The Project
- Building ITER
- Projects Underway
- Construction Archives
- Neutral Beam Test Facility
- Assembly Overview
- Tokamak Assembly
- Plant Assembly
- Commissioning
- Assembly Tooling
- Metrology
- Project Milestones
Coil Fabrication on Site
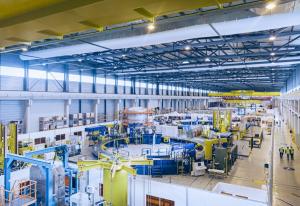
For the poloidal field coils under European responsibility, the different stages of fabrication—winding, impregnation, stacking, cold testing—were carried out on stations in this production facility on the ITER site.
One of only two manufacturing facilities located on the ITER site, the Poloidal Field Coils Winding Facility was constructed by Europe to house the winding and assembly activities for four of ITER's giant ring-shaped magnets.
Ranging in diameter from 17 to 24 metres and weighing 200 to 400 tonnes, coils PF2, PF3, PF4, and PF5 were simply too big to be manufactured off site and shipped to ITER.
The 250-metre-long facility was equipped with the high-tech machinery and handling equipment required to carry out the successive stages of the fabrication process, from winding the building blocks of each coil, to stacking and creating the final assembly, to cold testing. In April 2021, the first European-made coil, PF5, successfully completed all manufacturing and testing and was removed from the facility and stored until its installation in September 2021. A third completed coil, PF2, left the facility in December 2021 and is stored on site; PF4 and PF3 followed respectively in August 2023 and May 2024. European poloidal field coil procurement activities have now concluded, and the building will be fully transferred to the ITER Organization for other machine assembly activities.
The manufacturing process
The raw material for the four coils—niobium-titanium (NbTi) cable-in-conduit superconductor—was produced in China and delivered to the Poloidal Field Coils Winding Facility on 20-tonne spools.
In the winding stage of fabrication, the conductor was uncoiled from the spools and straightened before passing through cleaning and sandblasting machines that prepared its surface to receive several layers of glass-fibre insulating tape. Rotating tape heads entered into action as the conductor, fed from two spools simultaneously, joined the tooling table to be "turned" into the precise dimensions required for each coil. The resulting component was a spiralled, two-layer coil called a double pancake that weighed between 20 tonnes (PF2) and 34 tonnes (PF3). In all, 30 double pancakes were wound in the facility to build four coils.
