Le Projet
- Construire ITER
- Projets en cours
-
Projets réalisés
- Bâtiment de contrôle
- Alimentation injection de neutres
- Usine cryogénique
- Zone de rejet thermique
- Bâtiment radiofréquence
- Alimentation bobines
- Hall d'assemblage
- Atelier cryostat
- Siège d'ITER
- Usine de production d'aimants
- Les fondations du tokamak
- Excavation de la fosse
- Préparation du site
- Fabrication sur site
- Complexe tokamak
- Centre d'essais NBTF
- L'assemblage - en deux mots
- L'assemblage de la machine
- L'assemblage des systèmes
- Mise en service progressive
- Des outils sur mesure
- Métrologie optique
- Les grandes dates
Fabrication à ITER : bobines de champ poloïdal
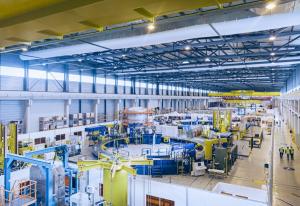
Pour les bobines sous responsabilité européenne, les étapes successives de fabrication—bobinage, imprégnation, assemblage, essais à froid—ont été réalisées sur des stations de travail dans cet atelier de fabrication sur le site ITER.
L'usine de production des bobines de champ poloïdal (l'Installation PF), l'une des deux unités de fabrication situées sur le site ITER, a été construite par l'Europe pour abriter les activités de fabrication des plus imposants des aimants annulaires qui ceintureront la chambre à vide et les aimants de champ toroïdal.
D'un diamètre de 17 à 24 mètres et d'un poids de 200 à 400 tonnes, quatre d'entre eux (sur les six que comptera ITER) sont trop encombrants pour être transportés à l'état fini.
Les entreprises sous contrat avec l'Europe ont progressivement installé l'outillage pour les différentes étapes de la fabrication—depuis le bobinage du câble supraconducteur en niobium-titane jusqu'à l'empilement des éléments en un assemblage final et enfin des tests cryogéniques. Au mois d'avril 2021, la première bobine (PF5) a été parachevée puis transférée dans un lieu de stockage provisoire sur le chantier ITER, avant de trouver sa place au fond de la fosse au mois de septembre 2021. La bobine PF2 a quitté l'installation en 2021 suivie par la bobine PF4 (2023) et la bobine PF3 (2024). Les activités de fabrication pour les bobines européennes sont maintenant terminées et l'espace a été transféré à ITER Organization pour d'autres activités d'assemblage.
Étapes de fabrication
