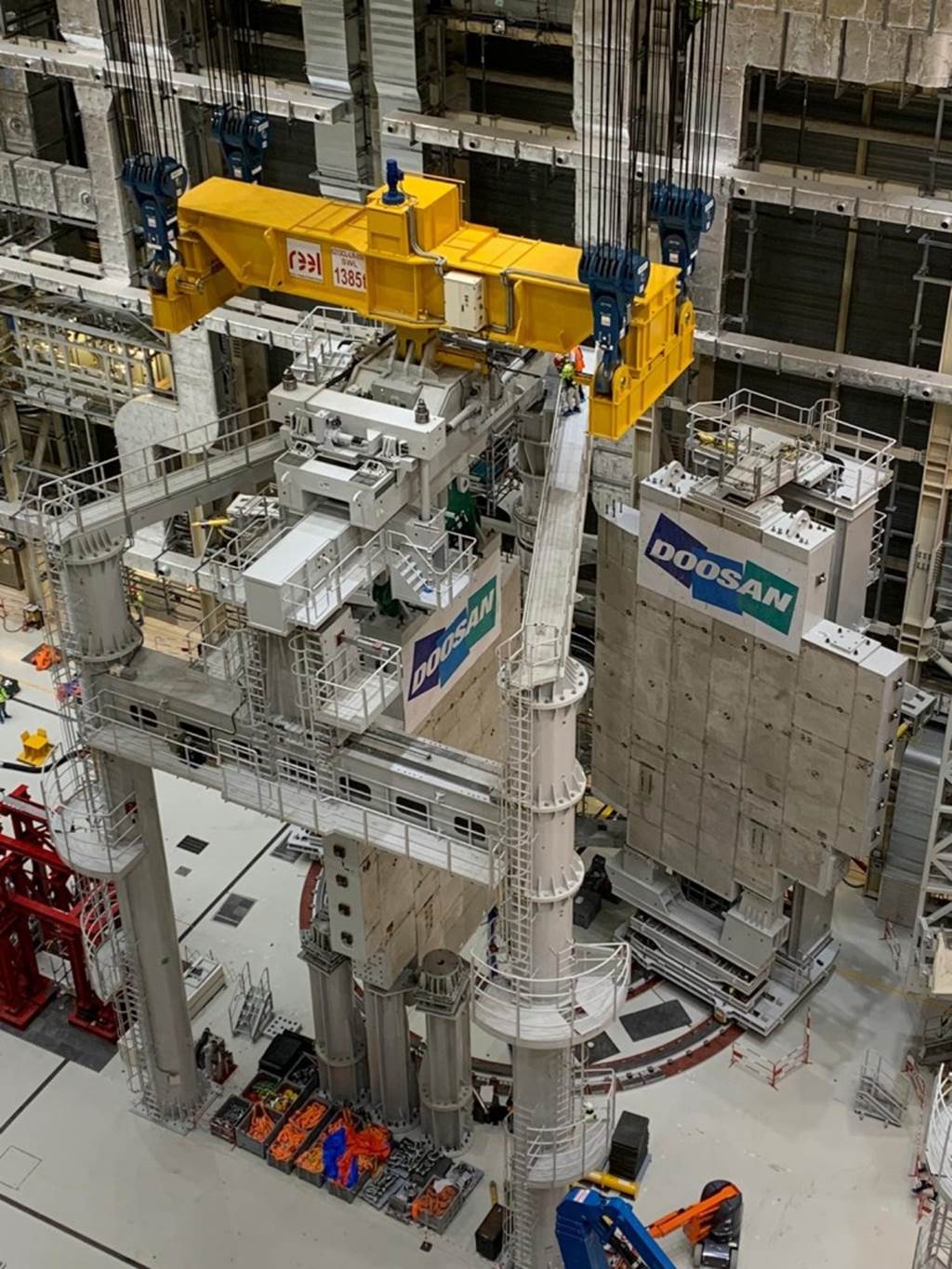
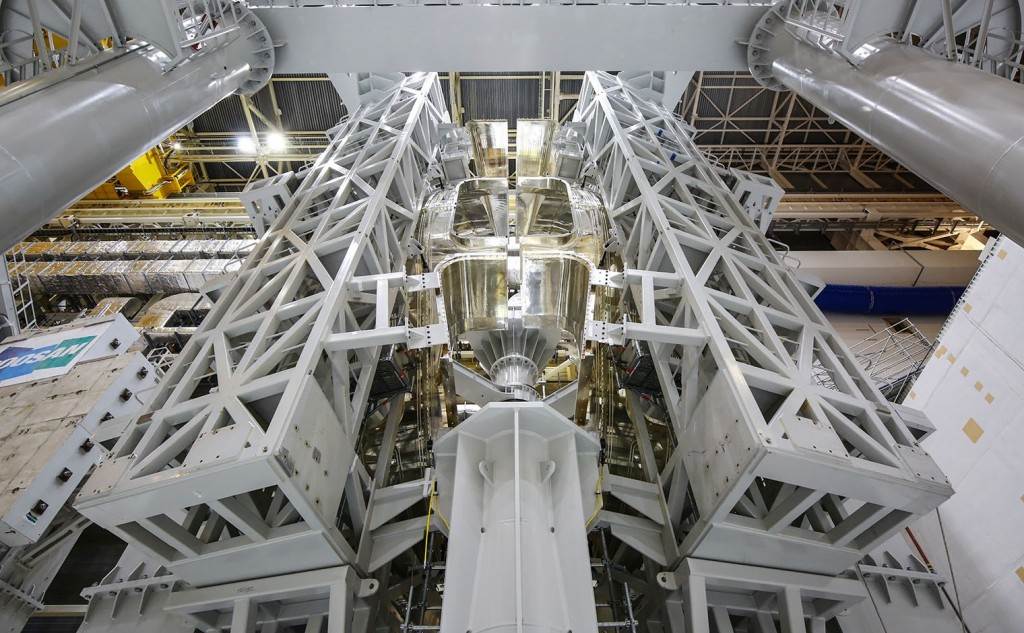
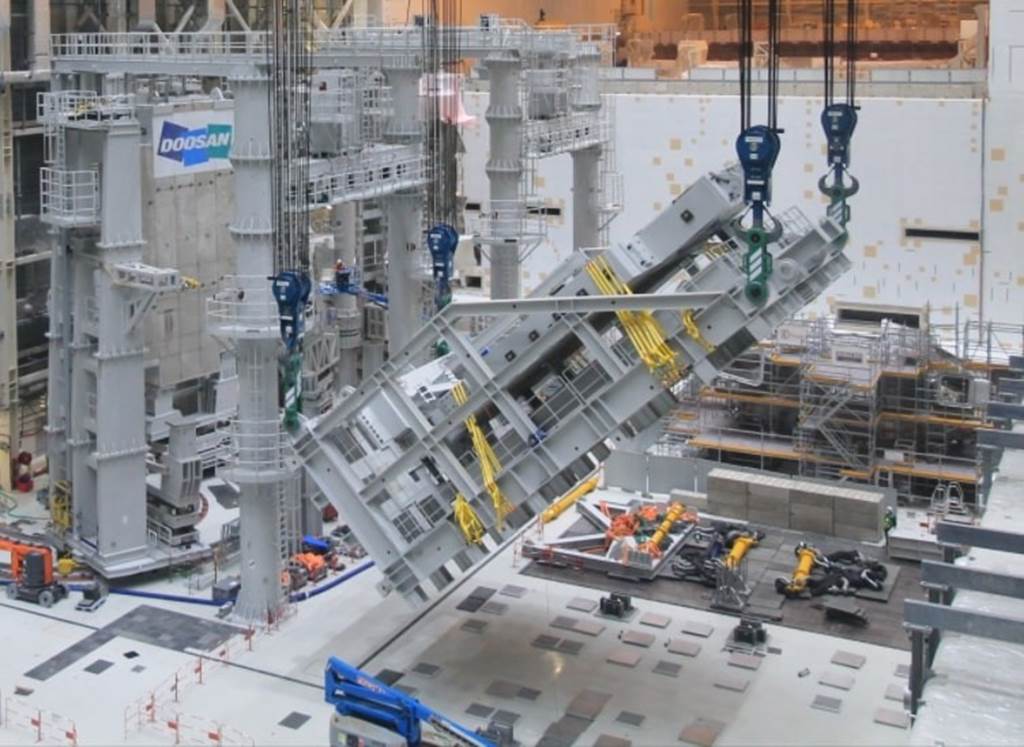
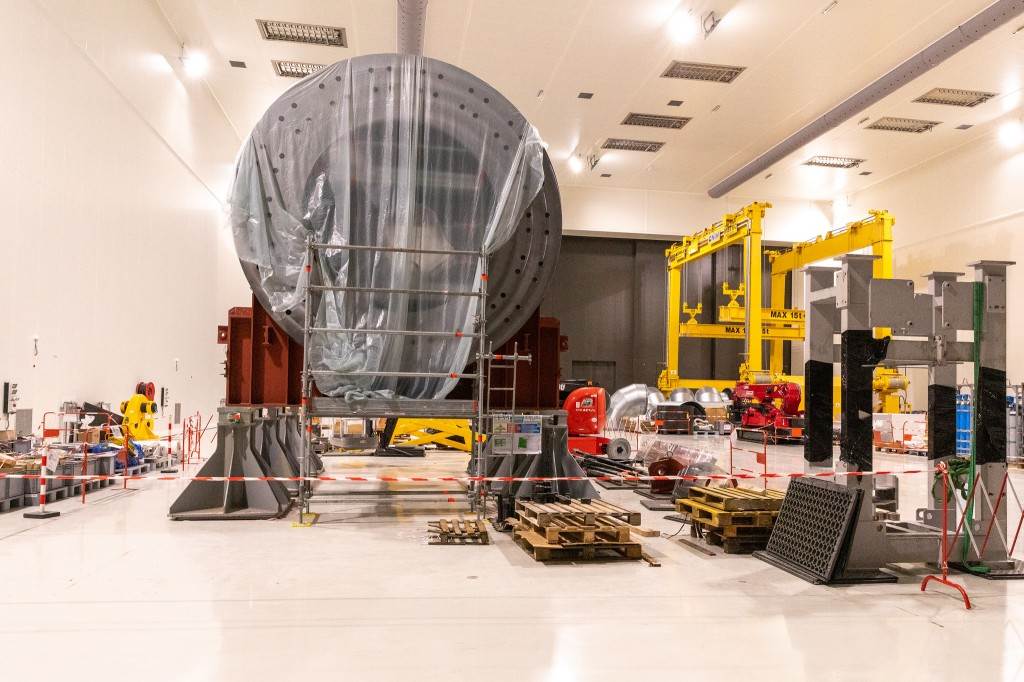
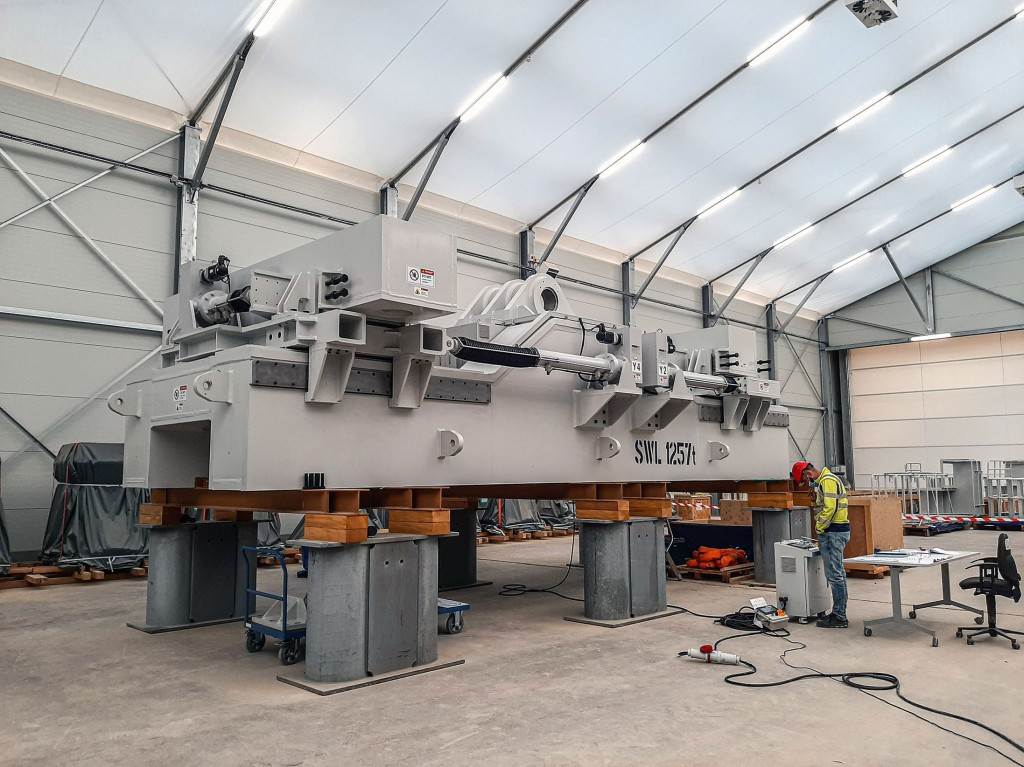
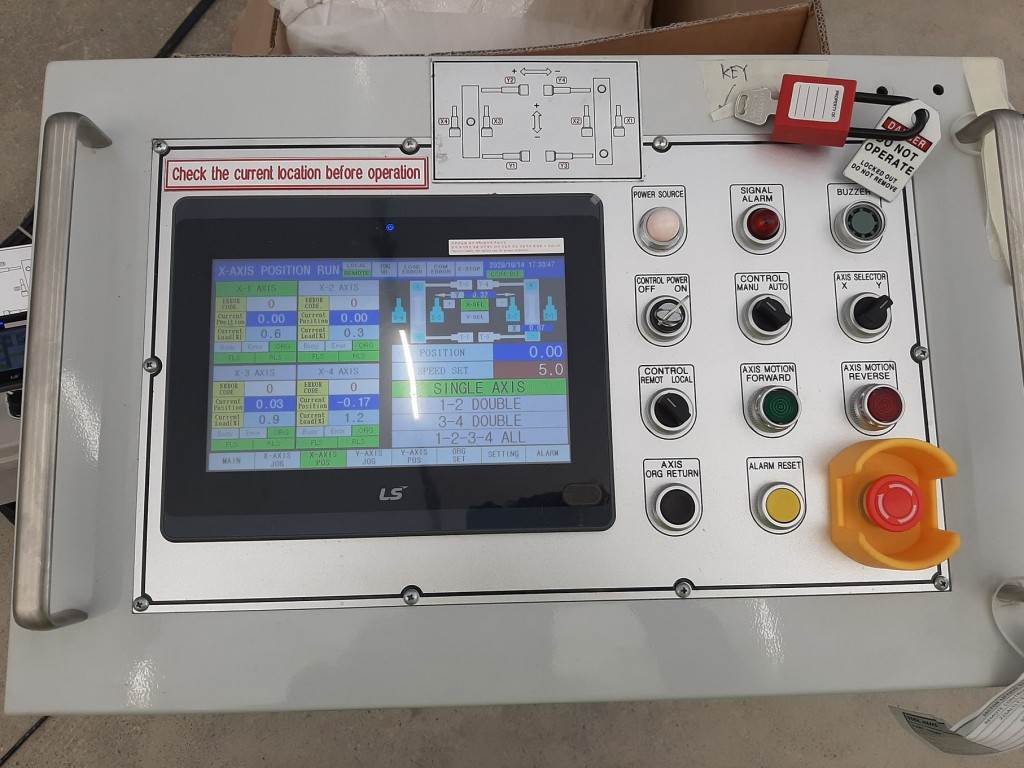
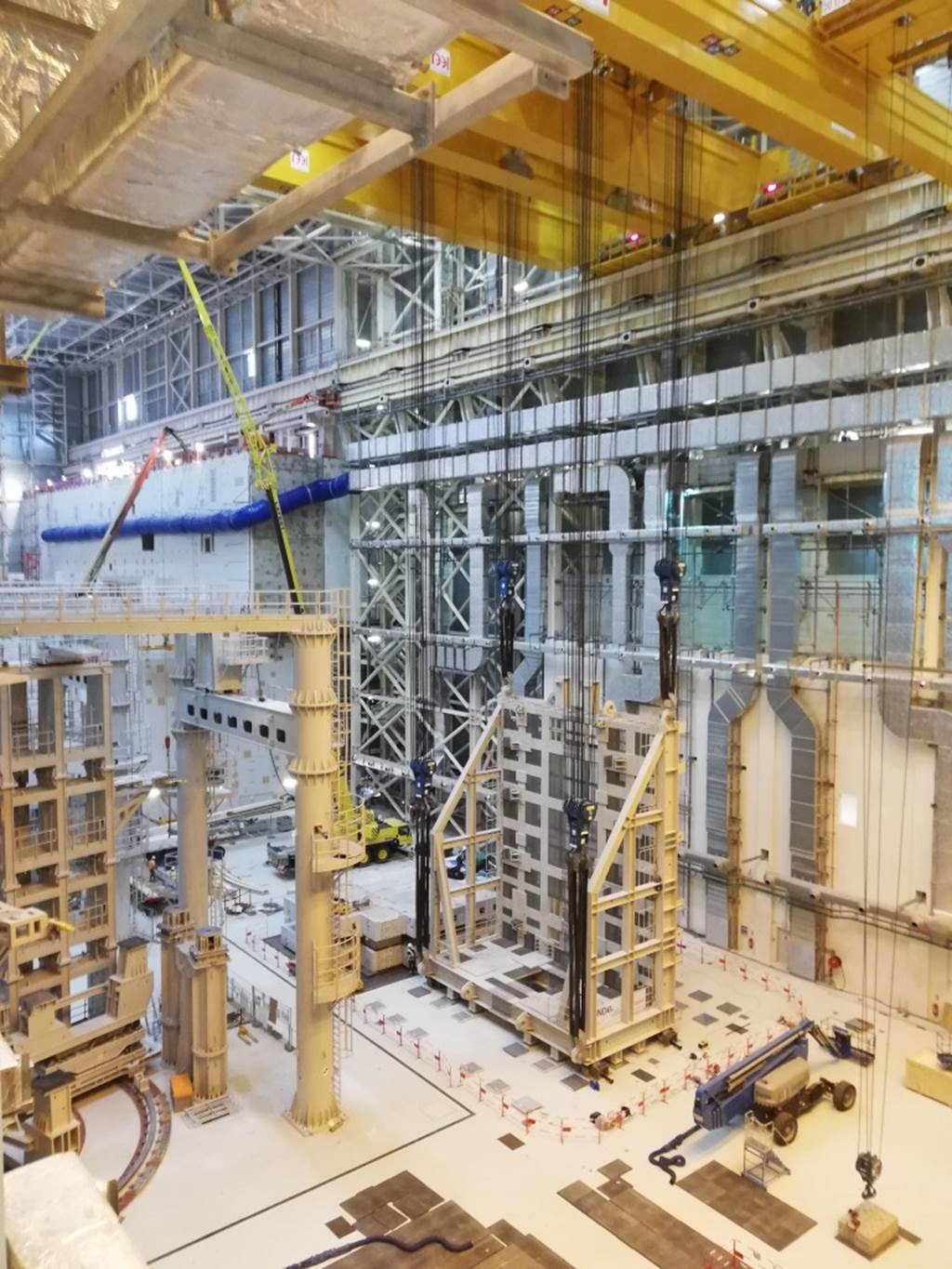
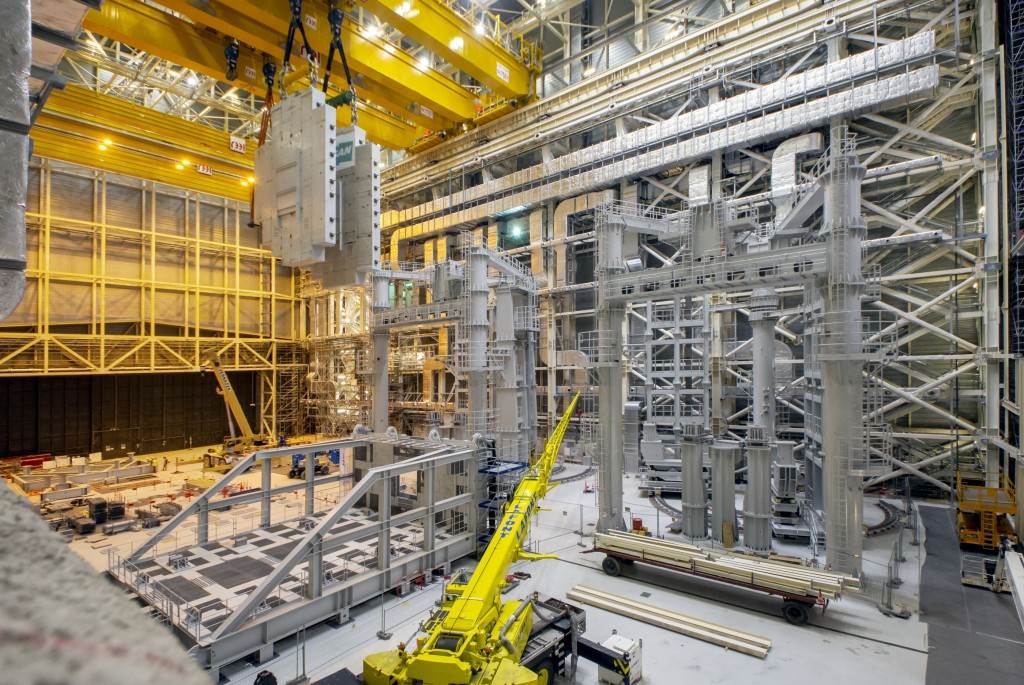
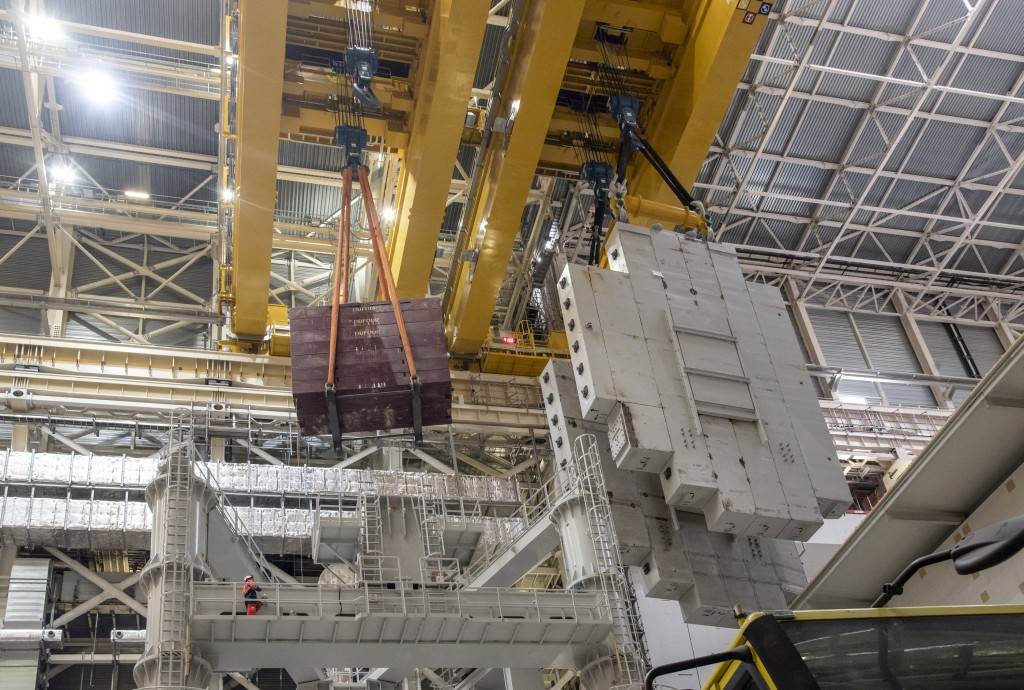
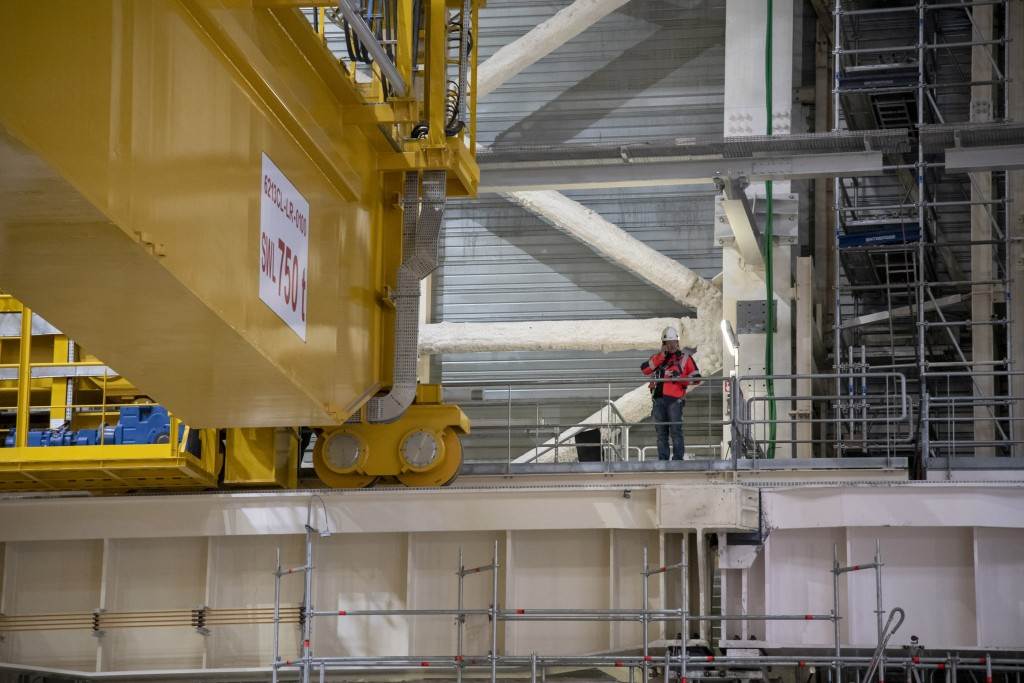
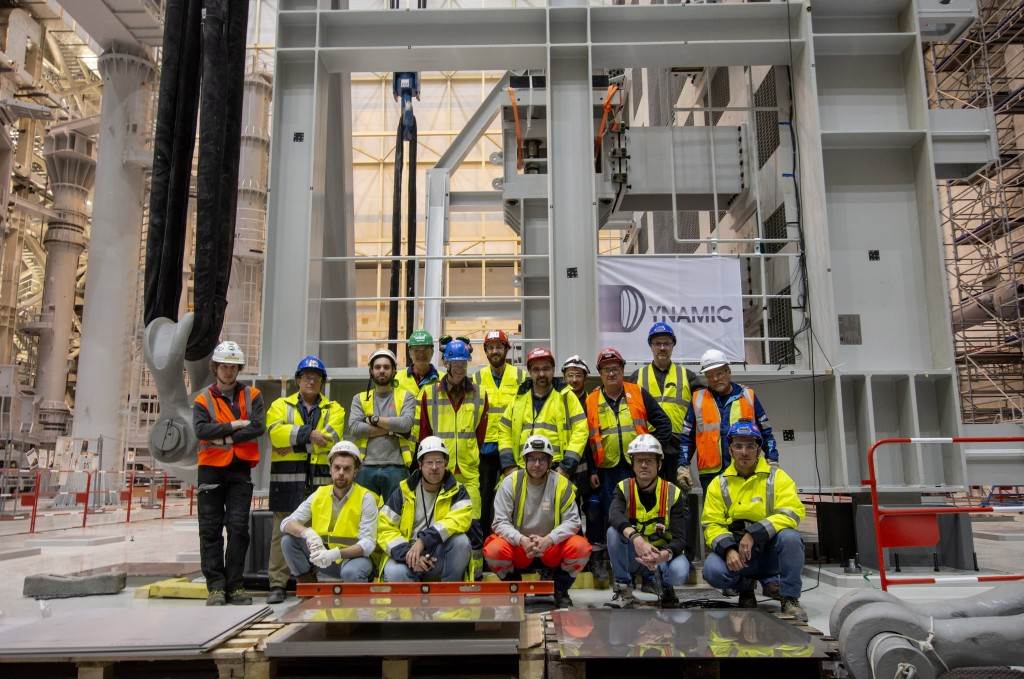
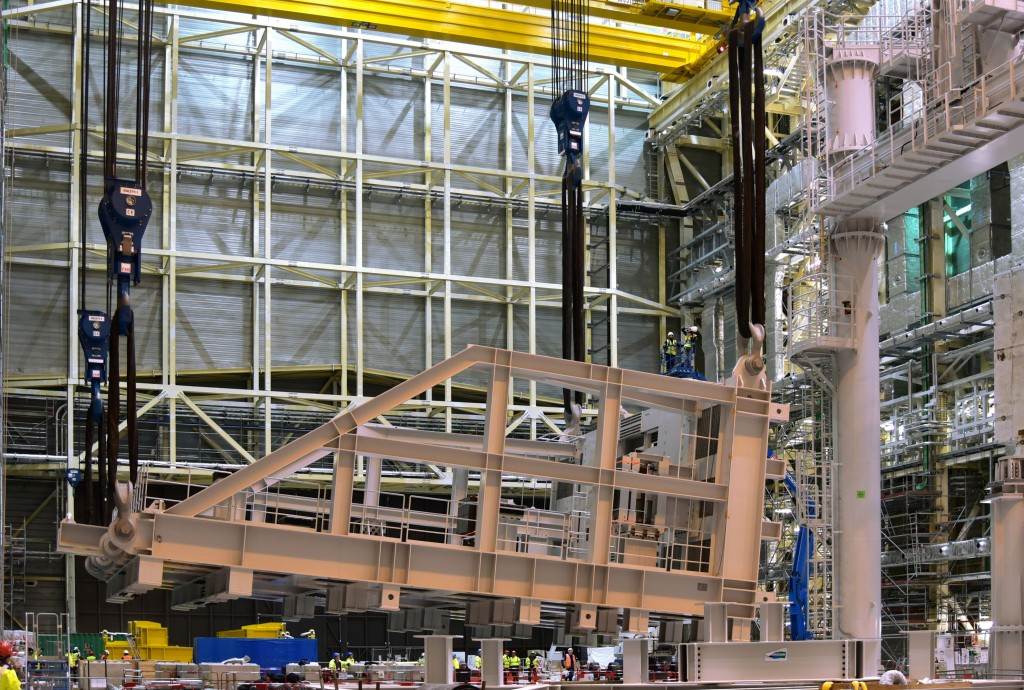
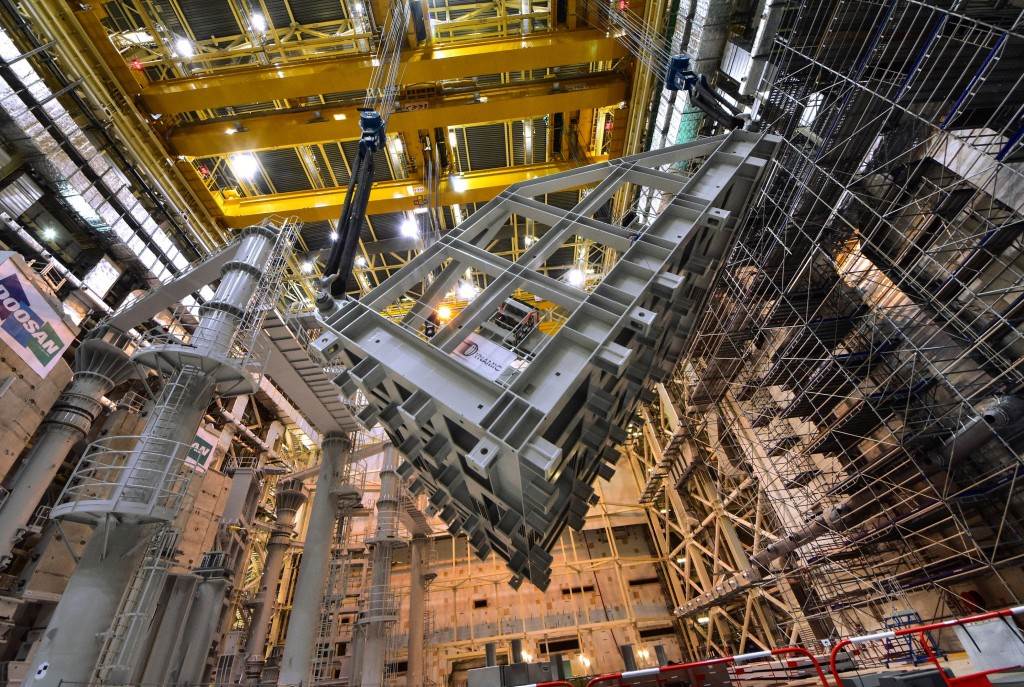
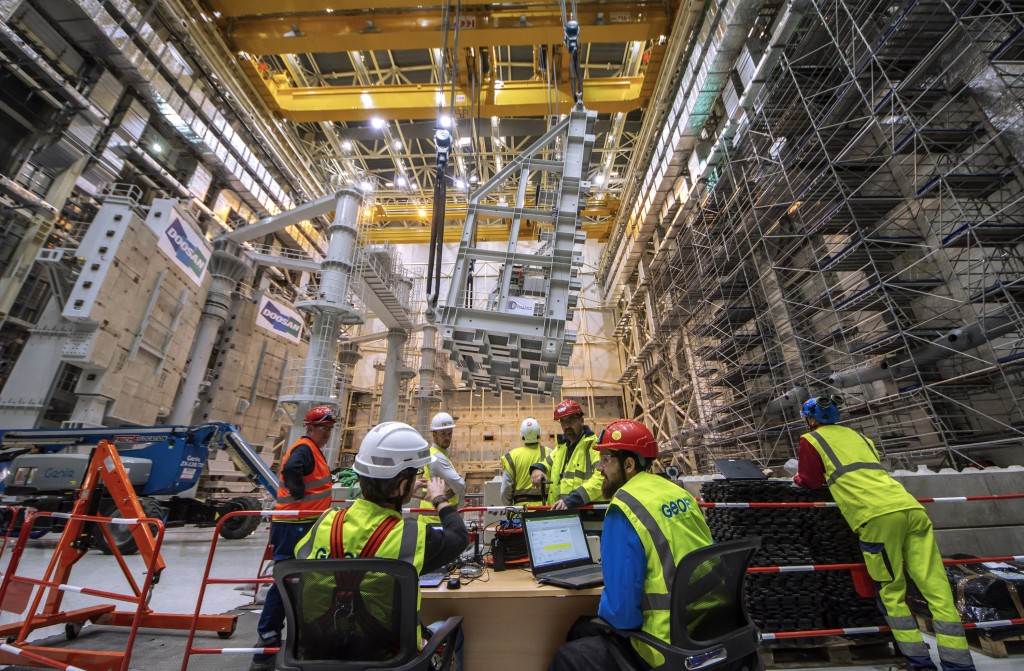
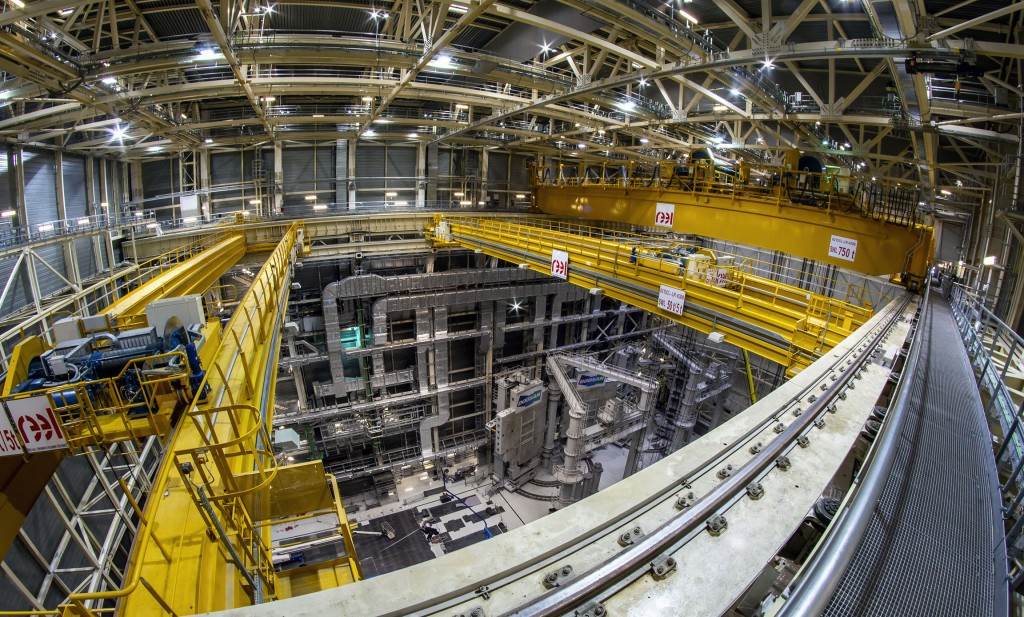
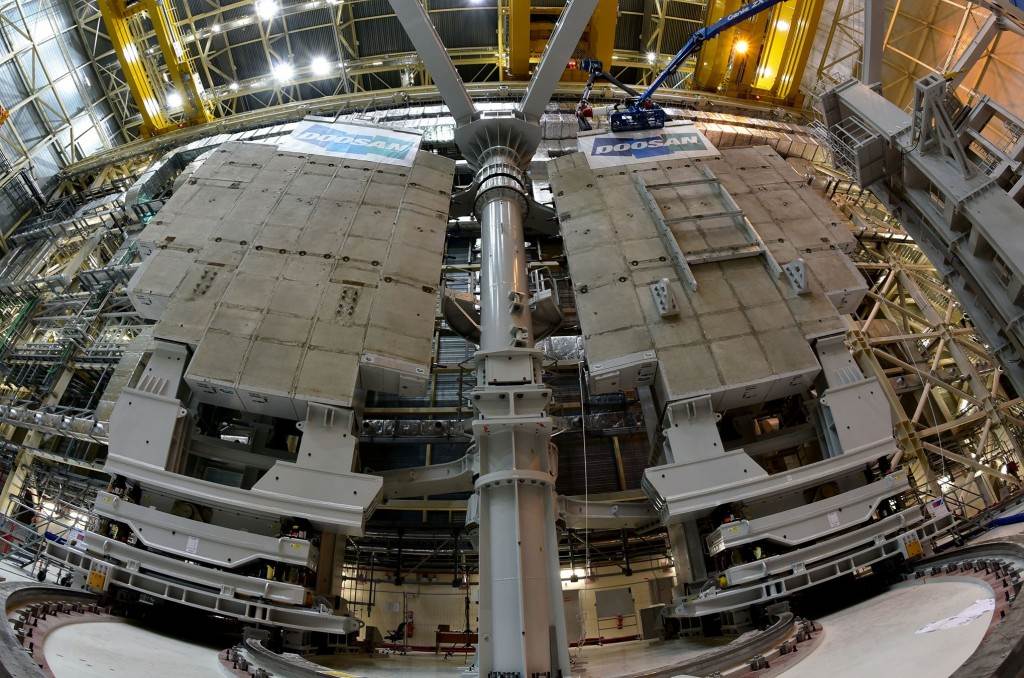
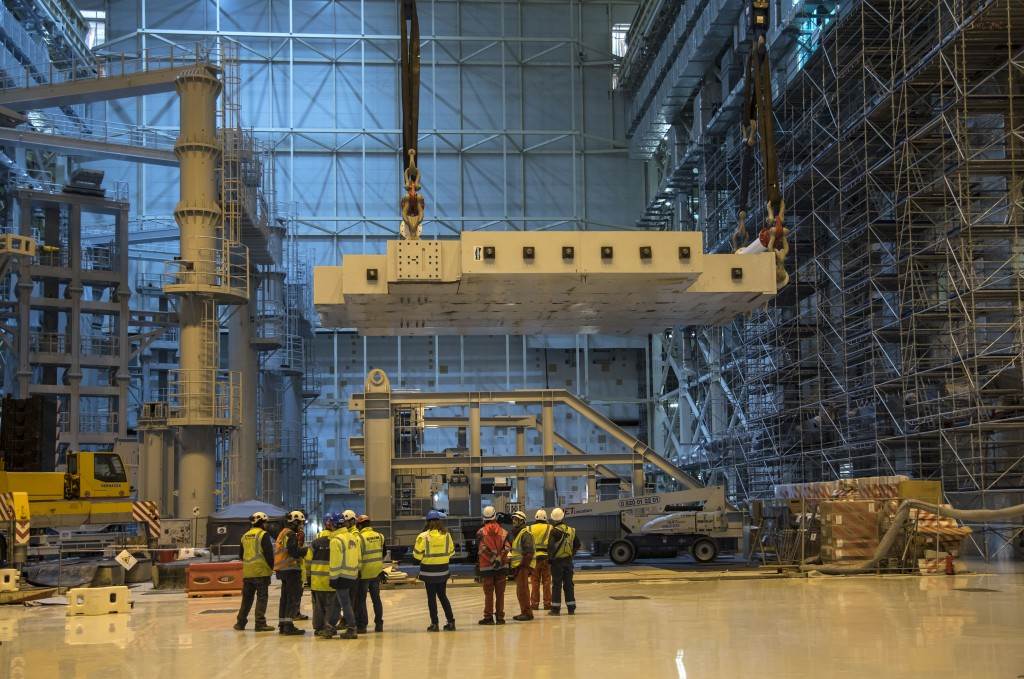
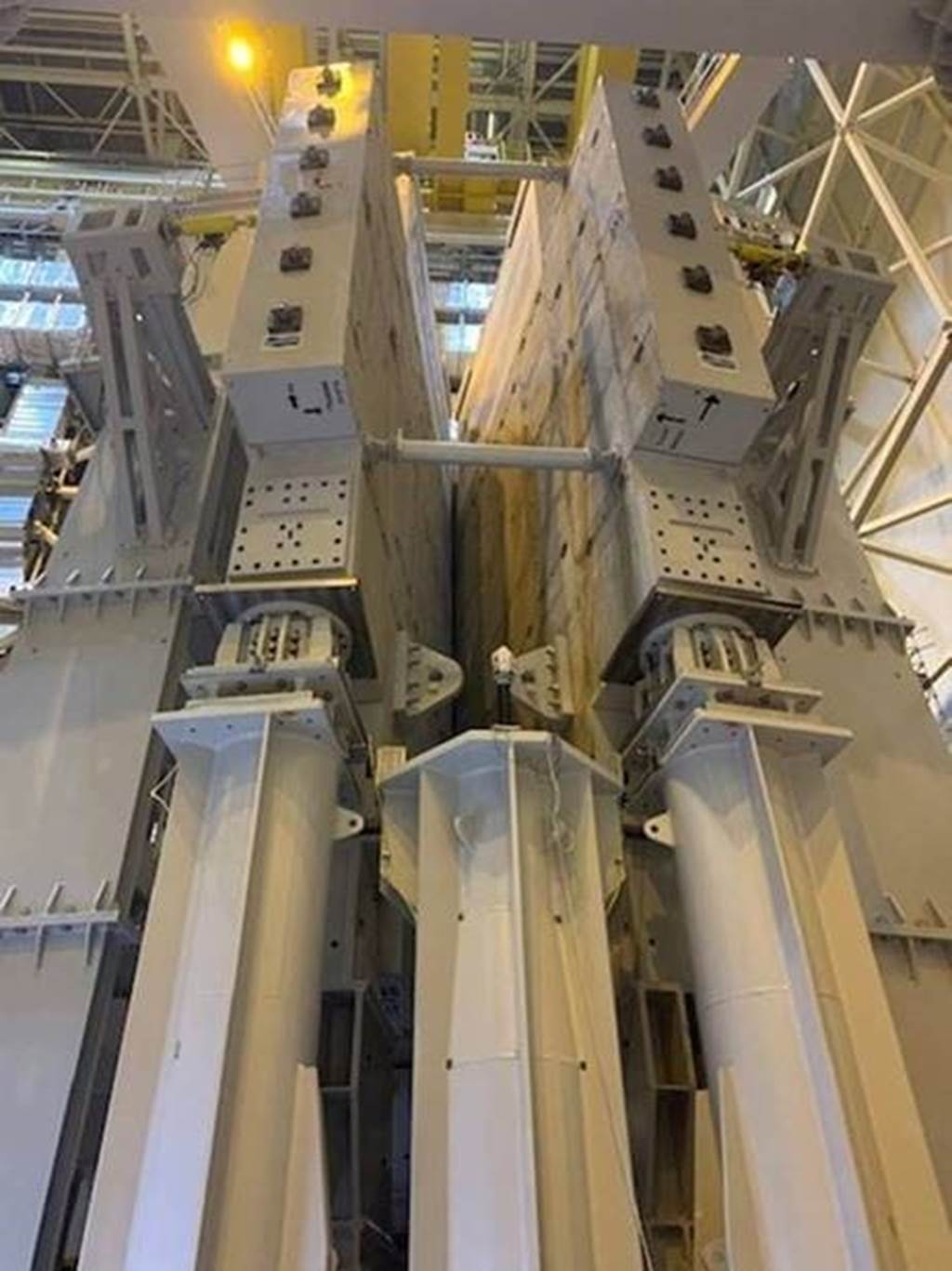
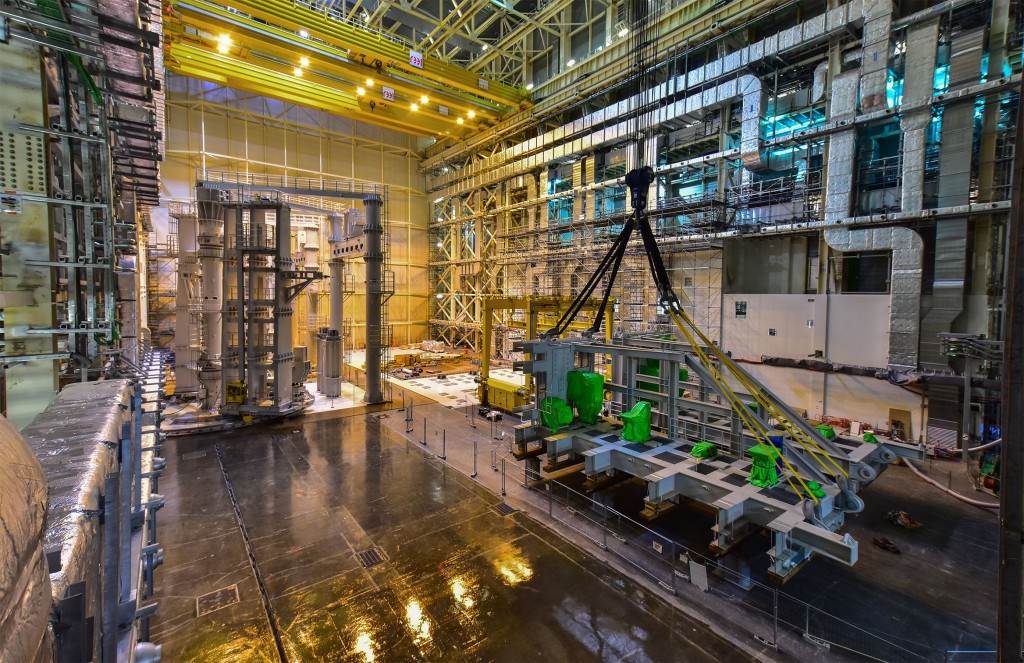
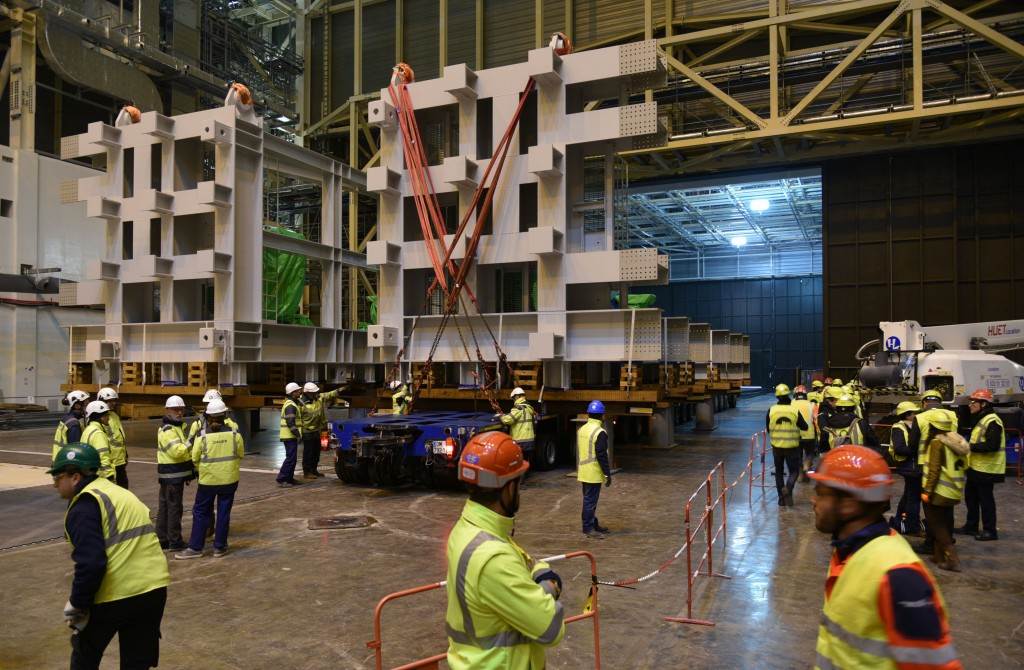
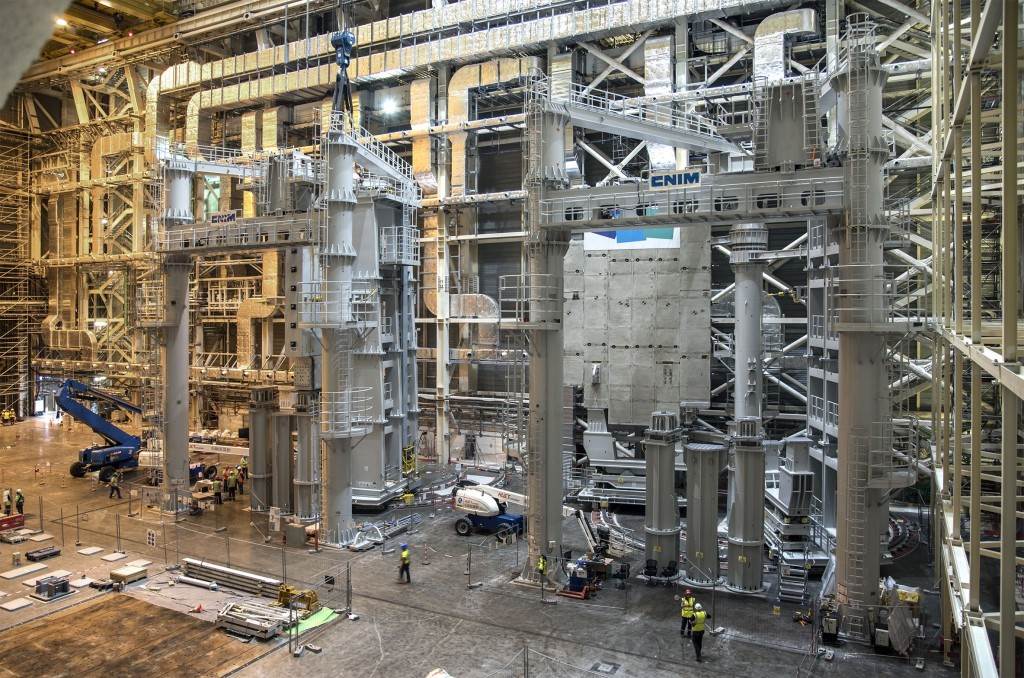
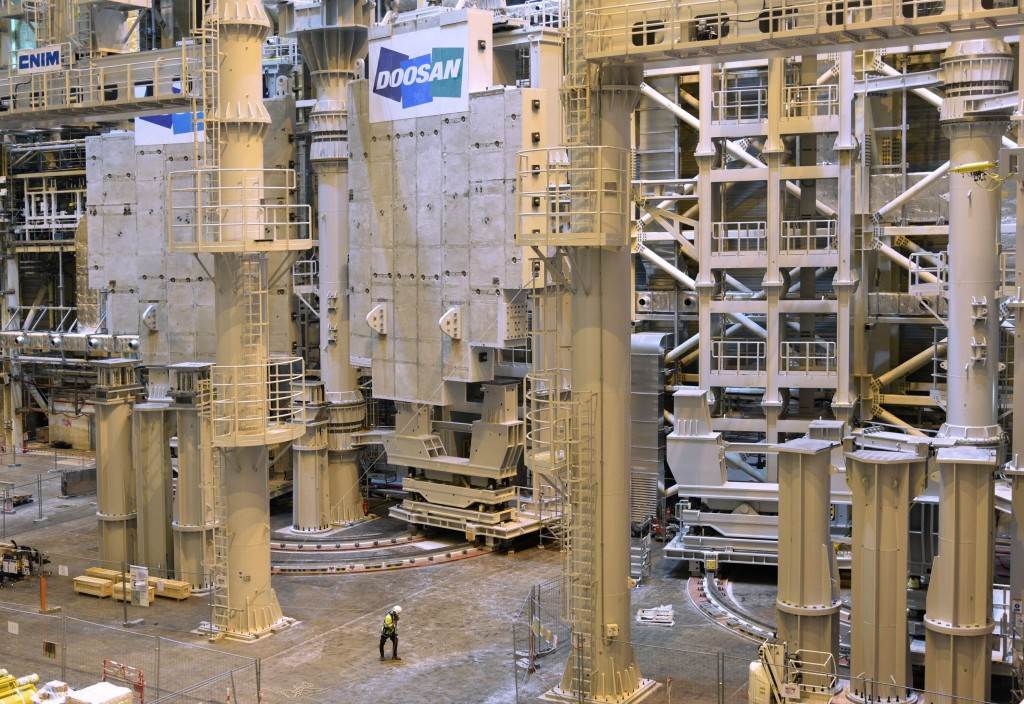
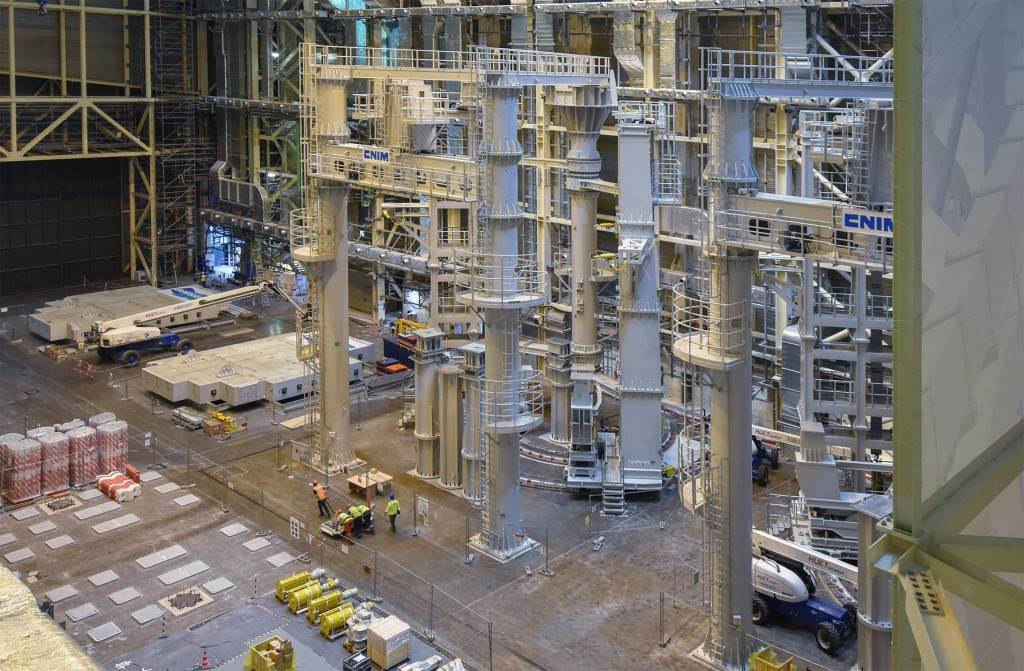
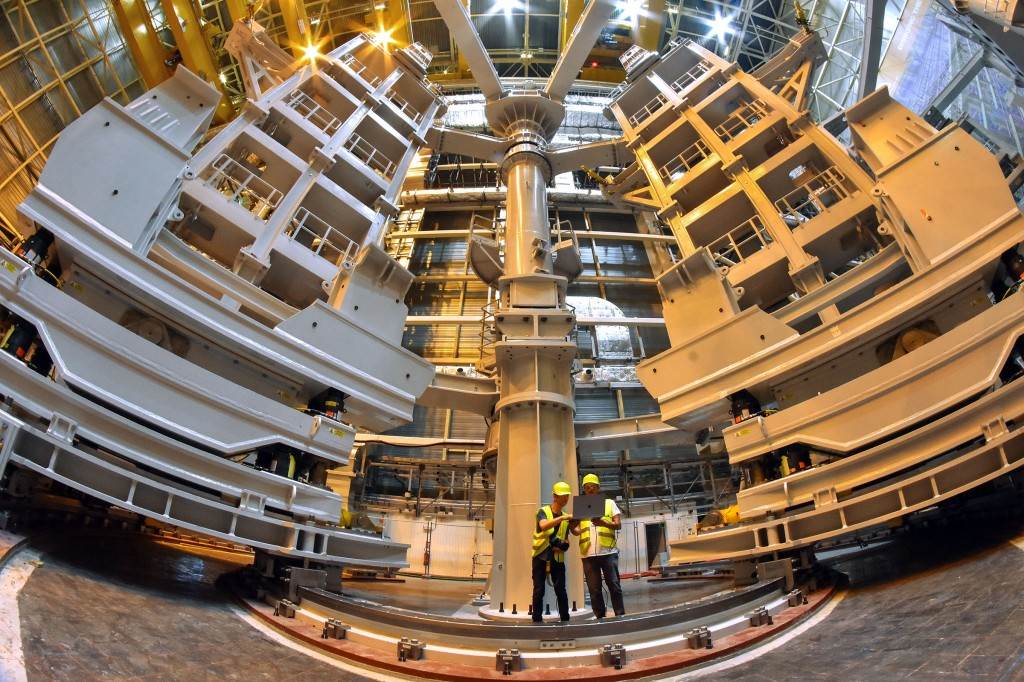
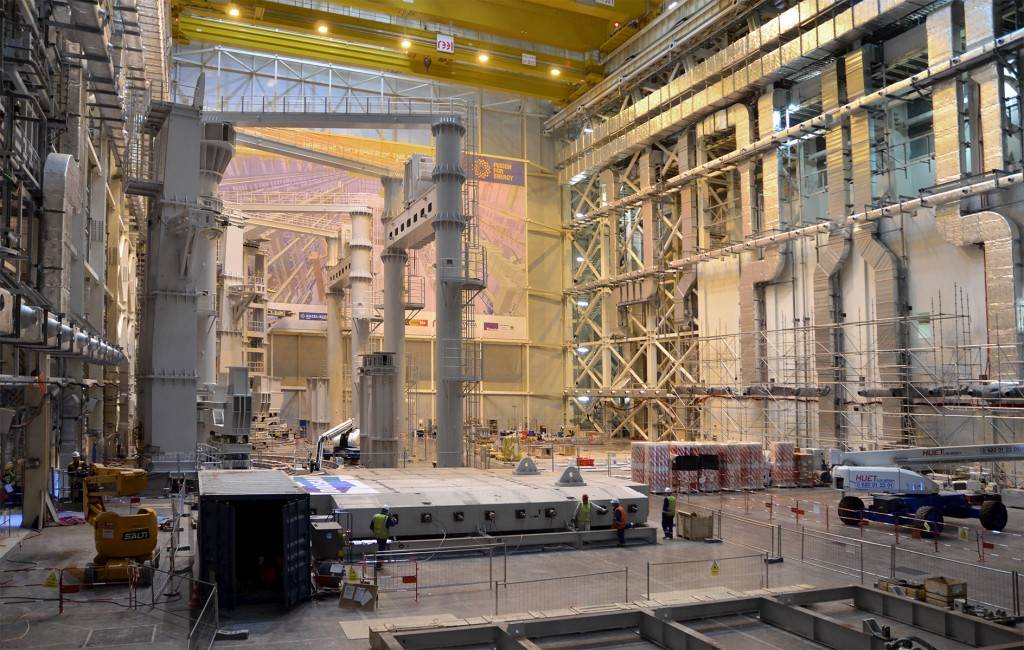
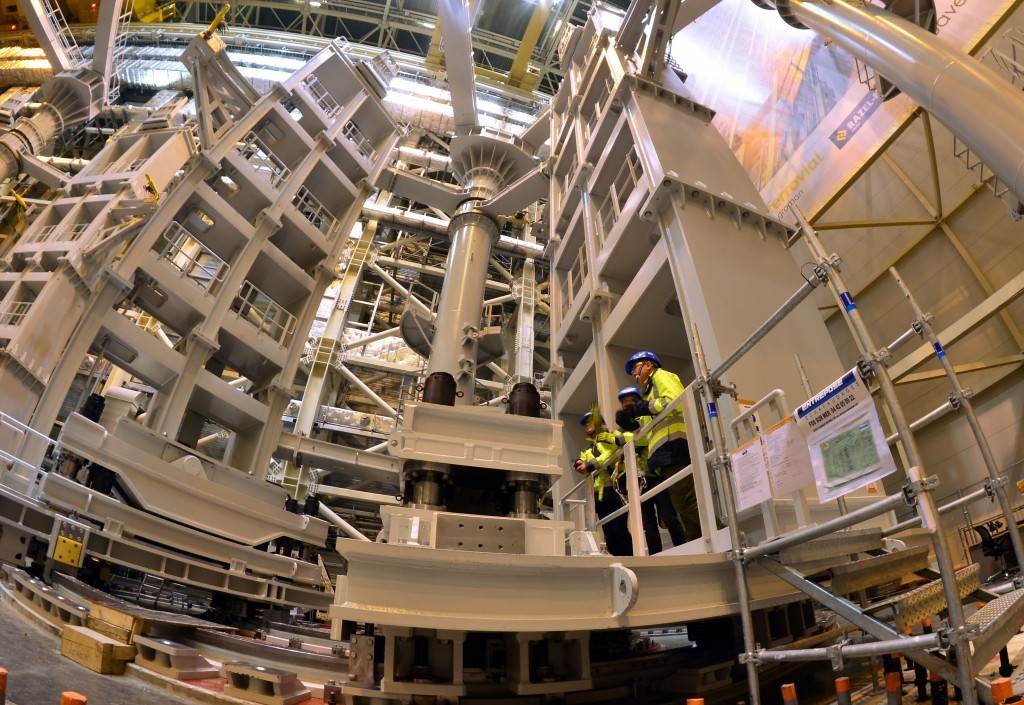
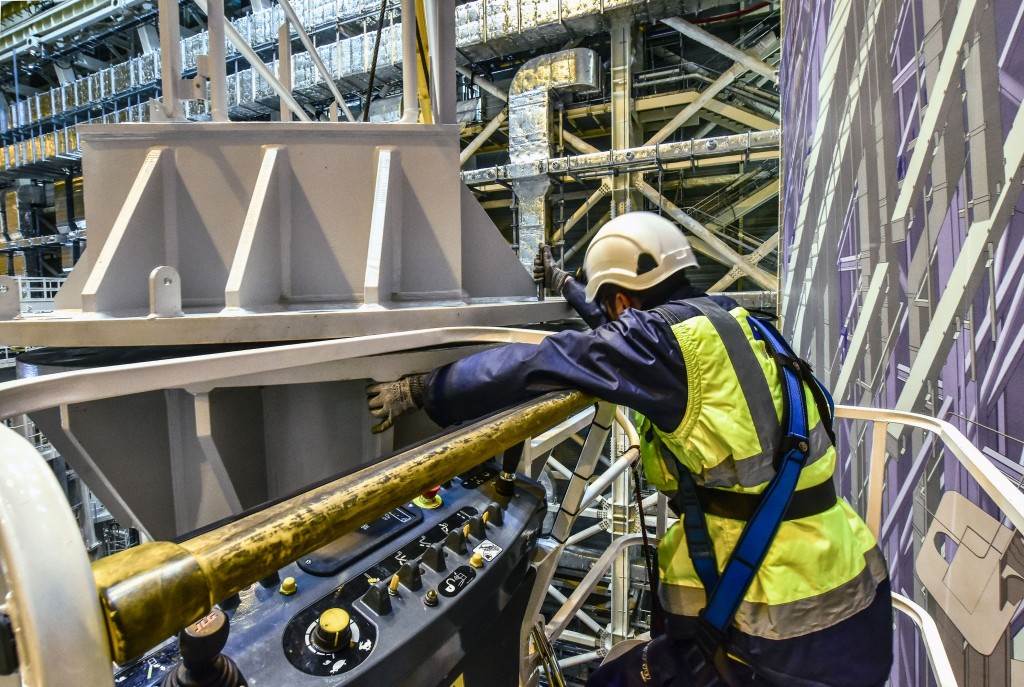
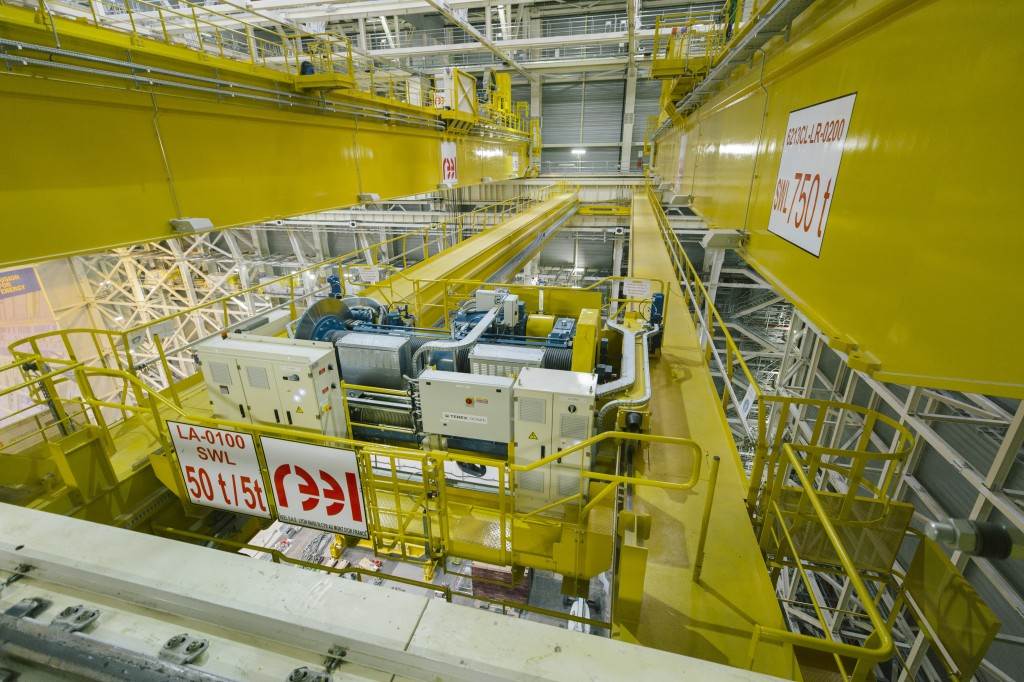