Next, the double pancake was transported by overhead crane to the vacuum pressure impregnation (VPI) station and lowered into a custom-fit mould. Epoxy resin, injected over the course of several hours, filled all gaps and hardened the glass tape under the effect of heat and pressure. A 36-hour "curing" phase at 140 °C completed the process, which gave the double pancake rigidity and ensured electrical insulation.
The rigid double pancake winding was transferred to the winding pack assembly area of the building where it was stacked with other double pancakes and joined together. A second vacuum impregnation was performed to harden the entire assembly and components such as clamps, protection covers and helium pipes were added.
The final step in coil production was cold testing, during which the completed poloidal field coils were repeatedly cooled to low temperature (approximately 80 K) in order to simulate the thermal stresses and the work conditions that will be experienced during operation, then brought back to room temperature.
Poloidal Field Coil Fabrication facts:
- Coil production: 2017-2024
- Coils manufactured on site: PF2, PF3, PF4, PF5
- Diameter of coils: from 17 metres (PF2, PF5) to 24 metres (PF3, PF4)
- Amount of NbTi cable-in-conduit superconductor per coil: from 6 km (PF2) to 14 km (PF3)
- Number of double pancakes per coil: six (PF2) or eight (PF3, PF4, PF5)
- Number of double pancakes produced on site: 30
- Weight of final assemblies: 200 to 400 tonnes
- Coil completion dates: PF5 (2021); PF2 (2021); PF4 (2023), PF3 (2024)
- Procurement responsibility: Europe
Photo Gallery
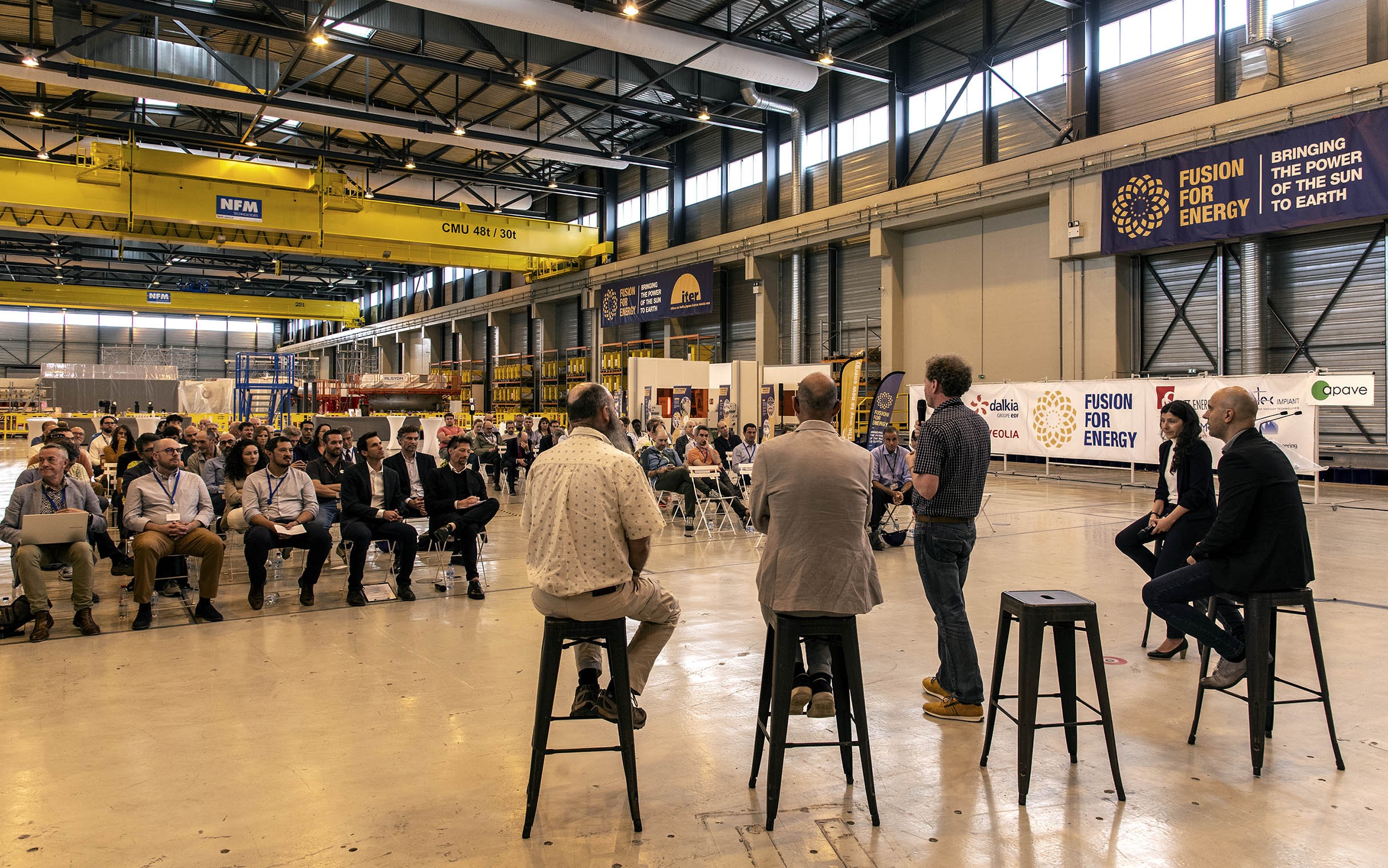
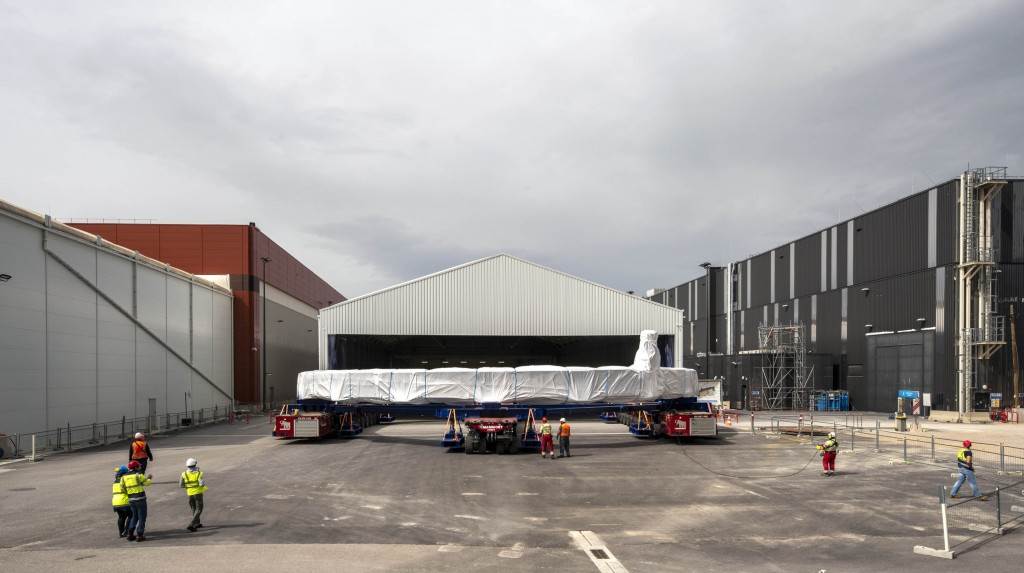
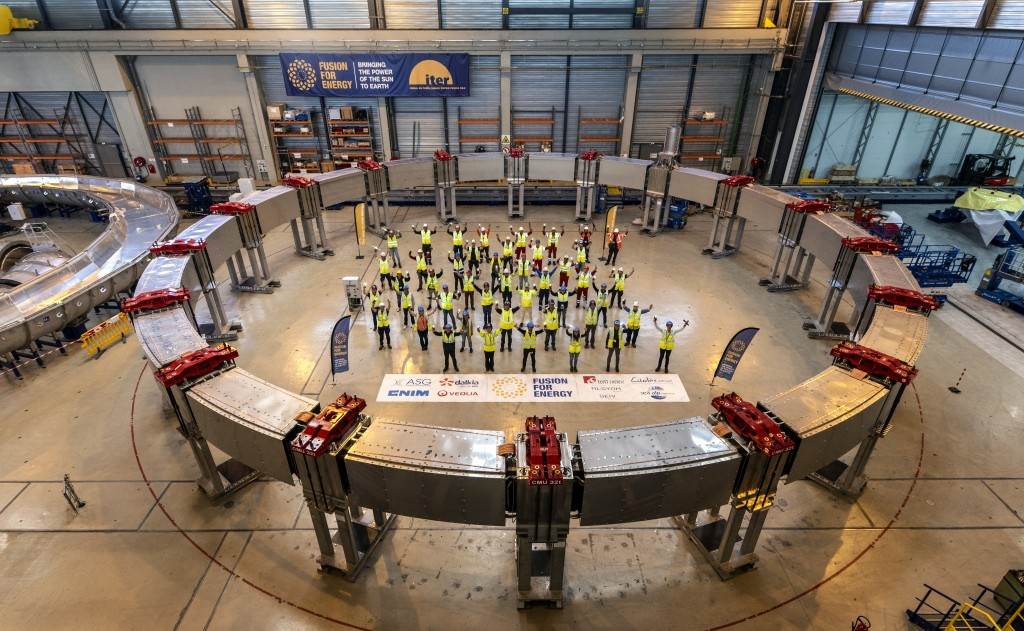
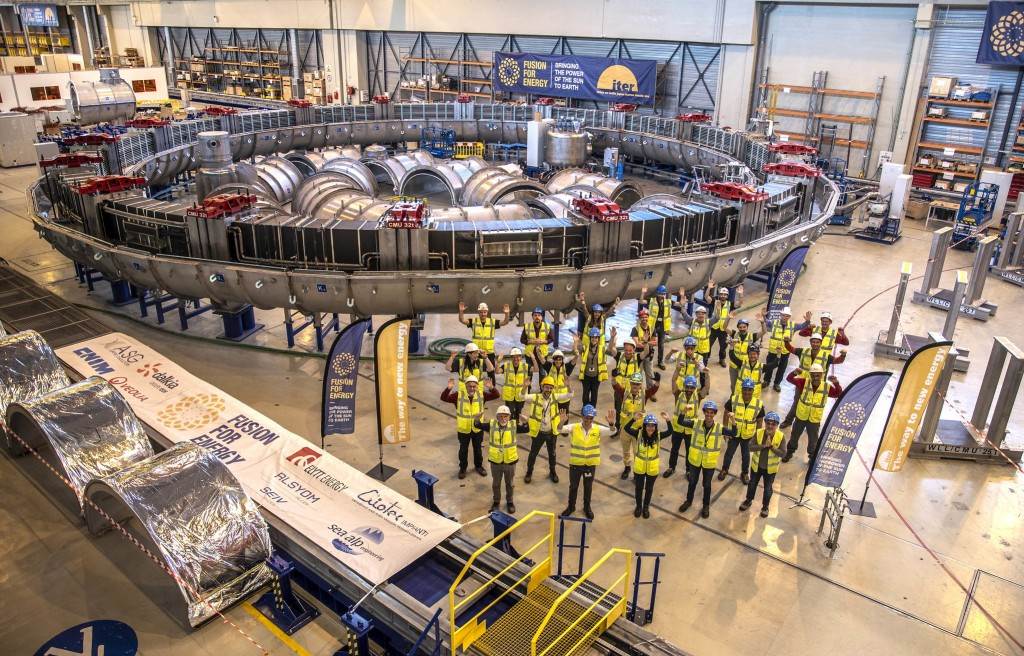
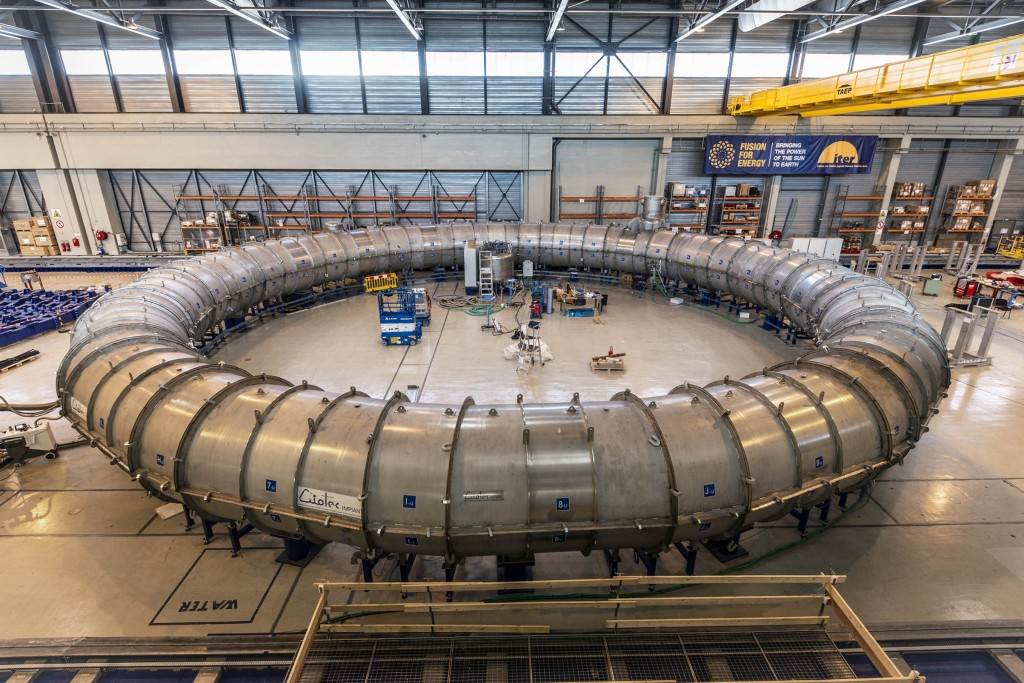
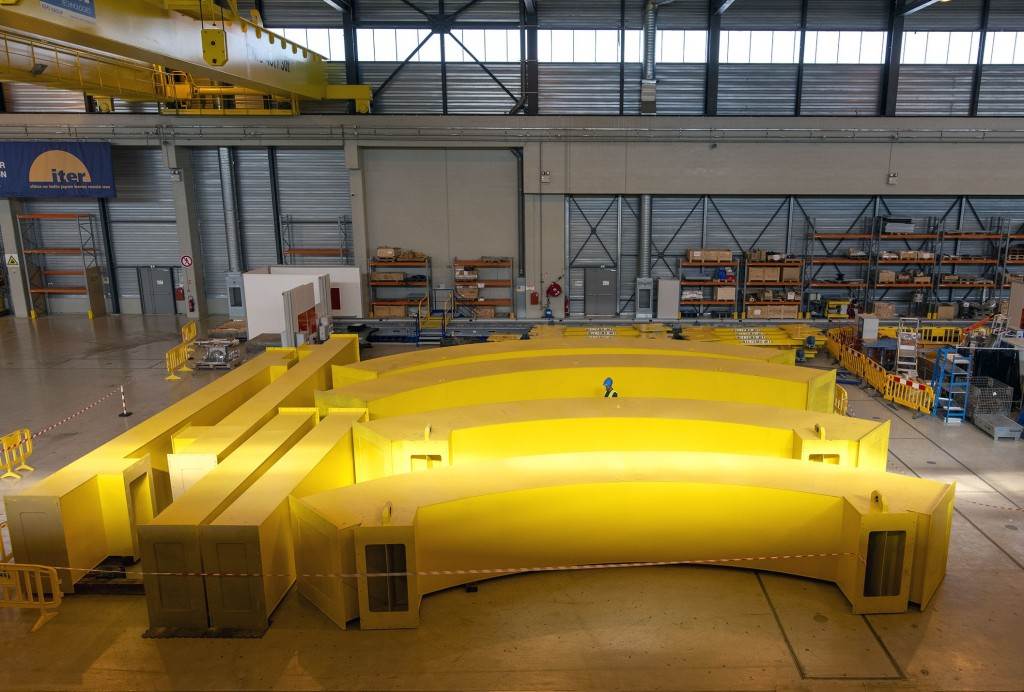
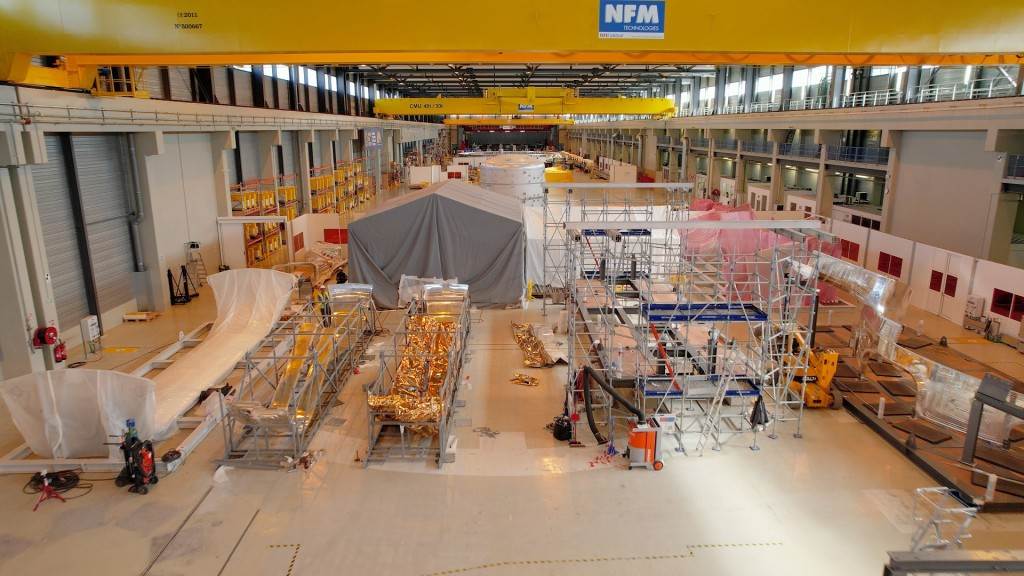
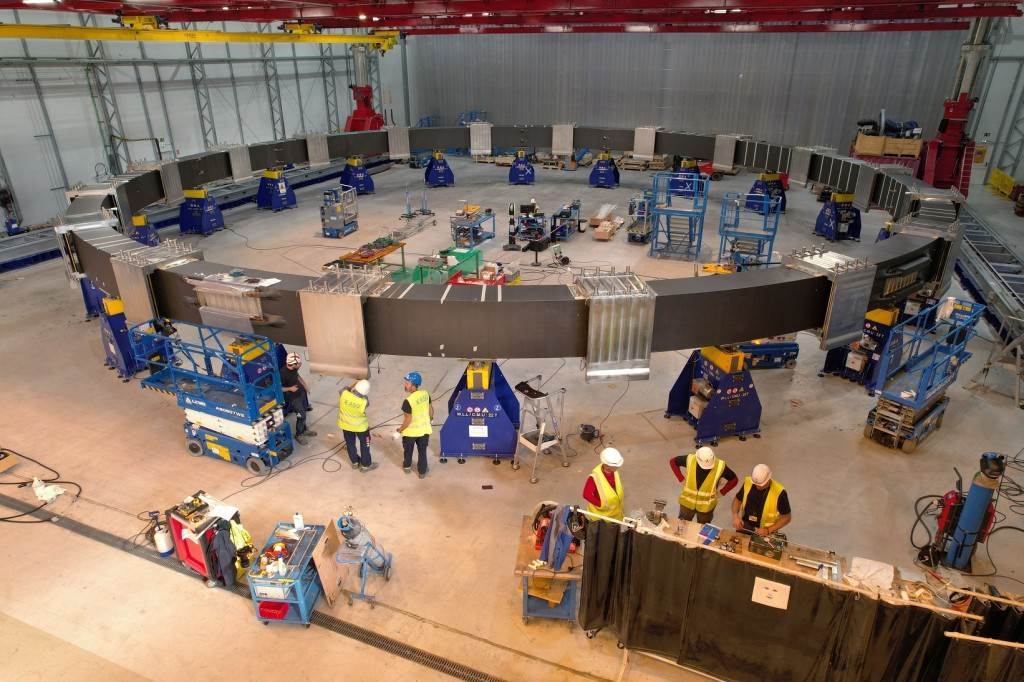
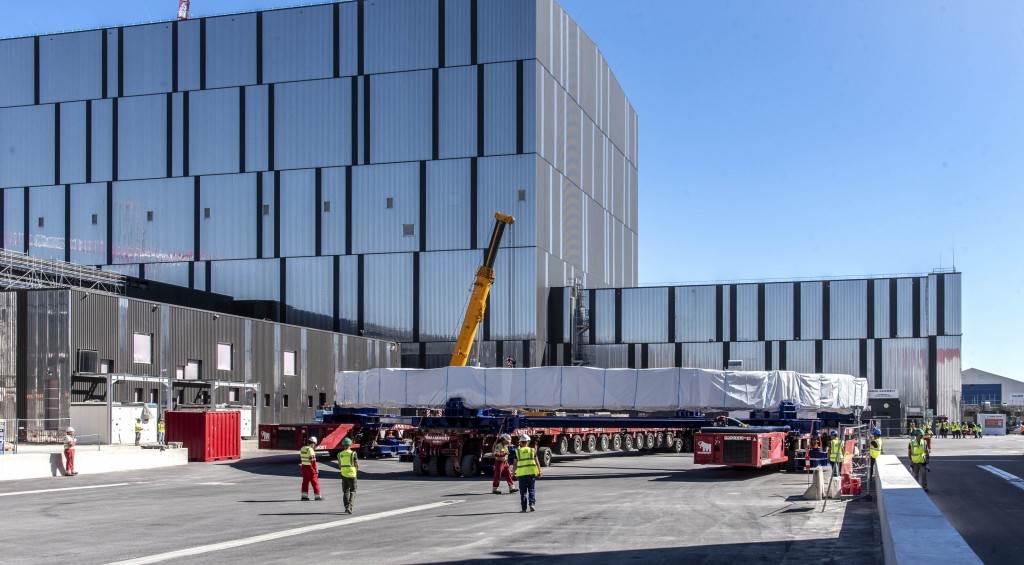
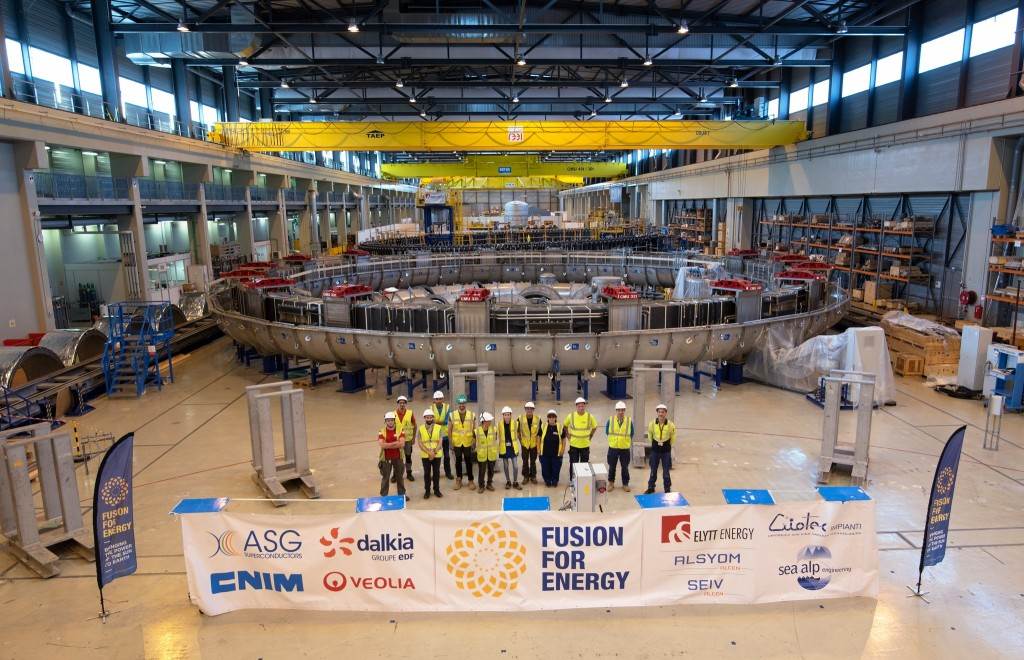
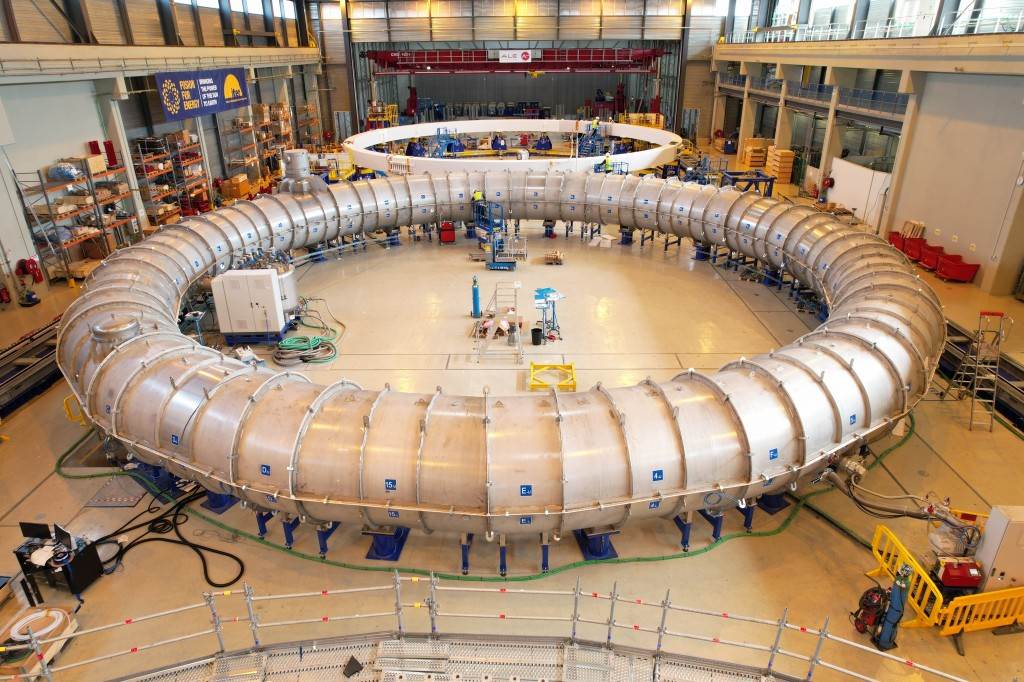
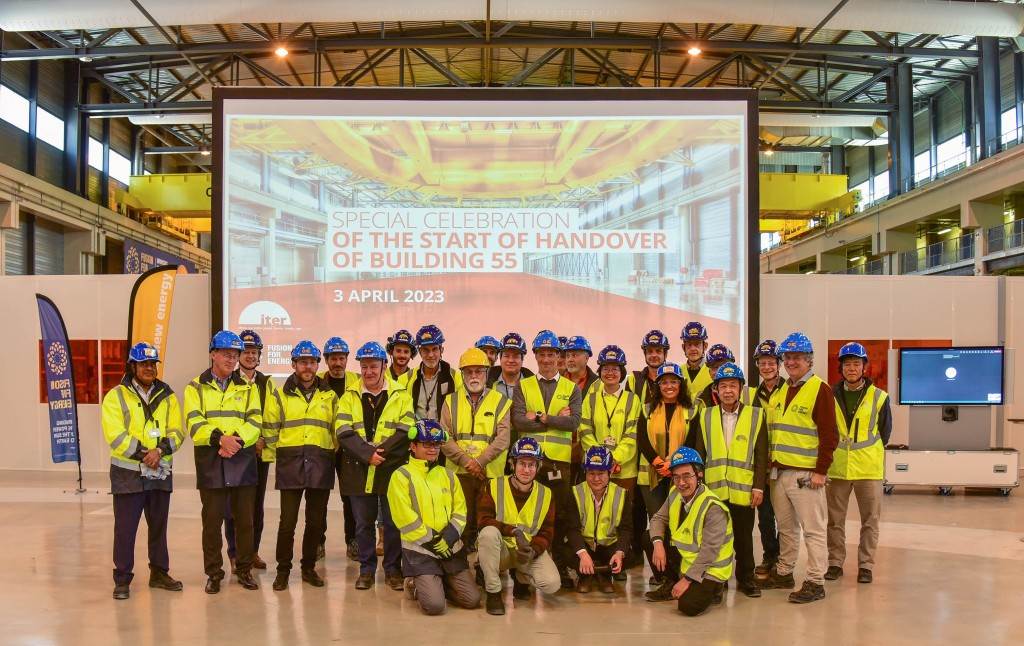
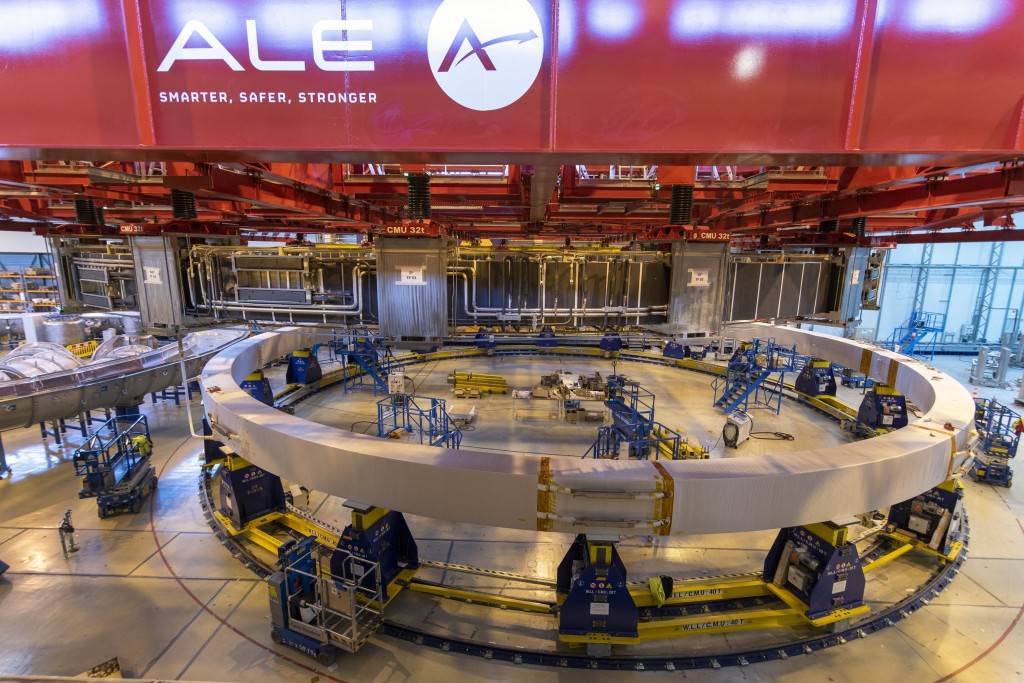