Fabriqués en Chine à partir d'un composé de niobium-titane (NbTi), les câbles supraconducteurs dits « câbles en conduit » (les brins sont enserrés dans une gaine en acier) ont été livrés en tourets de 20 tonnes.
Pendant la phase de bobinage le conducteur a été d'abord dévidé et redressé, puis nettoyé et sablé afin de préparer la surface du conducteur à recevoir plusieurs épaisseurs de ruban isolant. Les applicateurs de ruban, rotatifs, entraient en action au moment où le conducteur était acheminé sur la table de bobinage en deux points différents (« double hand winding »). Par une action de « cintrage » les opérateurs le faisaient épouser précisément, par enroulement successifs, le diamètre de la bobine à laquelle il était destiné.
La double galette (« double pancake ») qui en résultait pèse entre 20 tonnes (PF2) et 35 tonnes (PF3).
Lors de la deuxième étape de fabrication, le bobinage était transféré par pont roulant à la zone dite d'imprégnation, et inséré dans un moule dans lequel était injectée, à chaud sous vide et pendant plusieurs heures, de la résine de type époxy. Une fois totalement imprégné, le bobinage était soumis pendant 36 heures à une température de 140°C de manière à finaliser le durcissement de la résine. La phase d'imprégnation confère au bobinage isolation électrique et tenue mécanique.
Le bobinage « durci » pouvait rejoindre le troisième et dernier atelier de l'Installation PF où était réalisé l'assemblage. Pour fabriquer les quatre bobines de champ poloïdal, six à huit doubles galettes étaient empilés les uns sur les autres et joints aux deux extrémités. Une deuxième imprégnation était alors réalisée pour solidifier l'ensemble, auquel étaient fixées des attaches permettant la manutention.
Dans une dernière phase de production, les bobines assemblées étaient soumises à des « essais à froid ». Cette étape, qui consistait à refroidir les bobines à environ 80 K (moins 193°C), permet de reproduire certaines des contraintes thermiques que connaîtra la machine en phase opérationnelle.
La fabrication de bobines de champ poloïdal en chiffres :
- Production des bobines : 2017-2024
- Bobines fabriquées dans l'Installation PF : PF2, PF3, PF4, PF5
- Diamètre des bobines : de 17 mètres (PF2, PF5) à 24 mètres (PF3, PF4)