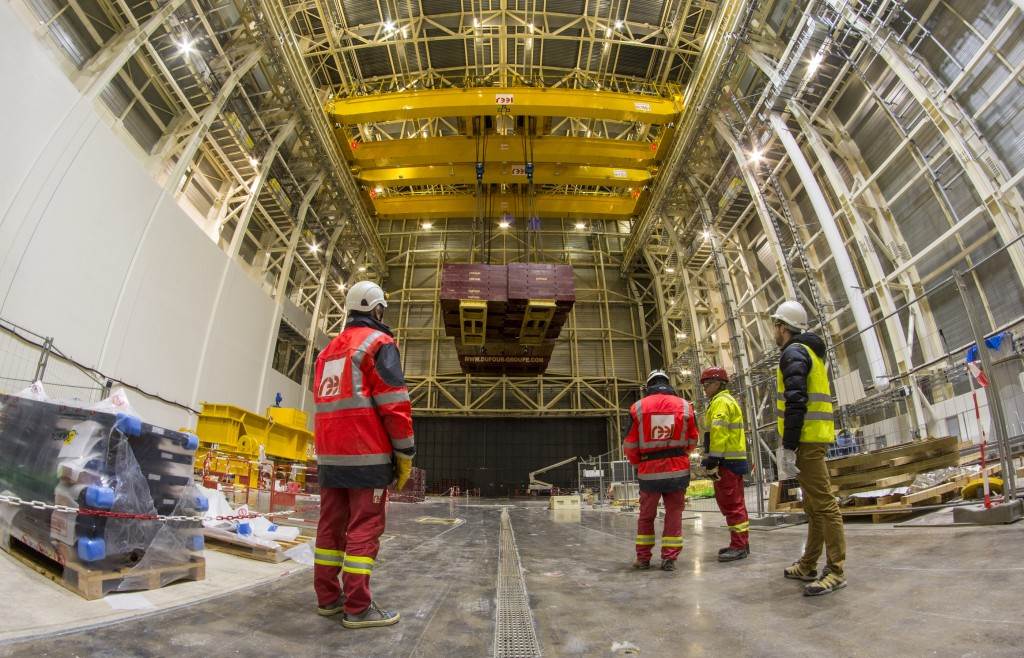
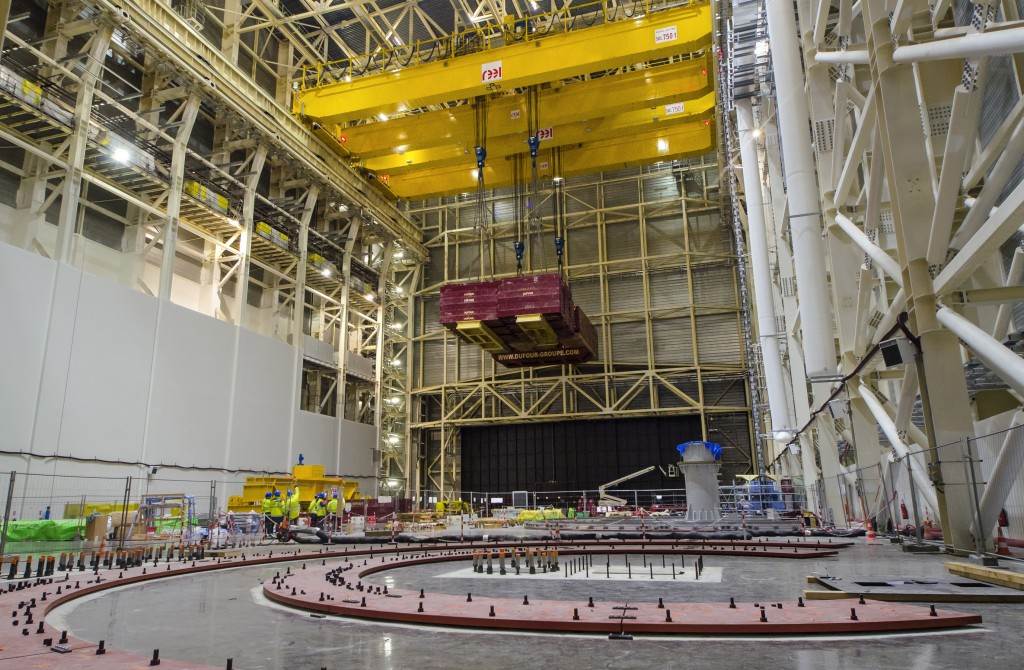
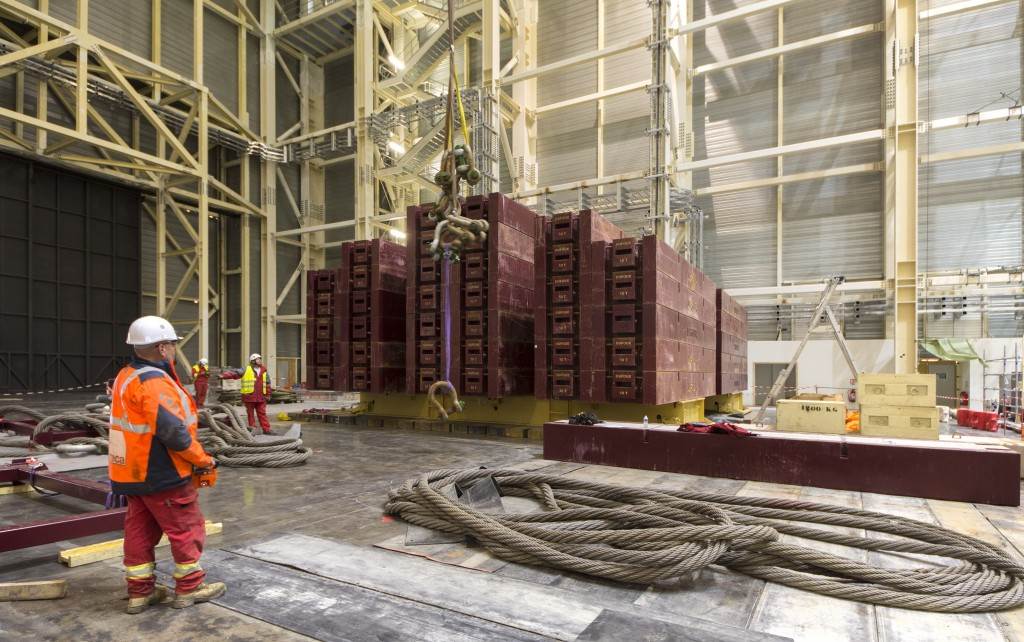
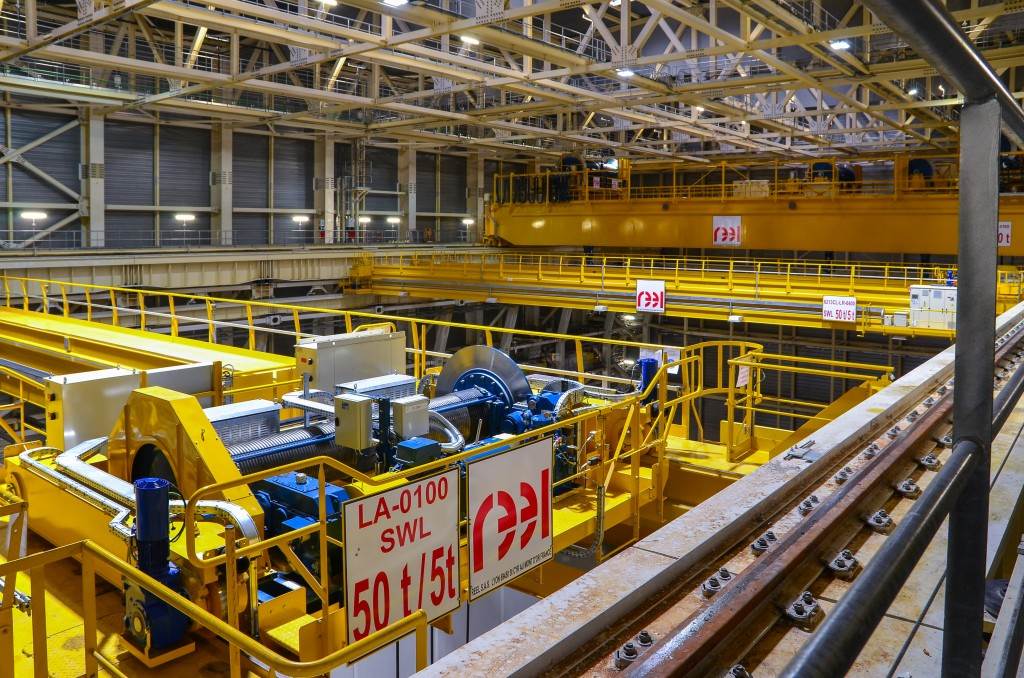
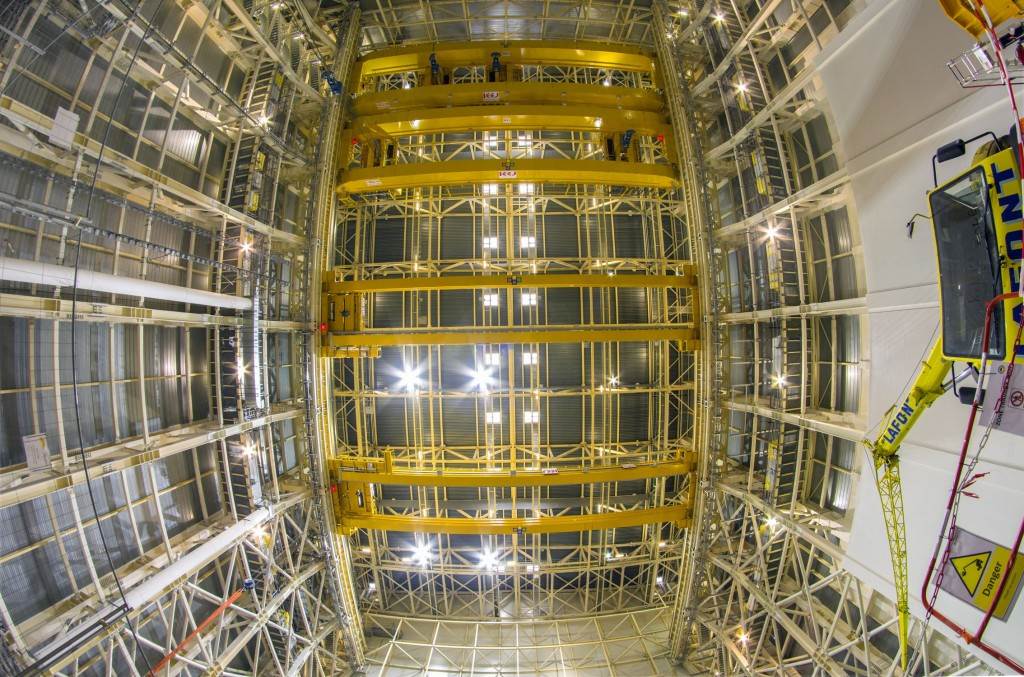
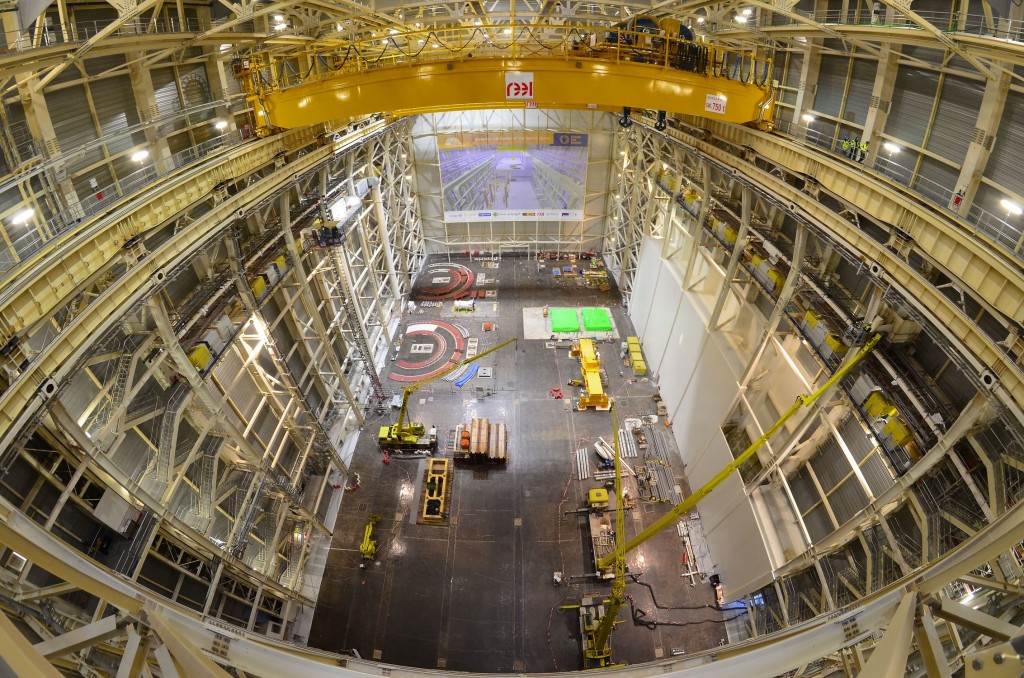
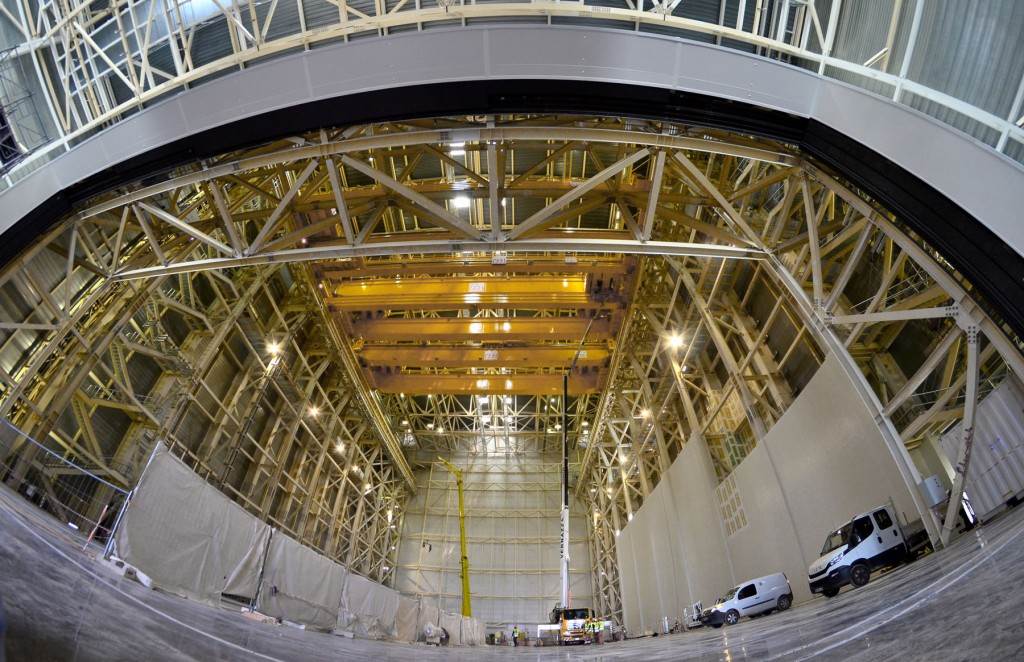
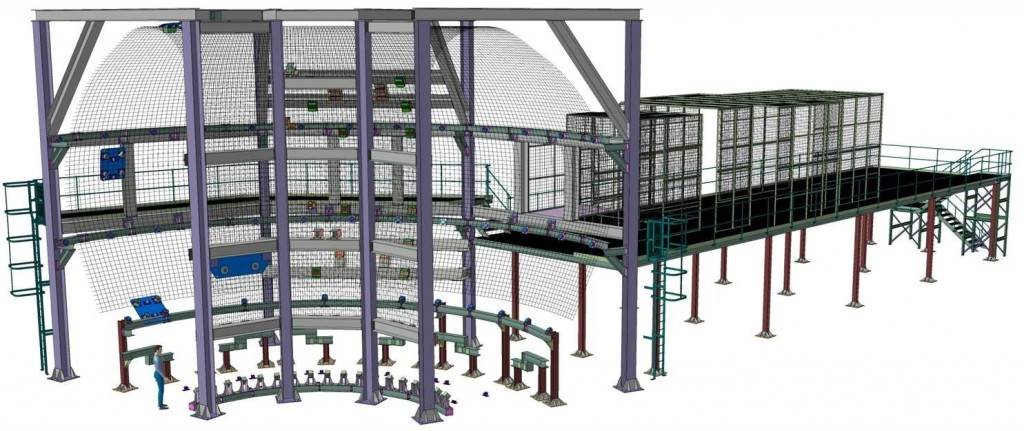
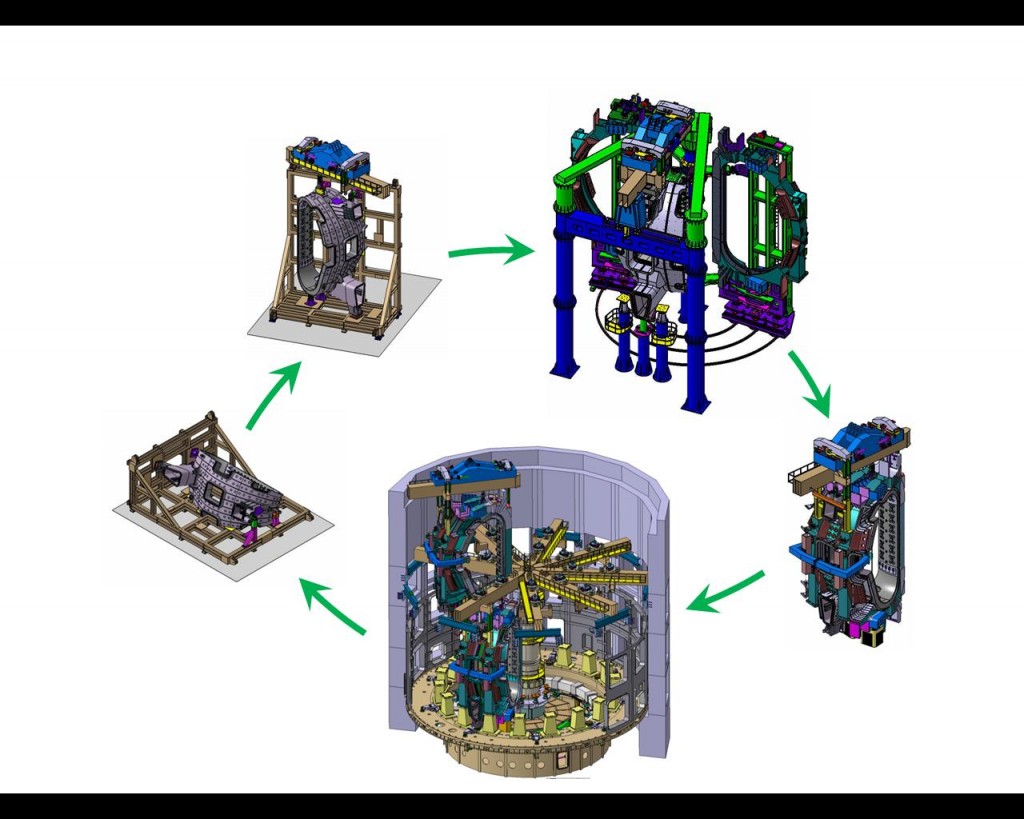
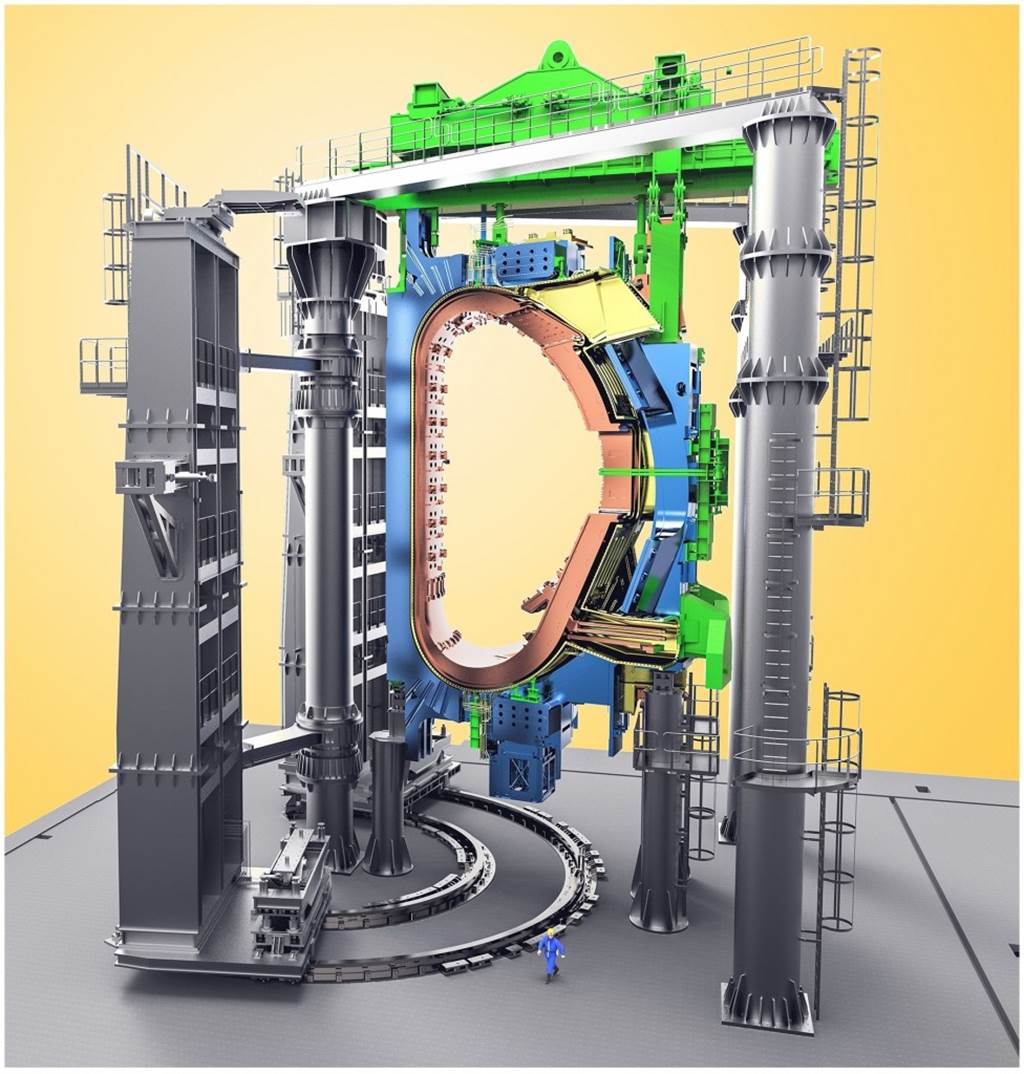
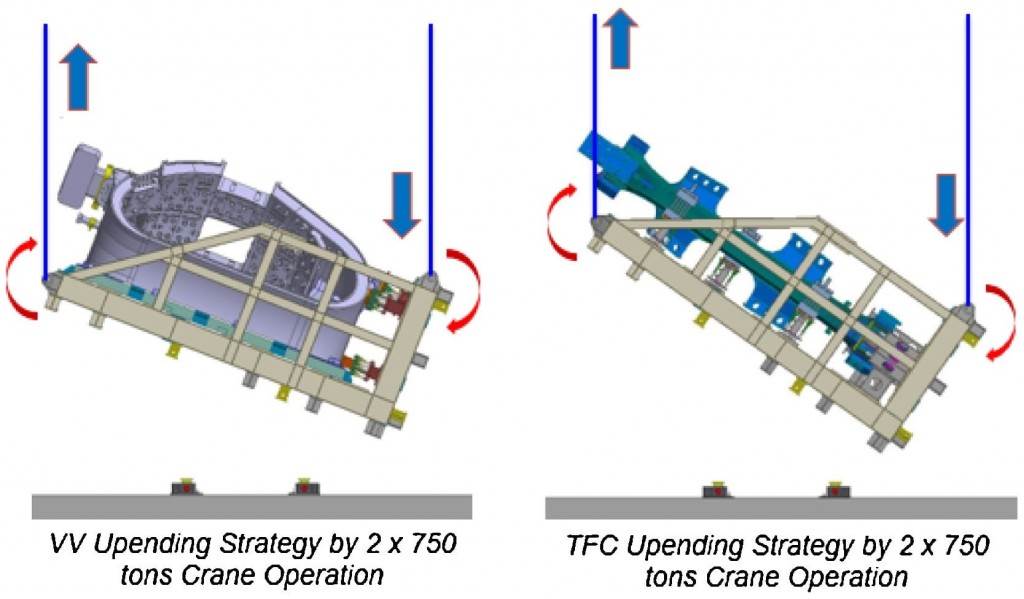
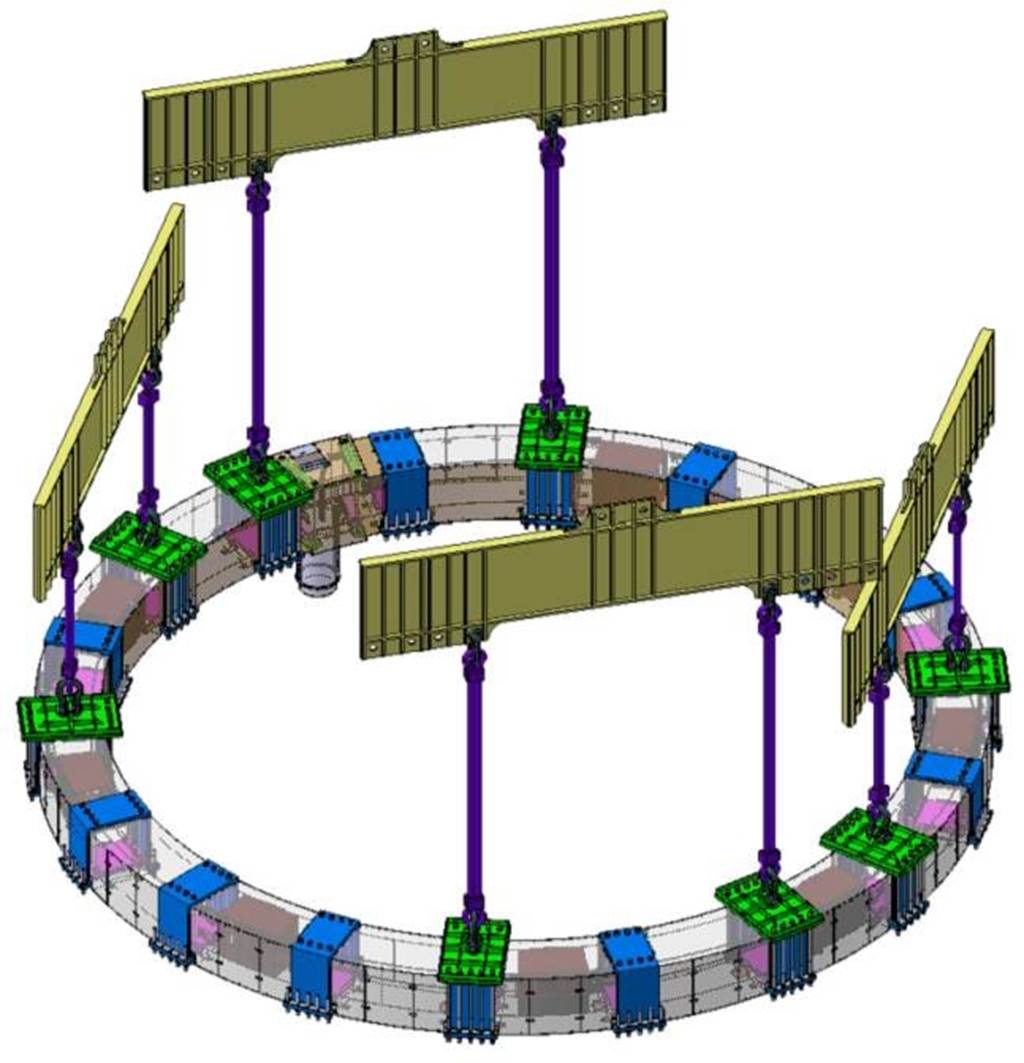
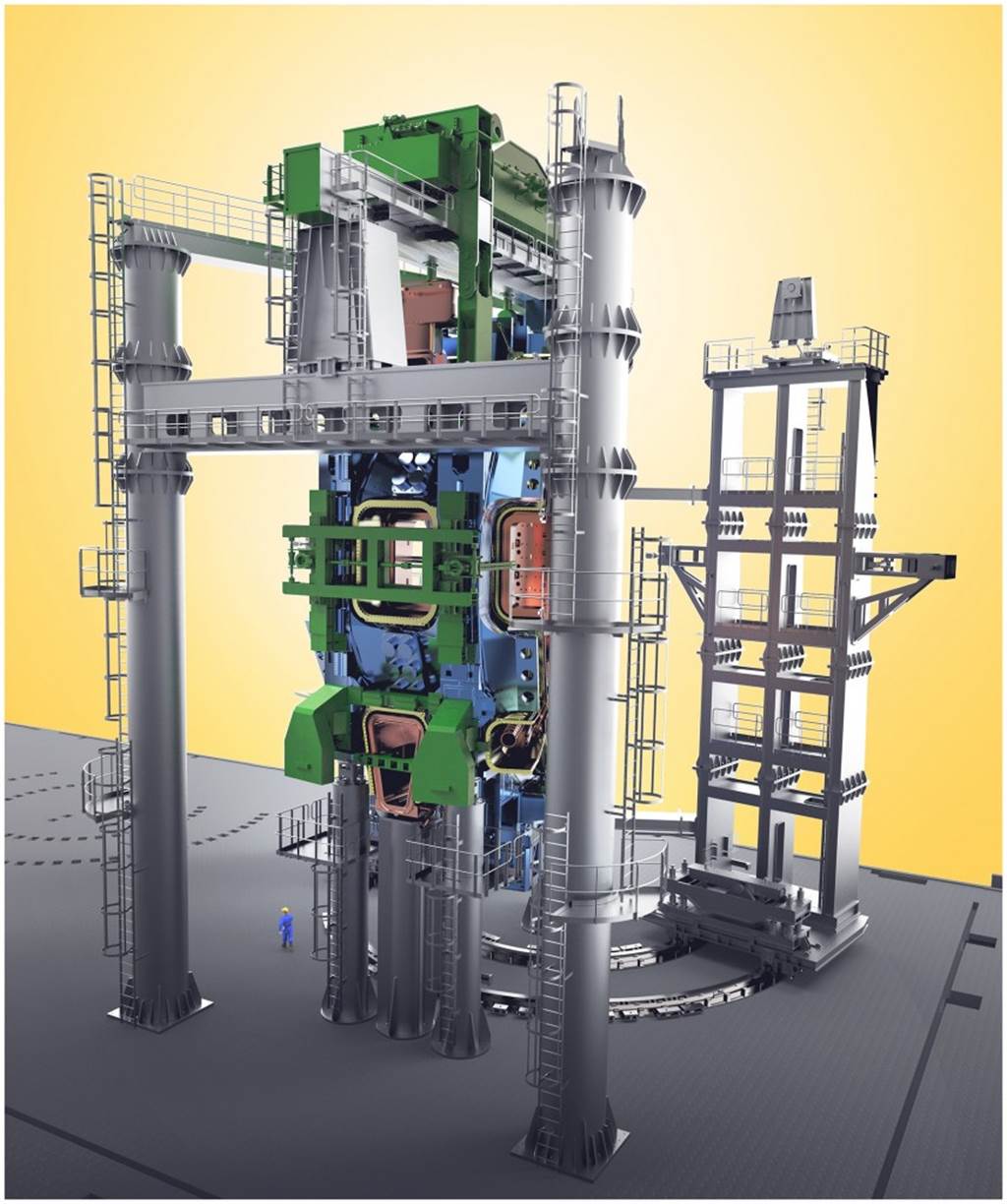
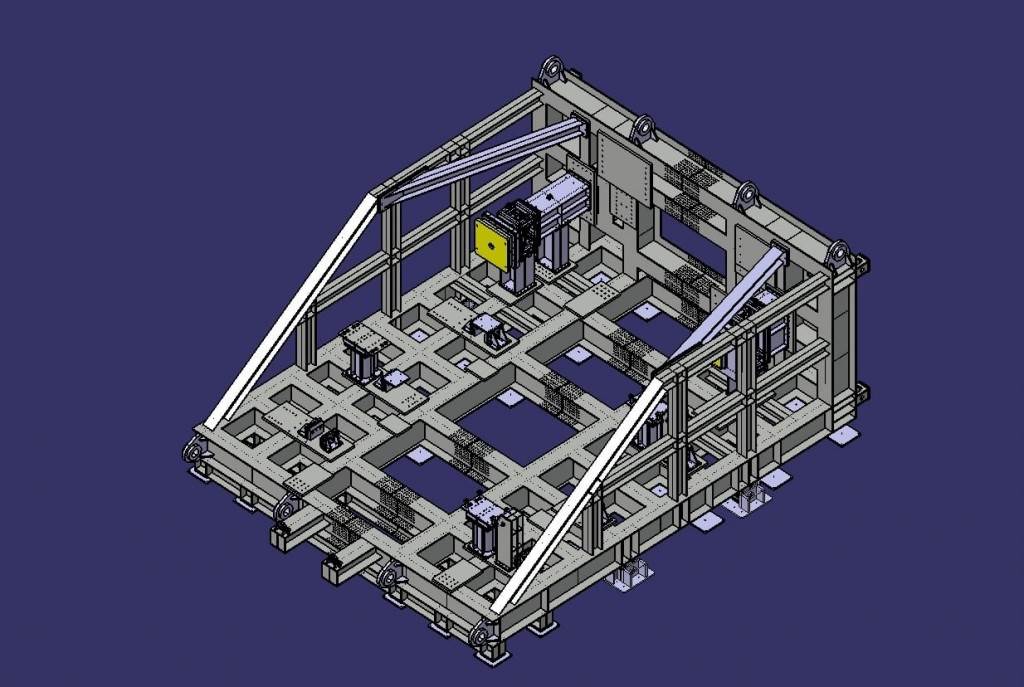
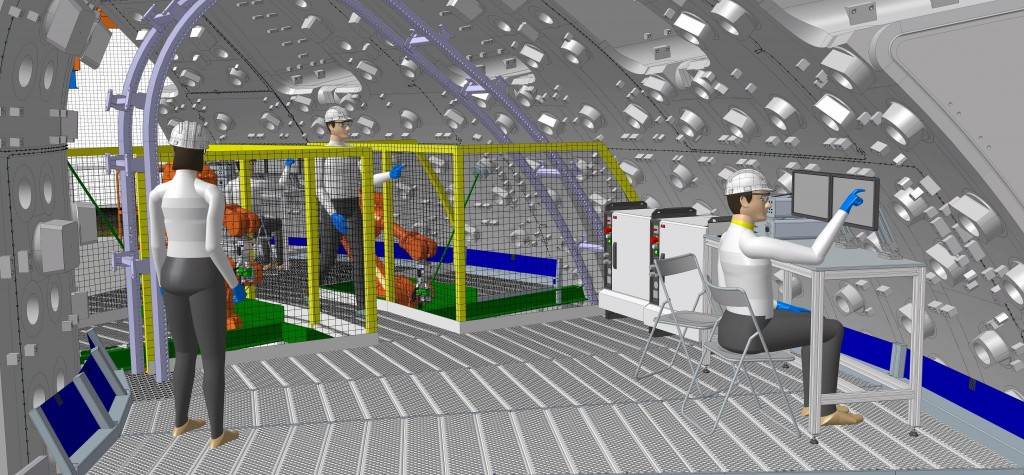
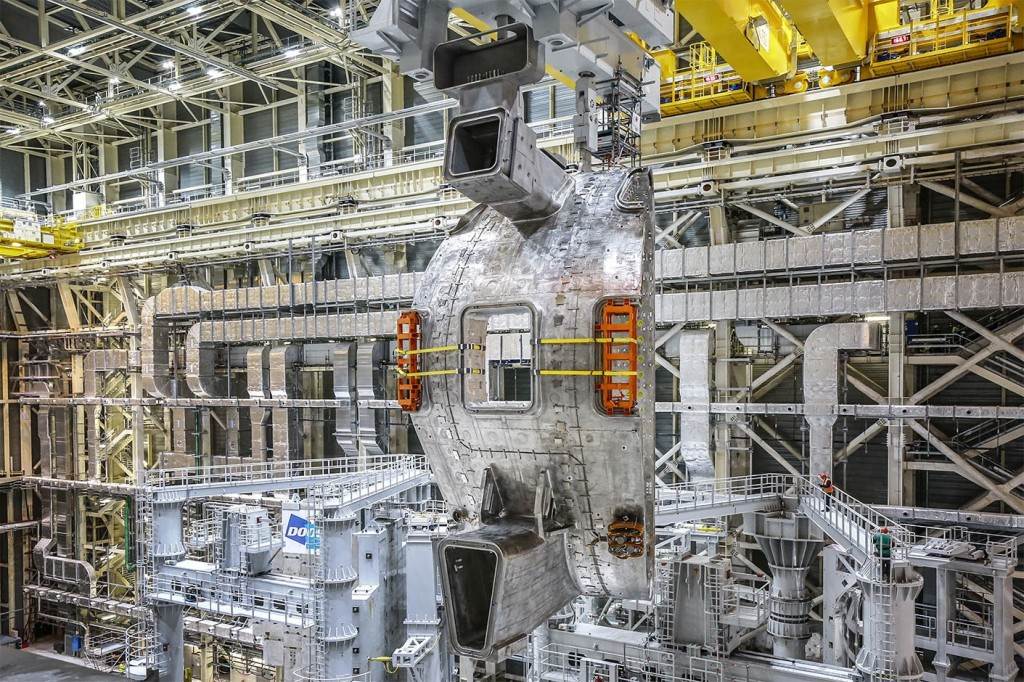
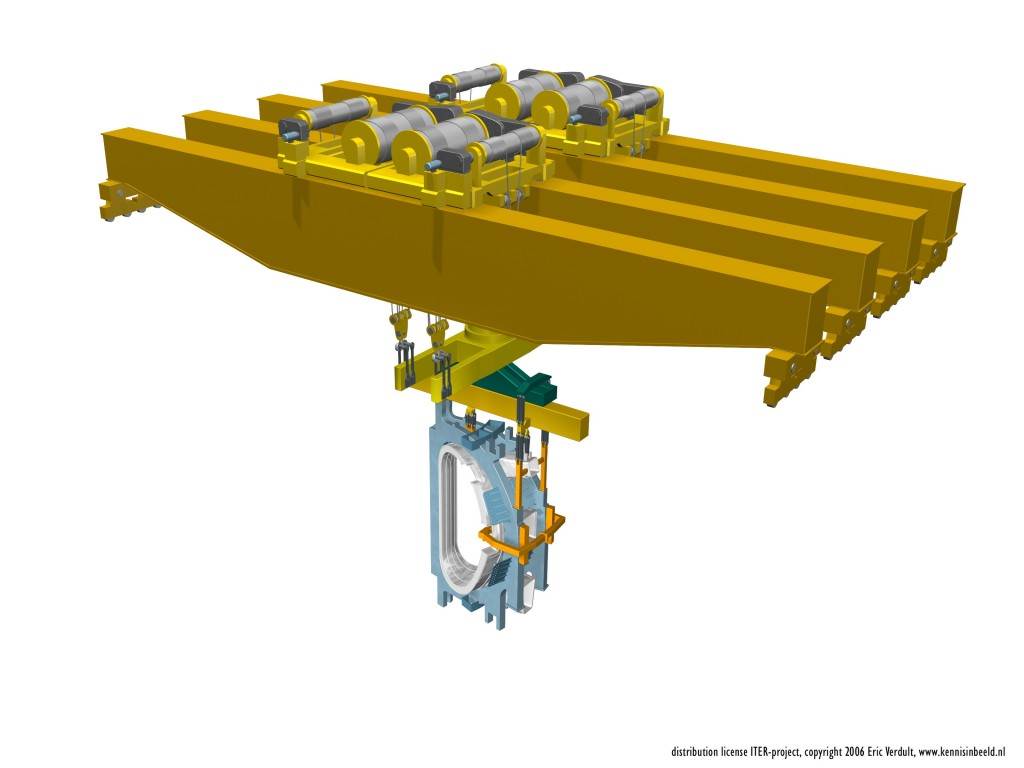
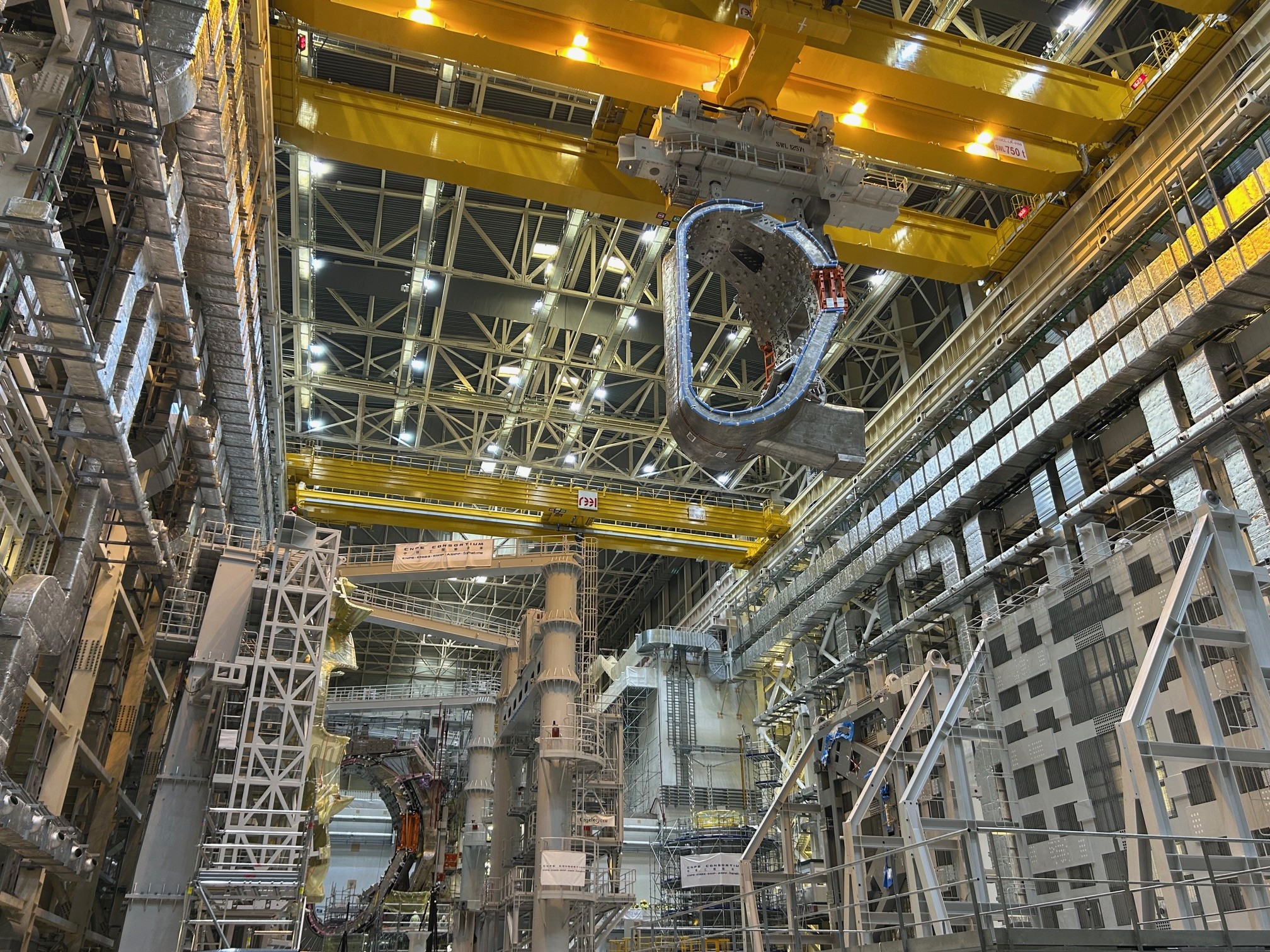
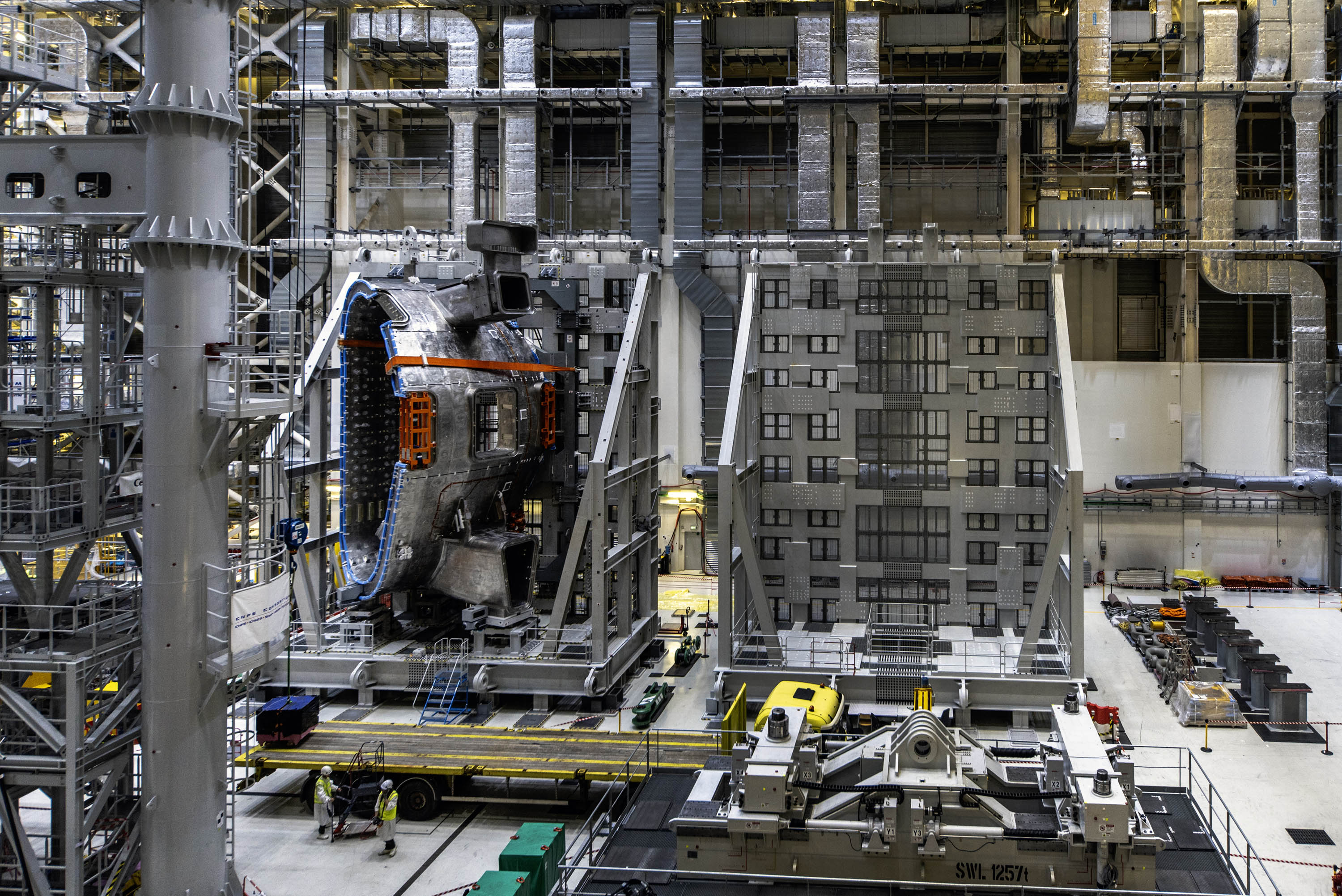
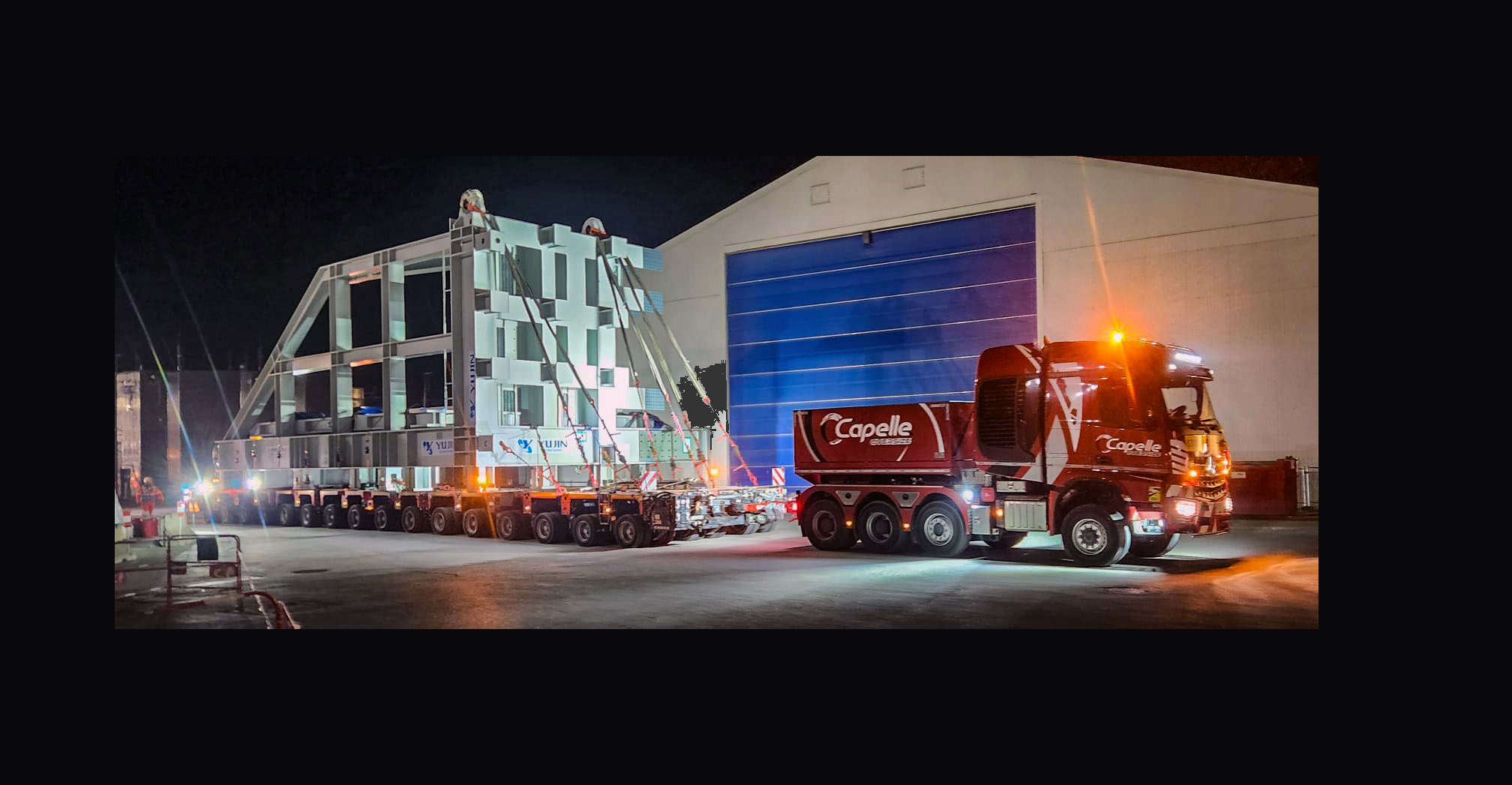
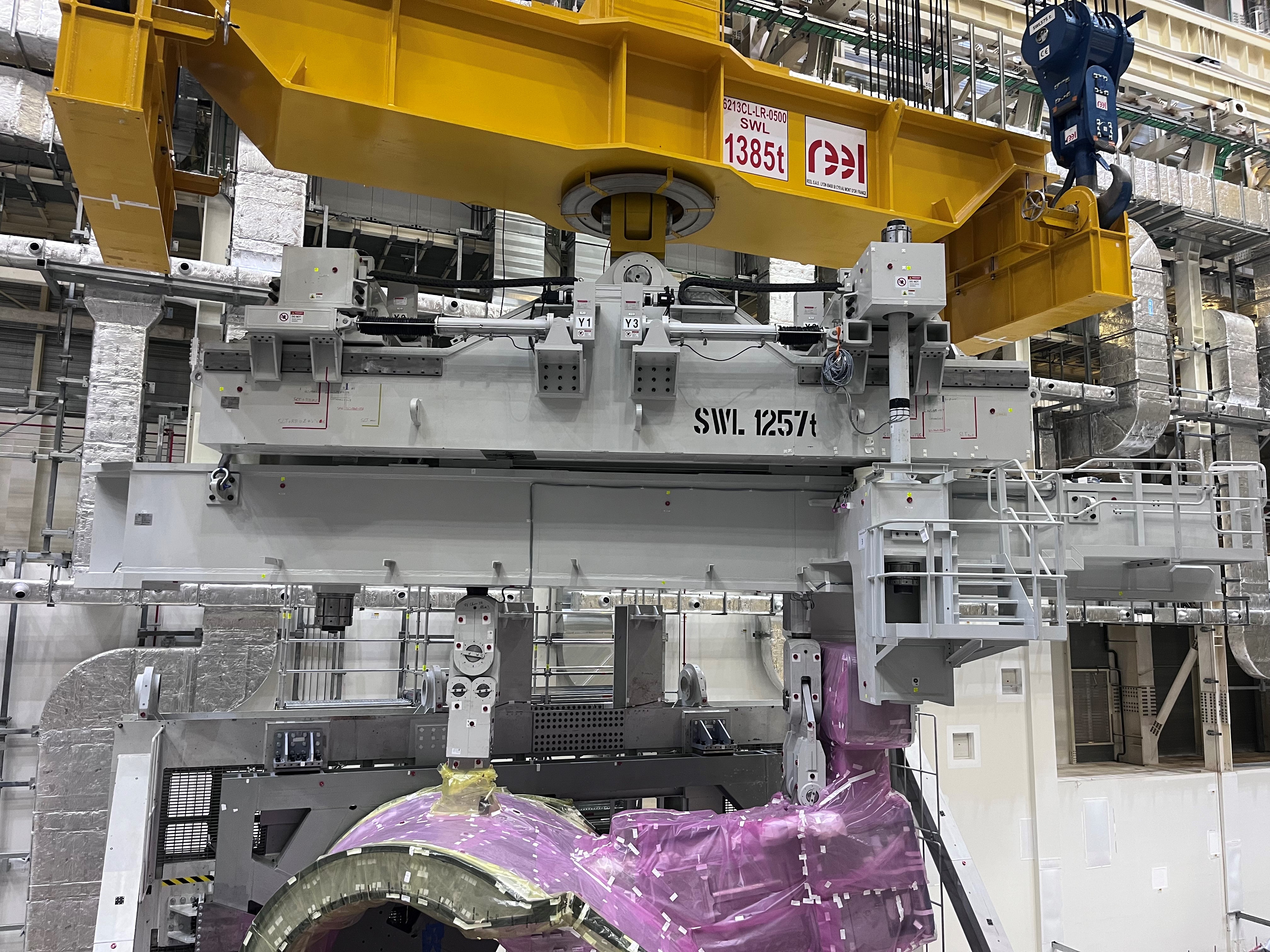
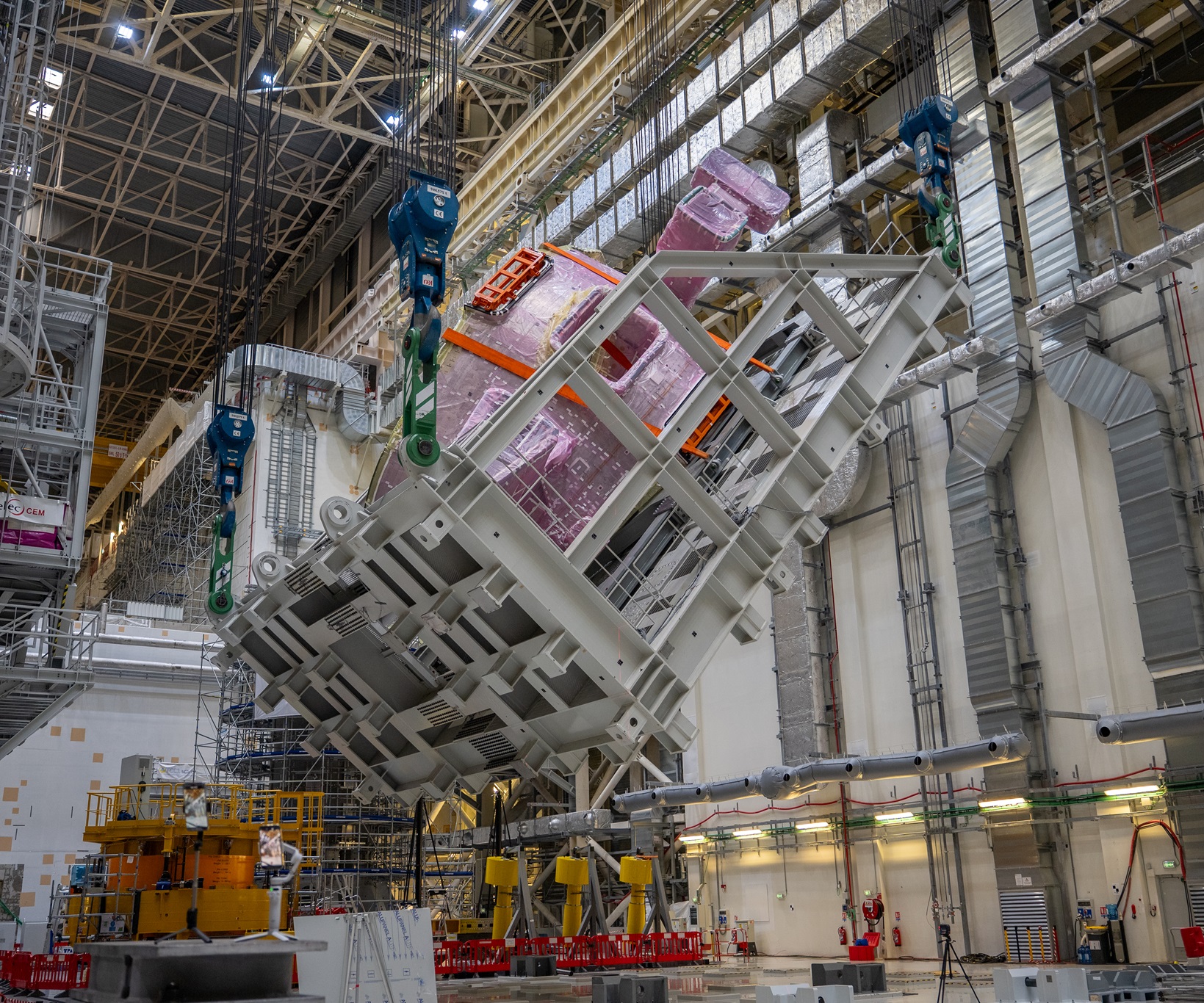
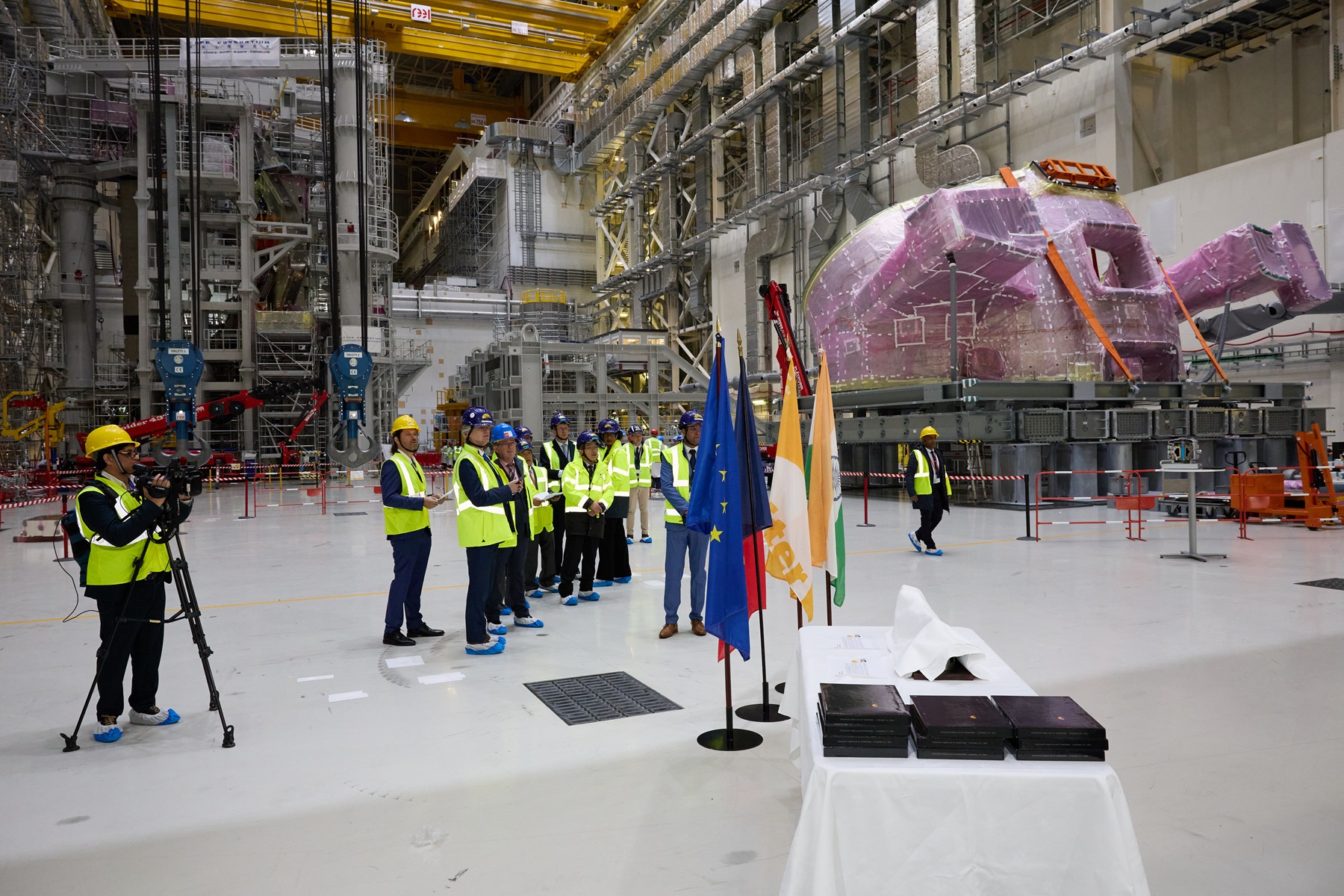
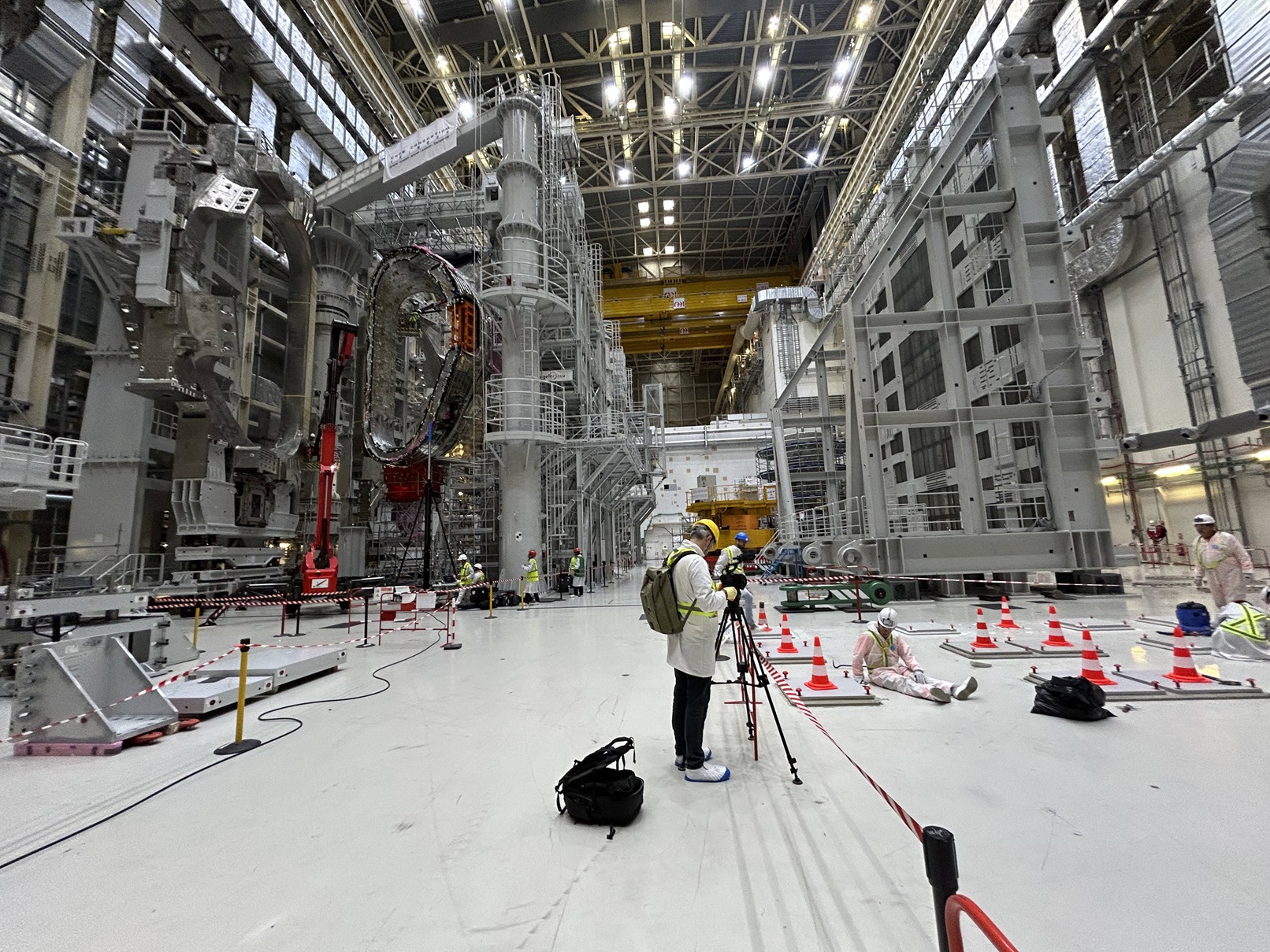
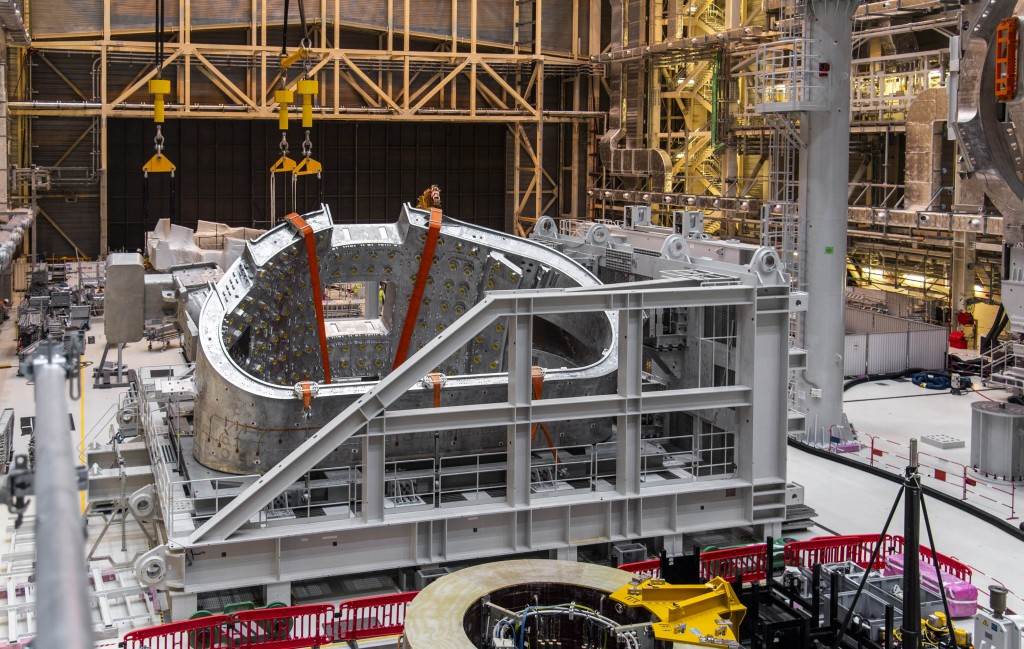
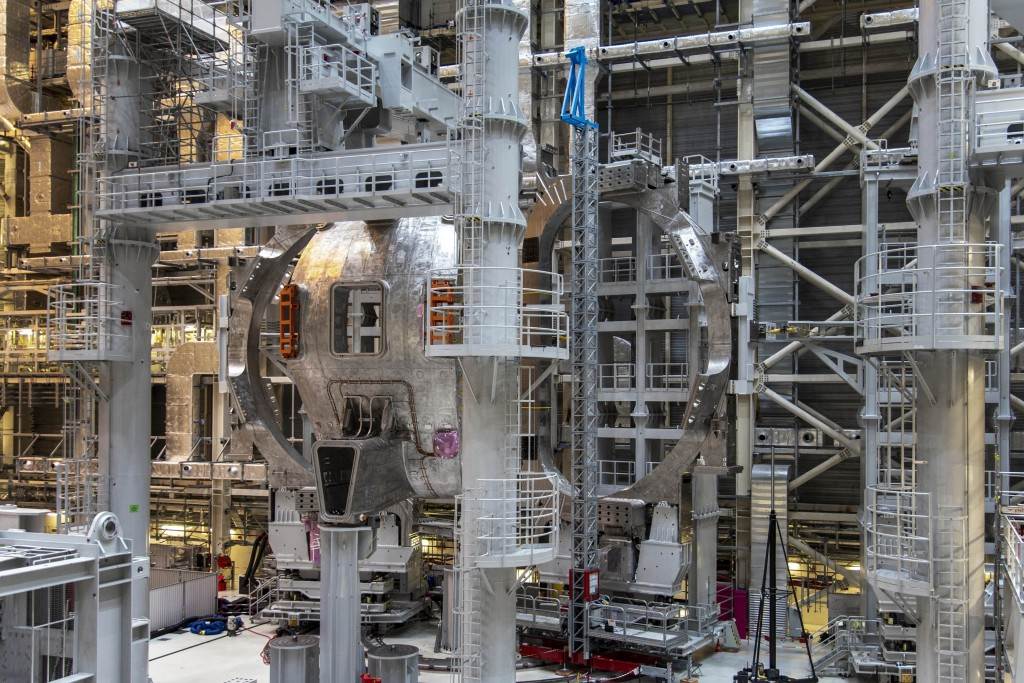
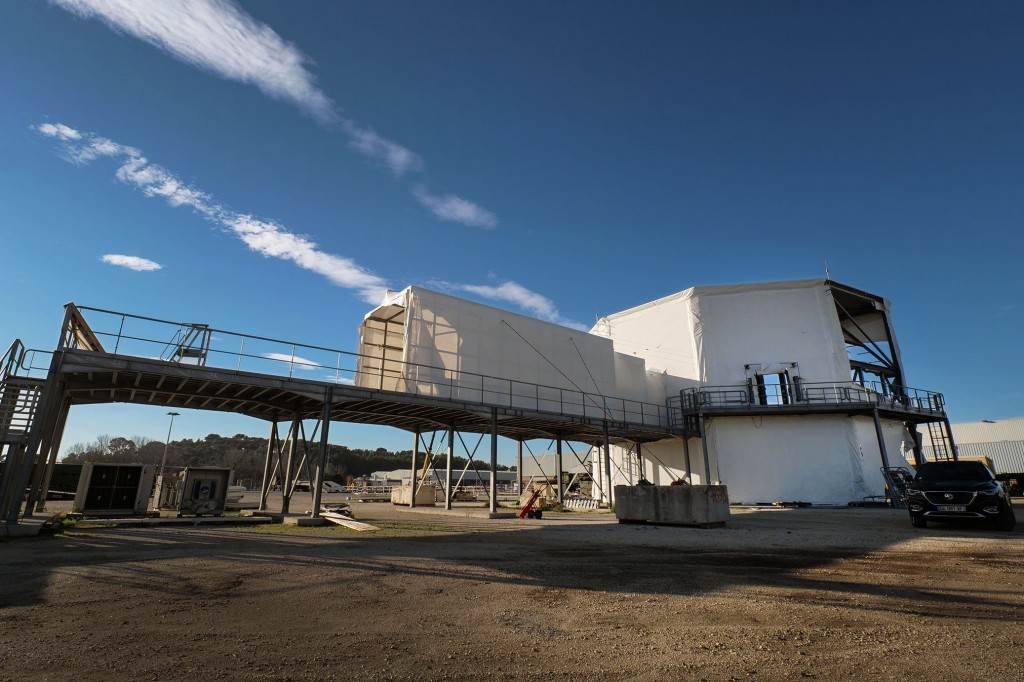
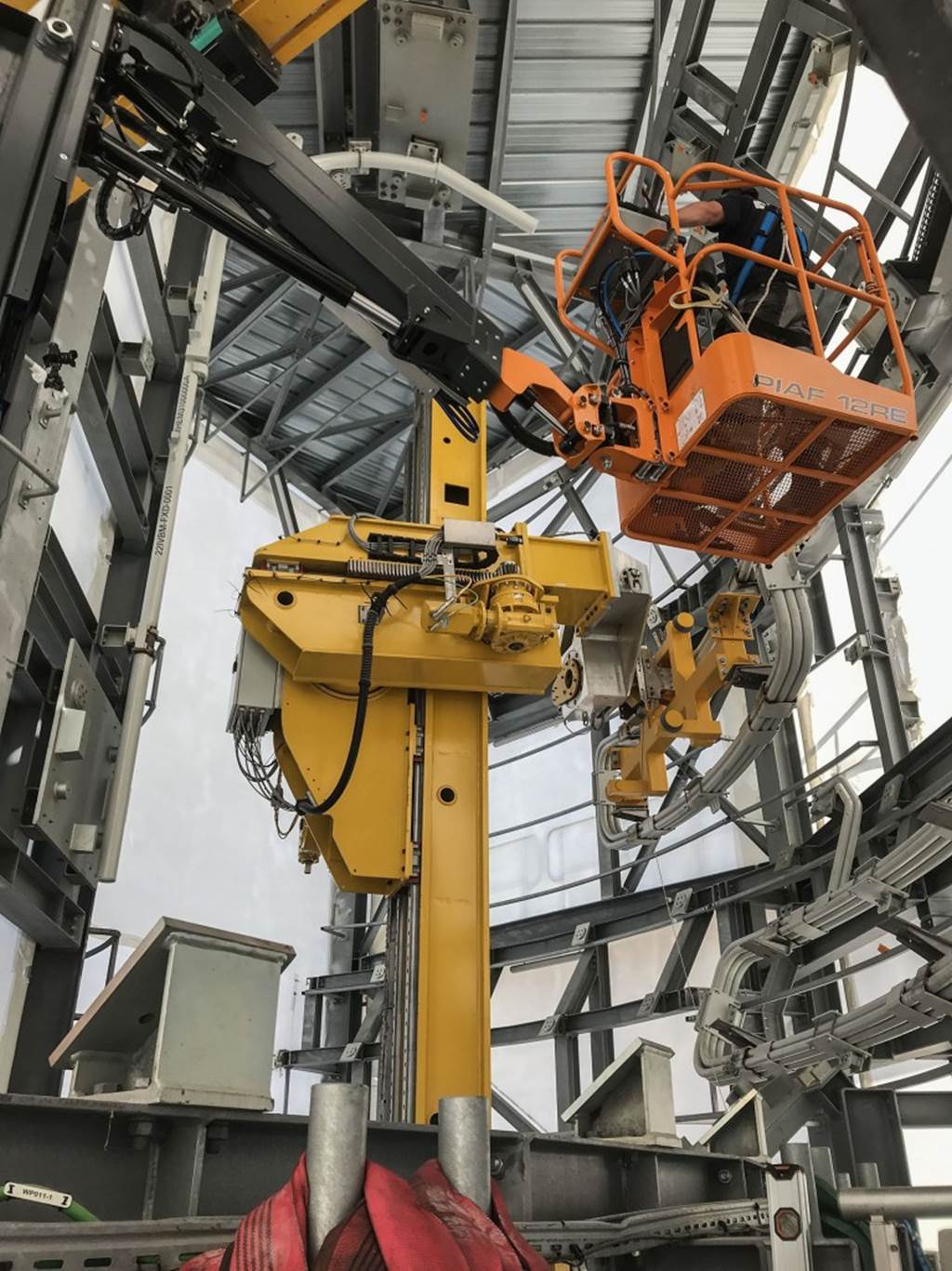
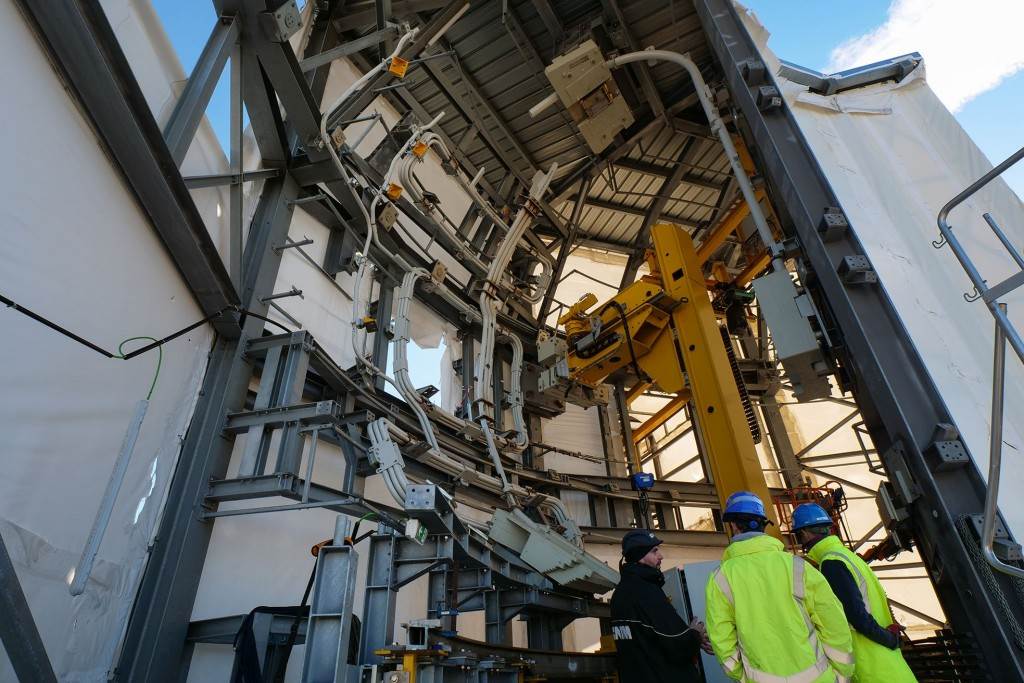