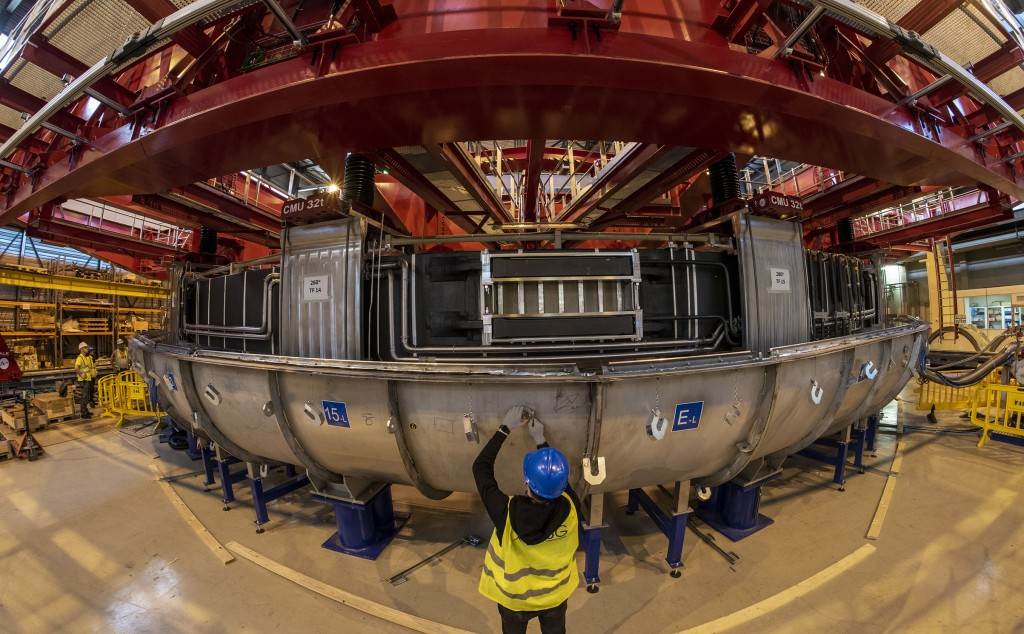
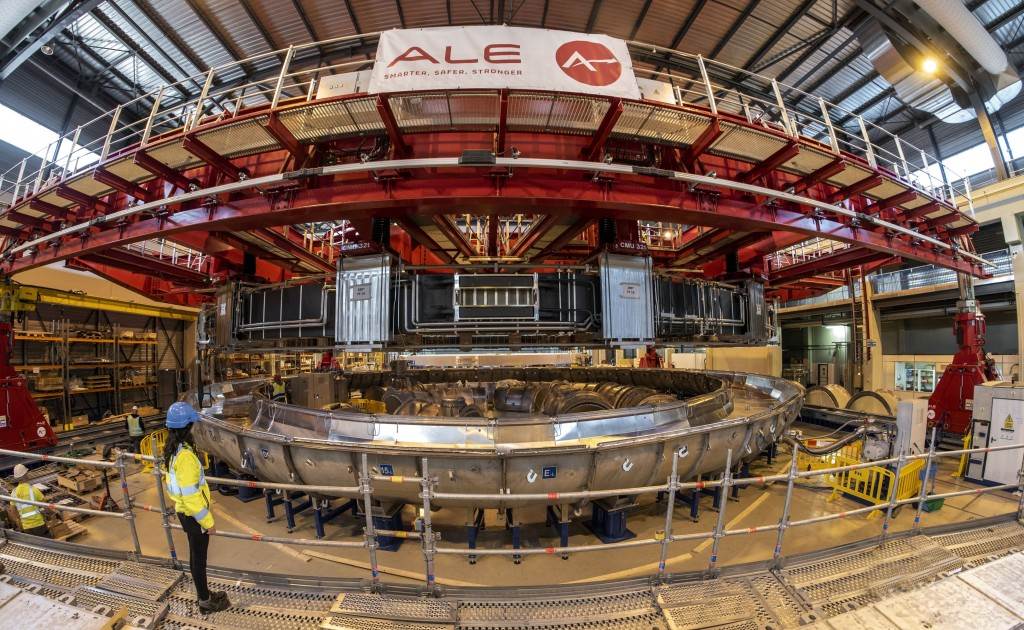
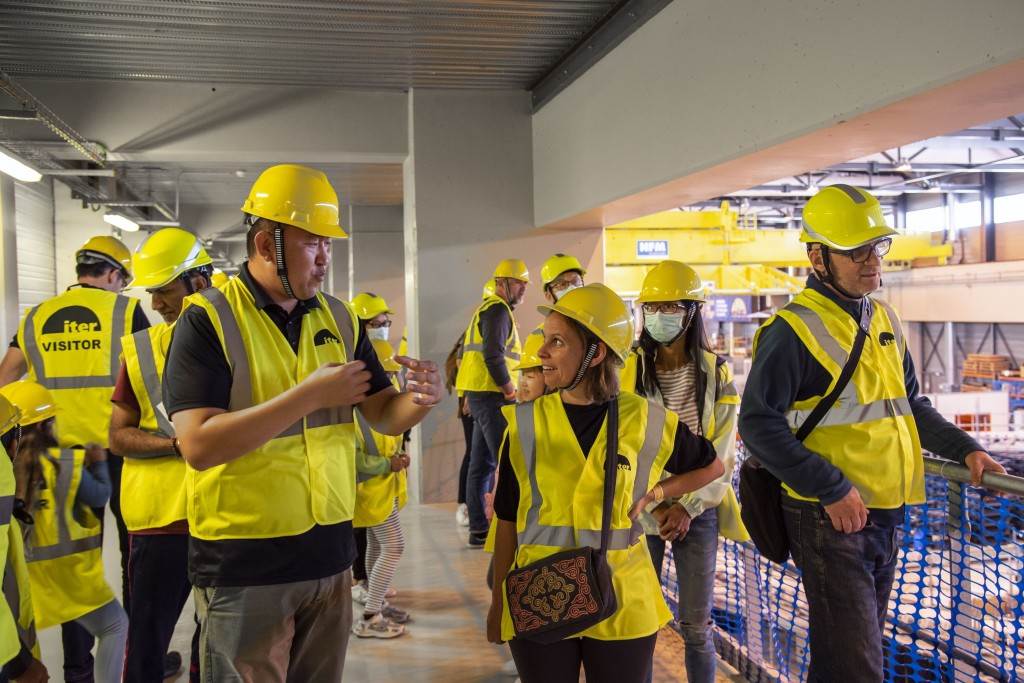
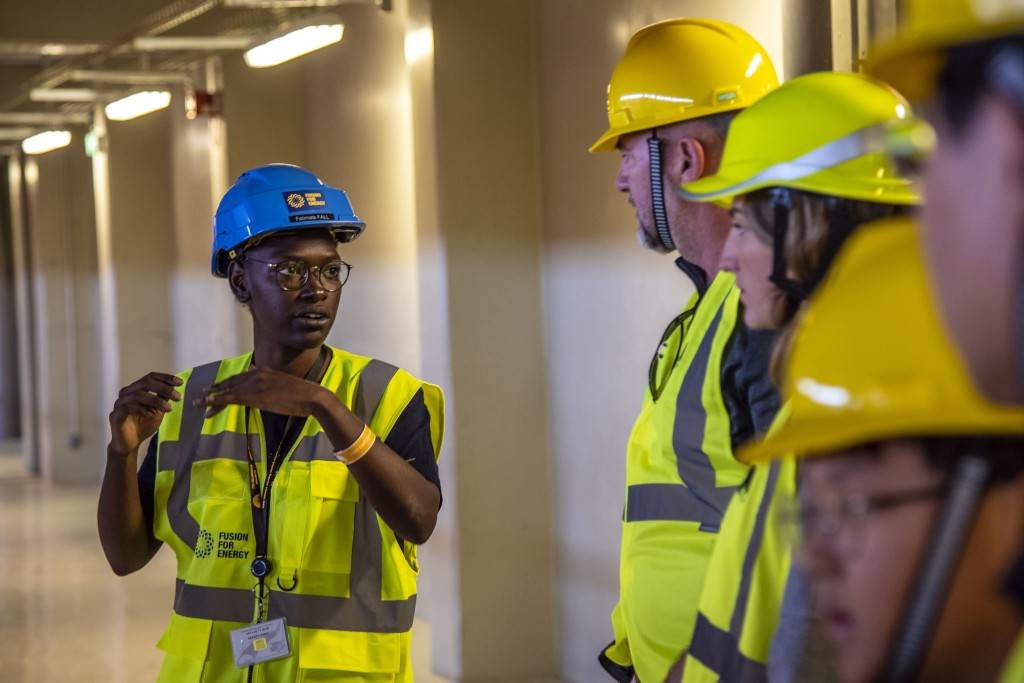
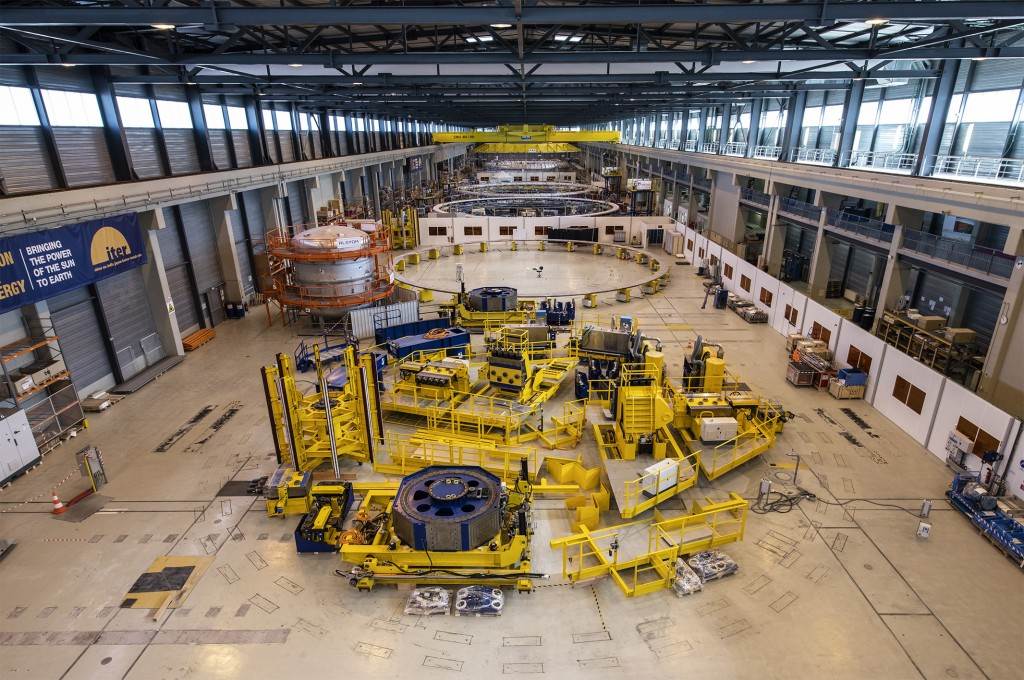
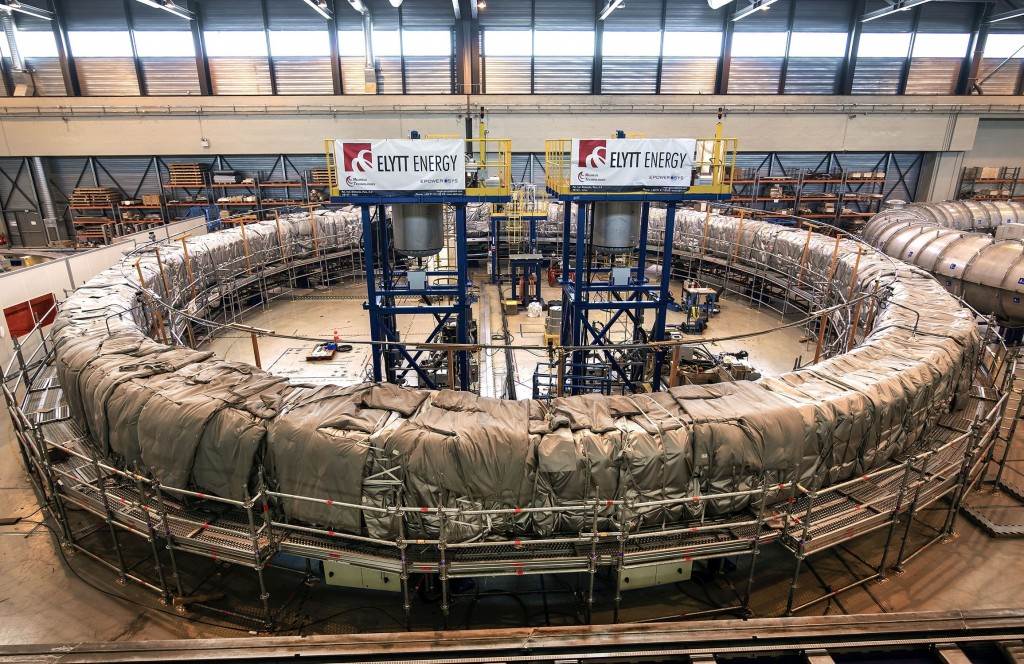
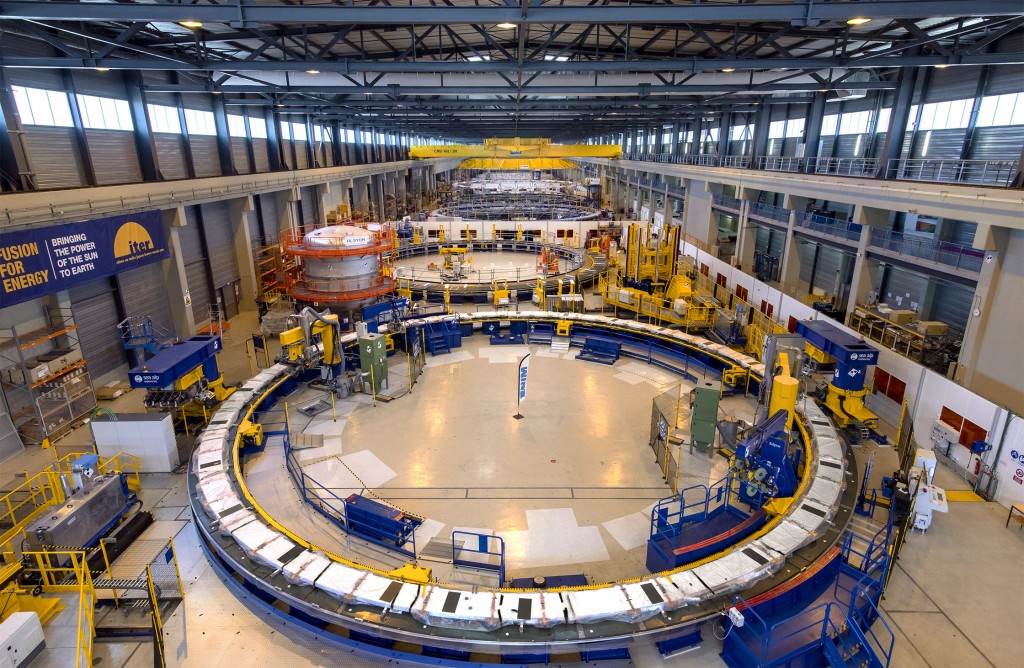
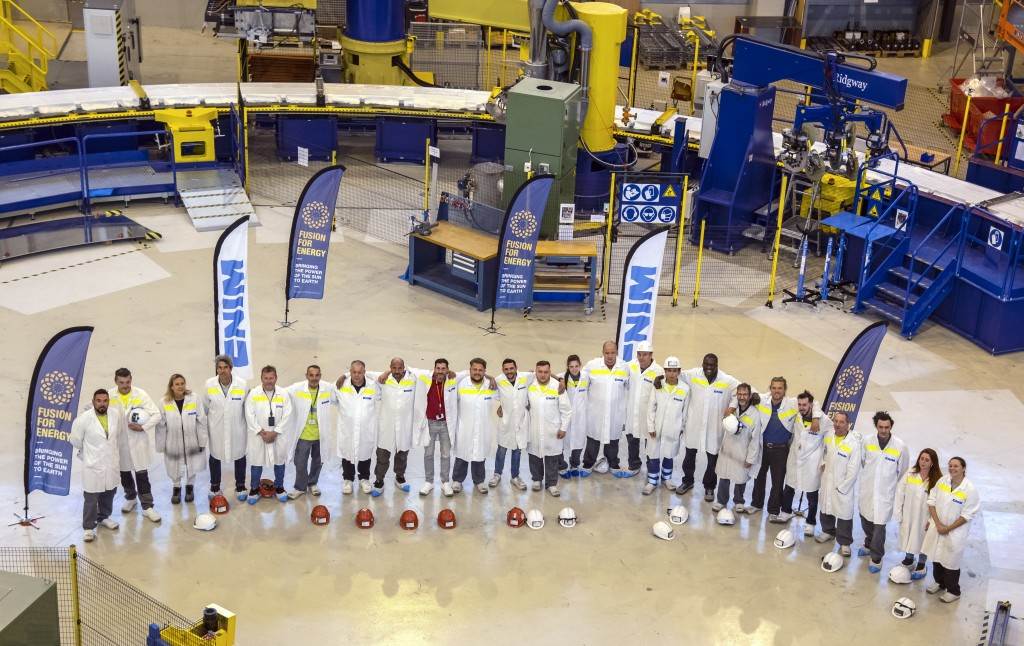
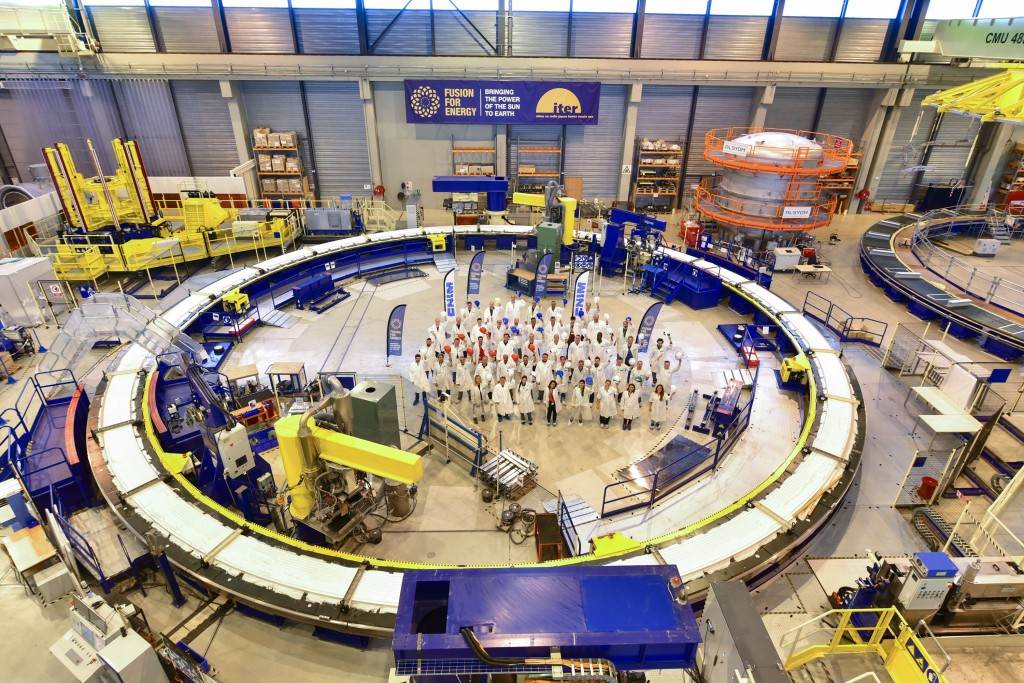
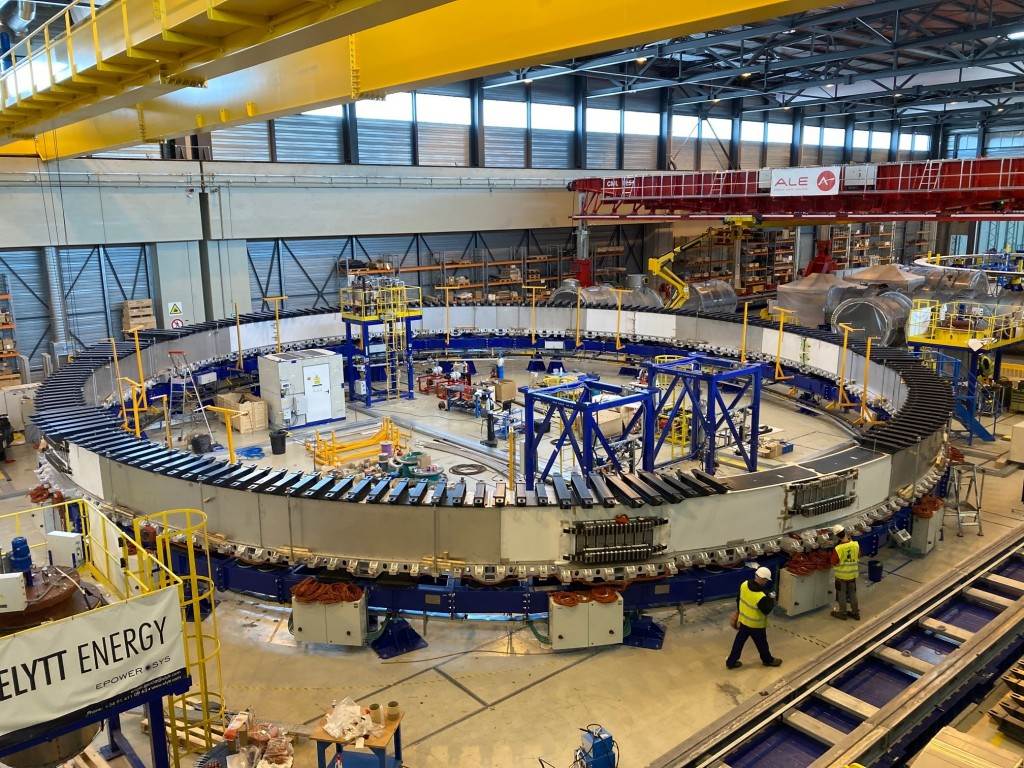
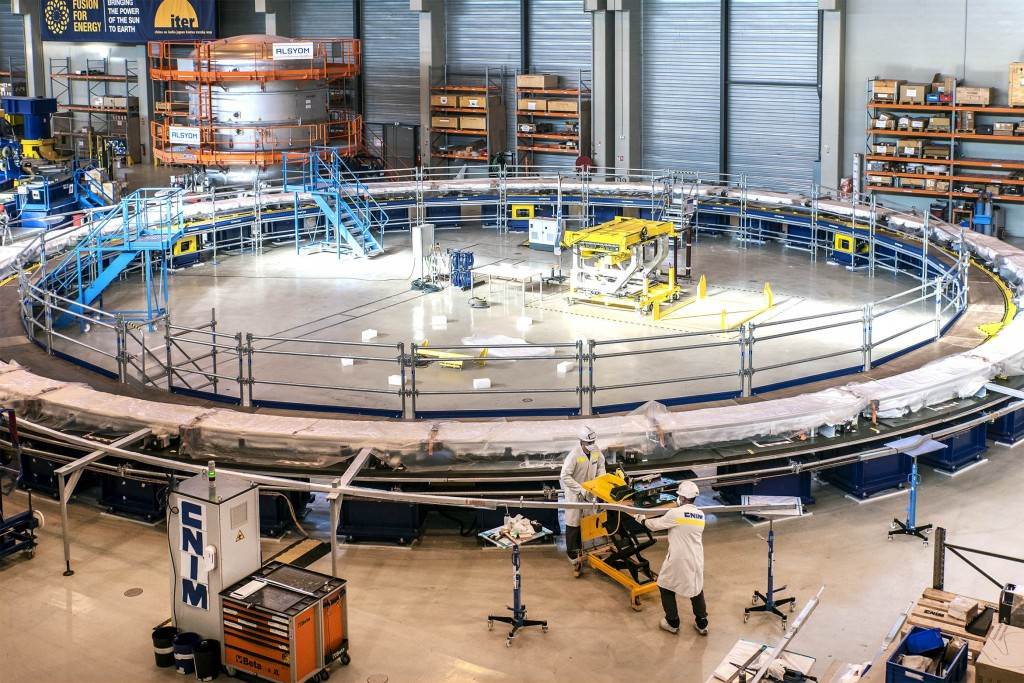
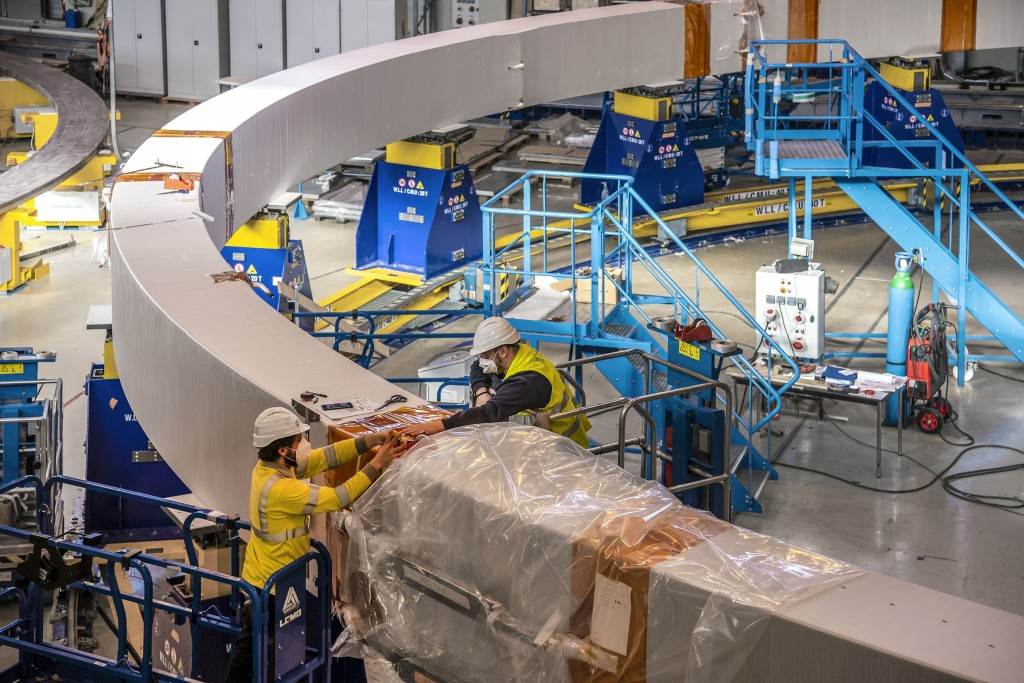
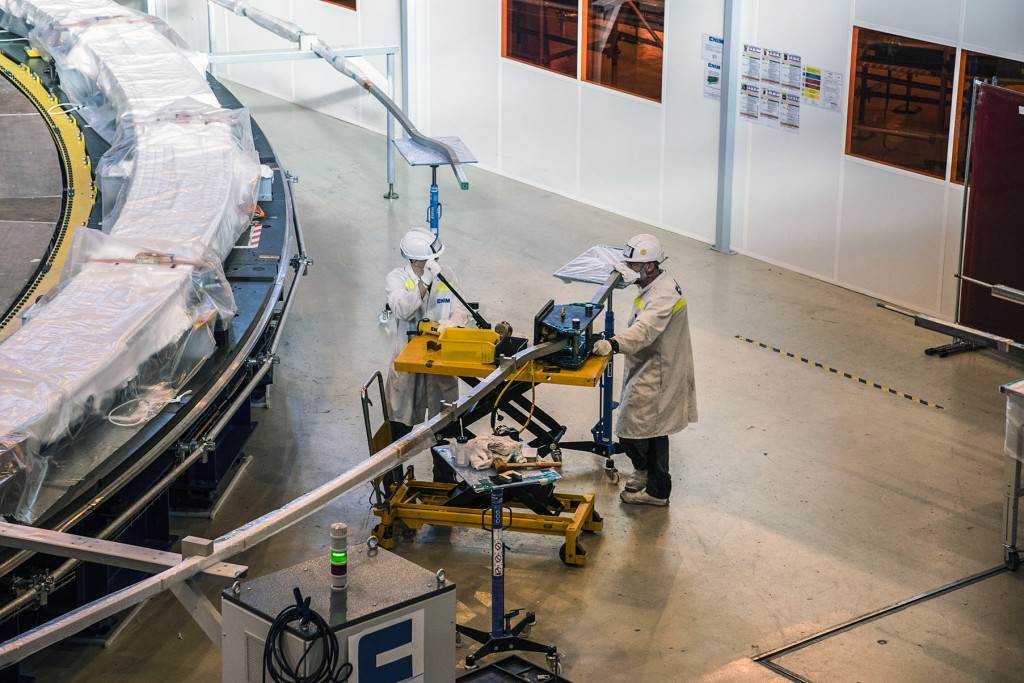
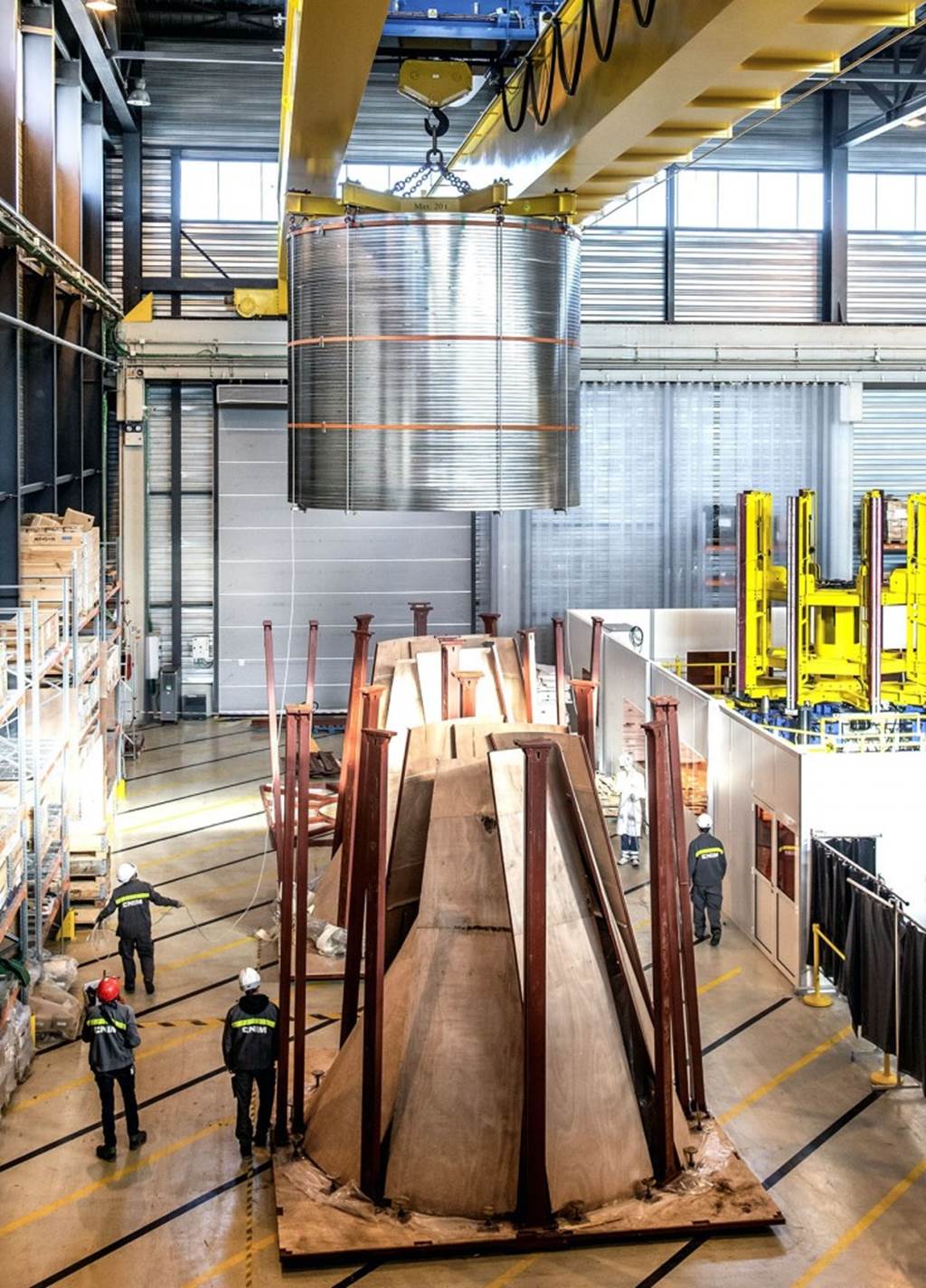
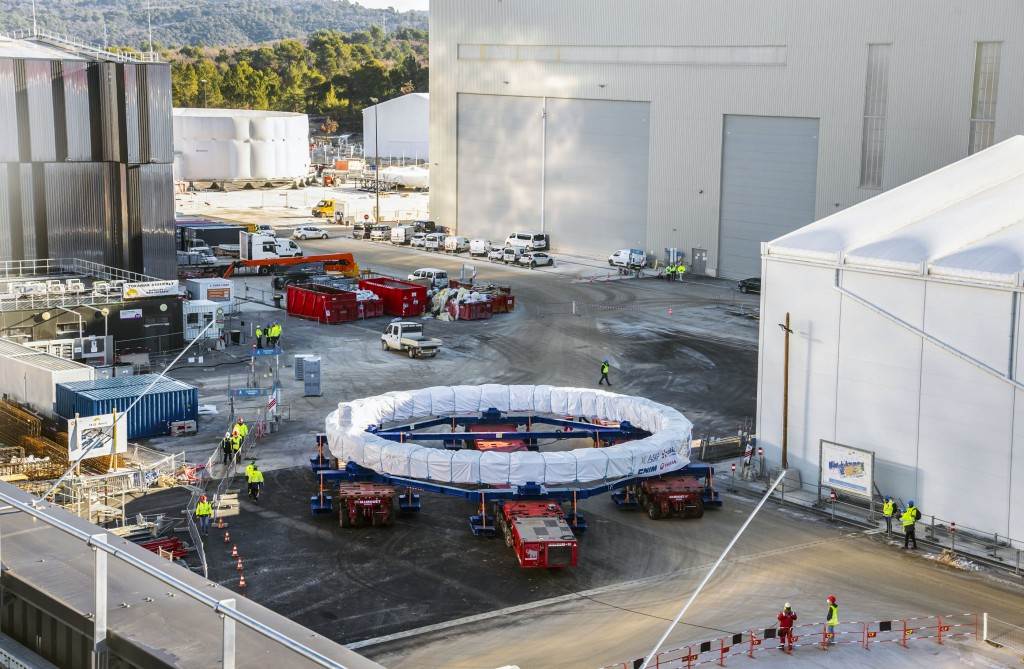
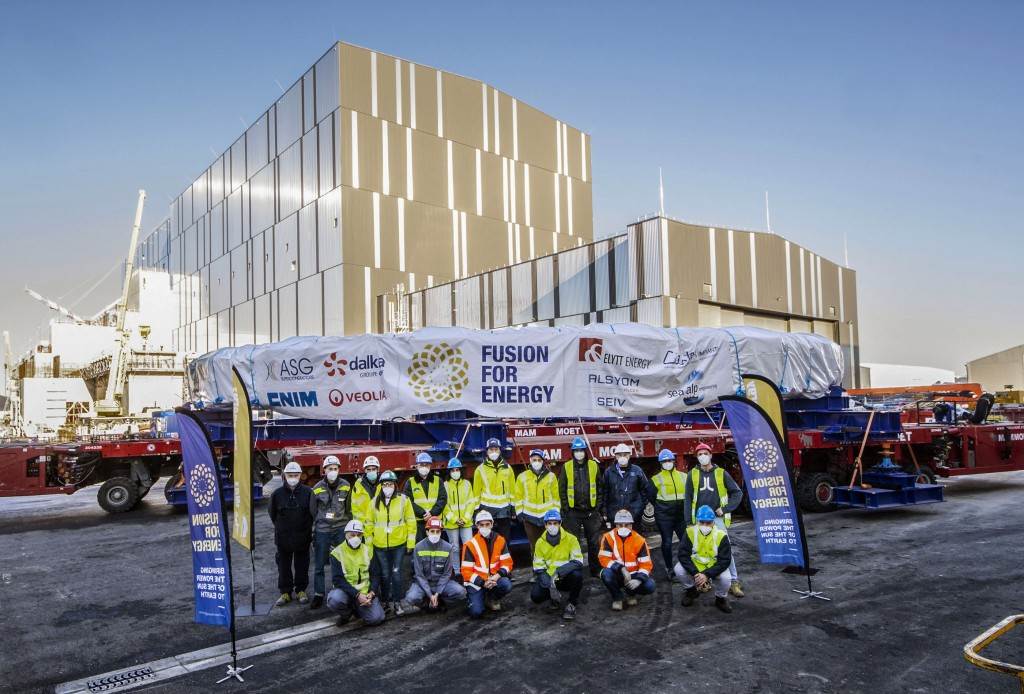
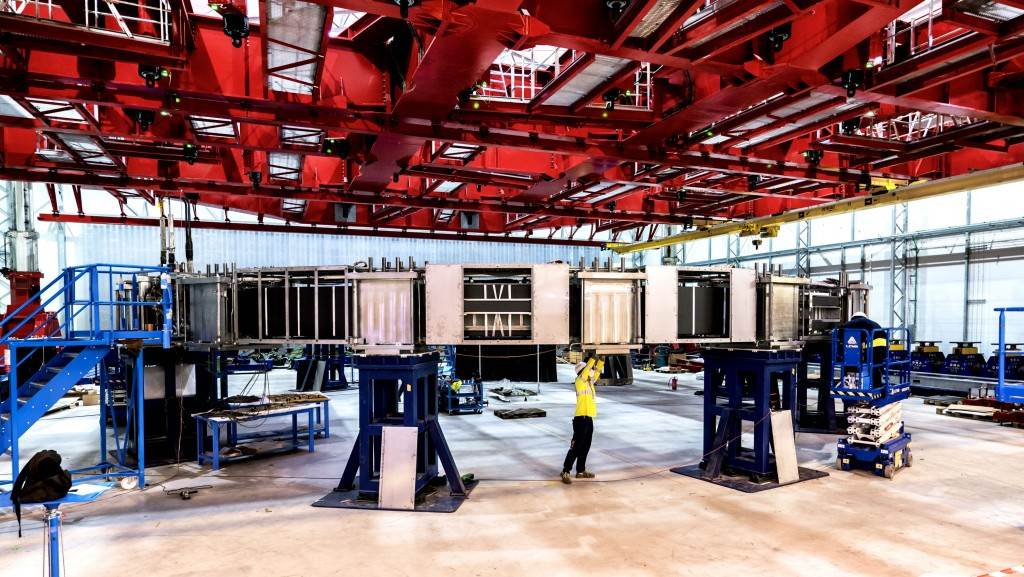
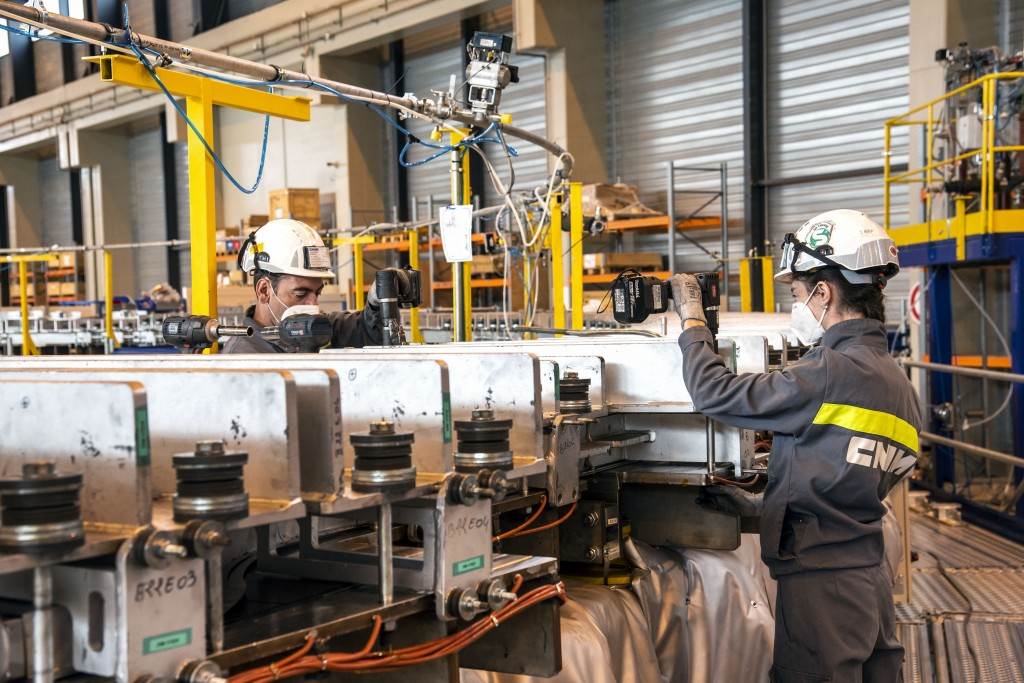
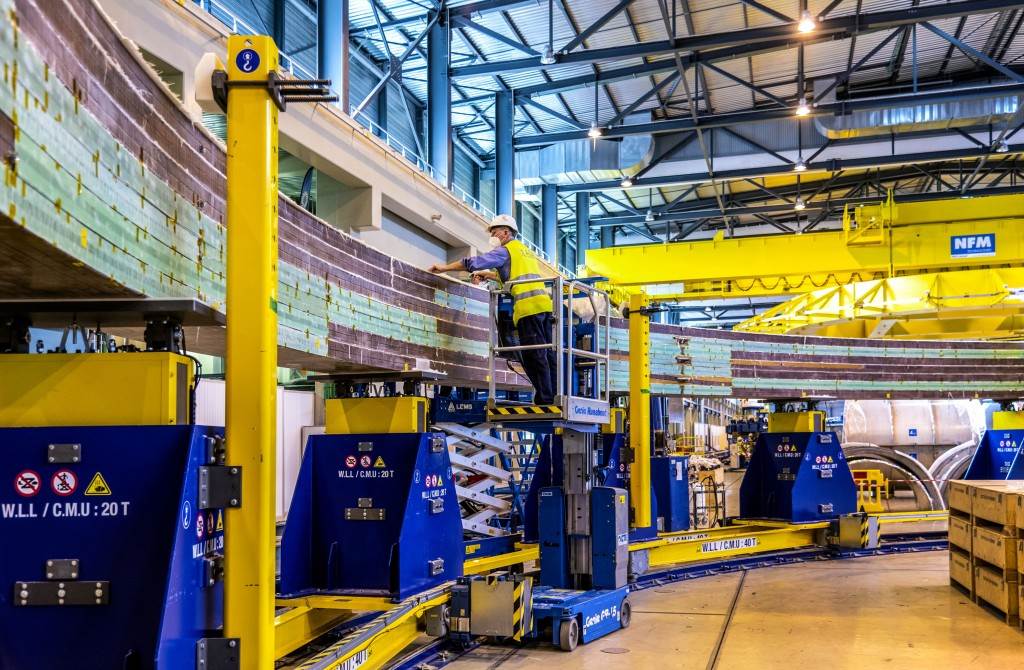
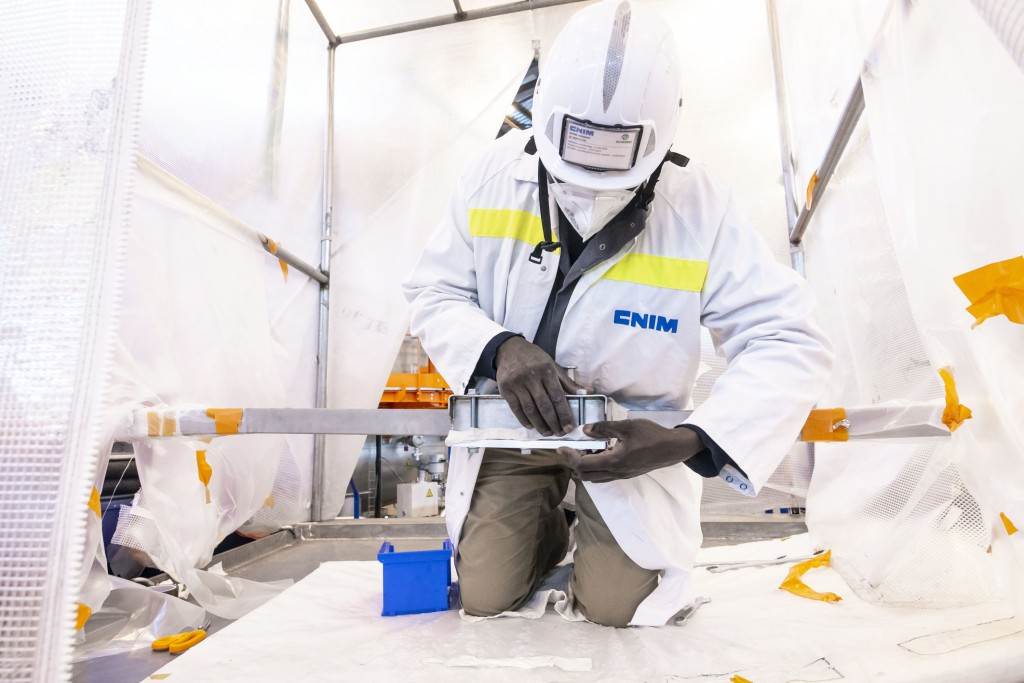
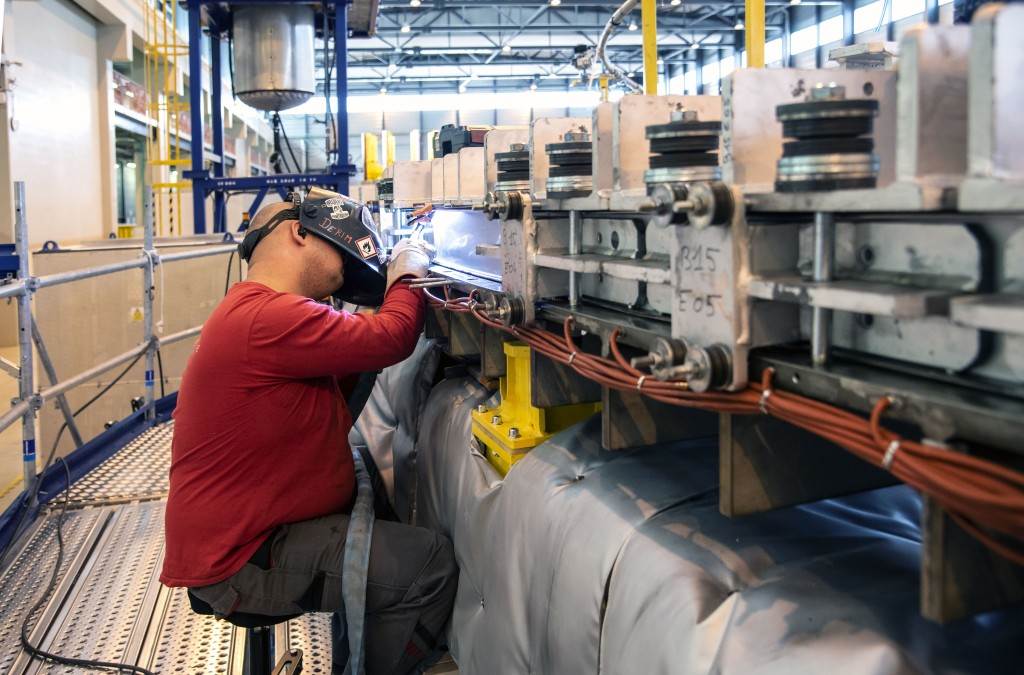
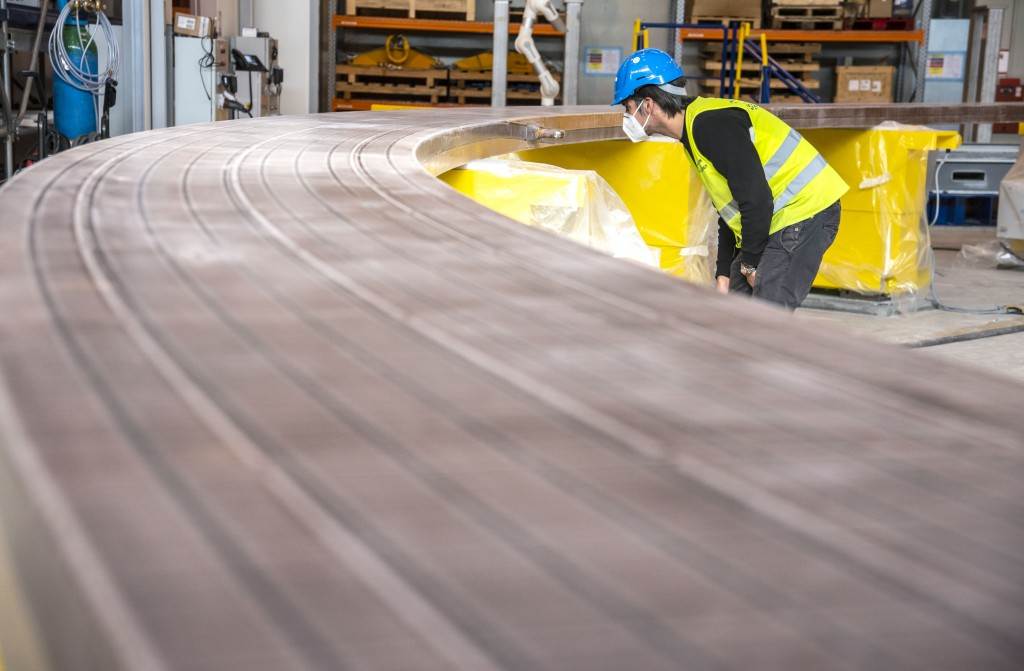

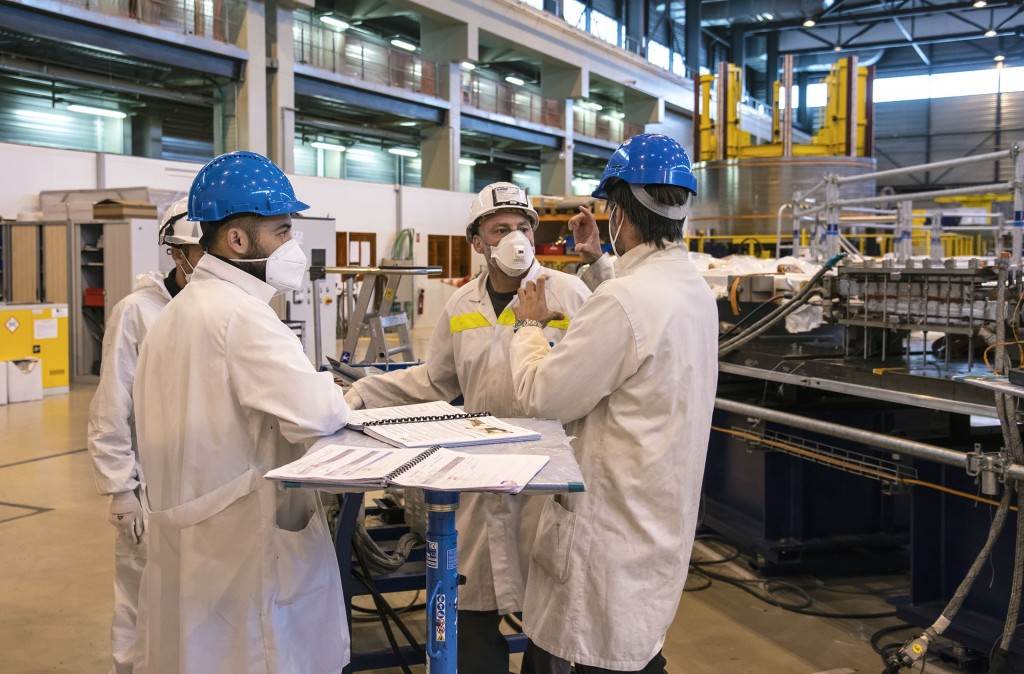
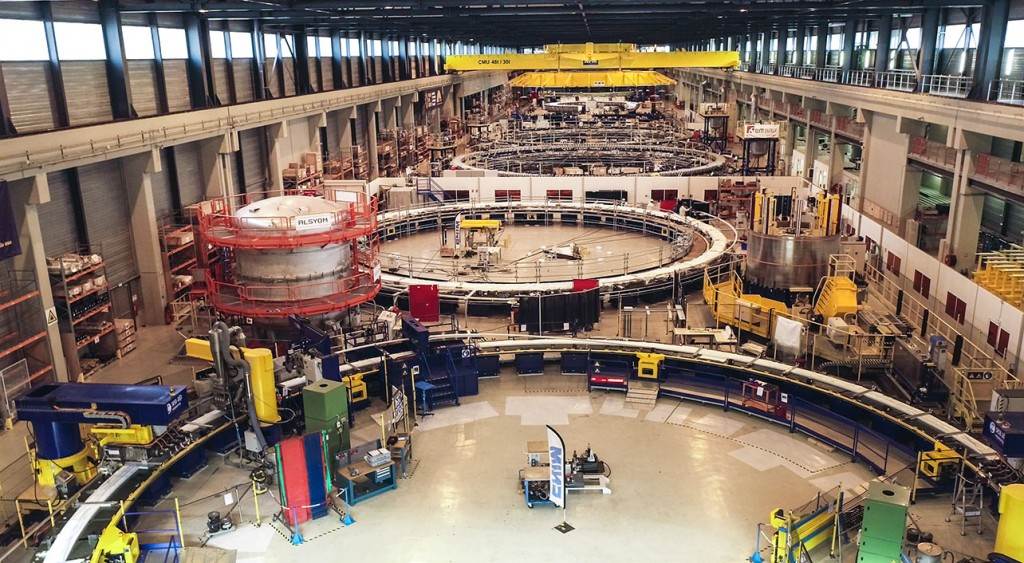
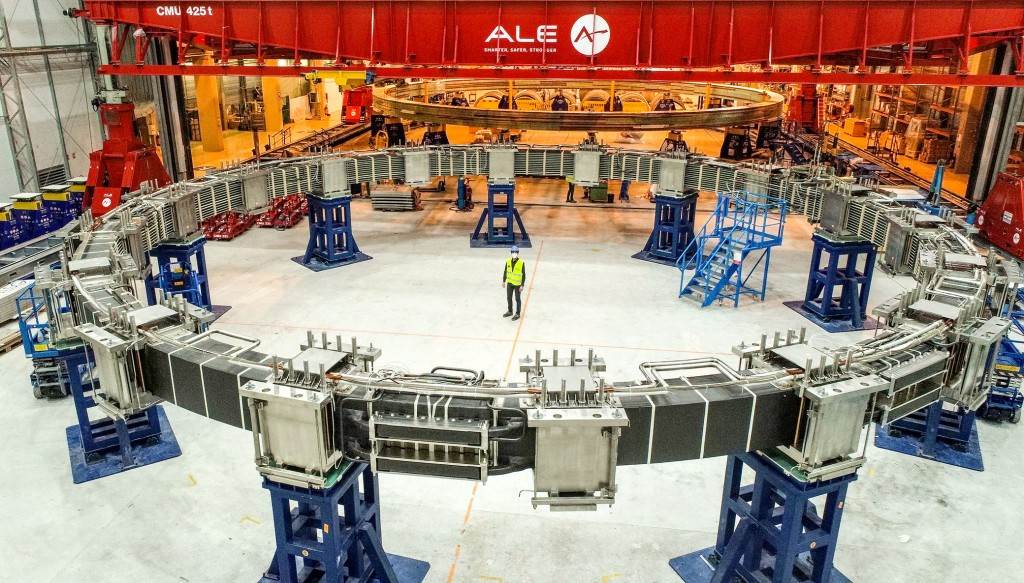
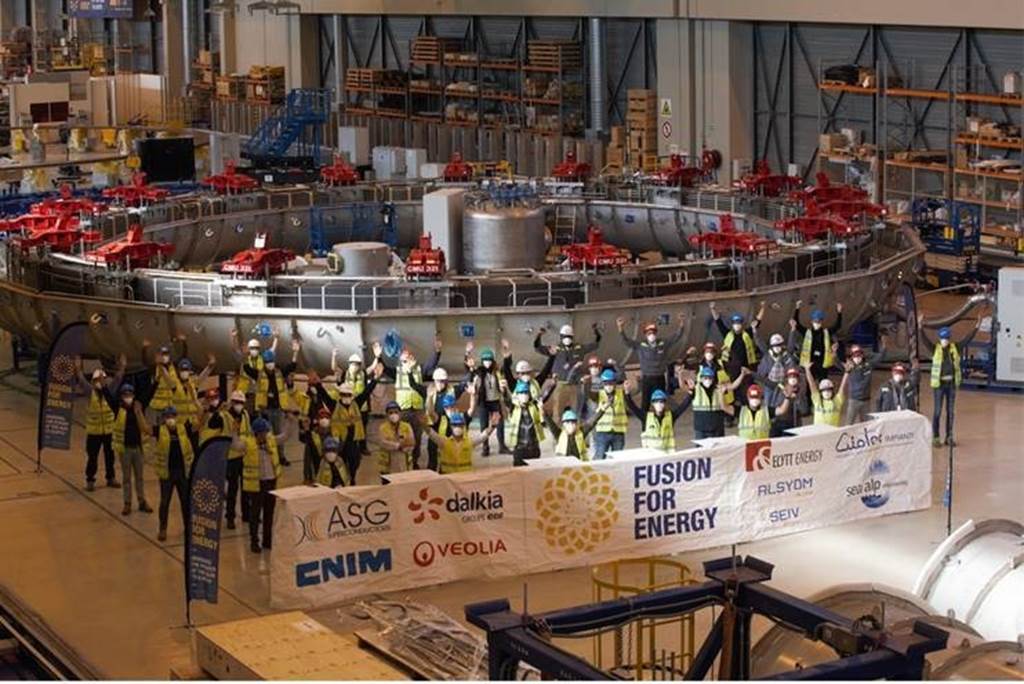
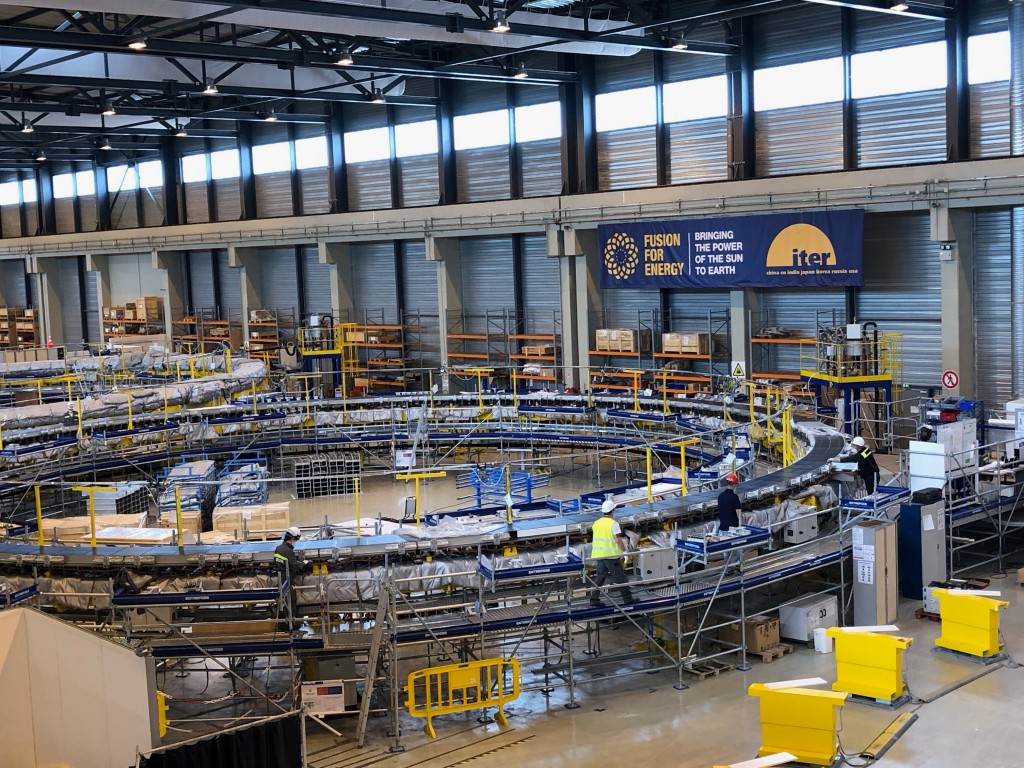
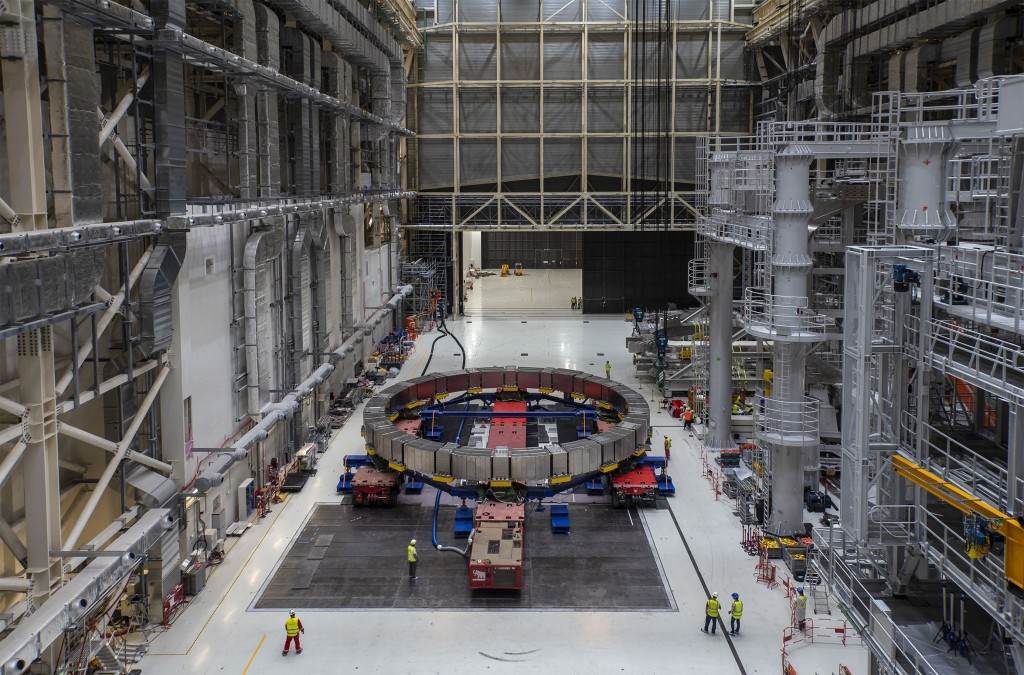
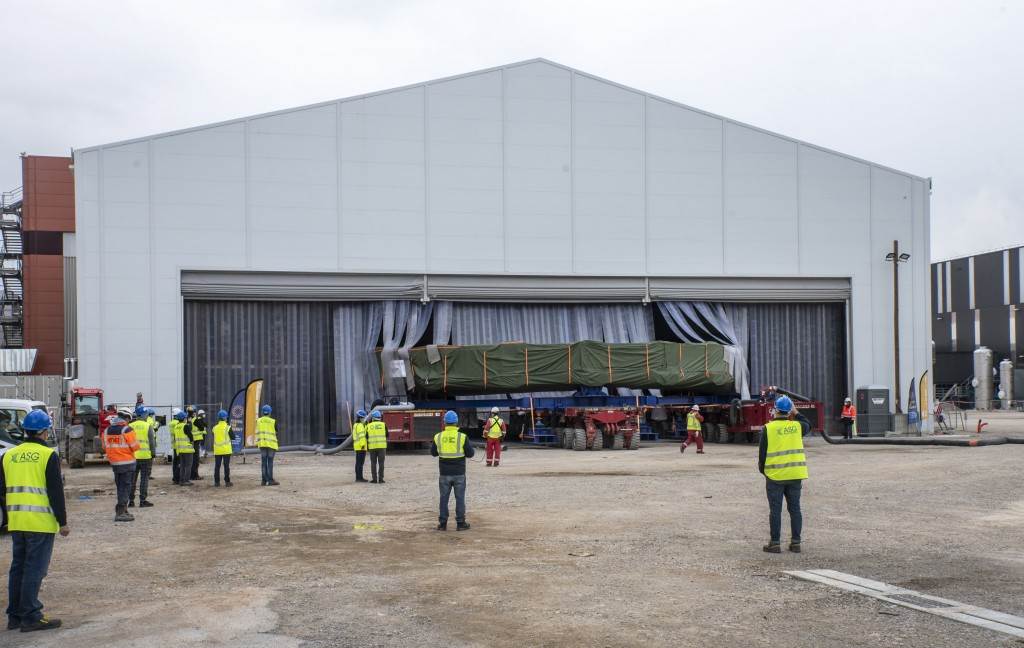
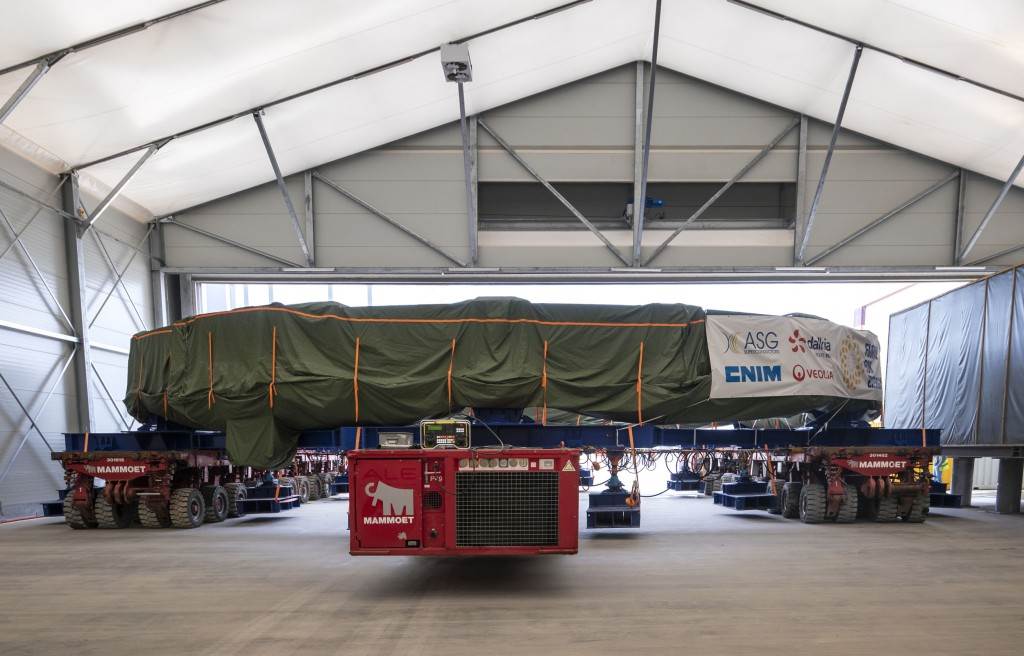
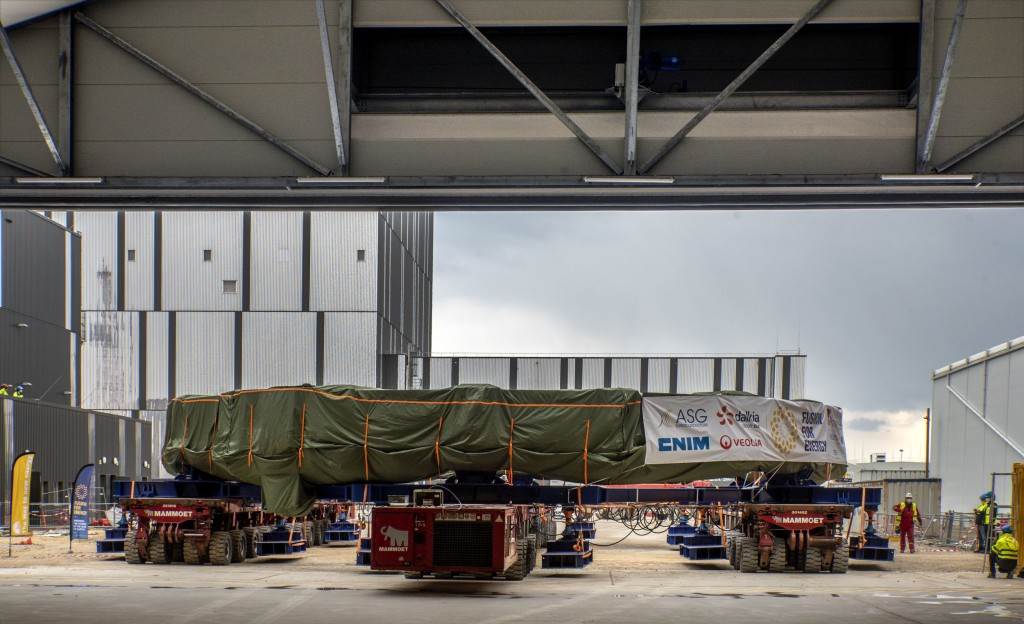
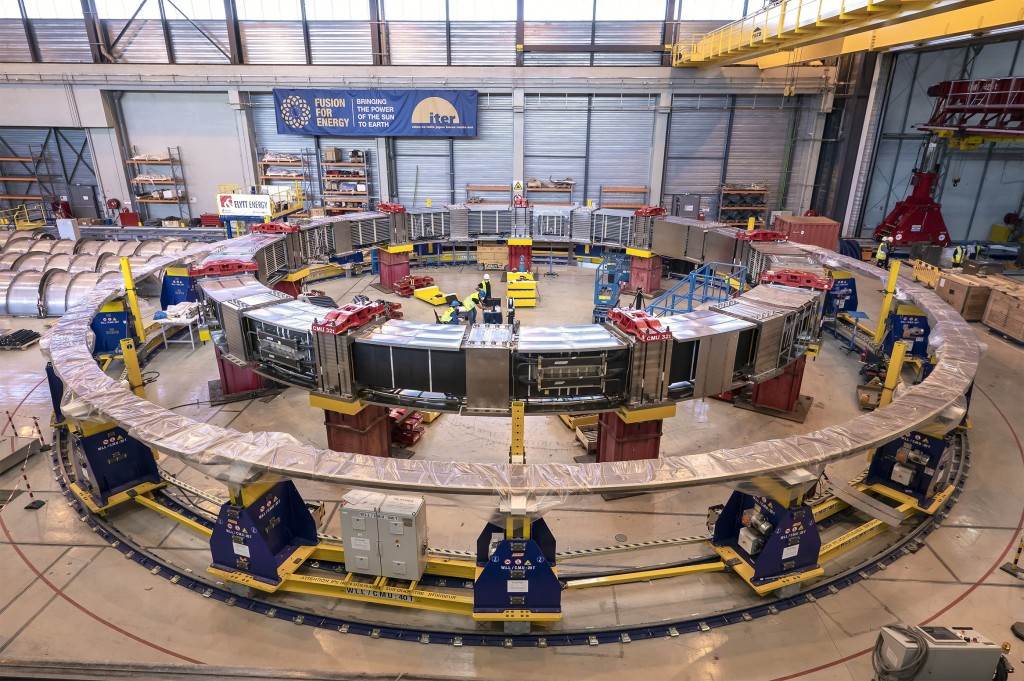
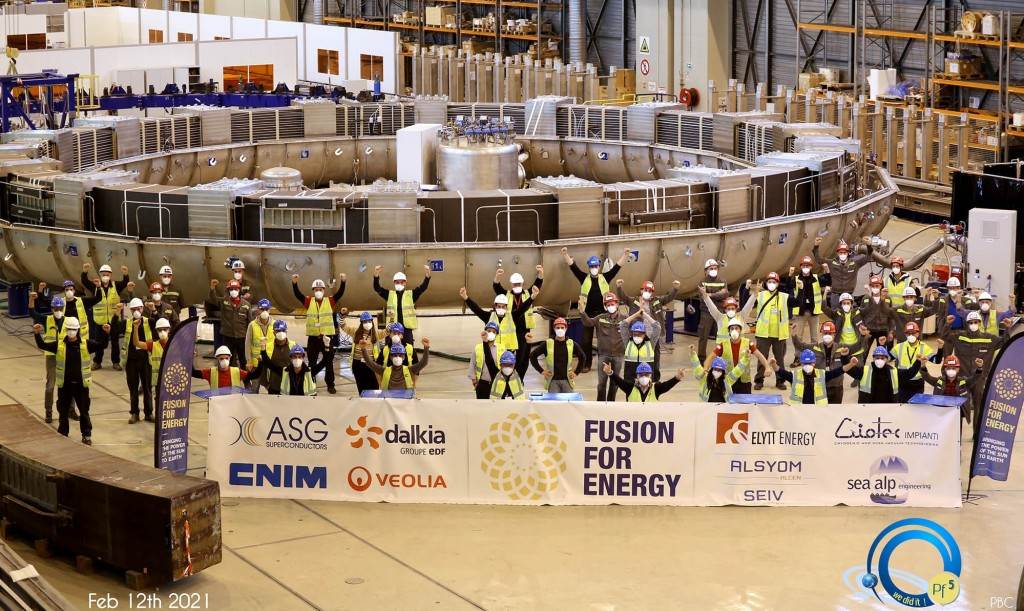
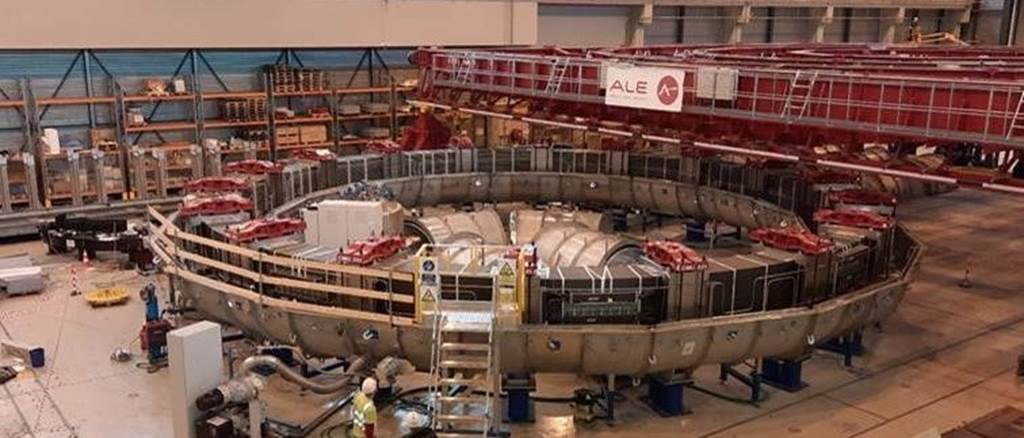
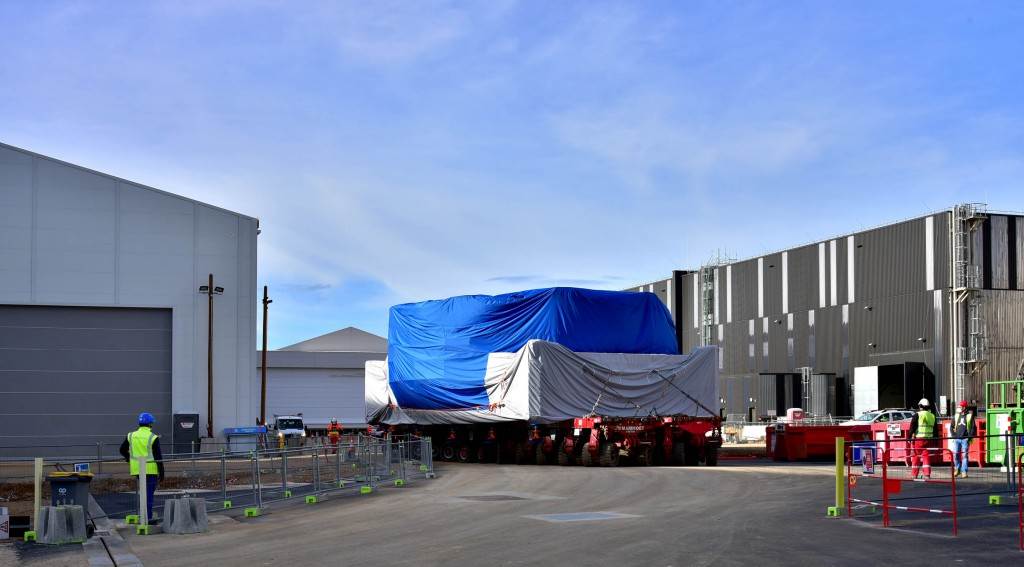
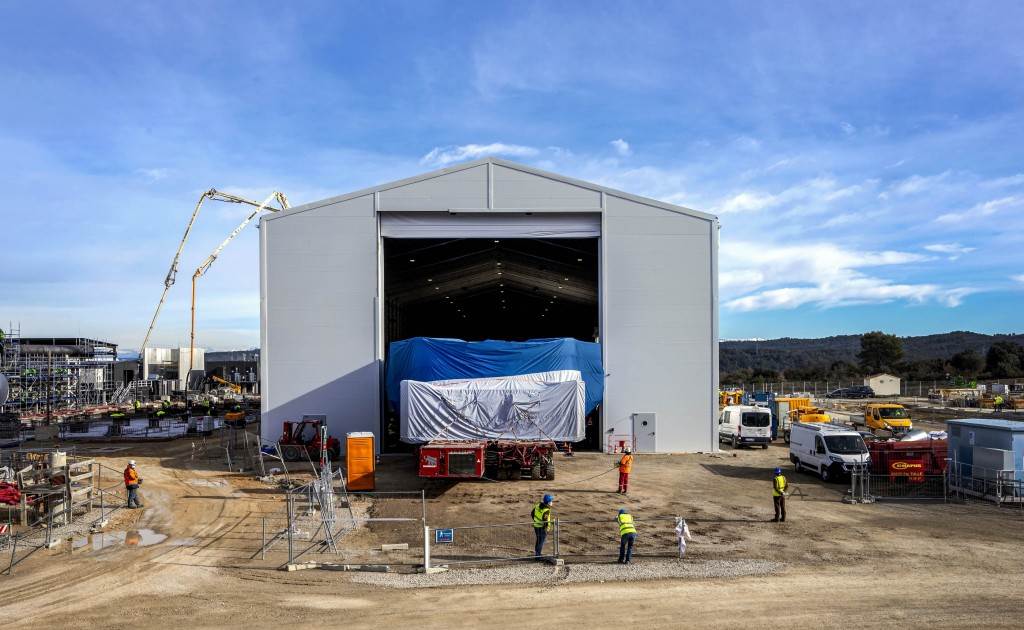
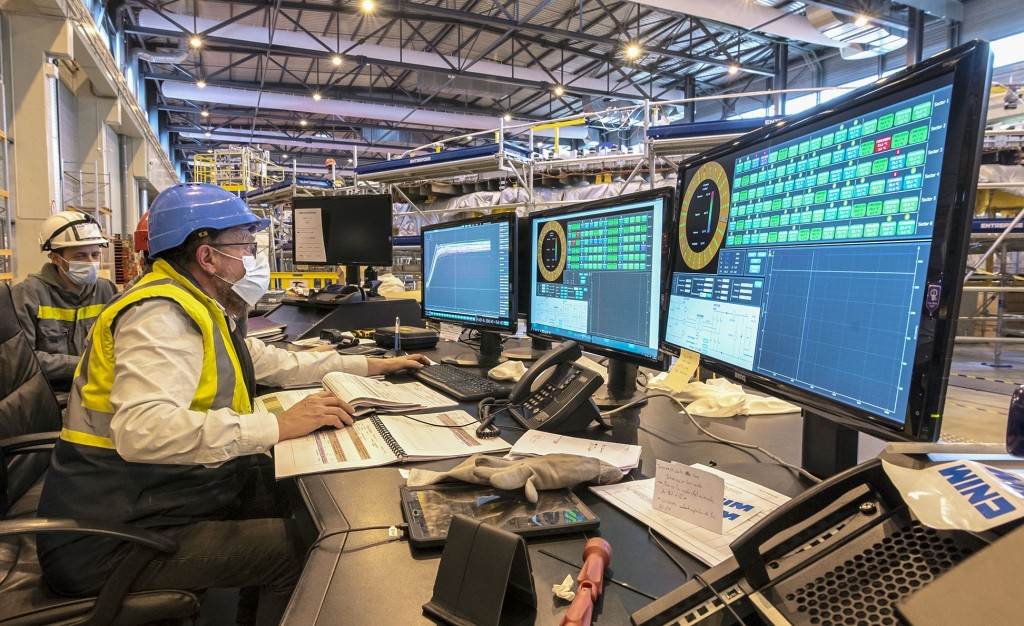
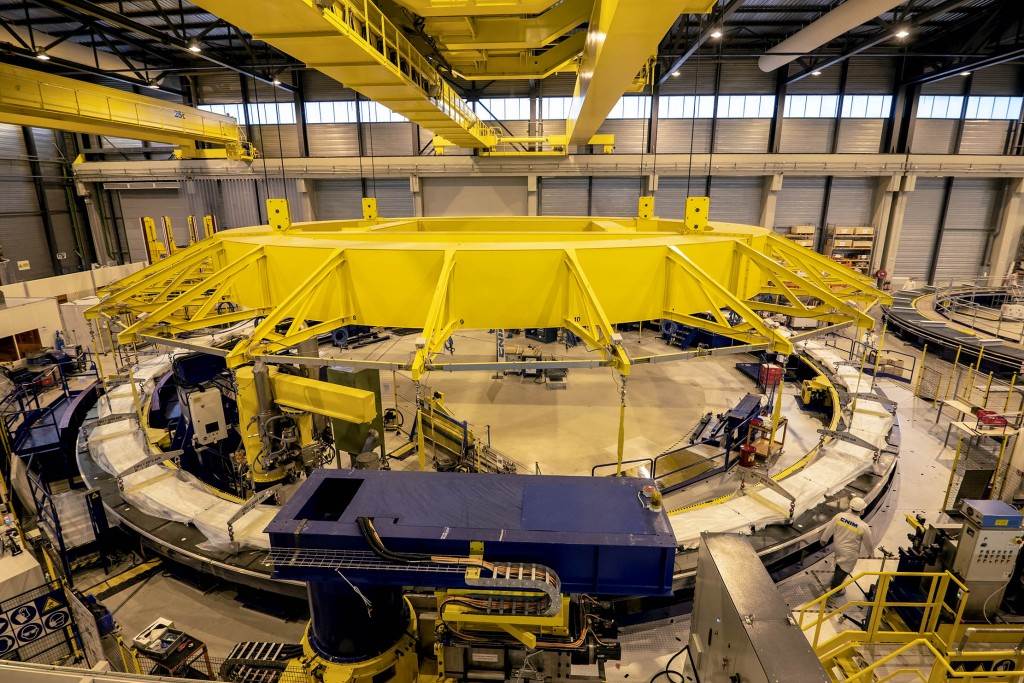
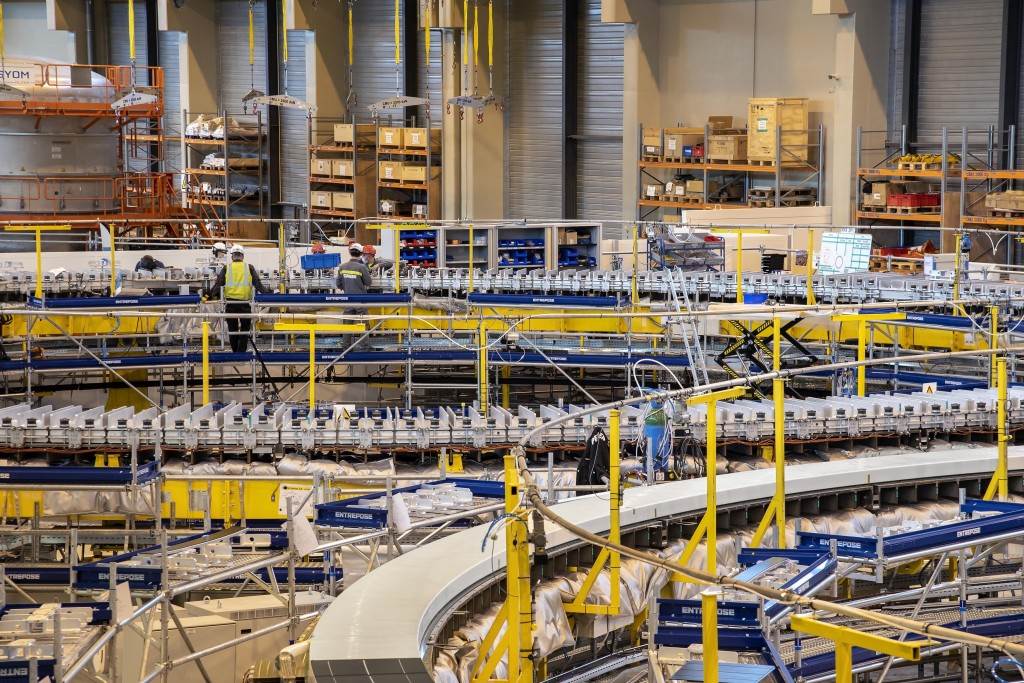
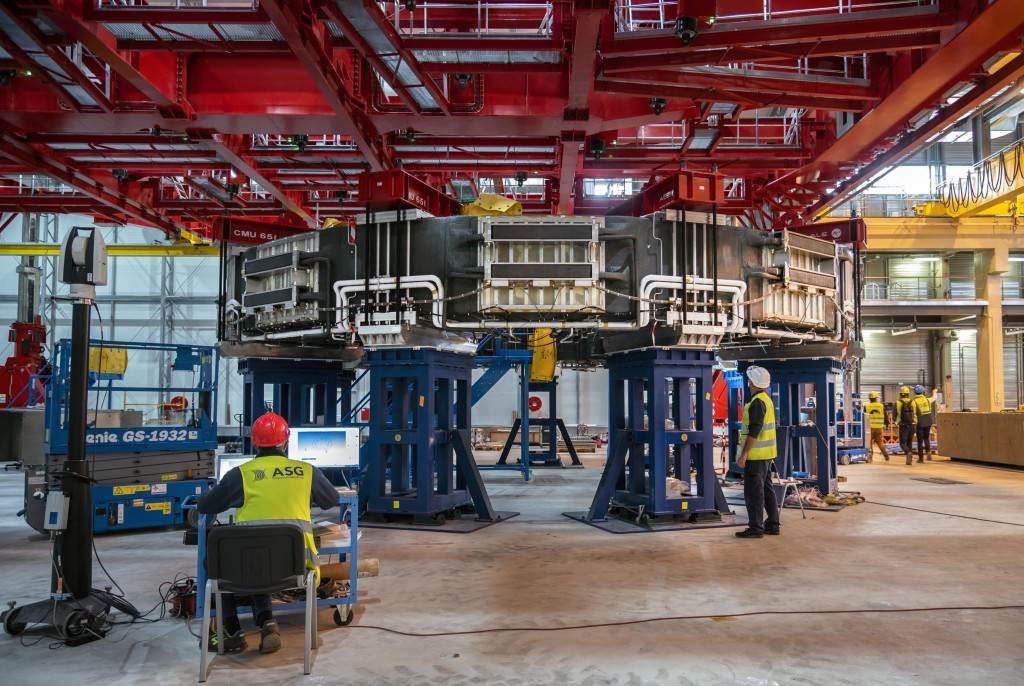
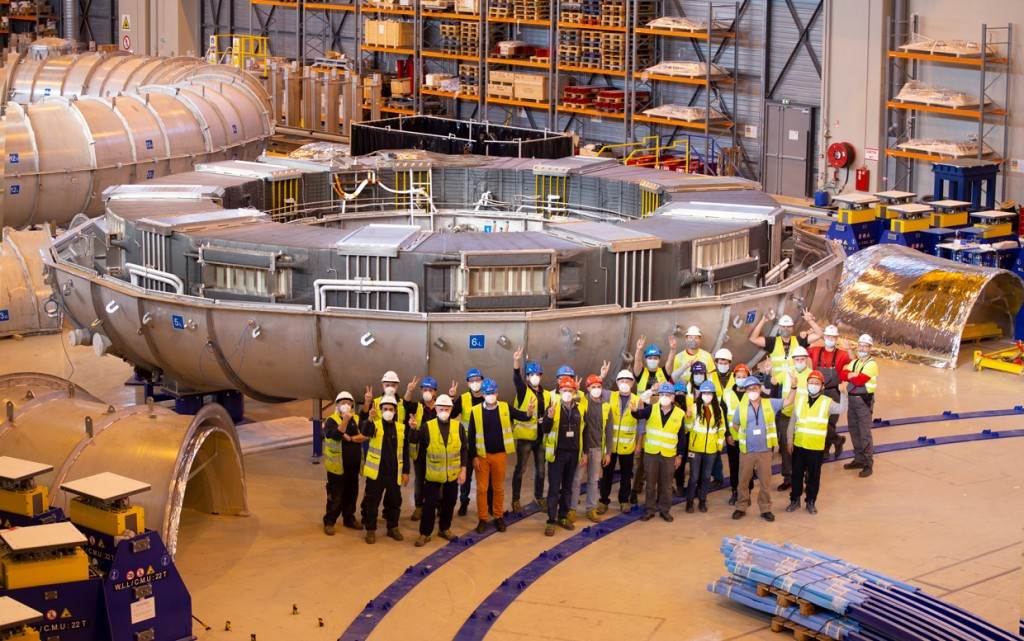
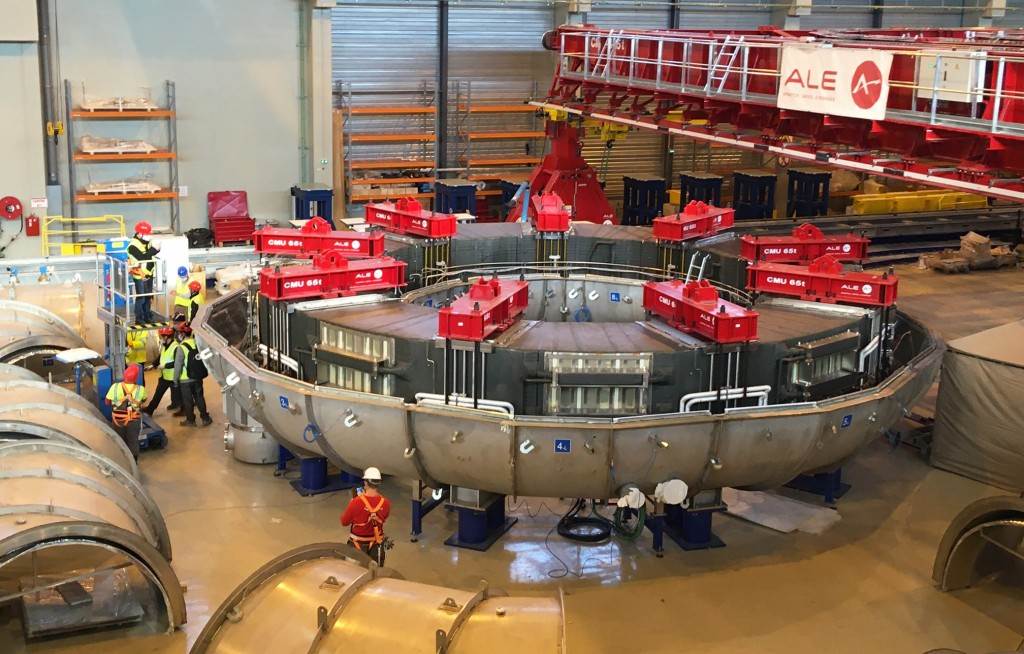
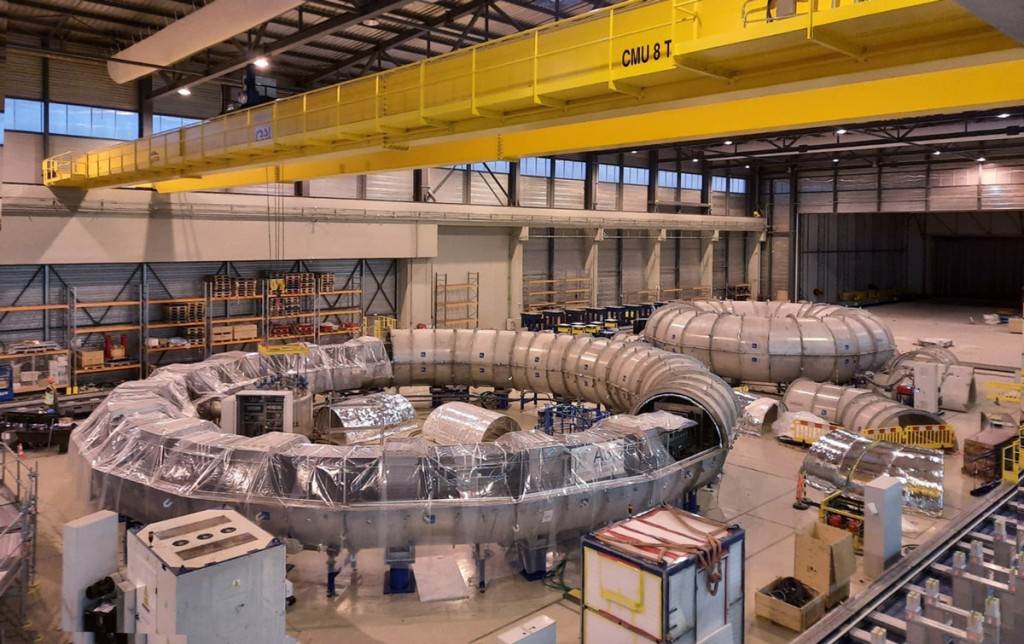
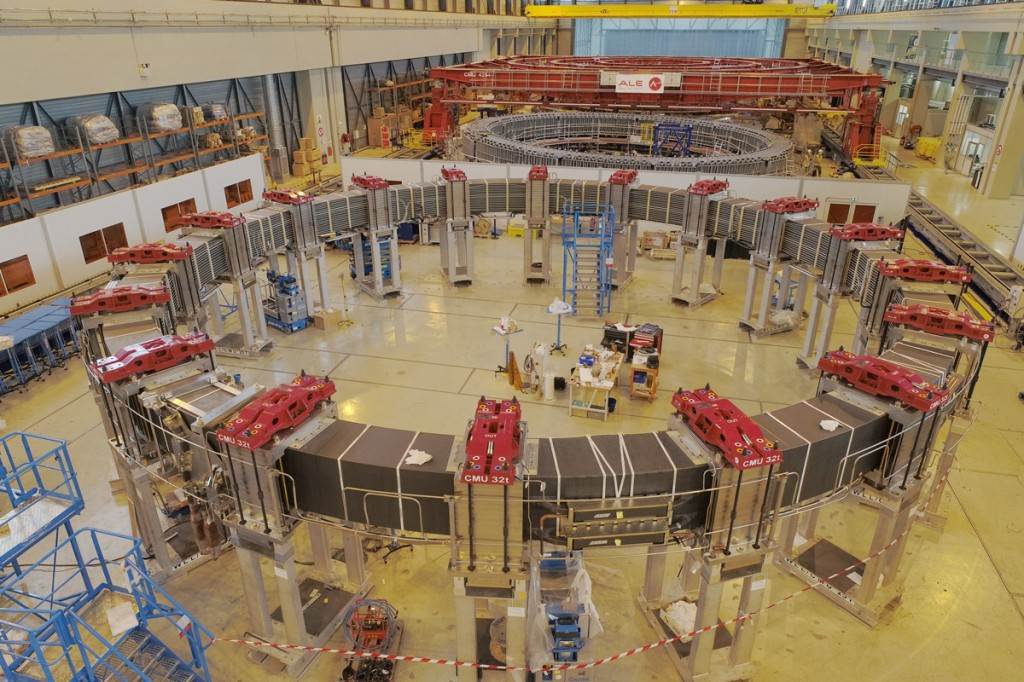
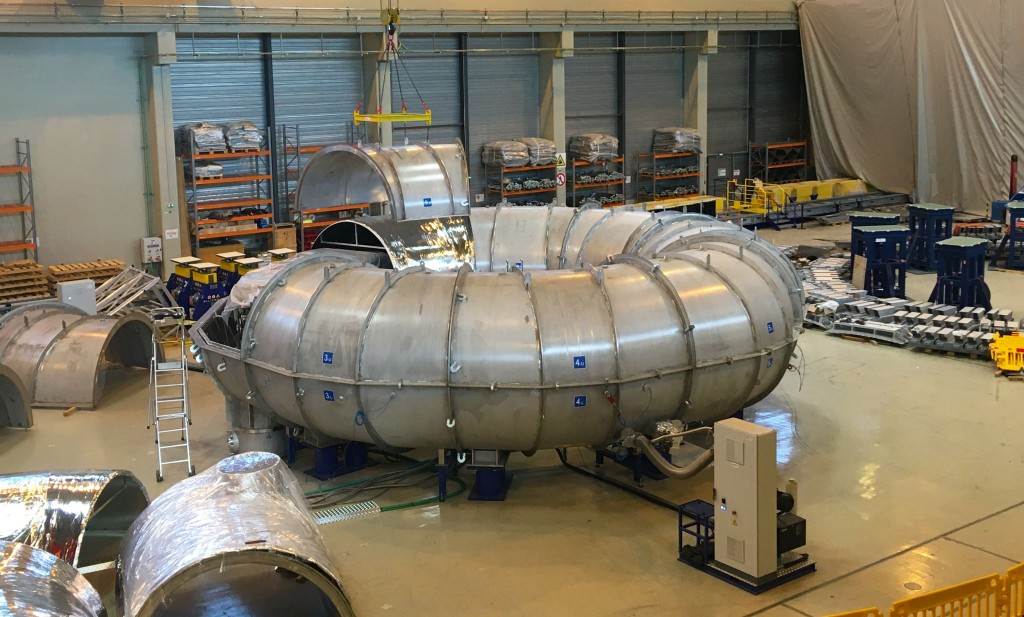
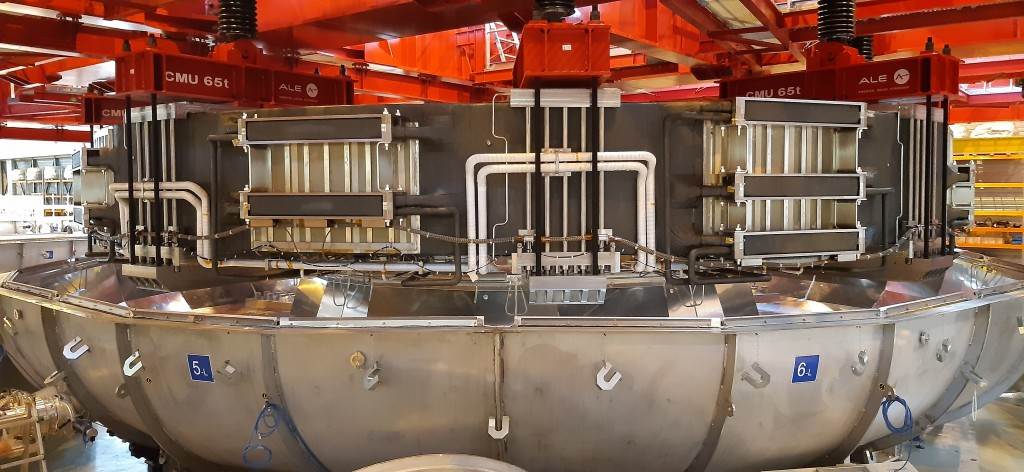
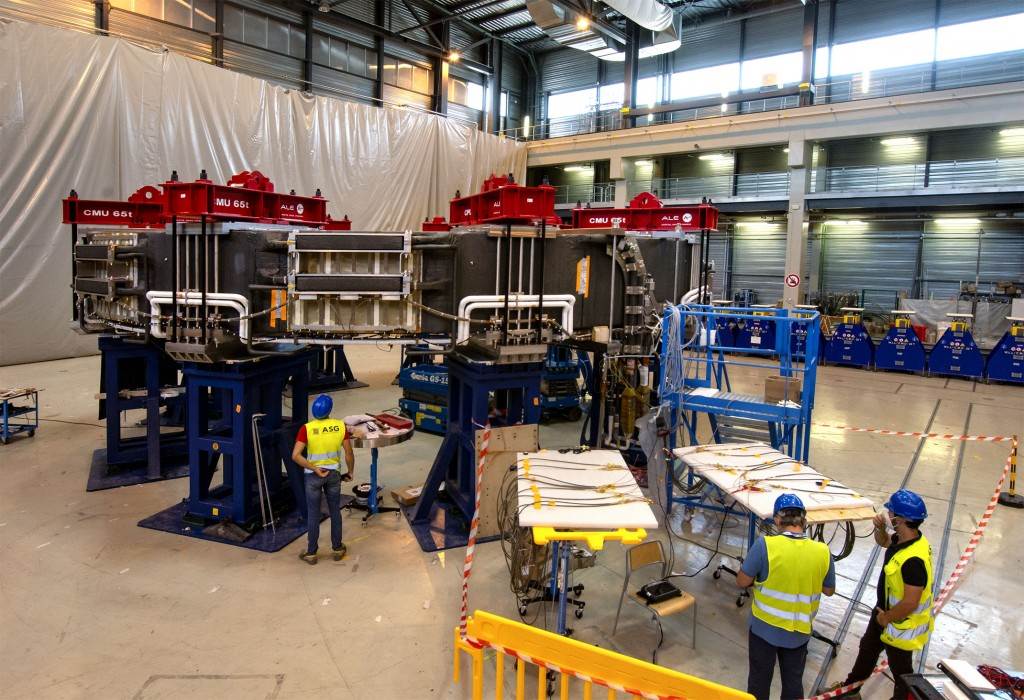
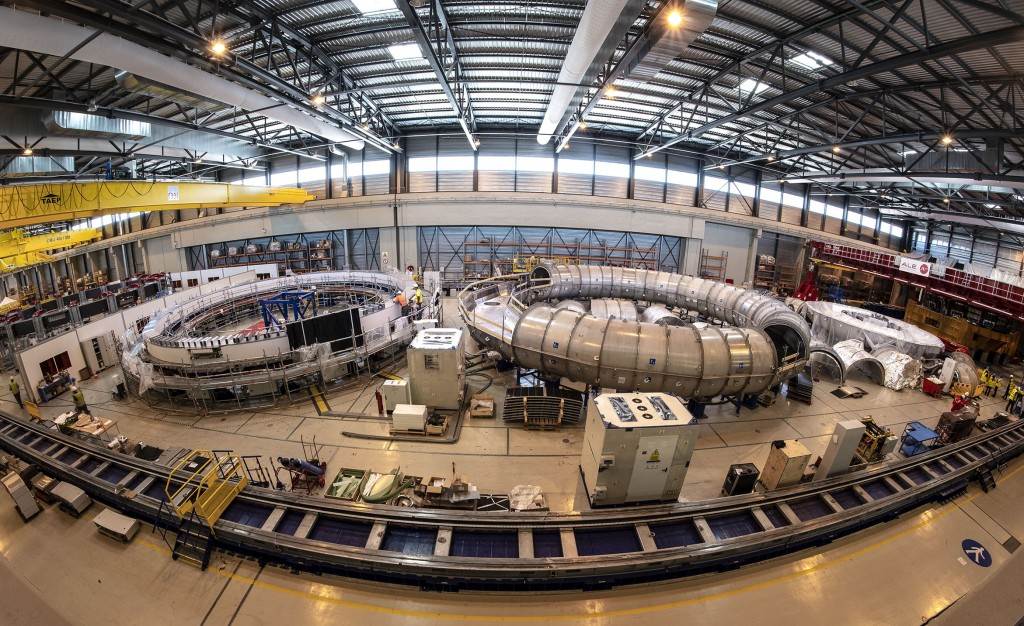
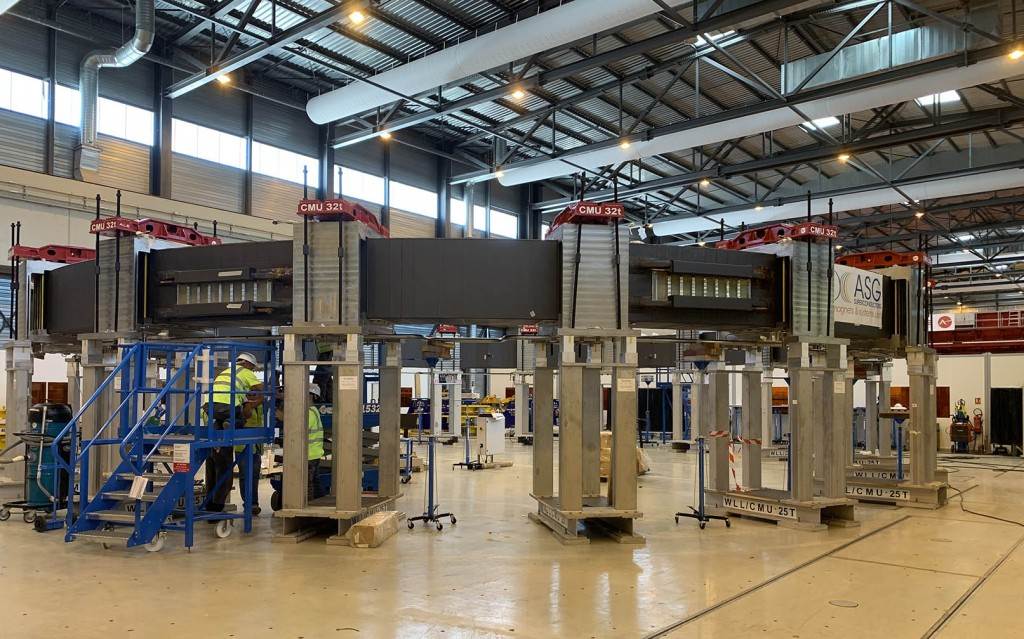
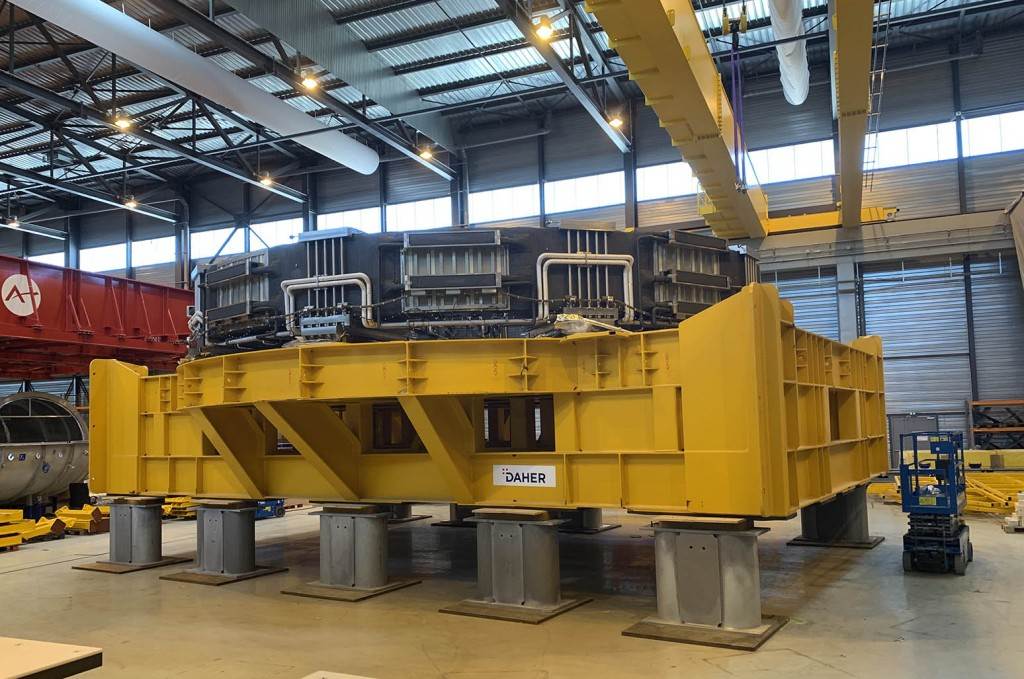
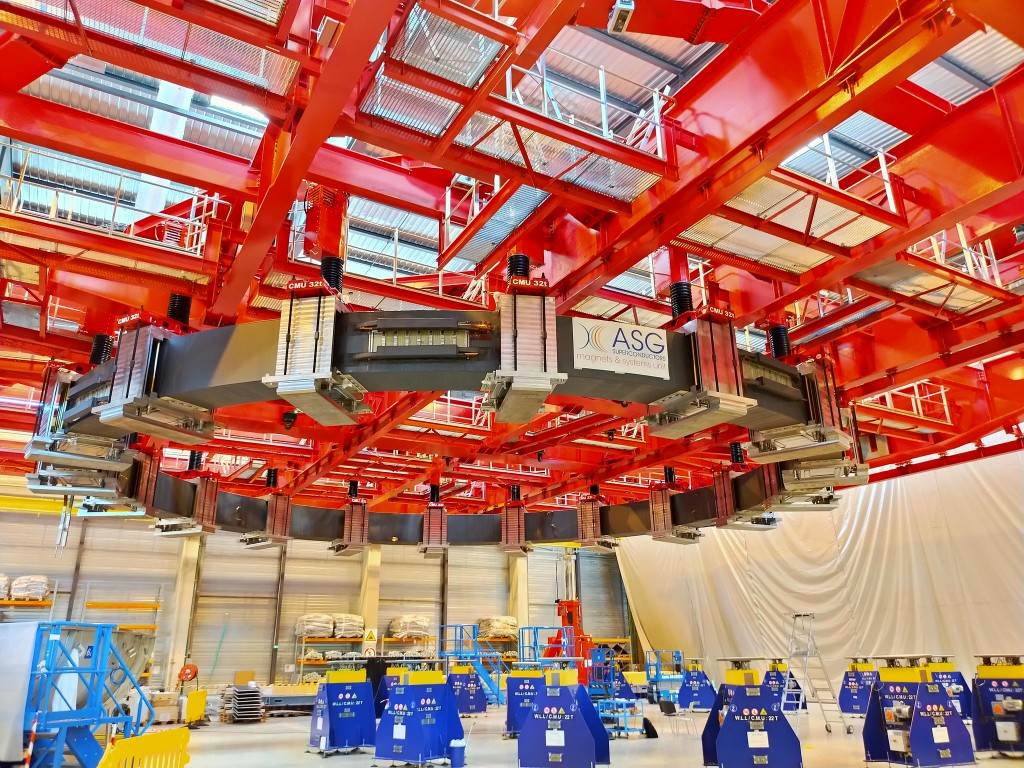
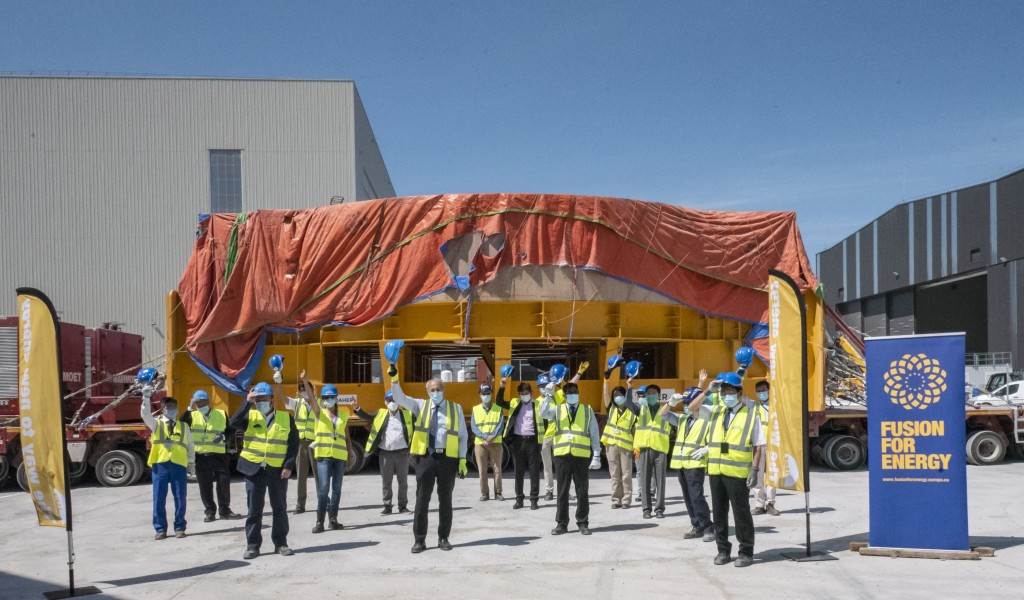
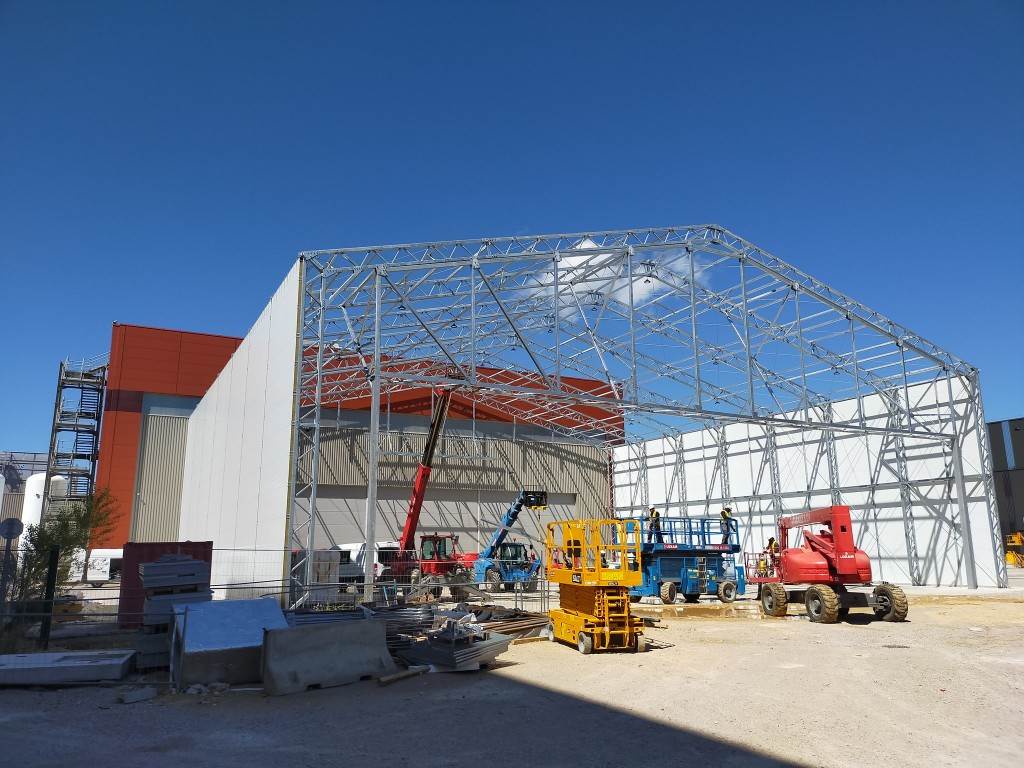
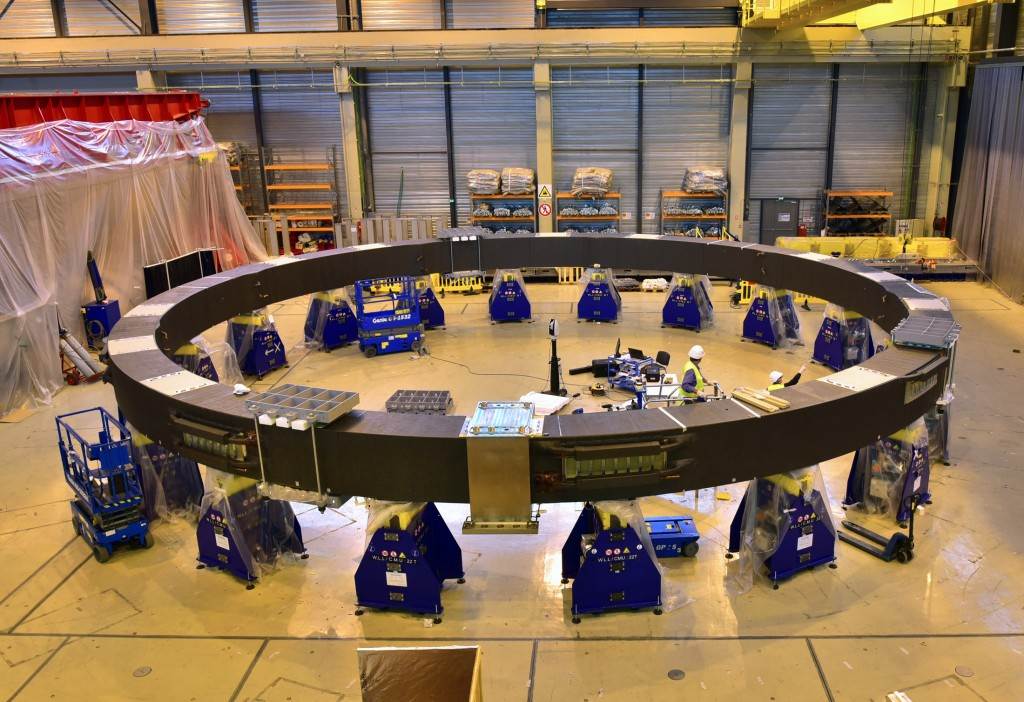
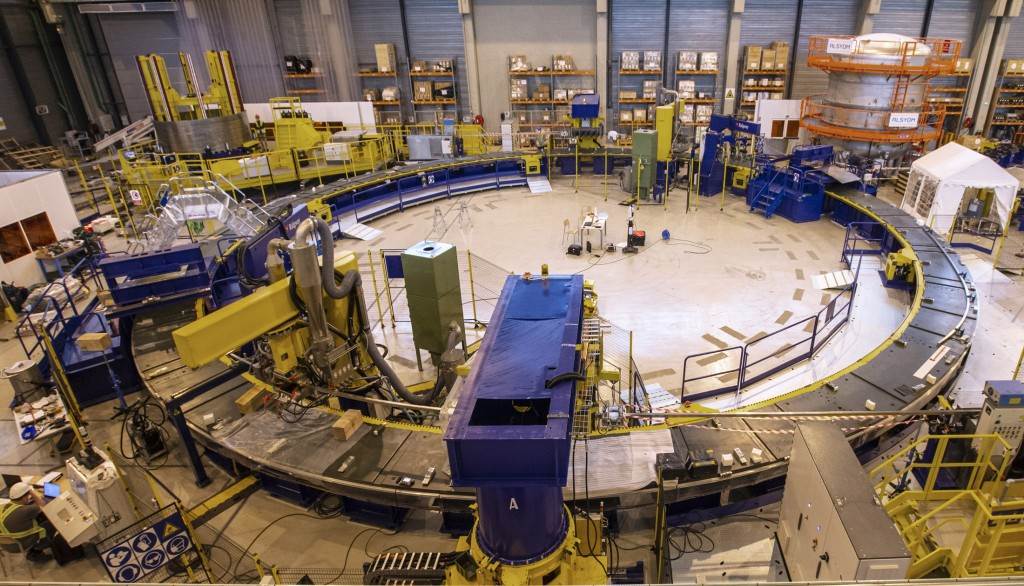
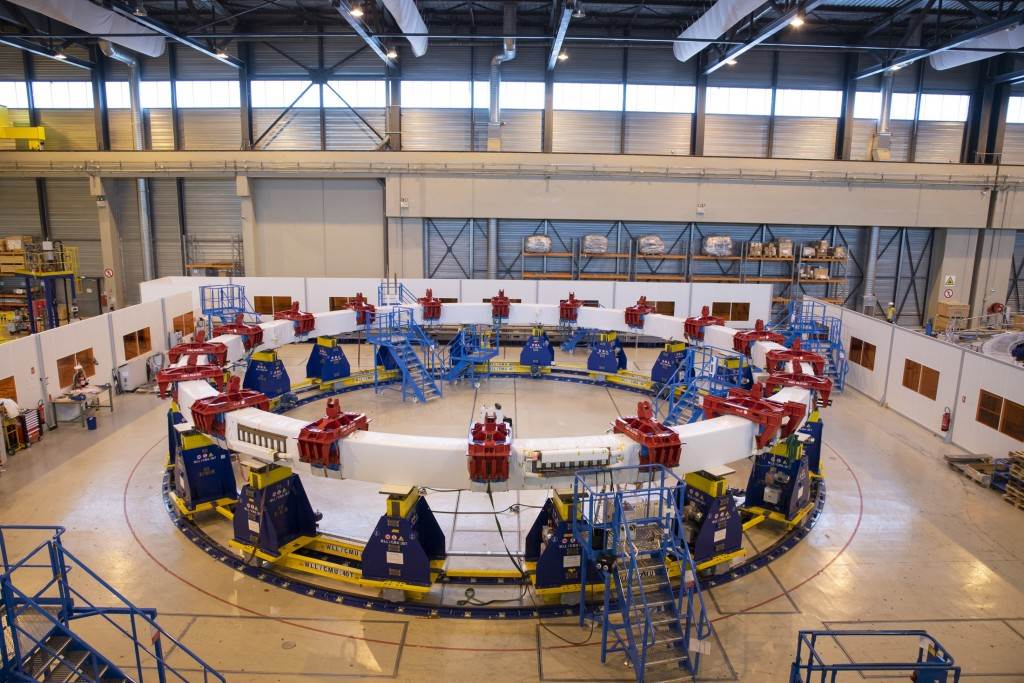
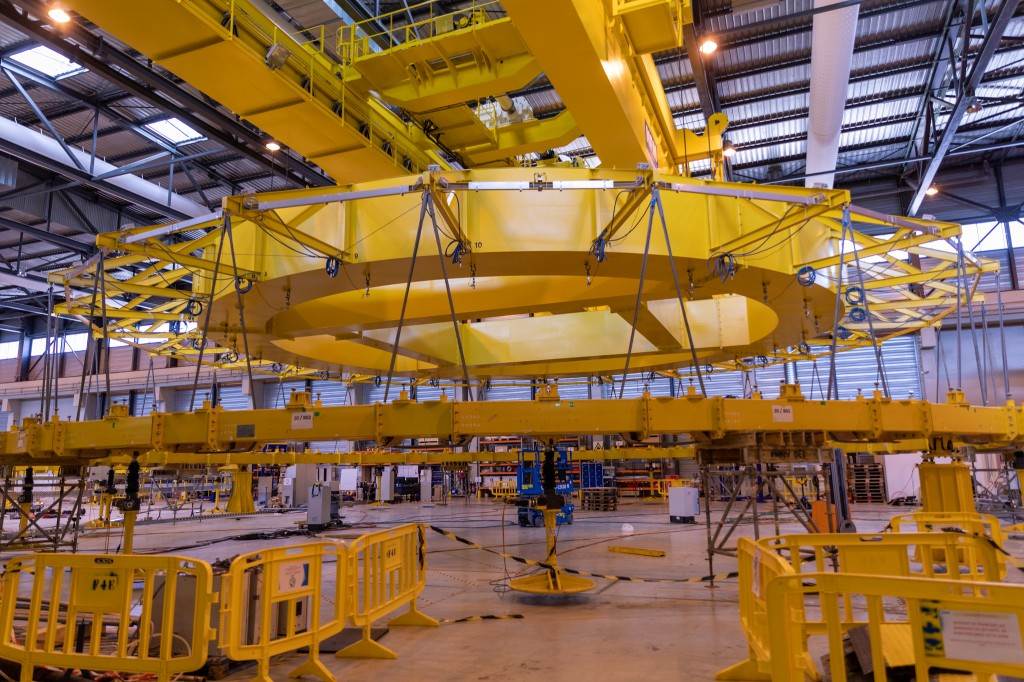