- Quantité de conducteur « câble-en-conduit » par aimant : de 6 km (PF2) à 14 km (PF3)
- Nombre de « galettes doubles » par bobine : de six (PF2) à huit (PF3, PF4, PF5)
- Nombre de « galettes doubles » produites dans l'Installation PF : 30
- Poids des assemblages finaux : 200 à 400 tonnes
- Bobines parachevées : PF5 (2021); PF2 (2021); PF4 (2023); PF3 (2024)
- Contribution : Europe
Images
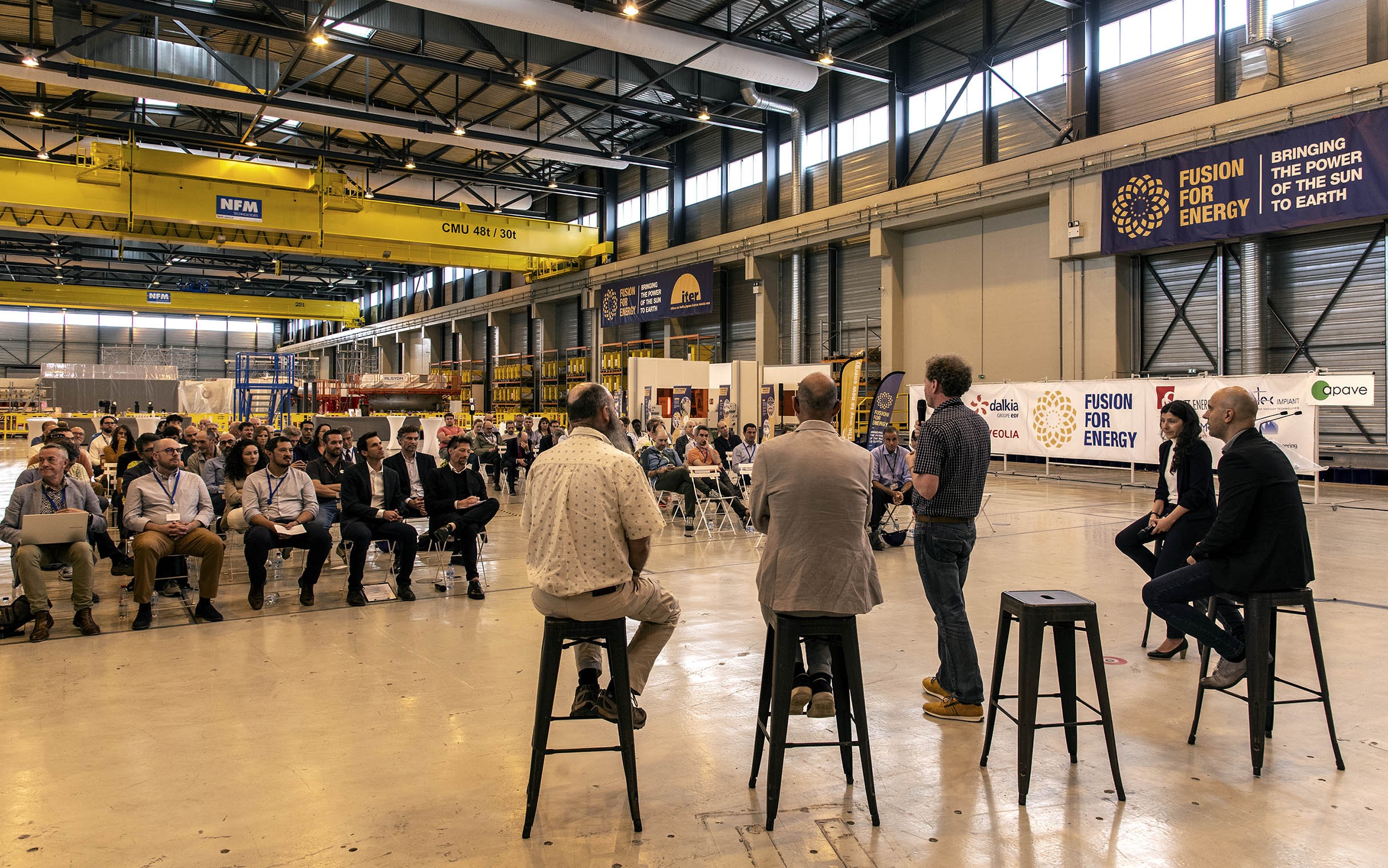
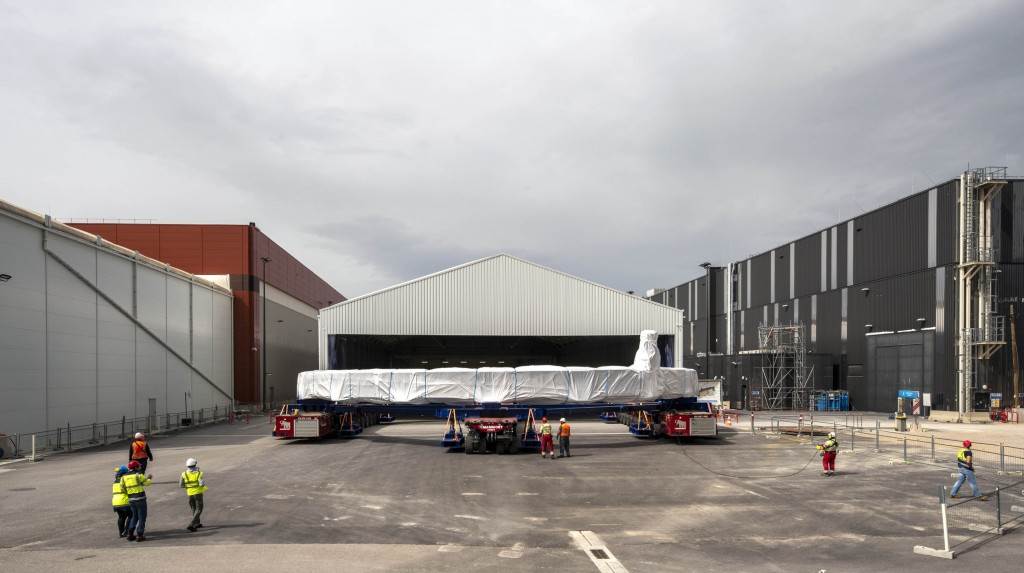
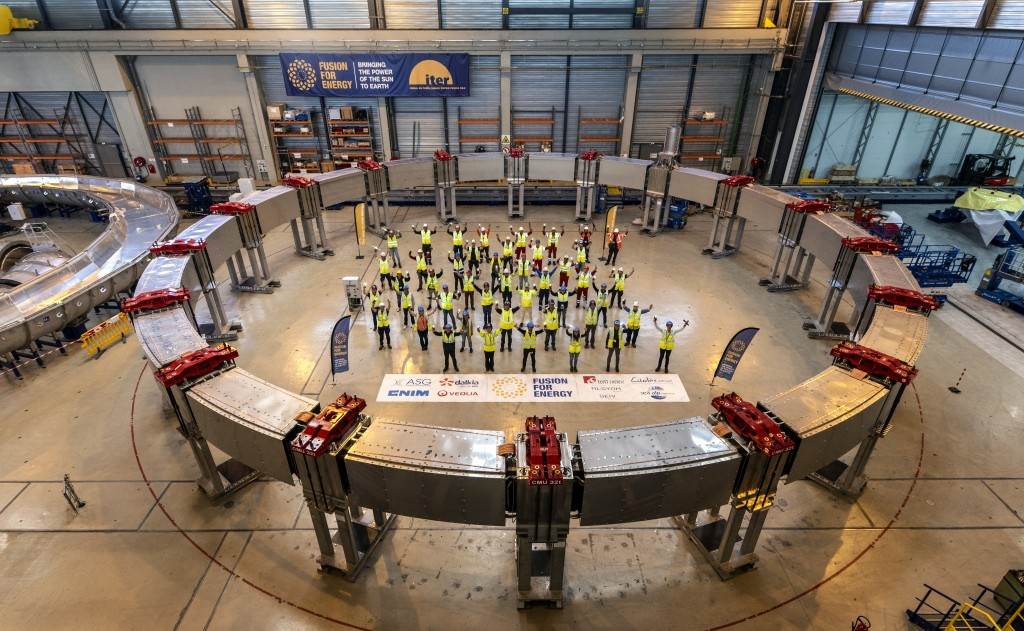
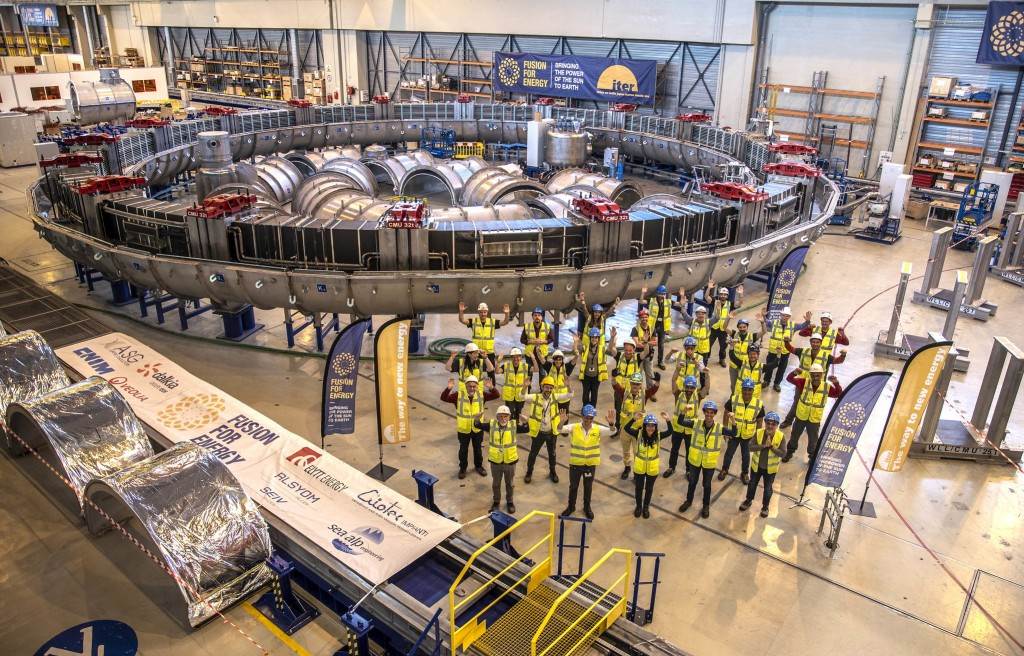
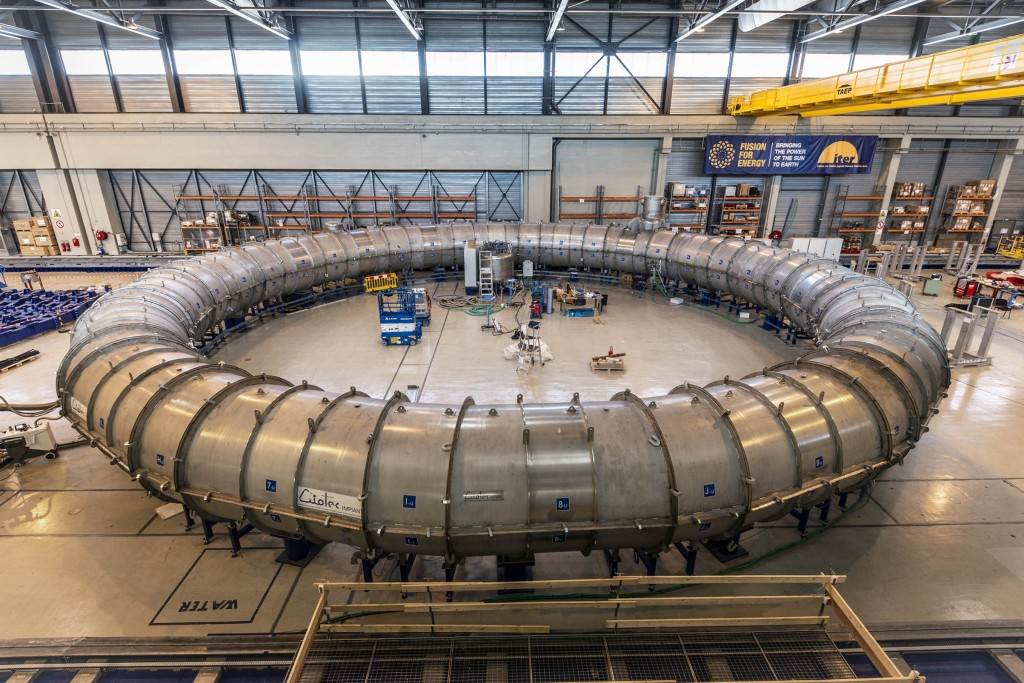
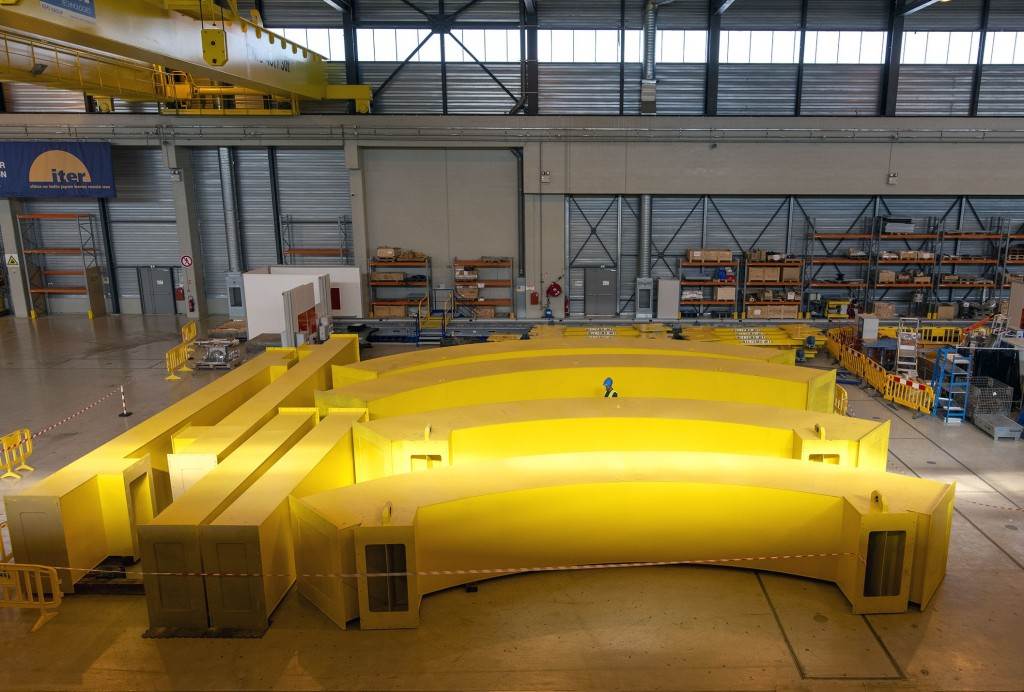
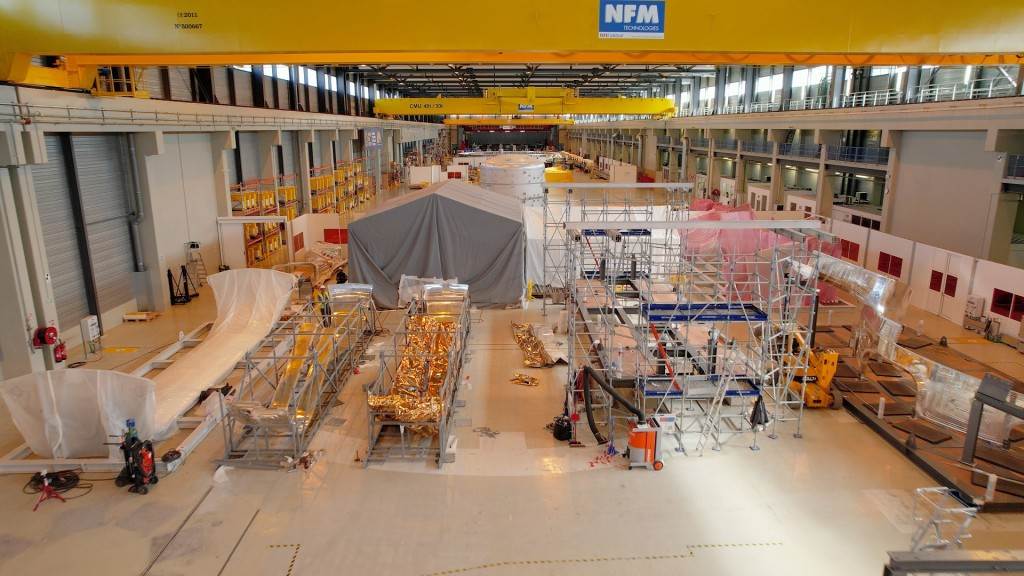
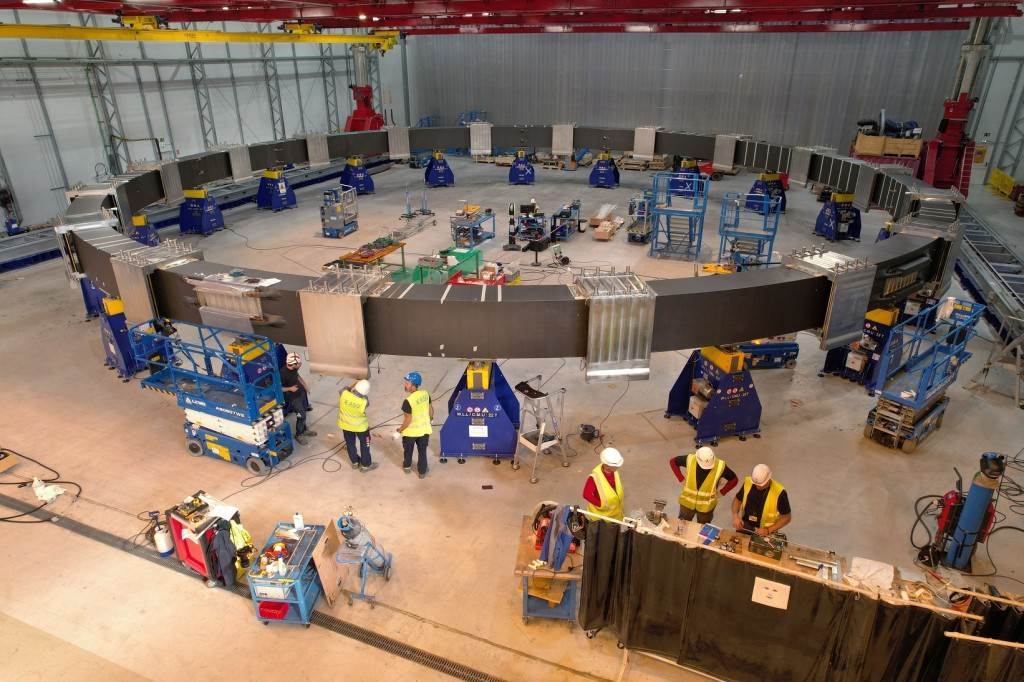
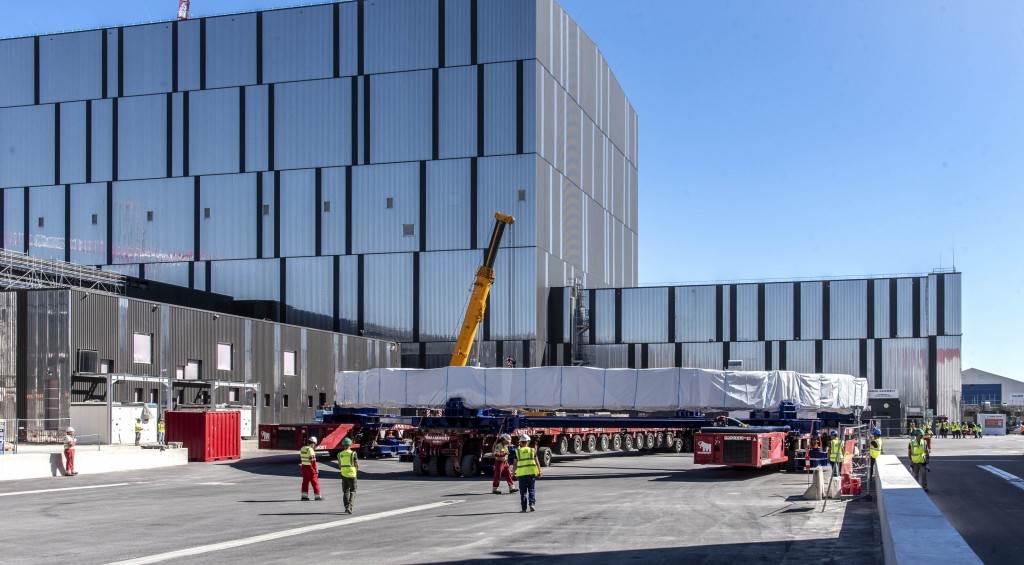
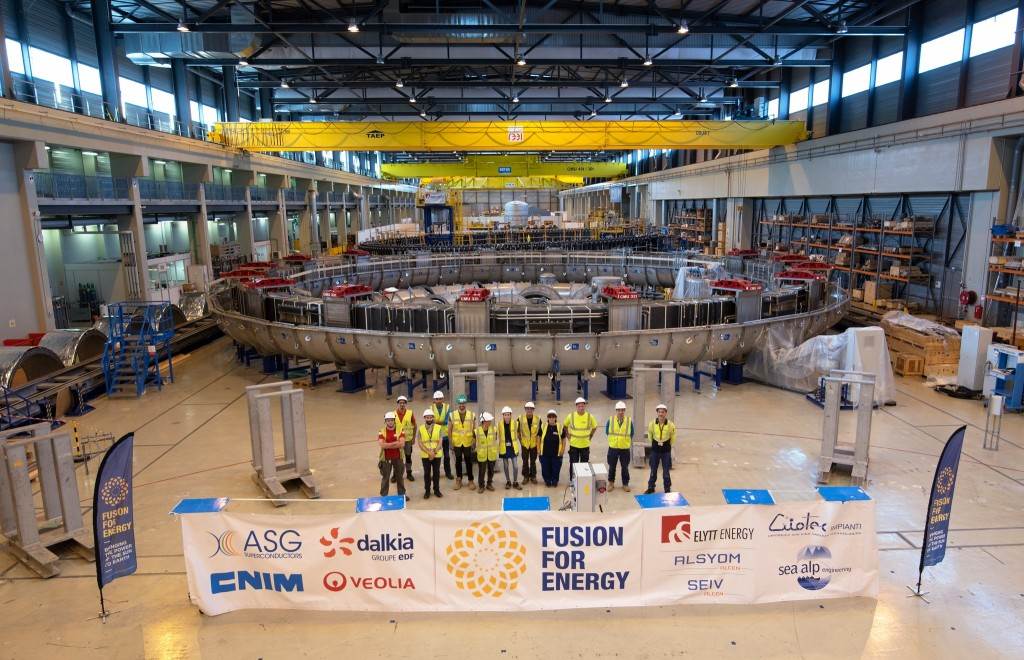
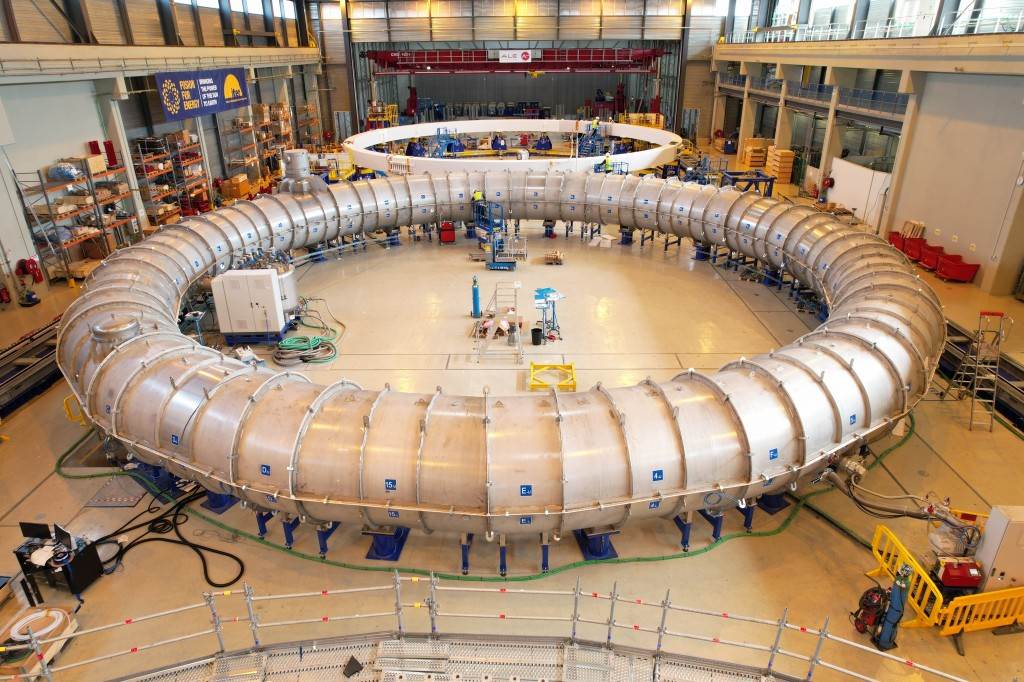
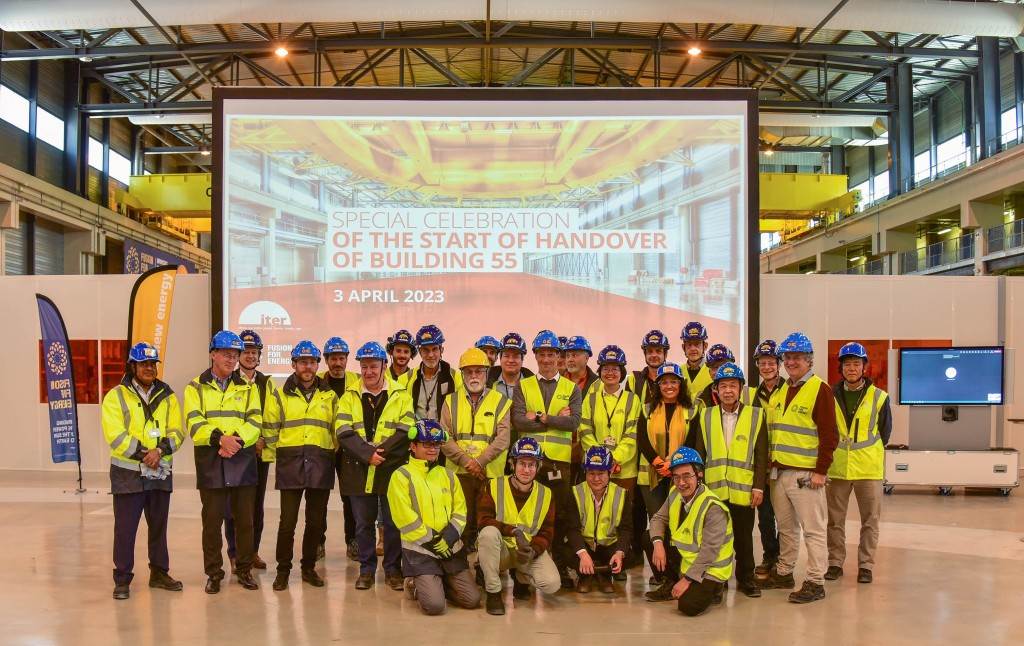
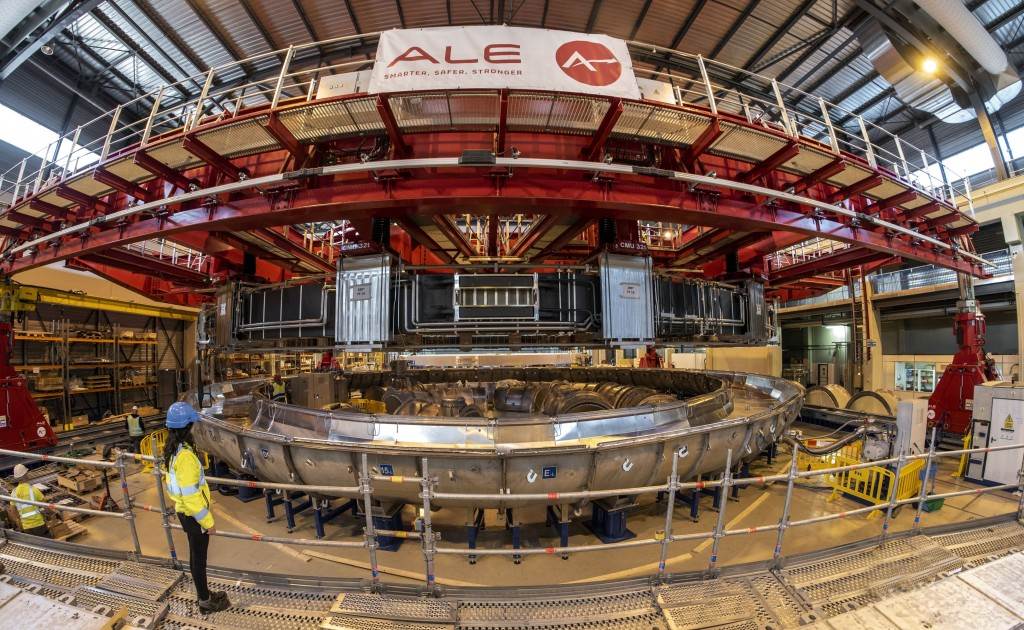
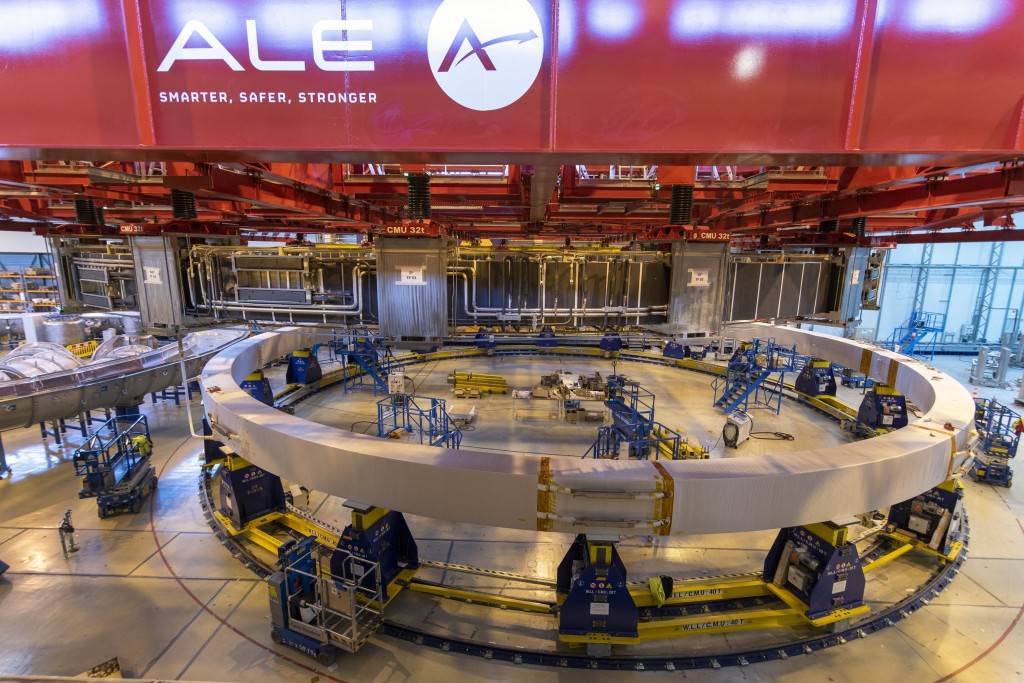
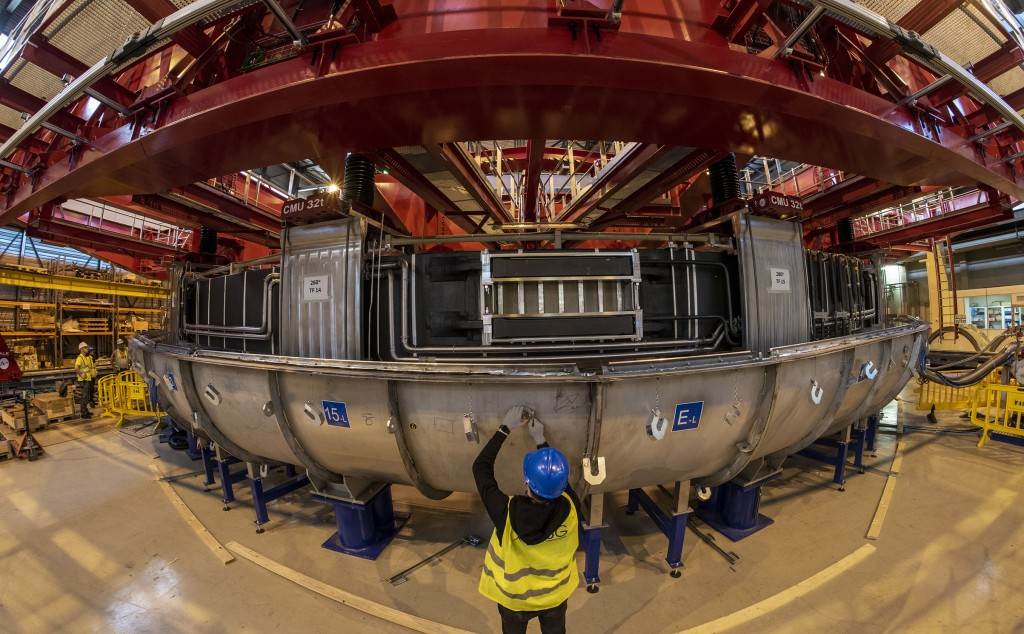
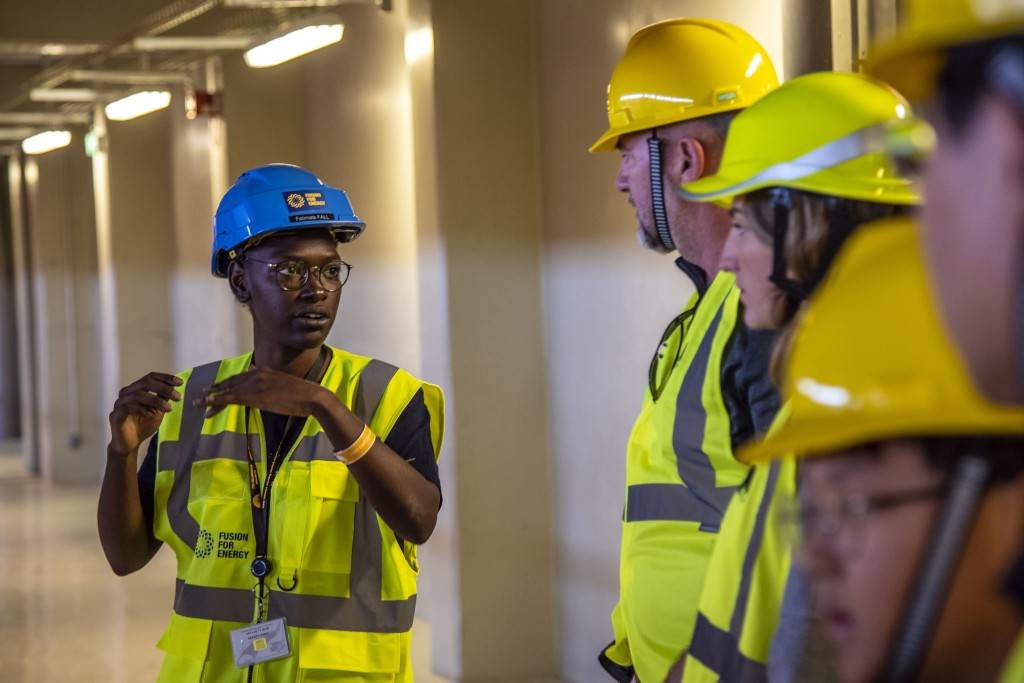
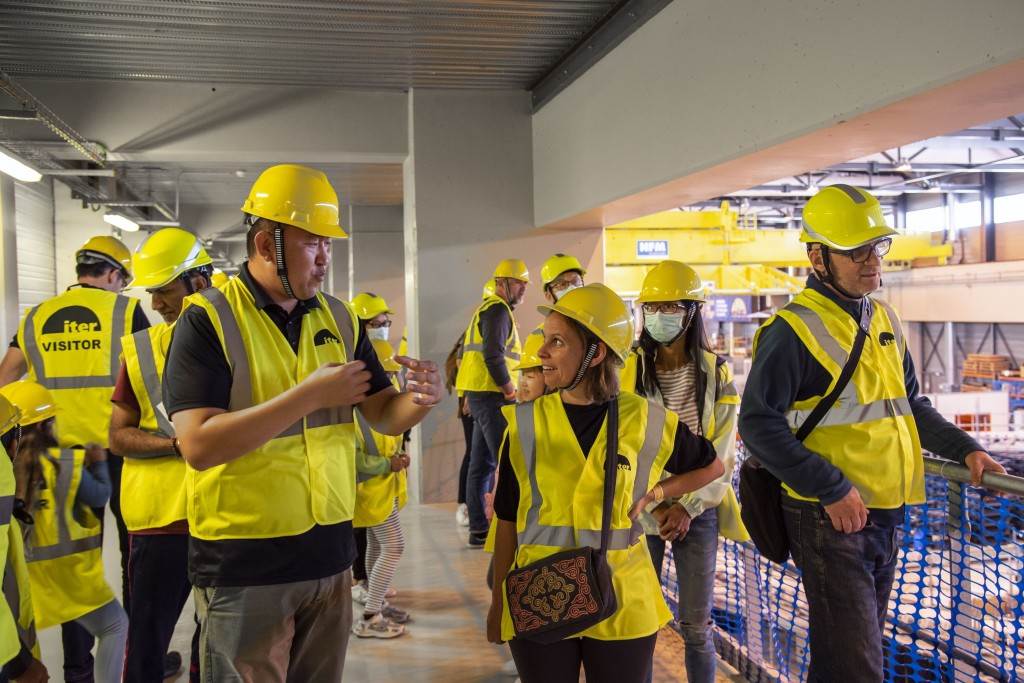
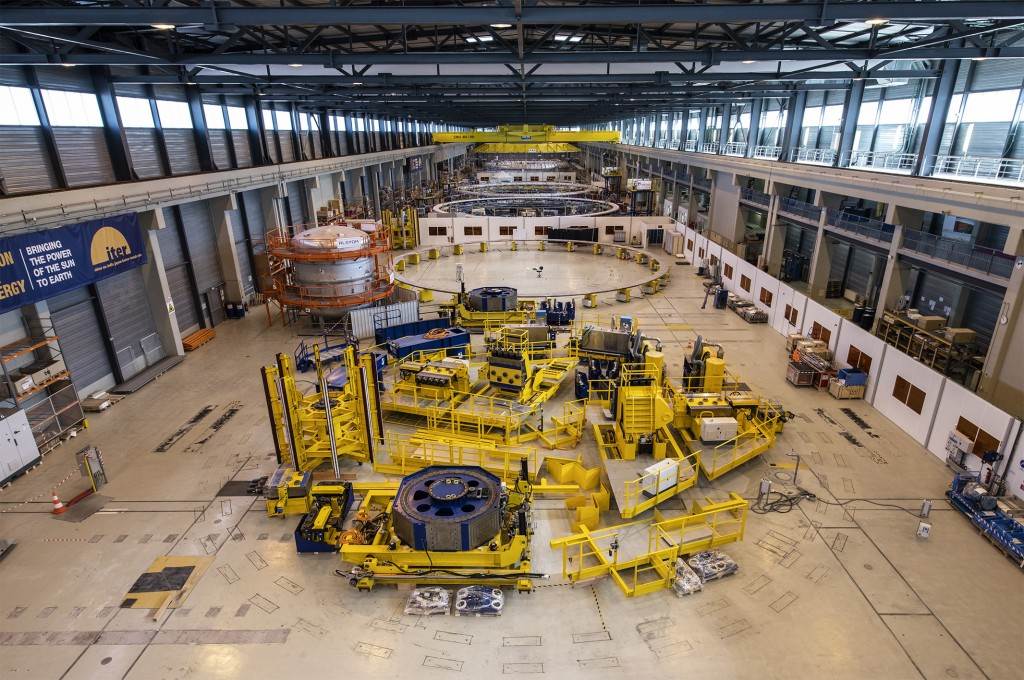
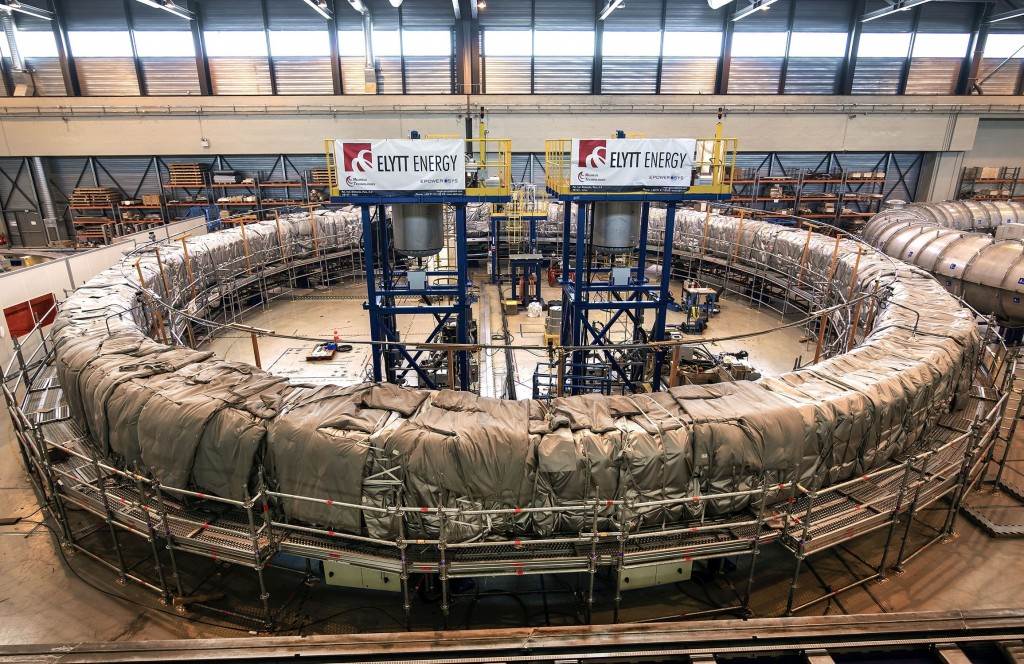
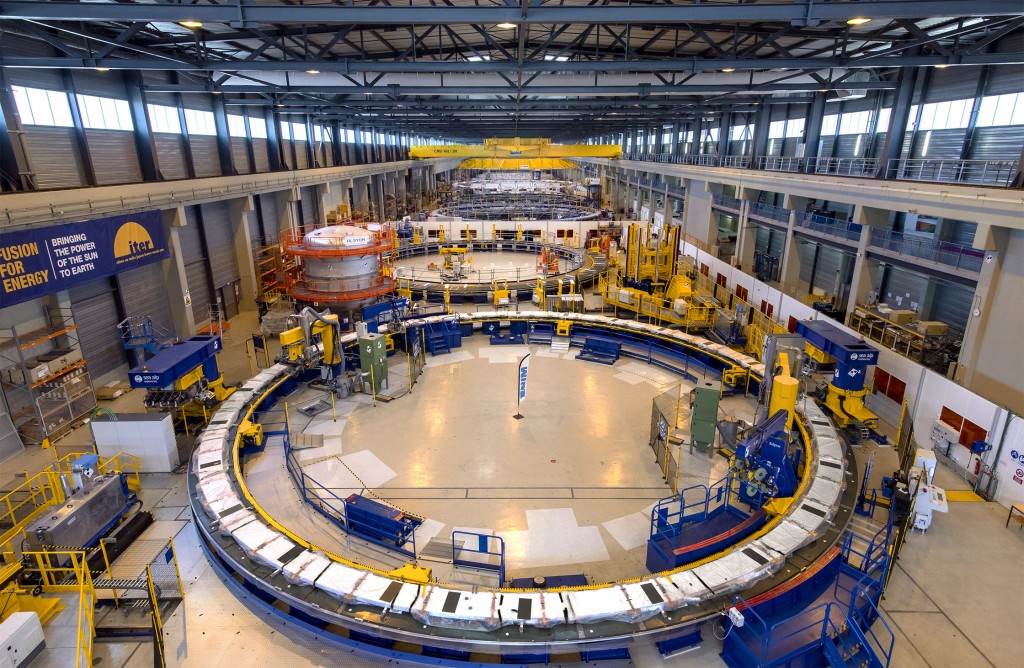
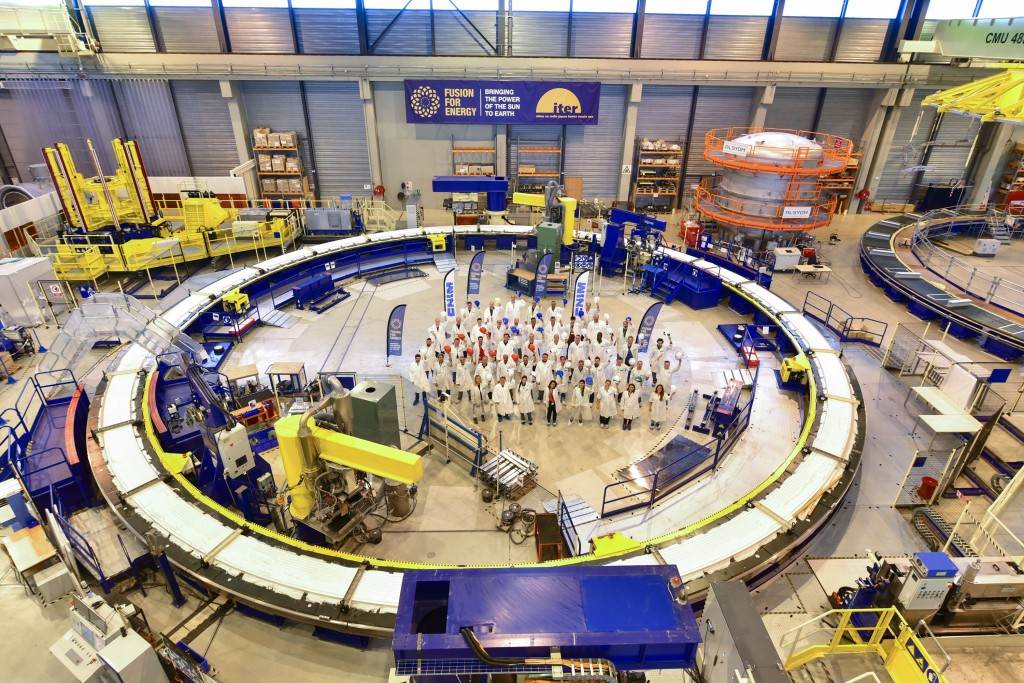
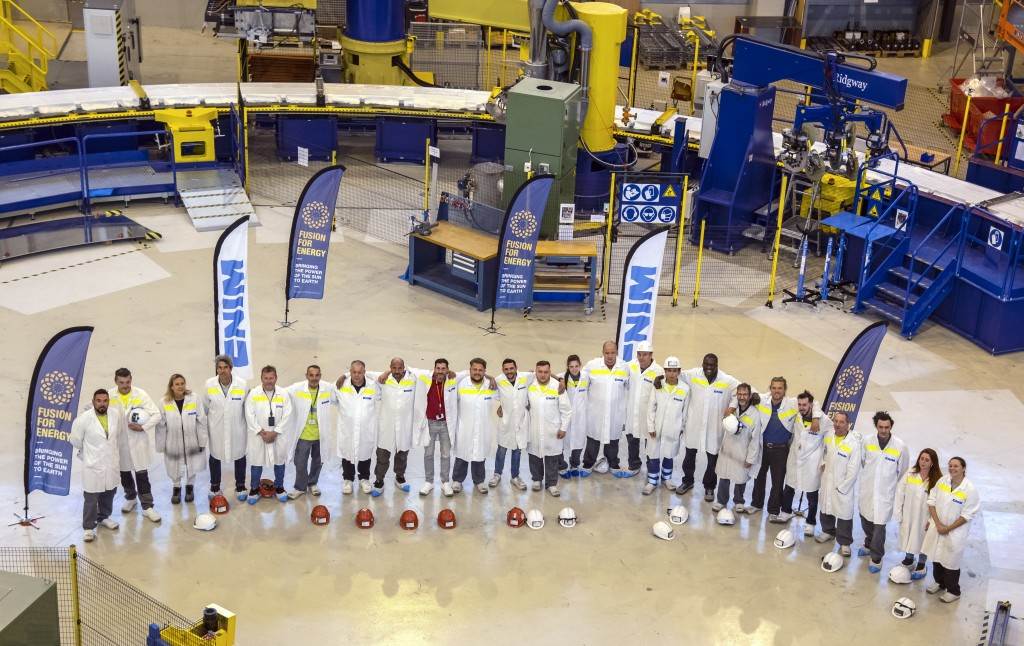
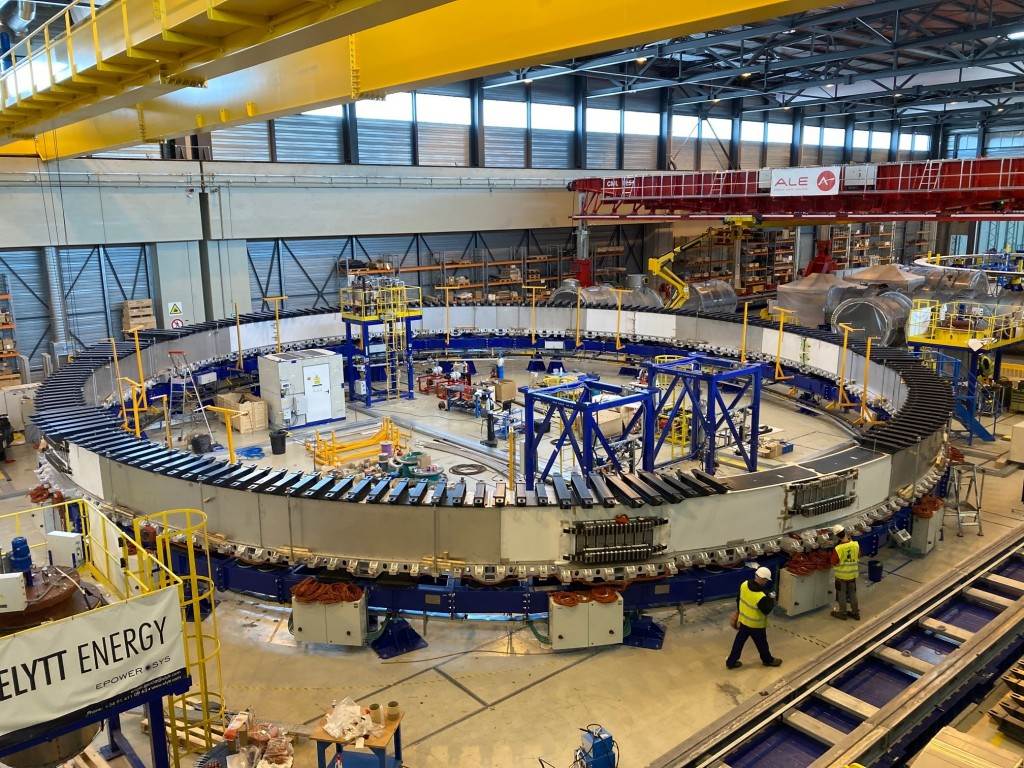
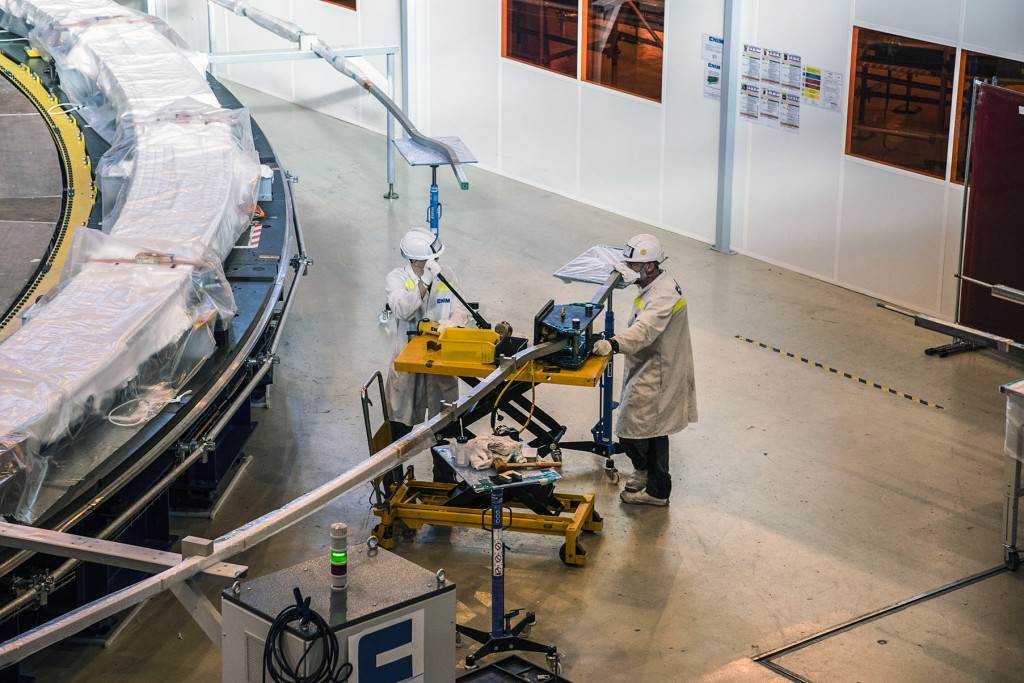
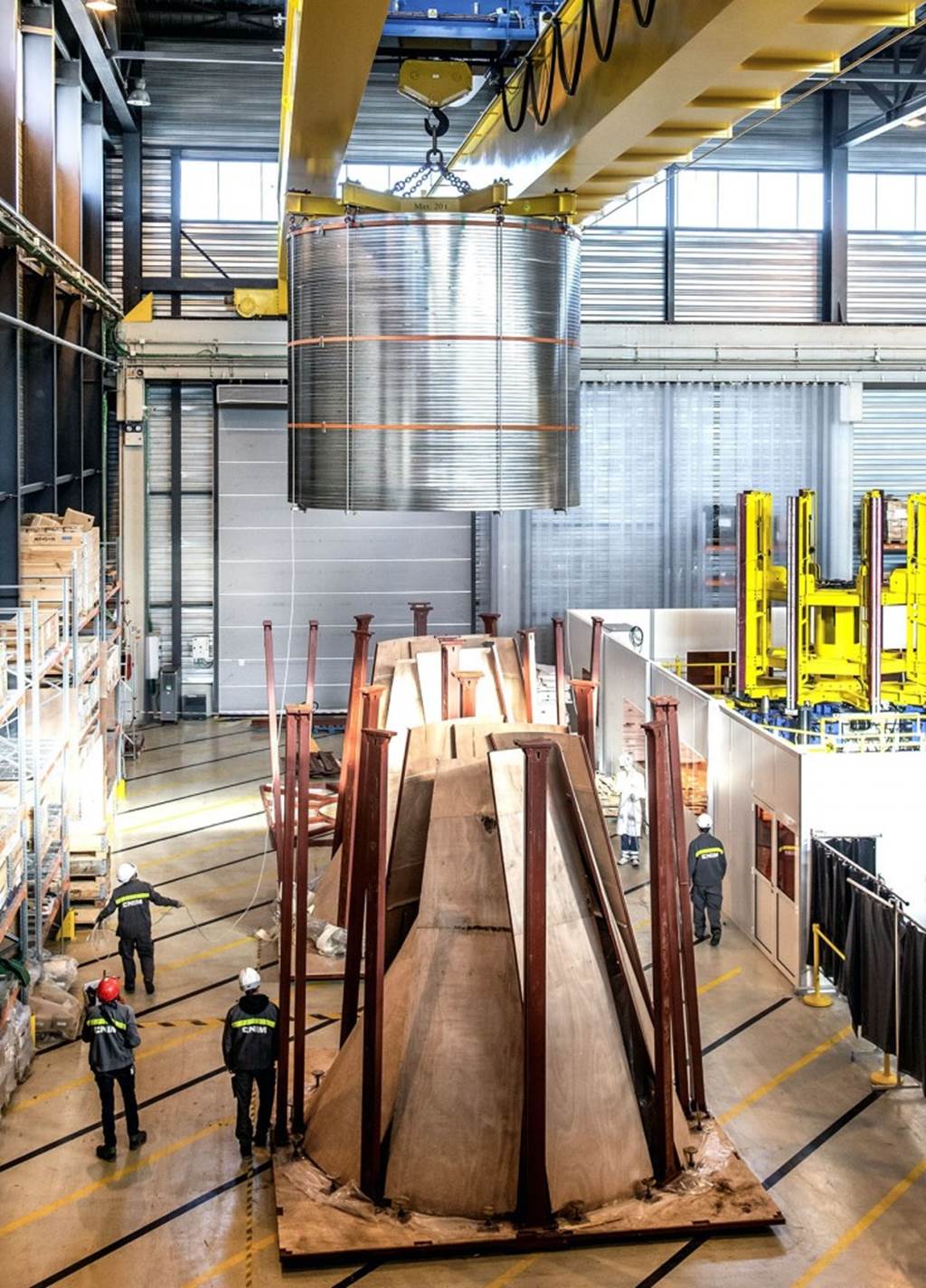
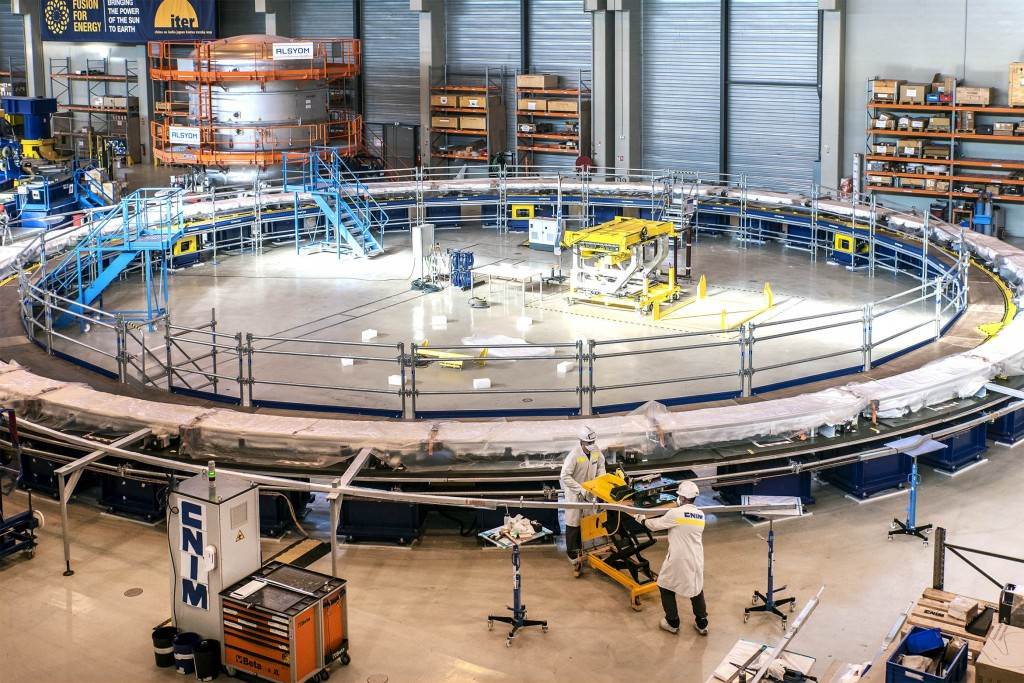
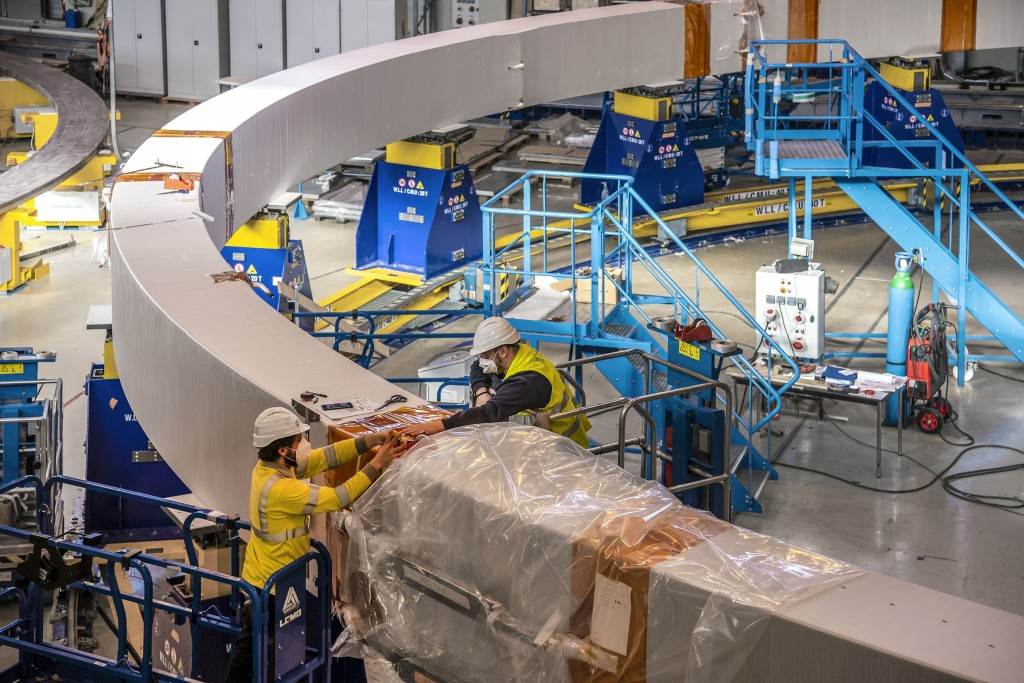
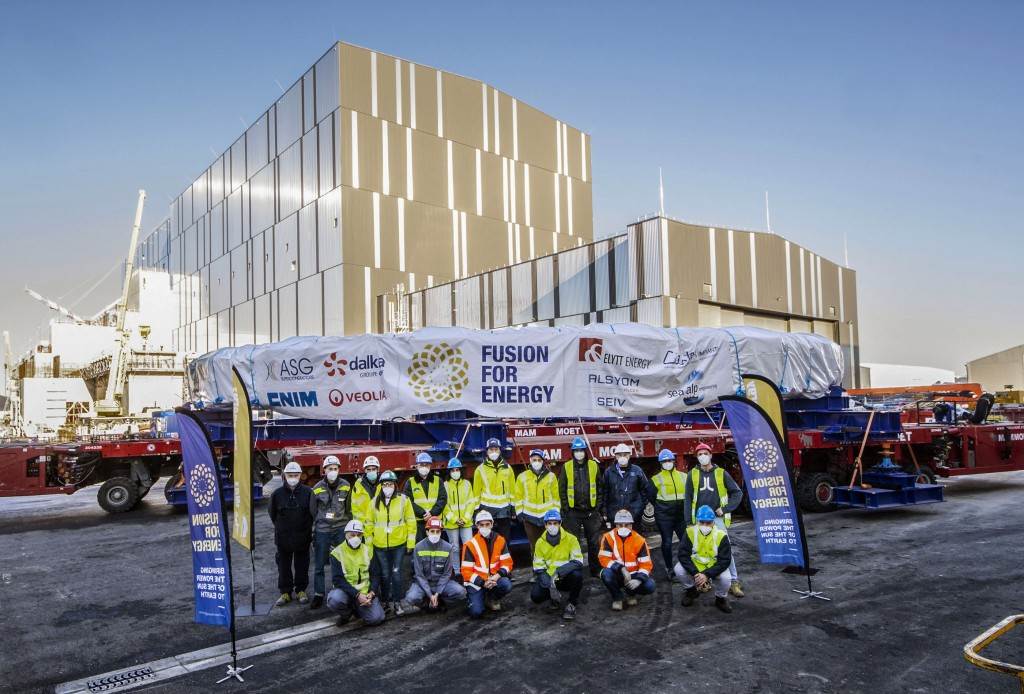
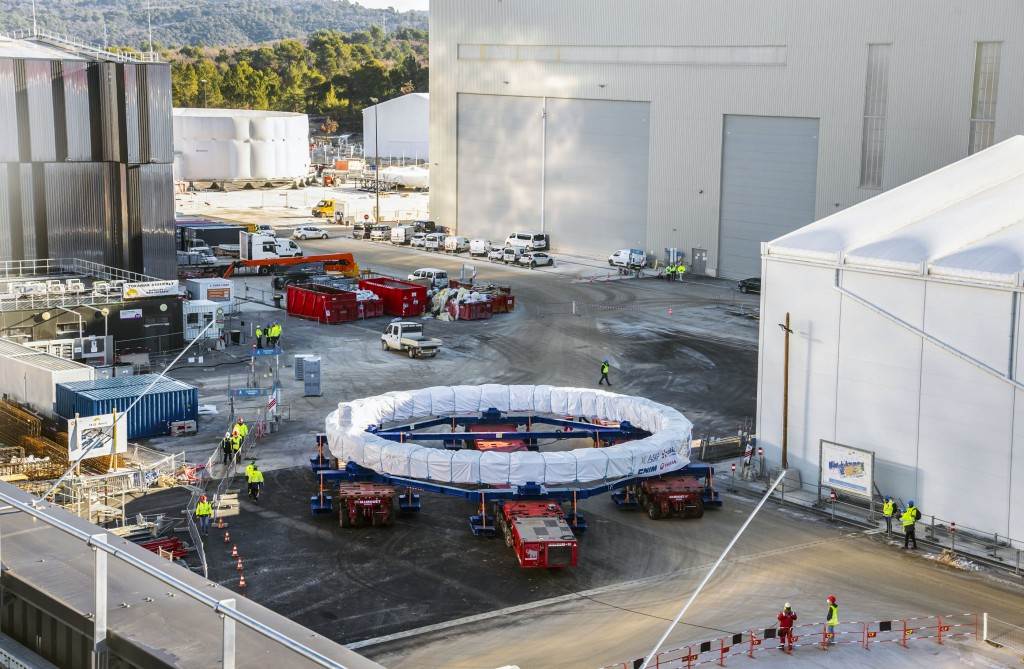
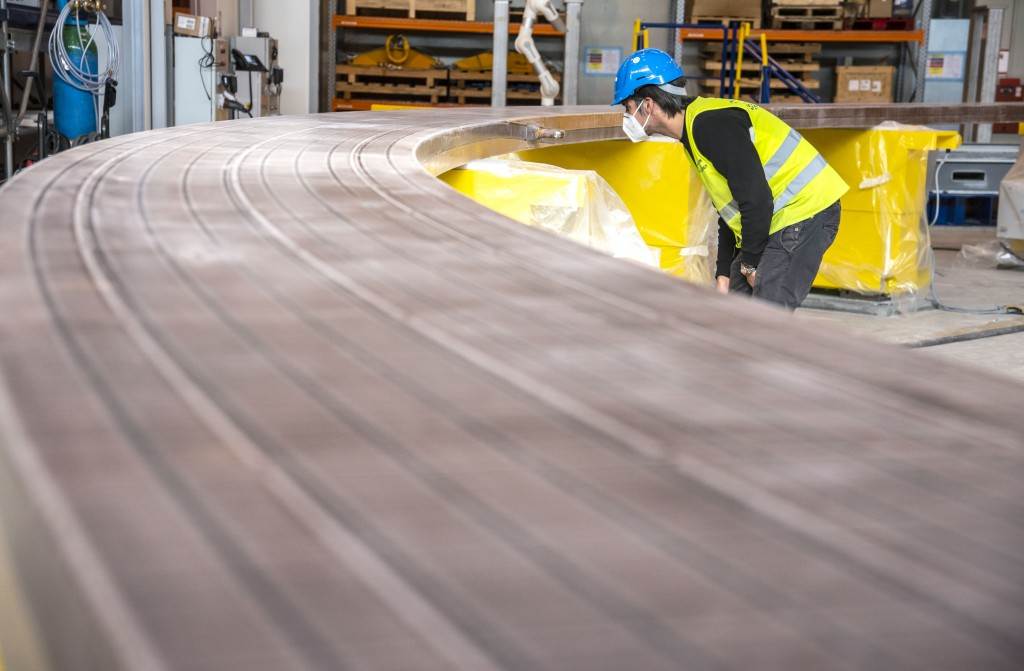

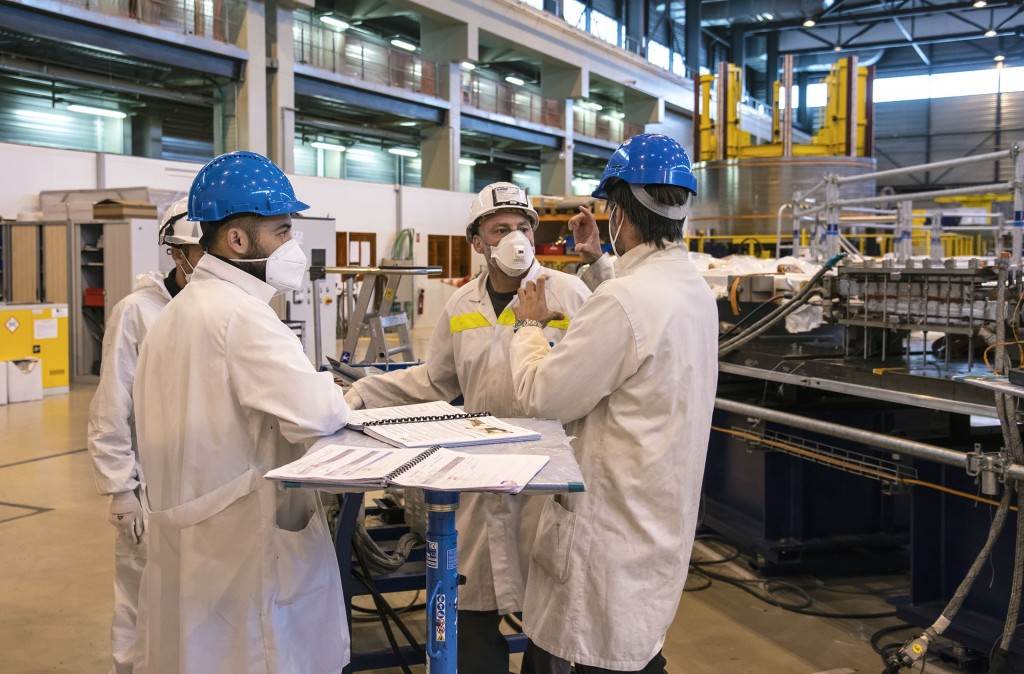
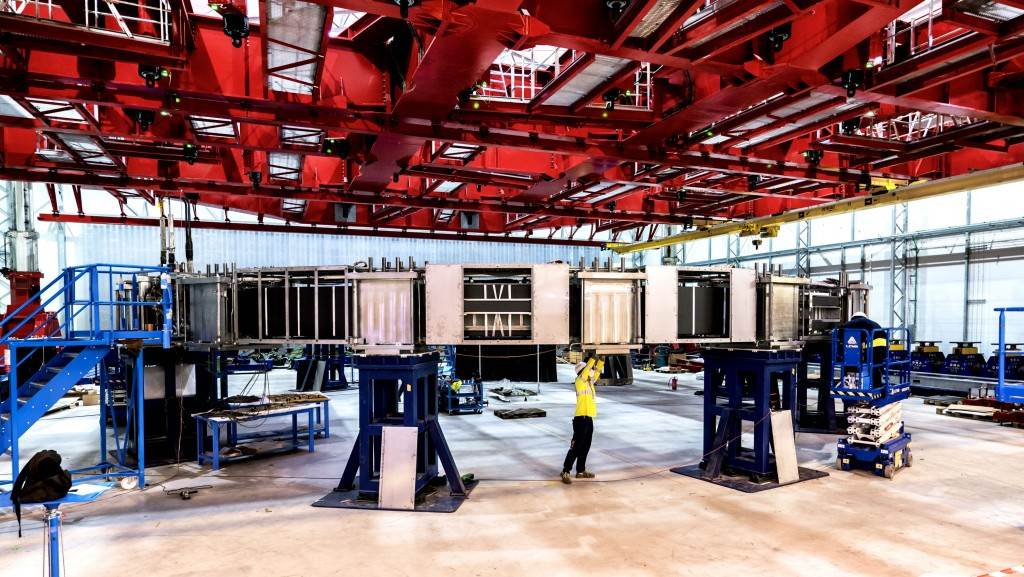
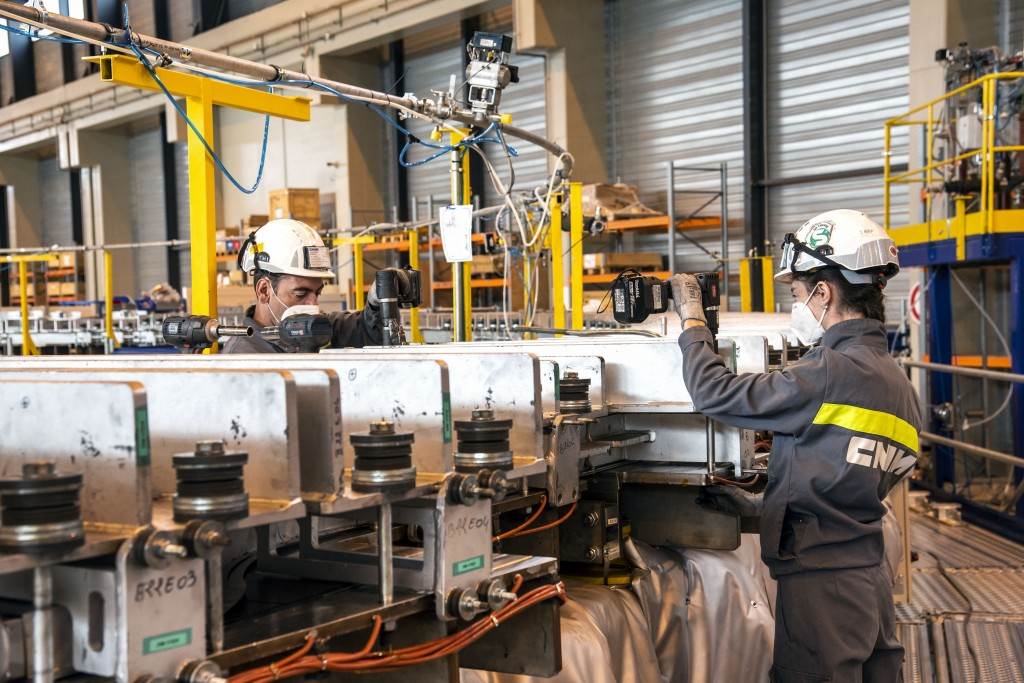
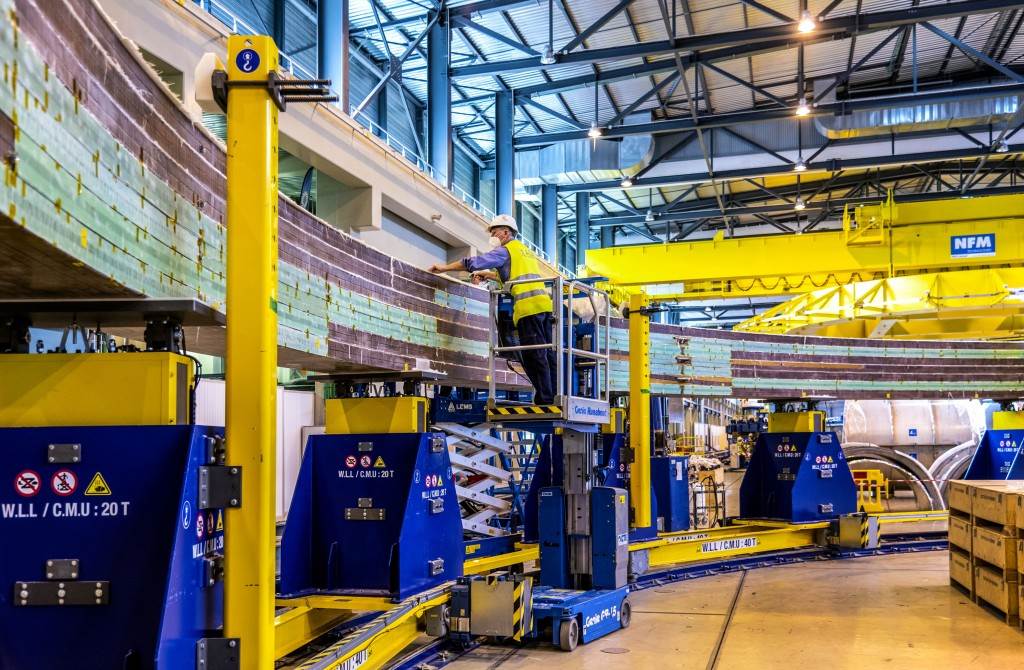
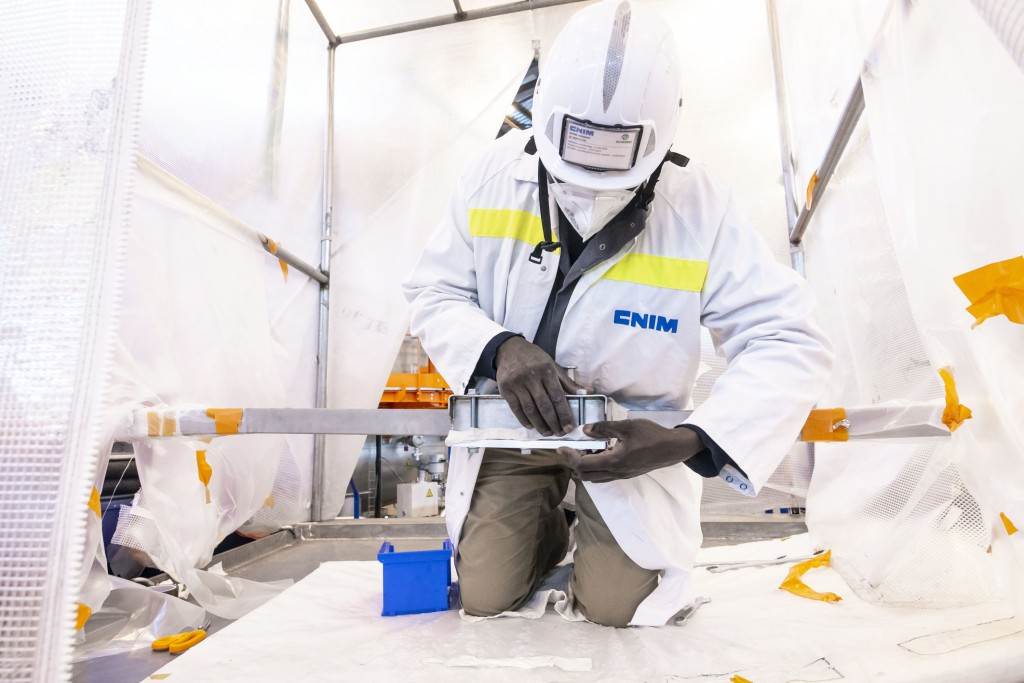
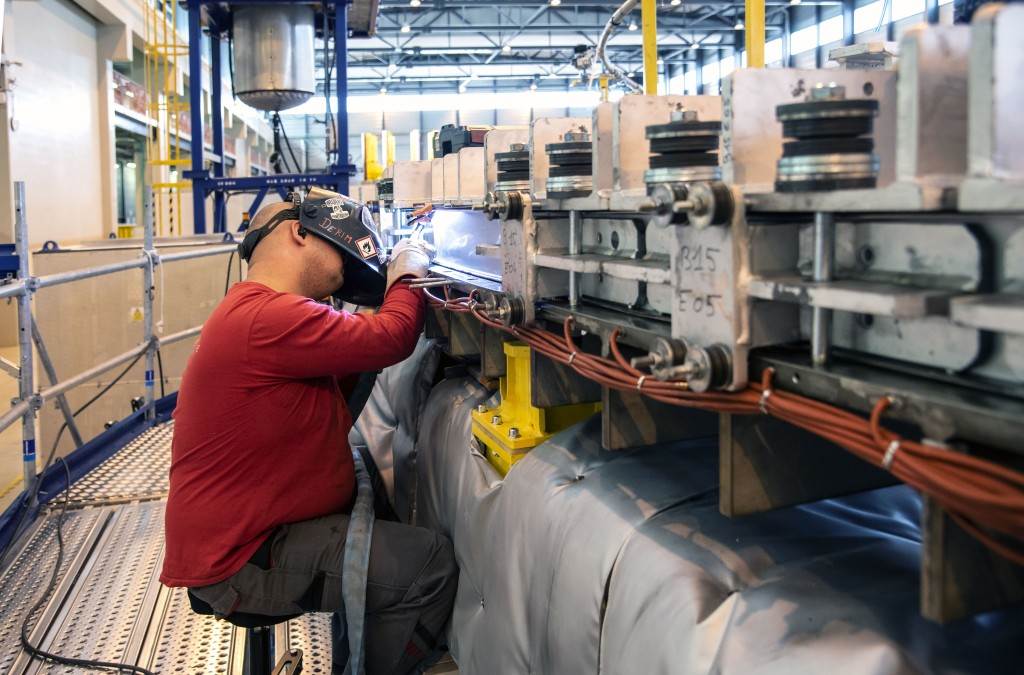
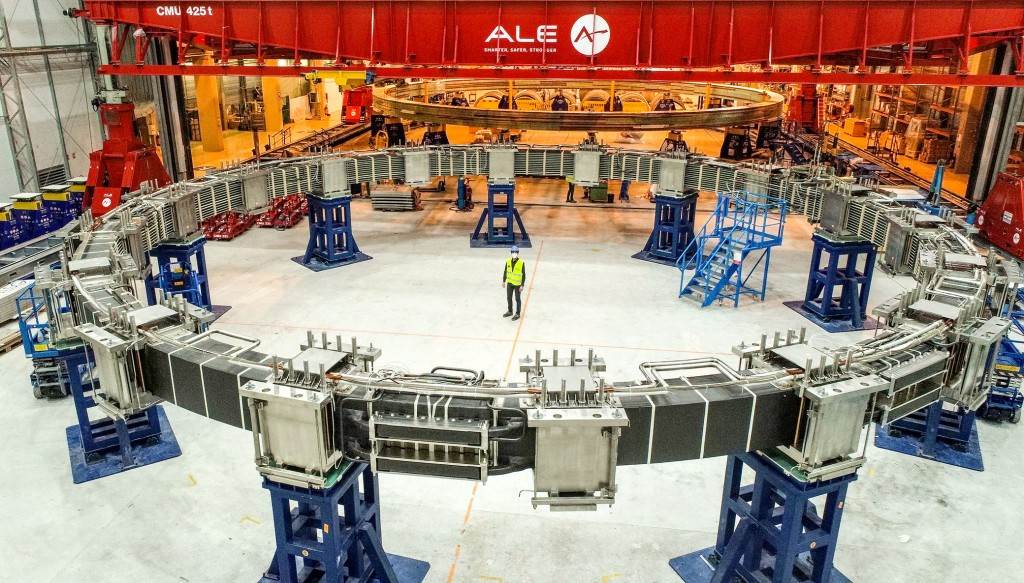
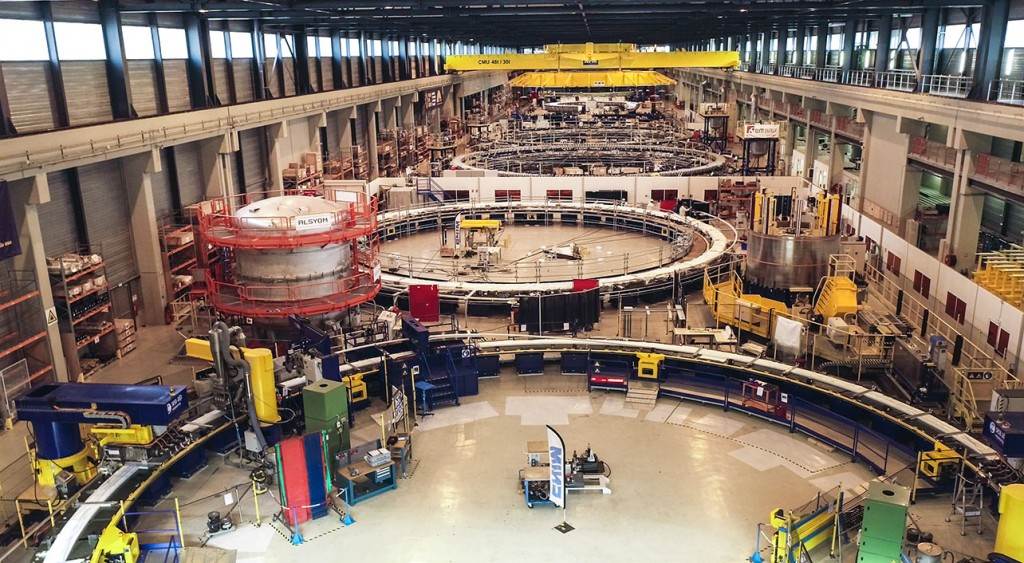
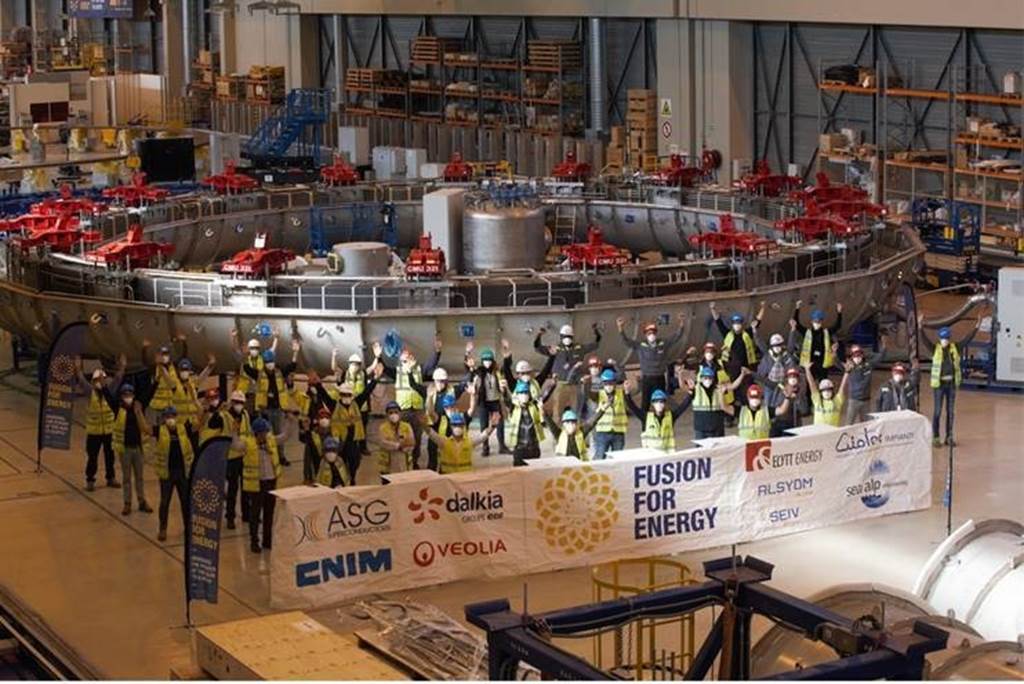
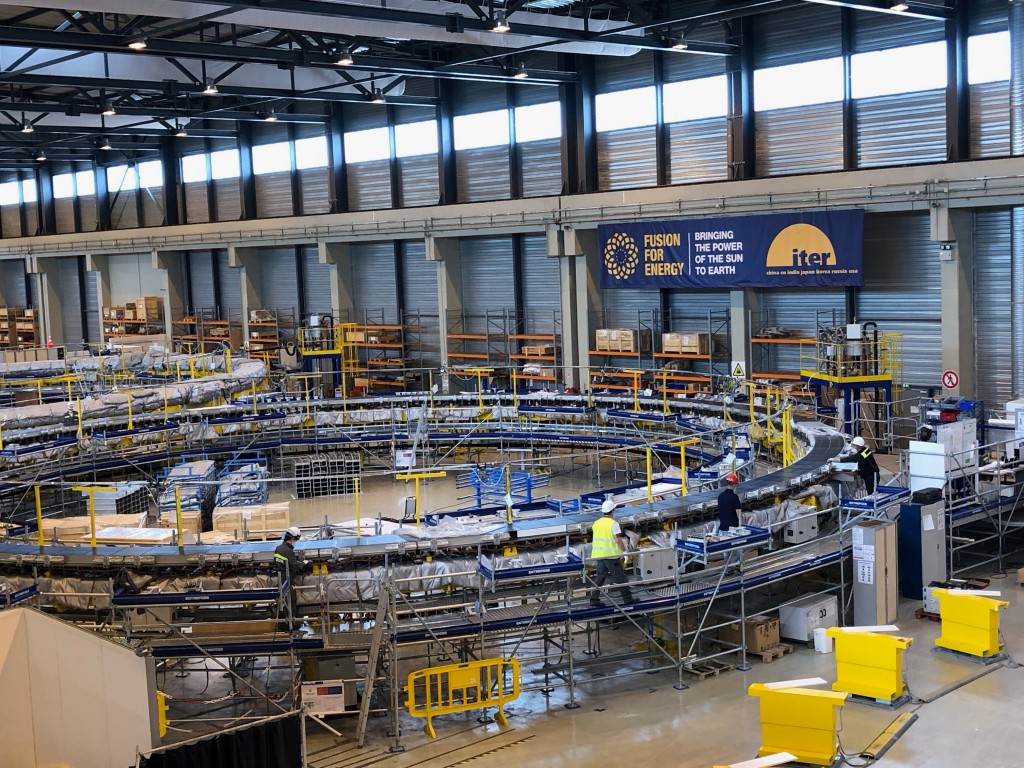
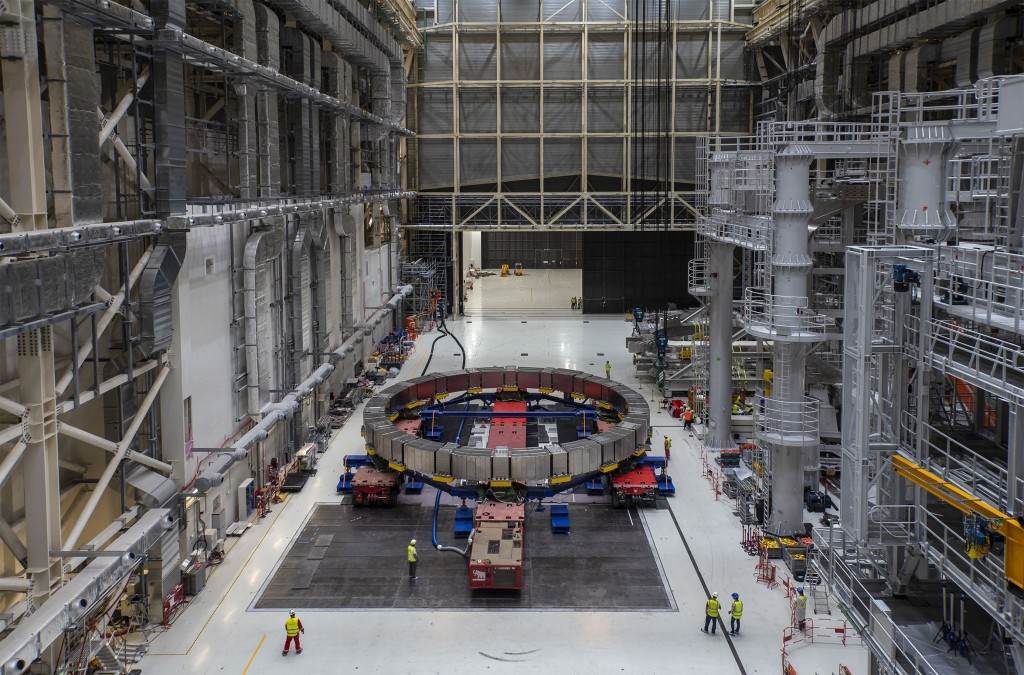
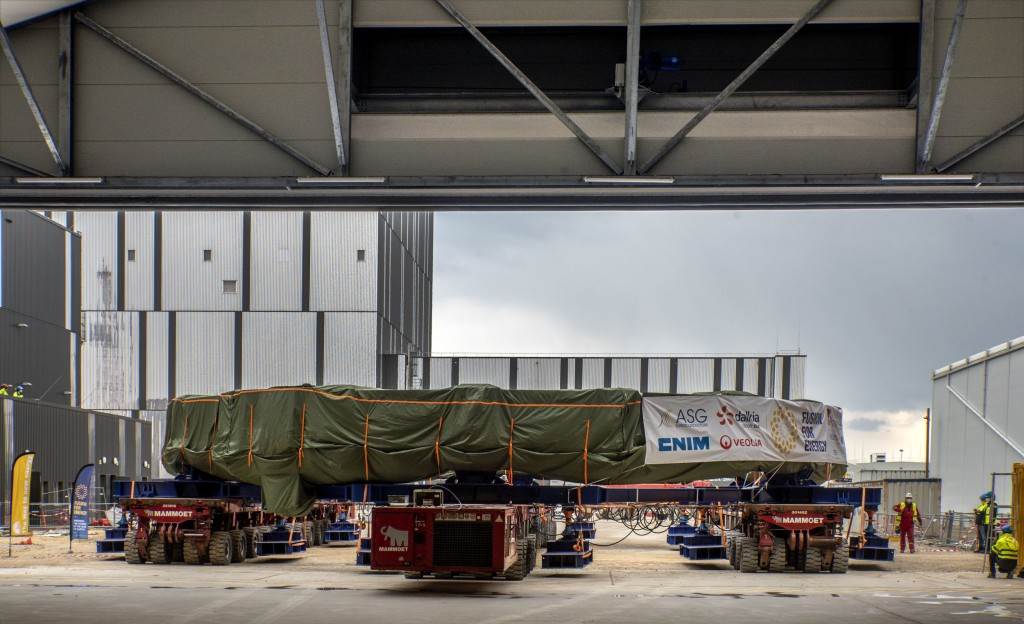
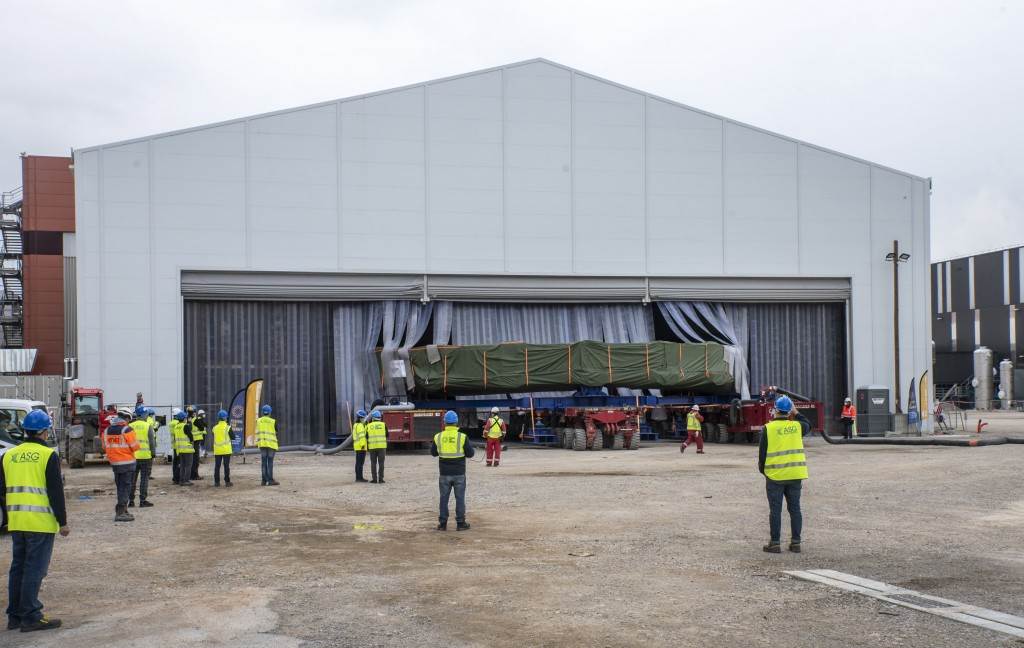
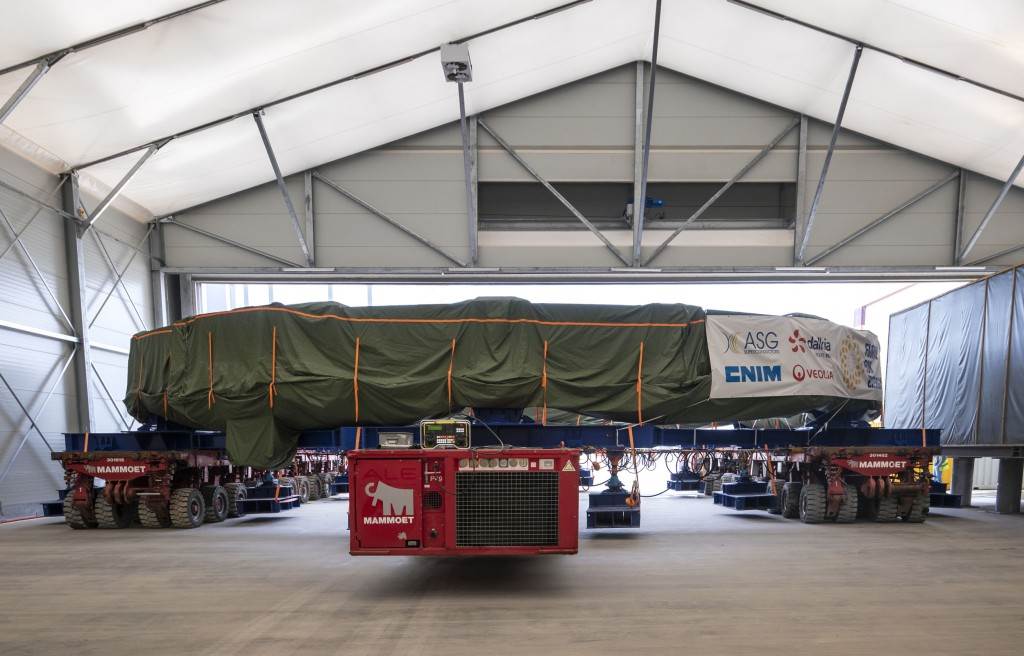
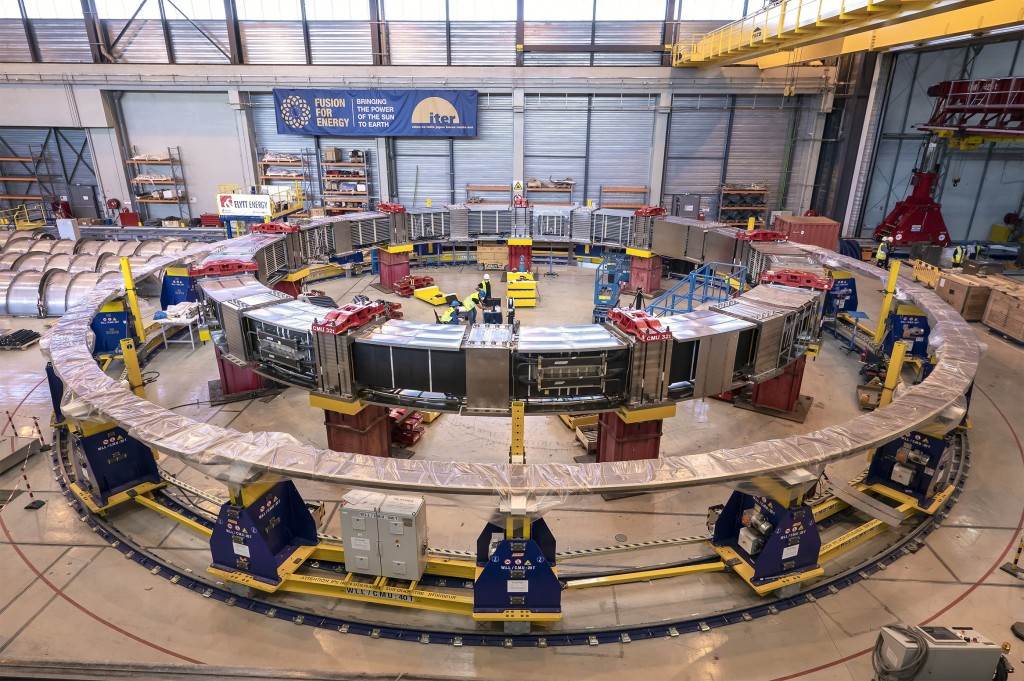
