Blanket
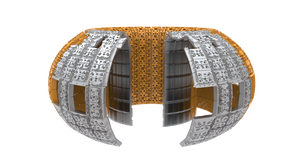
The 440 blanket modules that completely cover the inner walls of the vacuum vessel protect the steel structure and the superconducting toroidal field magnets from the heat and high-energy neutrons produced by the fusion reactions. As the neutrons are slowed in the blanket, their kinetic energy is transformed into heat energy and collected by the water coolant. In a fusion power plant, this energy will be used for electrical power production.
Each blanket module measures 1 x 1.5 metres and weighs up to 4.6 tonnes. Over 180 design variants exist (related to the position of the modules in the vacuum vessel), but all have a detachable first wall that directly faces the plasma and removes the plasma heat load, and a main shield block that is designed for neutron shielding. The blanket modules also provide passageways for diagnostic and plasma heating systems.
The ITER blanket, which covers a surface of 600 m², is one of the most critical and technically challenging components in ITER: together with the divertor it directly faces the hot plasma. Due to the high heat deposition expected during plasma operation, ITER will be the first fusion device to operate with an actively cooled blanket. The cooling water—injected at 4 MPa and 70 °C—is designed to remove up to 736 MW of thermal power.
During later stages of ITER operation, some of the blanket modules will be replaced with specialized modules to test materials for tritium breeding concepts. A future fusion power plant producing large amounts of power will be required to breed all of its own tritium. ITER will test this essential concept of tritium self-sustainment.
First wall panels
The ITER Organization made the decision in 2023 to modify the armour material planned for the first wall of the ITER blanket, replacing beryllium with tungsten. The rationale for this change is two-fold. First, all future fusion devices designed for a burning plasma plan to use tungsten as armour material; in this context, ITER operation with beryllium did not align with the fusion community’s roadmap to fusion energy. Second, specific concerns about beryllium—for example the quantity of dust generated through erosion, the metal’s toxicity and implications for maintenance, and recent modelling that suggests that the strong melting of beryllium during off-normal plasma events at medium plasma currents can lead to premature failure of the first wall panels due induced electromagnetic forces—justified the consideration of an alternative.
Starting with a tungsten first wall will mean that there is no longer the need to plan for full first wall replacement (as would have been the case for beryllium), resulting in time saved and a significant reduction in radwaste. Other consequences of this modification will require additional planning and preparation by the global ITER team: new first wall panels have to be developed, qualified and procured; significant additional electron cyclotron resonance heating power will be required as part of a modified mix of heating and current drive power; and a new process—boronization—must be implemented in the tokamak to coat the tungsten wall with a thin boron layer in order to improve the capture of oxygen atoms that could increase the contamination of the plasma (beryllium was a natural oxygen “getter”). These planned changes to components and systems must be designed into the machine and buildings. The ITER Research Plan must also be refined. All of these efforts are underway.
Shield blocks
The shield blocks (the heavier of the two elements, at left) provide nuclear shielding for the vacuum vessel and coil systems as well as support for the first wall panels. Cooling water will run to and from the shield blocks through manifolds and branch pipes to remove the high heat load expected during ITER operation.
Each shield block will be bolted directly to the vacuum vessel at four points. Installation of the 440 modules will be challenging, as they must be aligned with tolerances of approximately 10 mm globally and with nominal gap requirements between adjacent modules (both vertically and horizontally) of +/-4 mm. Customizable components will be individually machined as installation progresses to achieve these tolerance parameters. (The image shows how a shield block "recieves" the replaceable plasma-facing first-wall panel.)
The other components
Please note that all images are for illustrative purposes only.