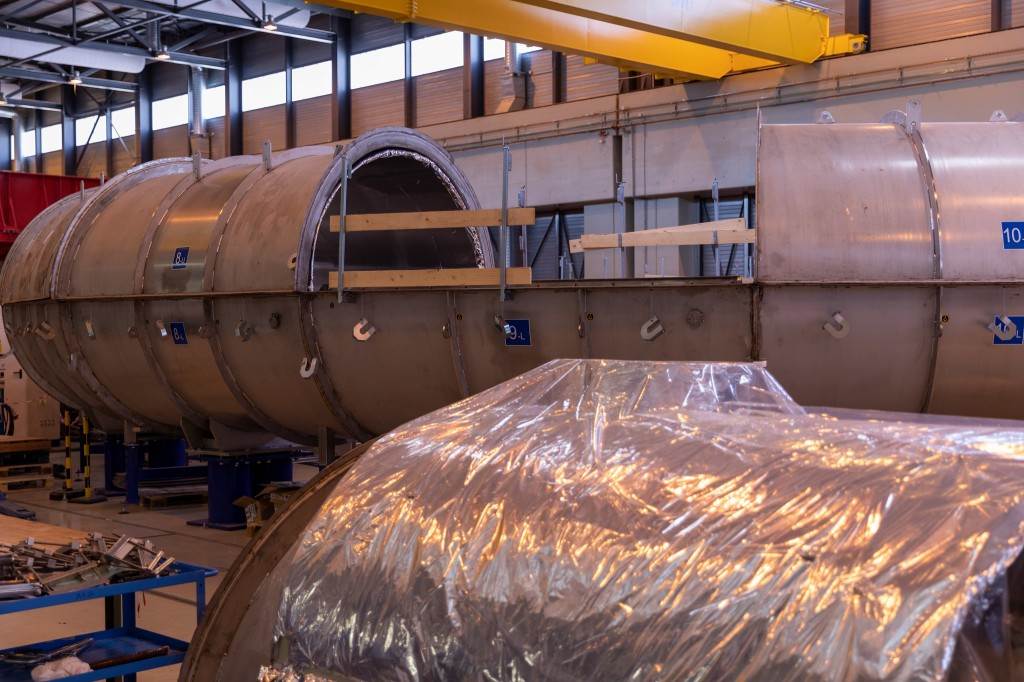
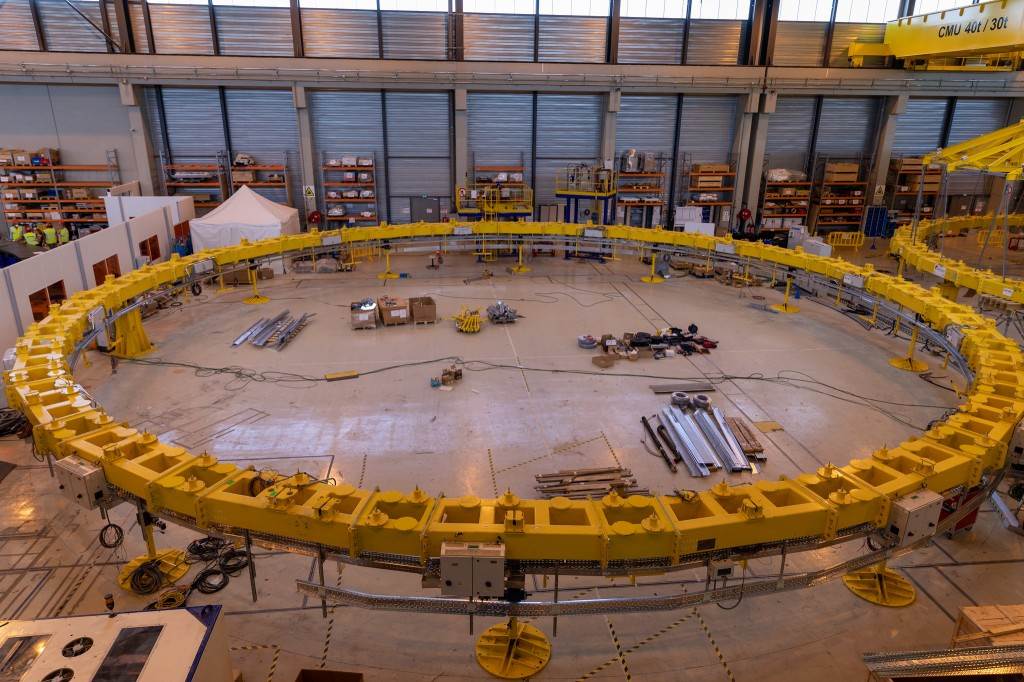
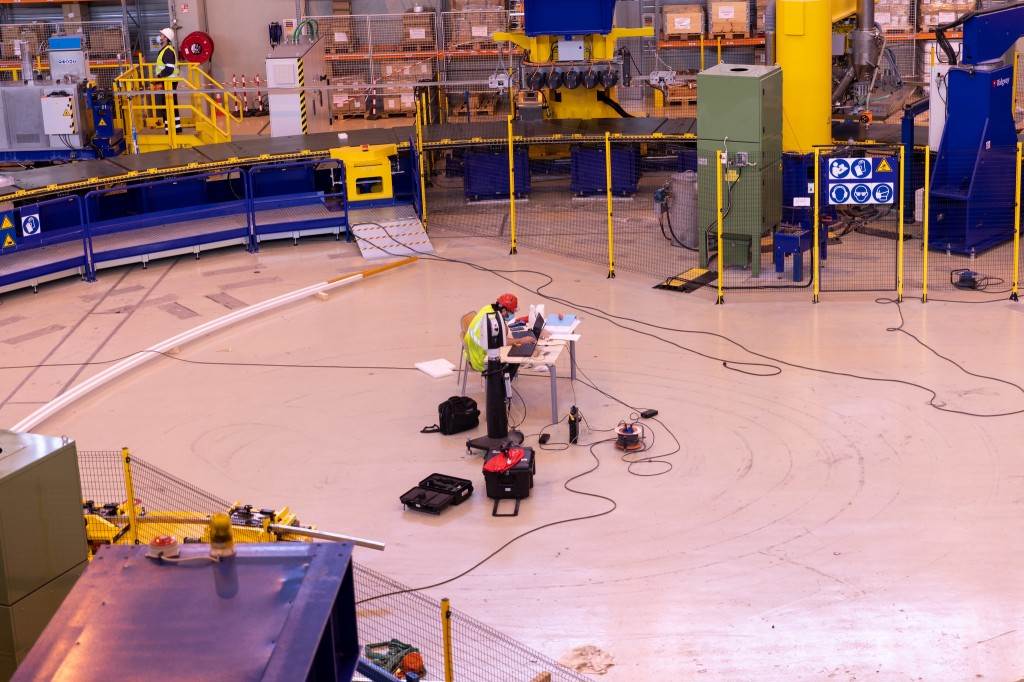
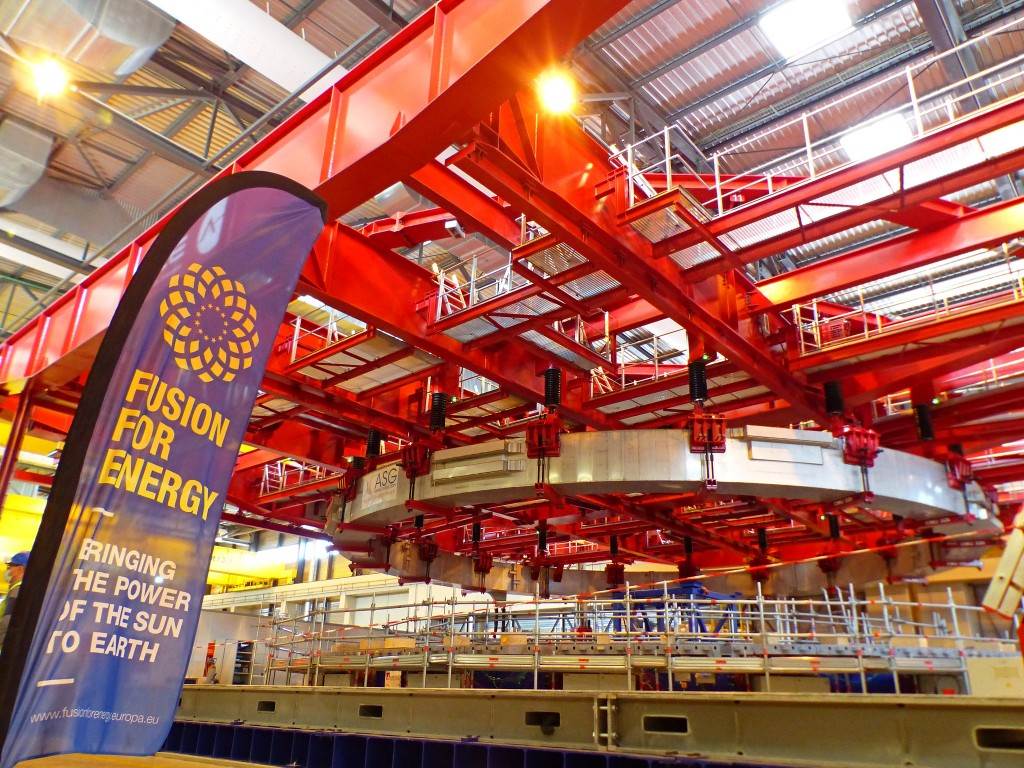
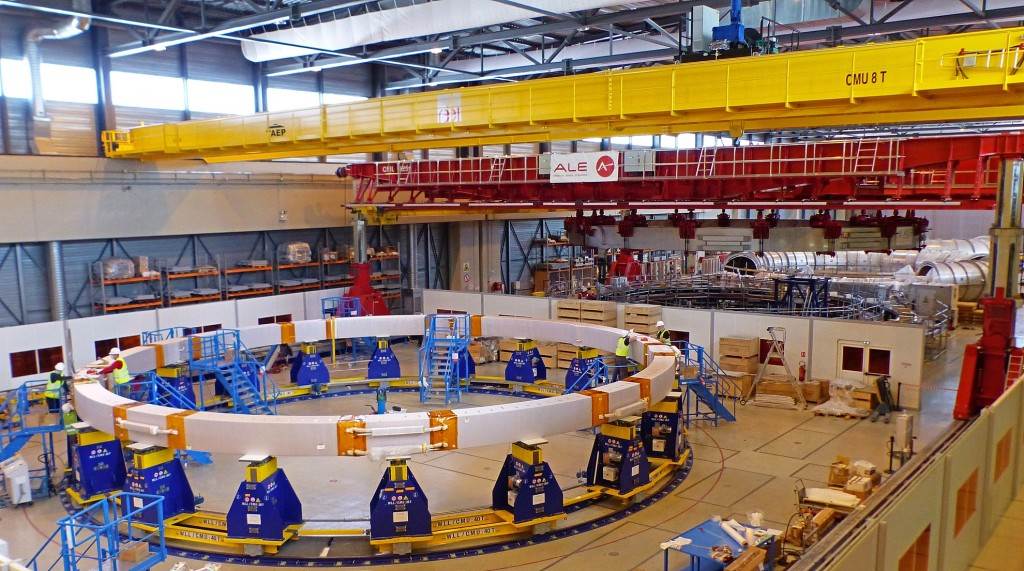
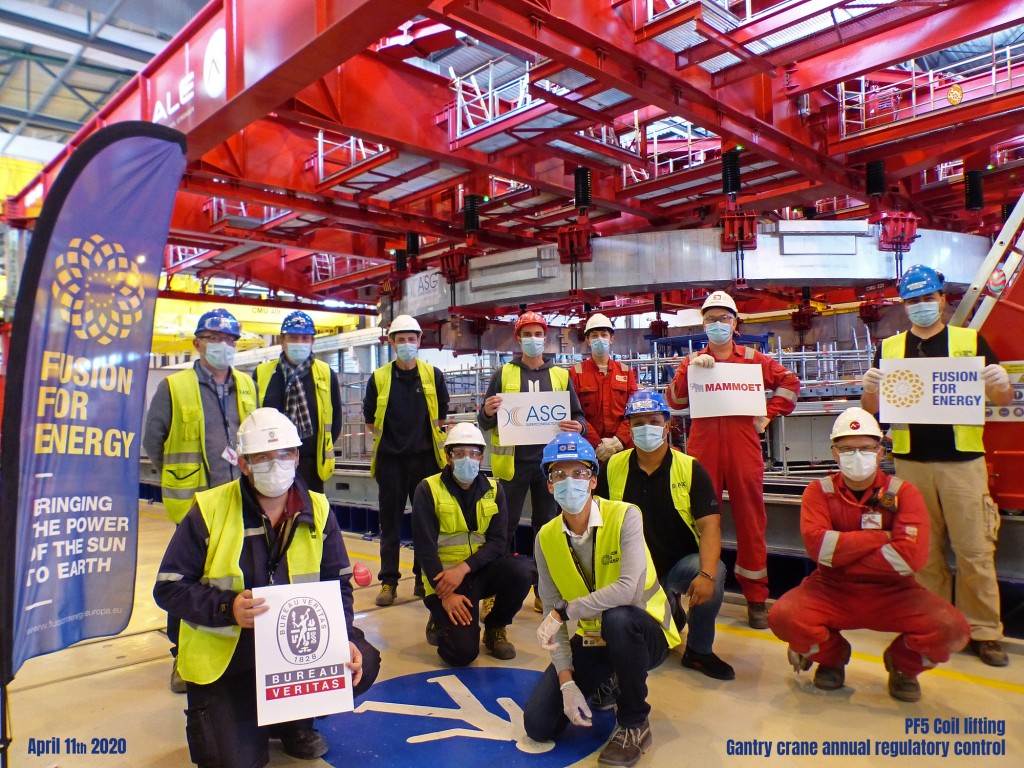
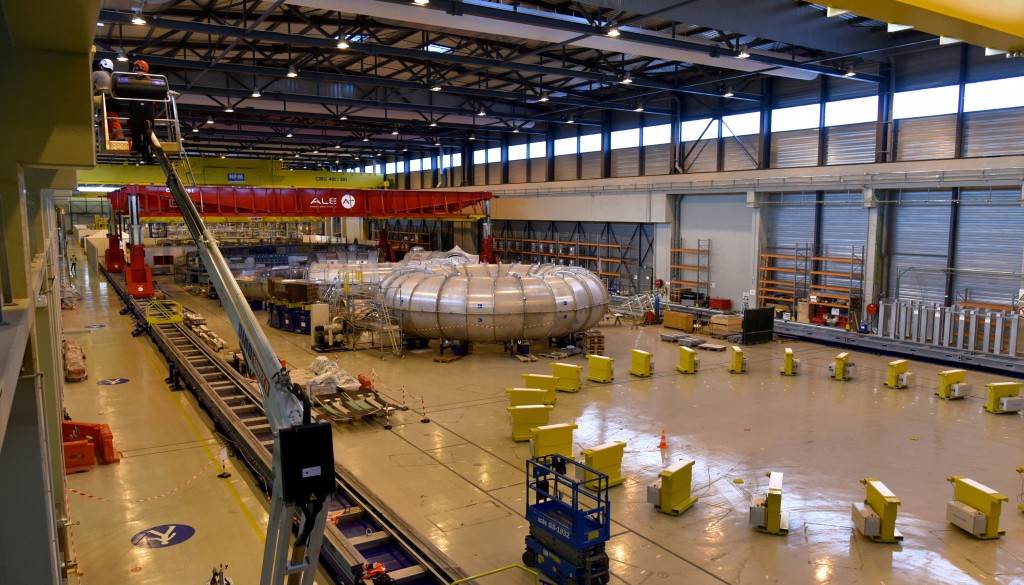
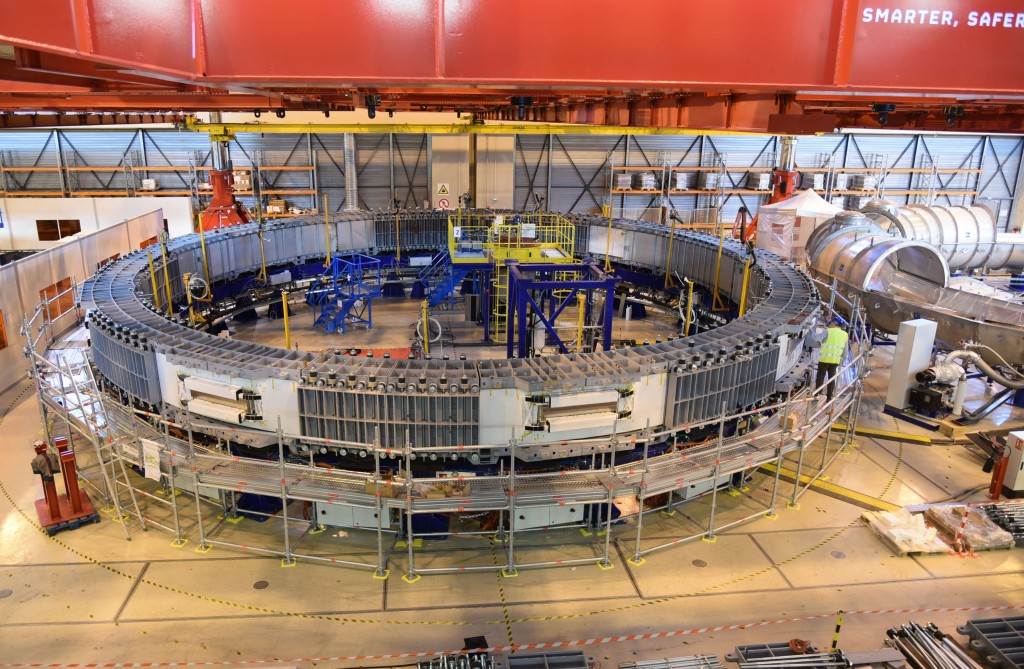
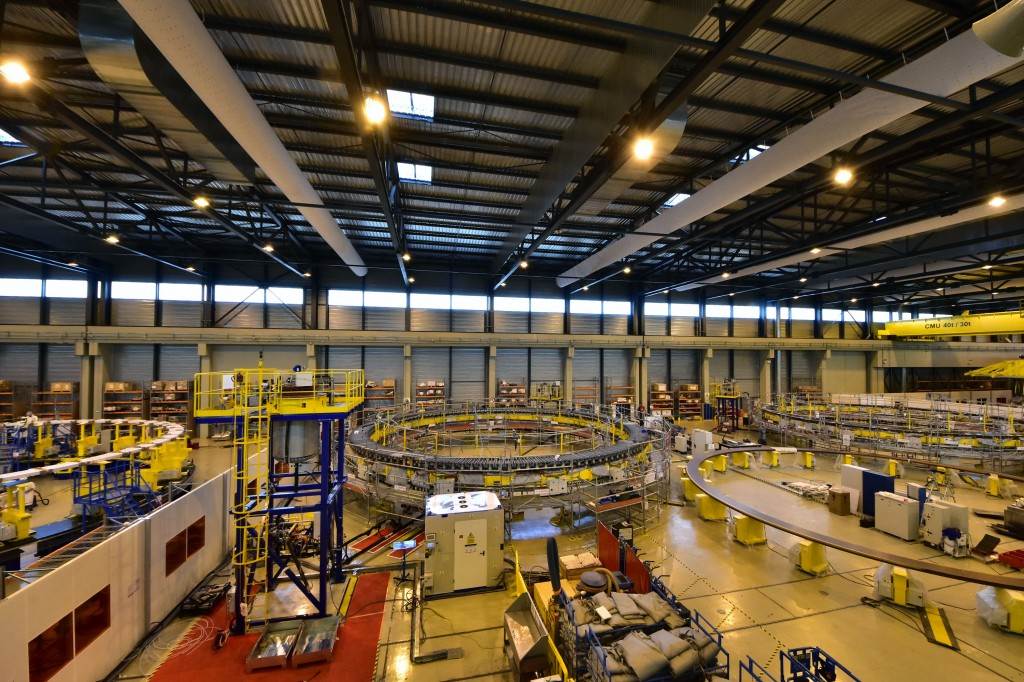
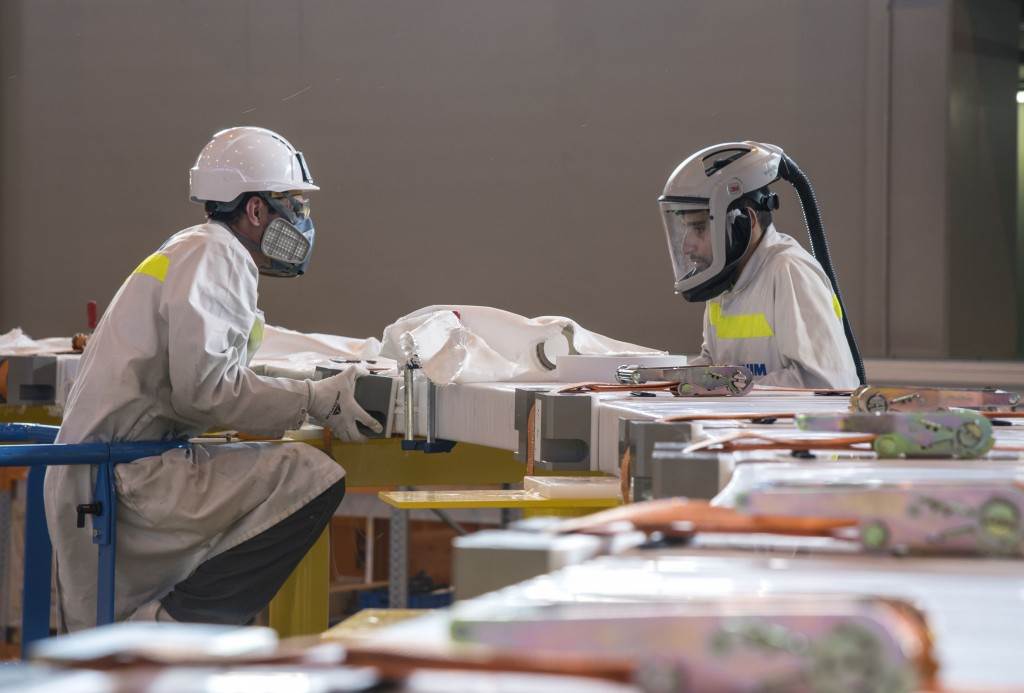
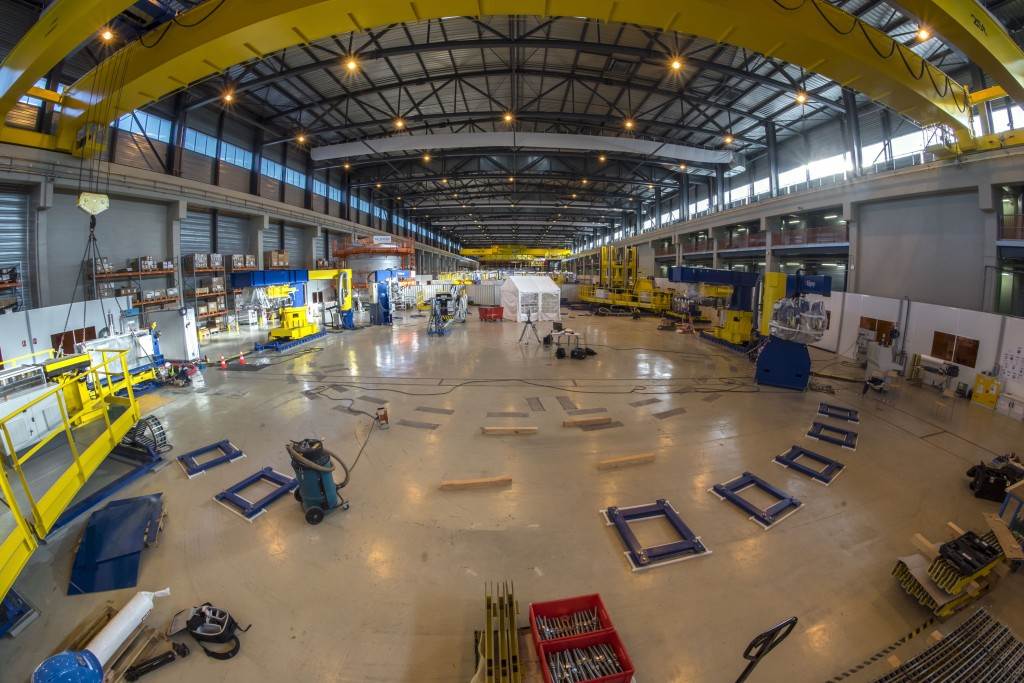
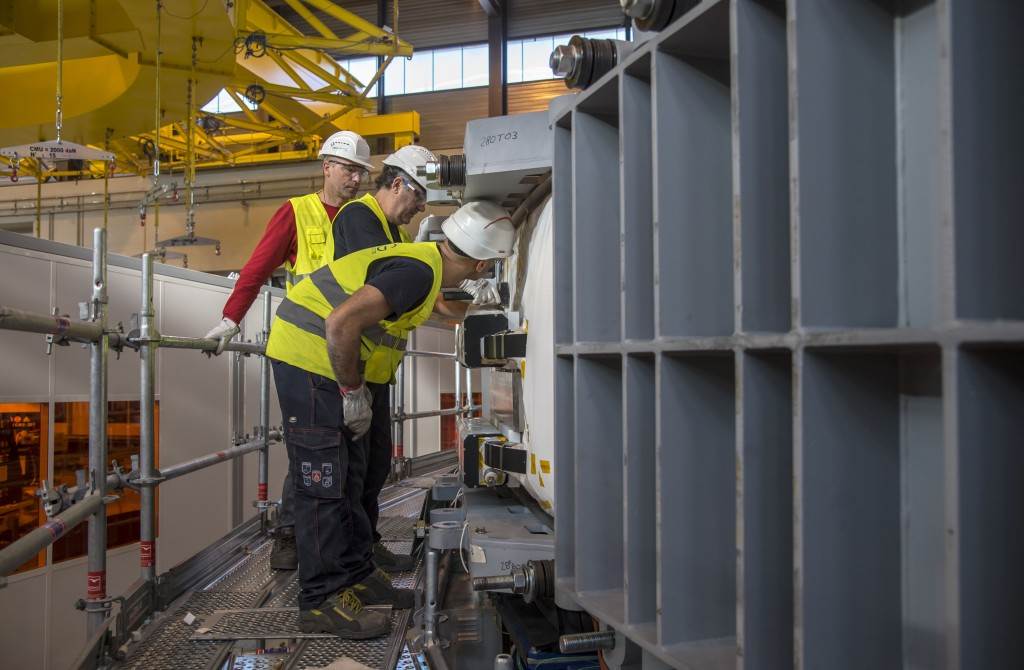
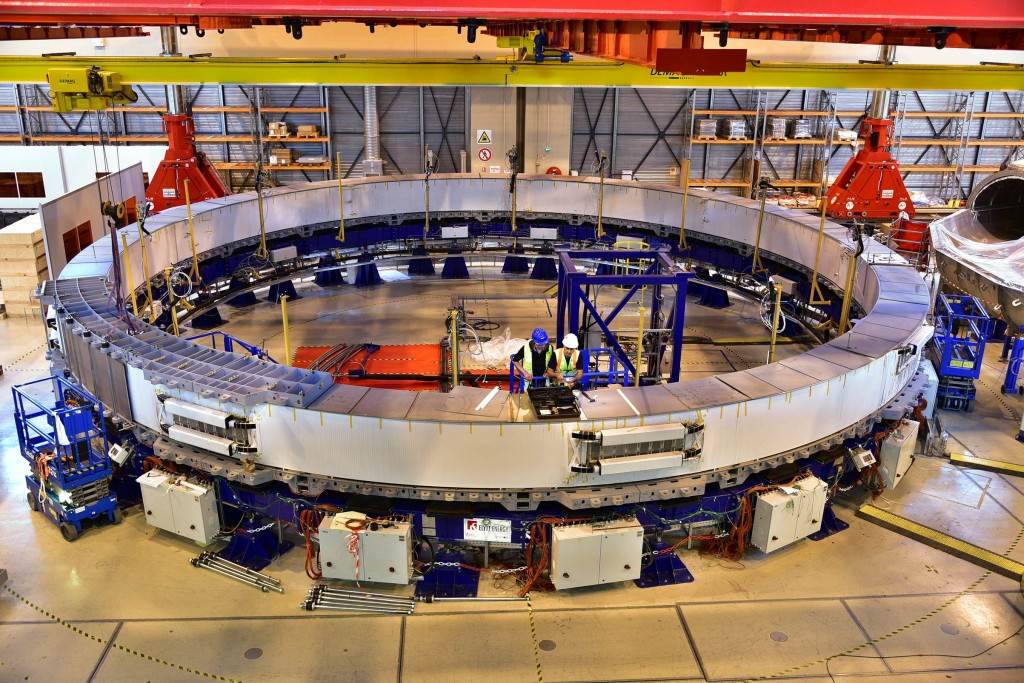
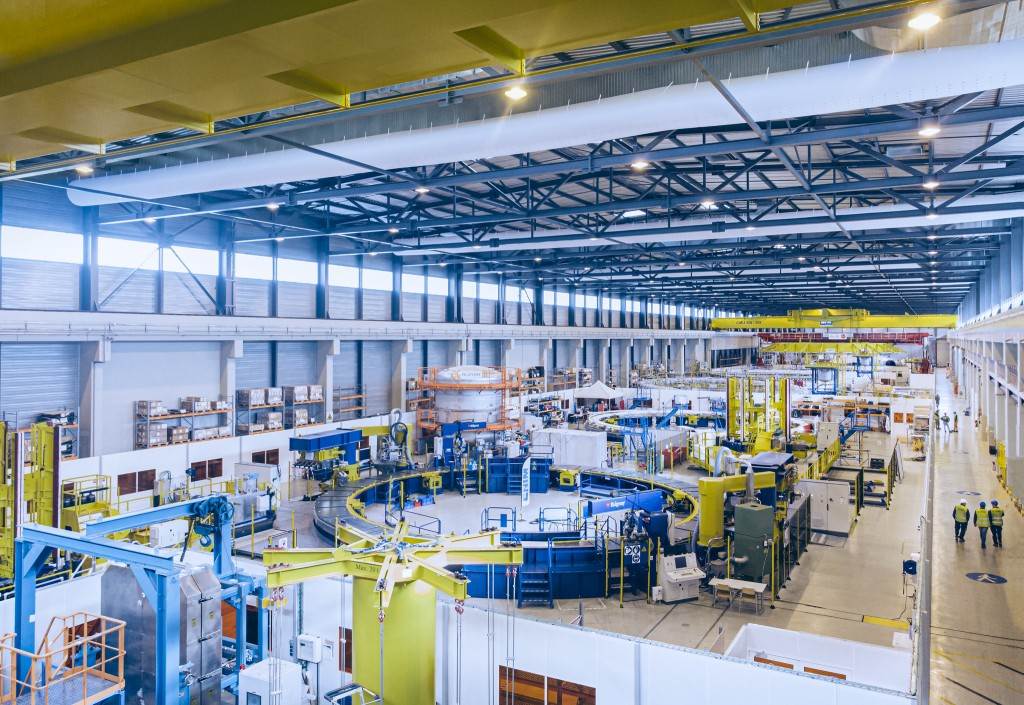
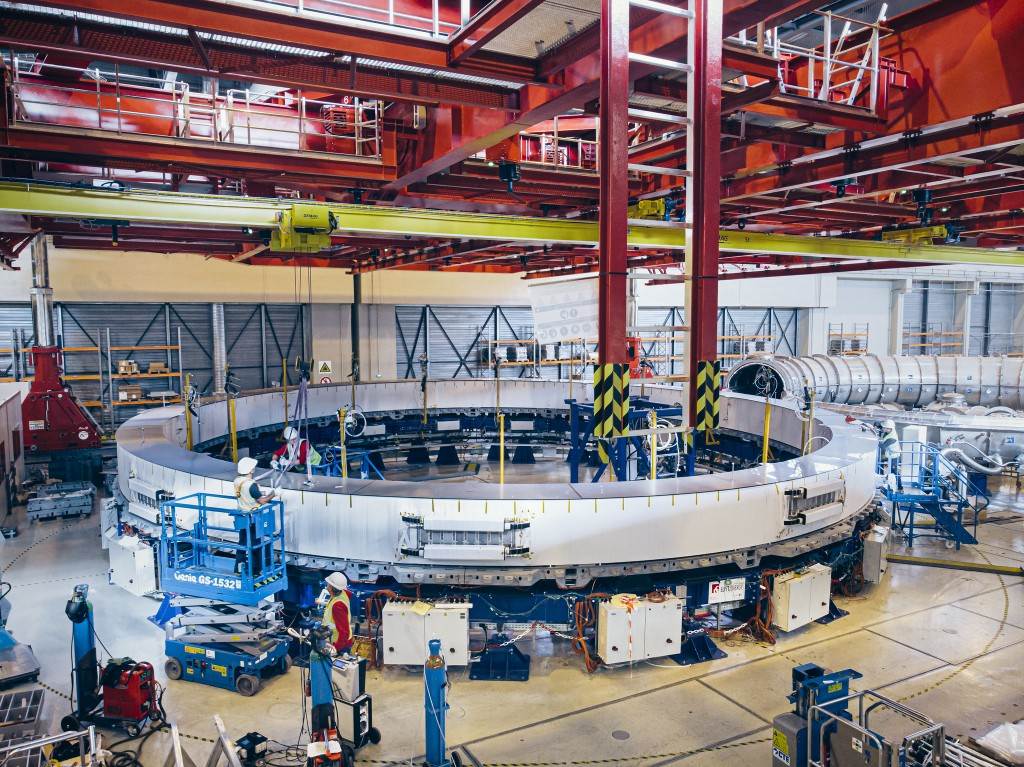
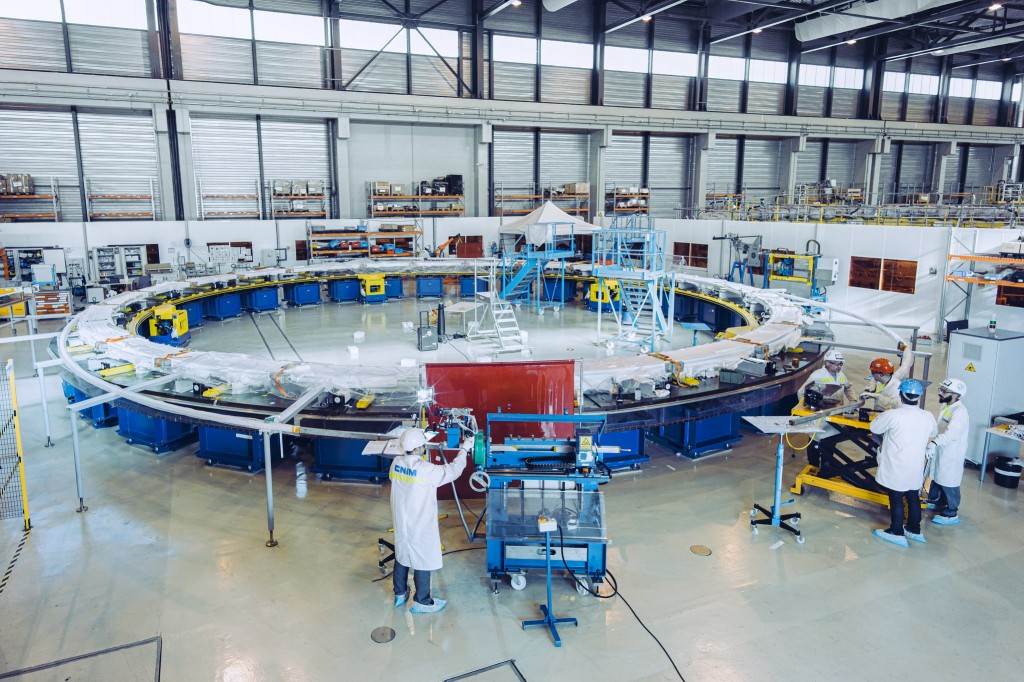
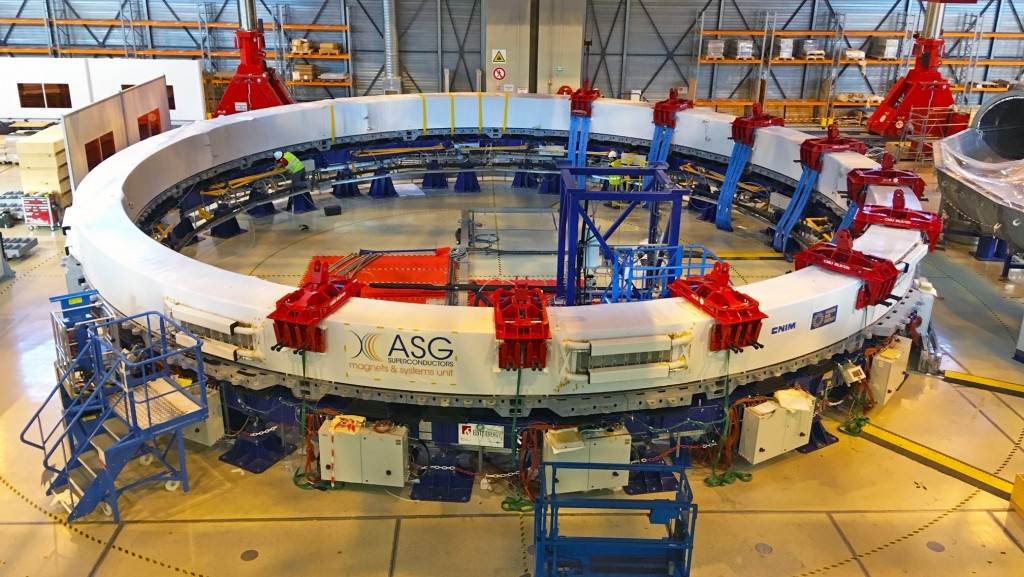

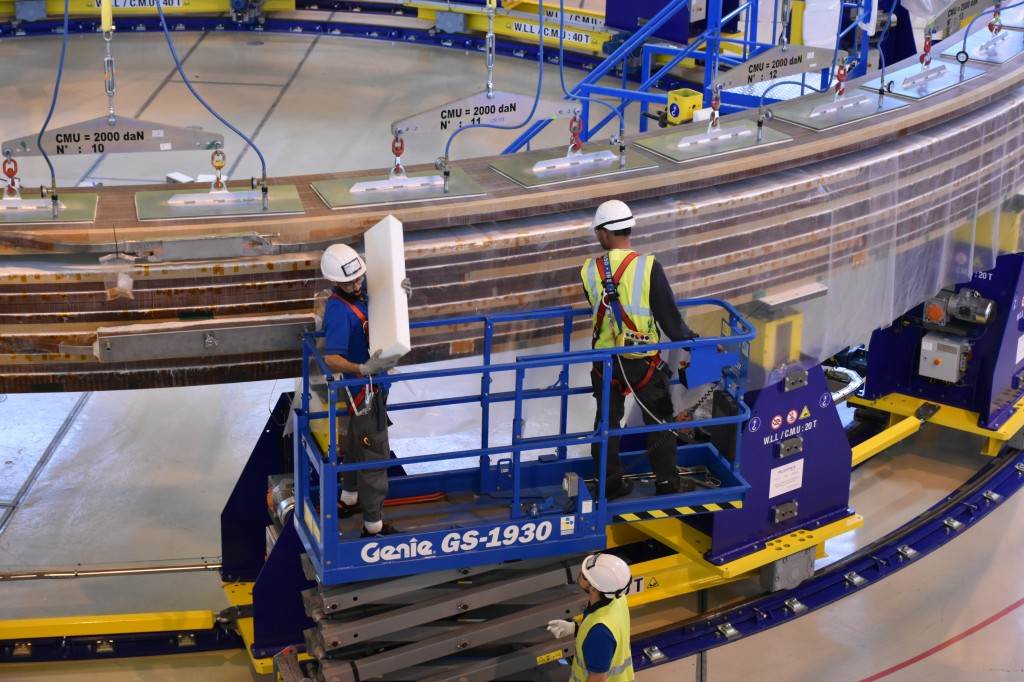
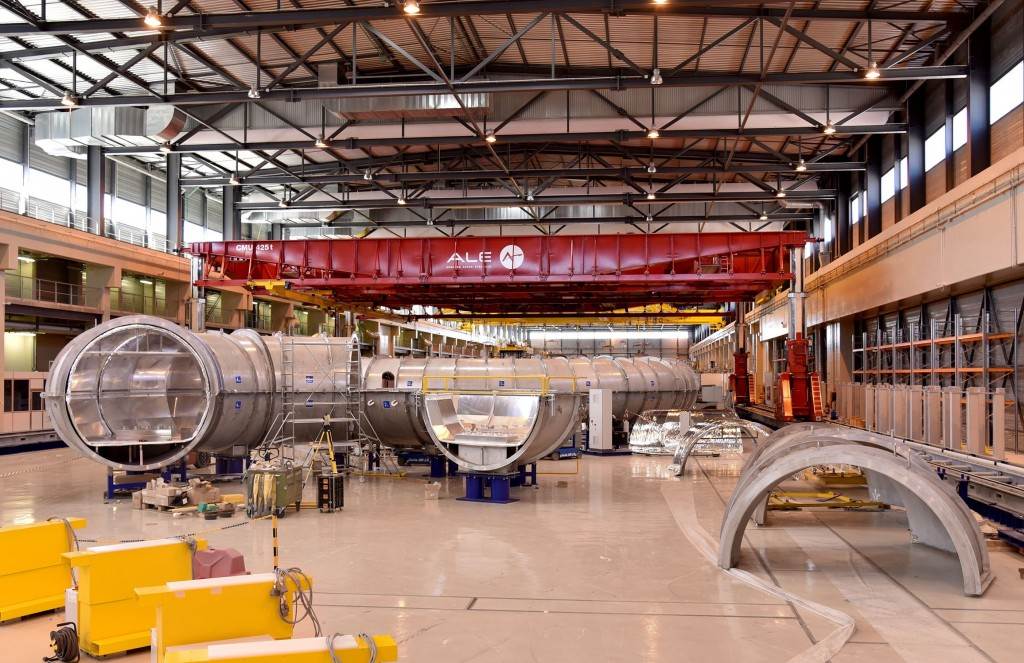
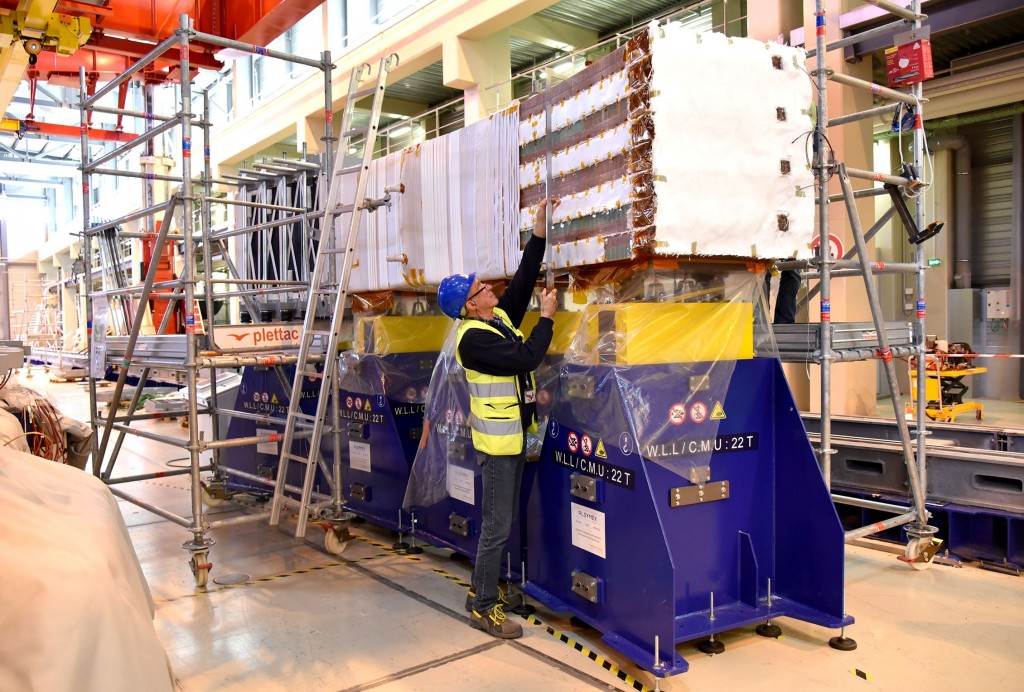
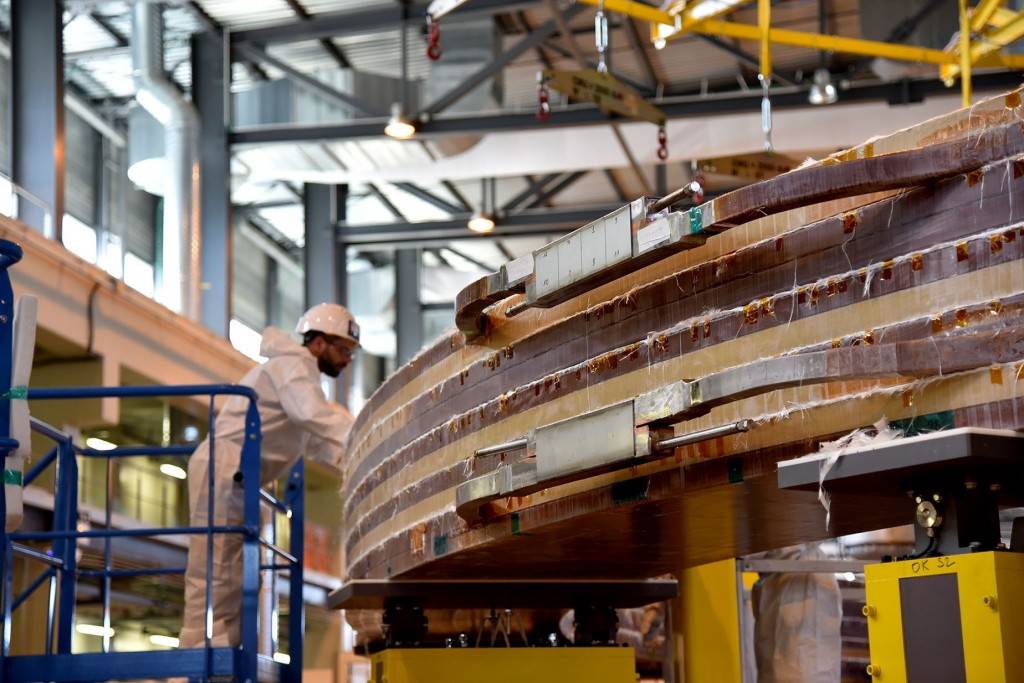
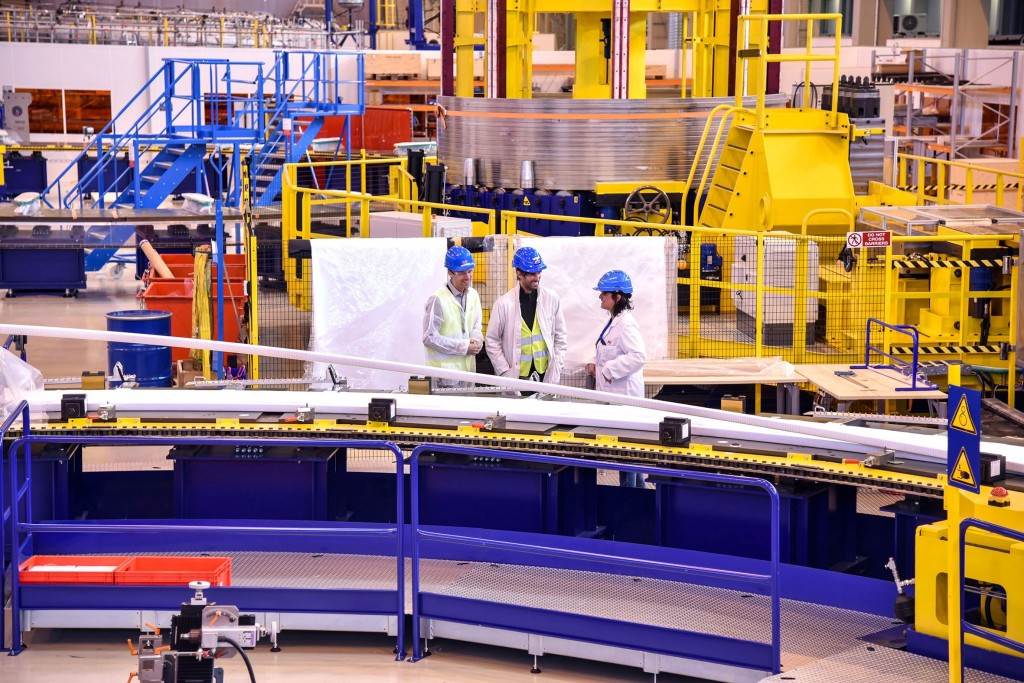
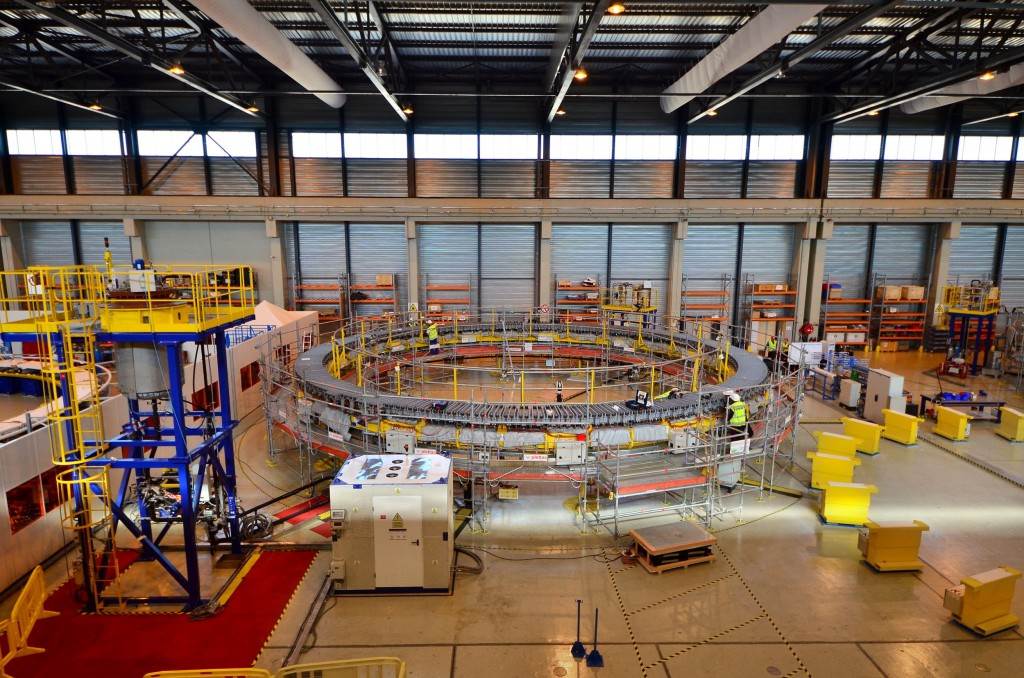
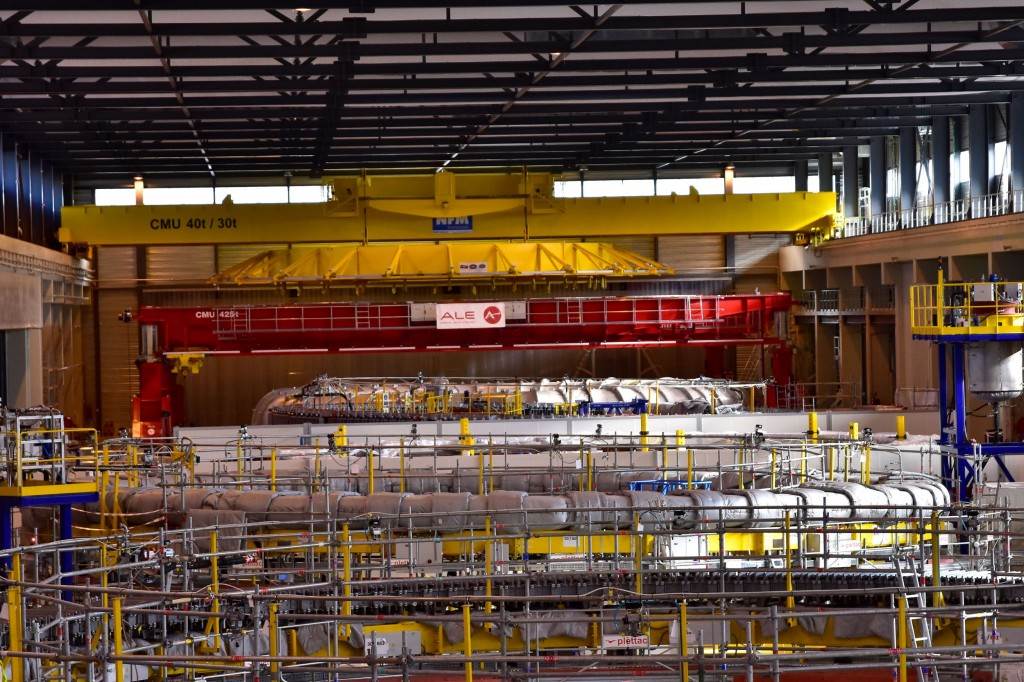
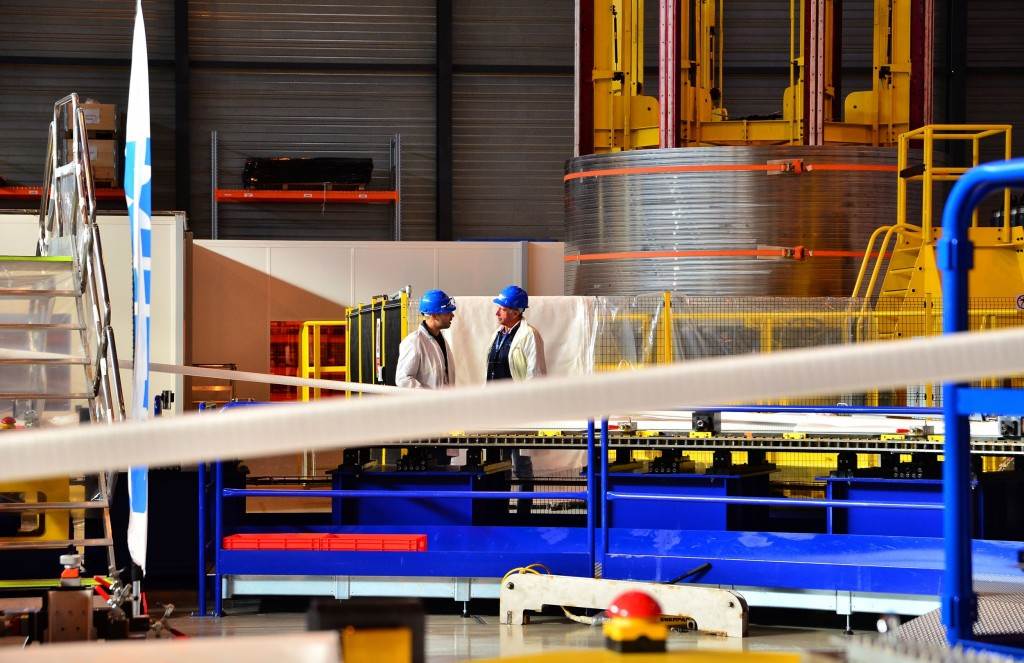
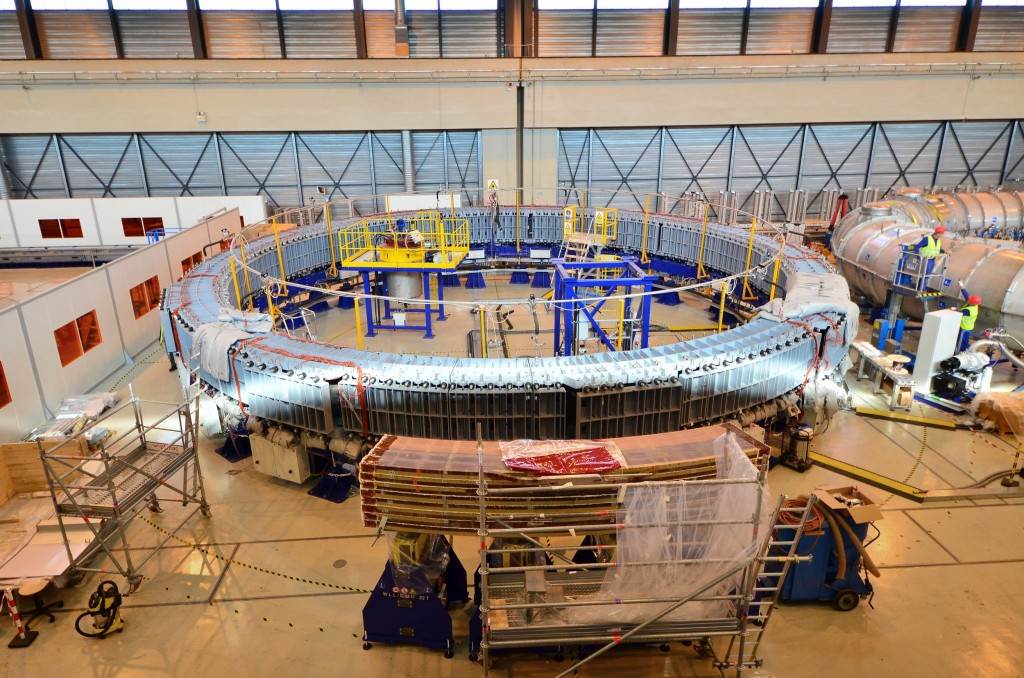
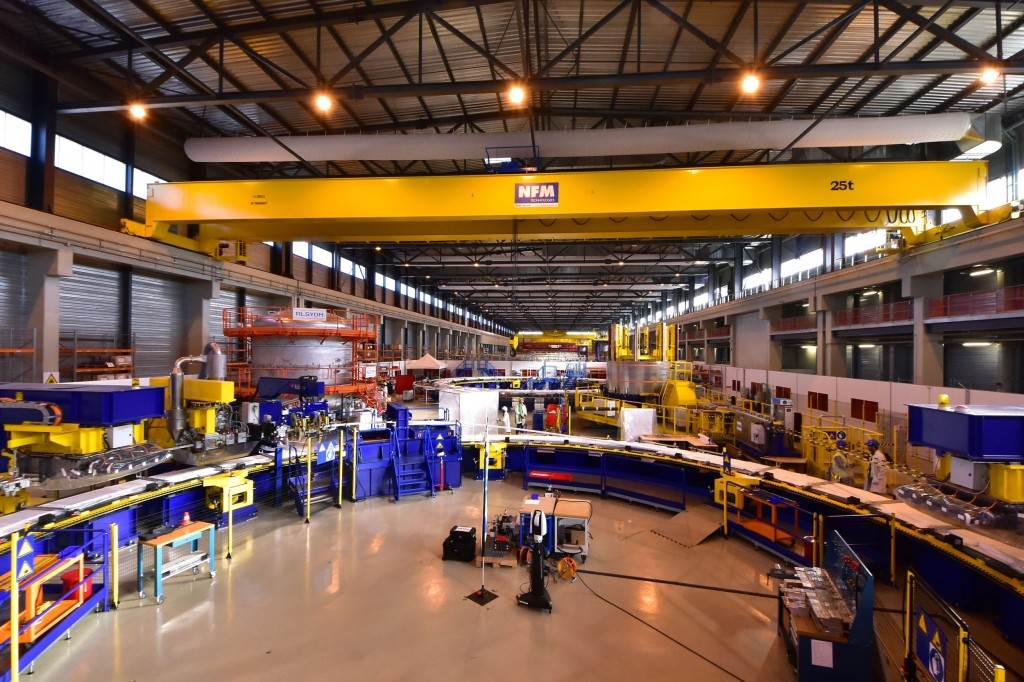
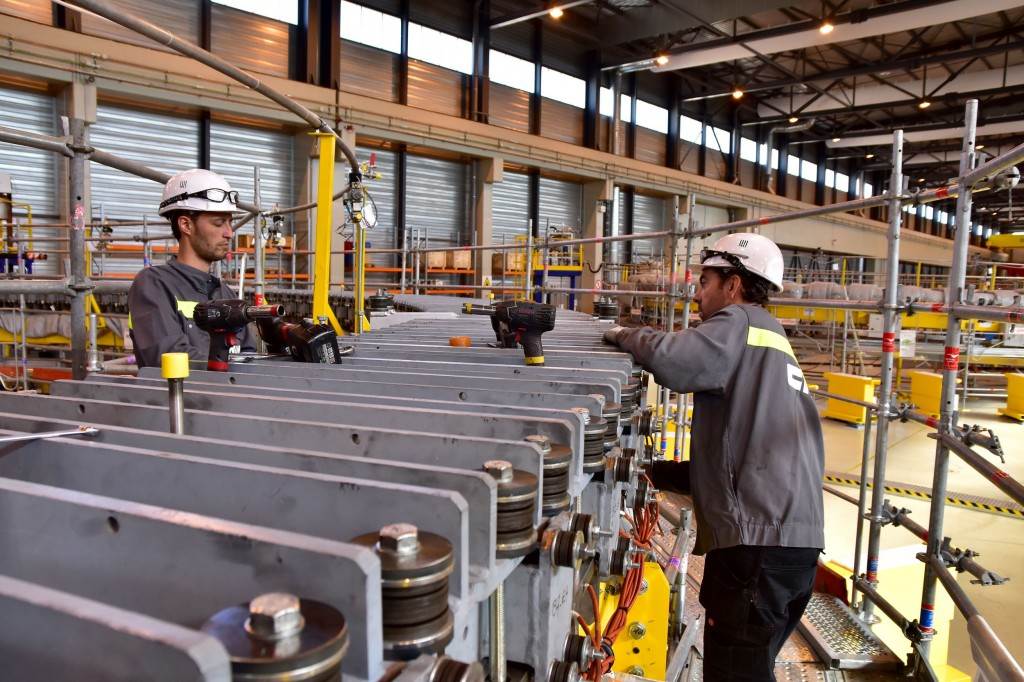
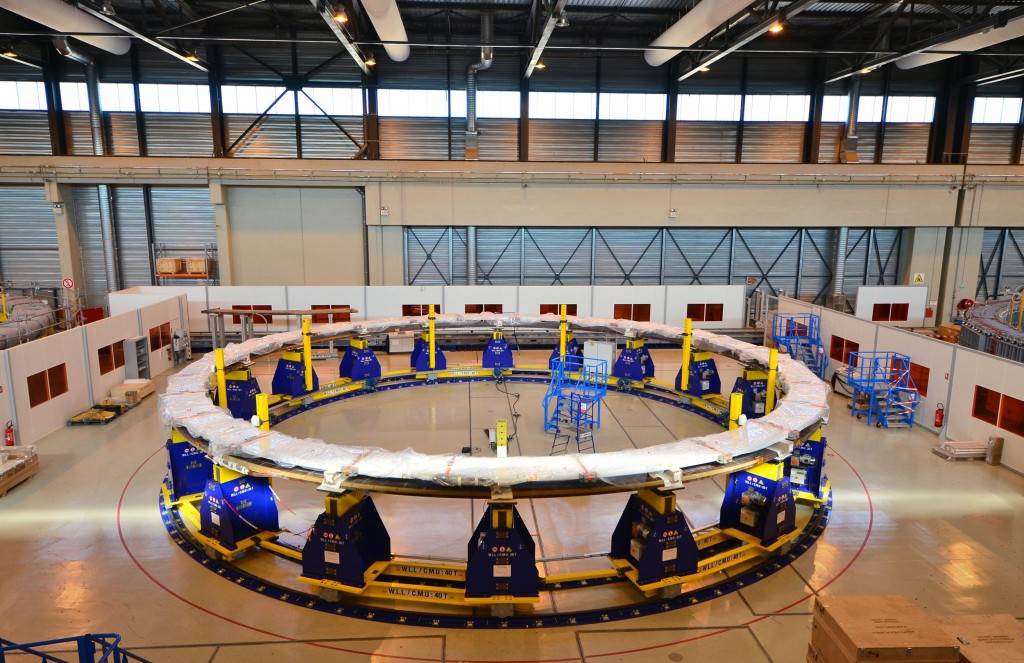
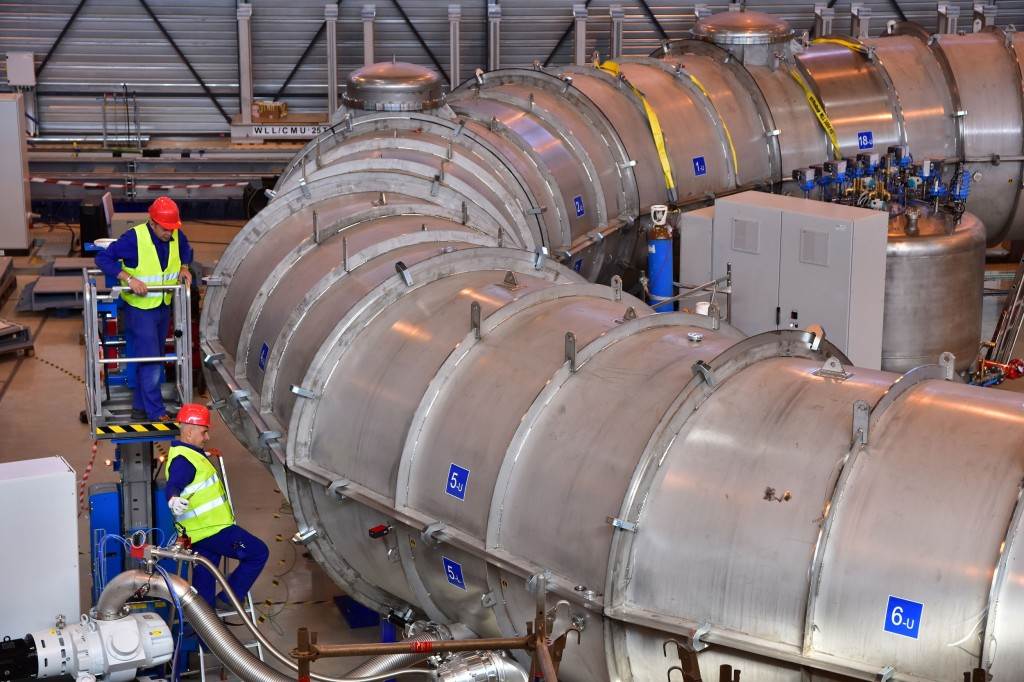
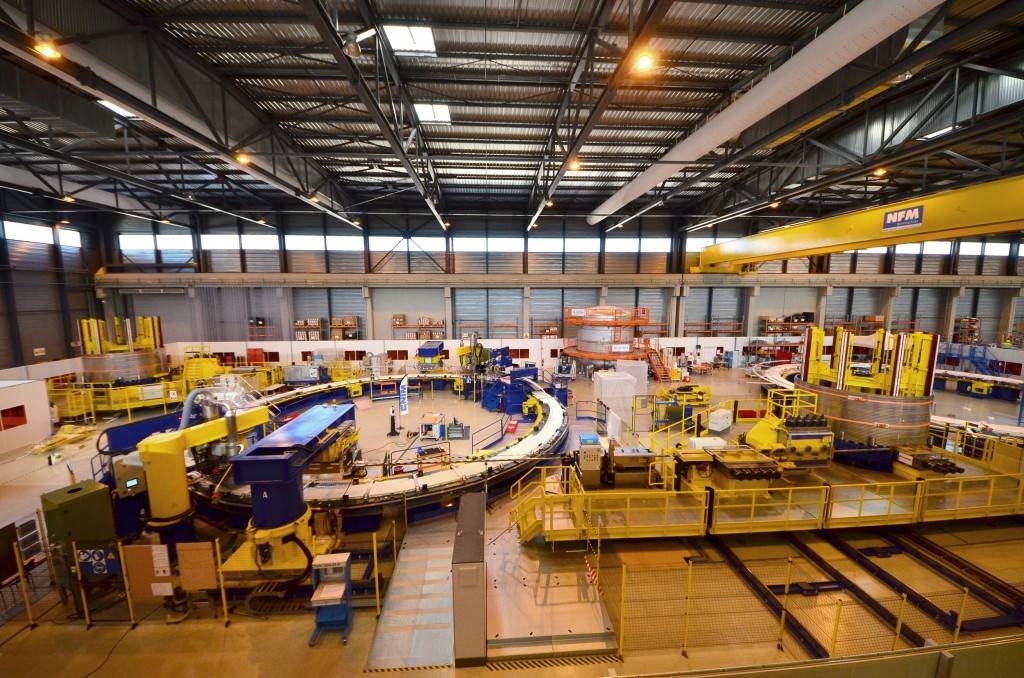
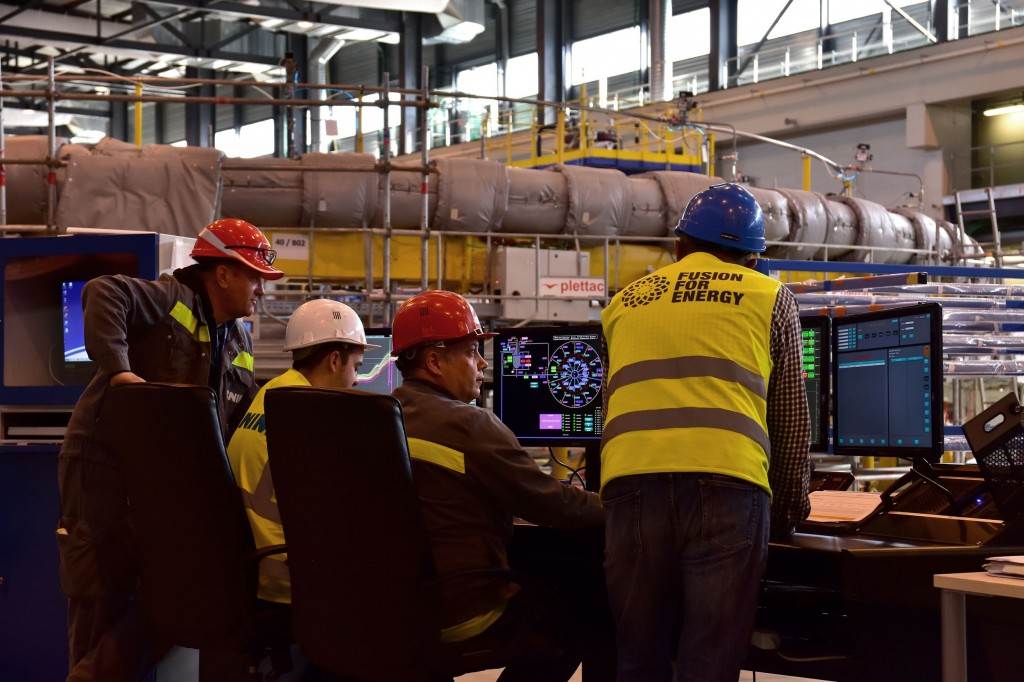
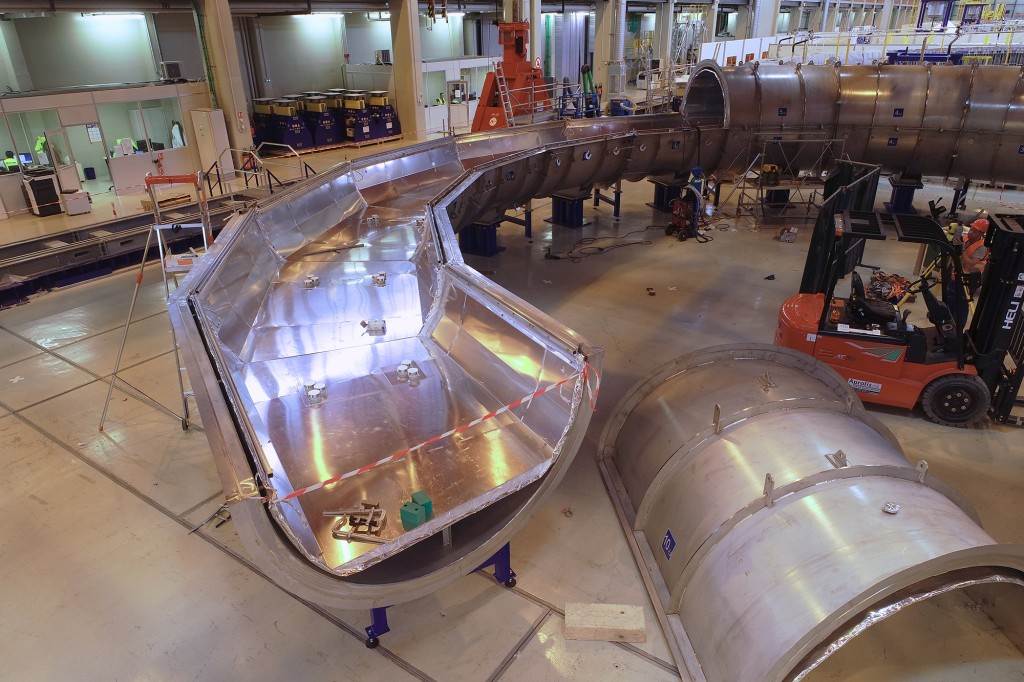

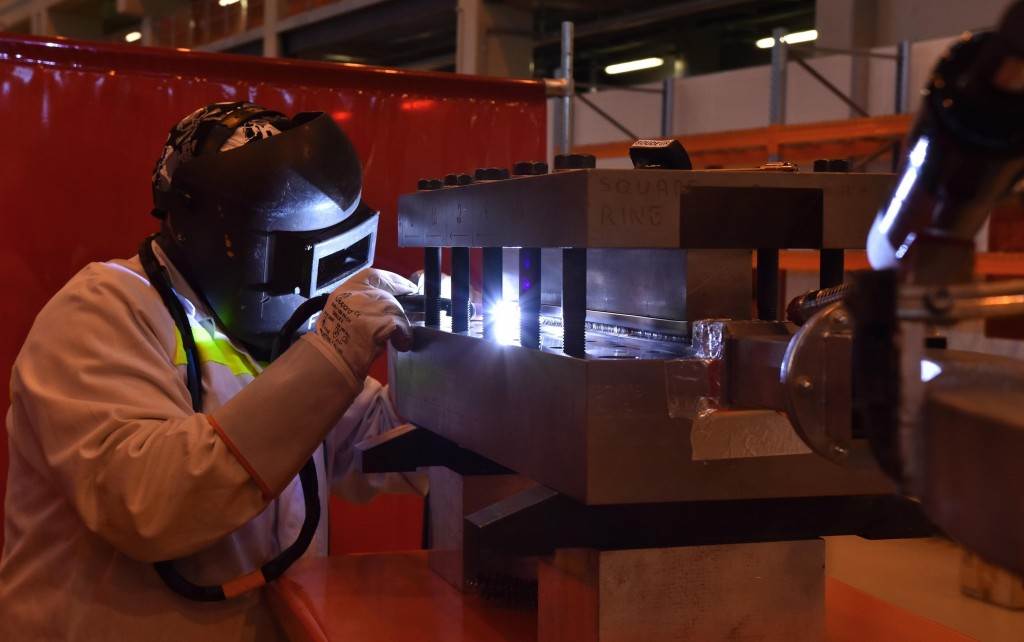
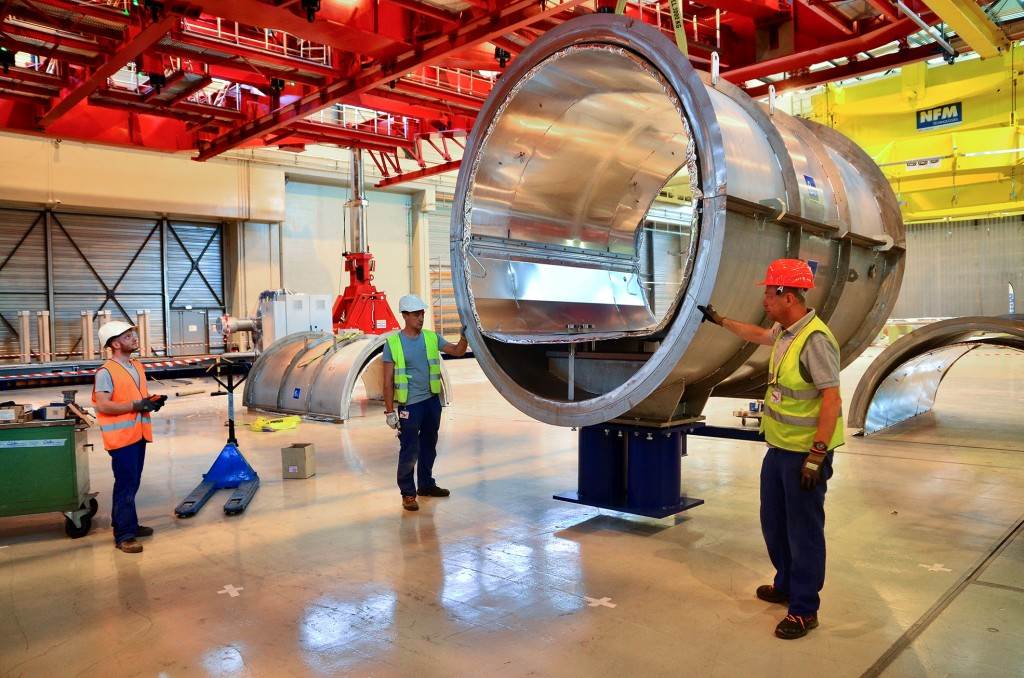
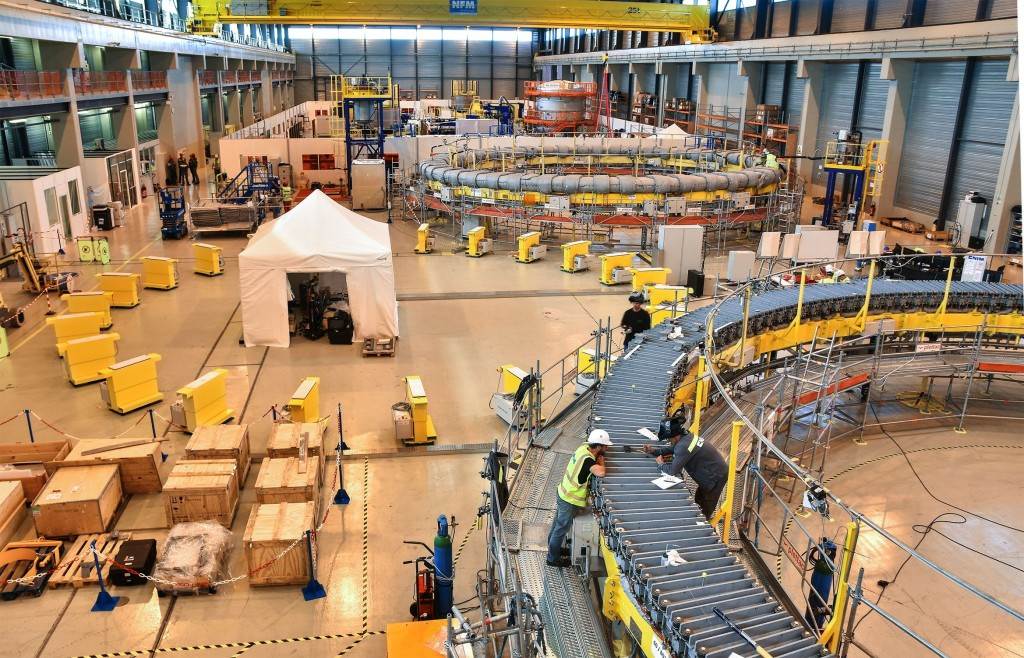
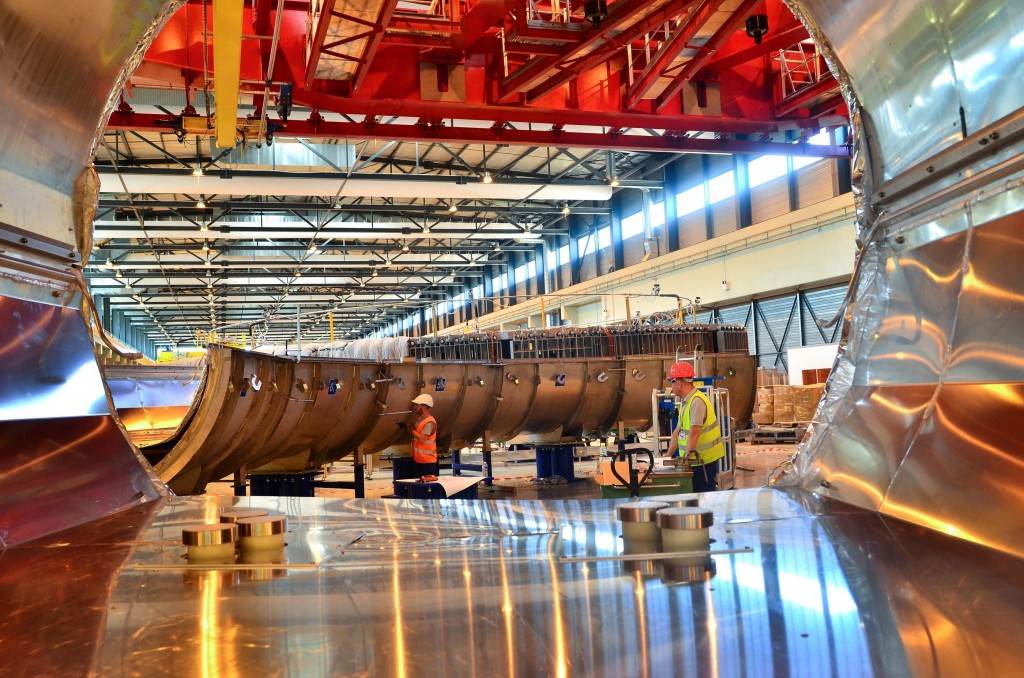
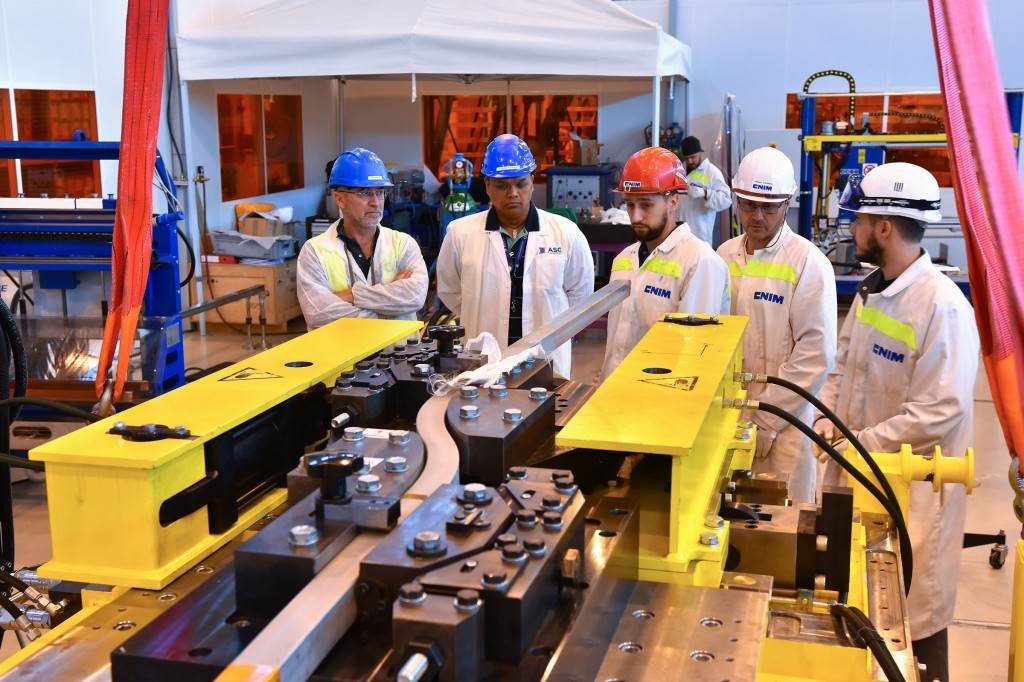
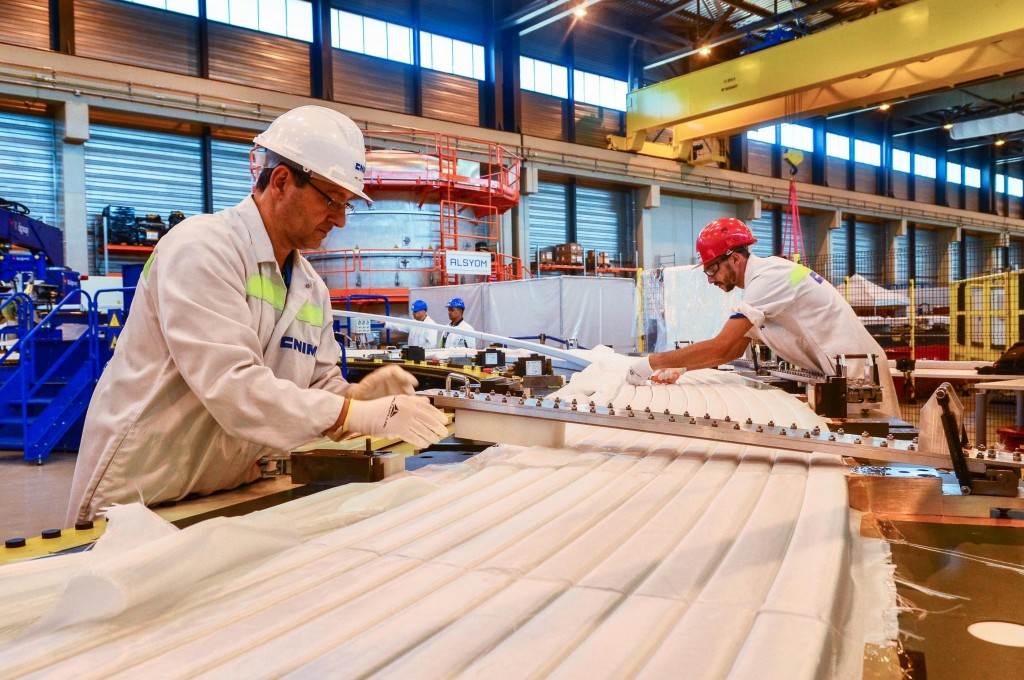
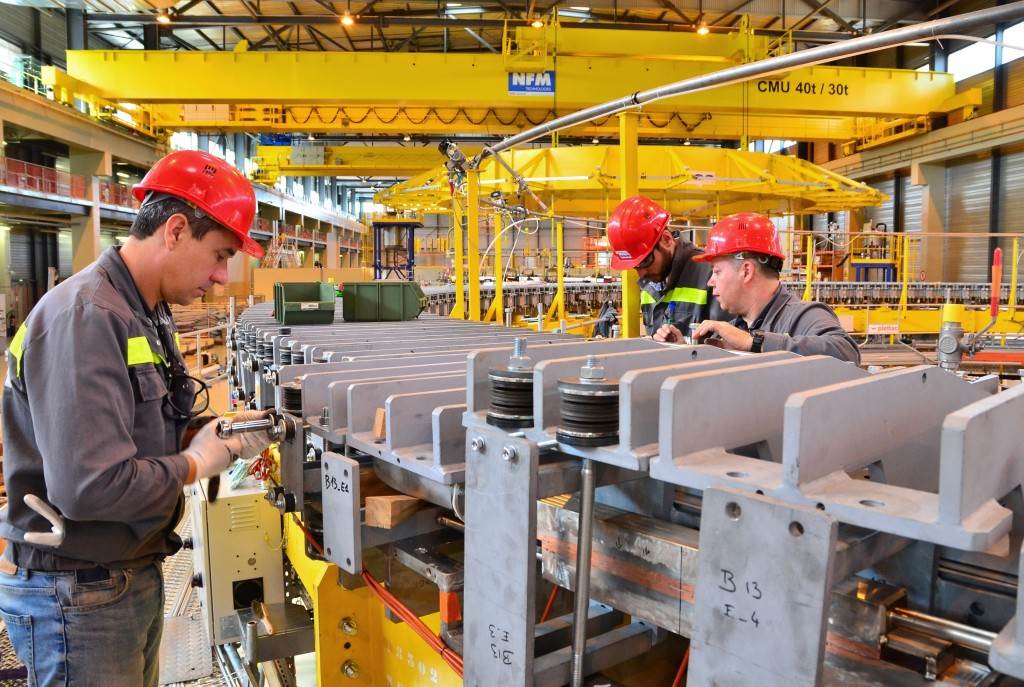
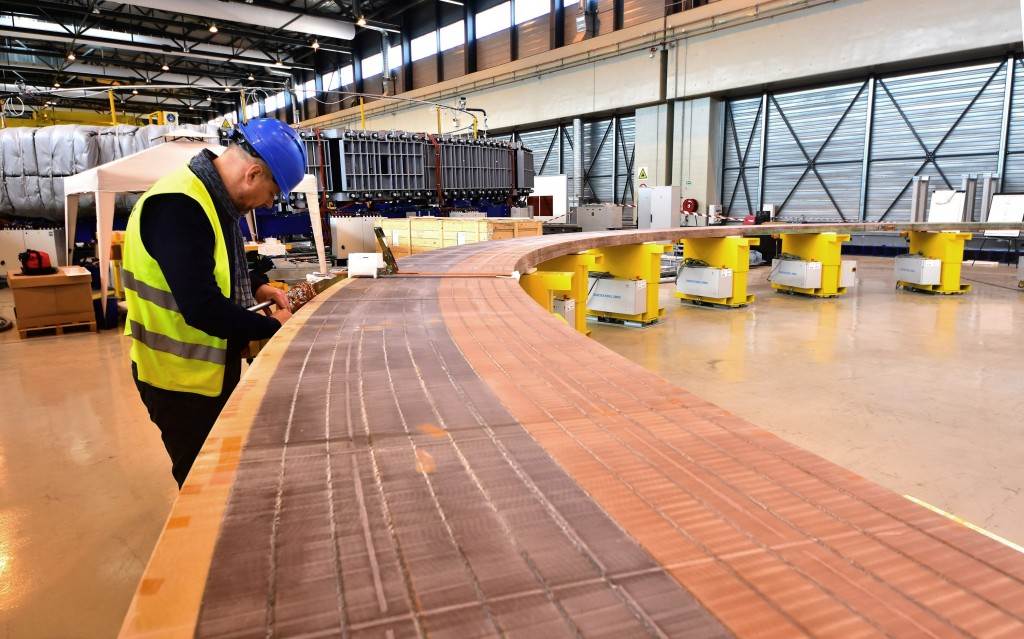
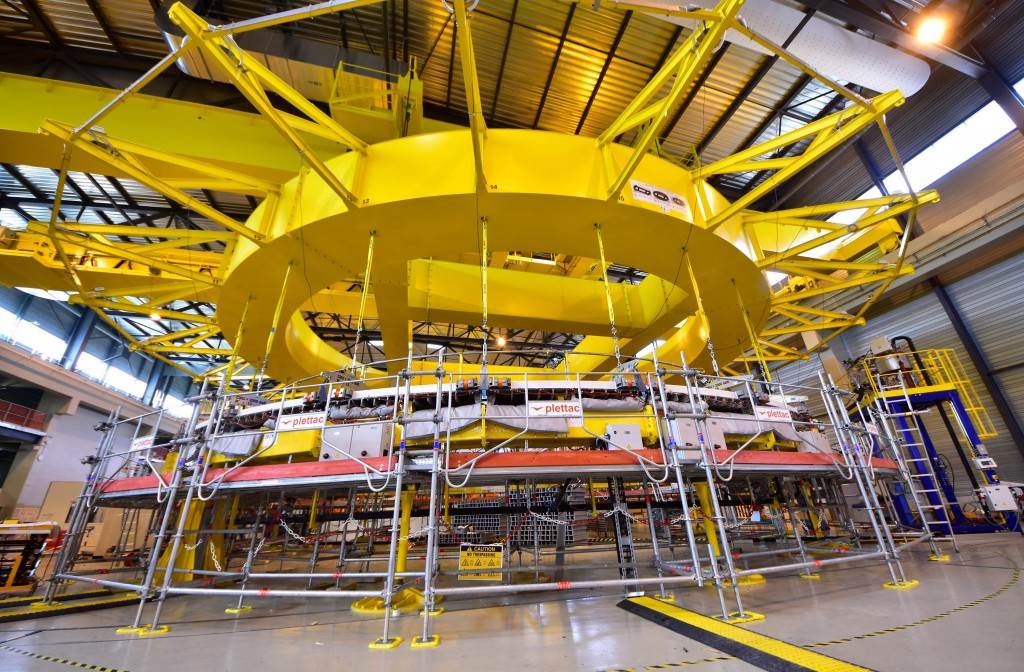
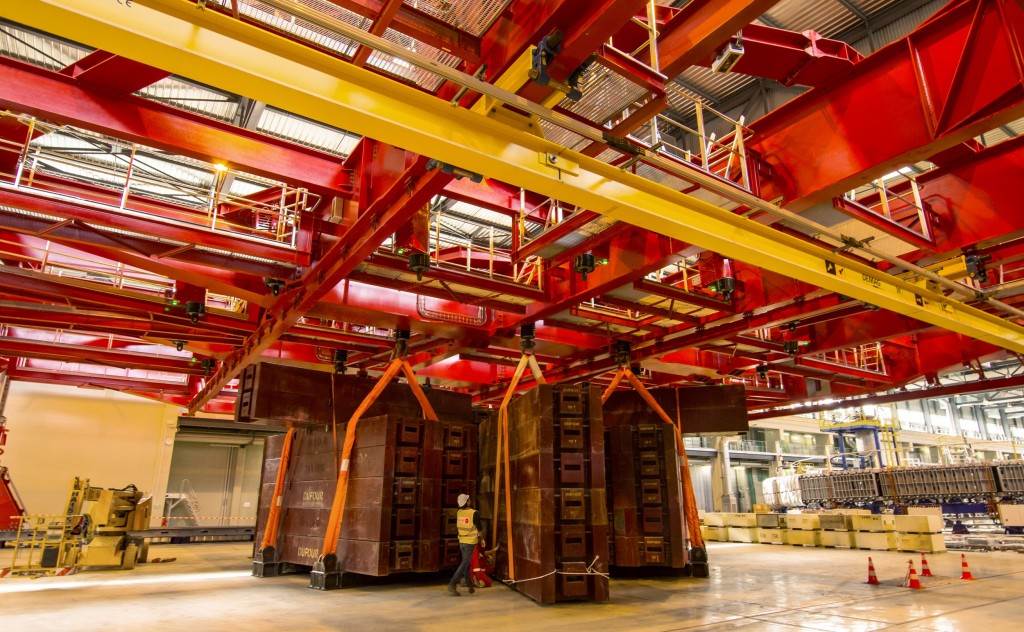
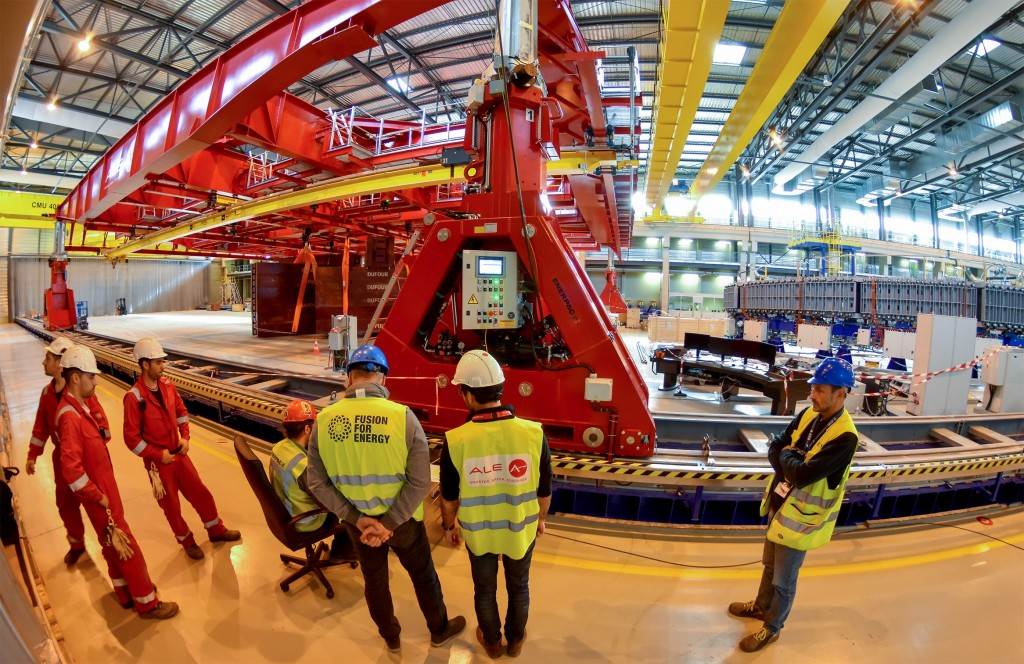
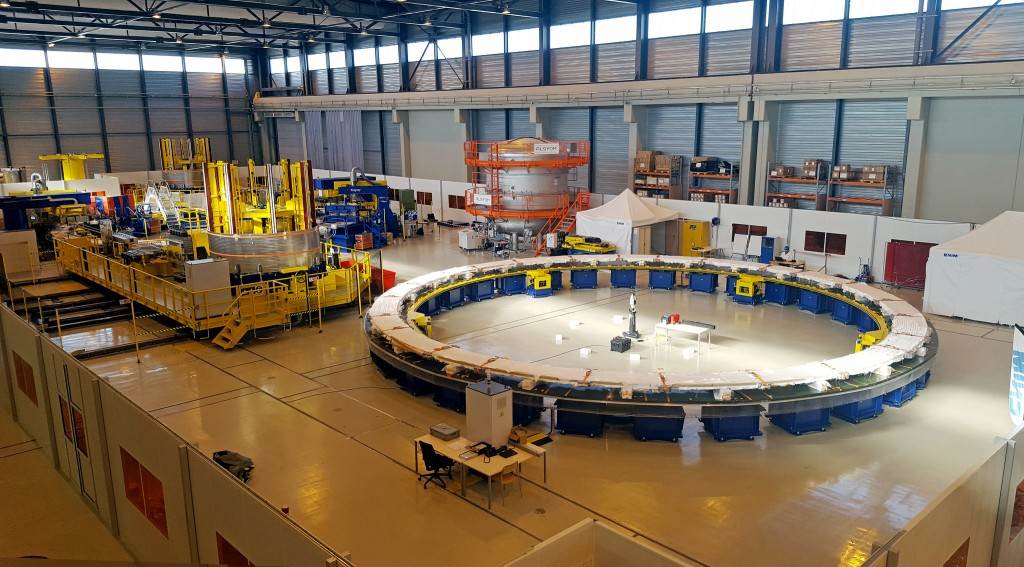
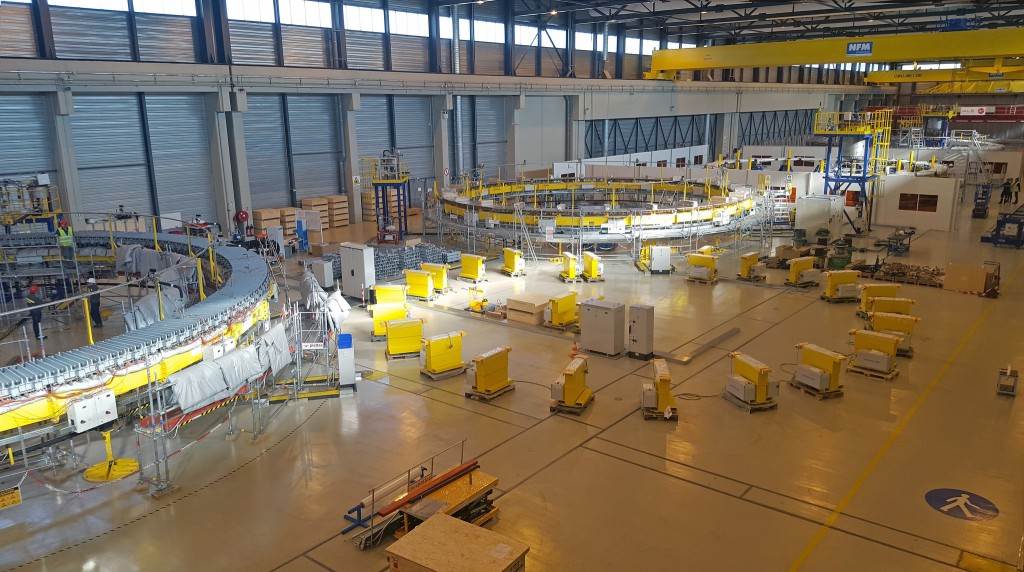
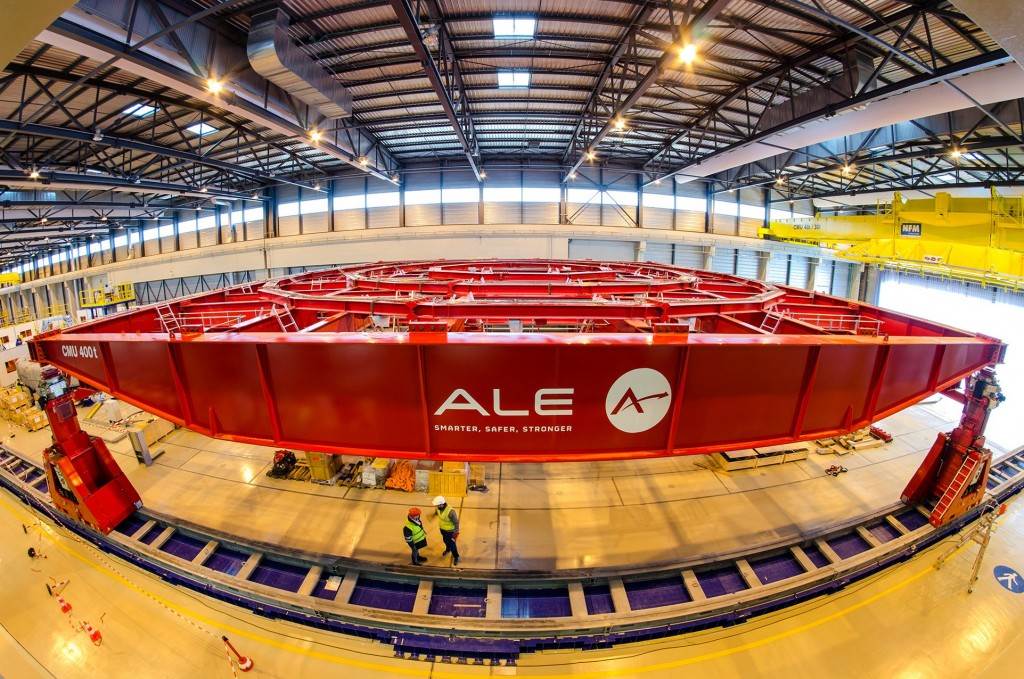
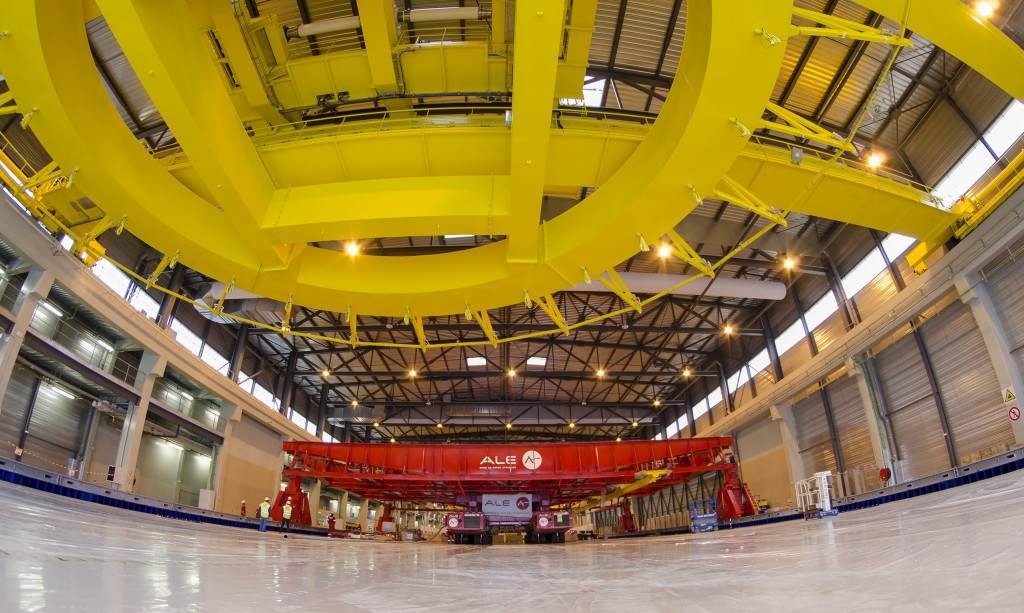
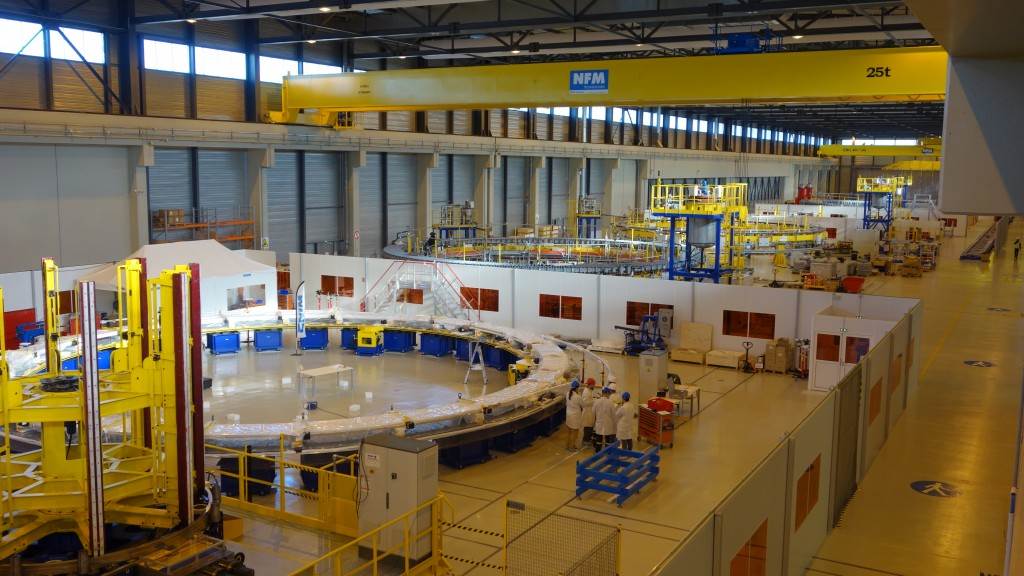
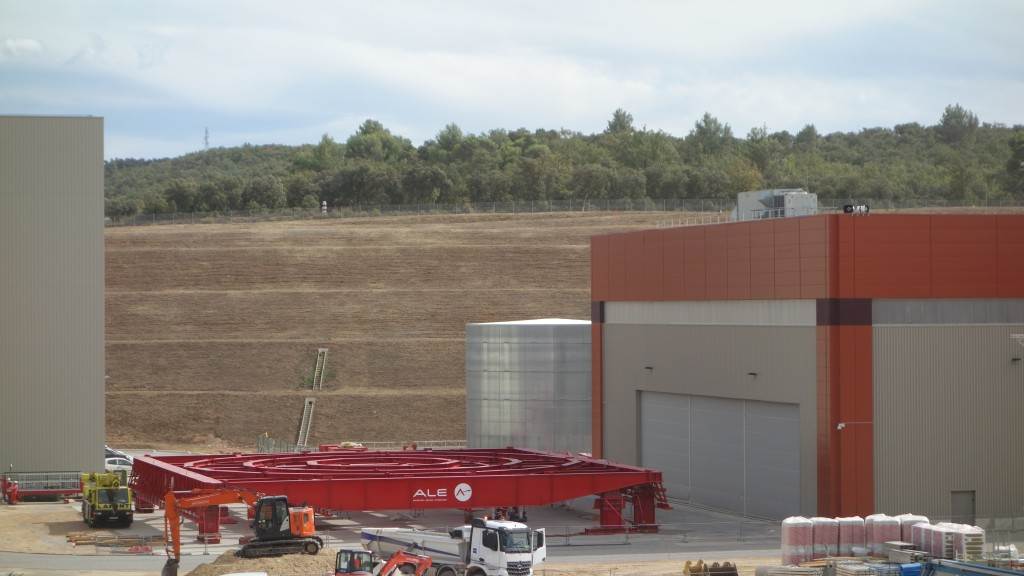
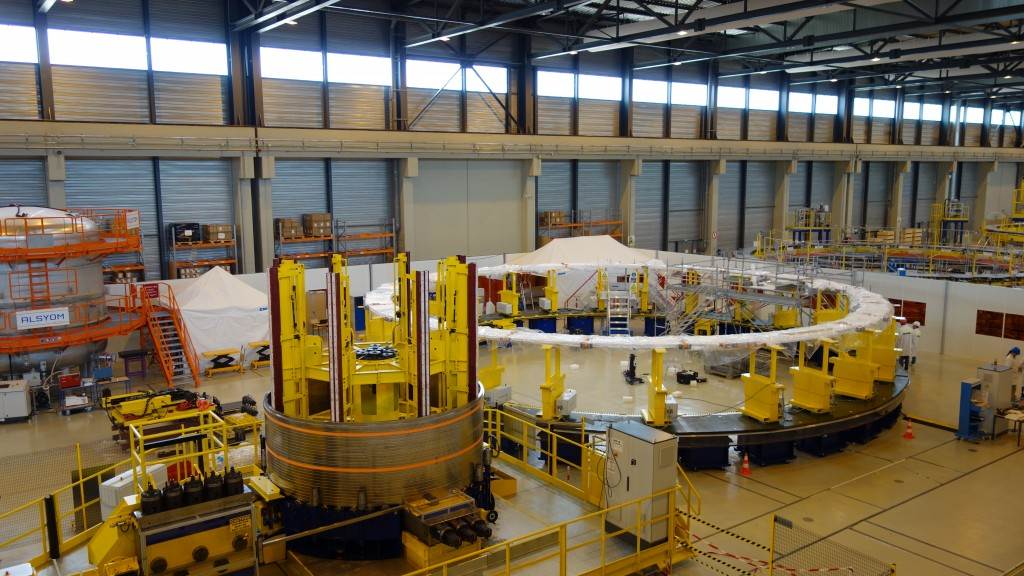
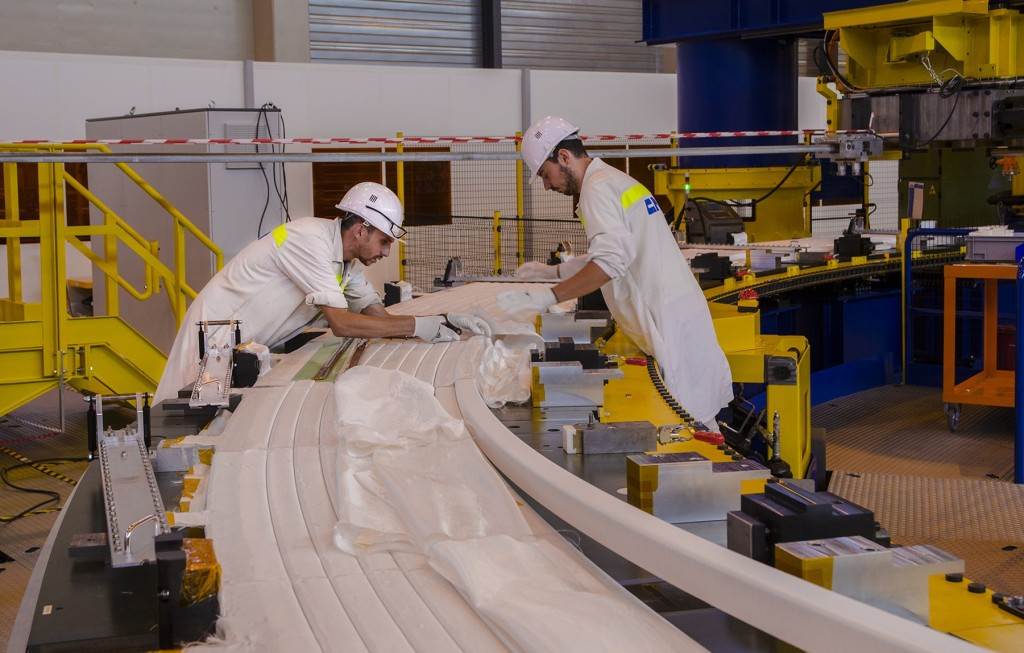
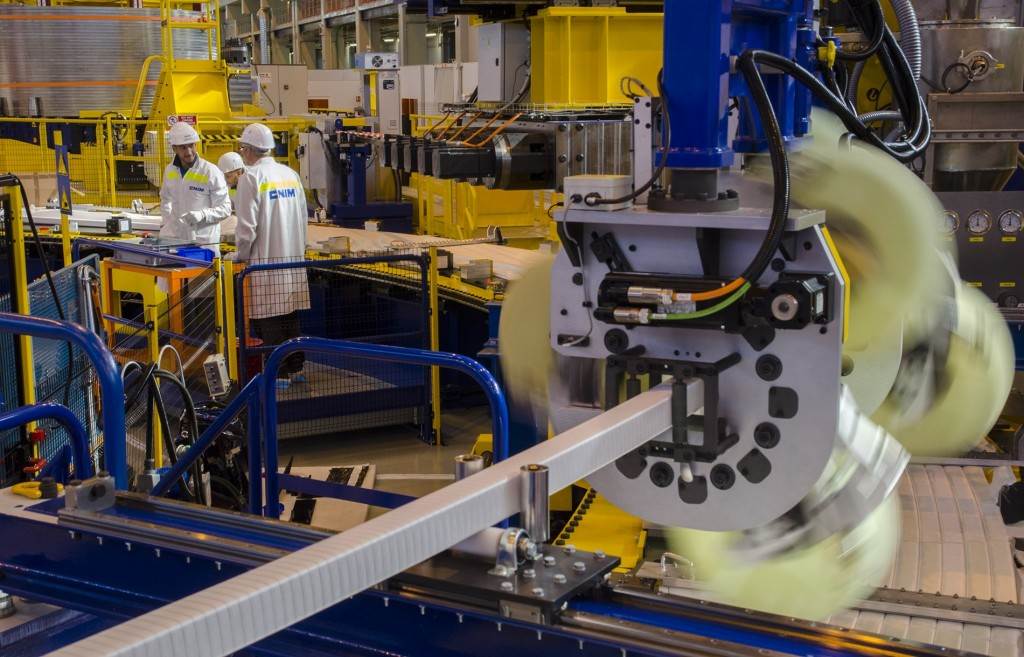
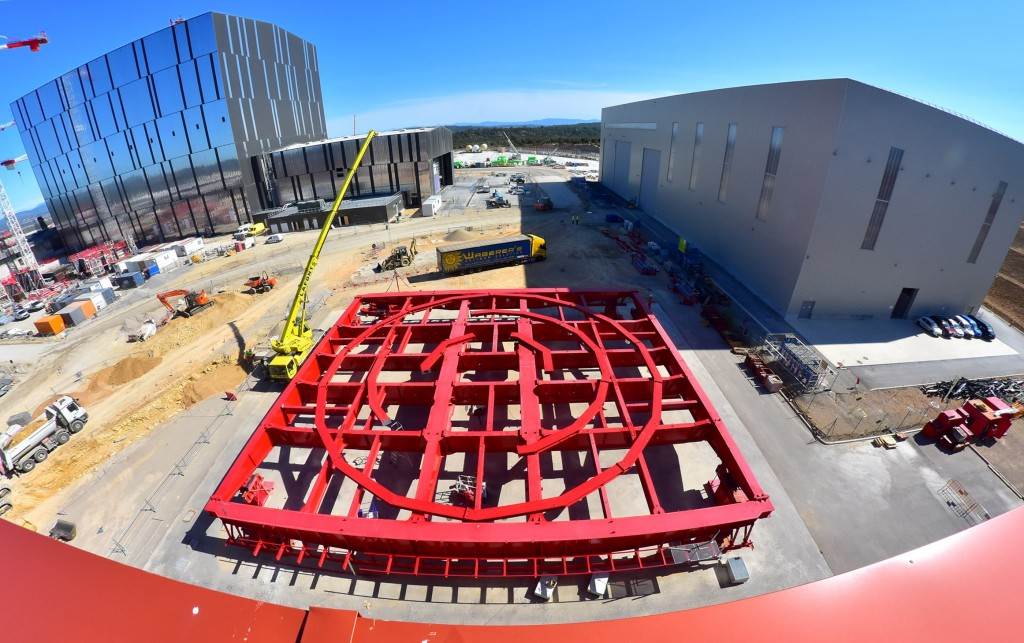
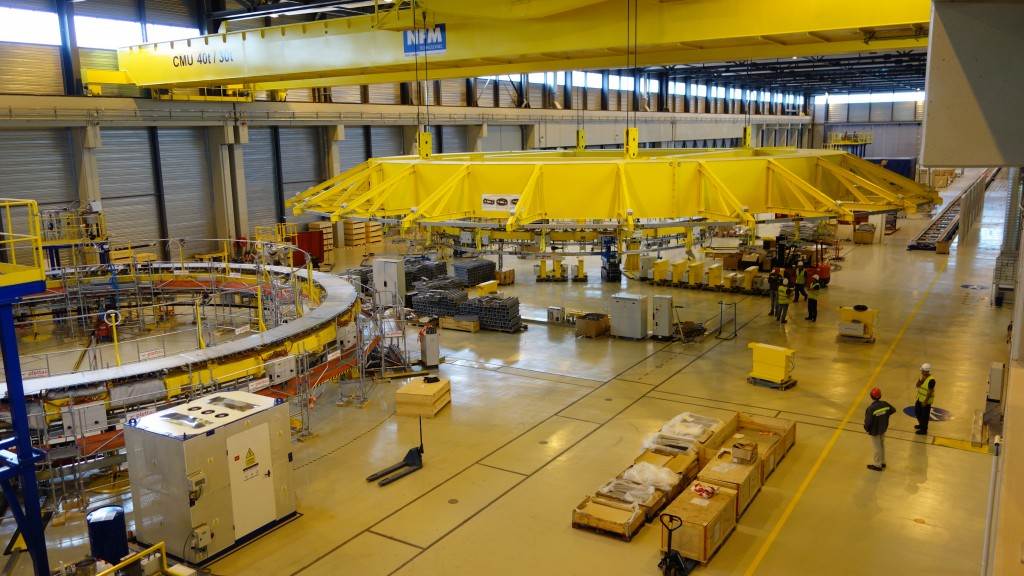
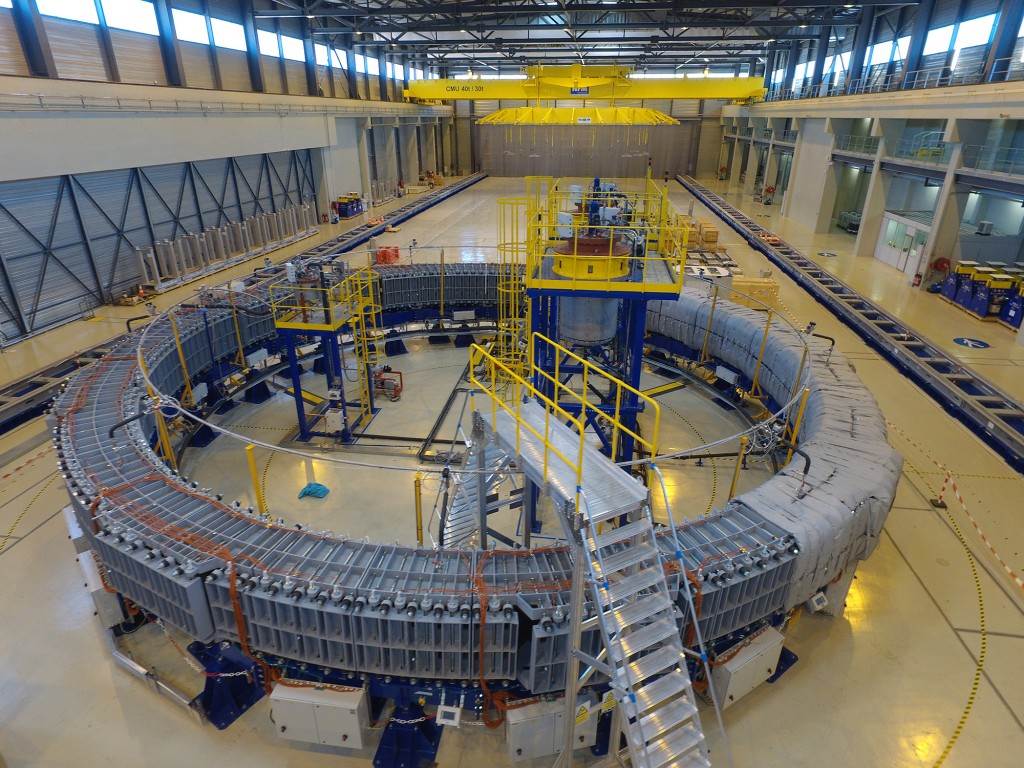
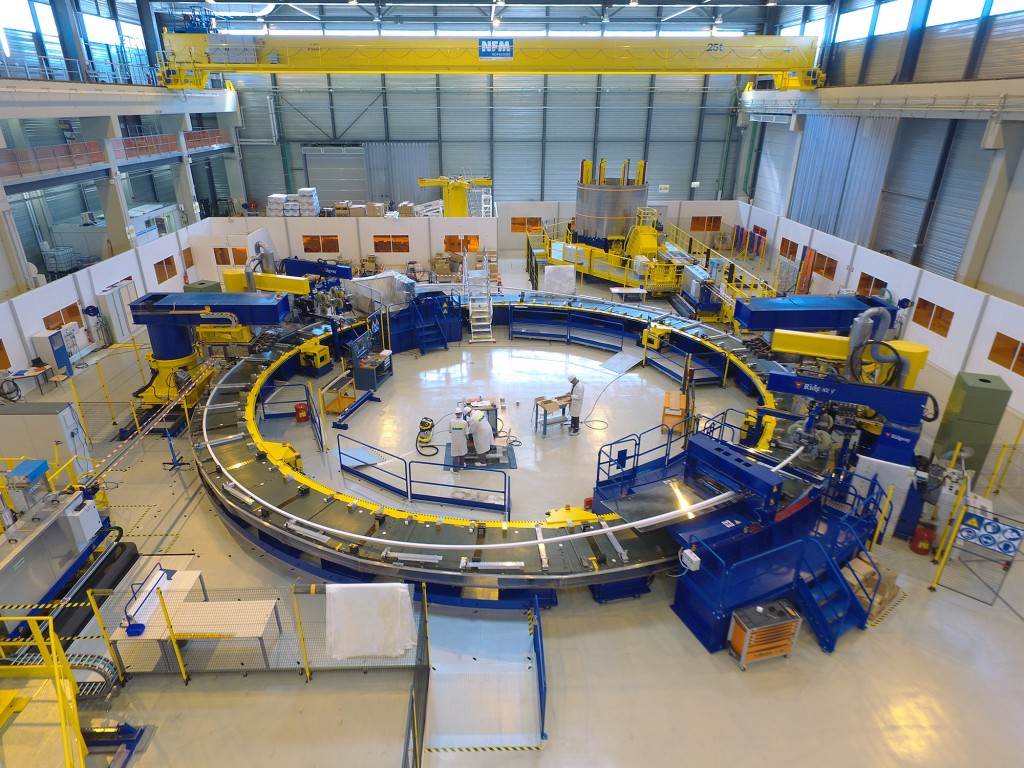