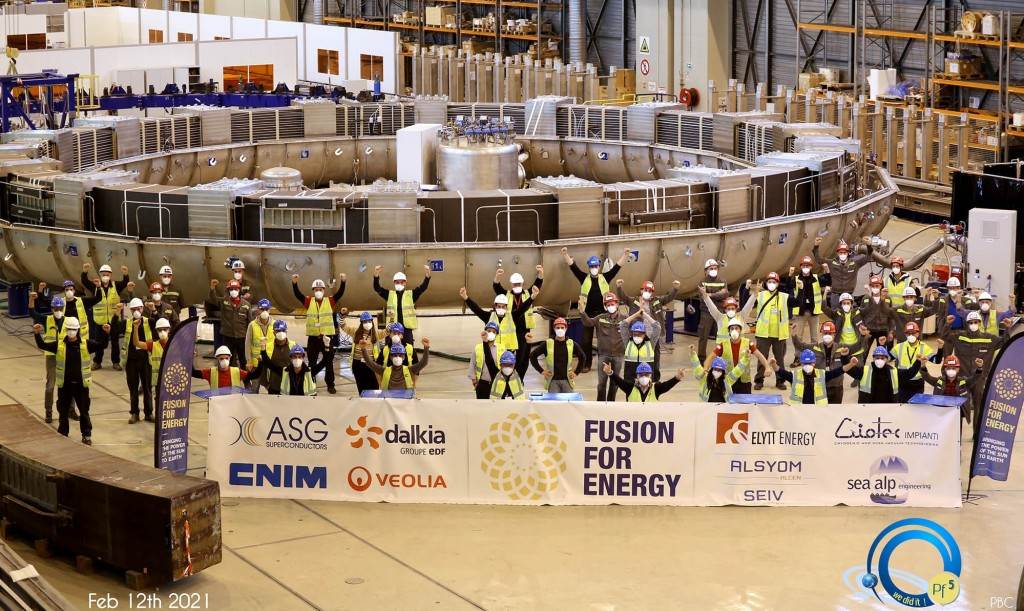
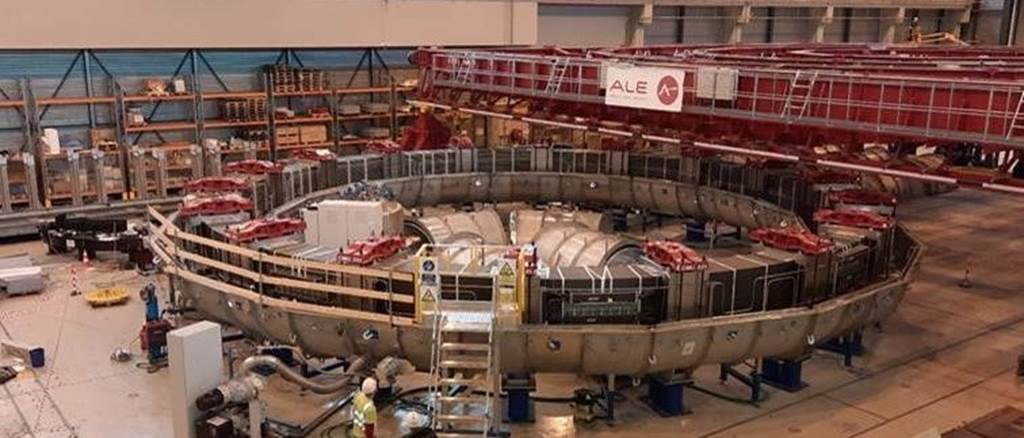
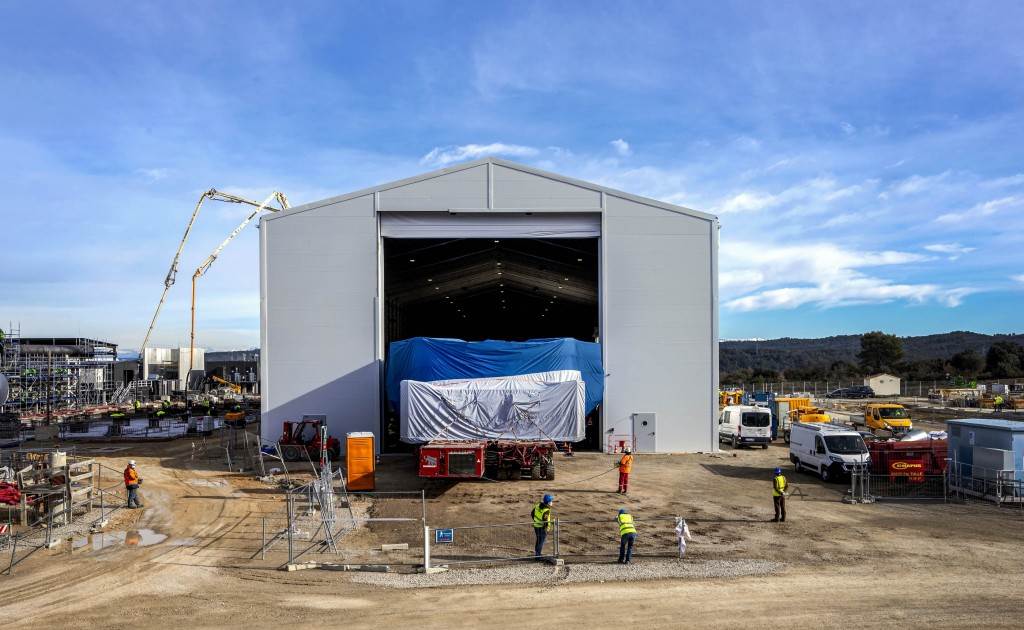
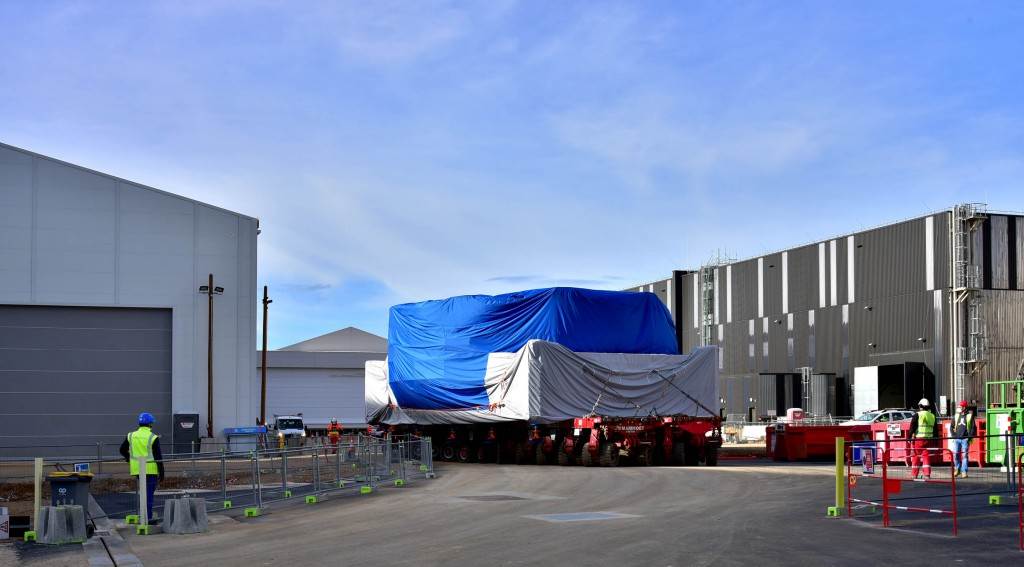
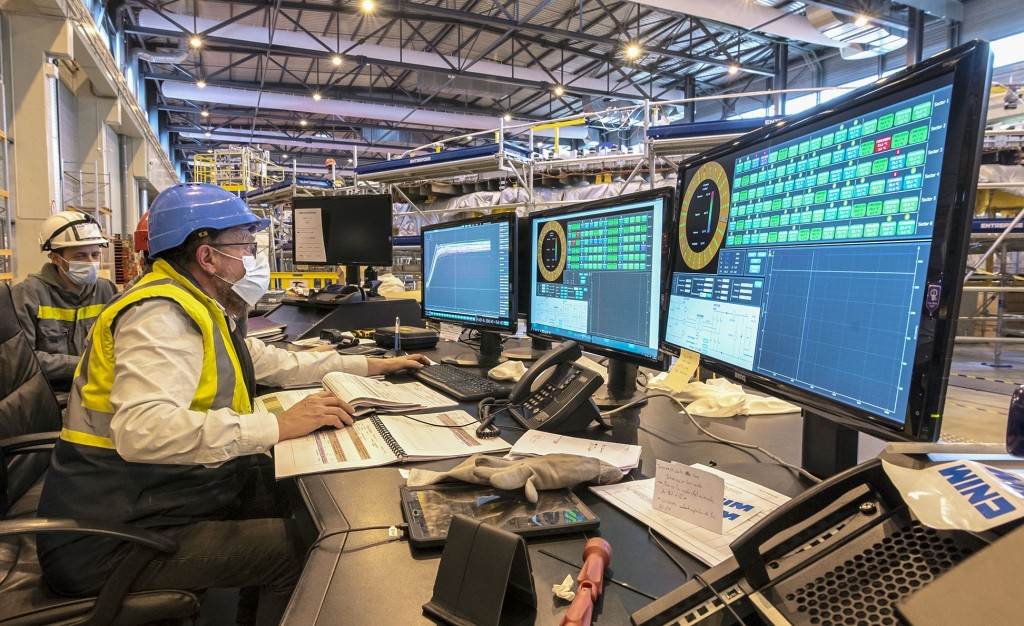
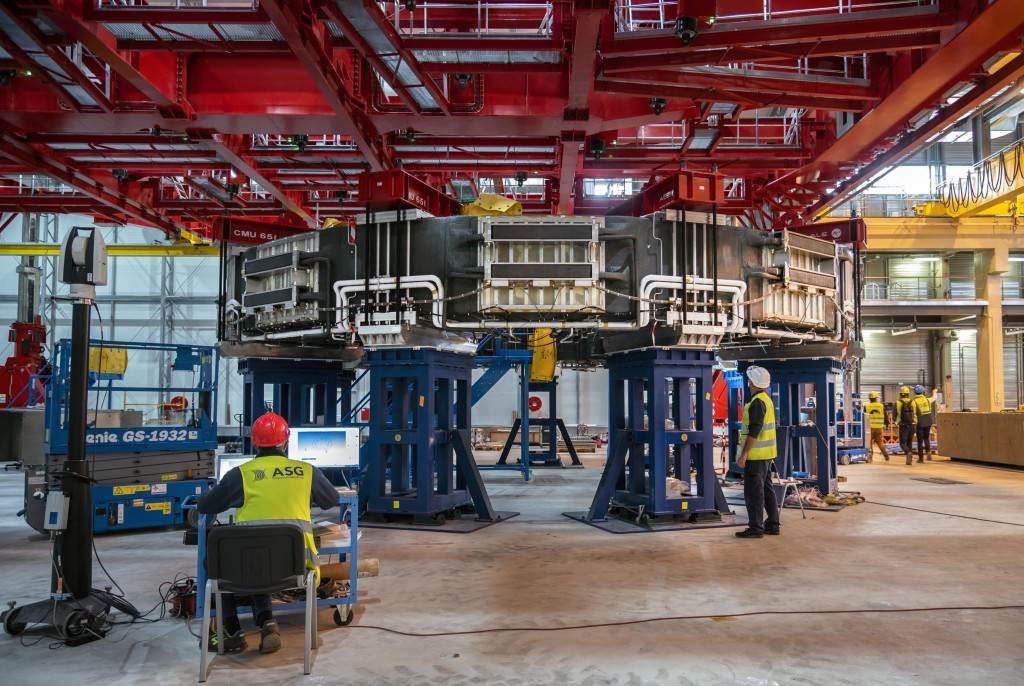
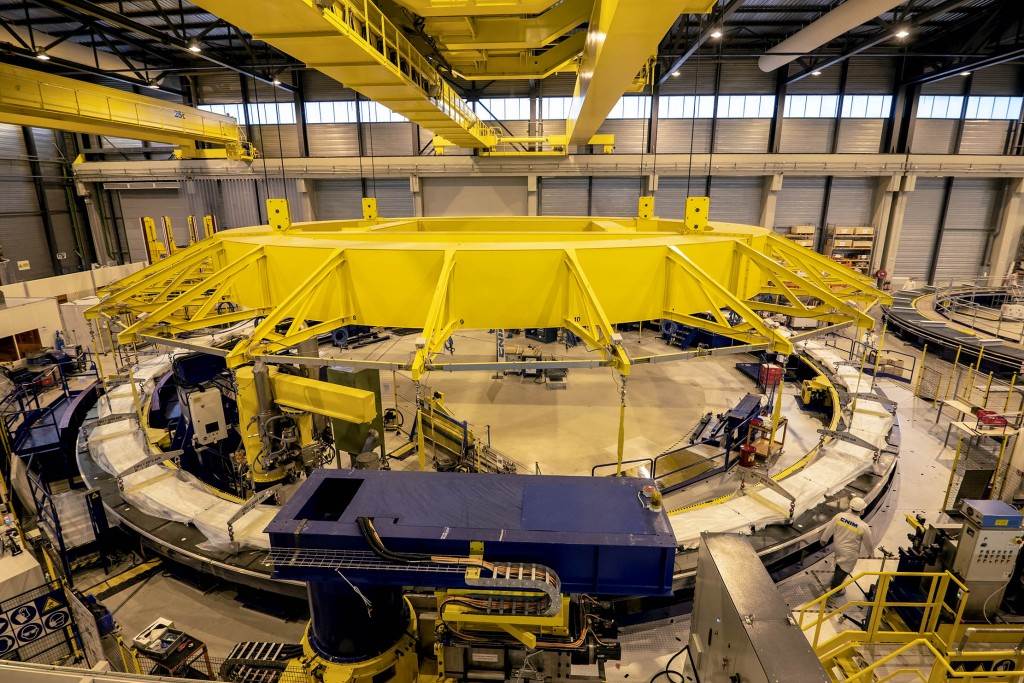
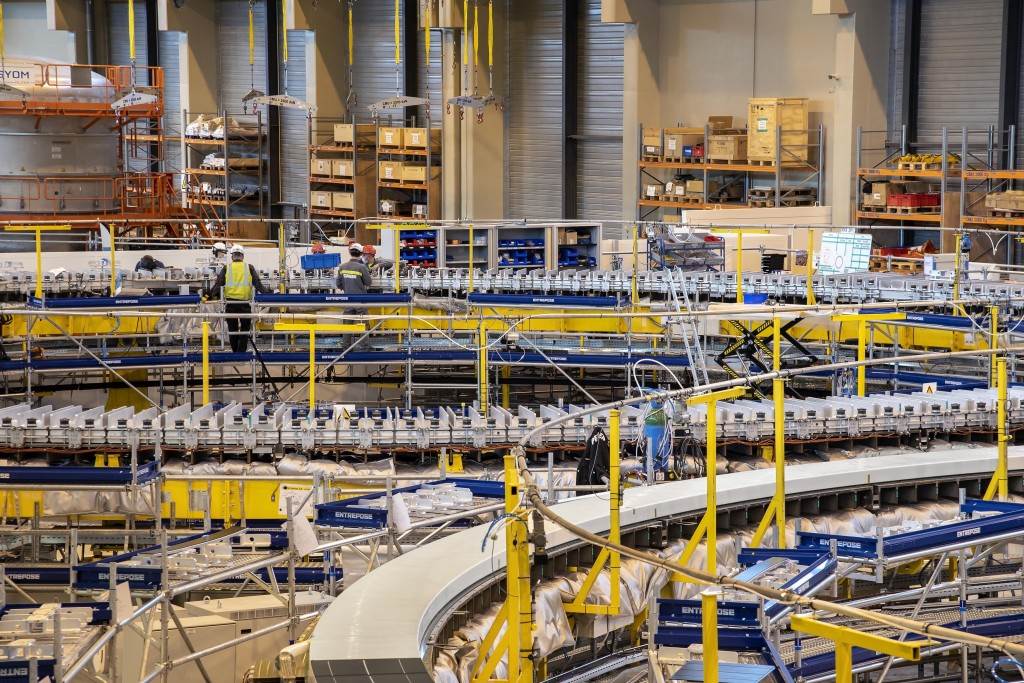
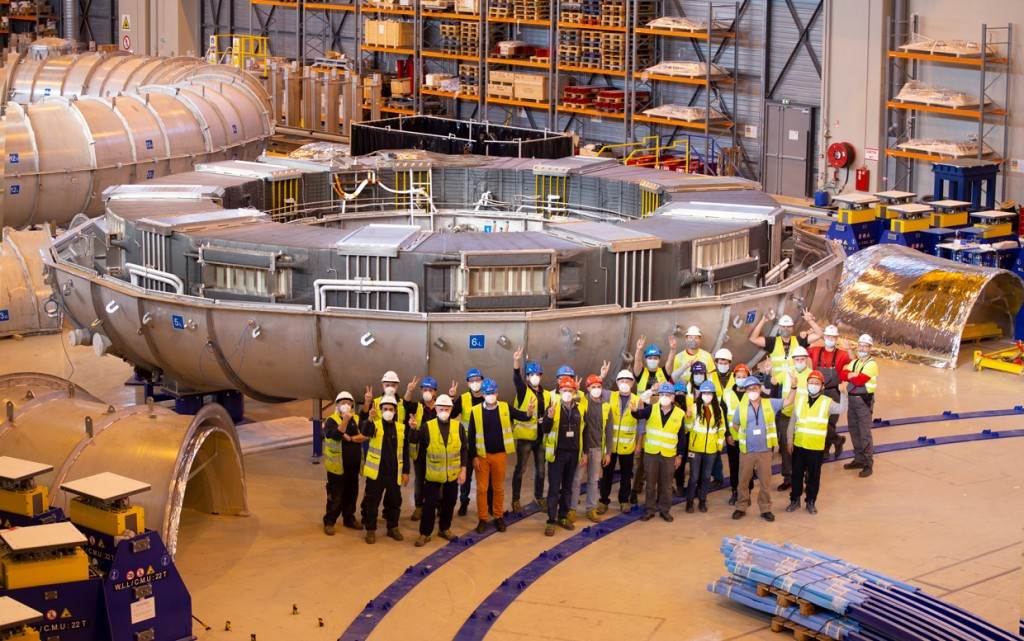
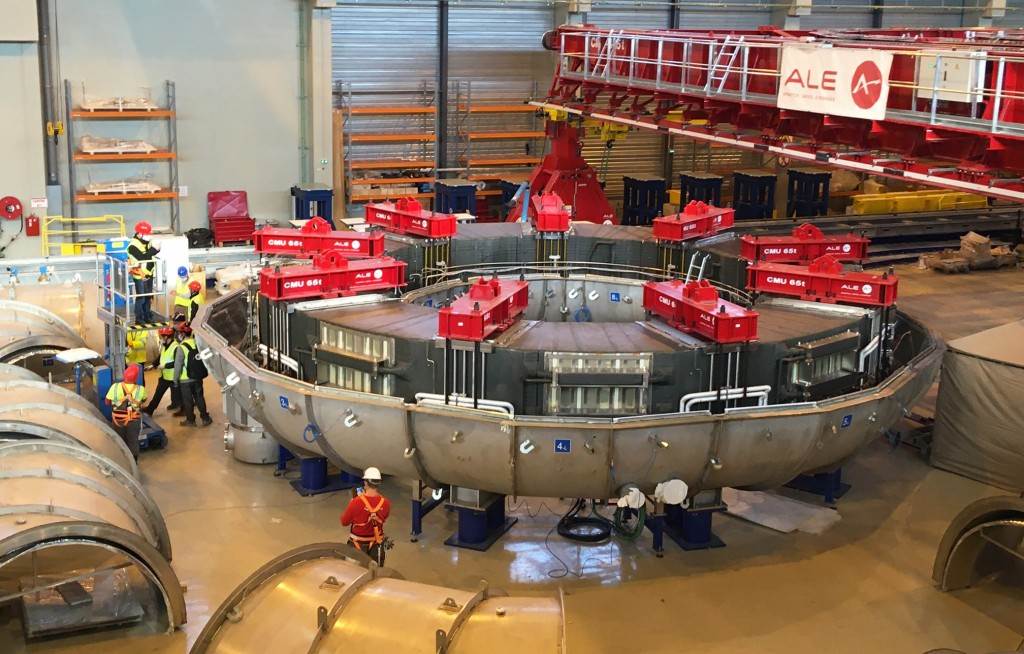
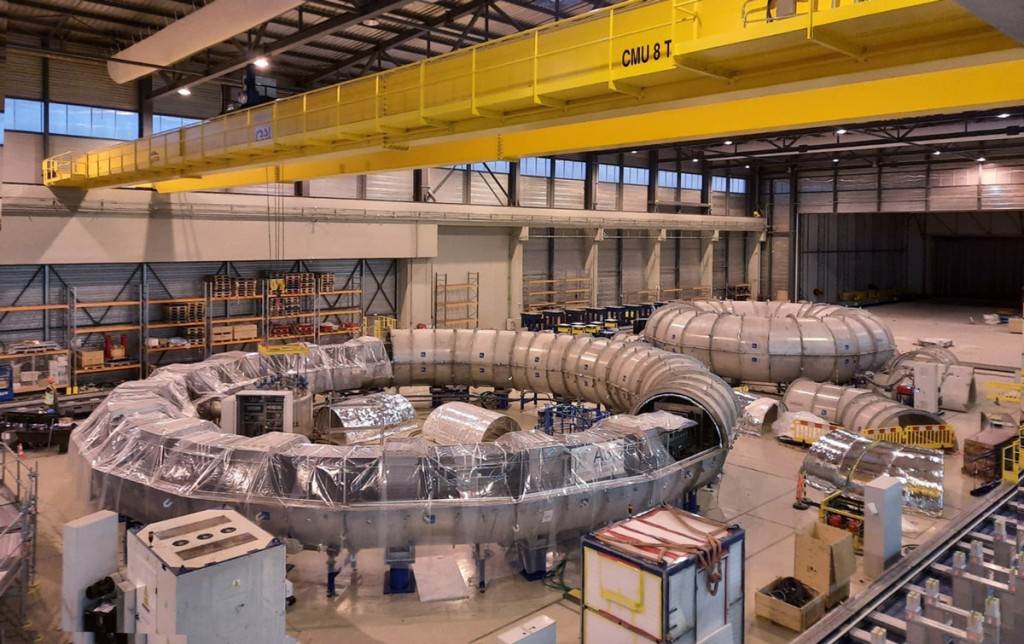
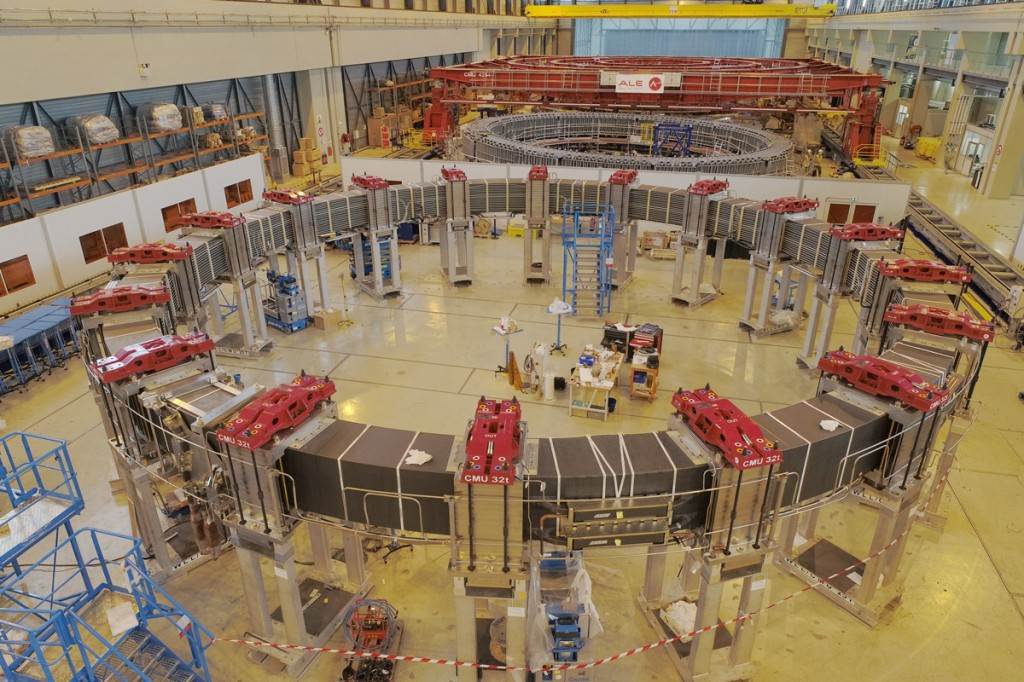
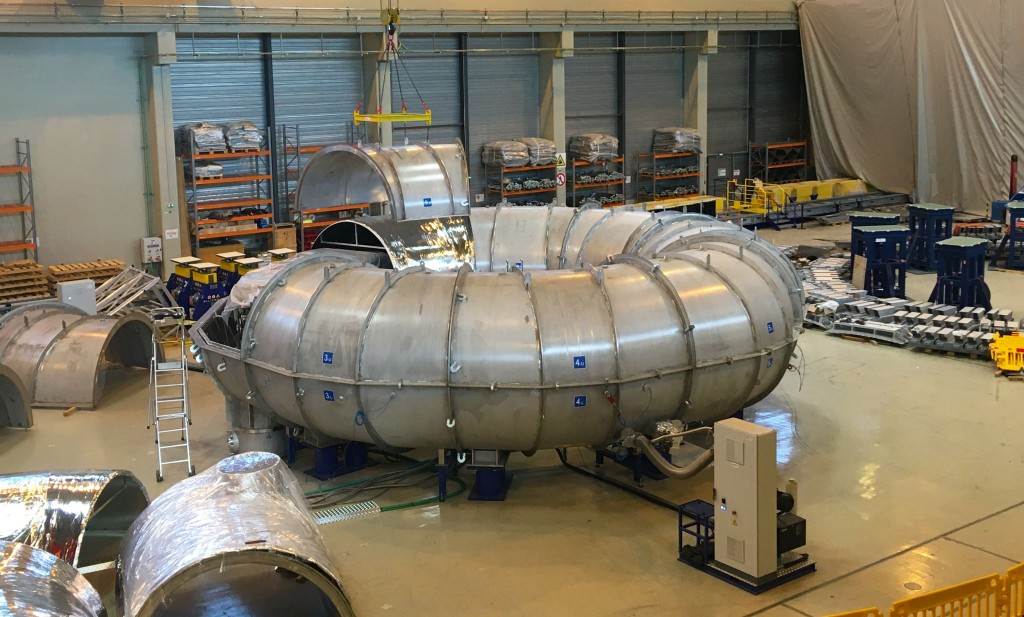
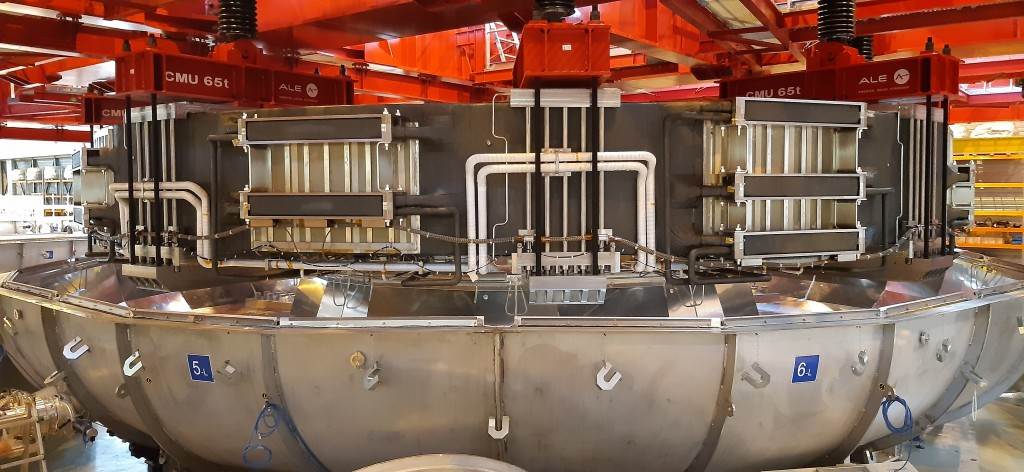
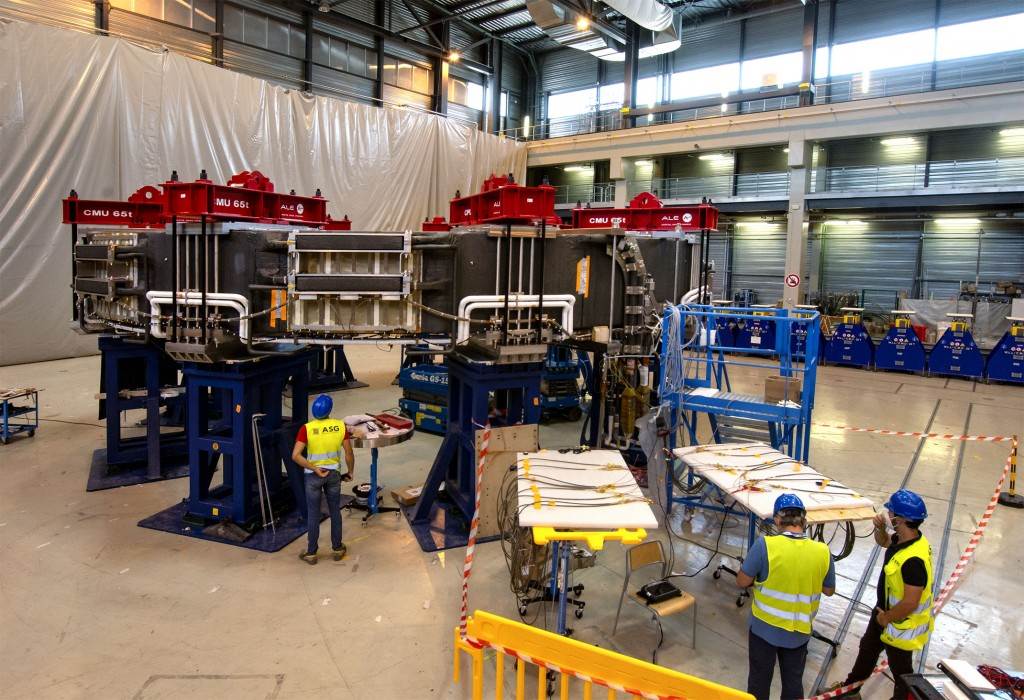
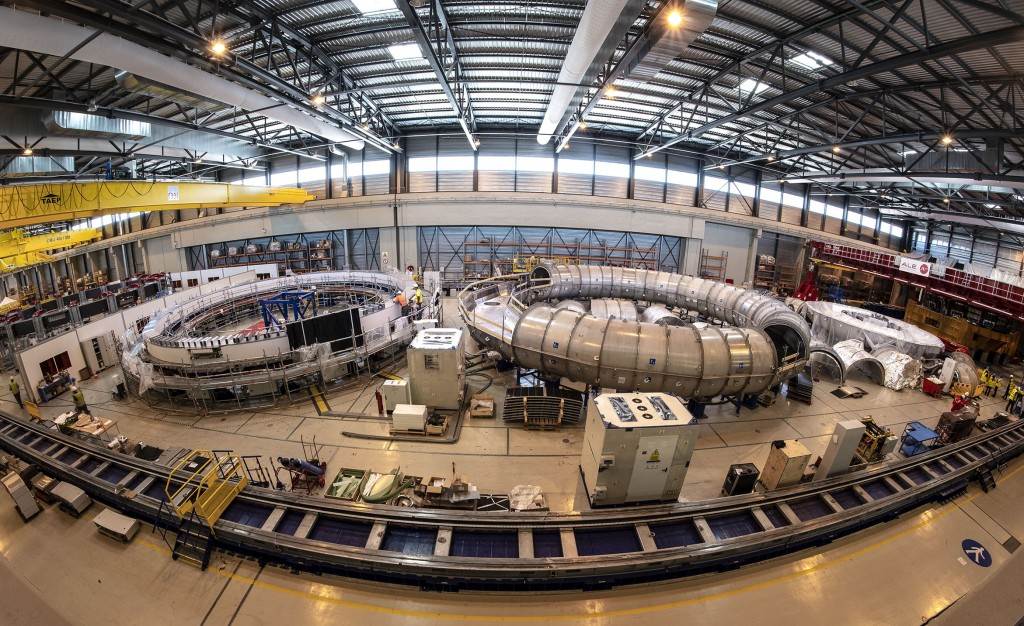
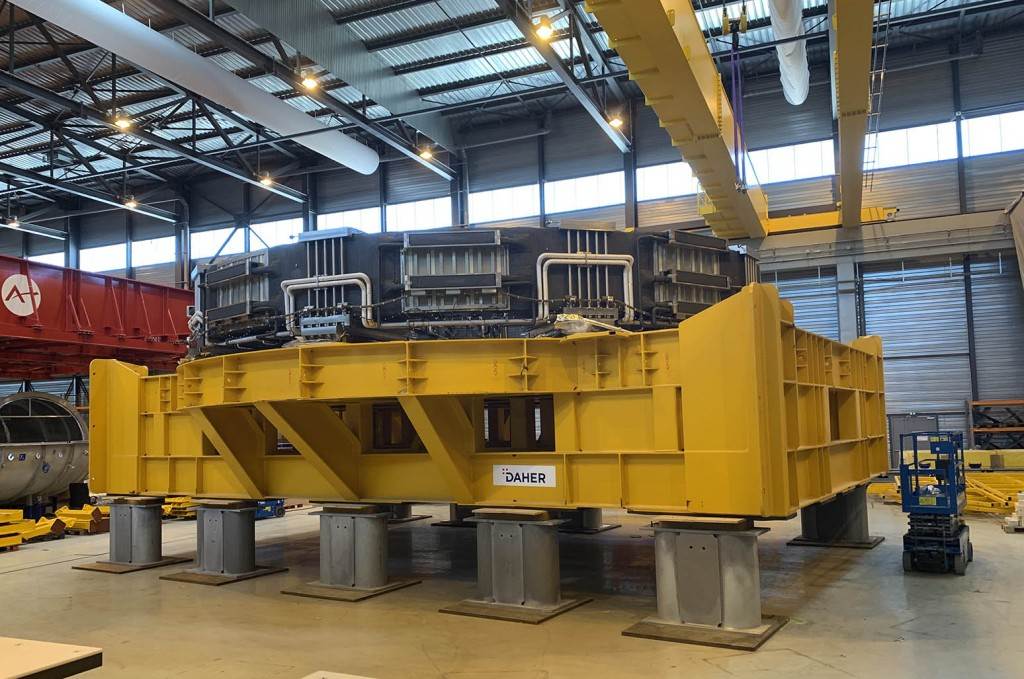
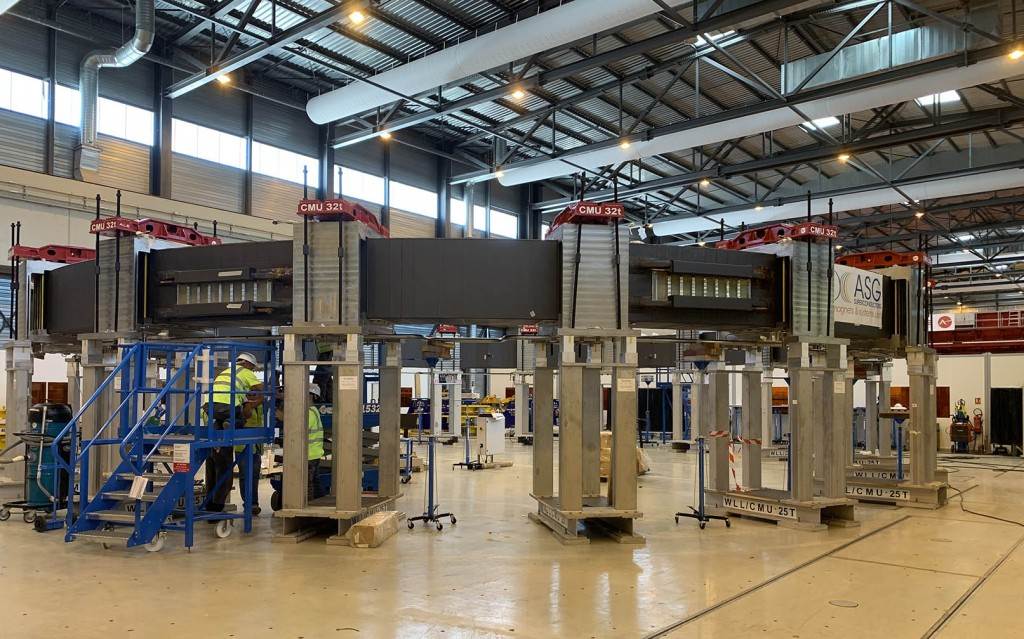
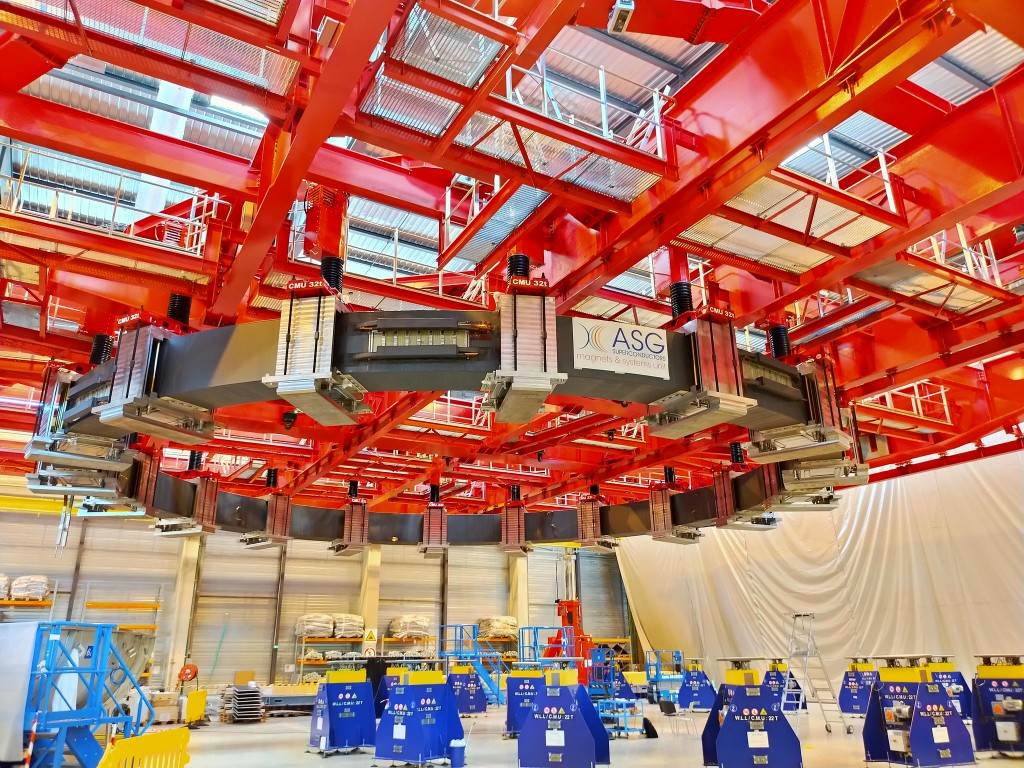
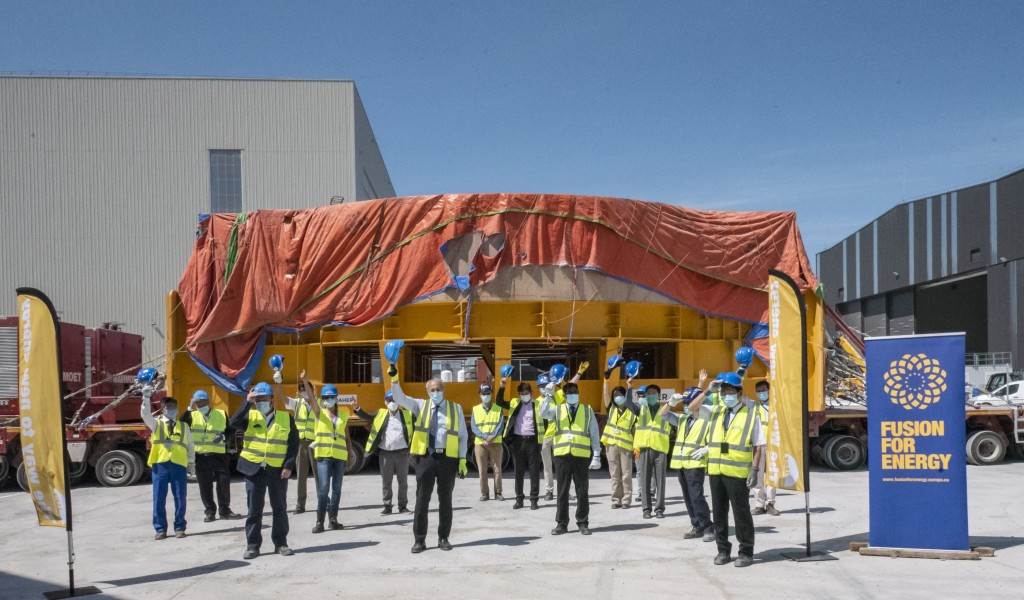
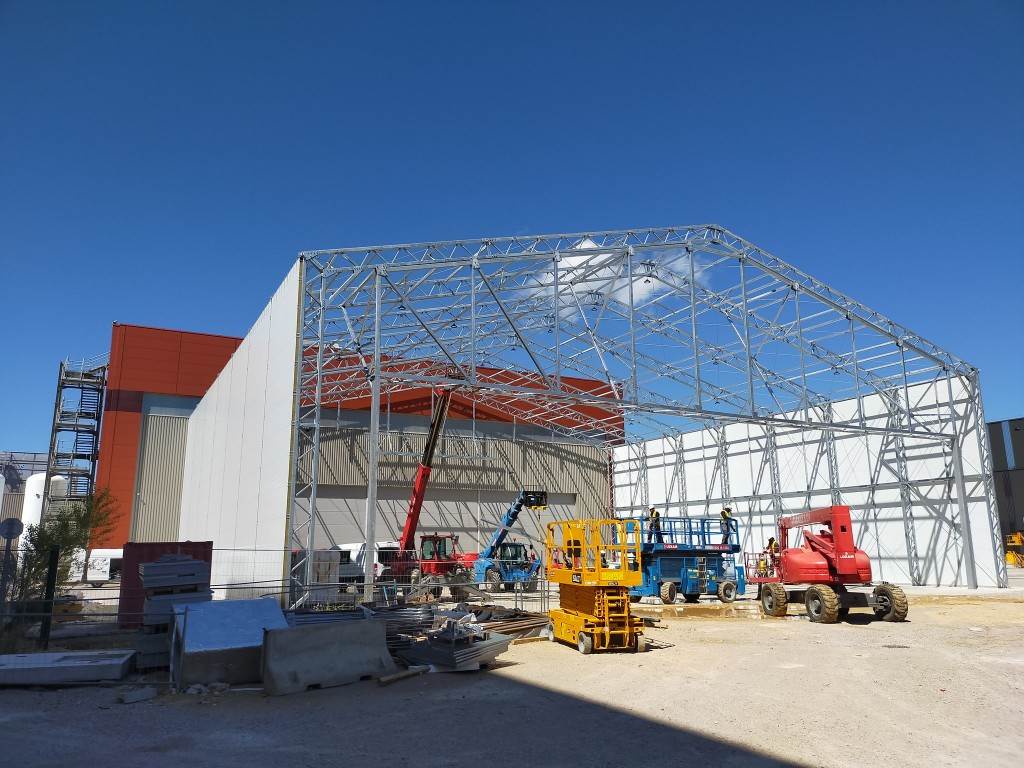
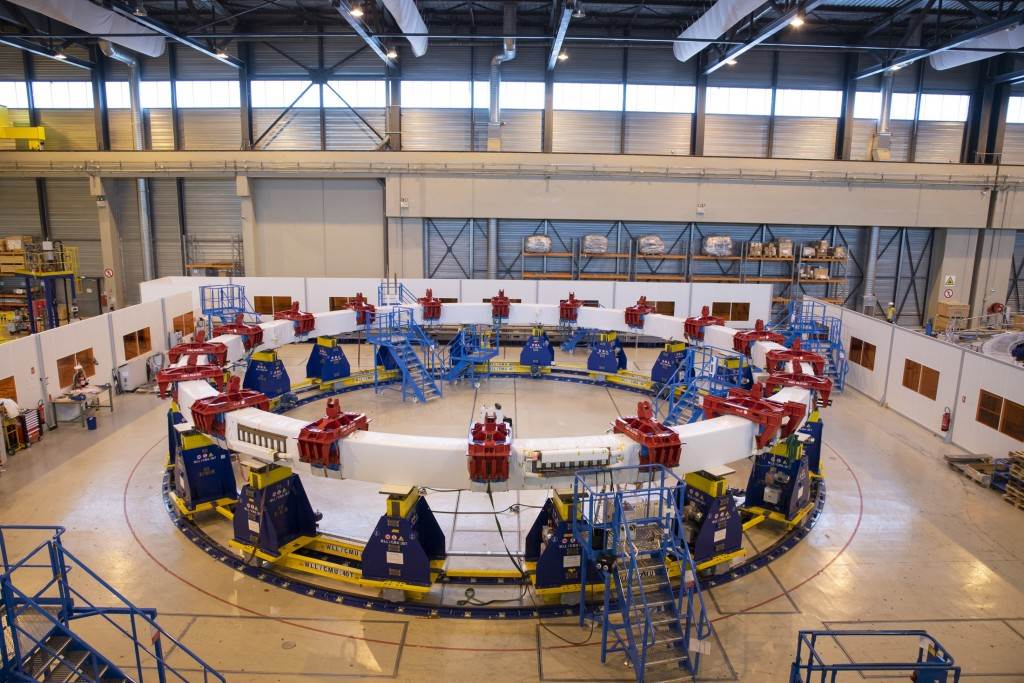
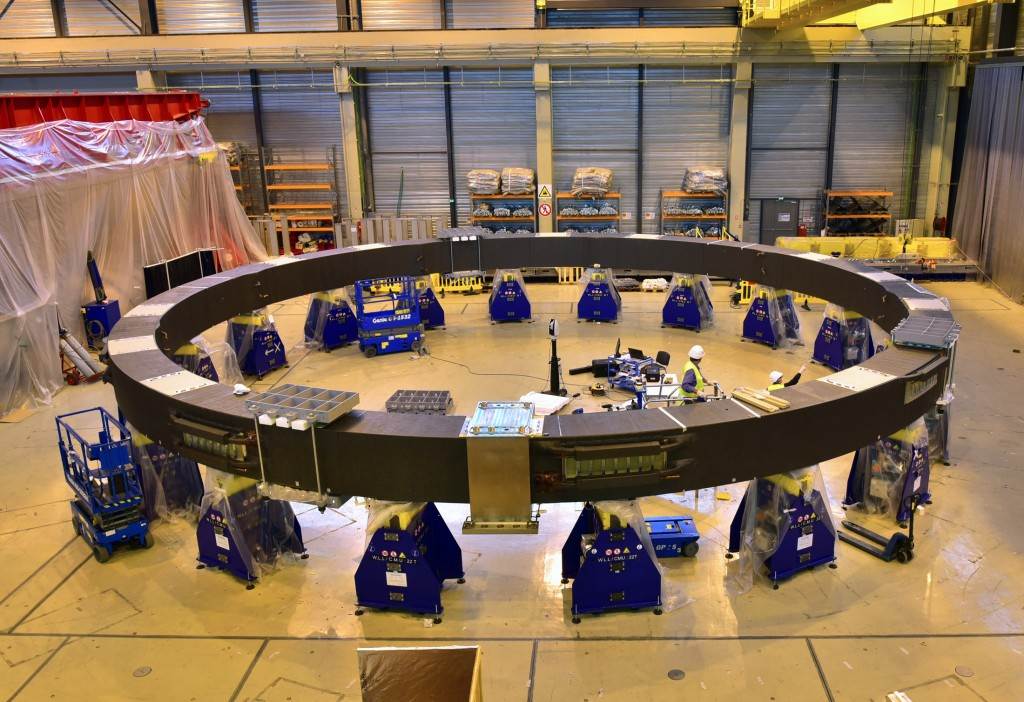
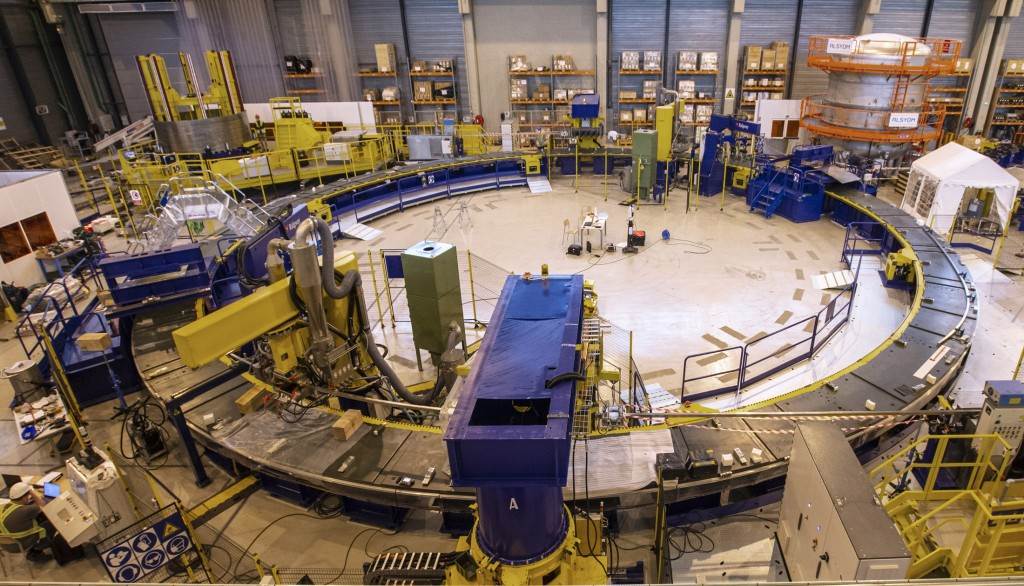
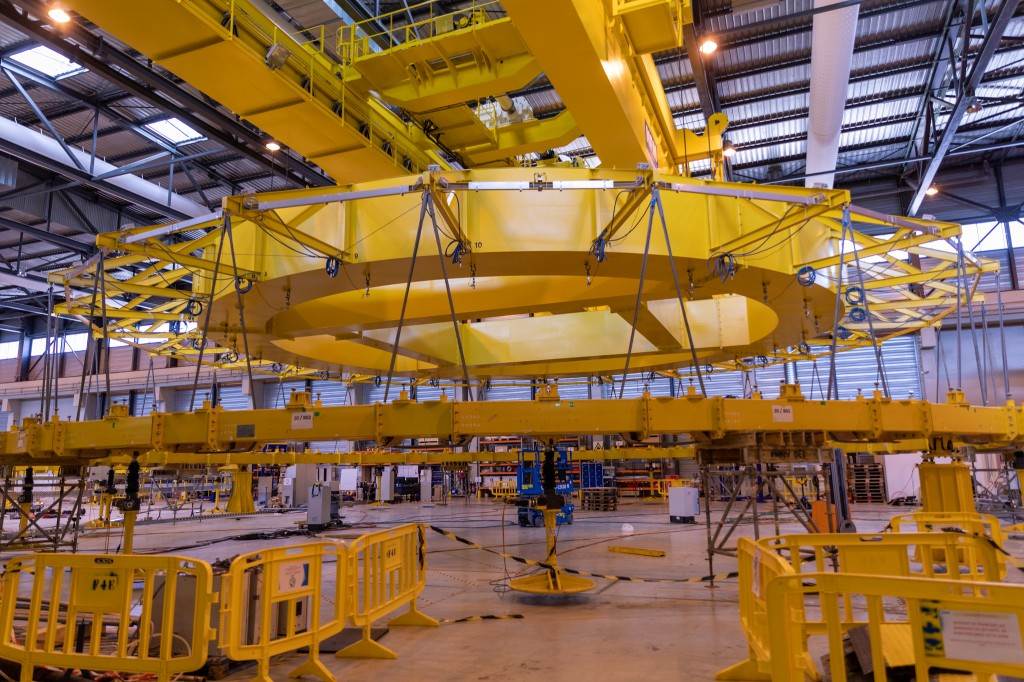
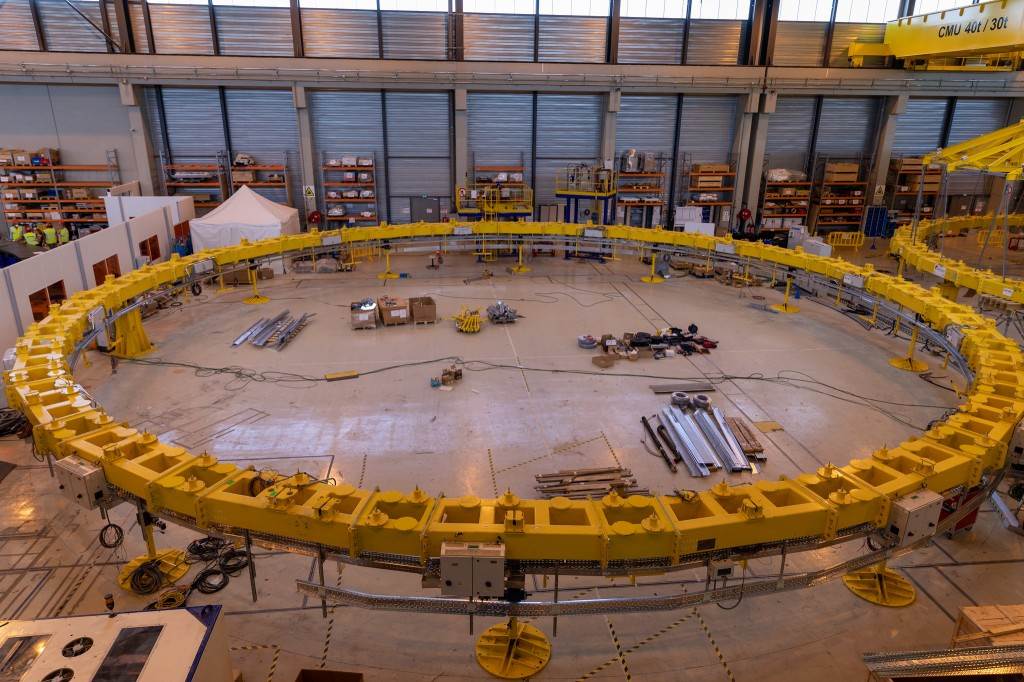
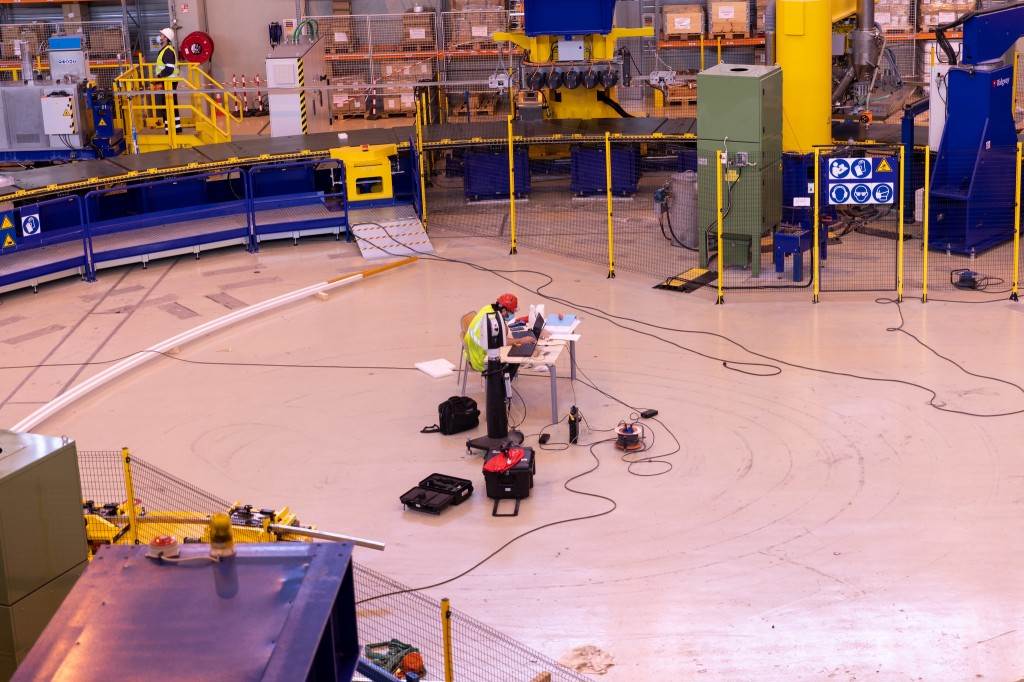
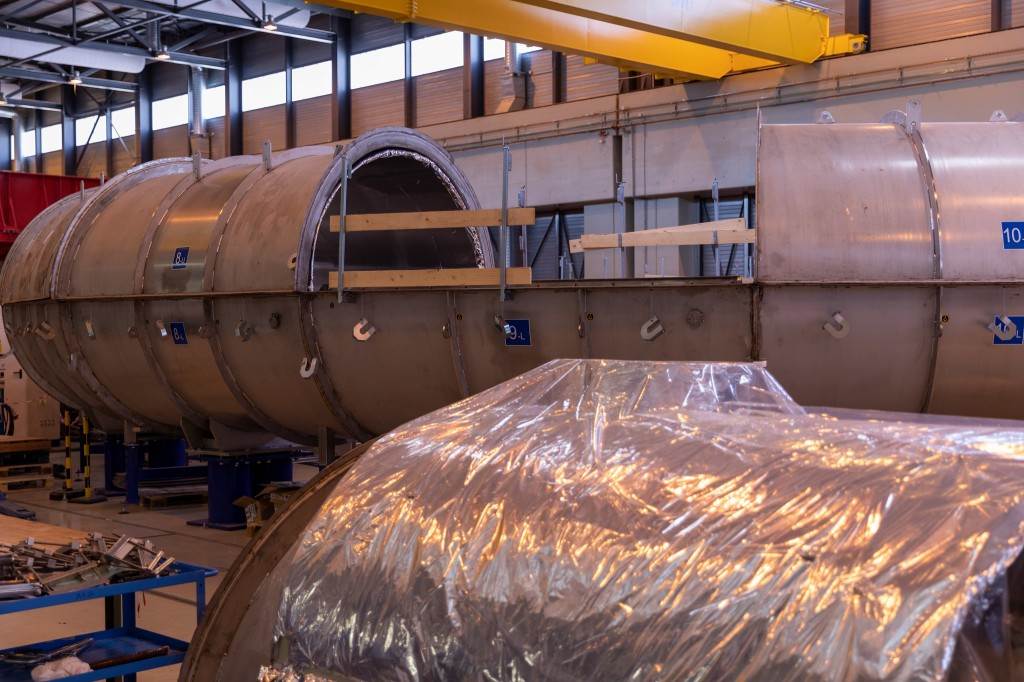
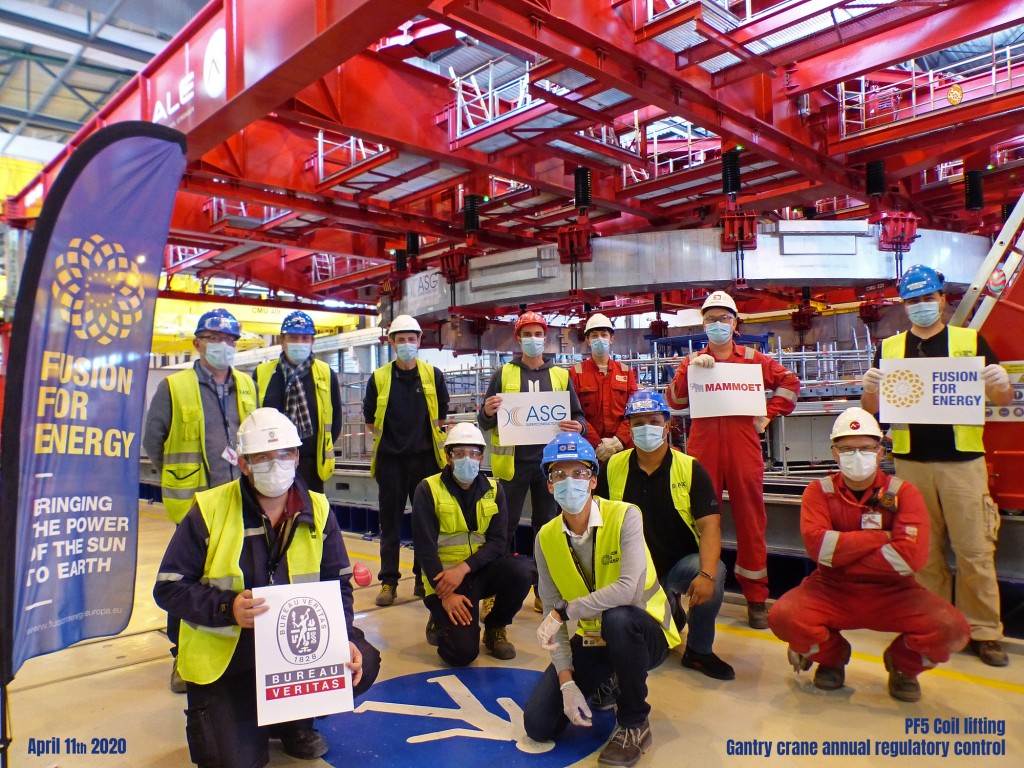
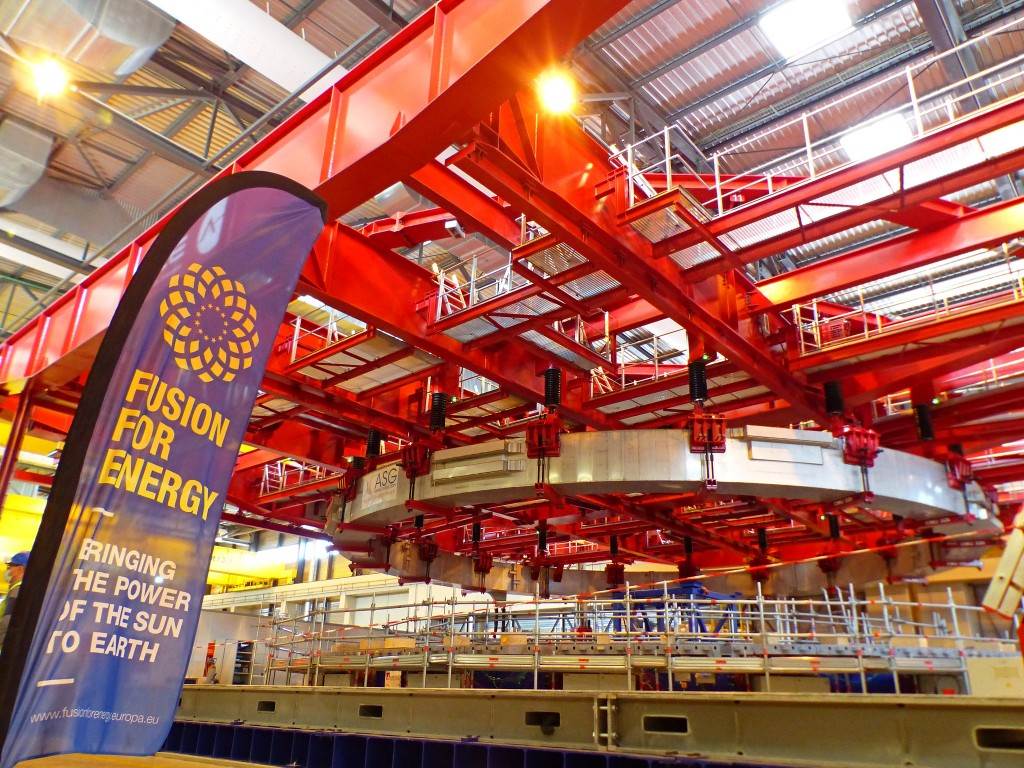
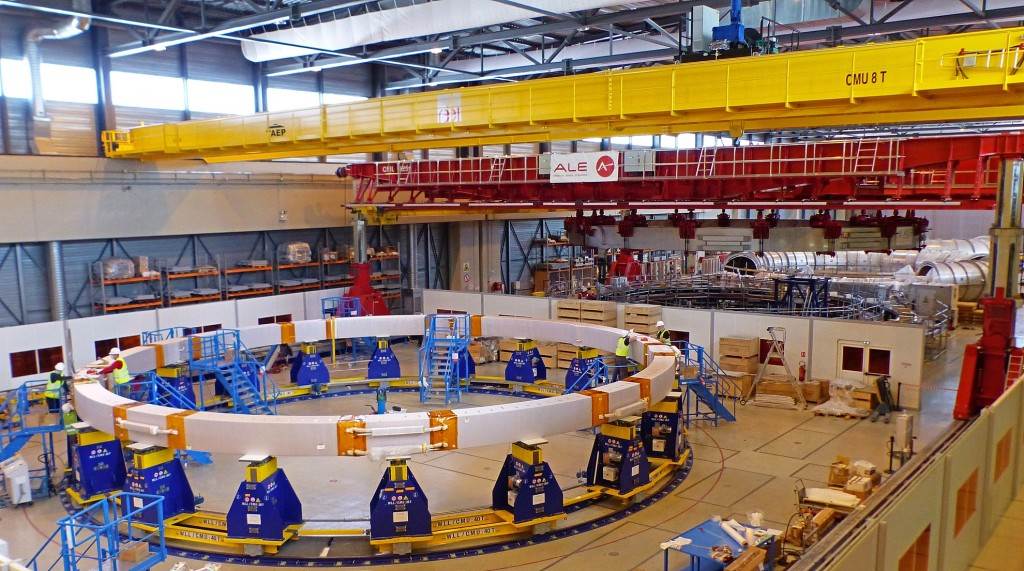
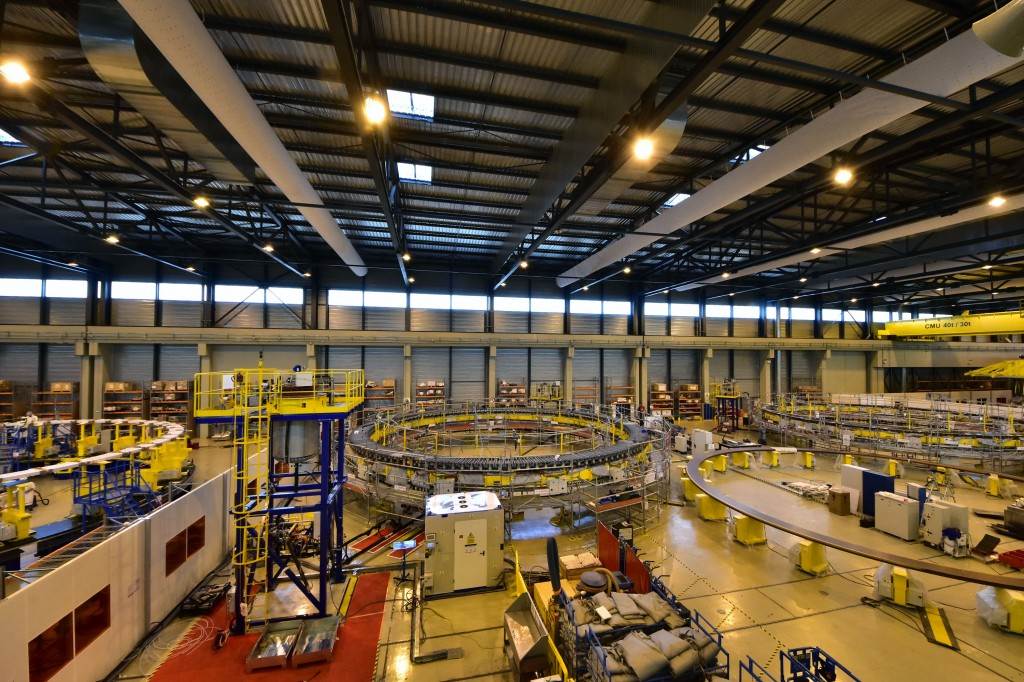
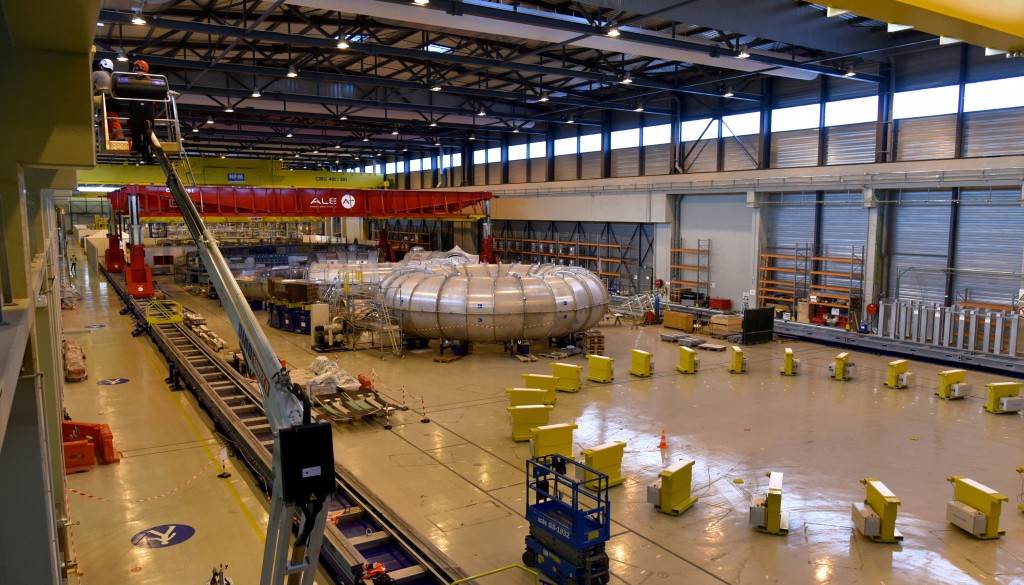
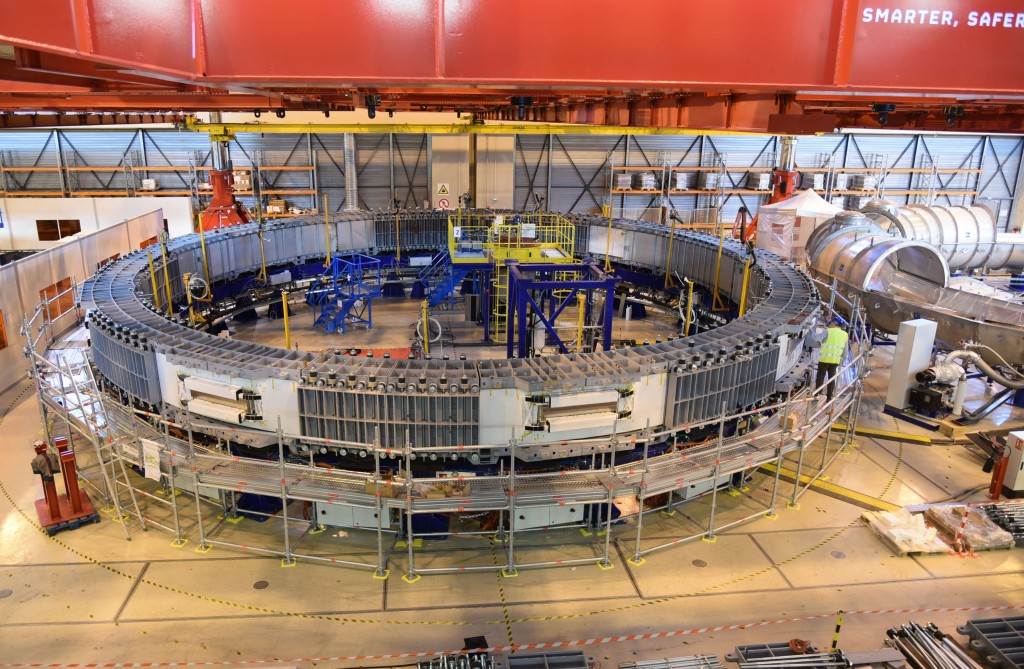
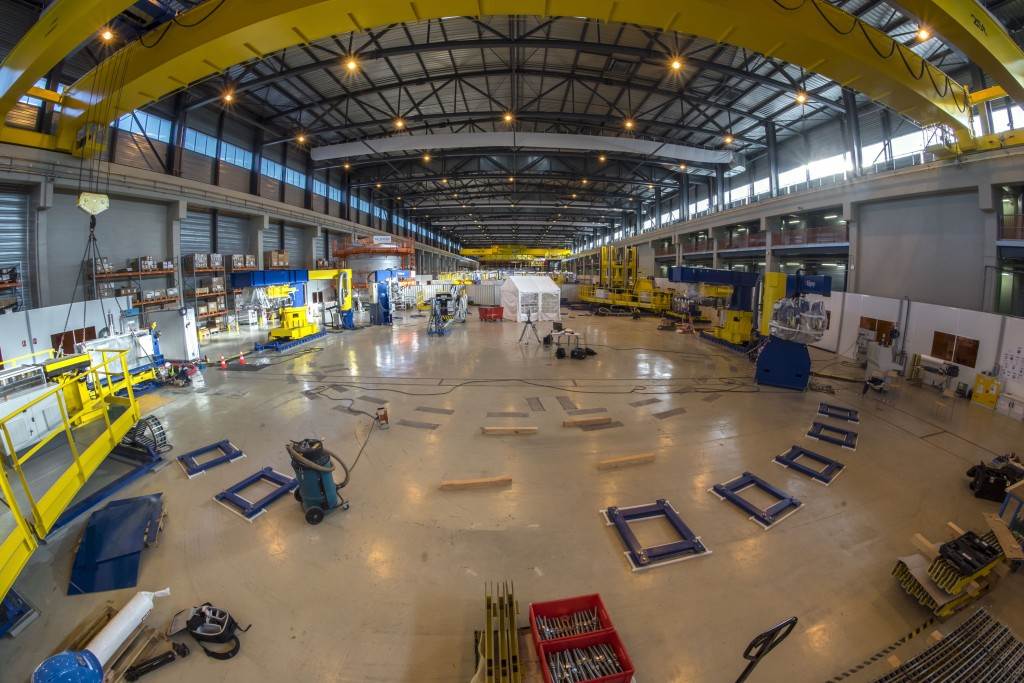
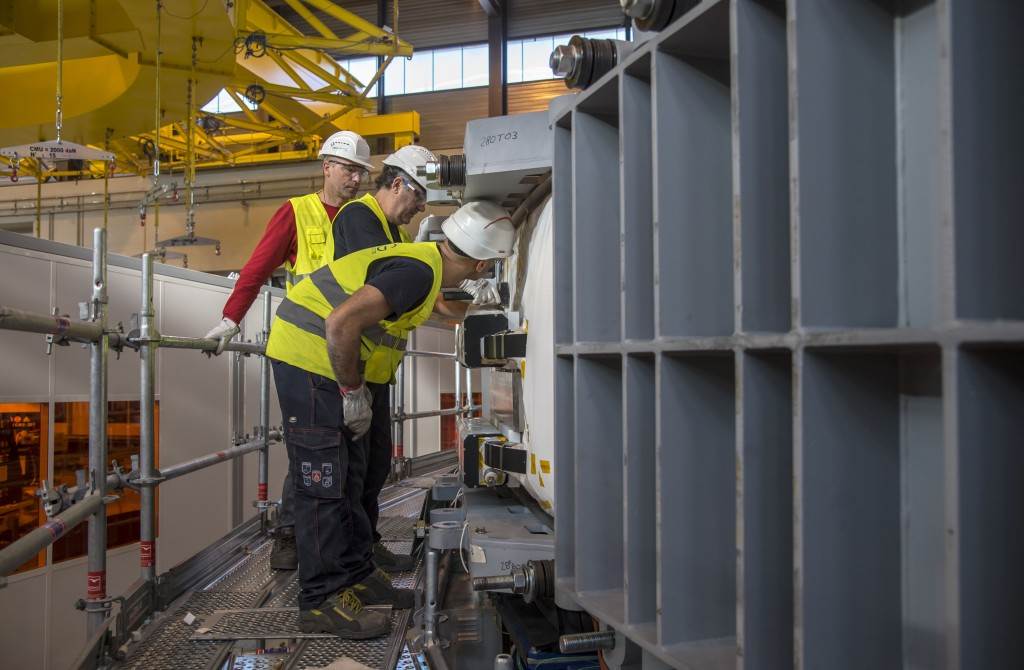
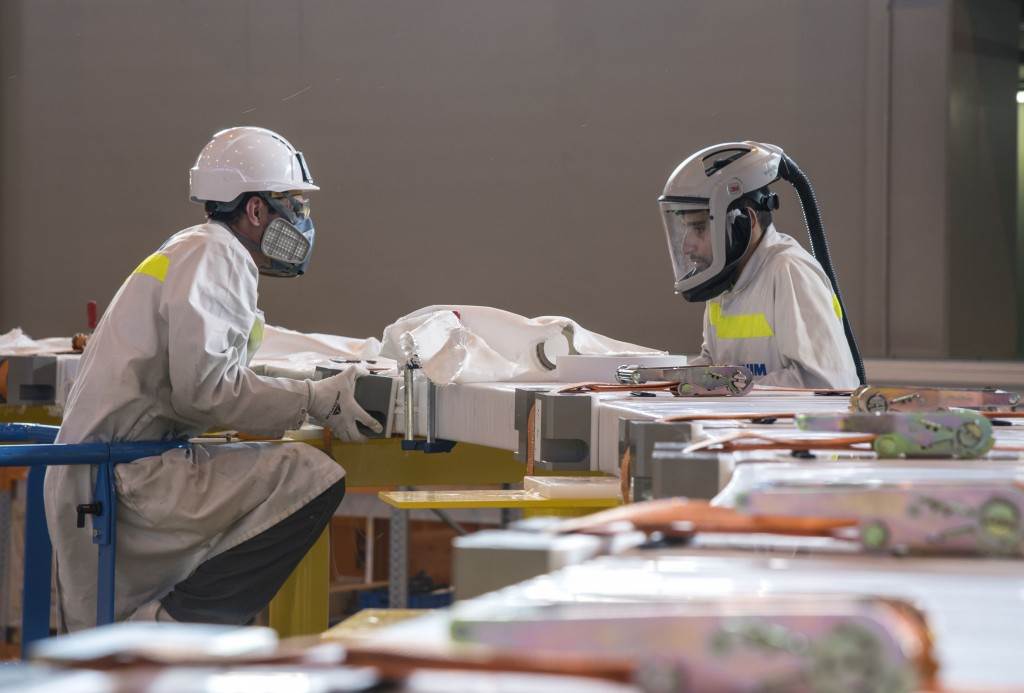
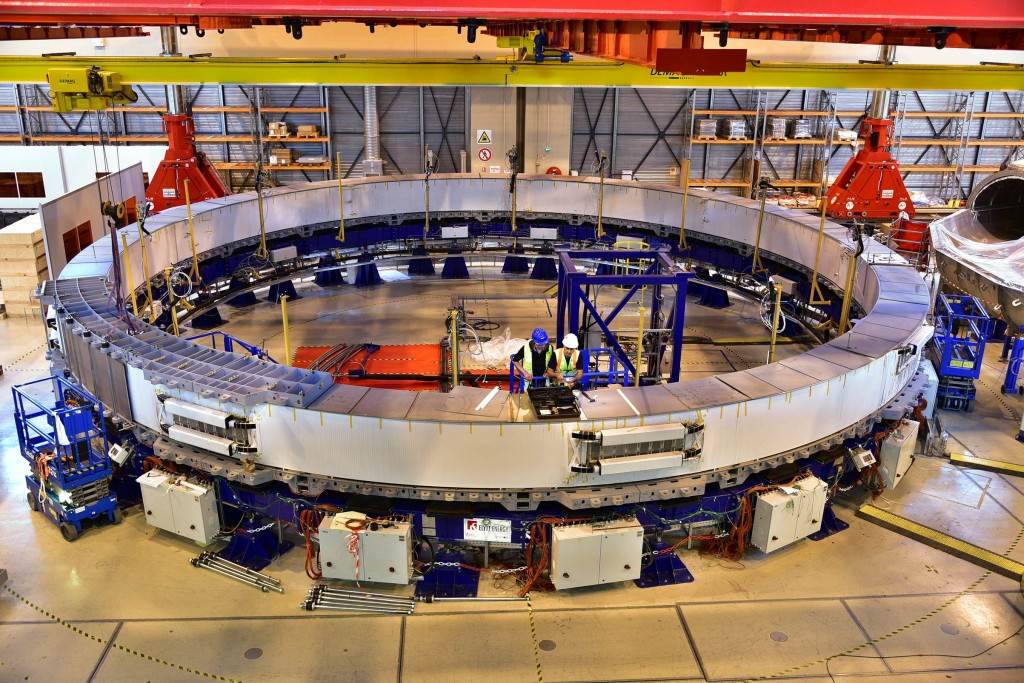
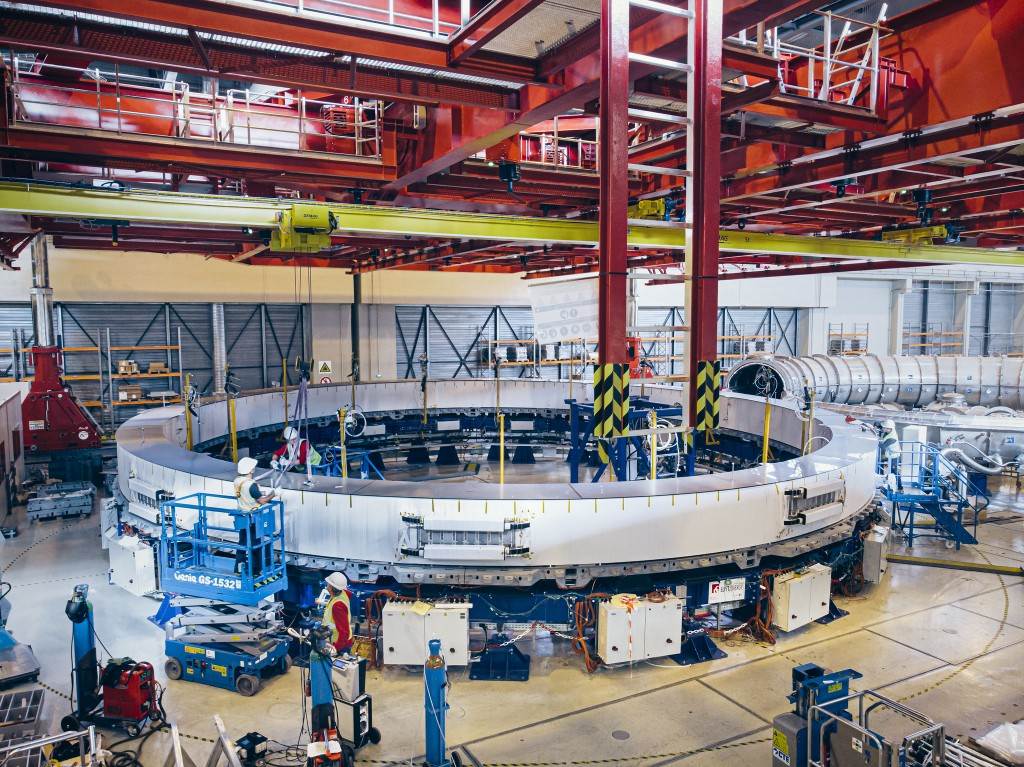
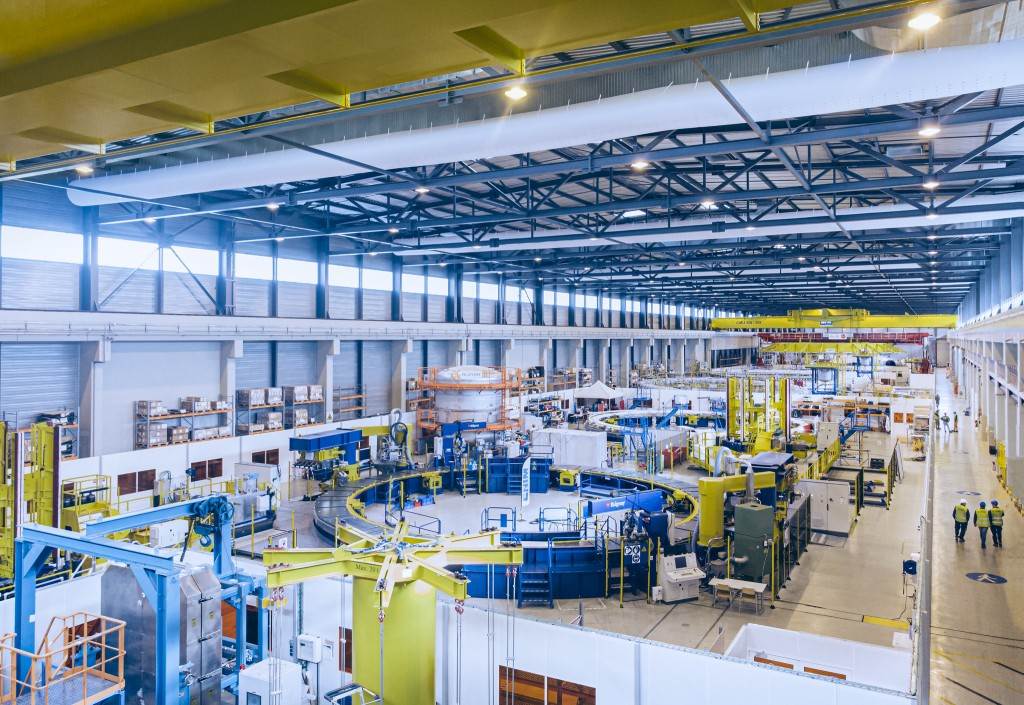
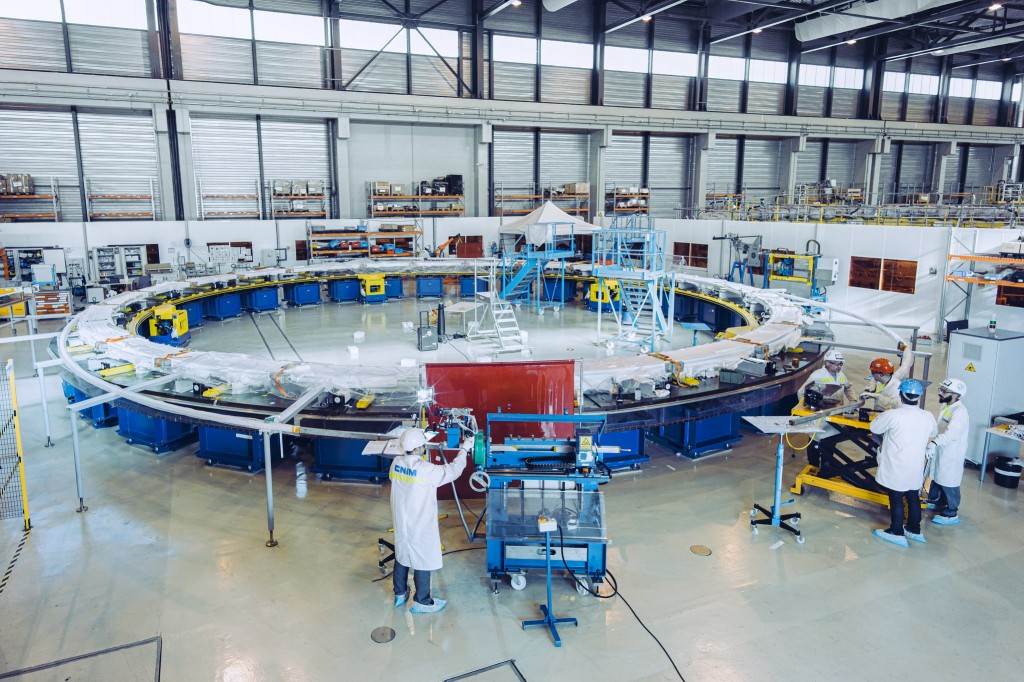
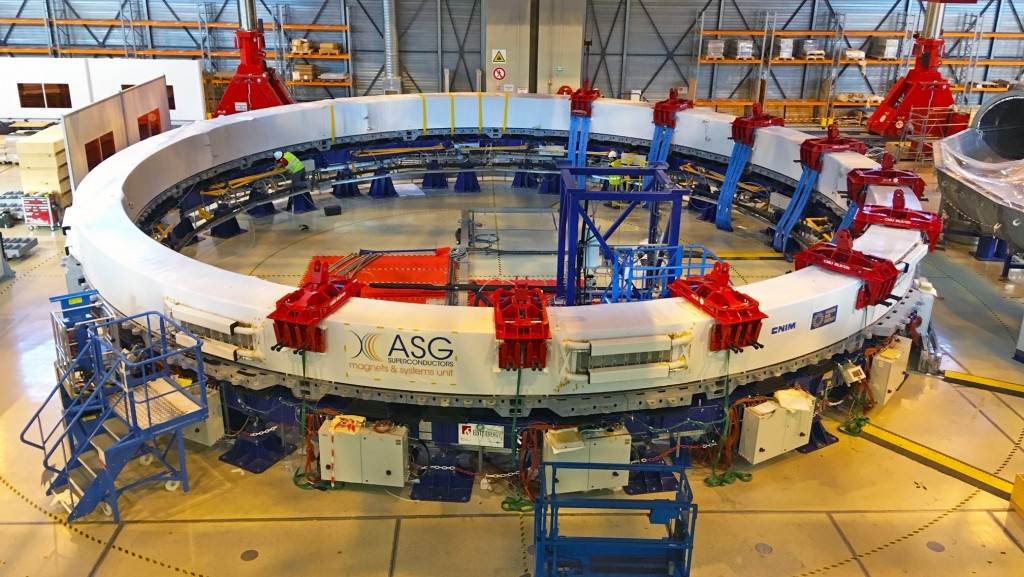

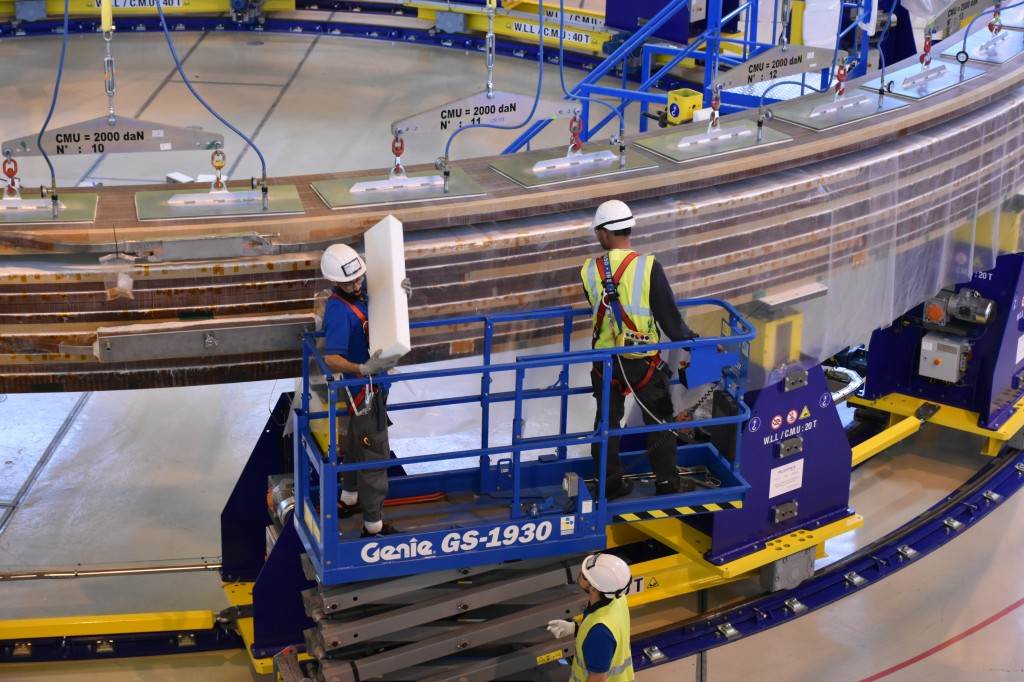
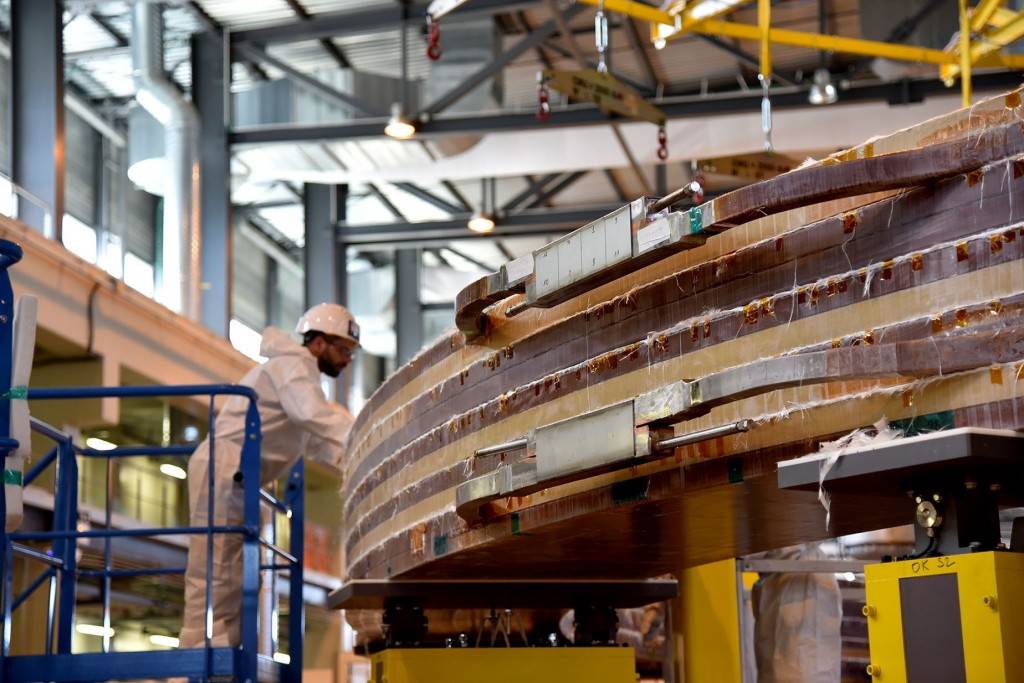
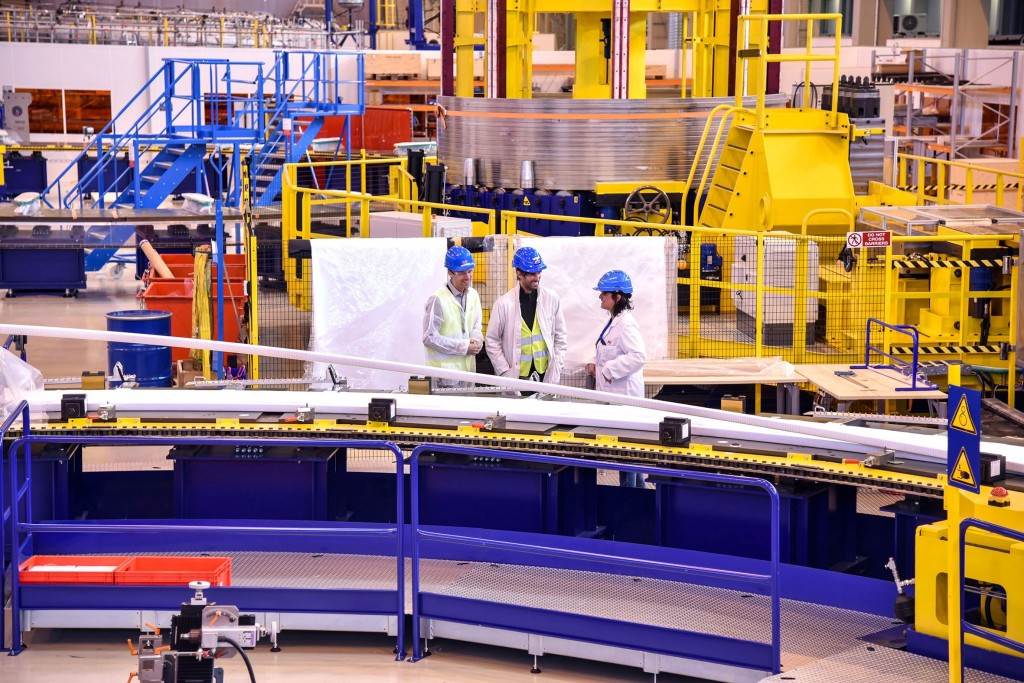
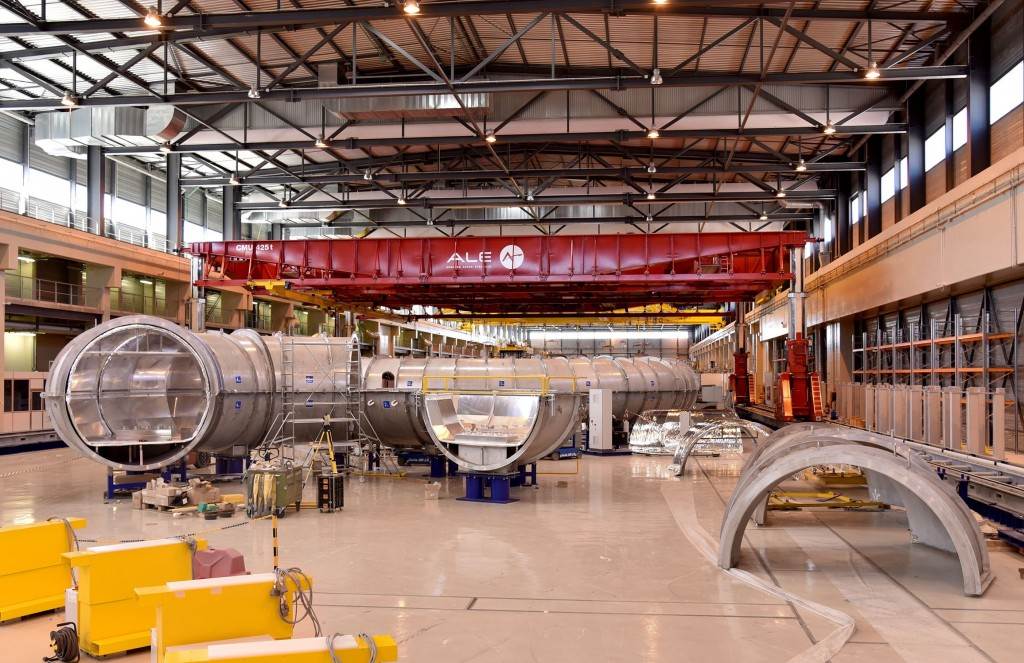
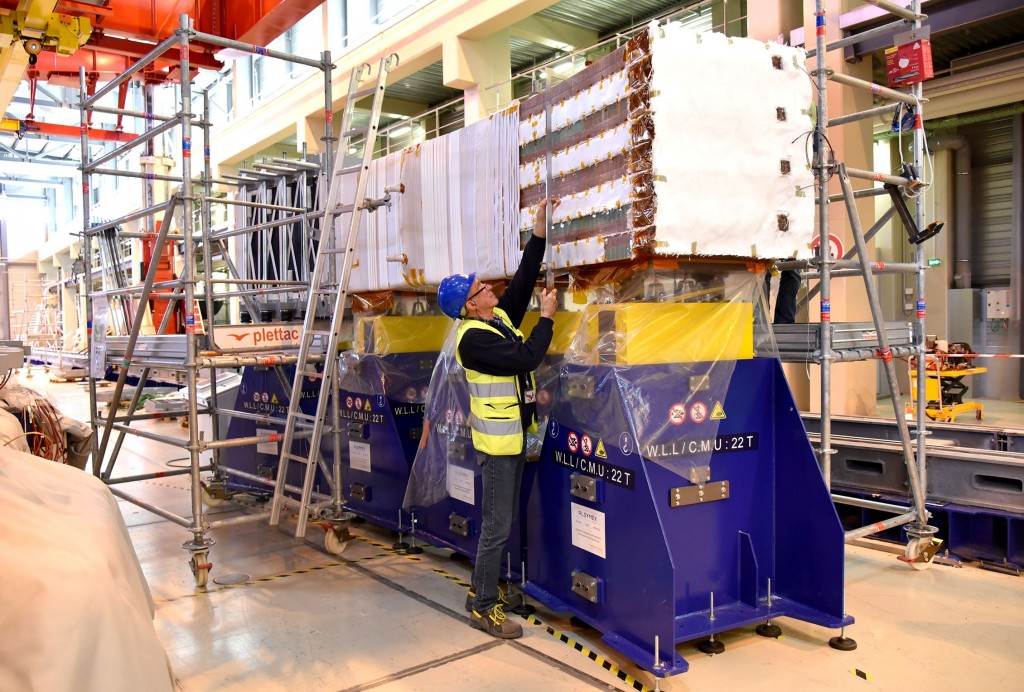
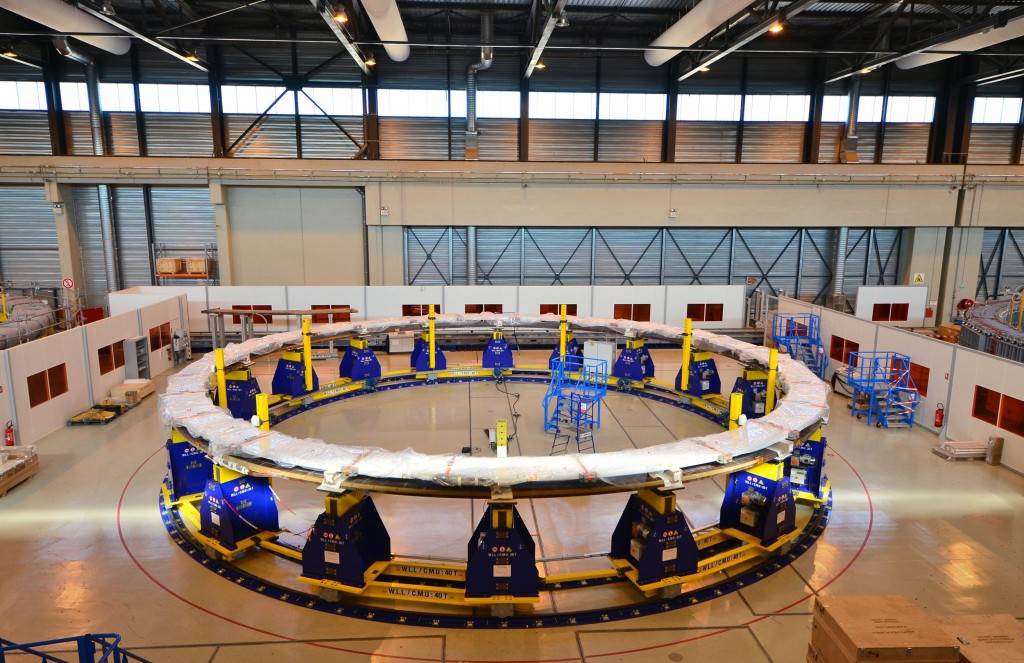
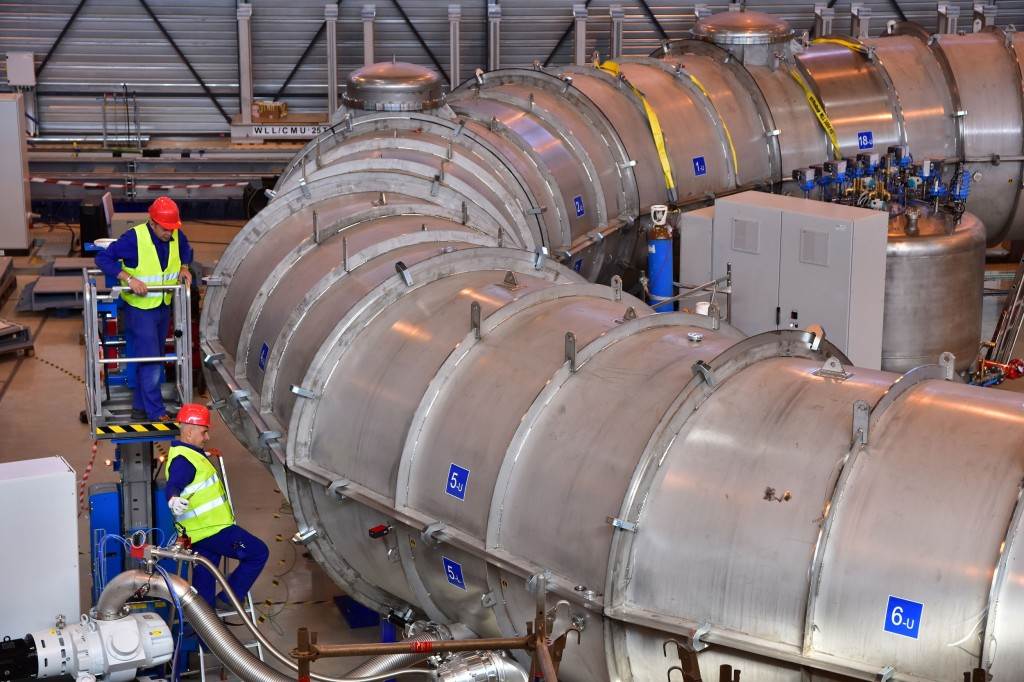
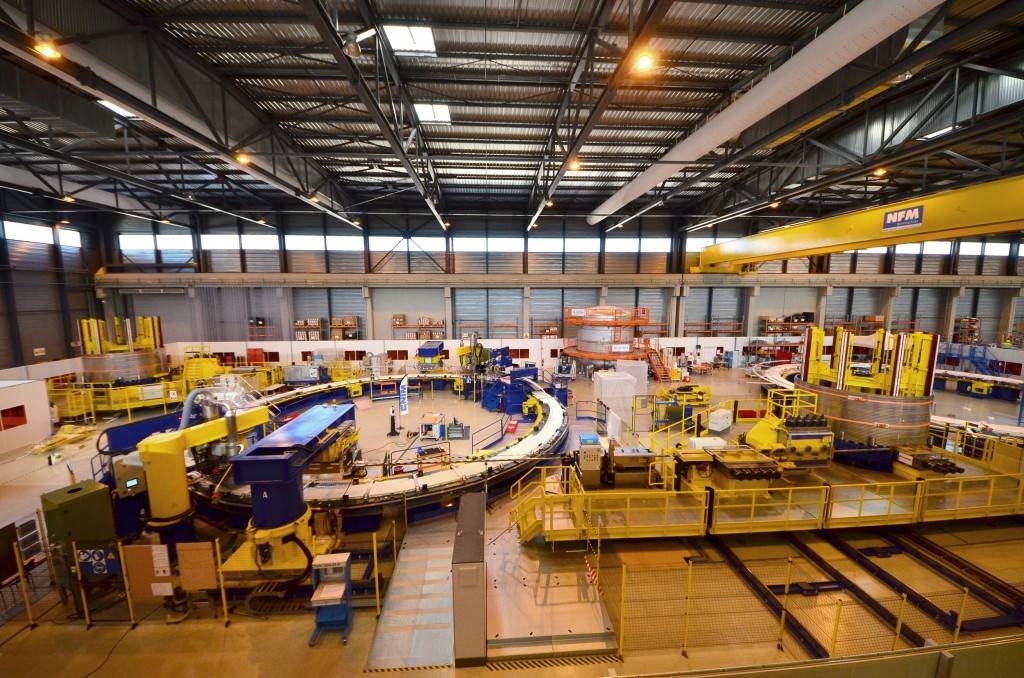
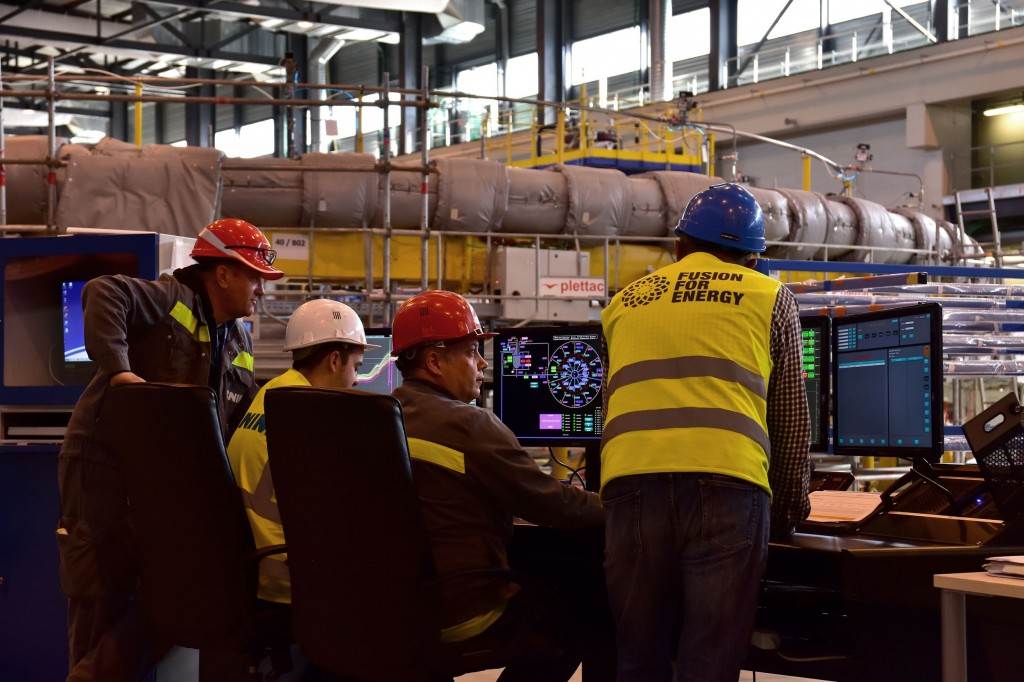
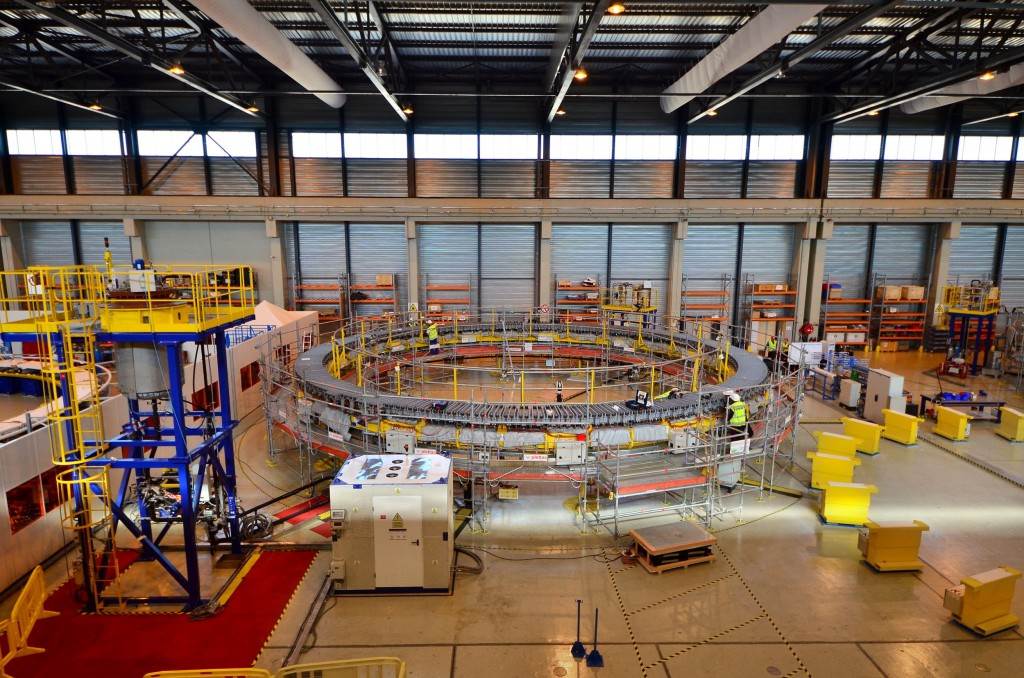
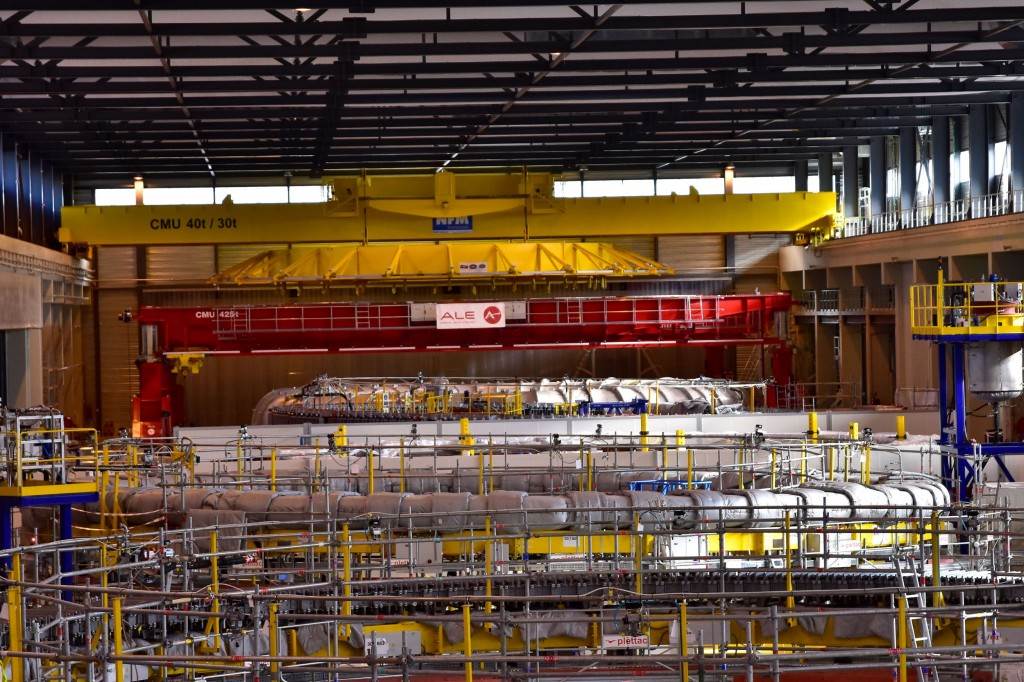
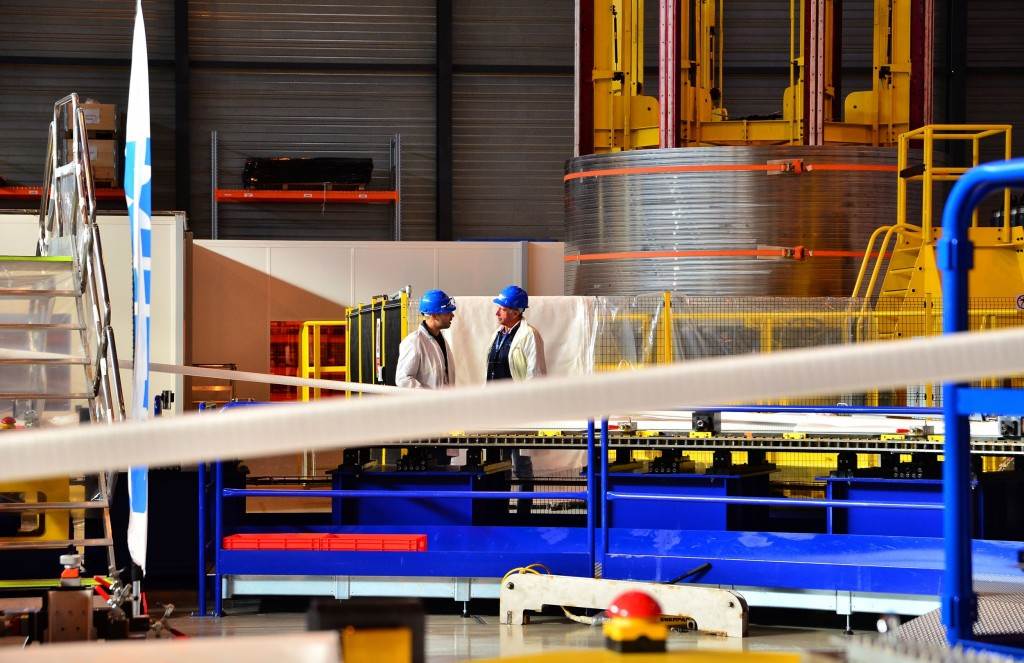
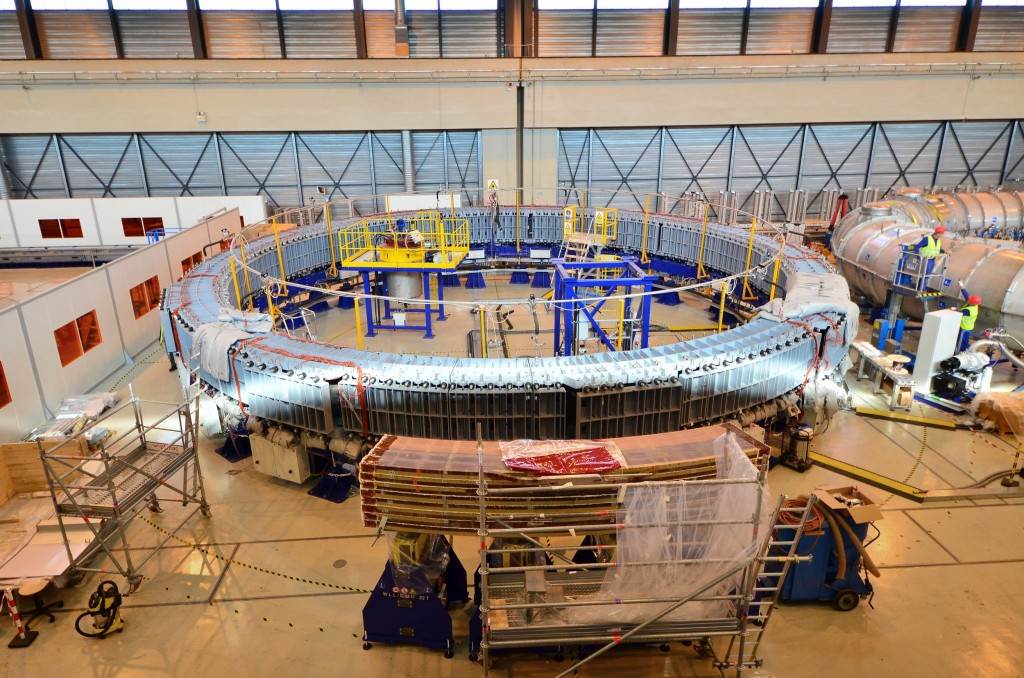