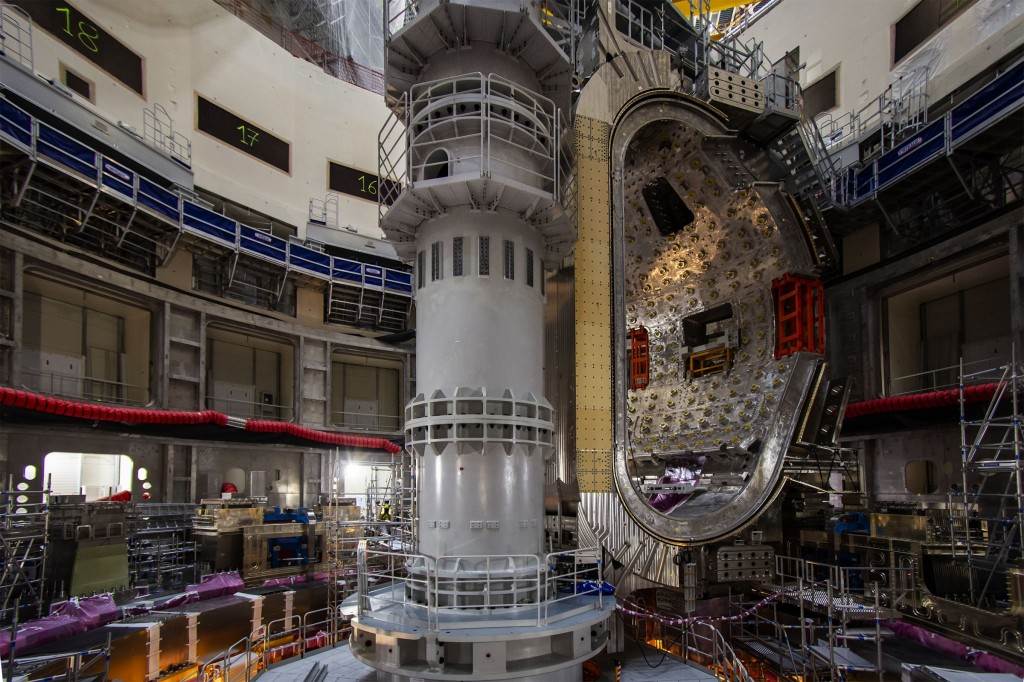
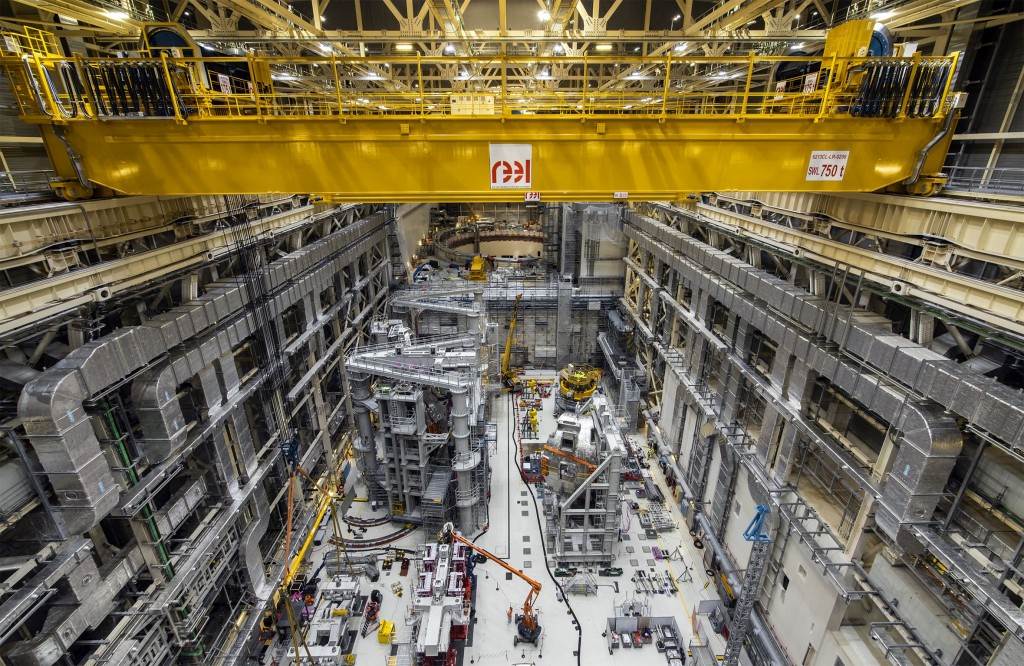
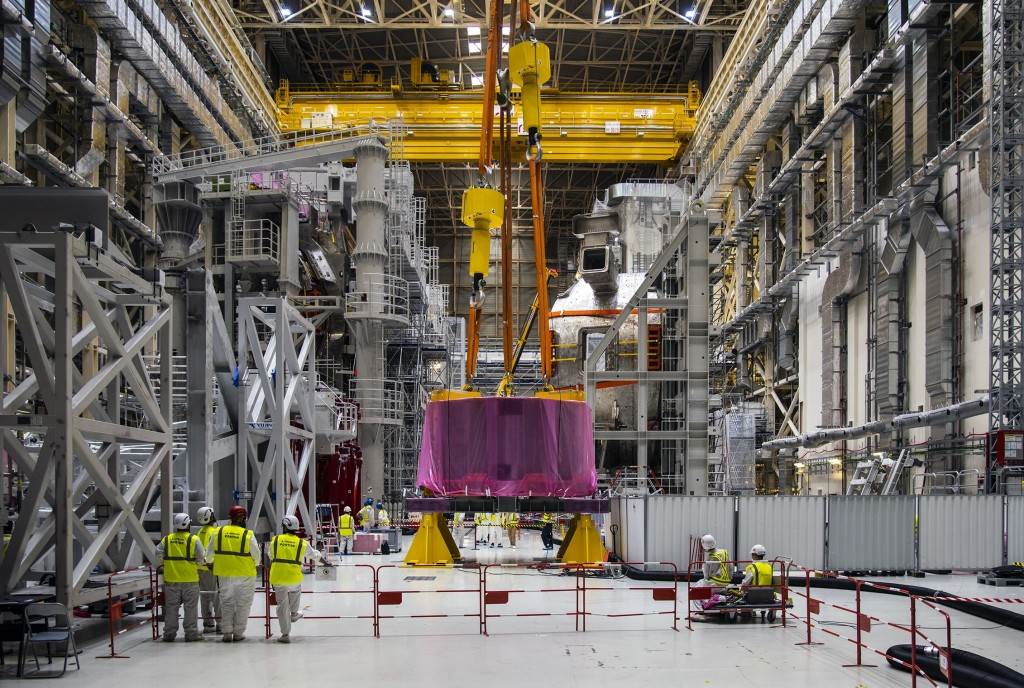
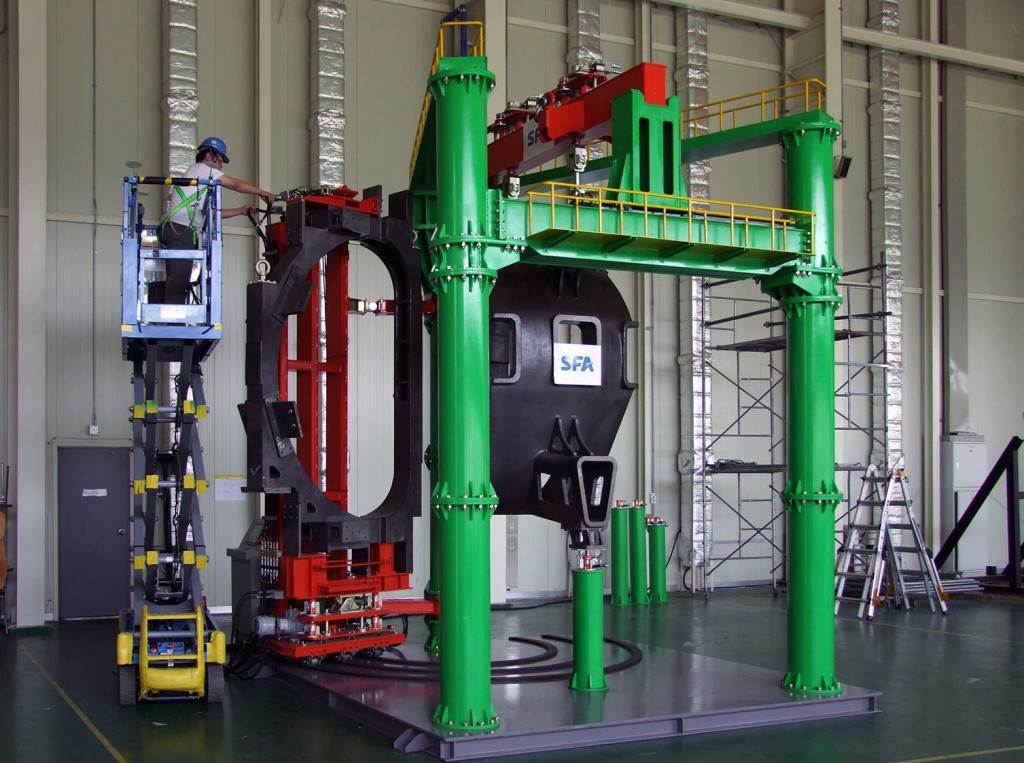
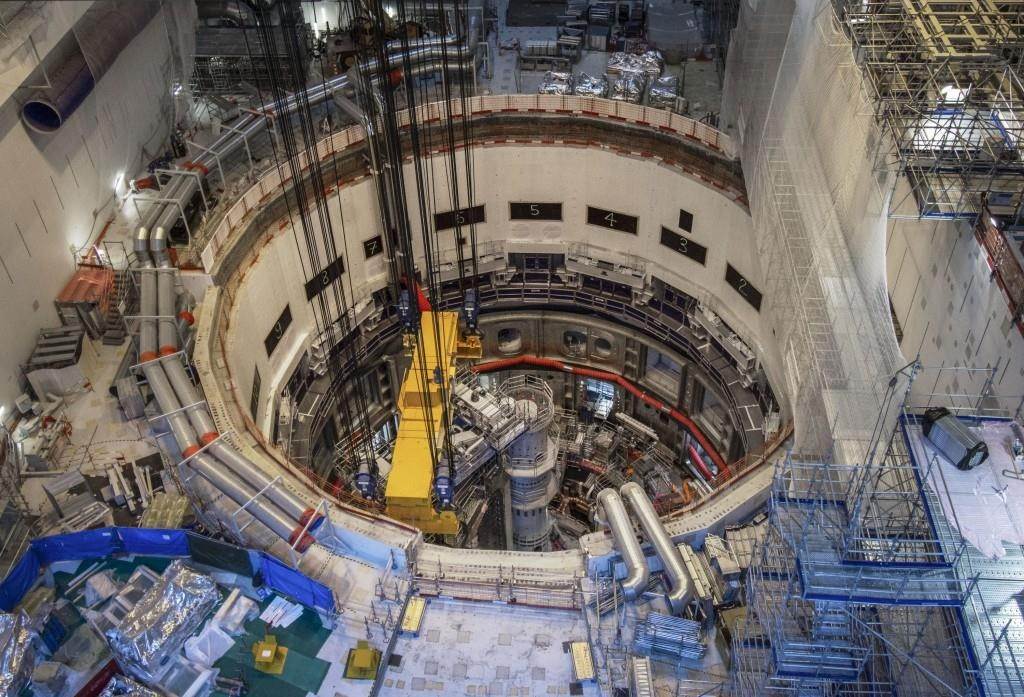
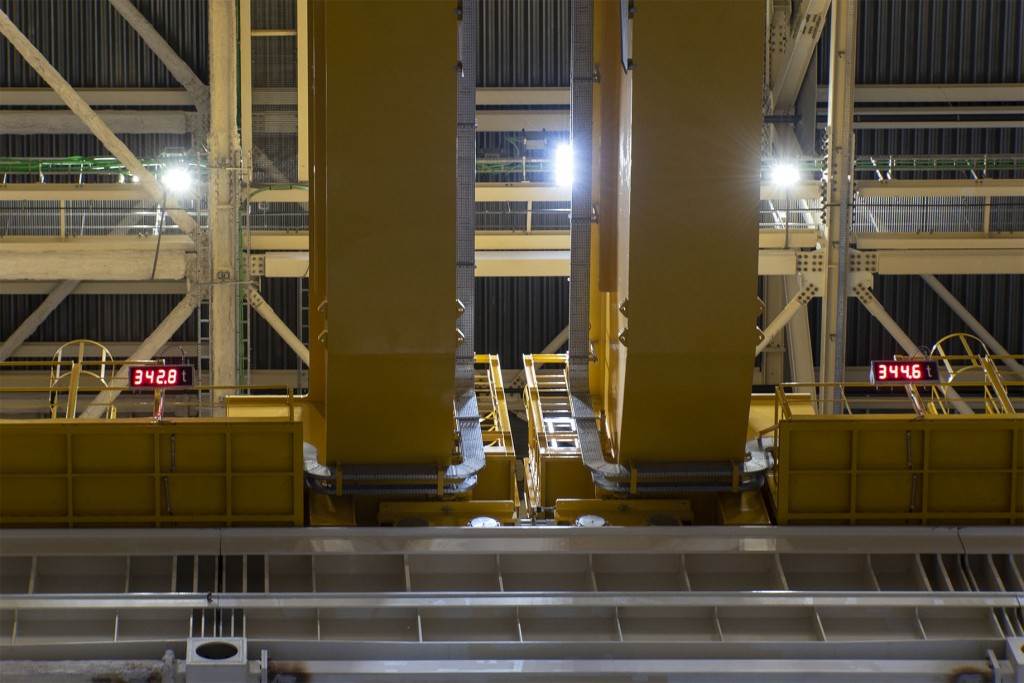
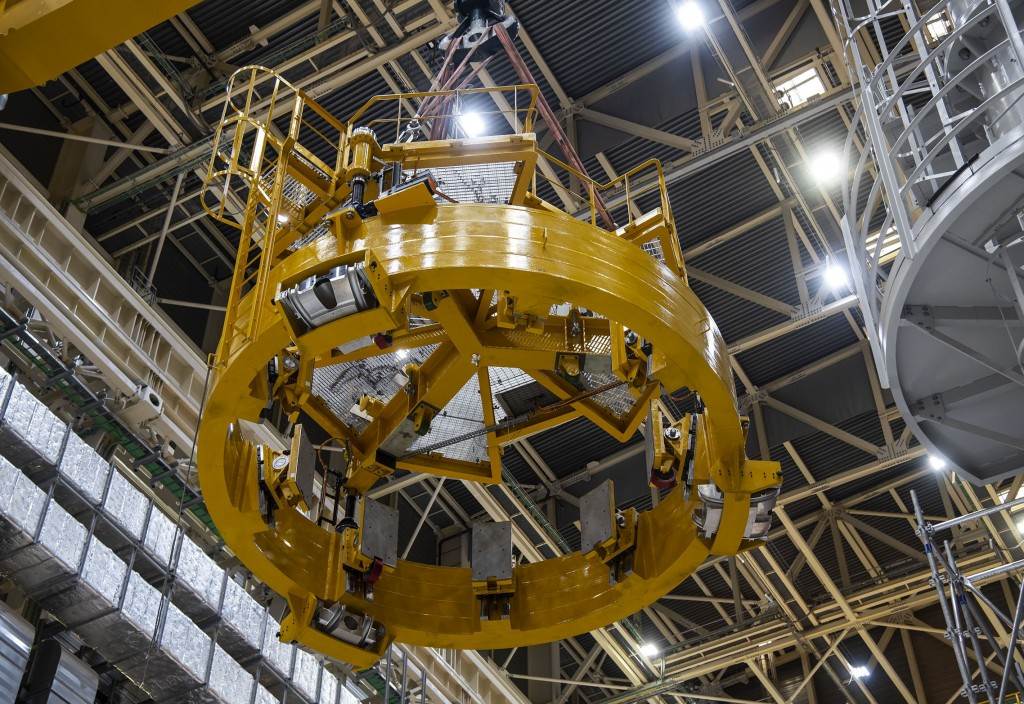
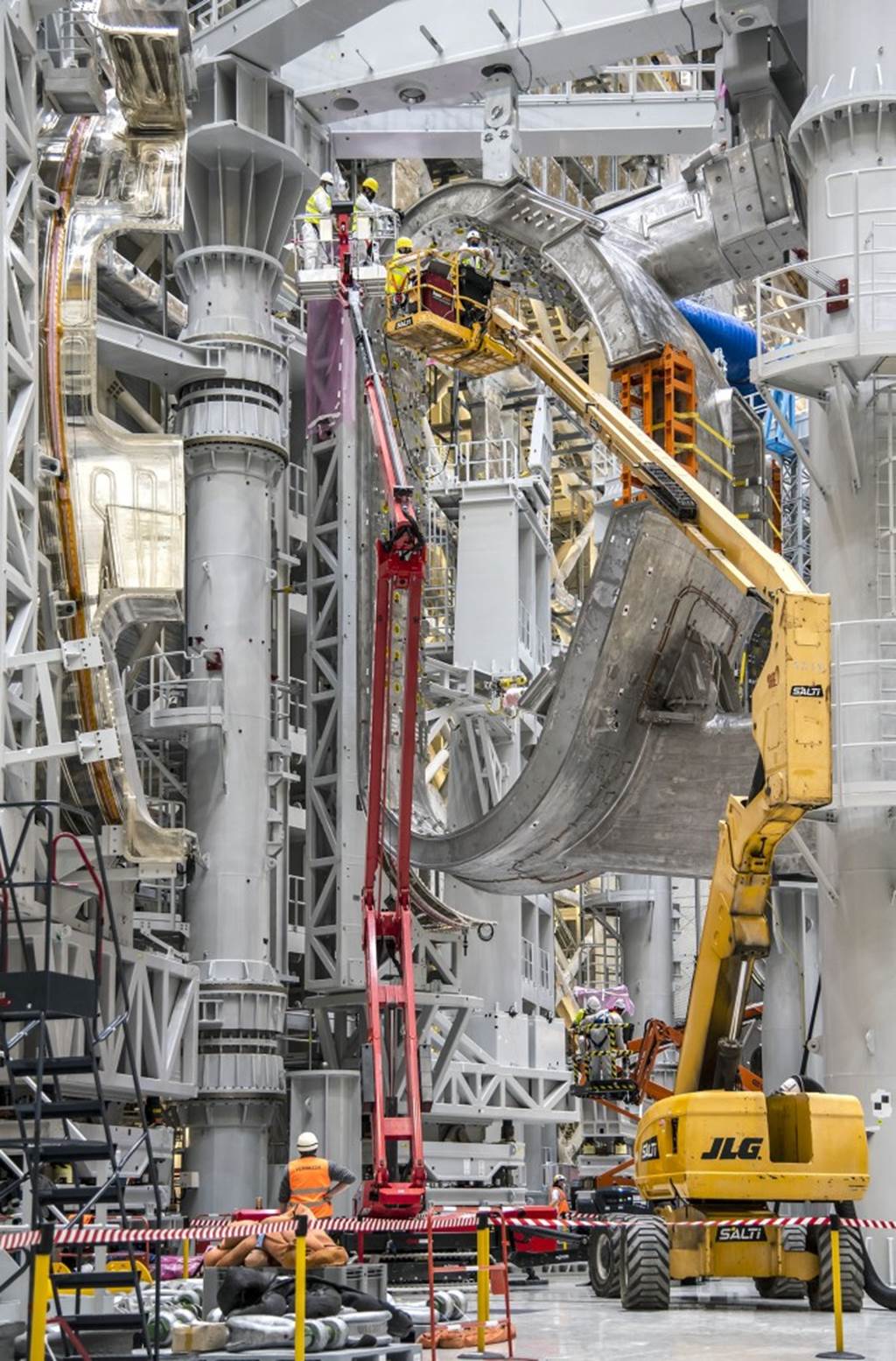
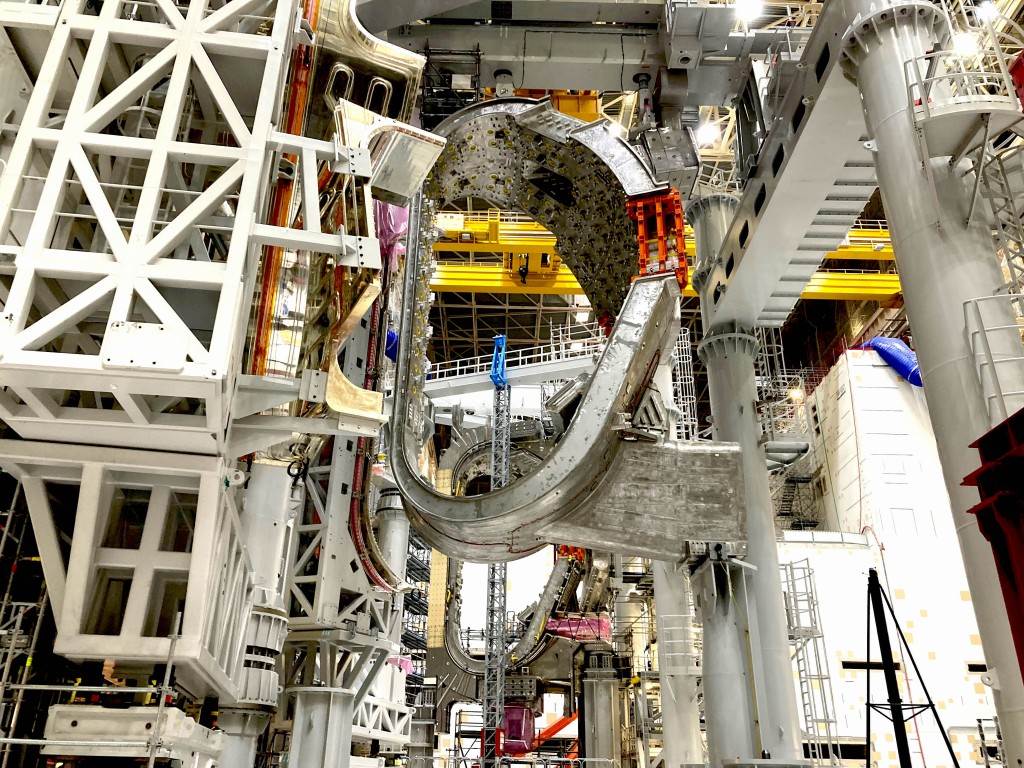
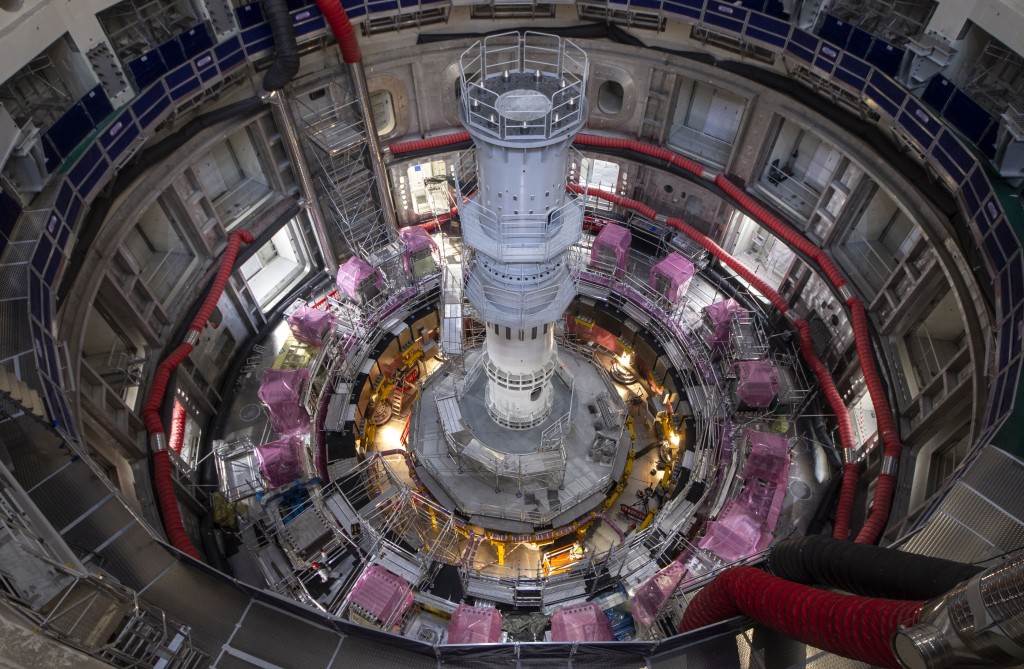
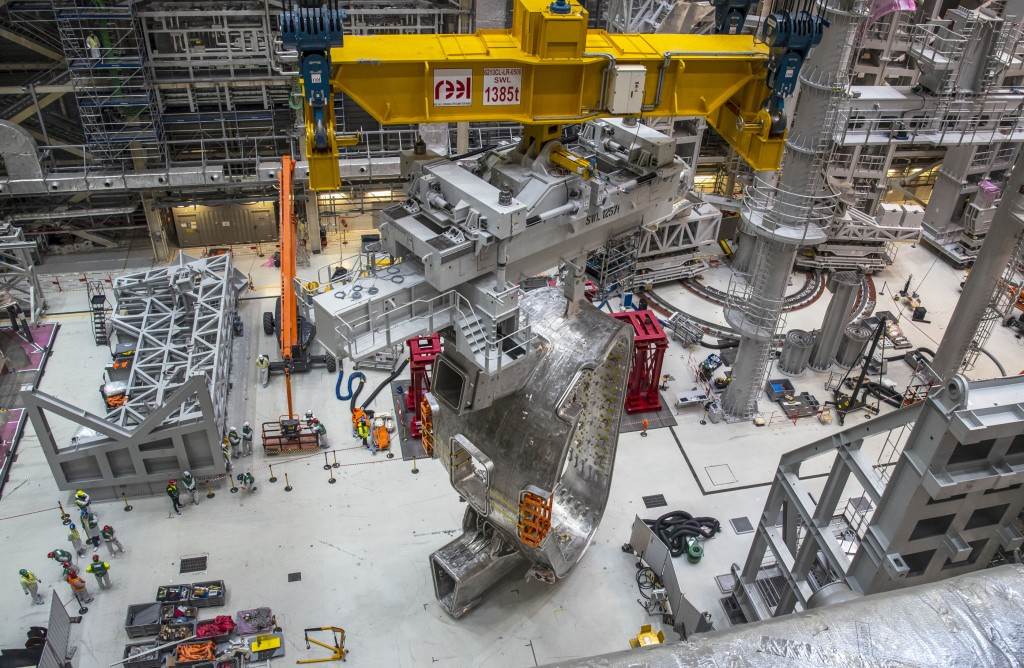
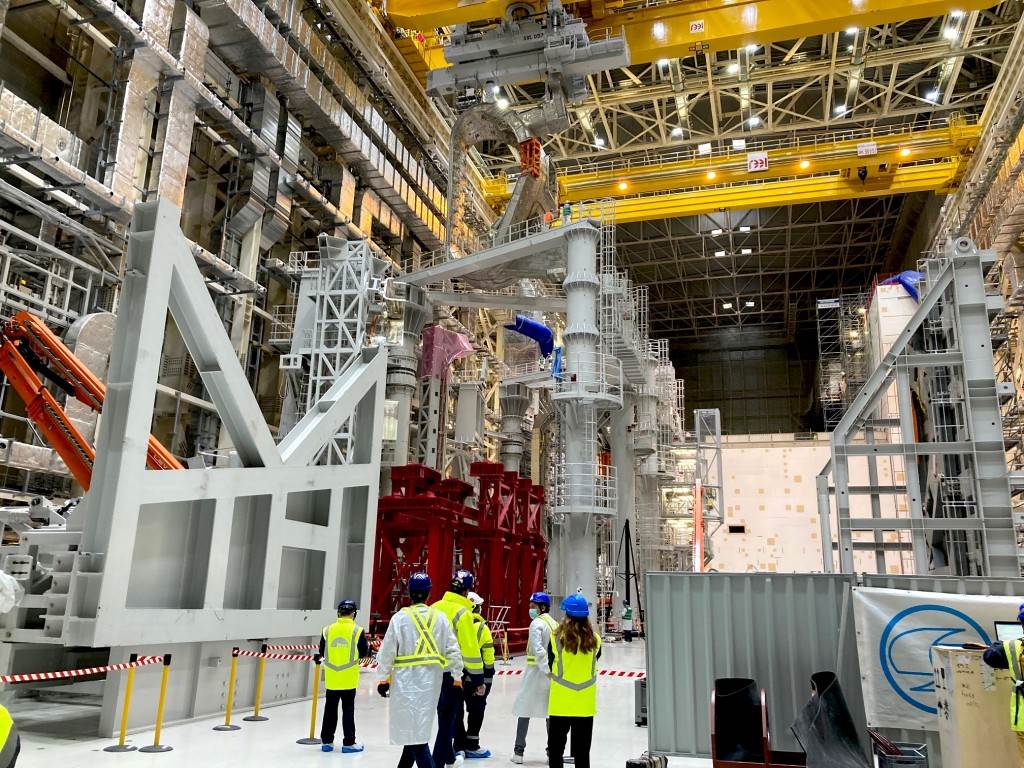
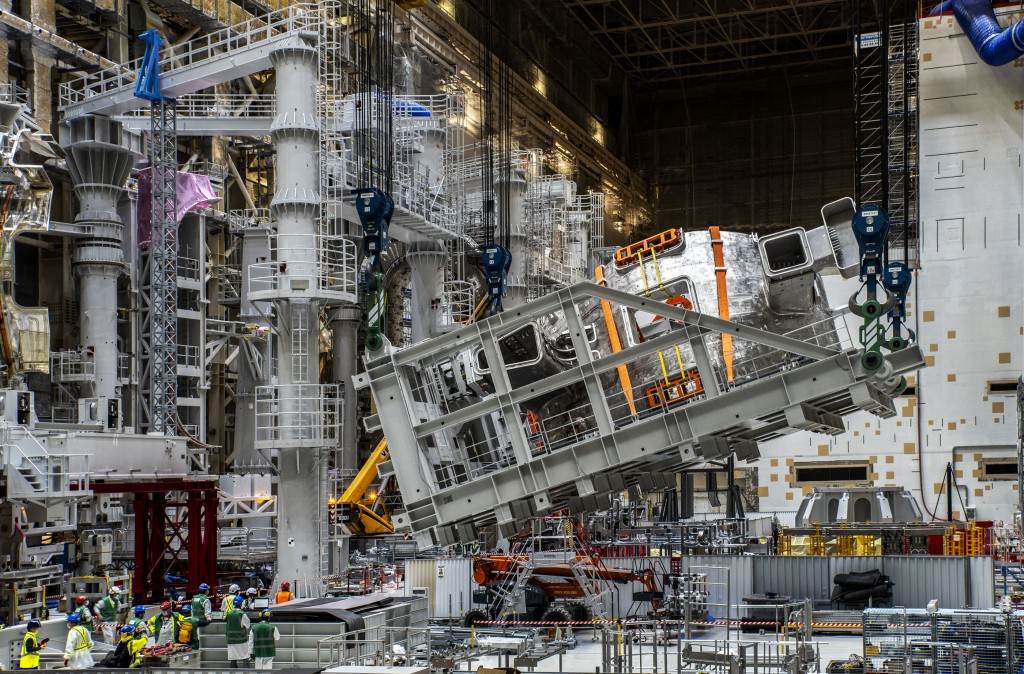
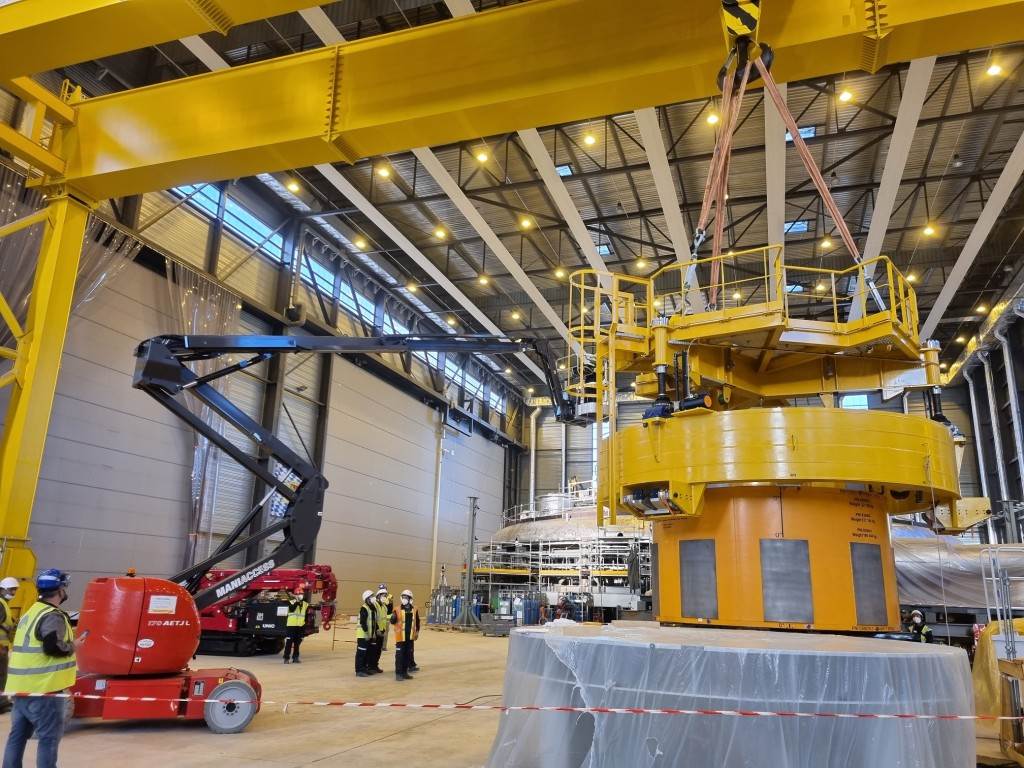
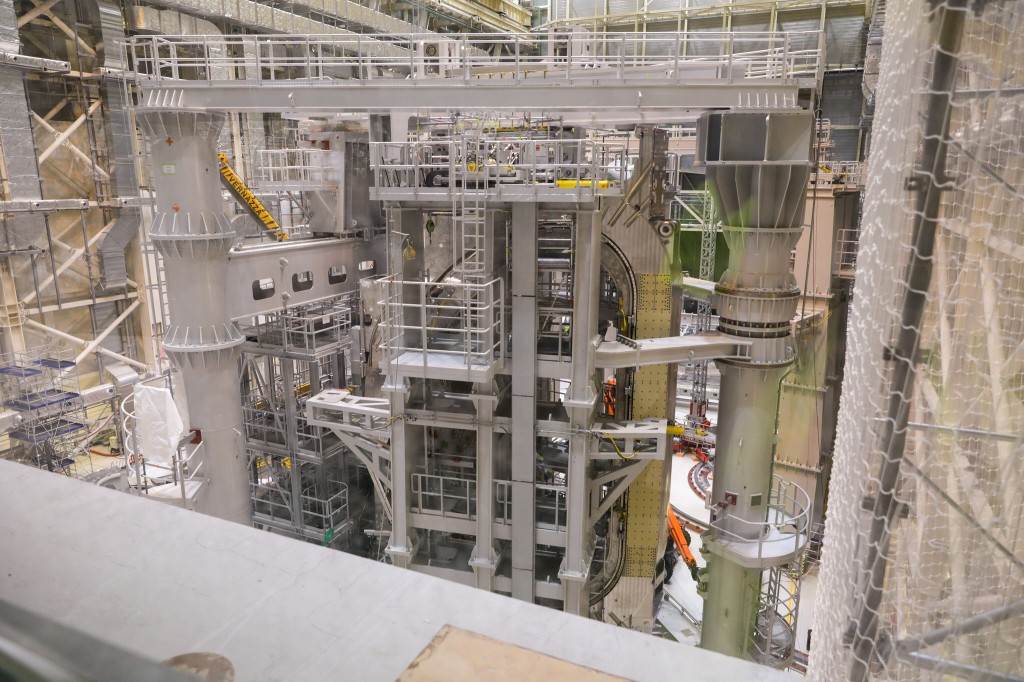
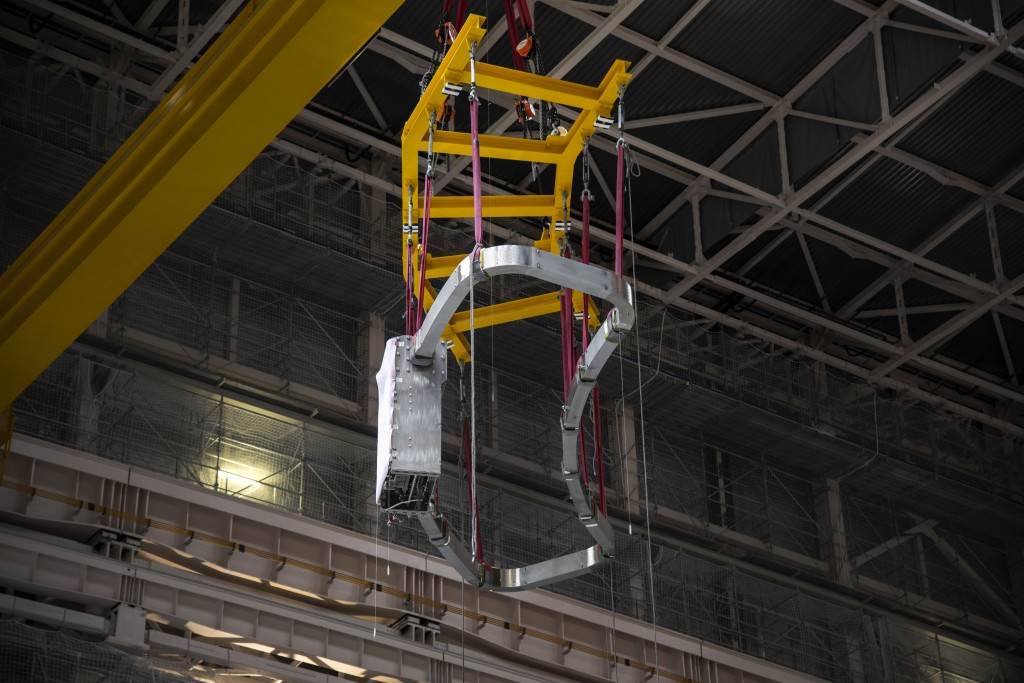

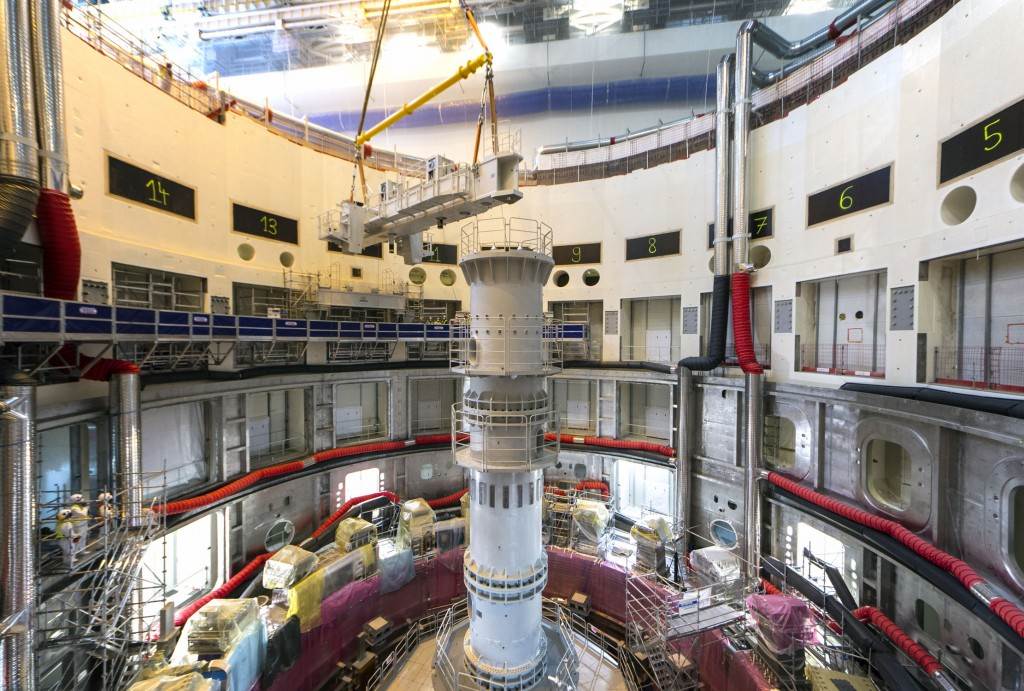
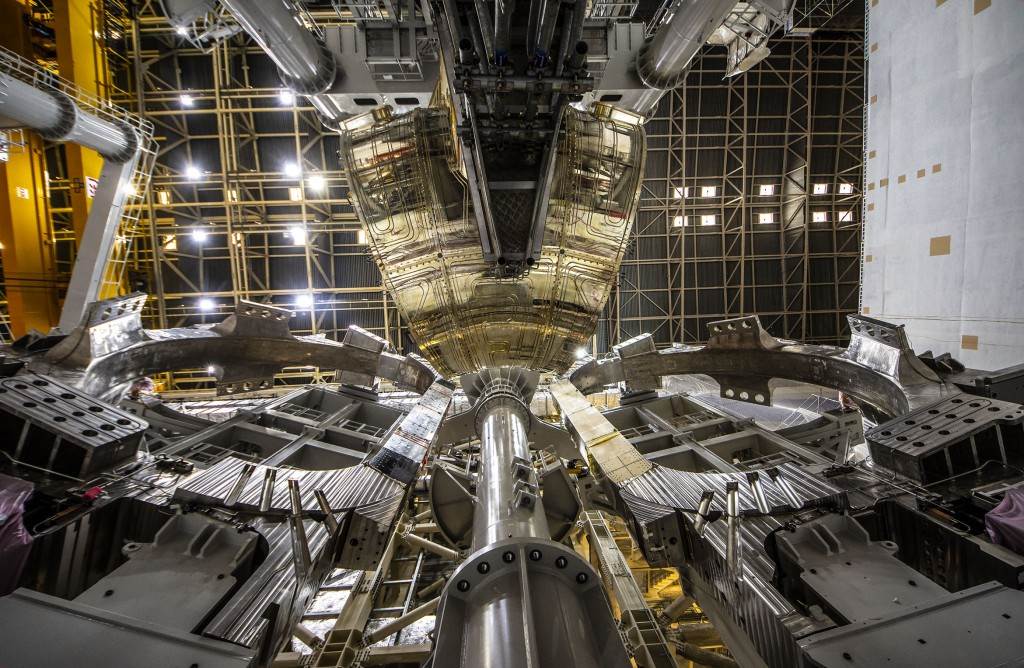
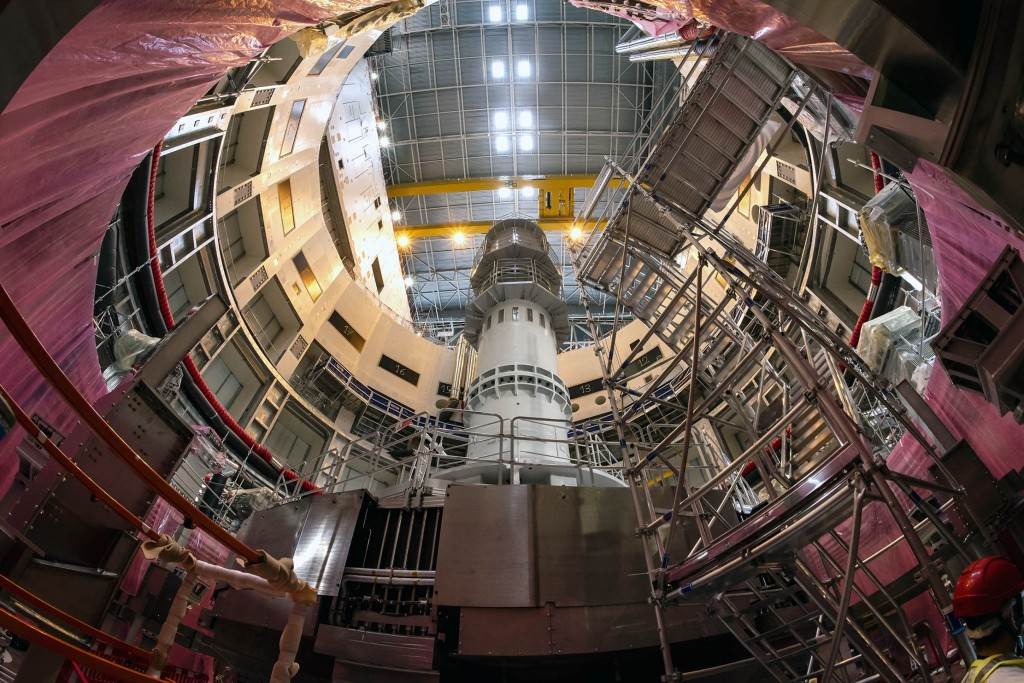
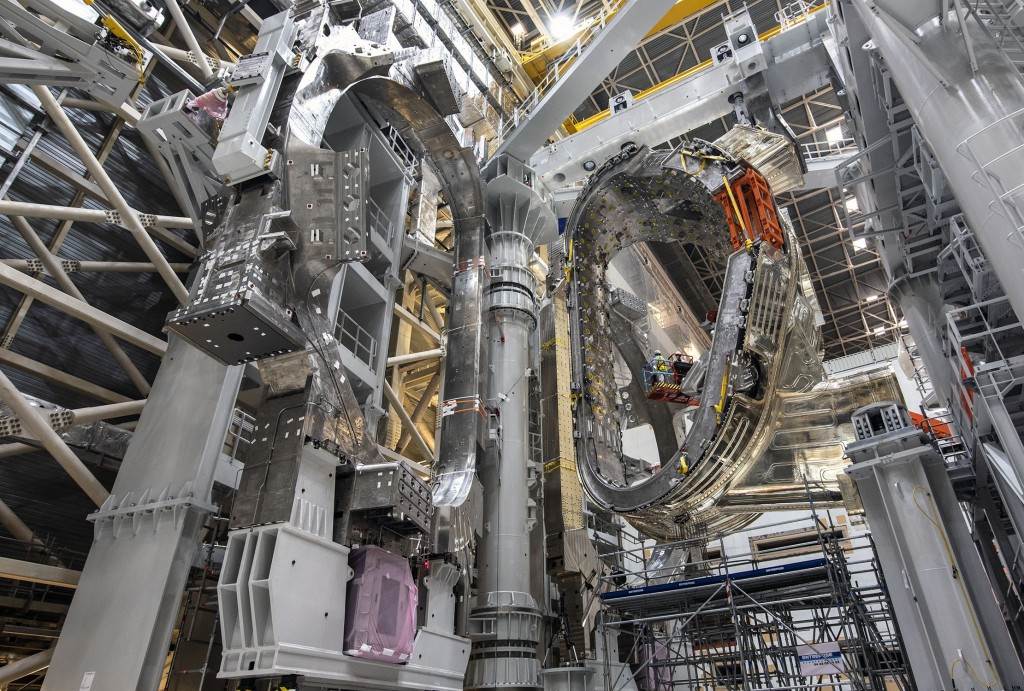
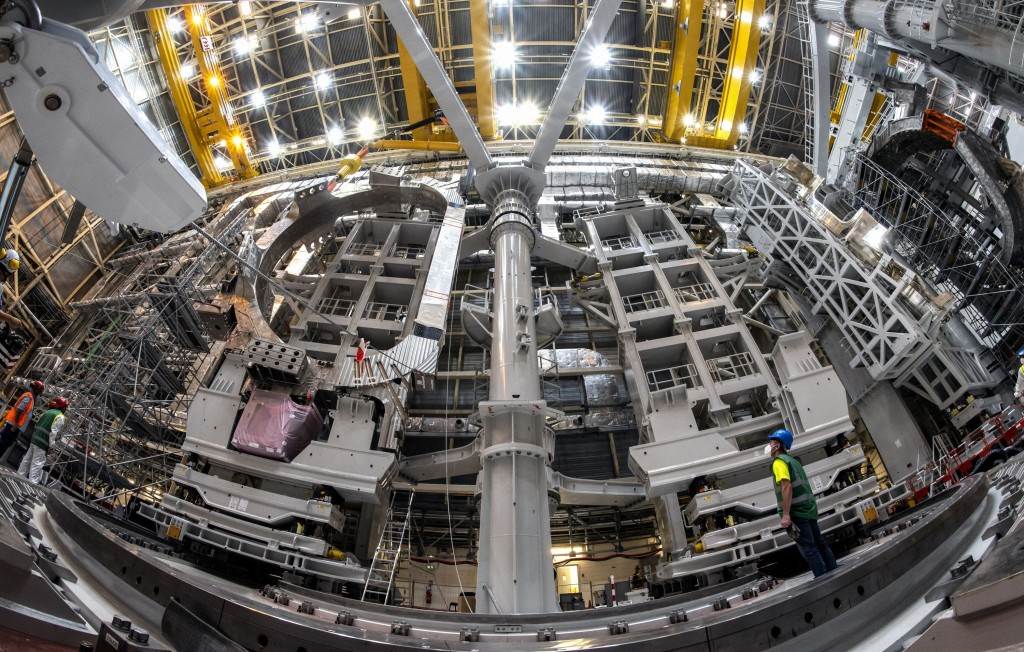
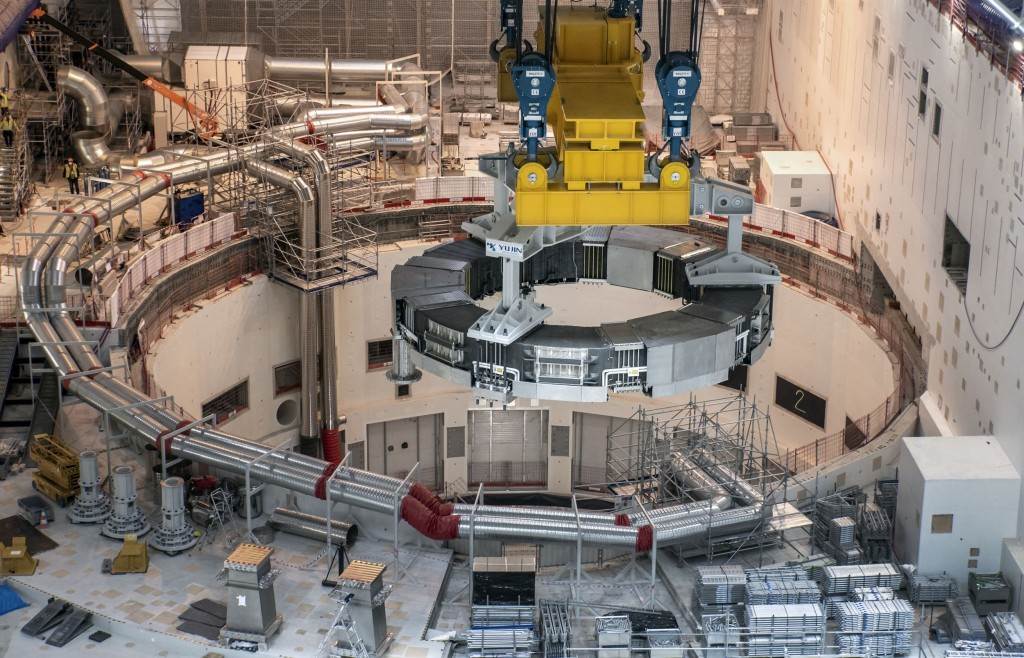
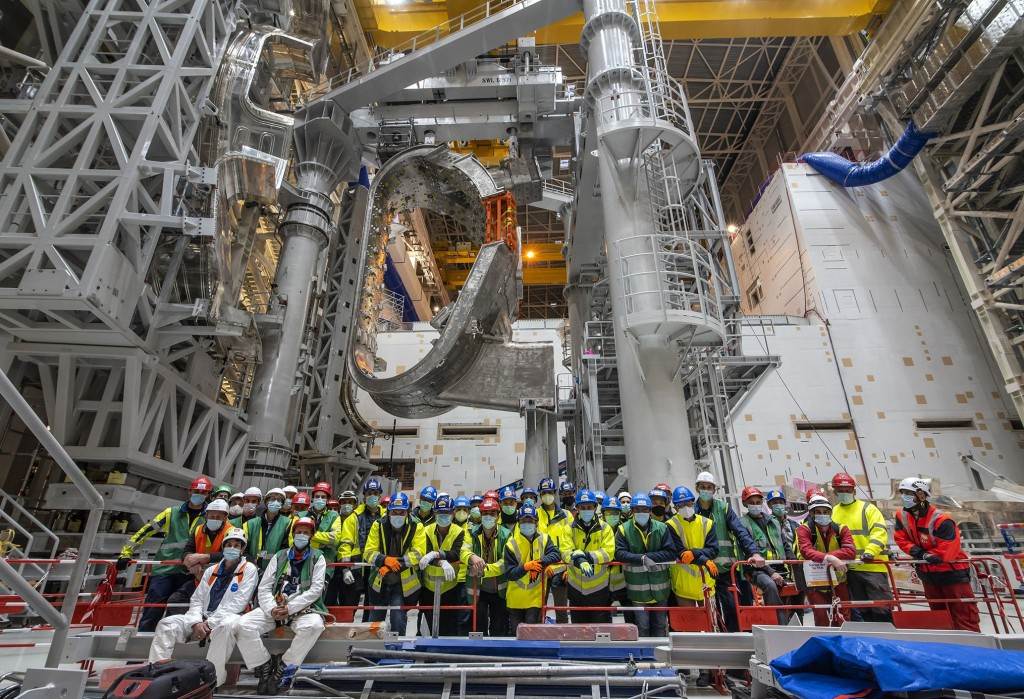
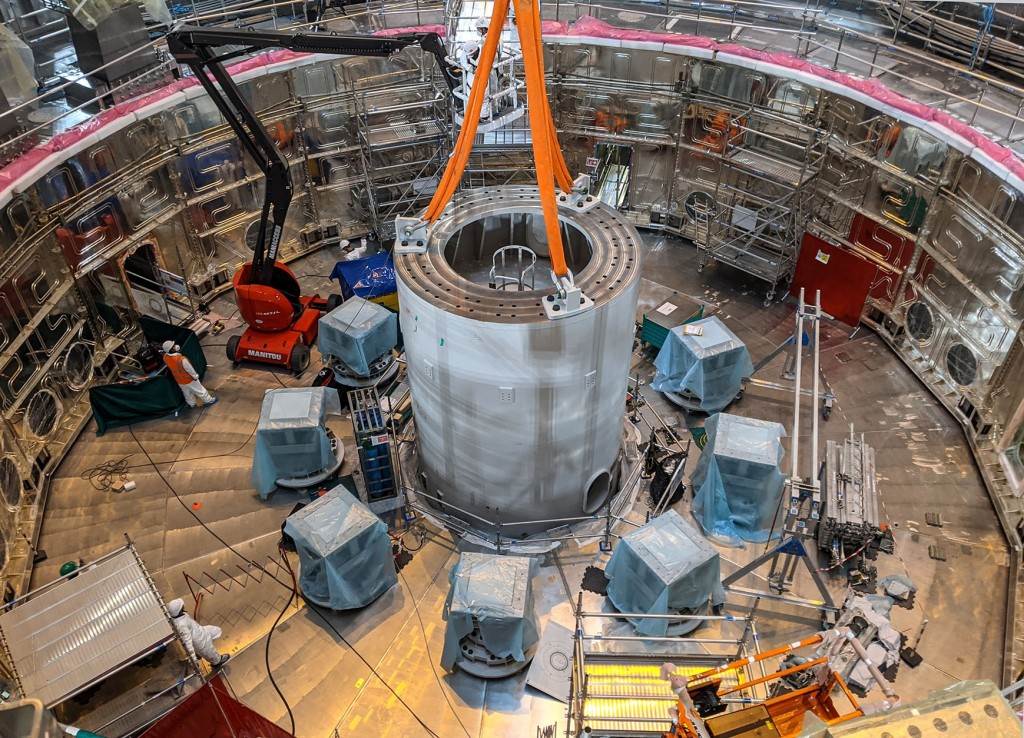
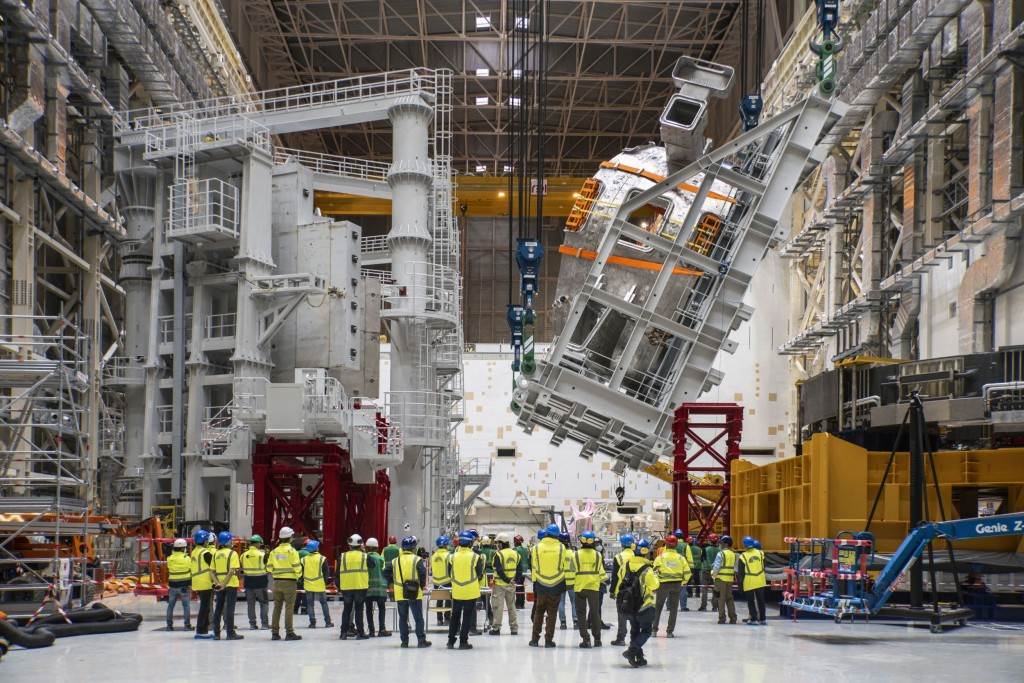
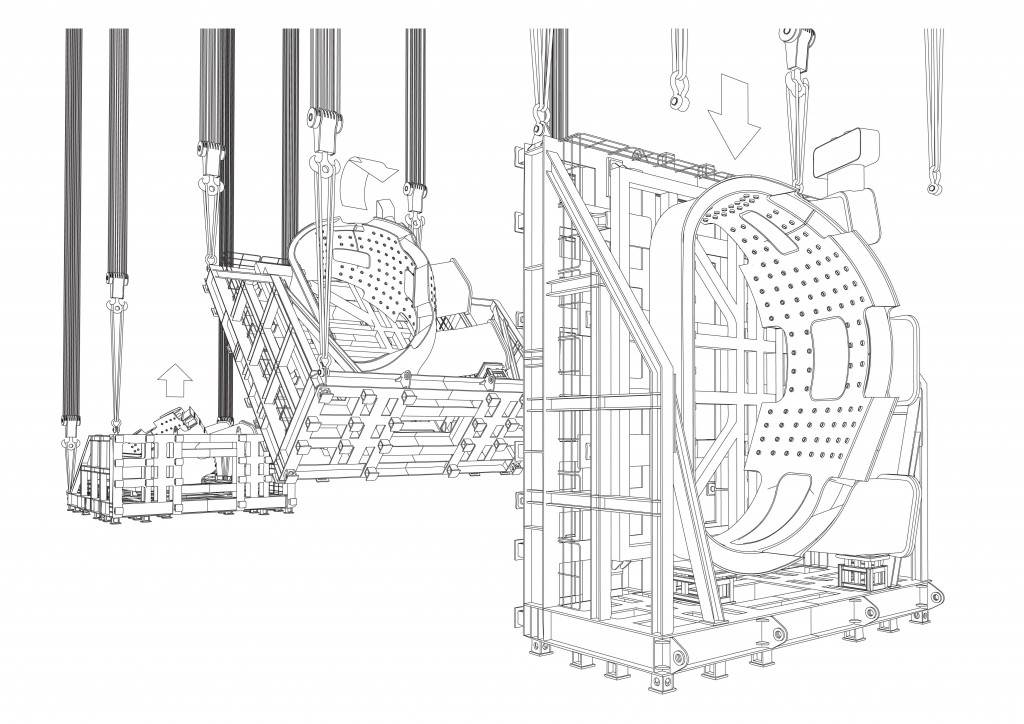
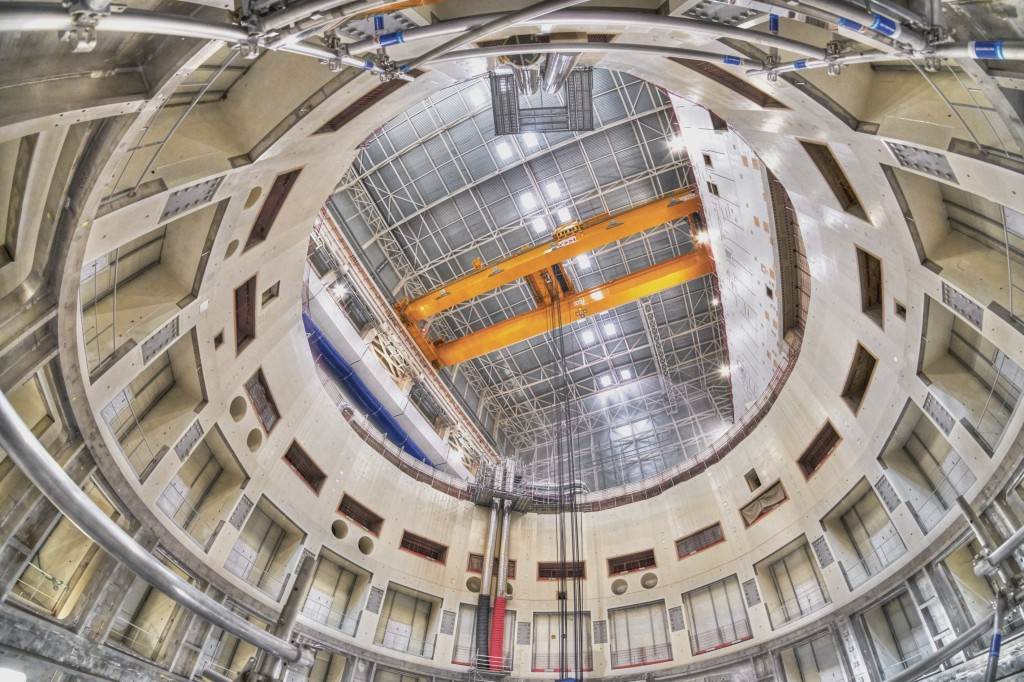
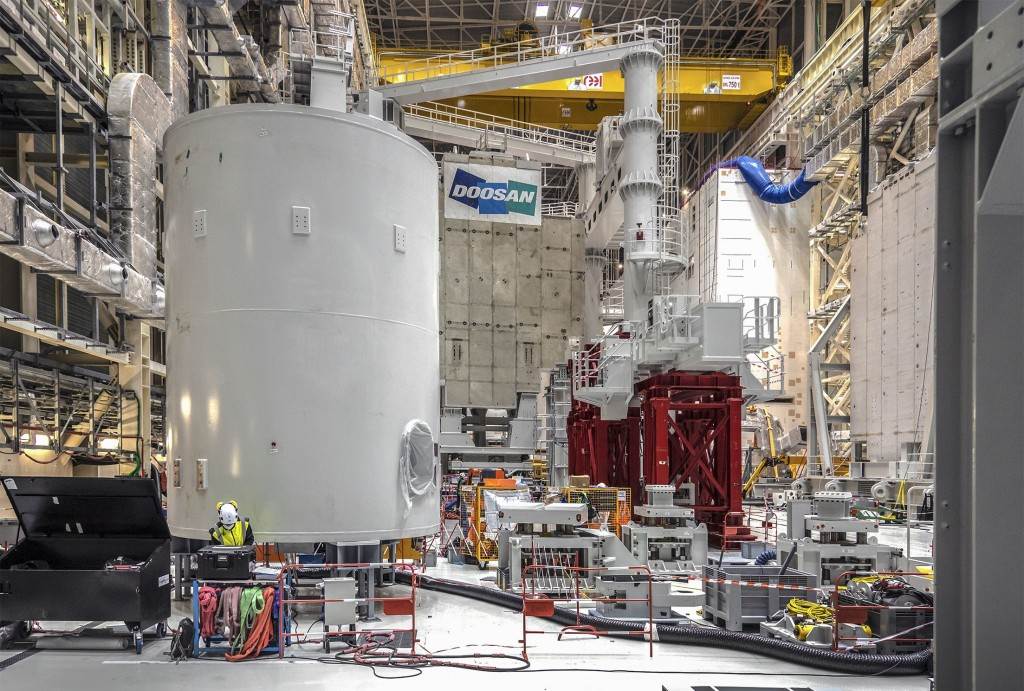