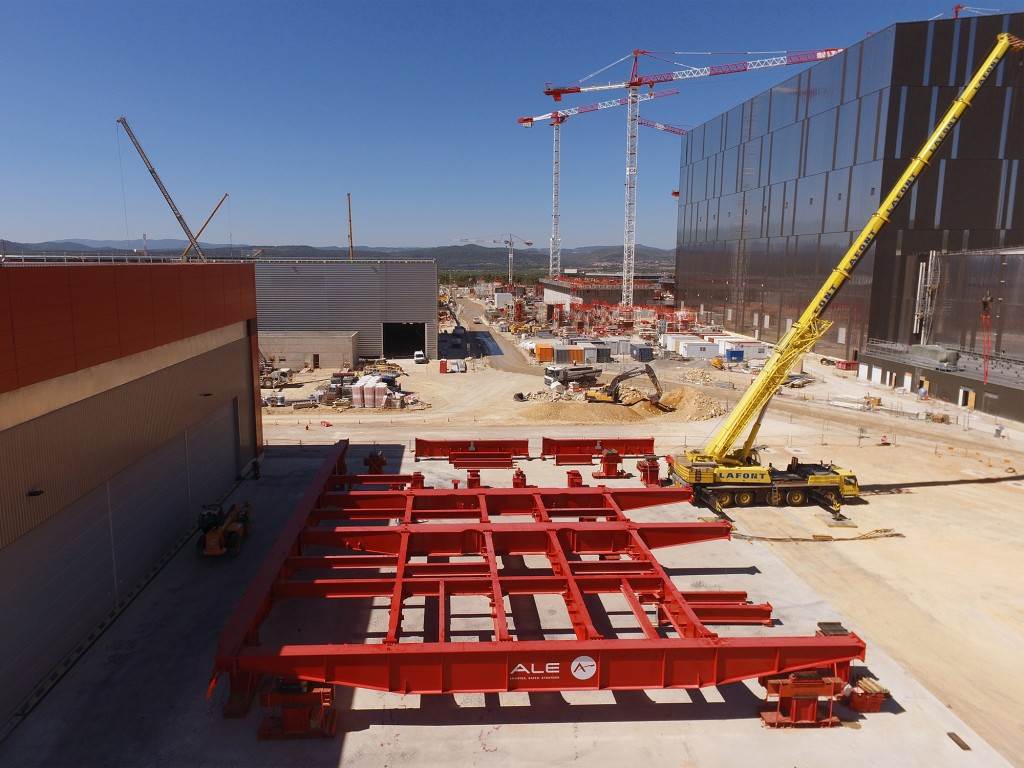
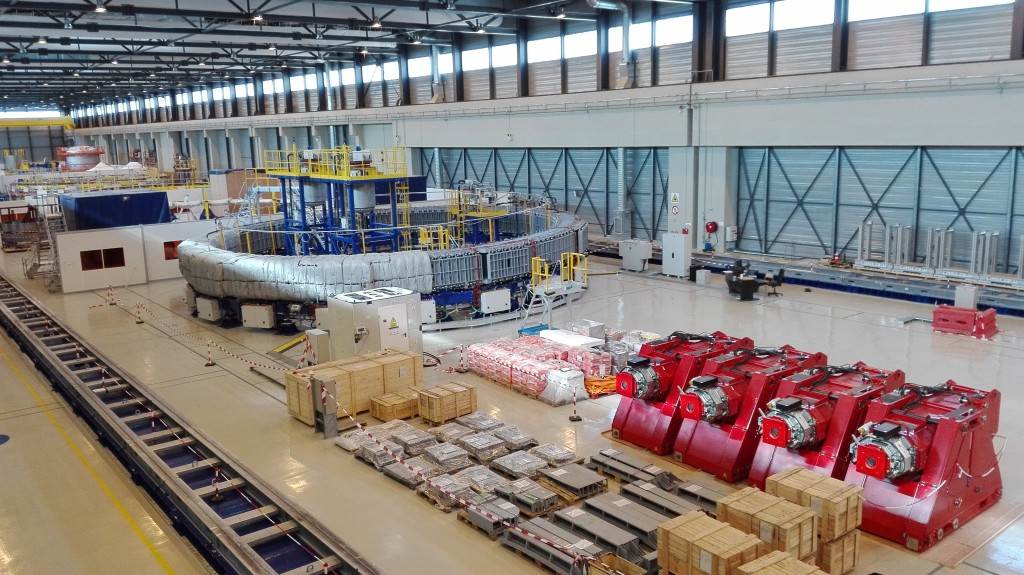
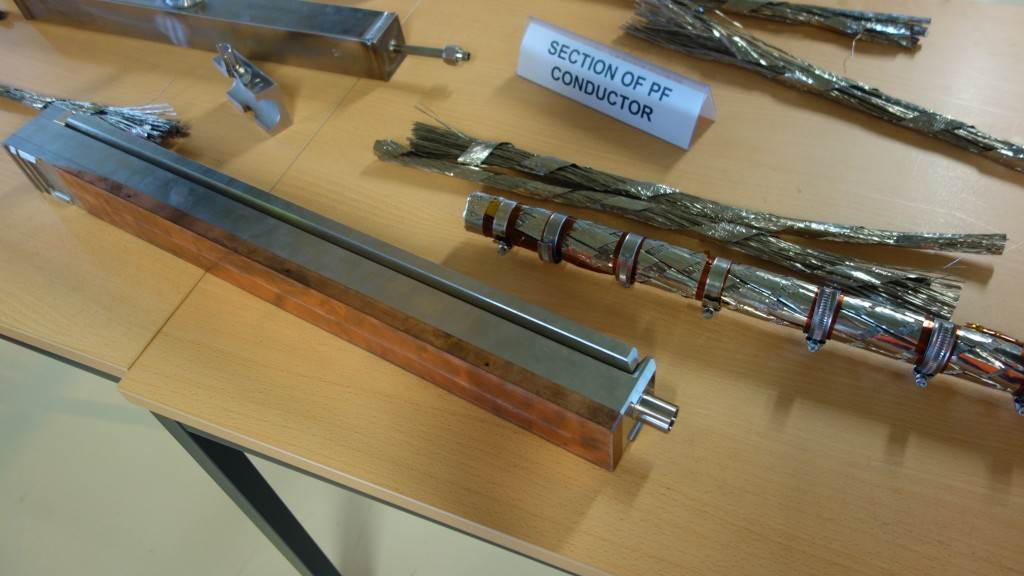
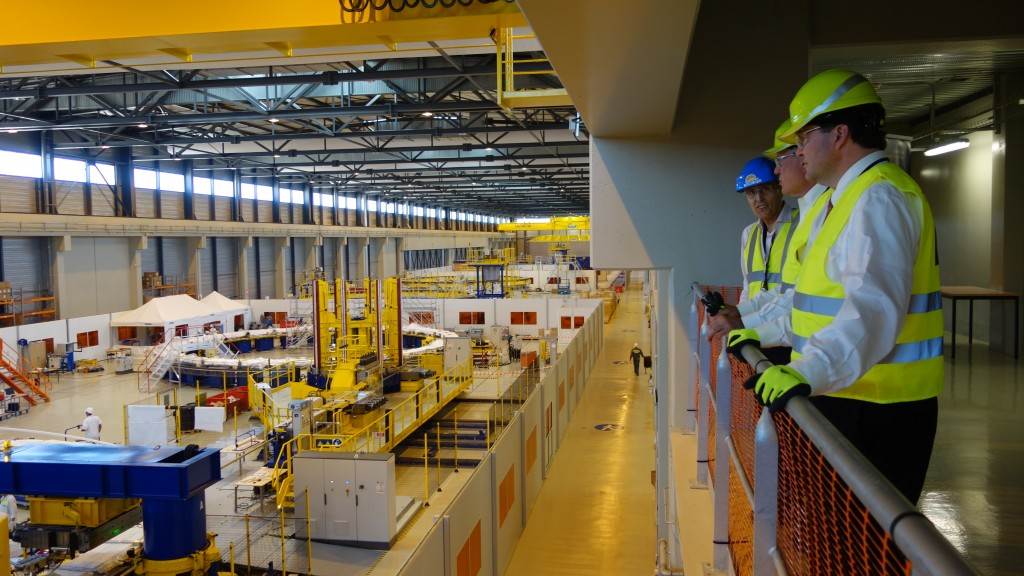
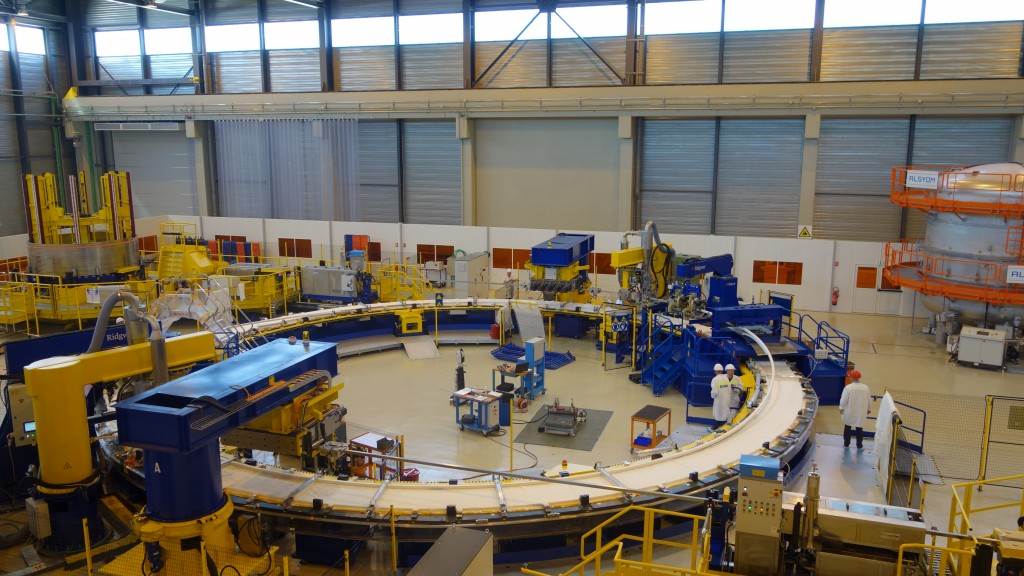
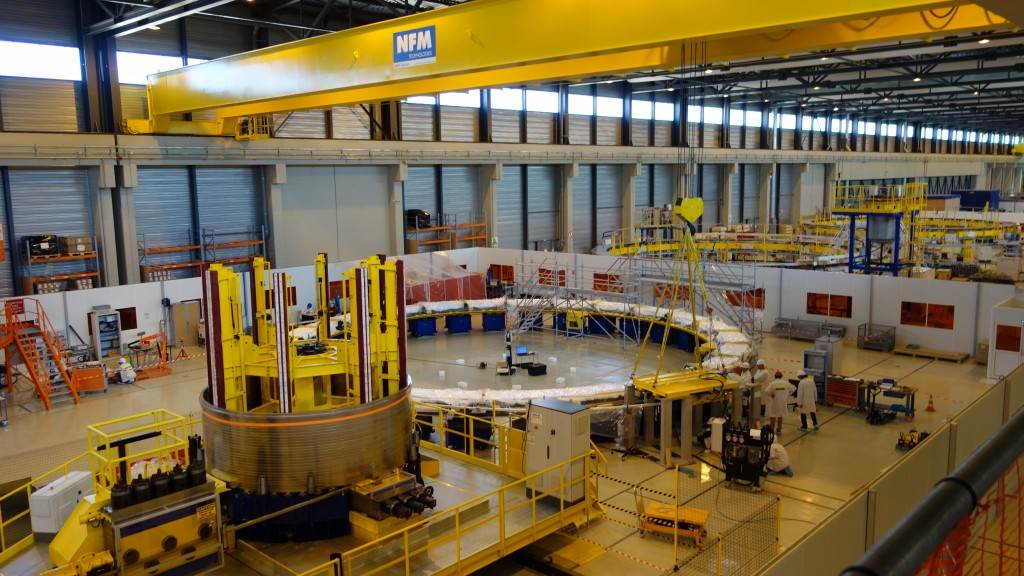
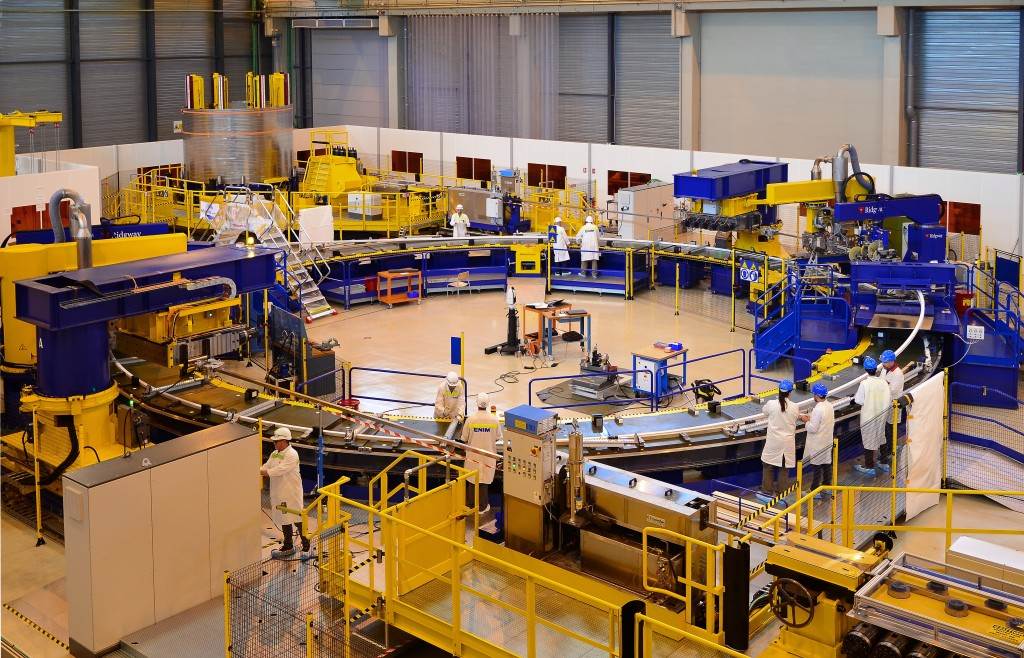
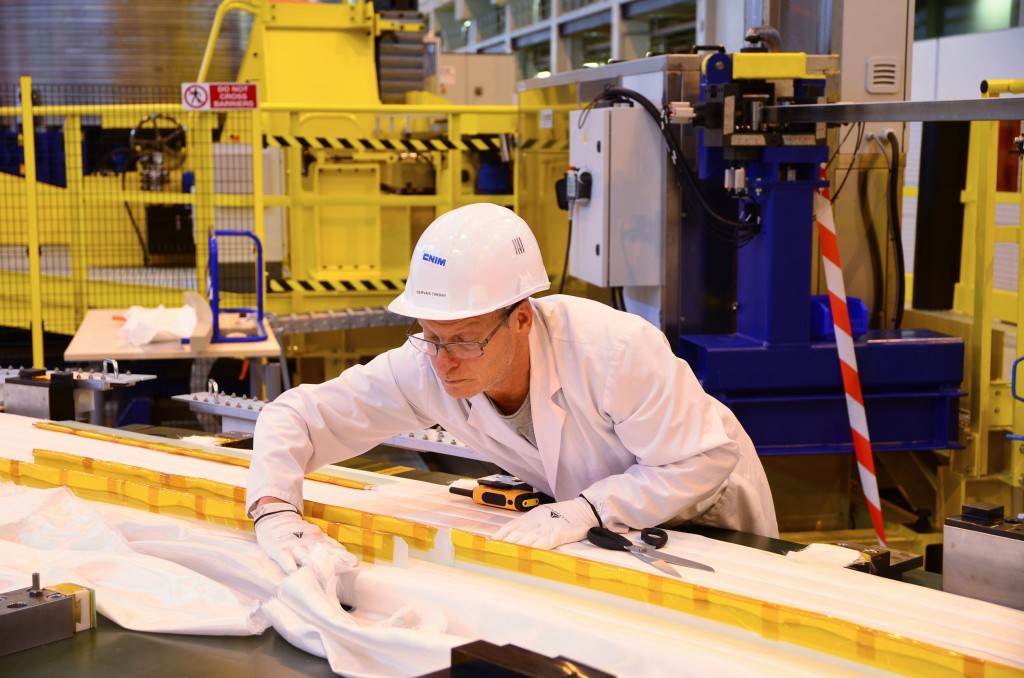
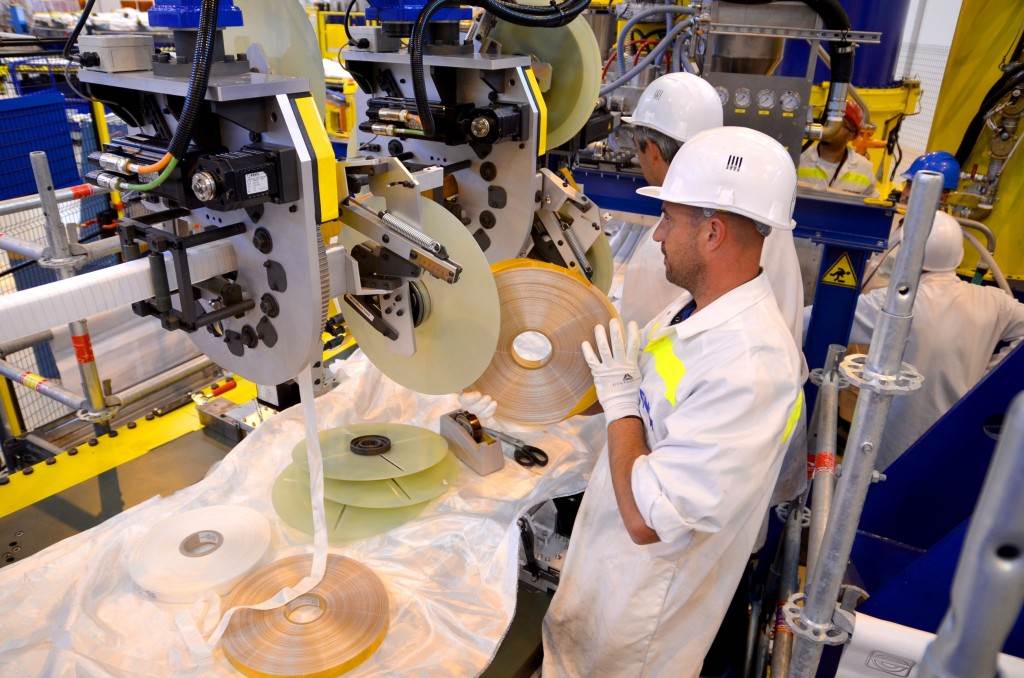
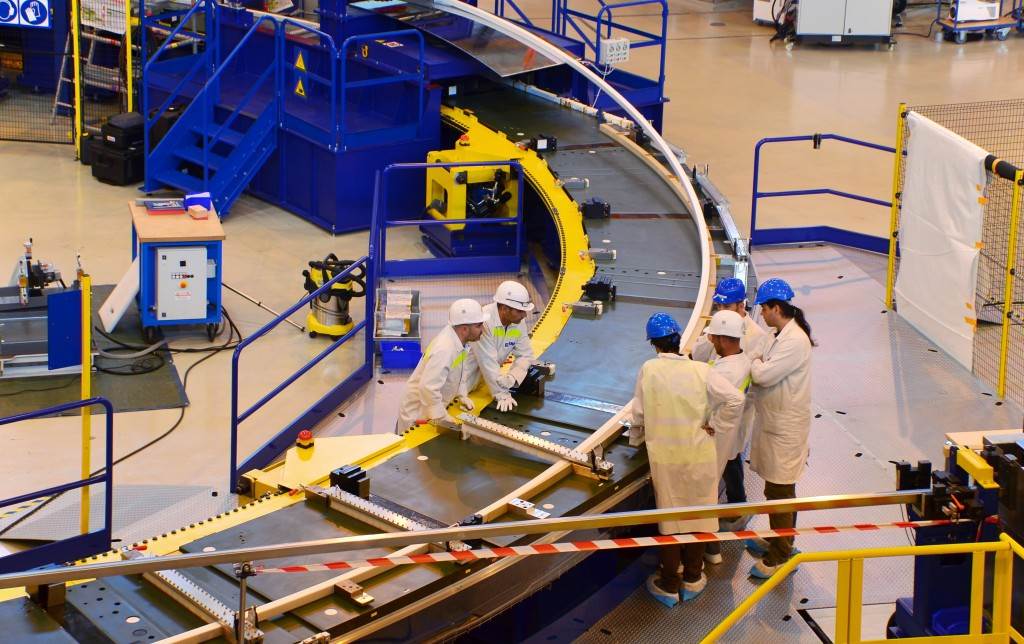

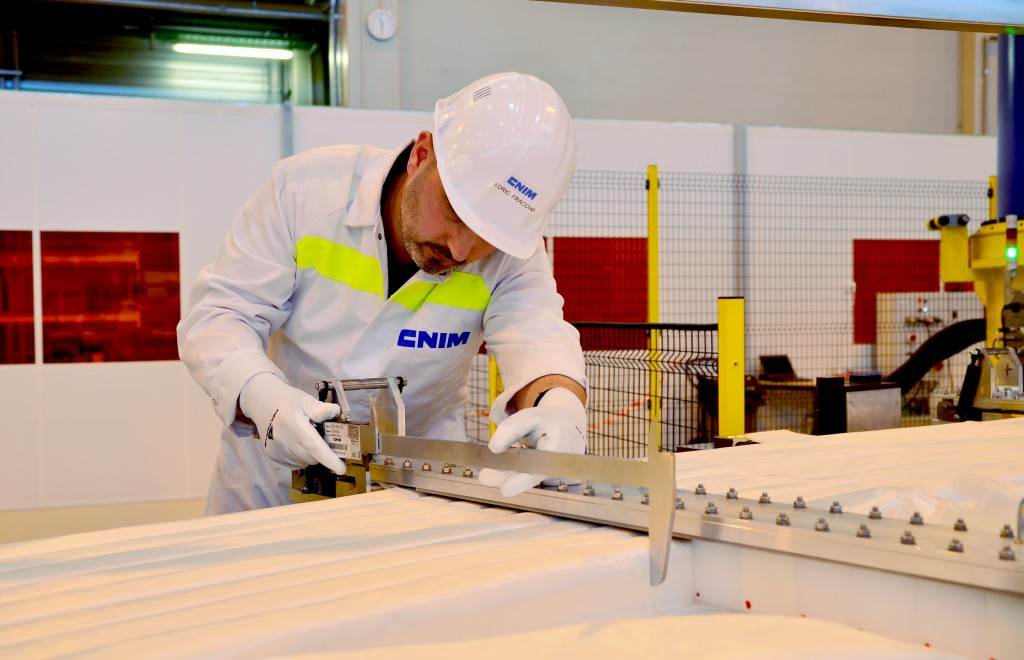
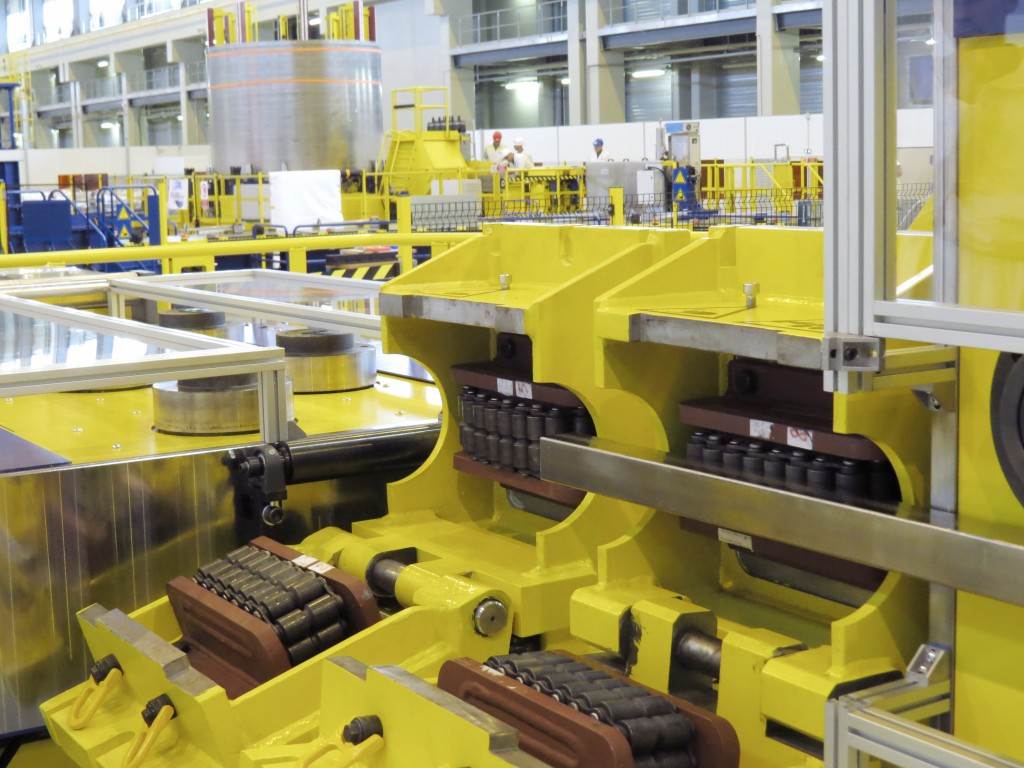
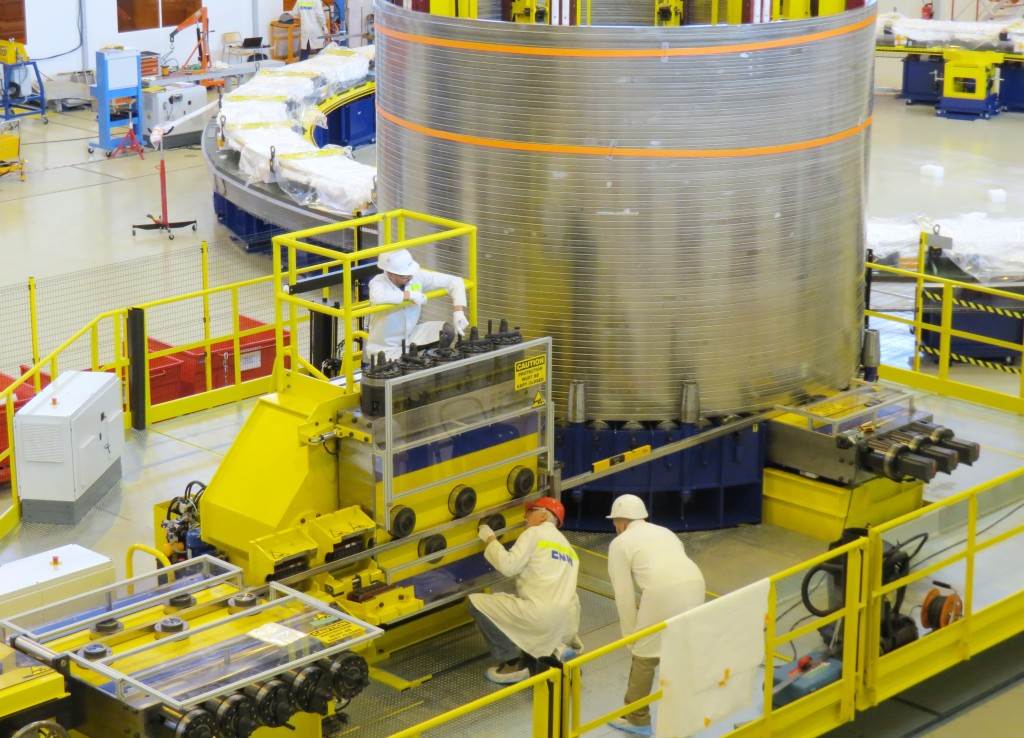
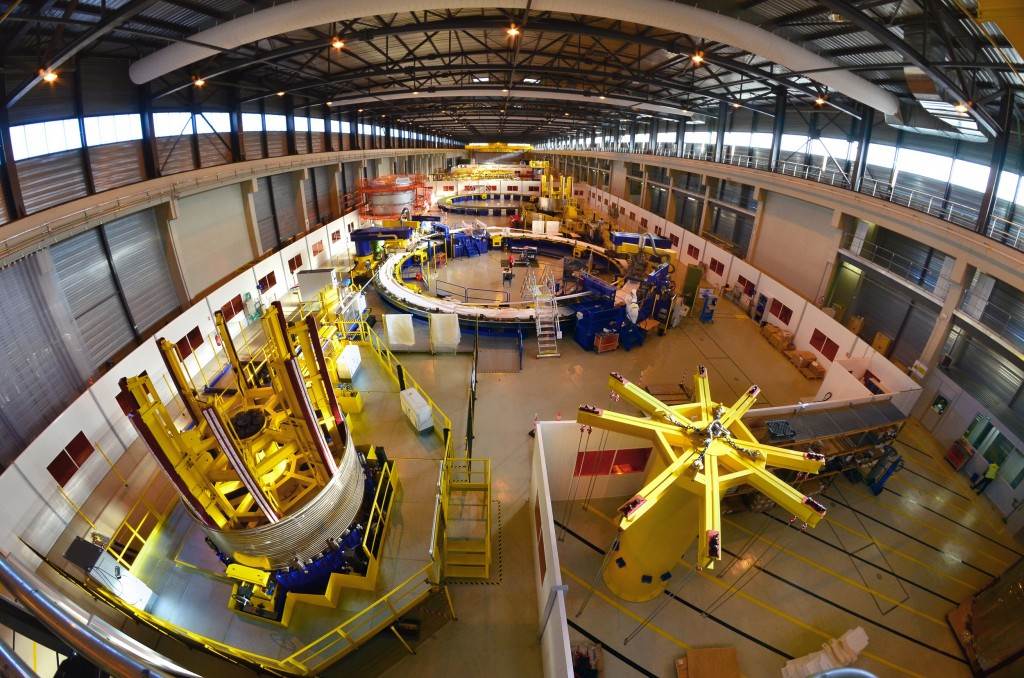
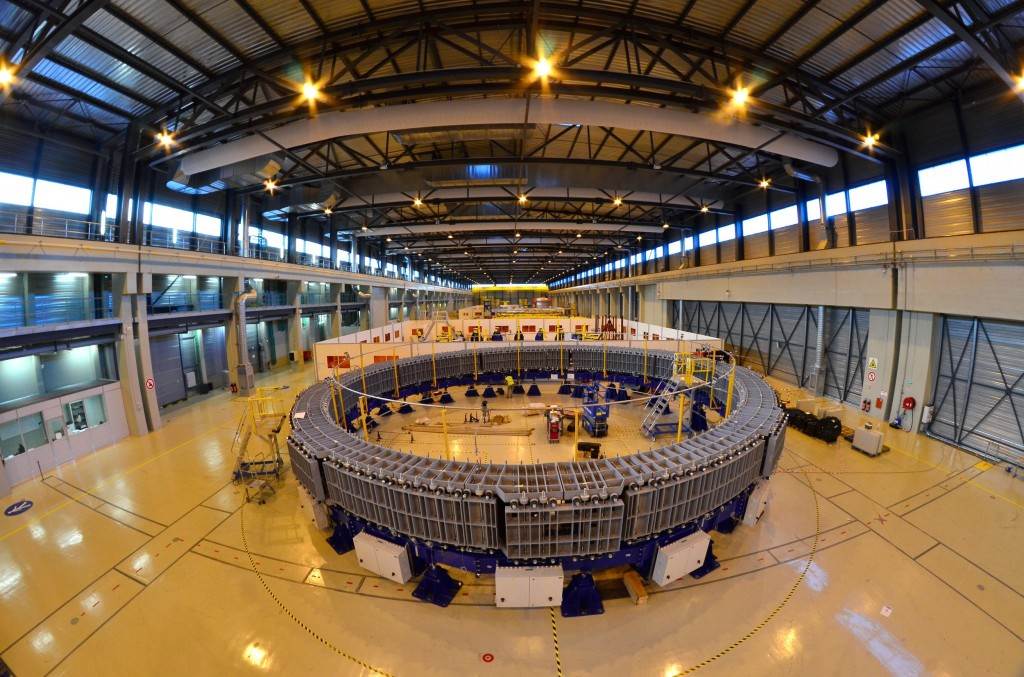
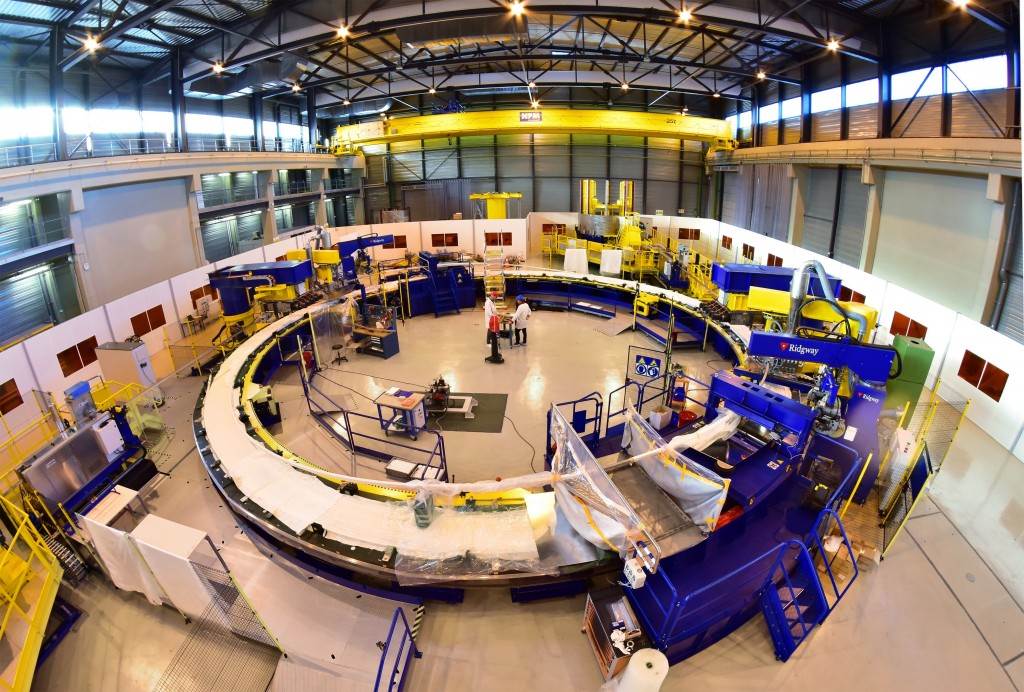
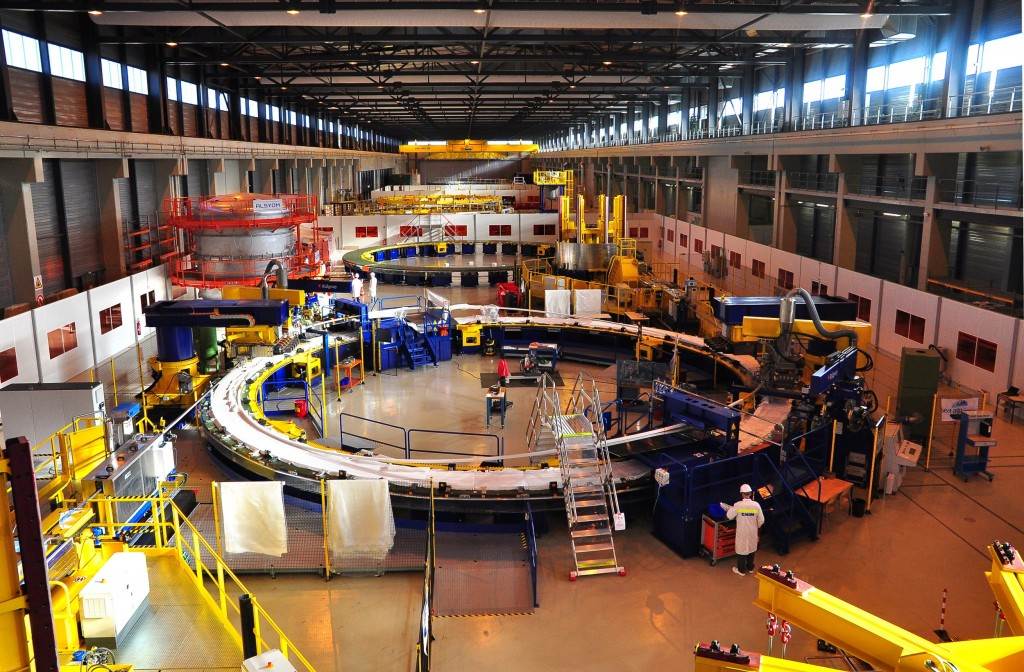
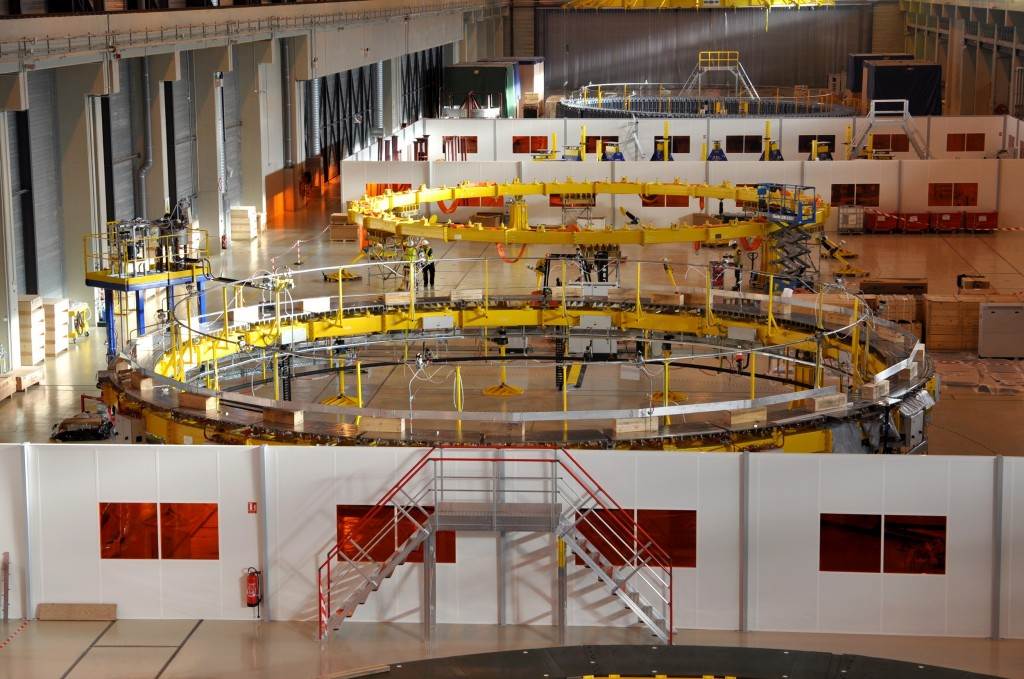
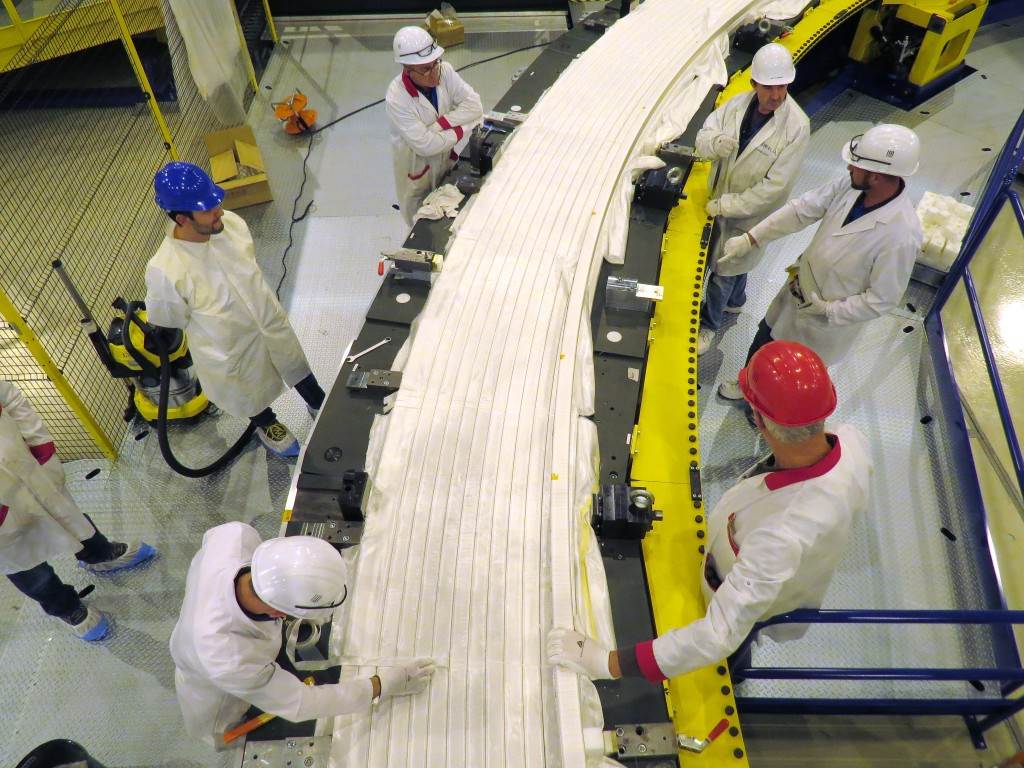
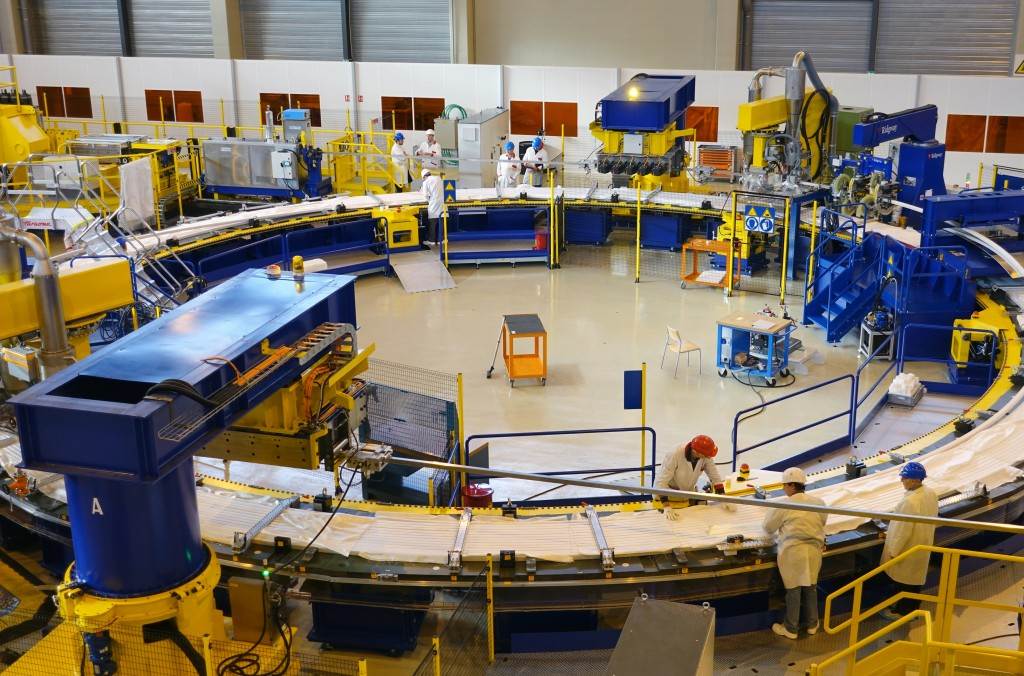
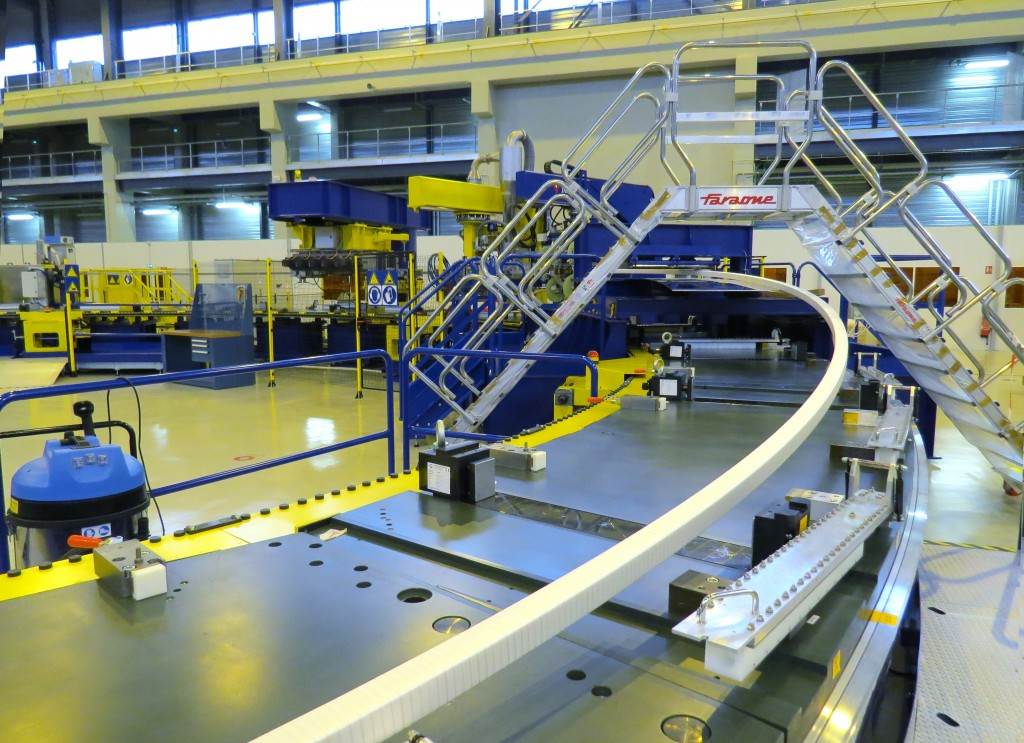
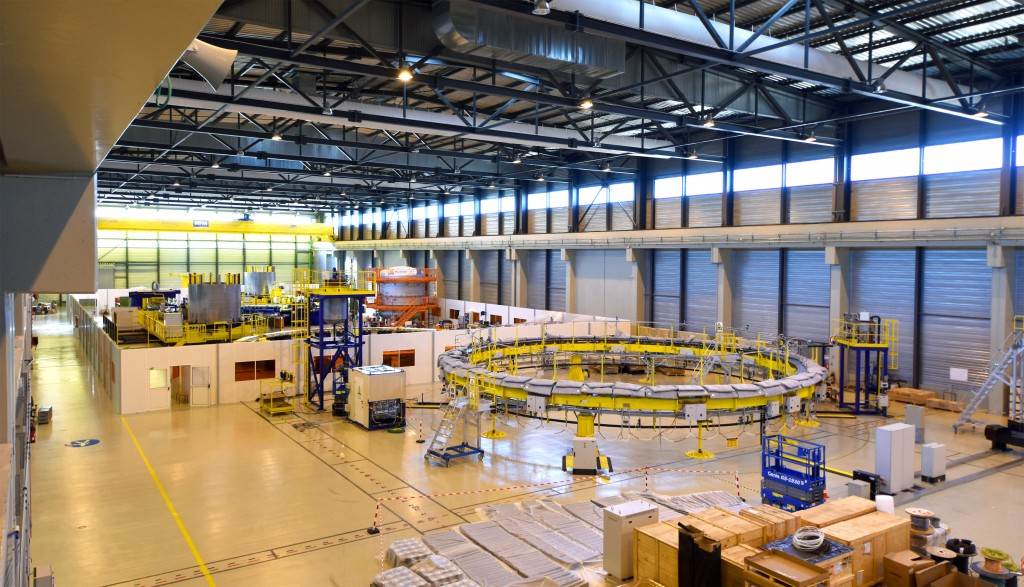
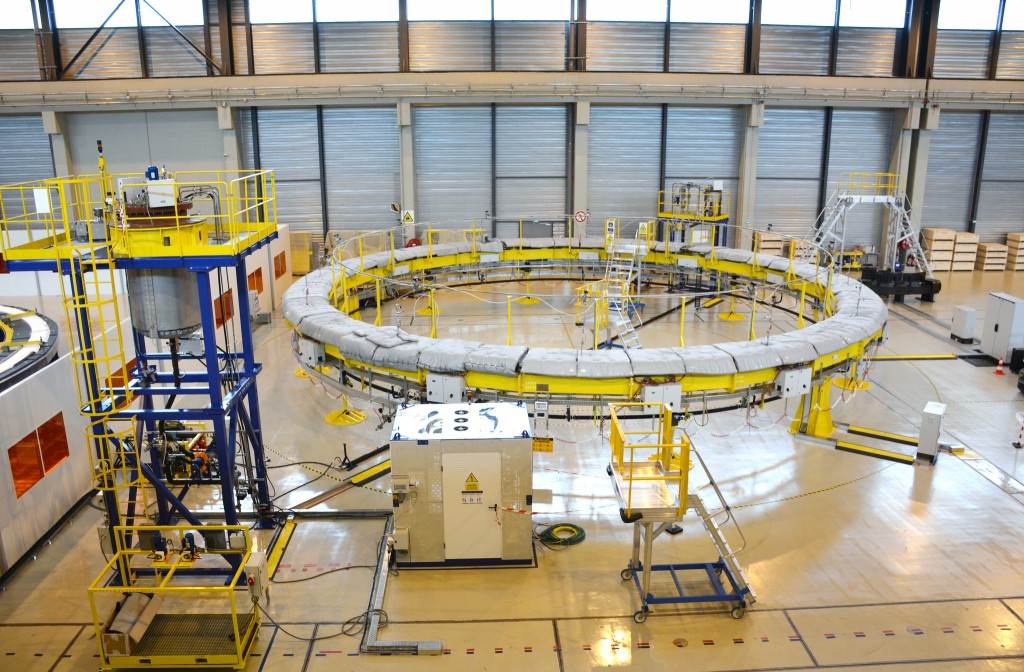
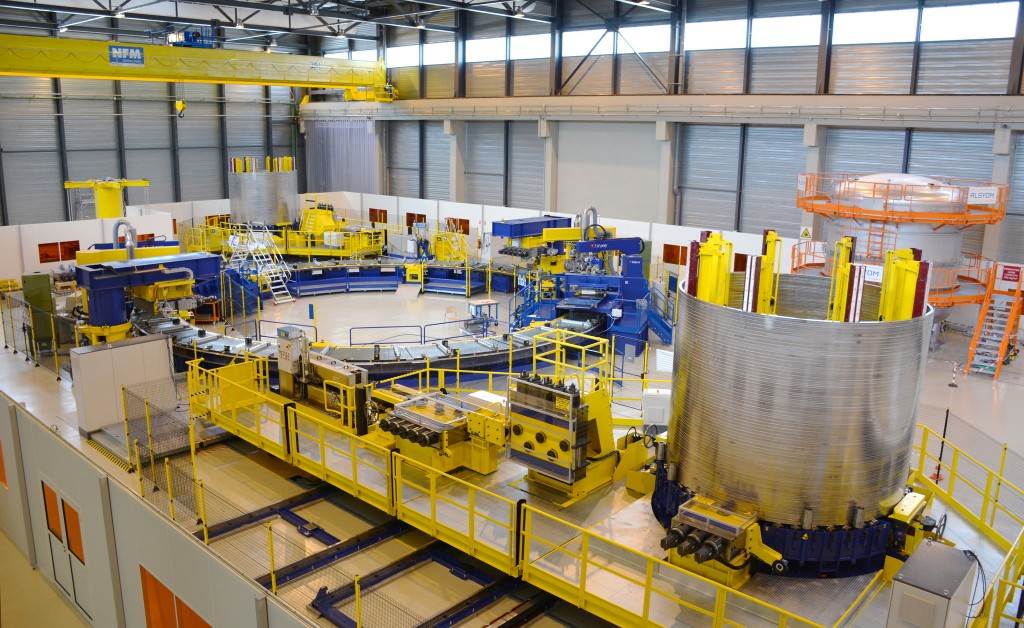
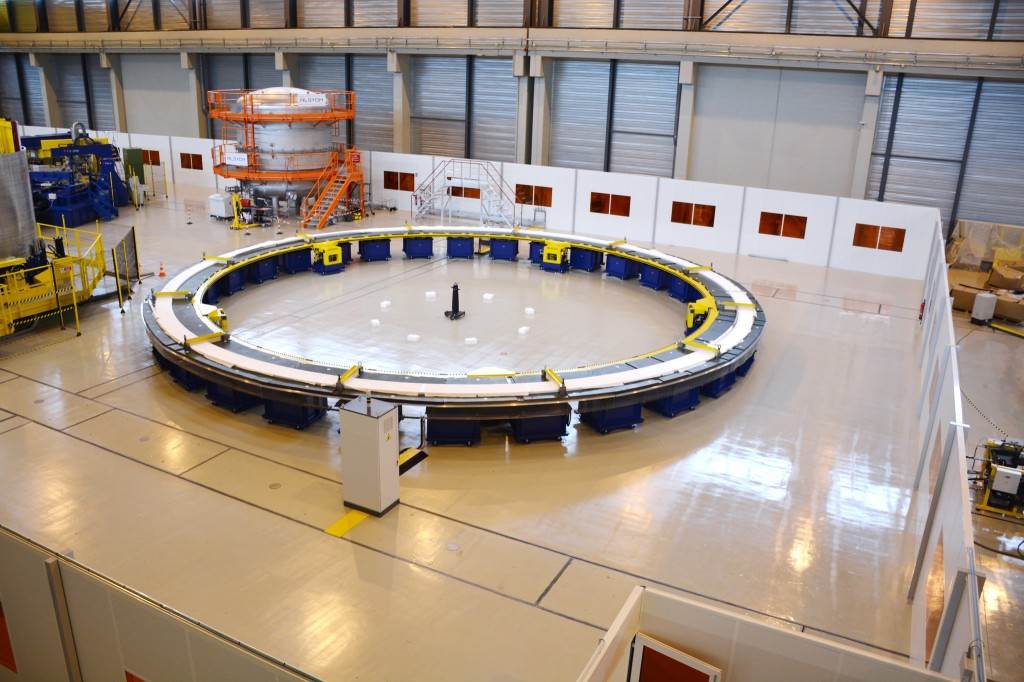
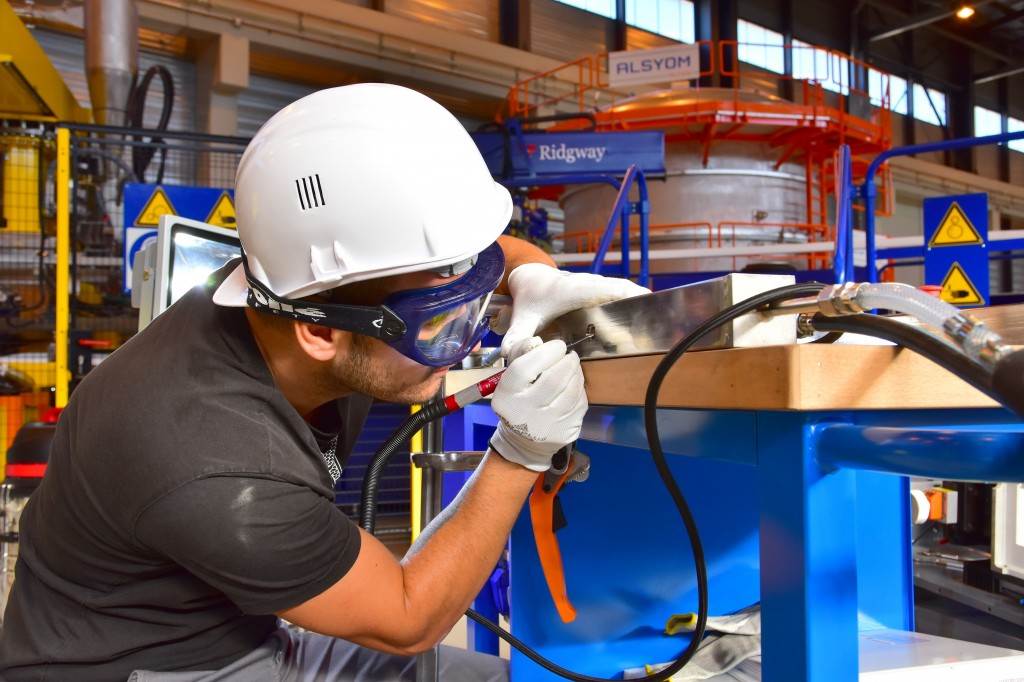
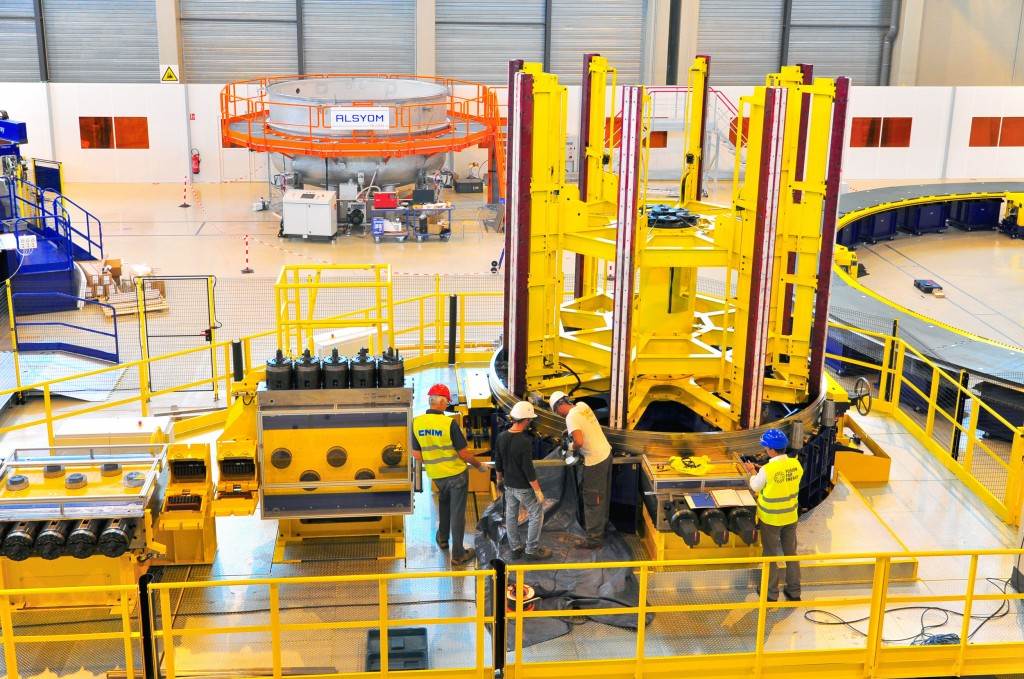
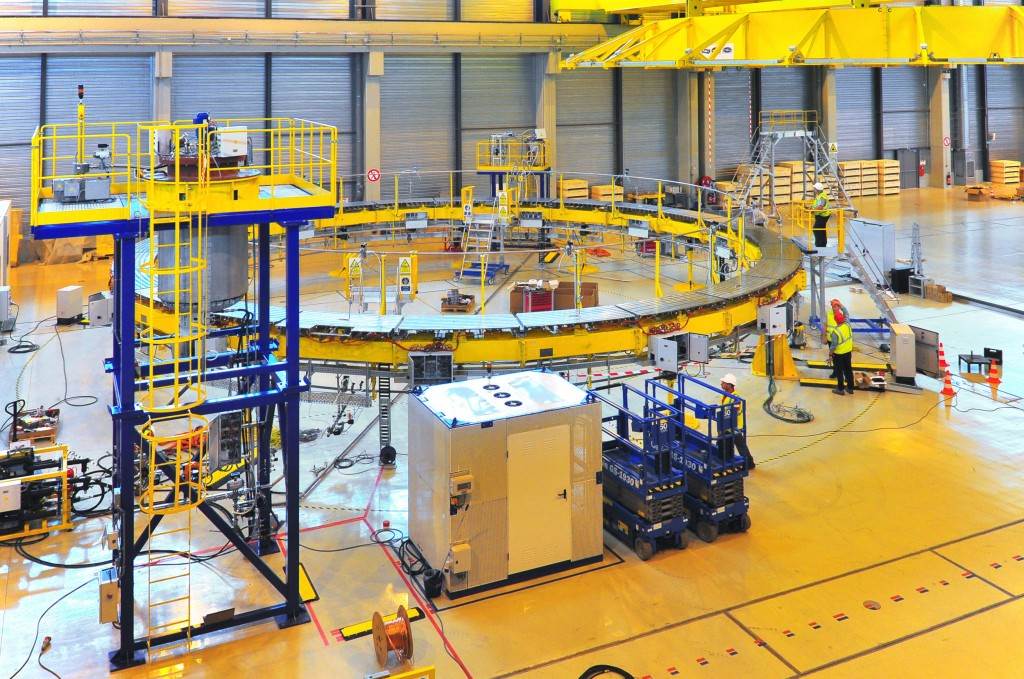
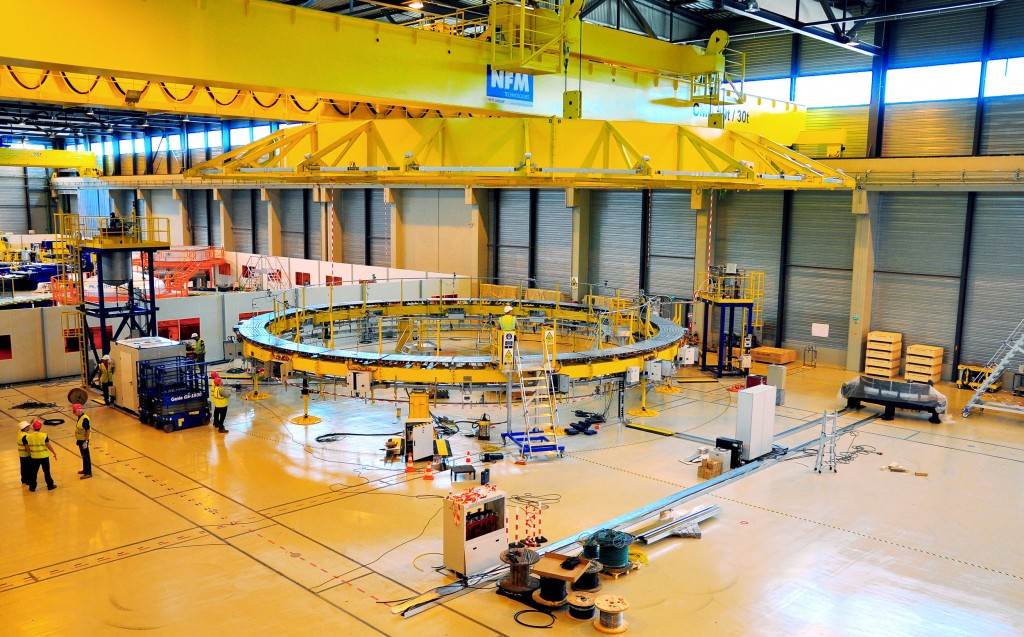
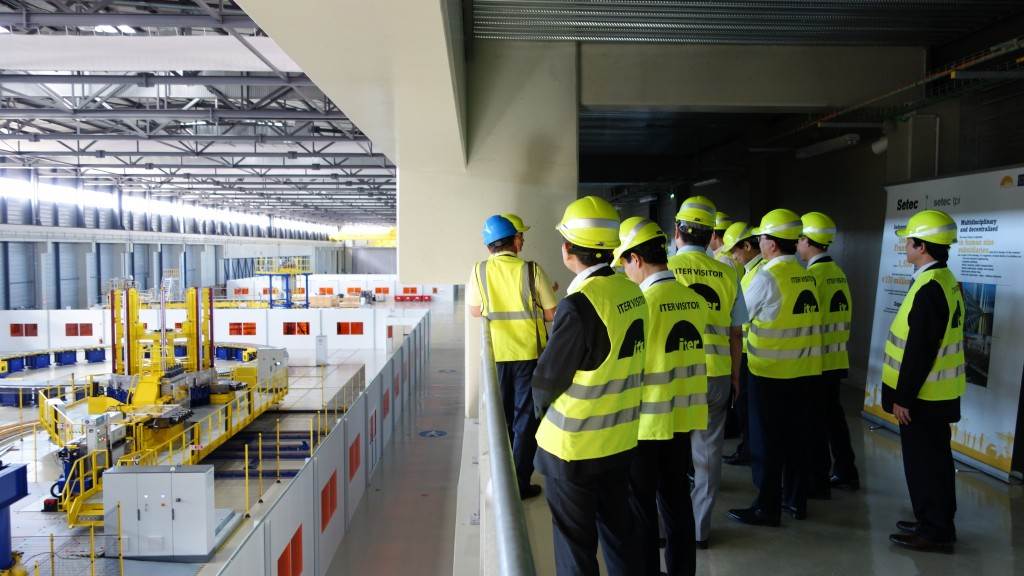
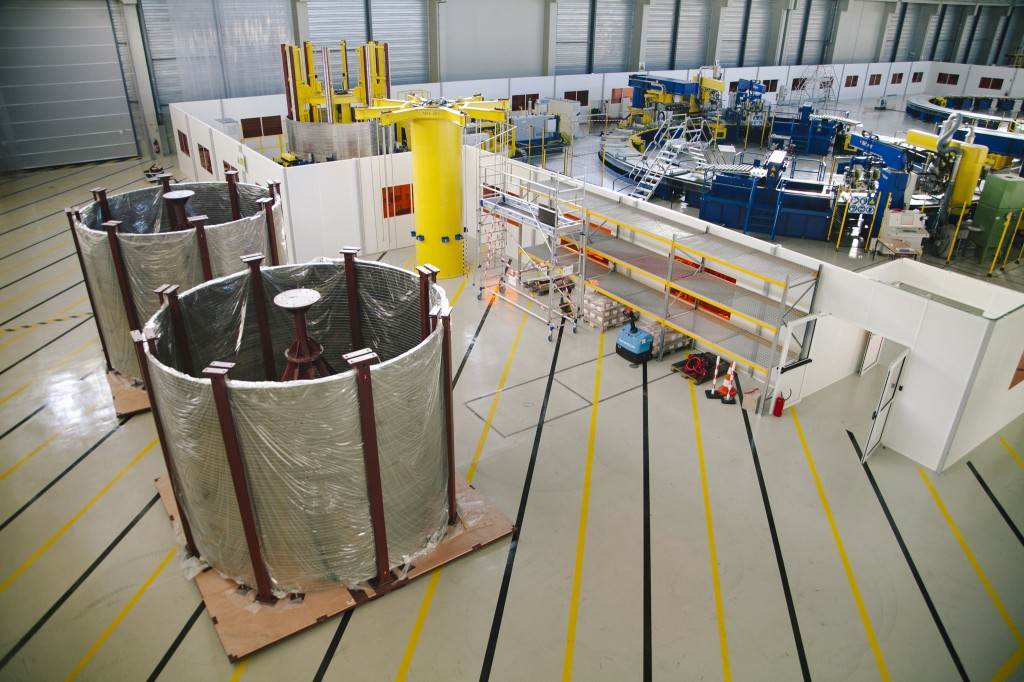
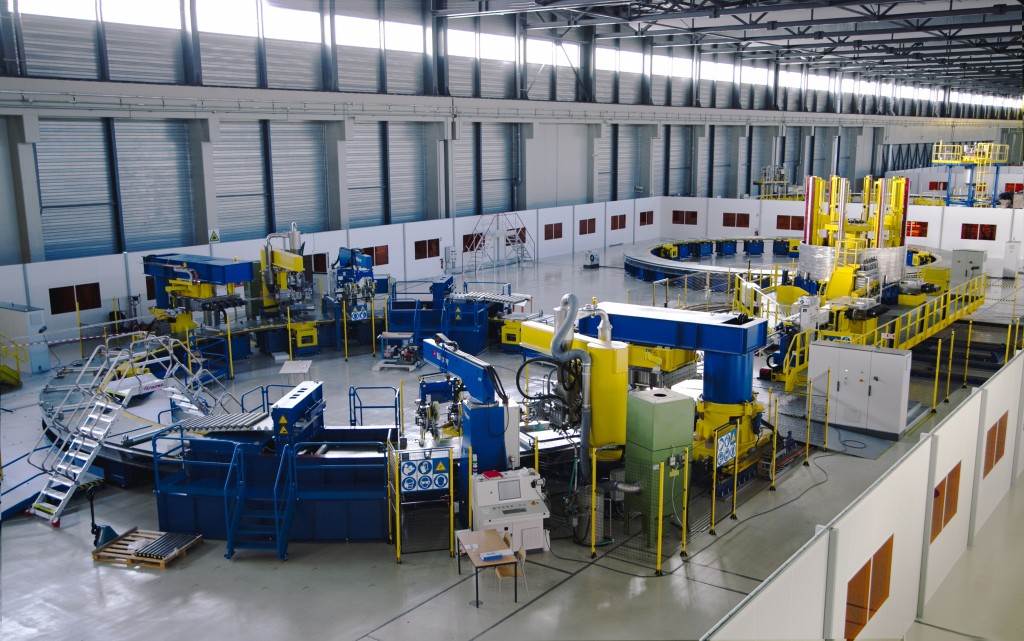
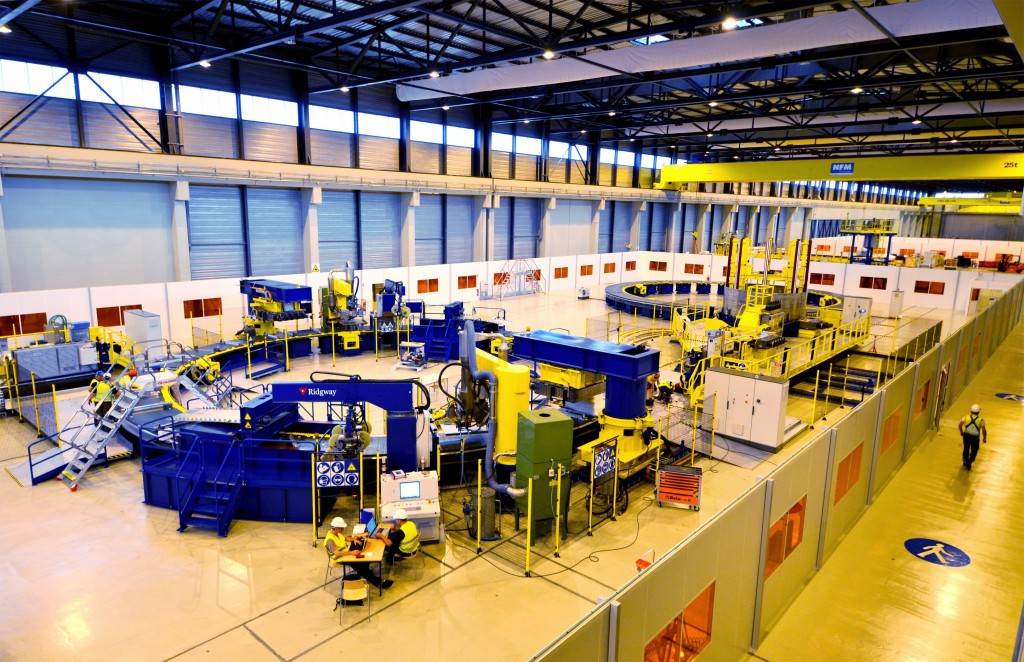
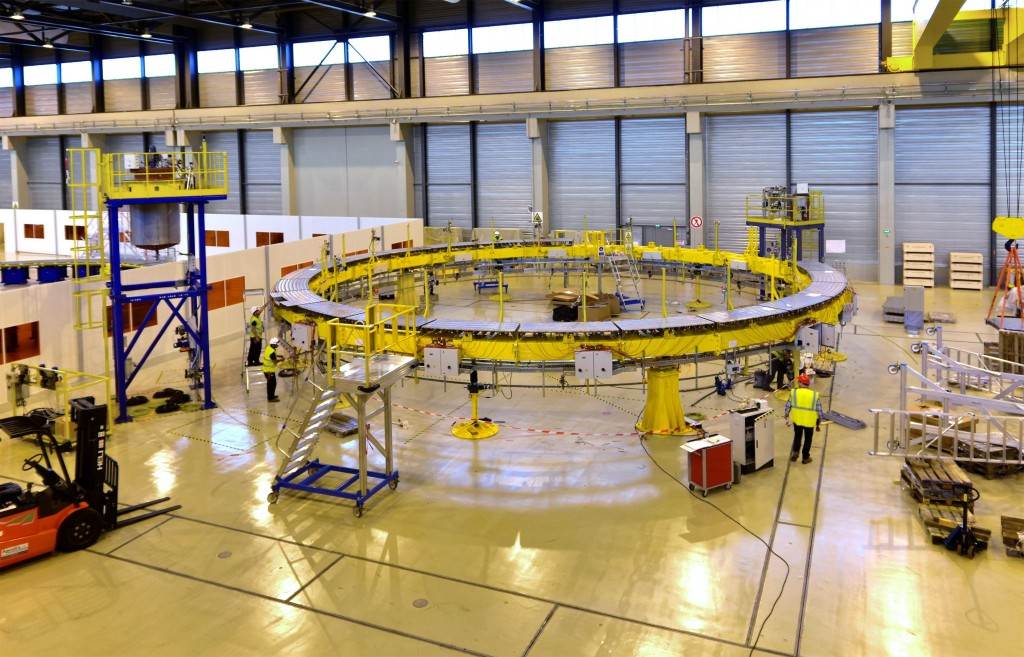
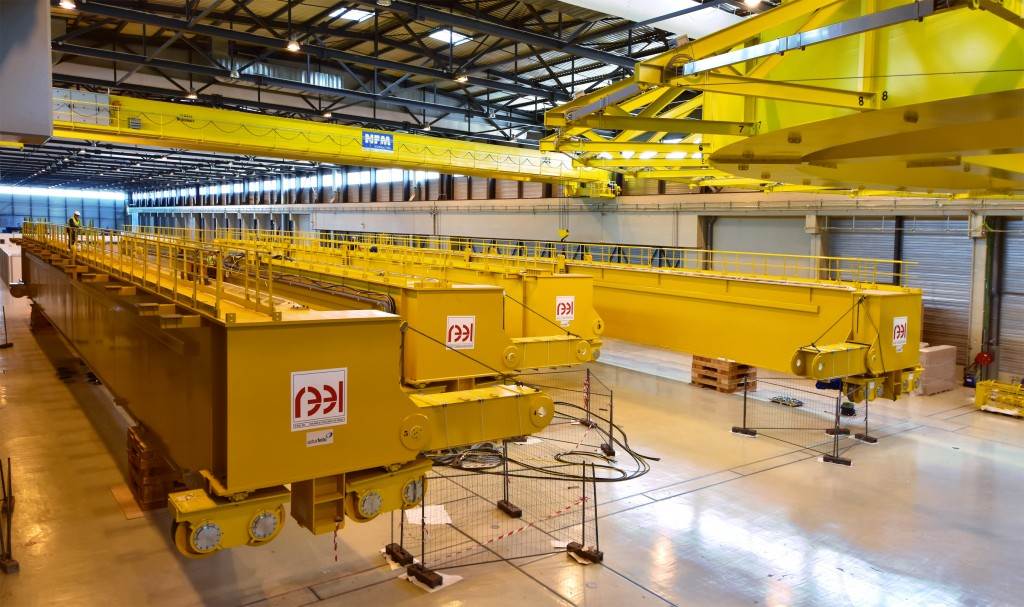
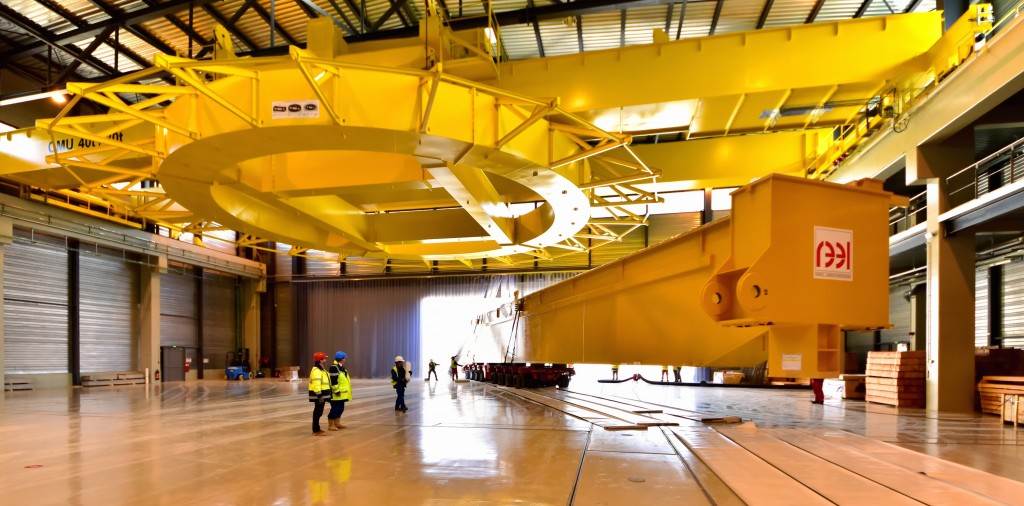
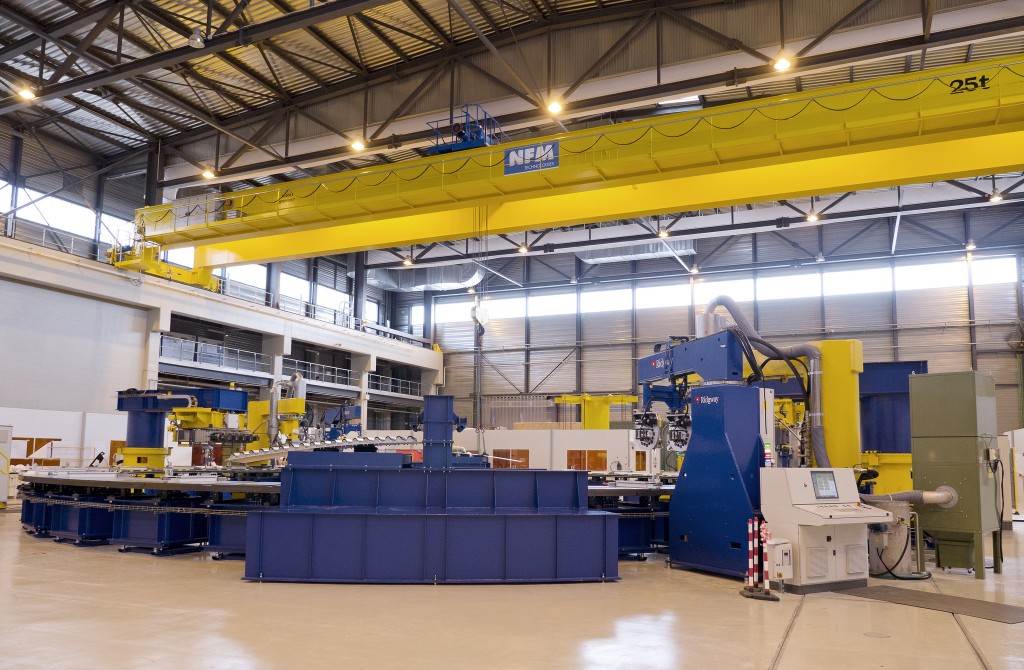
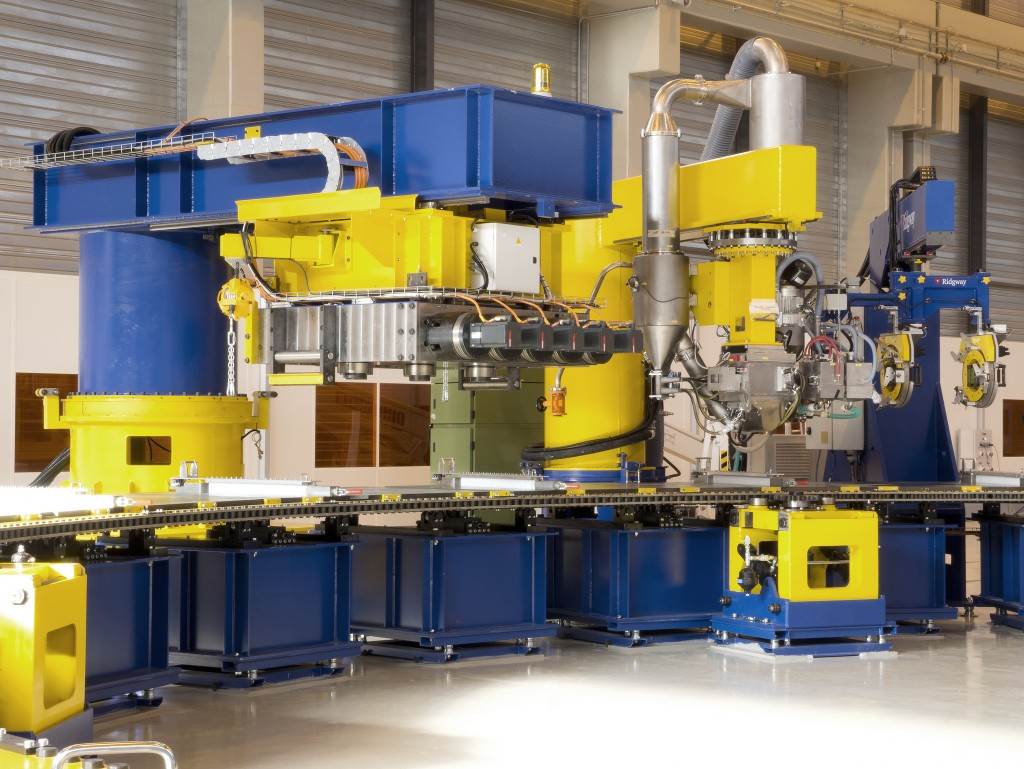
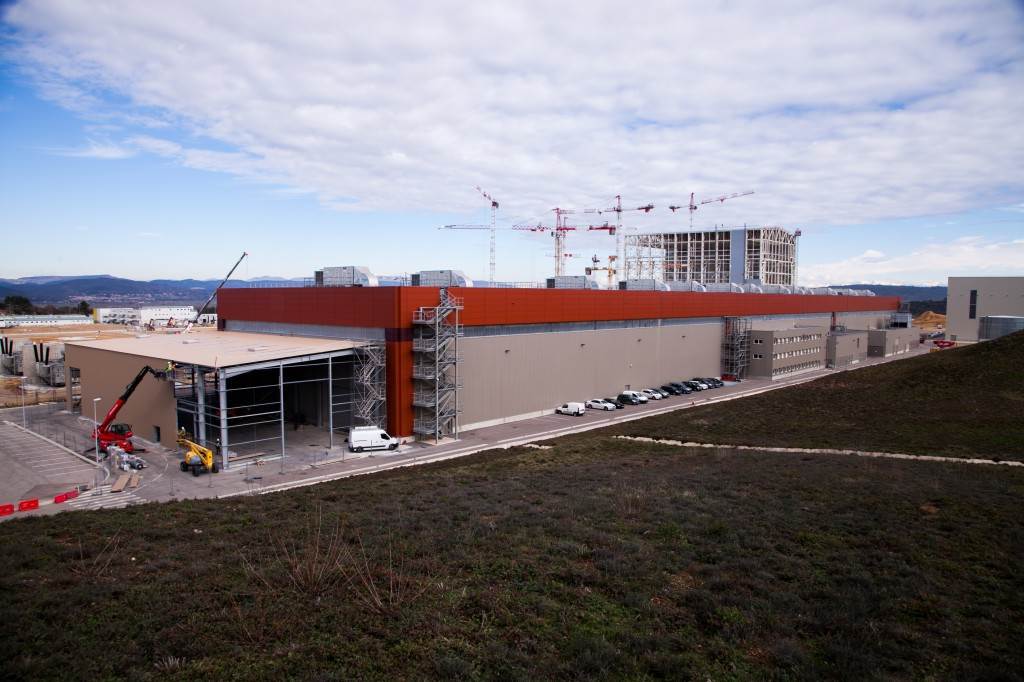
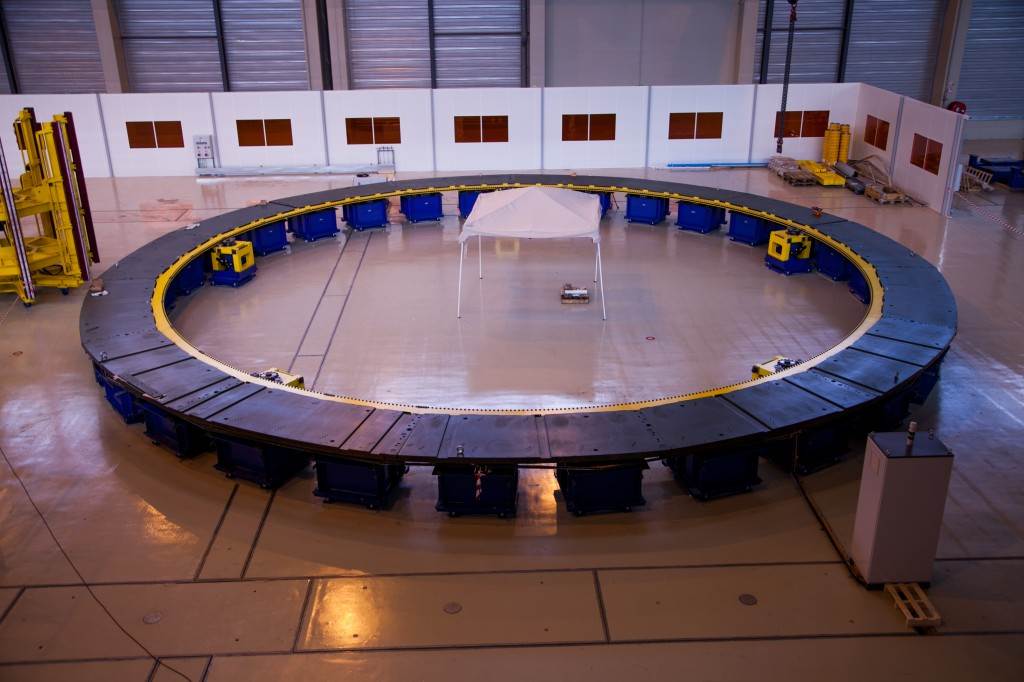
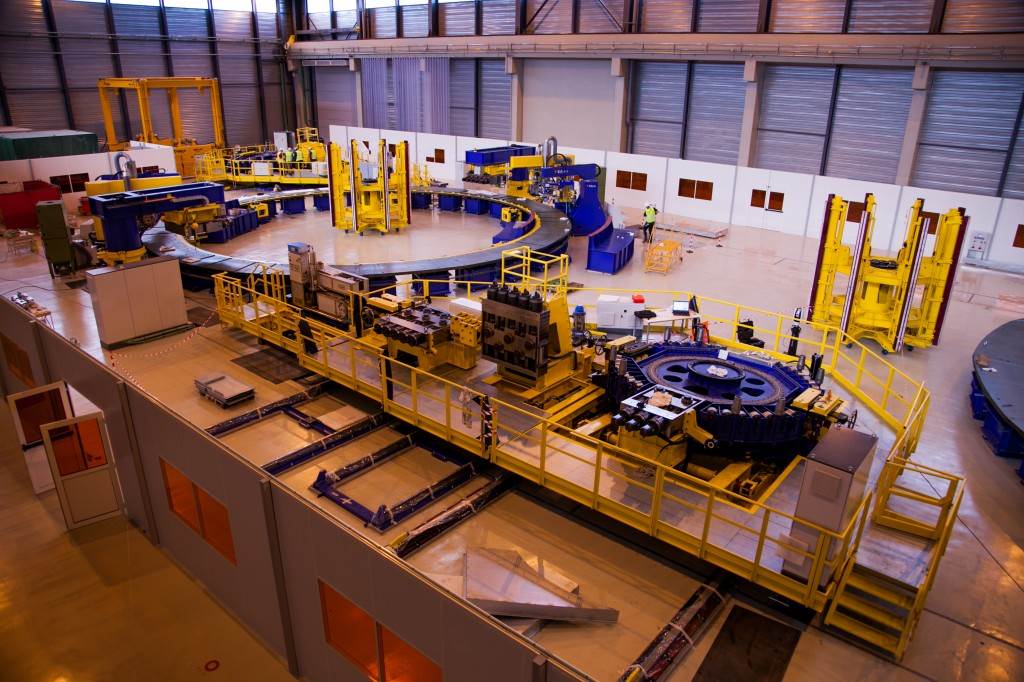
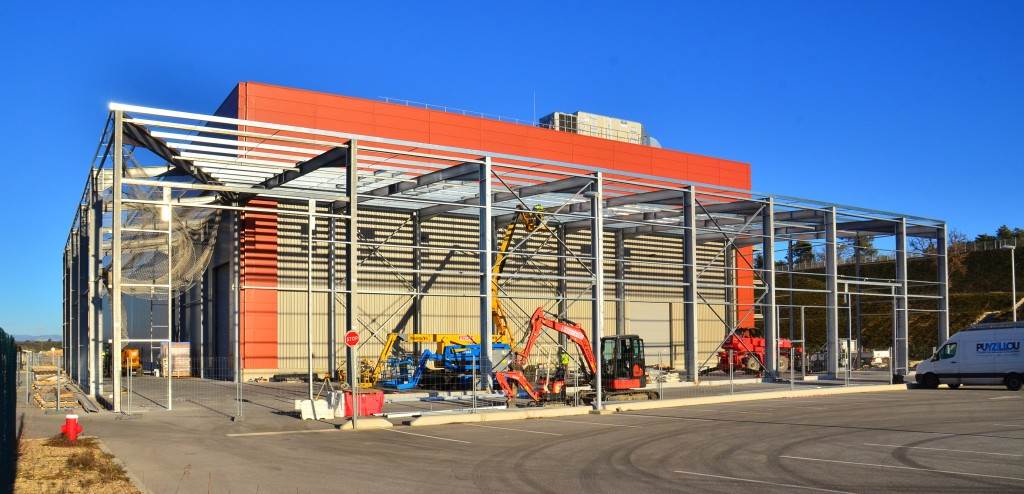
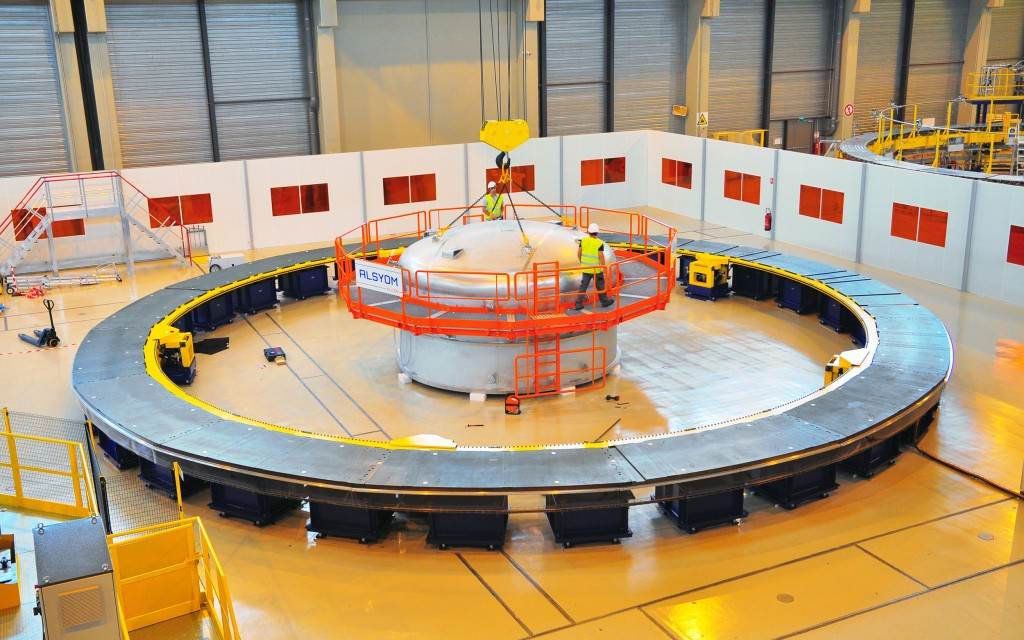
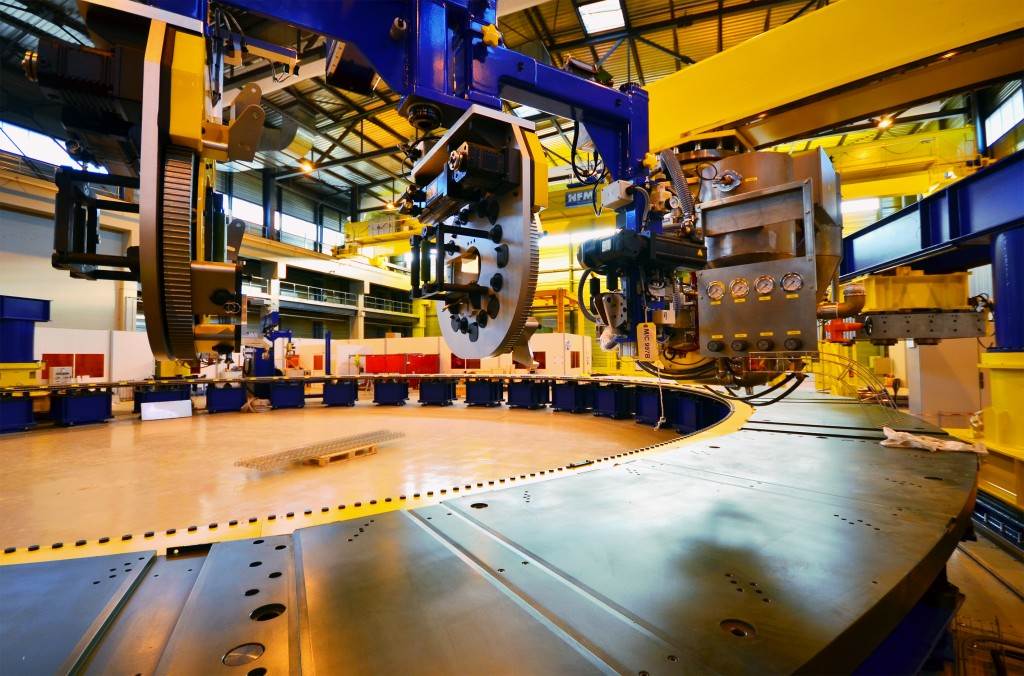
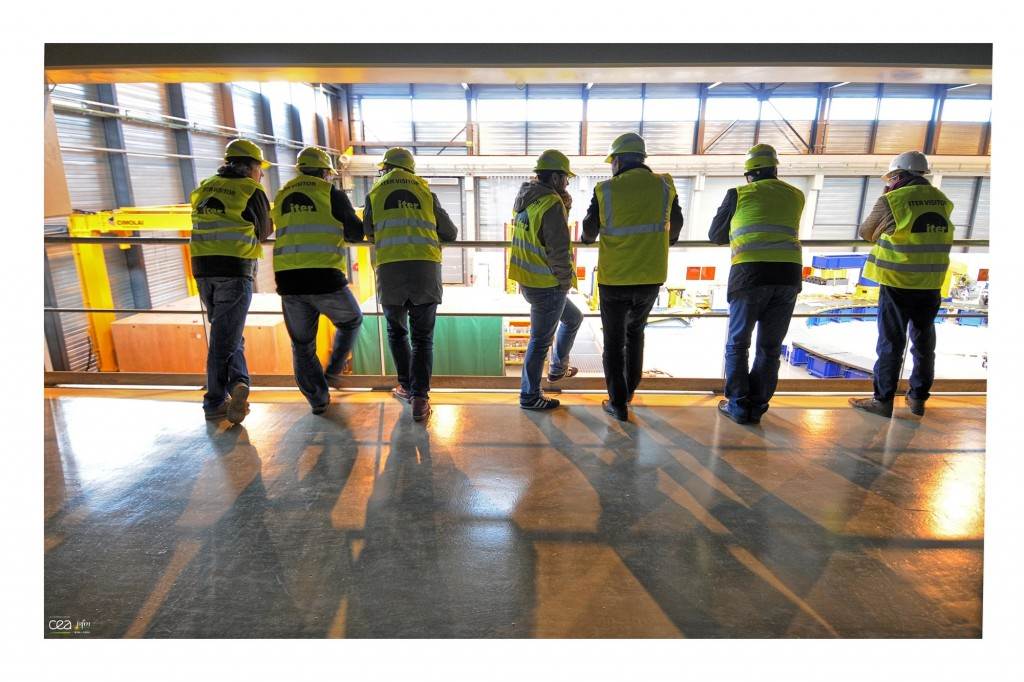
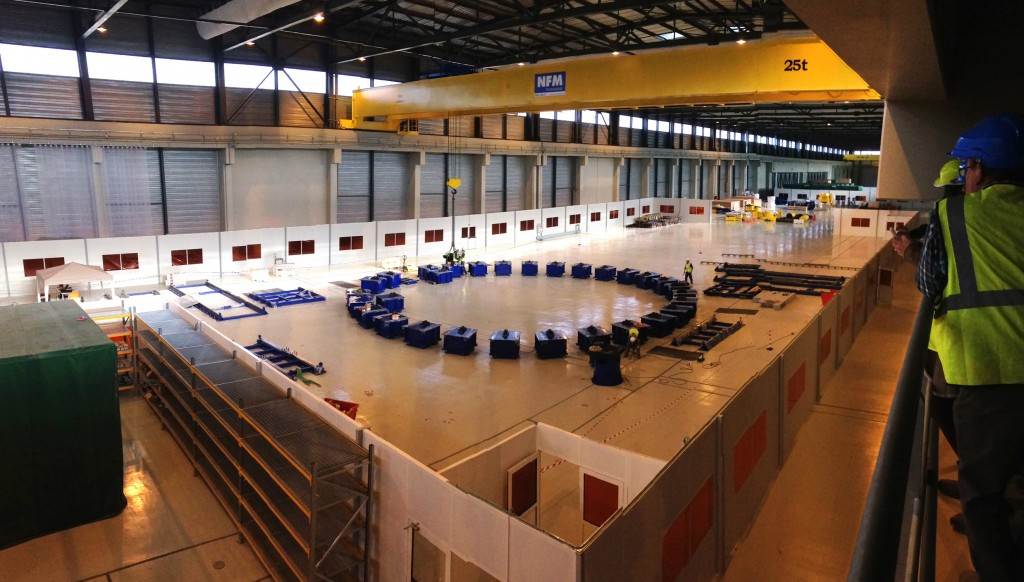
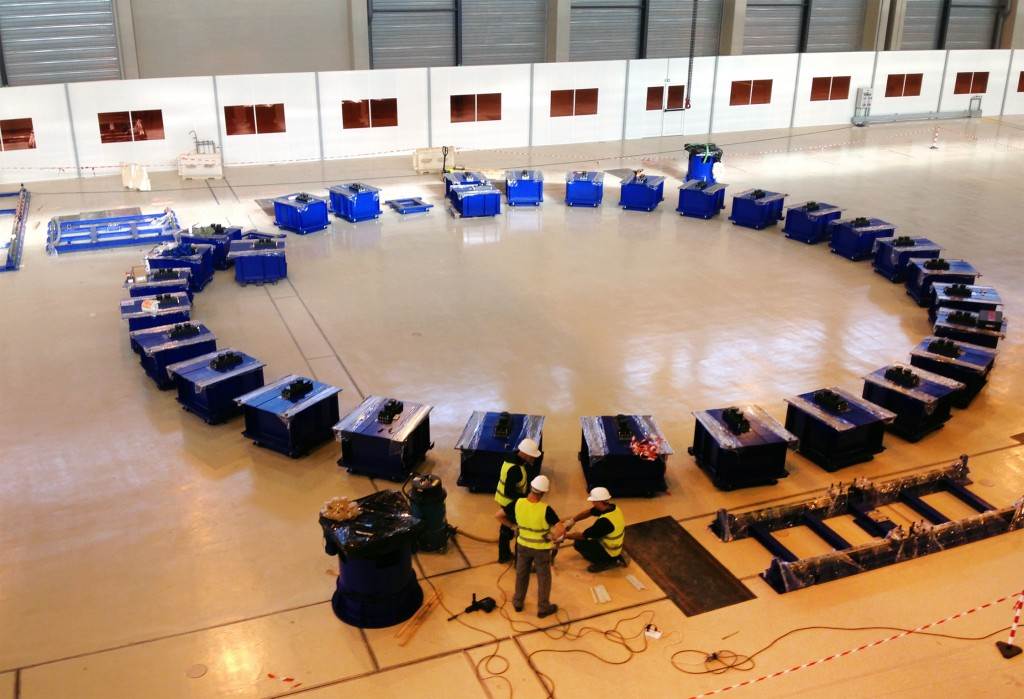
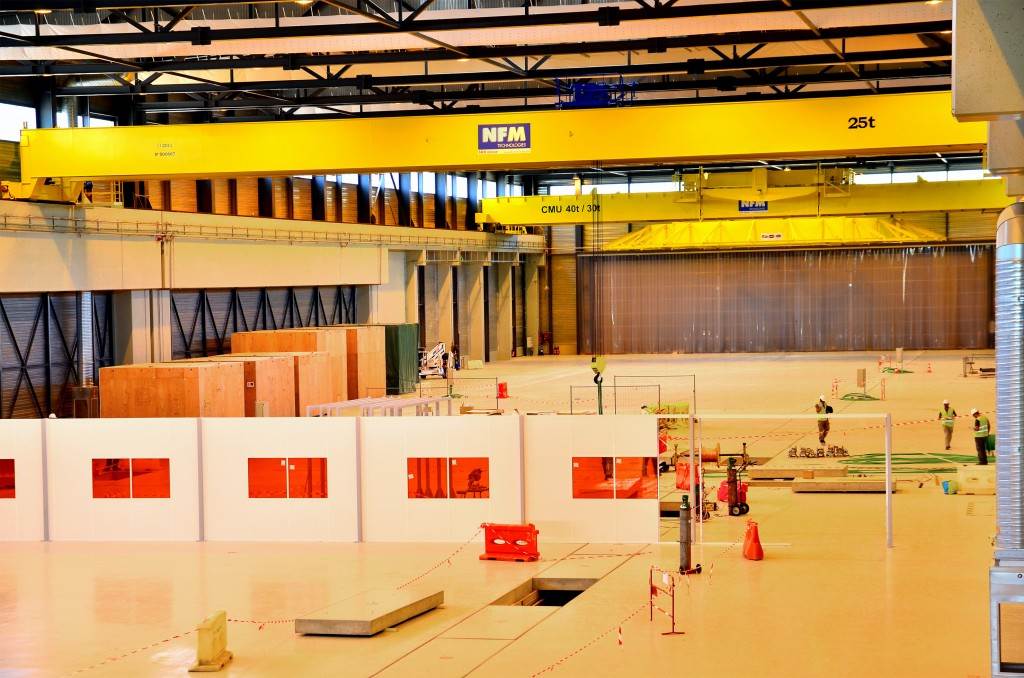
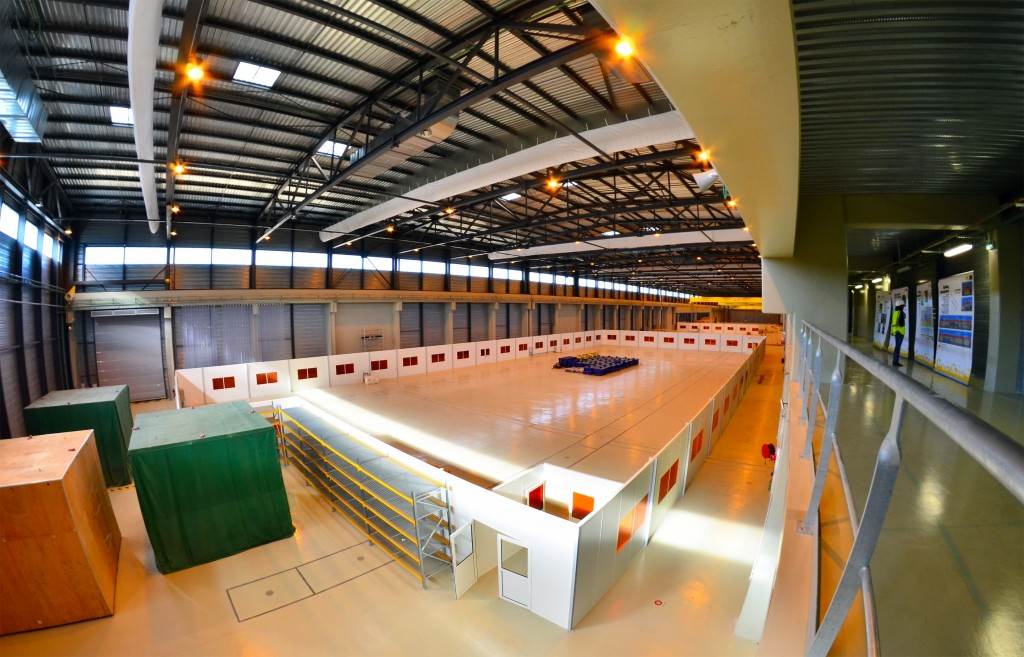
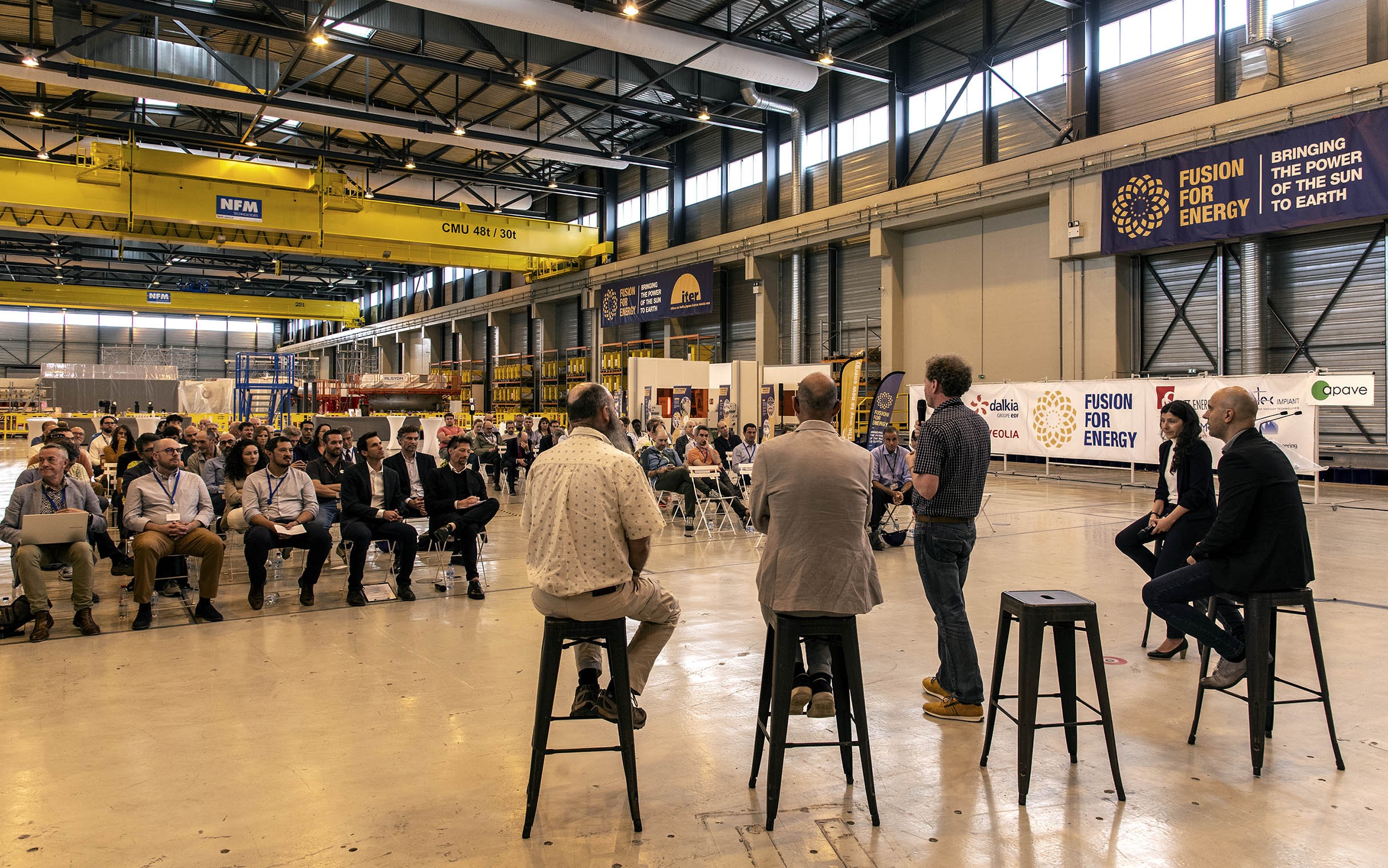
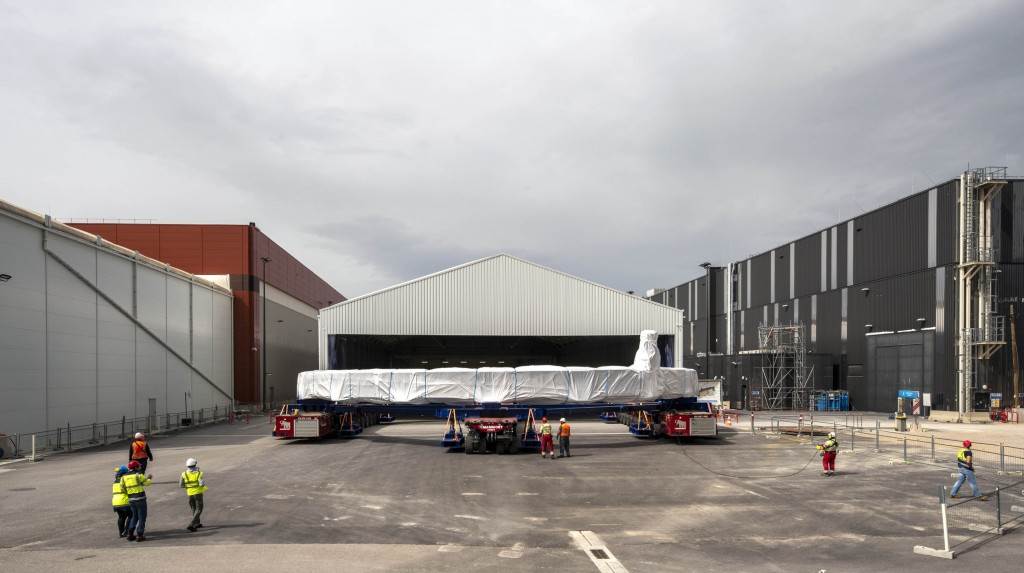
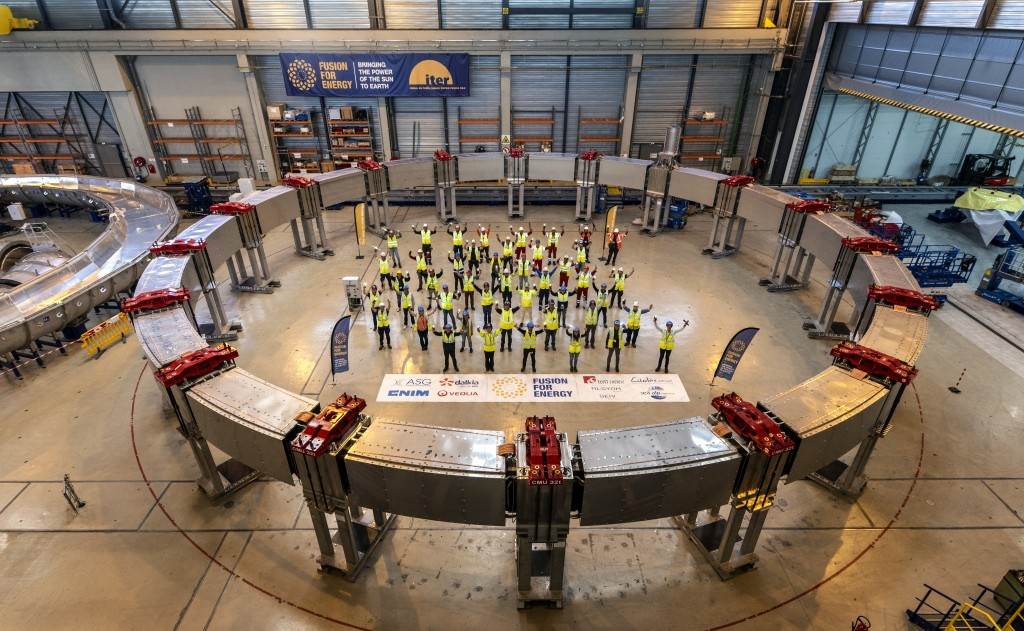
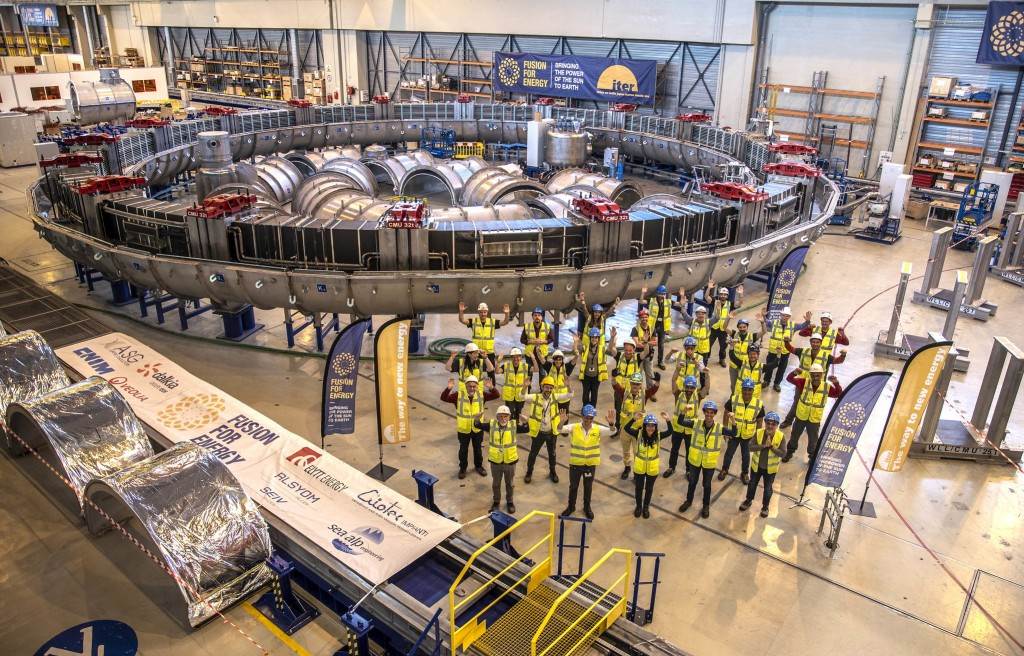
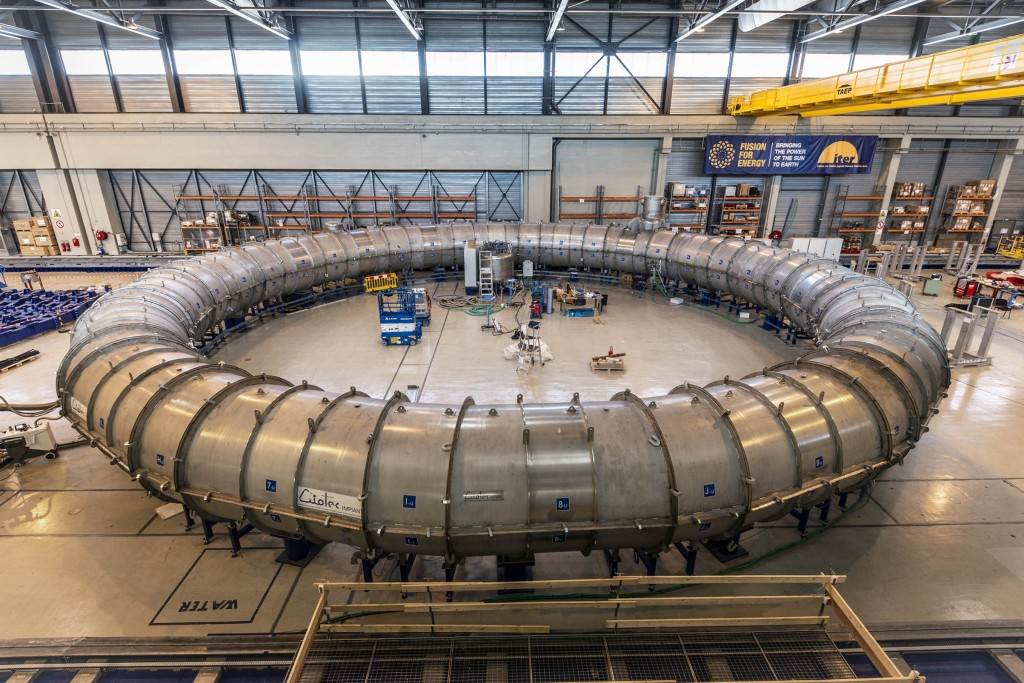
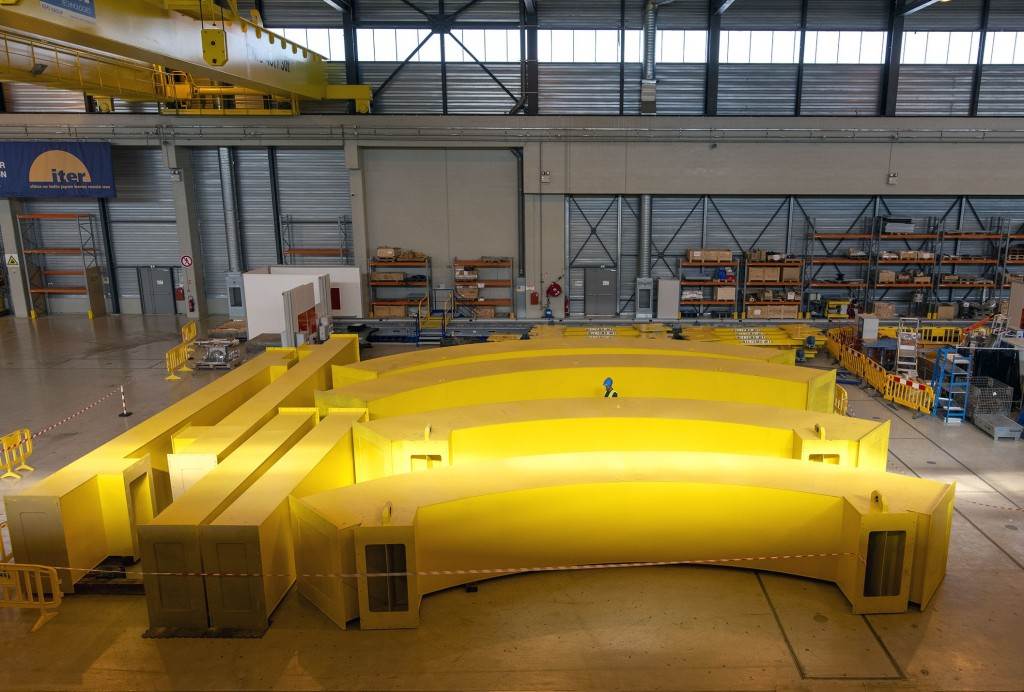
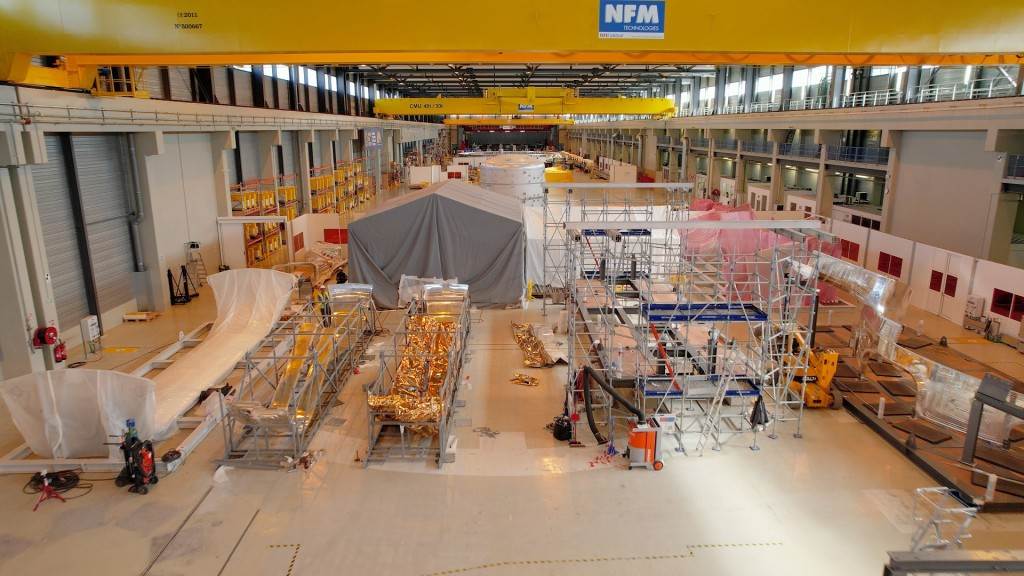
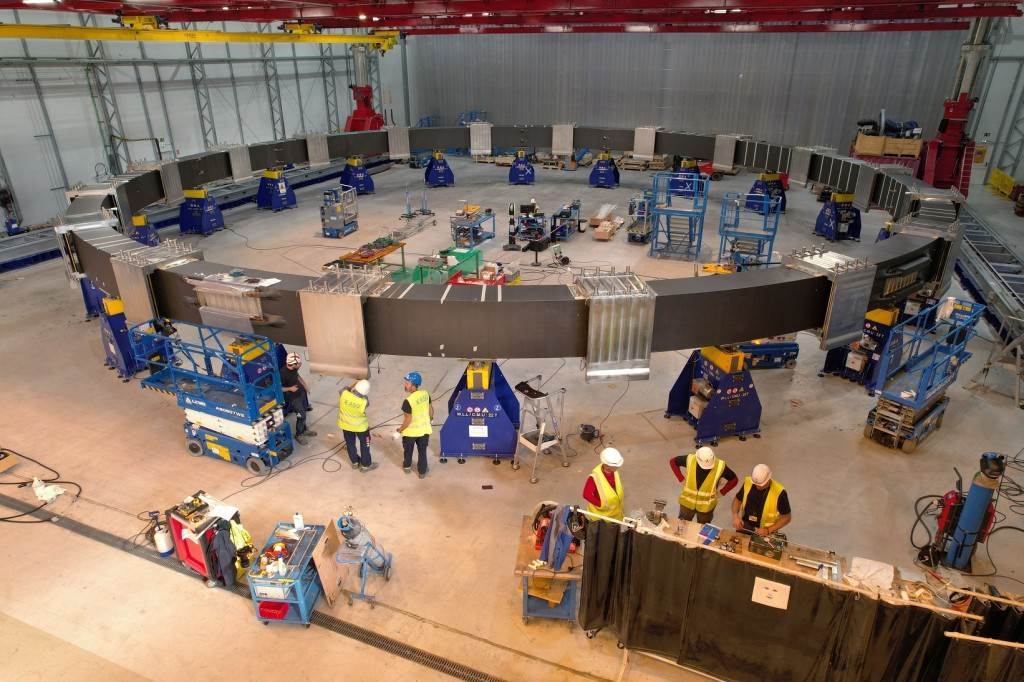