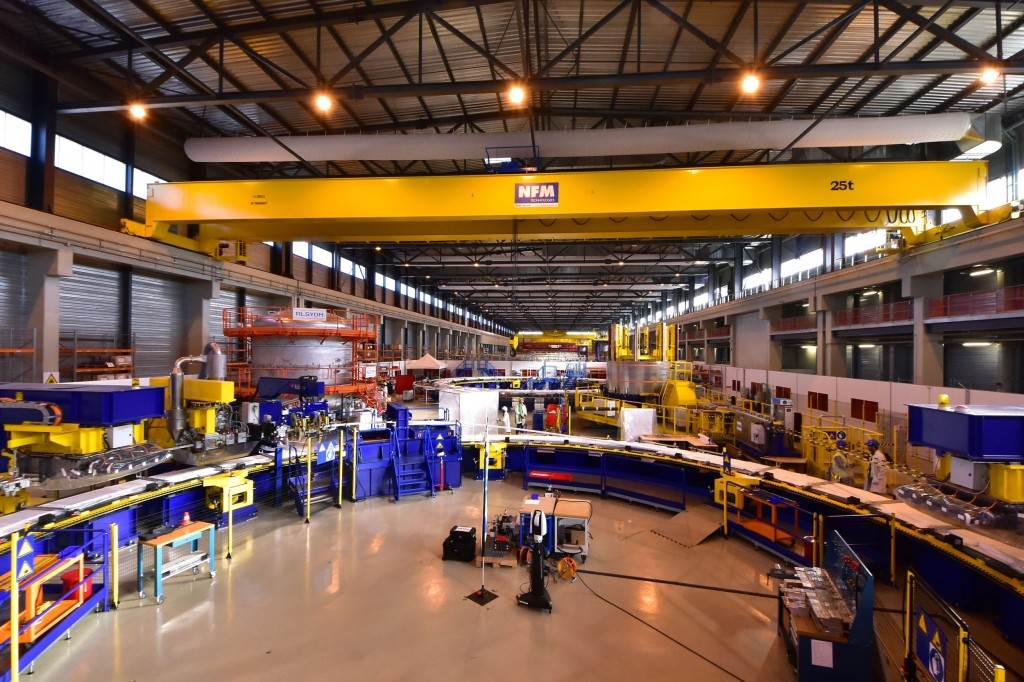
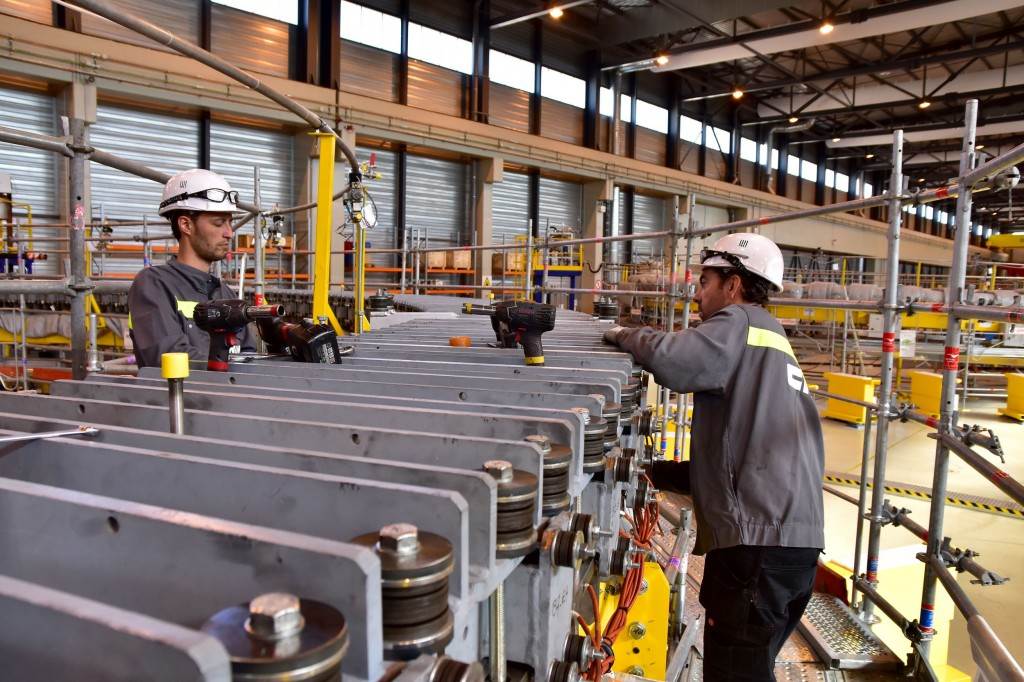
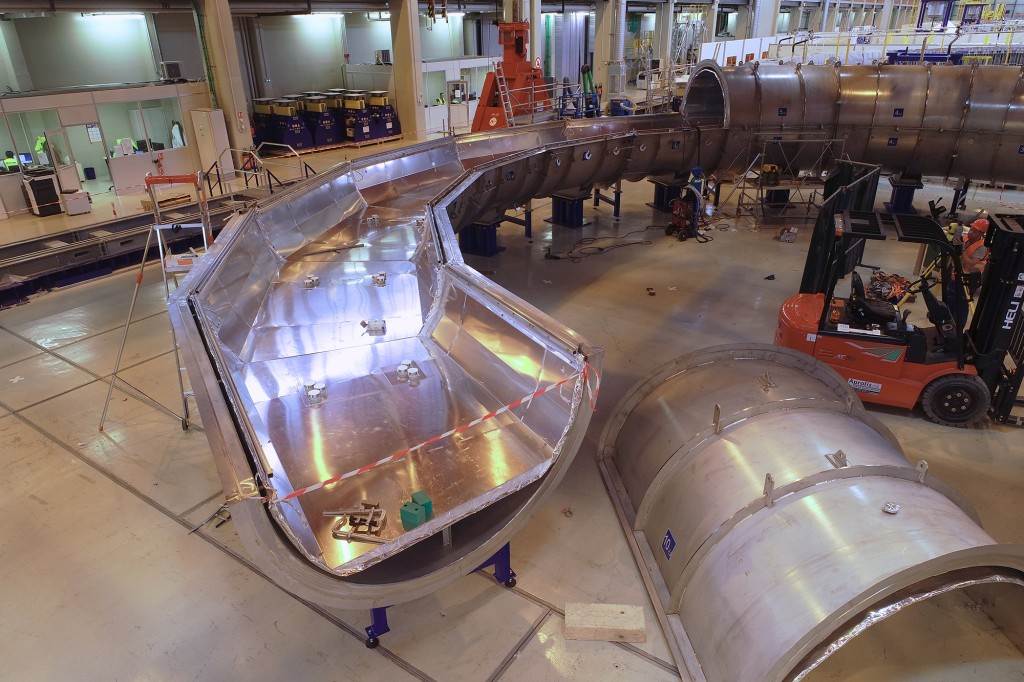

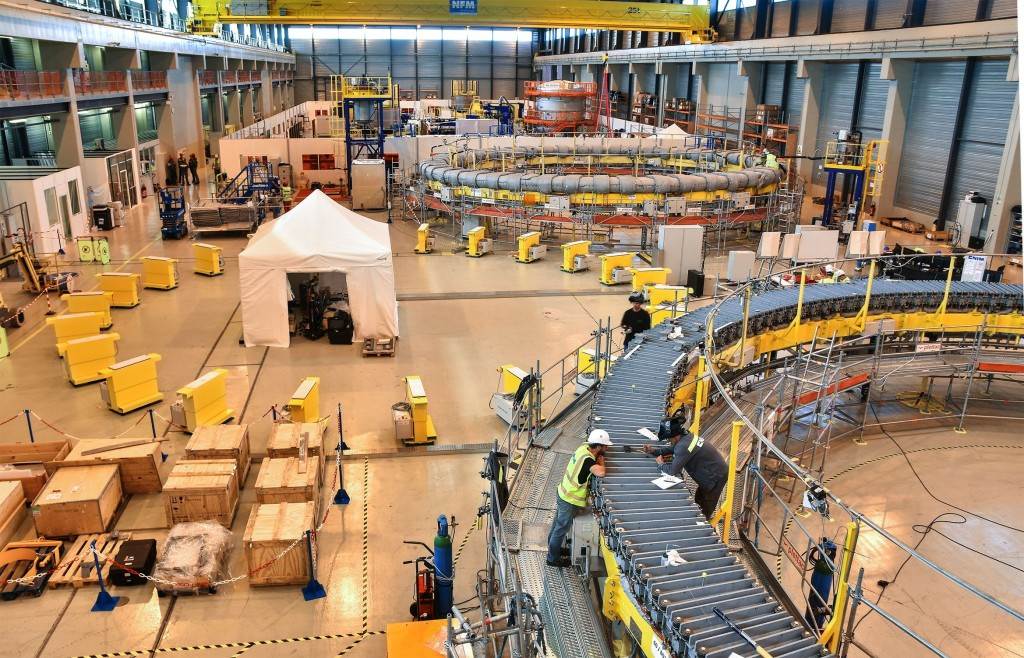
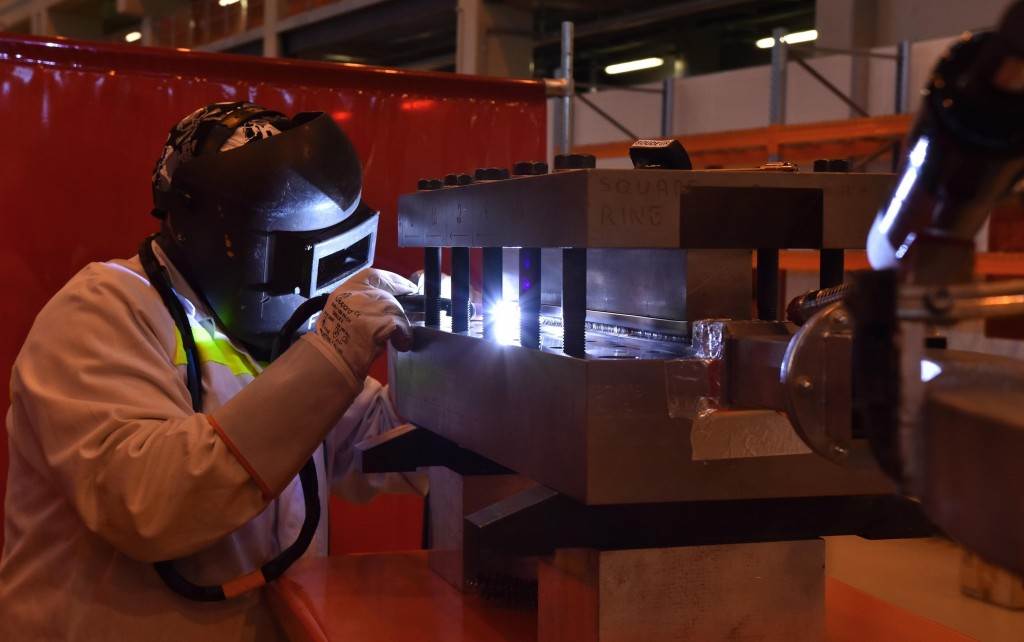
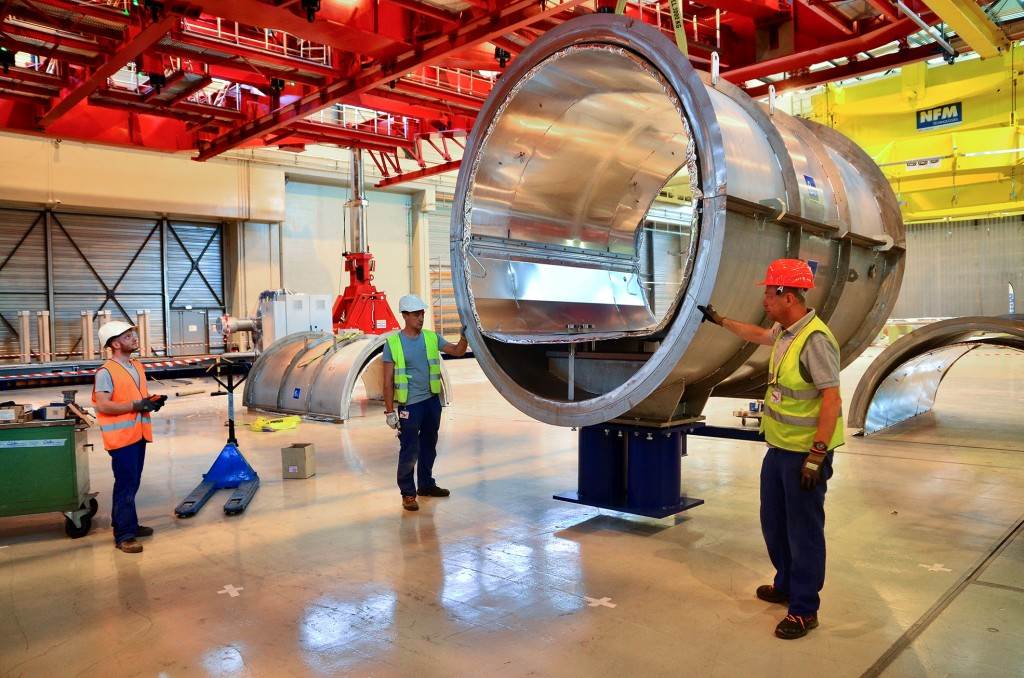
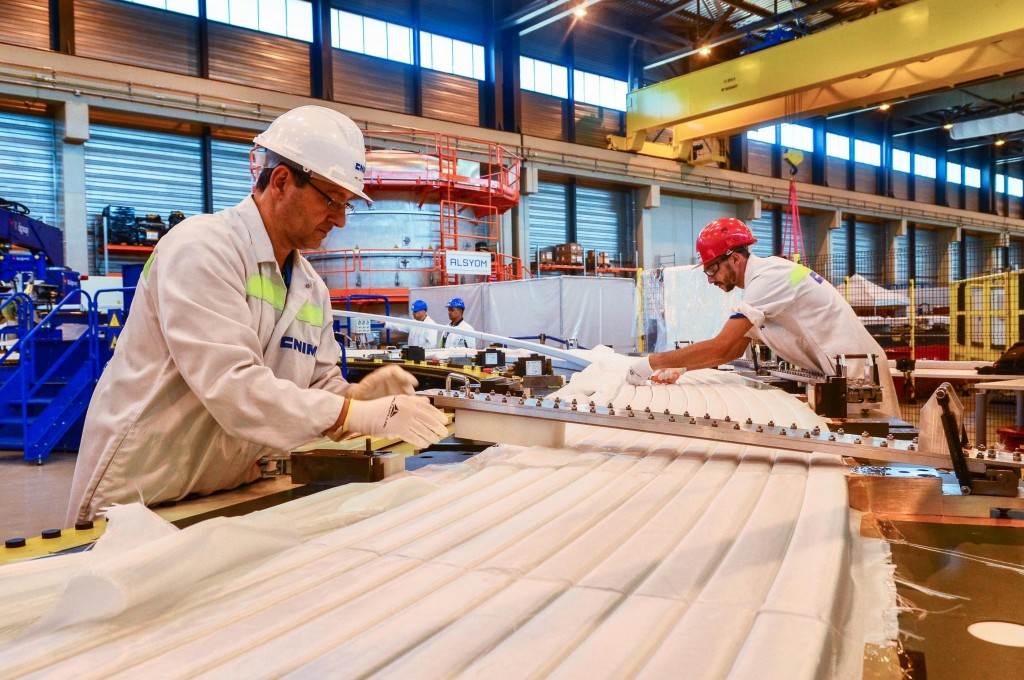
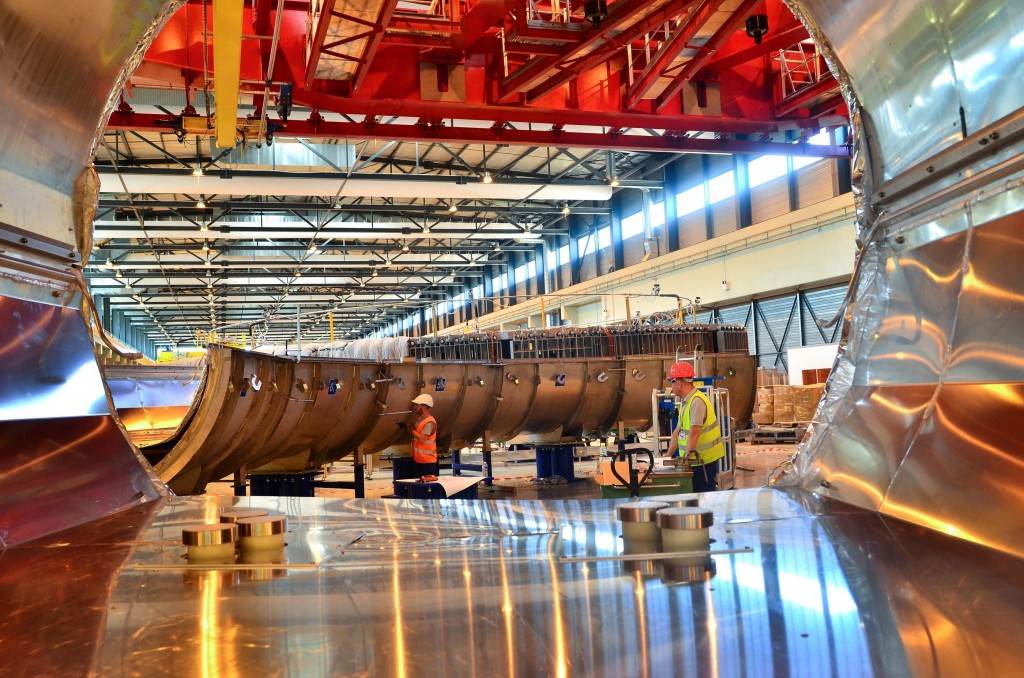
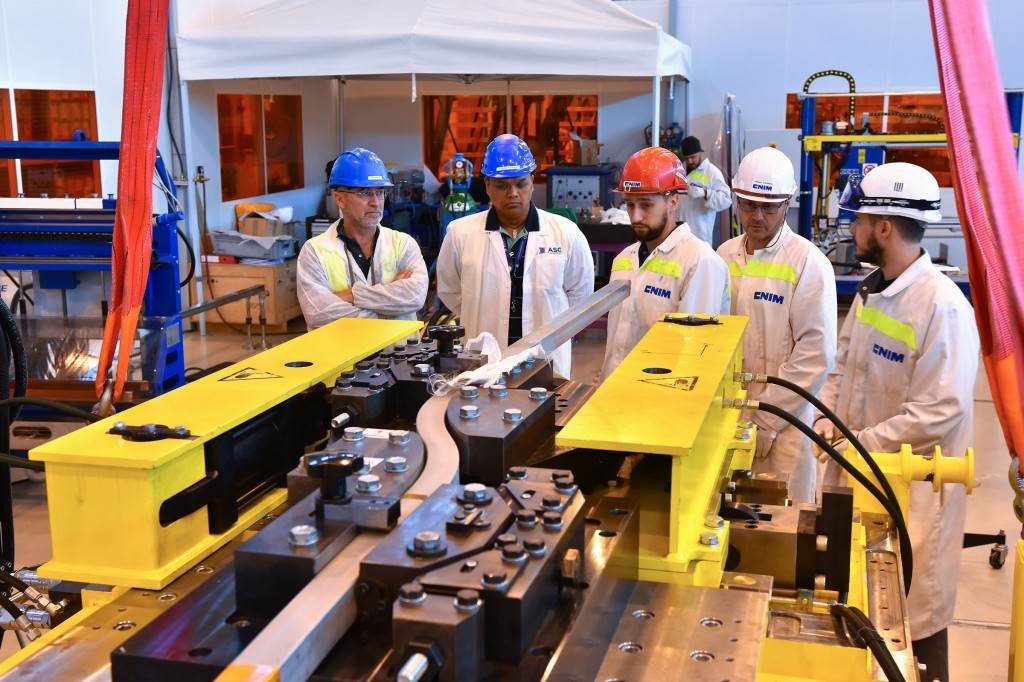
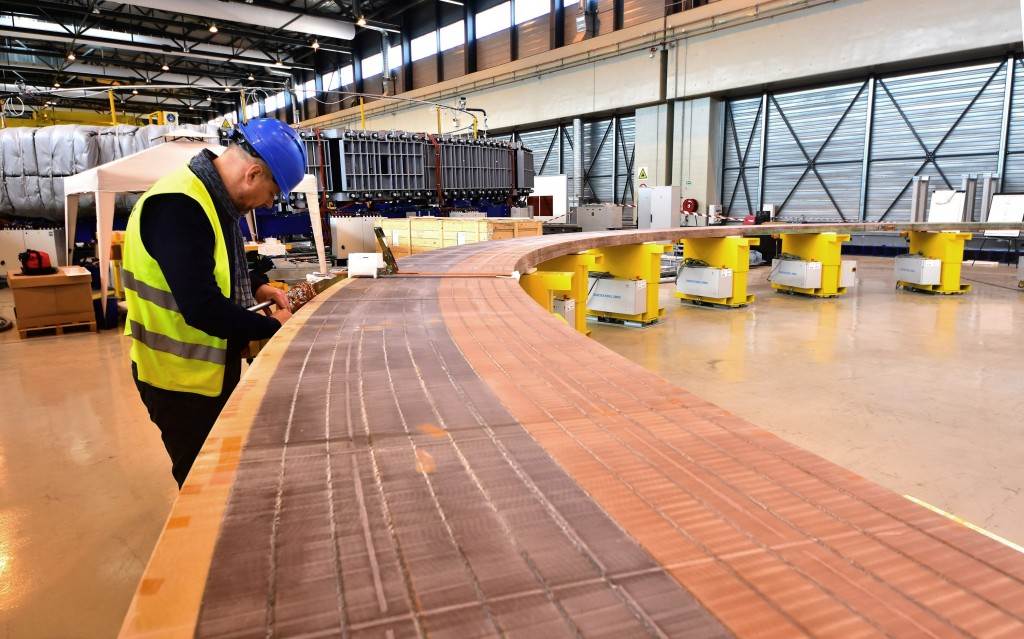
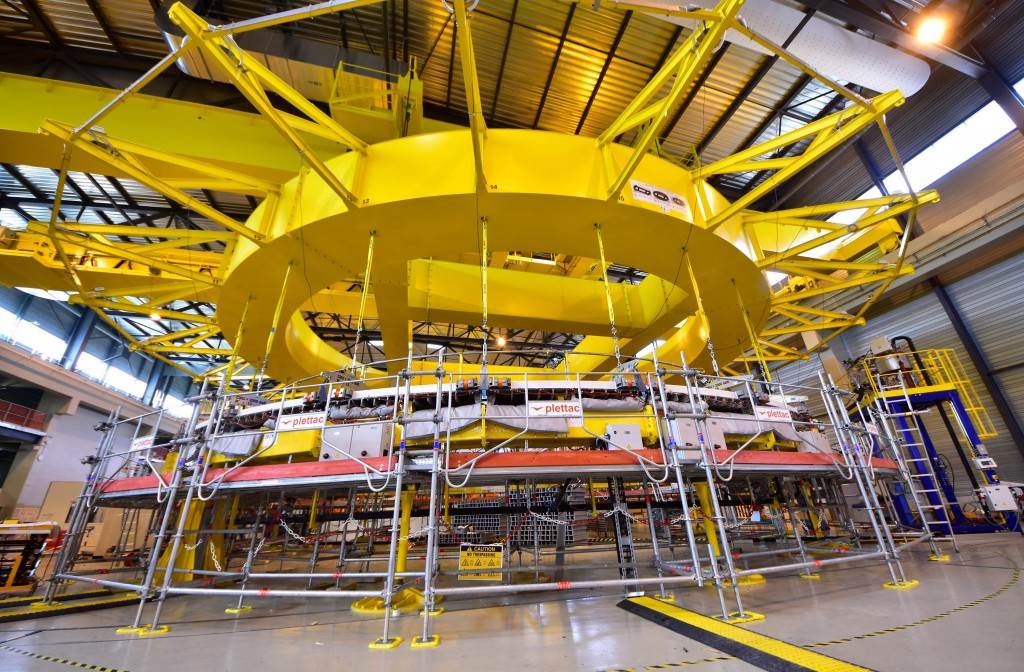
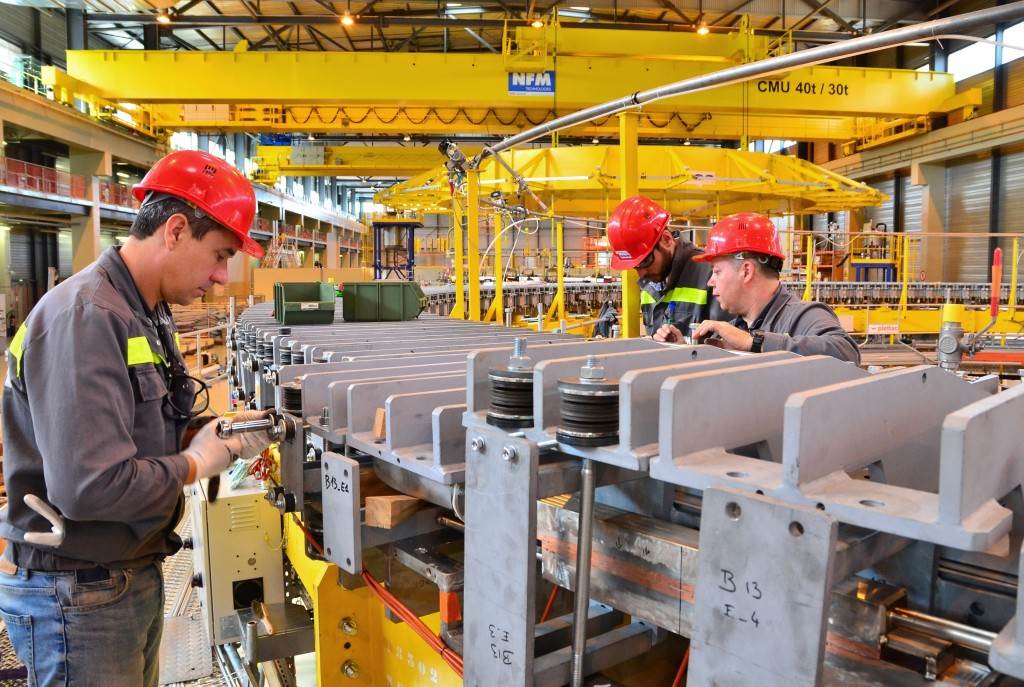
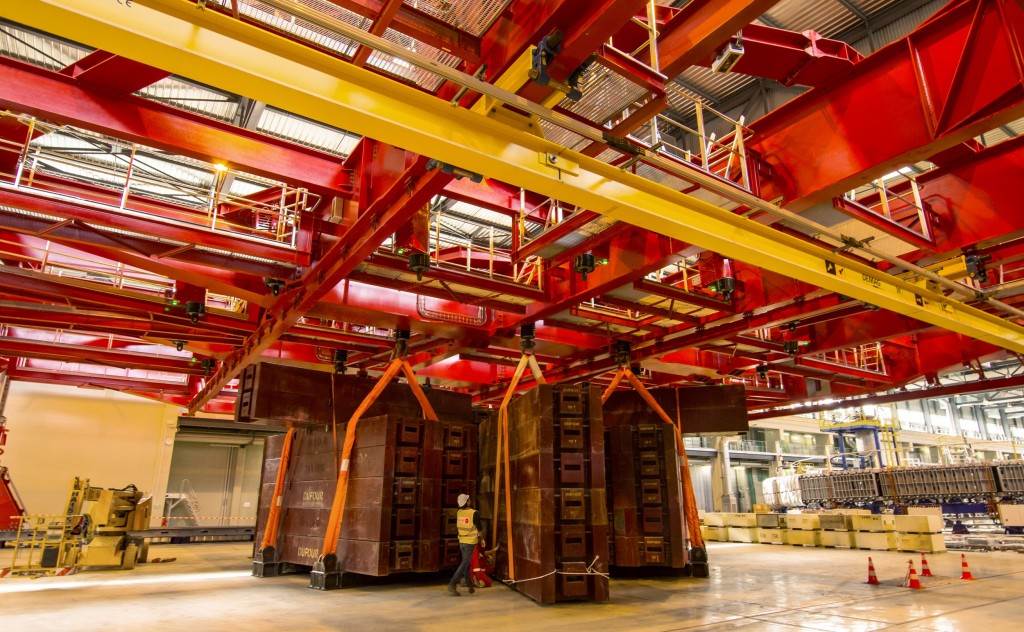
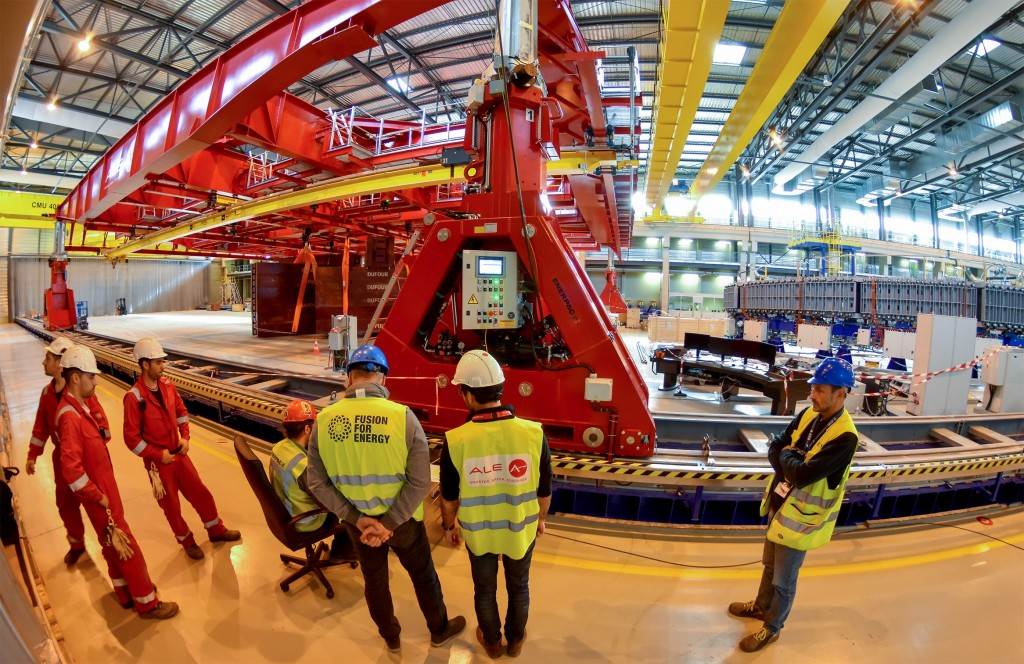
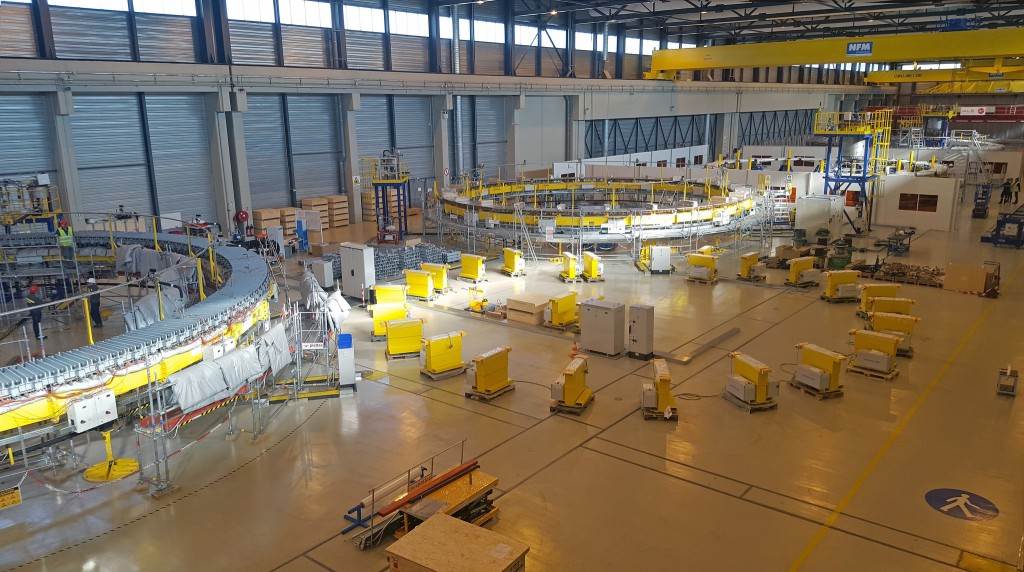
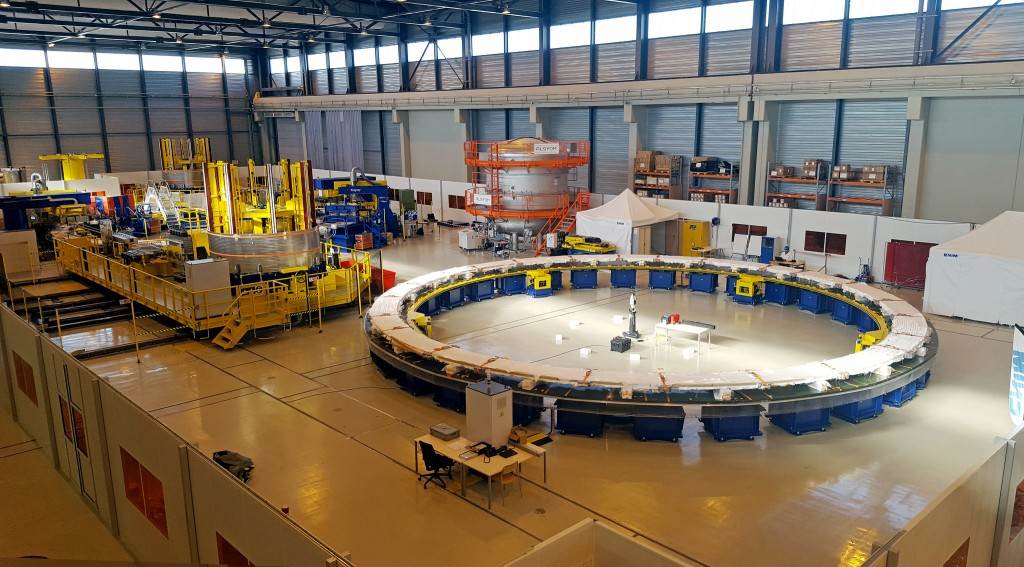
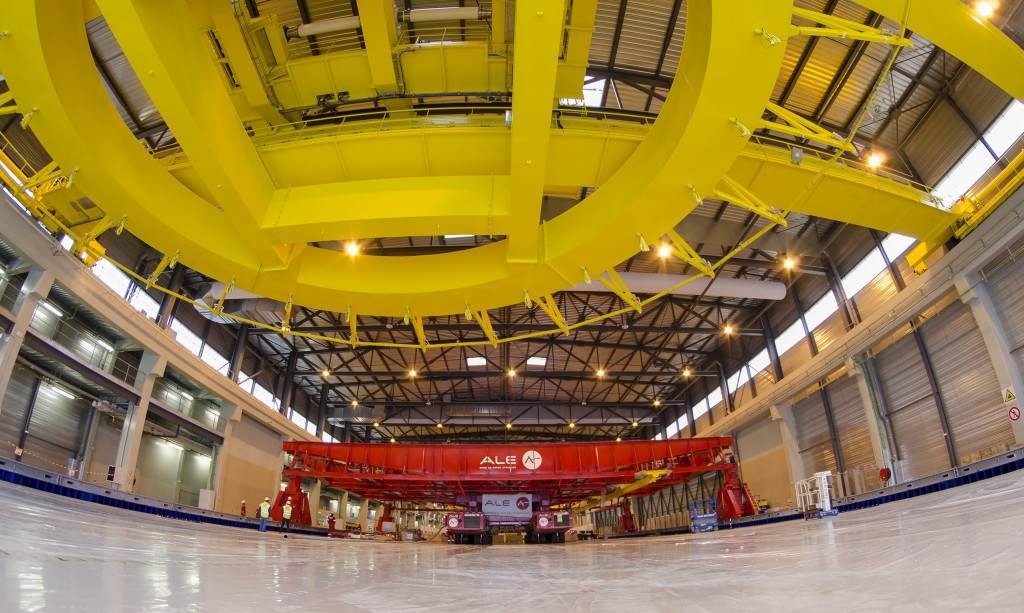
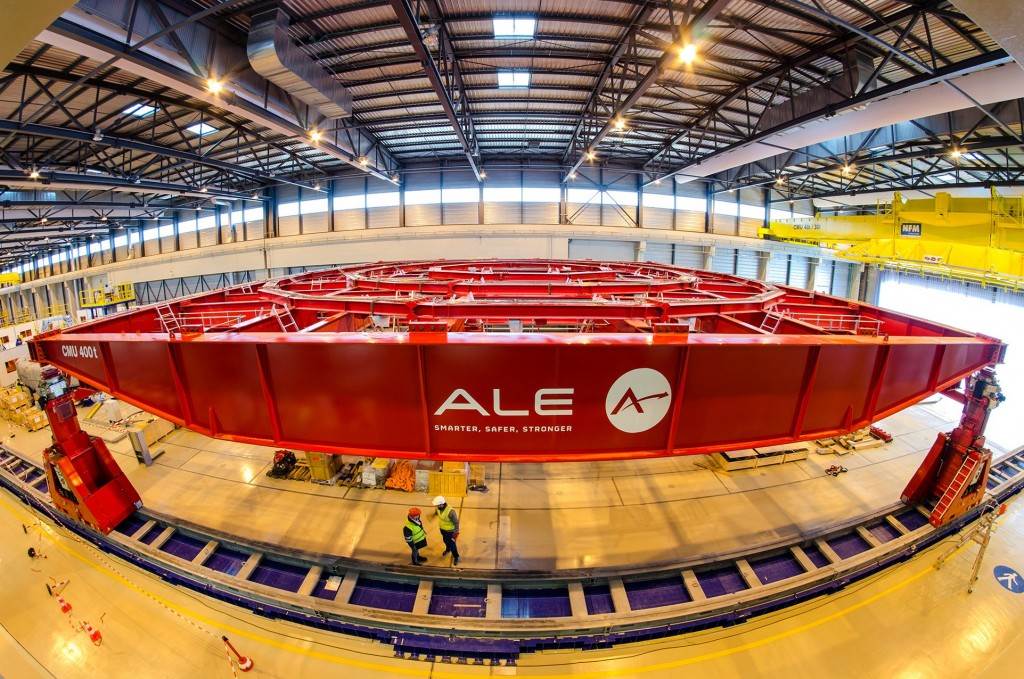
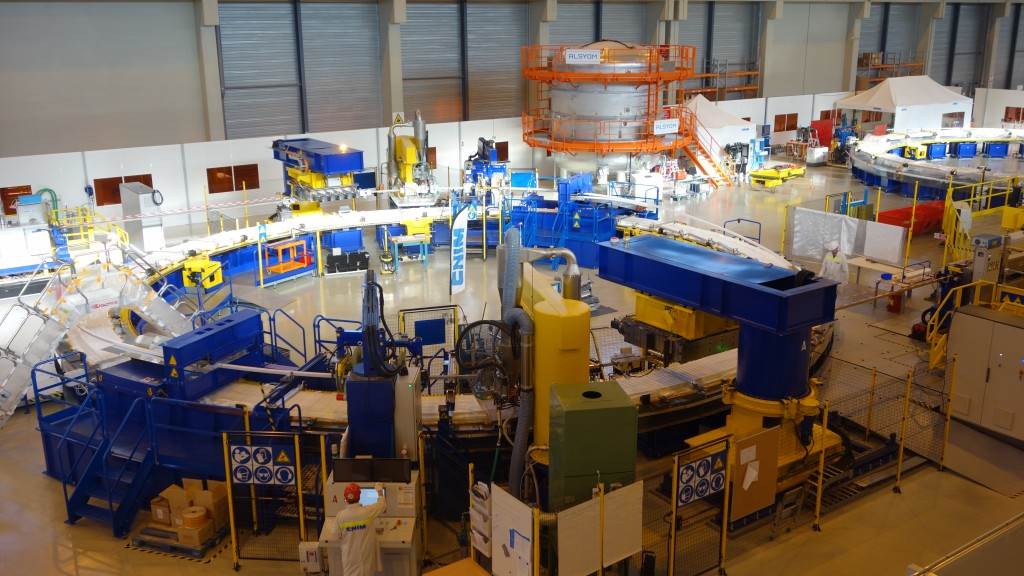
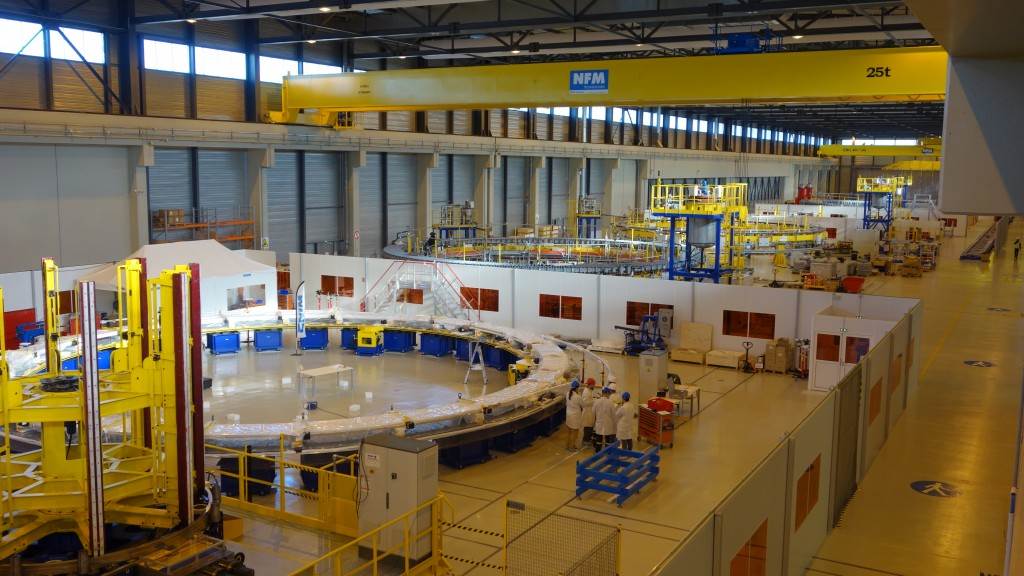
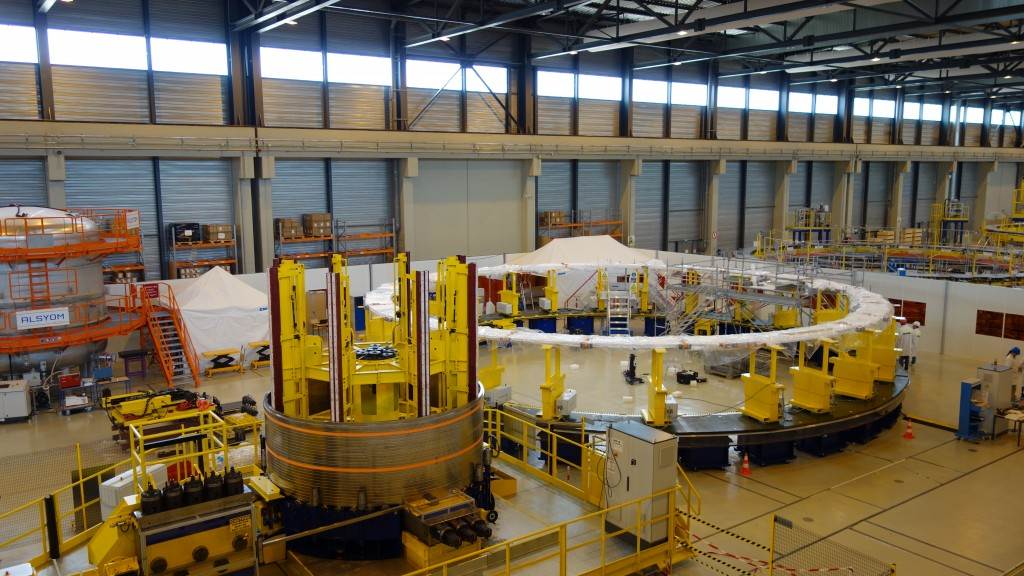
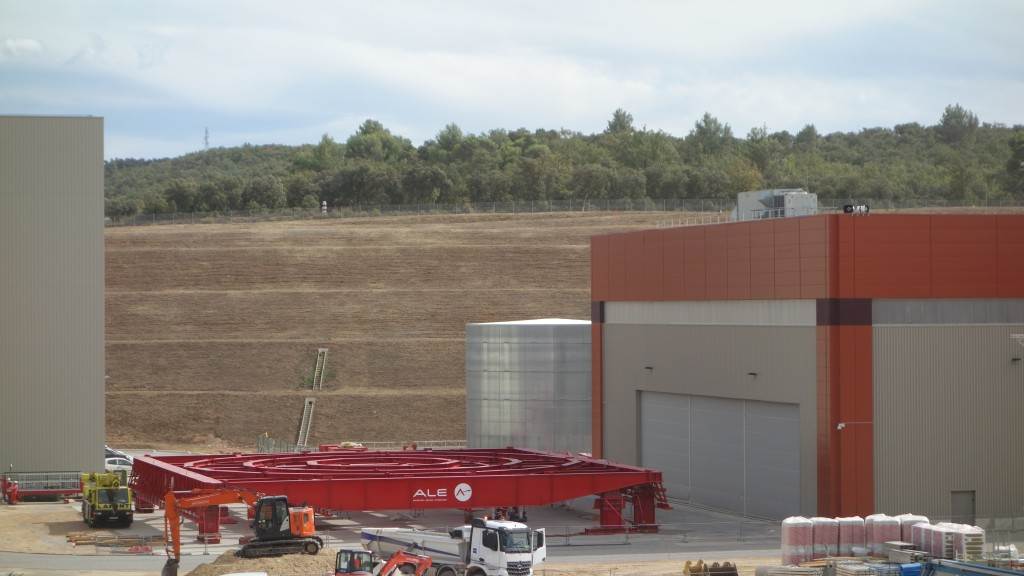
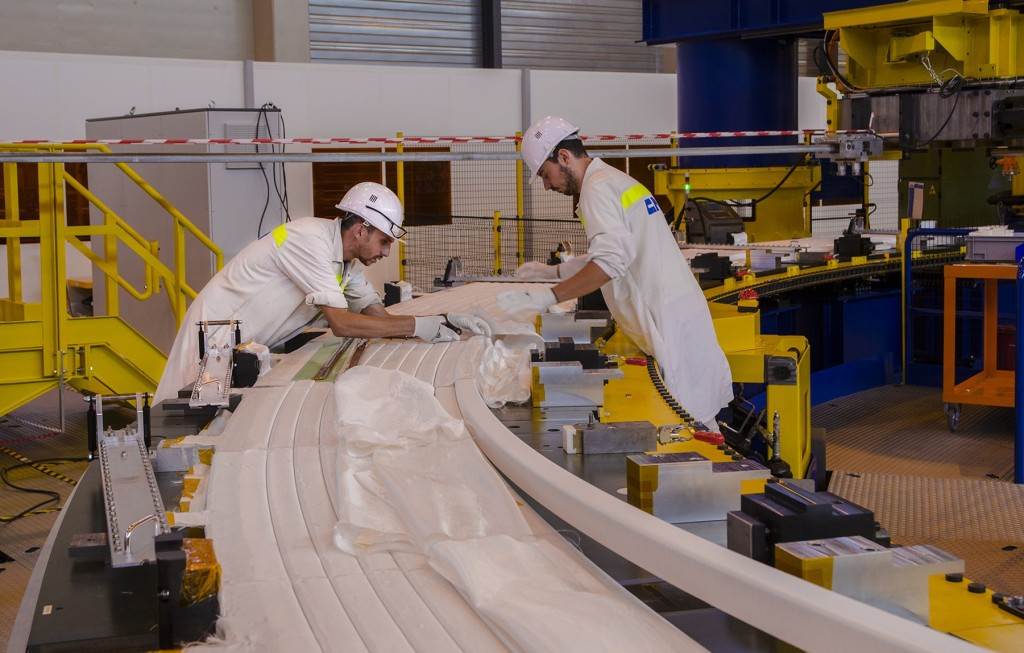
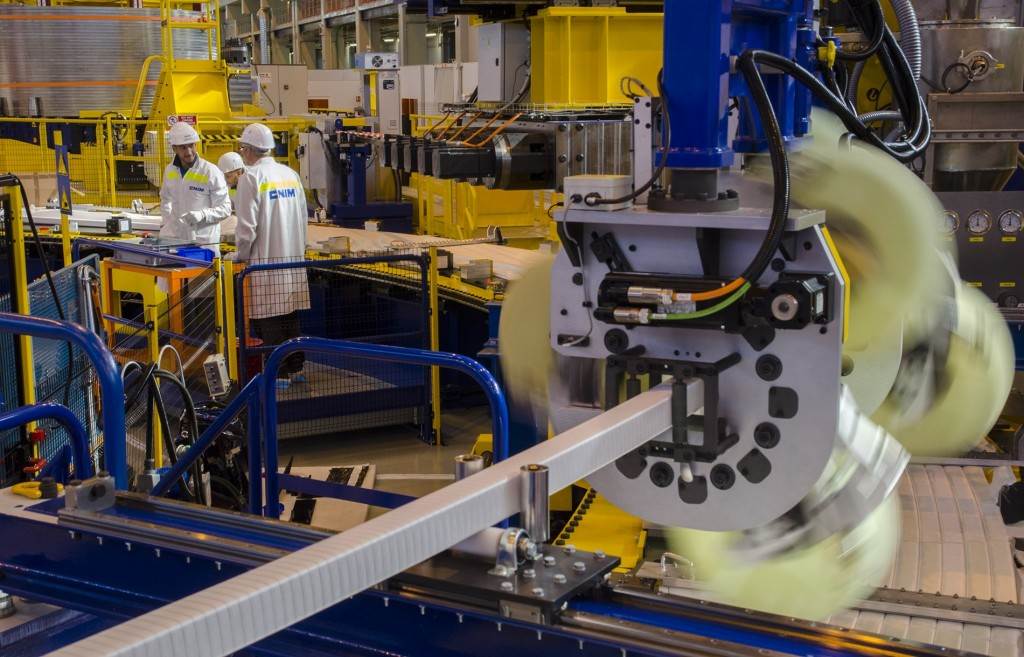
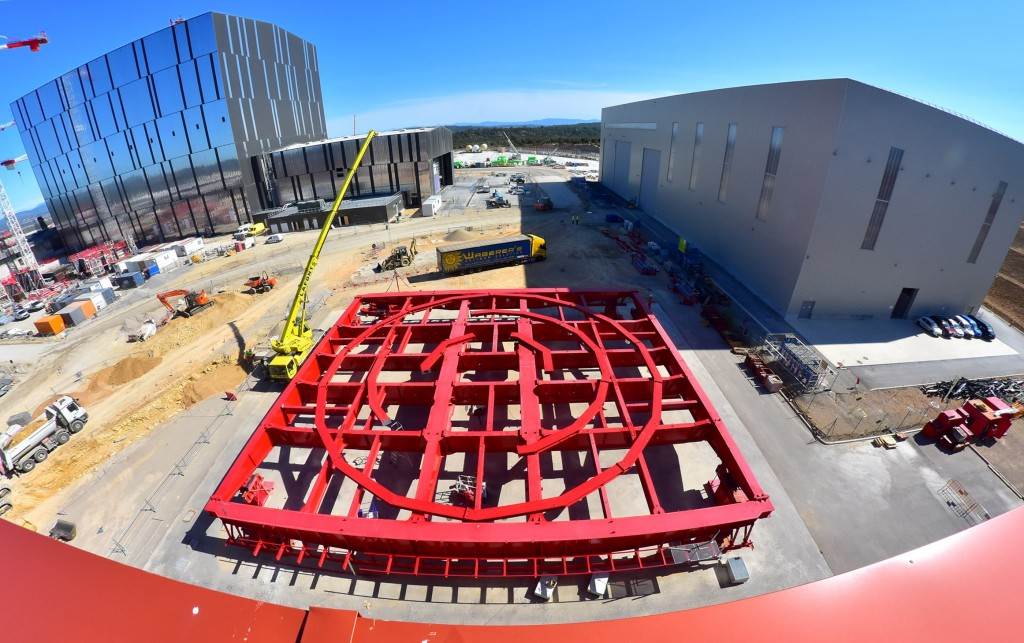
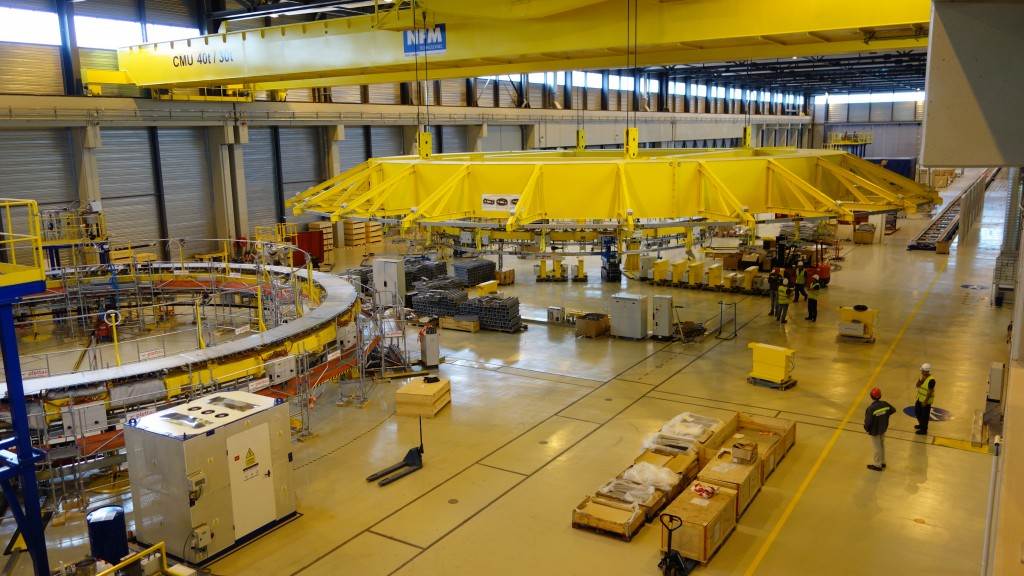
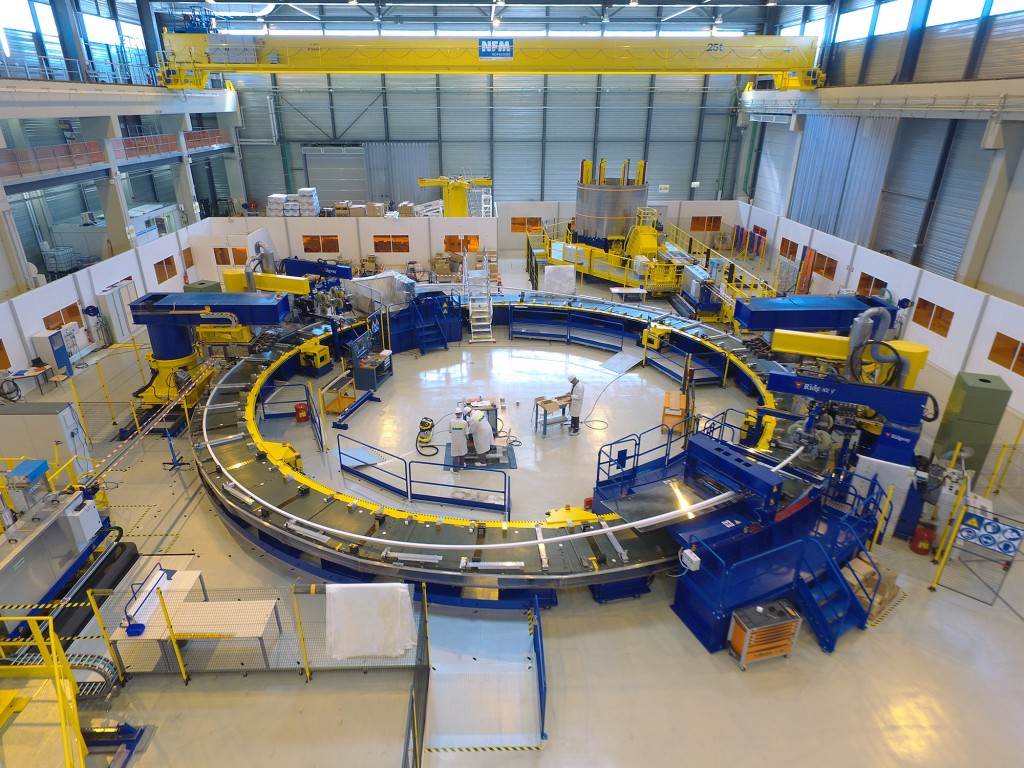
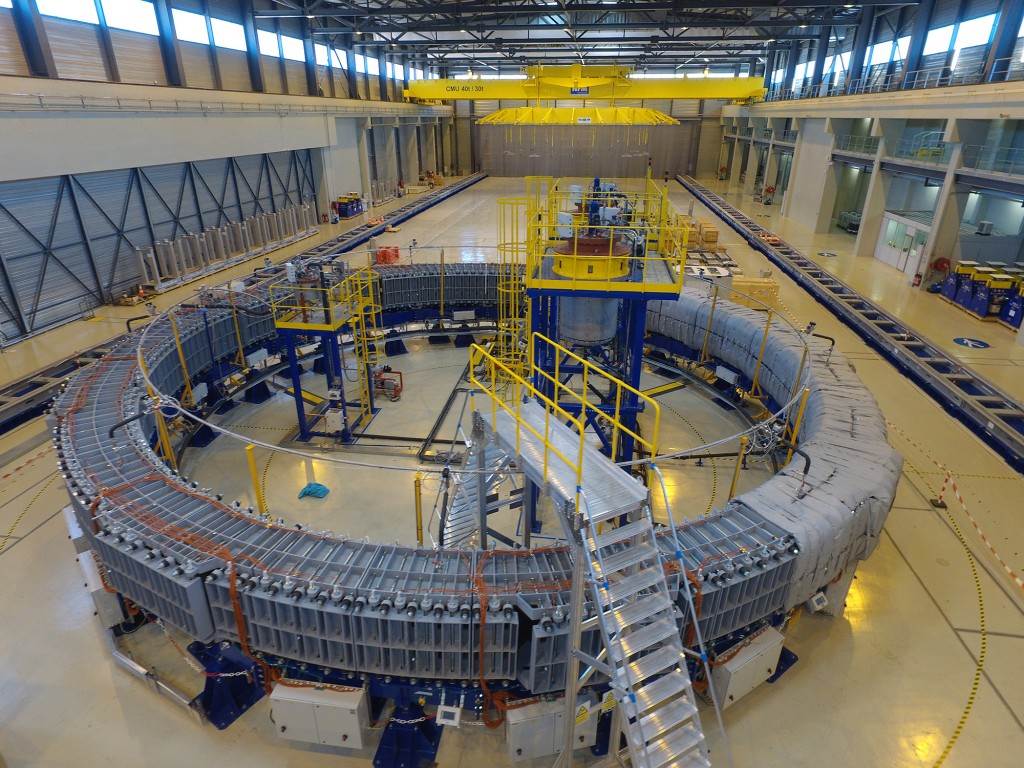
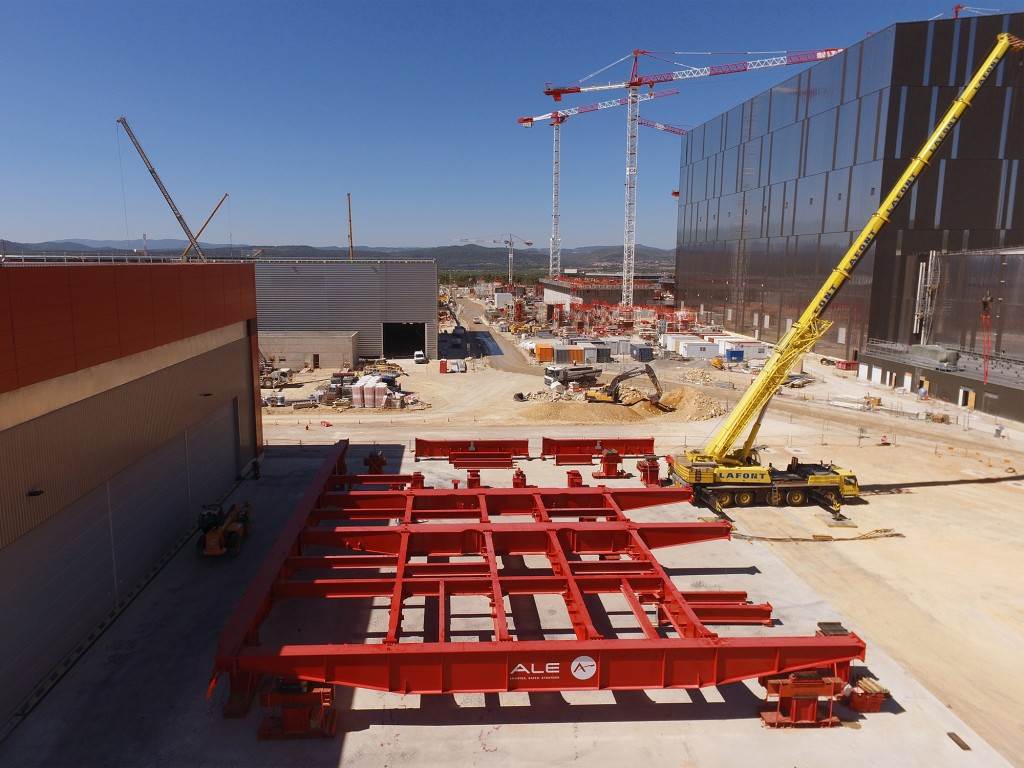
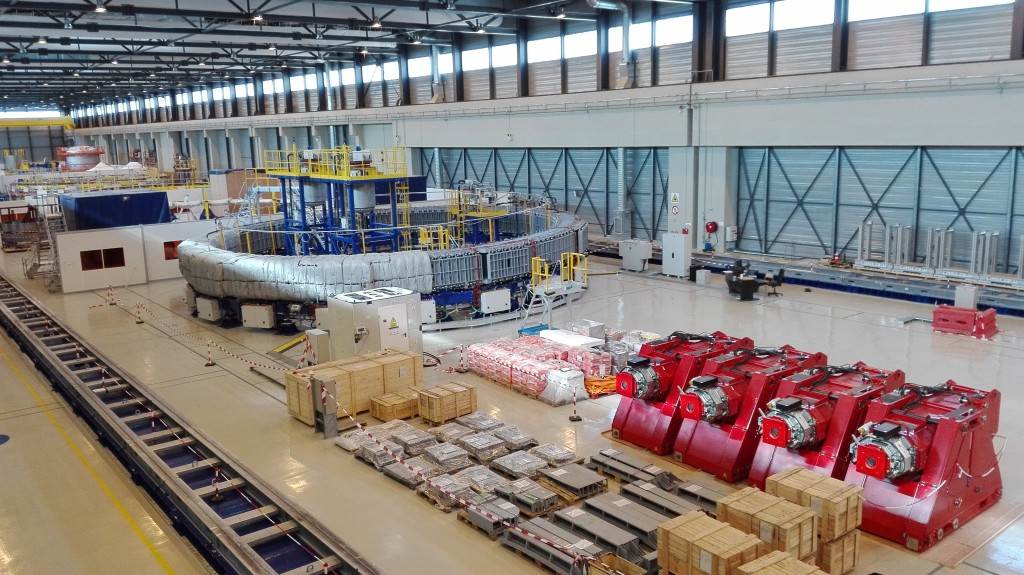
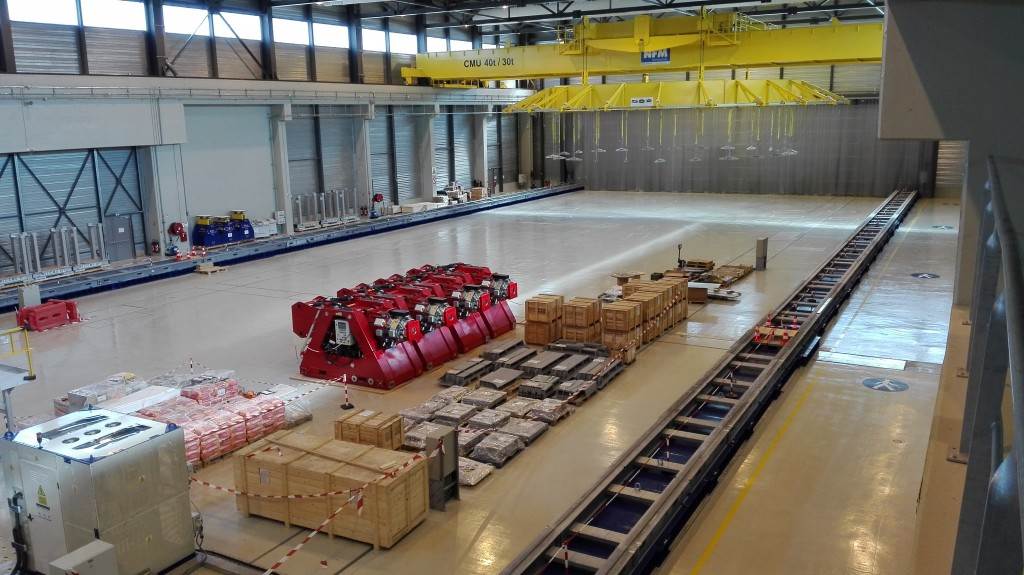
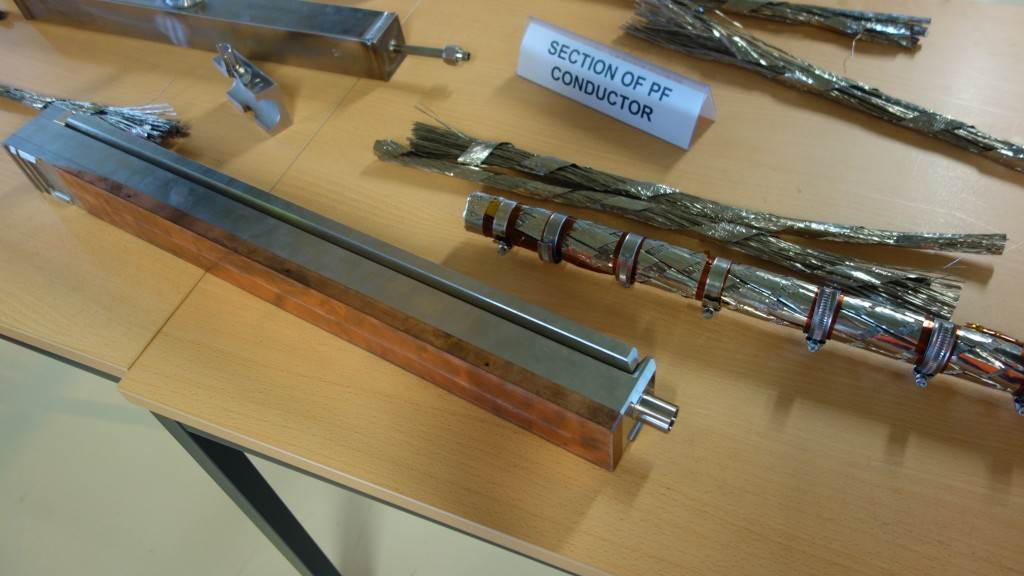
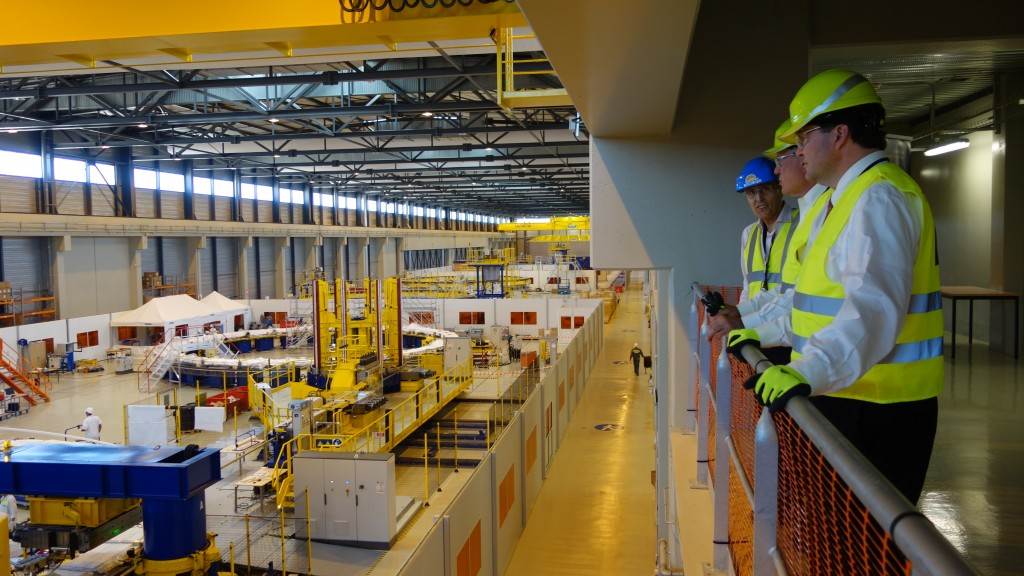
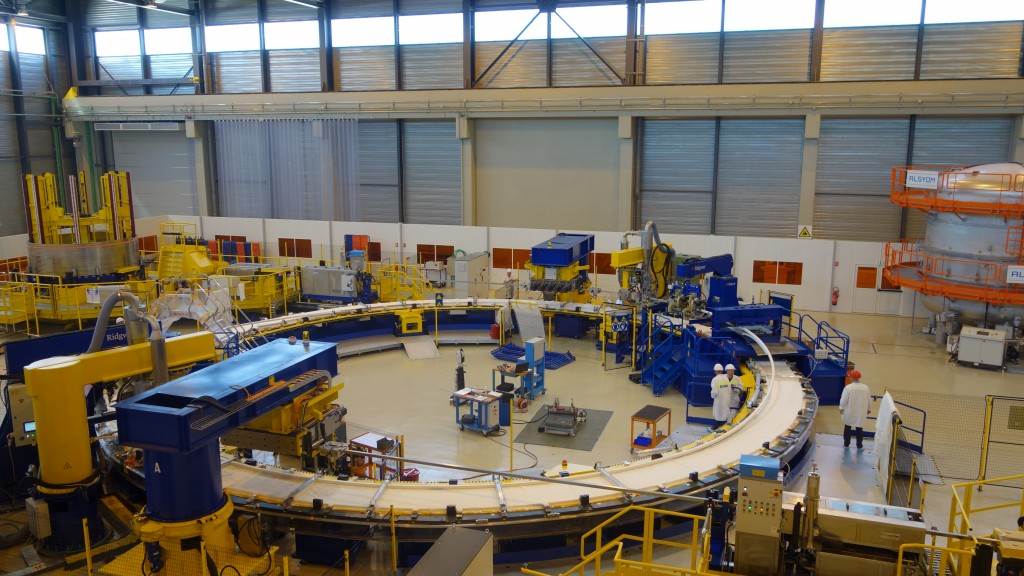
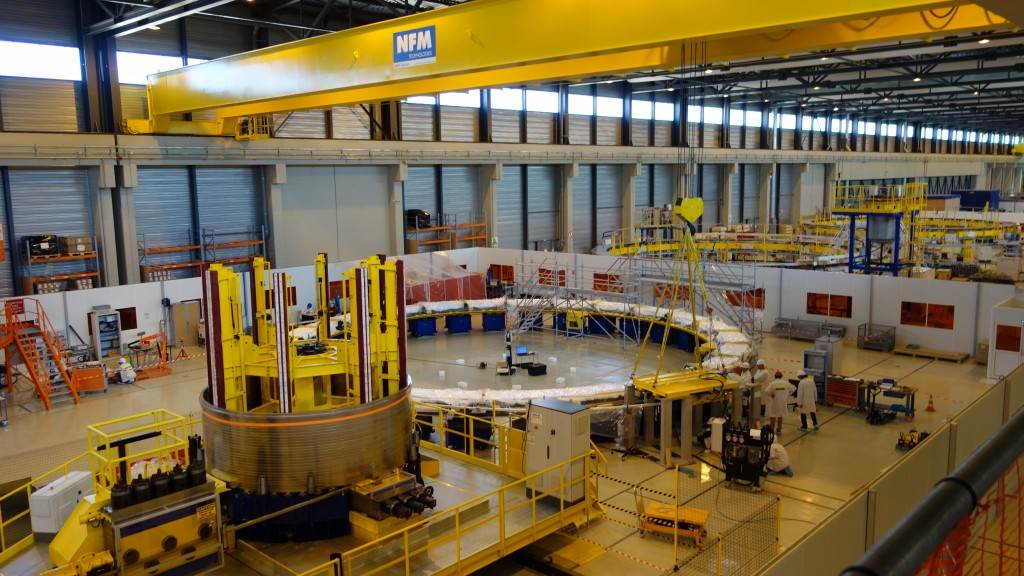

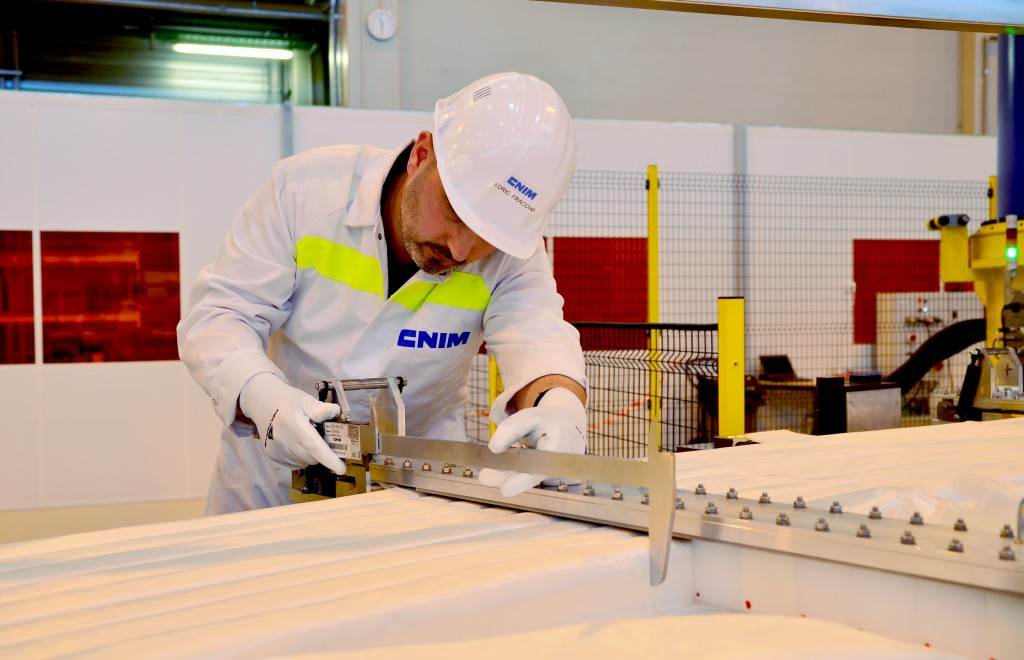
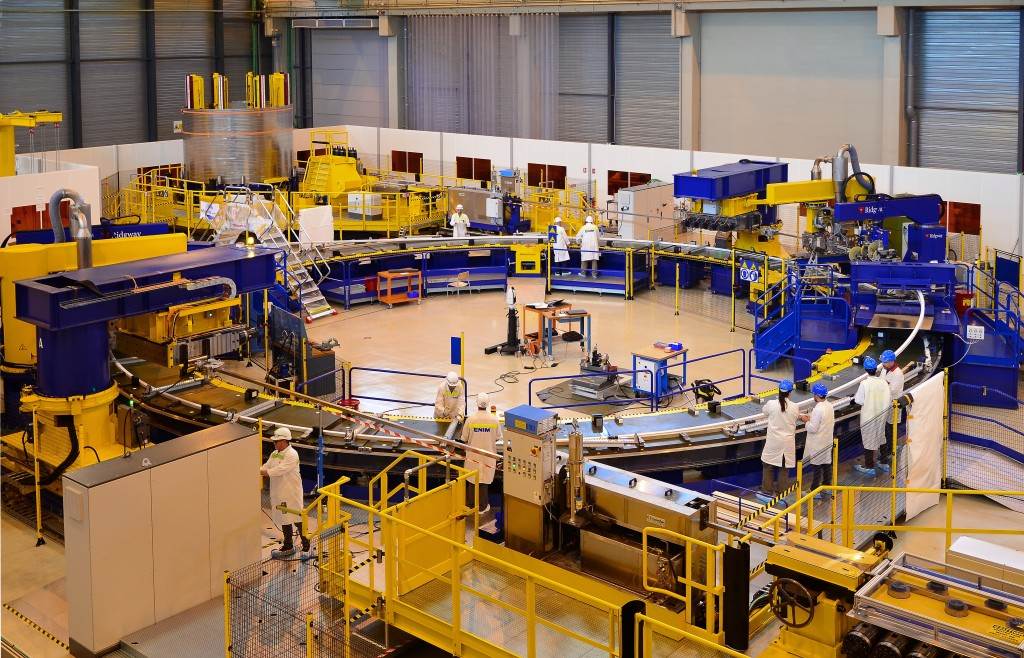
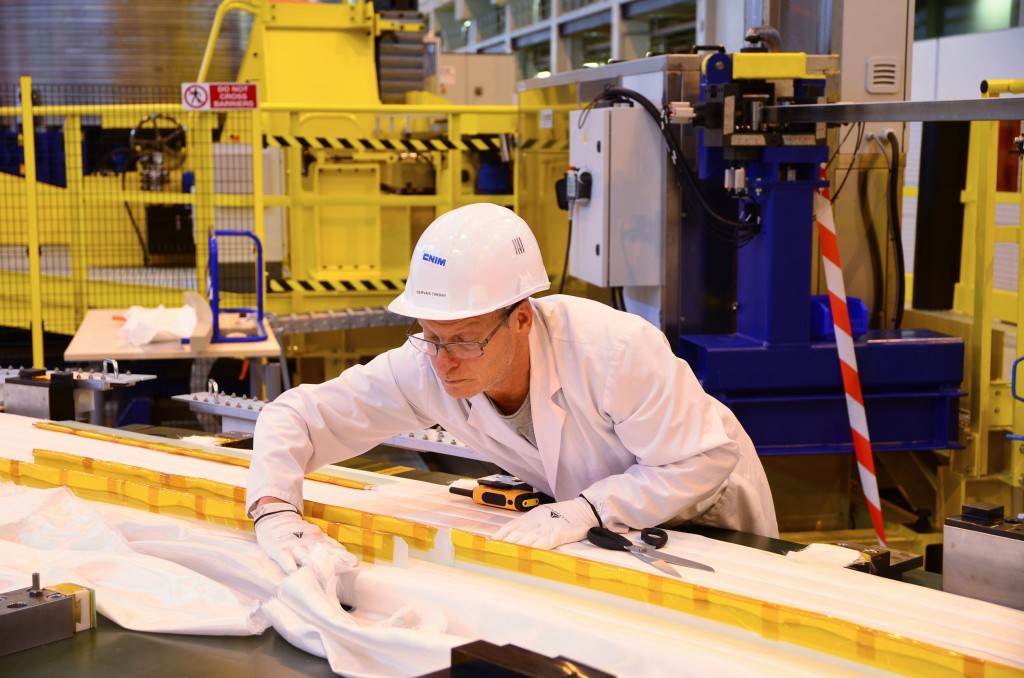
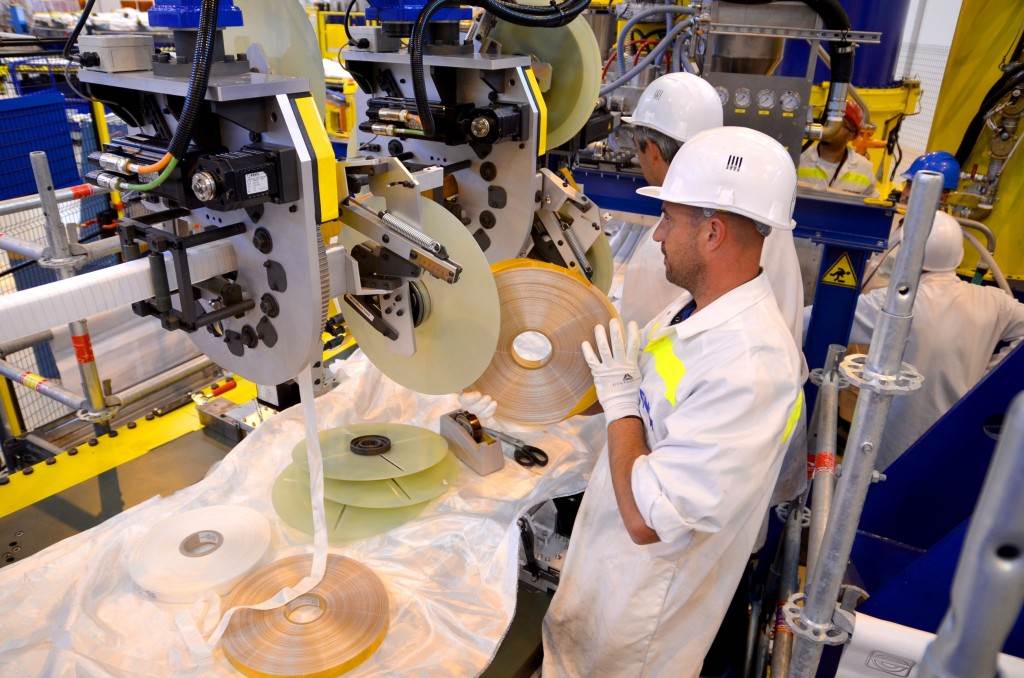
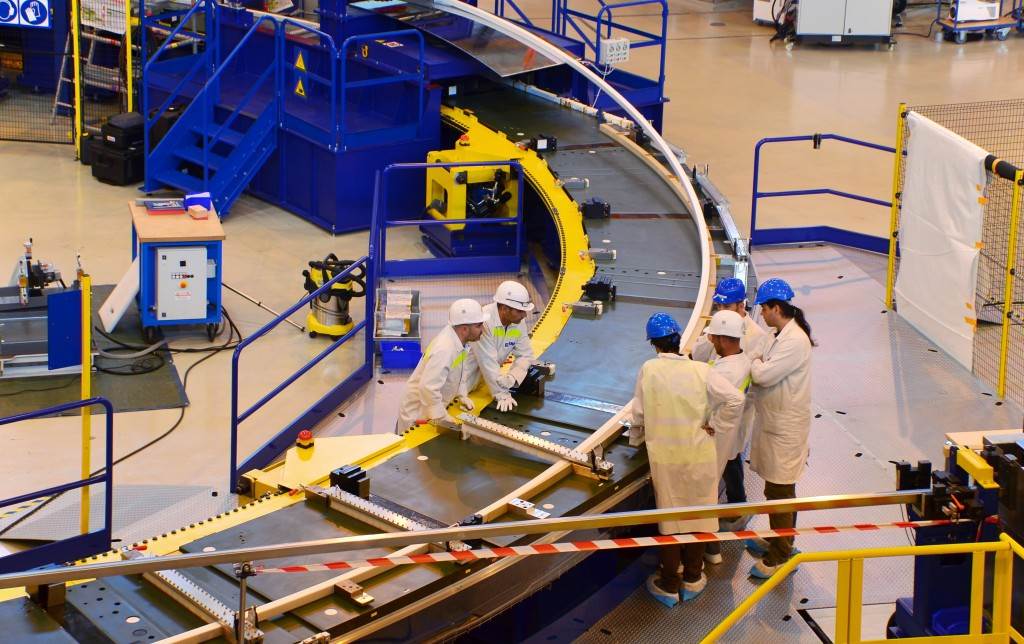
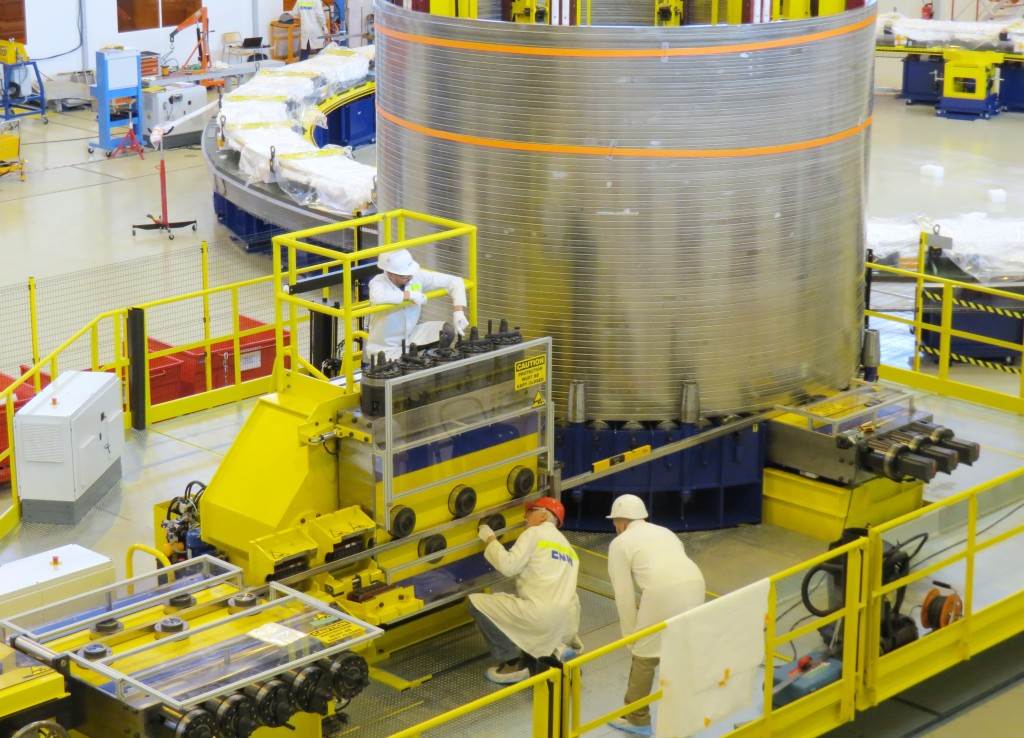
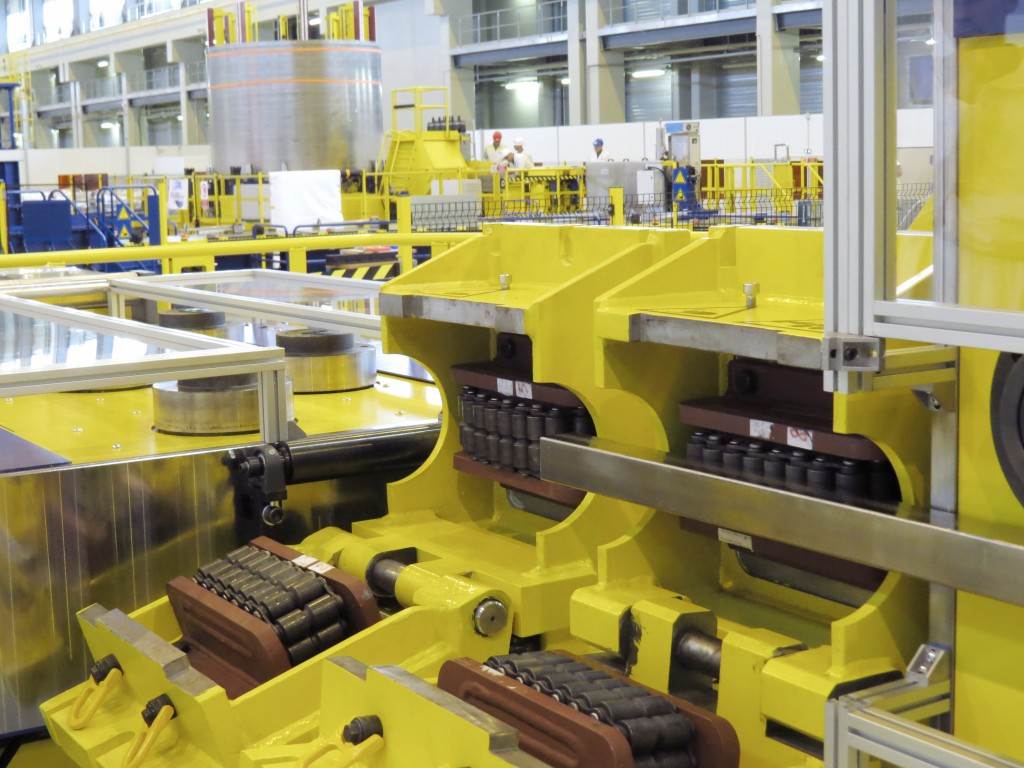
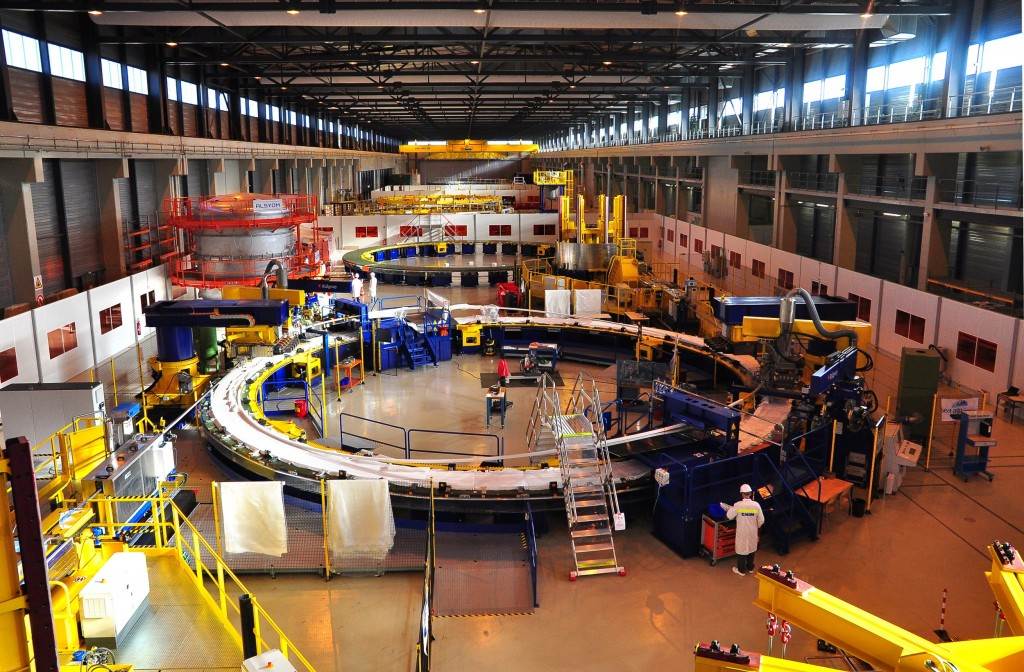
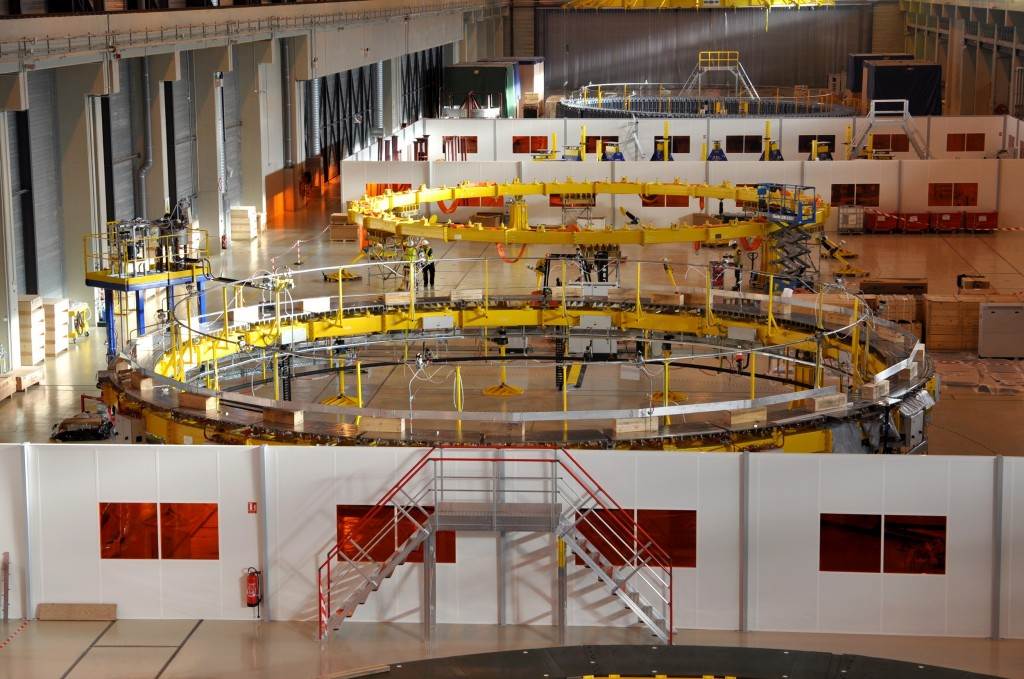
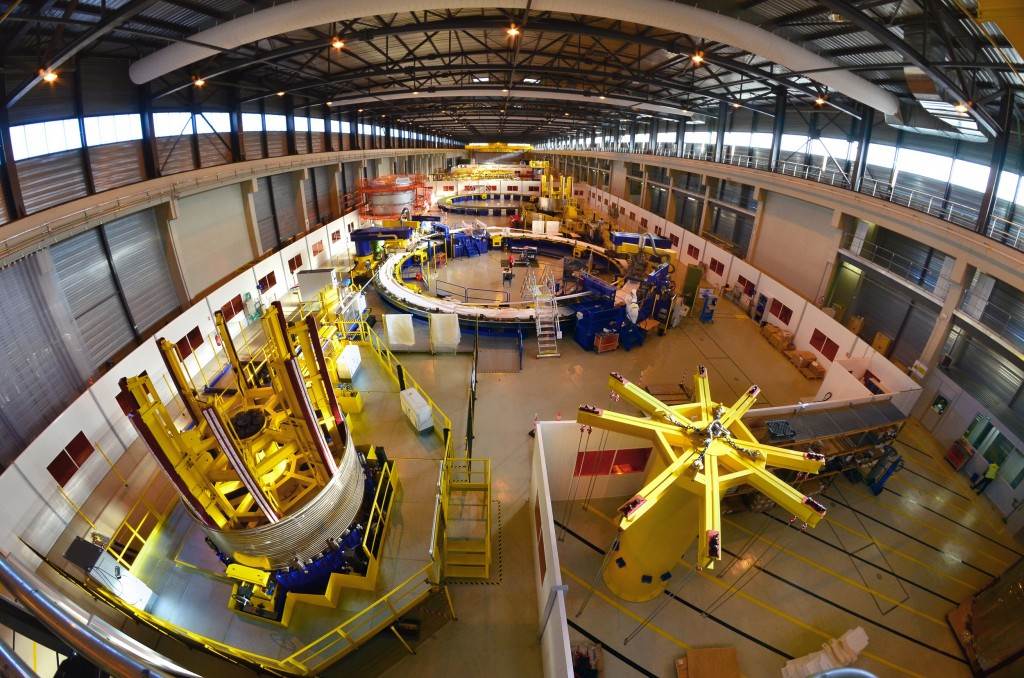
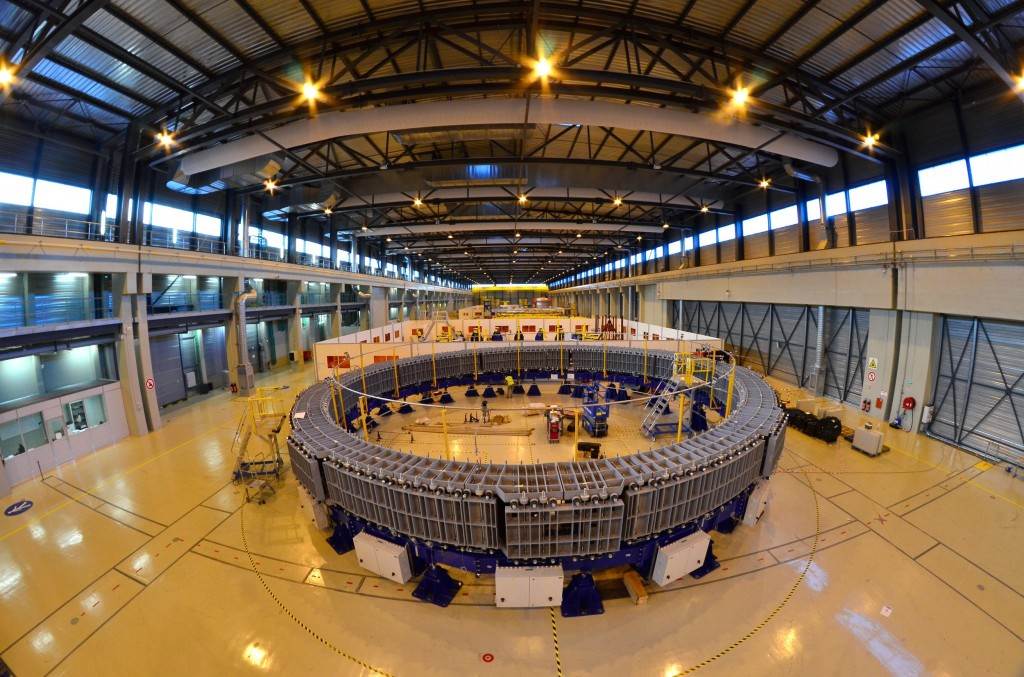
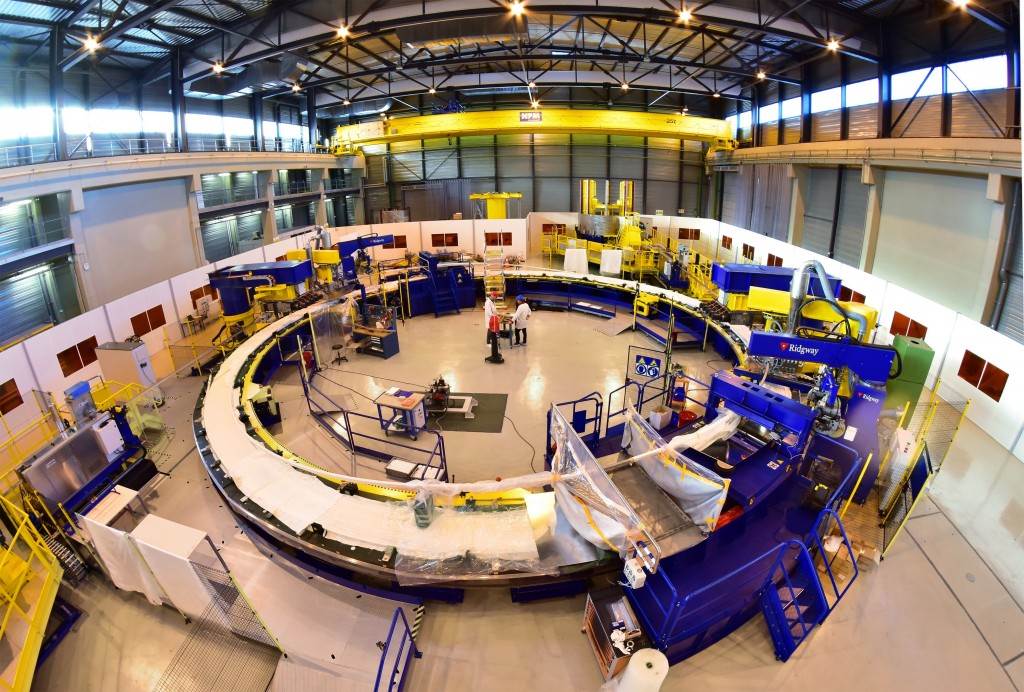
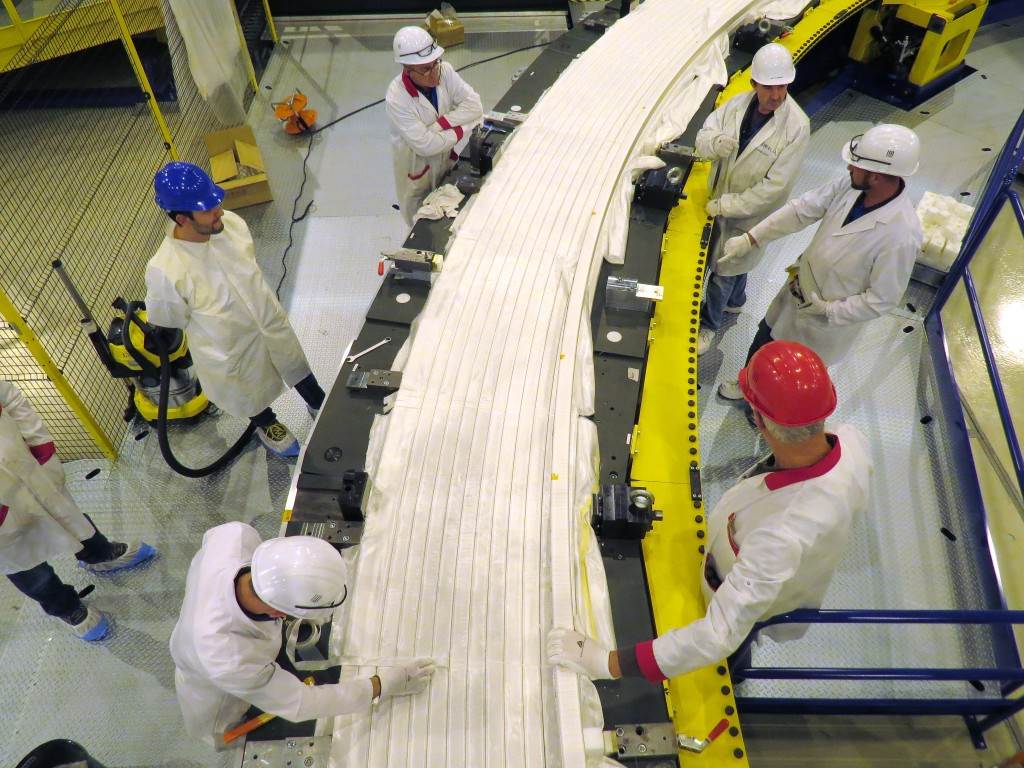
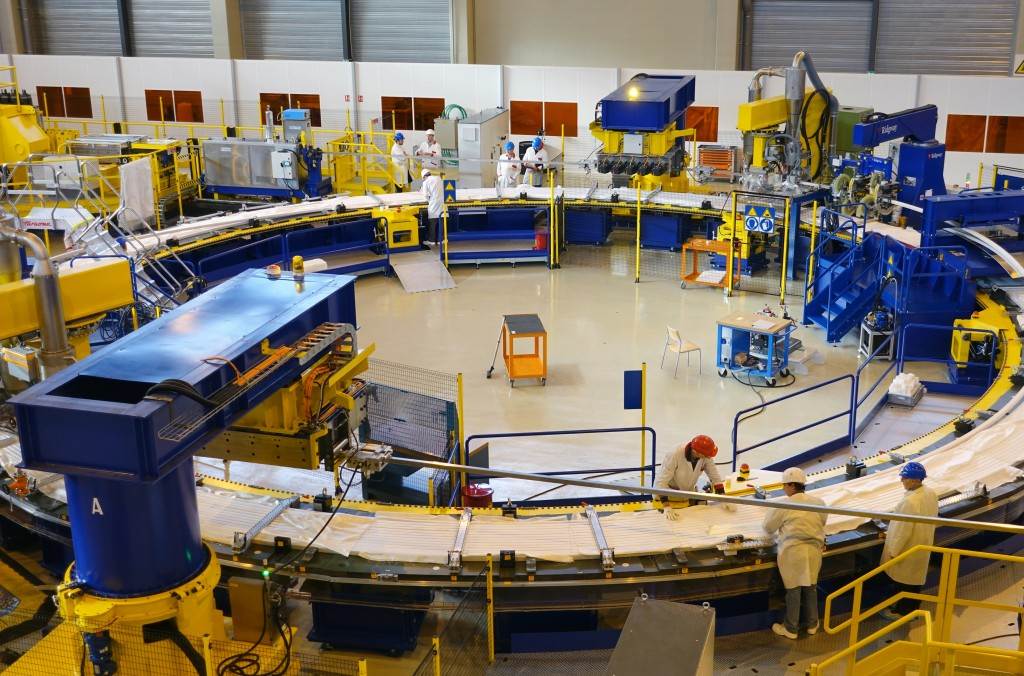
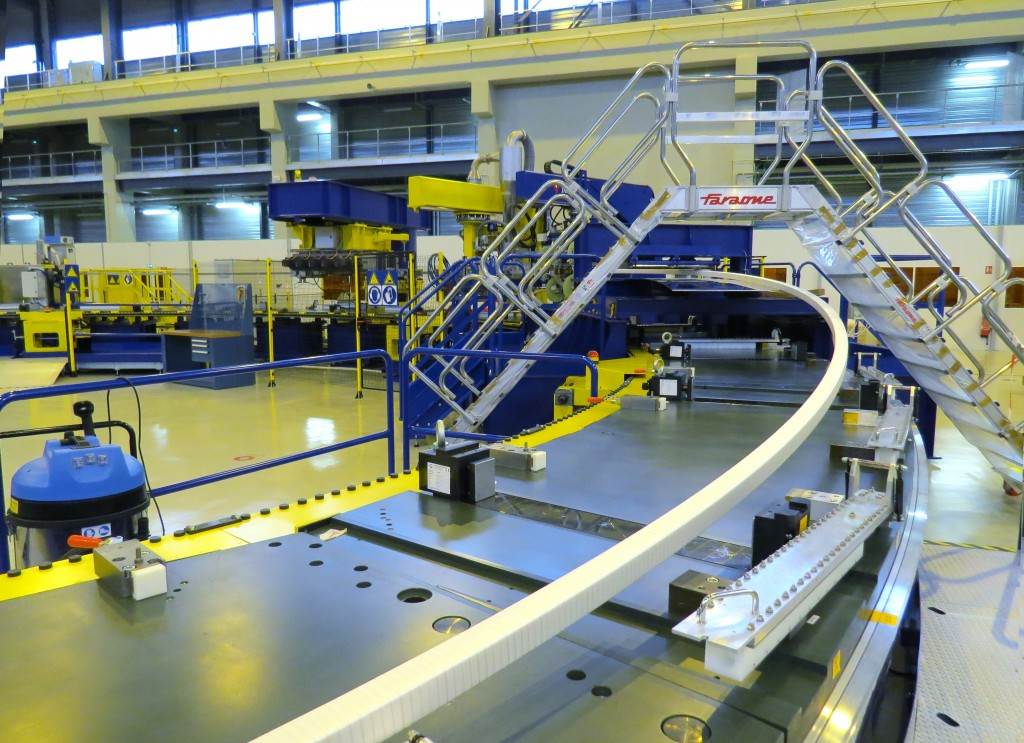
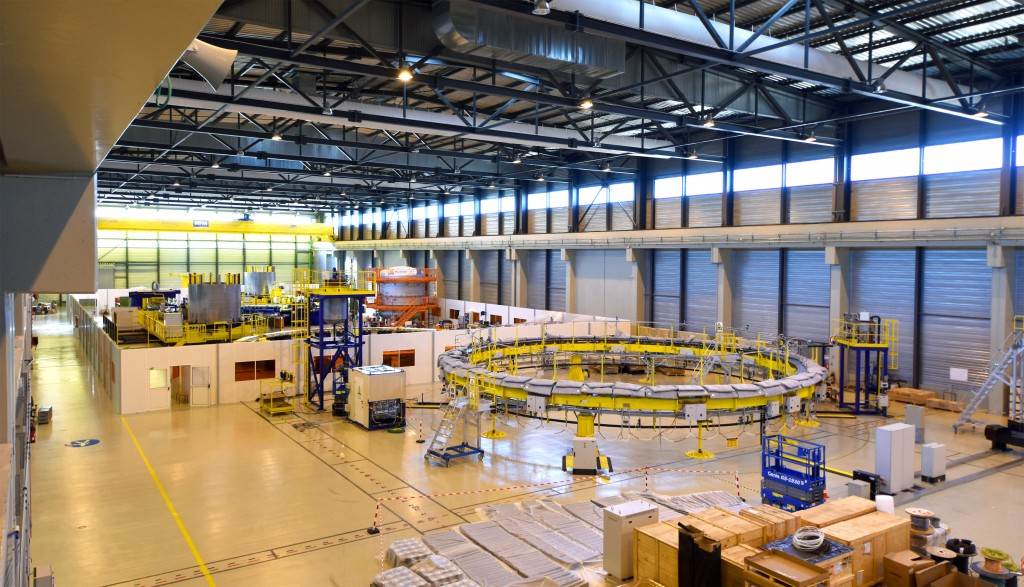
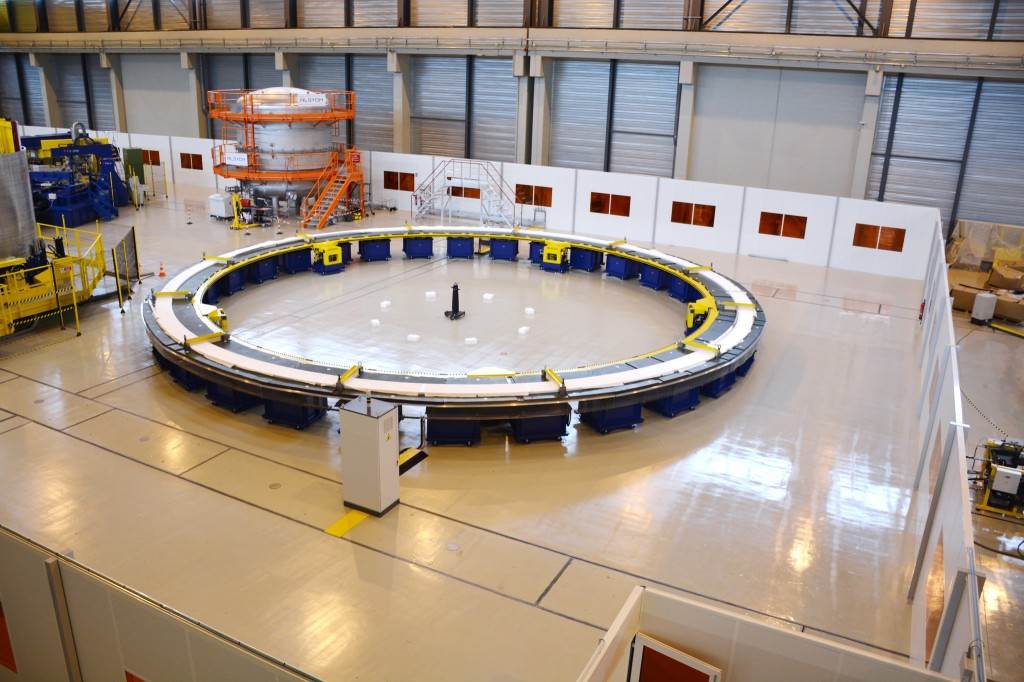
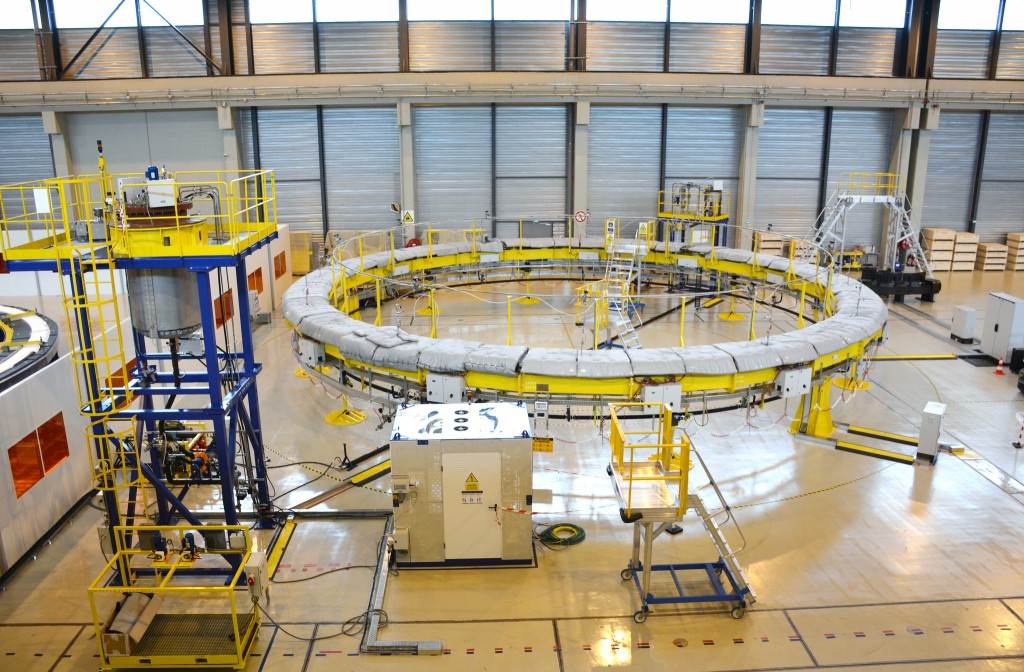
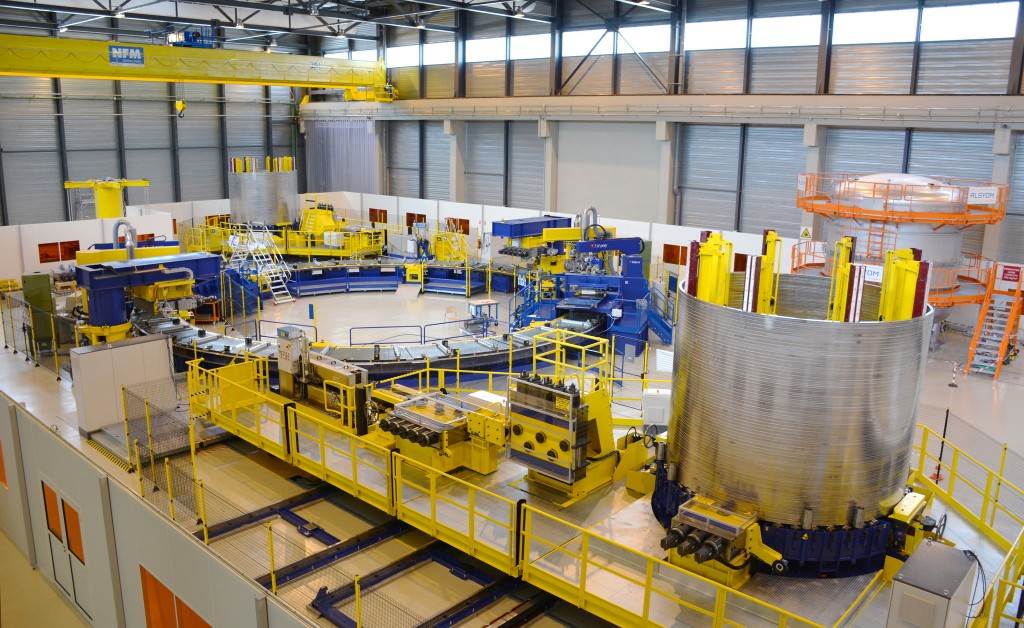
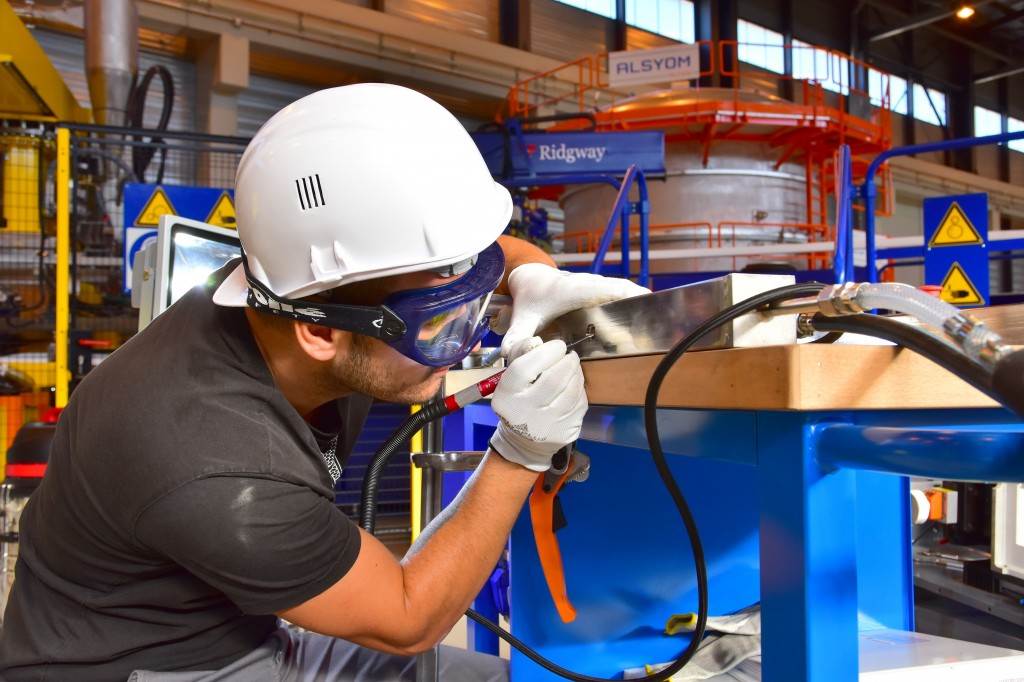