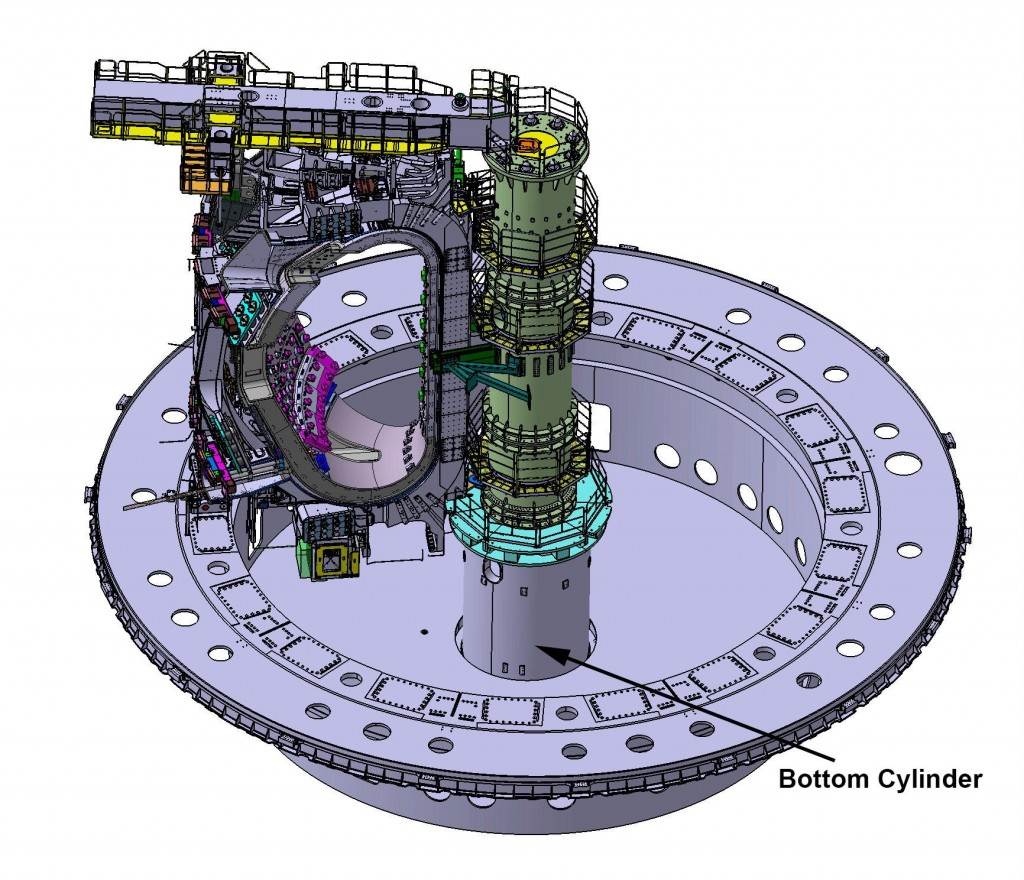
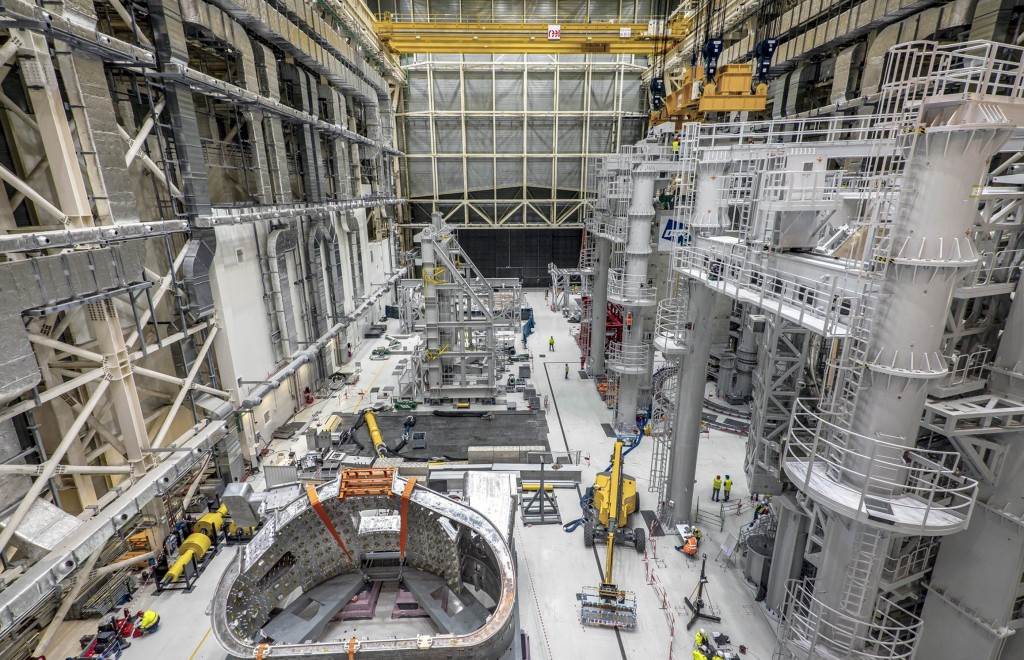
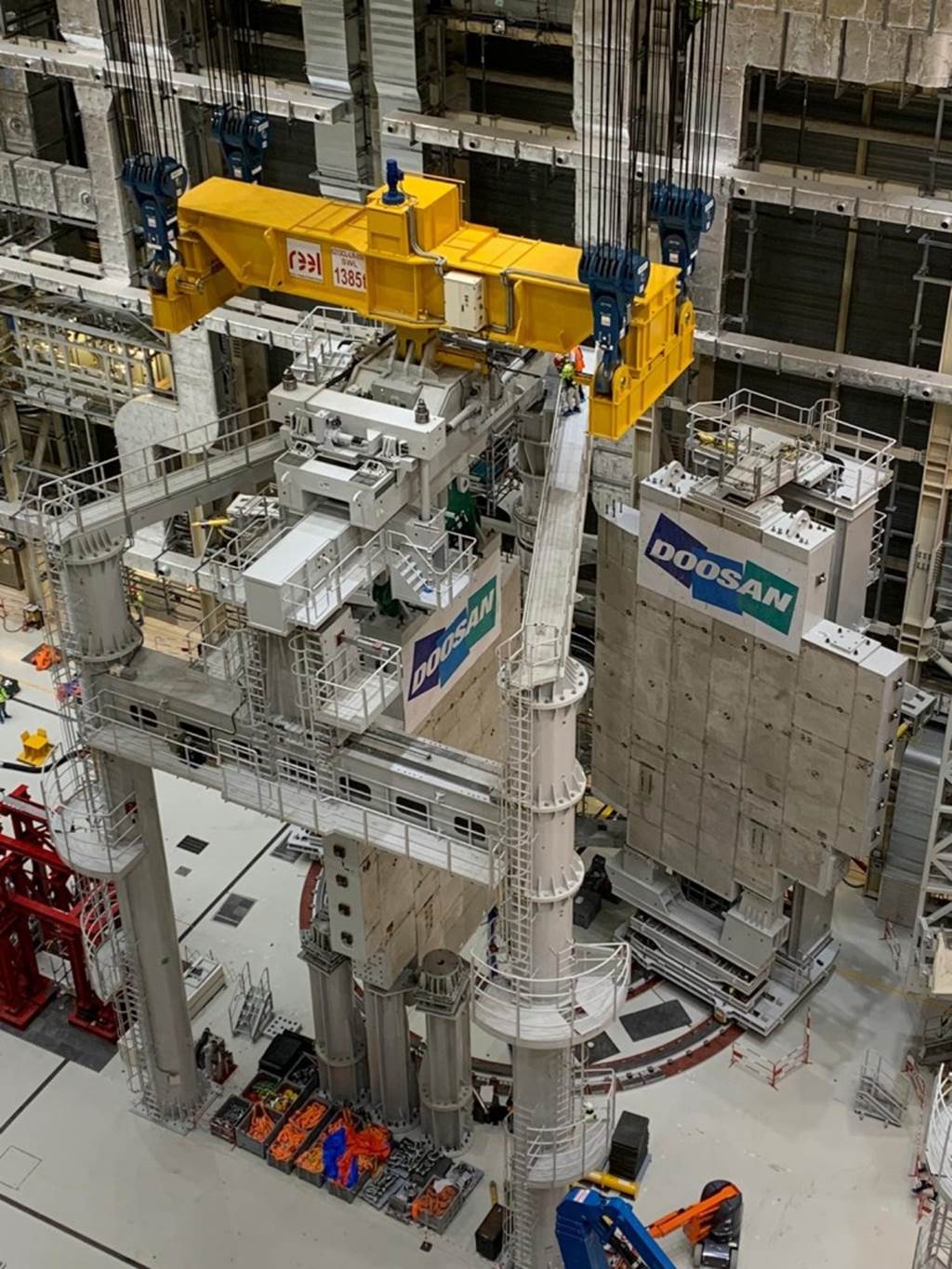
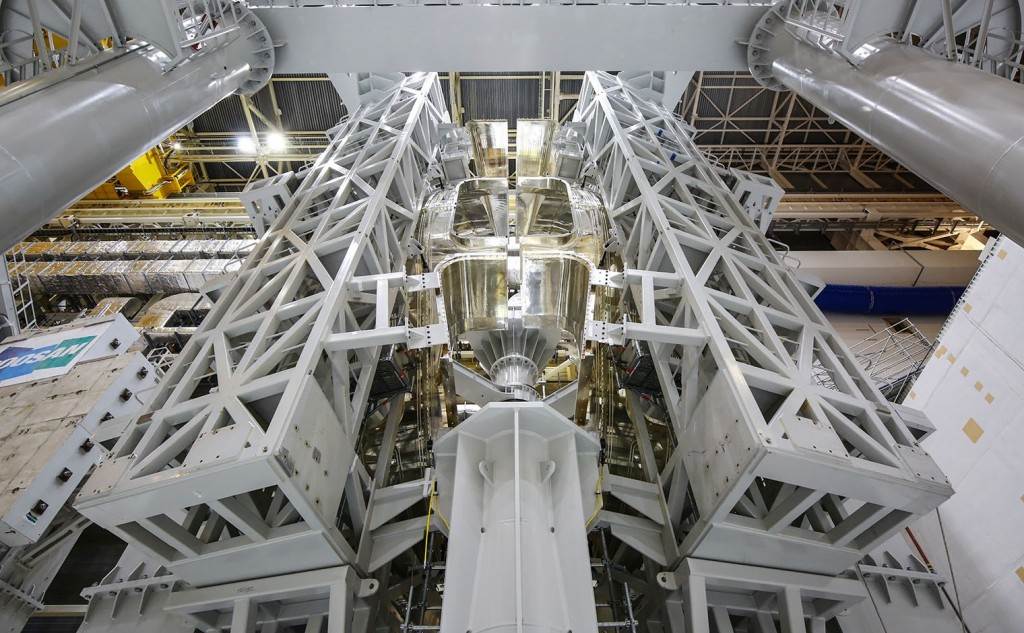
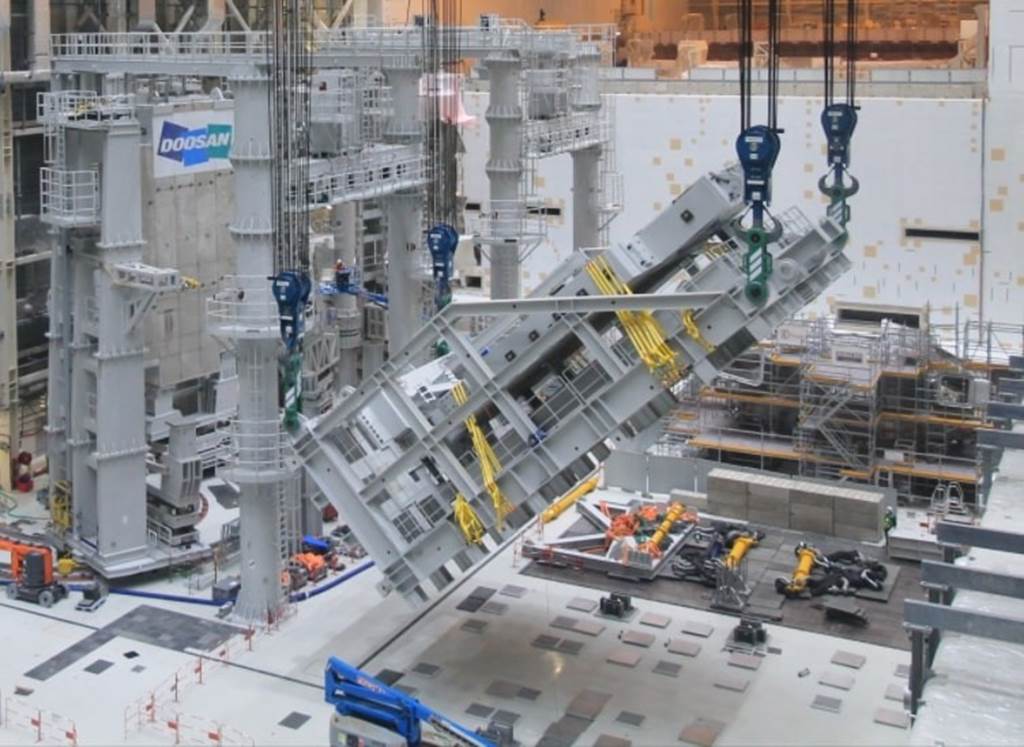
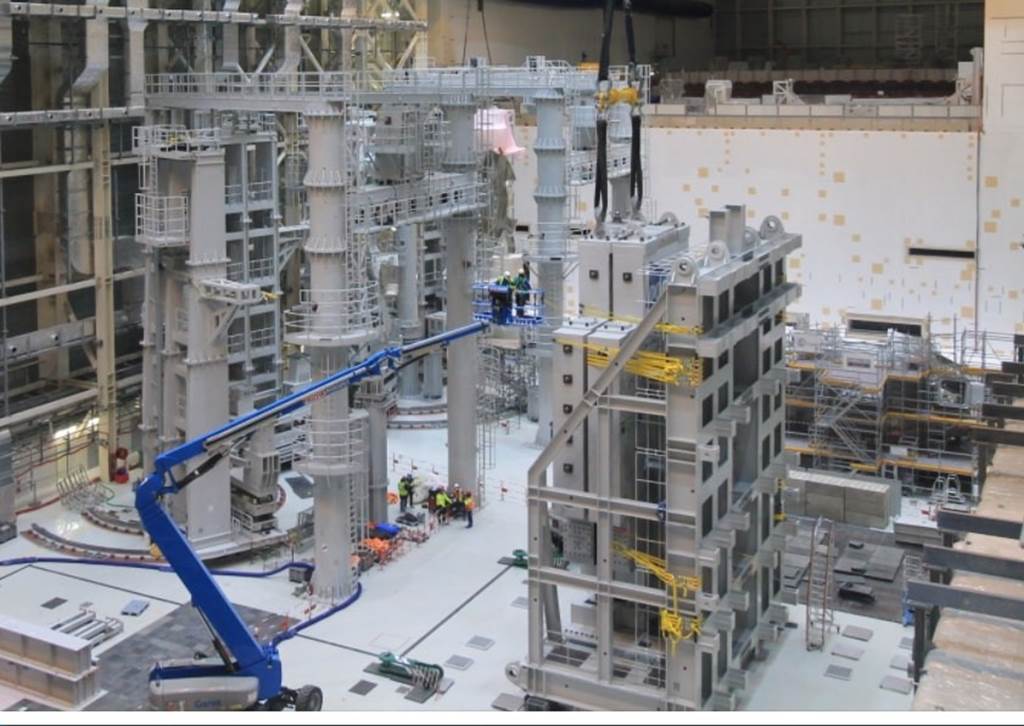
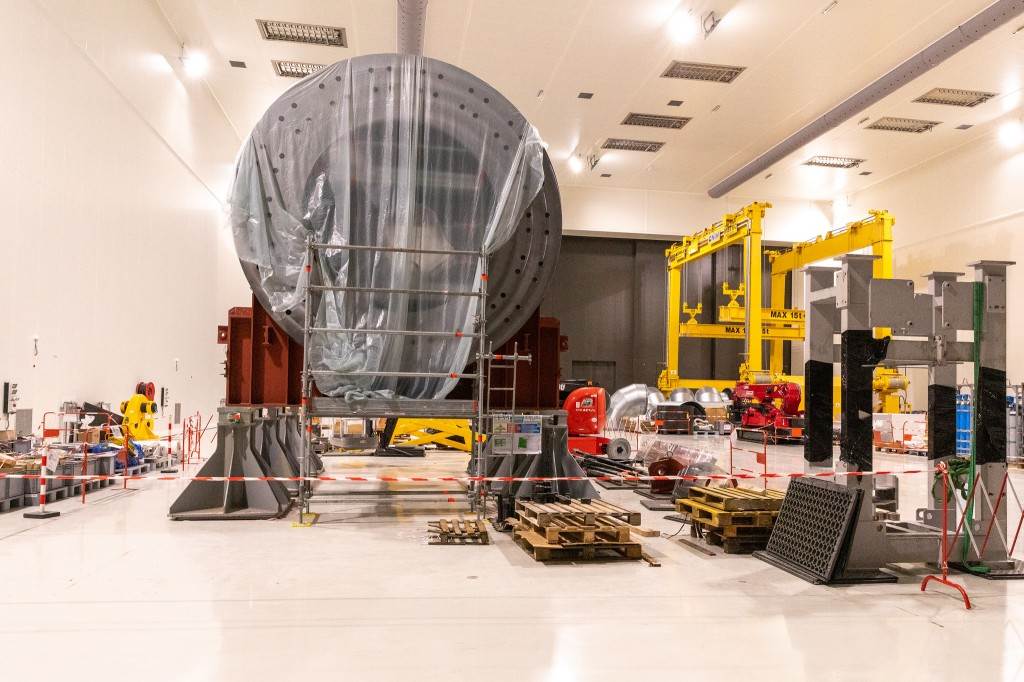
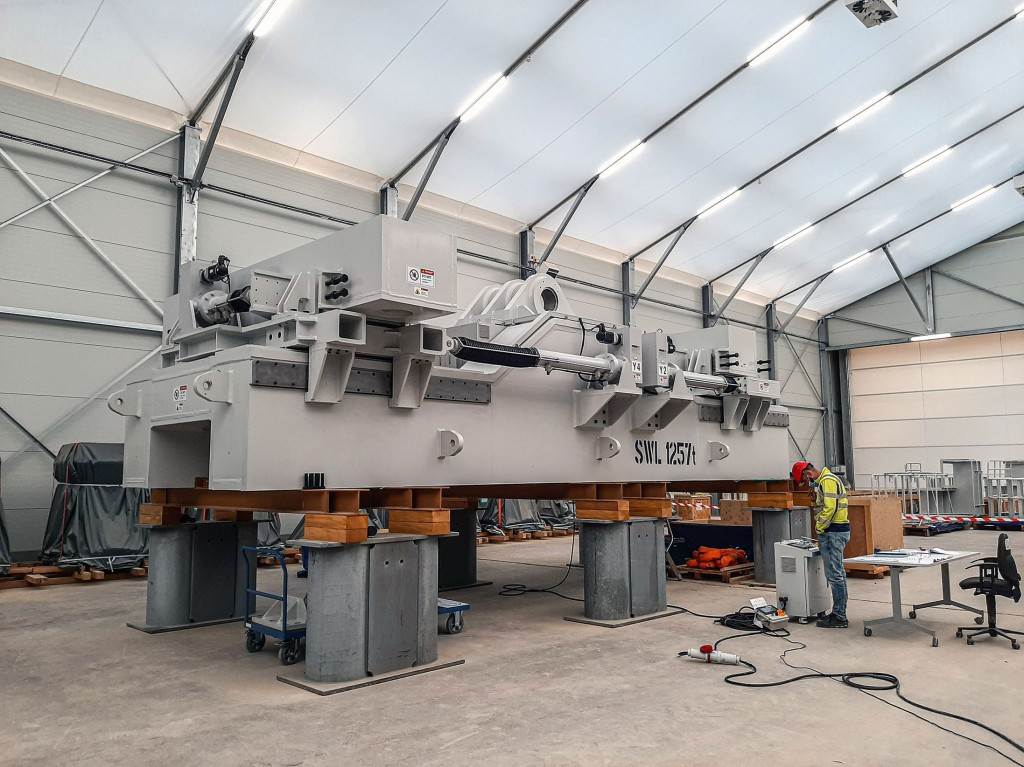
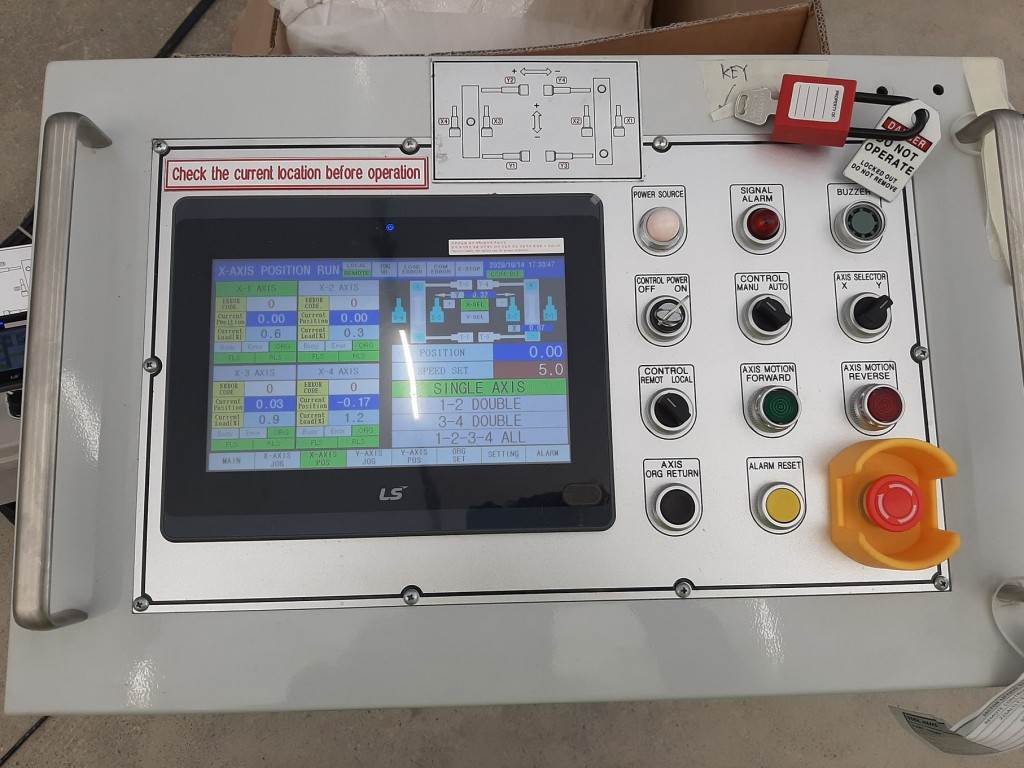
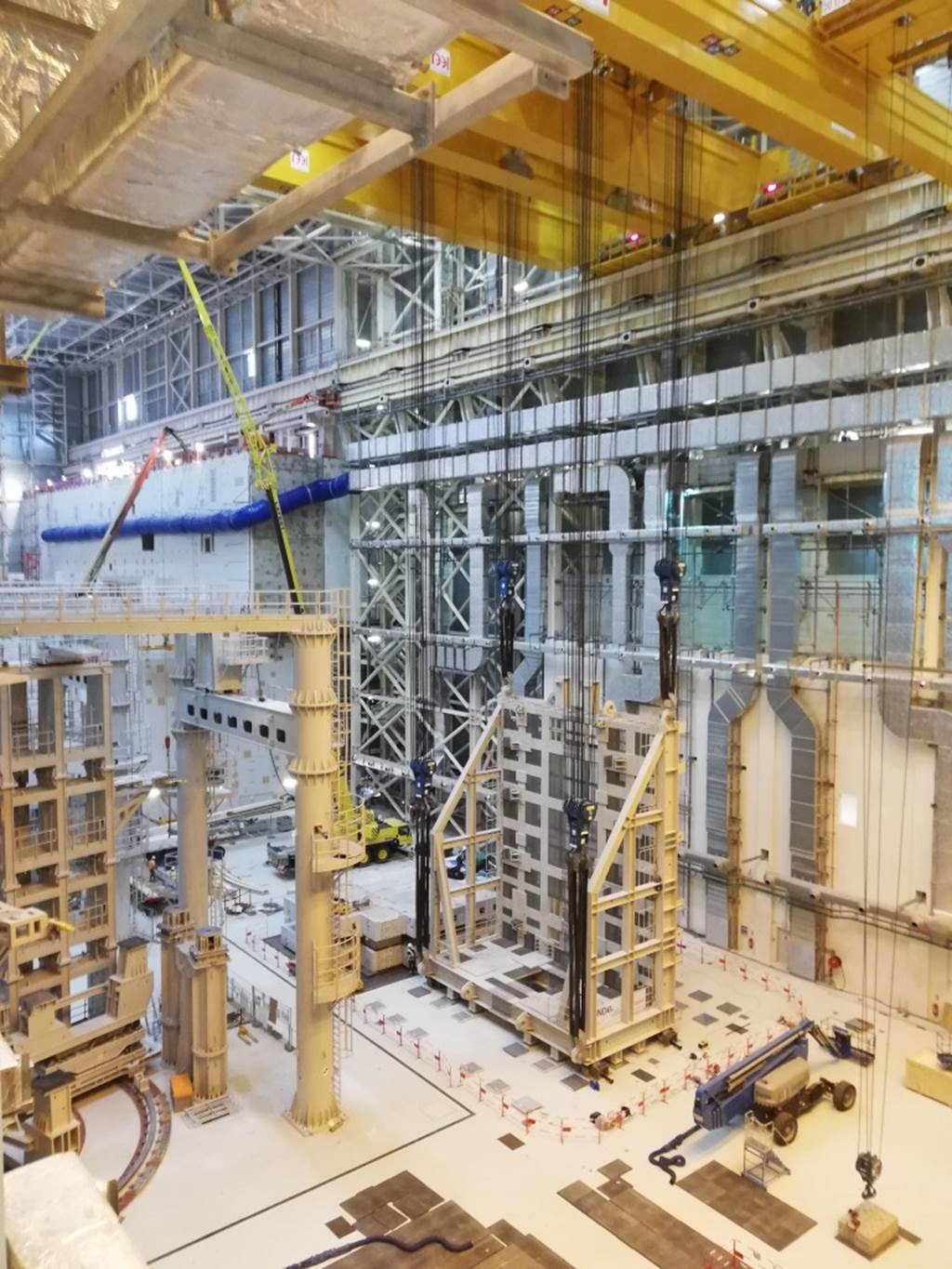
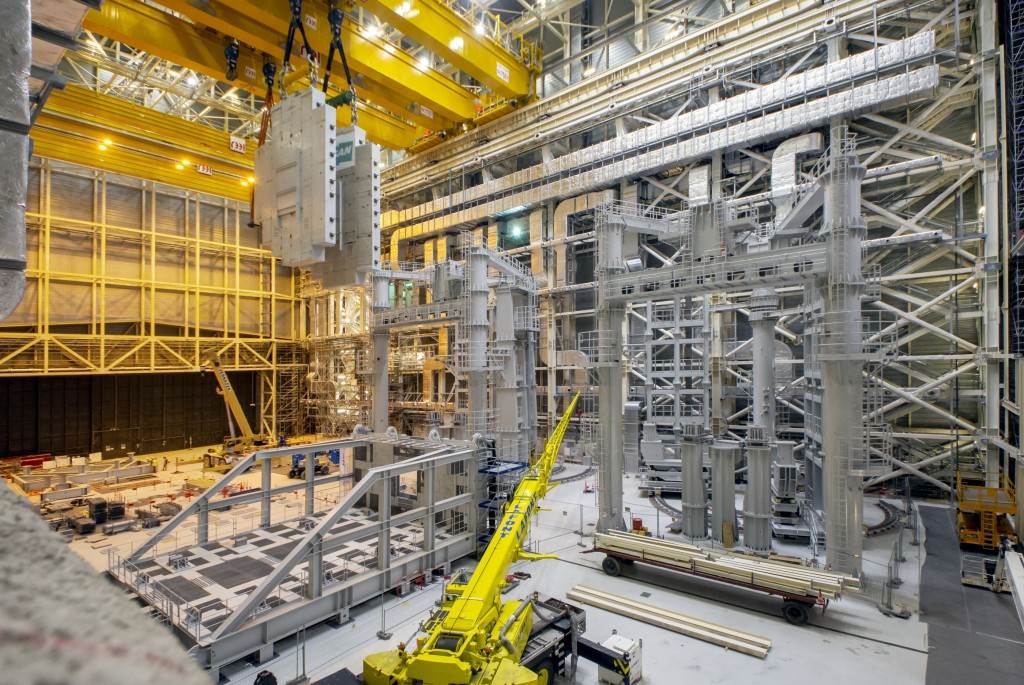
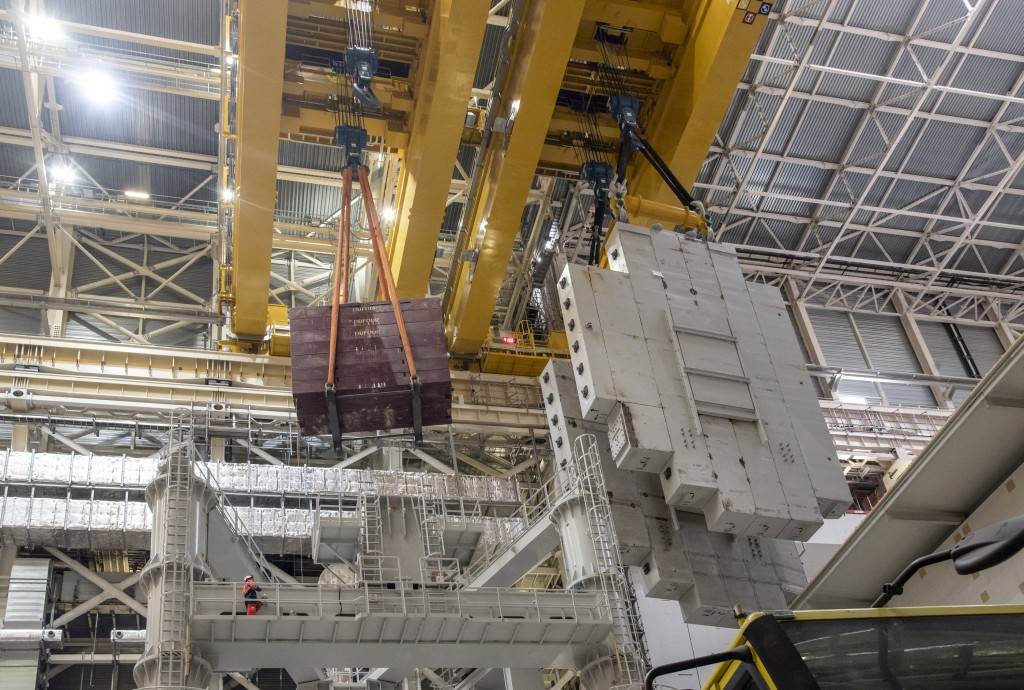
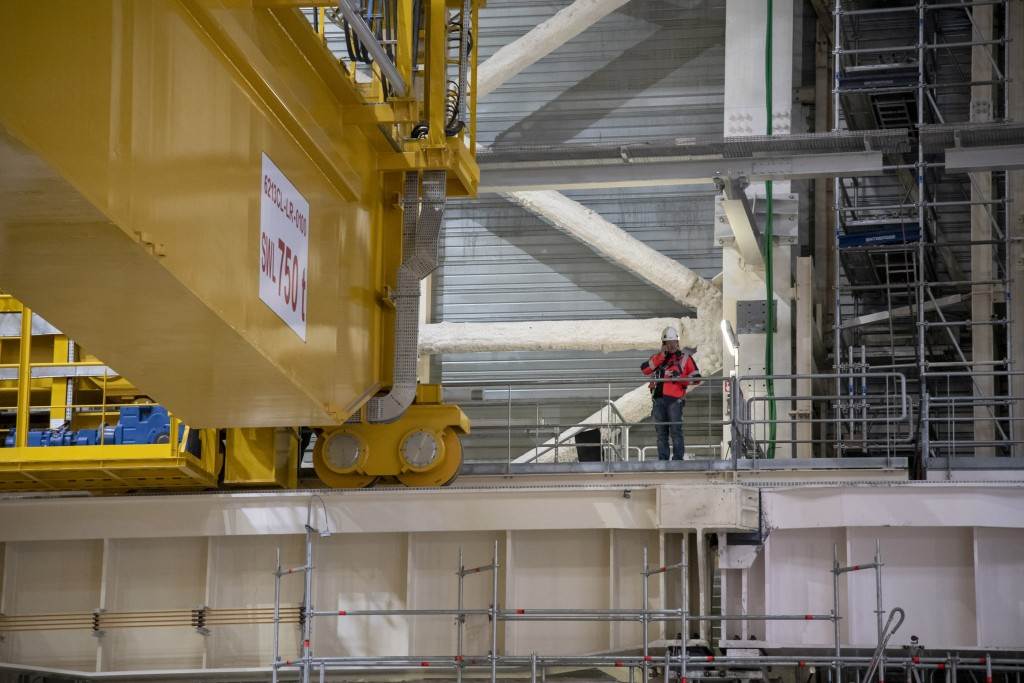
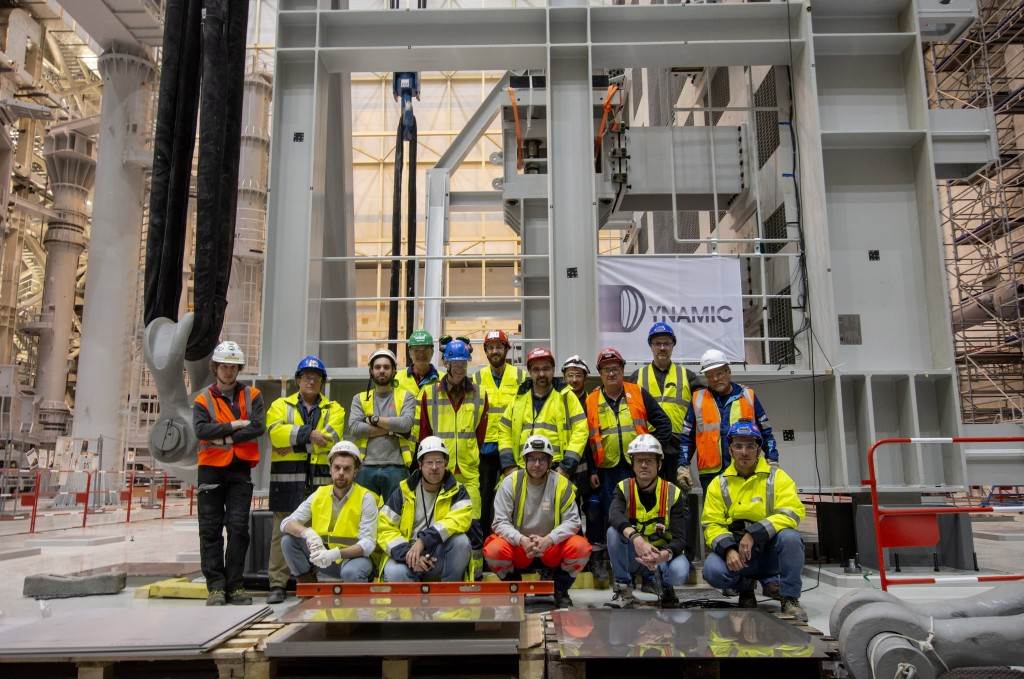
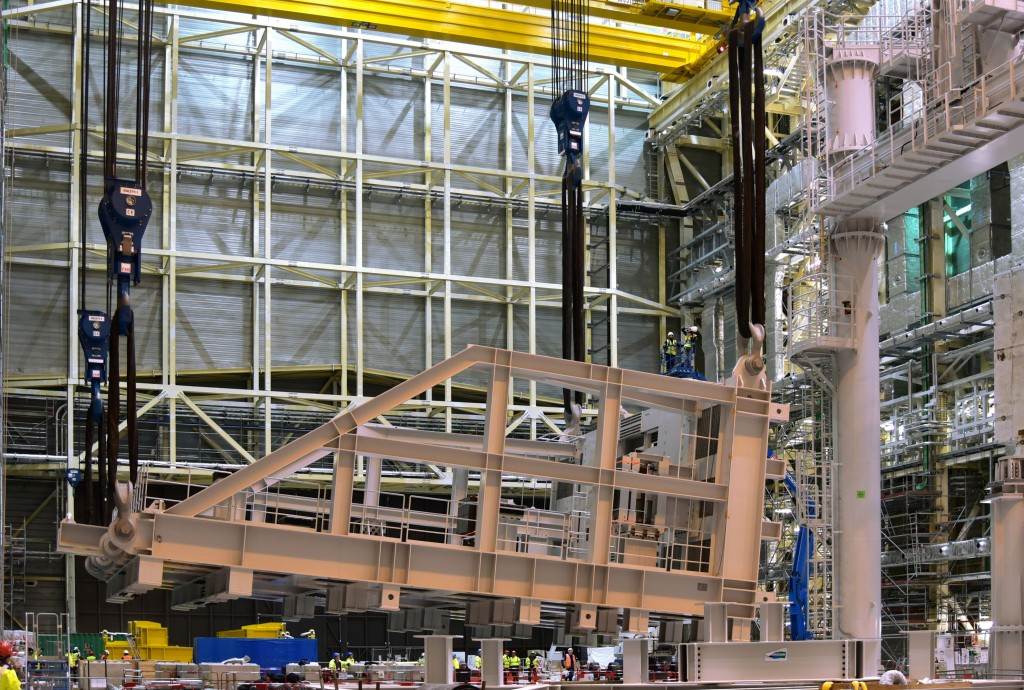
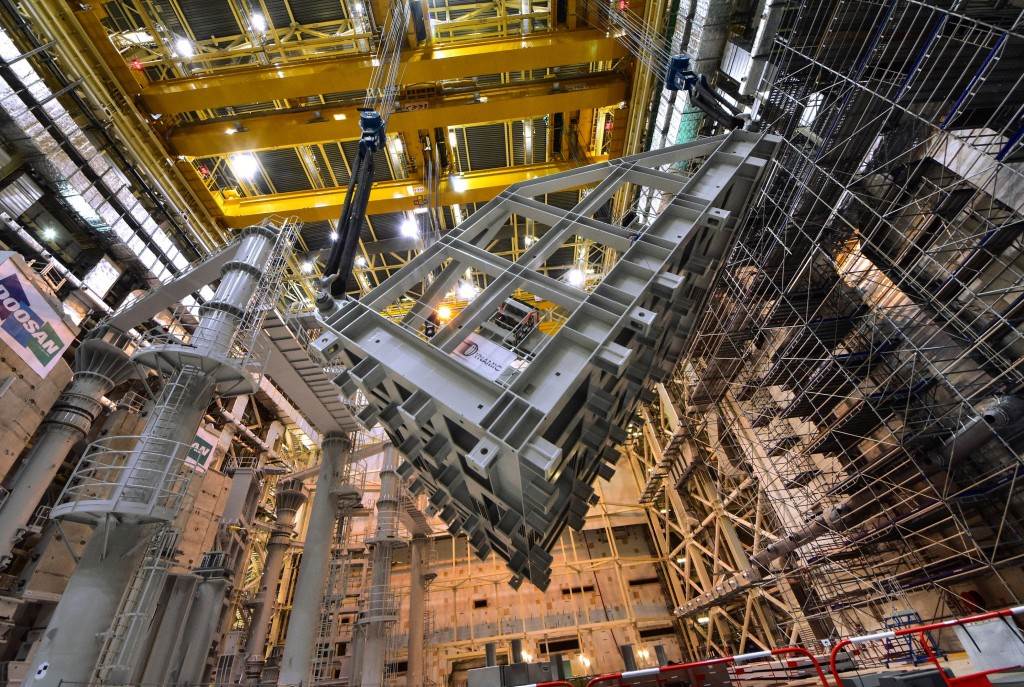
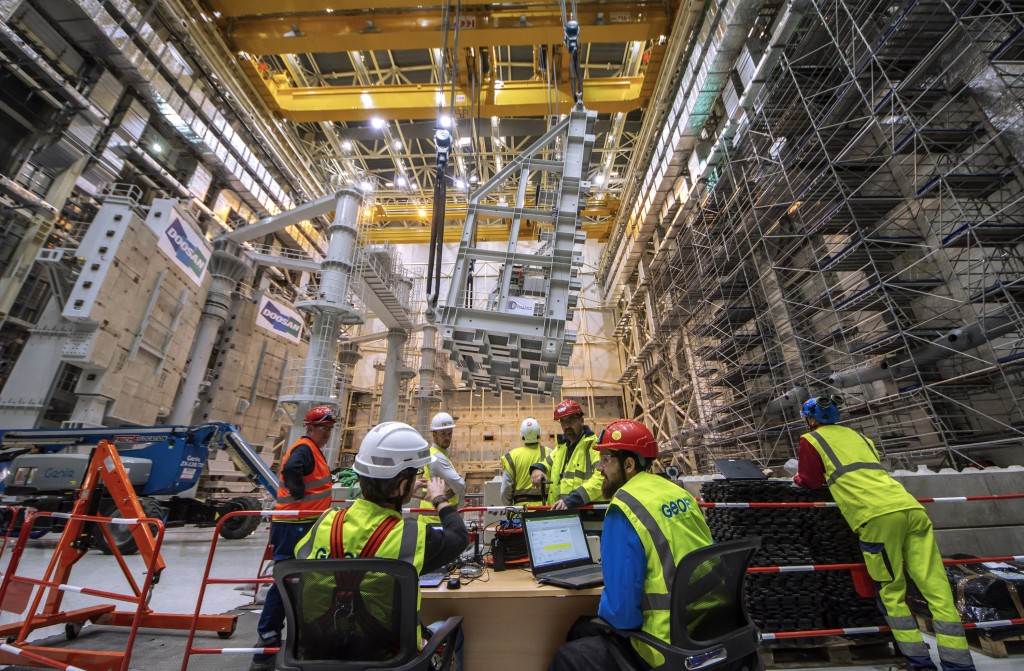
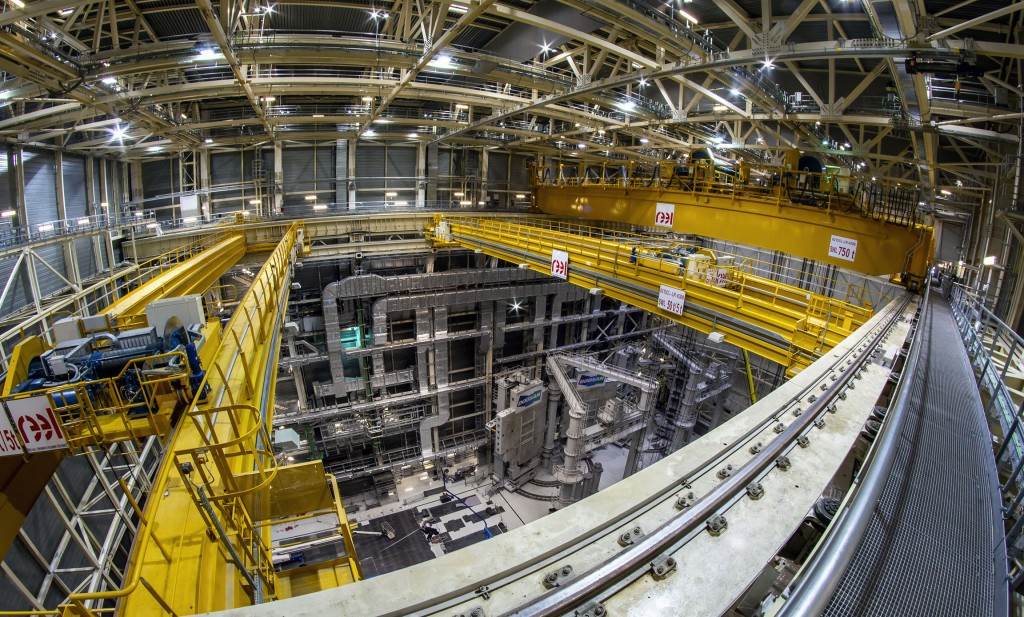
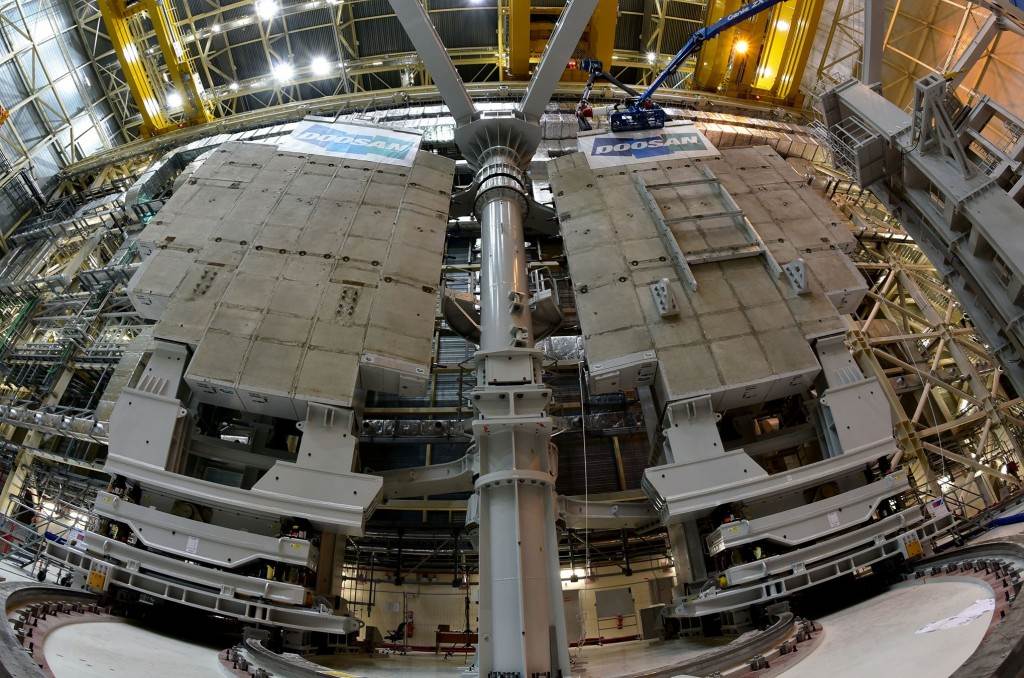
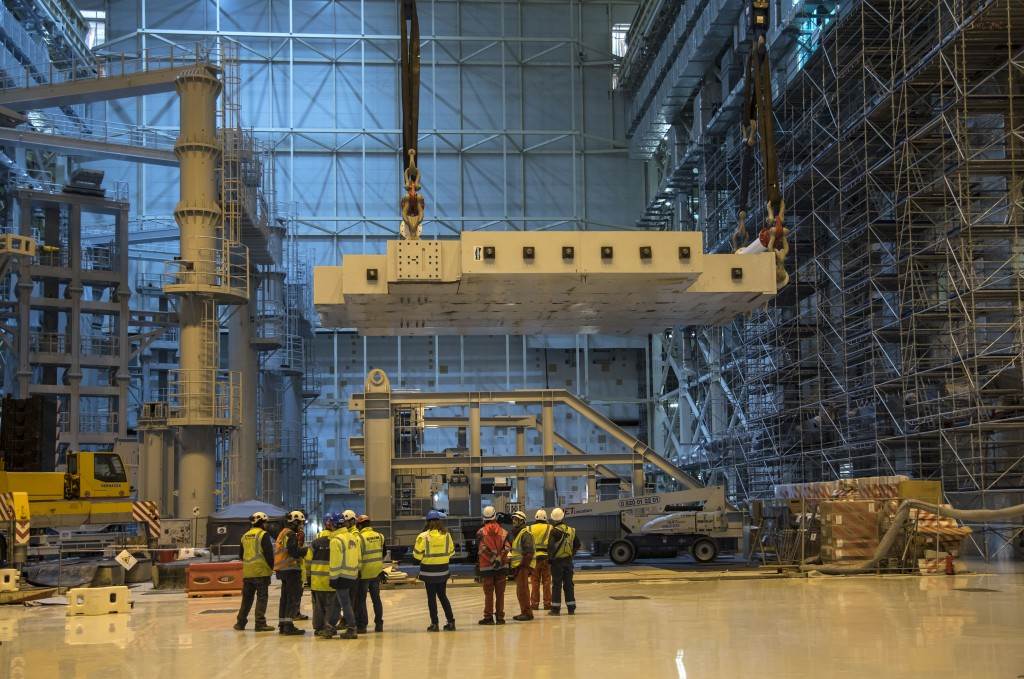
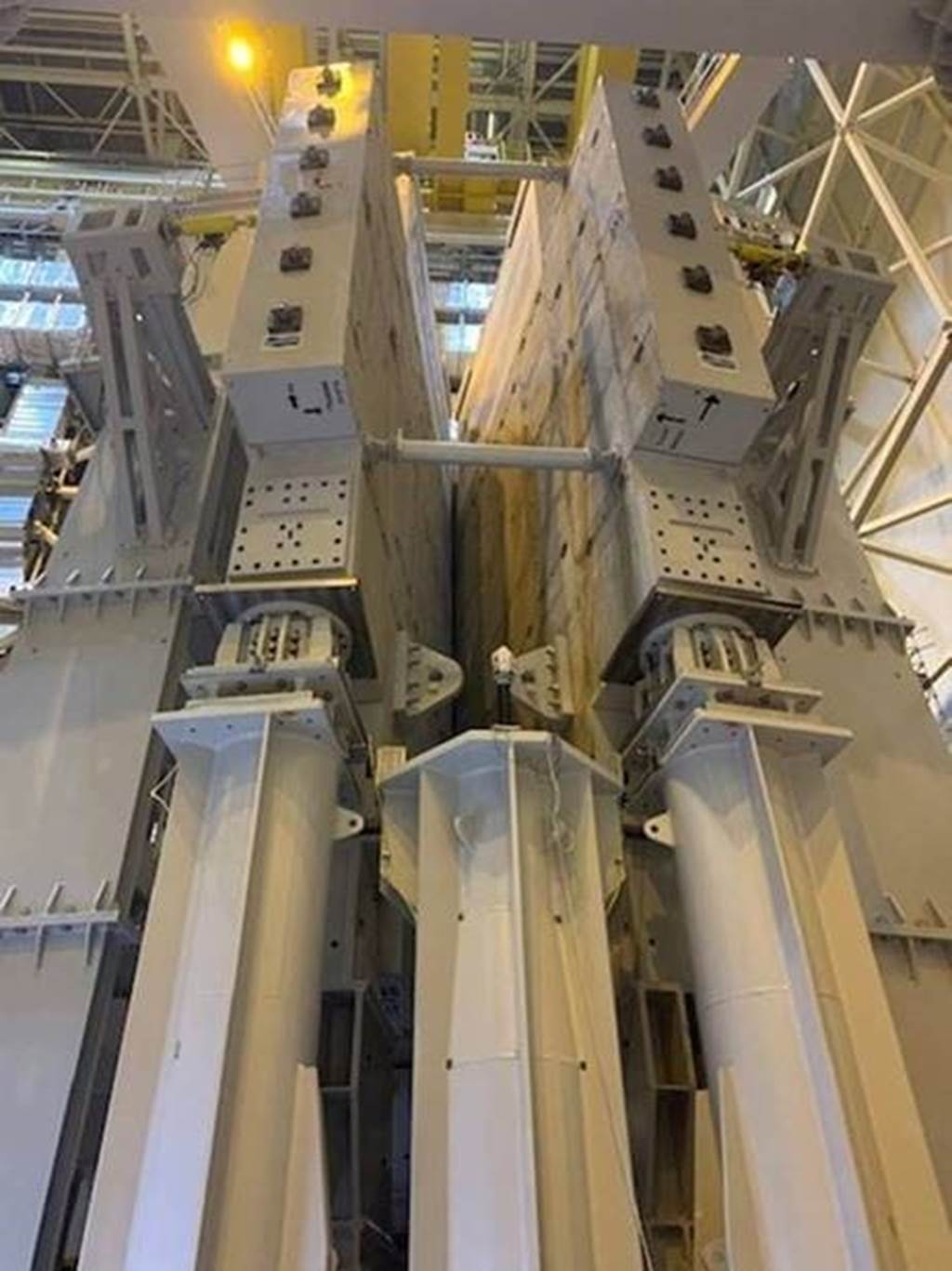
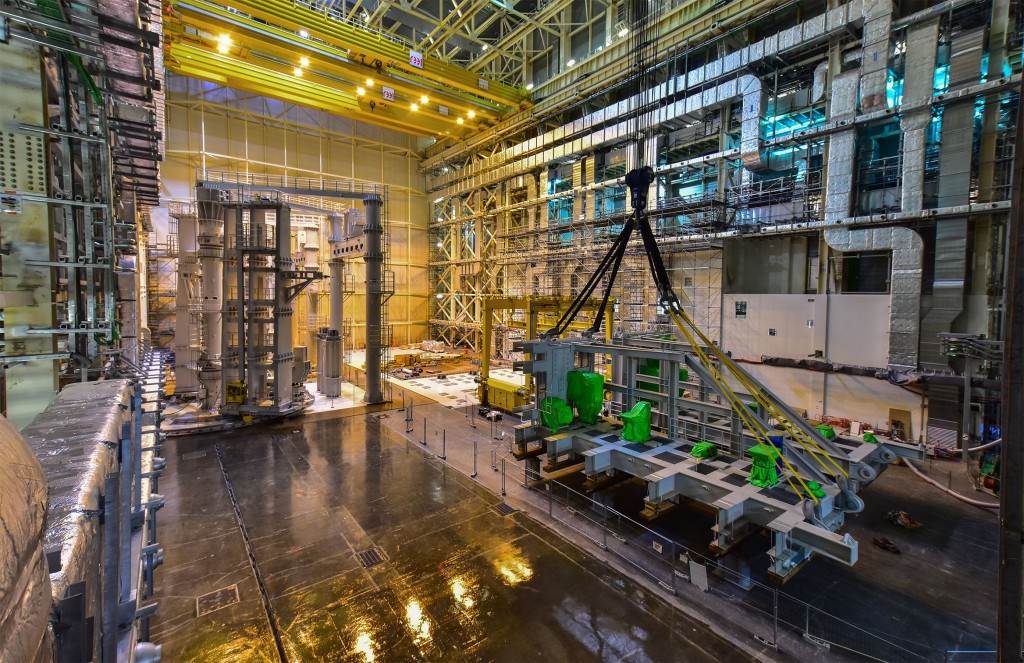
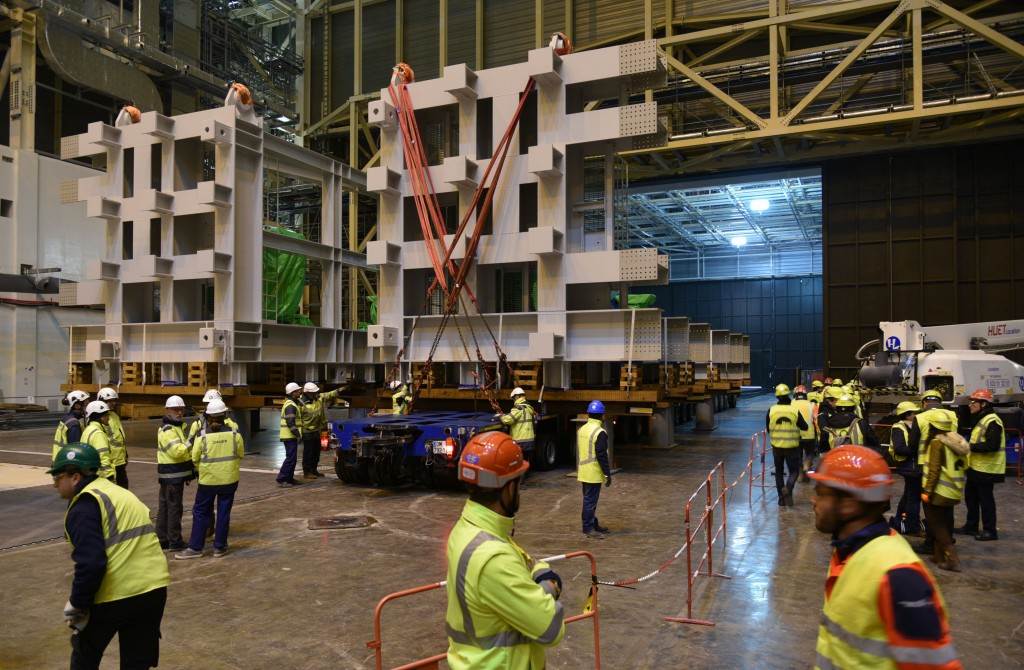
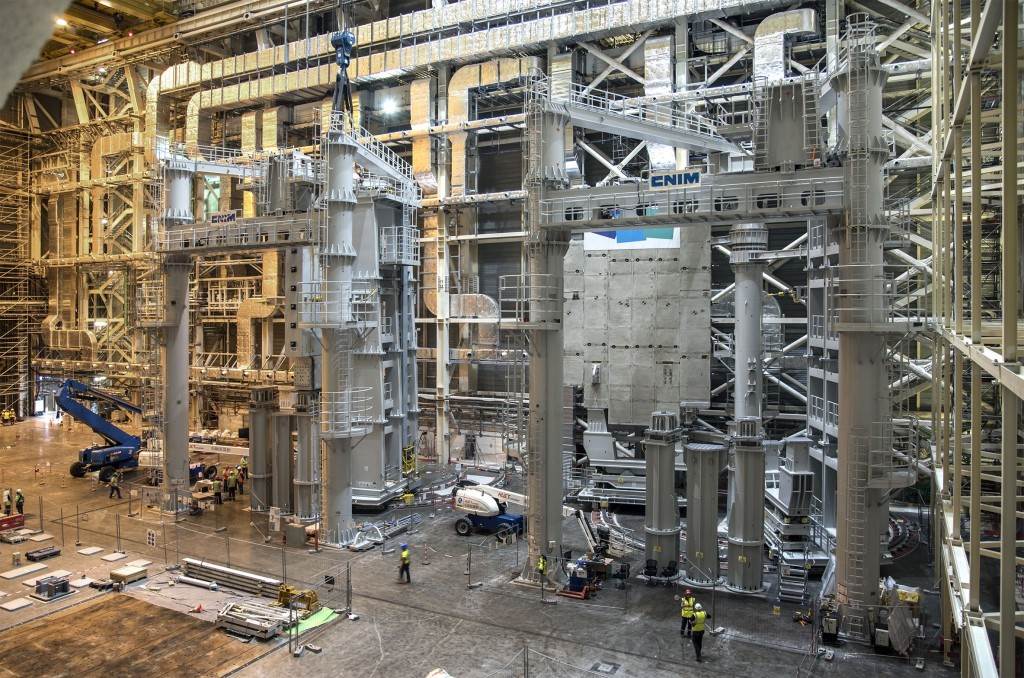
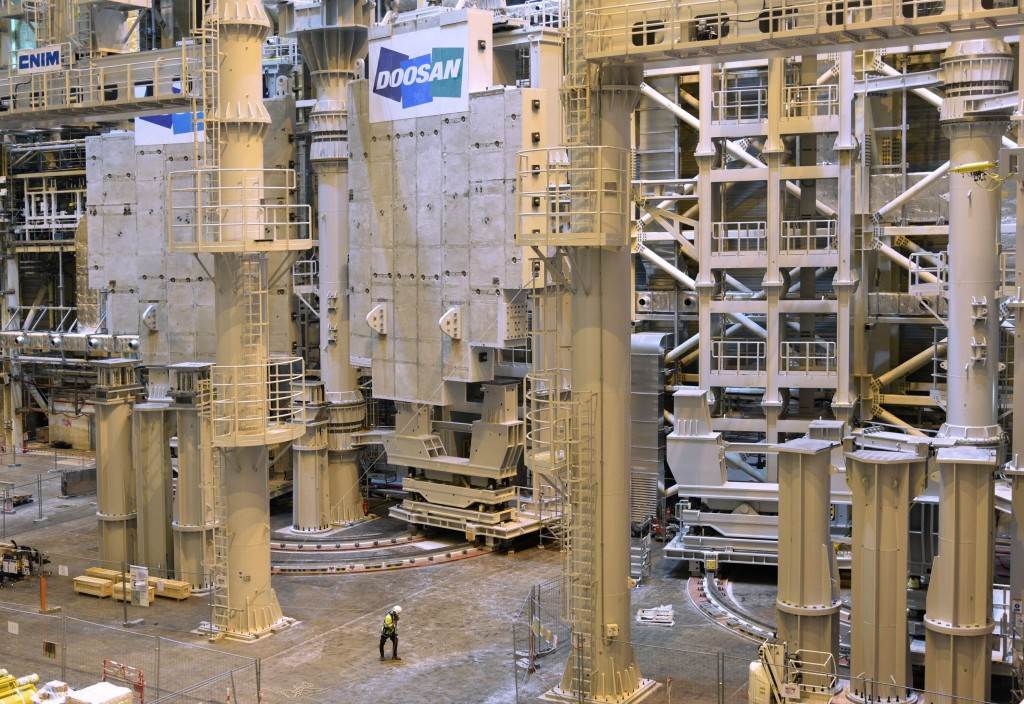
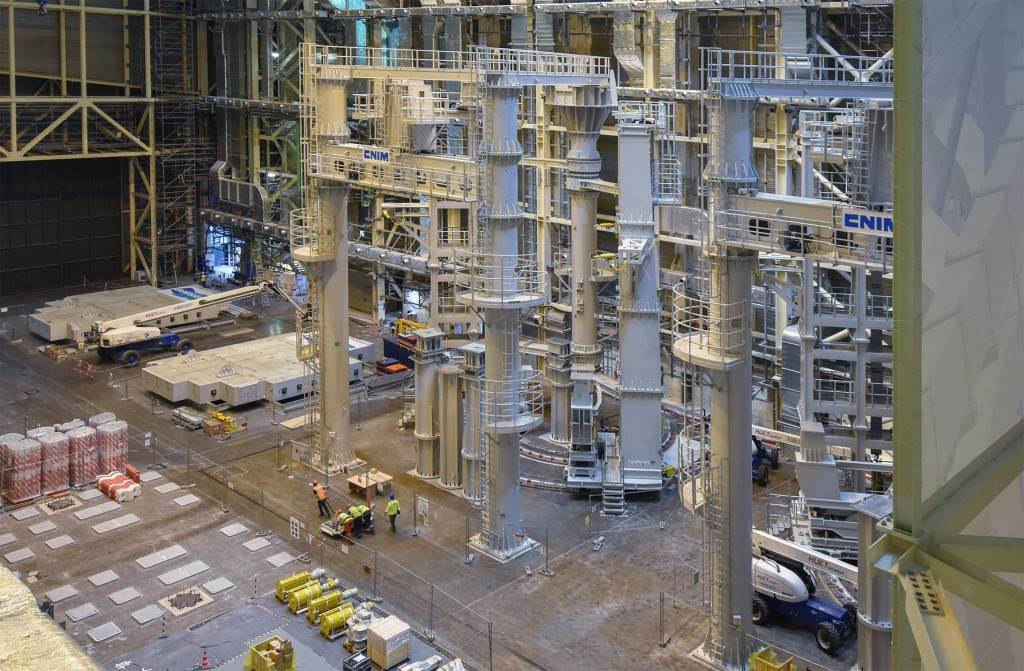
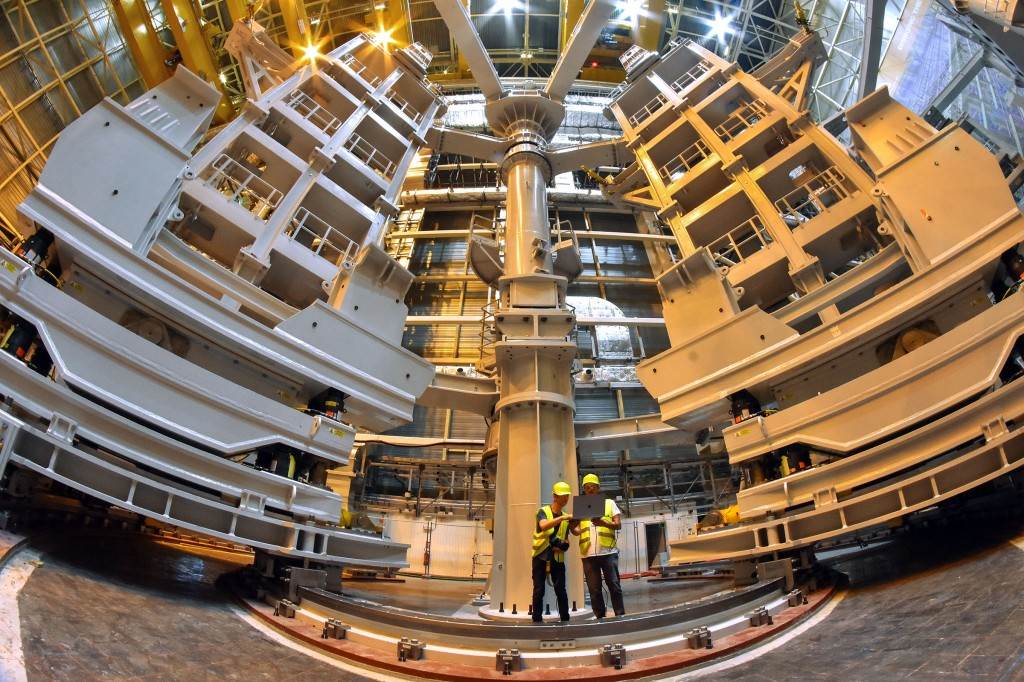
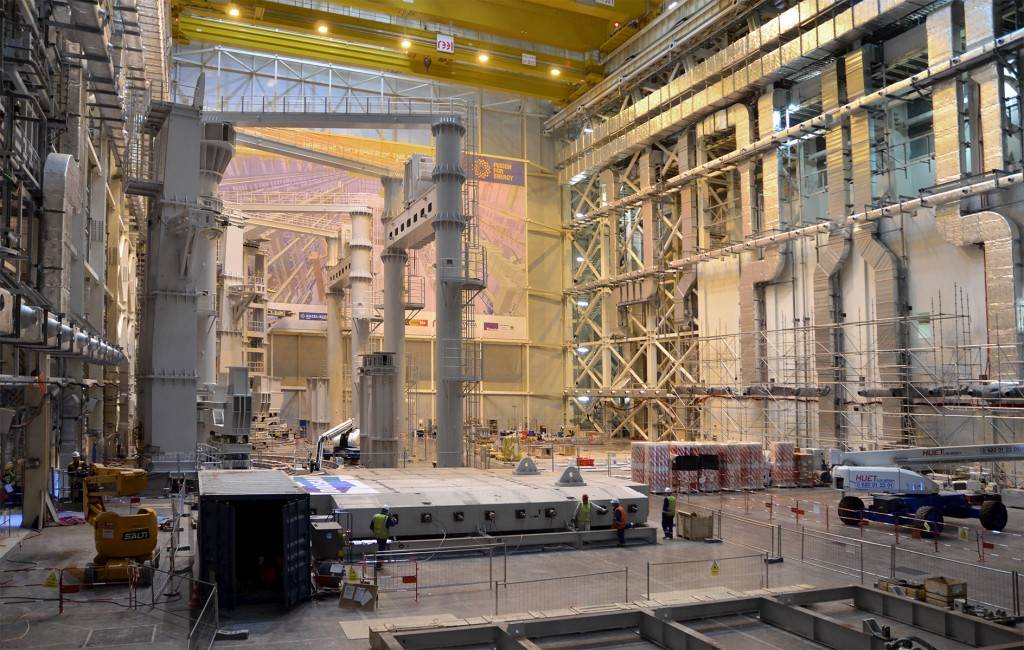
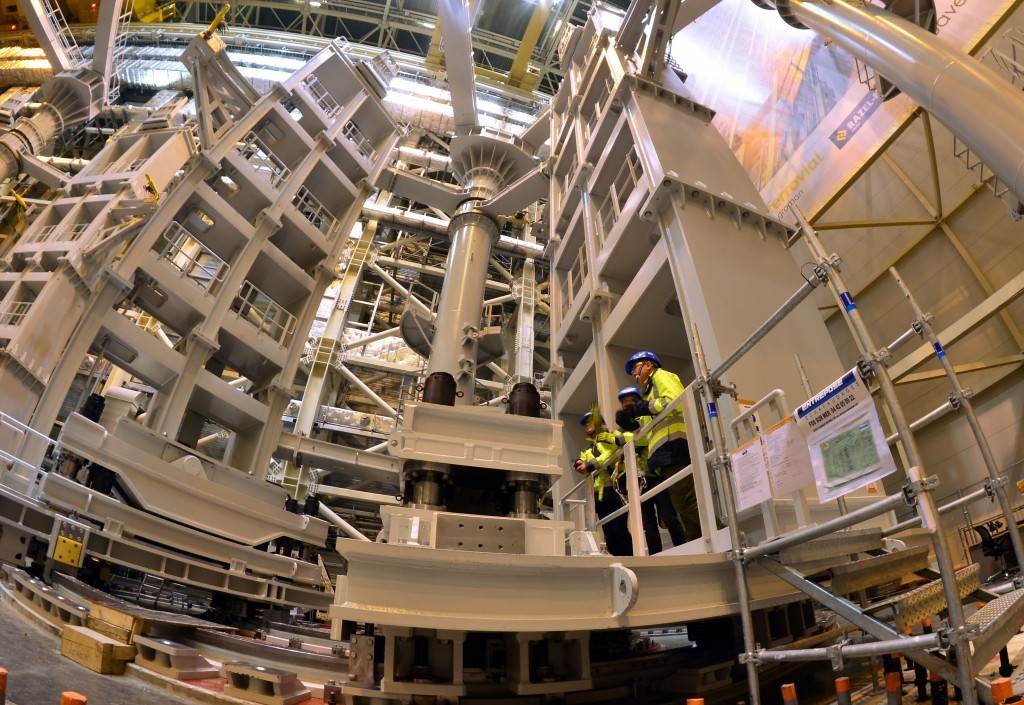