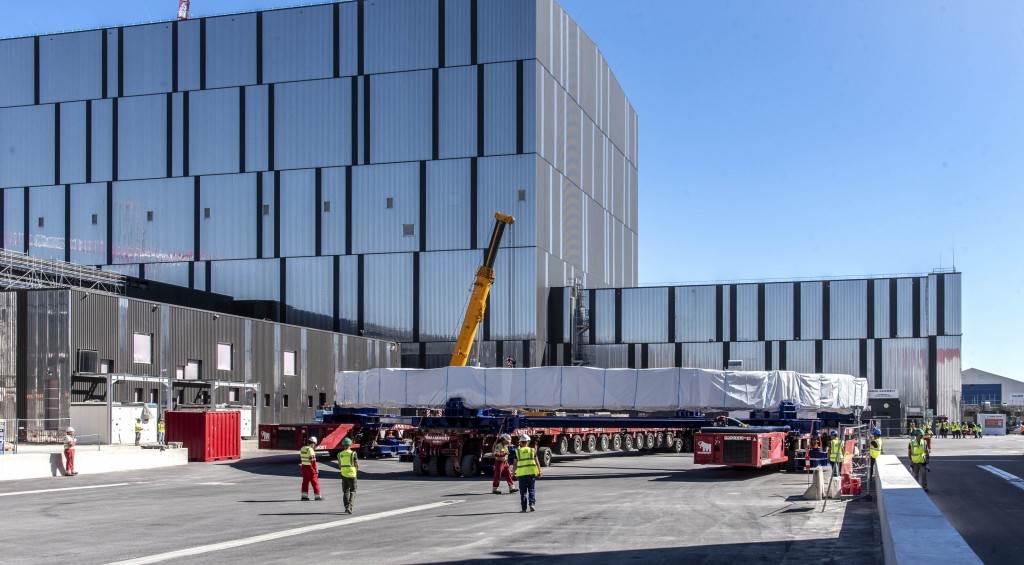
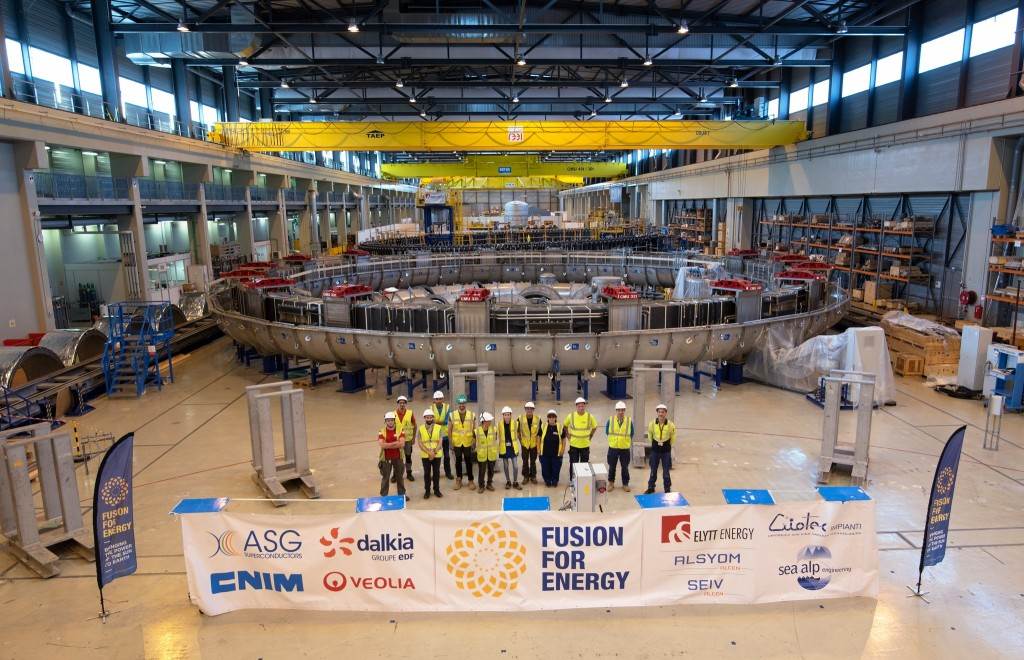
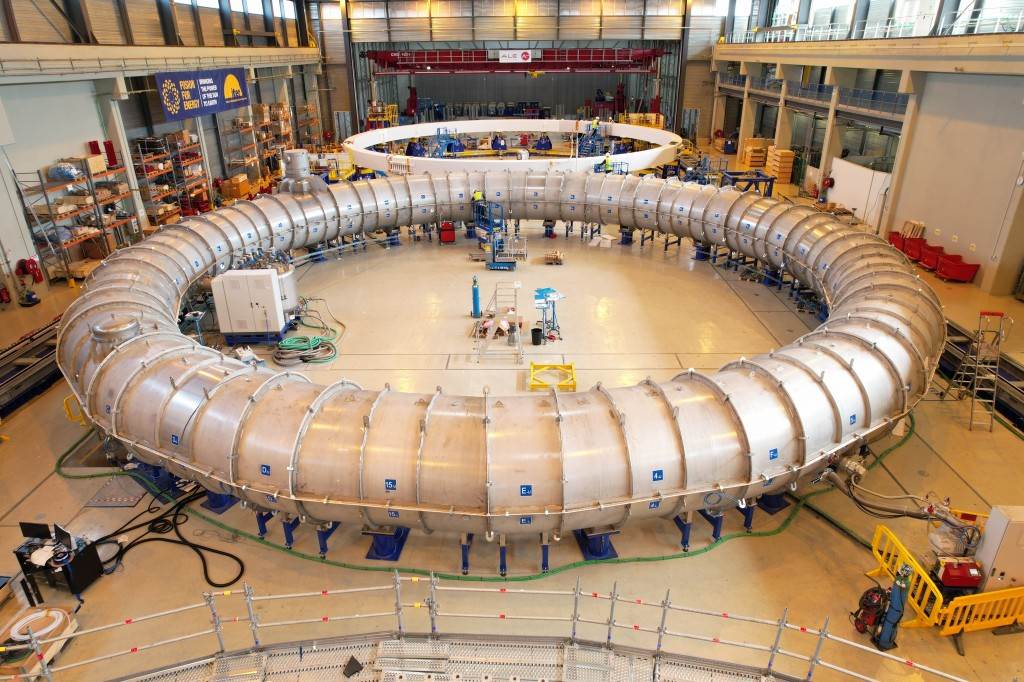
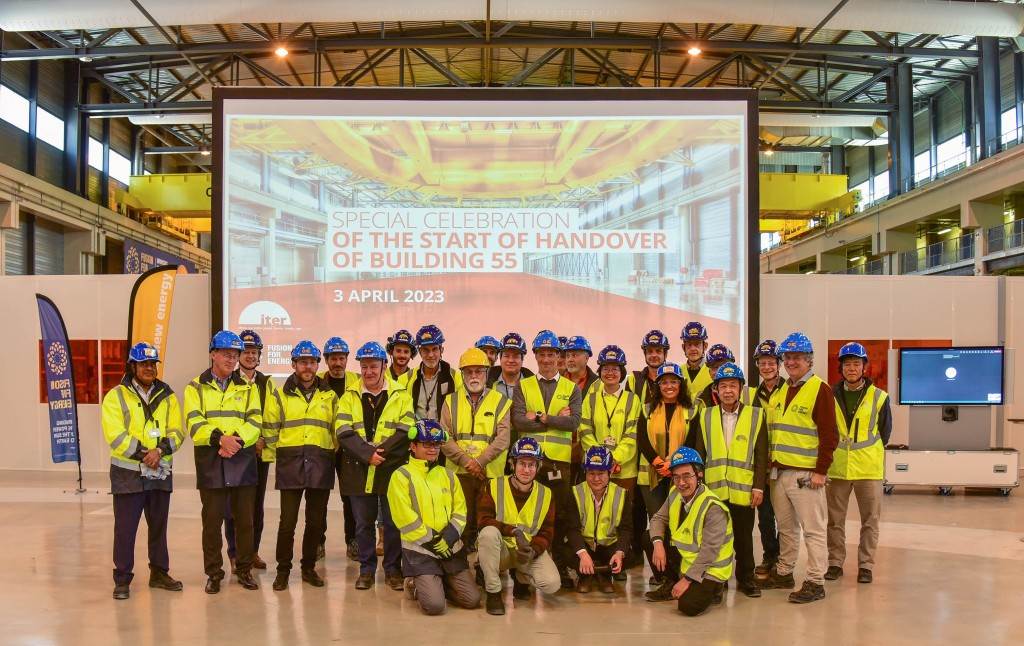
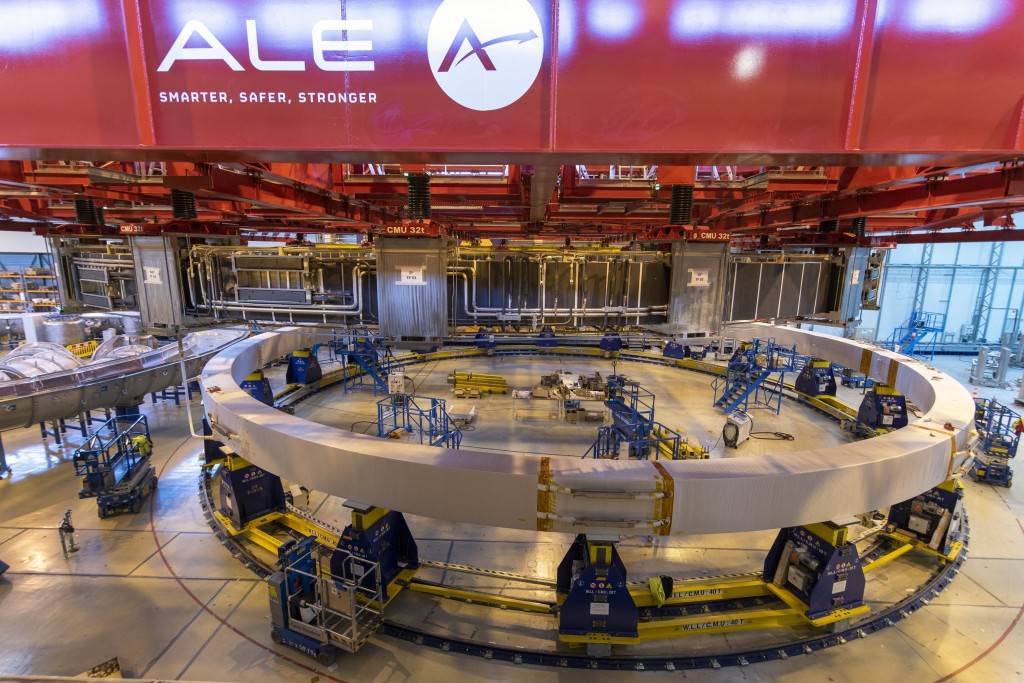
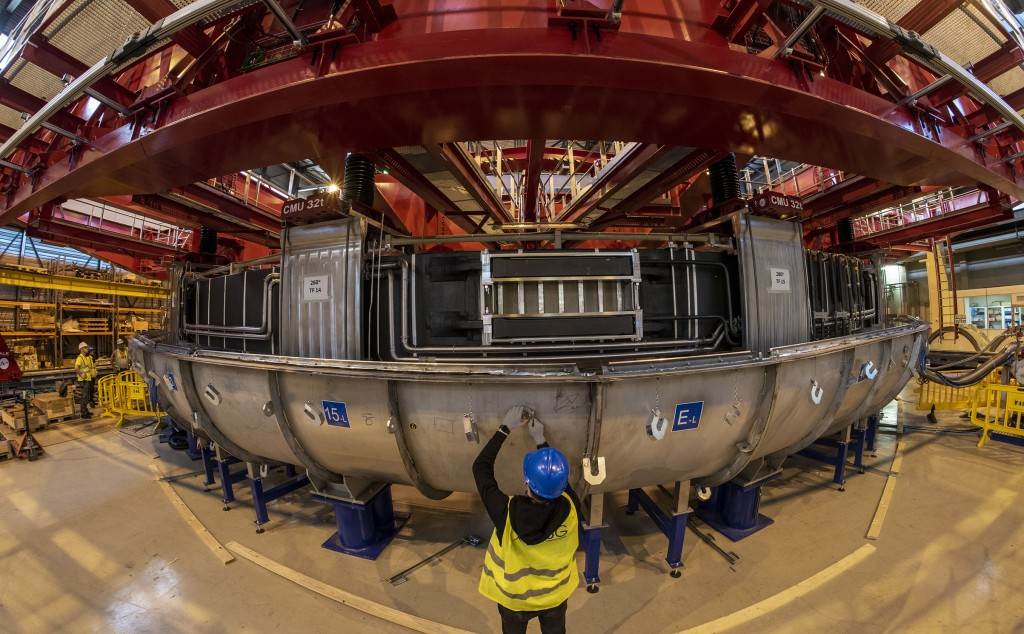
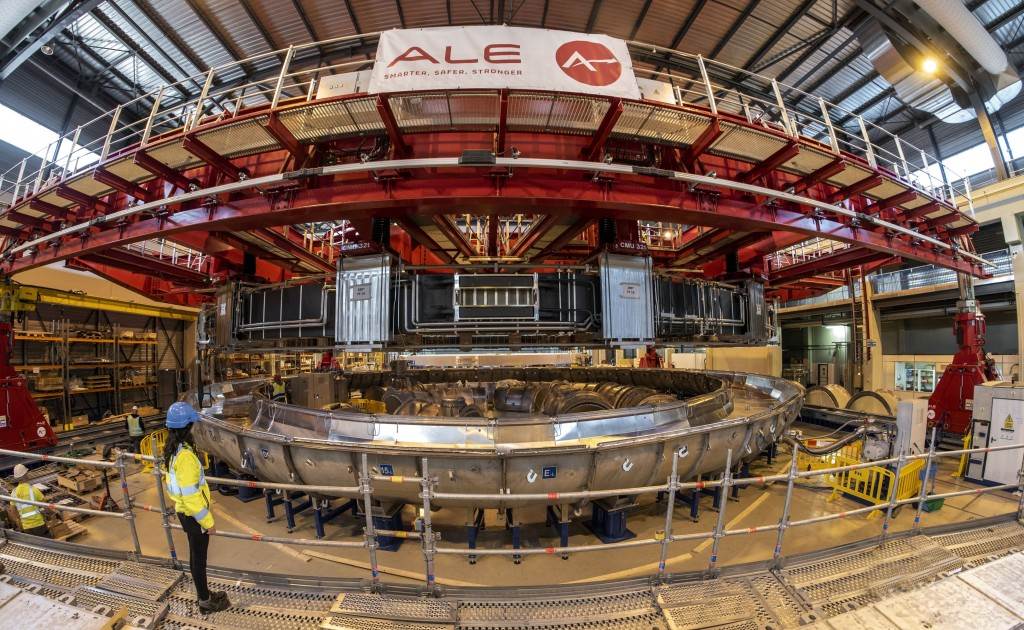
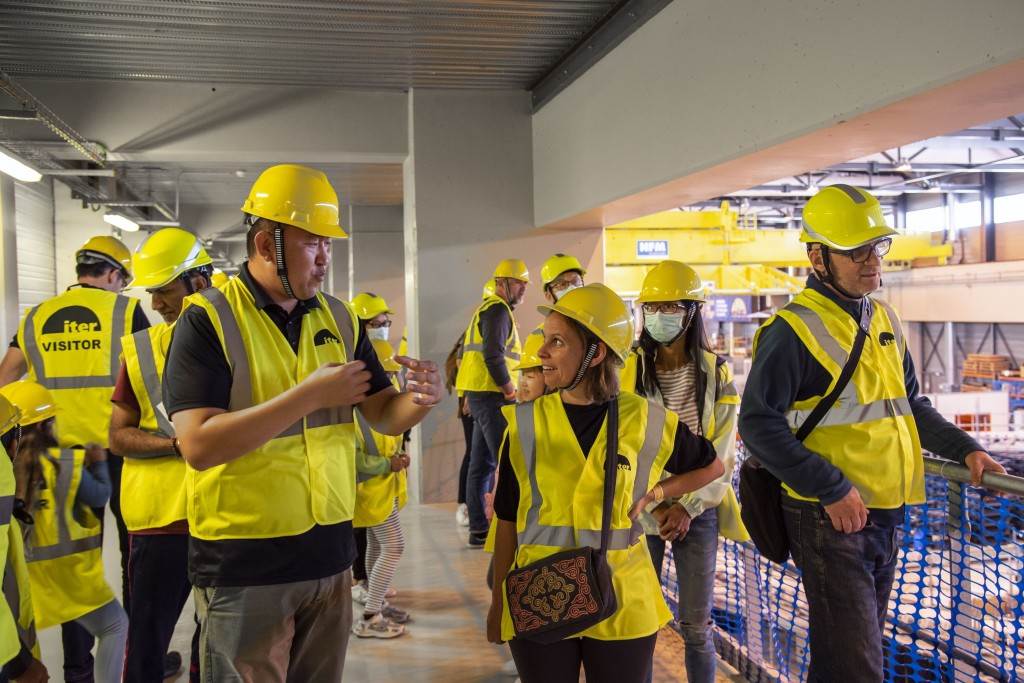
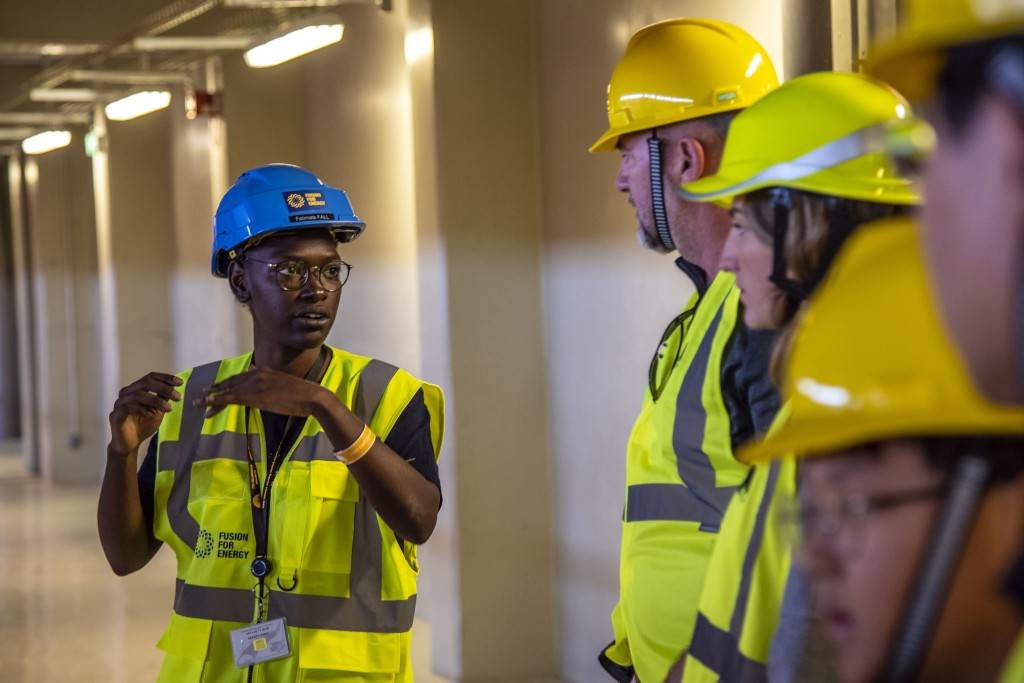
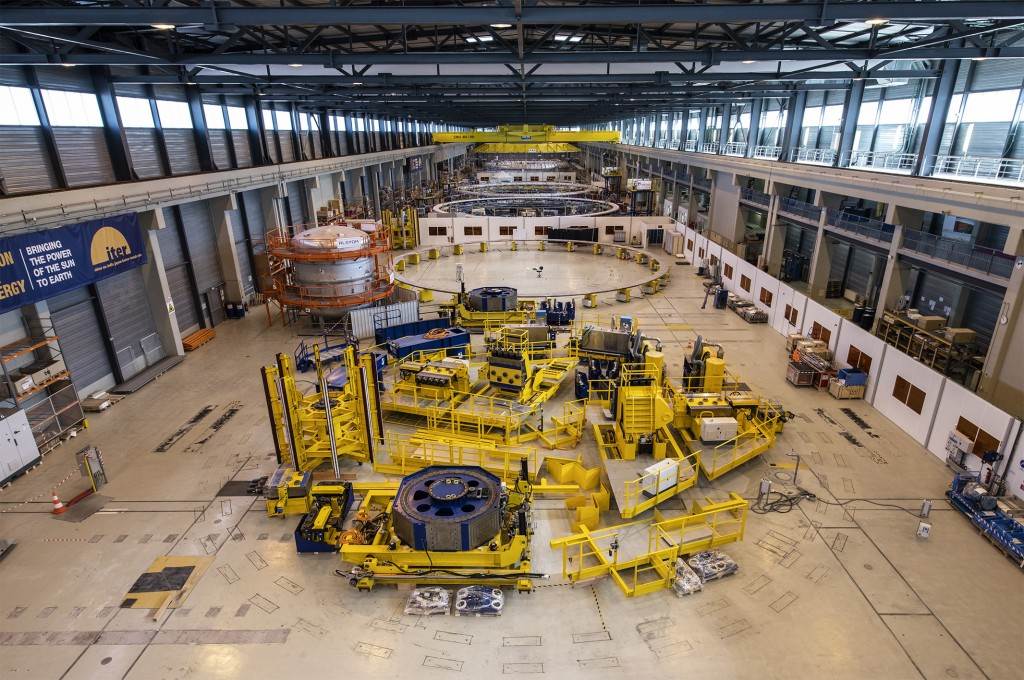
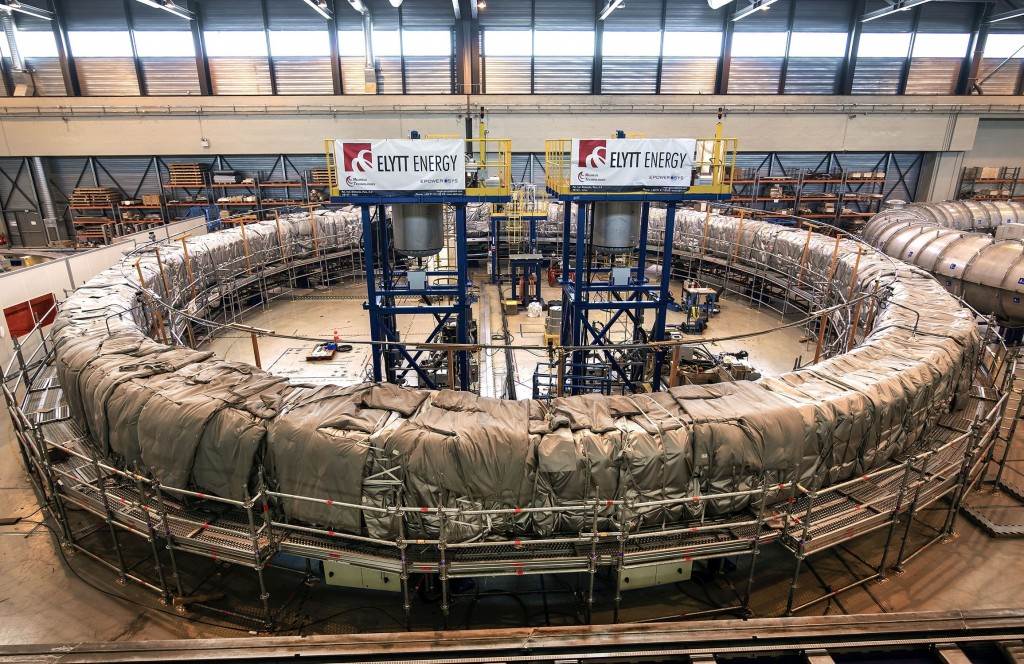
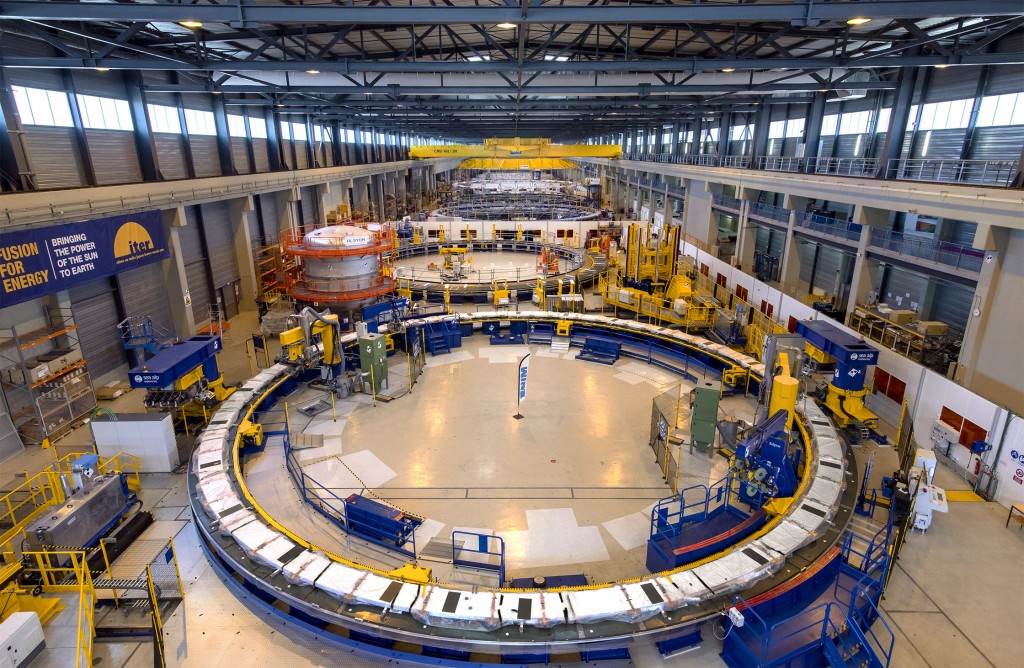
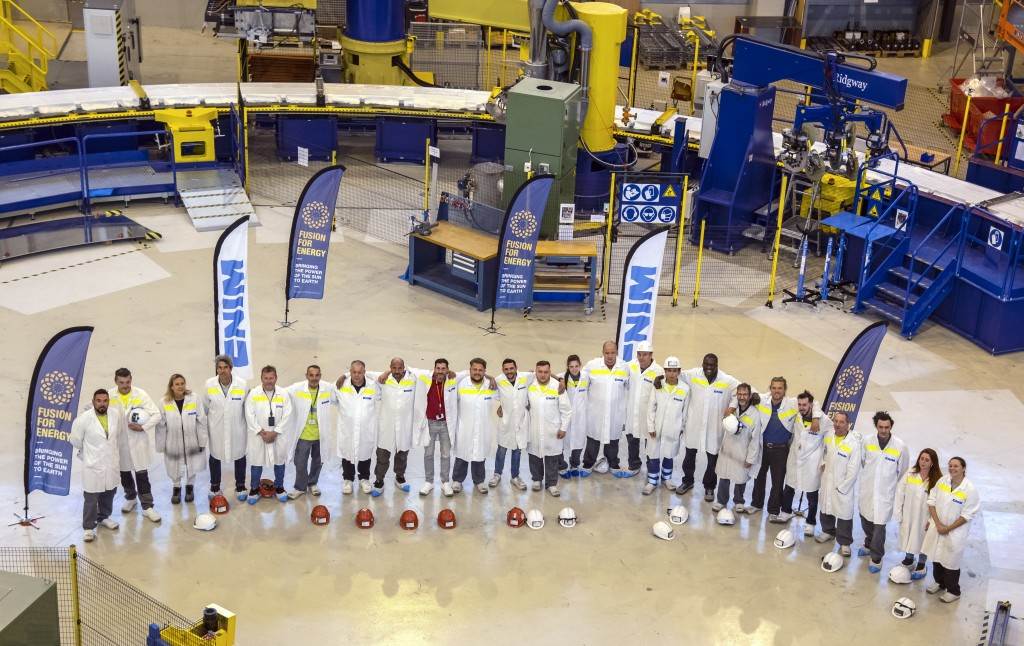
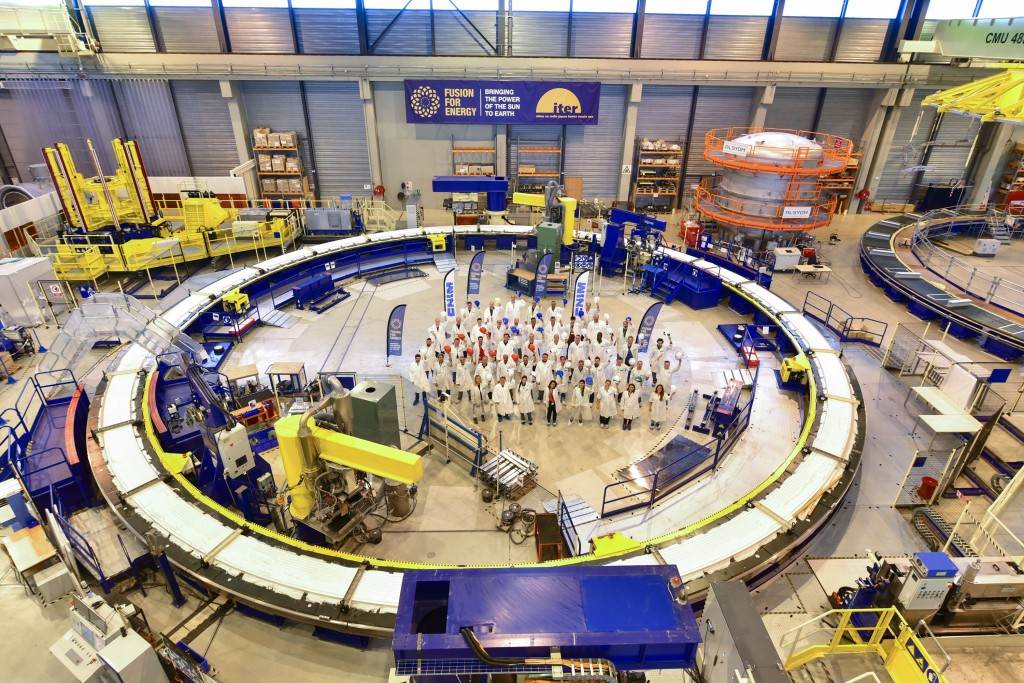
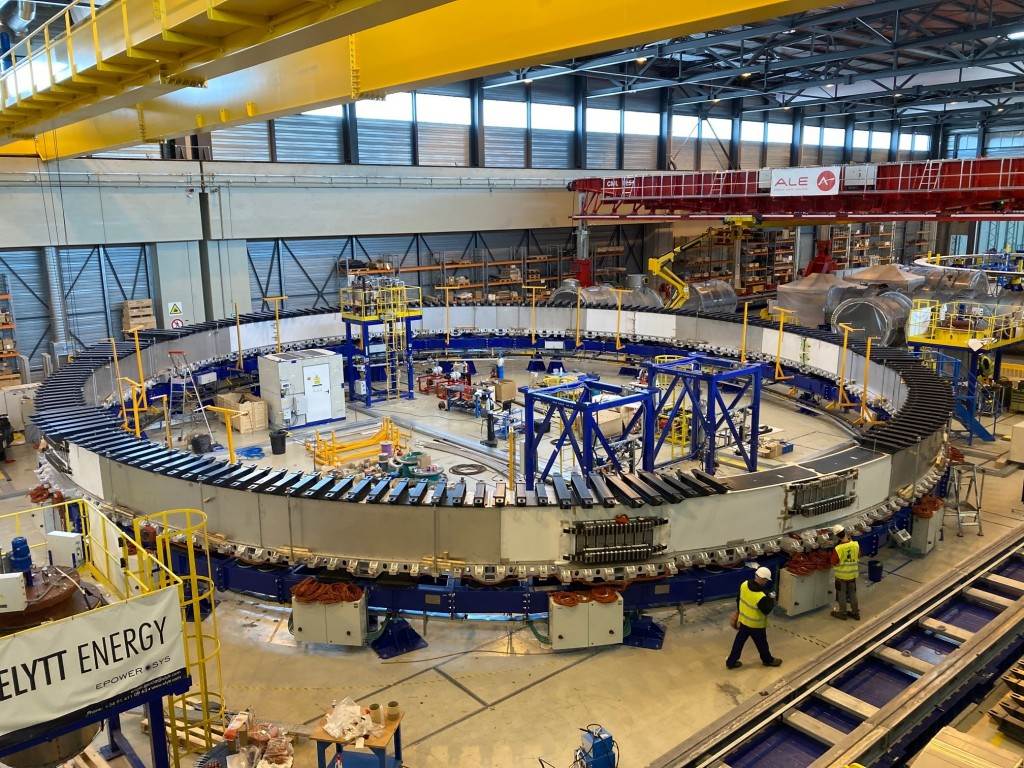
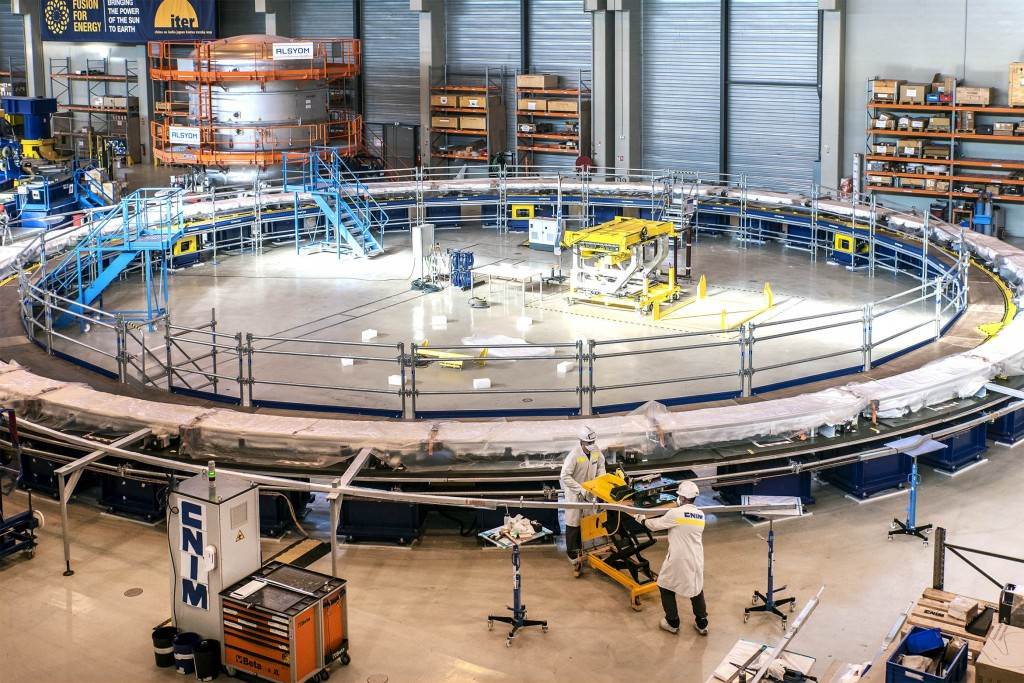
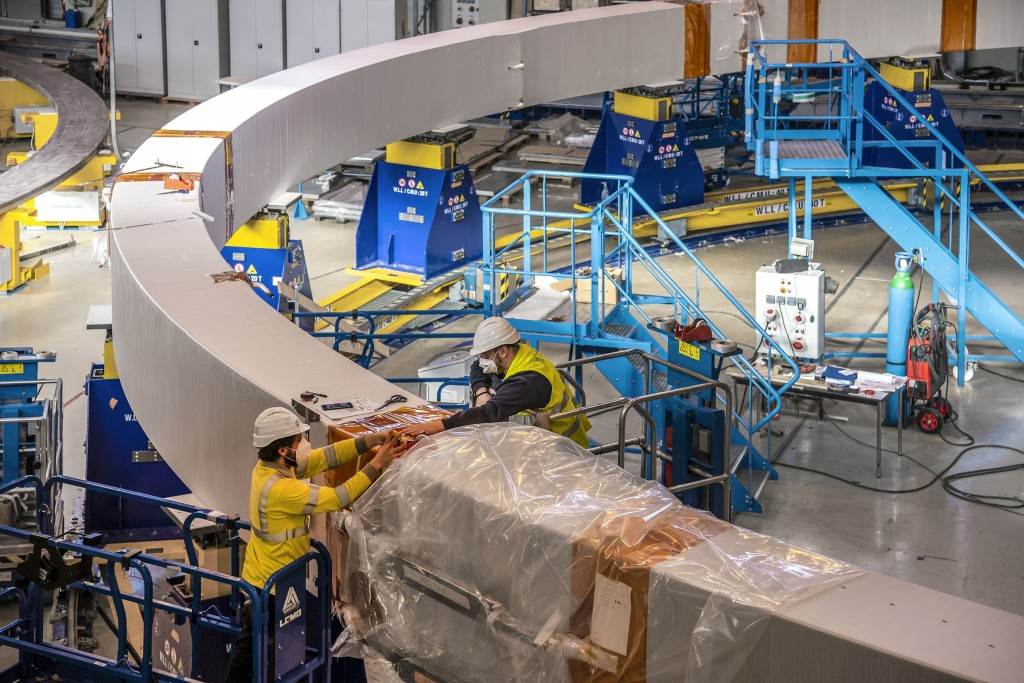
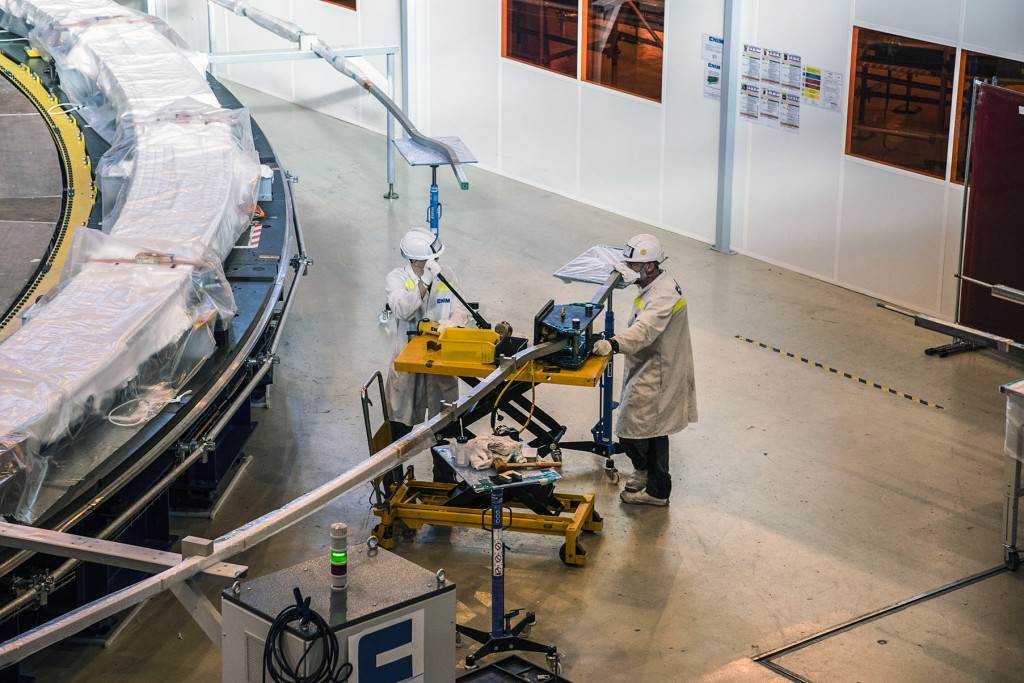
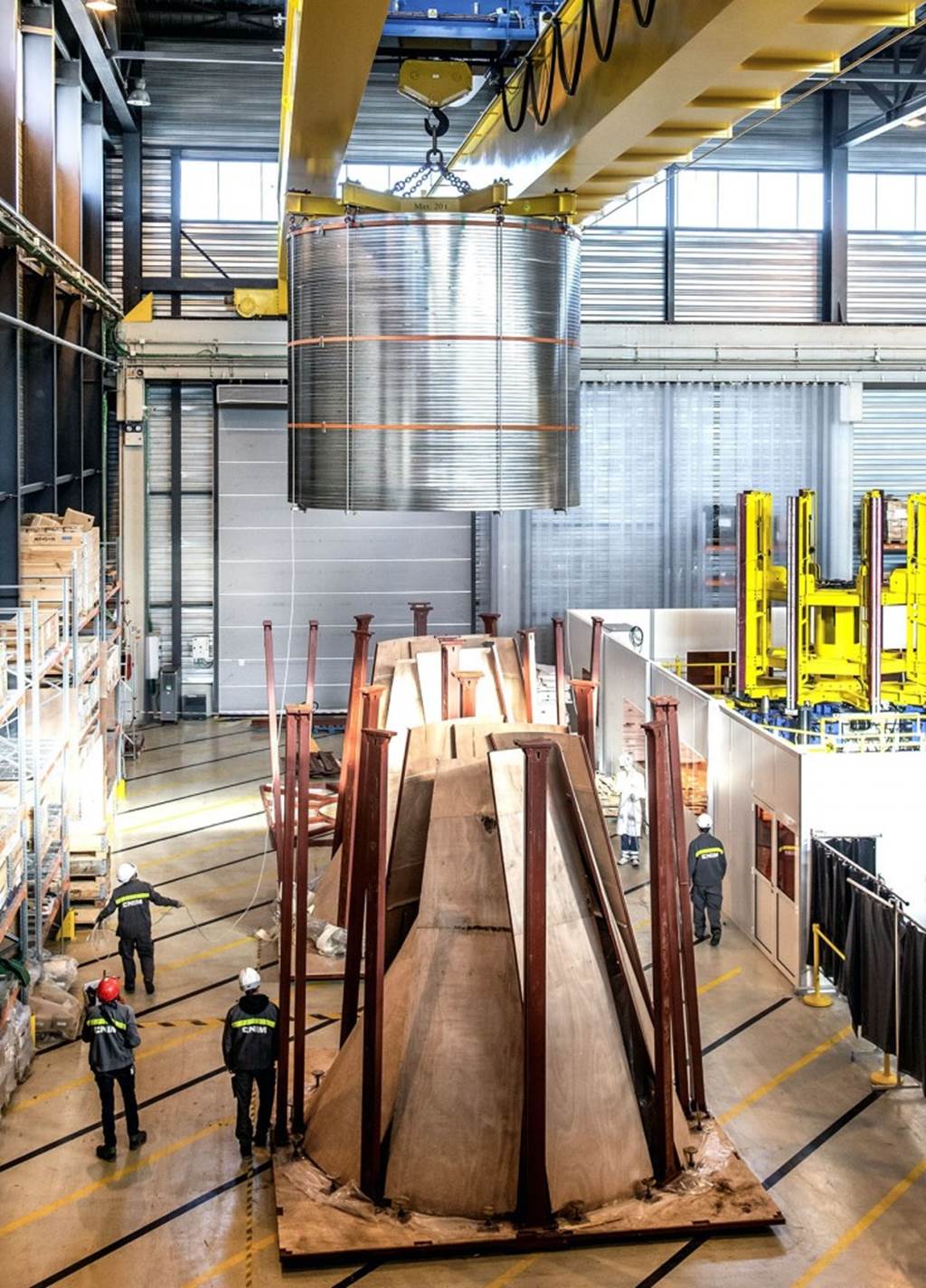
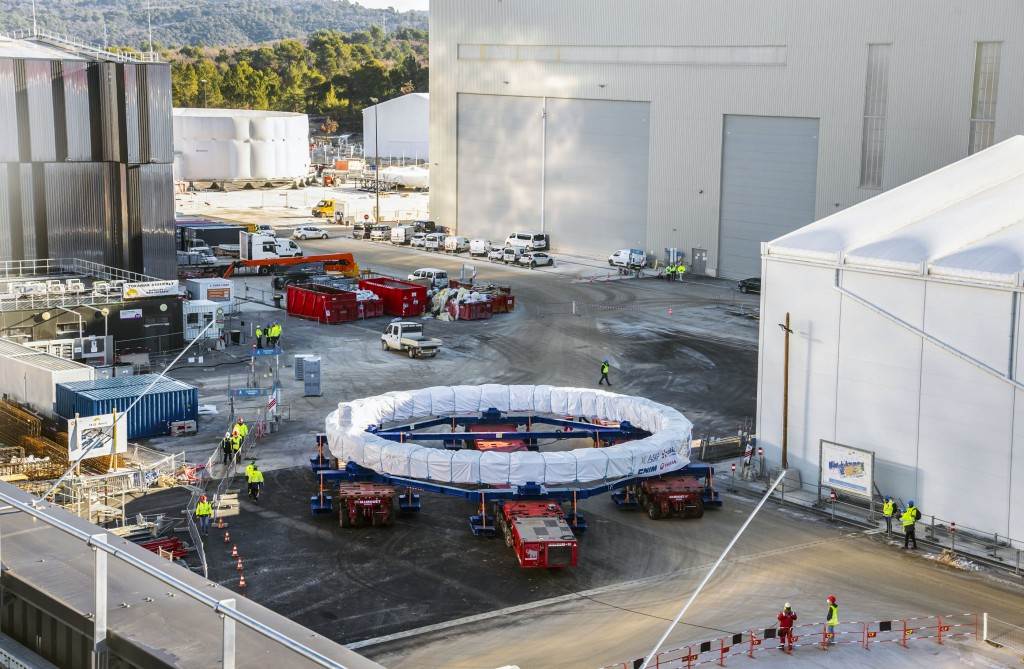
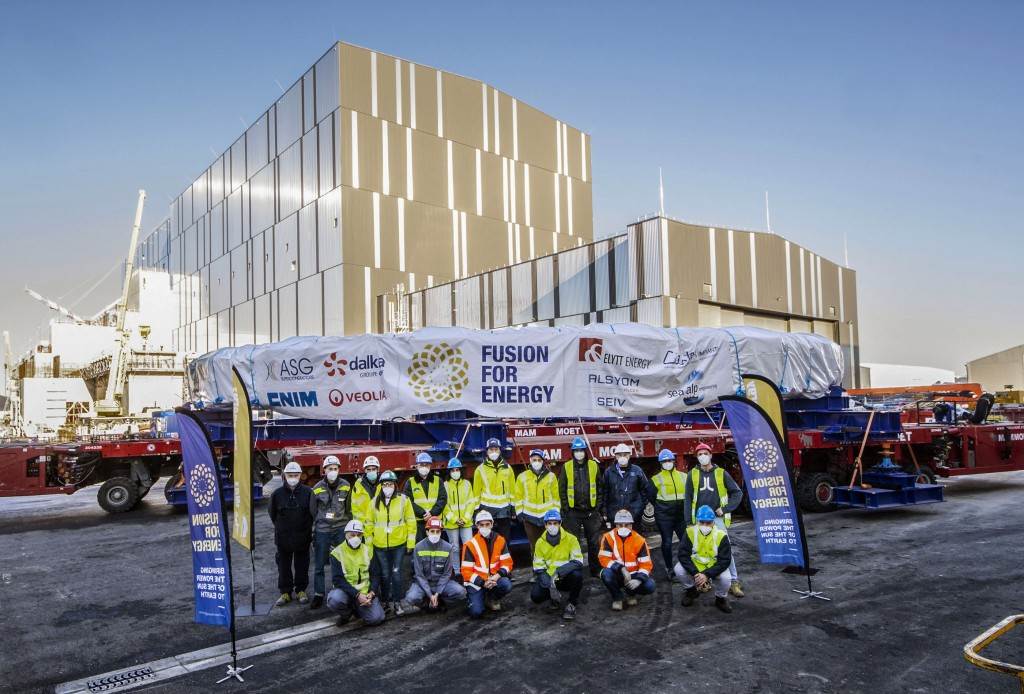
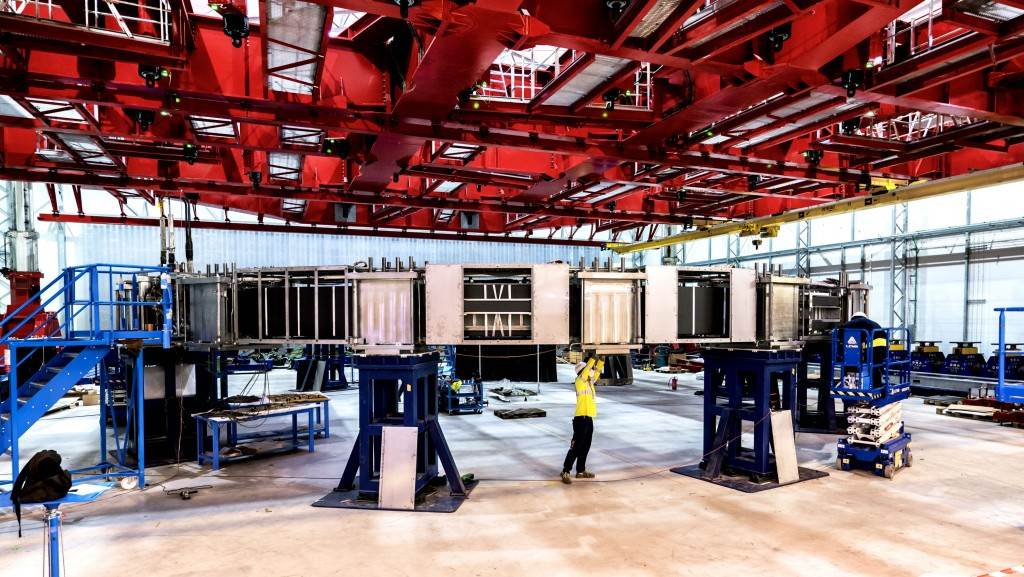
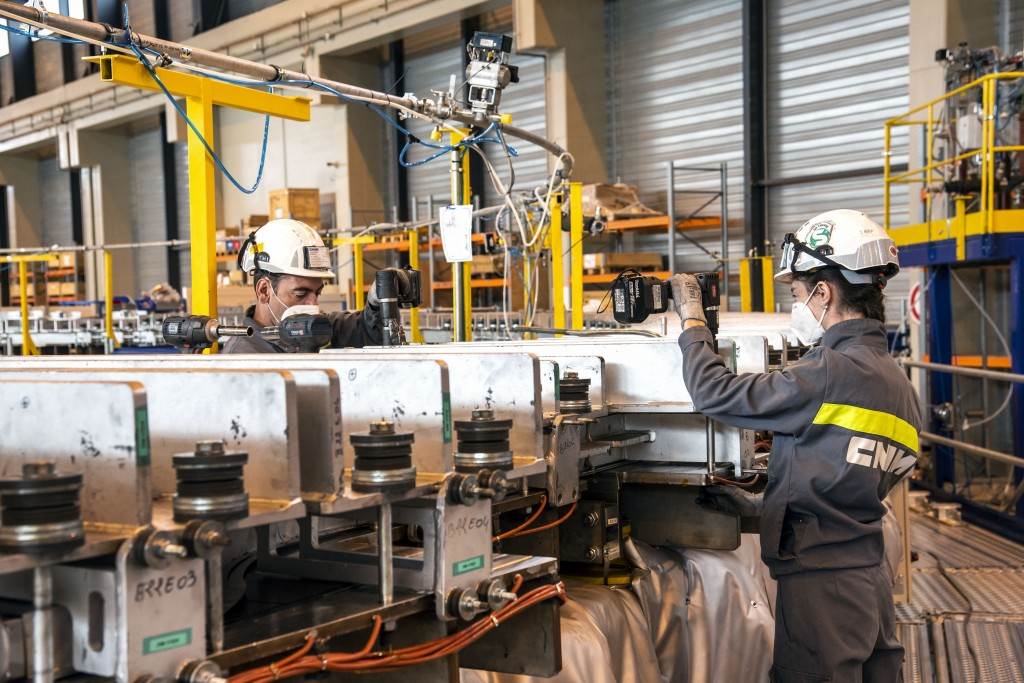
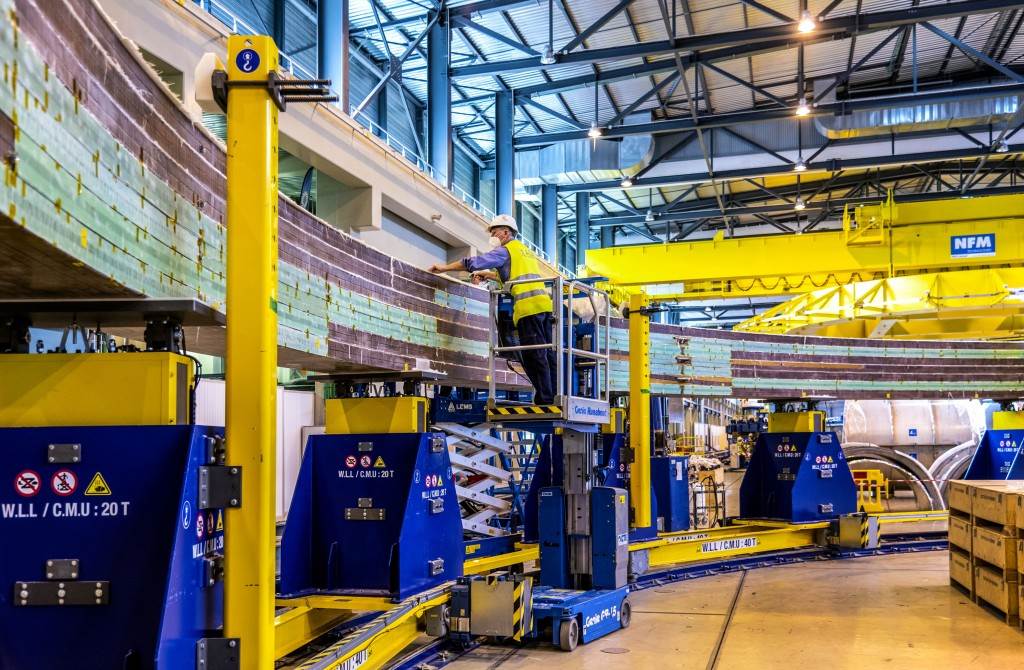
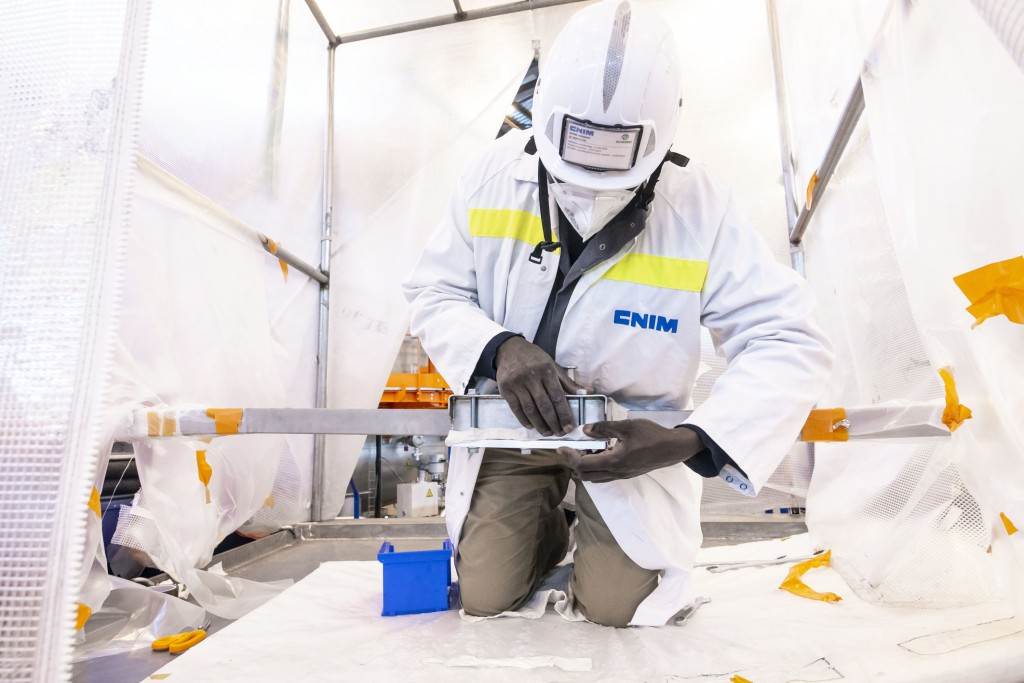
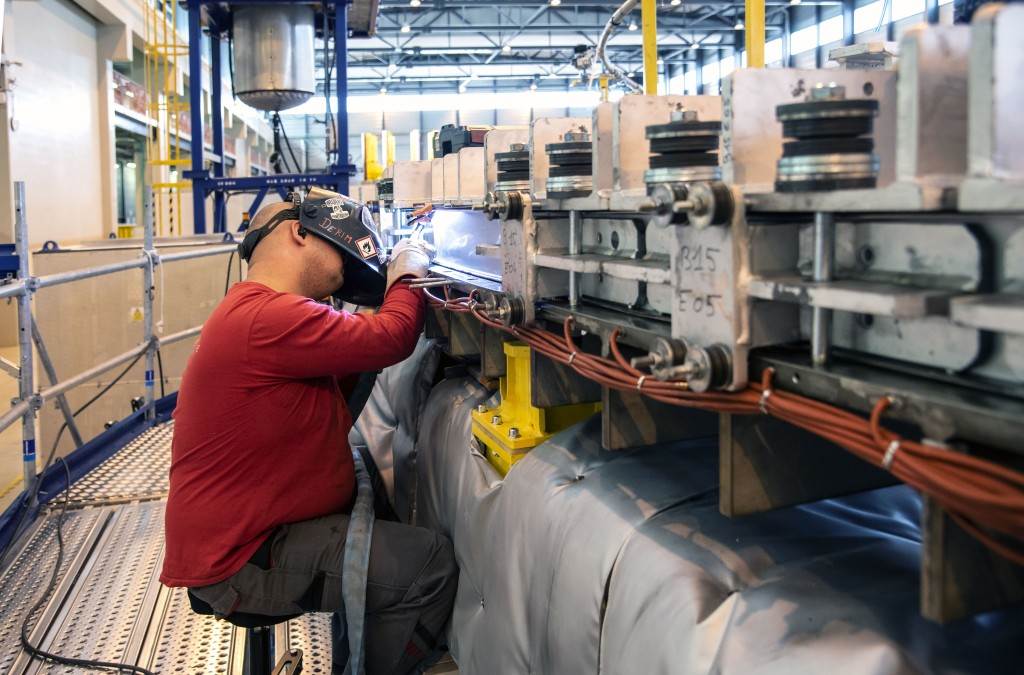
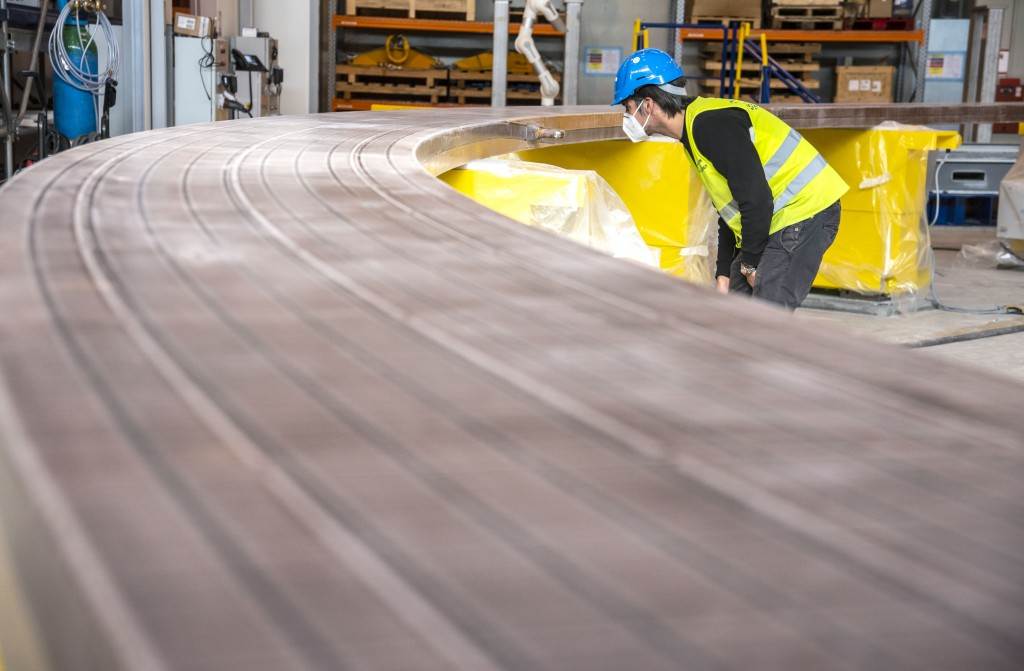

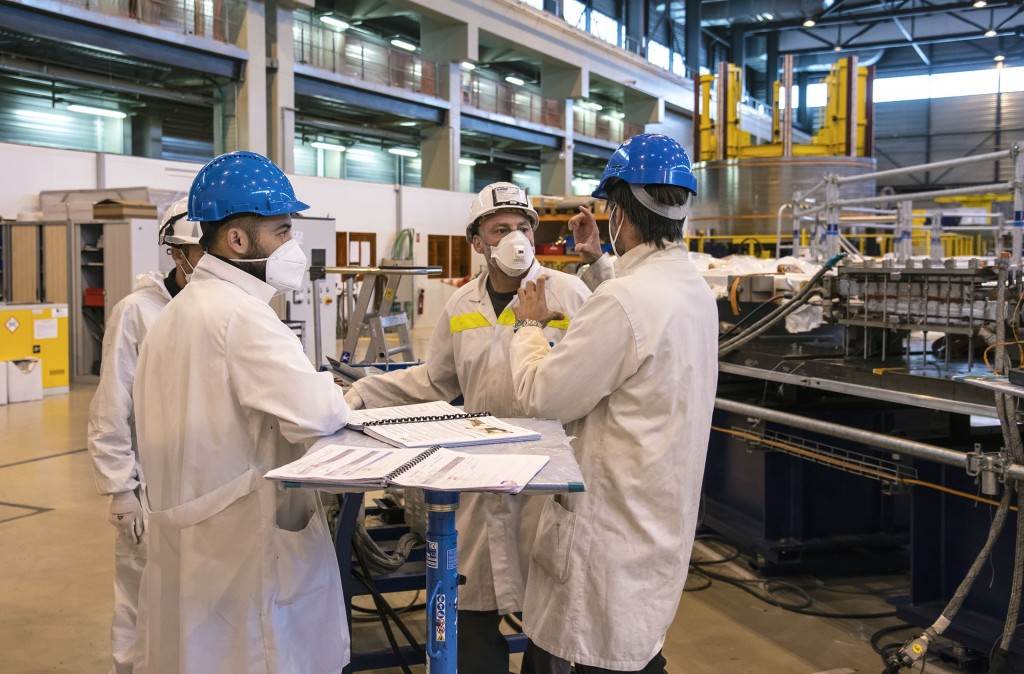
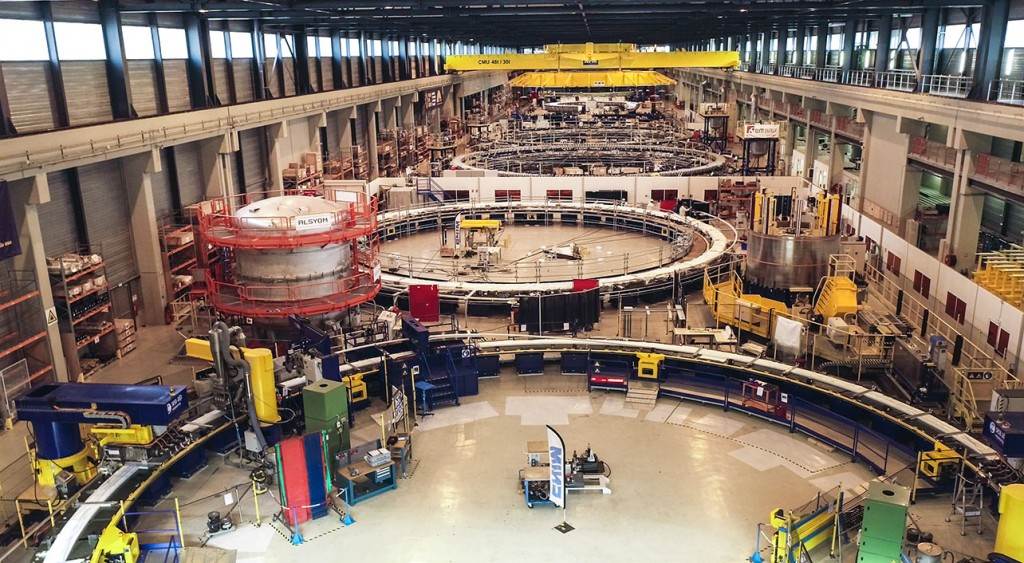
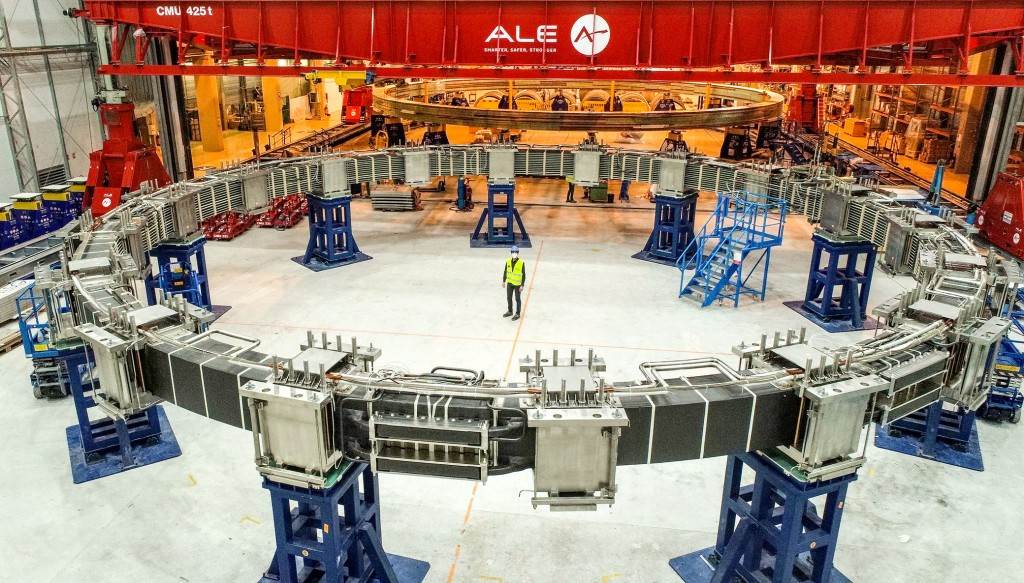
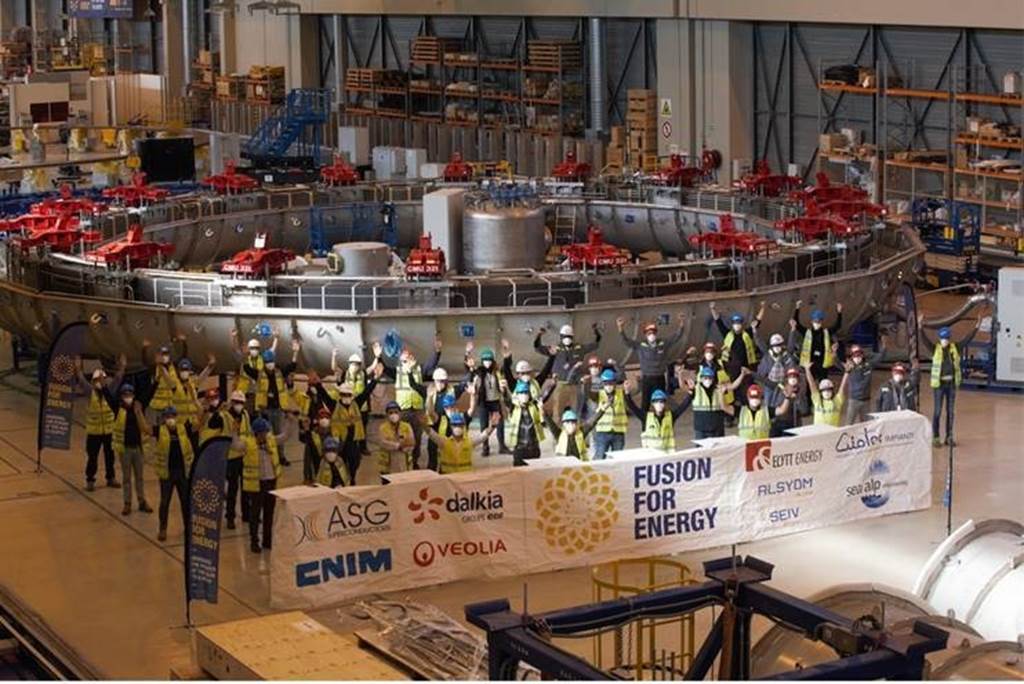
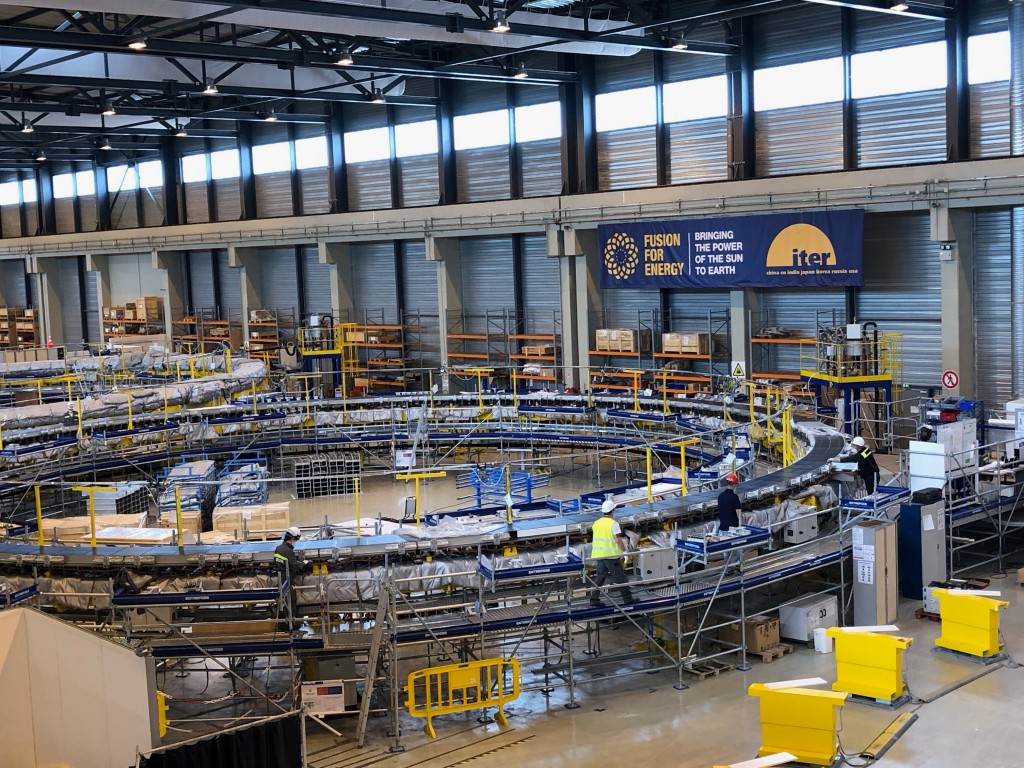
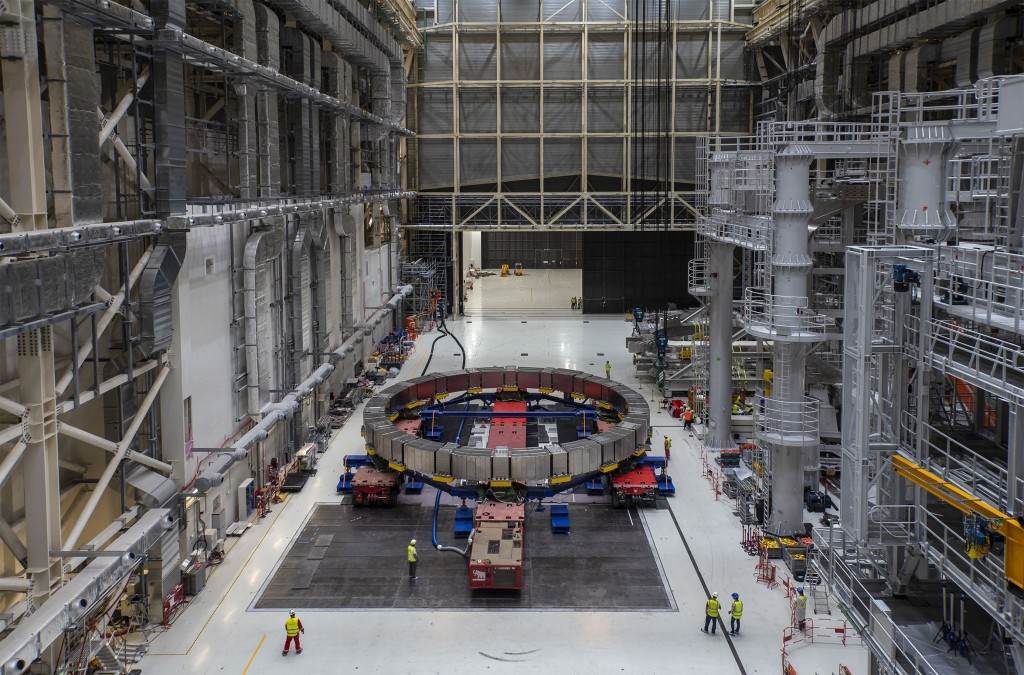
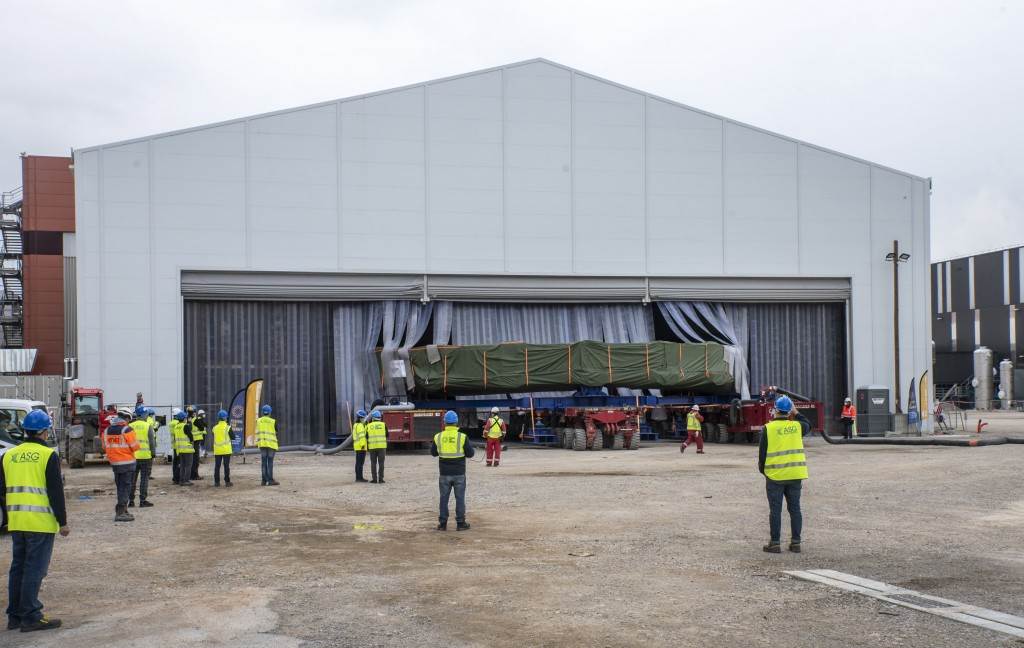
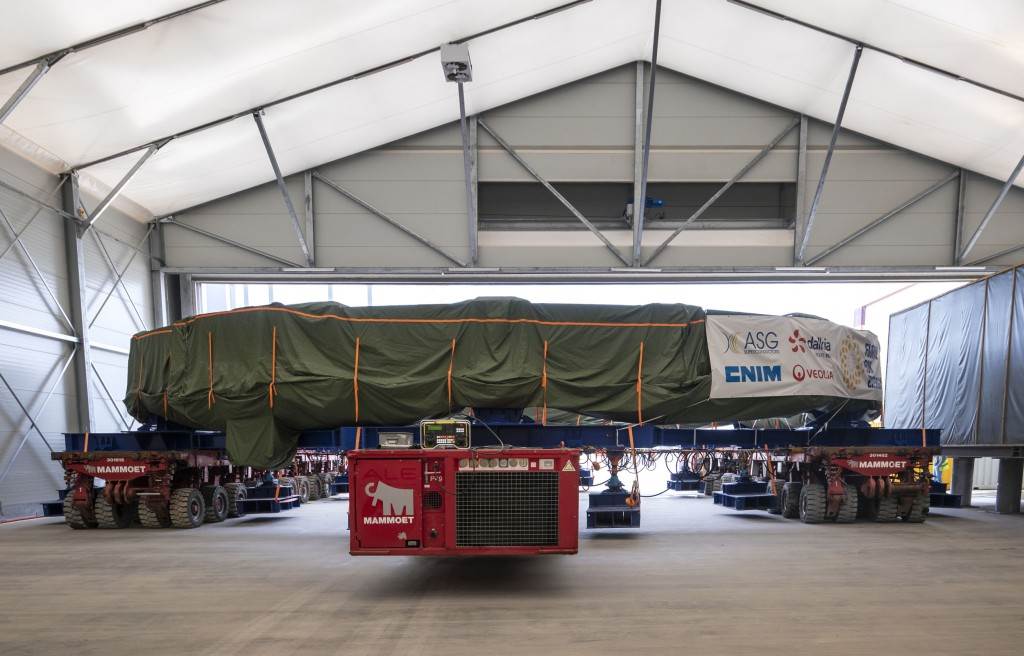
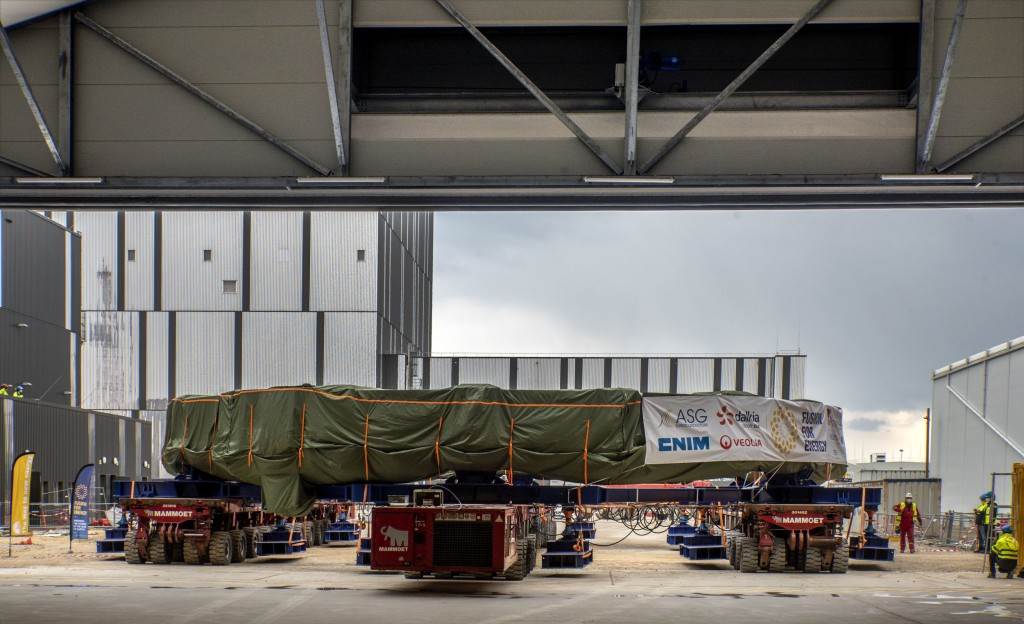
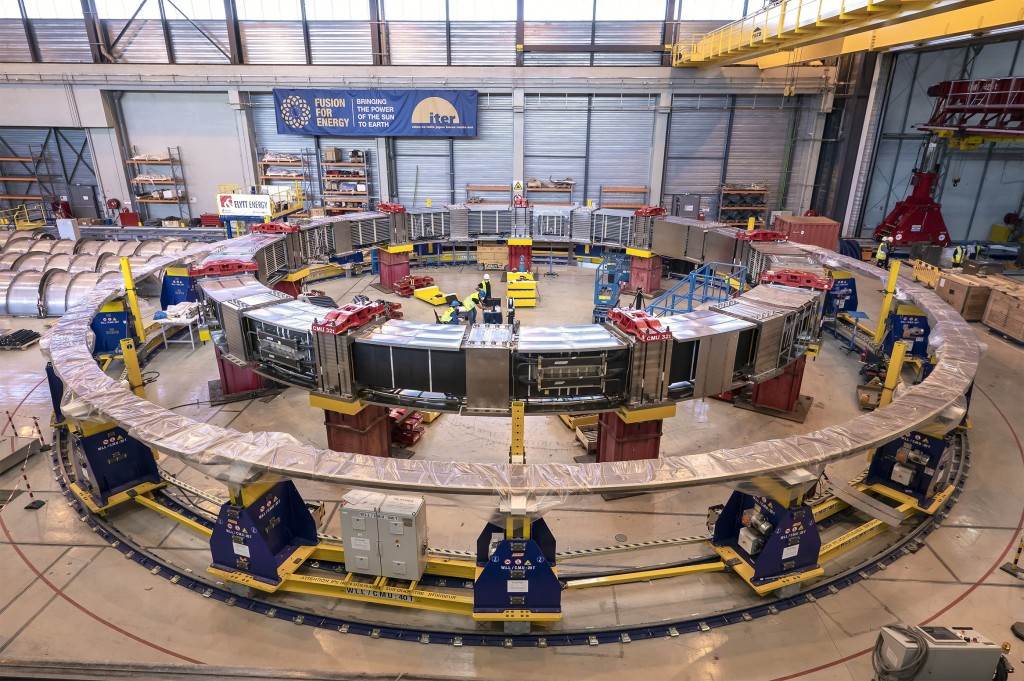
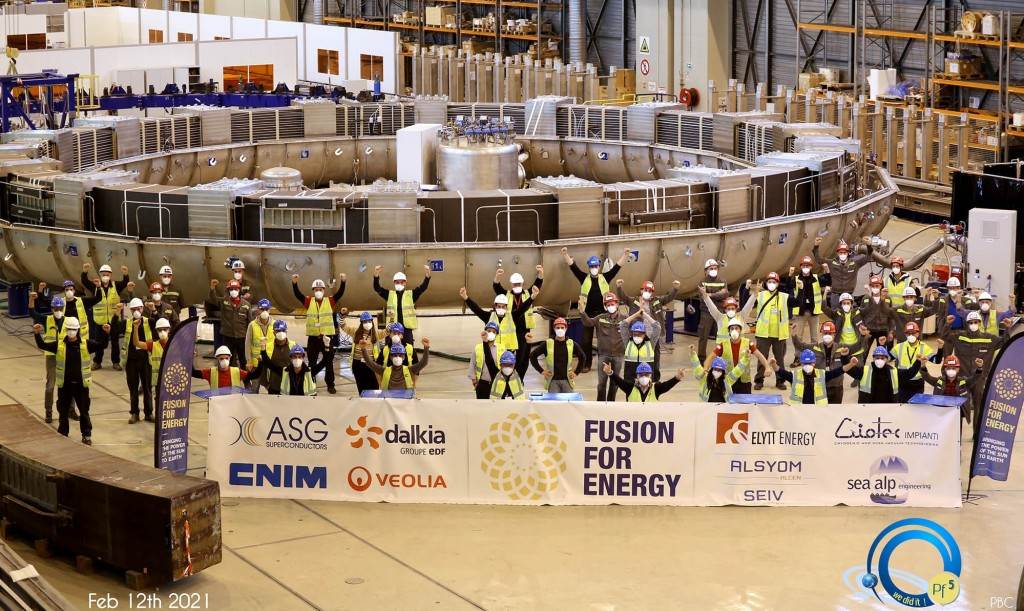
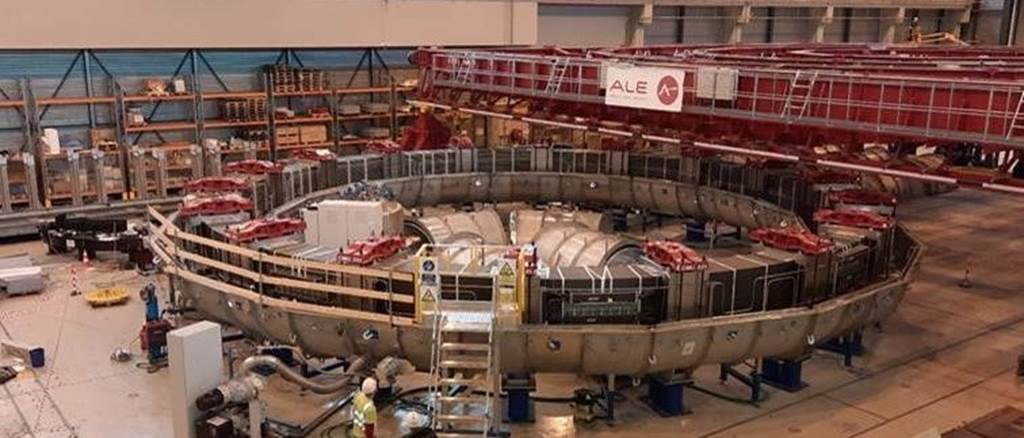
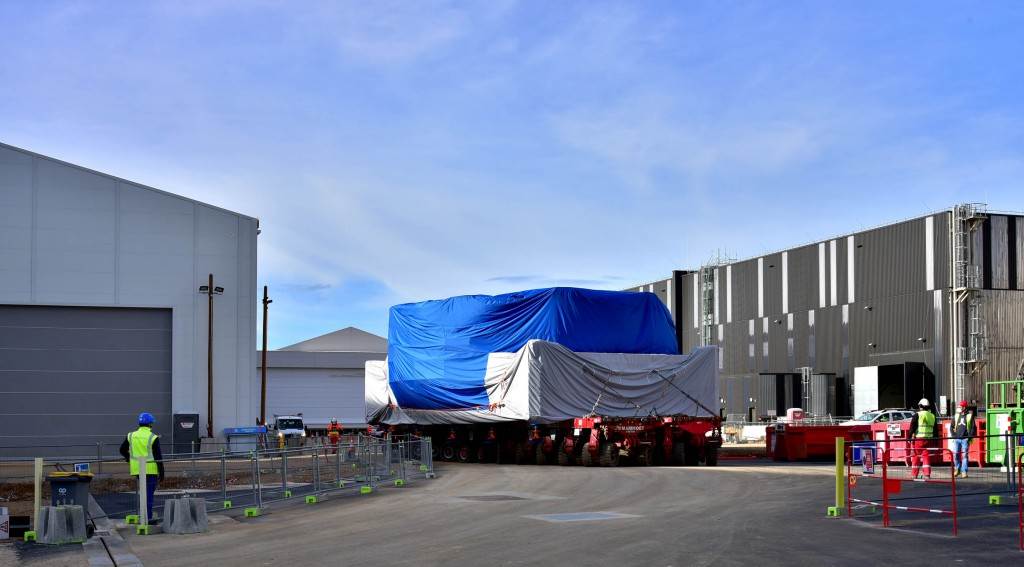
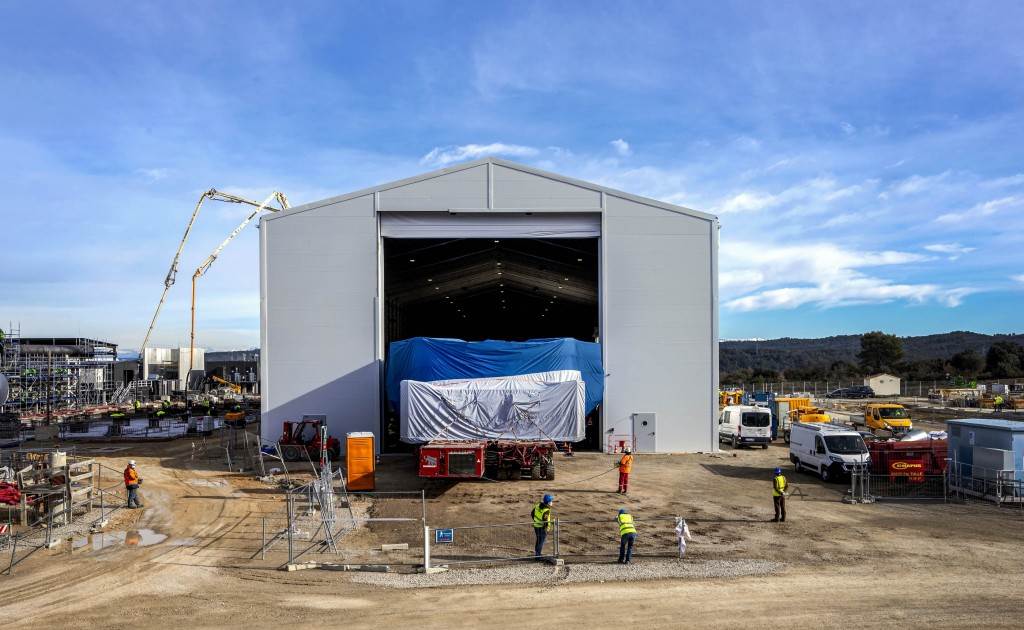
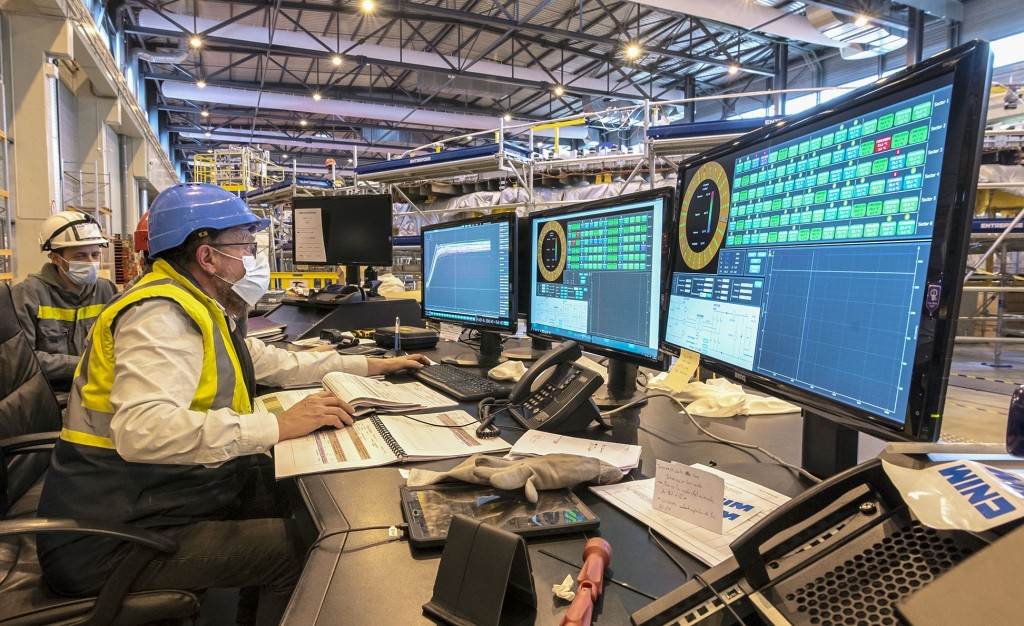
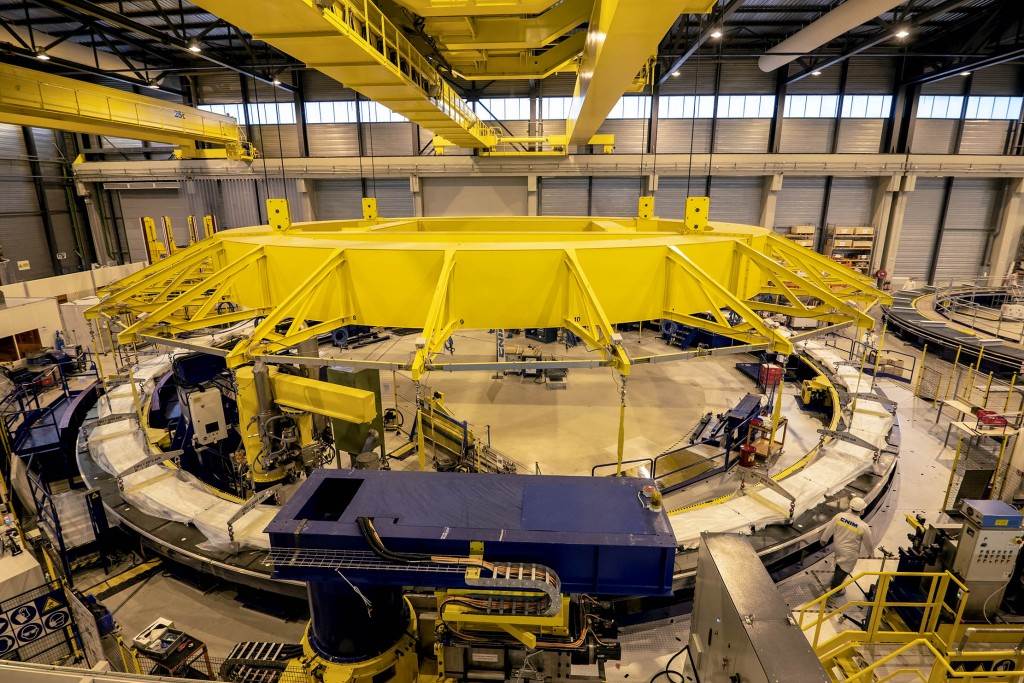
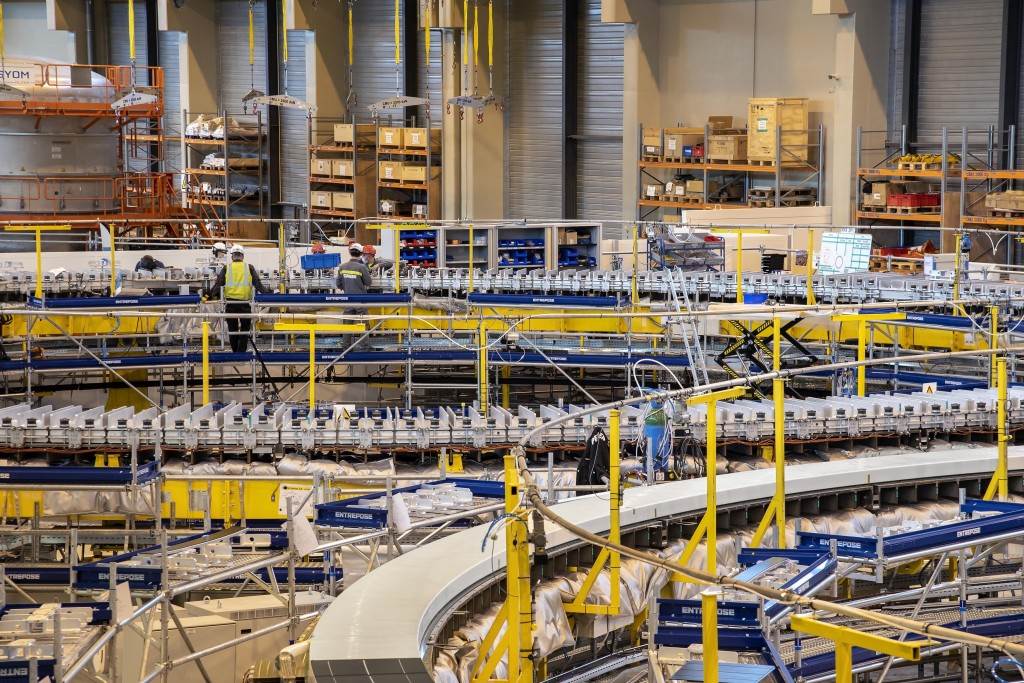
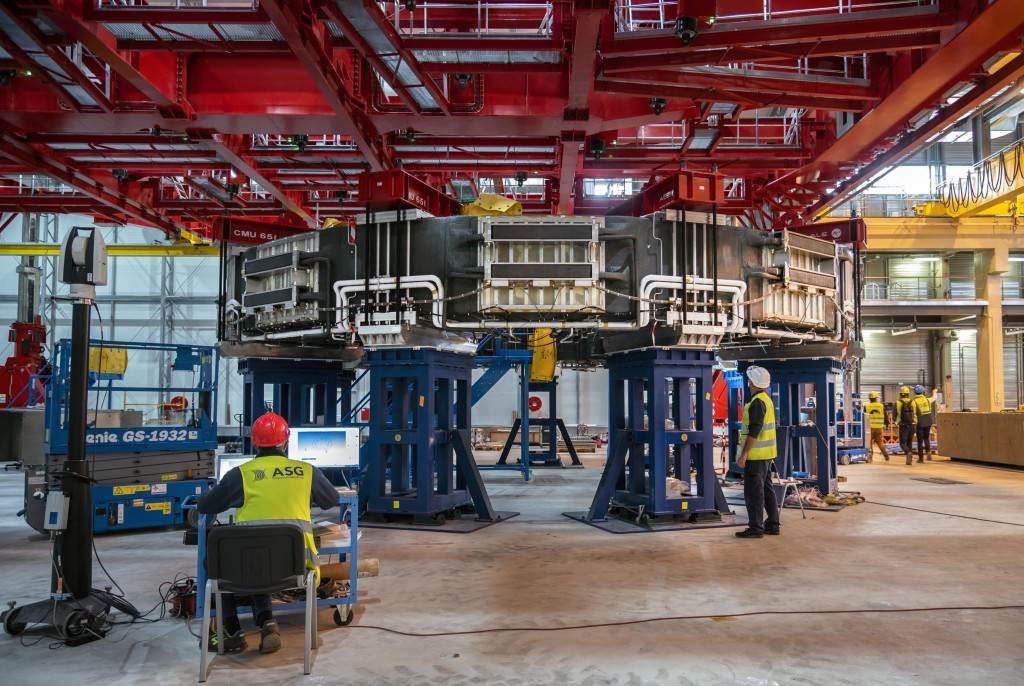
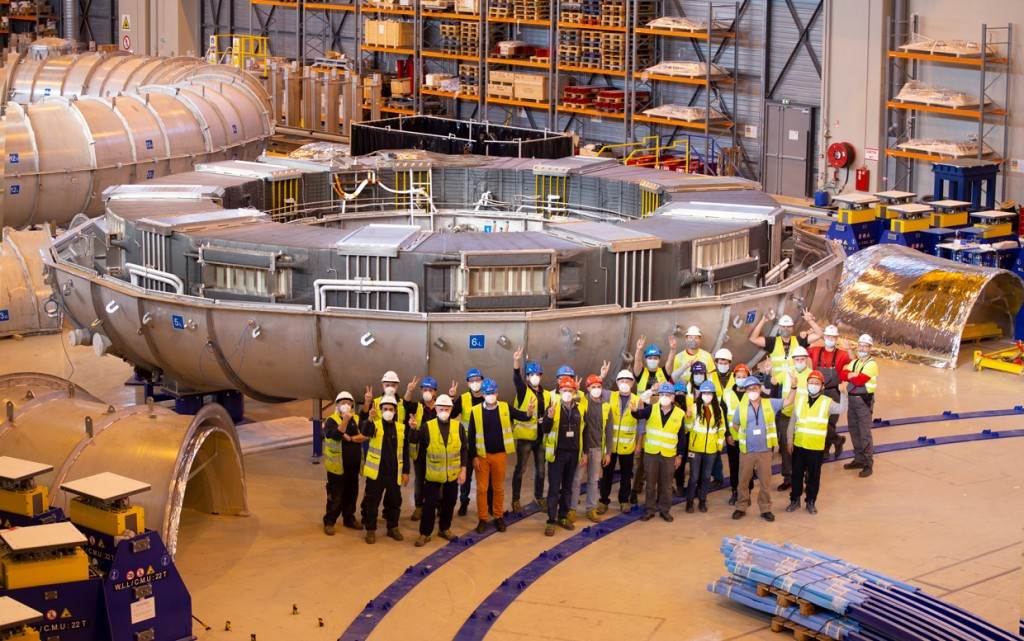
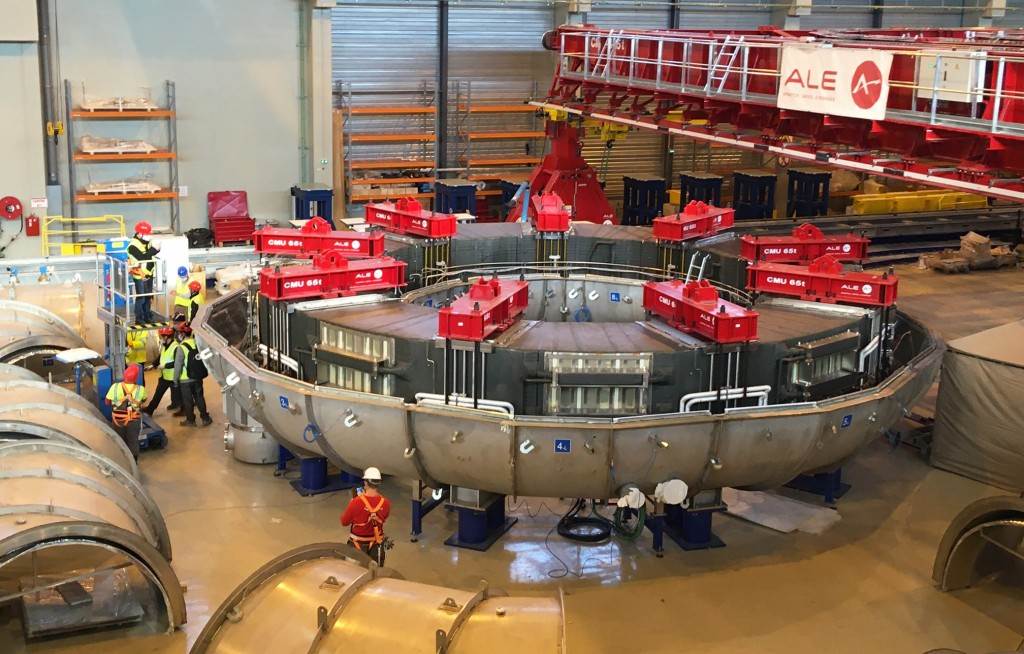
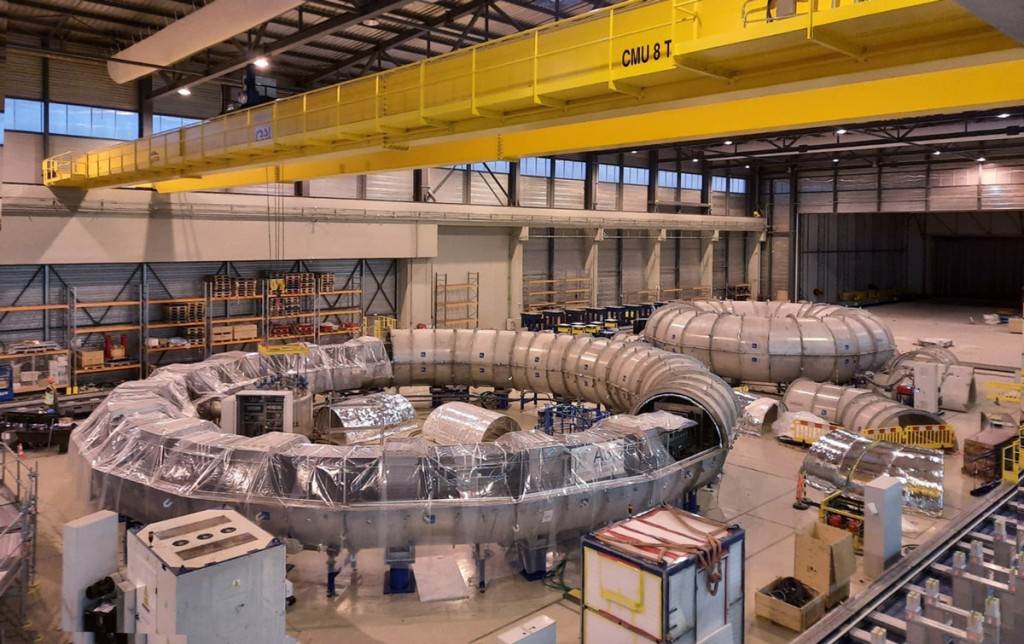
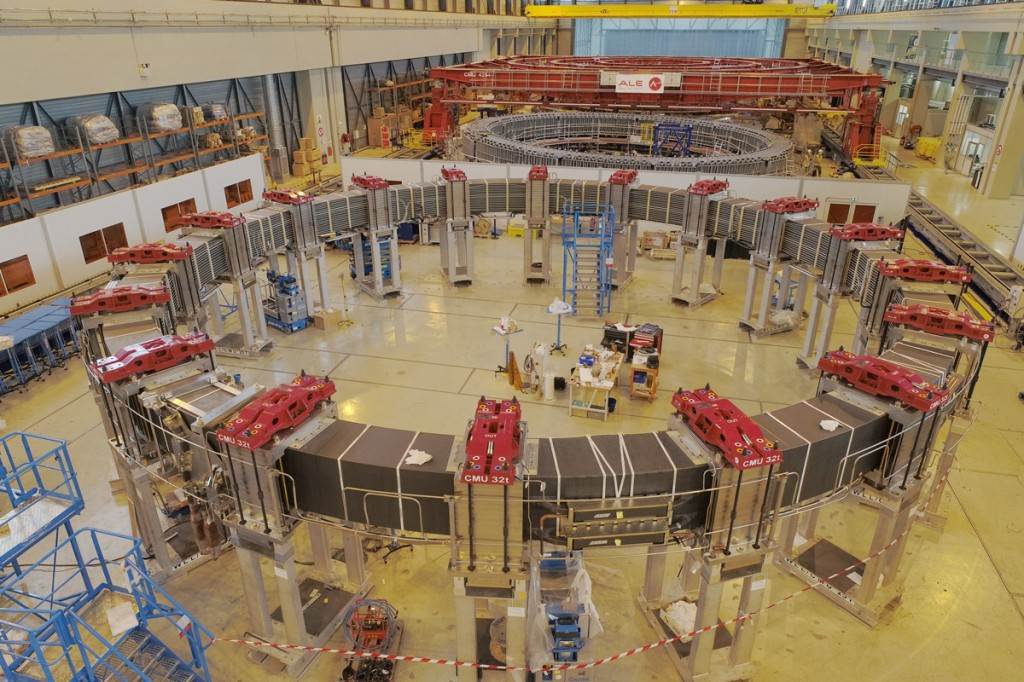
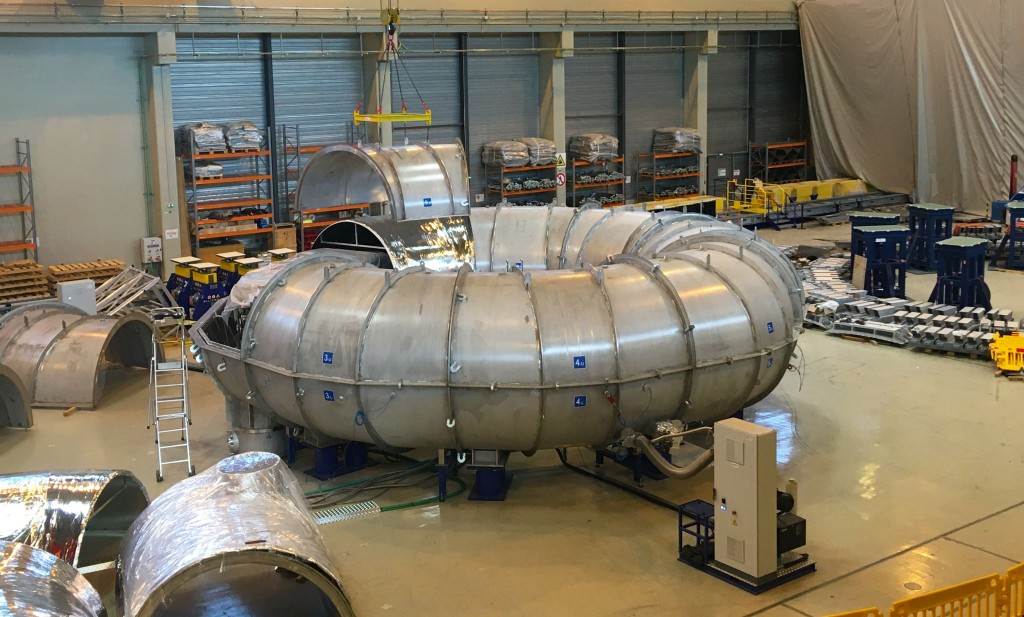
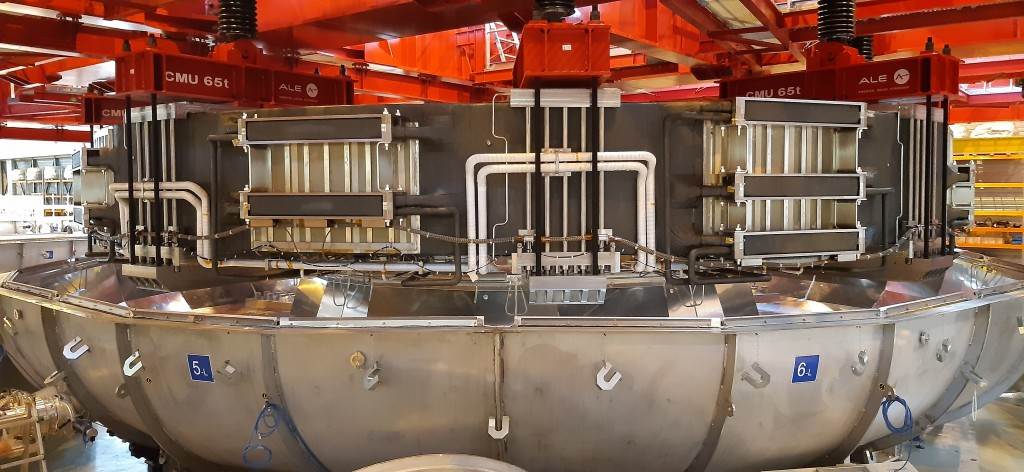
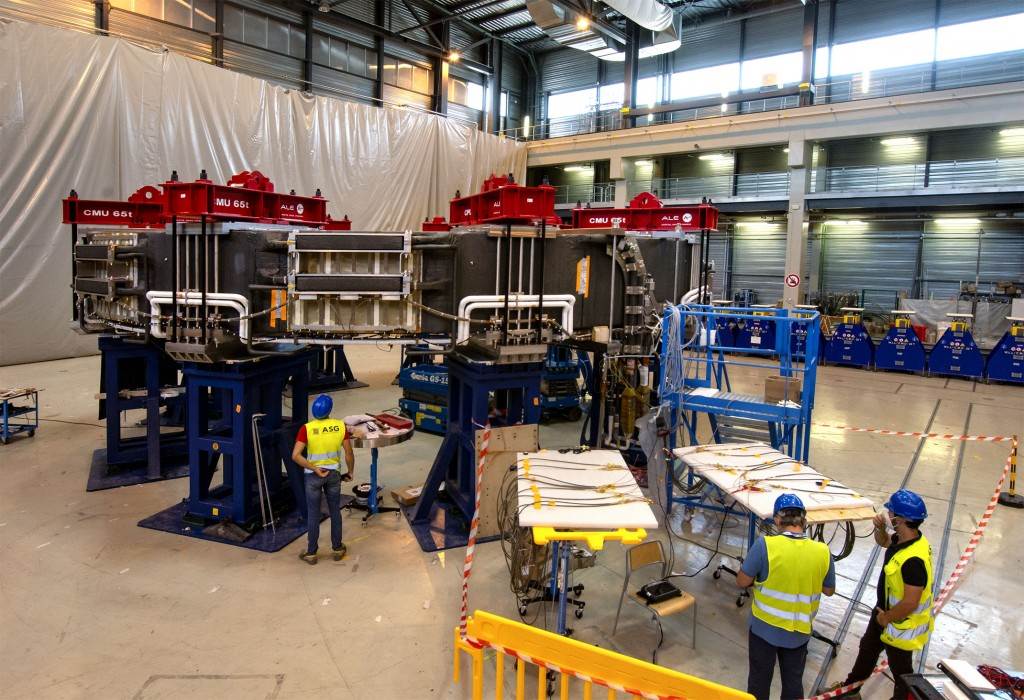
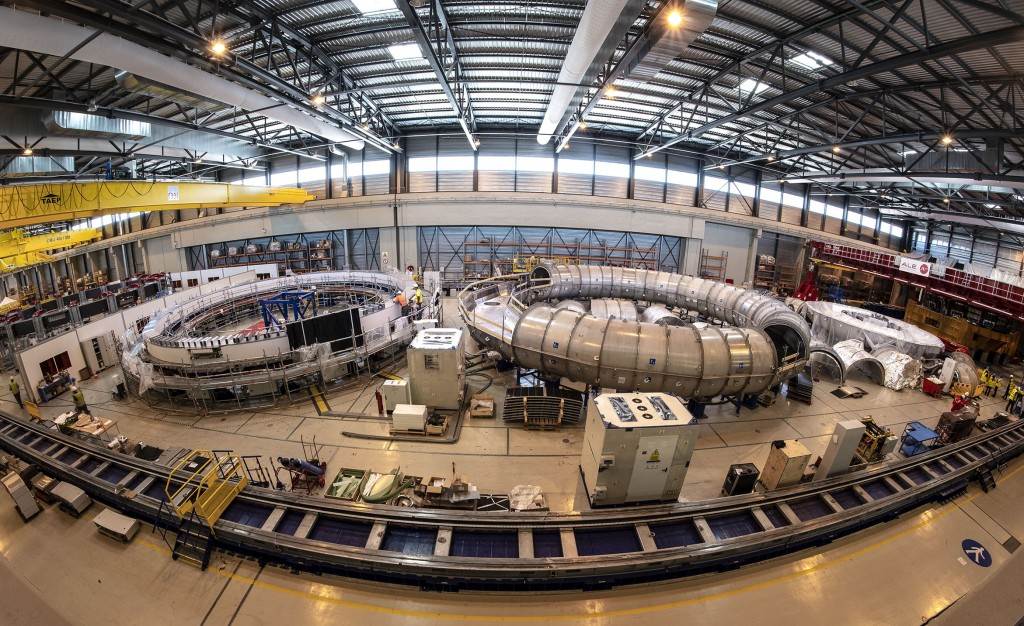
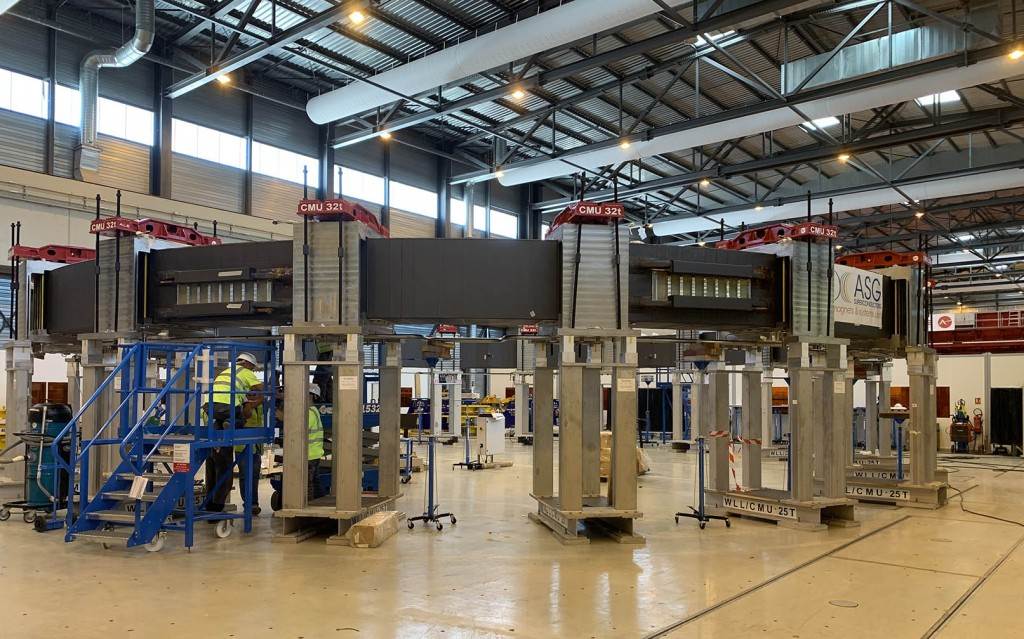
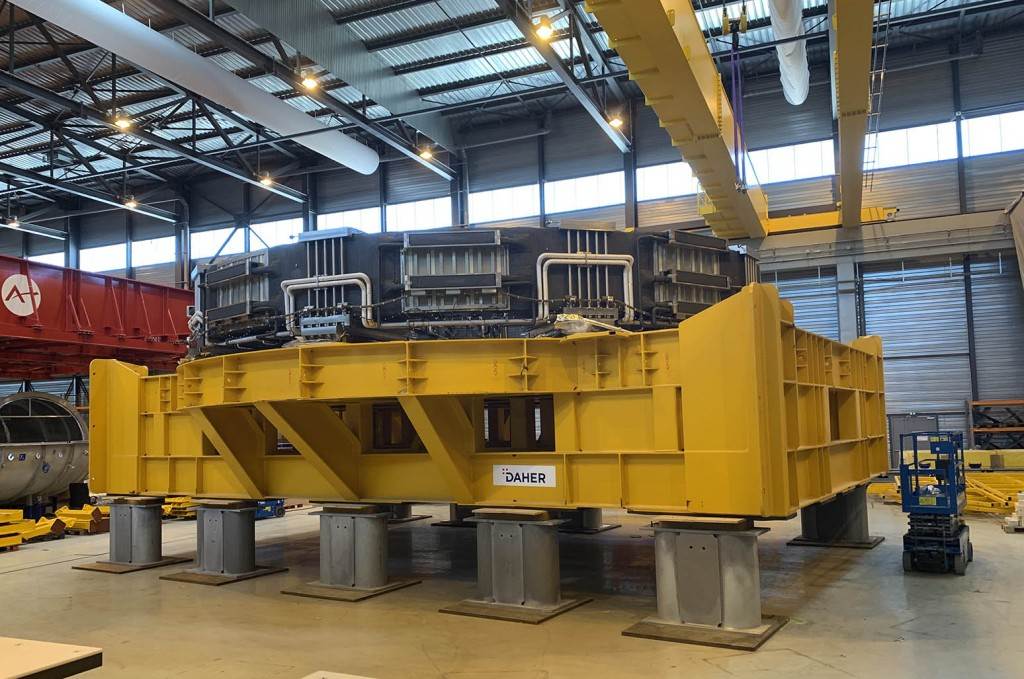
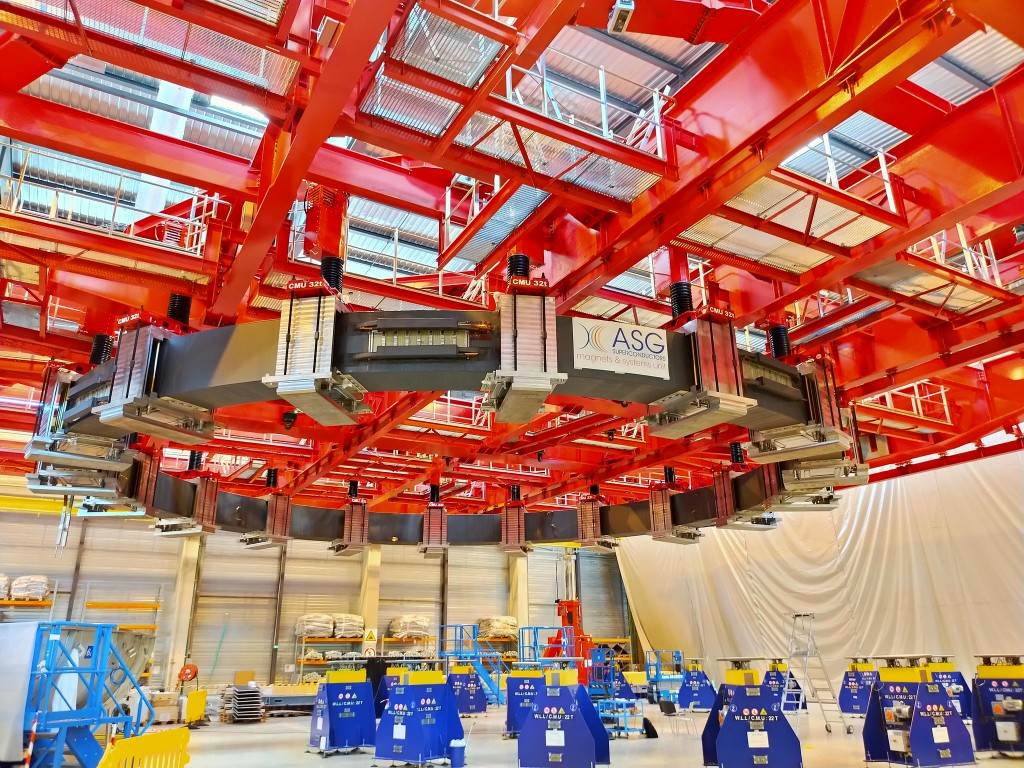
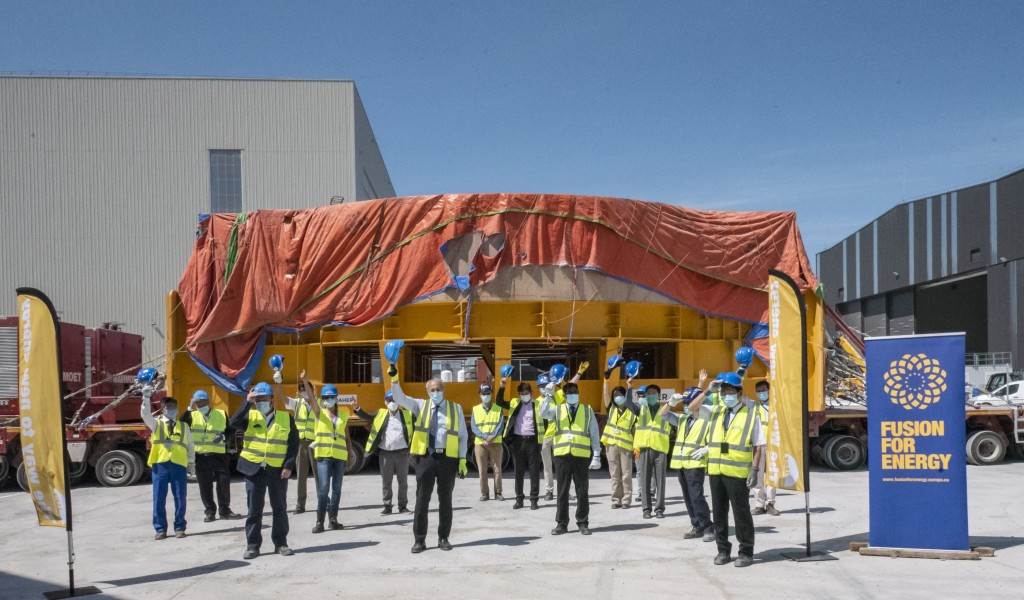
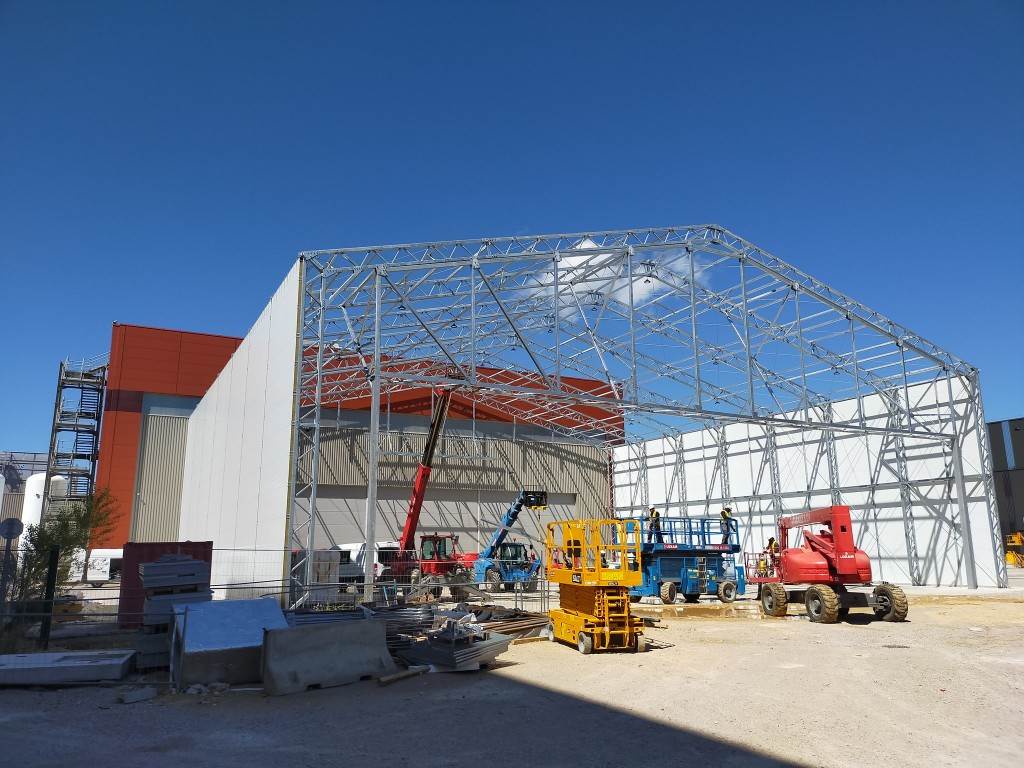