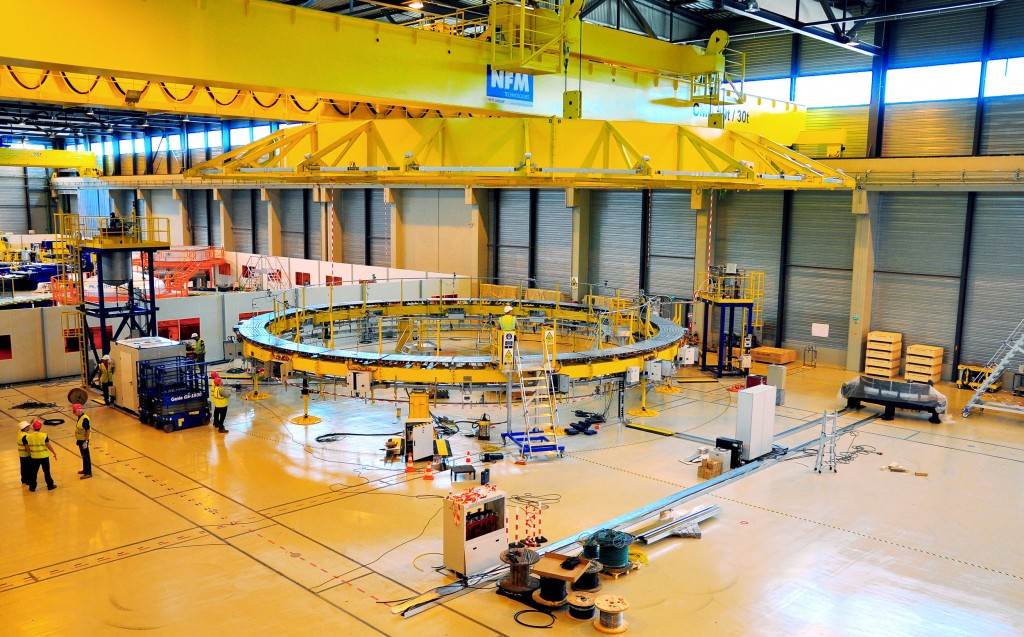
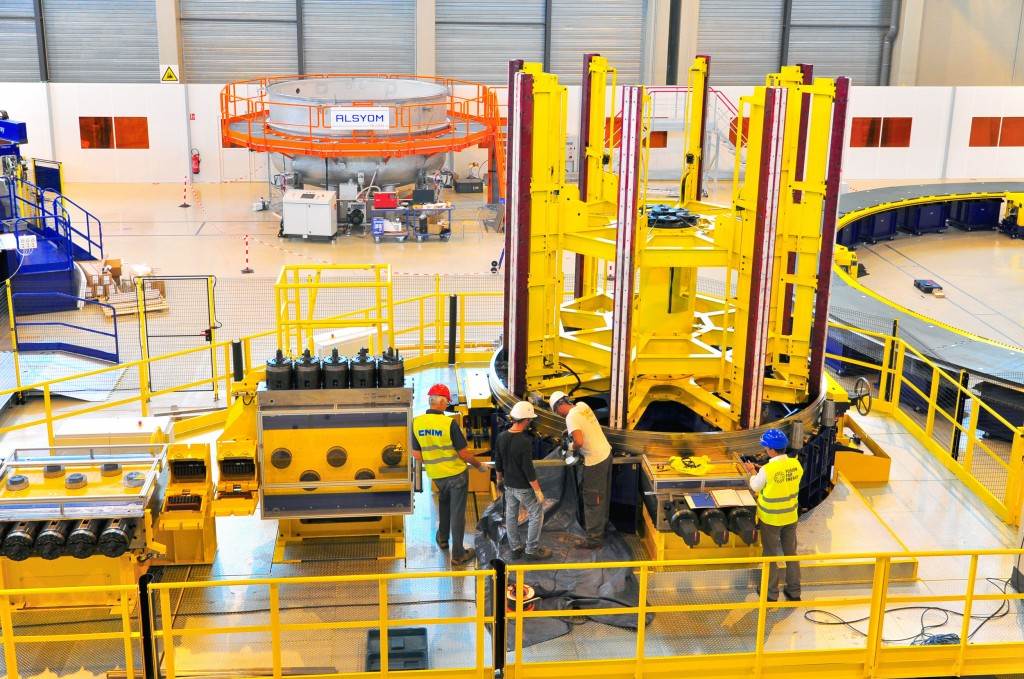
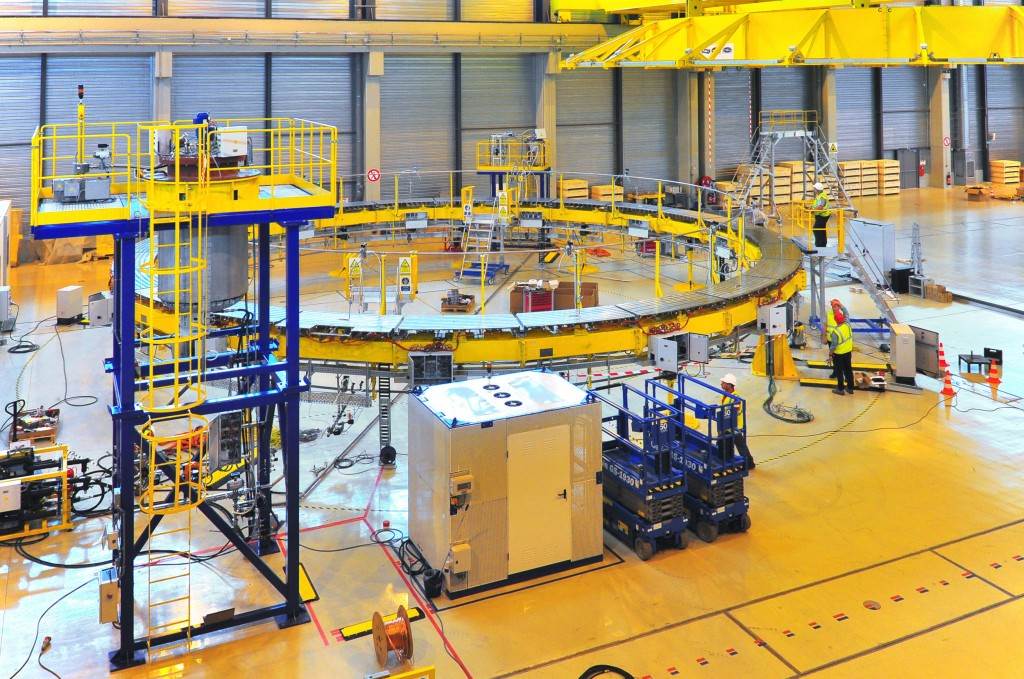
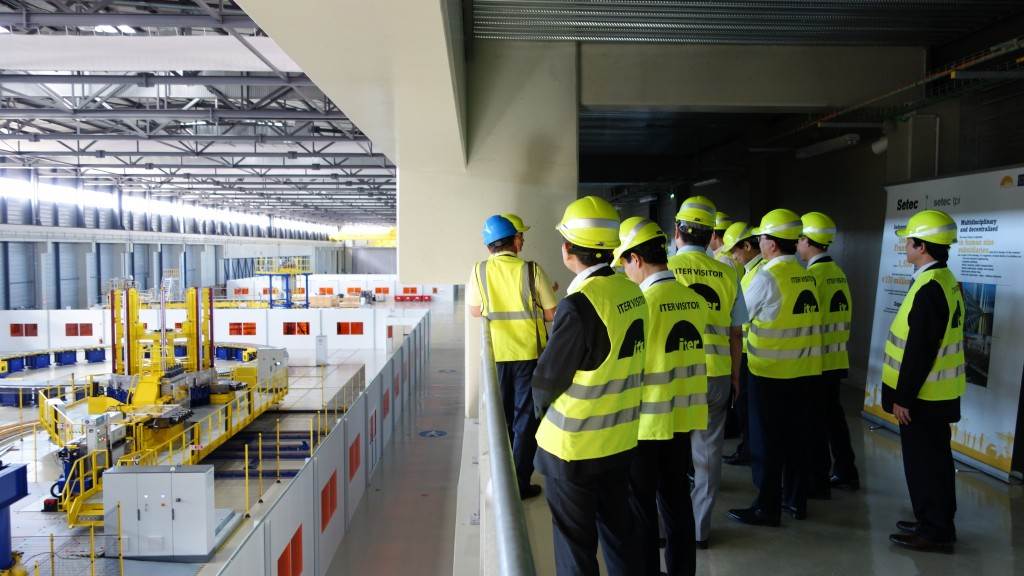
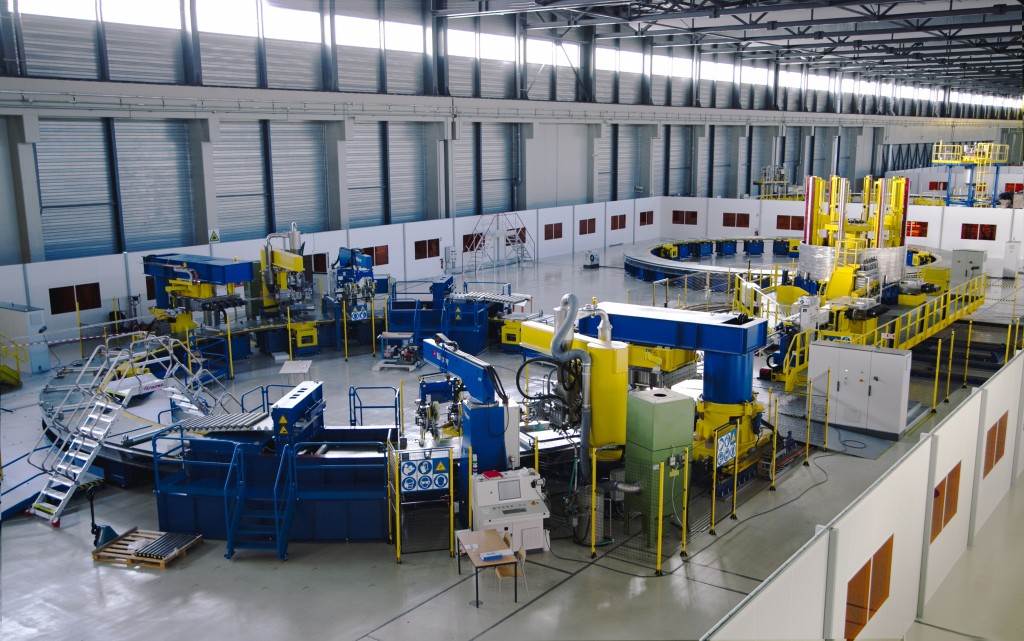
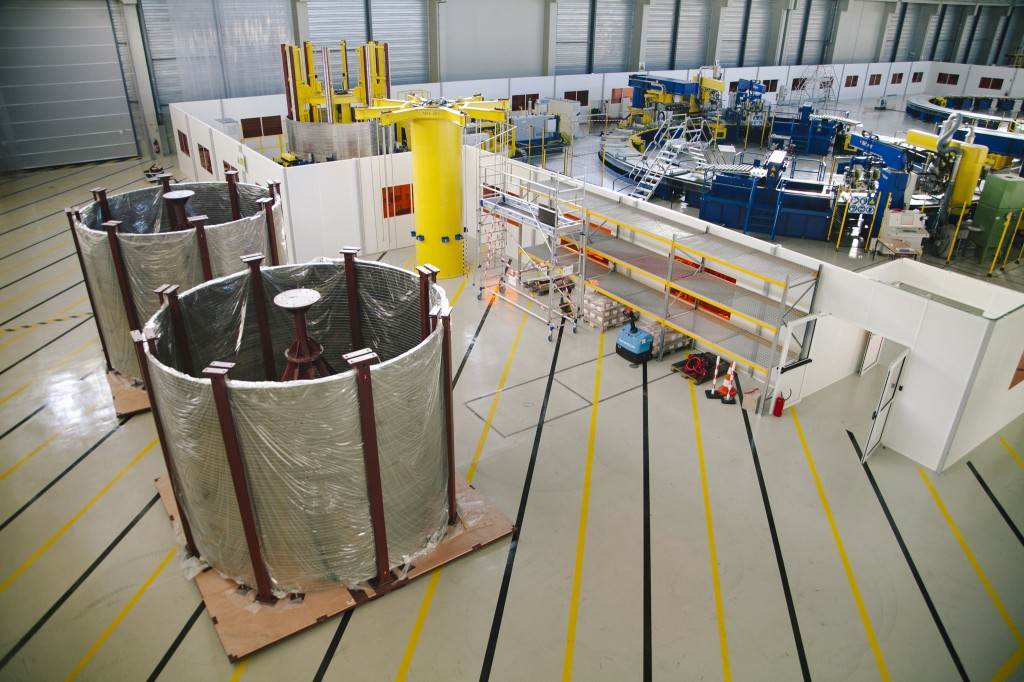
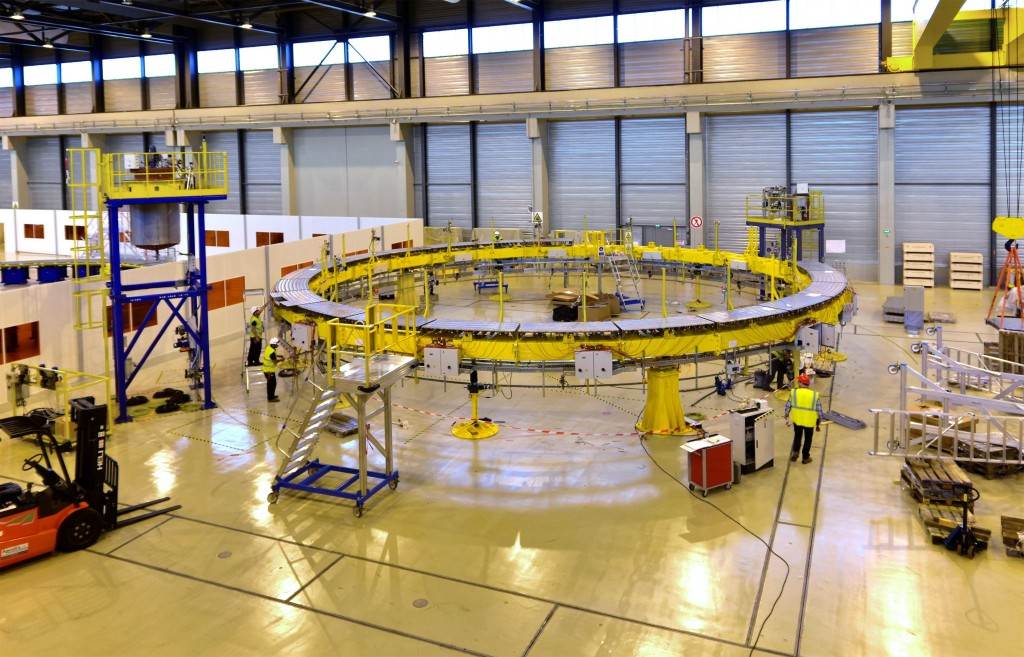
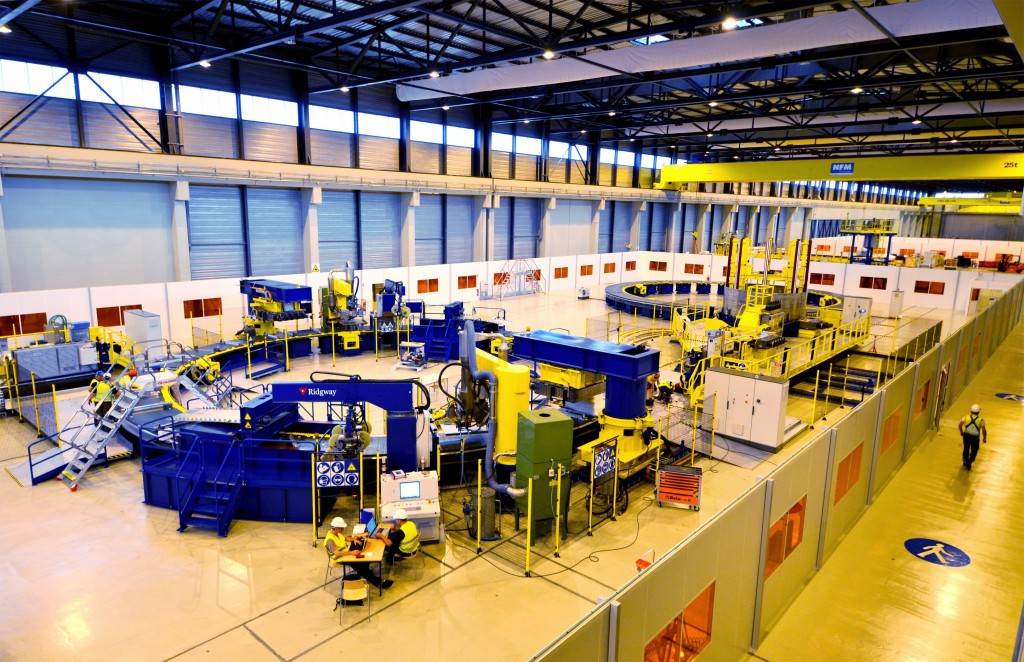
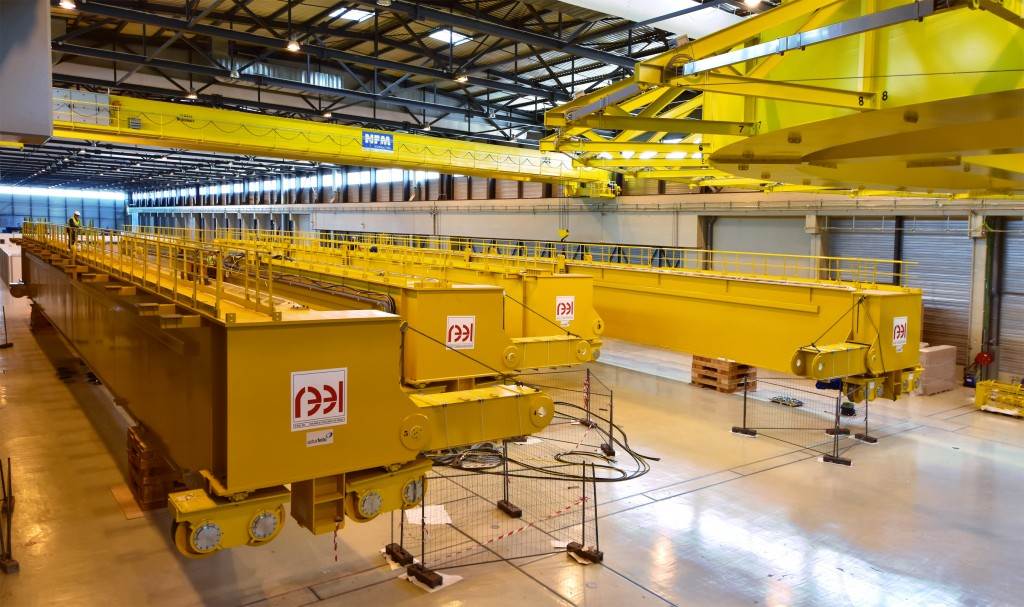
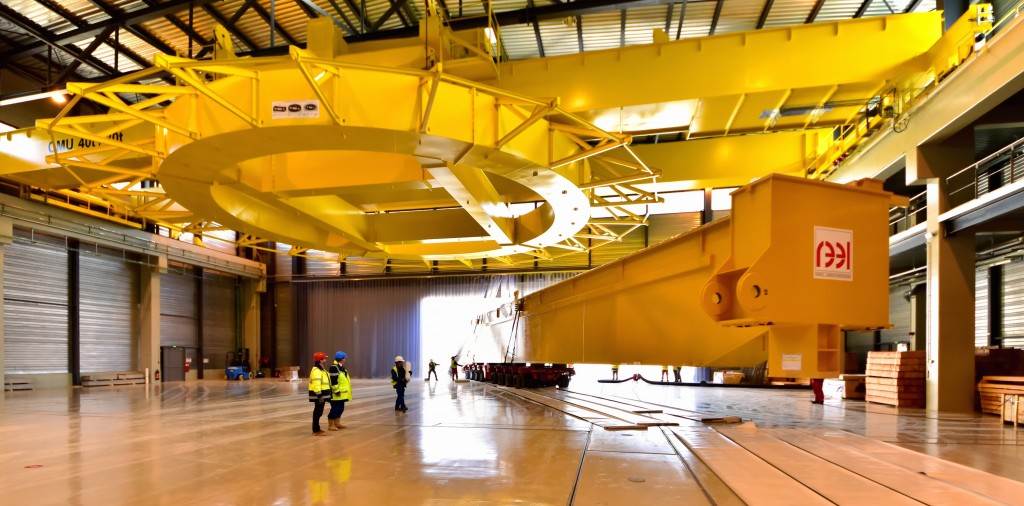
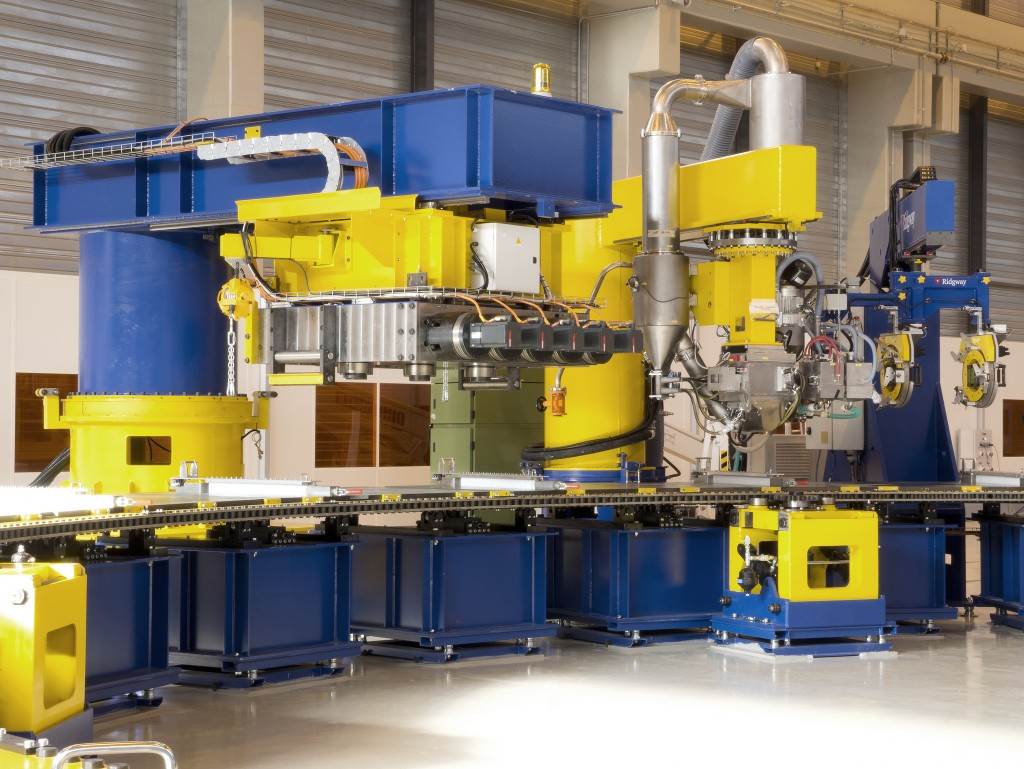
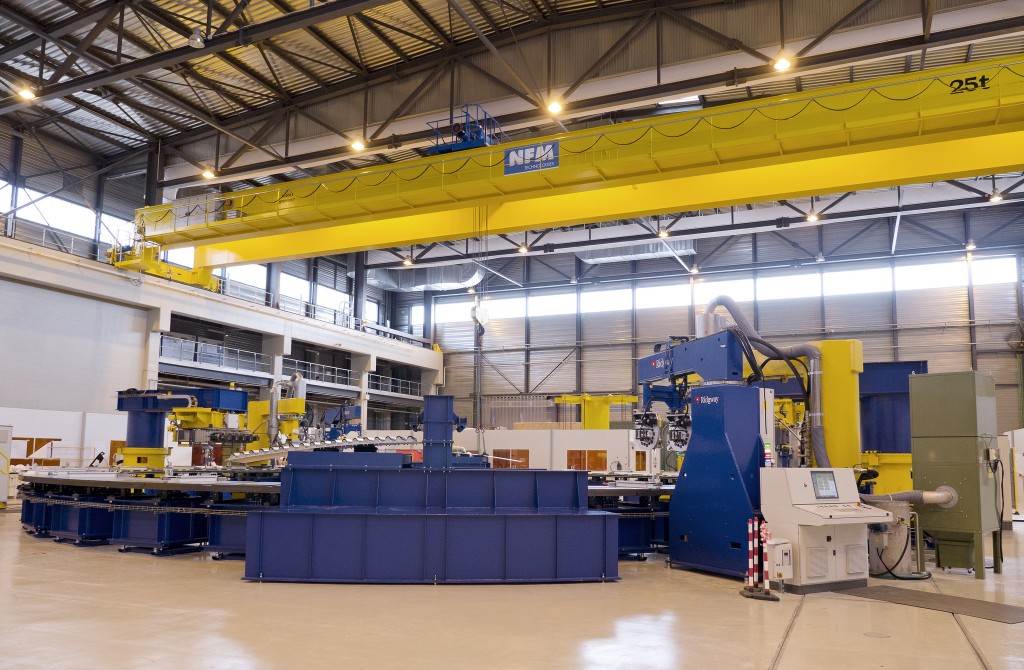
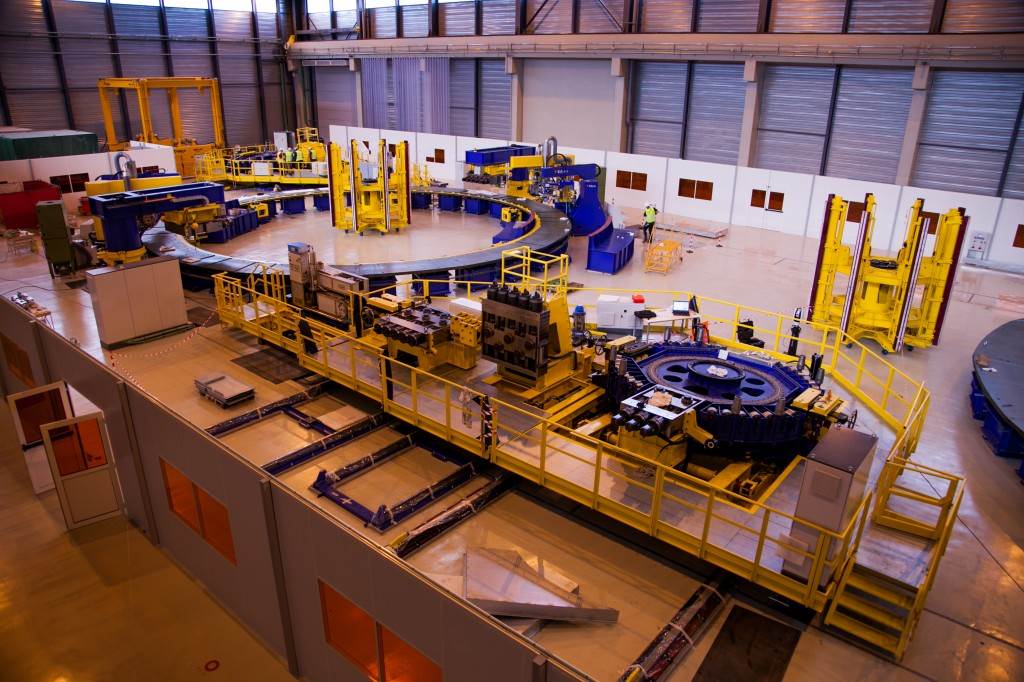
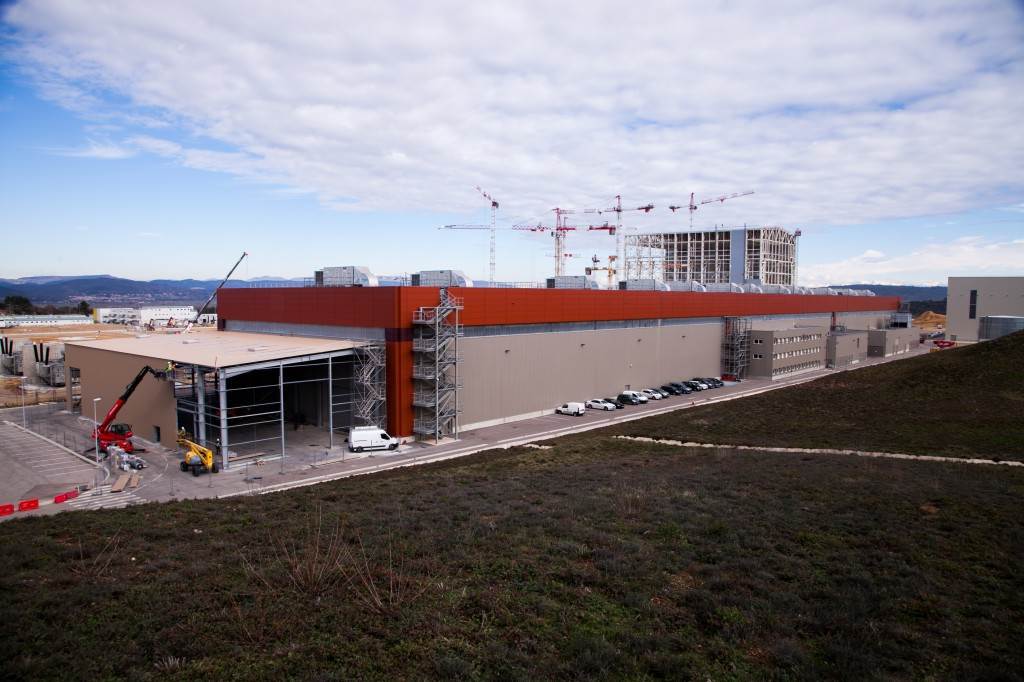
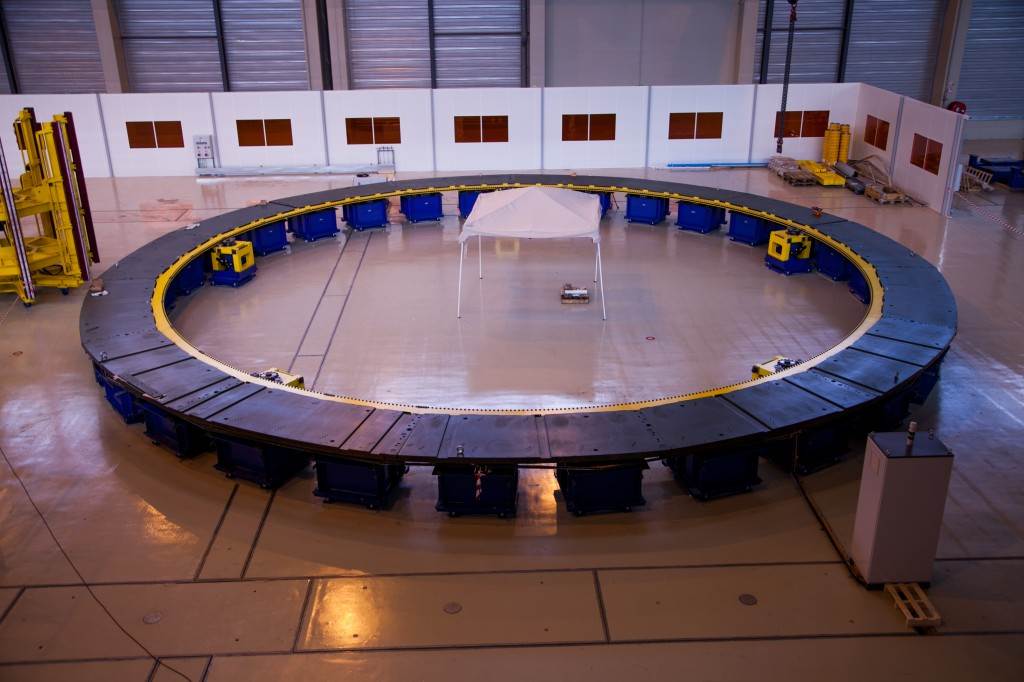
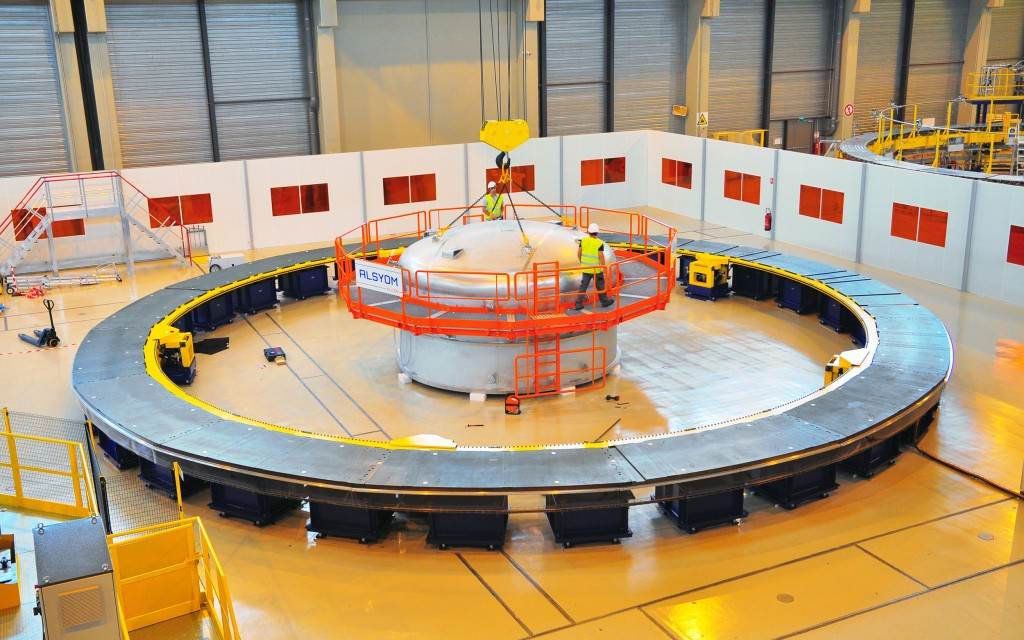
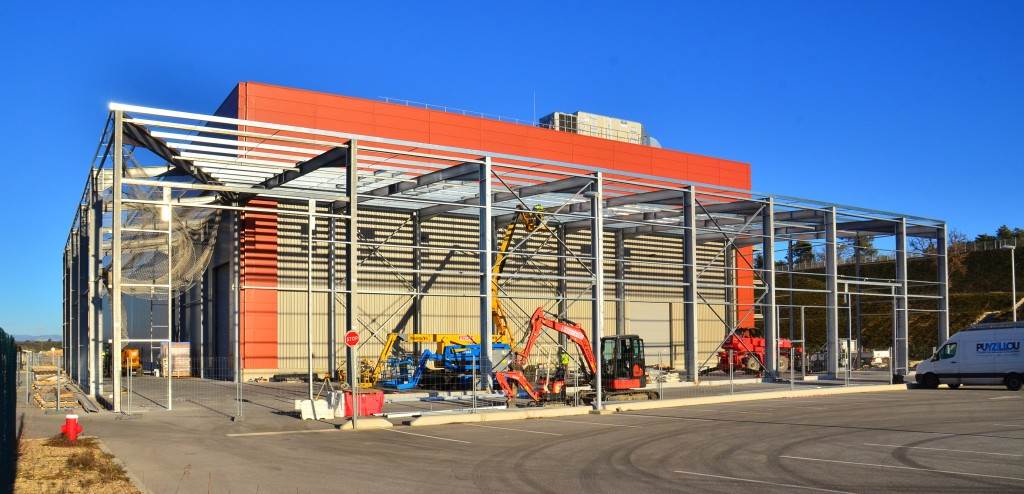
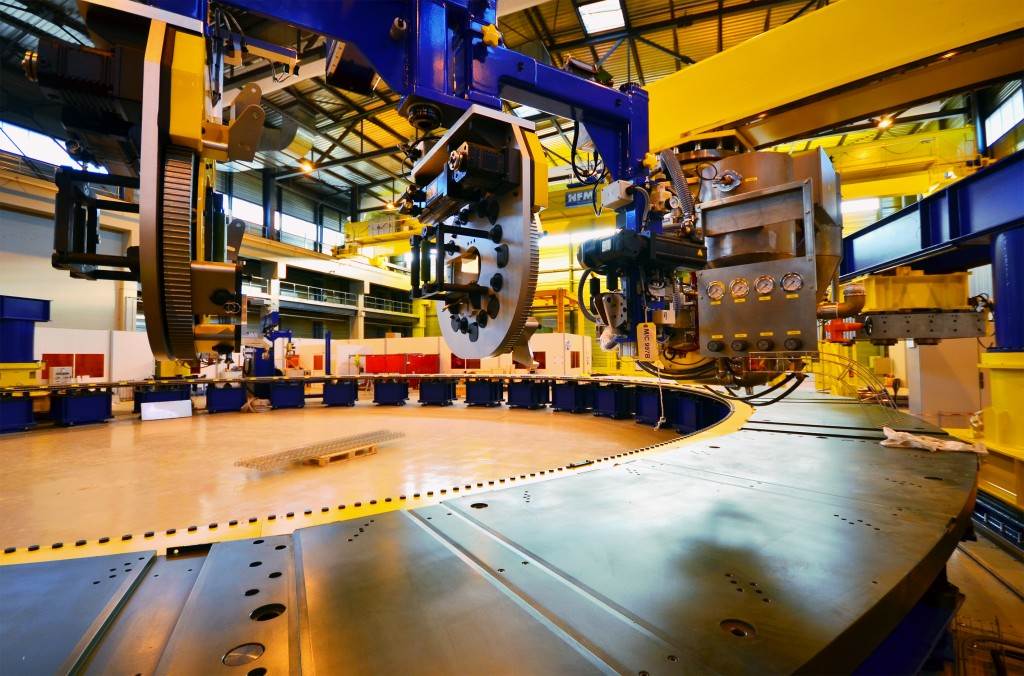
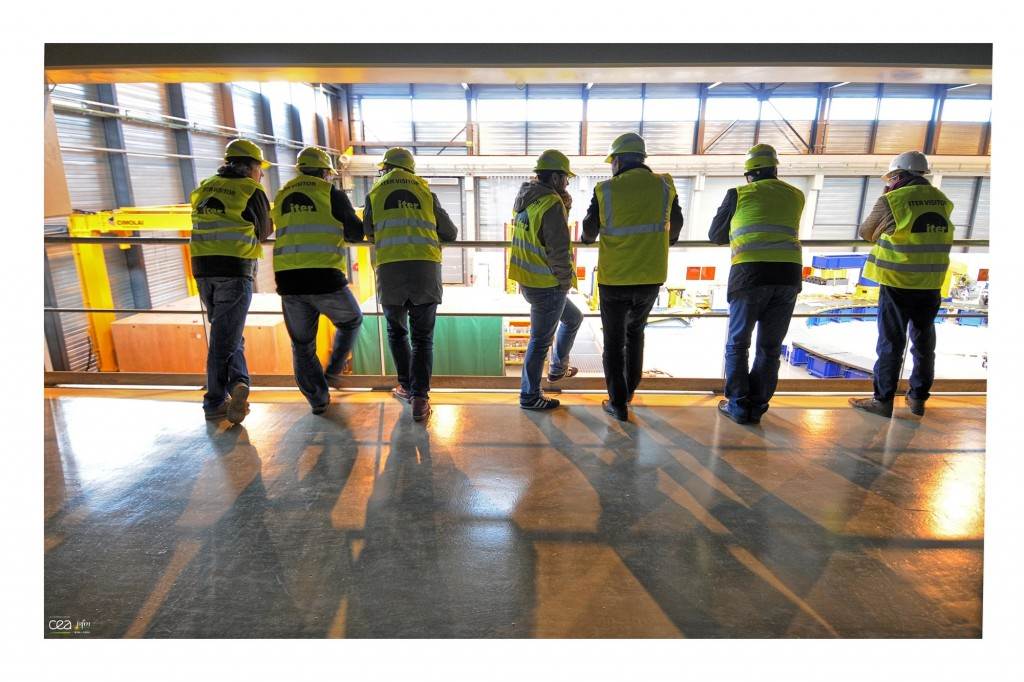
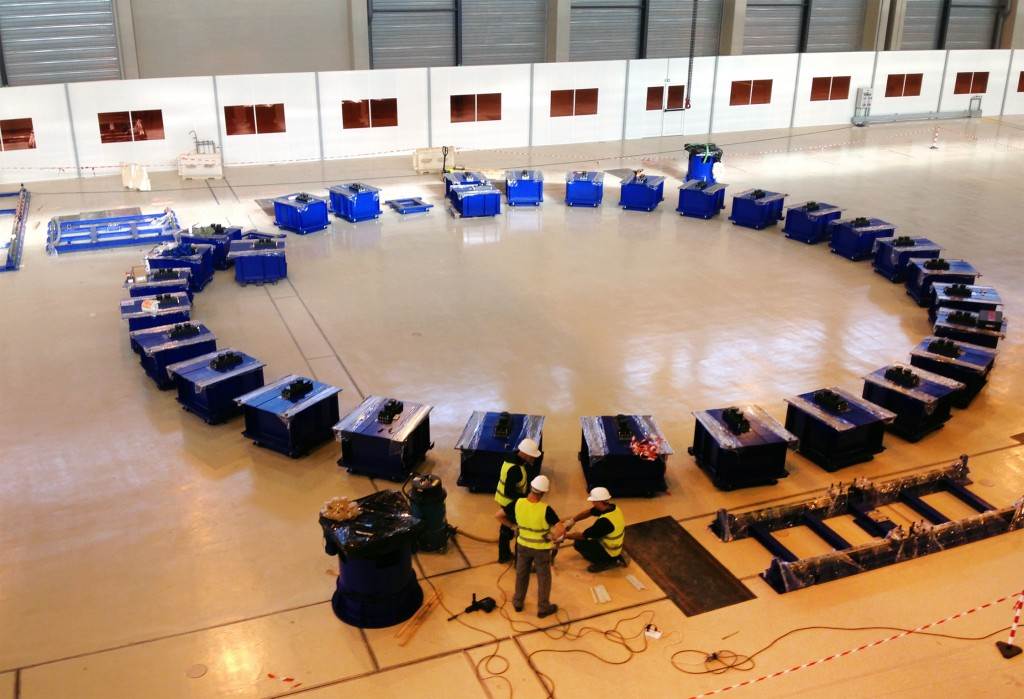
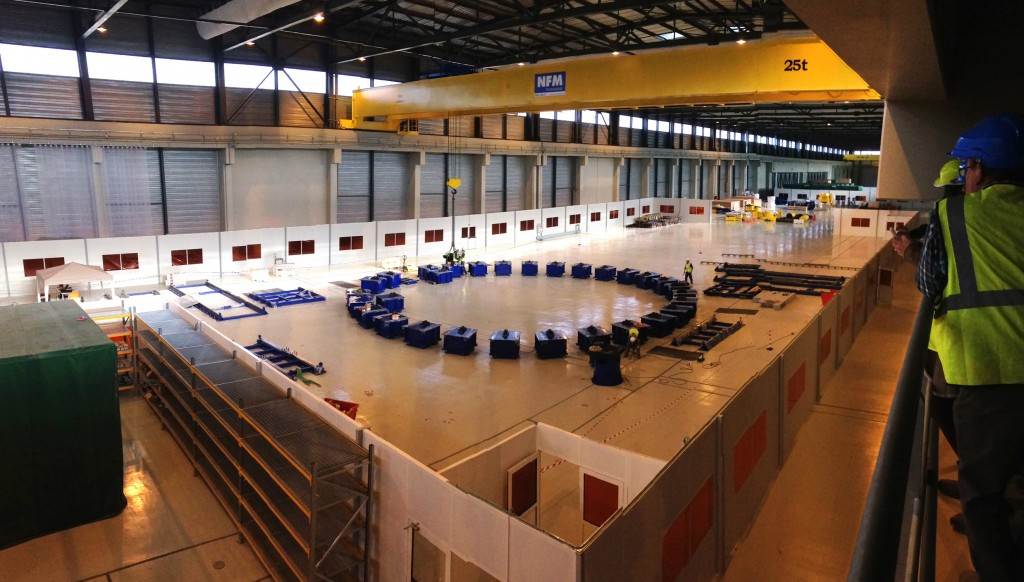
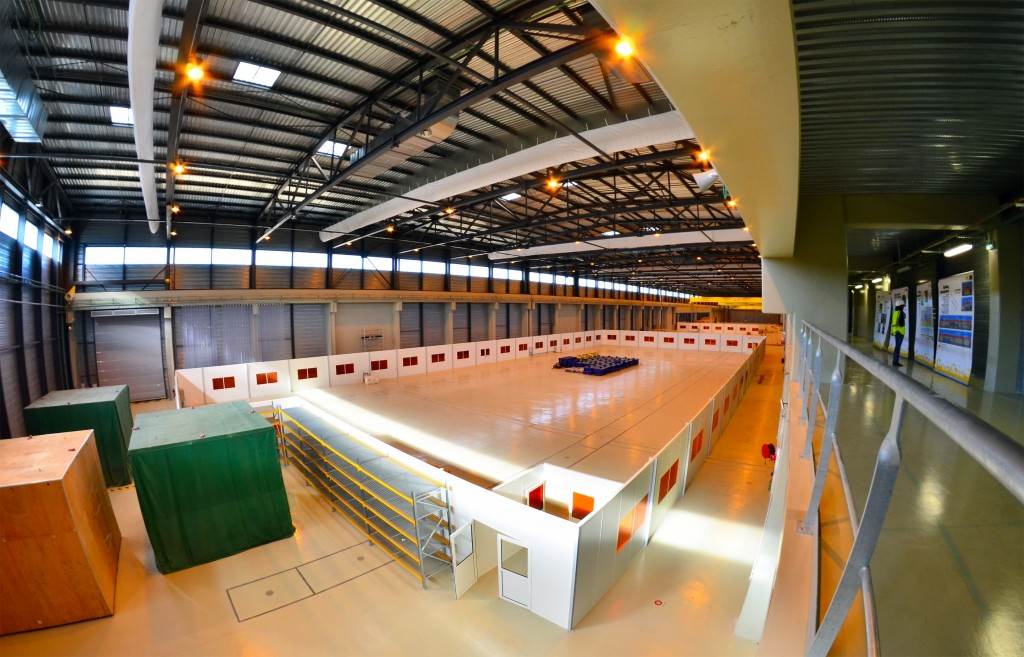
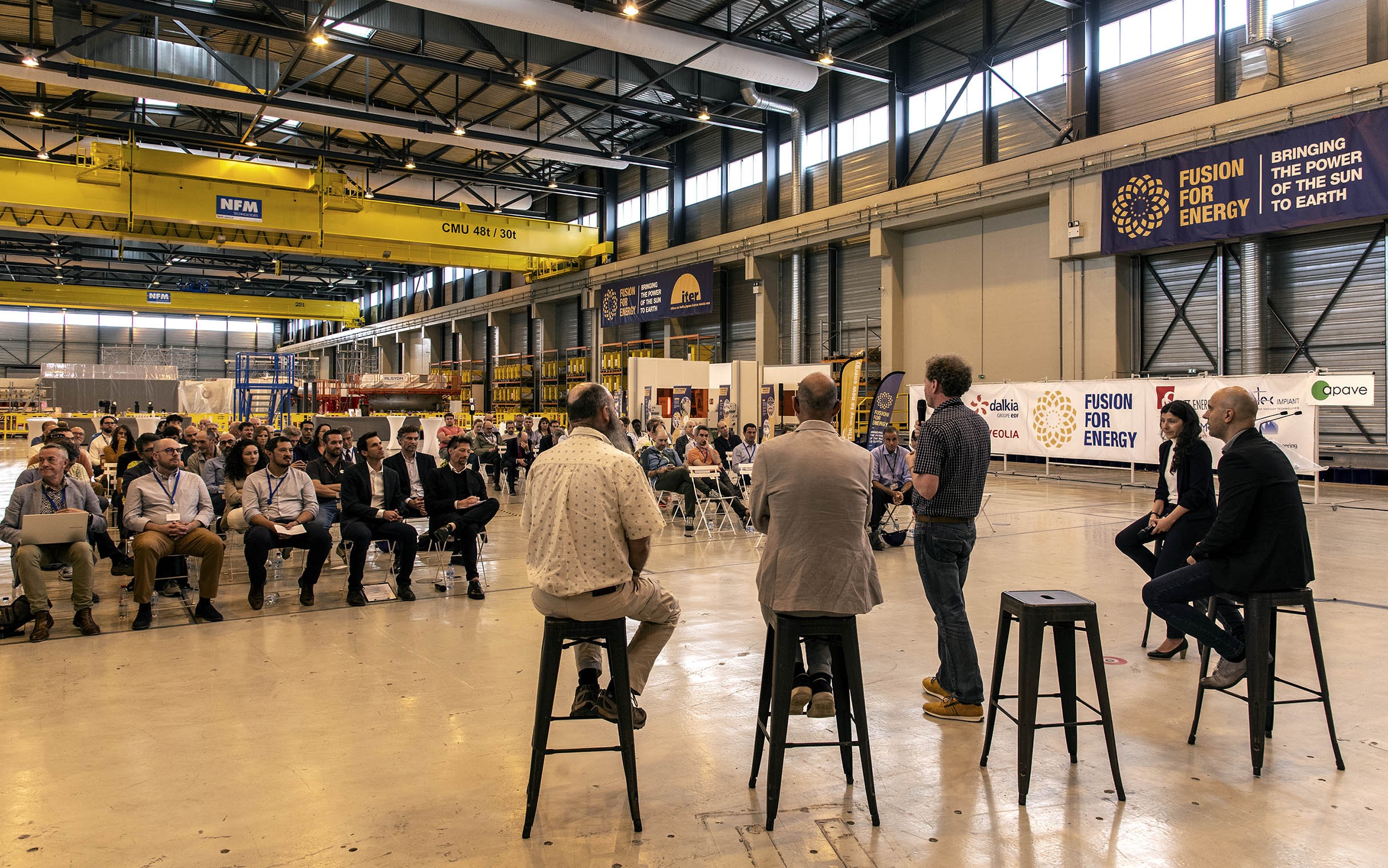
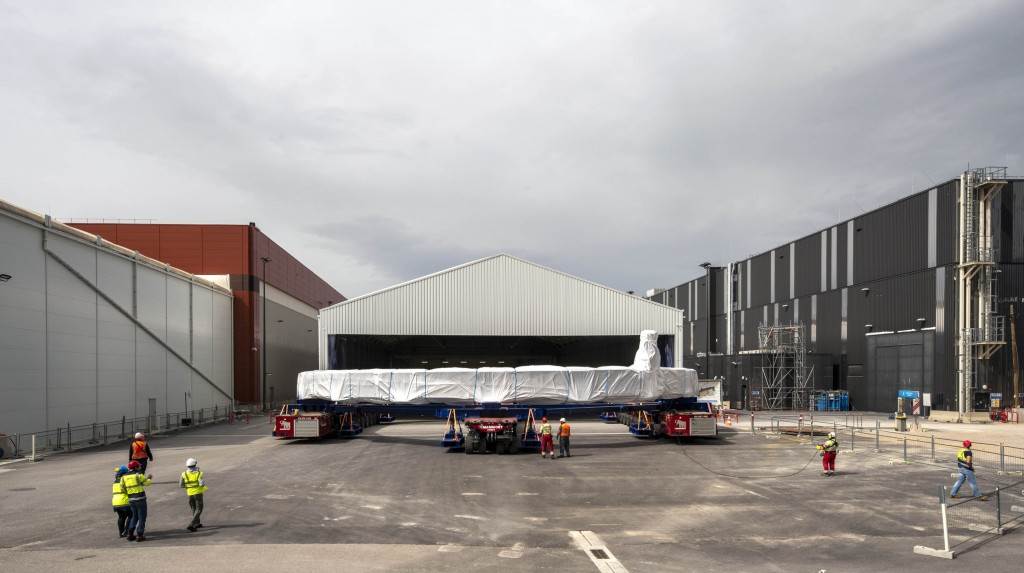
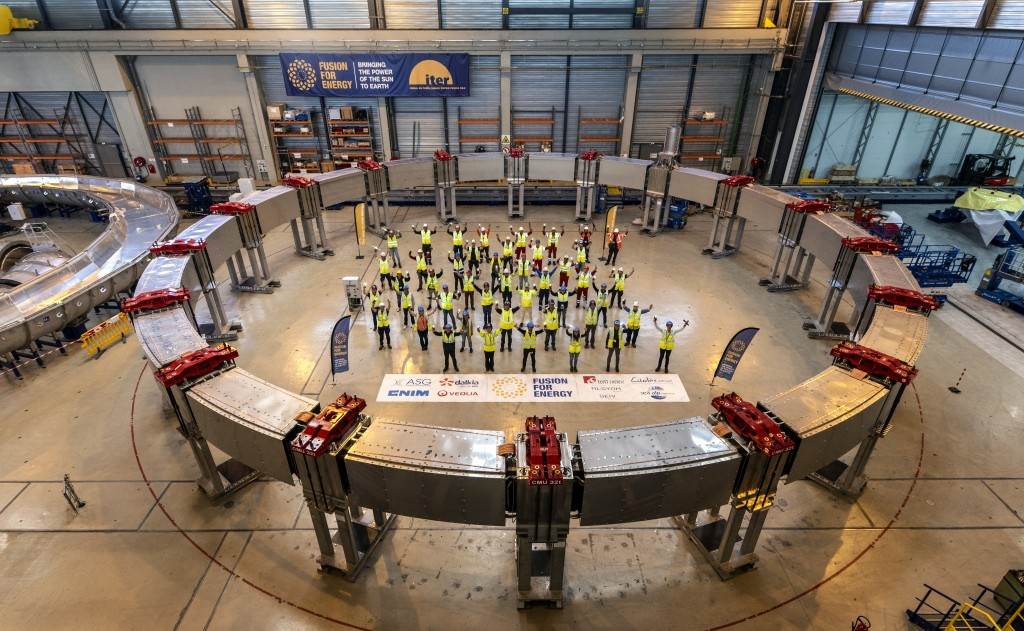
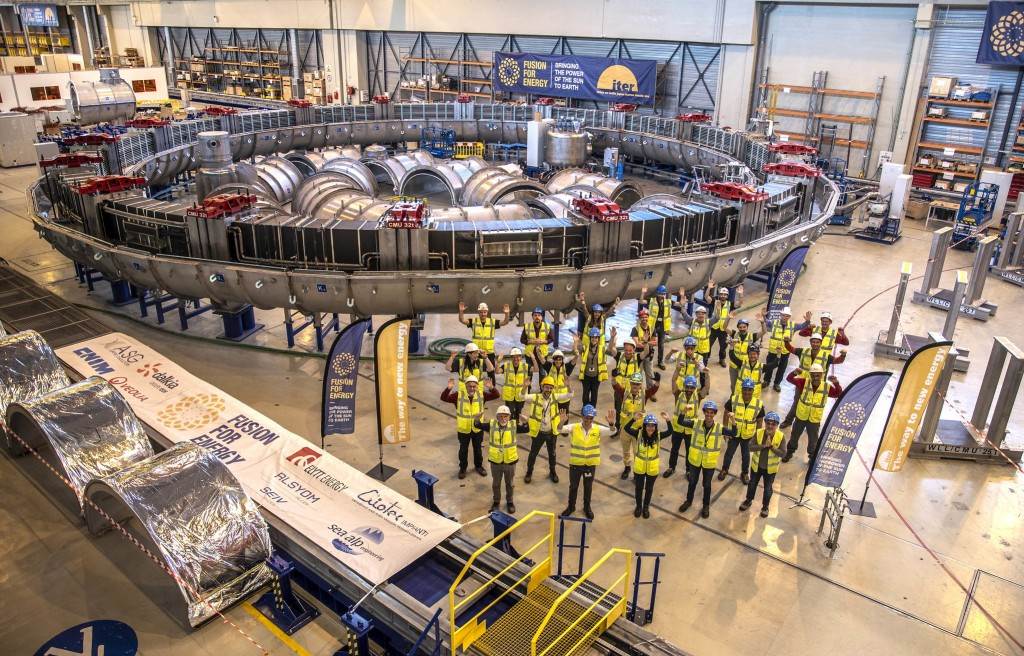
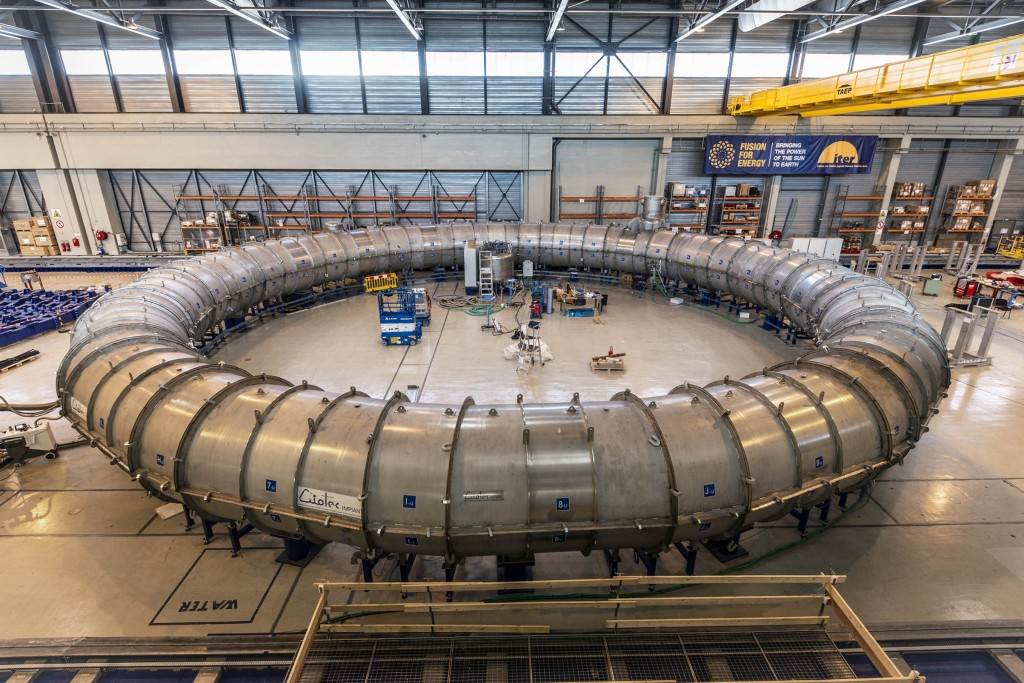
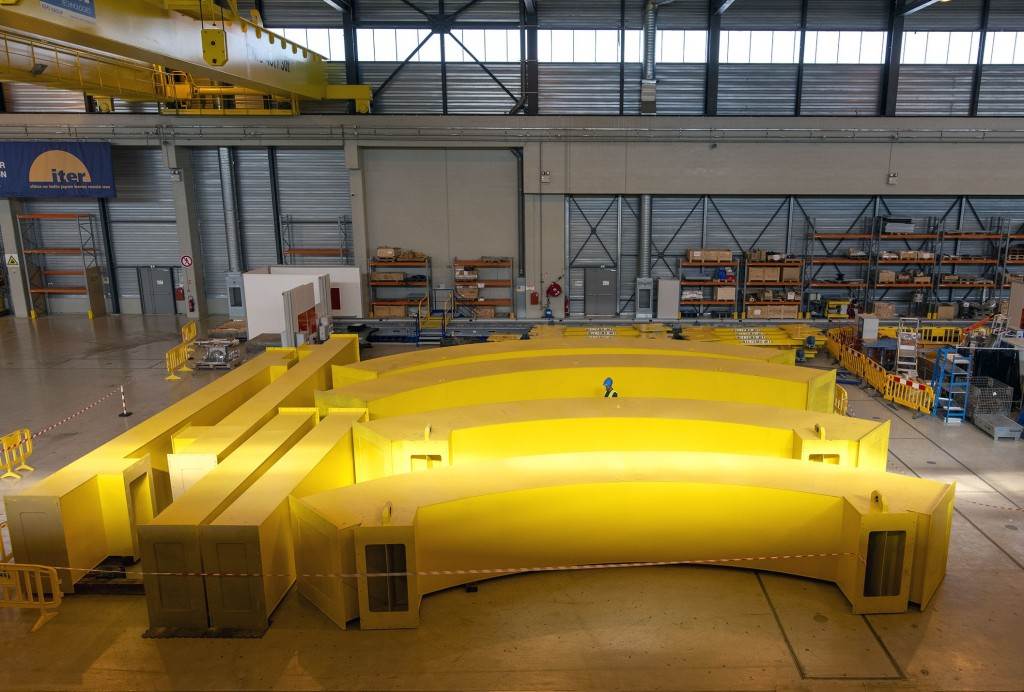
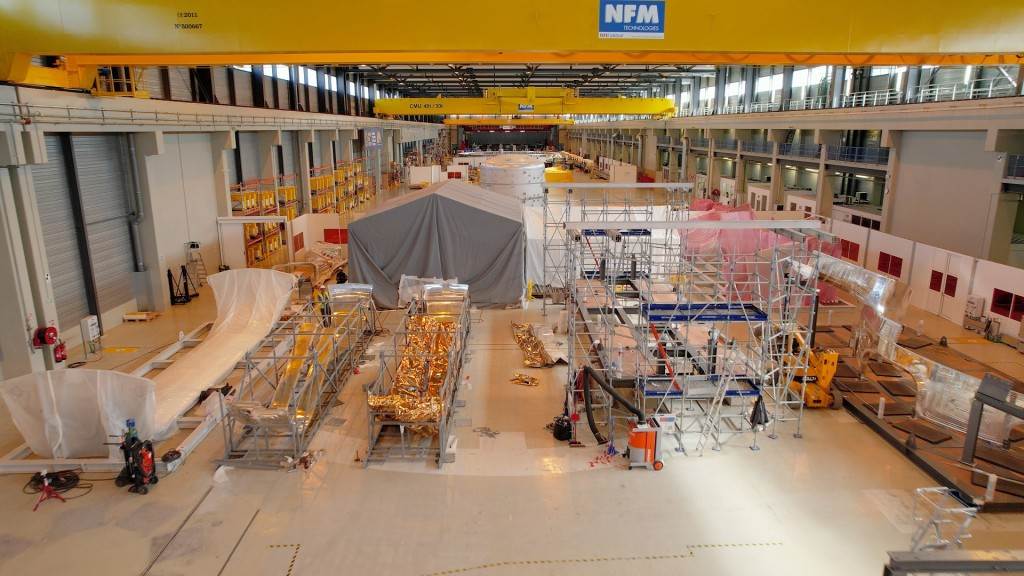
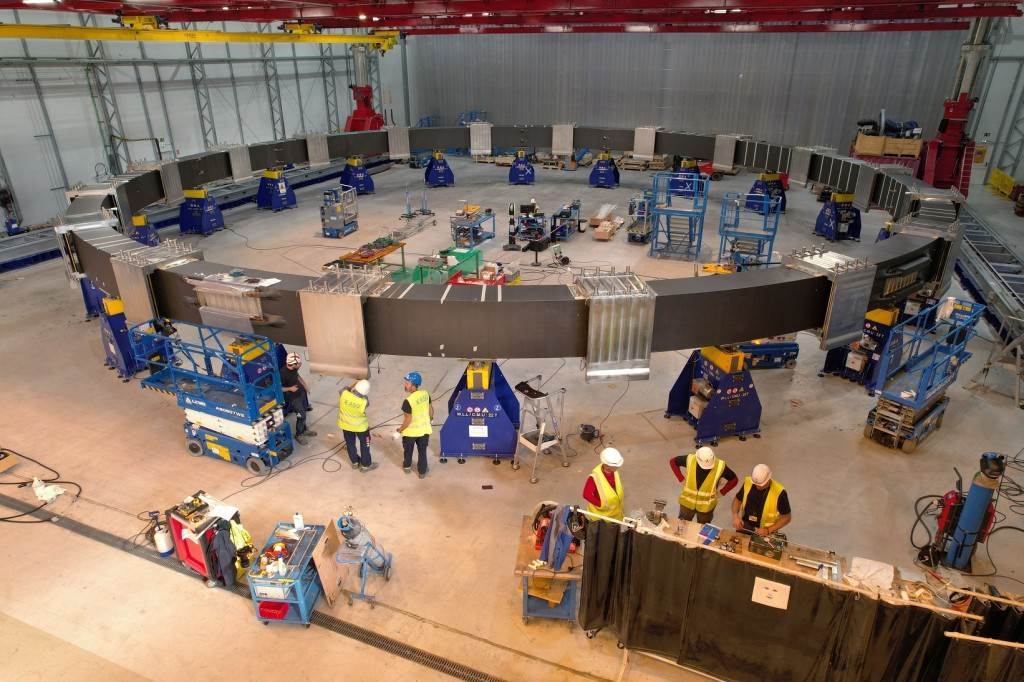
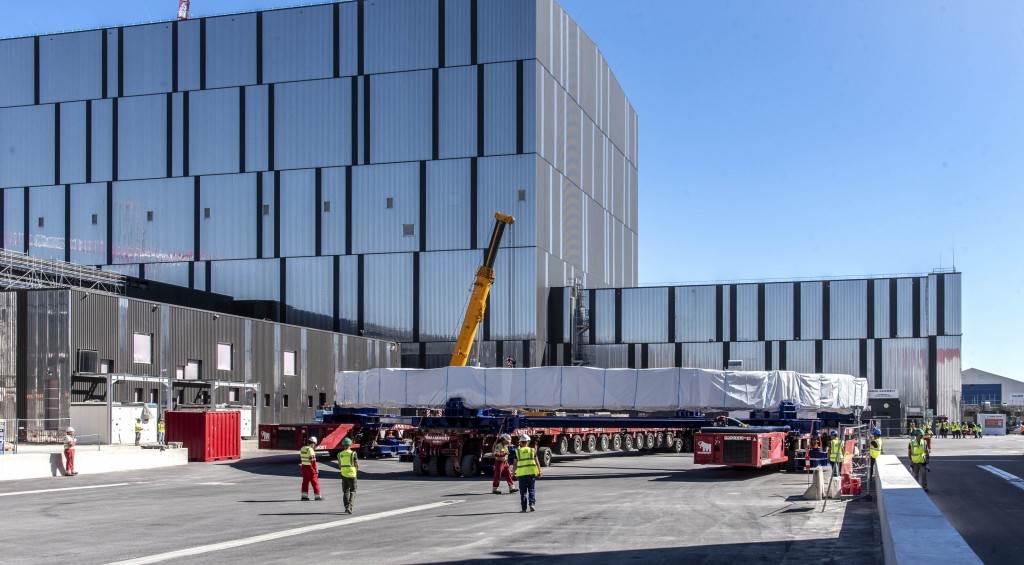
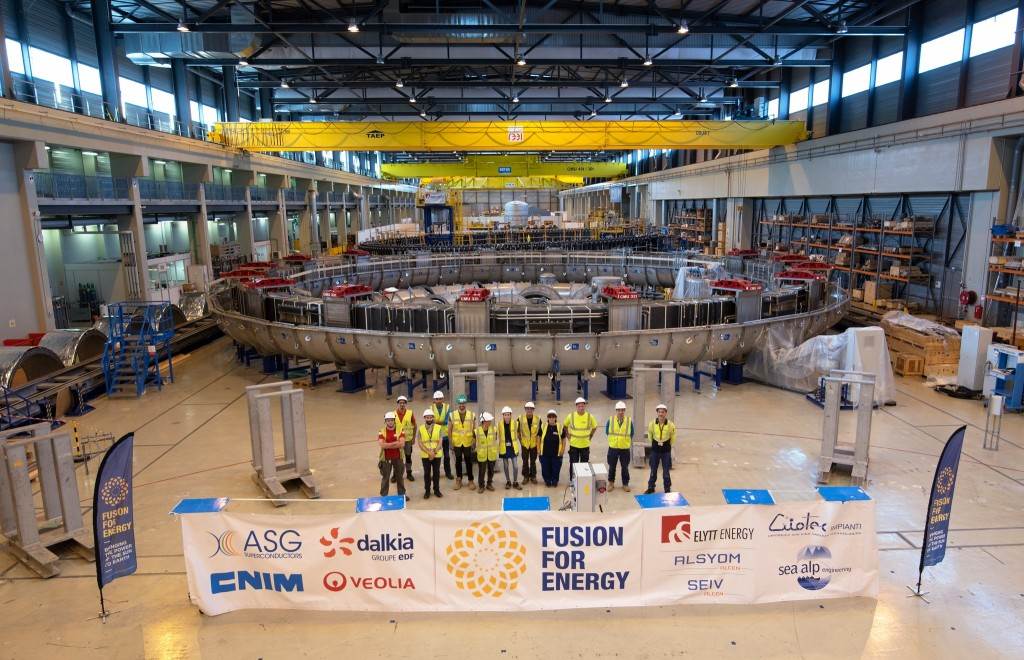
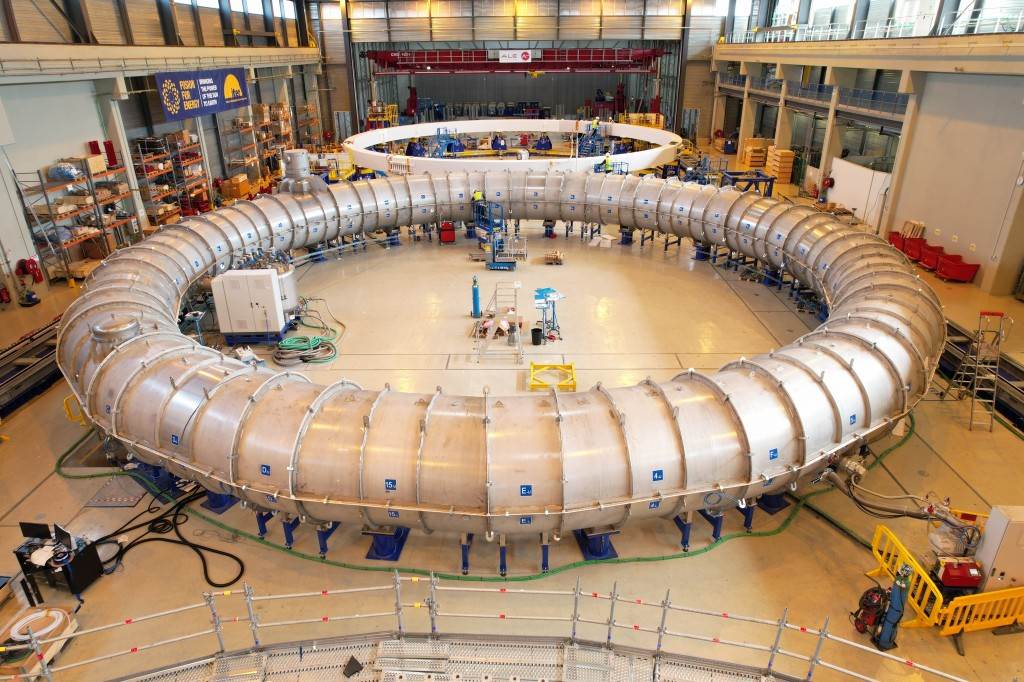
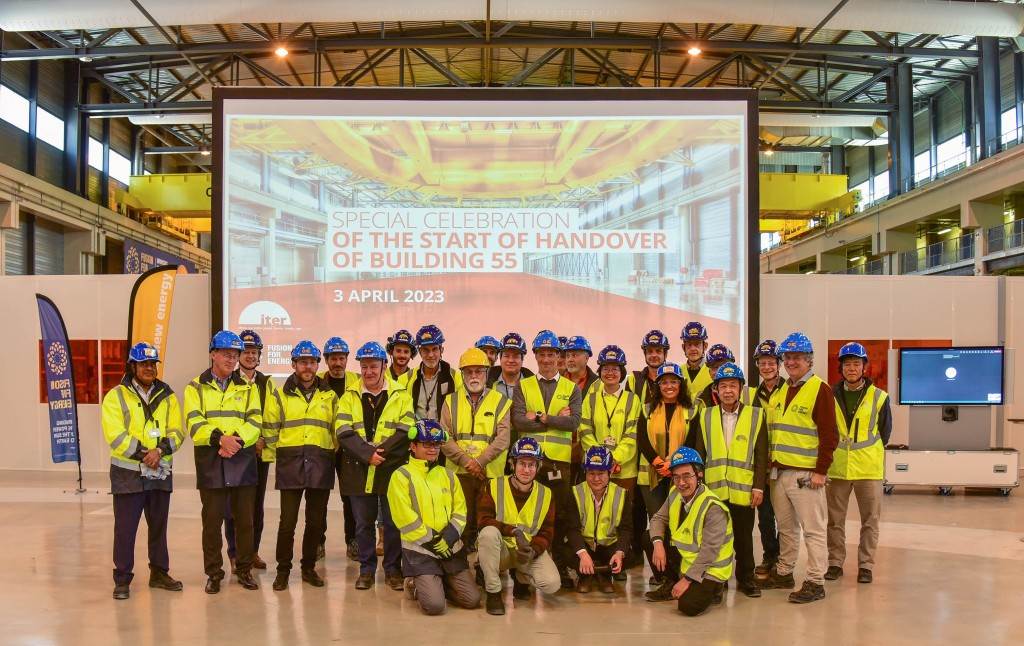
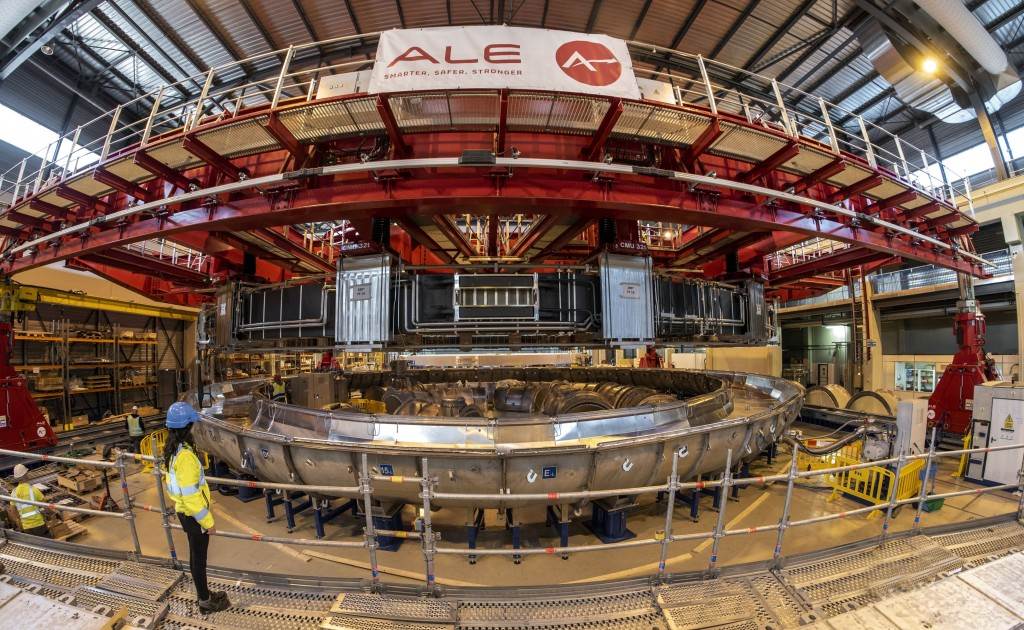
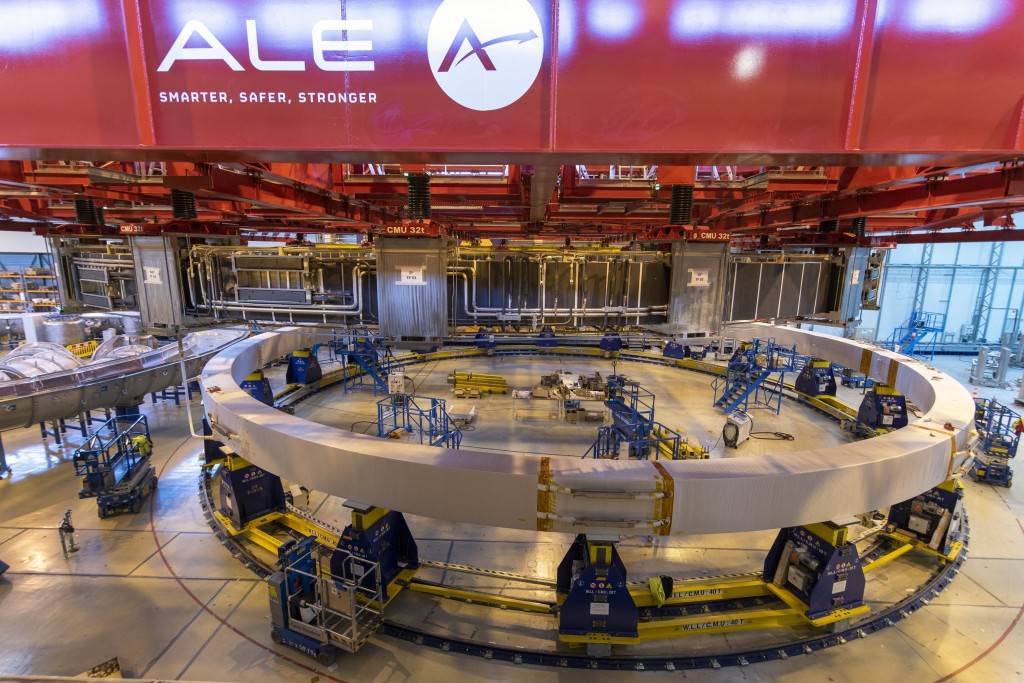
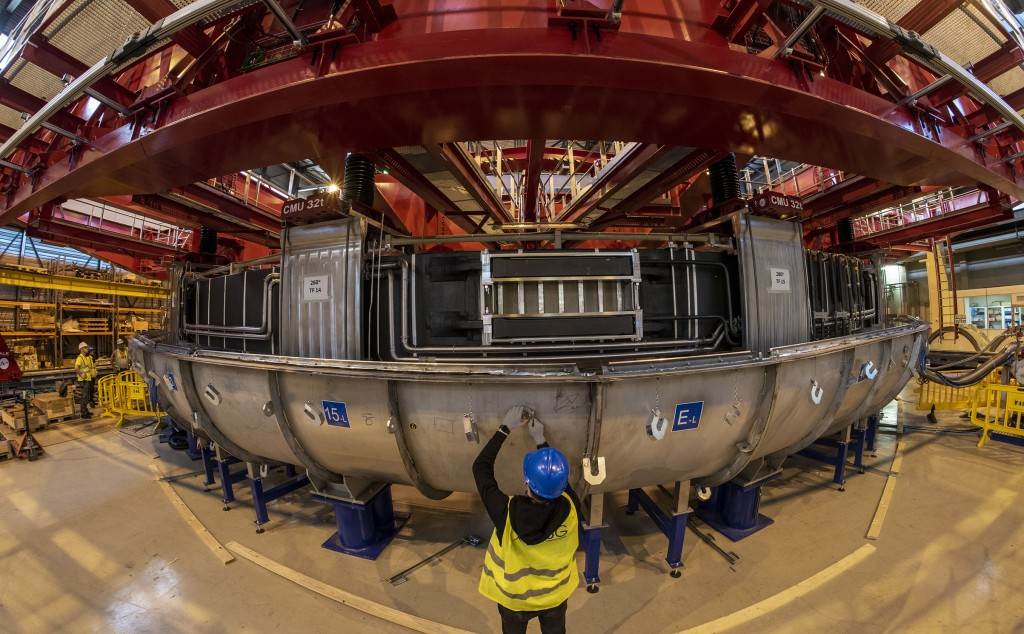
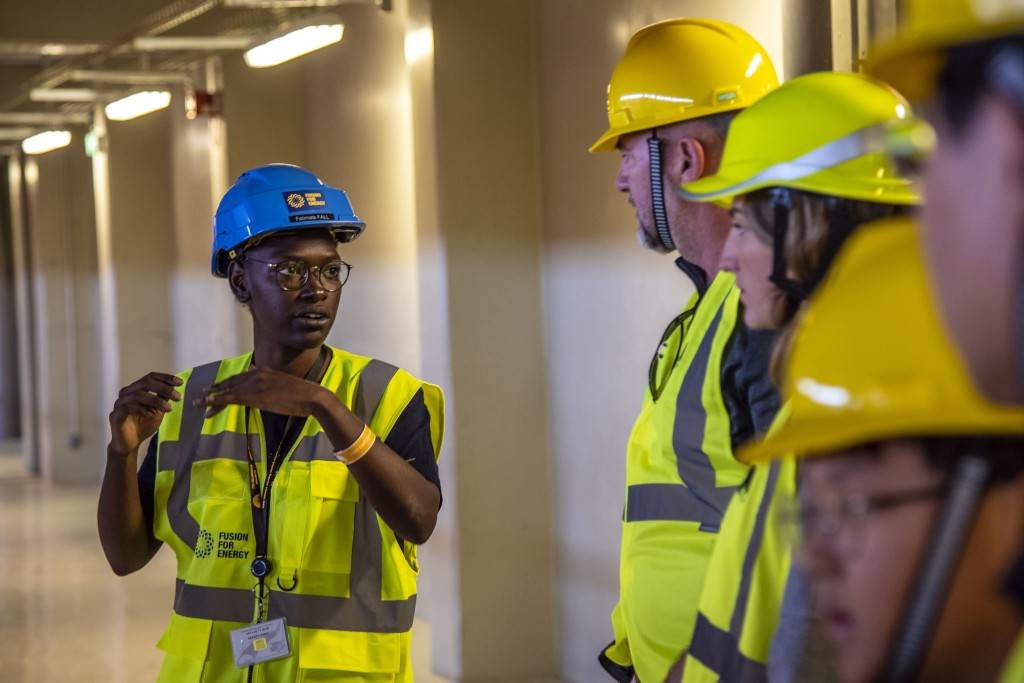
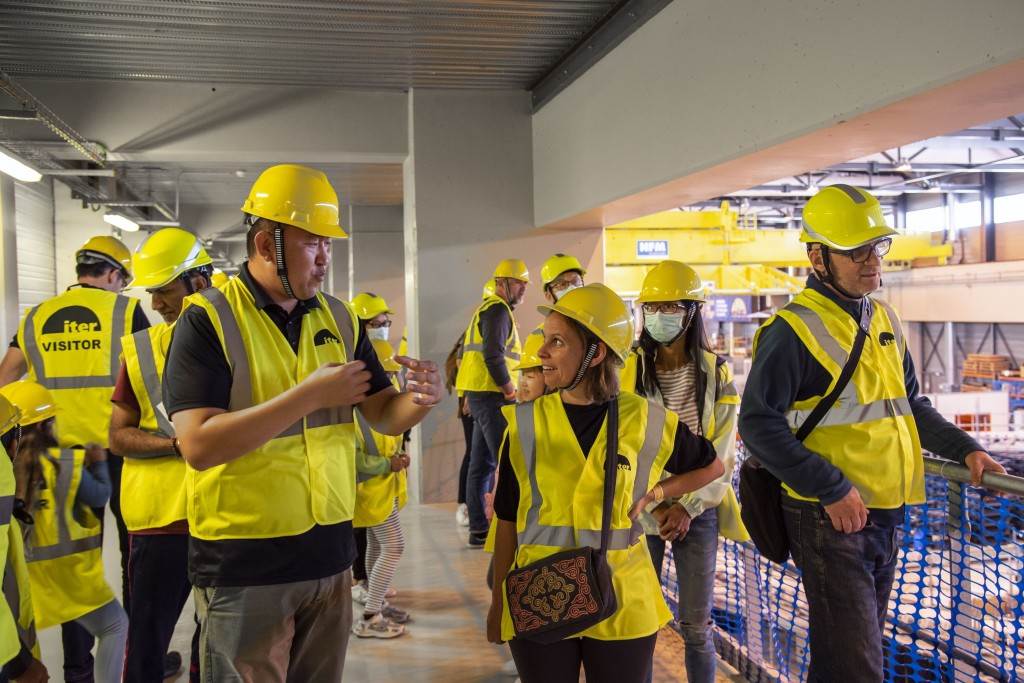
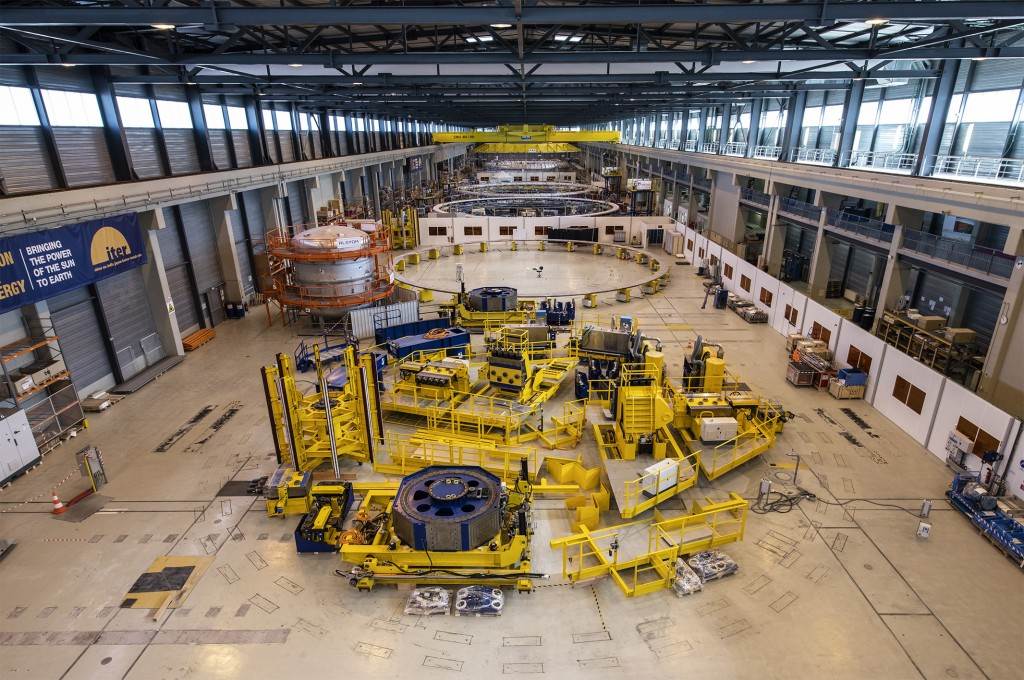
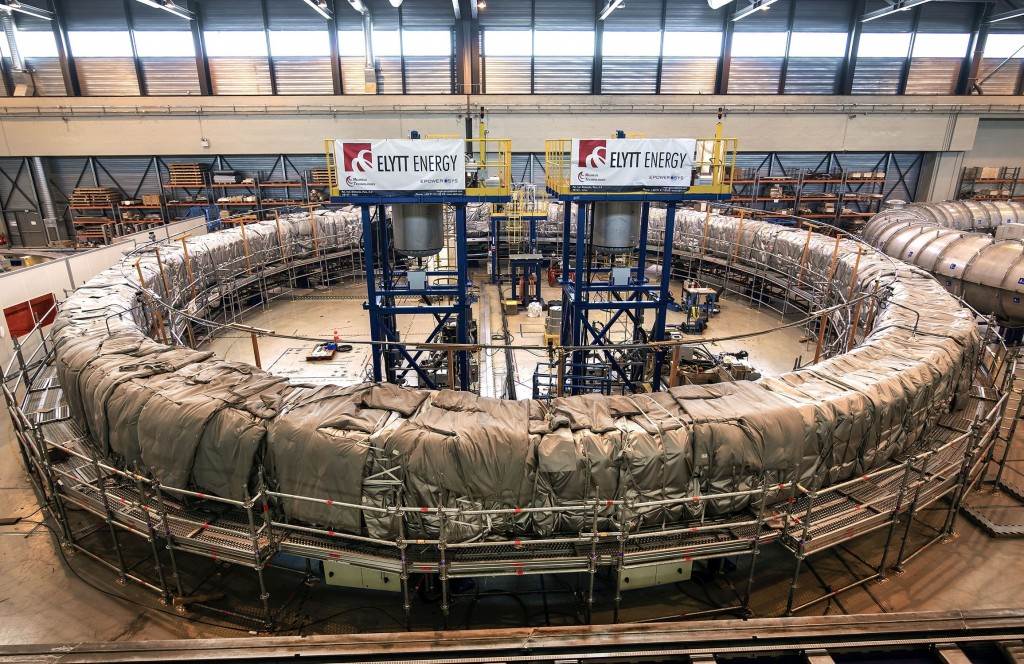
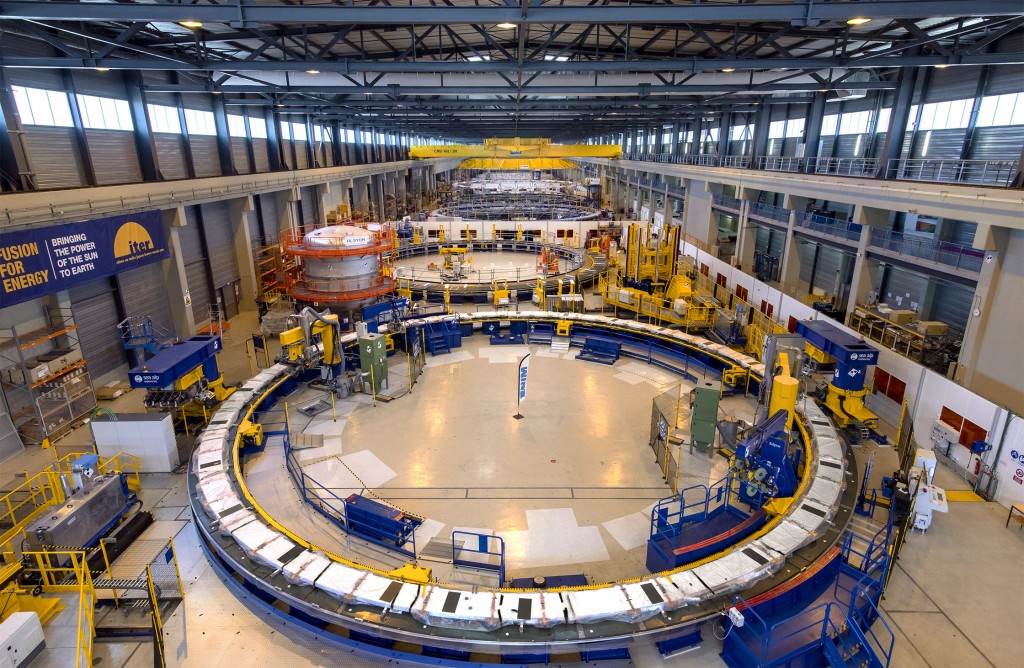
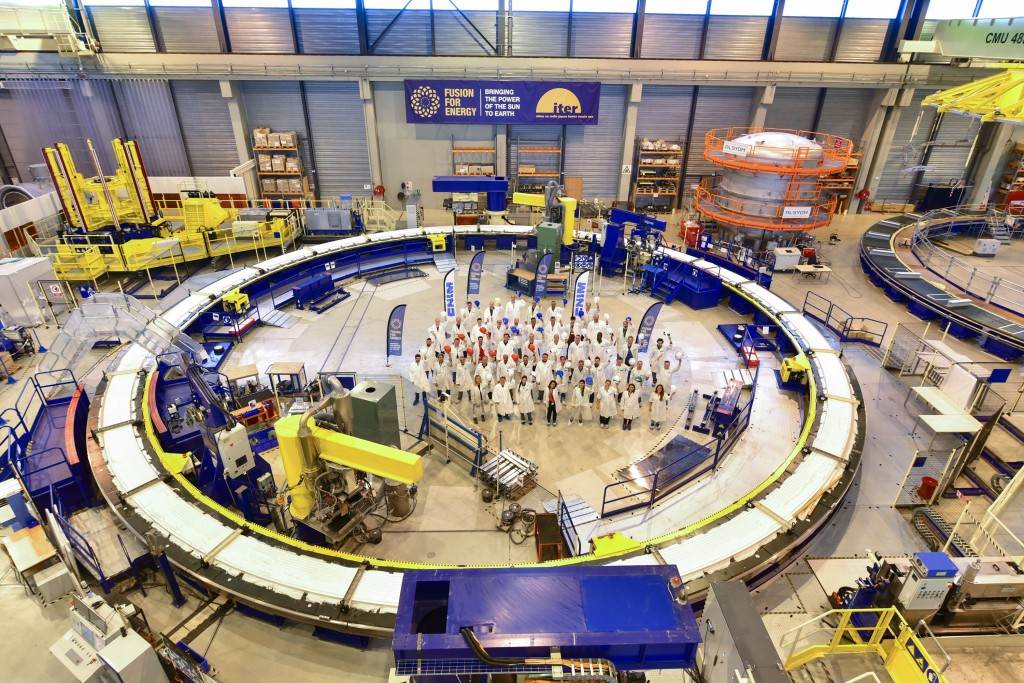
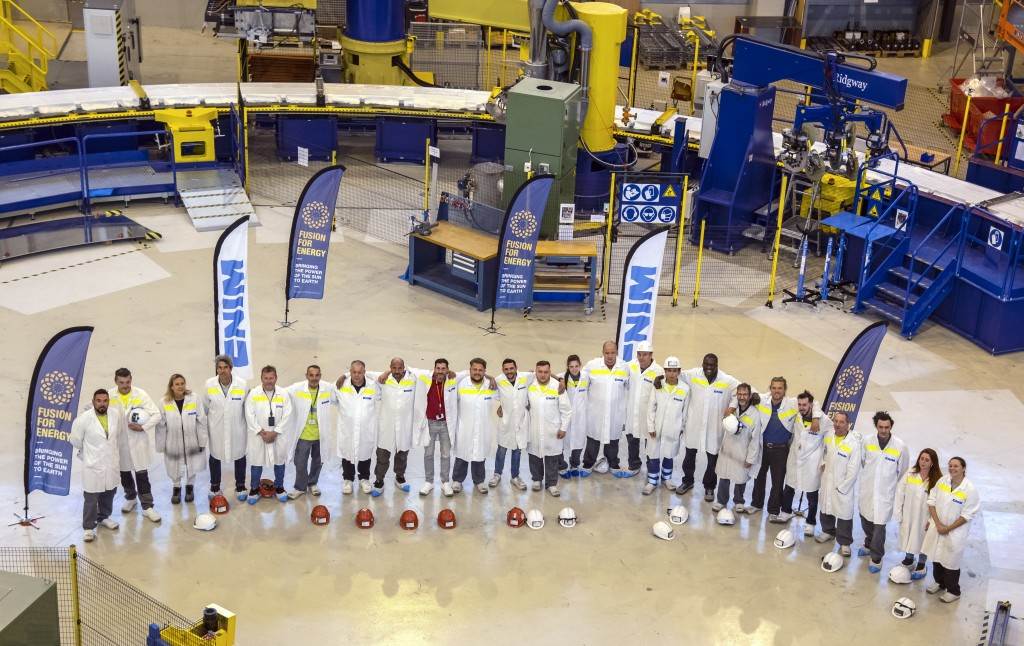
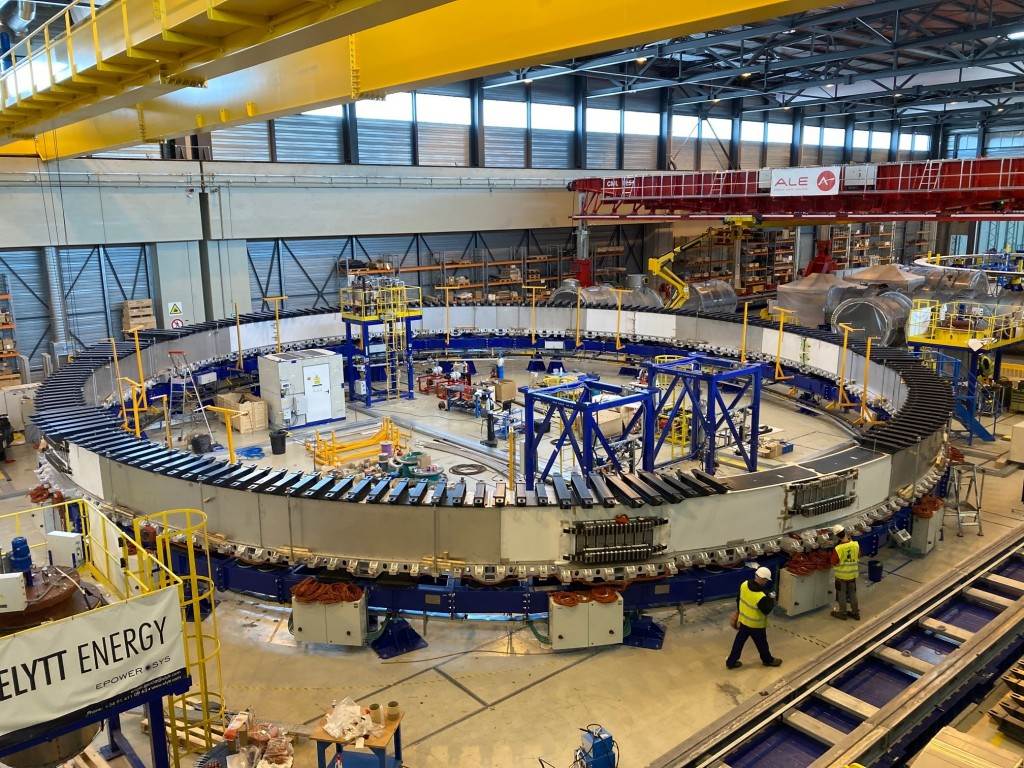
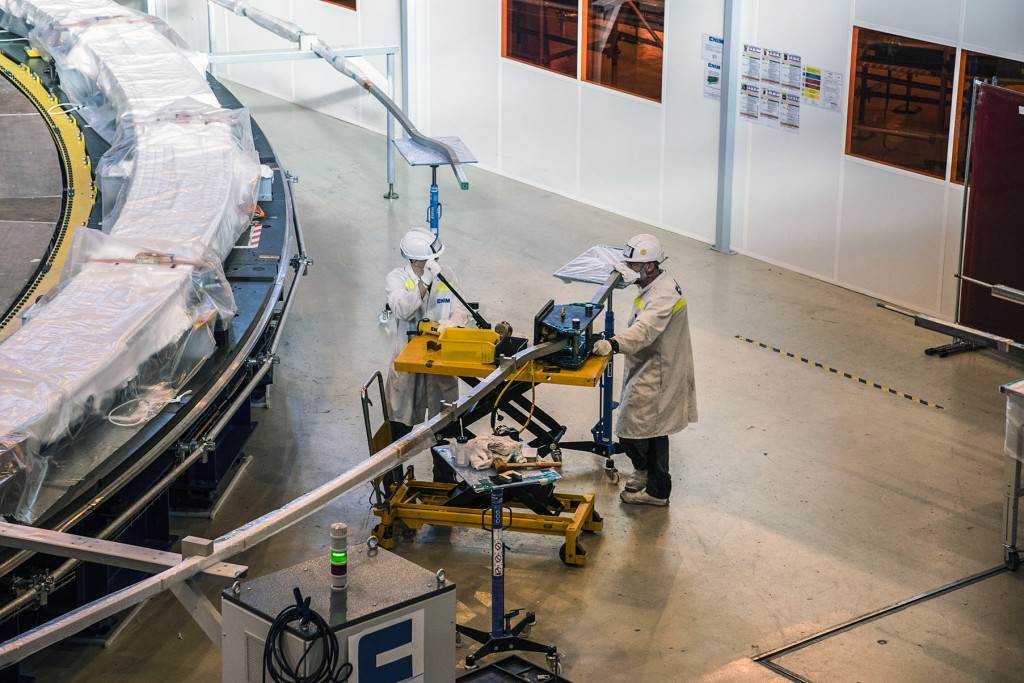
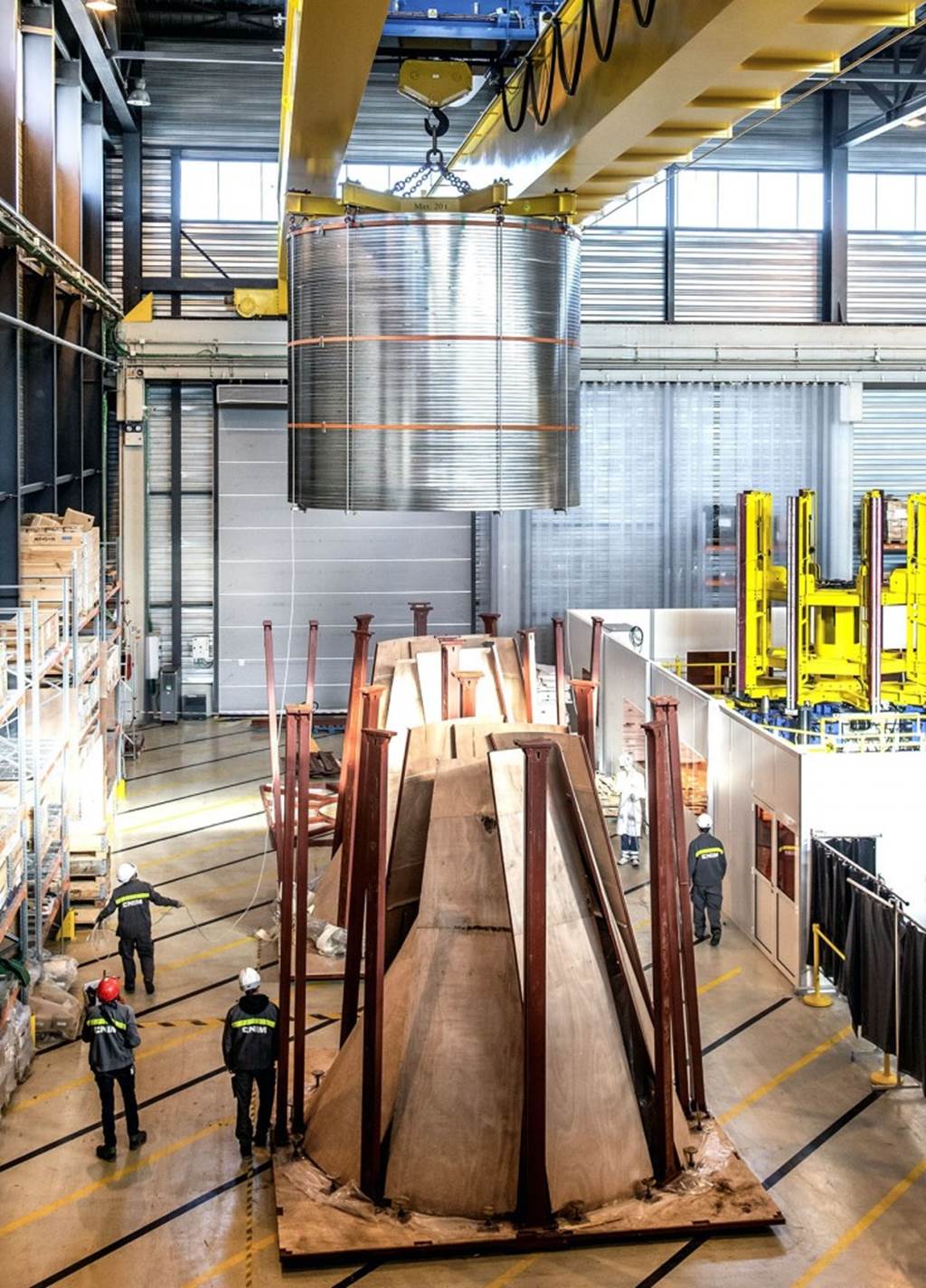
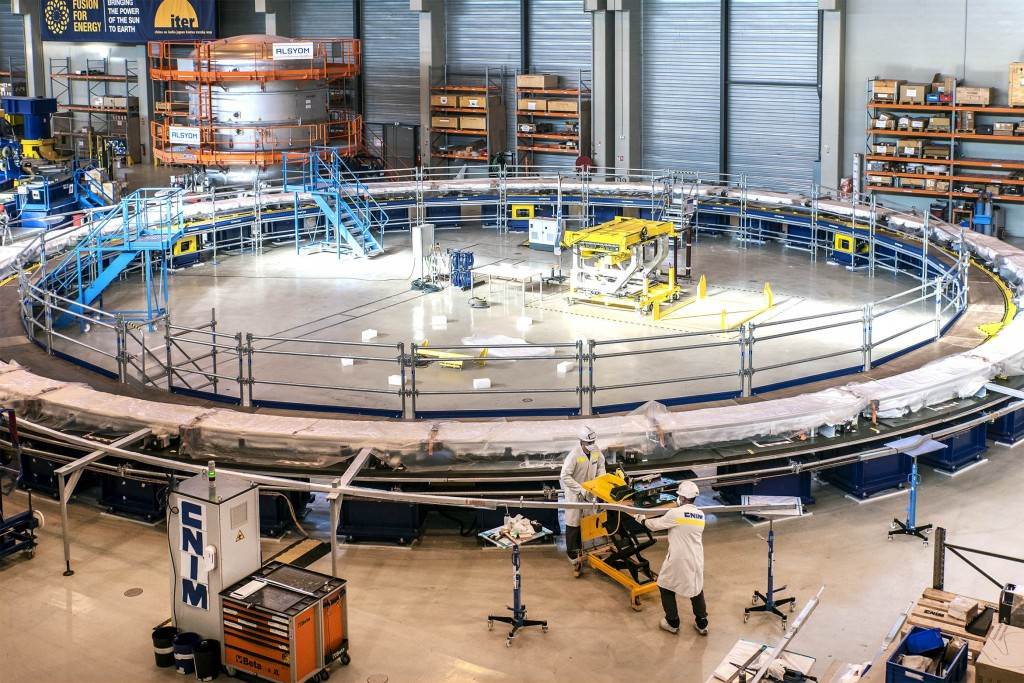
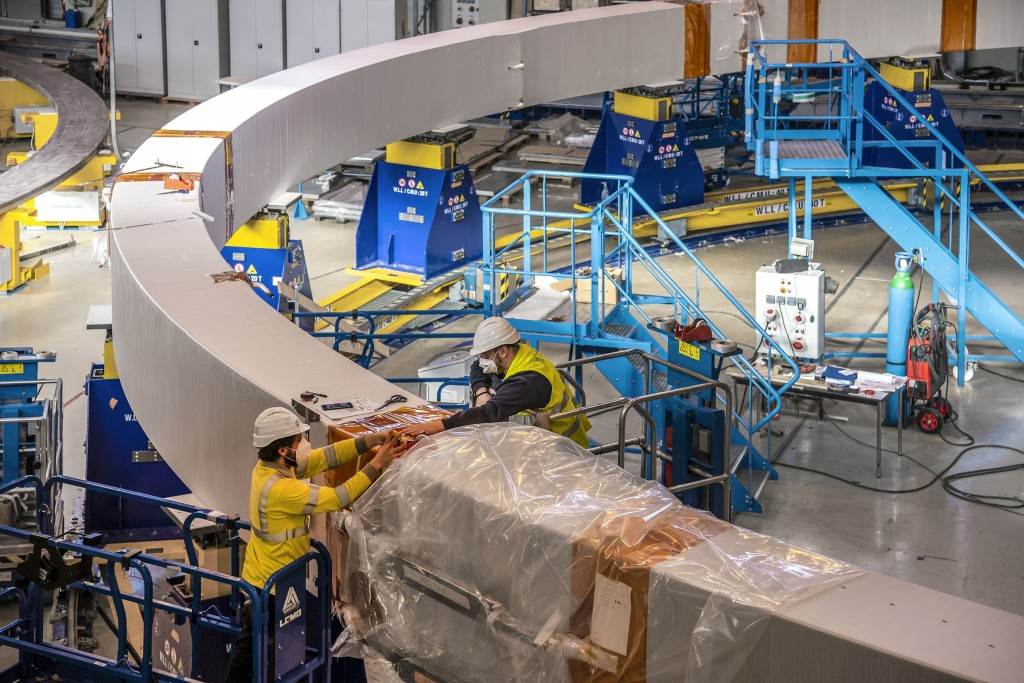
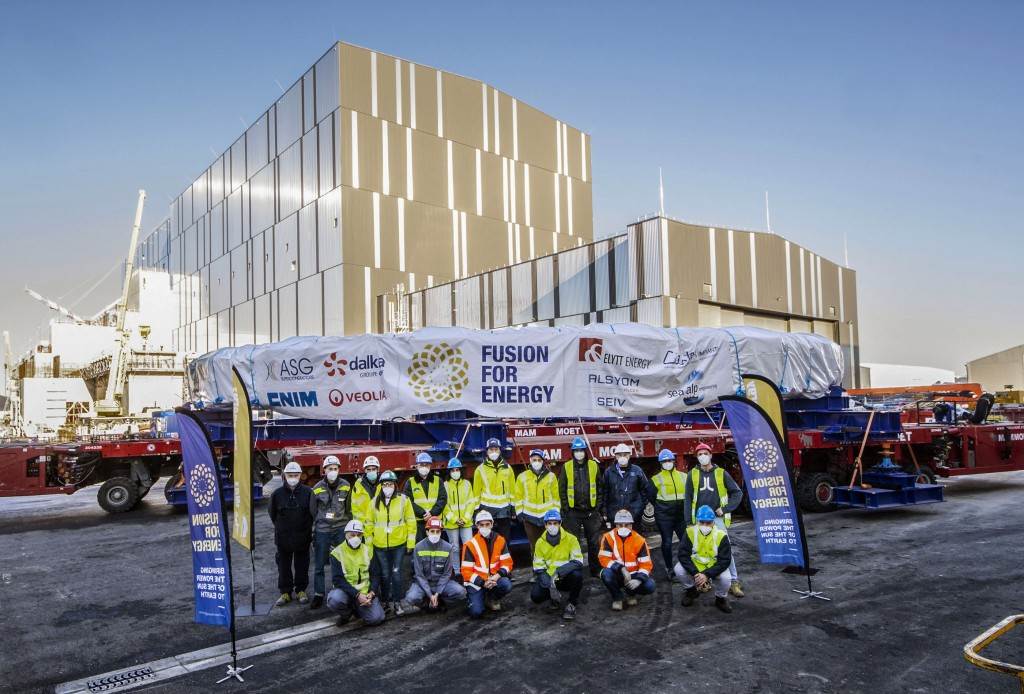
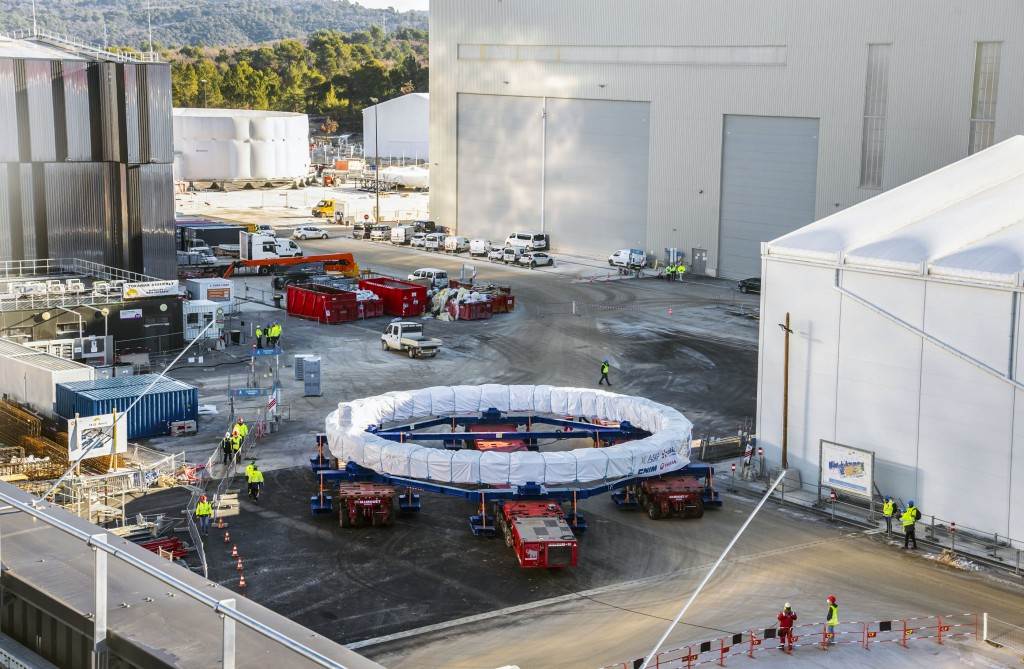
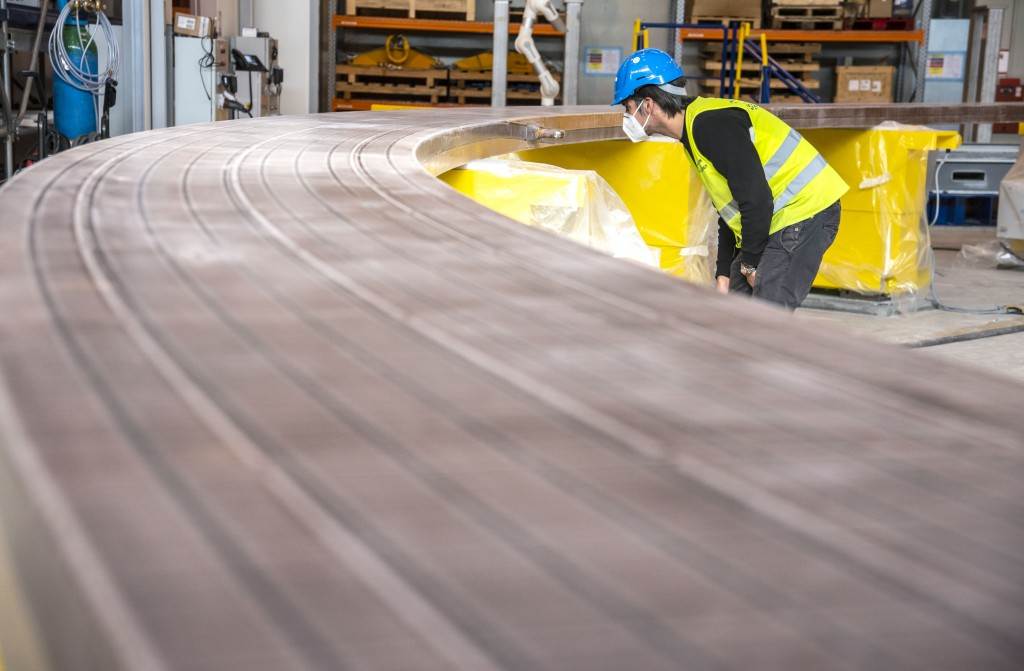

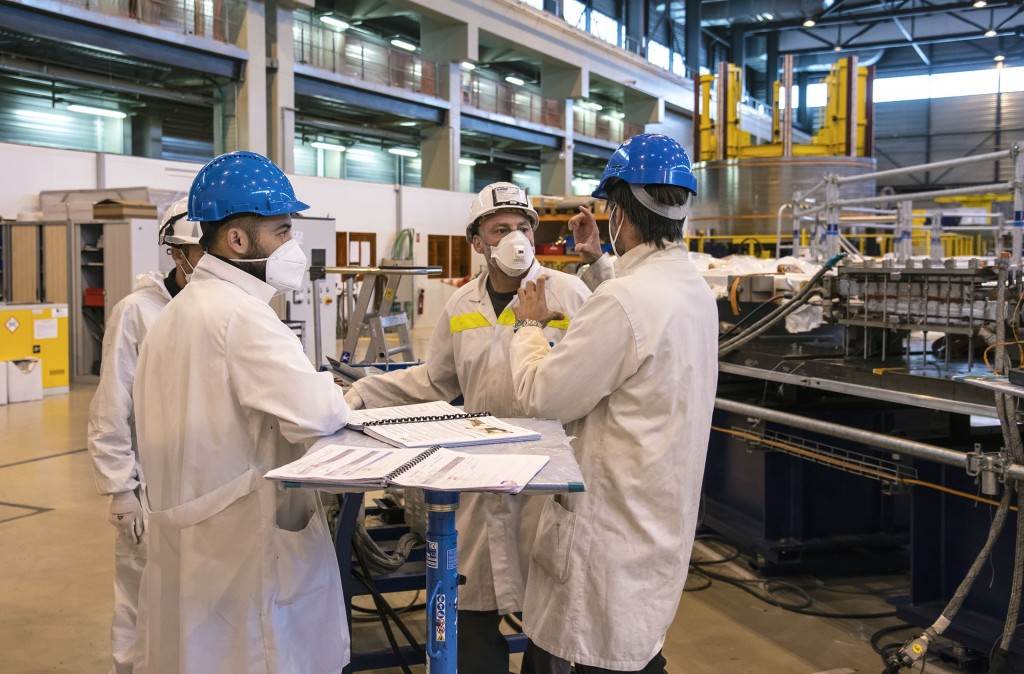
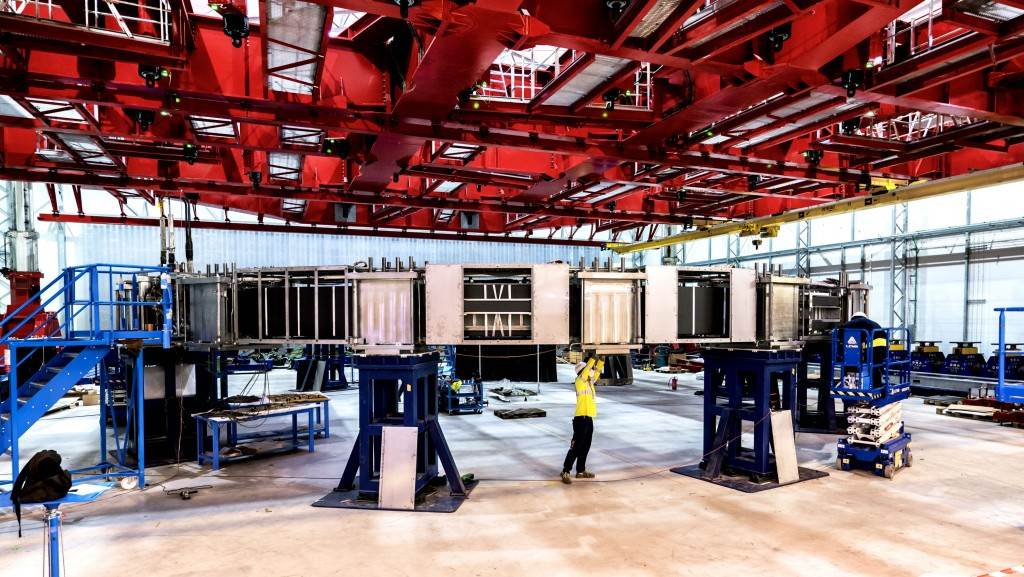
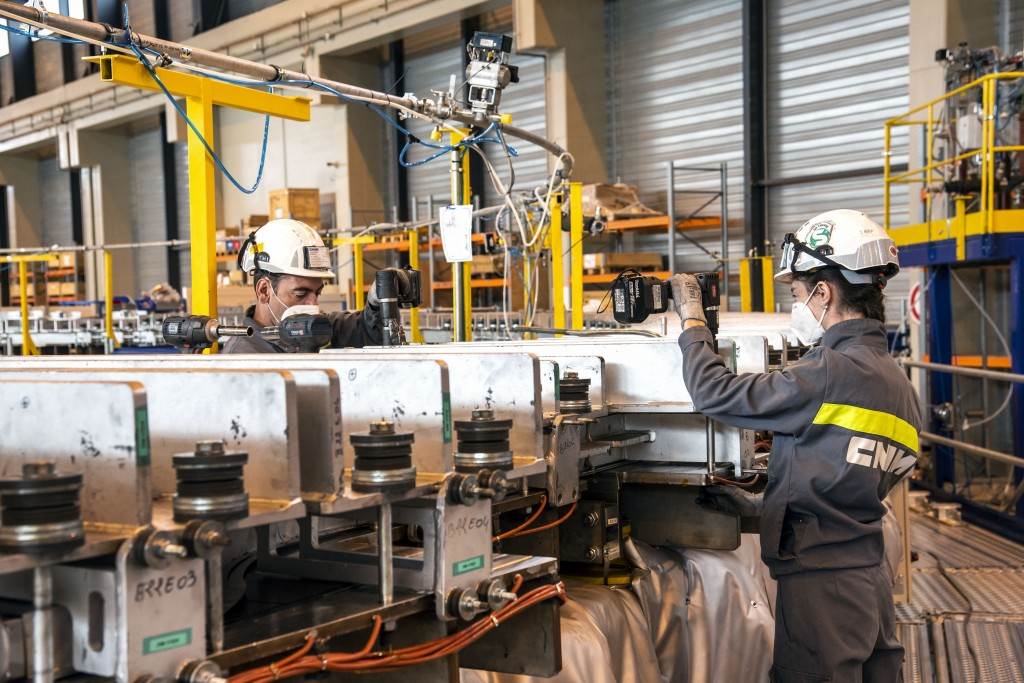