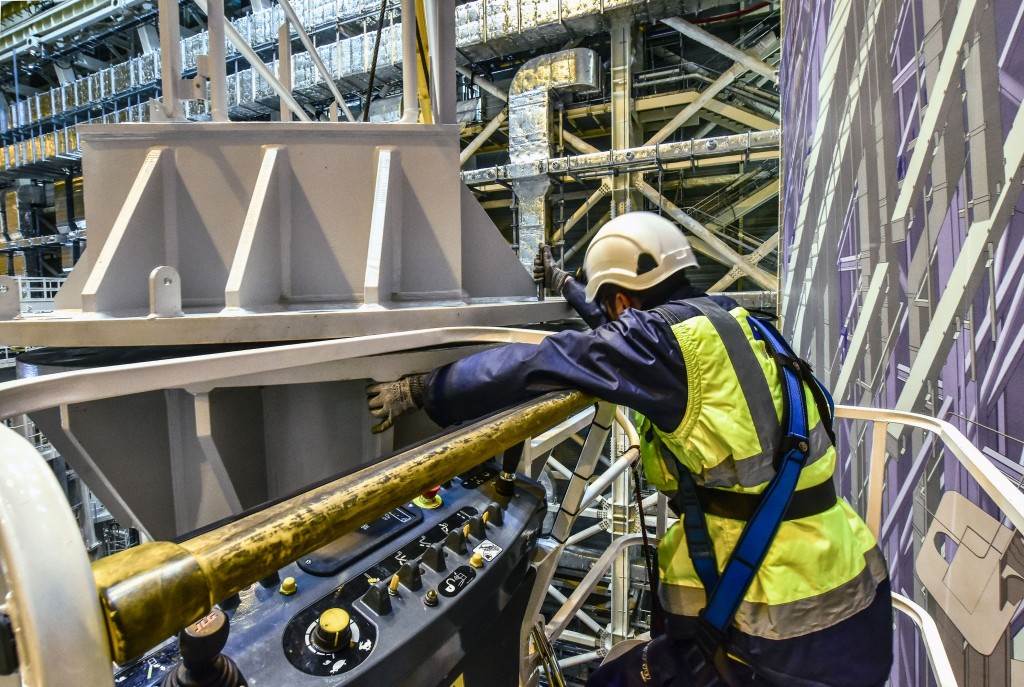
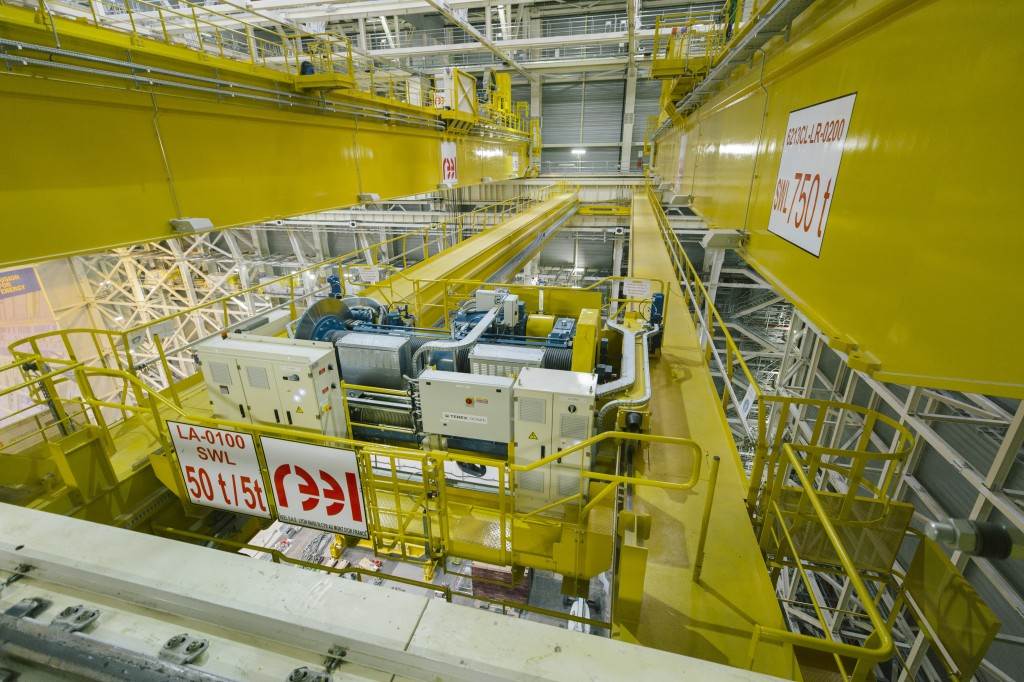
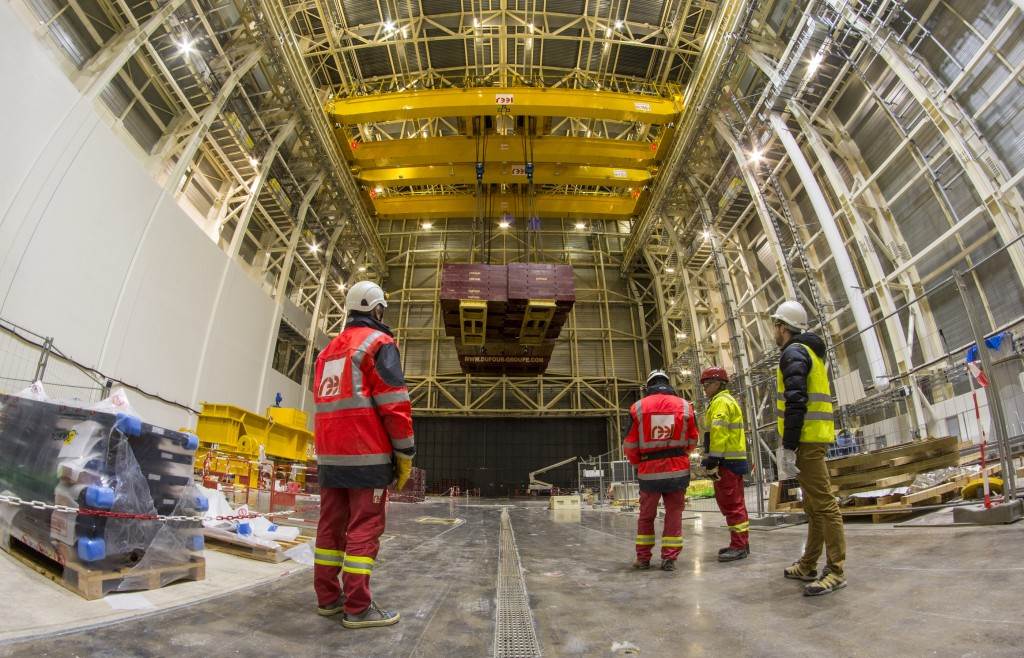
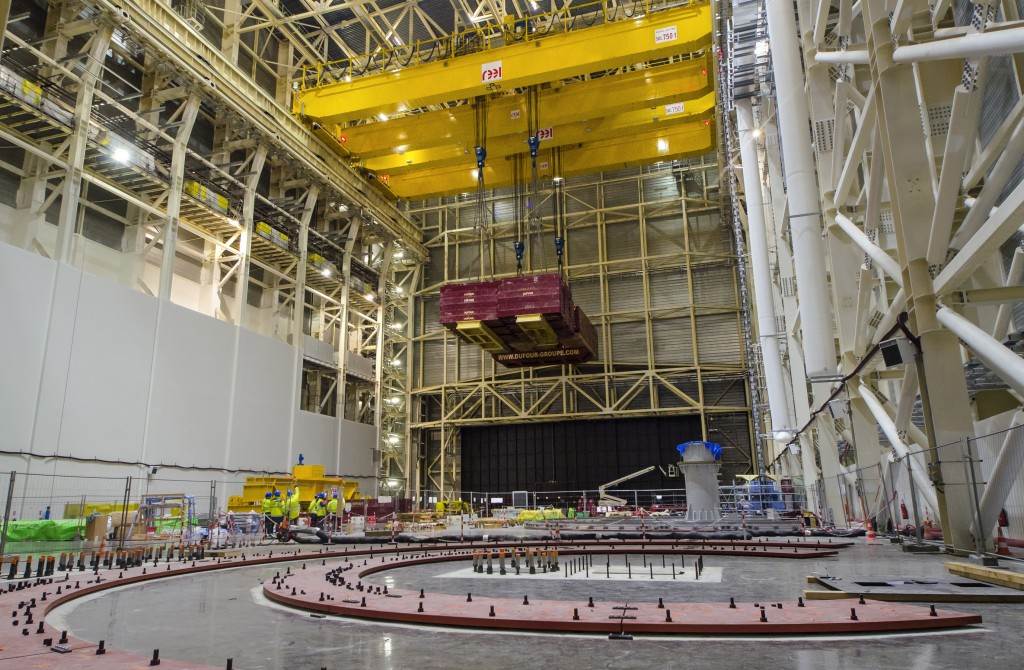
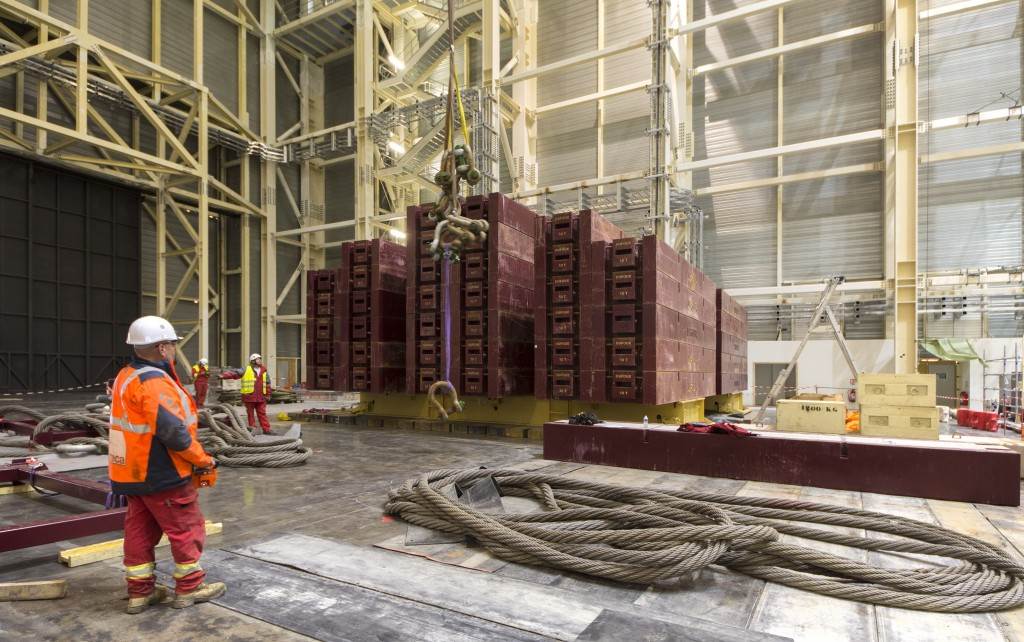
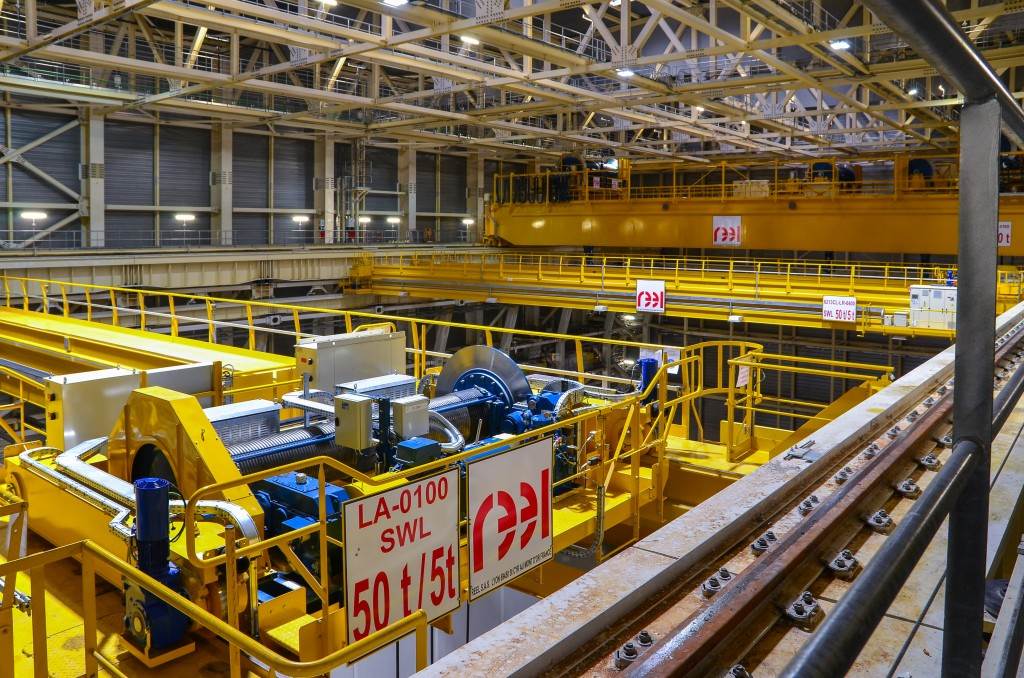
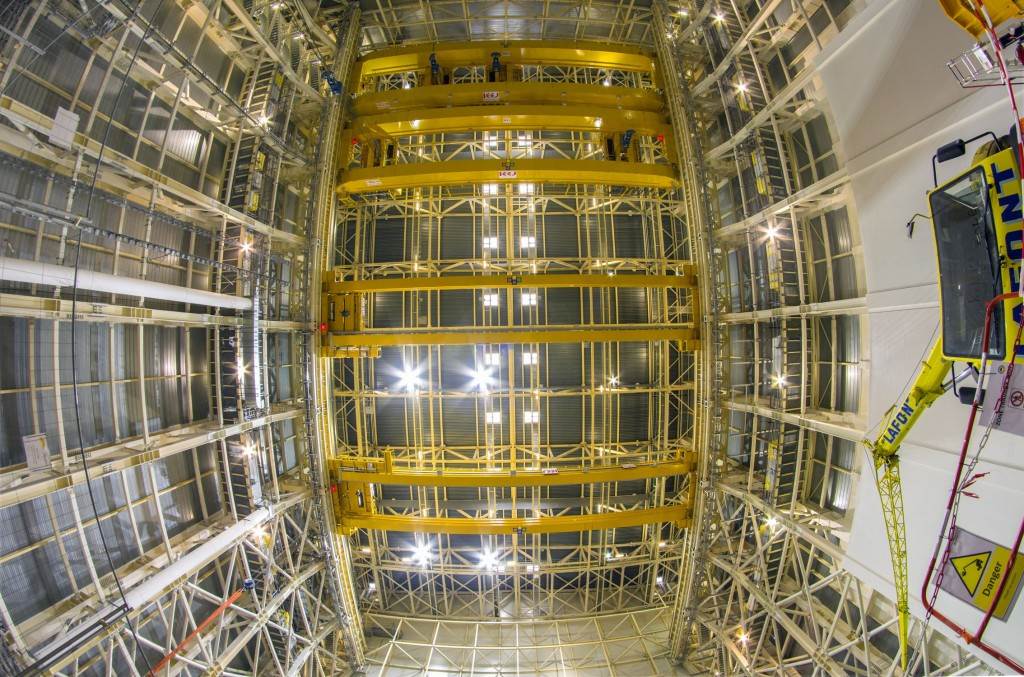
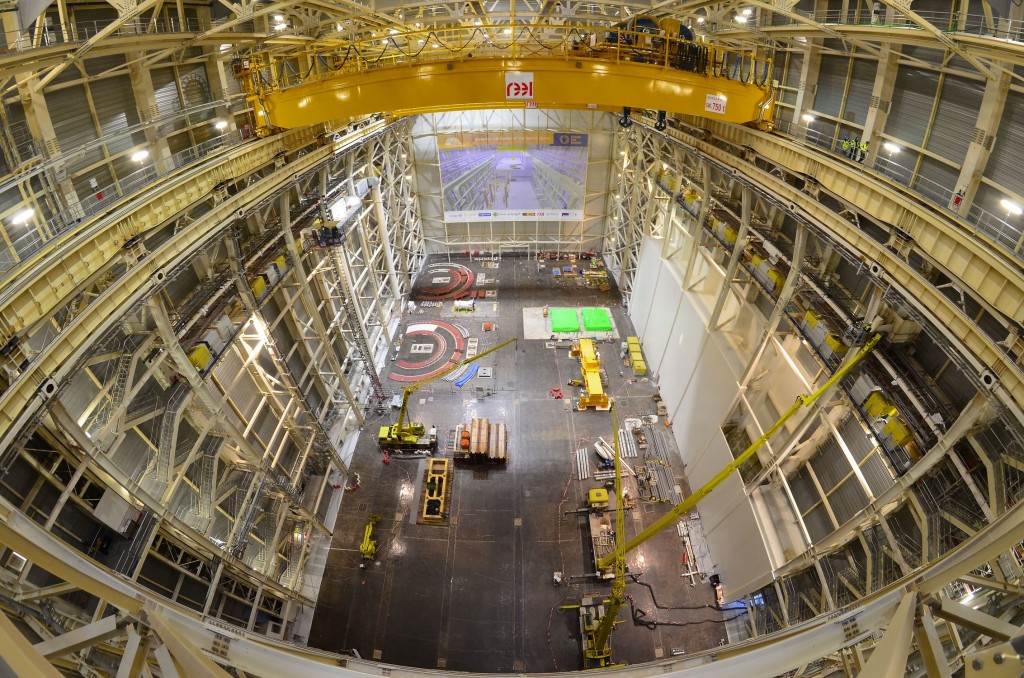
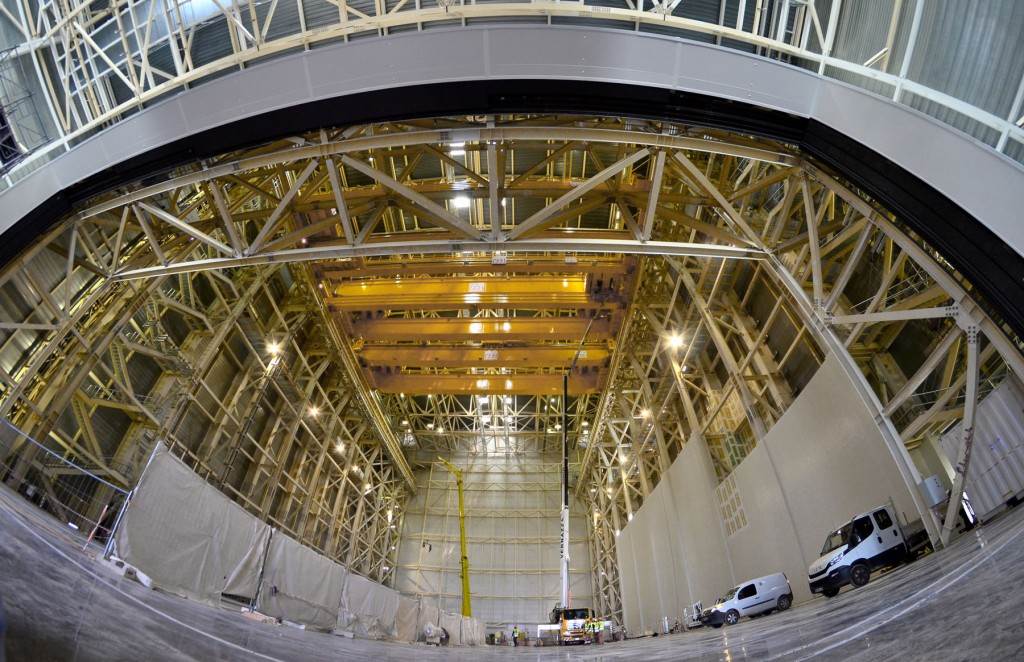
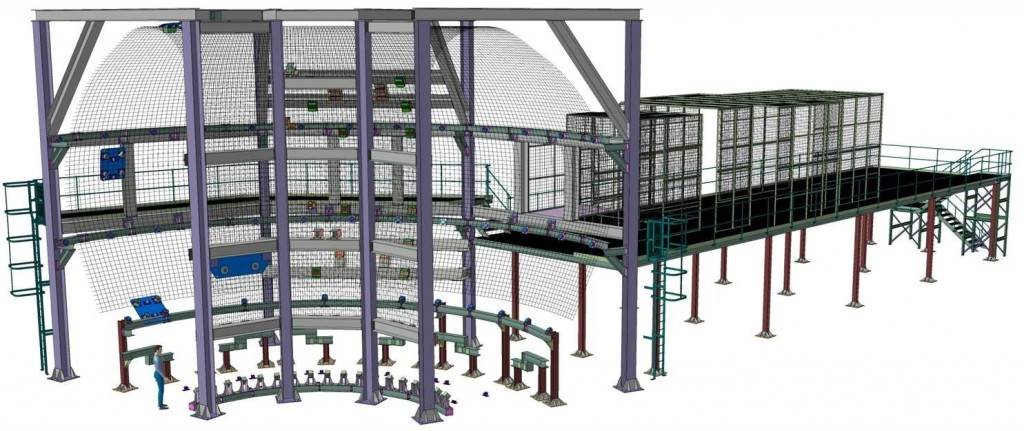
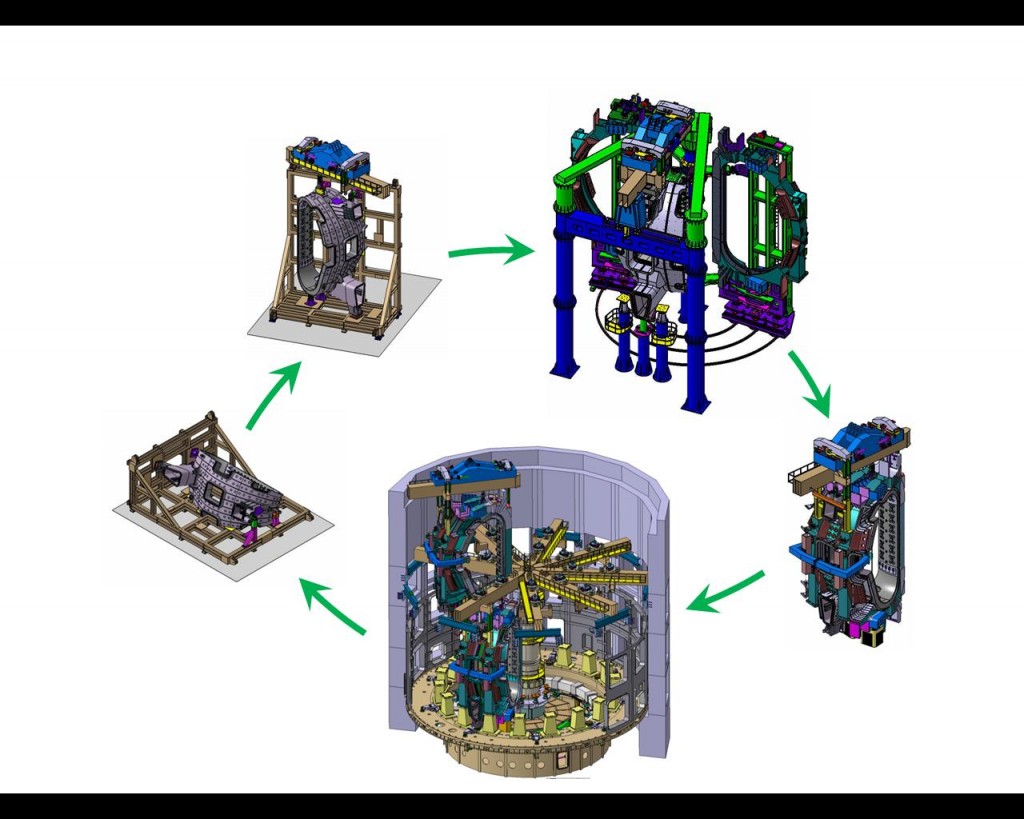
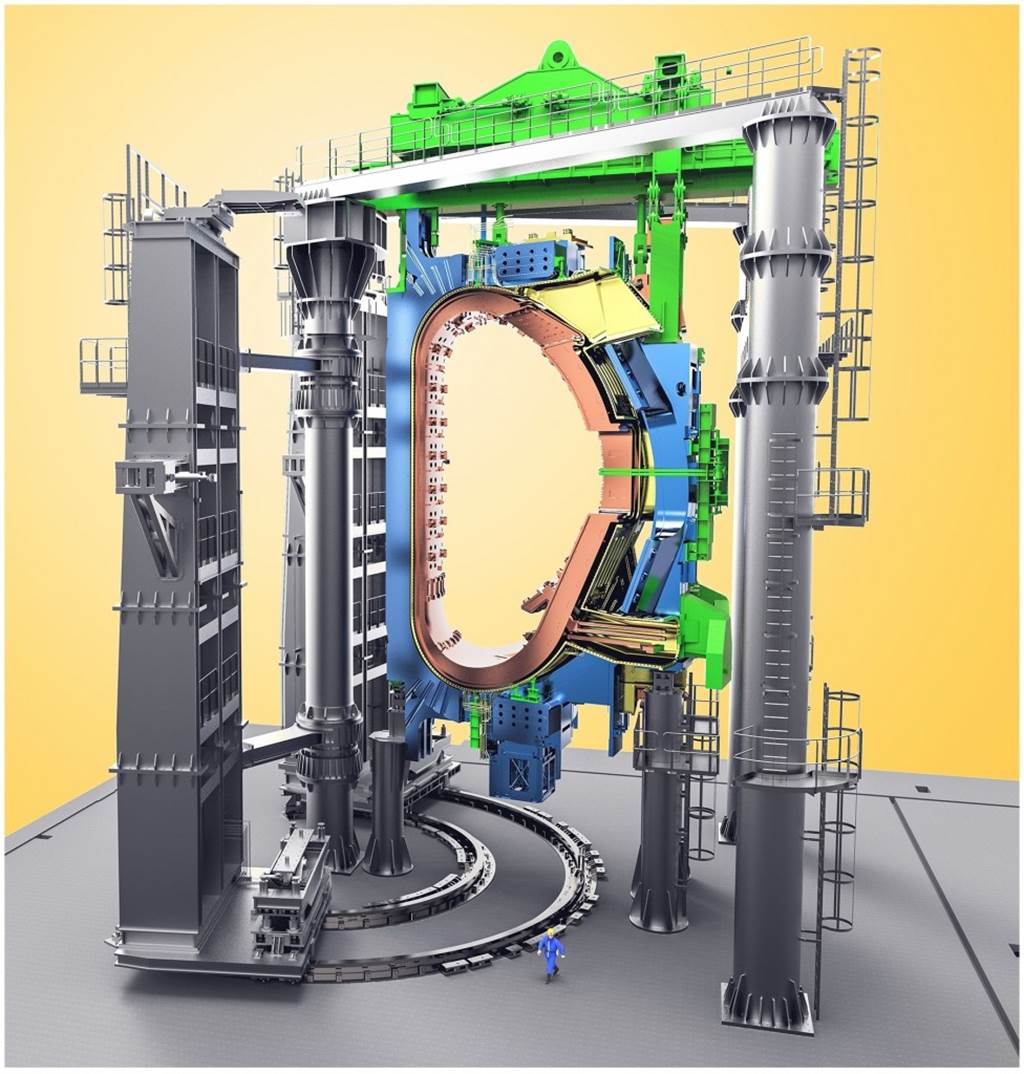
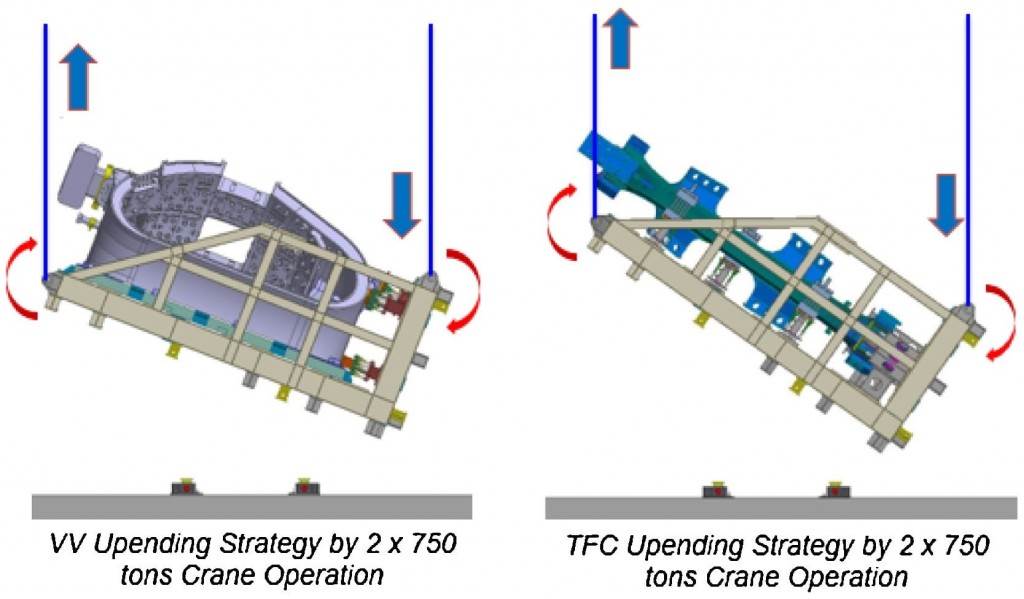
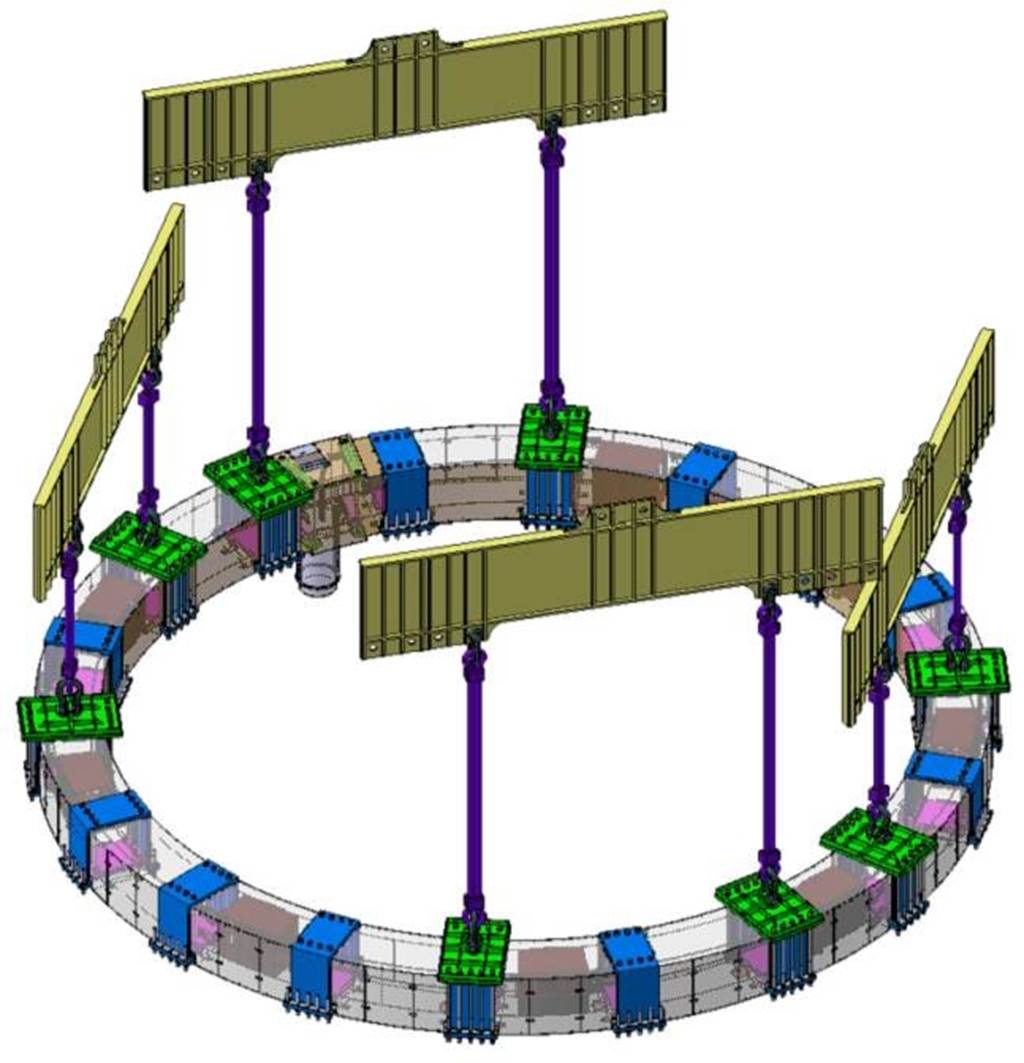
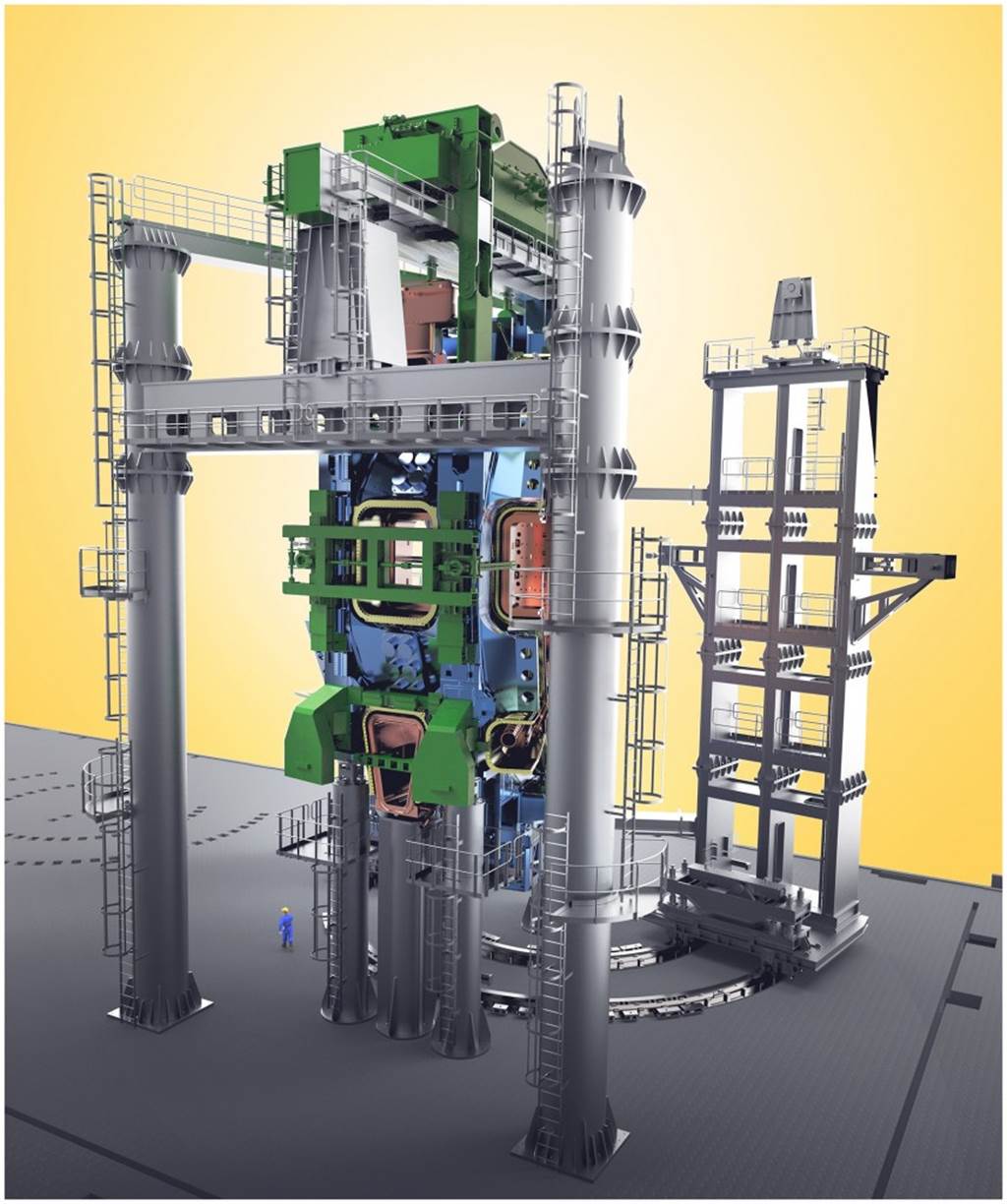
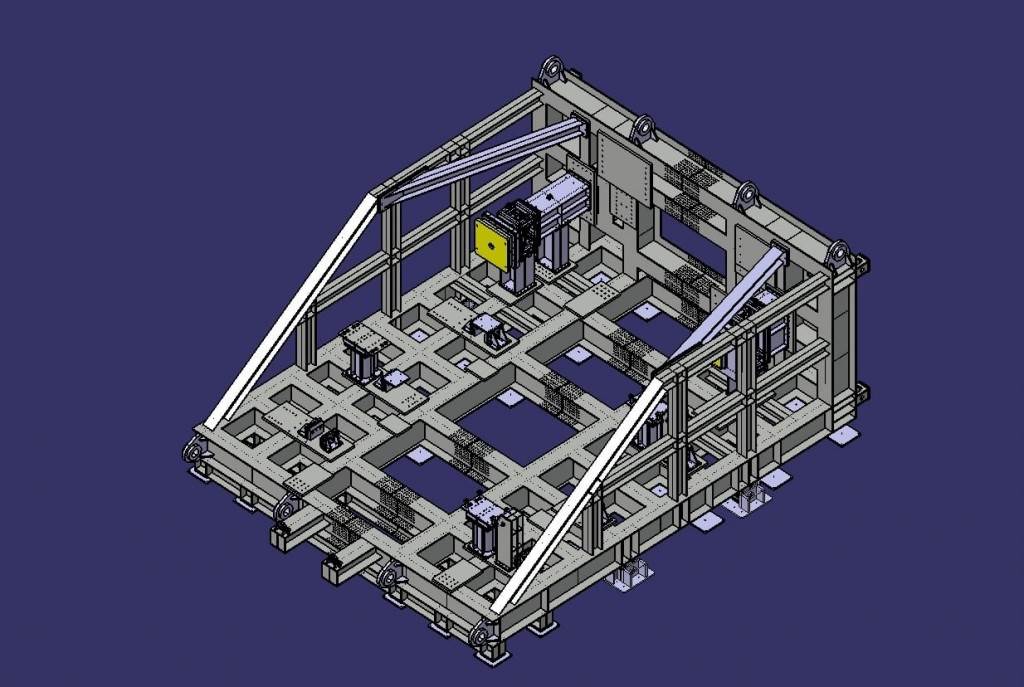
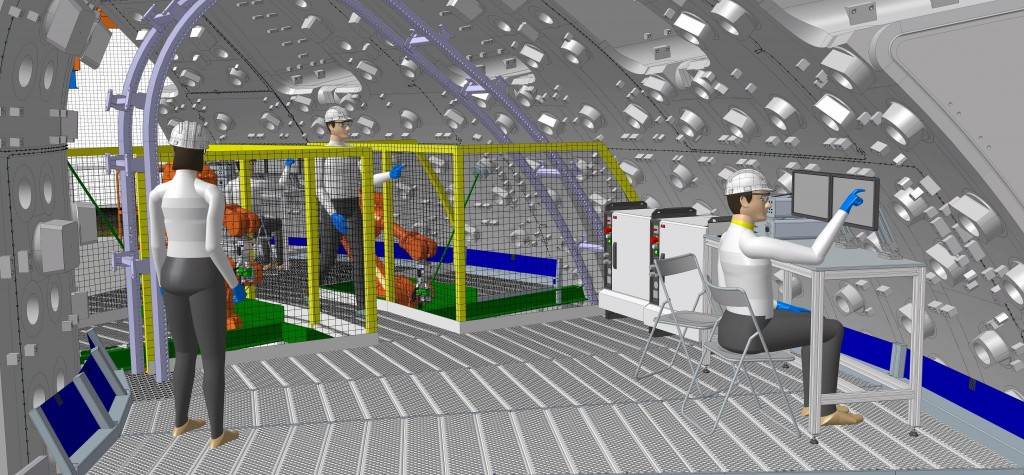
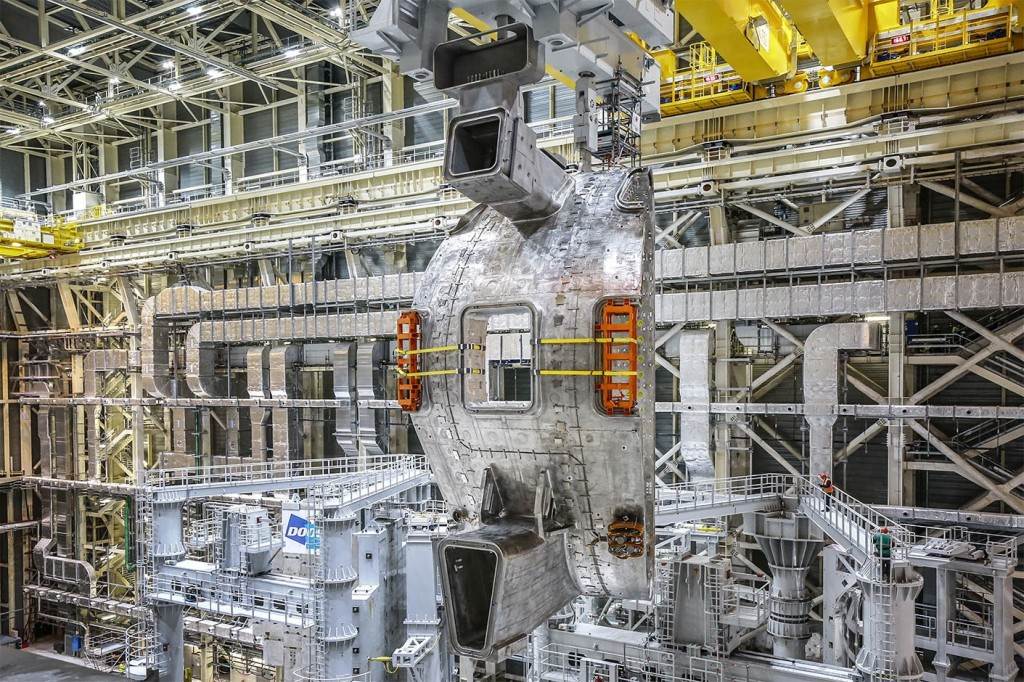
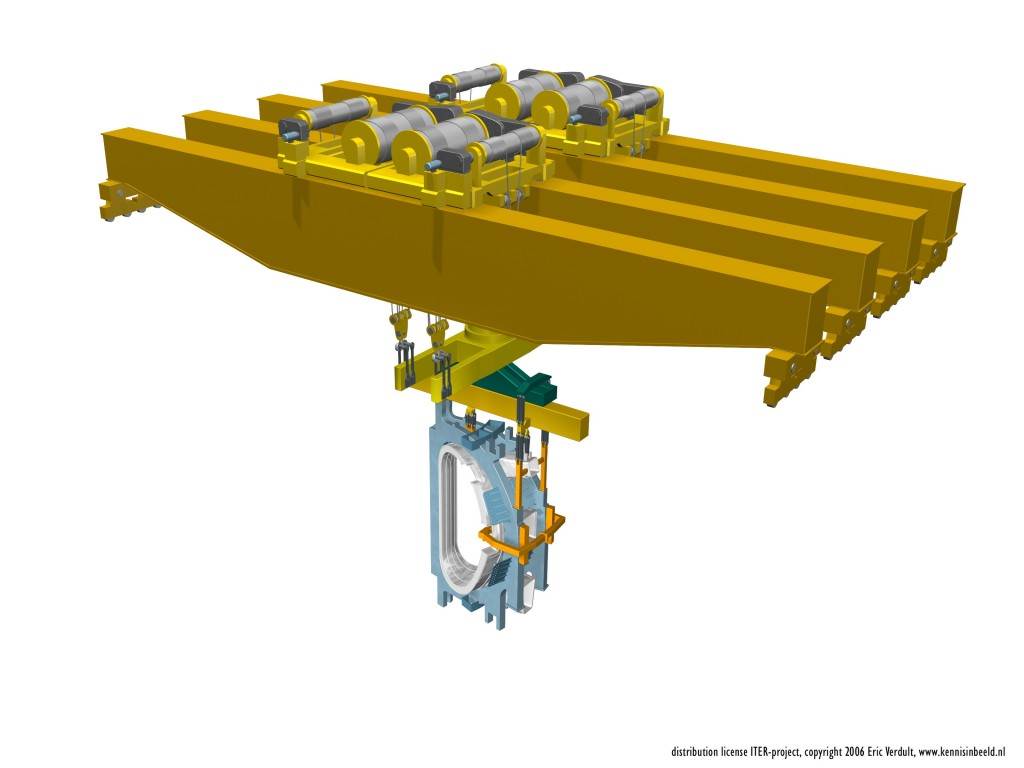
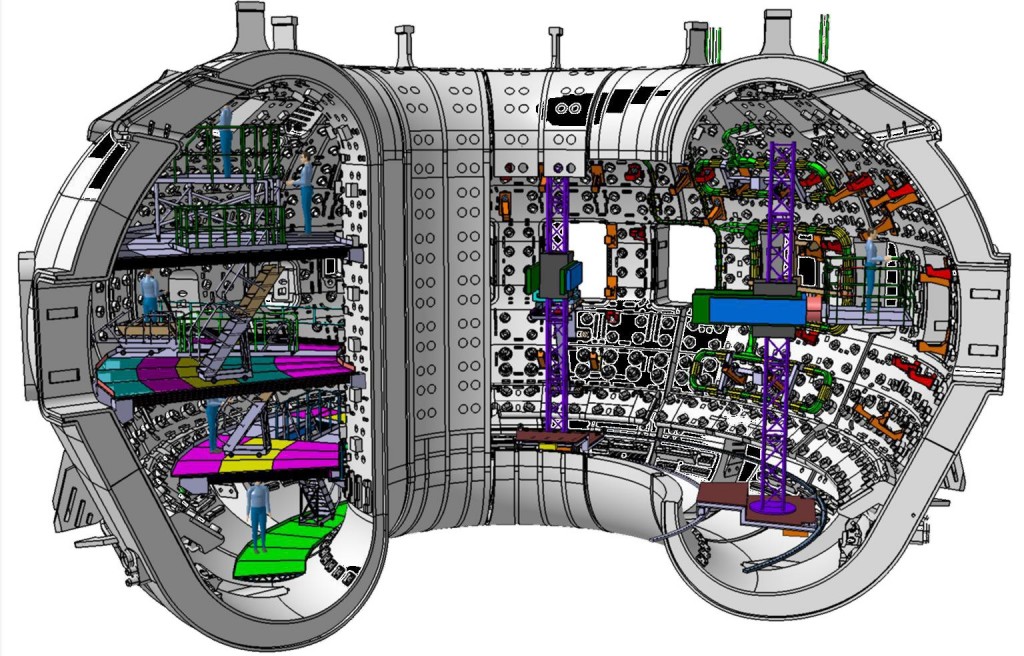
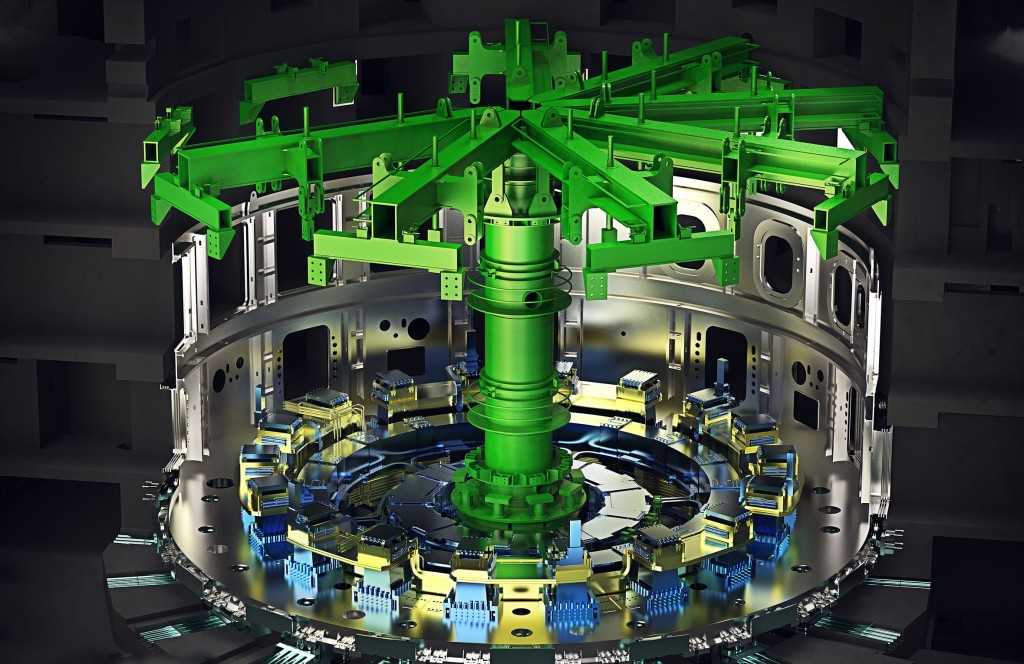
1200
tonnes heaviest component
22
metres tallest tool
100
custom devices
1500
tonnes bridge crane capacity
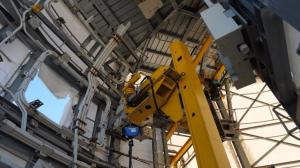
Manipulator arms: super strong and ultra precise
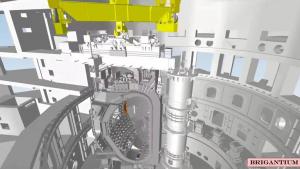
Installing a 40° section of the ITER vacuum vessel (Brigantium Engineering)