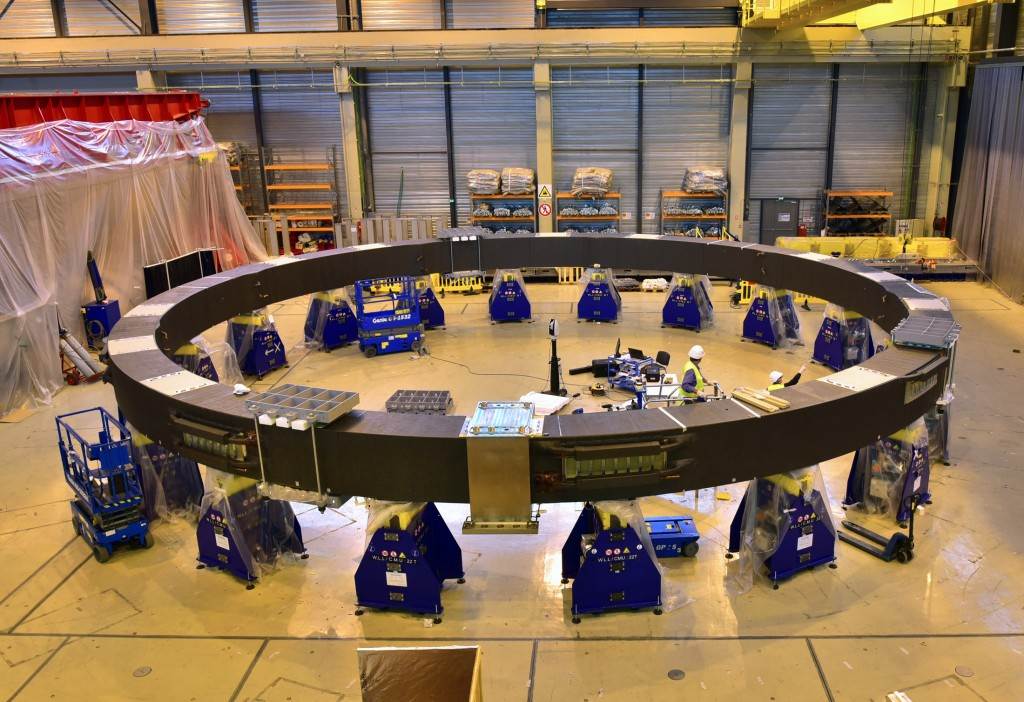
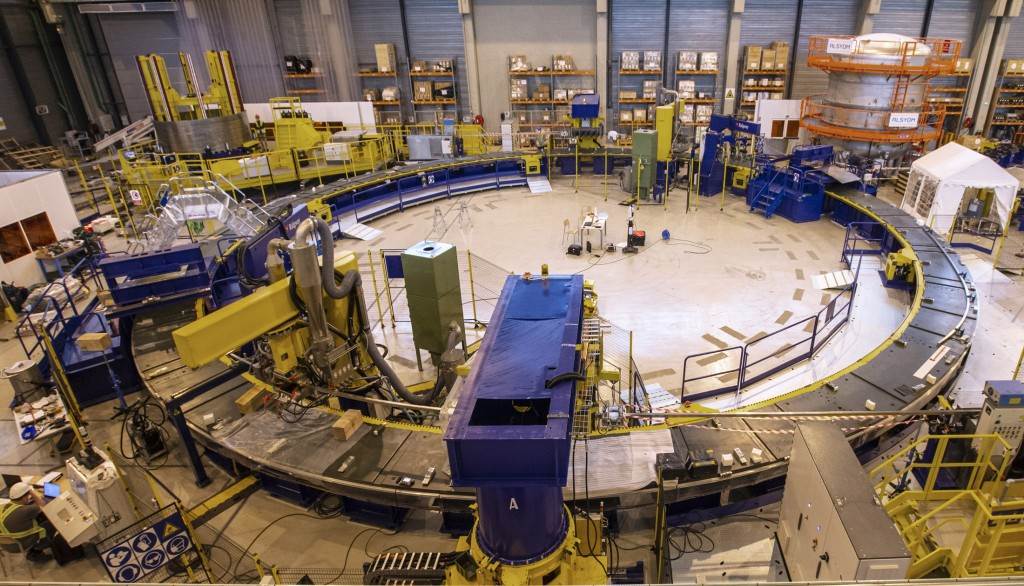
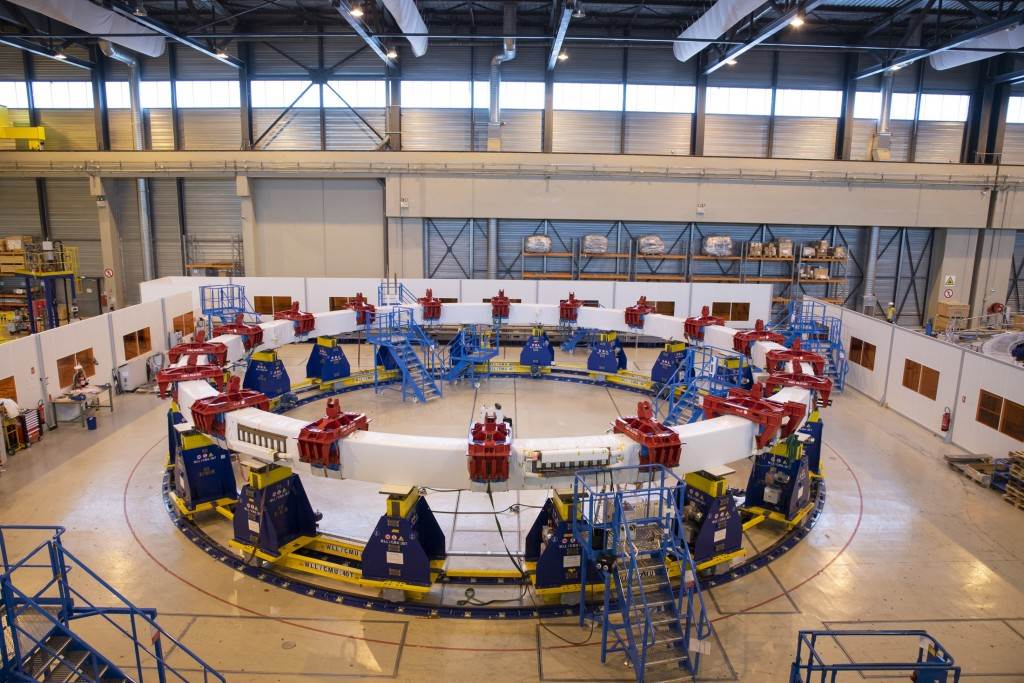
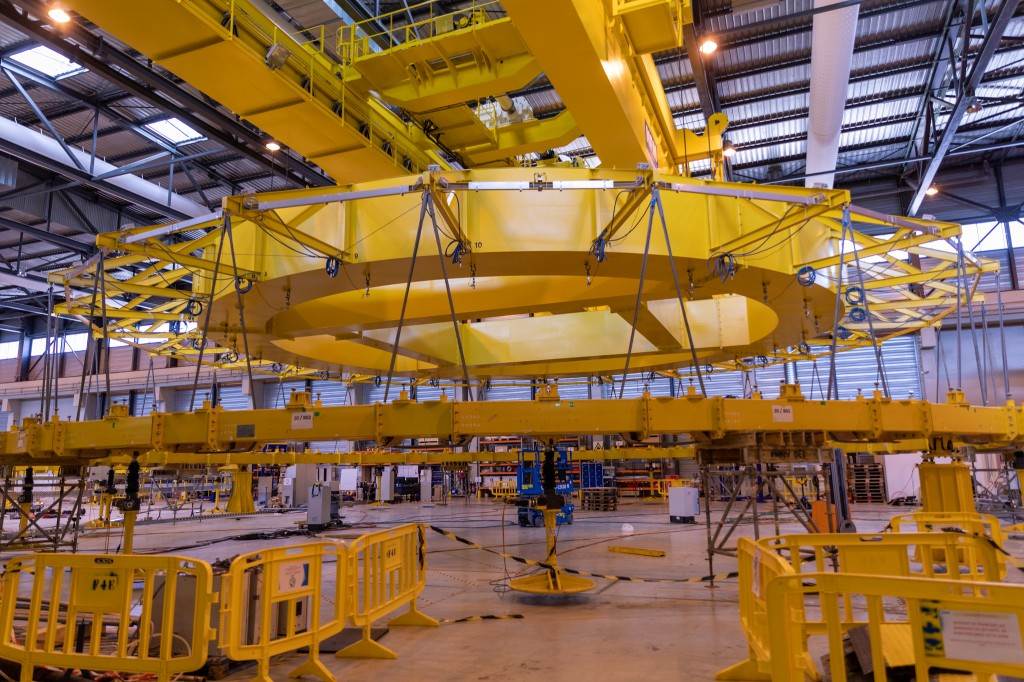
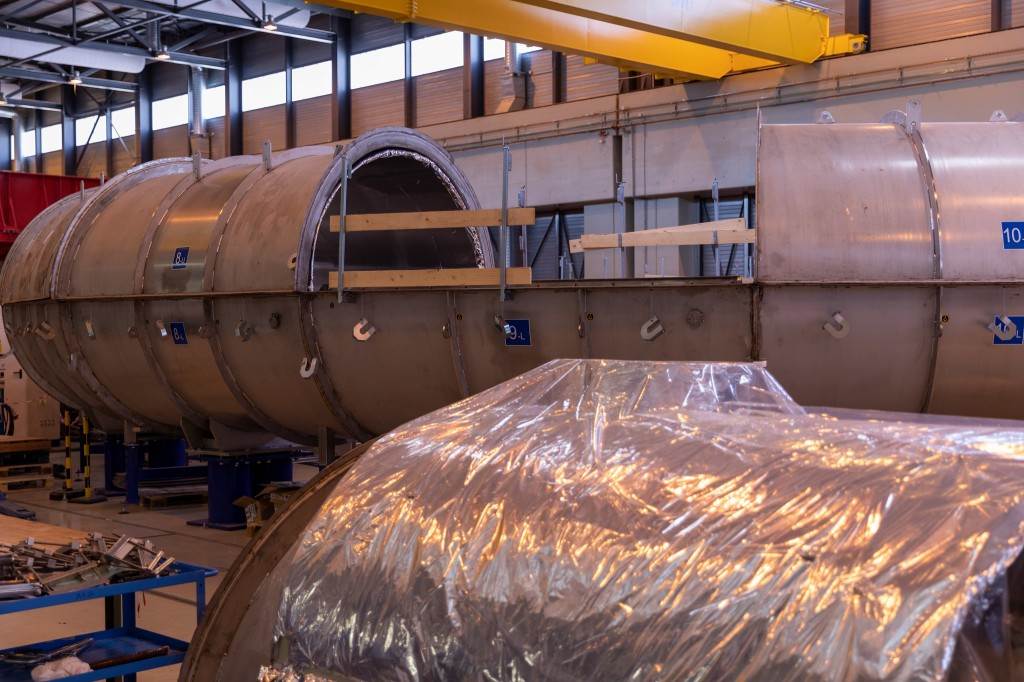
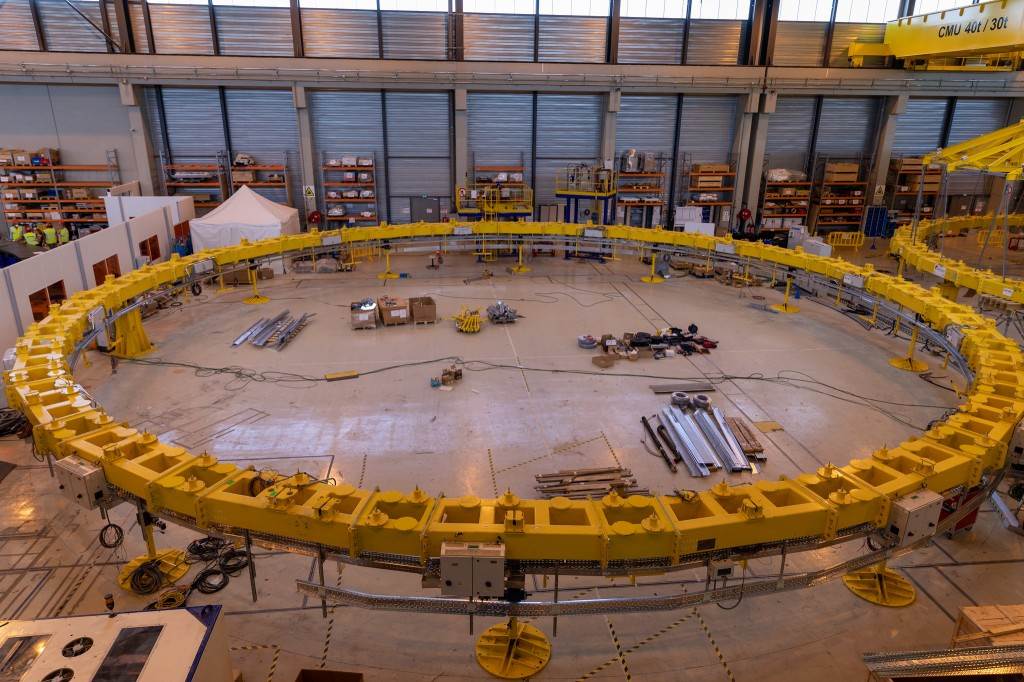
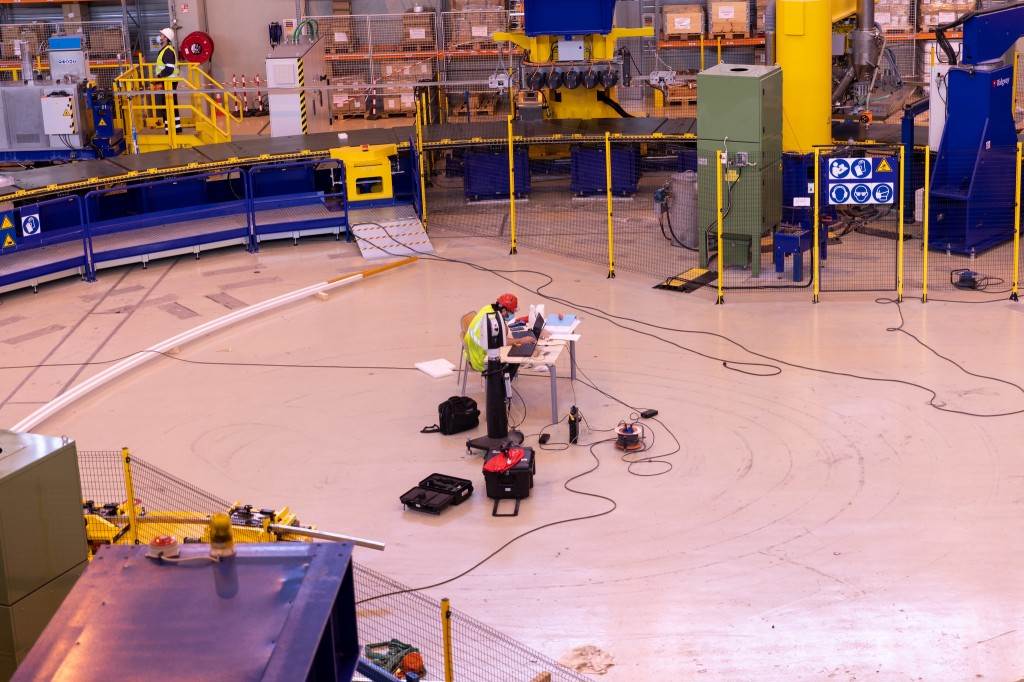
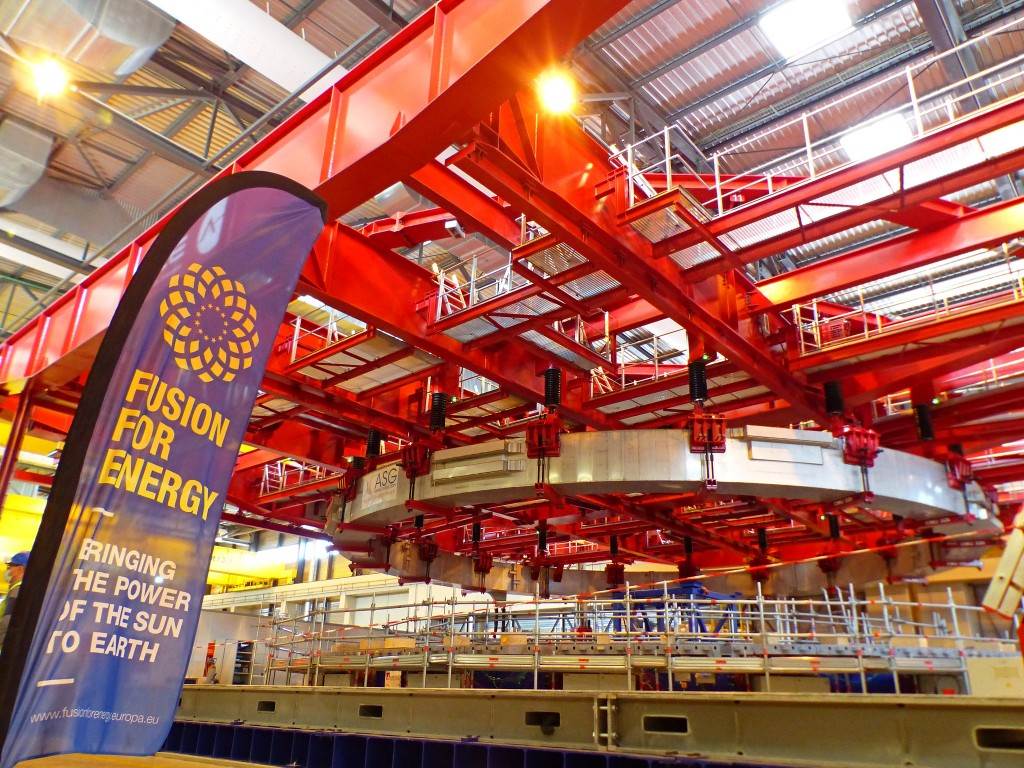
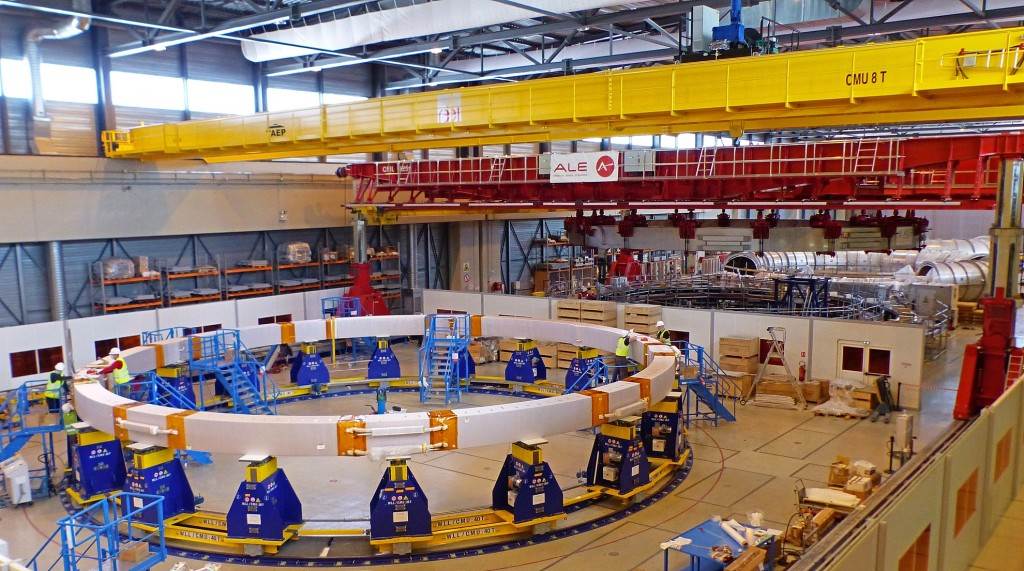
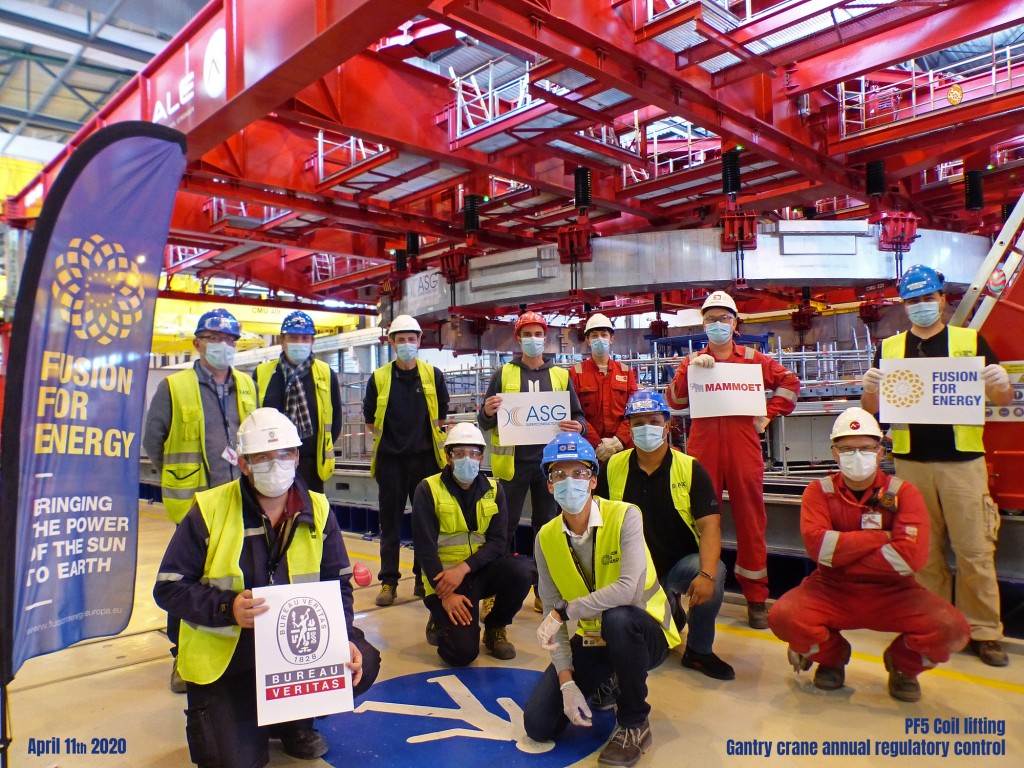
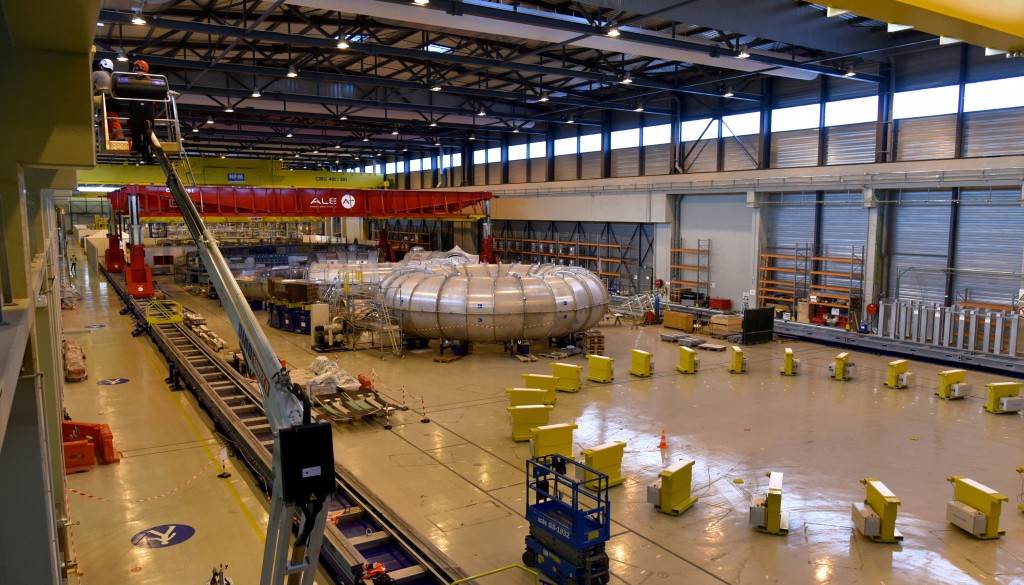
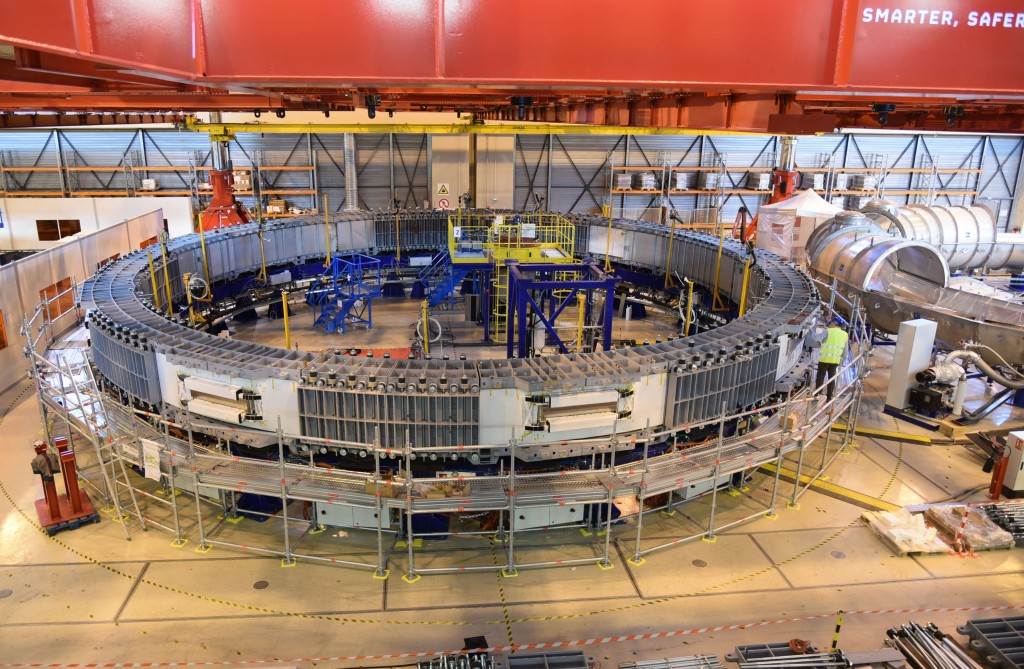
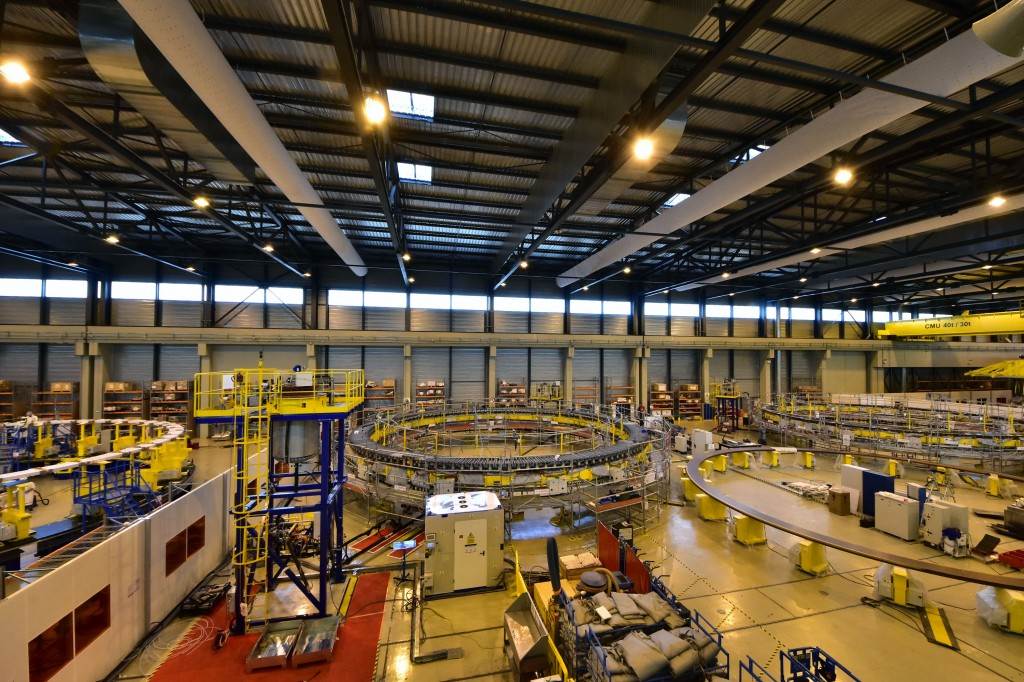
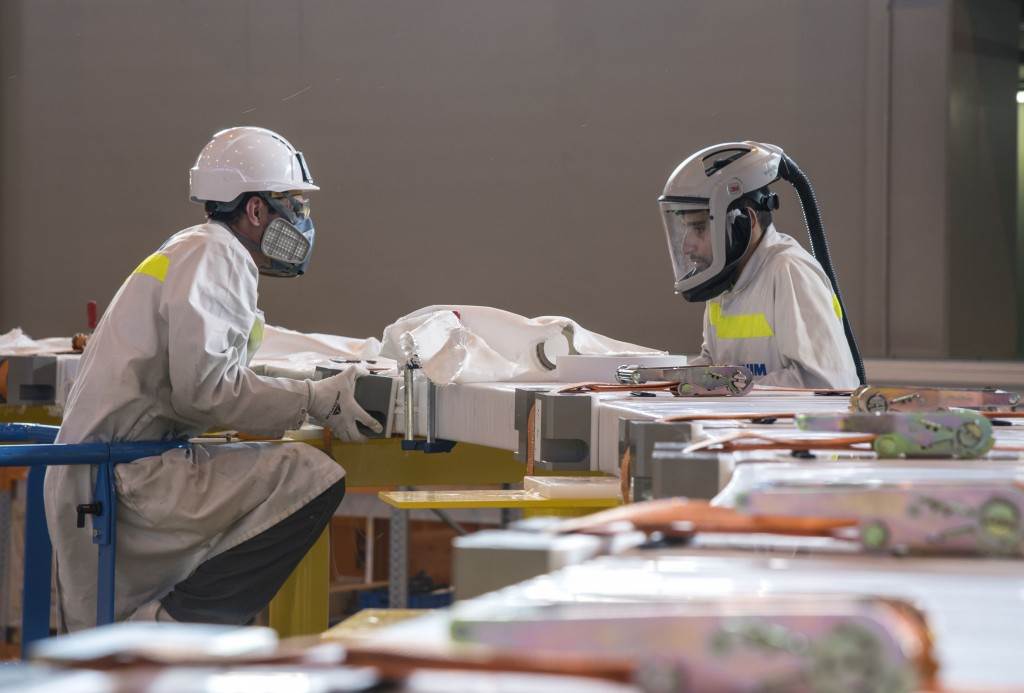
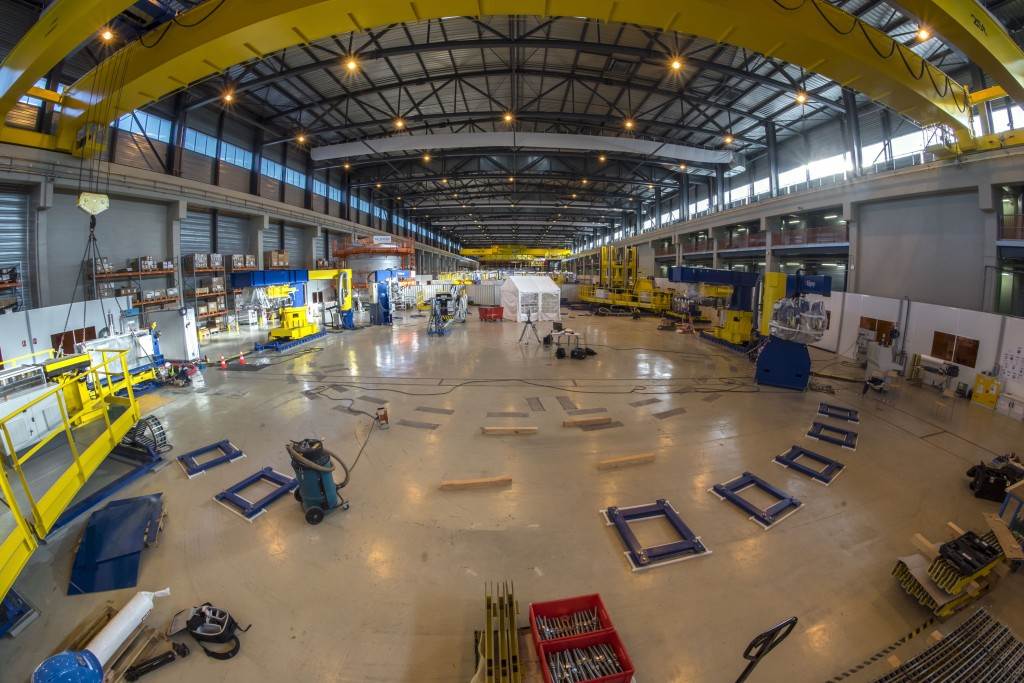
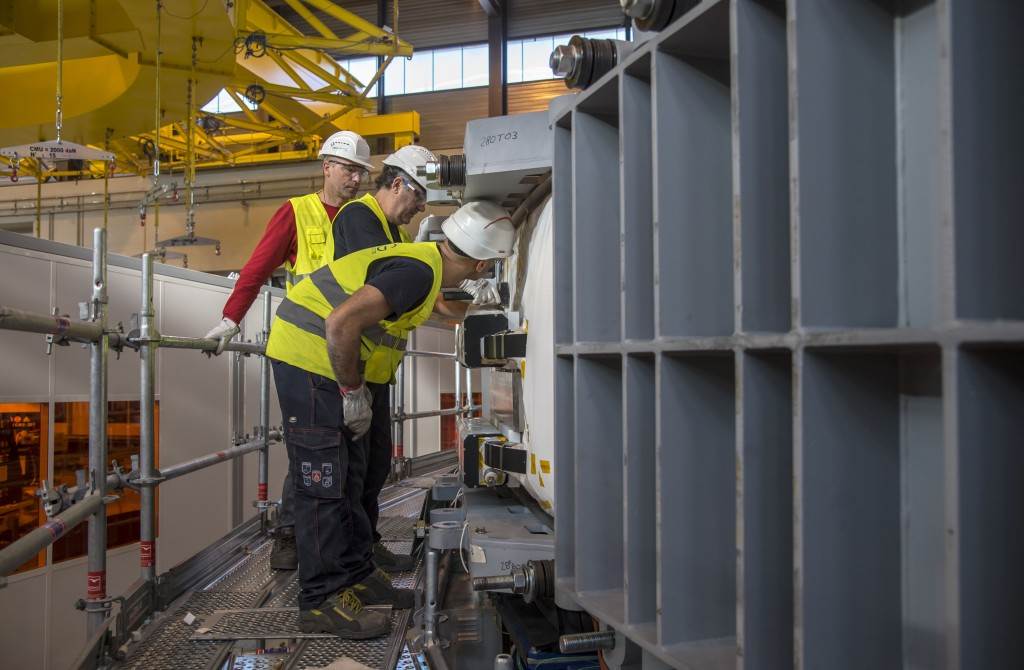
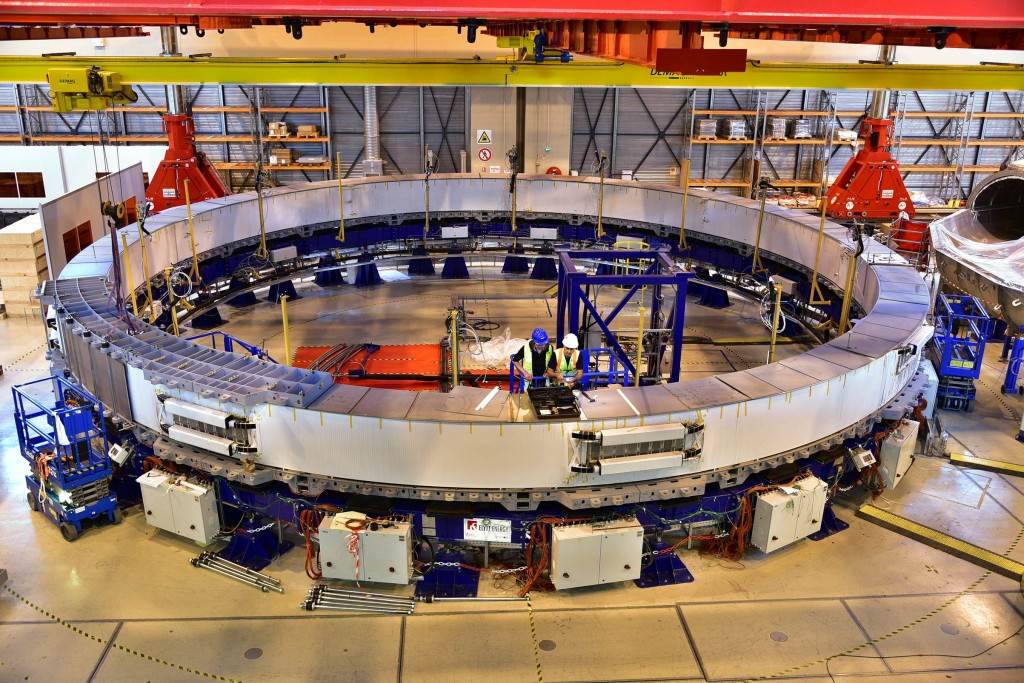
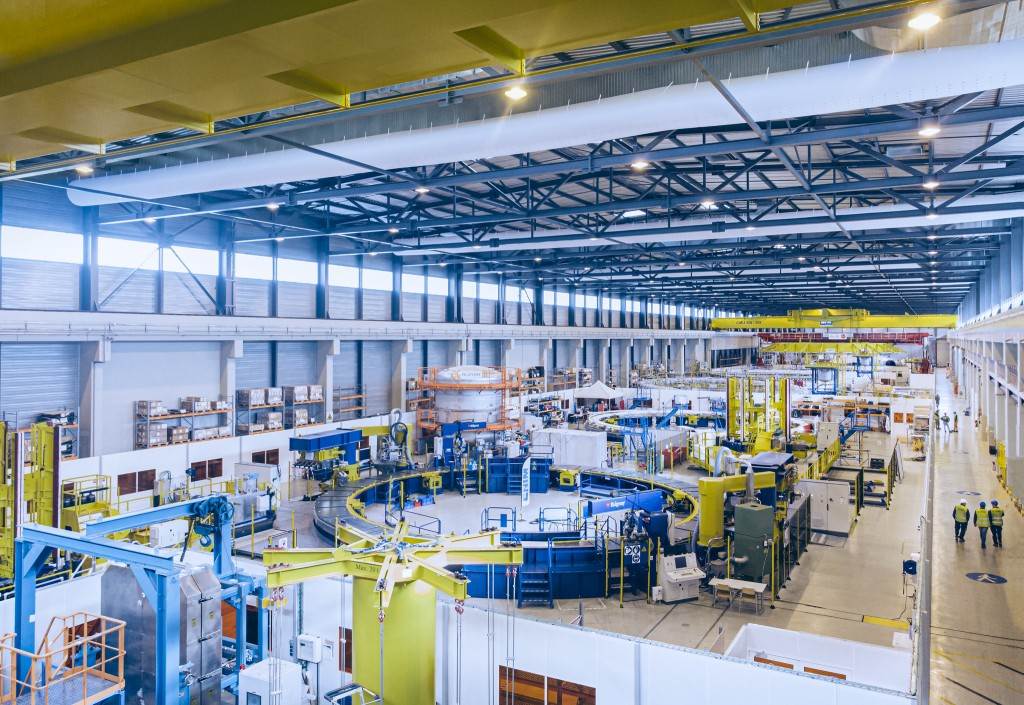
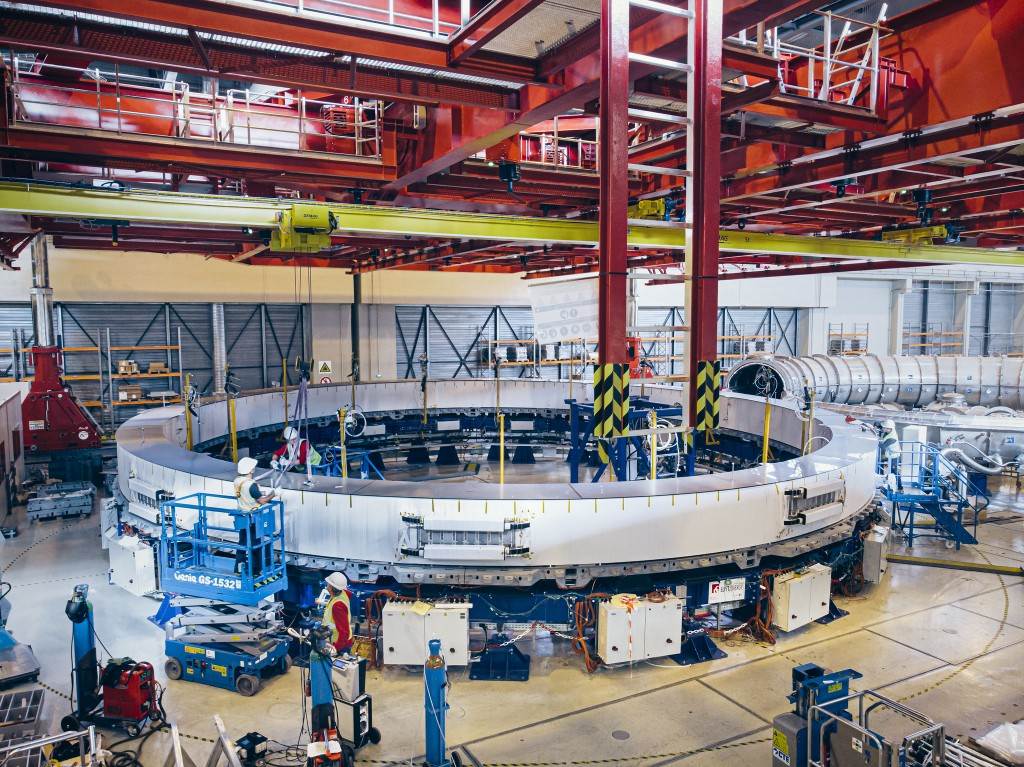
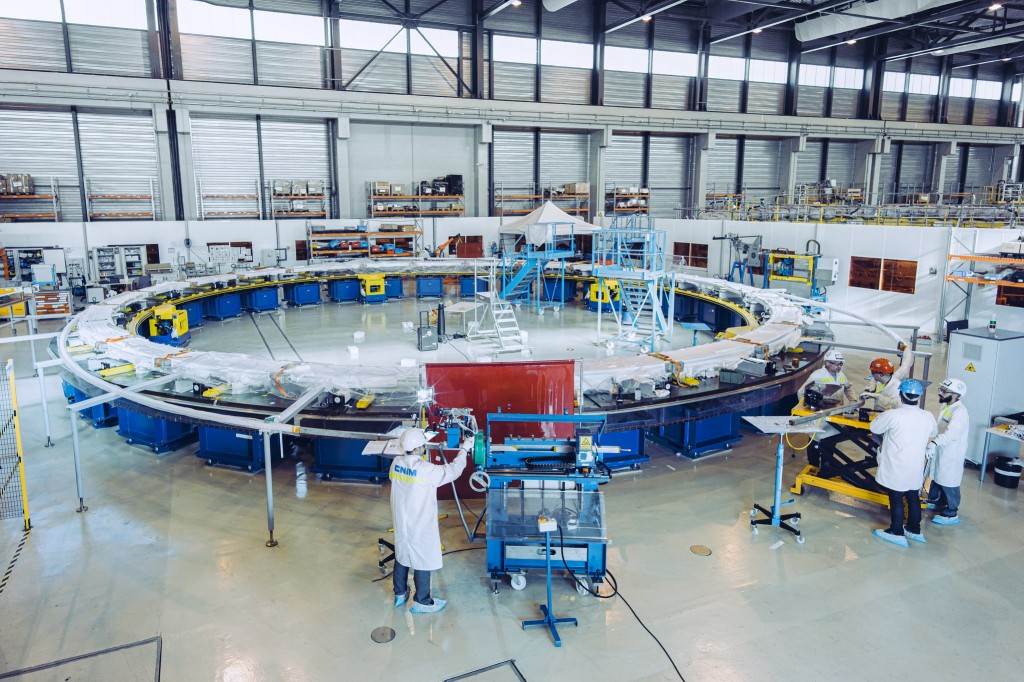
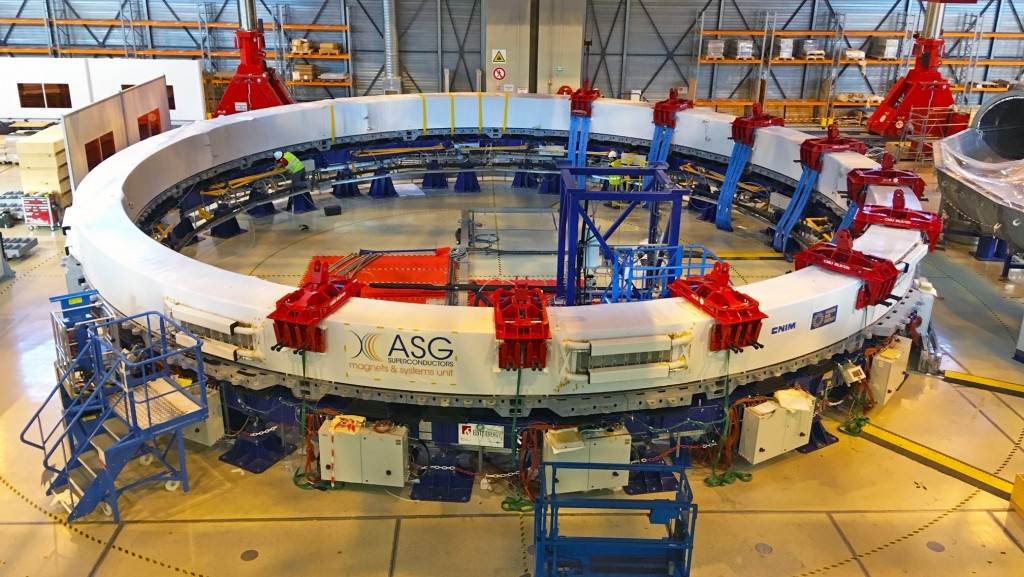

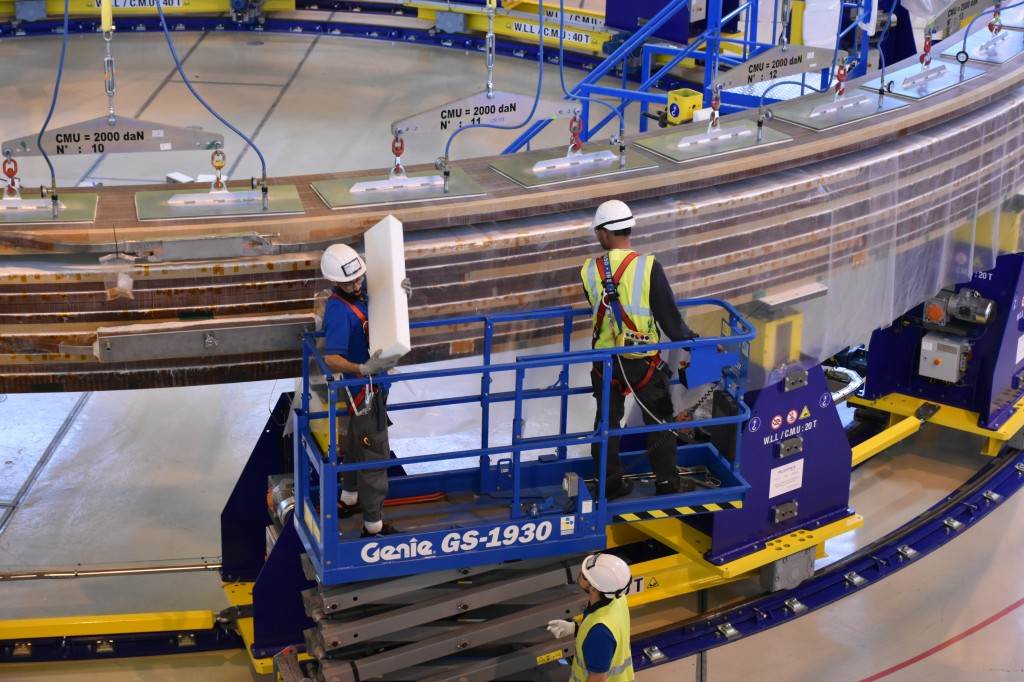
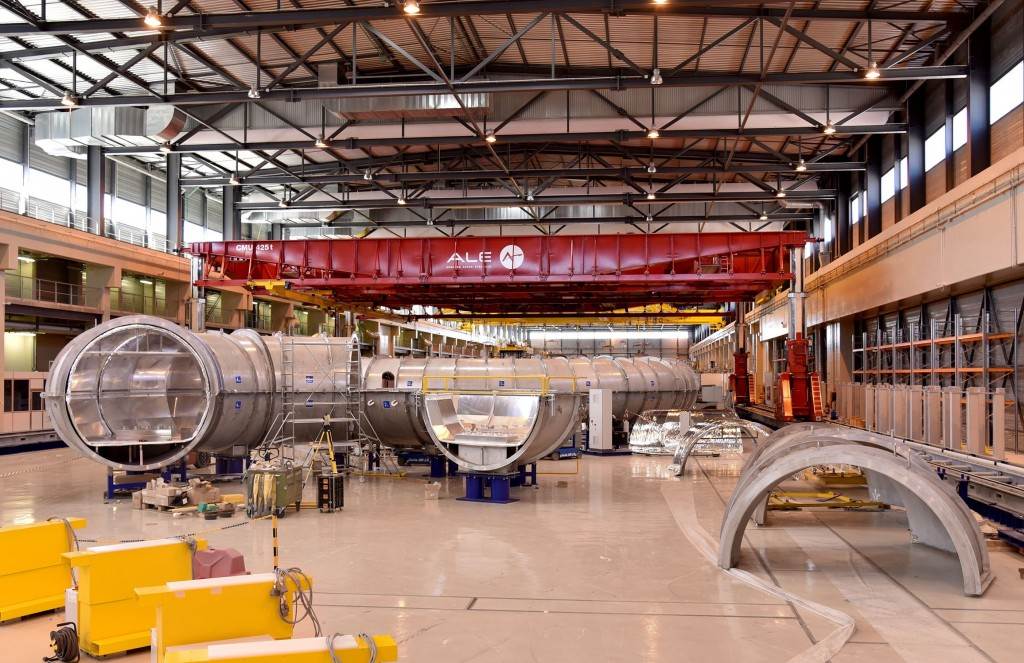
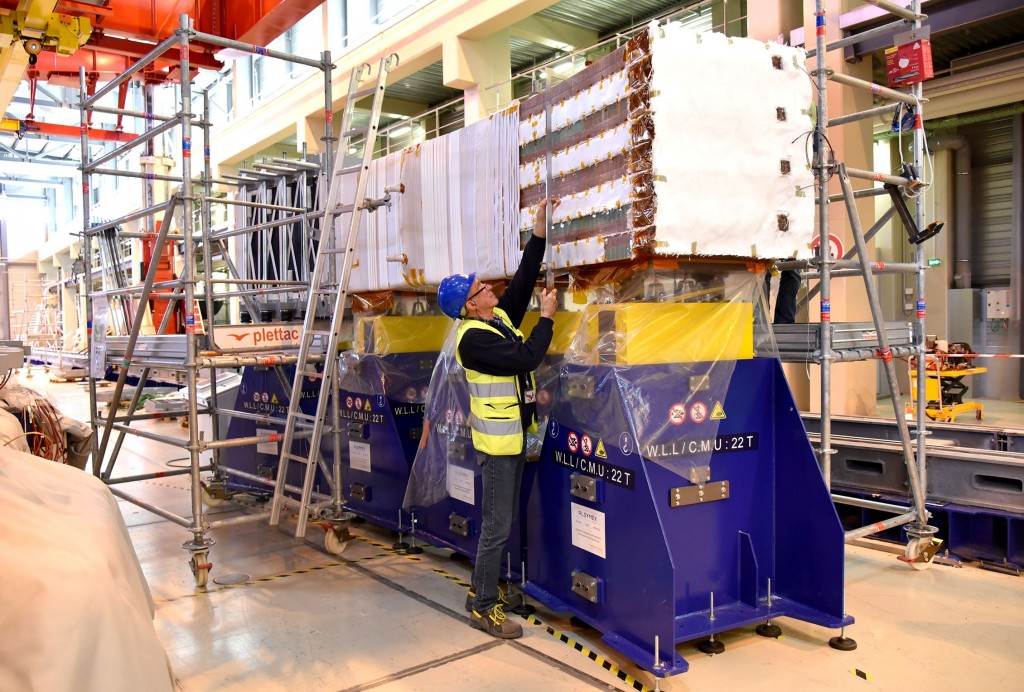
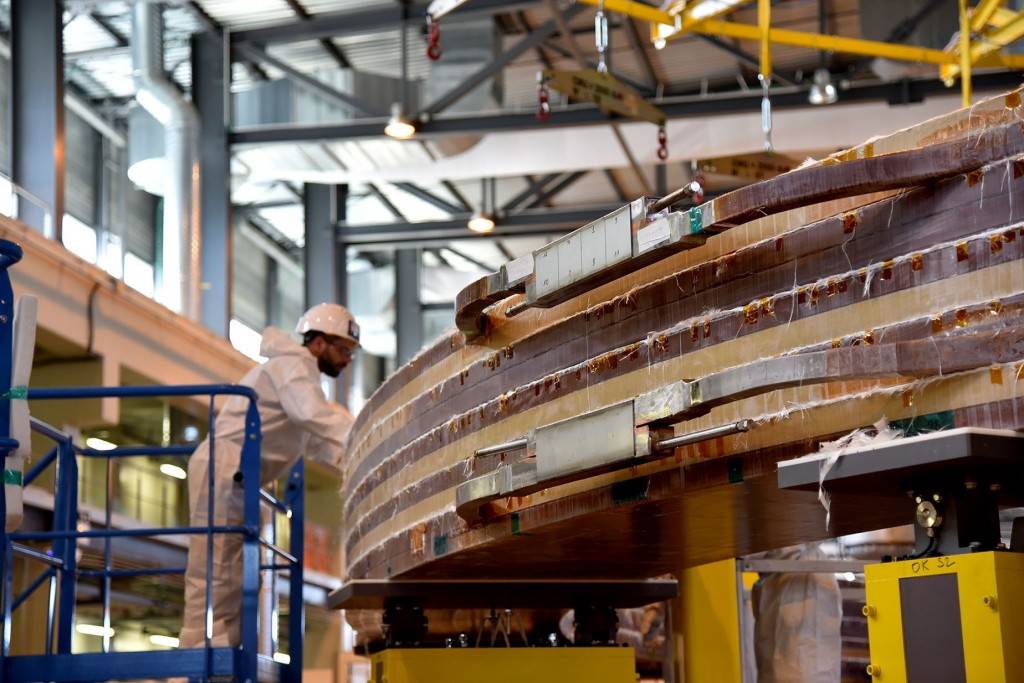
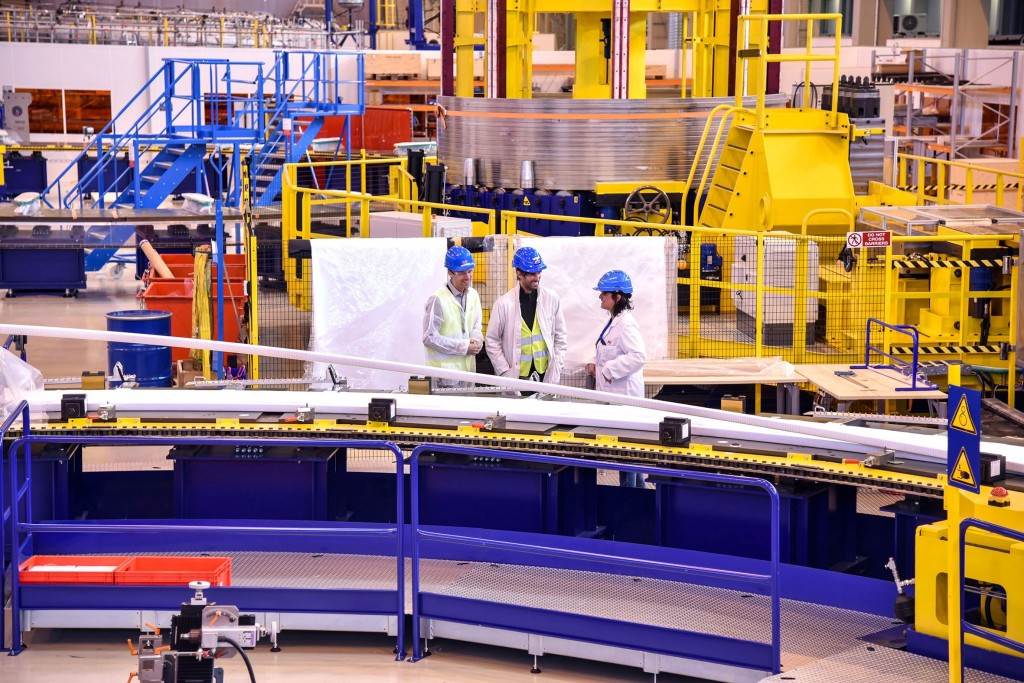
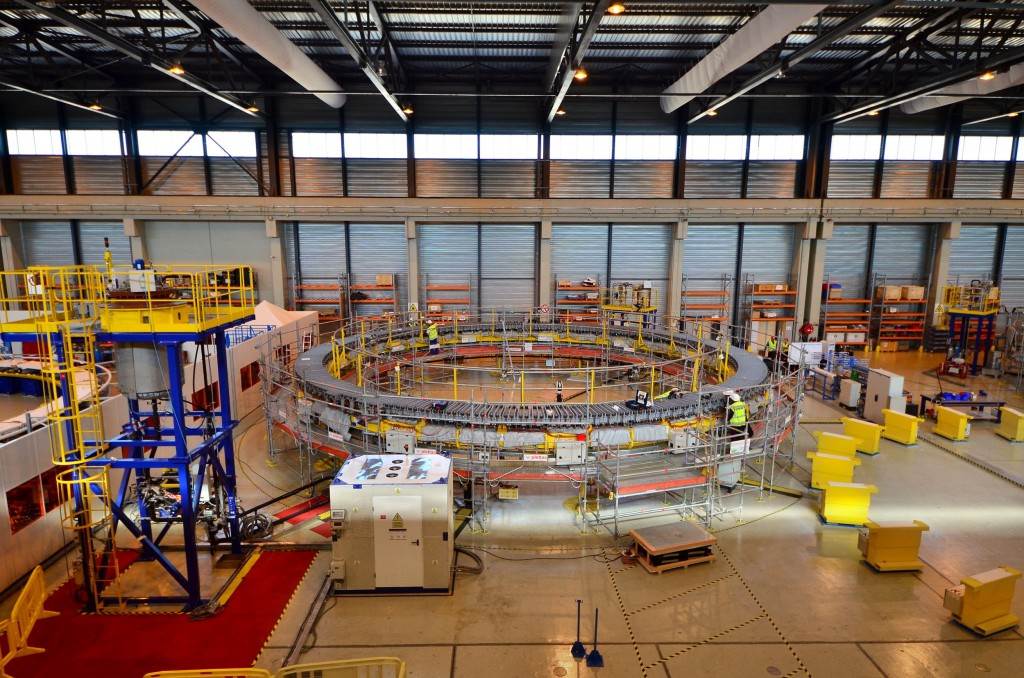
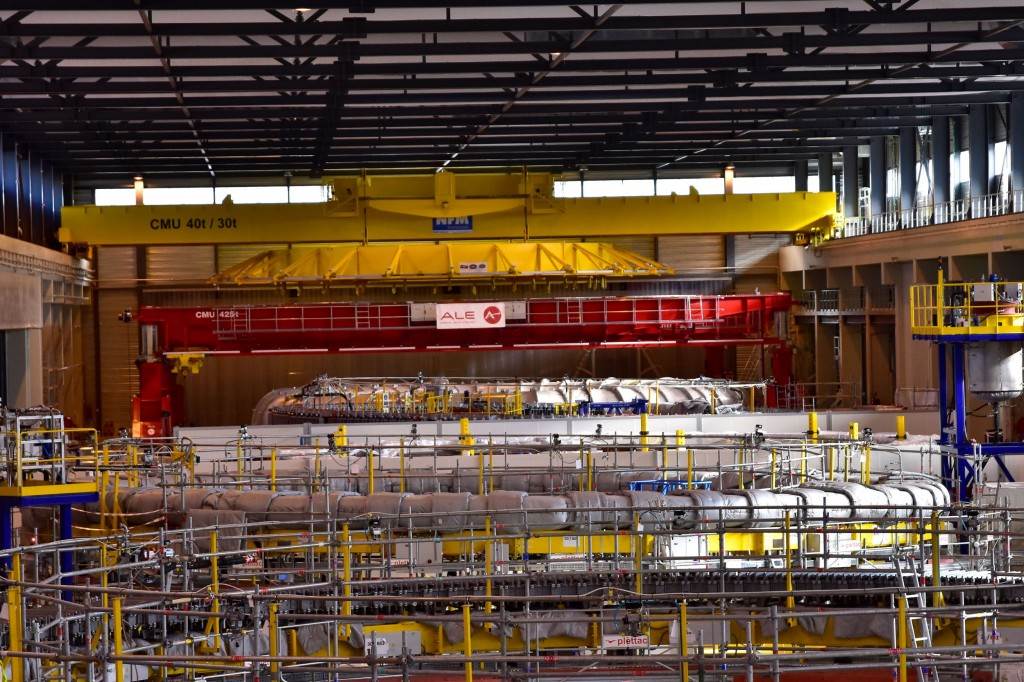
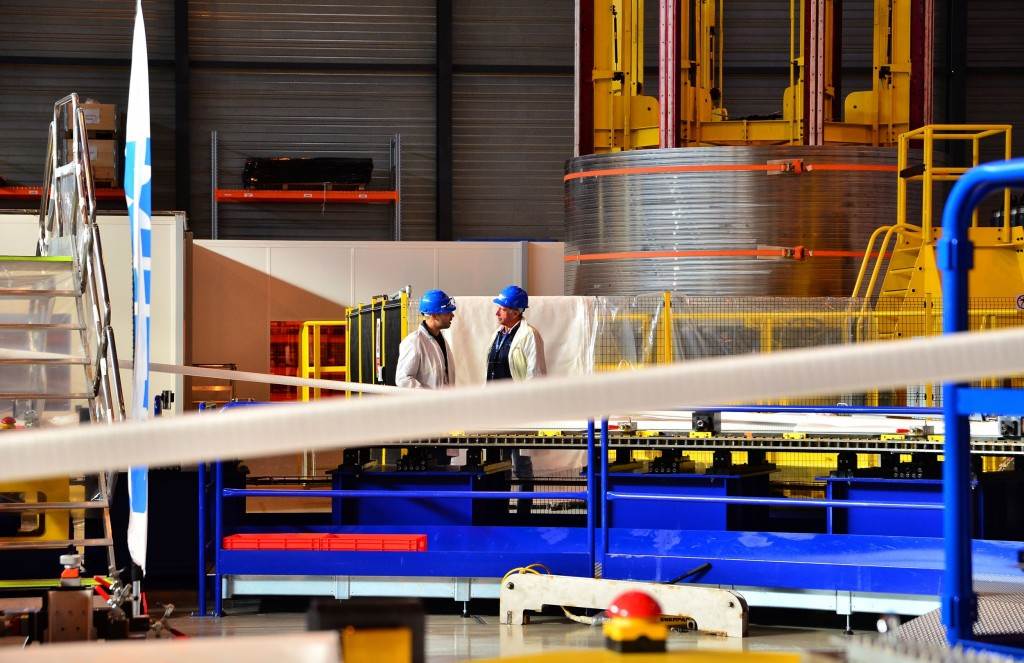
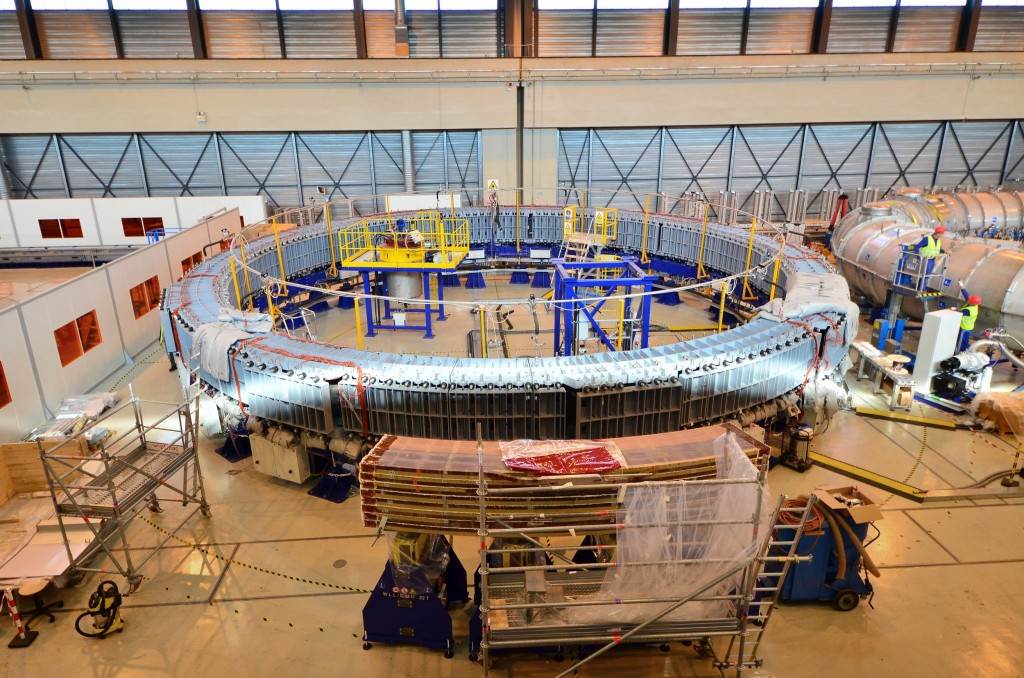
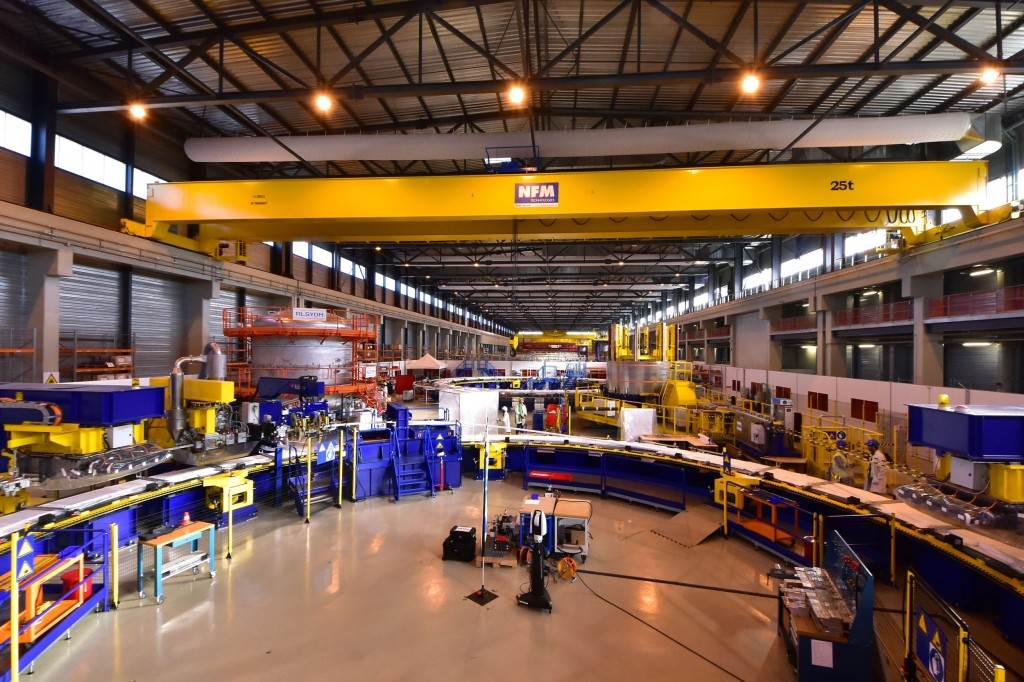
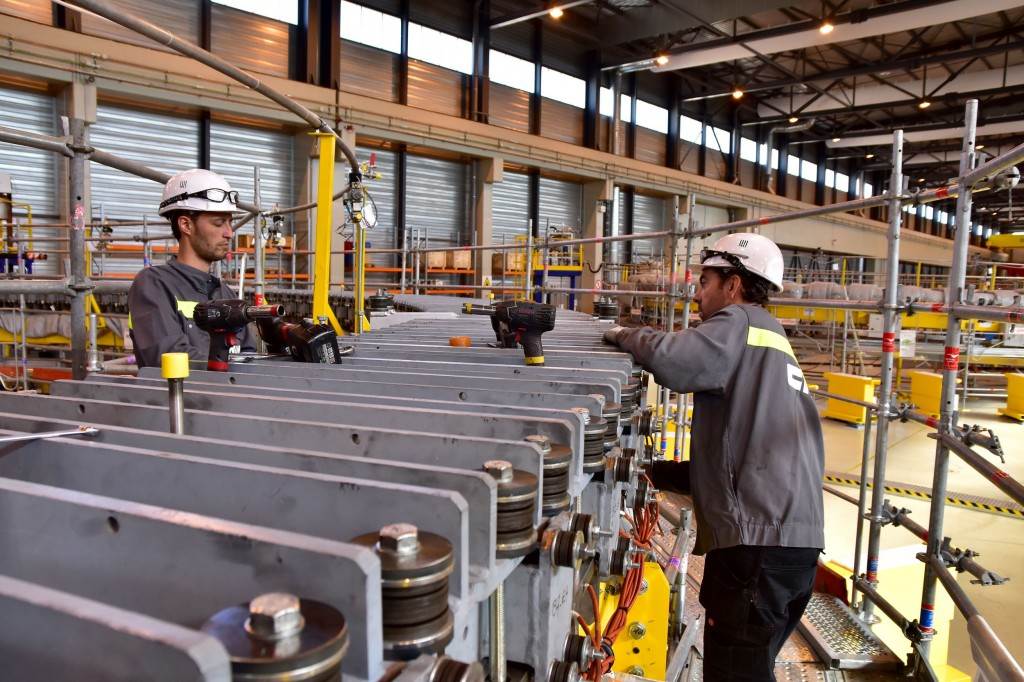
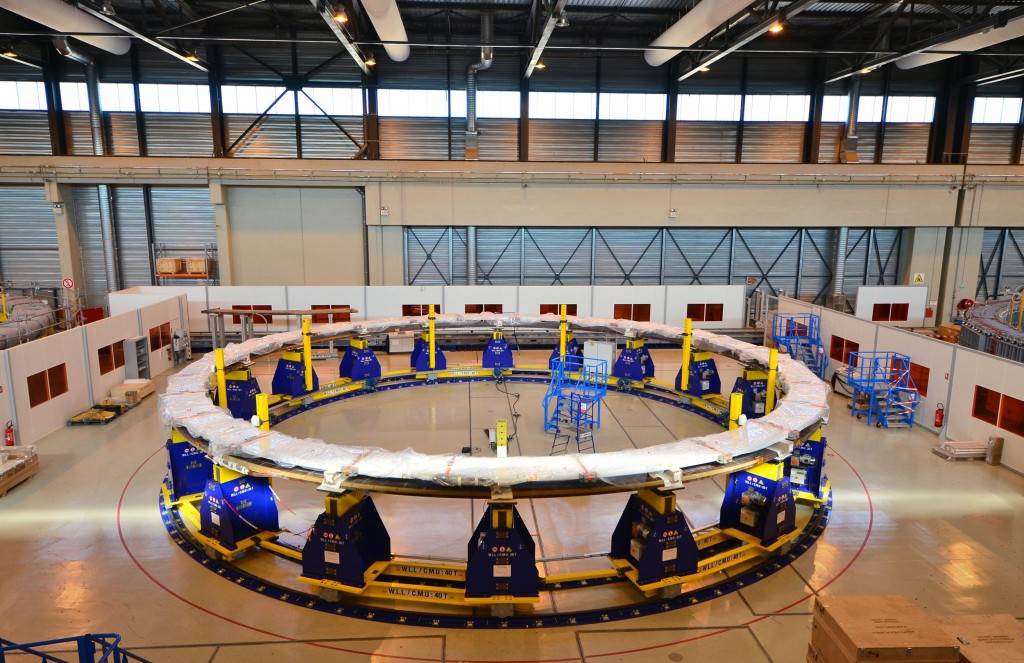
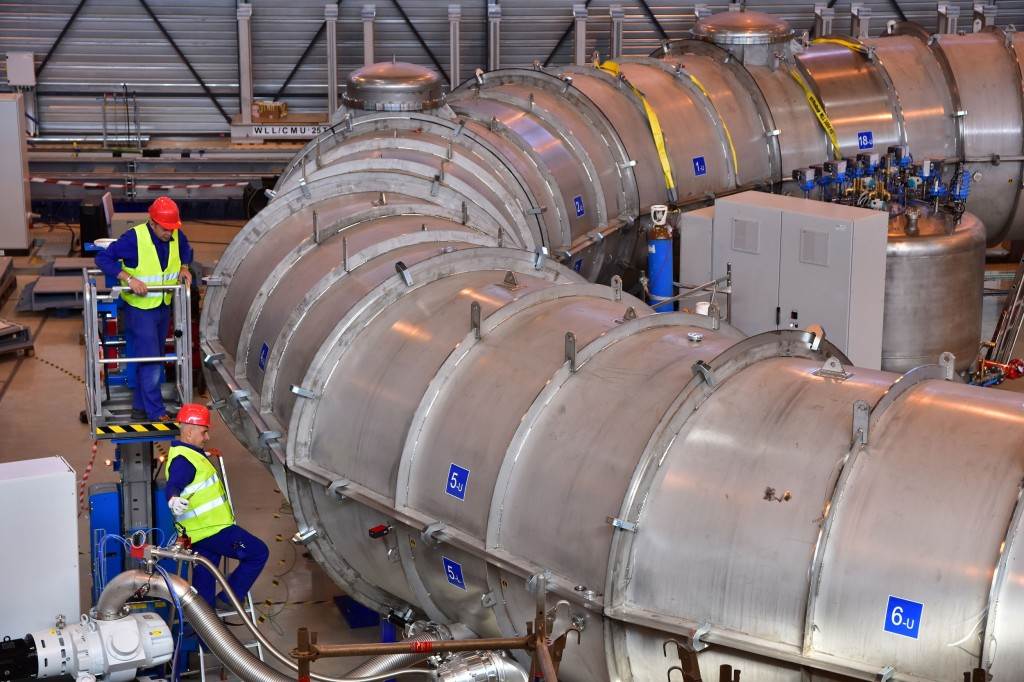
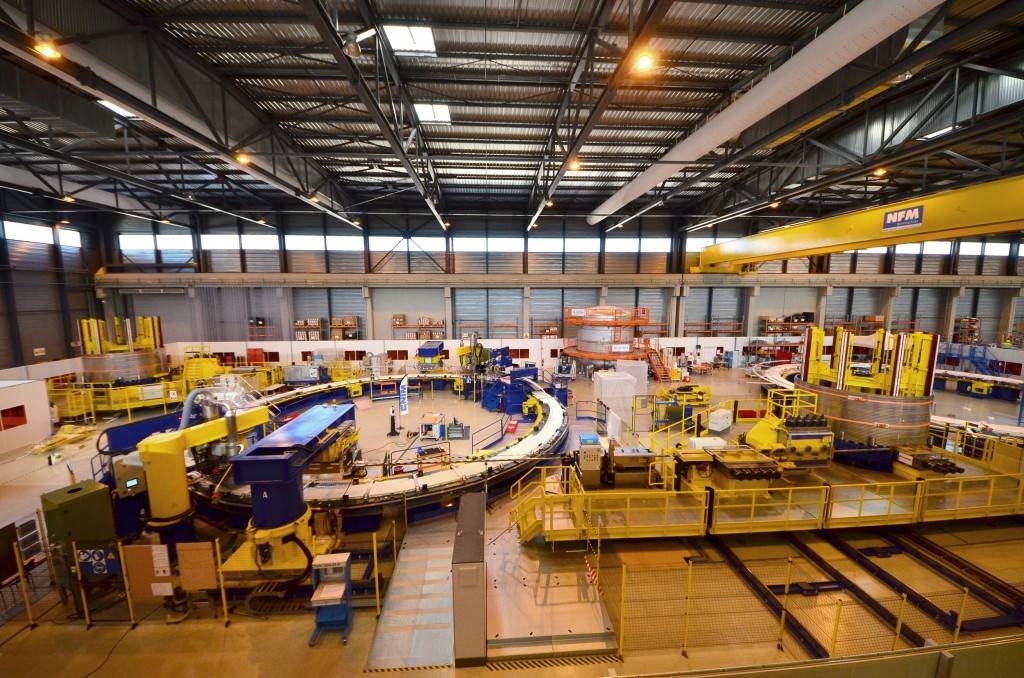
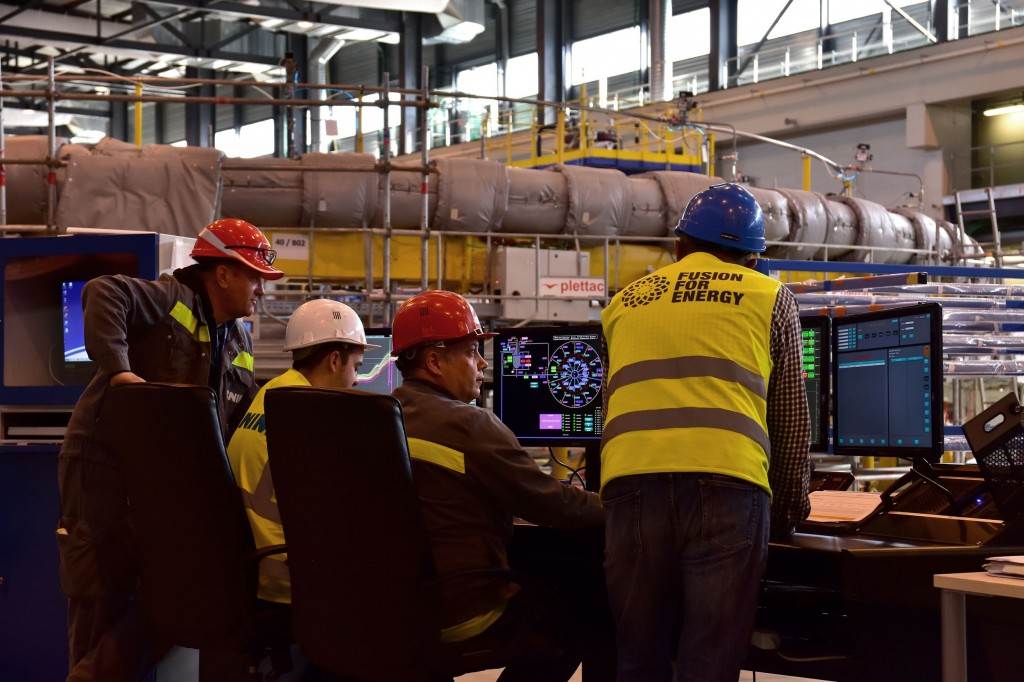
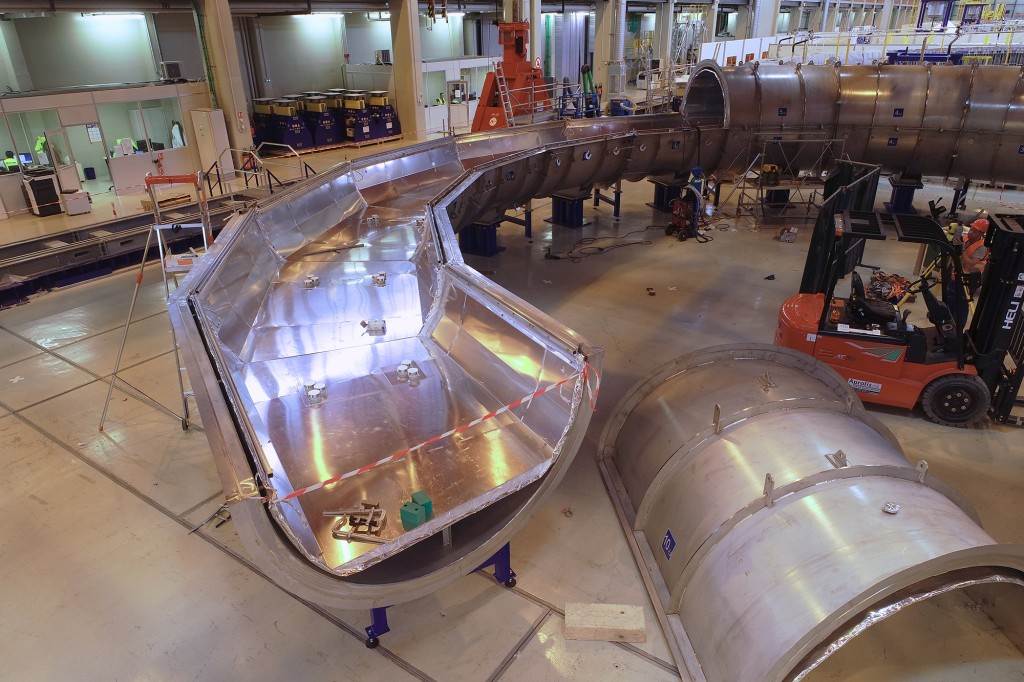

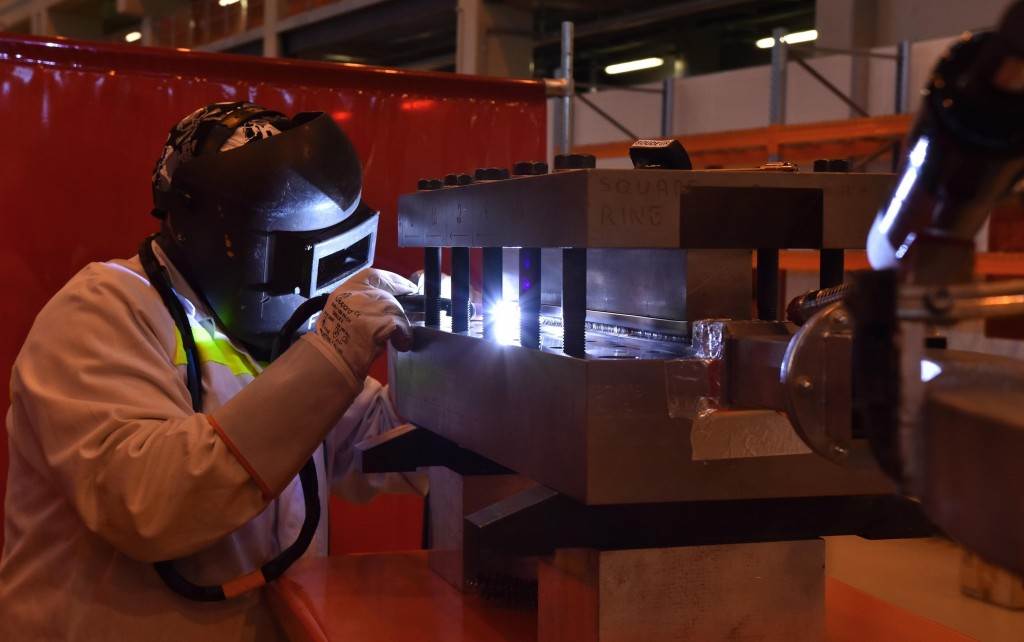
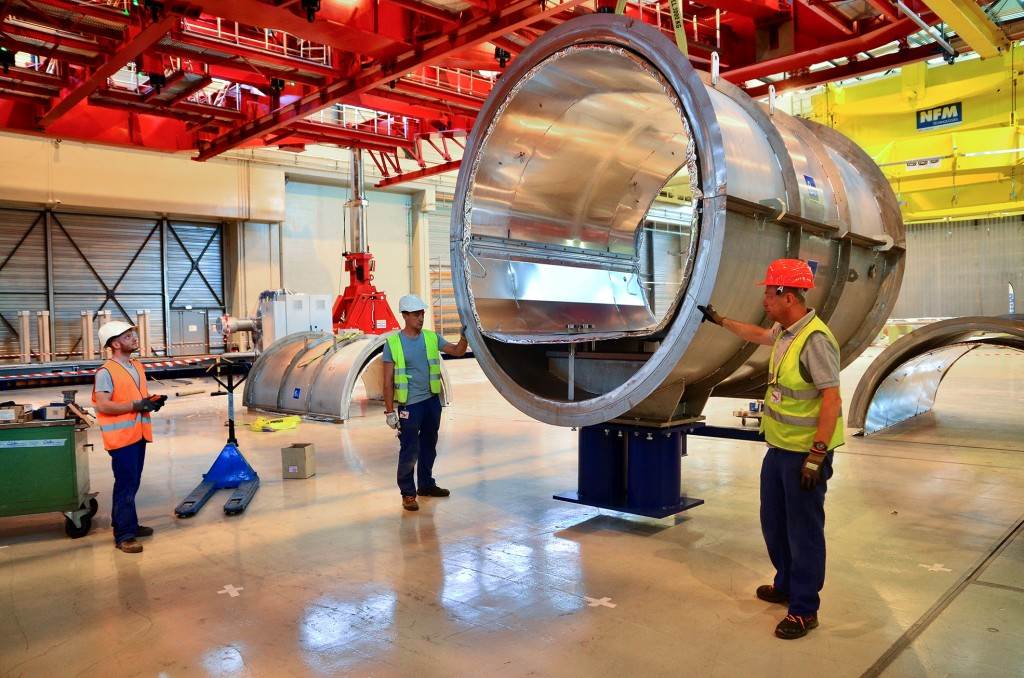
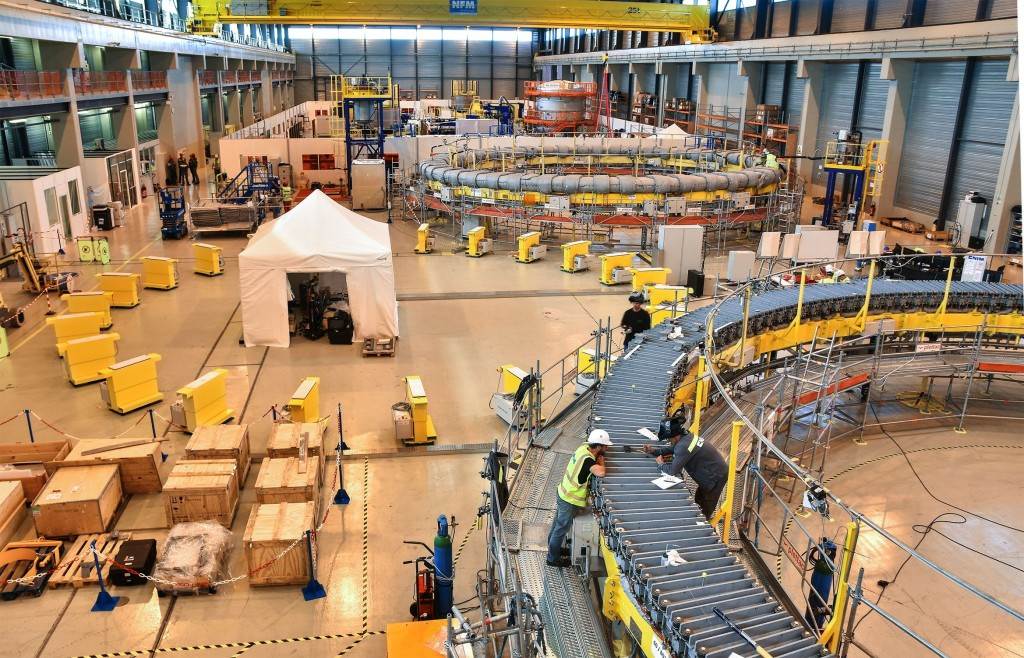
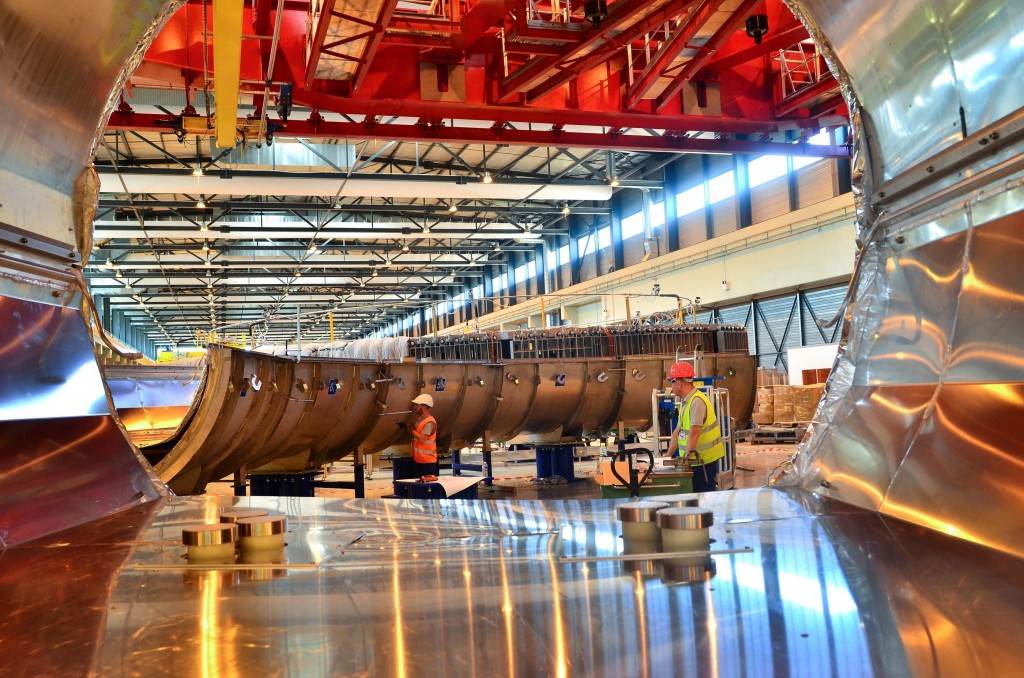
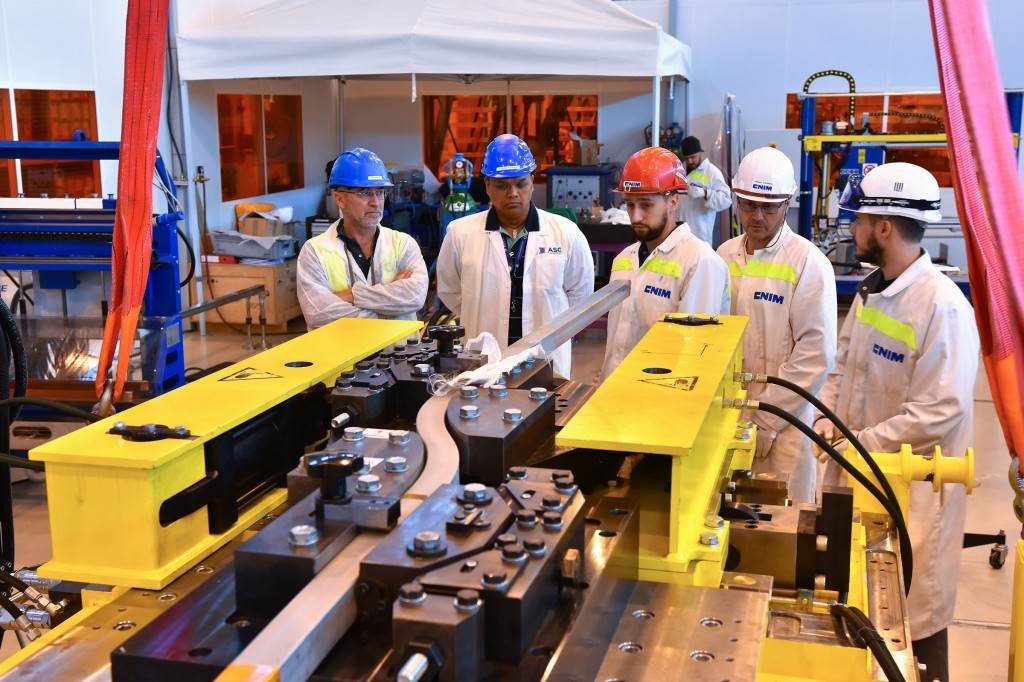
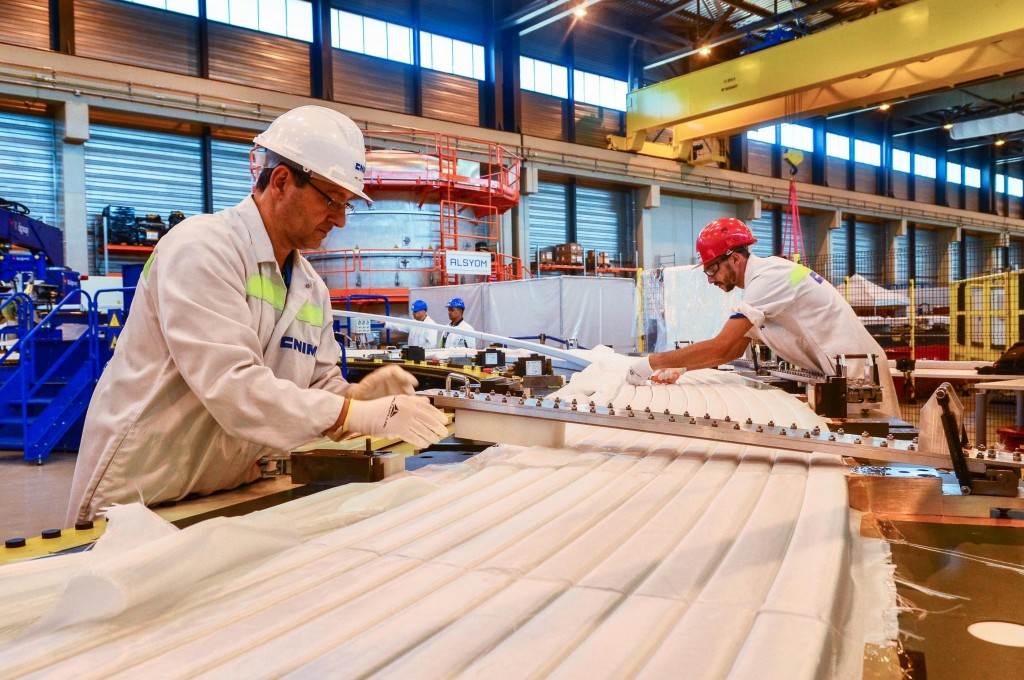
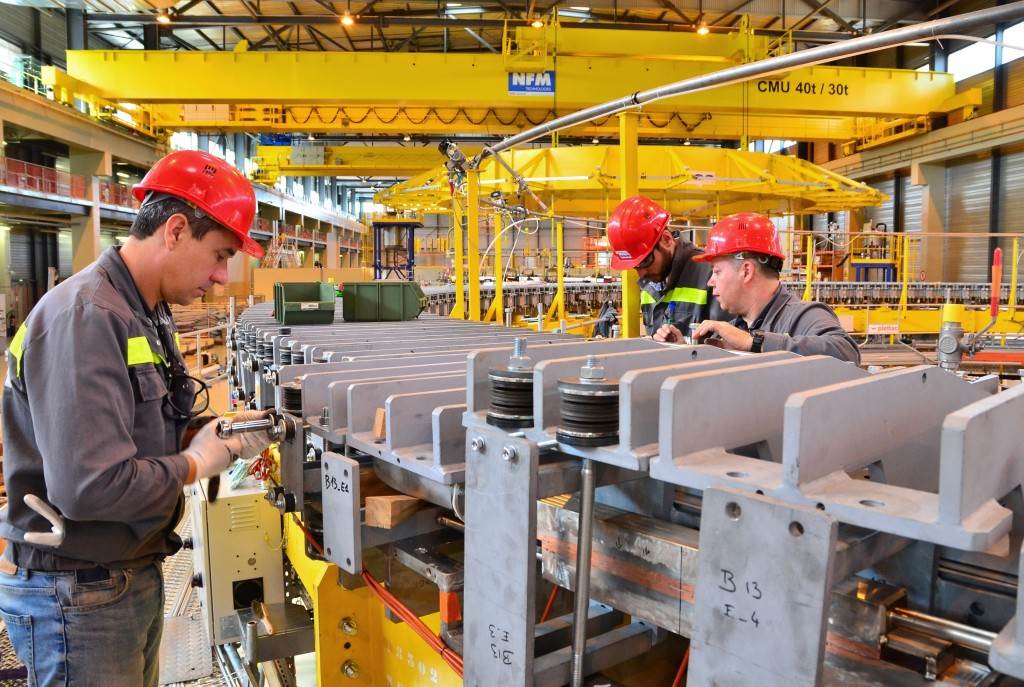
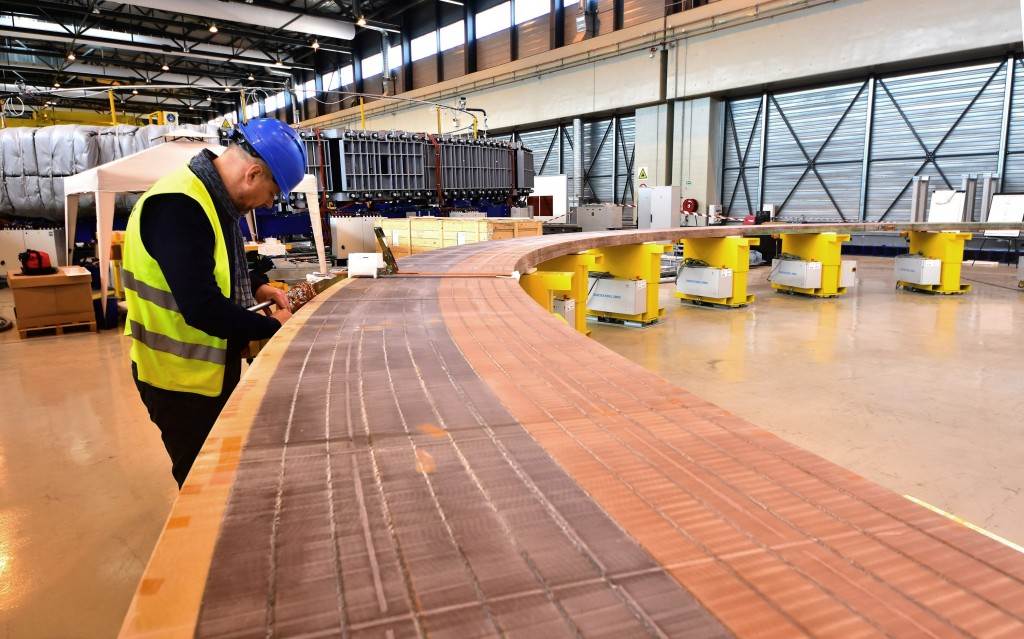
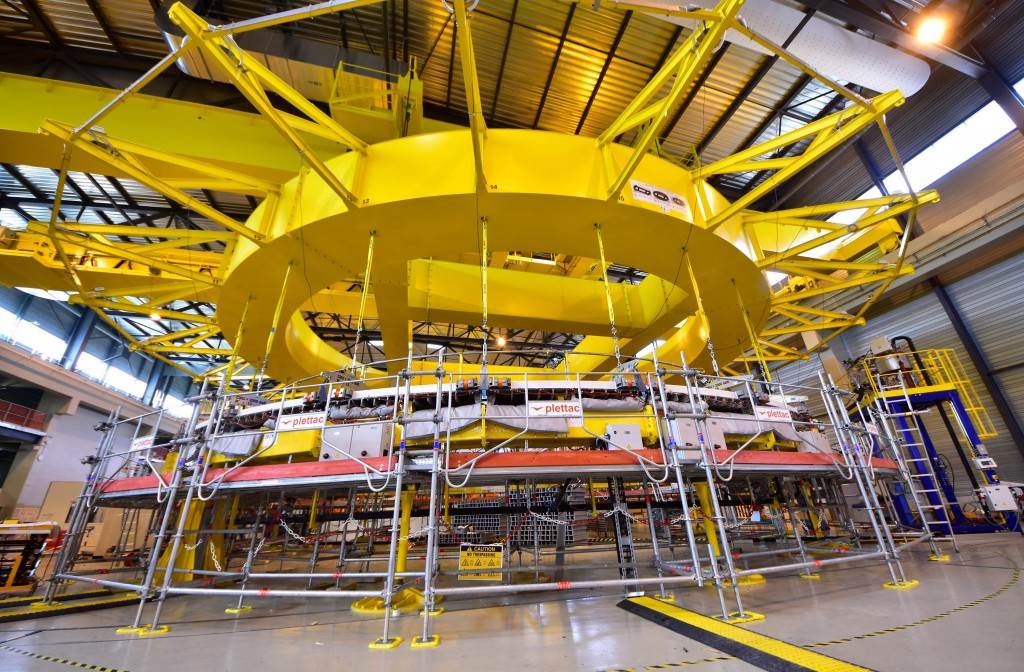
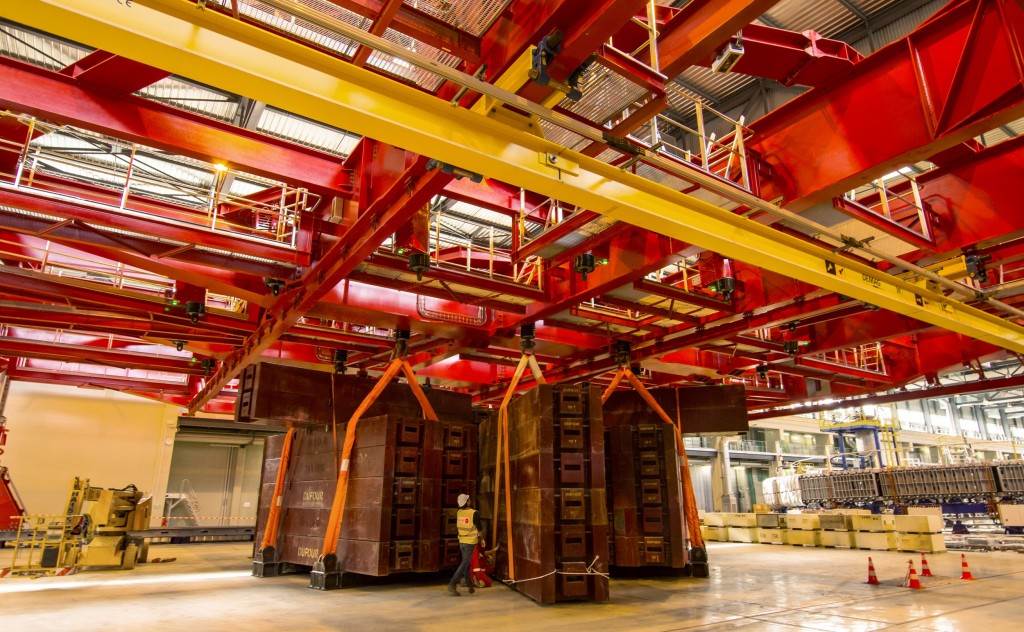
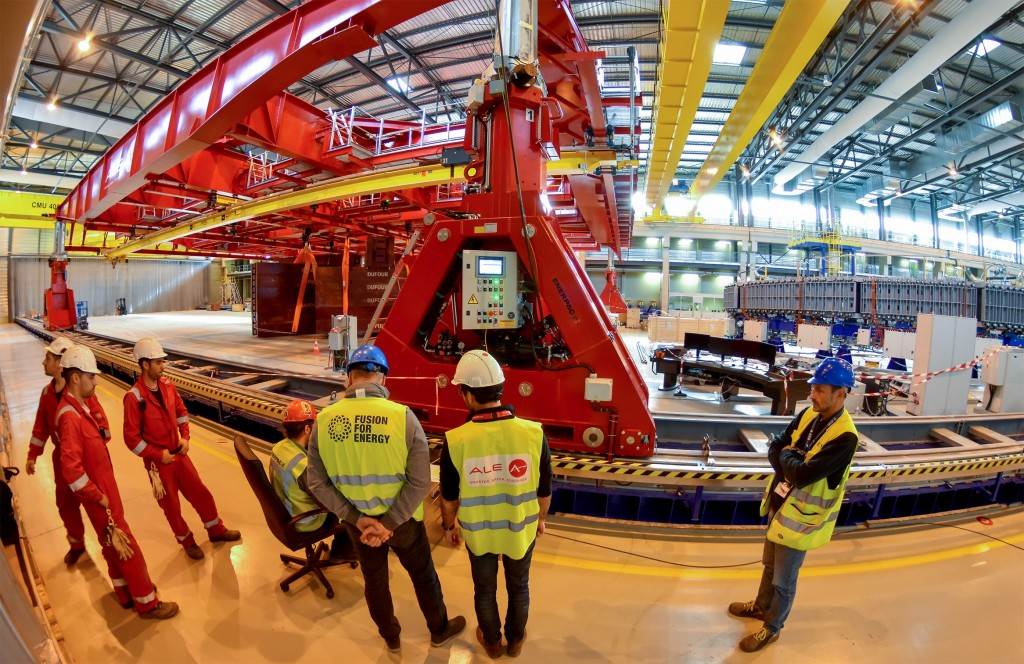
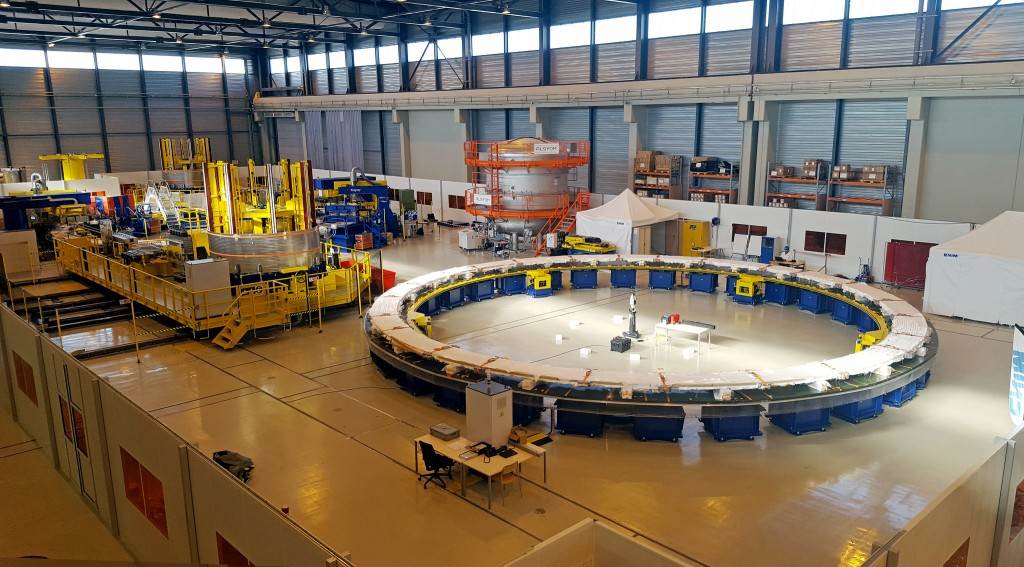
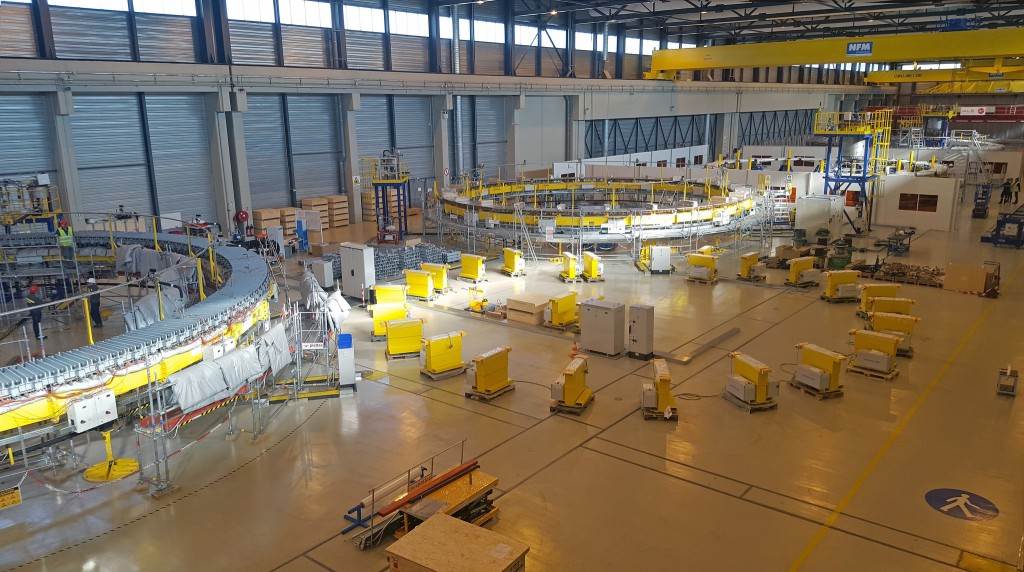
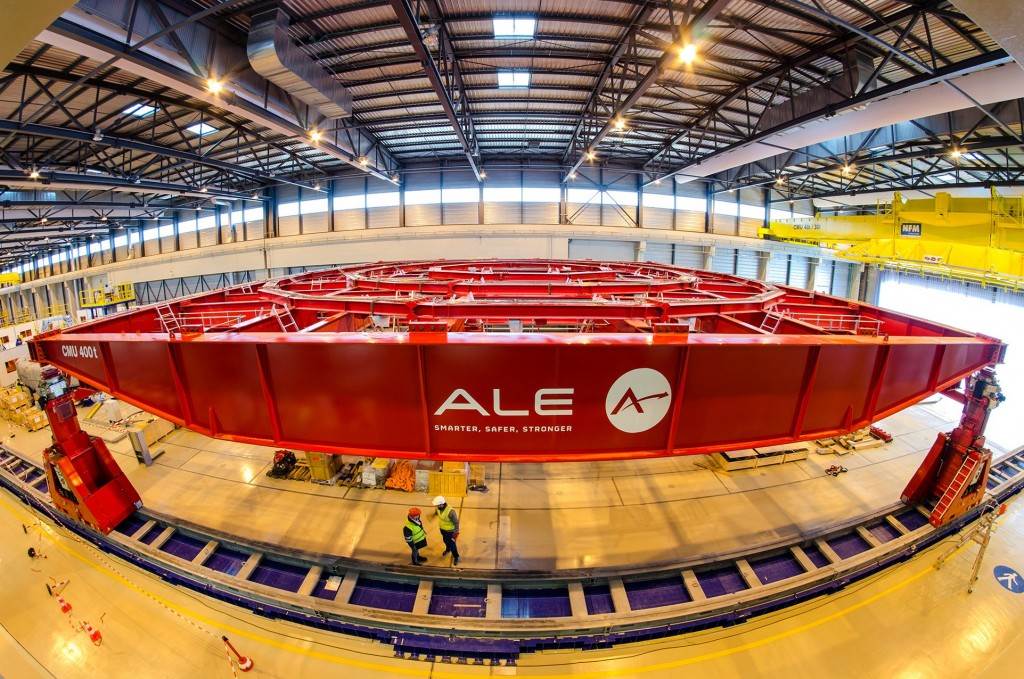
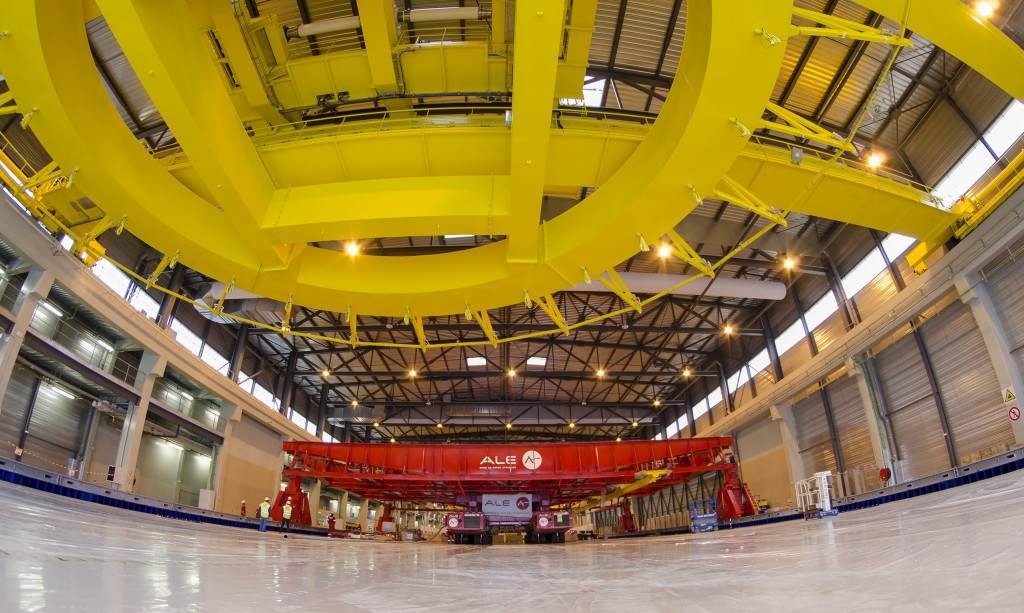
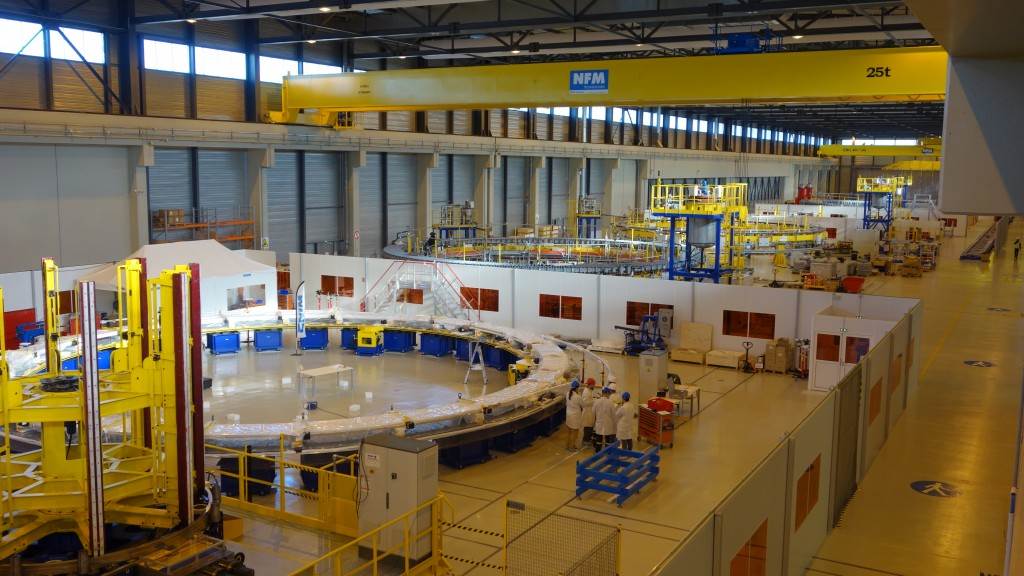
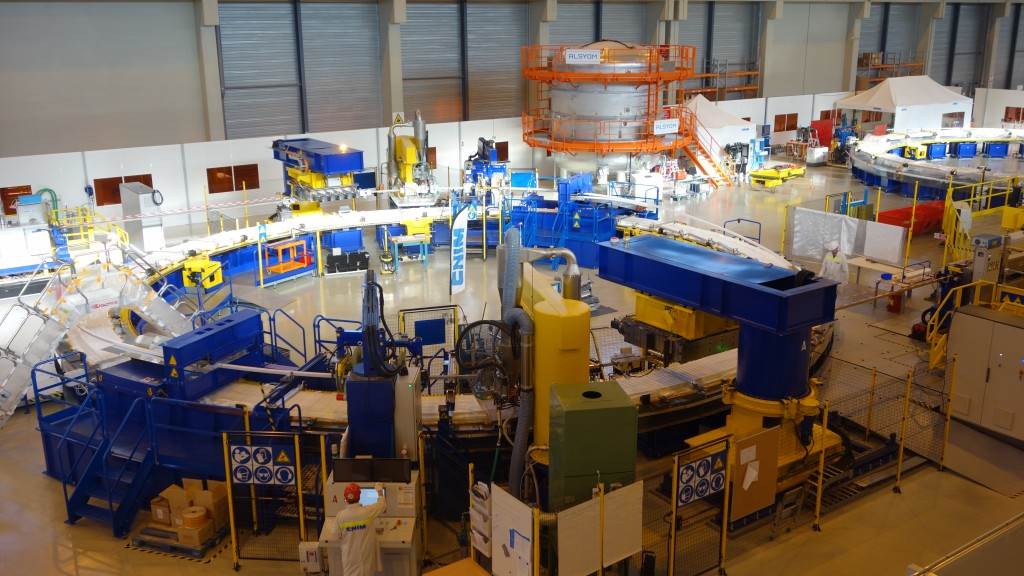
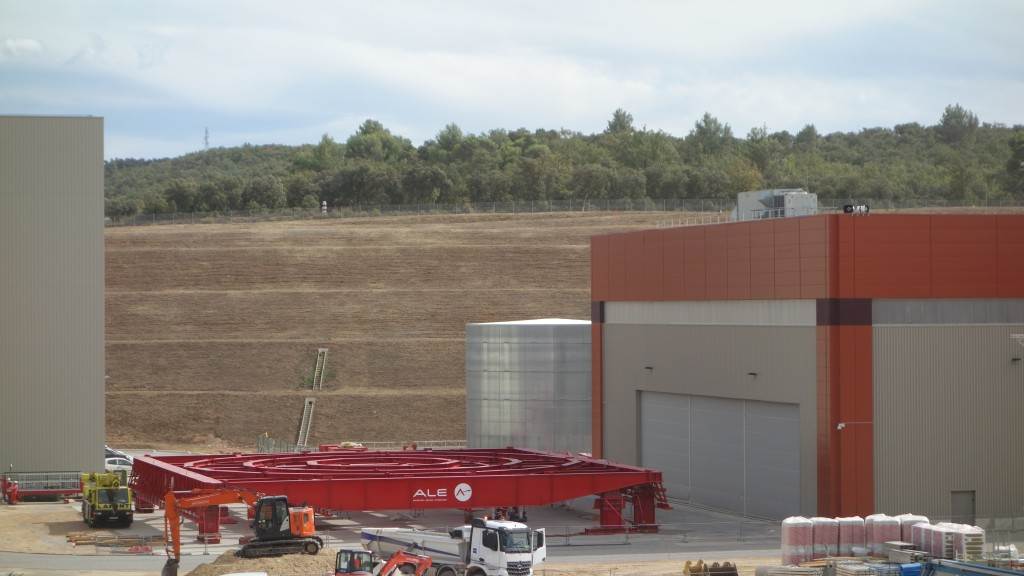
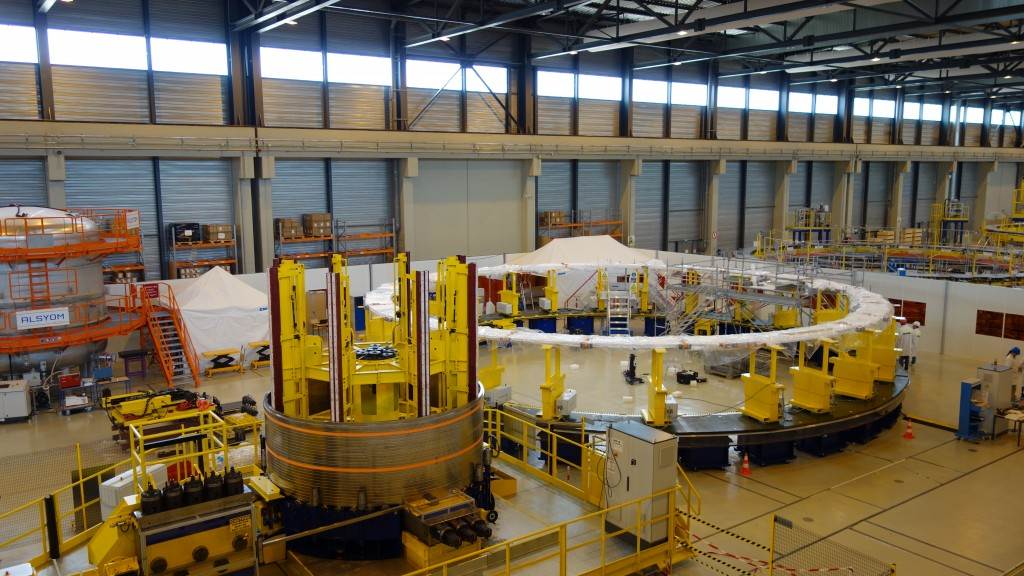
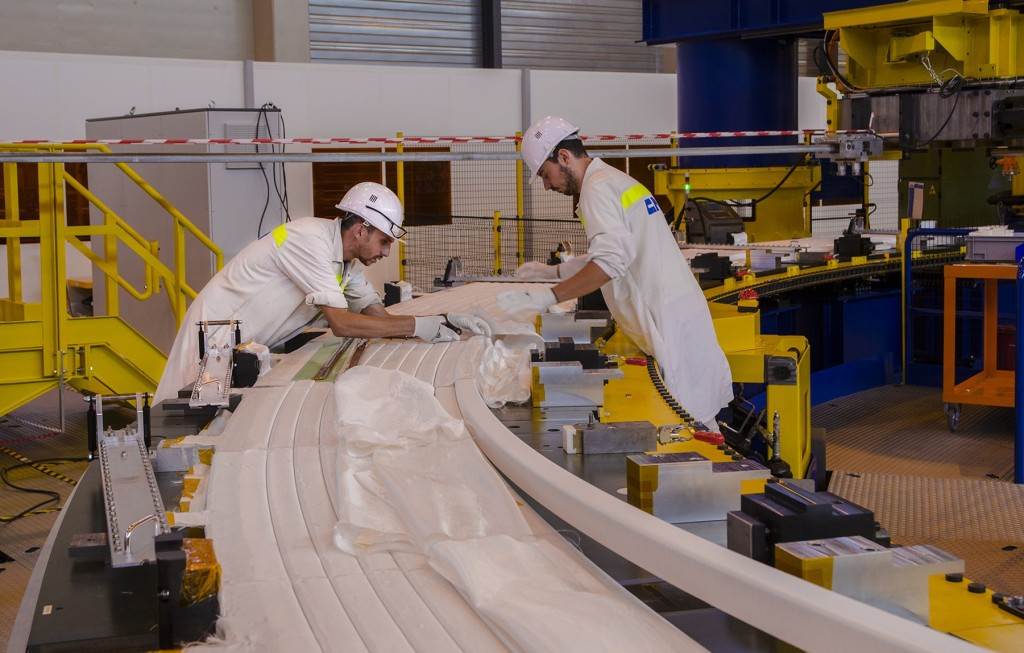