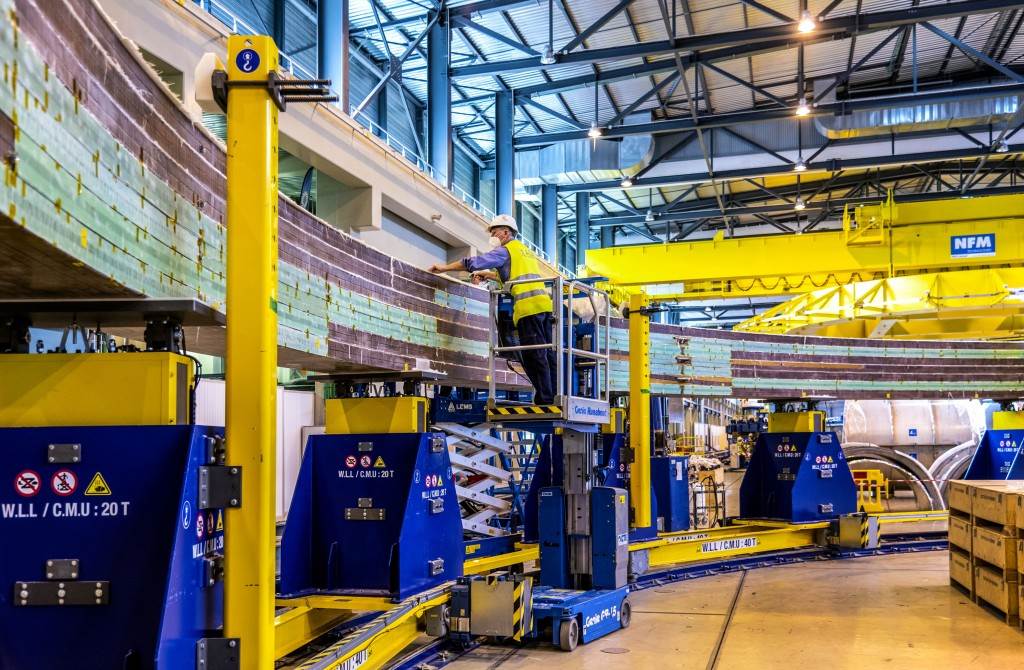
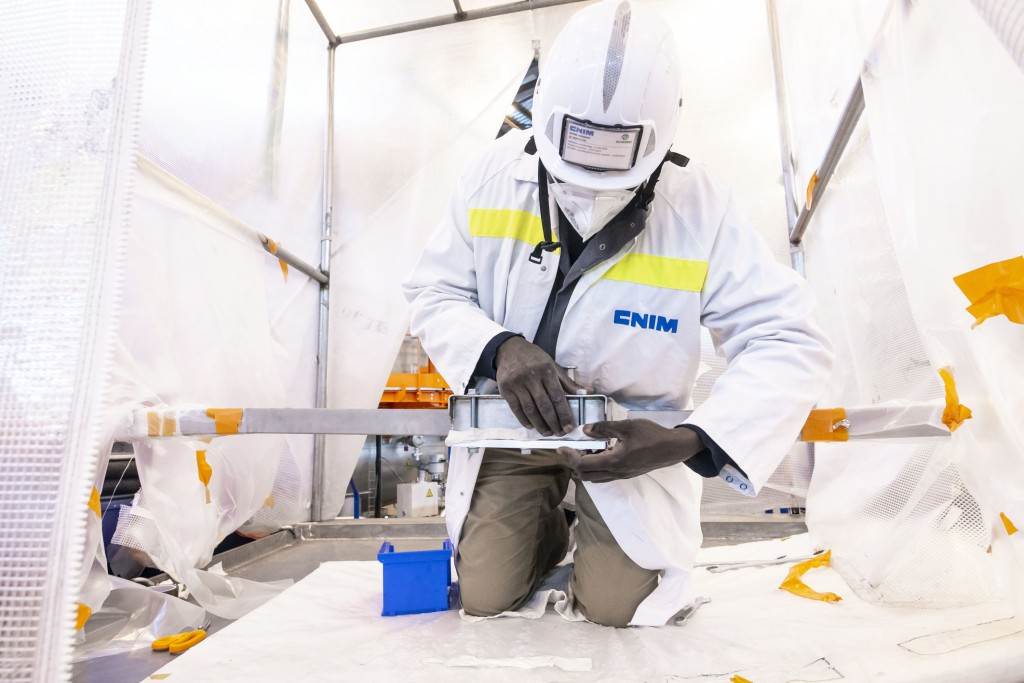
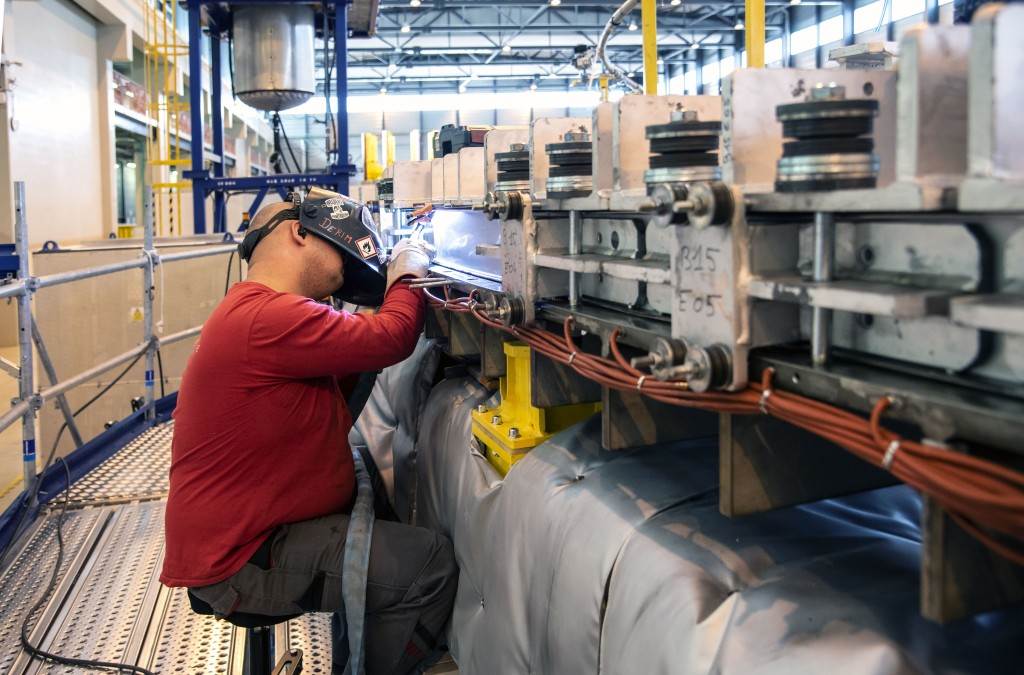
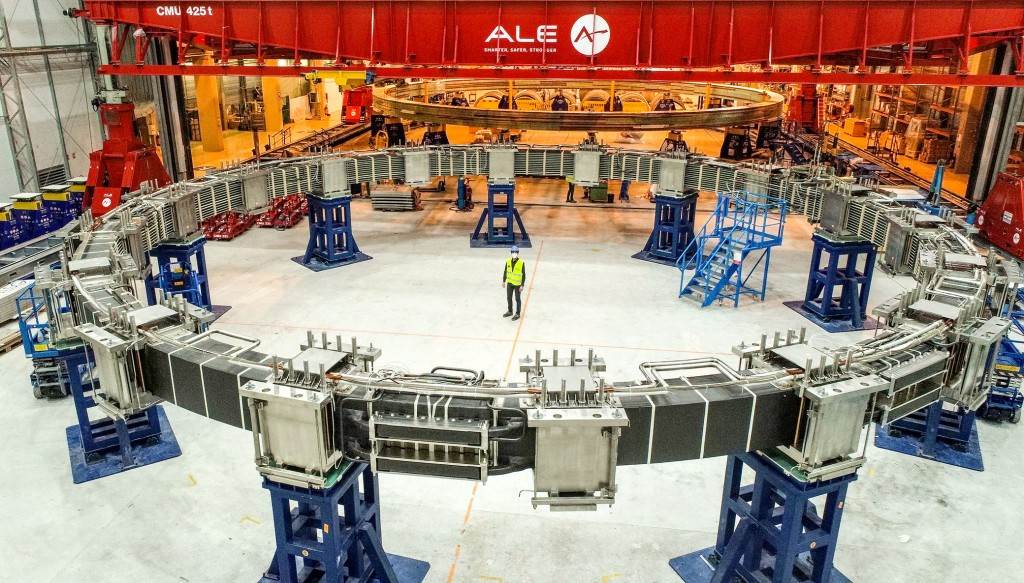
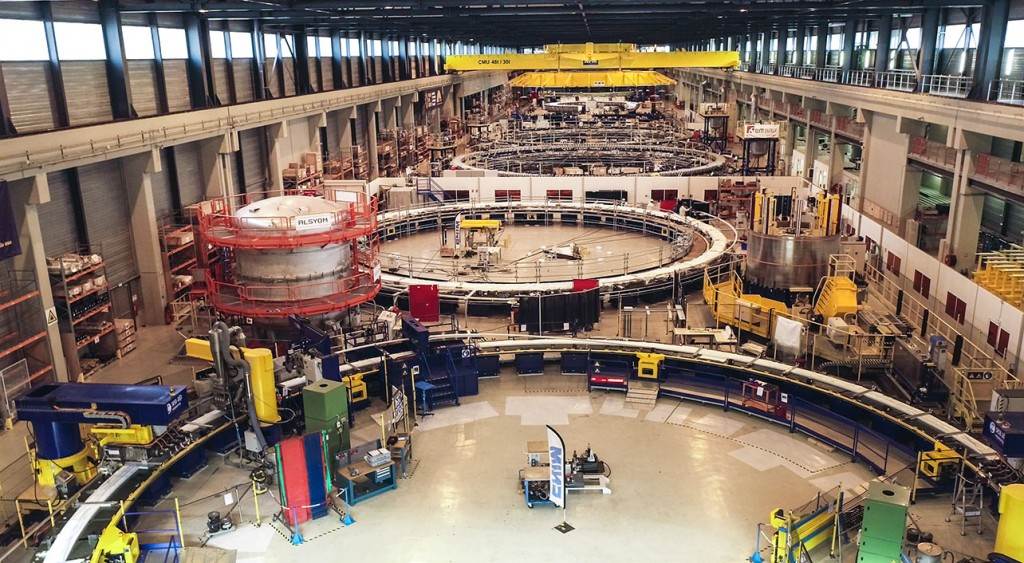
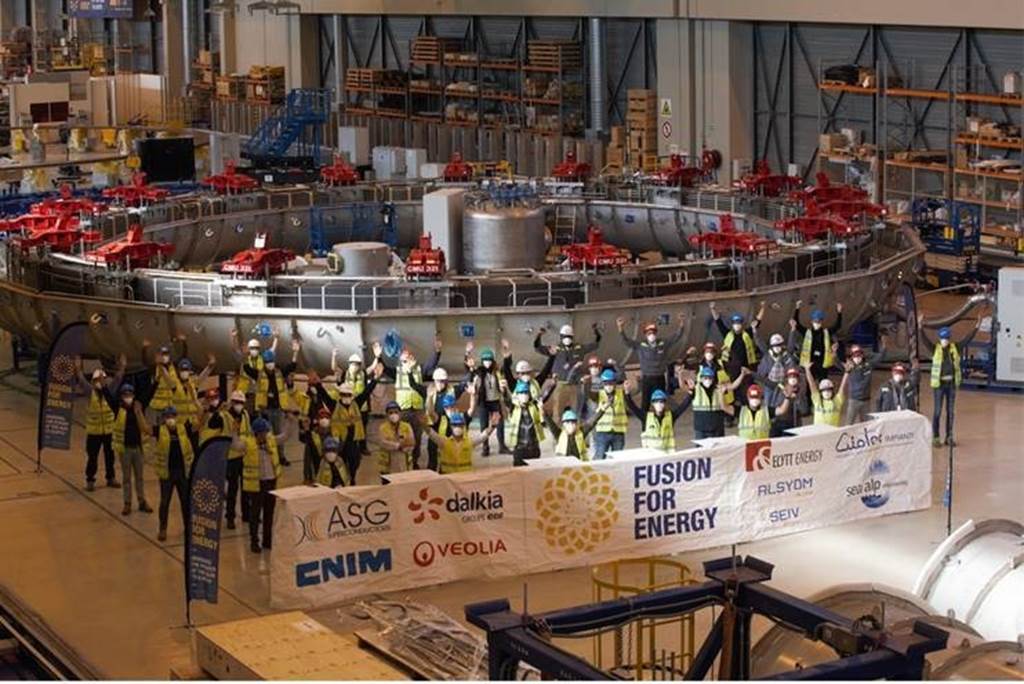
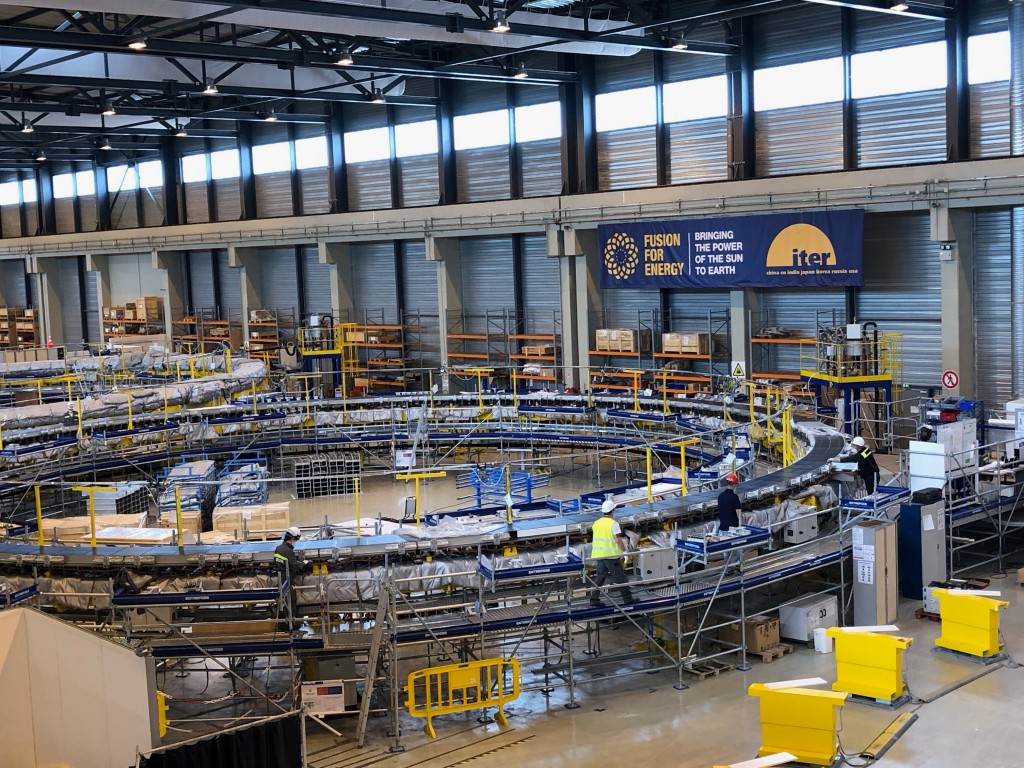
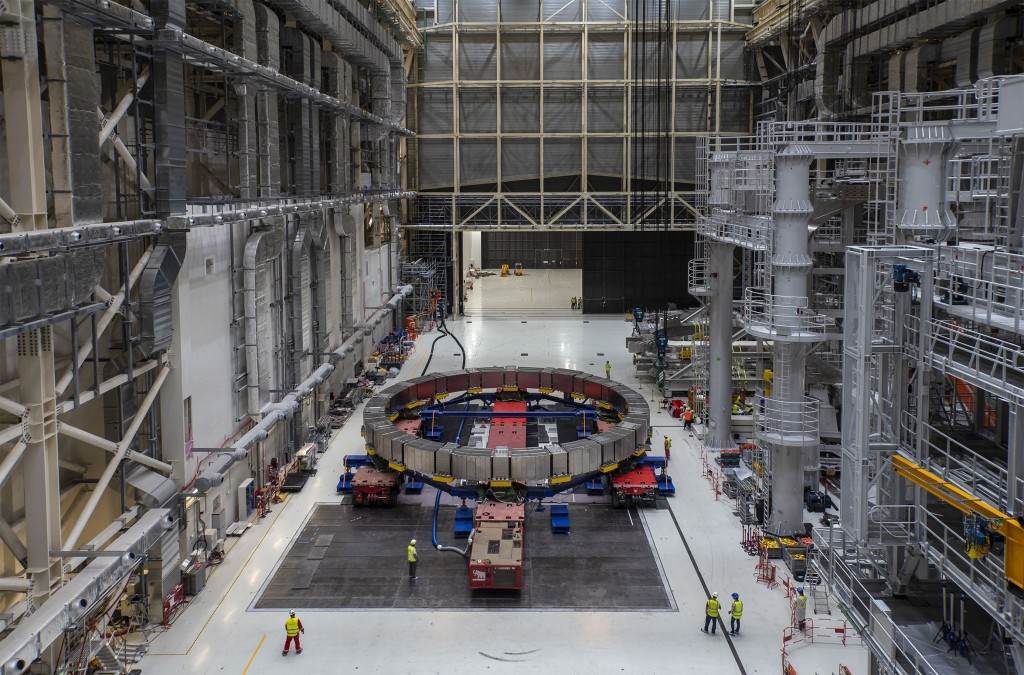
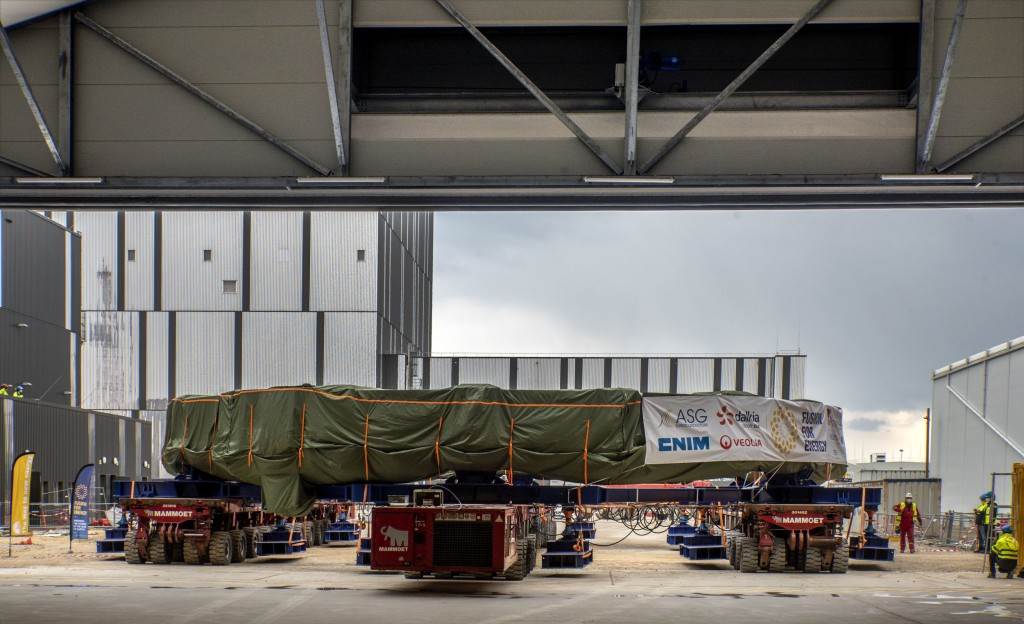
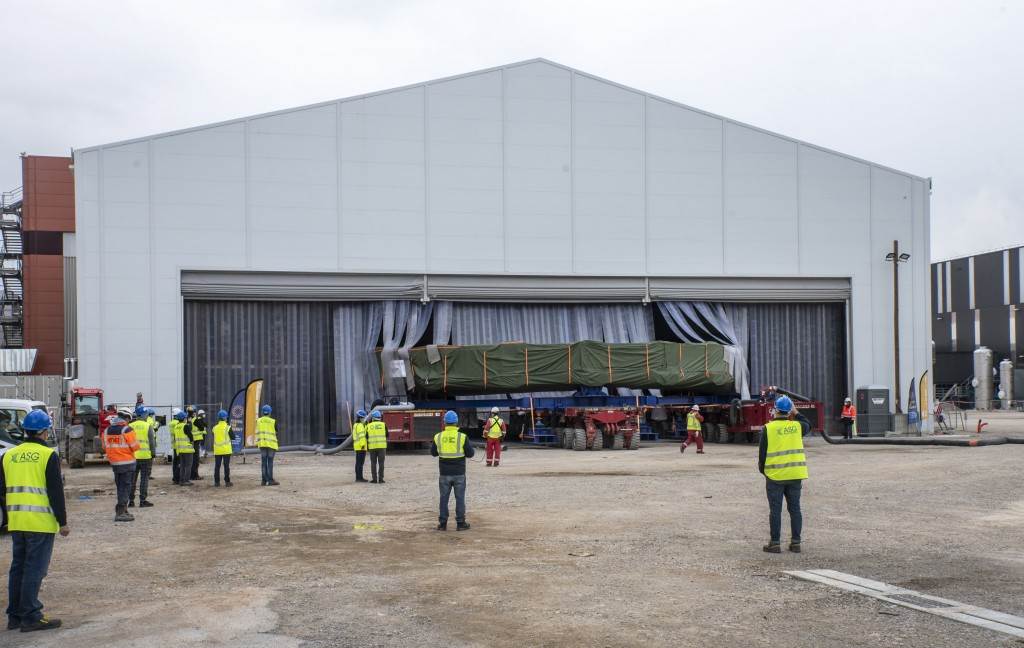
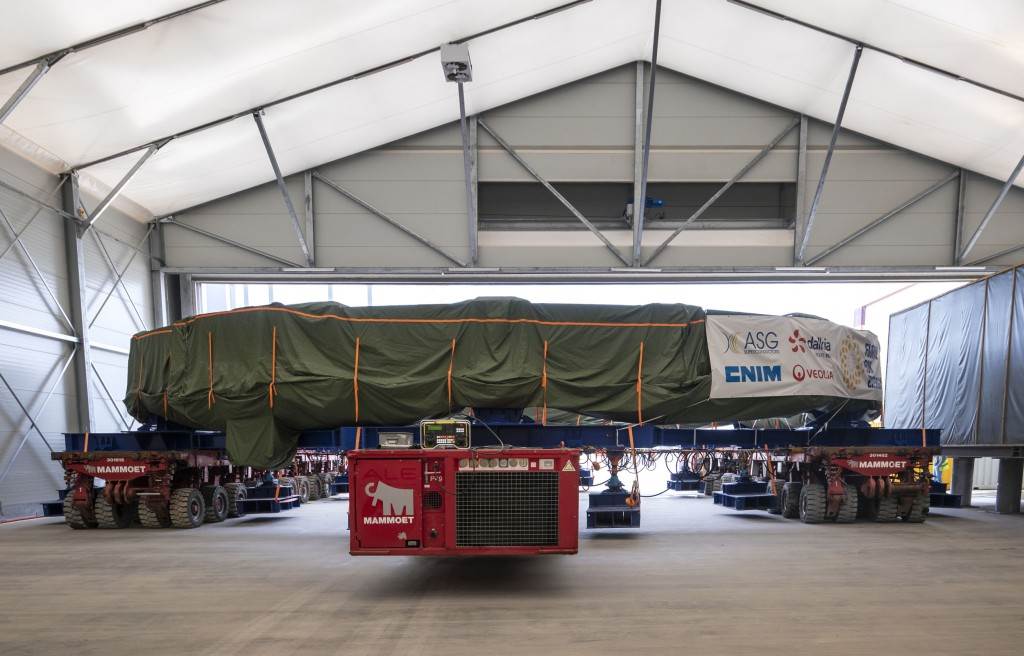
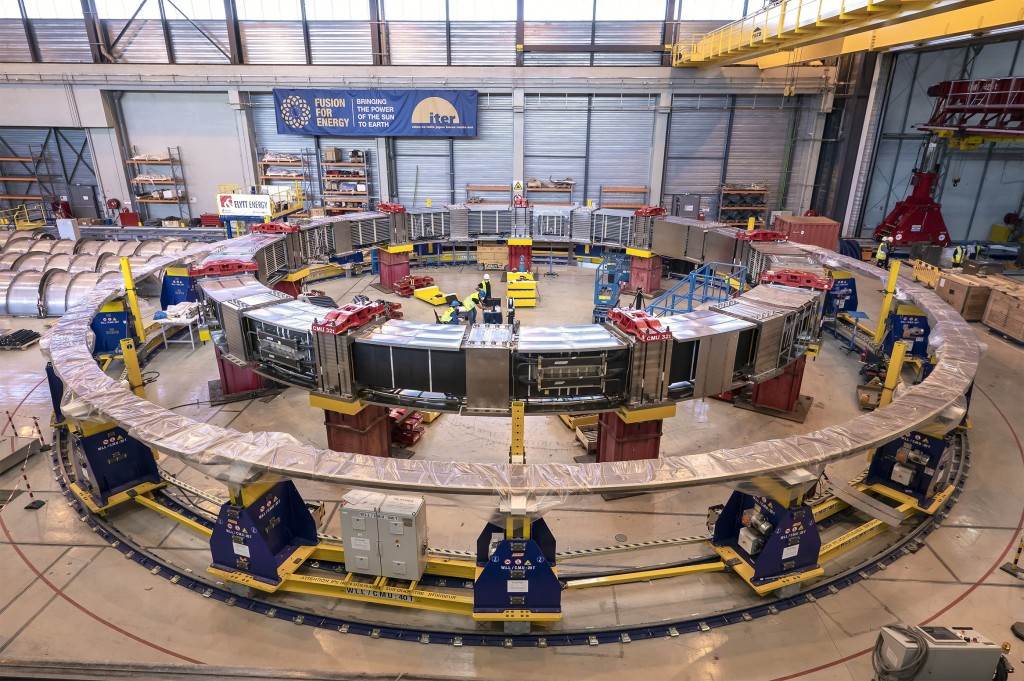
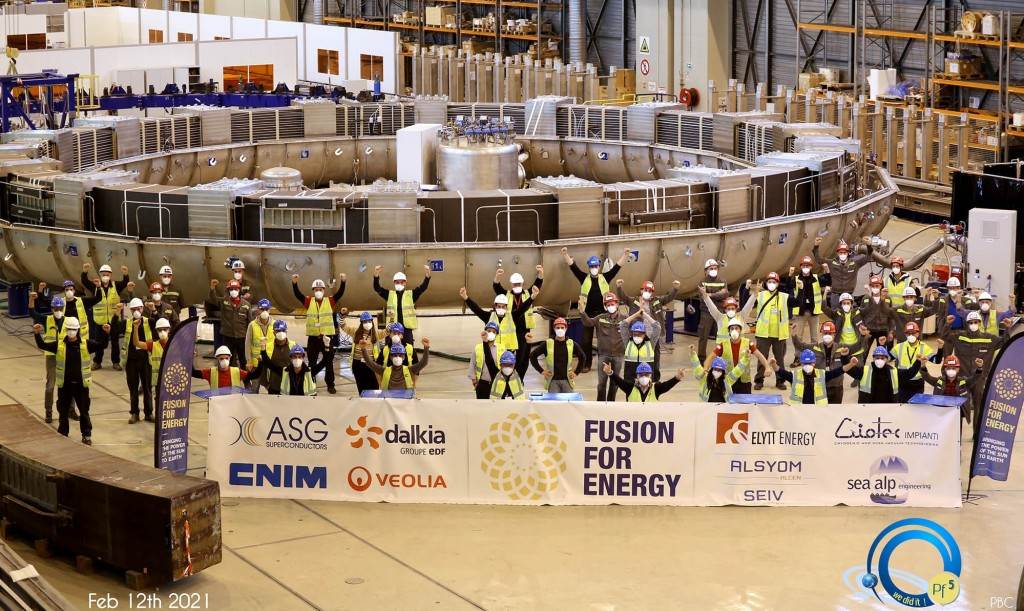
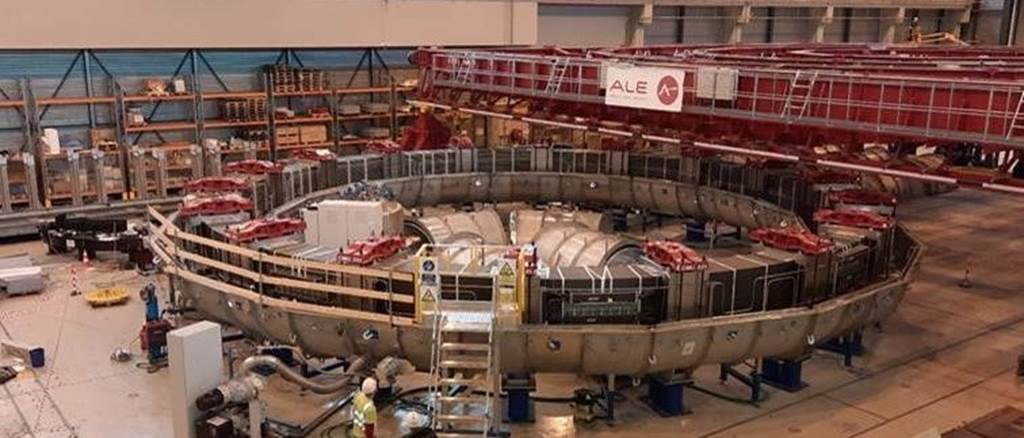
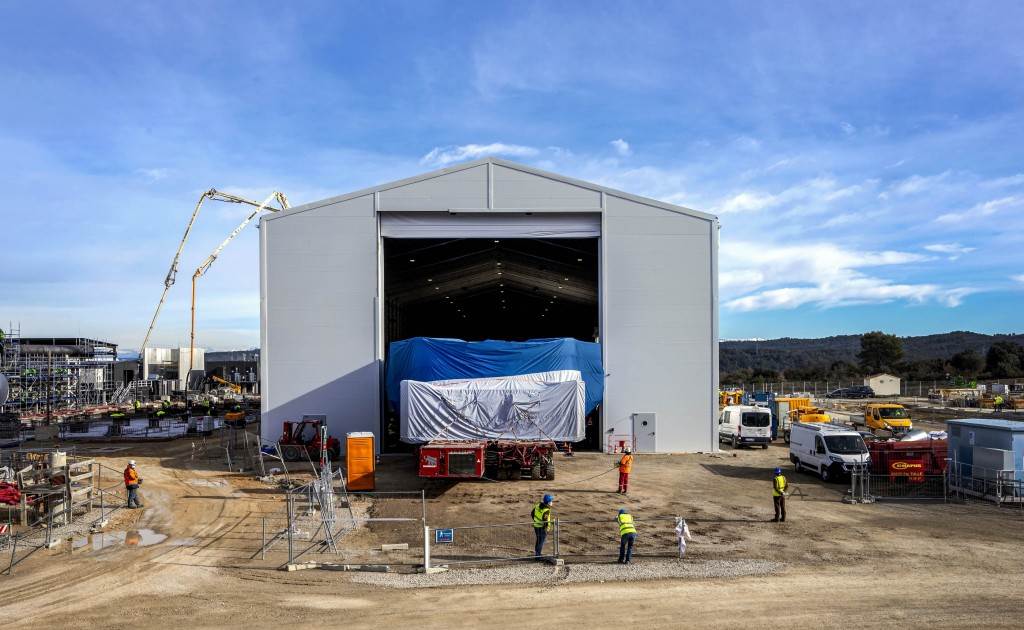
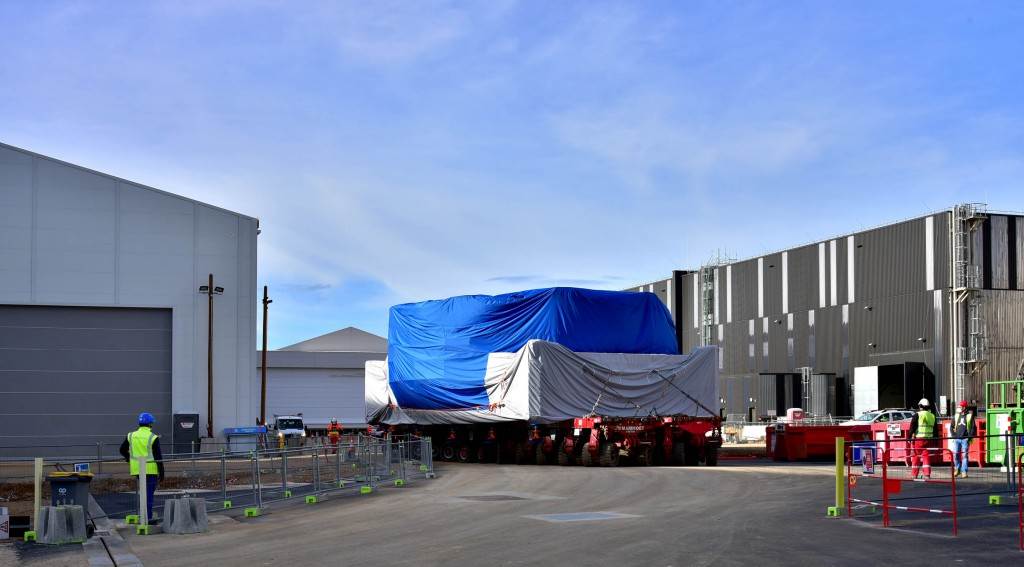
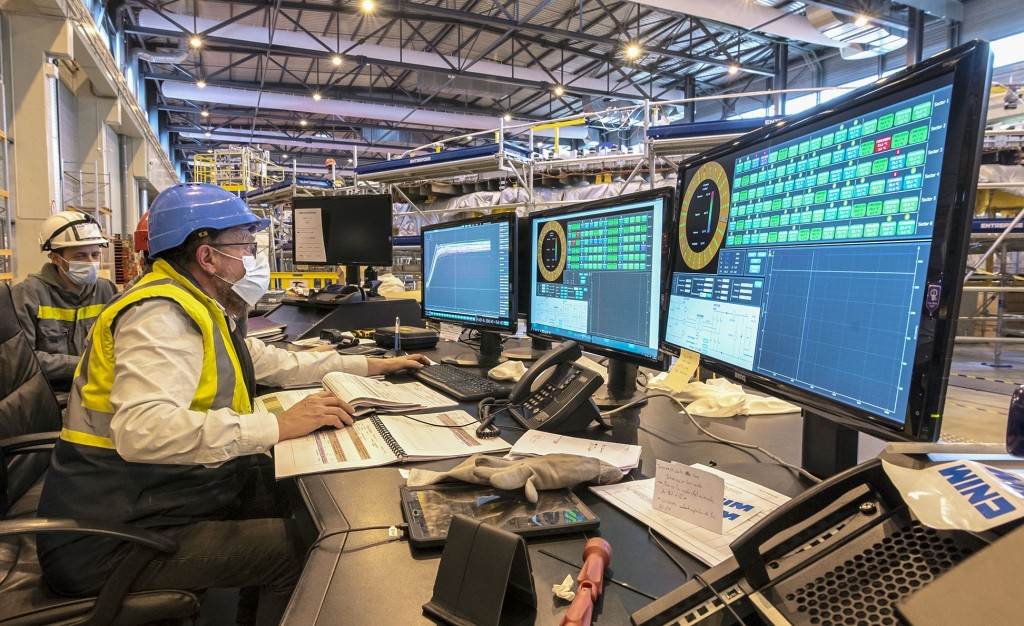
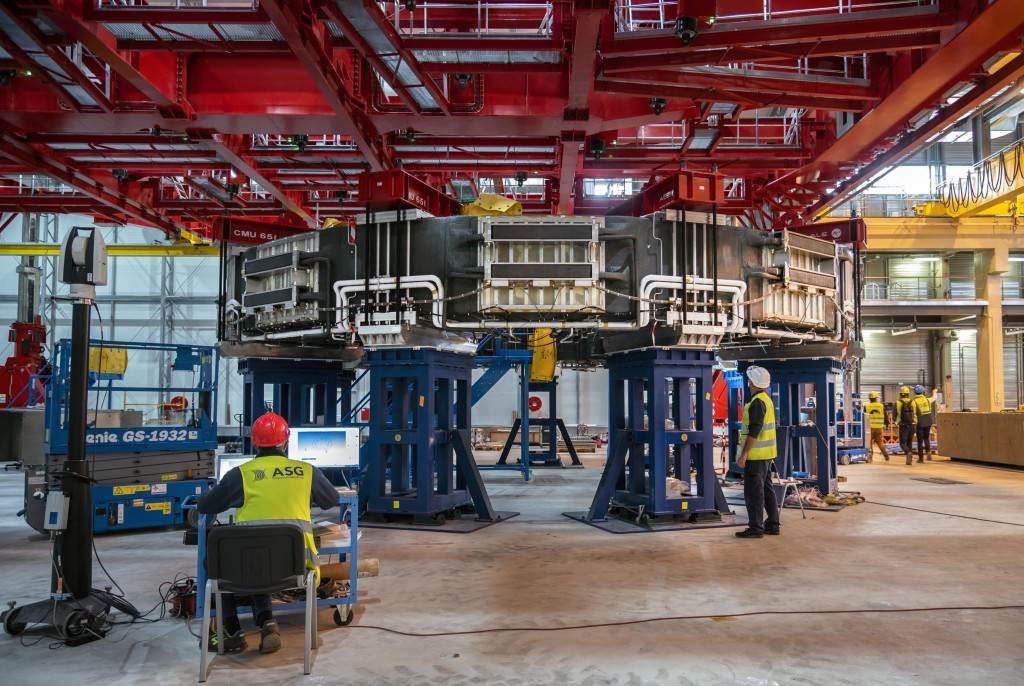
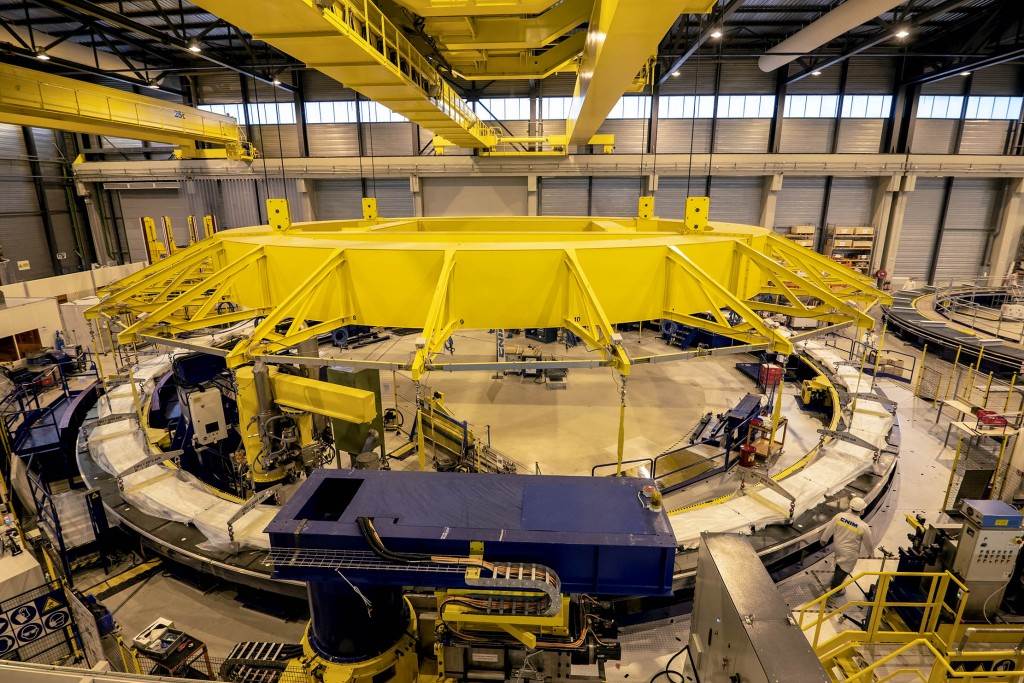
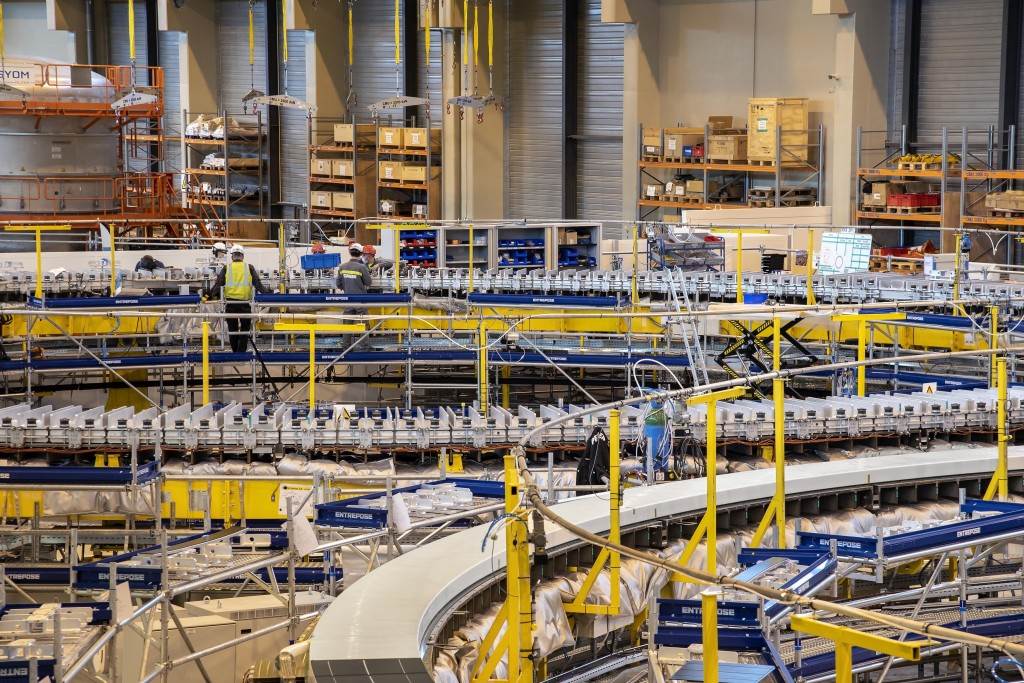
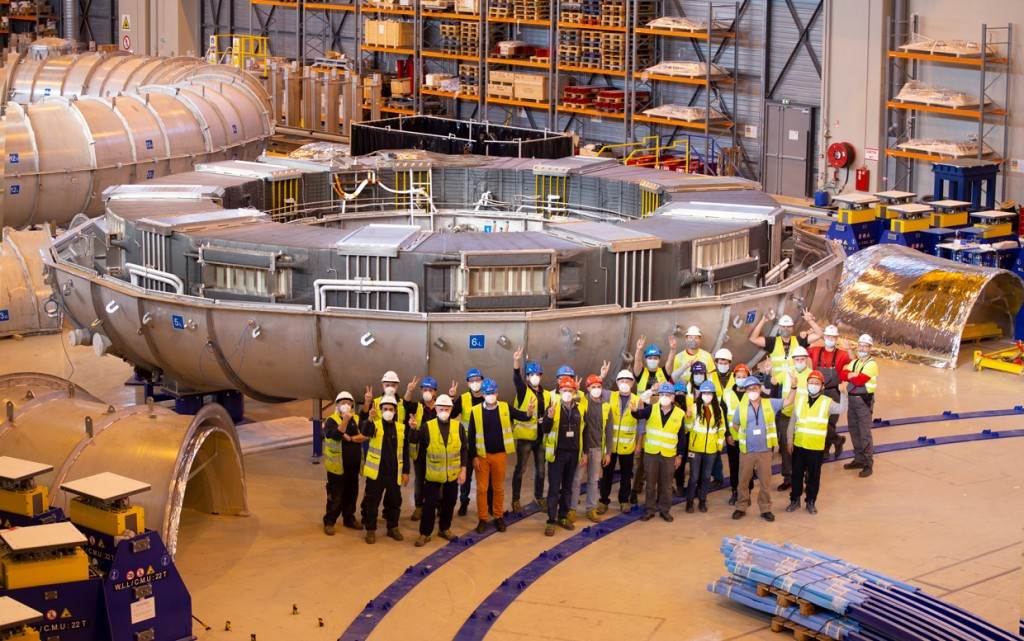
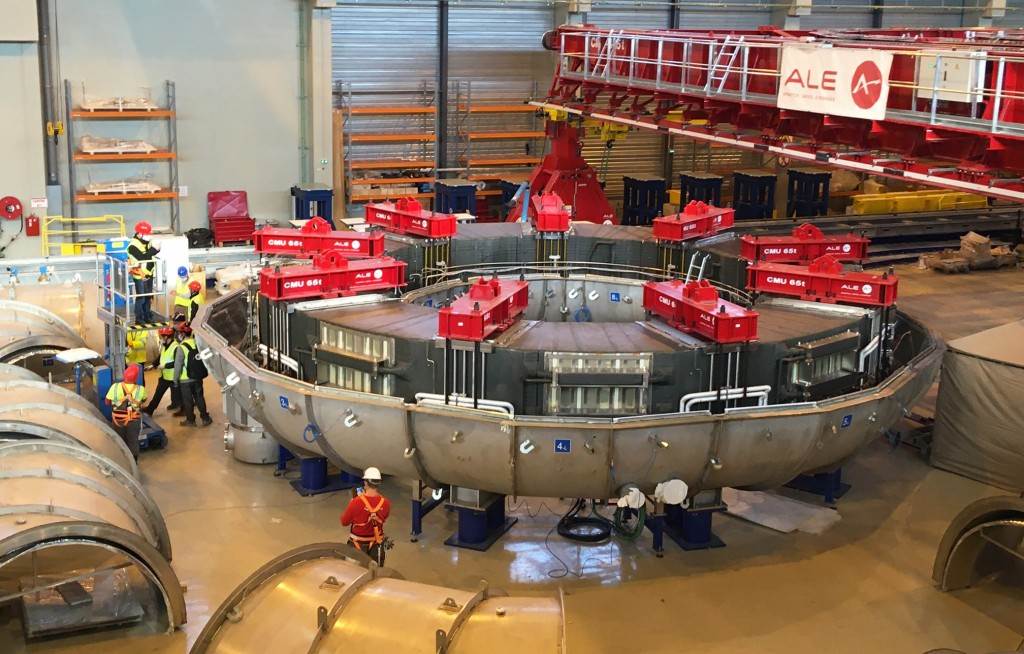
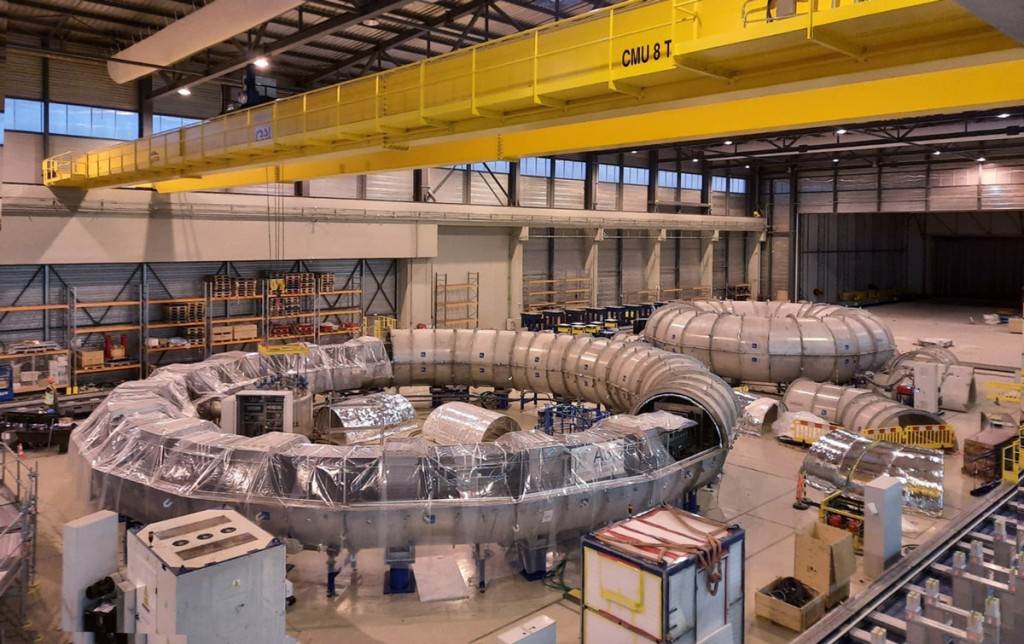
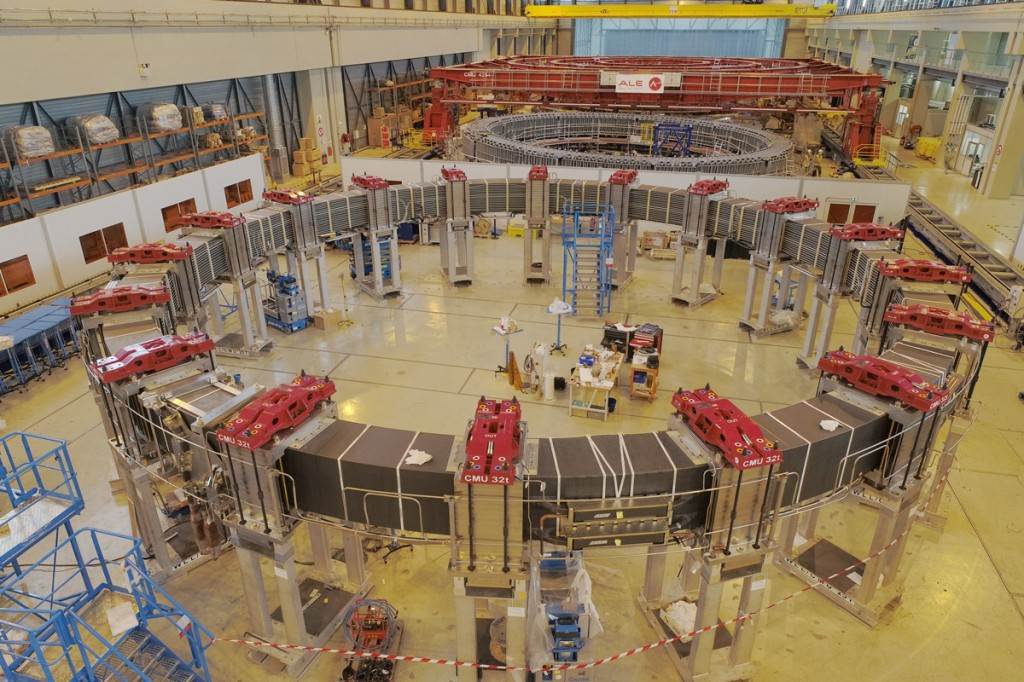
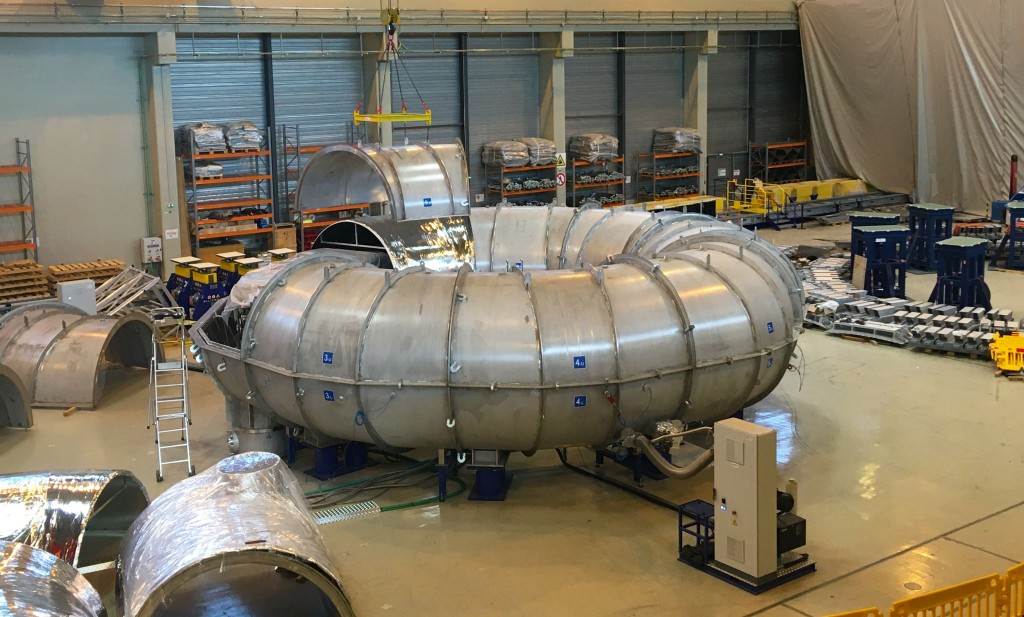
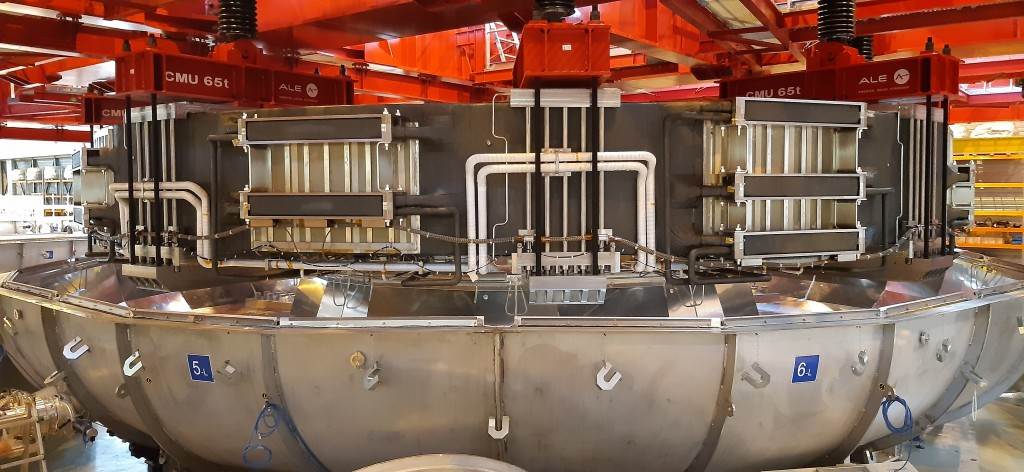
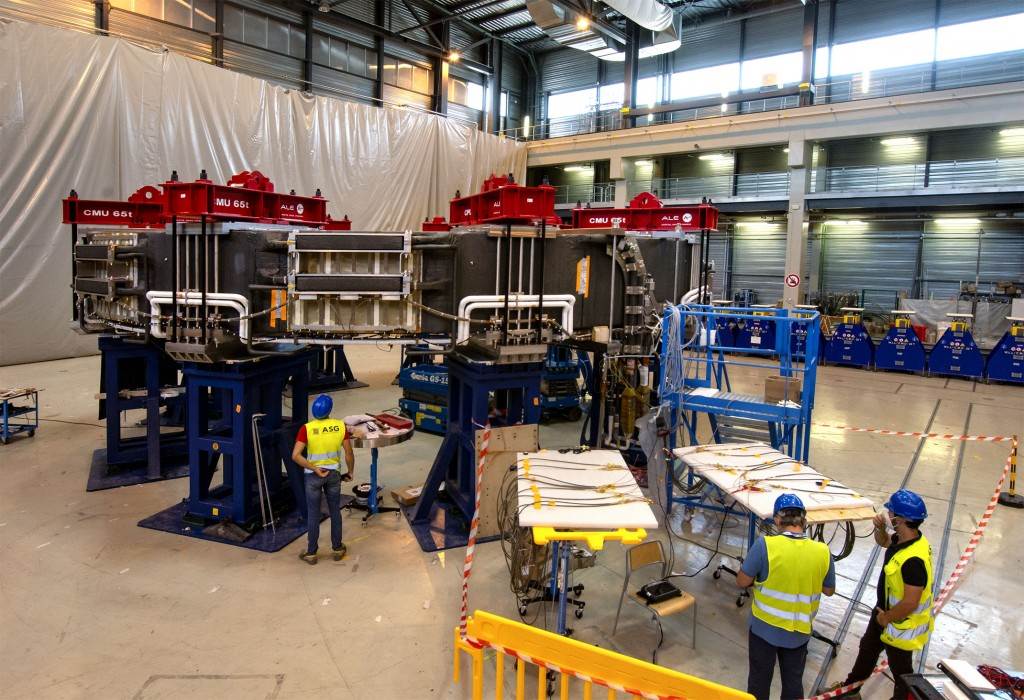
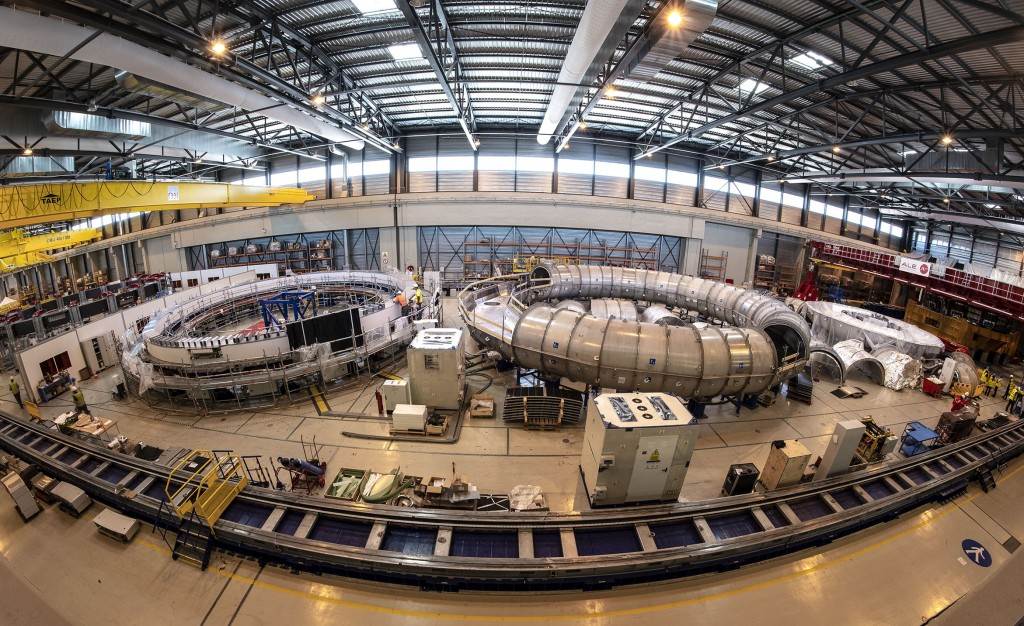
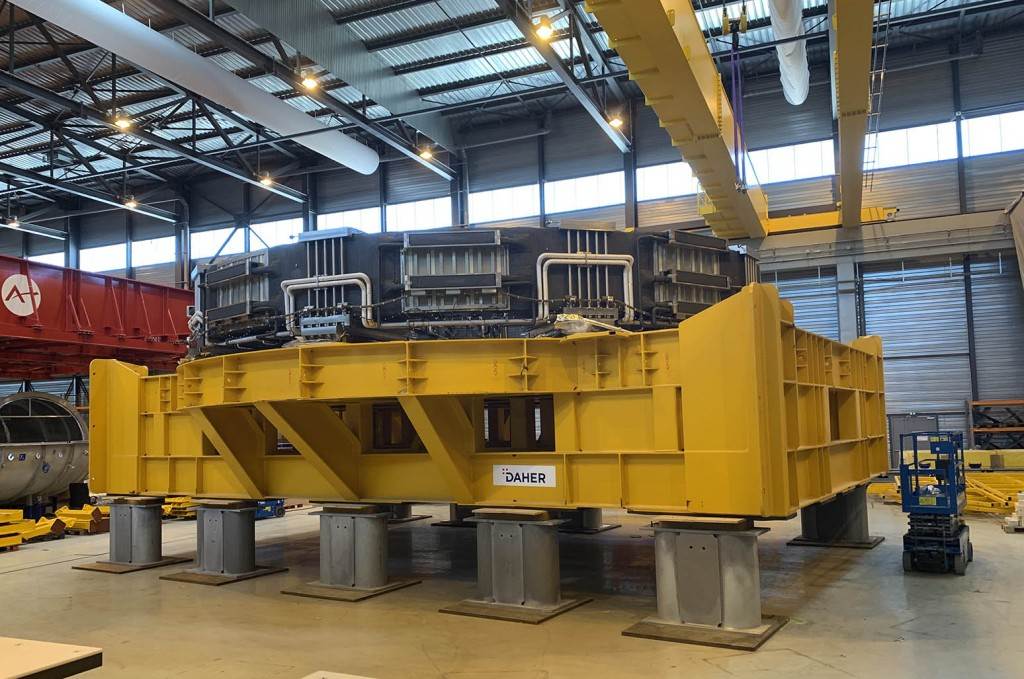
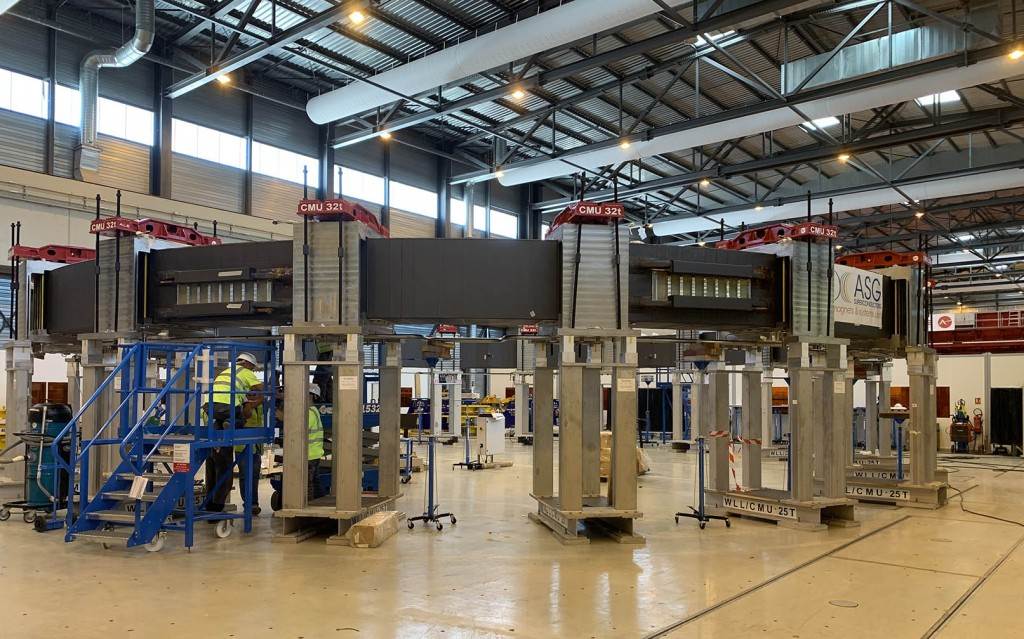
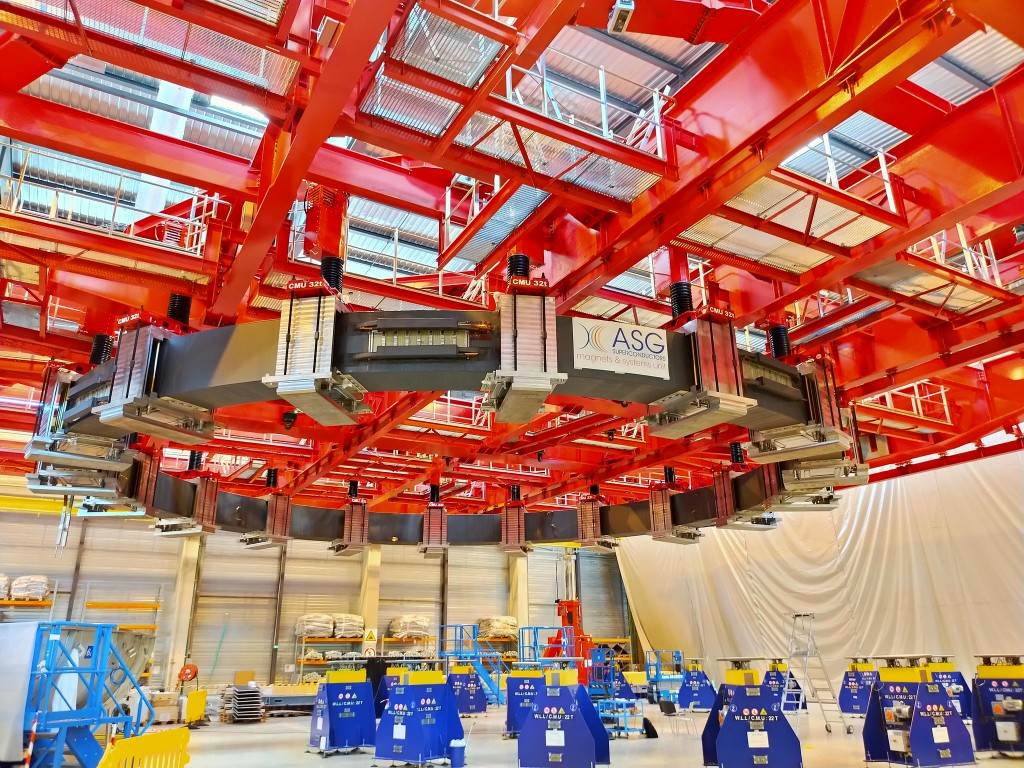
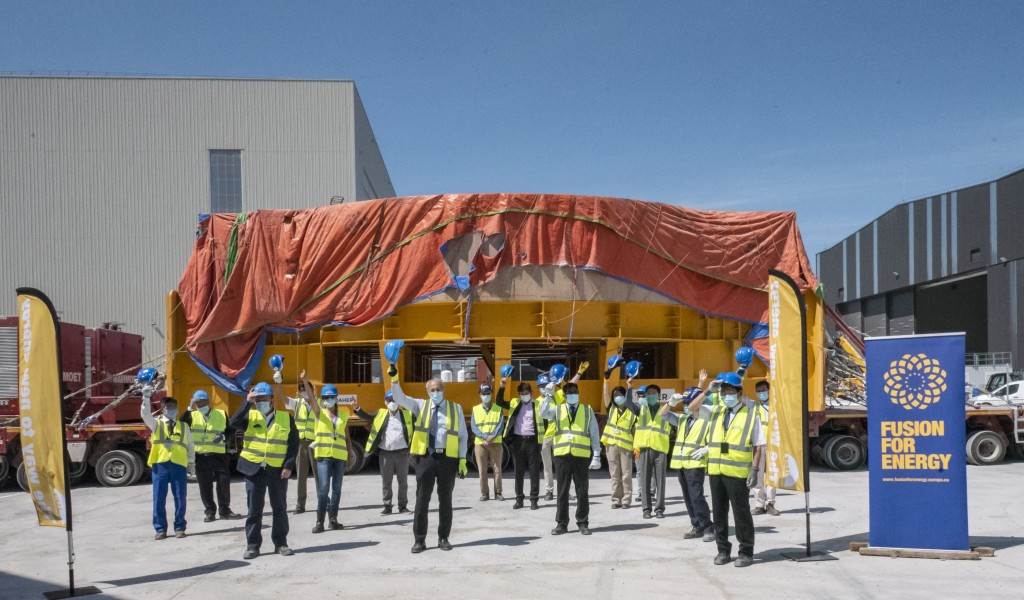
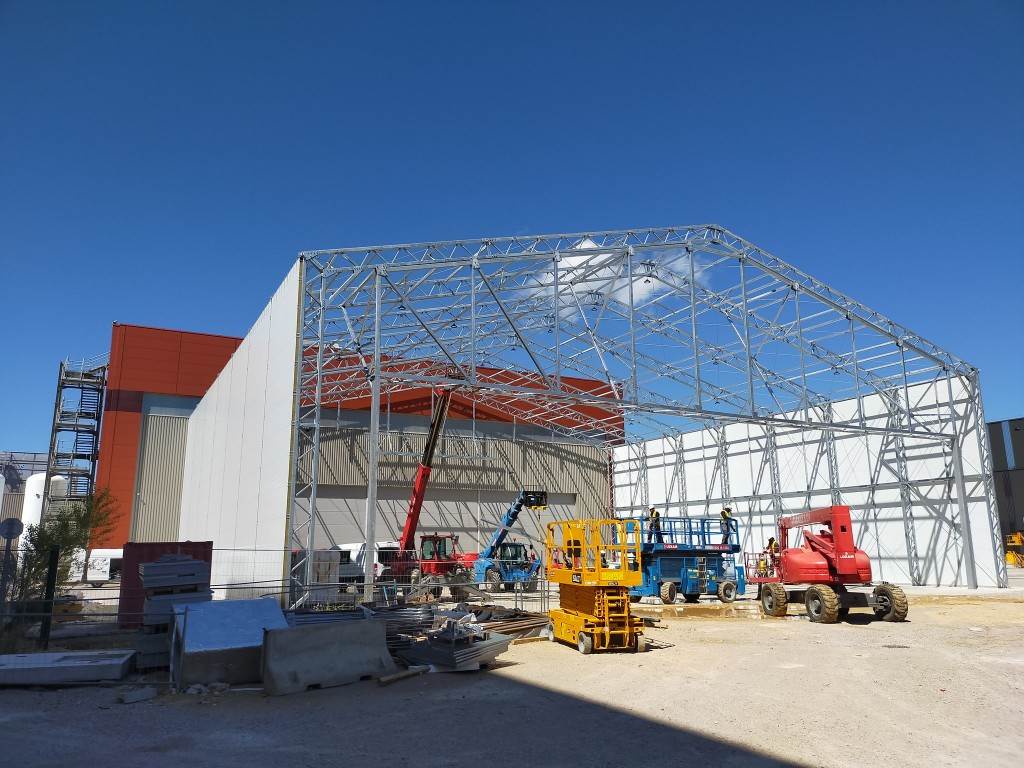
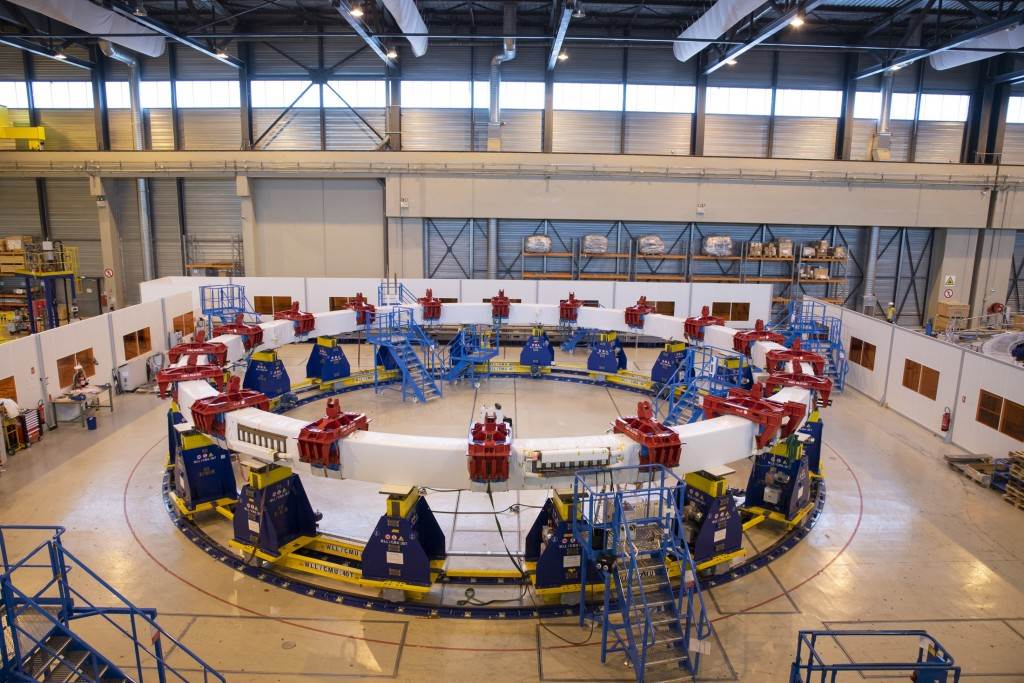
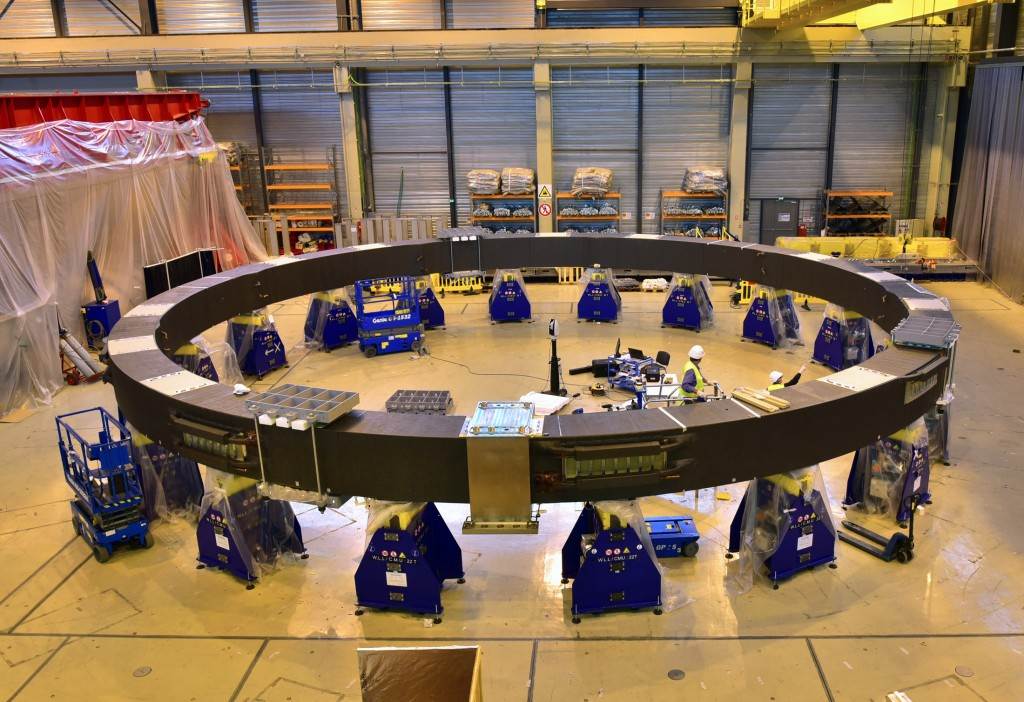
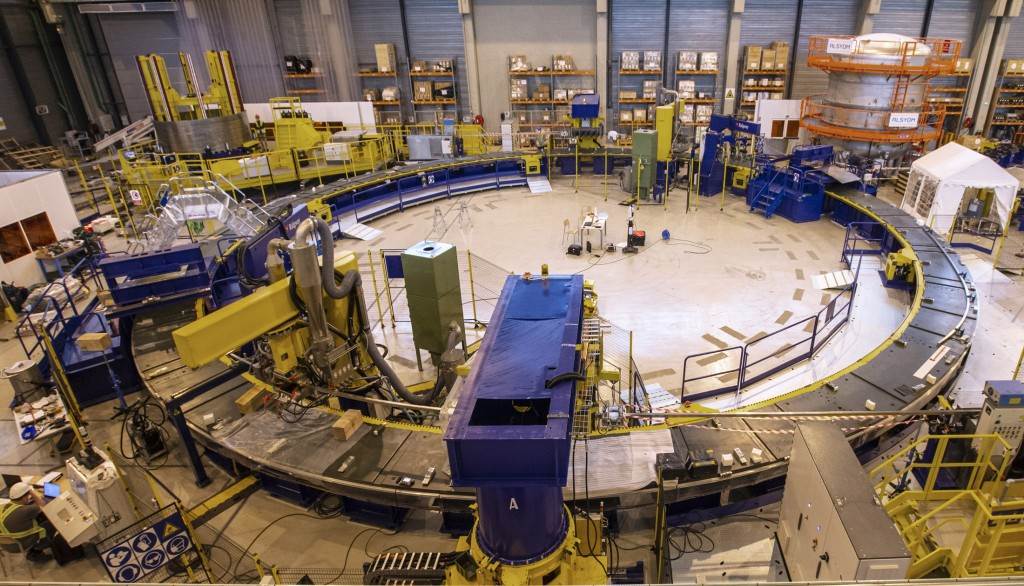
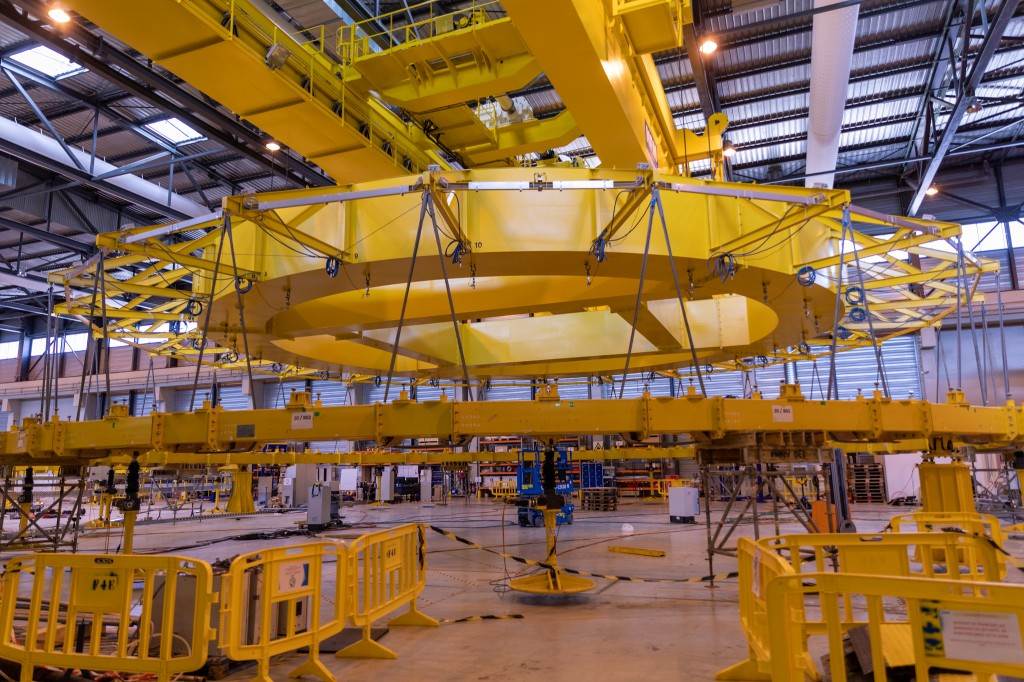
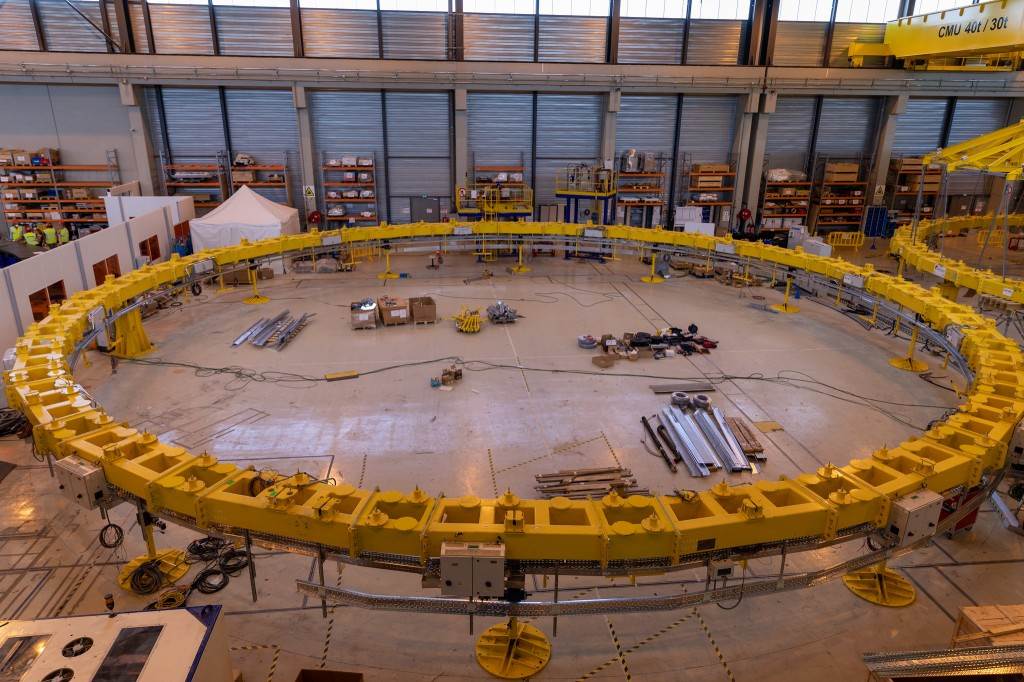
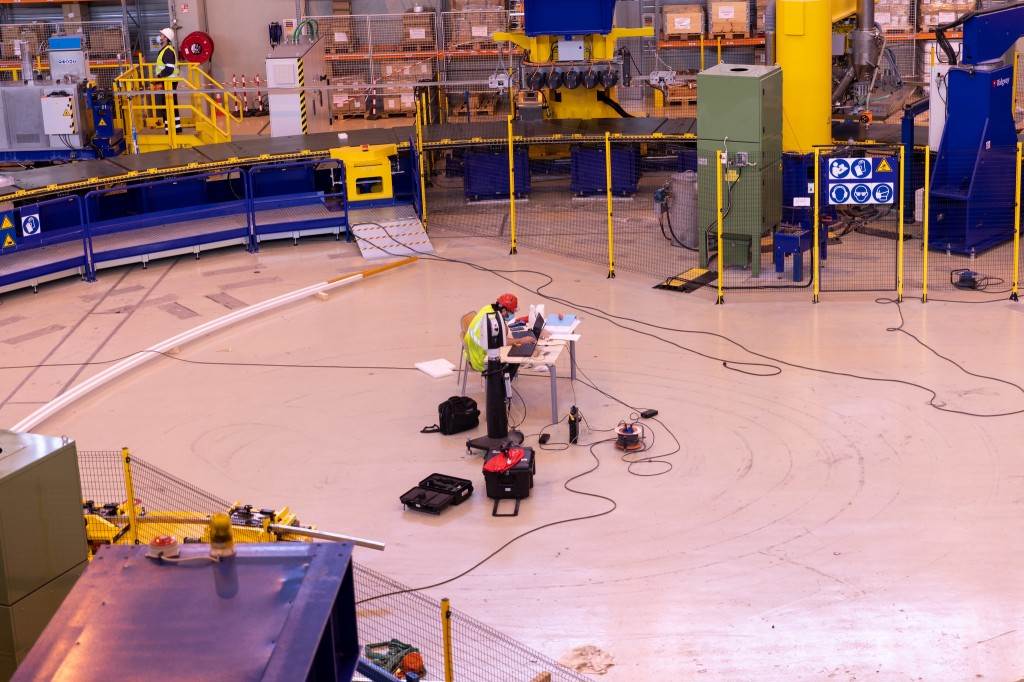
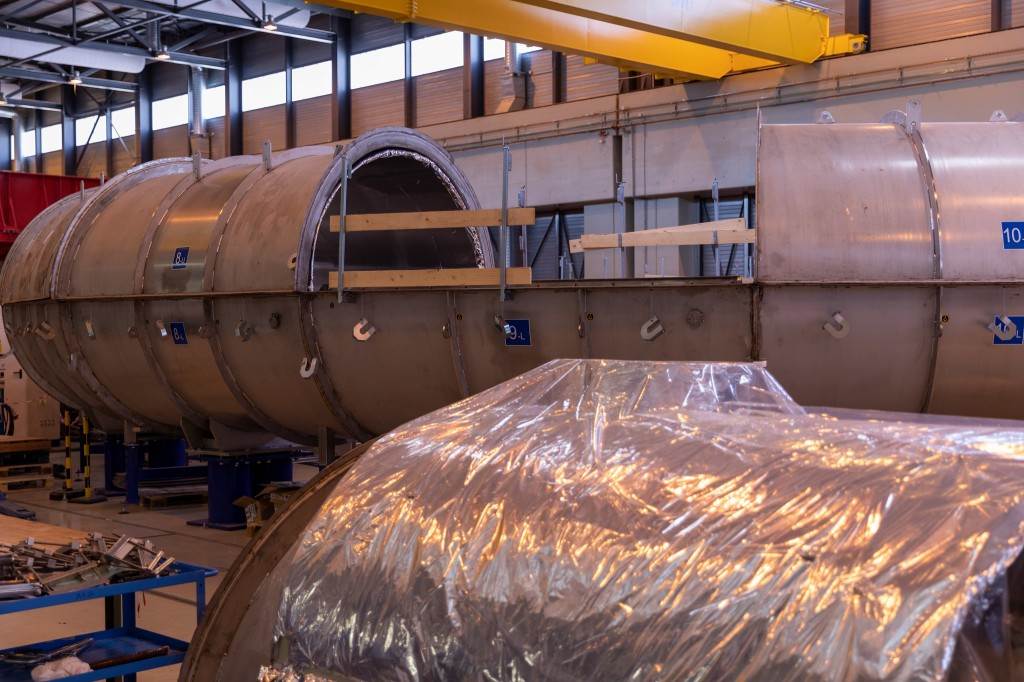
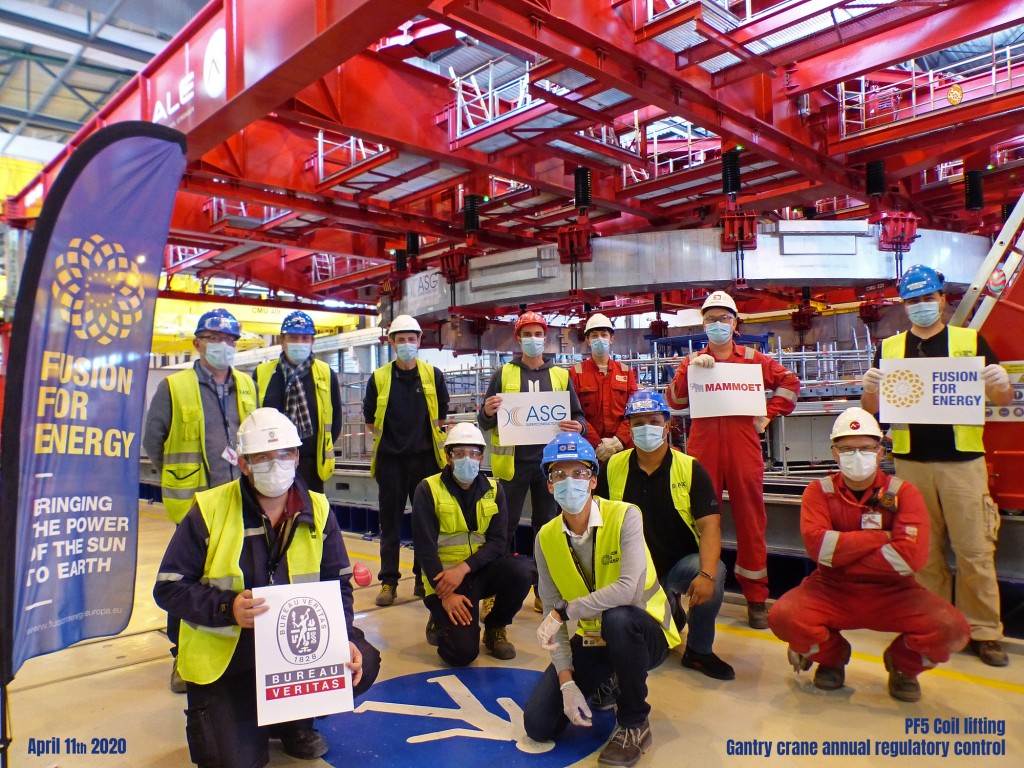
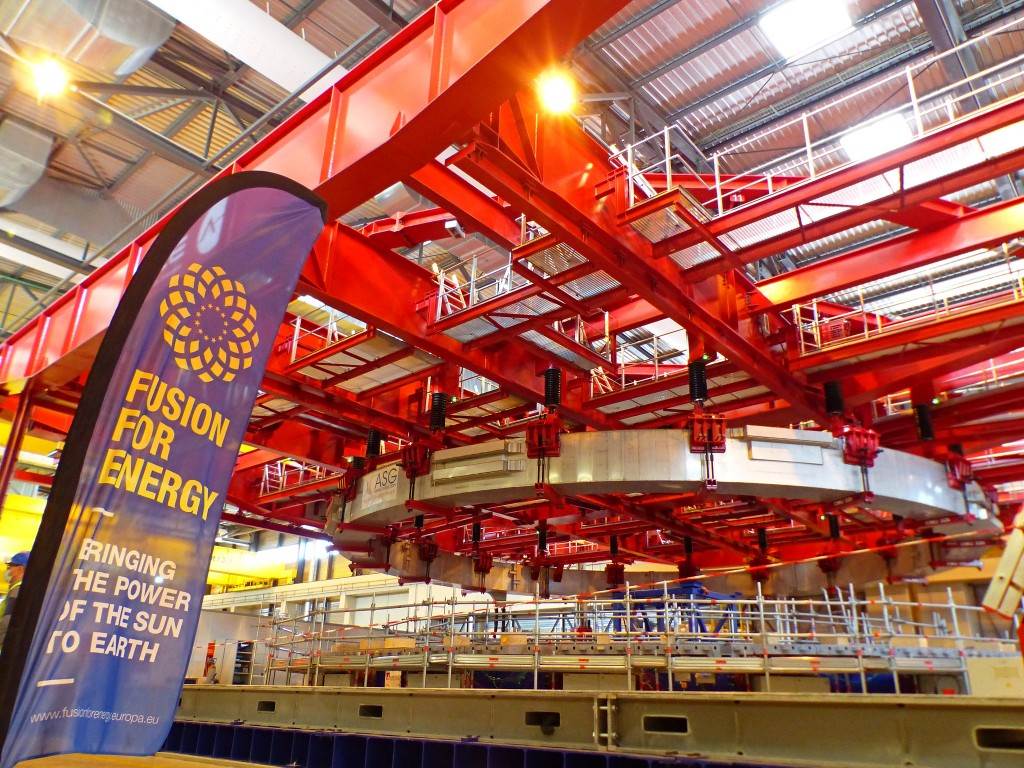
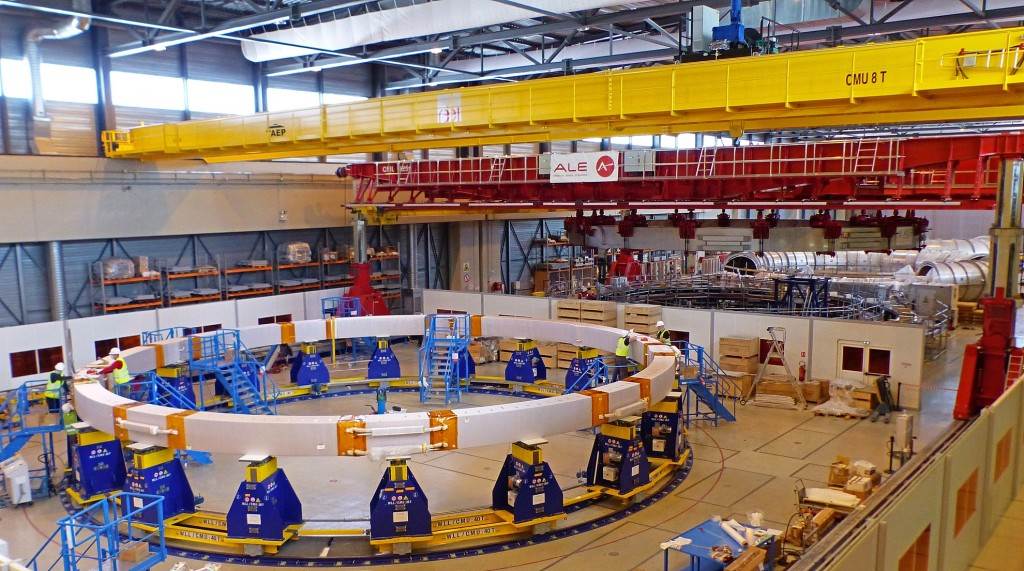
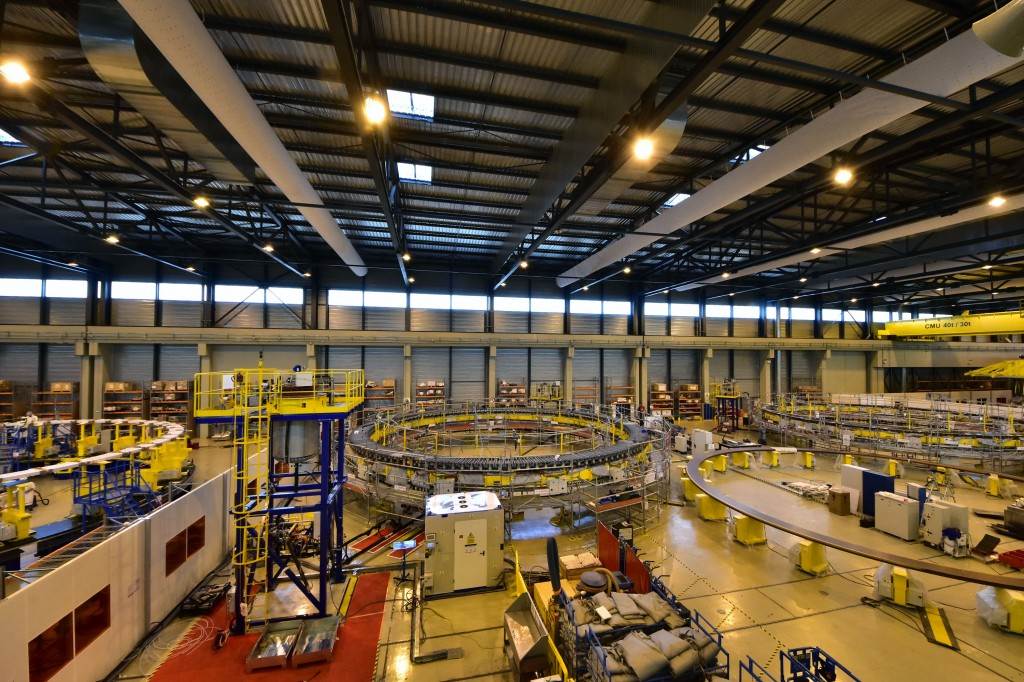
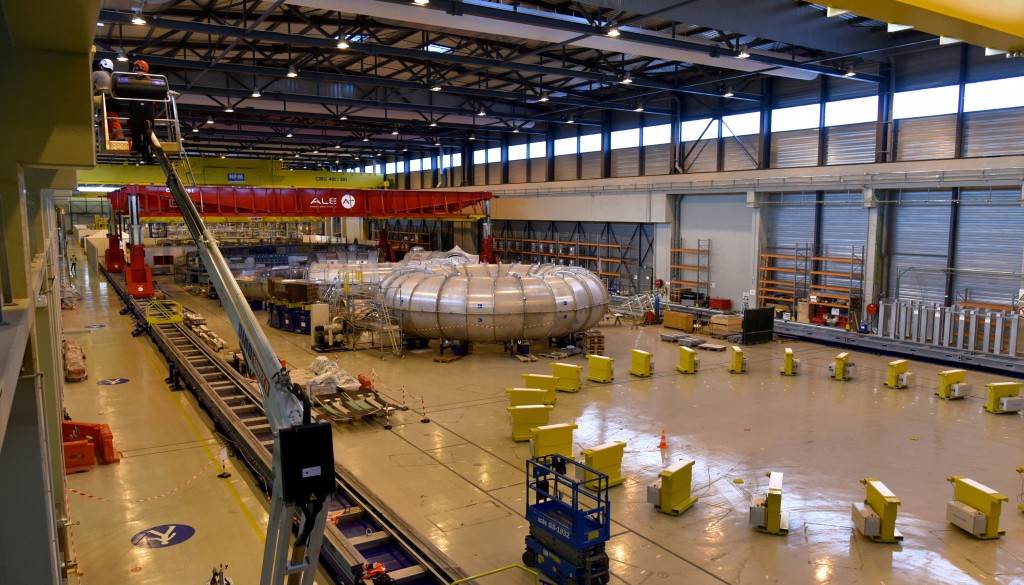
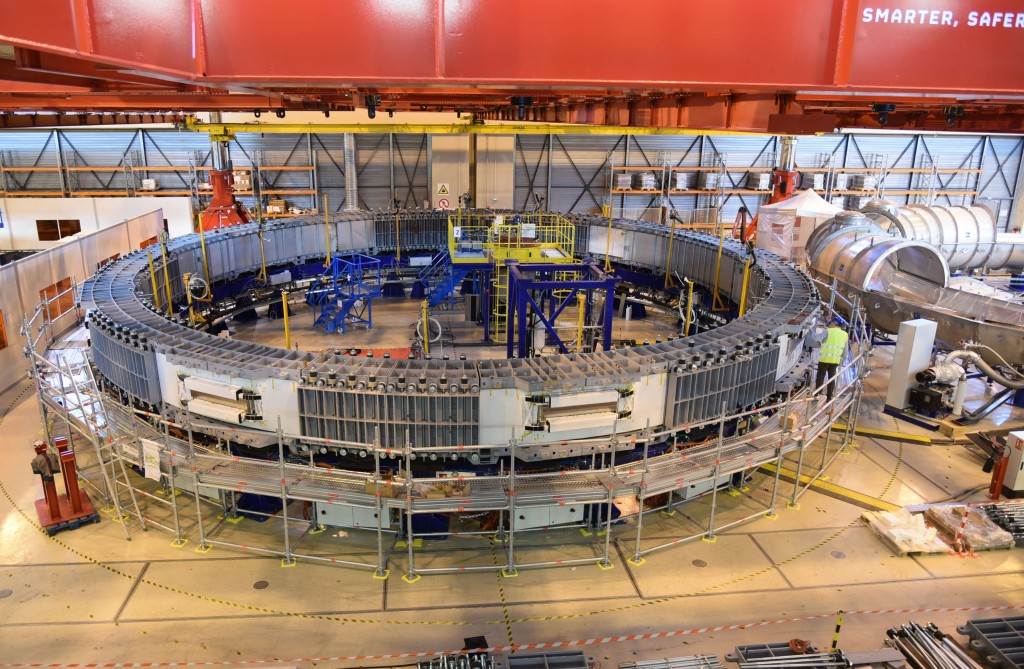
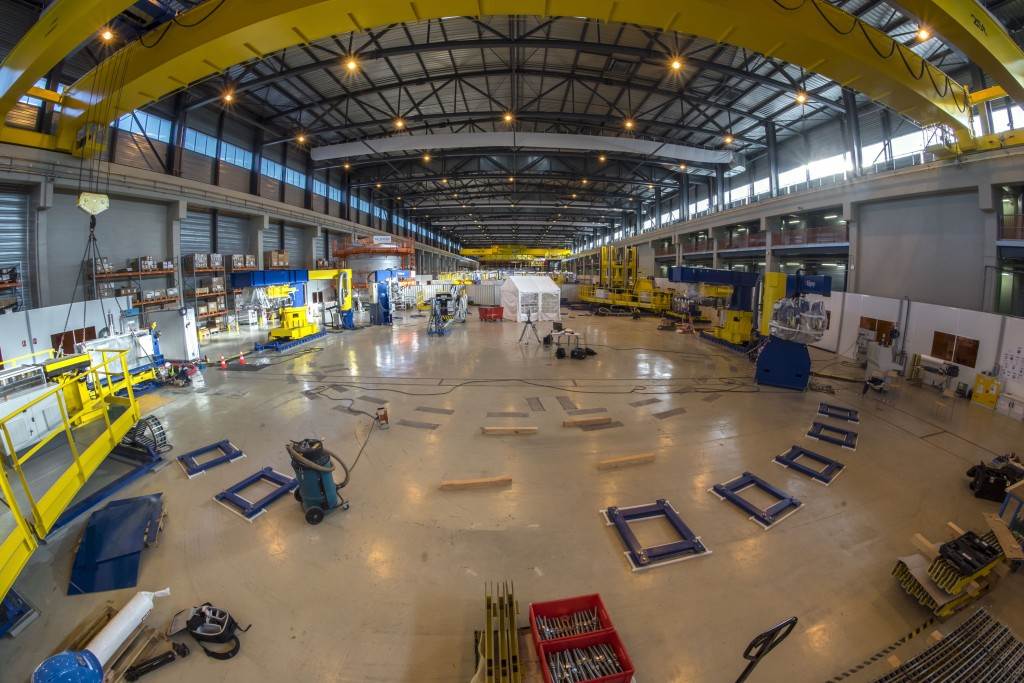
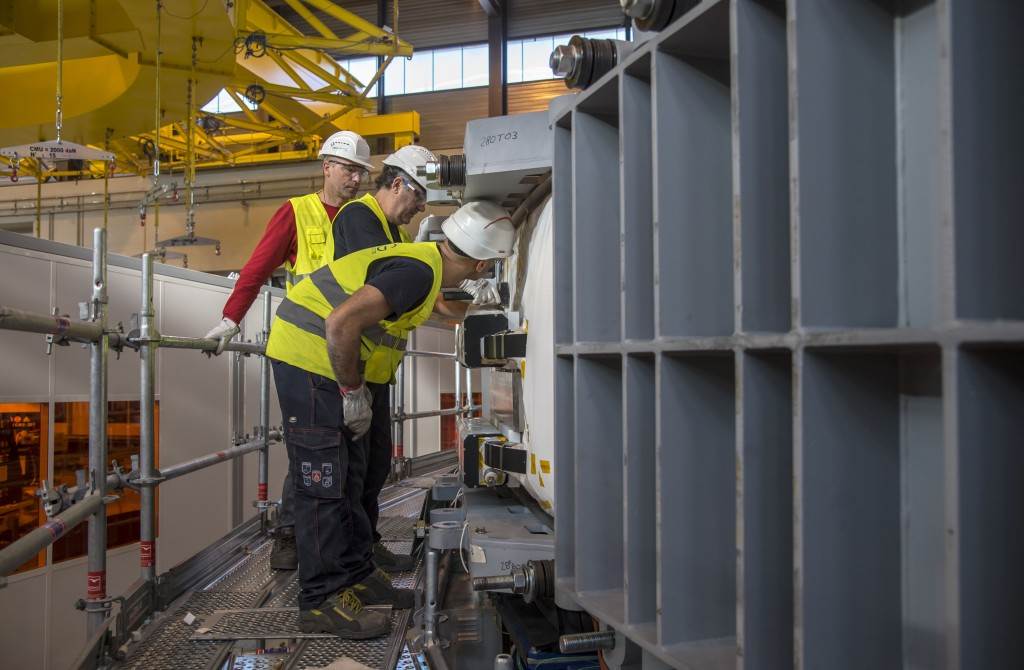
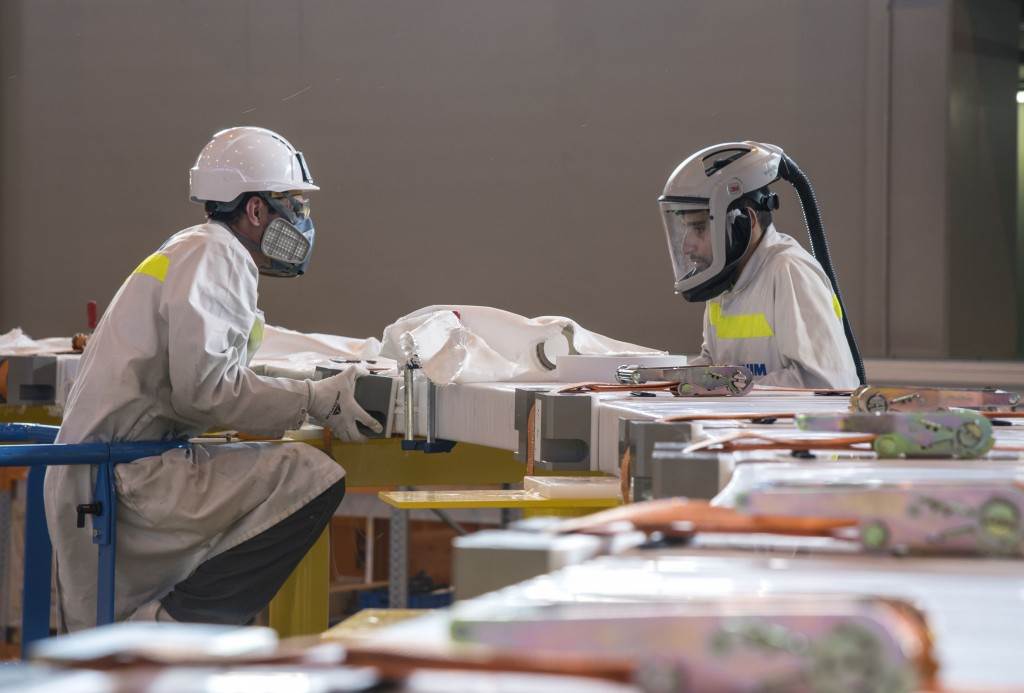
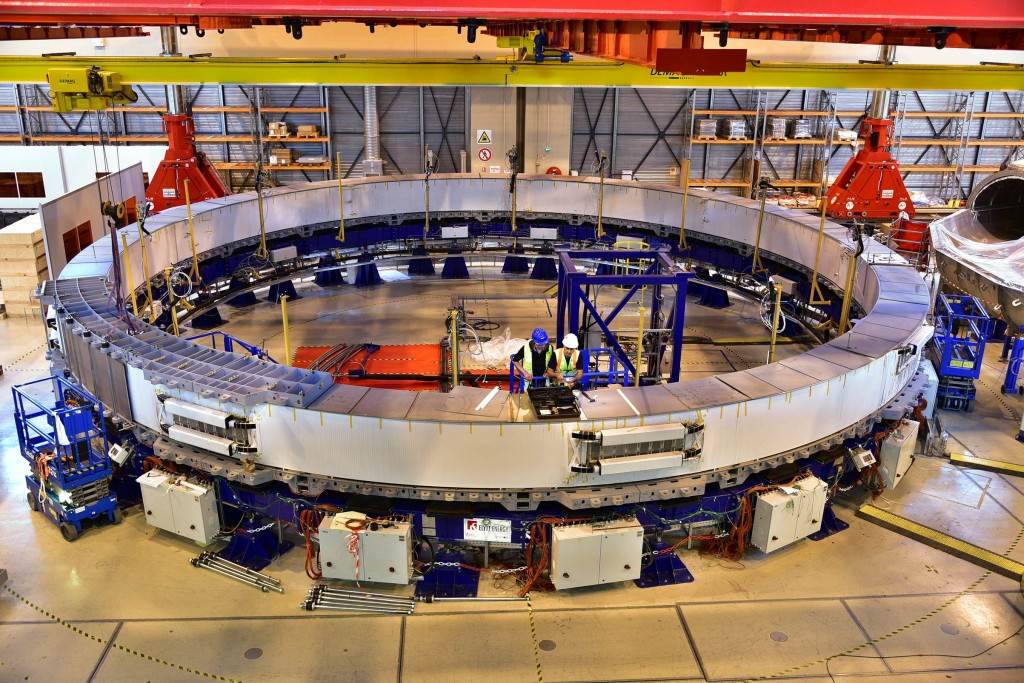
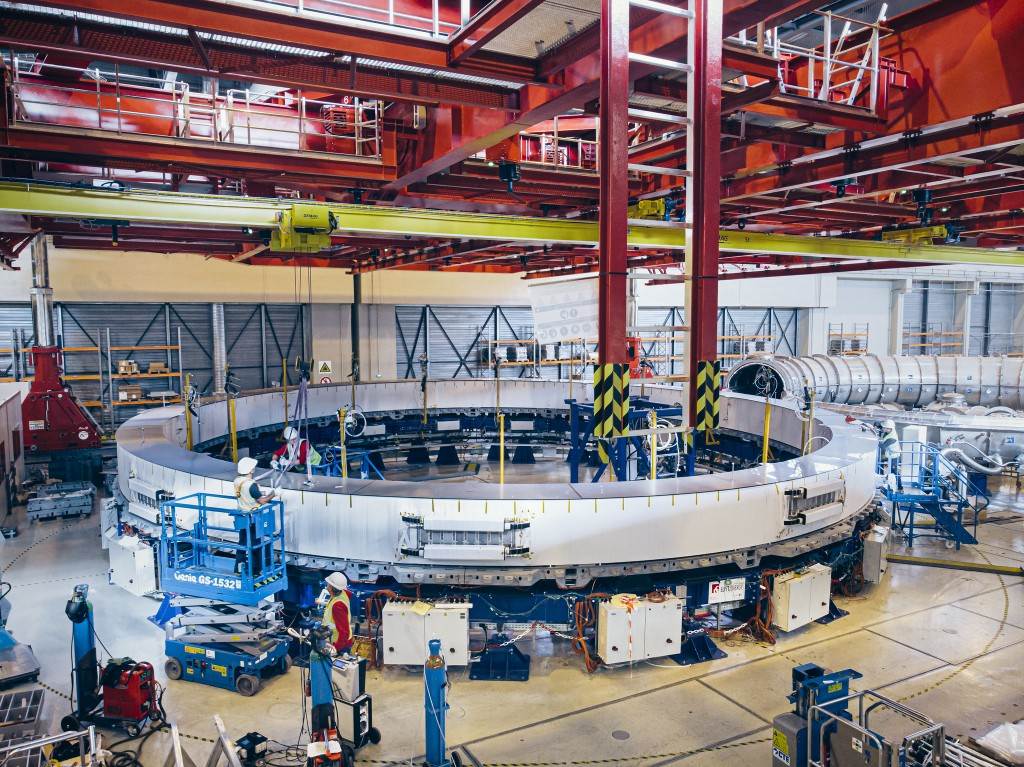
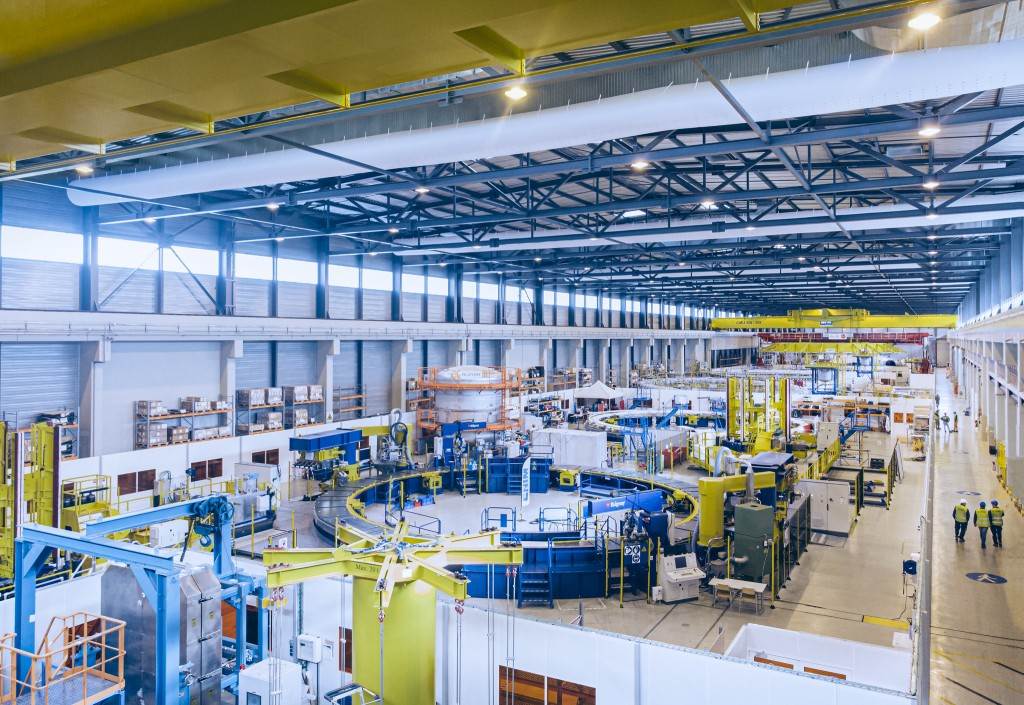
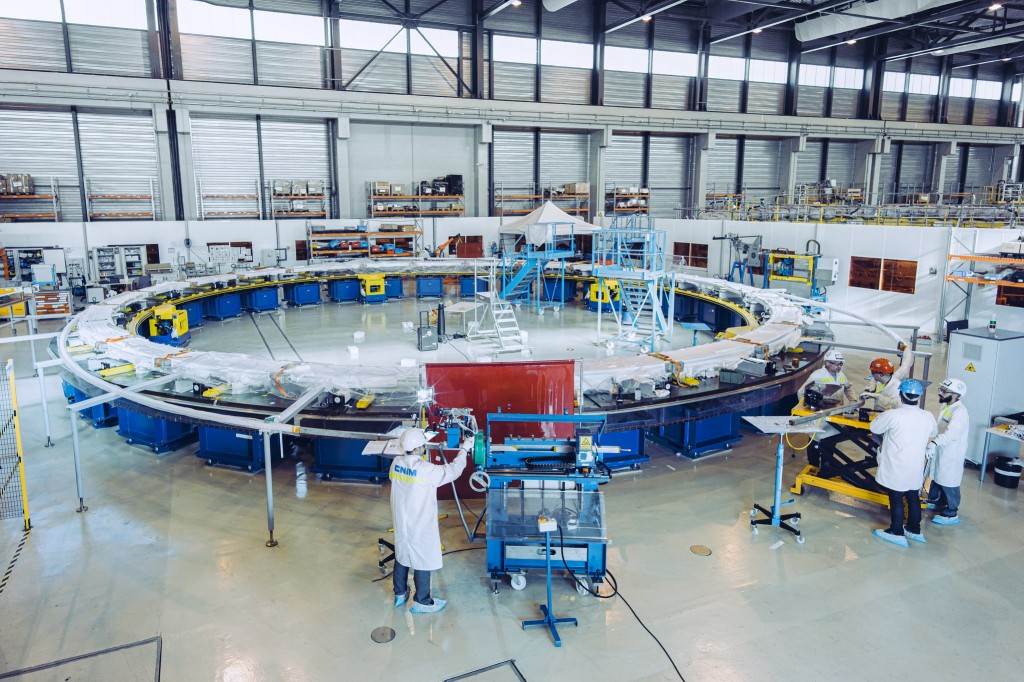
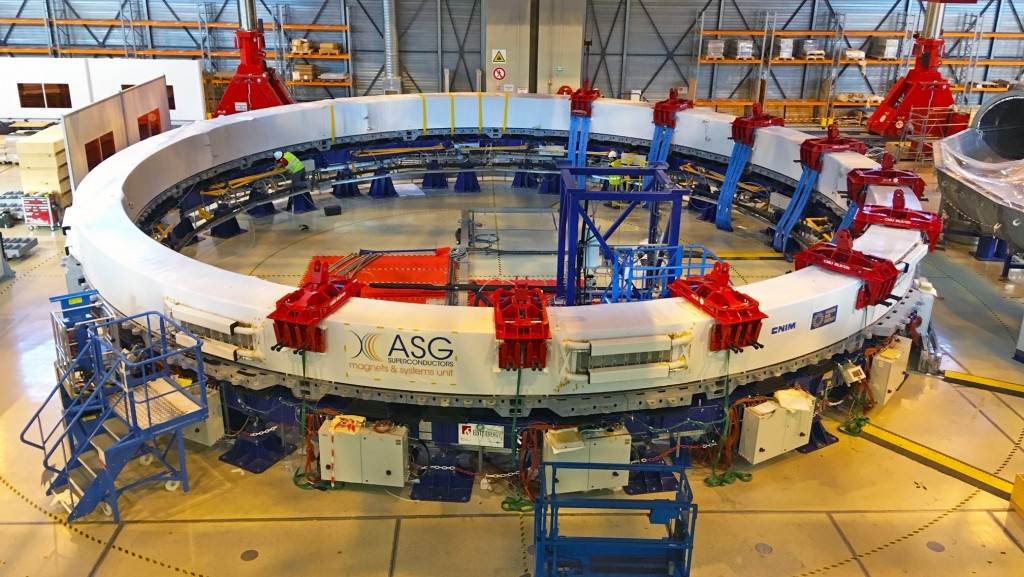

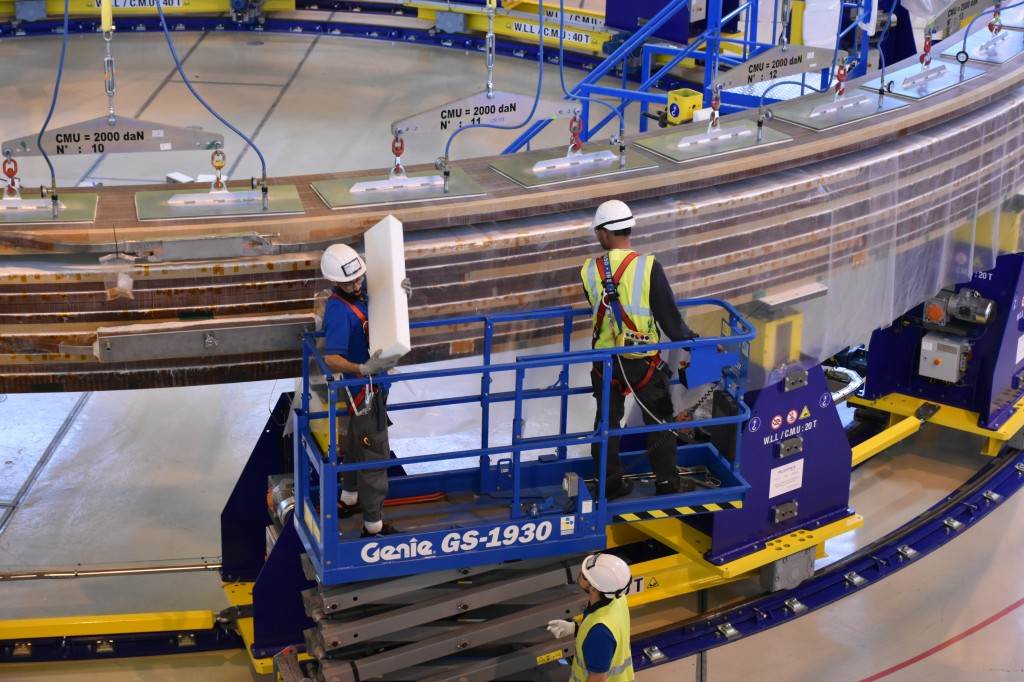