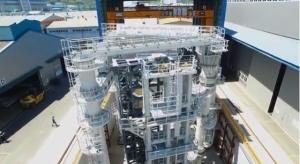
Twin giants to handle ITER components
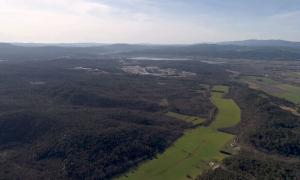
ITER NOW 1.8: Preparing for the Big Lifts
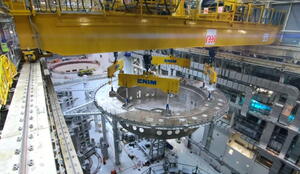
First machine component installed
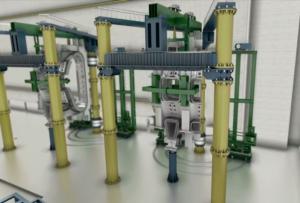
Sector sub-assembly tools in action
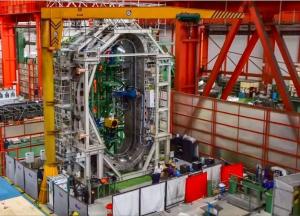
Inside the big "D"
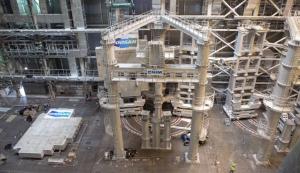
Load tests: ITER Heavyweight Champion
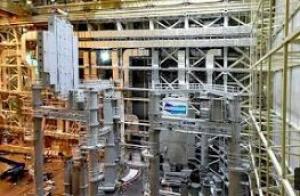
Load tests: As heavy as a 747
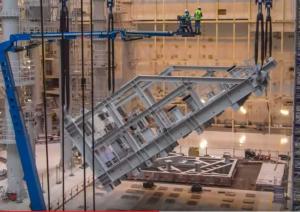
Rehearsing for assembly: the upending tool
Assembly tools
ITER BRIDGE CRANES
Two sets of bridge cranes installed at a height of 46 metres are the major lift and transport tools for delivering components from the Assembly Hall to the Tokamak pit. The heavy-duty set (two 750-tonne cranes) can work together to lift loads of 1,500 tonnes—or the approximate weight of four jetliners. The system is complemented by two smaller 50-tonne auxiliary cranes. (Procured by Europe)
SECTOR SUB-ASSEMBLY TOOLS