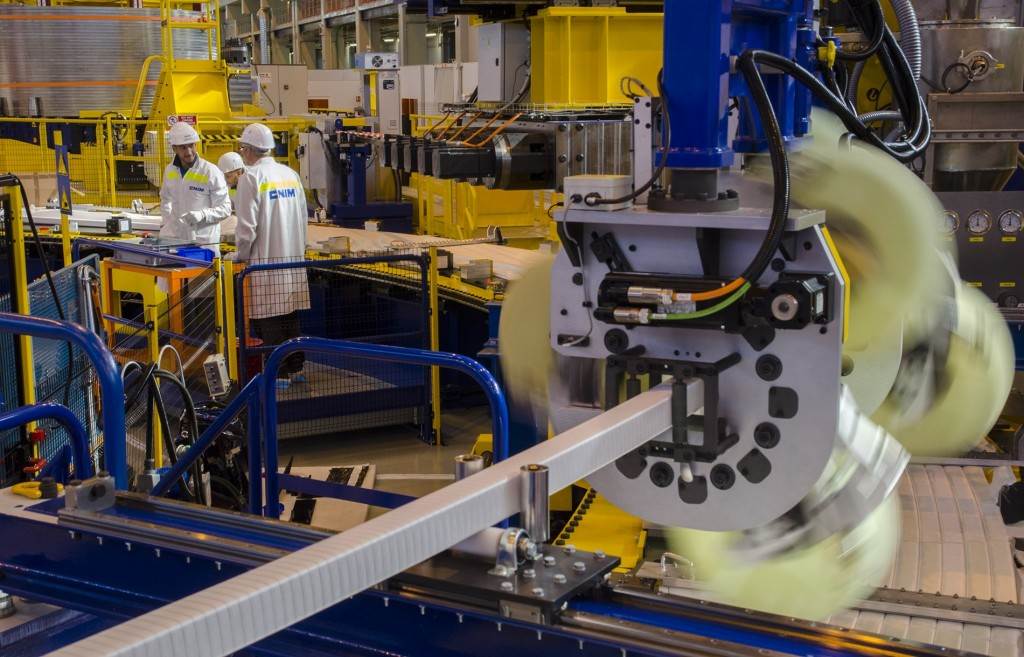
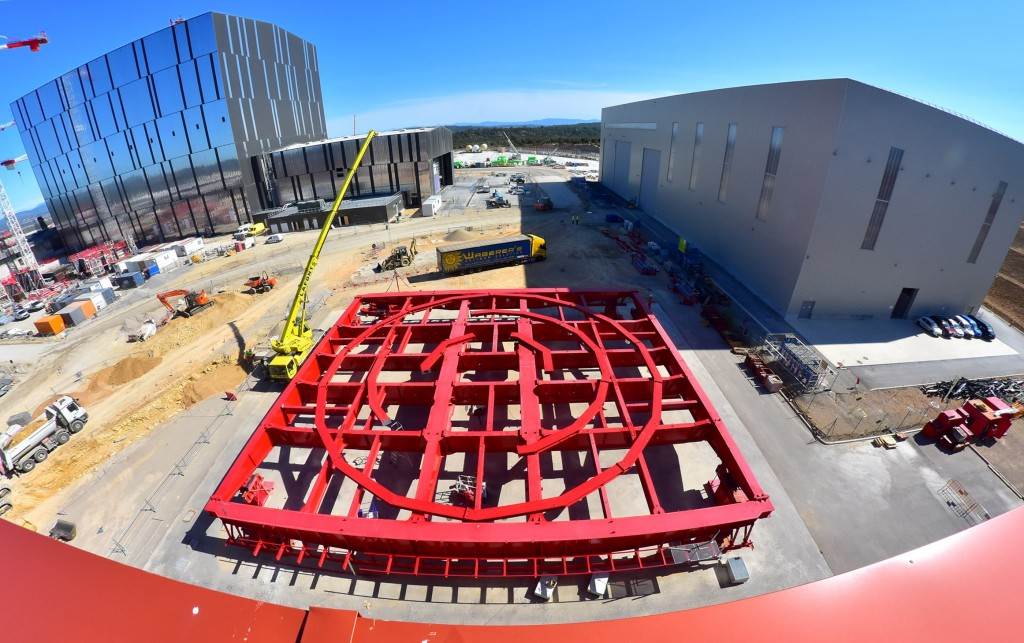
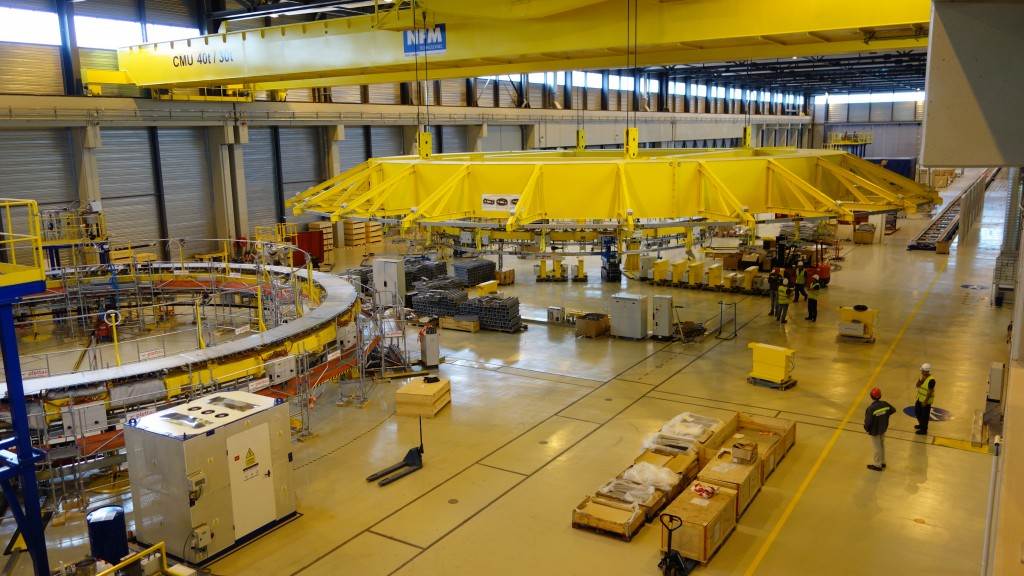
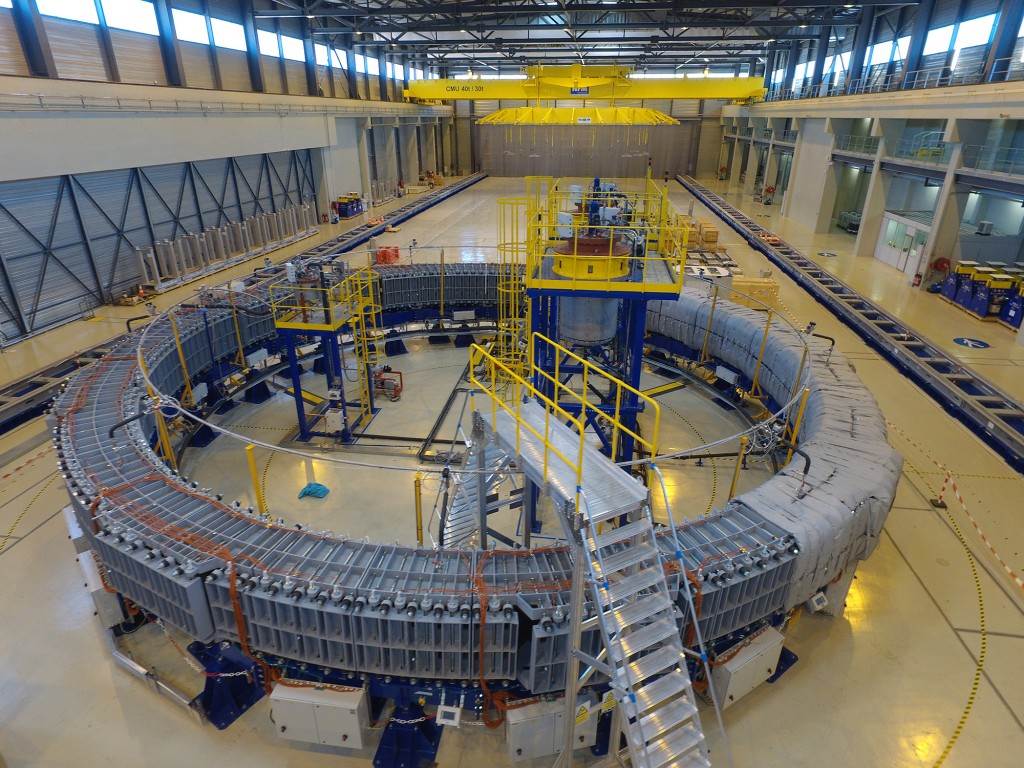
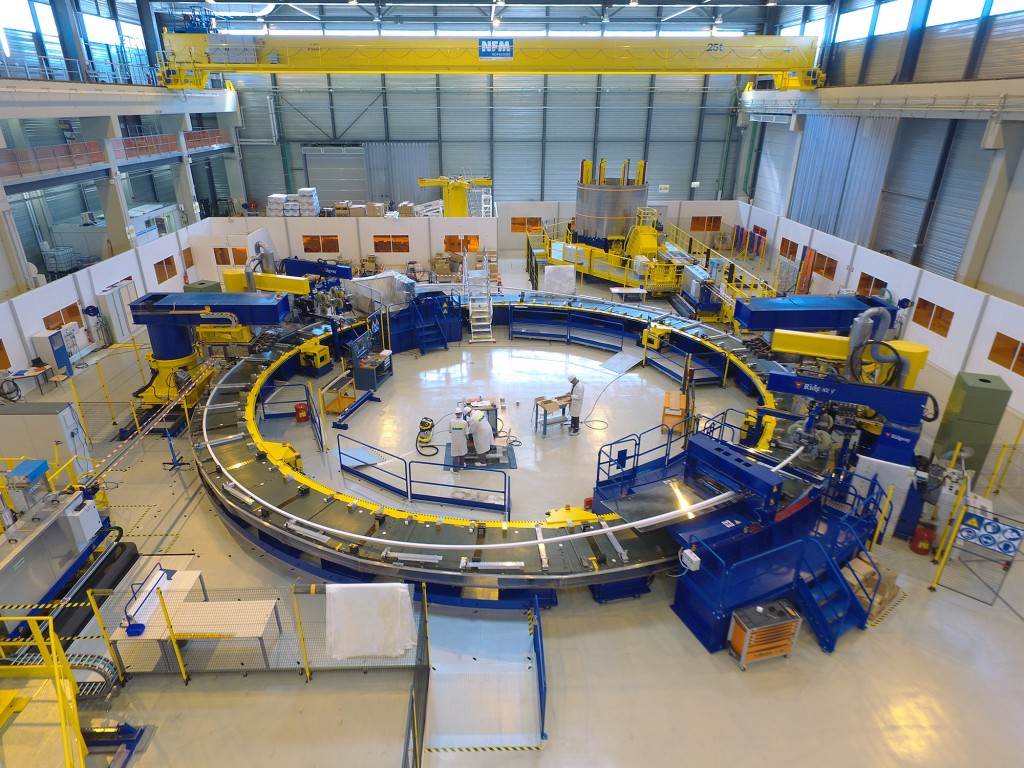
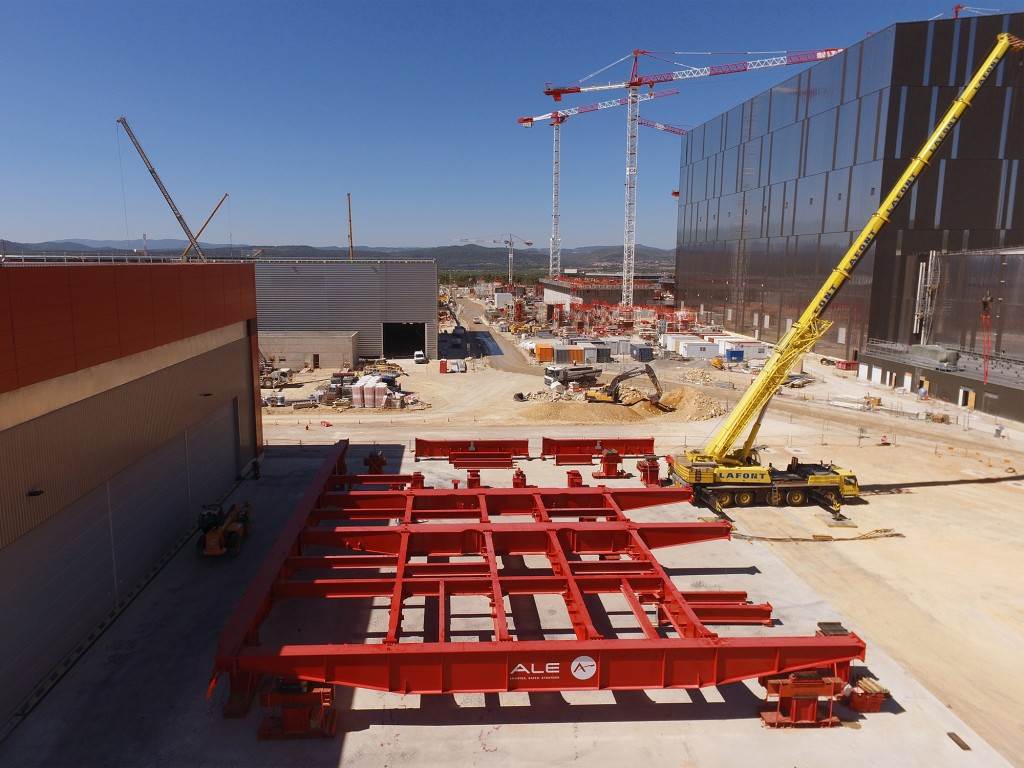
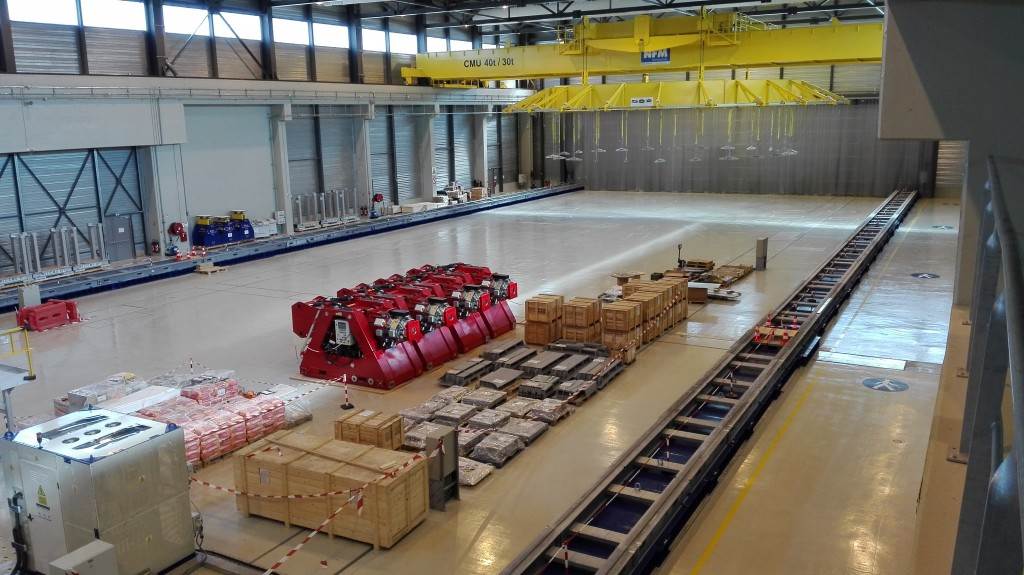
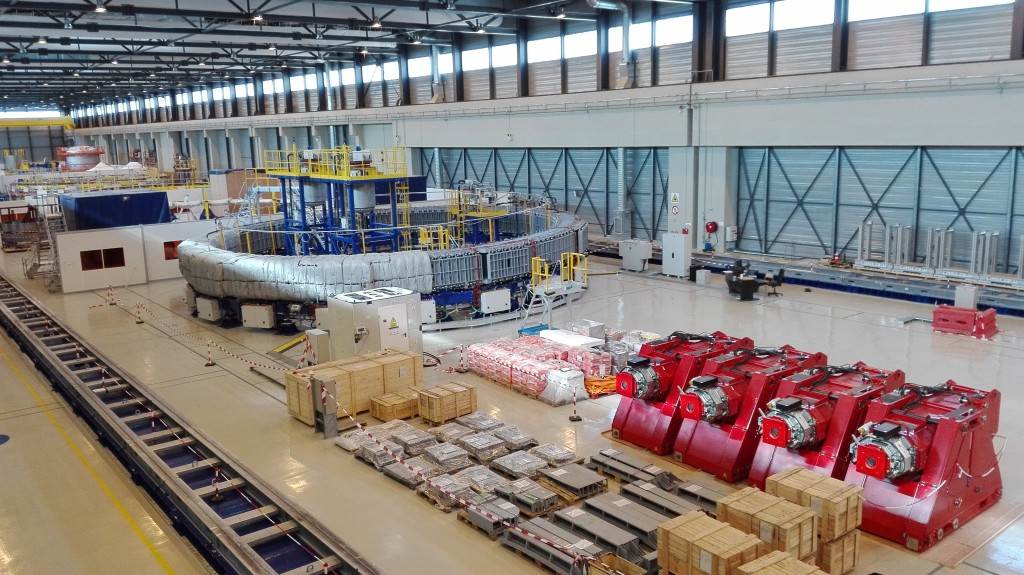
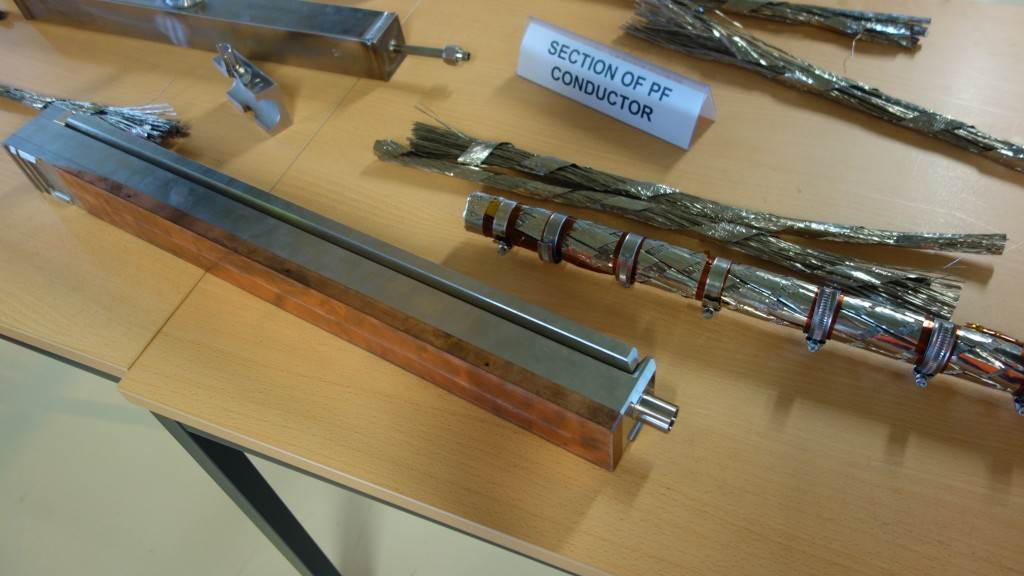
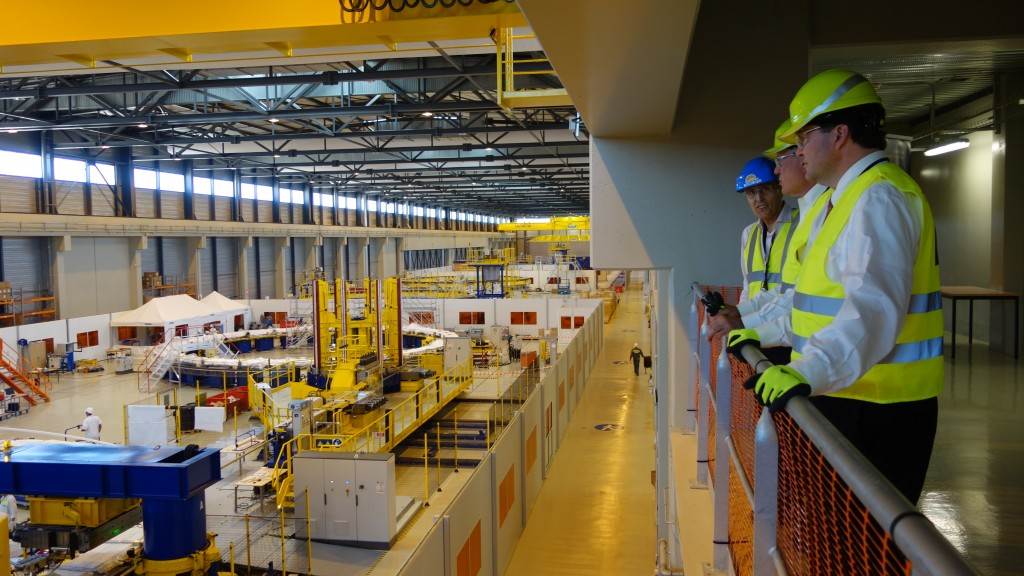
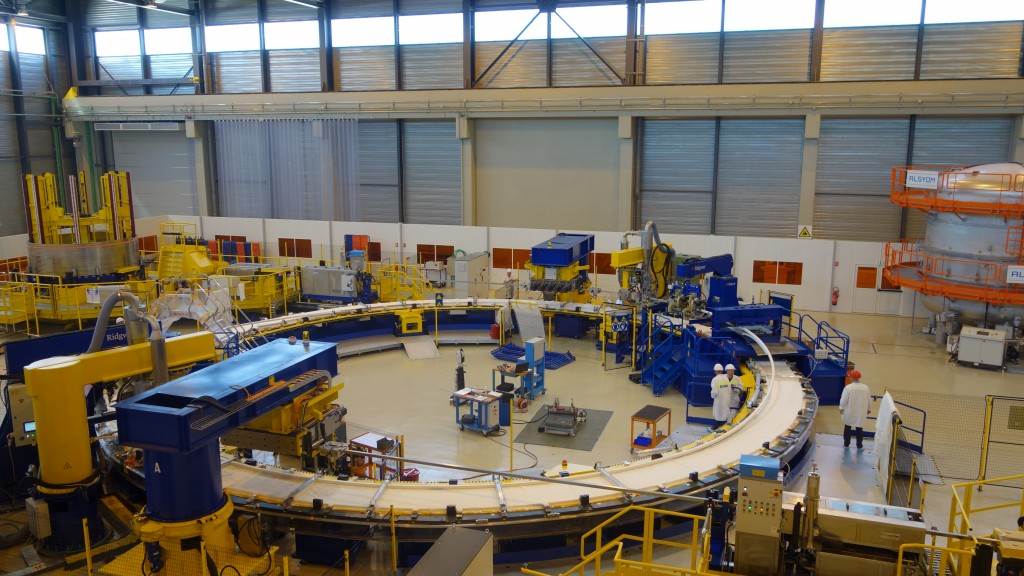
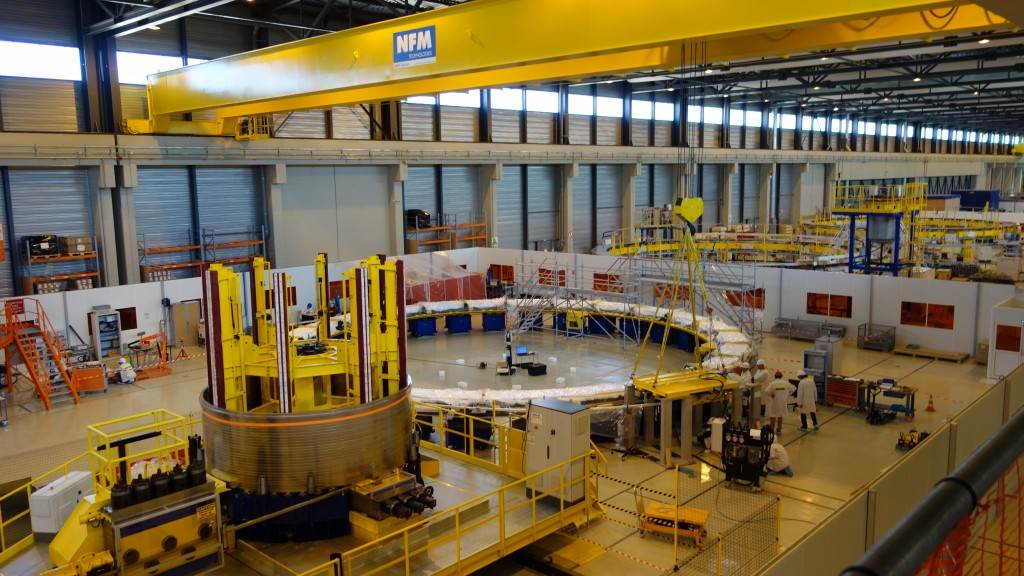
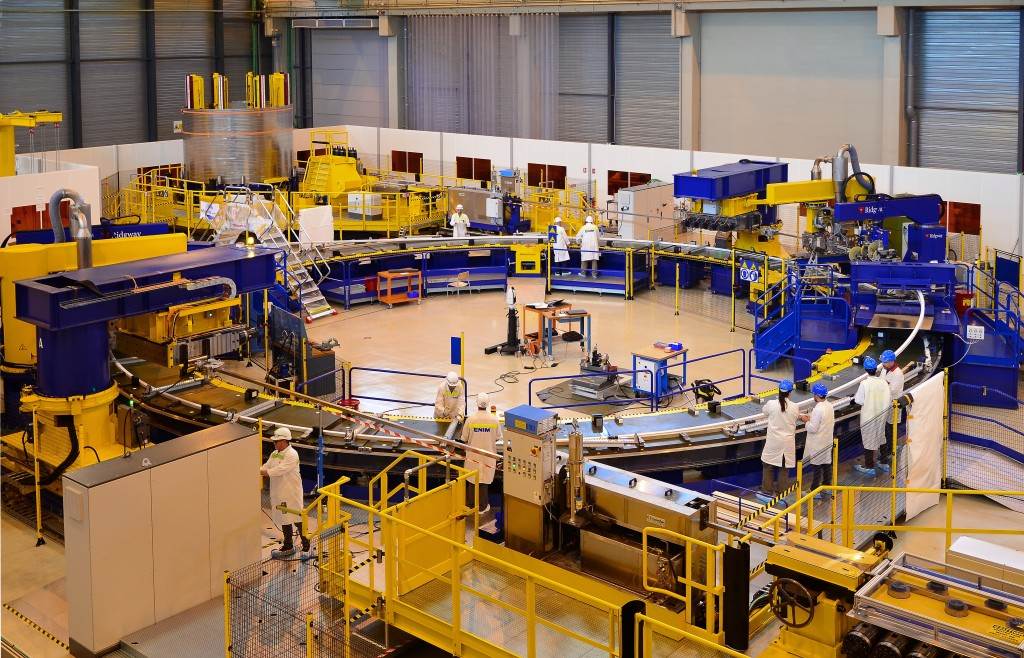
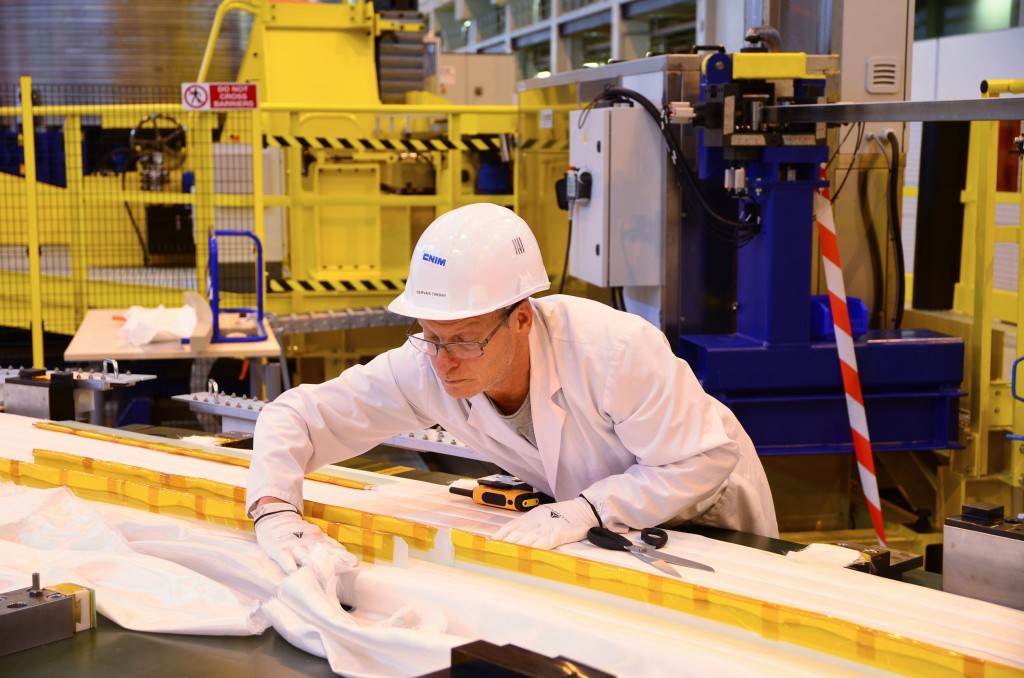
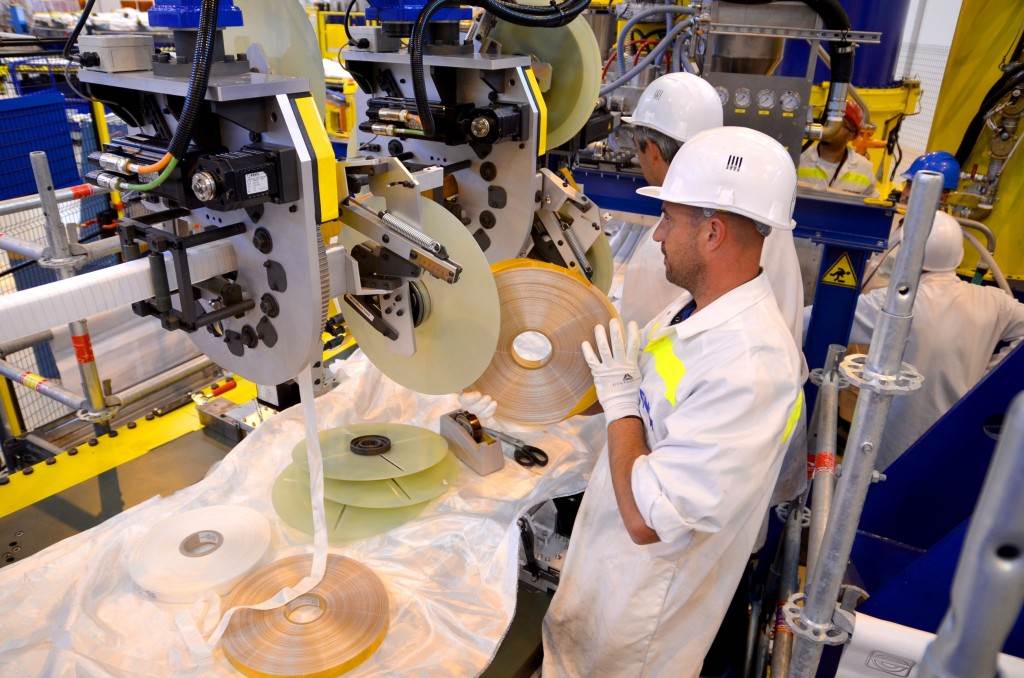
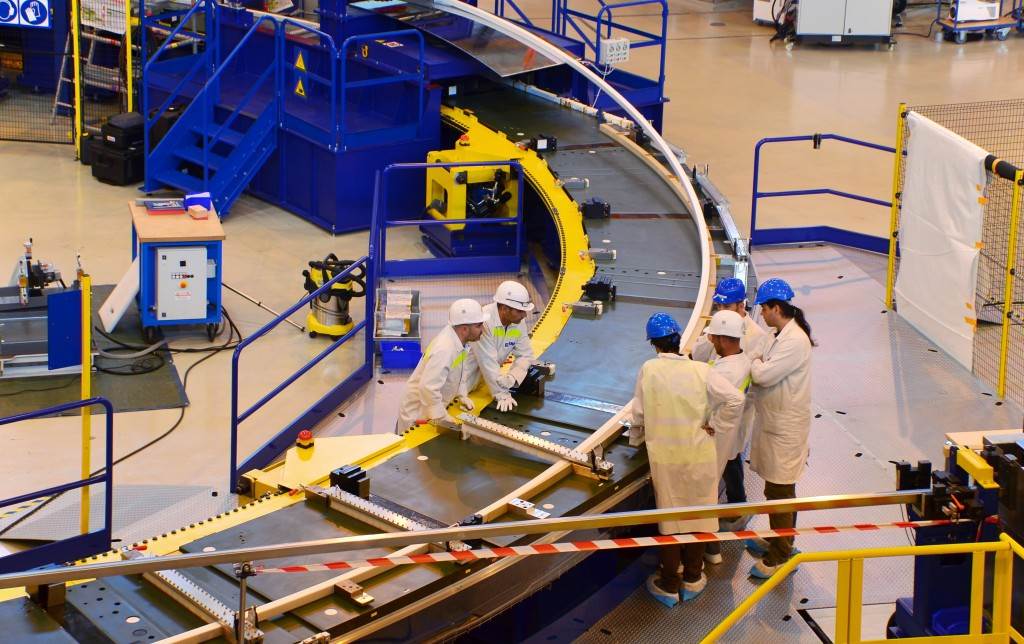

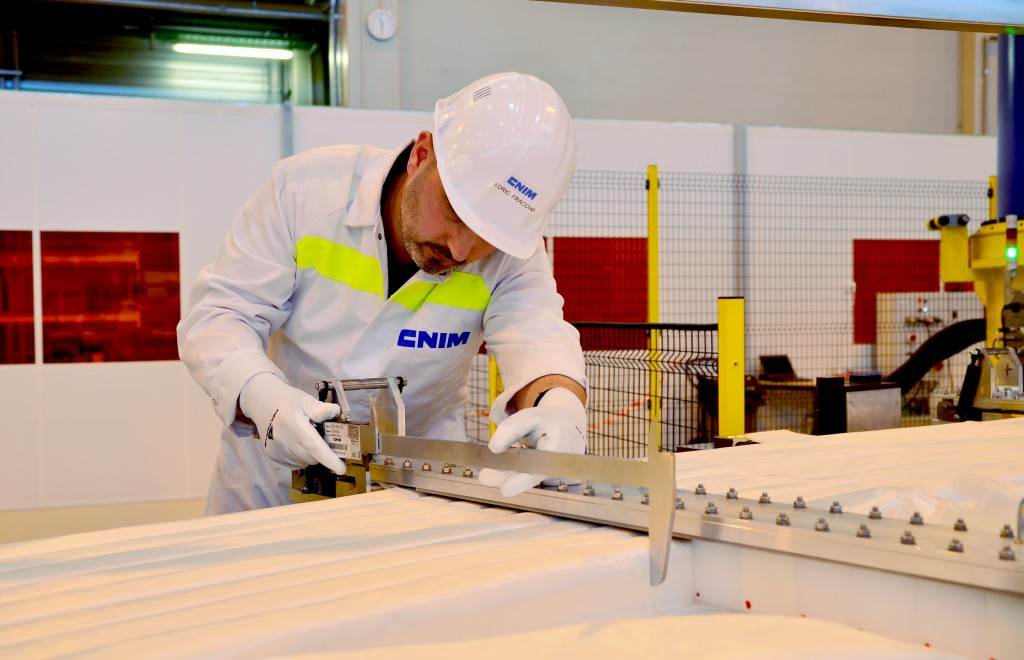
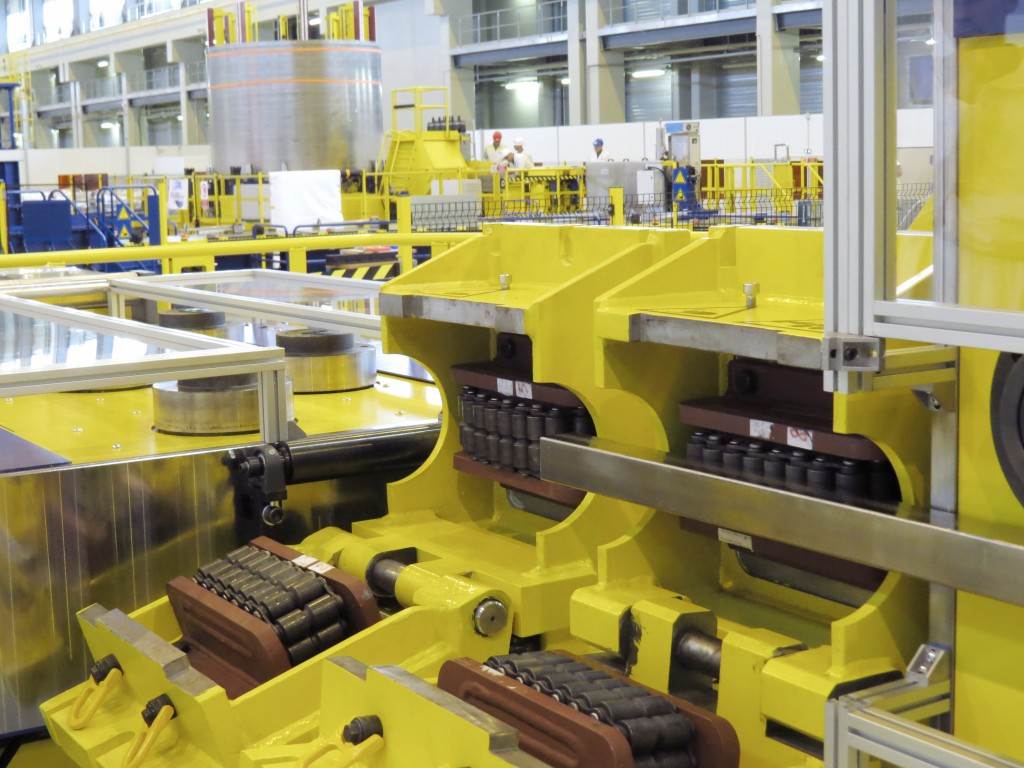
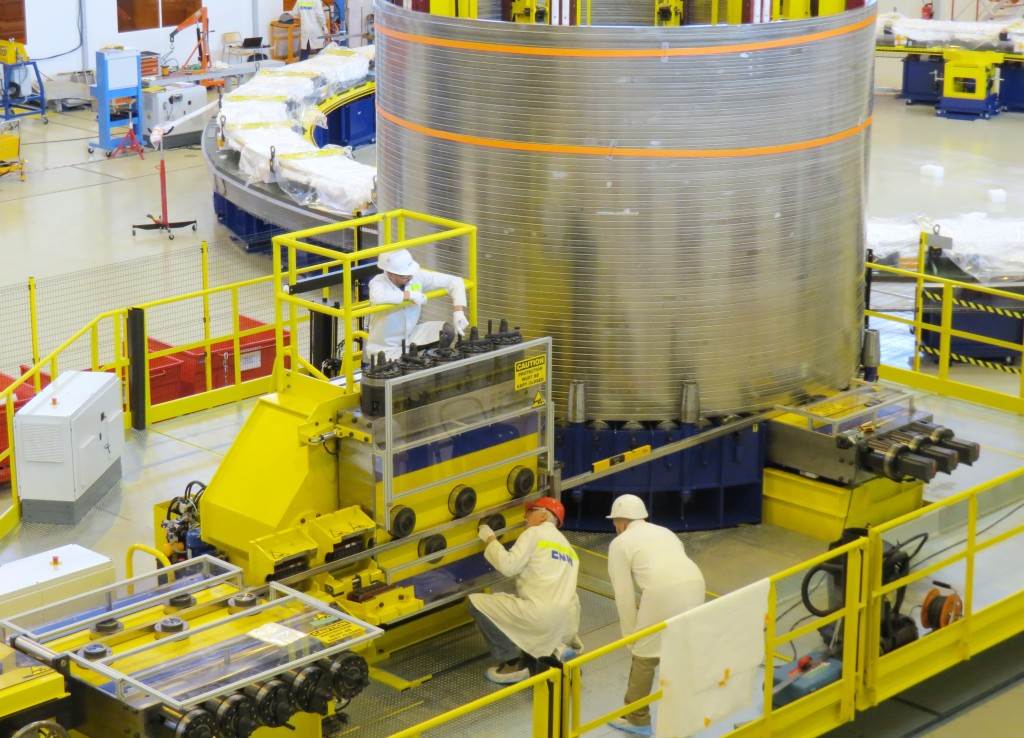
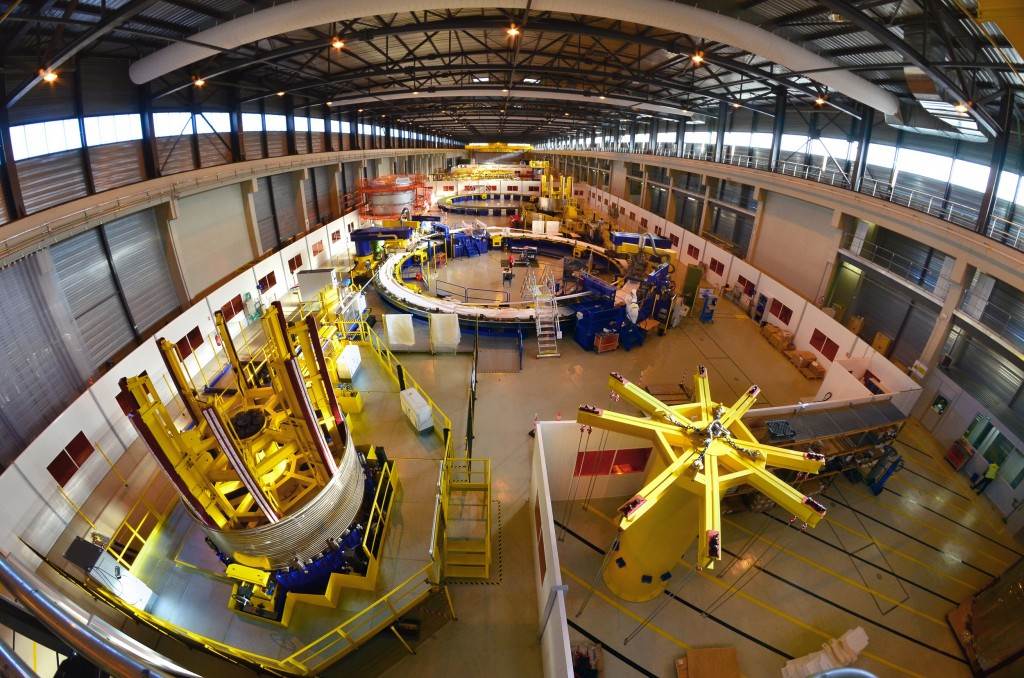
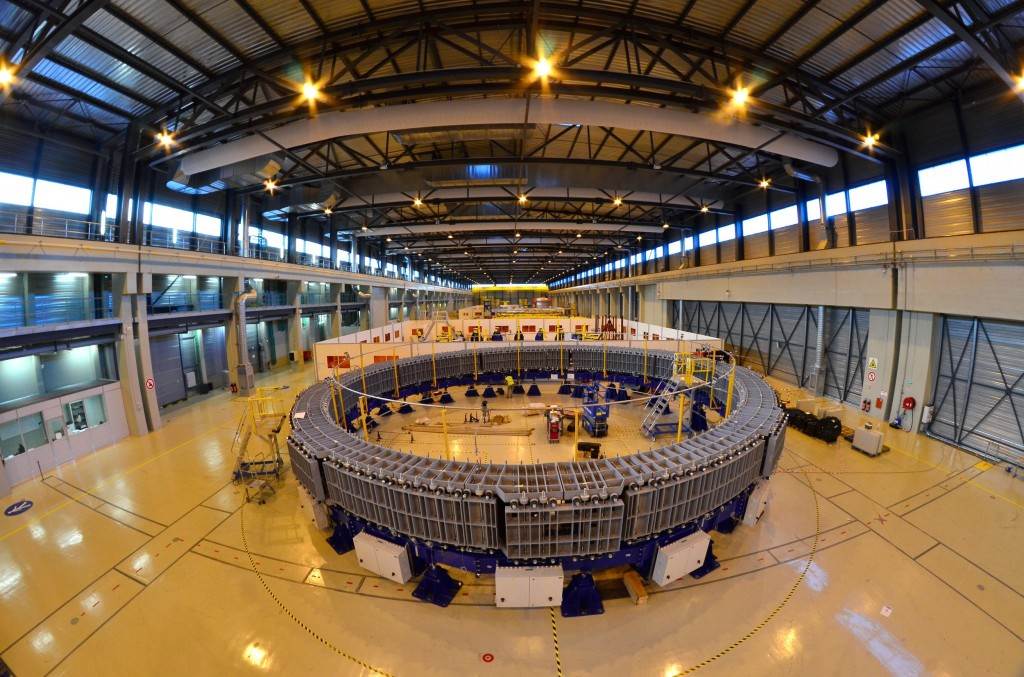
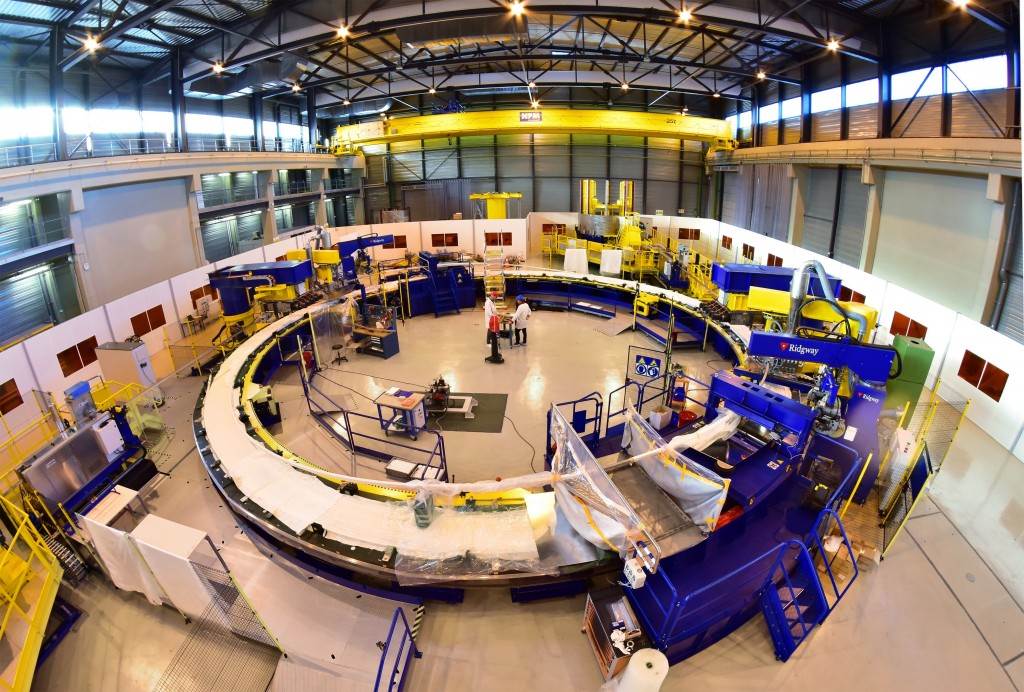
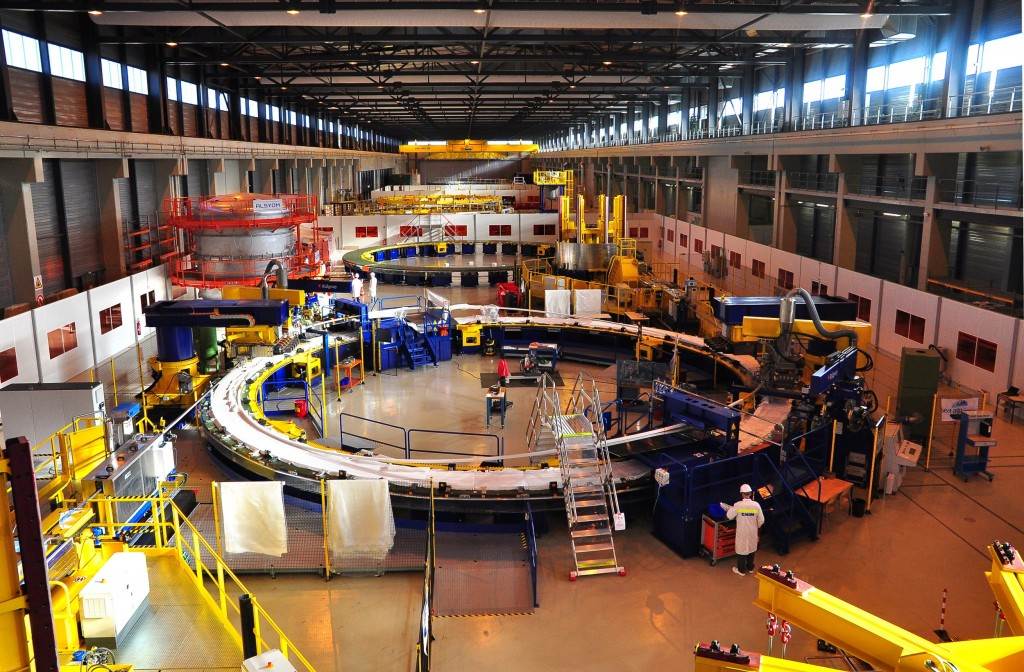
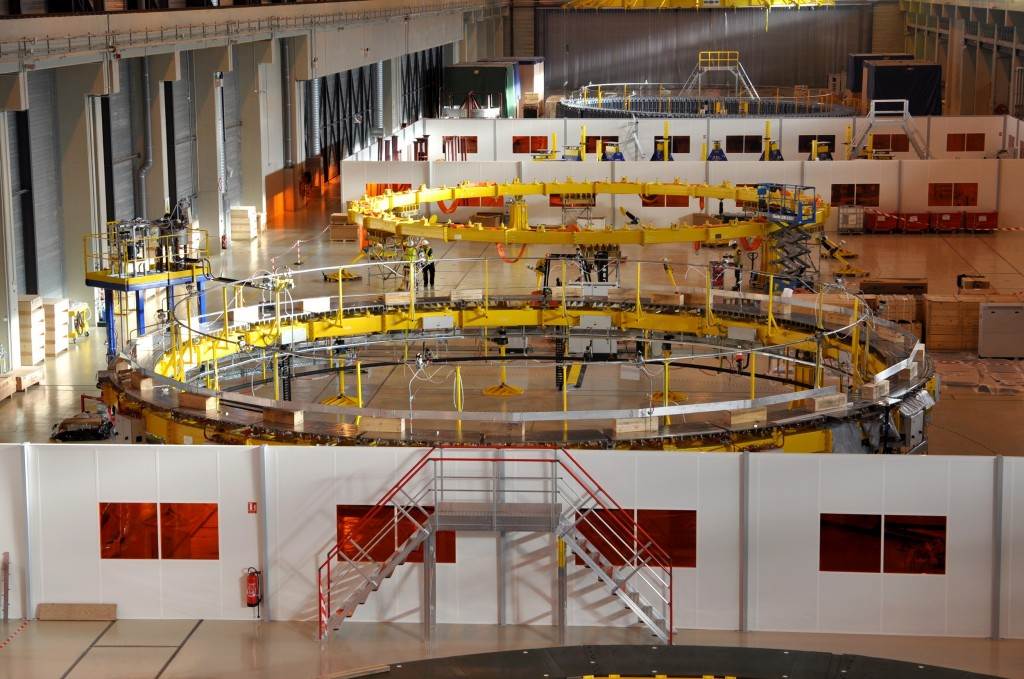
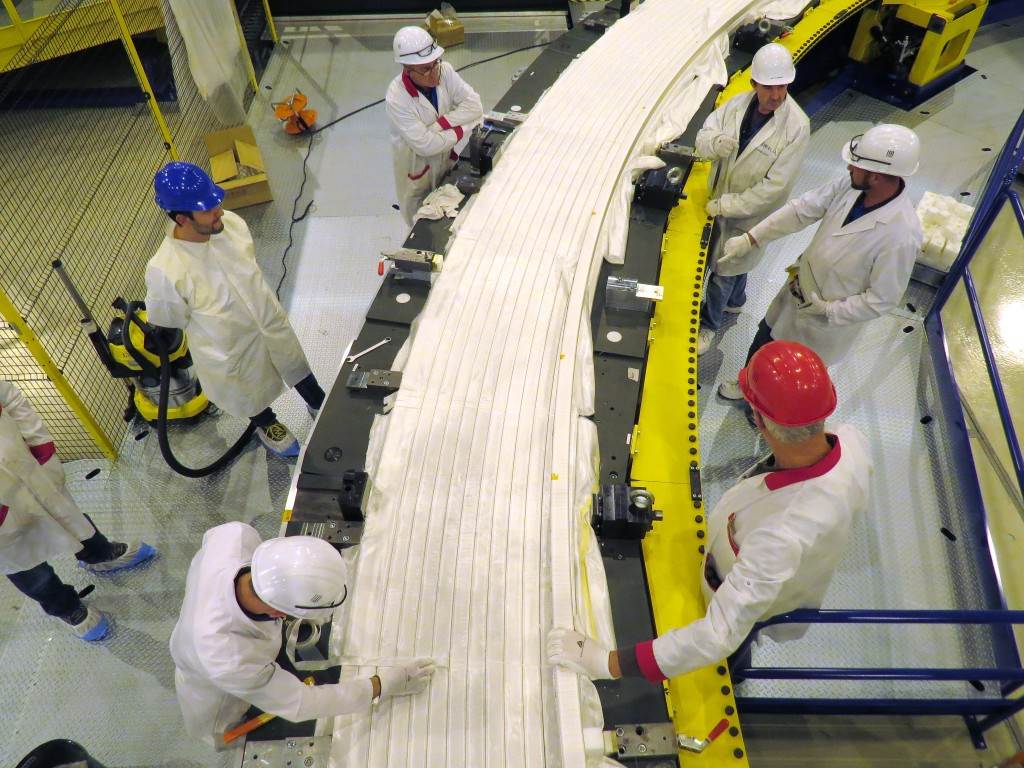
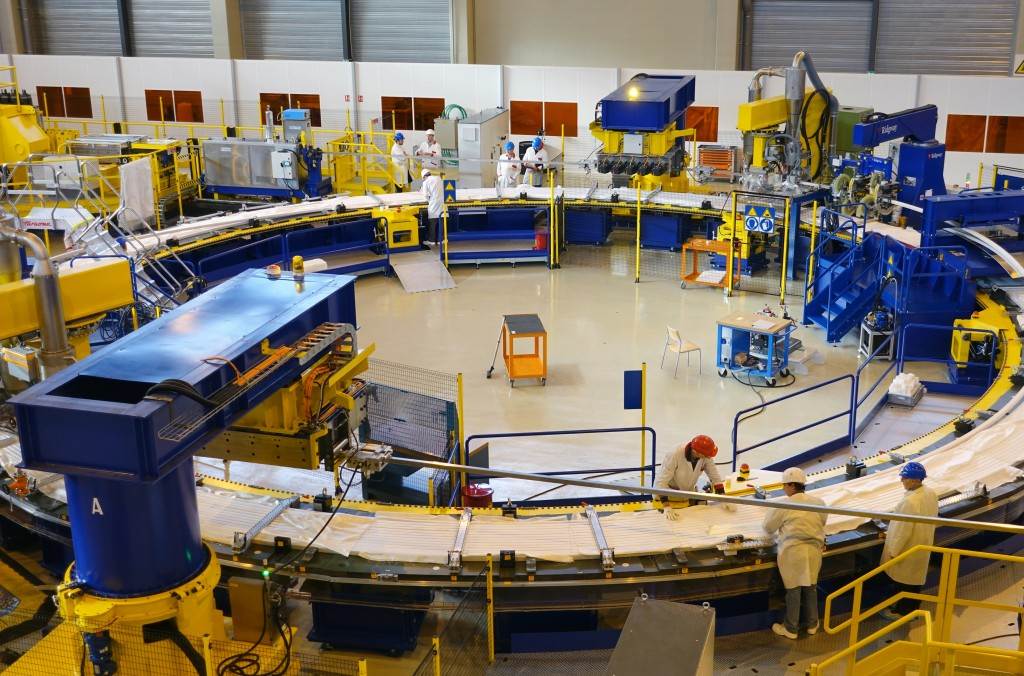
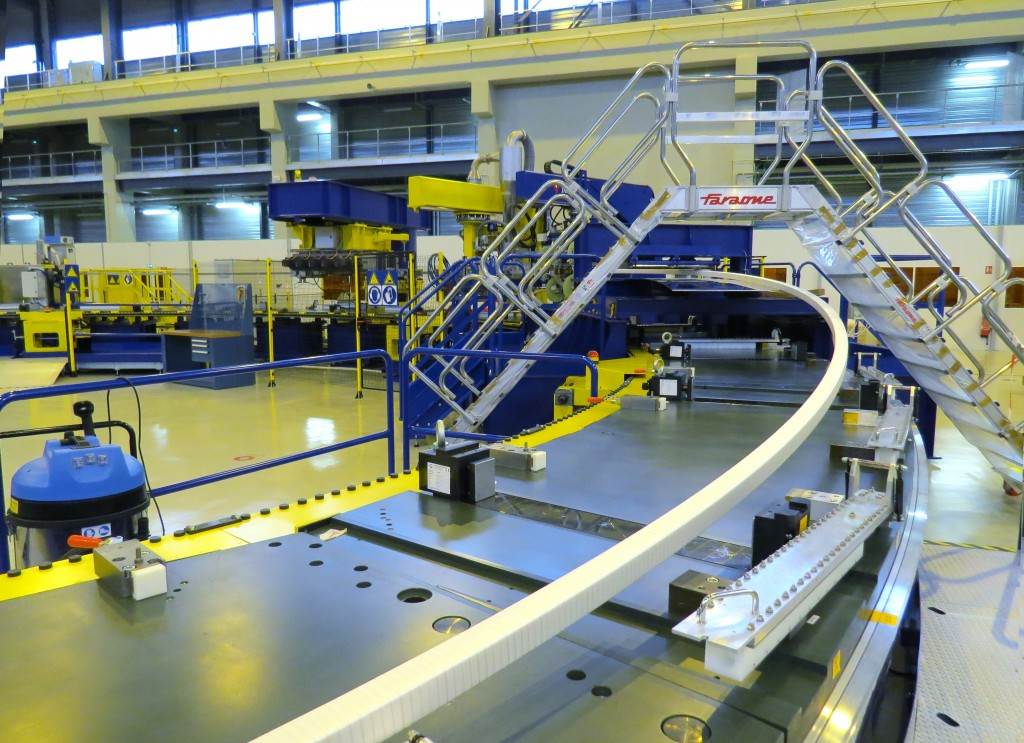
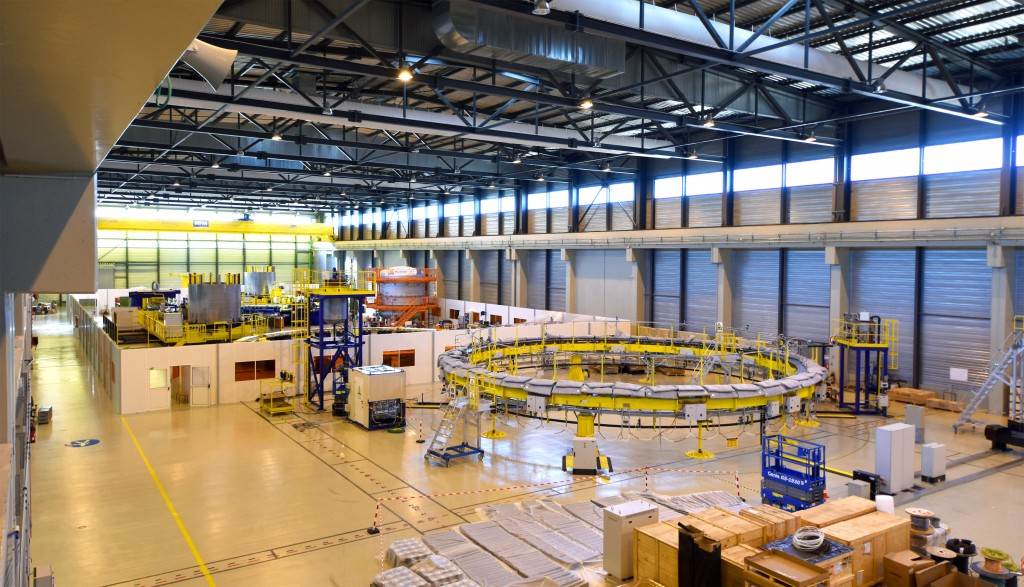
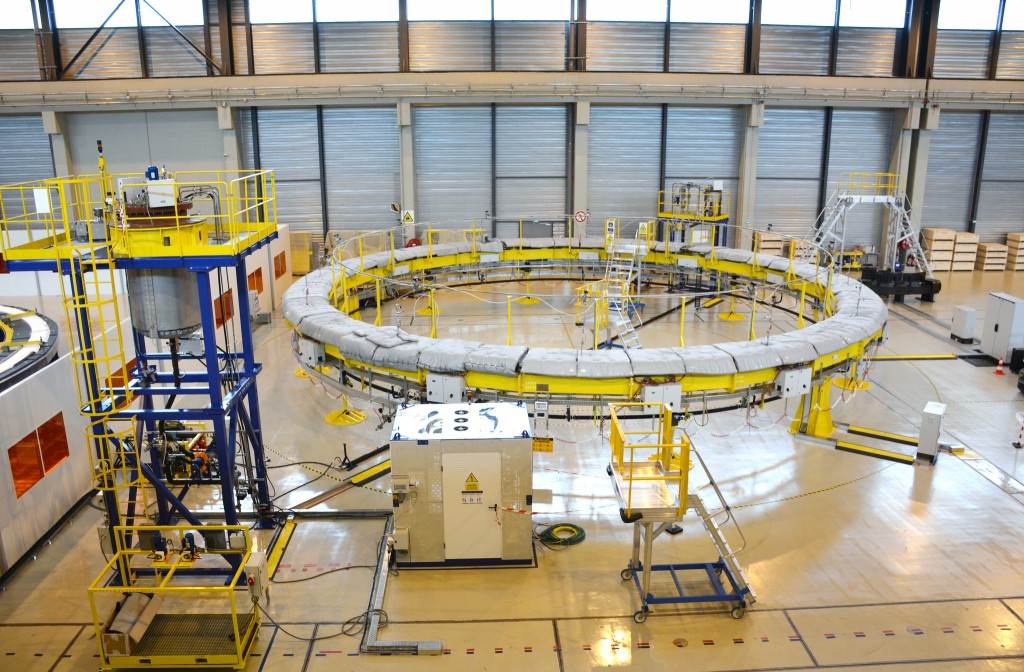
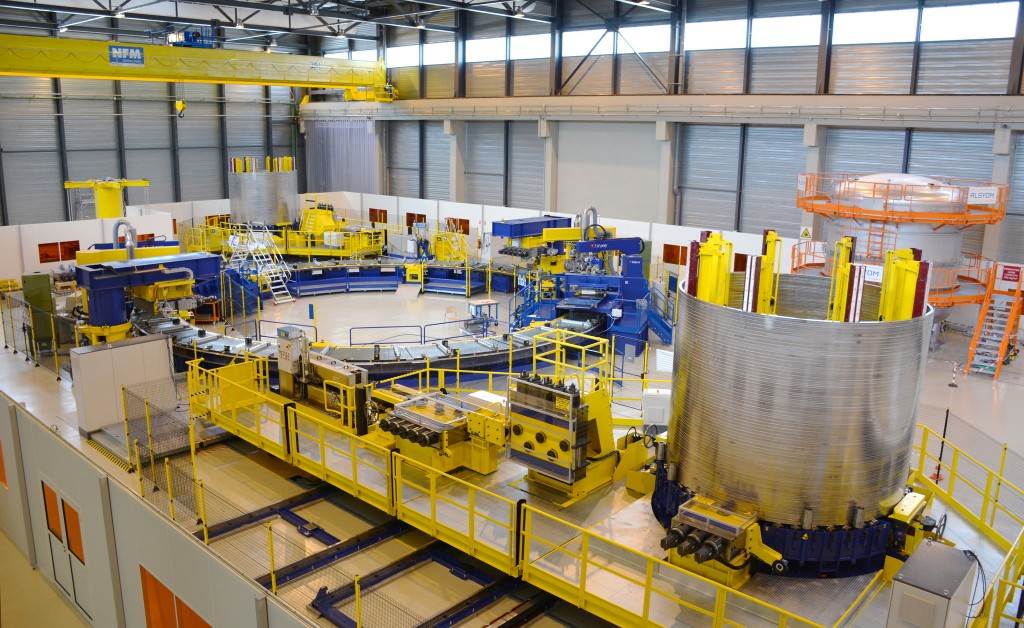
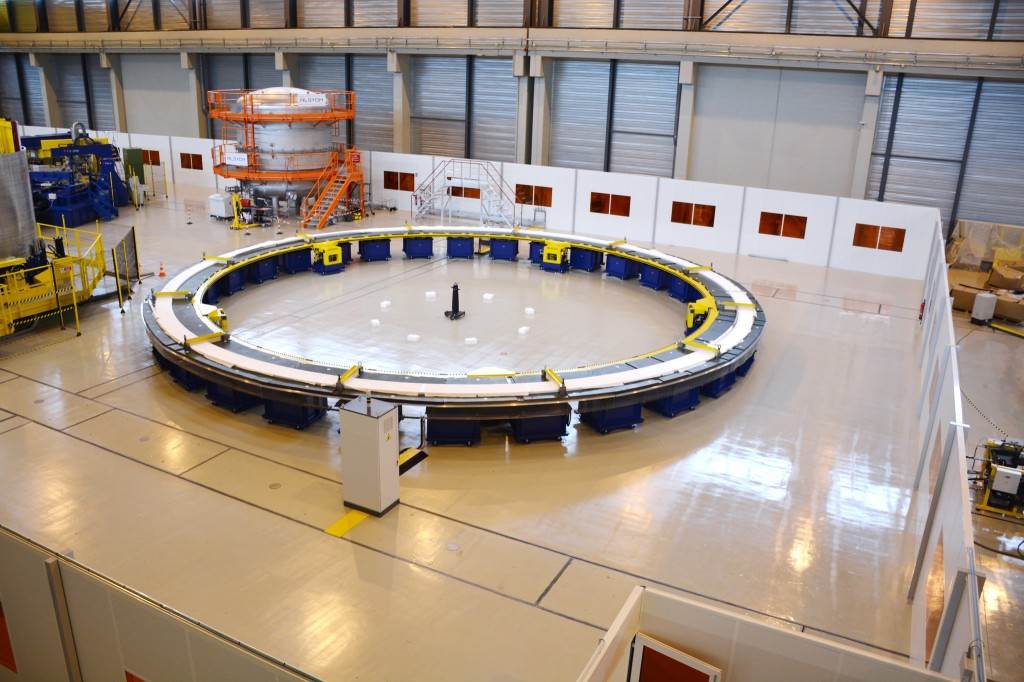
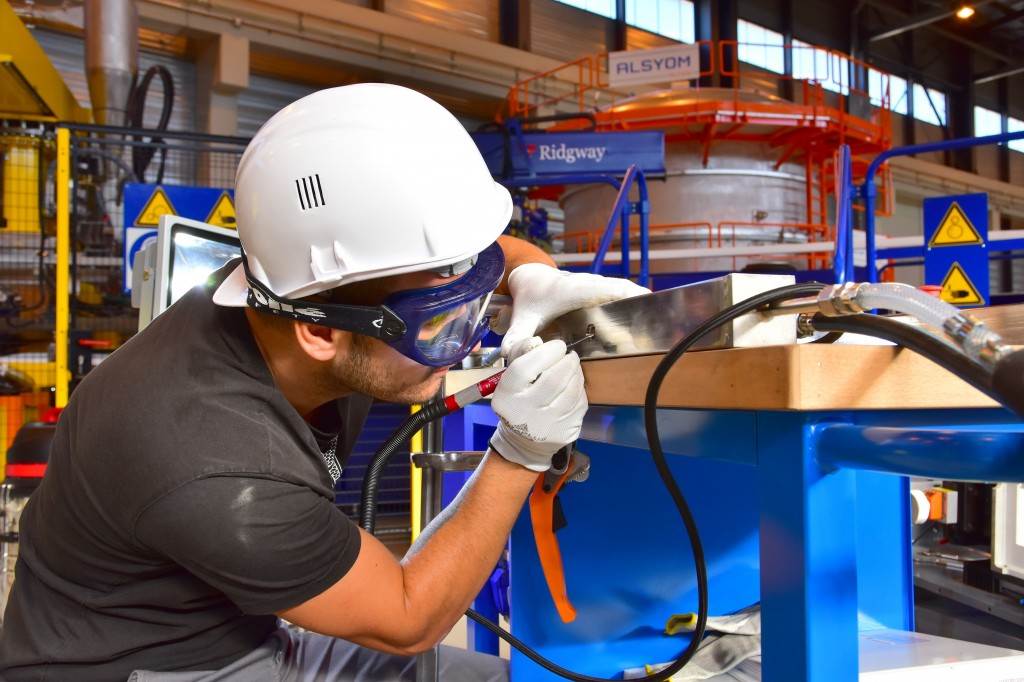
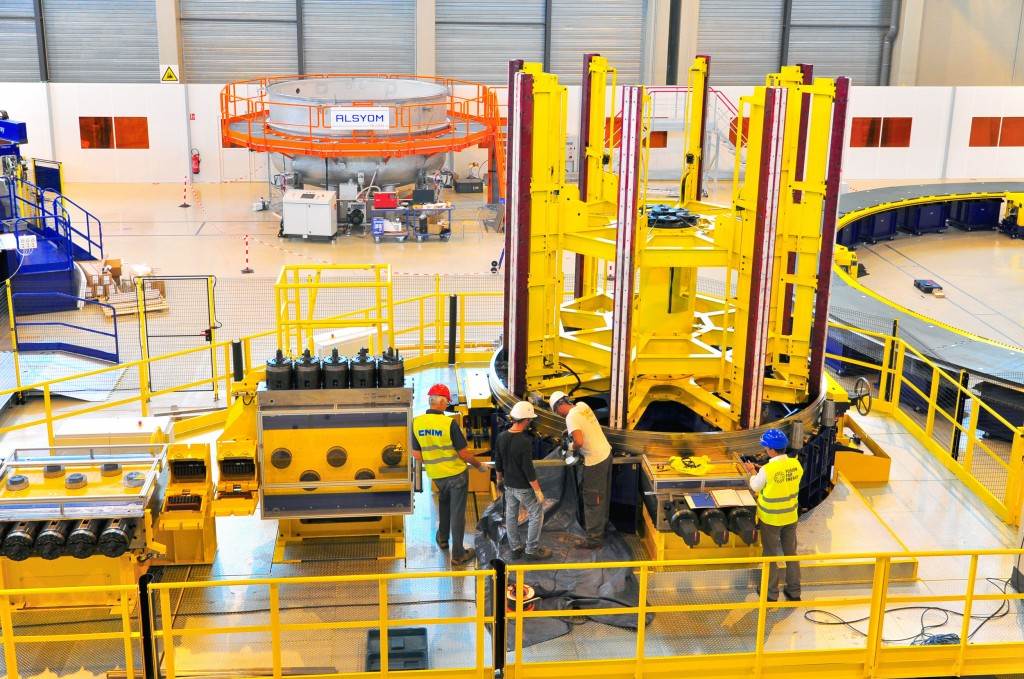
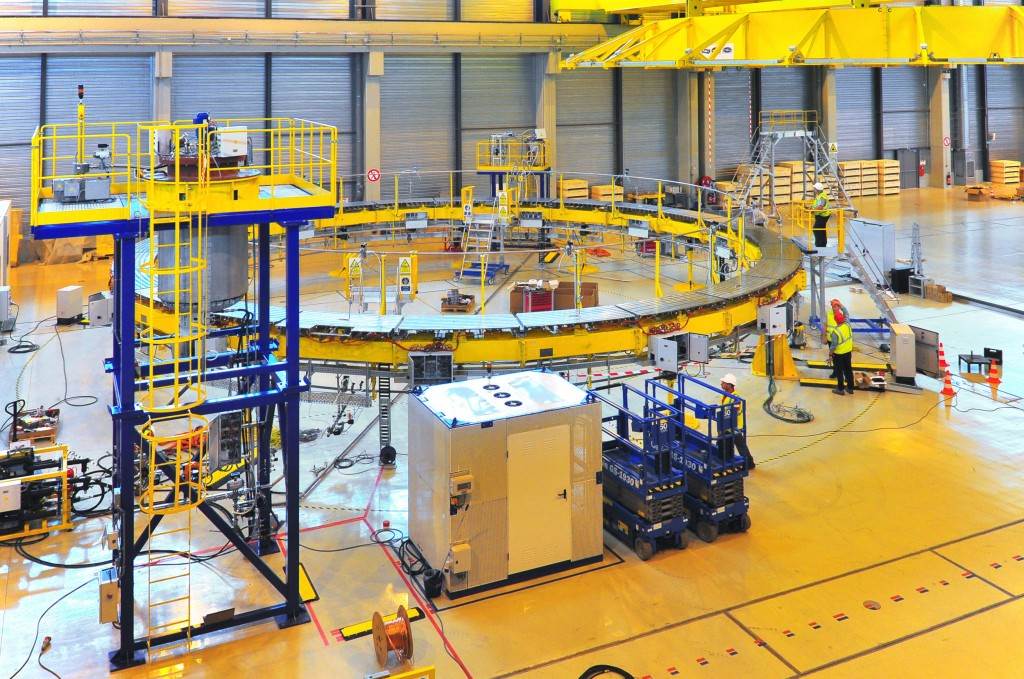
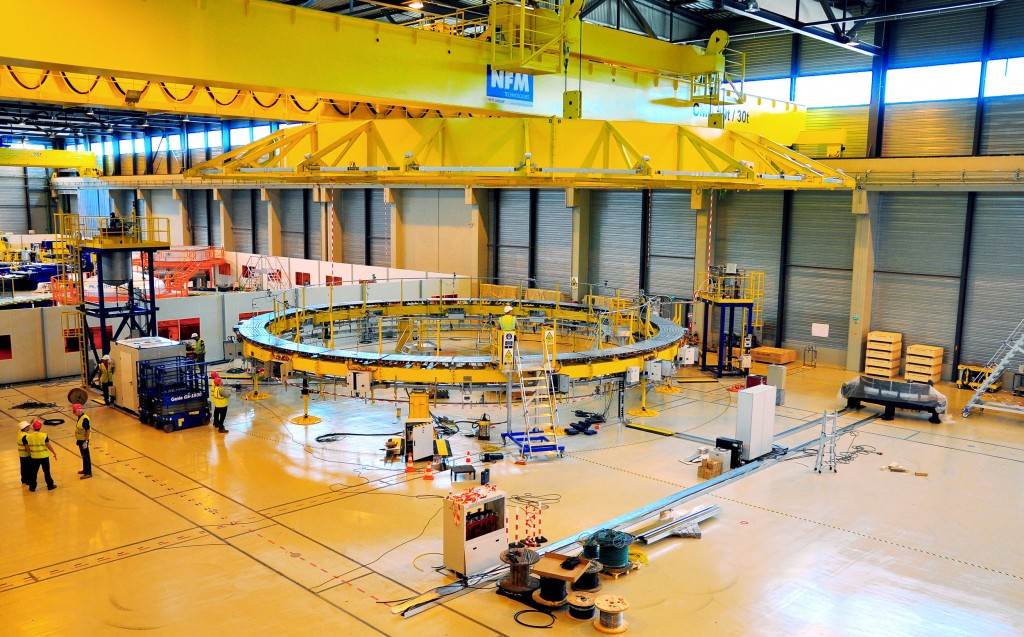
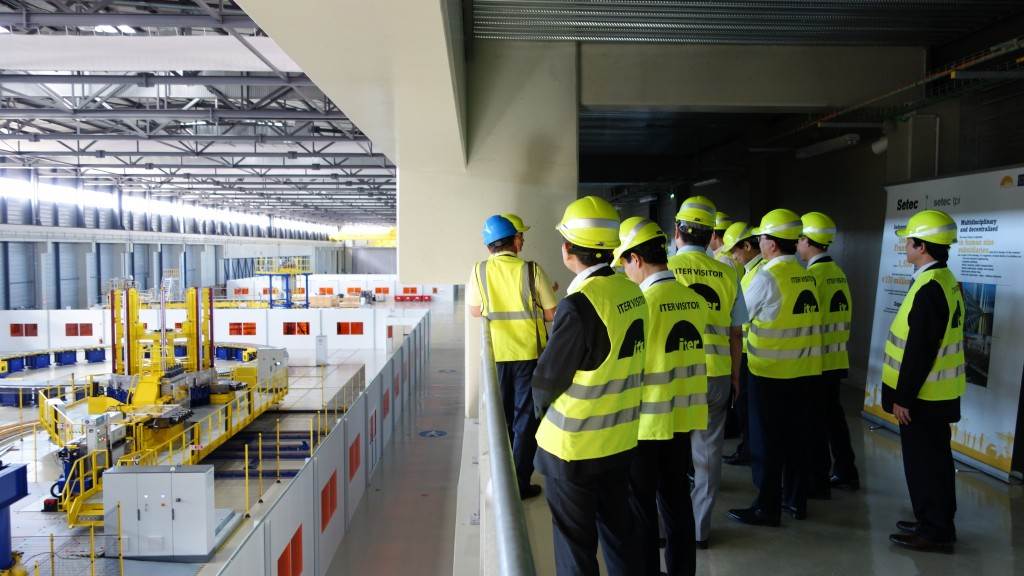
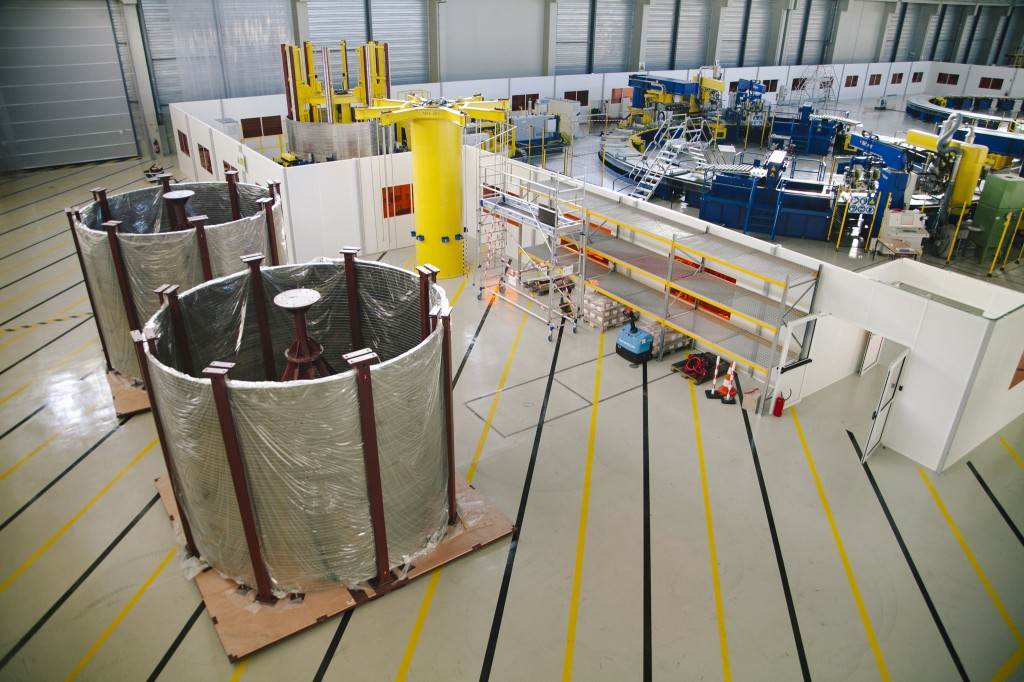
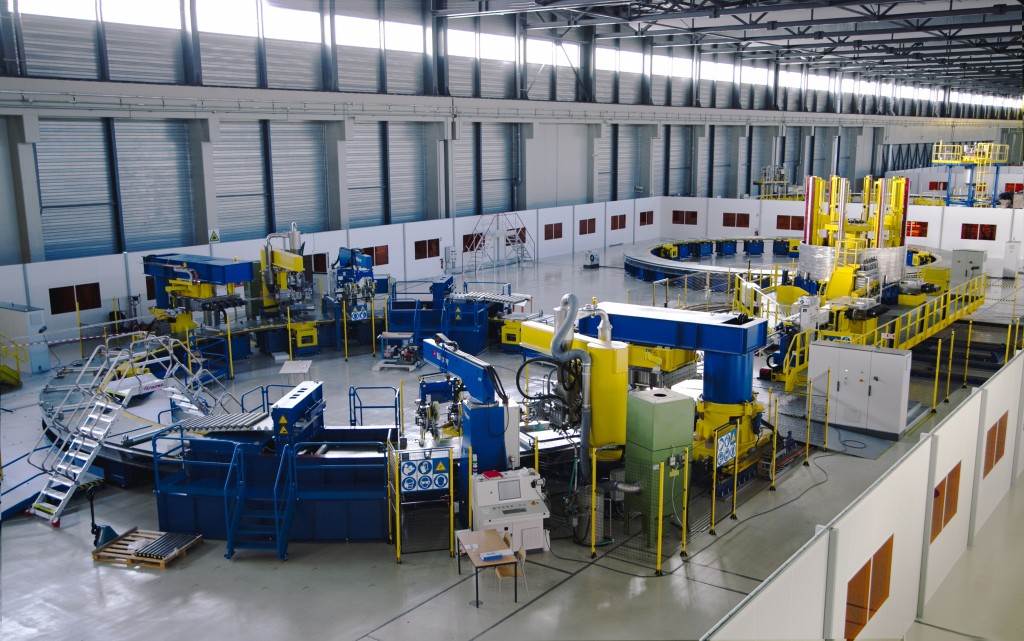
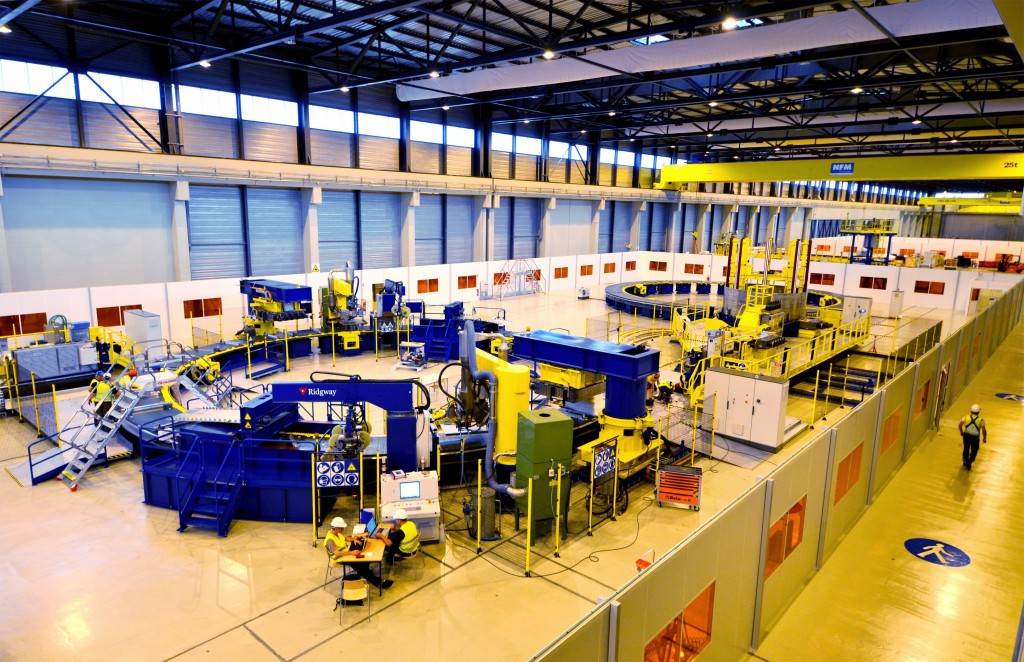
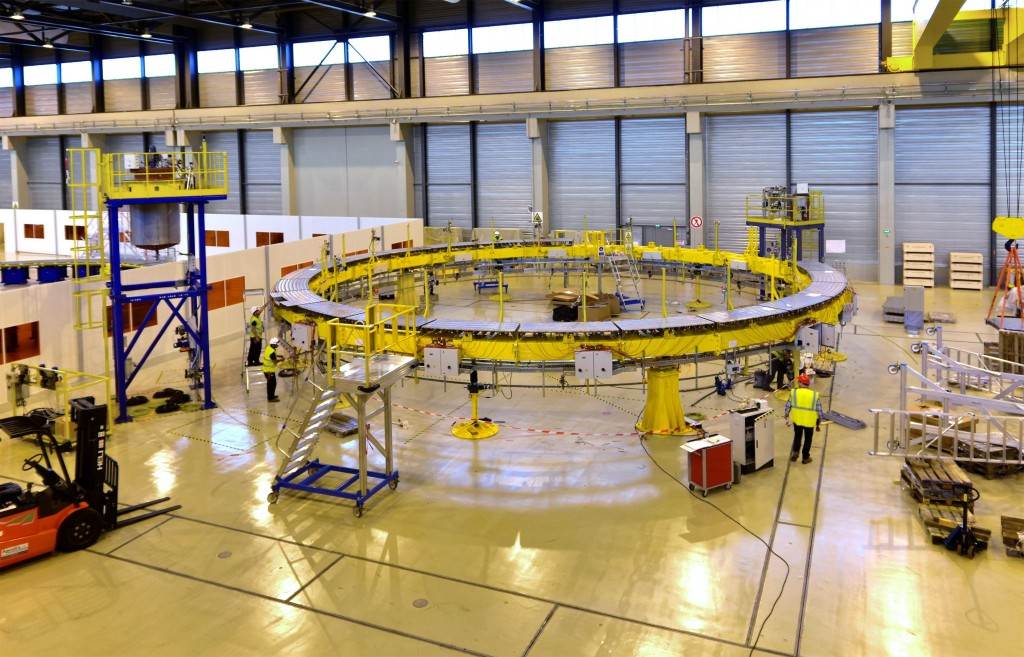
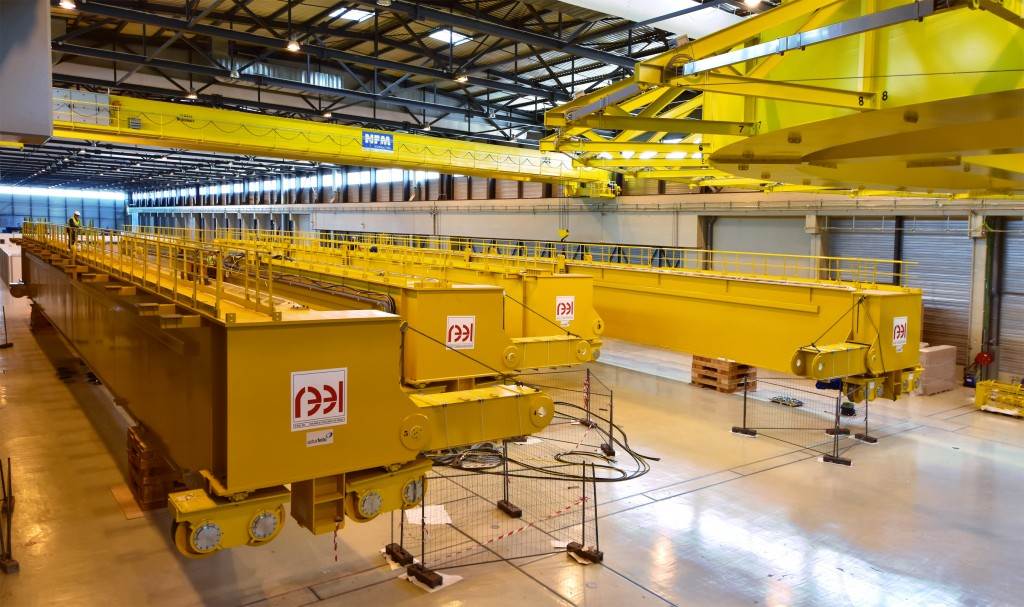
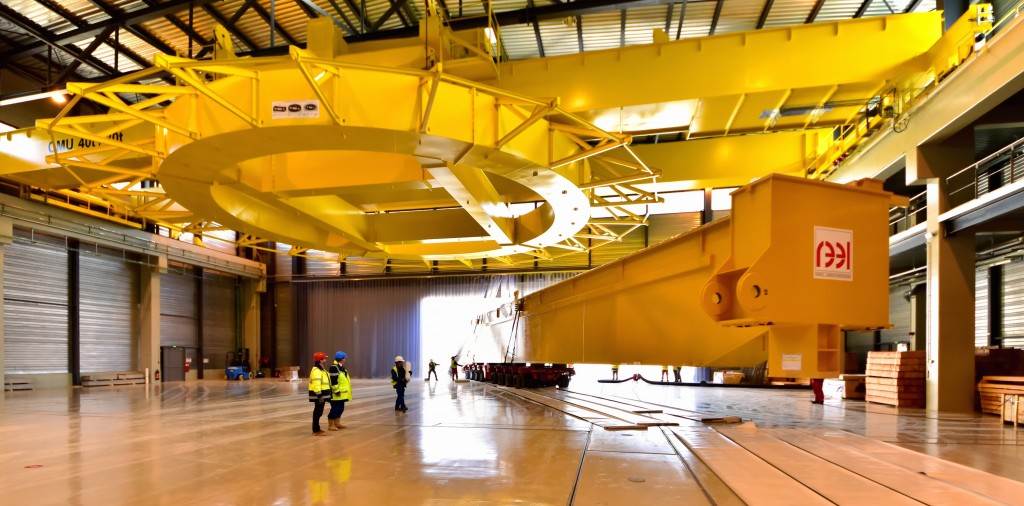
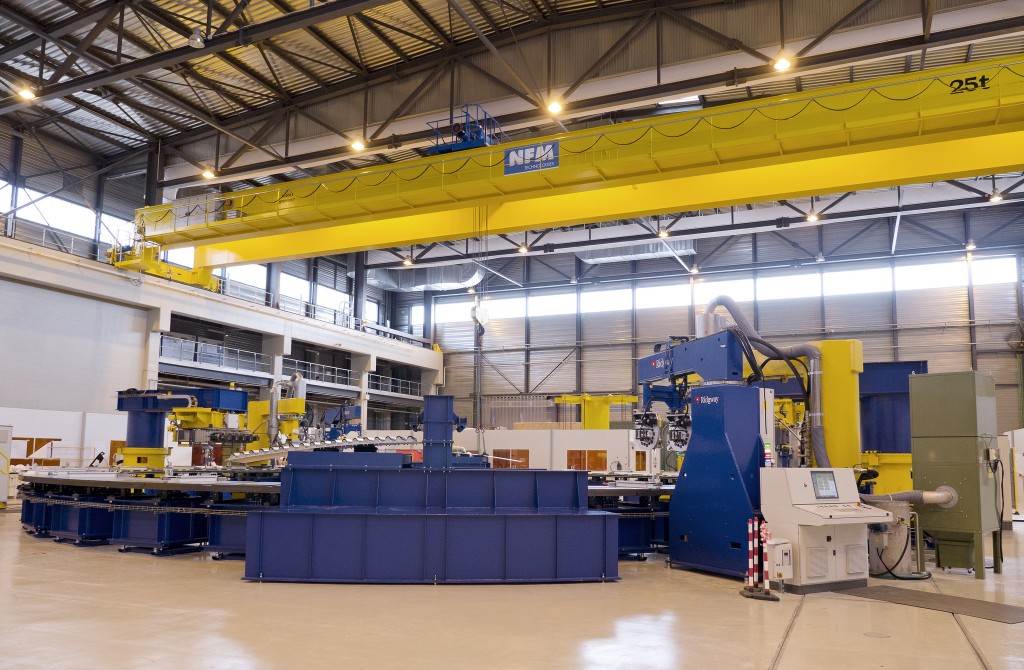
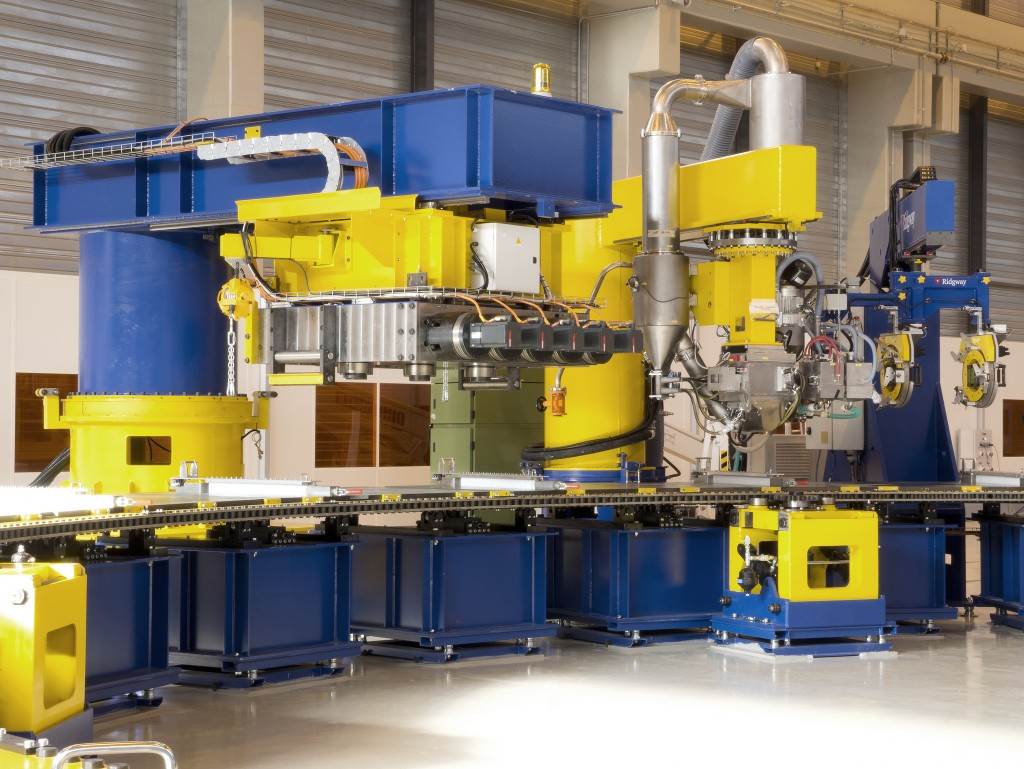
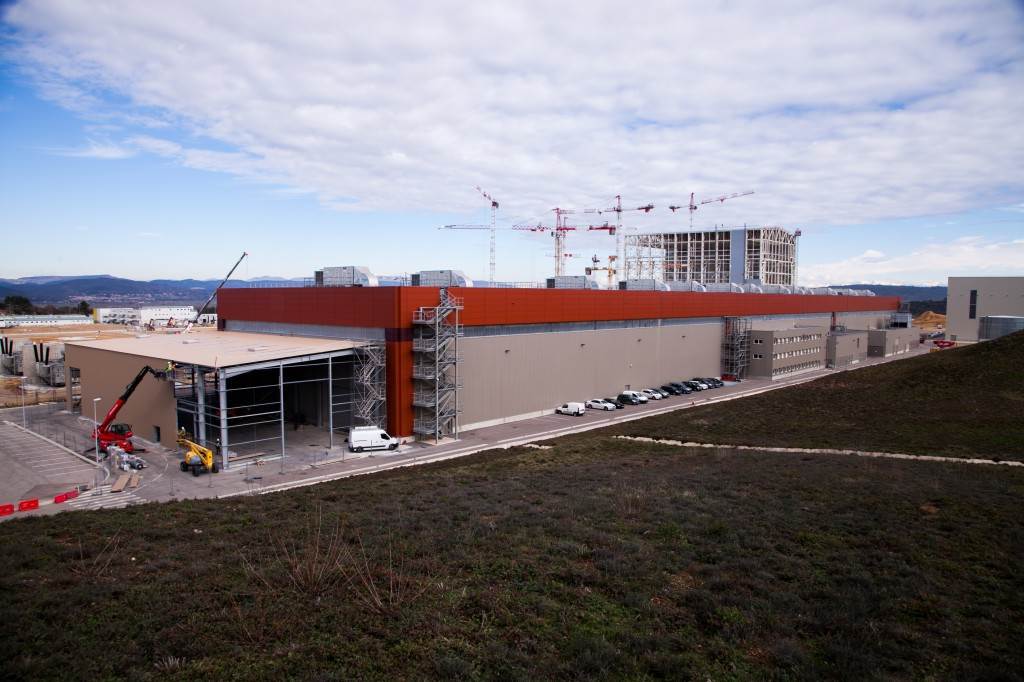
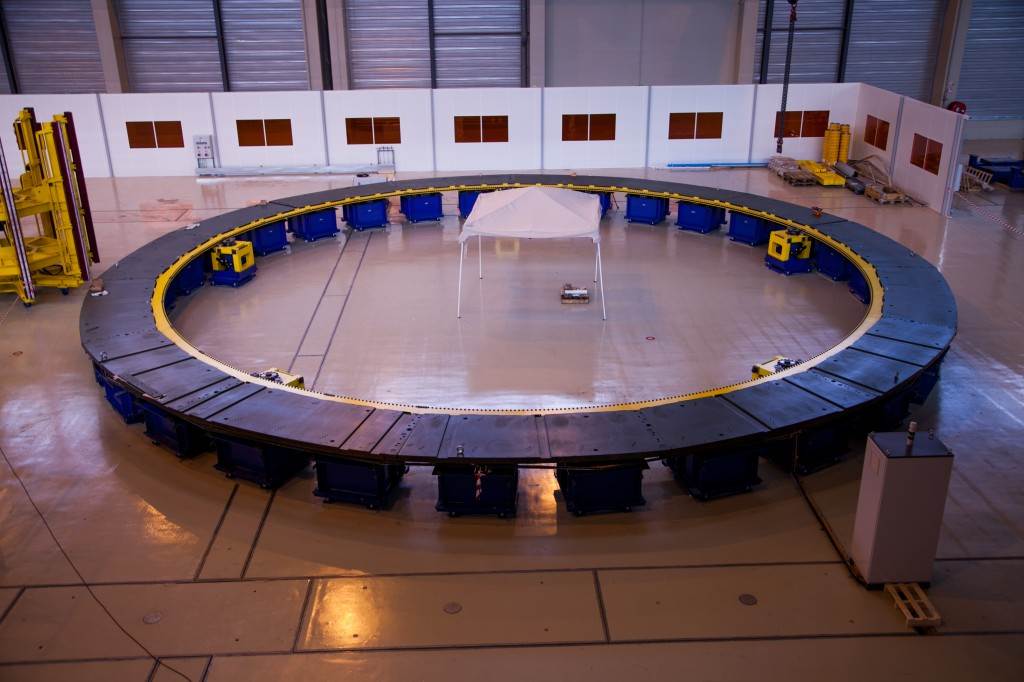
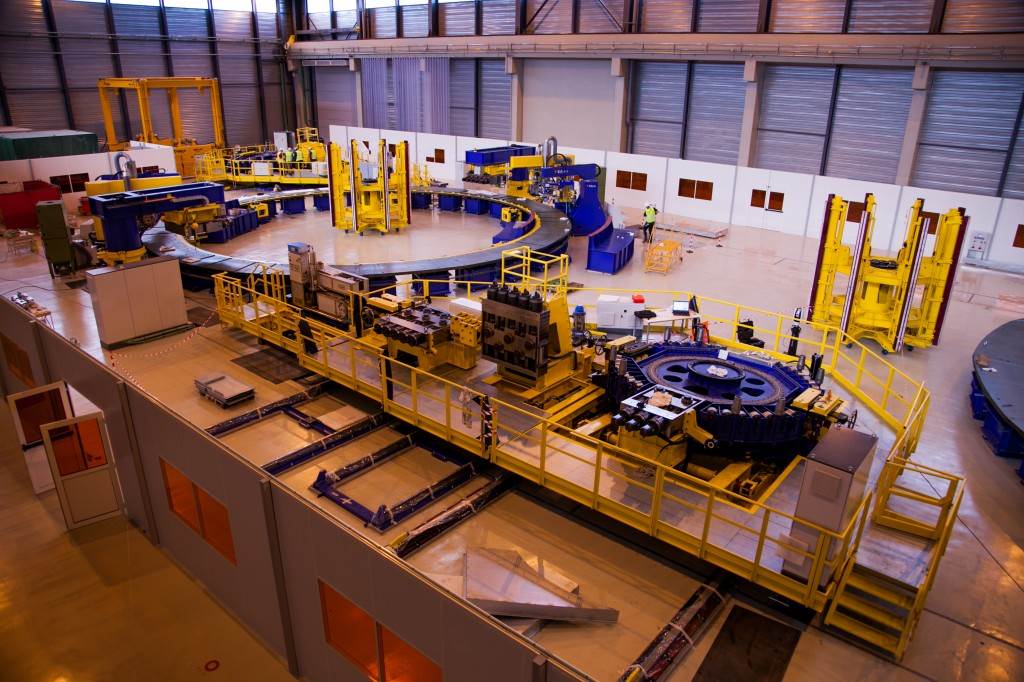
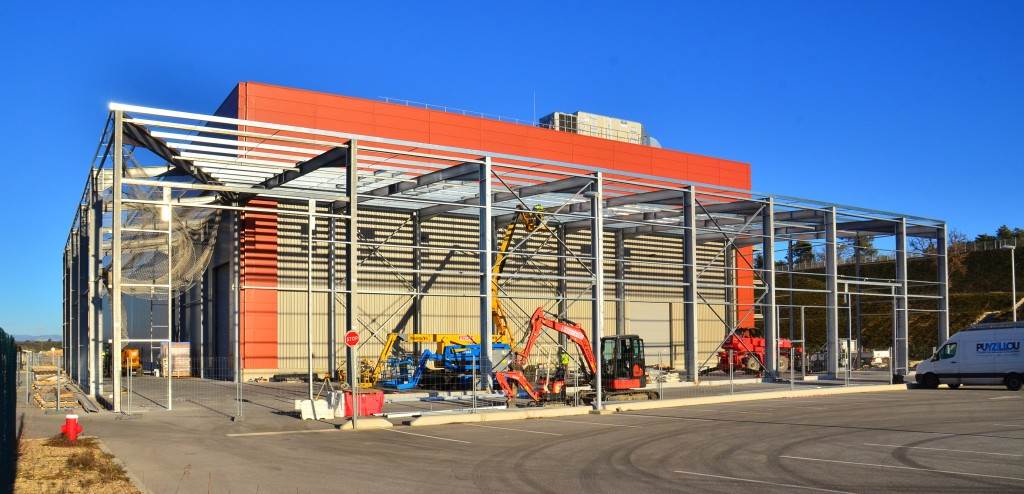
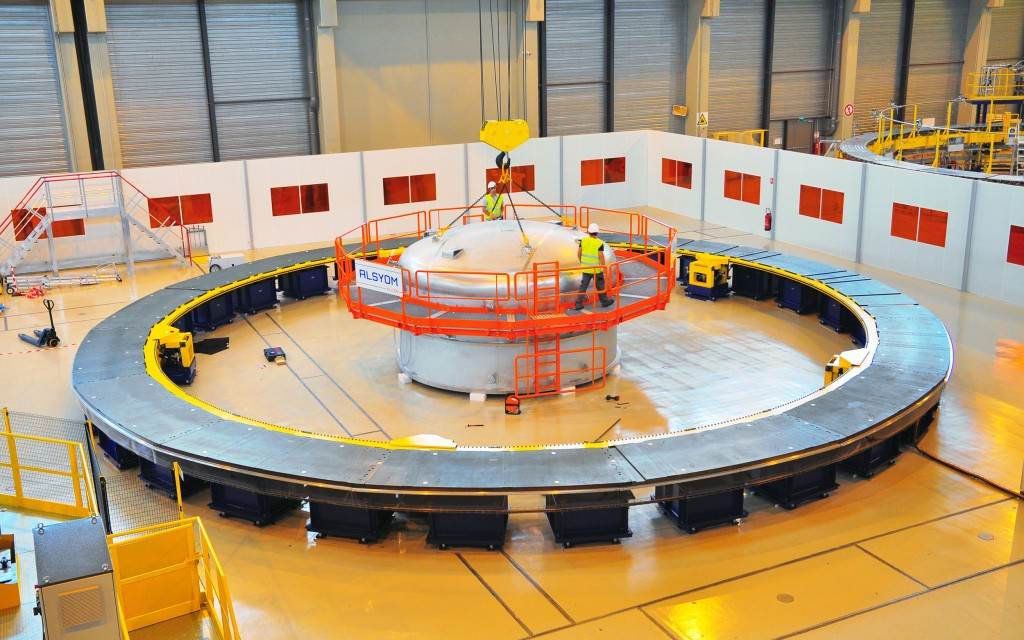
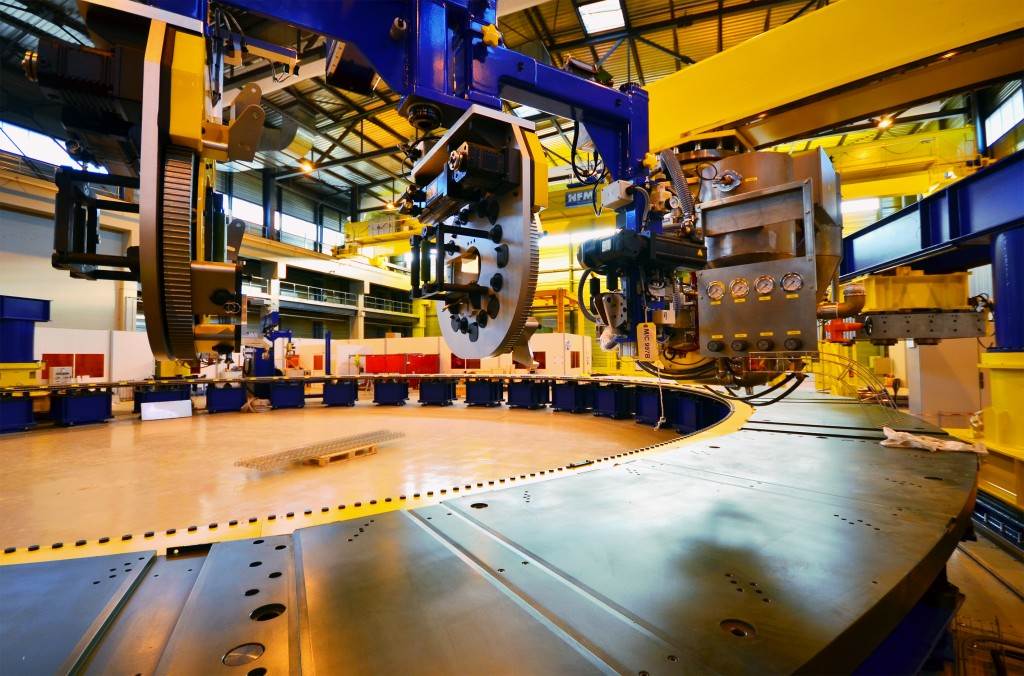
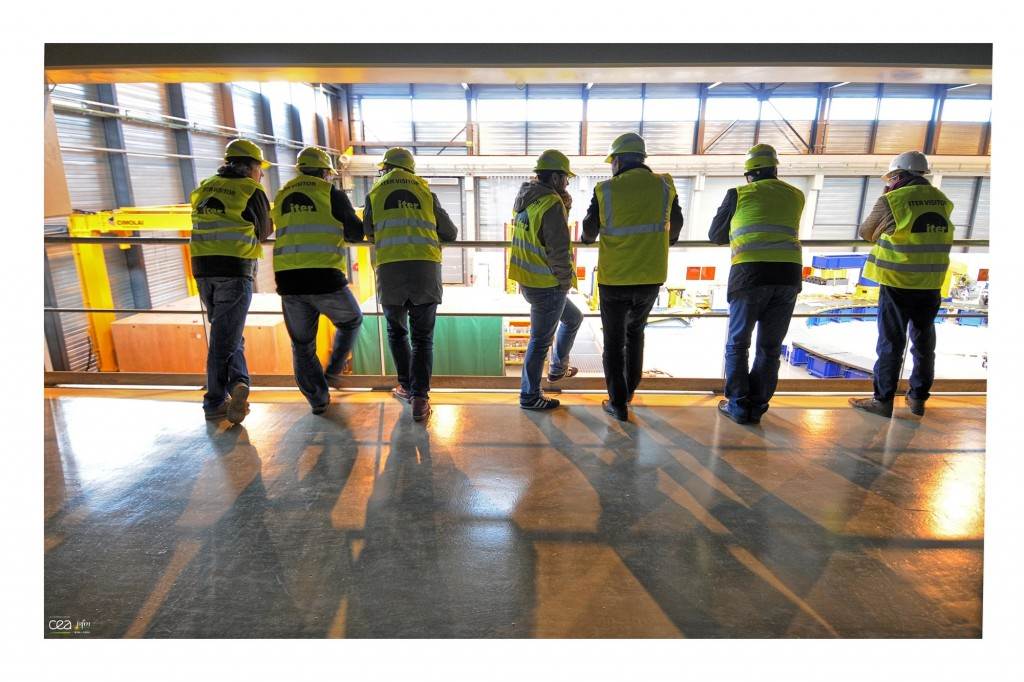
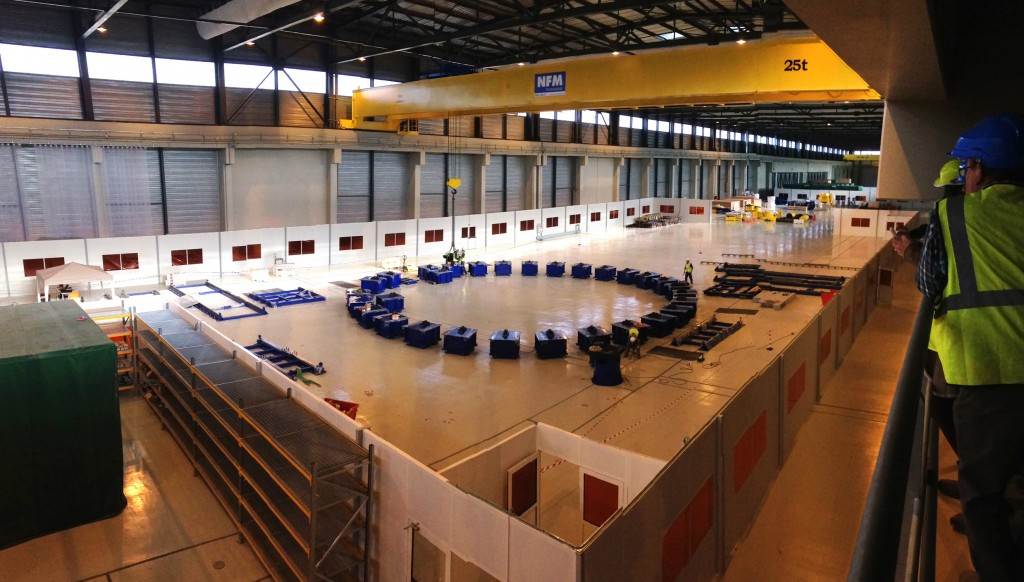
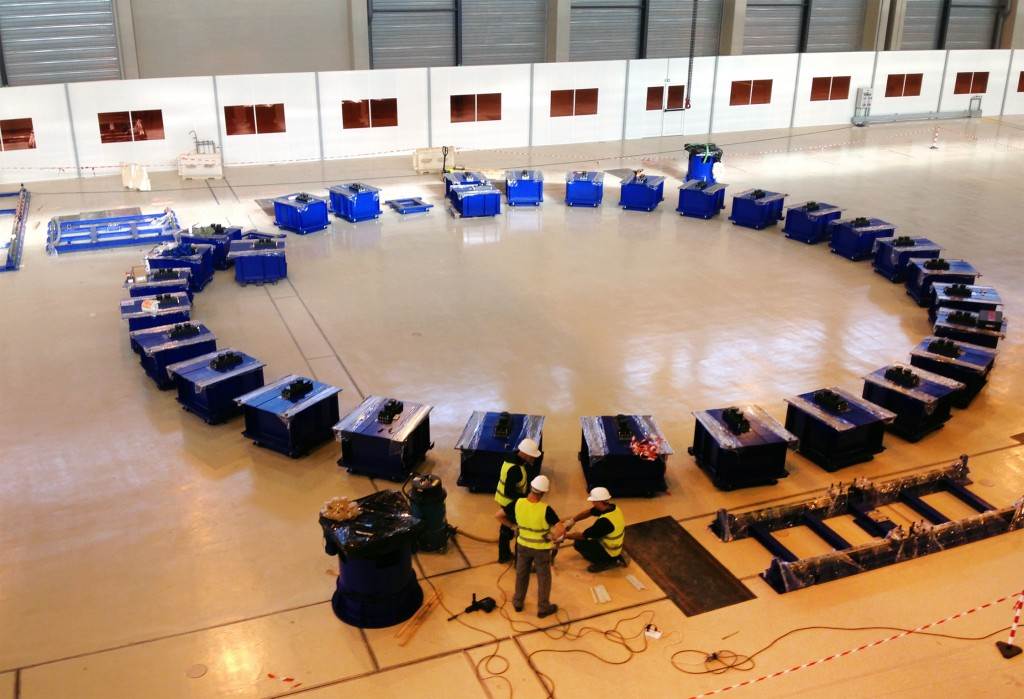
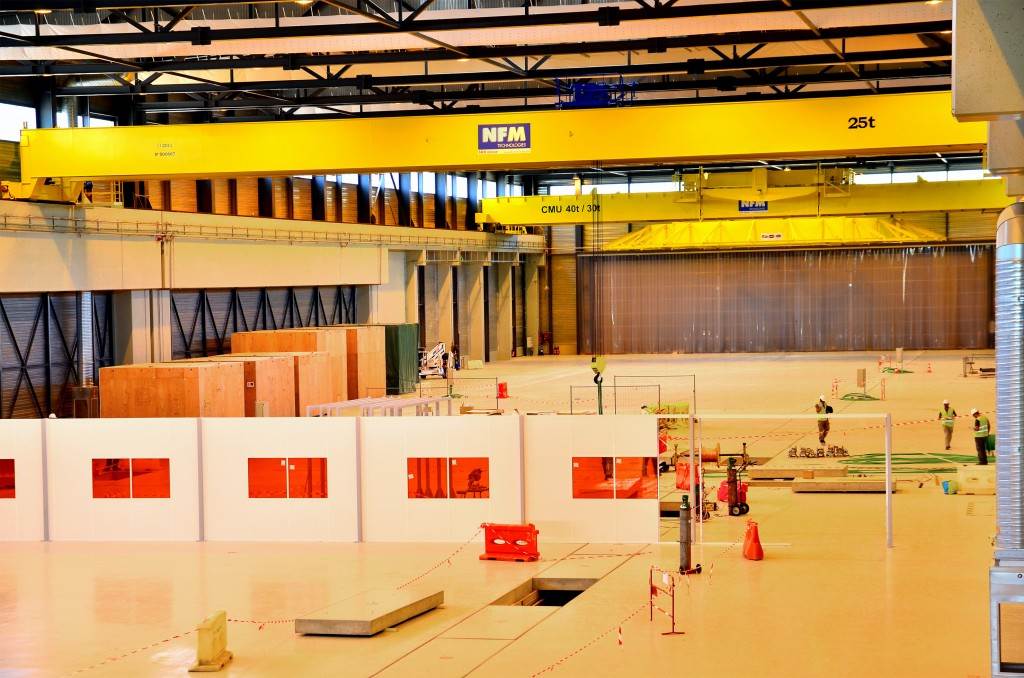
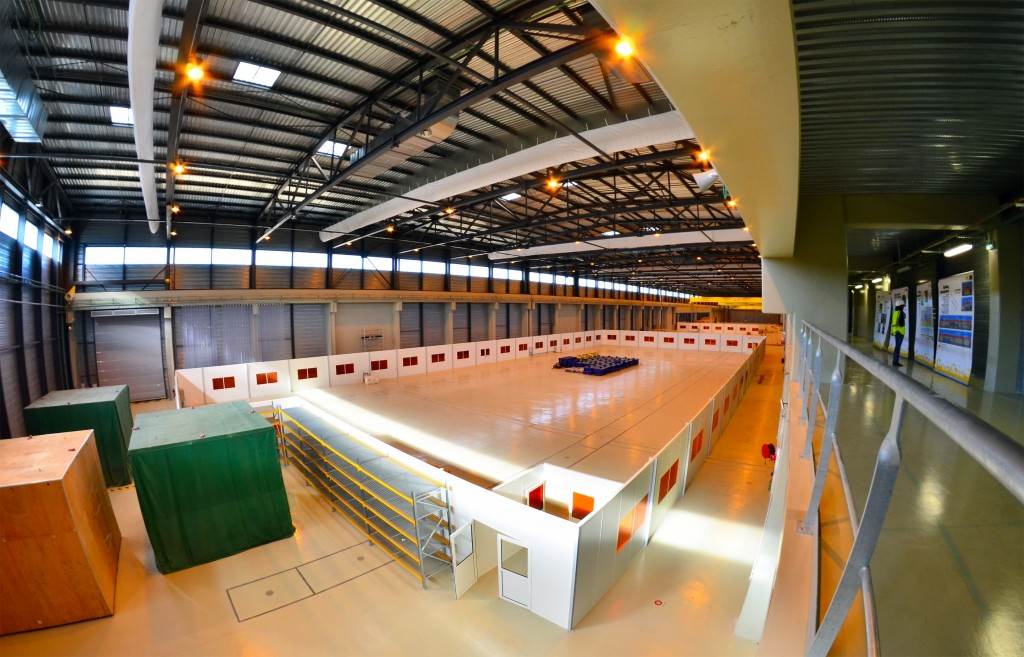
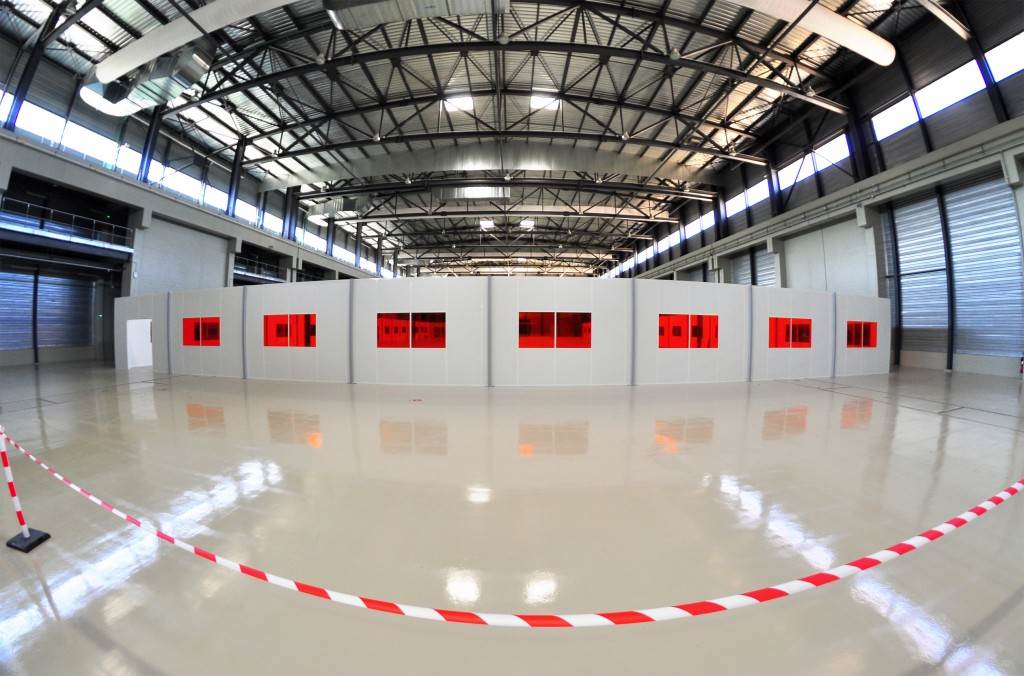
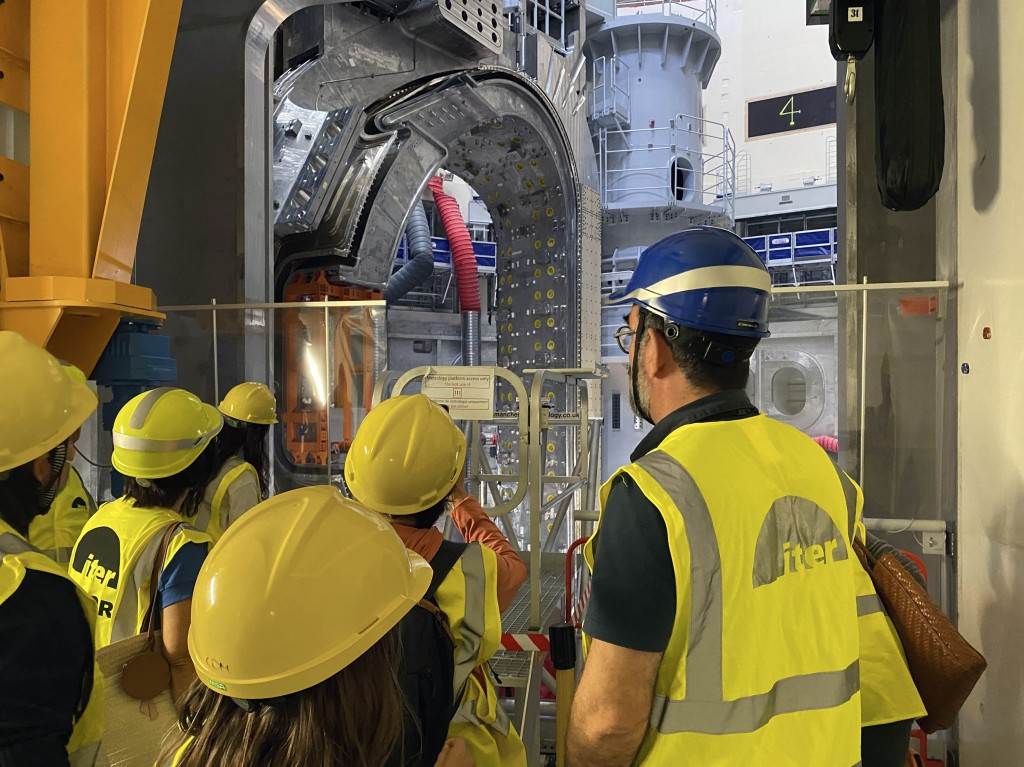