Standing six storeys high in the Assembly Hall, the 800-tonne tools suspend the vacuum vessel sectors while carefully positioning and installing—via the rotary motion of the "wings"—thermal shield panels and two toroidal field coils. Actuators will permit the components to be positioned with the highest degree of accuracy (1.5 mm for the toroidal field coils) and adjusted to six degrees of freedom (up and down, side-to-side, forward and backward, swivel, tilt, and pivot). The completed "sector sub-assembly" to be transported to the Tokamak pit weighs 1,200 tonnes. The operation must be carried out nine times, for nine vacuum vessel sectors. (Procured by Korea)
IN-PIT ASSEMBLY TOOL
Formed from a central column and nine radial beams, this tool is installed inside of the Tokamak Pit to support, align and stabilize vacuum vessel sub-assemblies as they are joined and welded. With the central column anchored to the Tokamak Building basemat and the radial beams supported between the column and the concrete bioshield, the in-pit assembly tool is designed to support a nominal weight of 5,400 tonnes. (Procured by Korea)
CRYOSTAT INSTALLATION AND ALIGNMENT TOOLS
Purpose-built transportation and lifting tools have been designed for the installation of each cryostat section (base, lower cylinder, upper cylinder, top lid). Once installed, the sections are brought into alignment with the tokamak global coordinate system through hydraulic jacks. (Procured by the ITER Organization)
TOROIDAL FIELD COIL ALIGNMENT TOOL
The in-pit installation tool for toroidal field coil pairs moves the D-shaped superconducting coils a few millimetres along three axes and ensures their precise positioning inside of the Tokamak pit to within 1/10th of a millimetre. It also performs the final adjustment of the Tokamak's nine sectors. (Procured by the ITER Organization)
POLOIDAL FIELD COIL ASSEMBLY TOOLS
This group of tools includes, for each coil: a transportation frame, purpose-built survey tools, lifting adapters to interface with lifting beams, and installation tools and adjustable supports. (Procured by Korea)
CENTRAL SOLENOID TOOLS
Assembly of the six central solenoid modules into an 18-metre-tall stack (including support structures) requires a dedicated space in the ITER Assembly Hall and specialized tooling including an assembly platform designed to support 1,300 tonnes and a module lifting fixture. (Procured by the US)