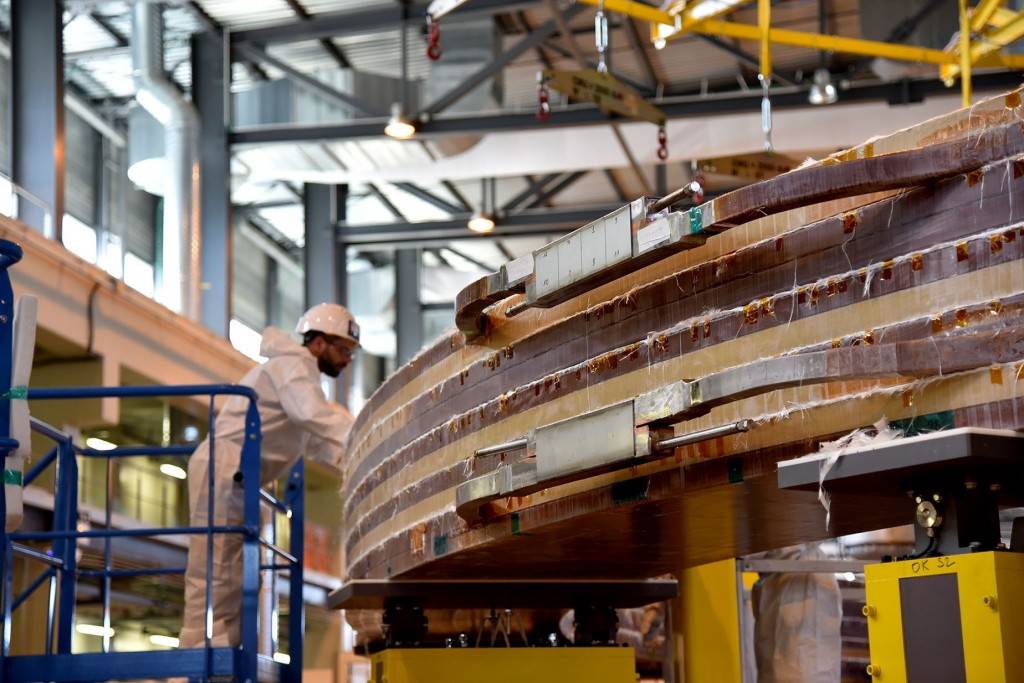
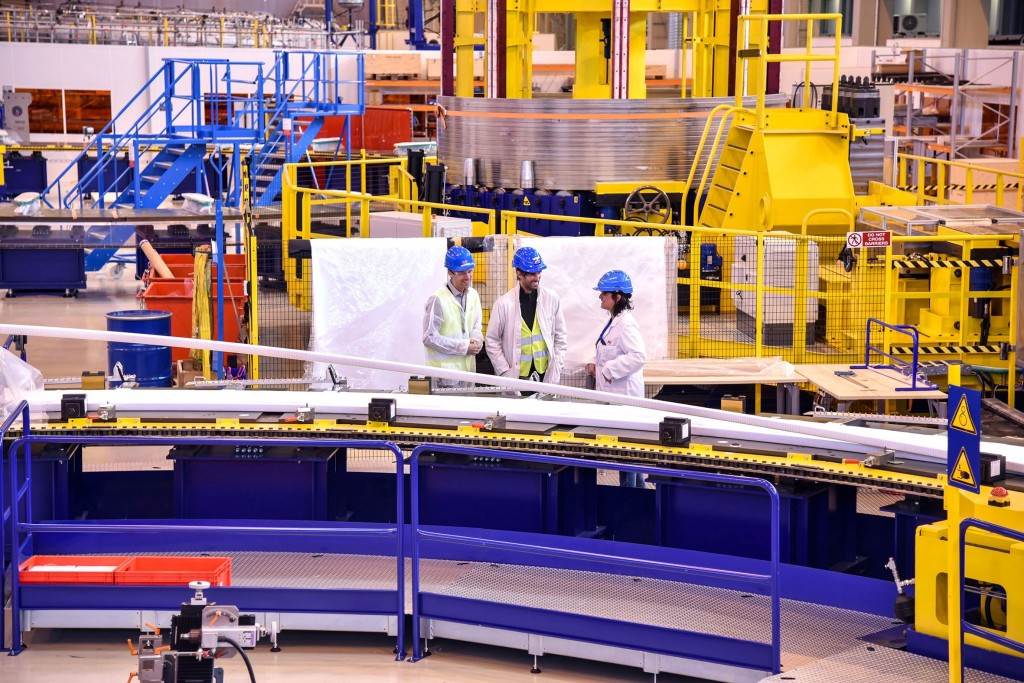
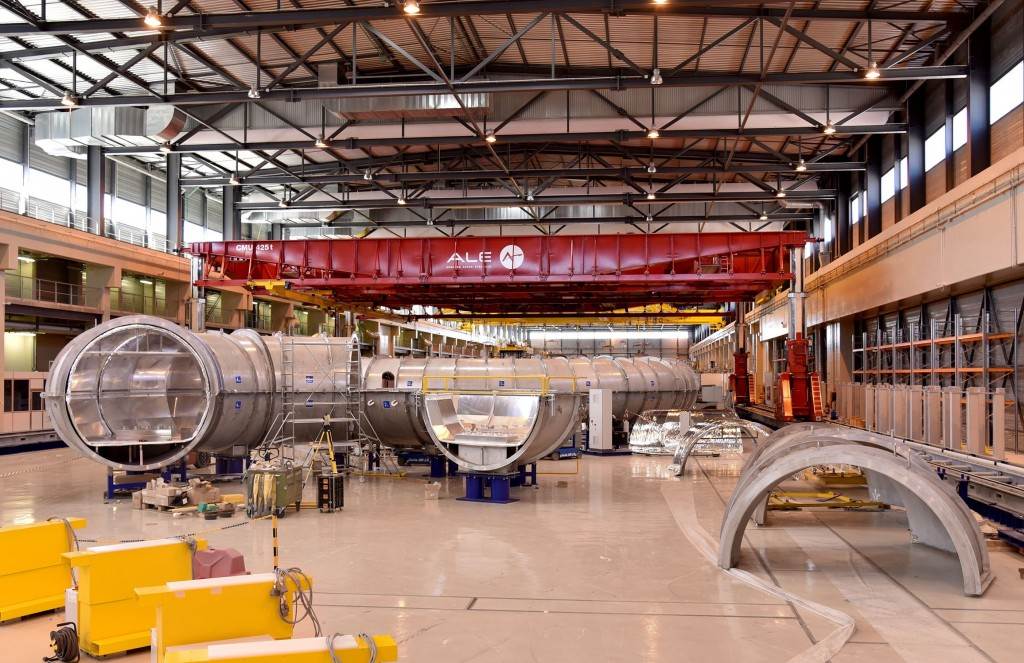
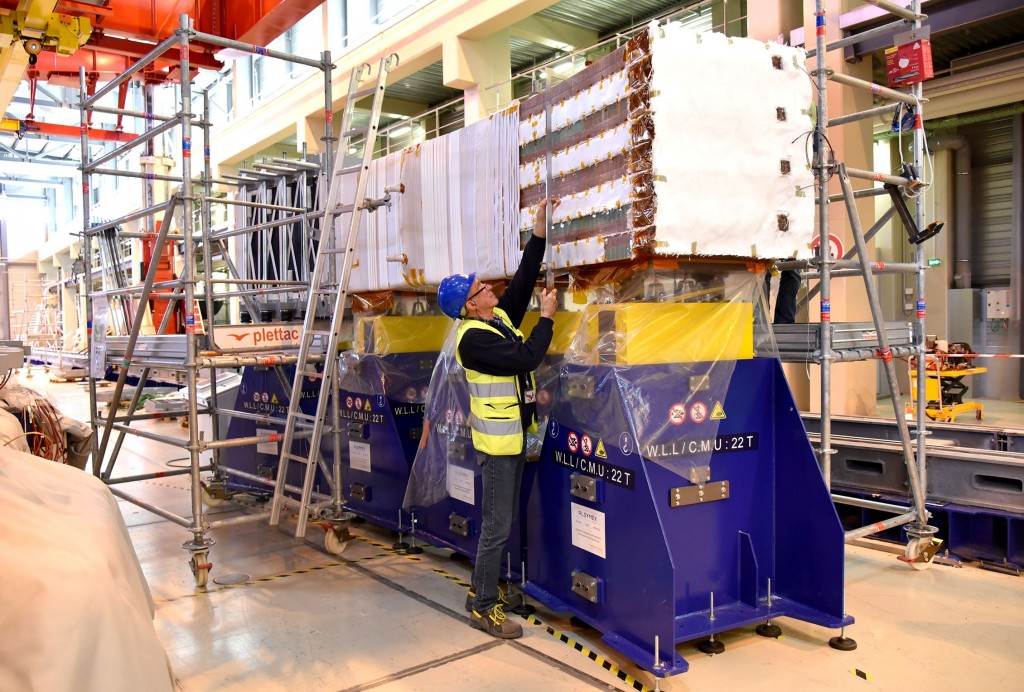
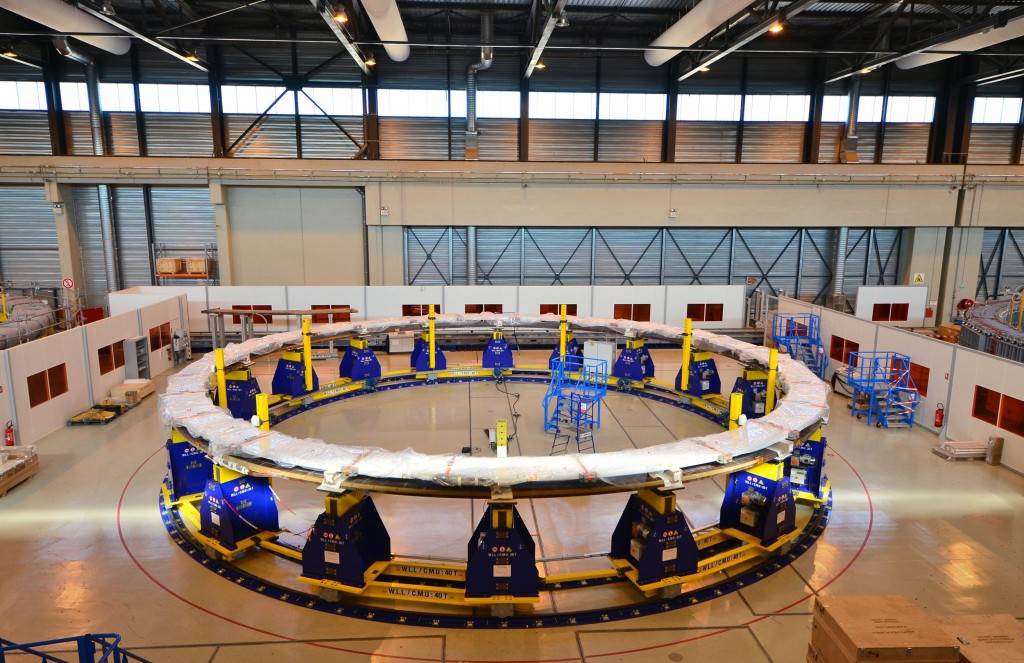
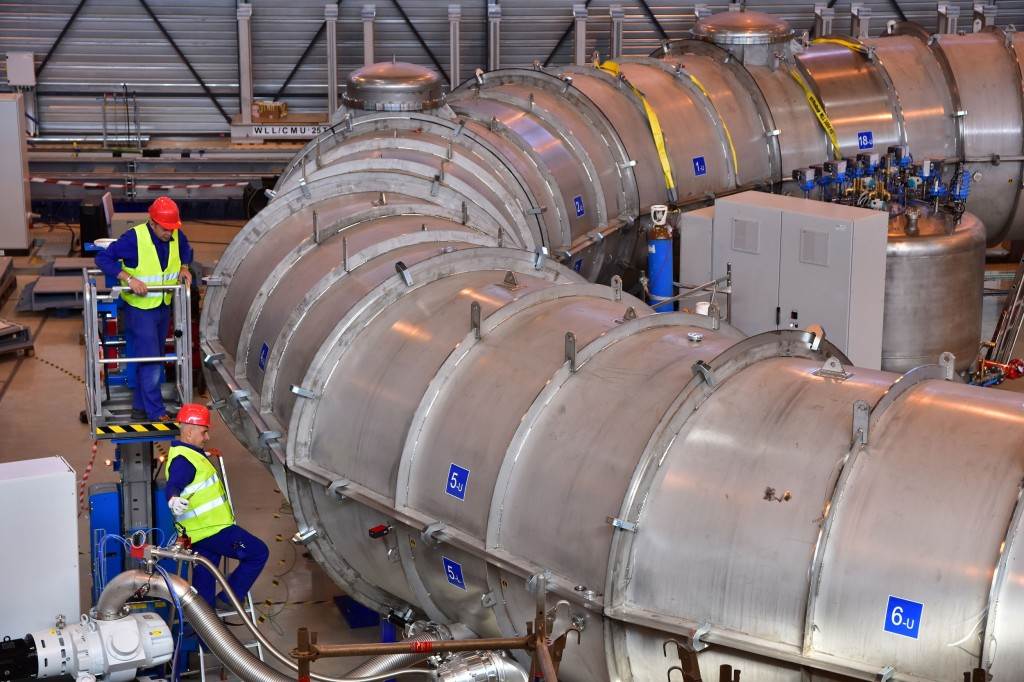
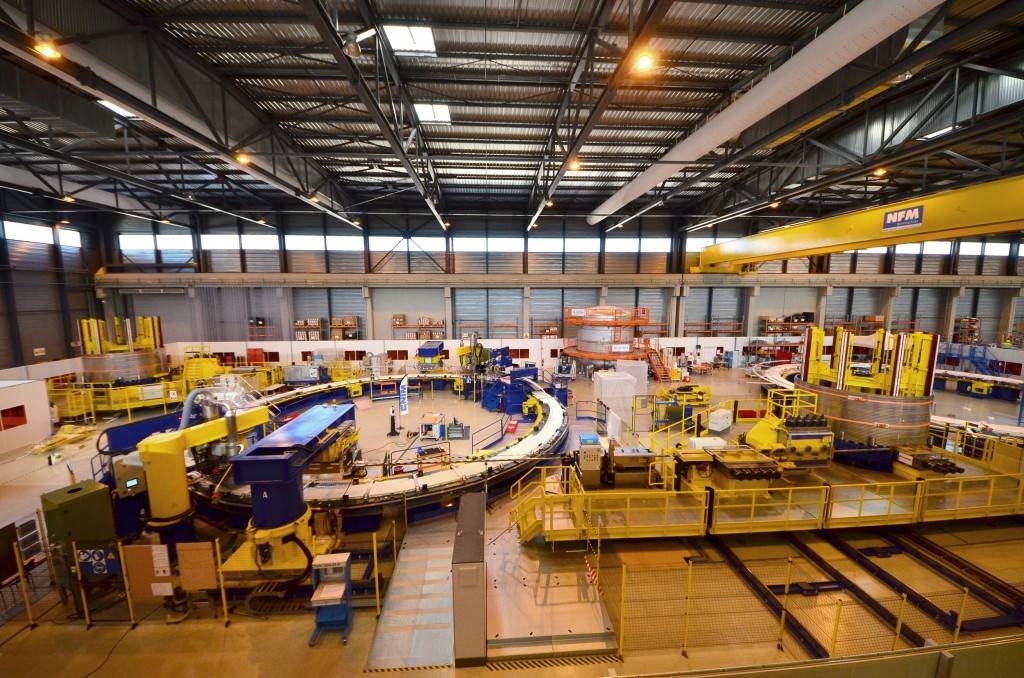
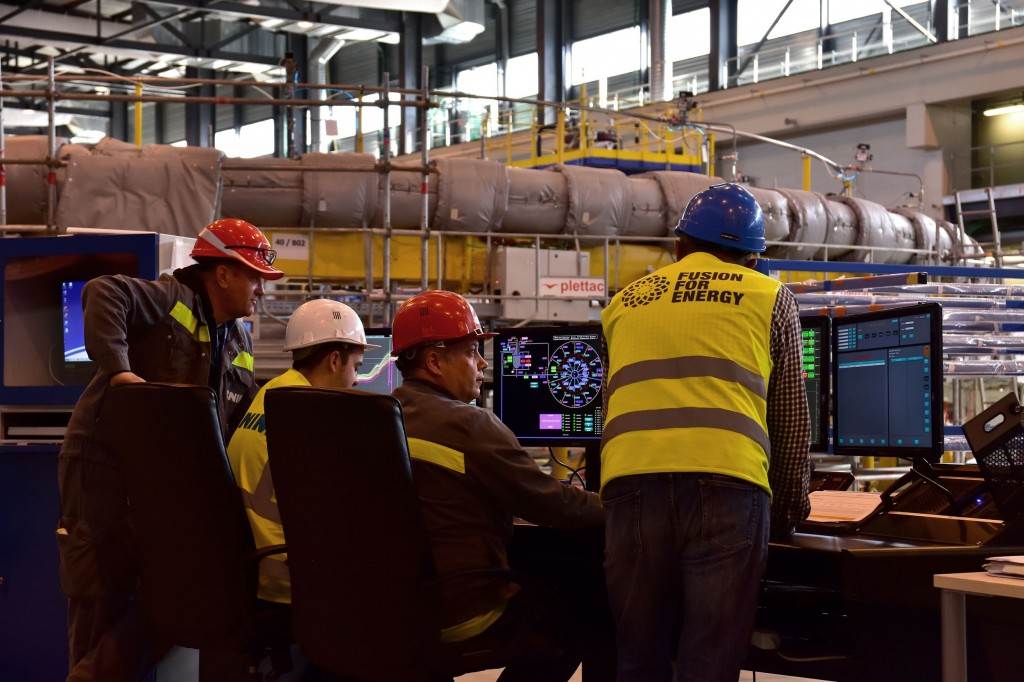
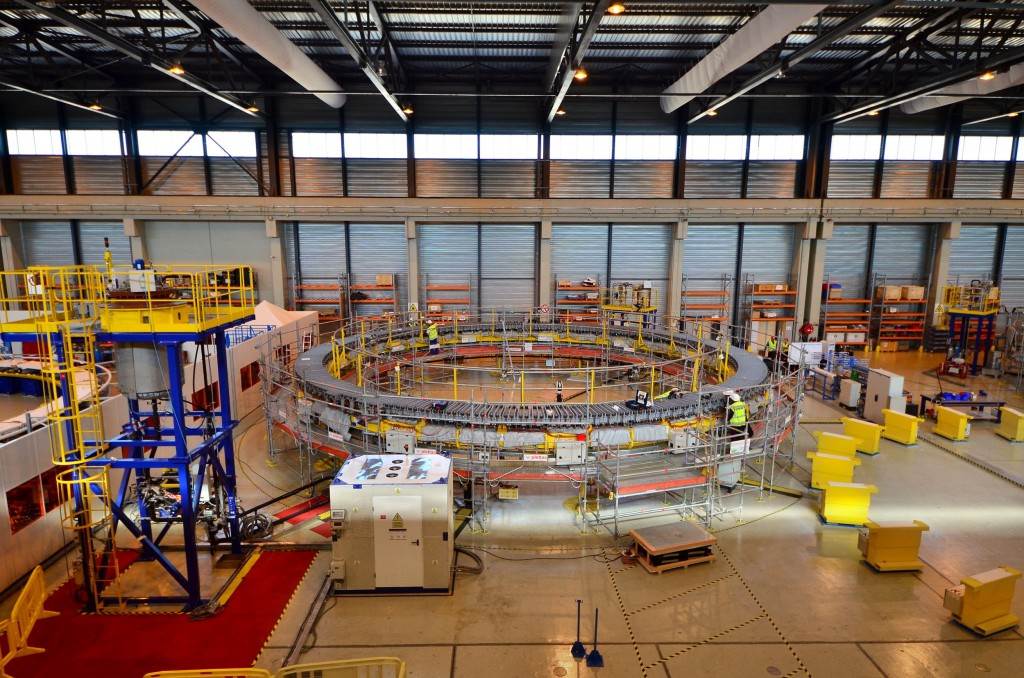
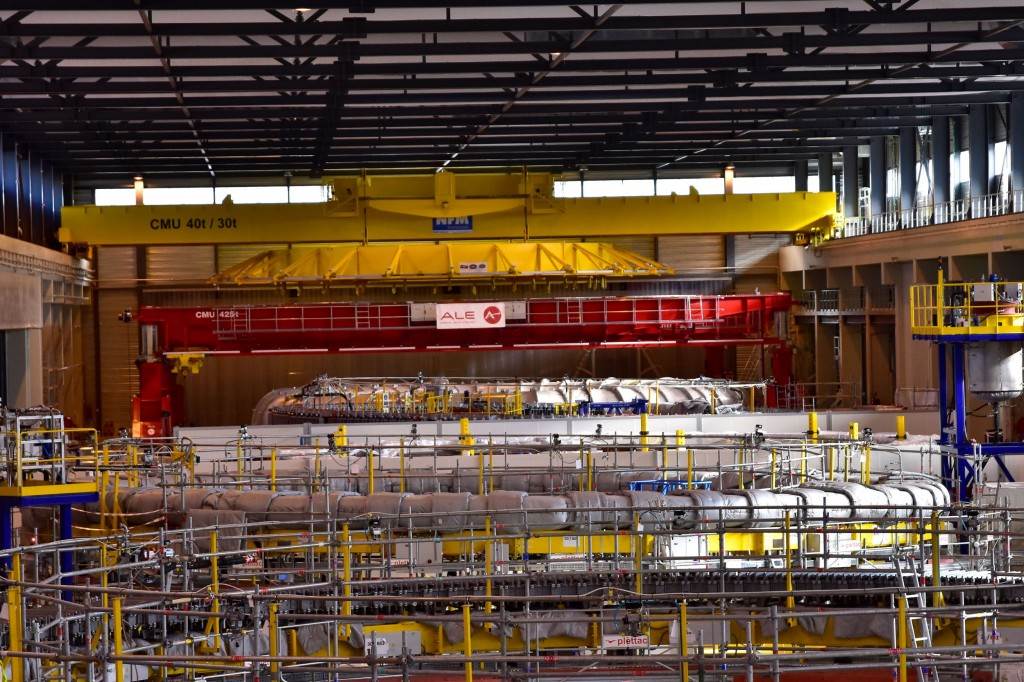
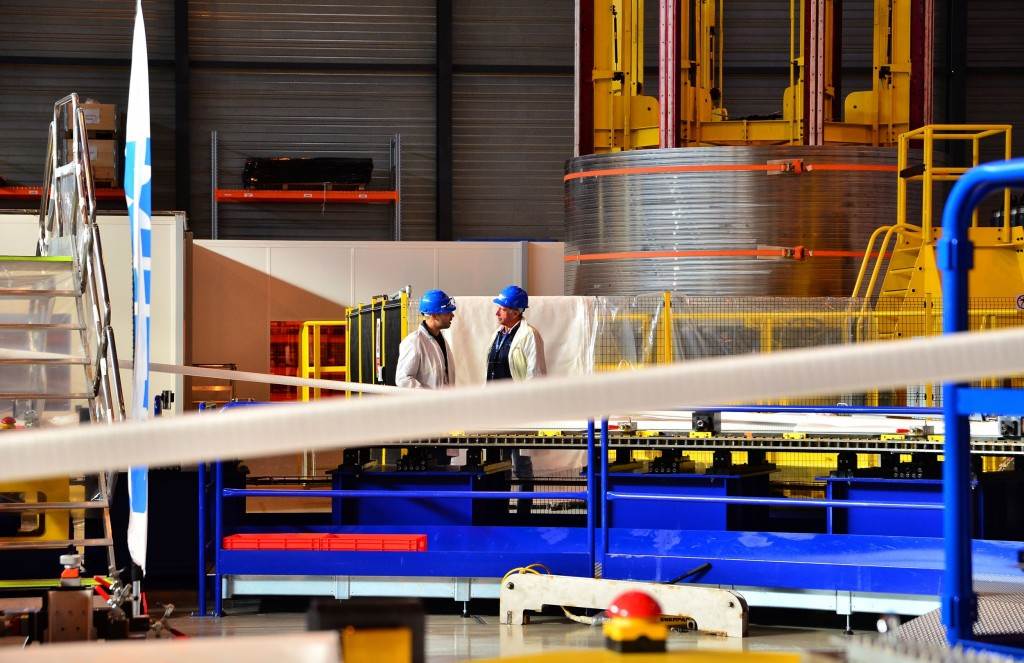
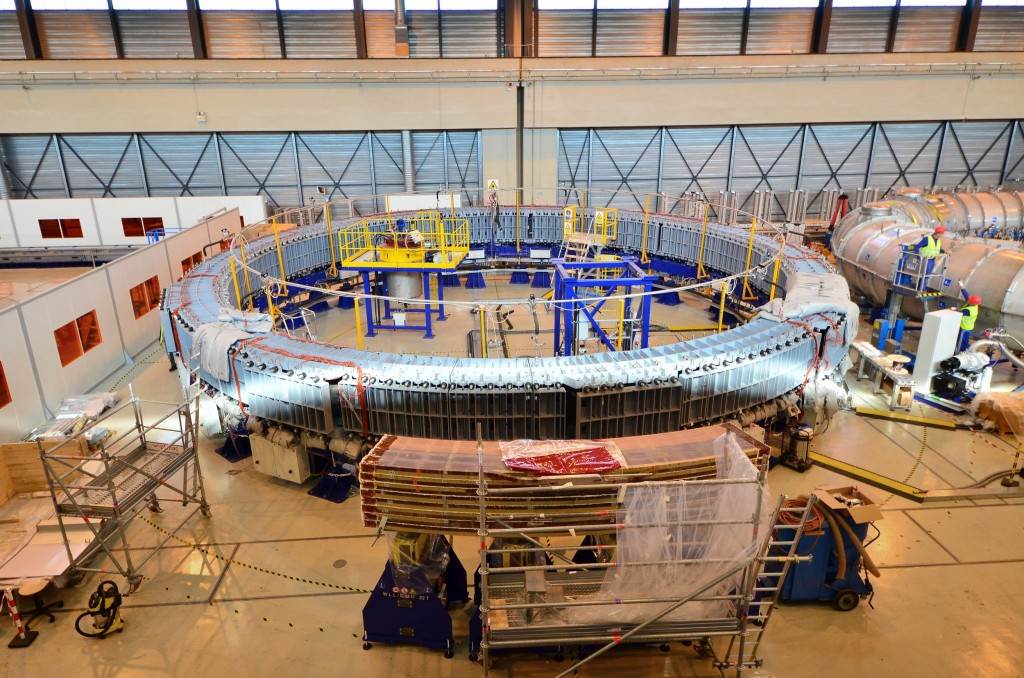
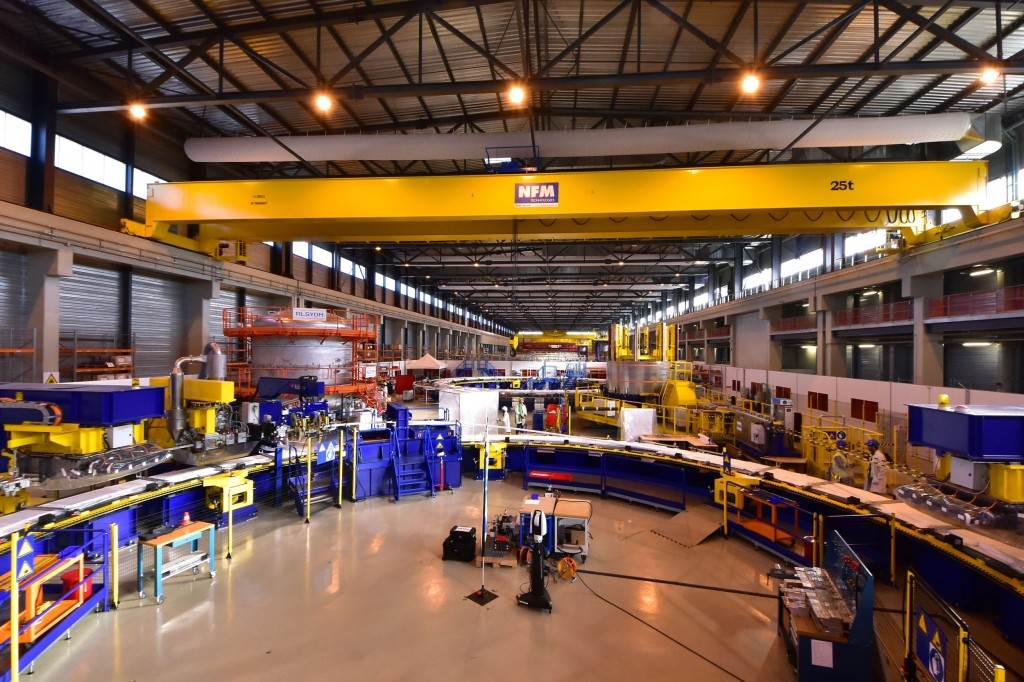
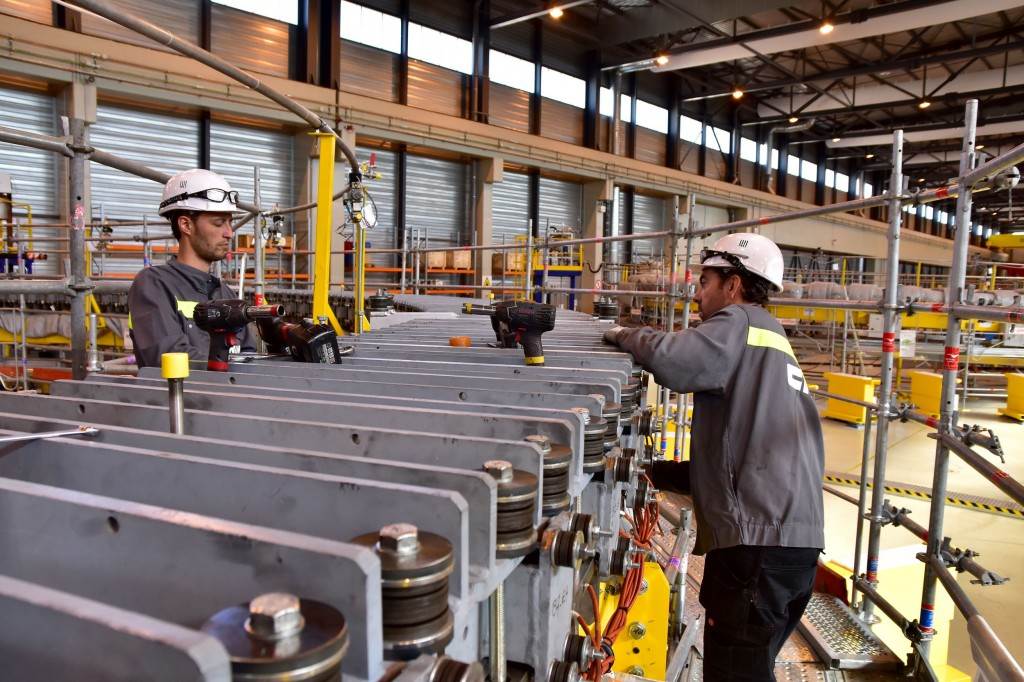
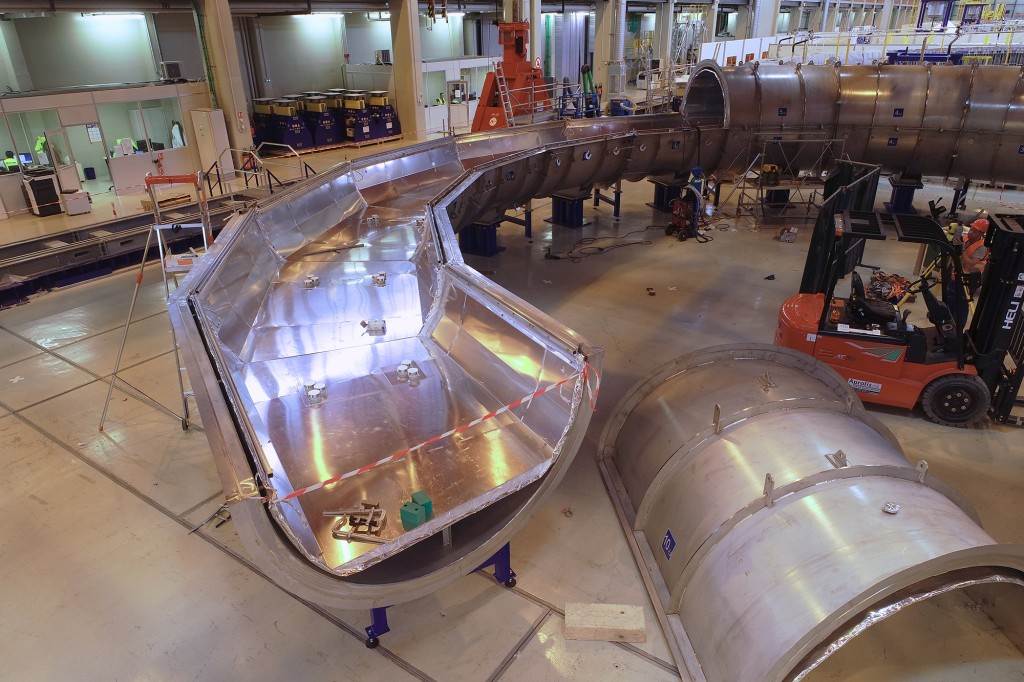

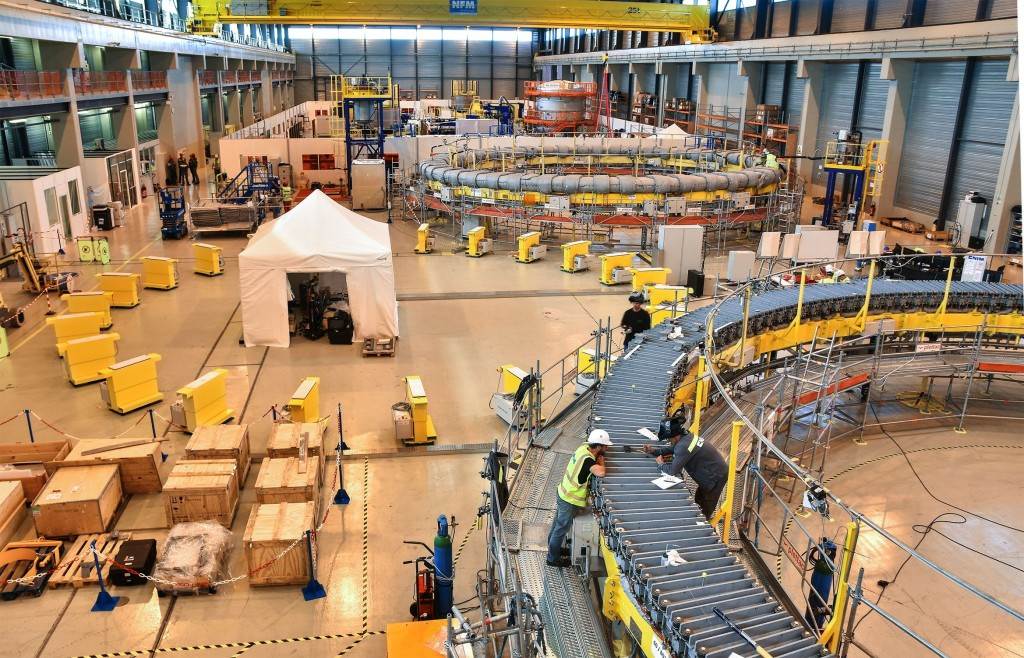
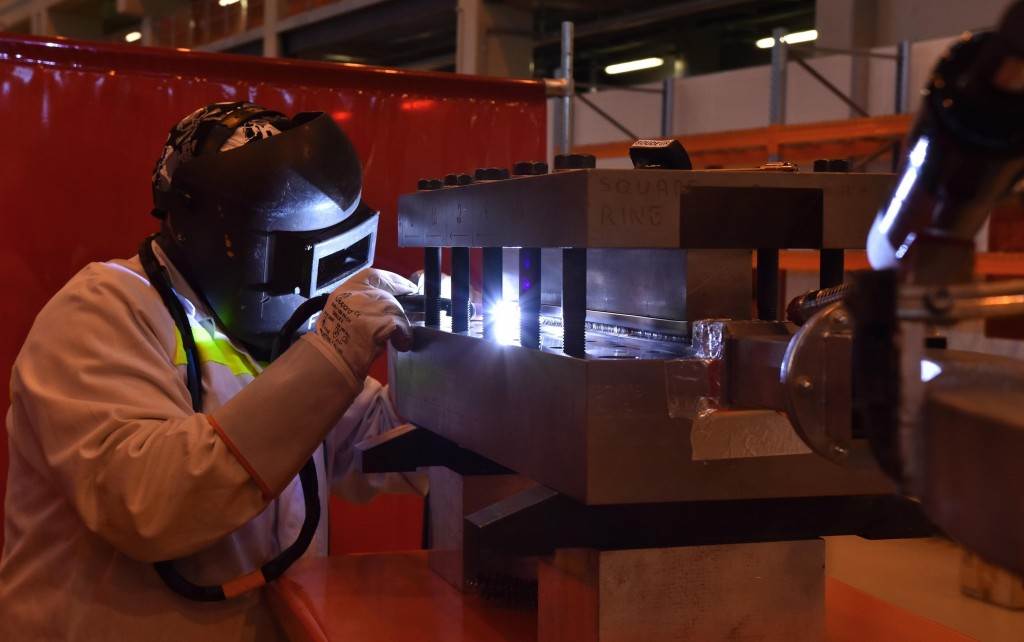
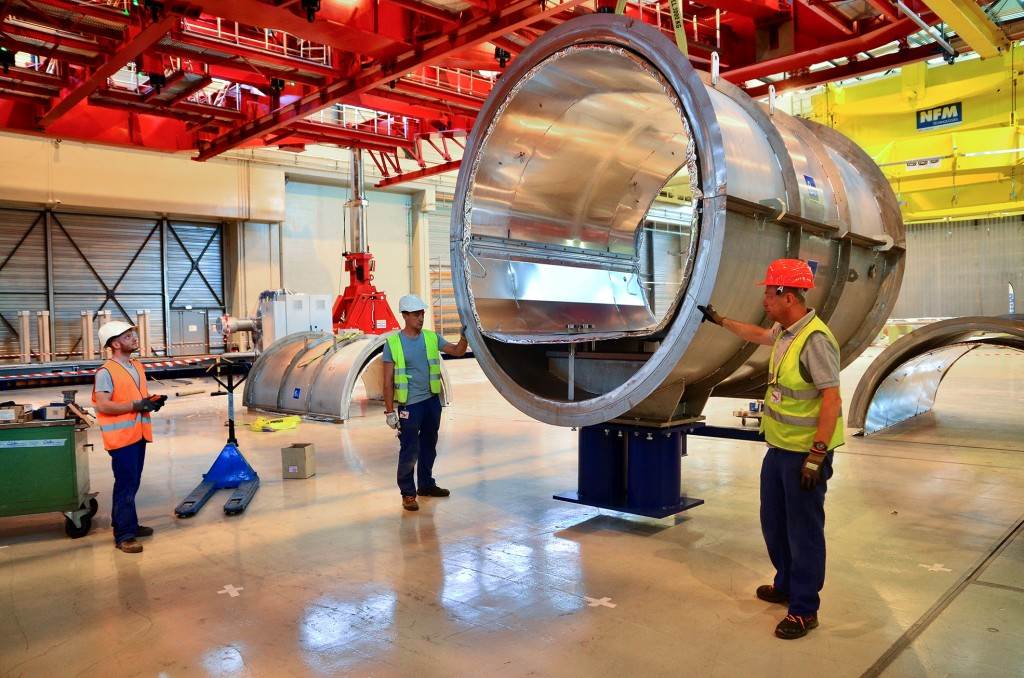
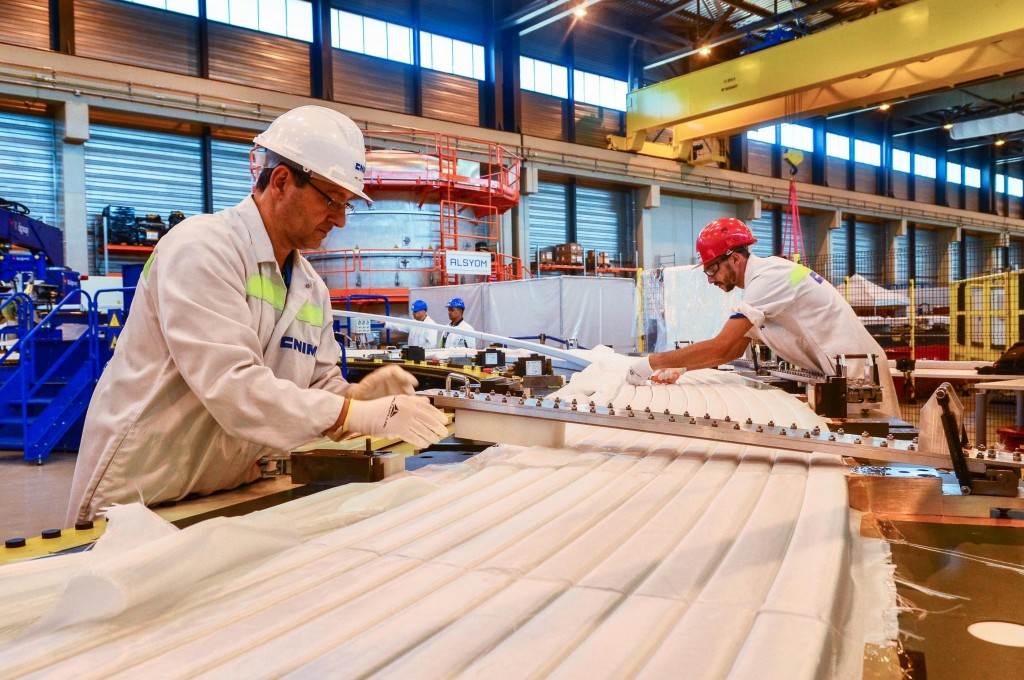
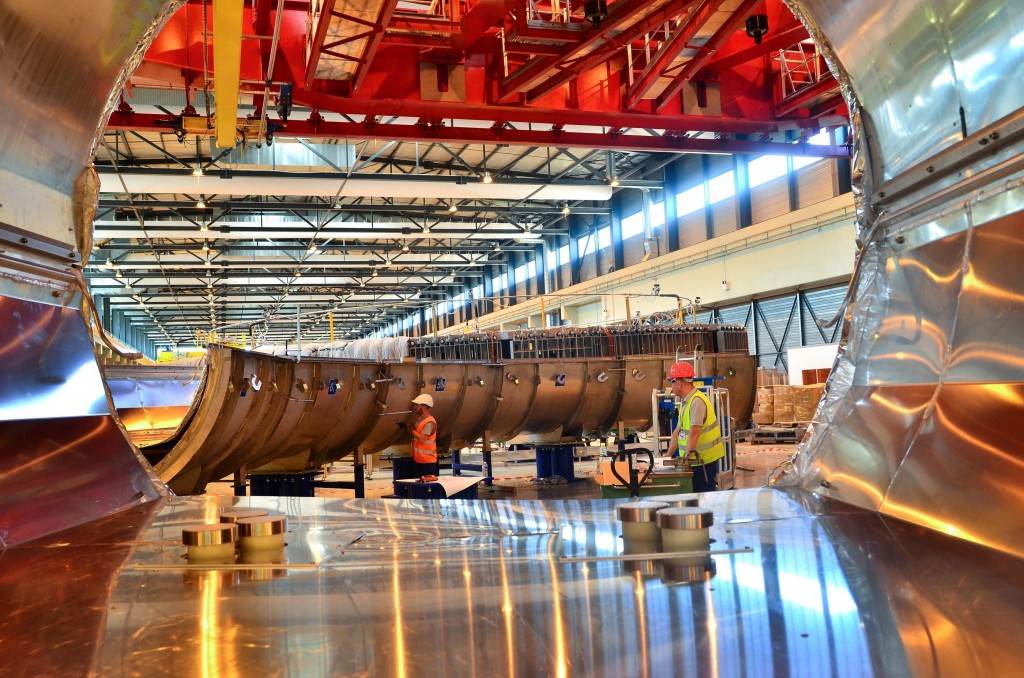
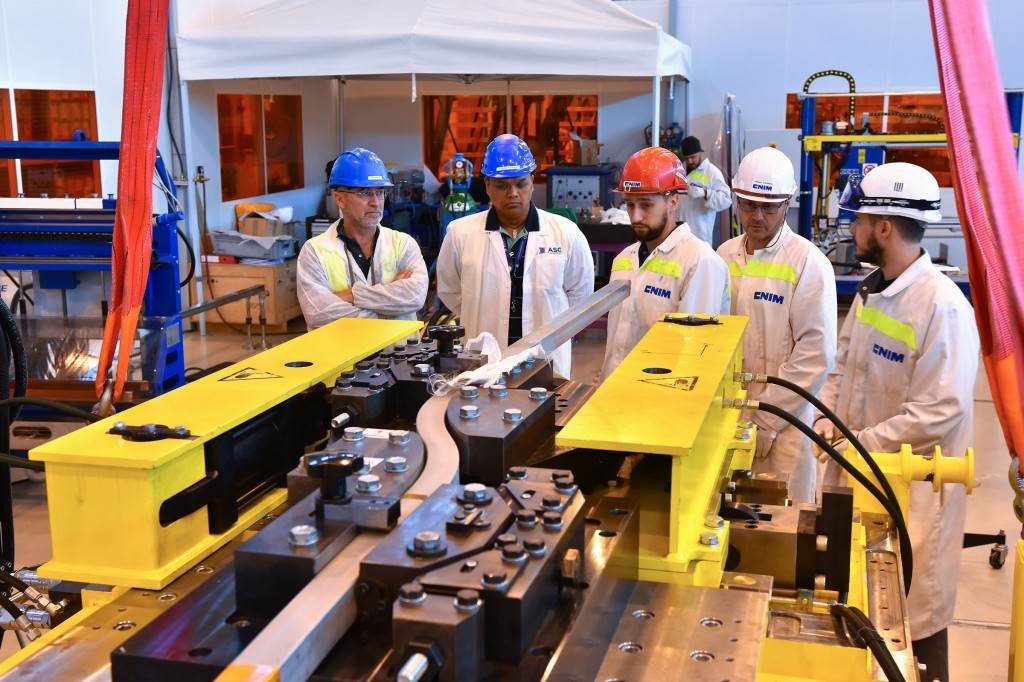
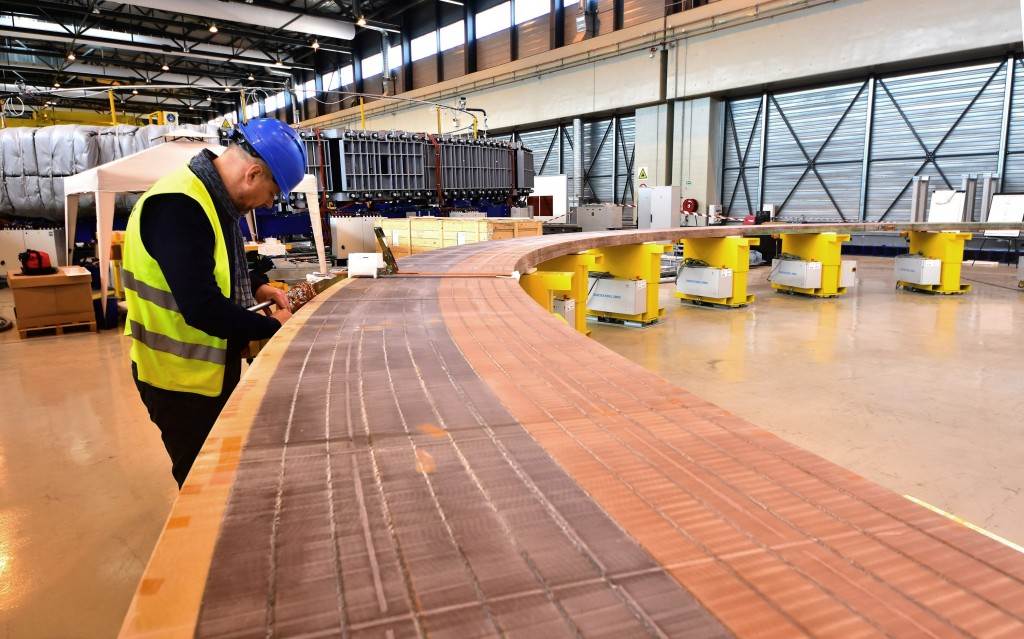
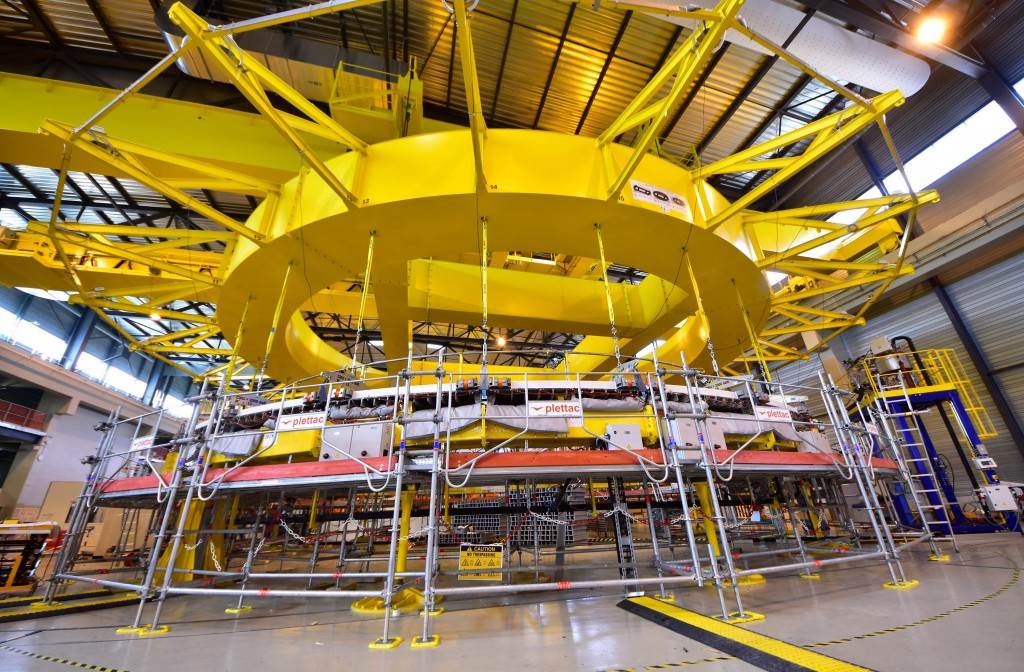
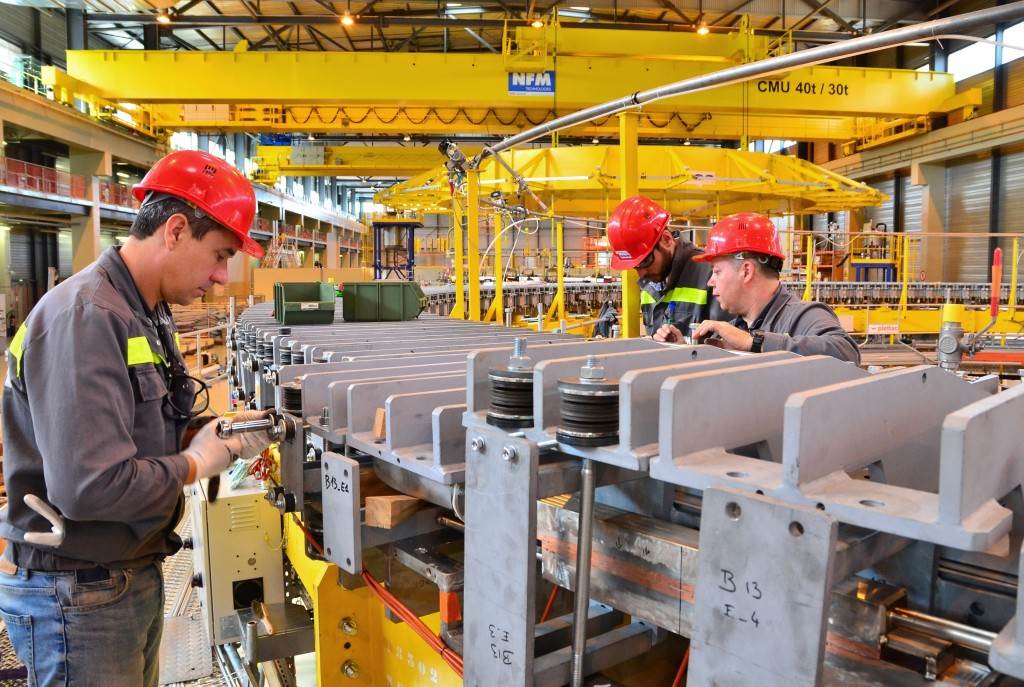
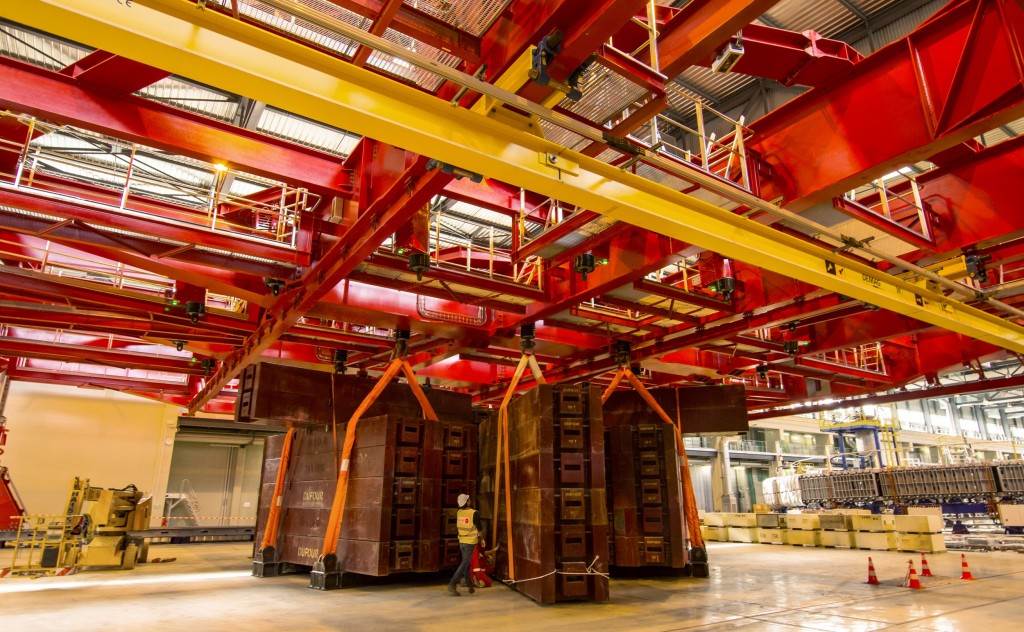
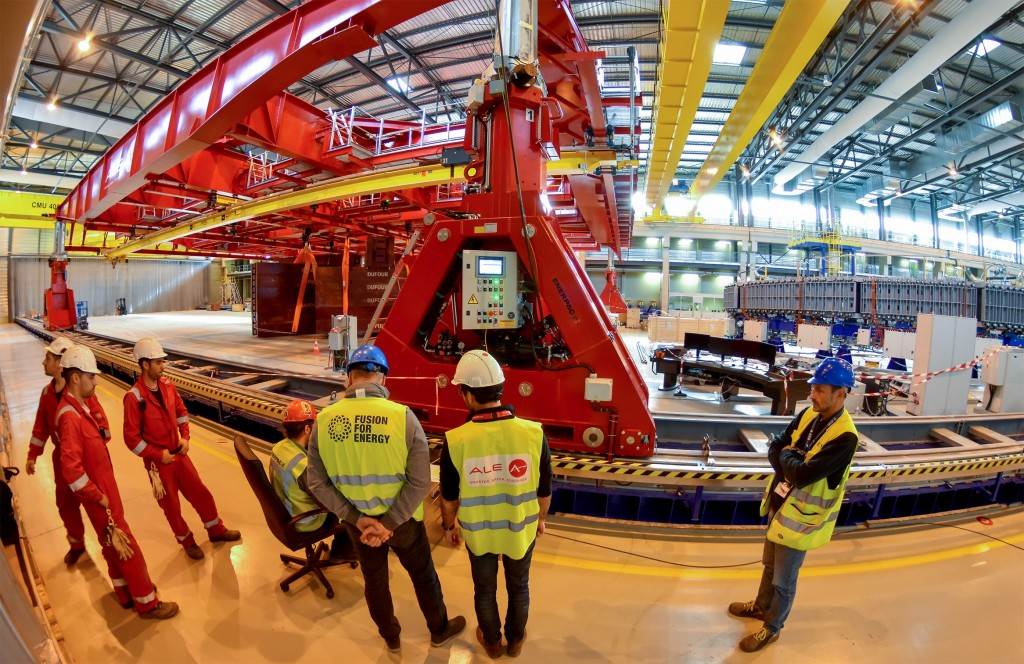
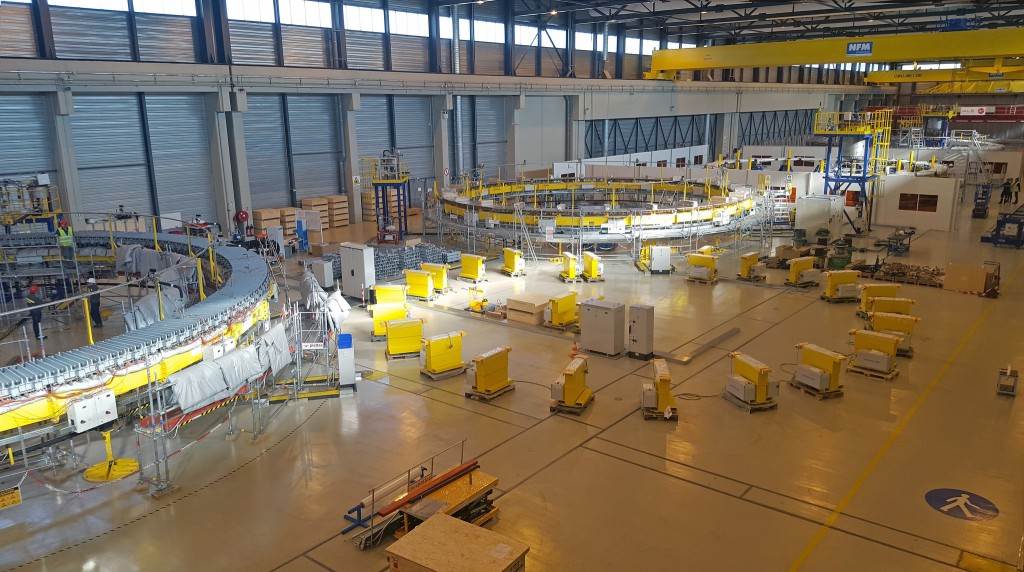
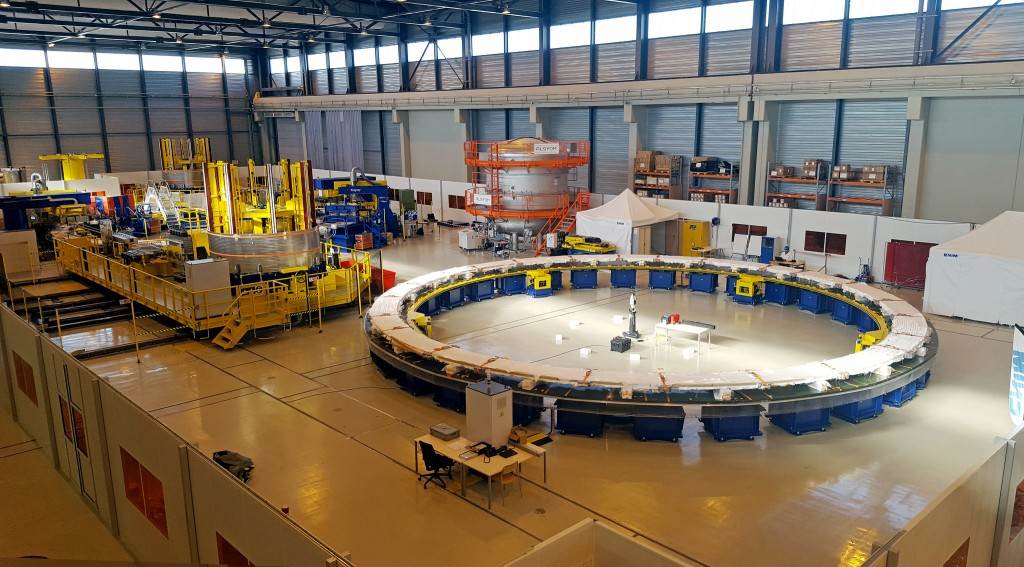
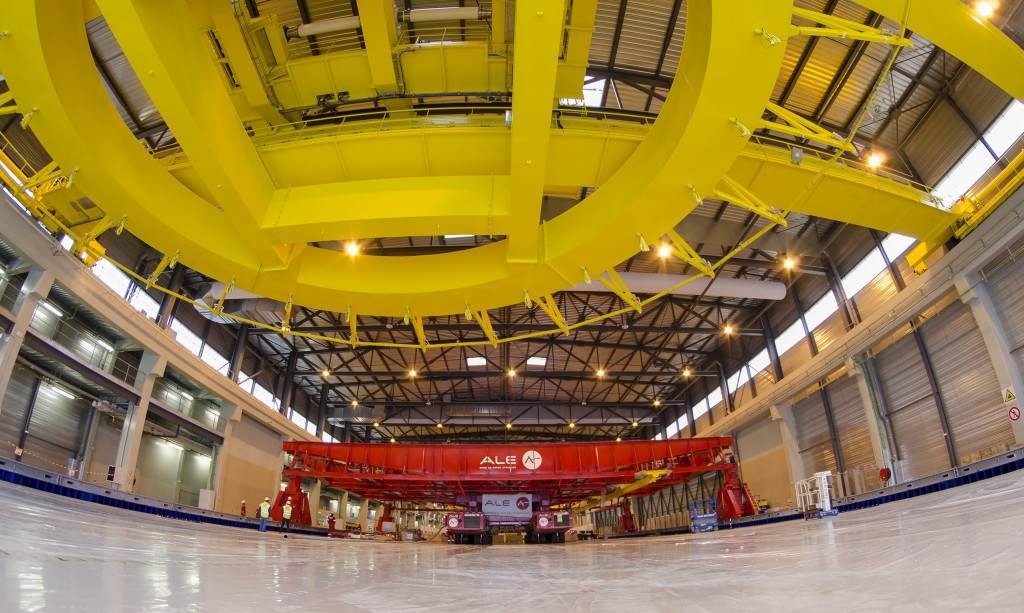
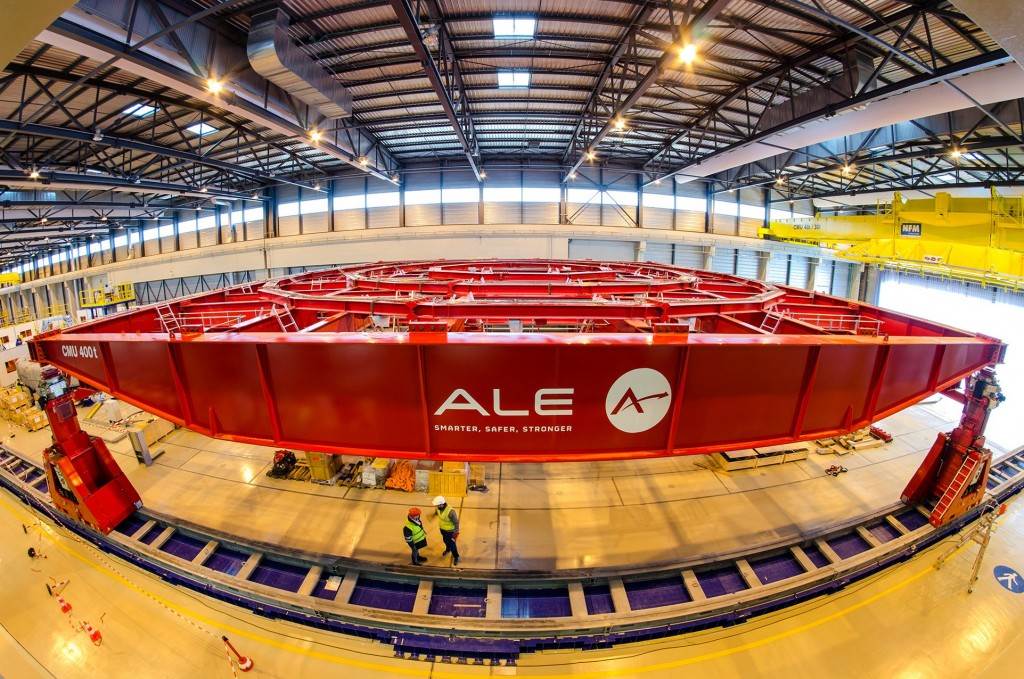
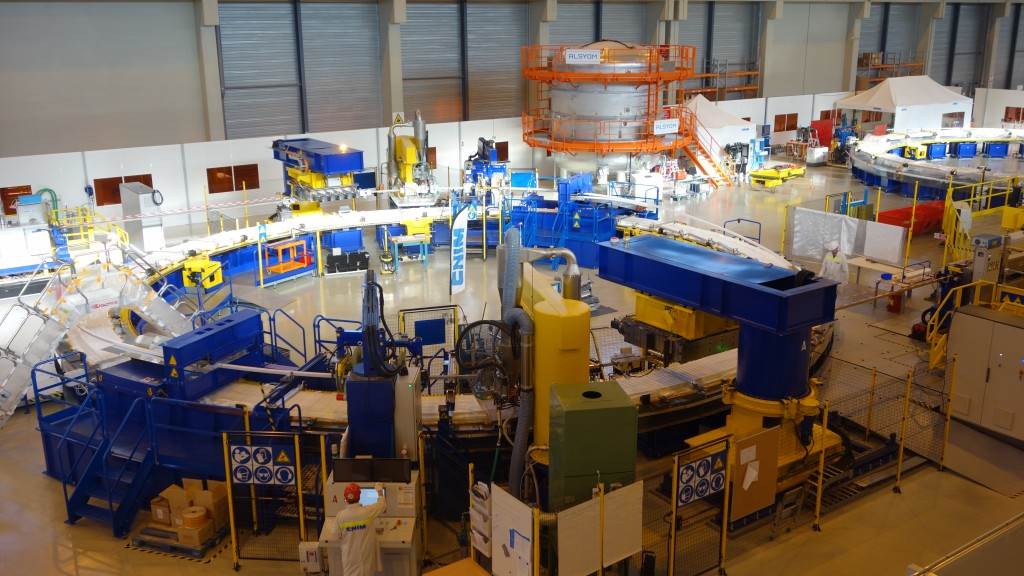
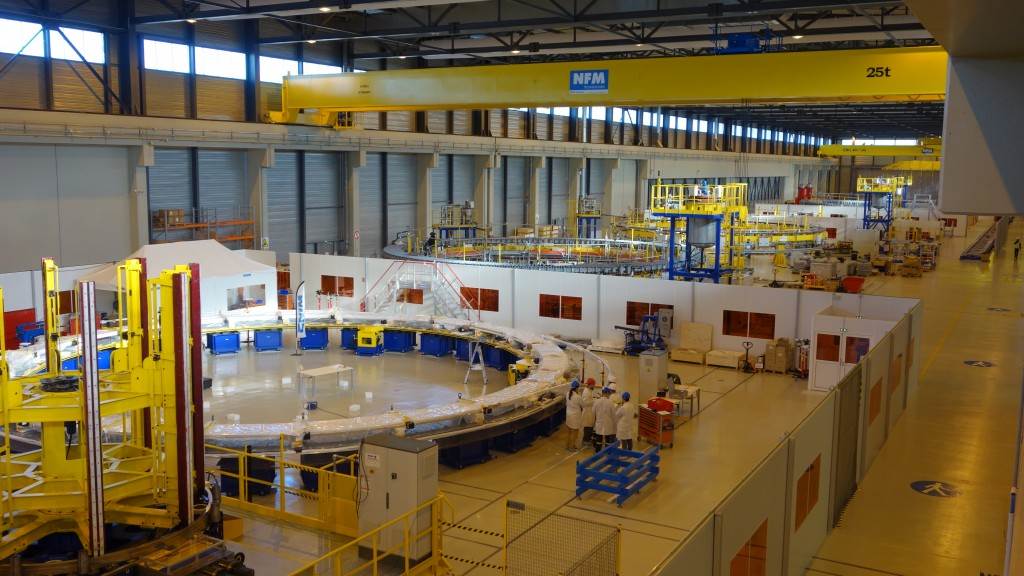
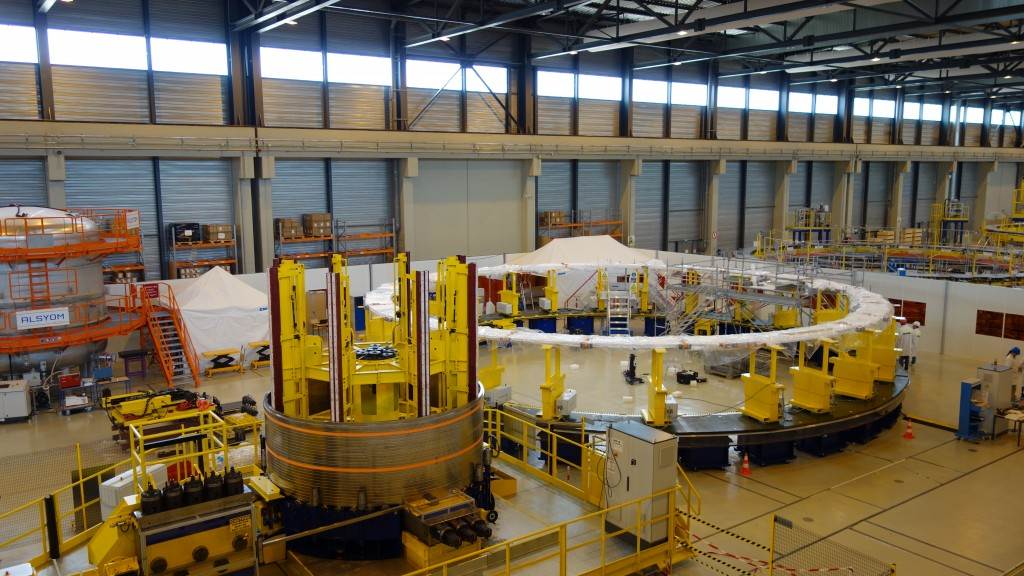
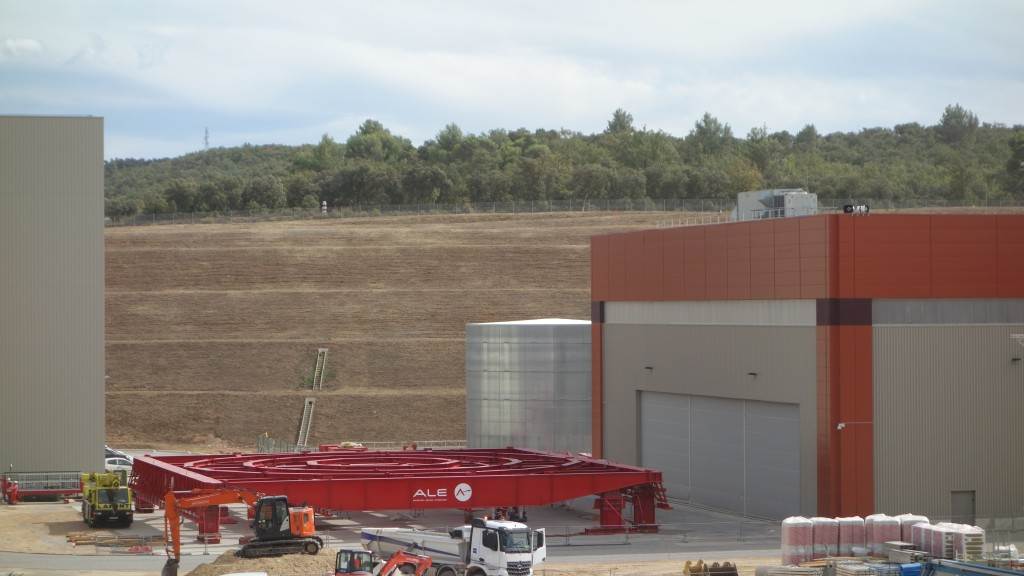
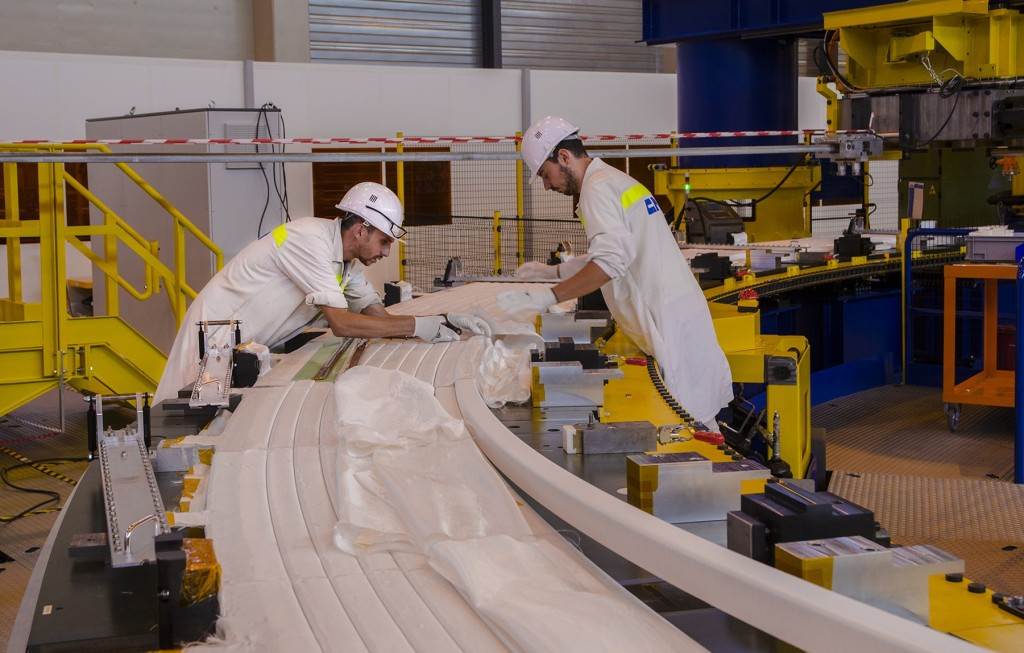
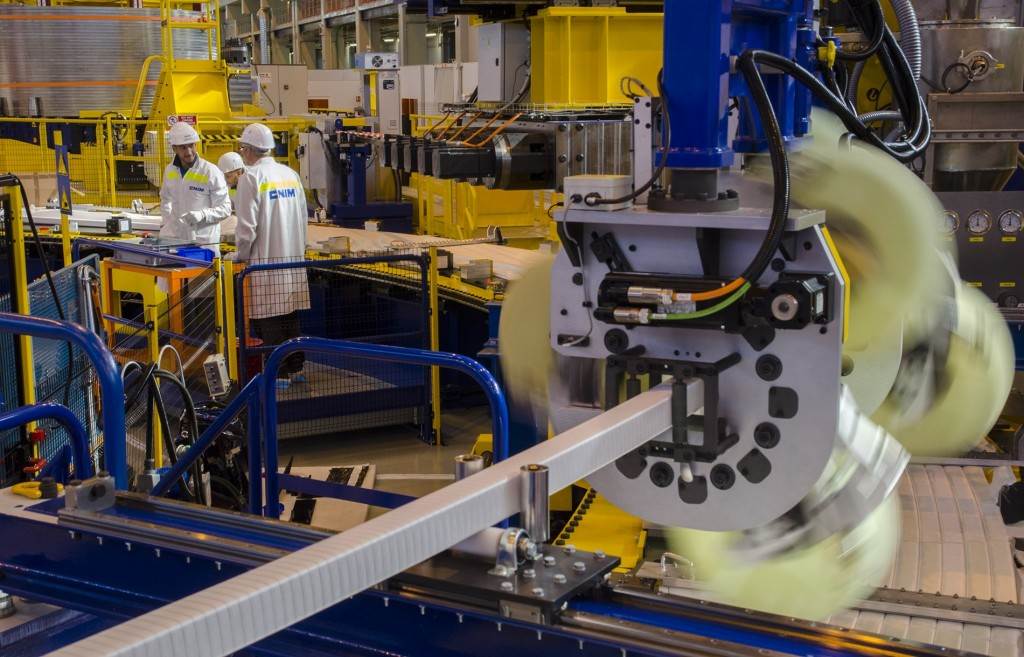
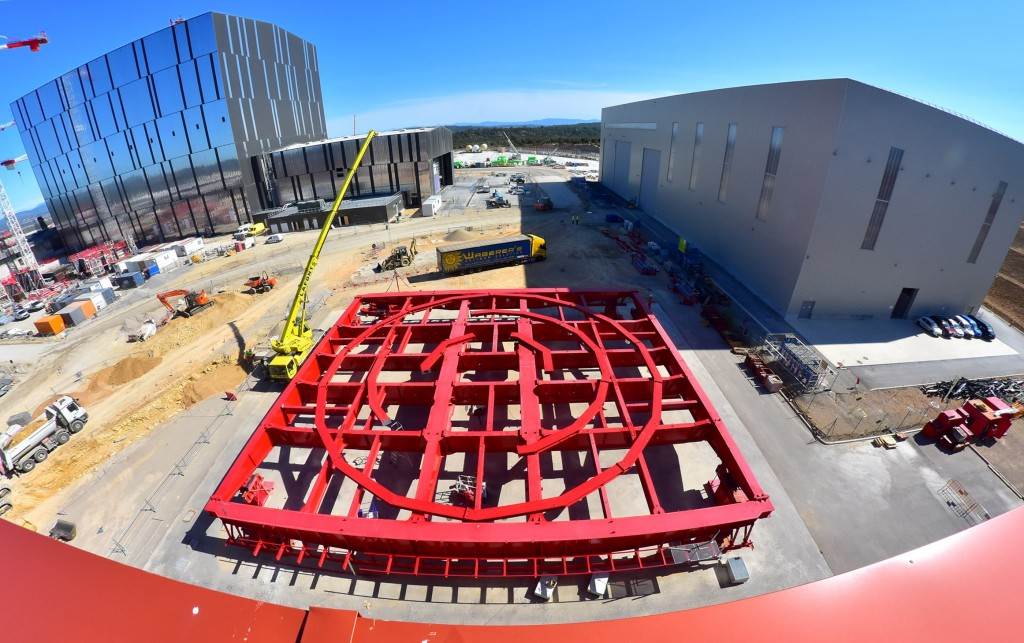
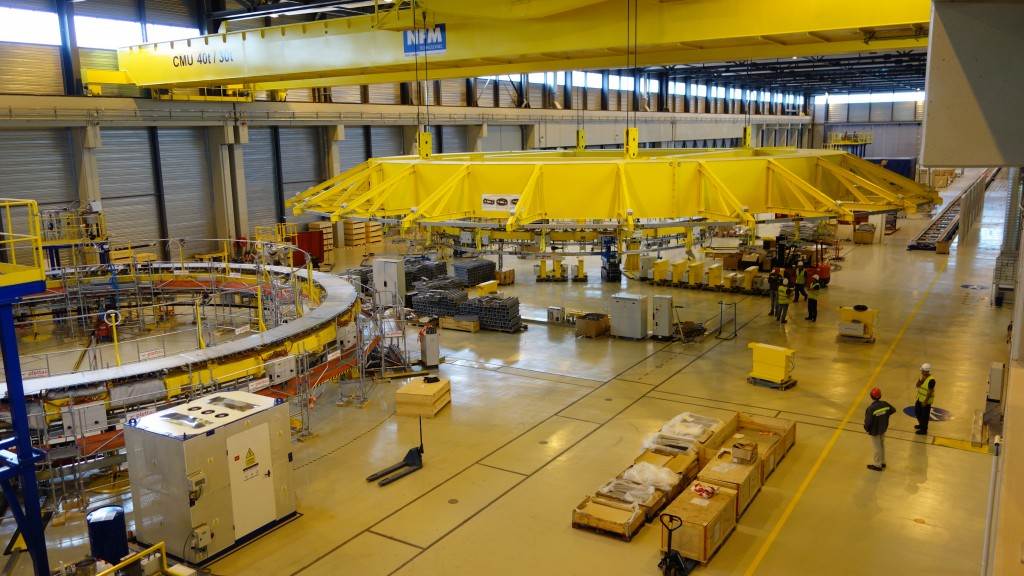
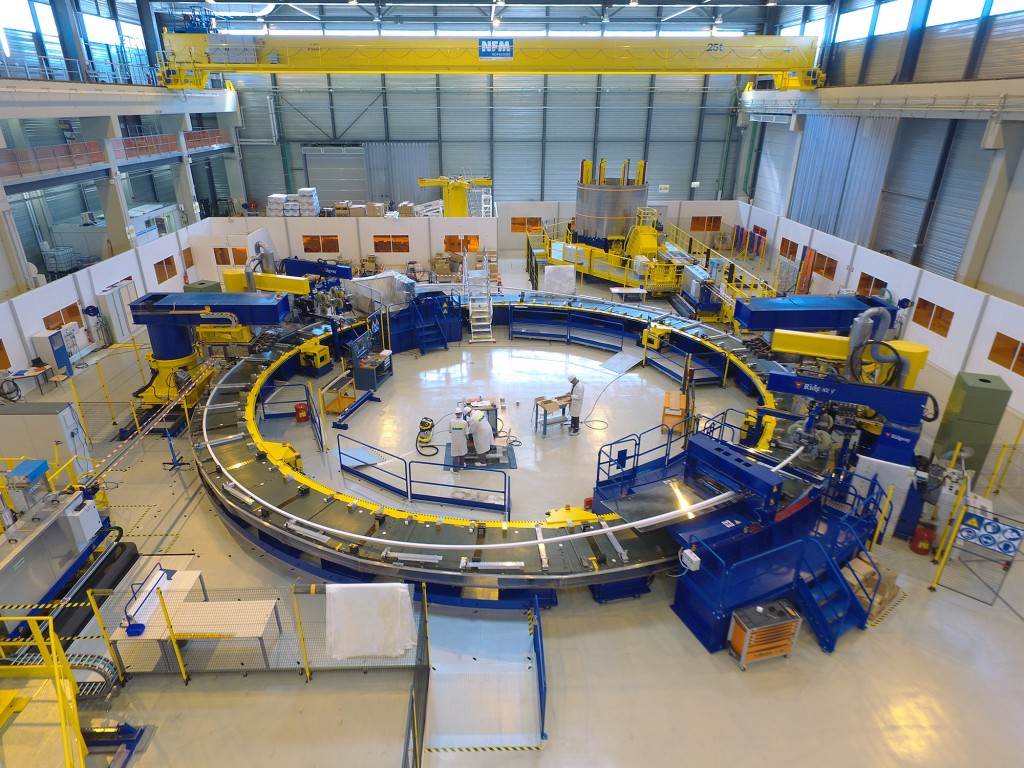
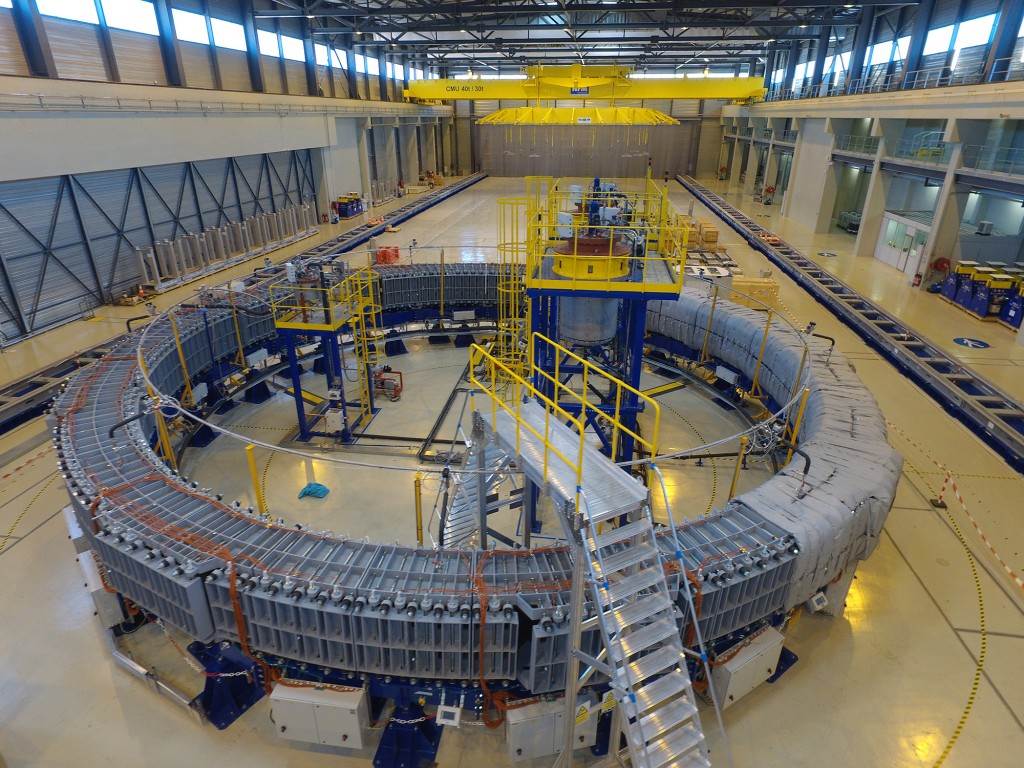
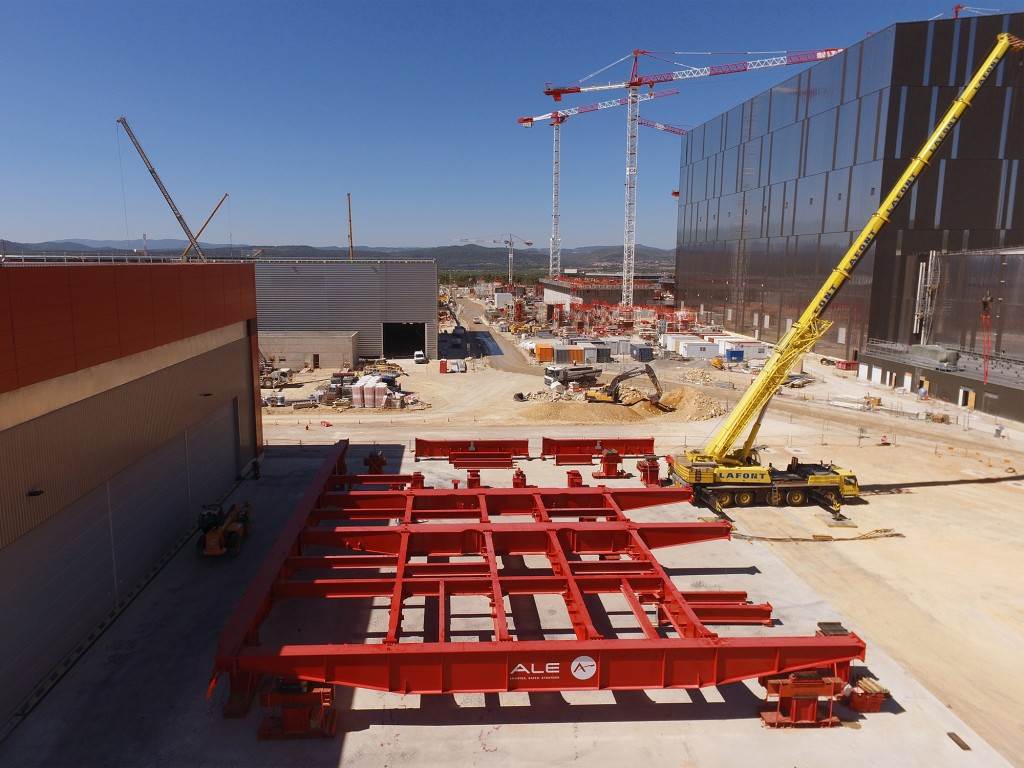
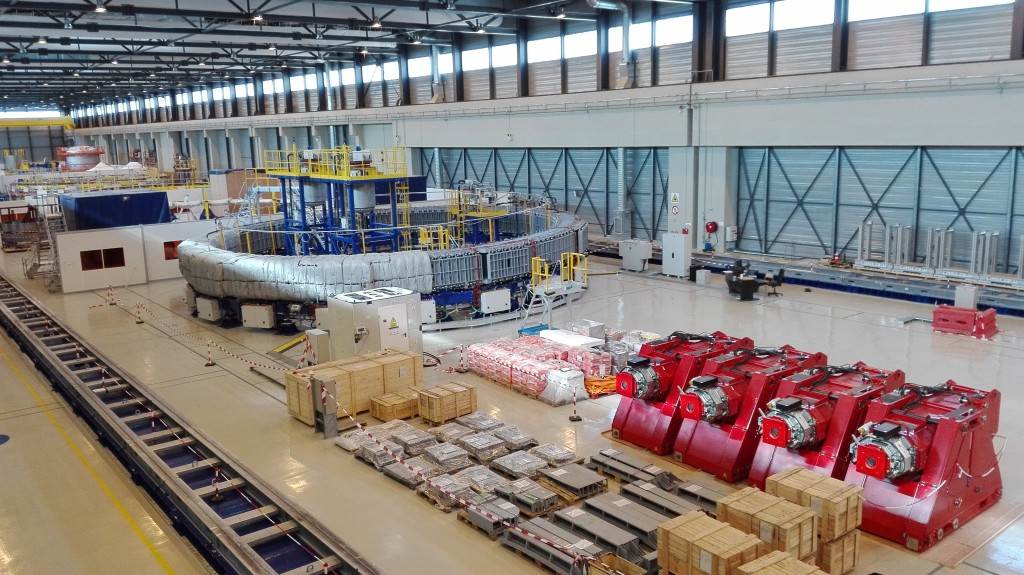
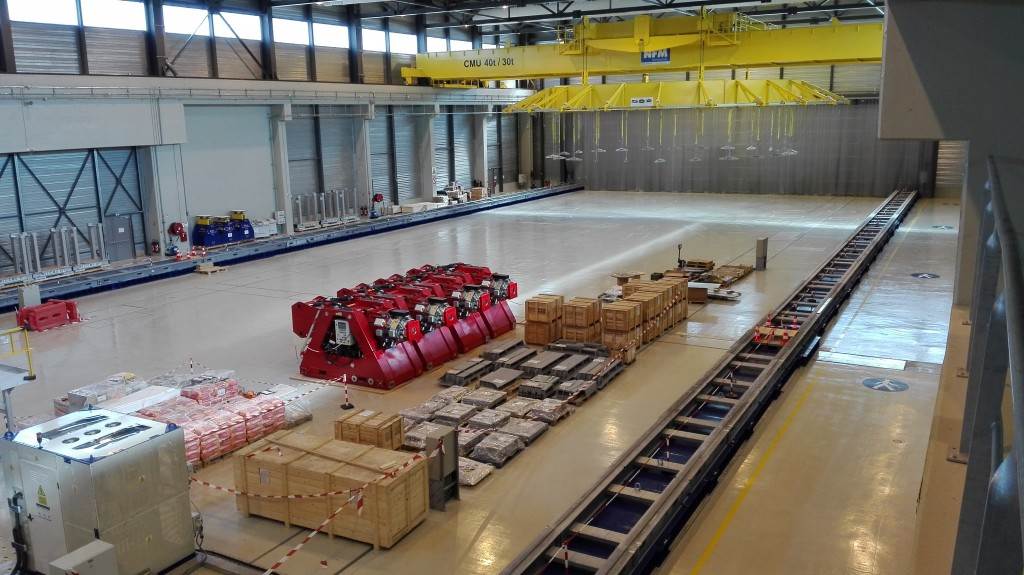
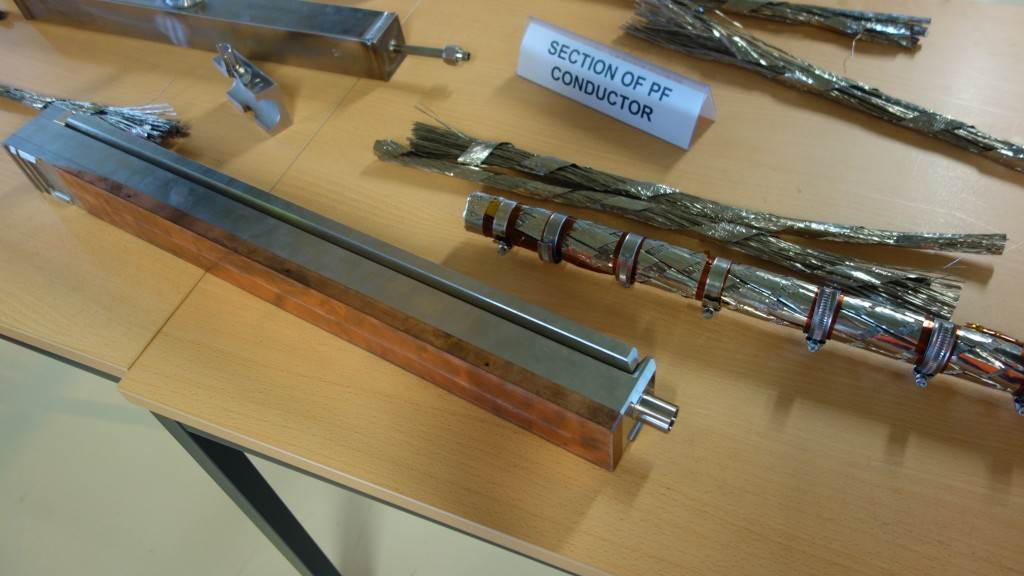
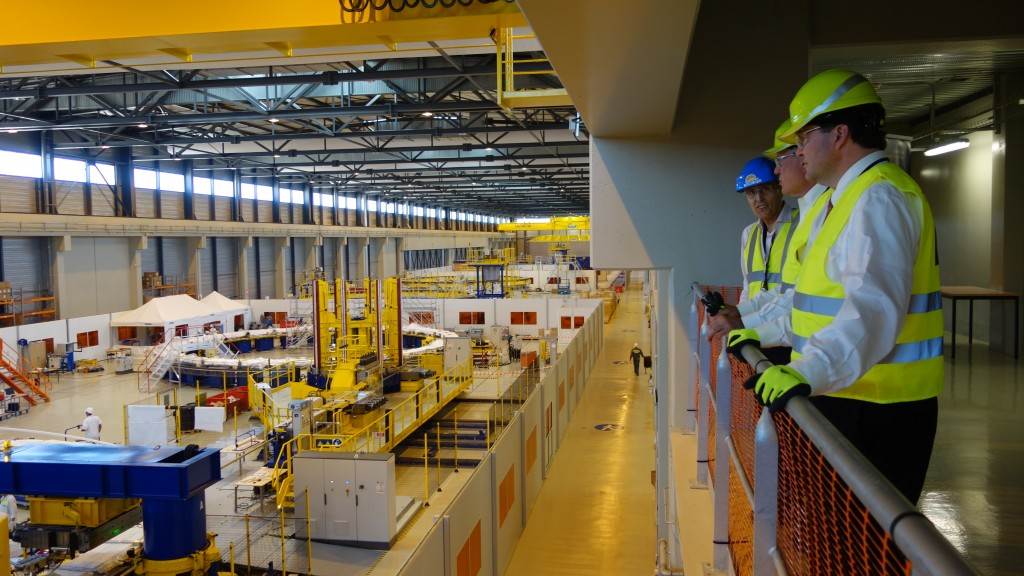
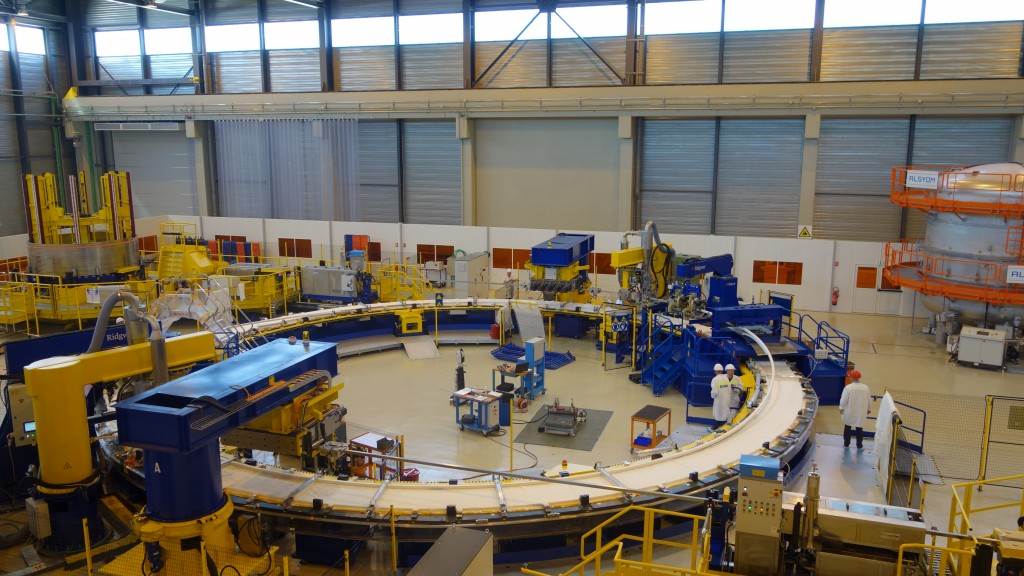
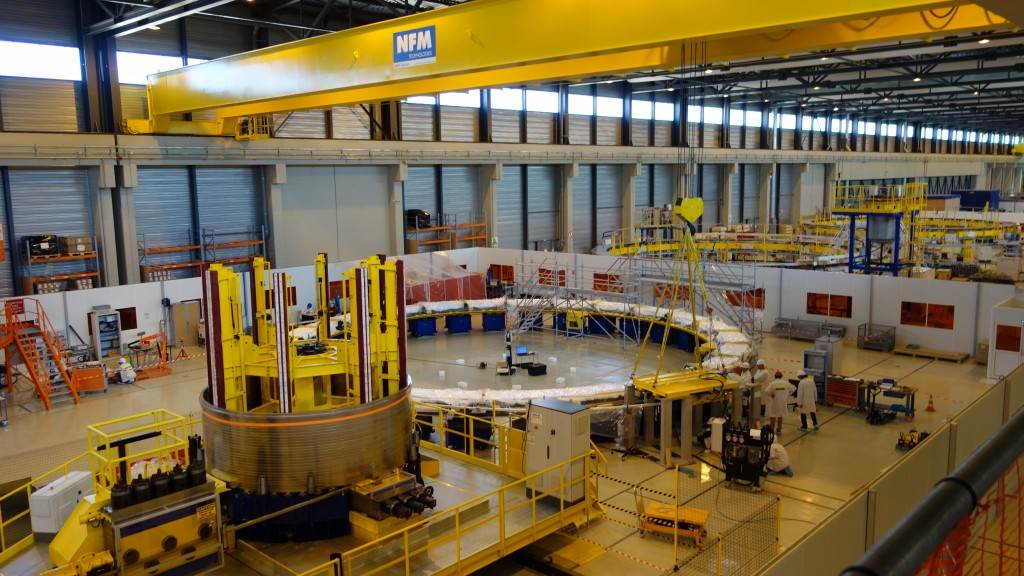

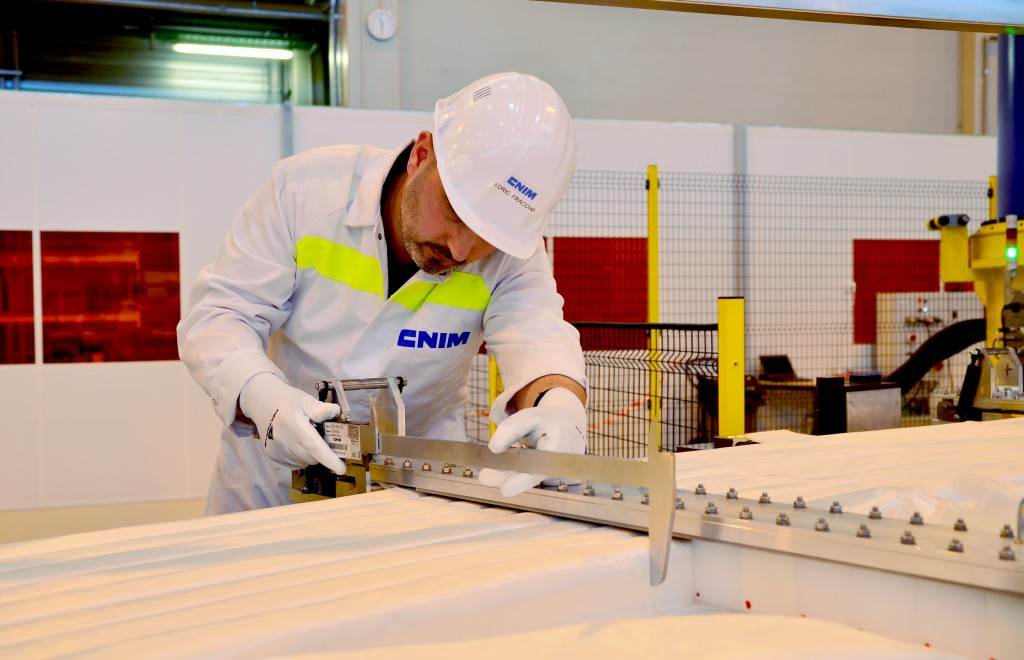
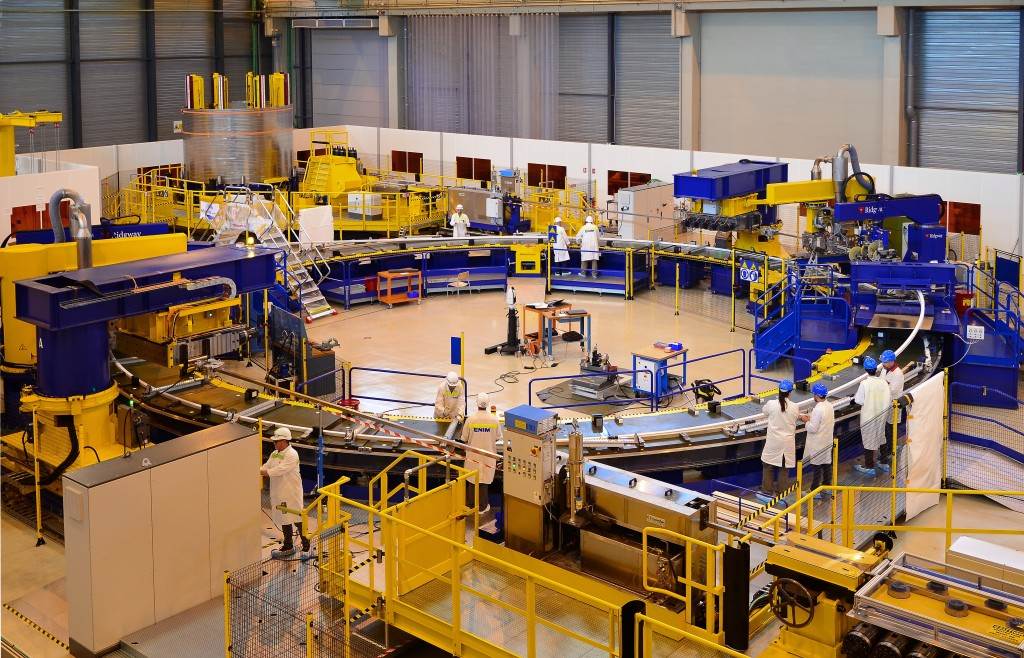
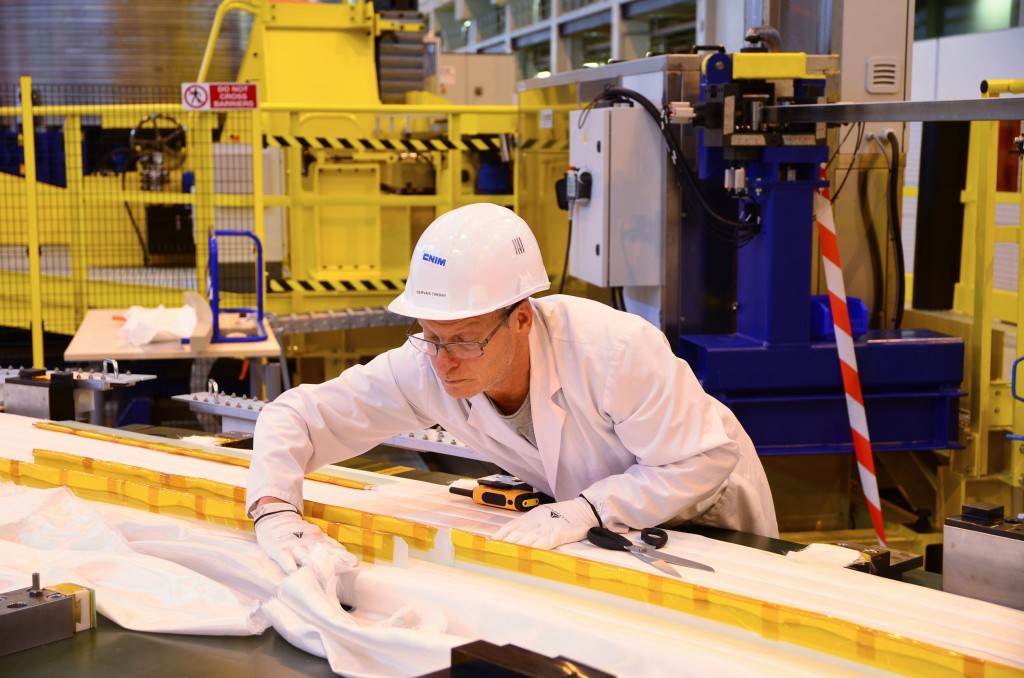
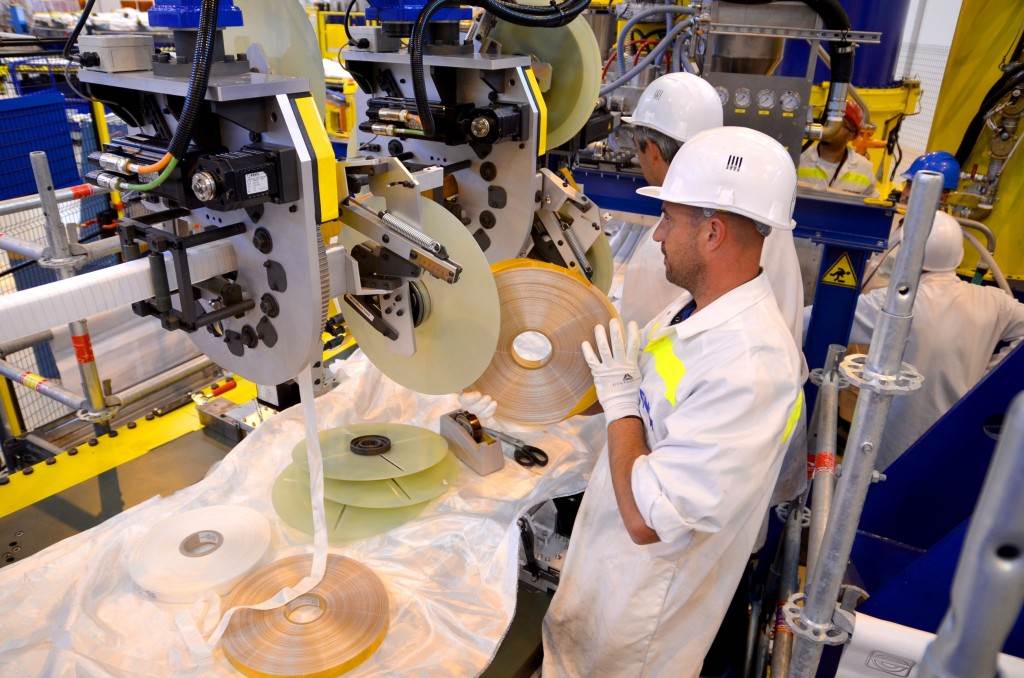
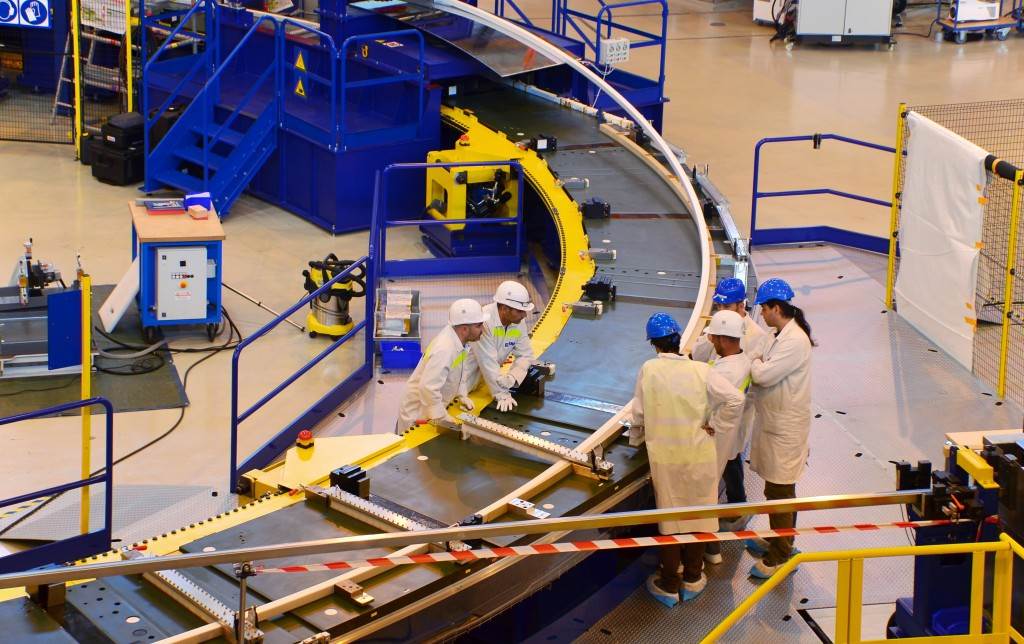
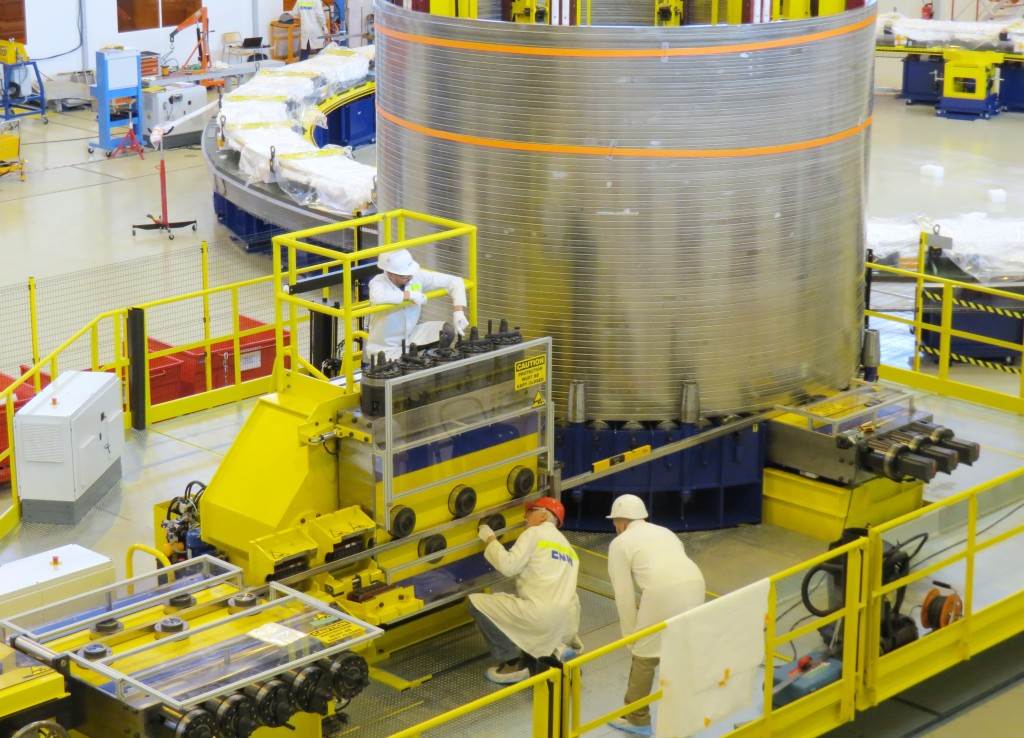
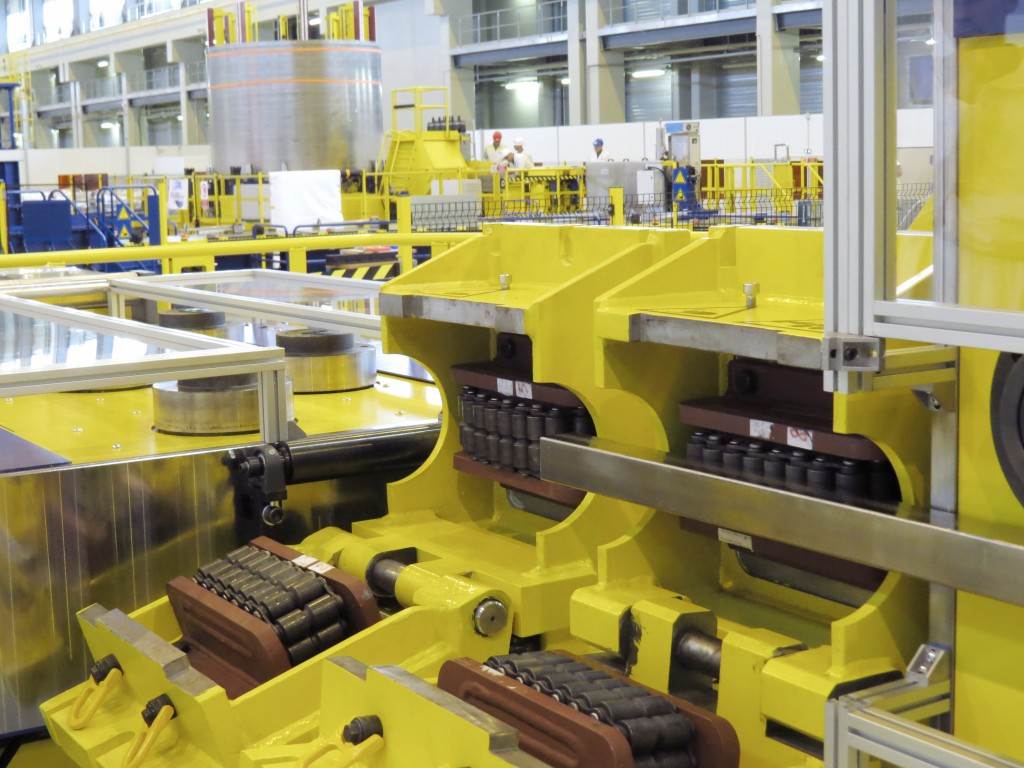
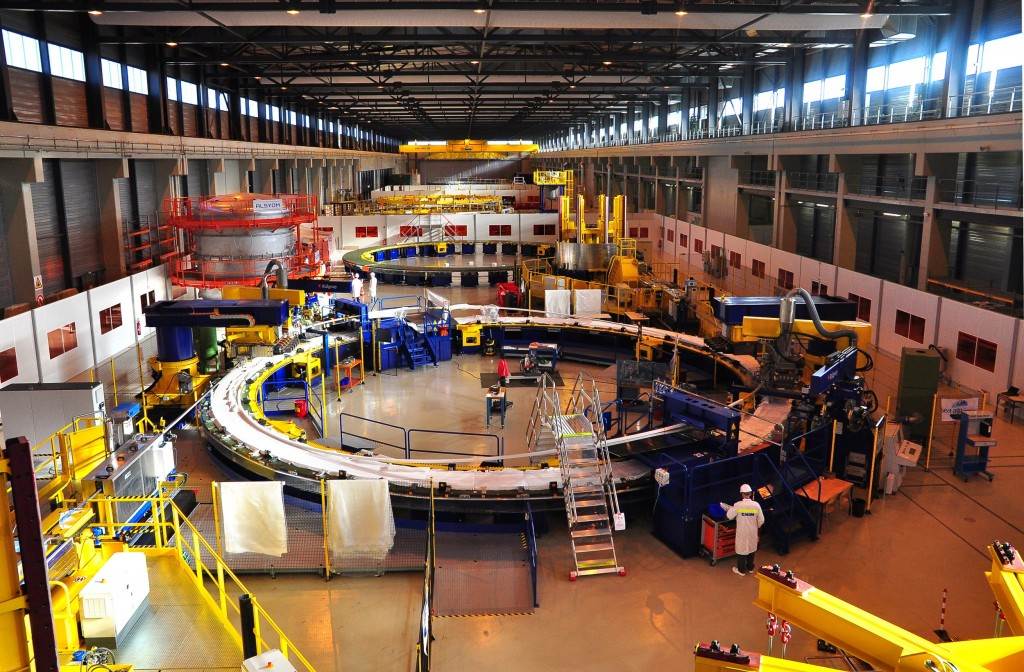
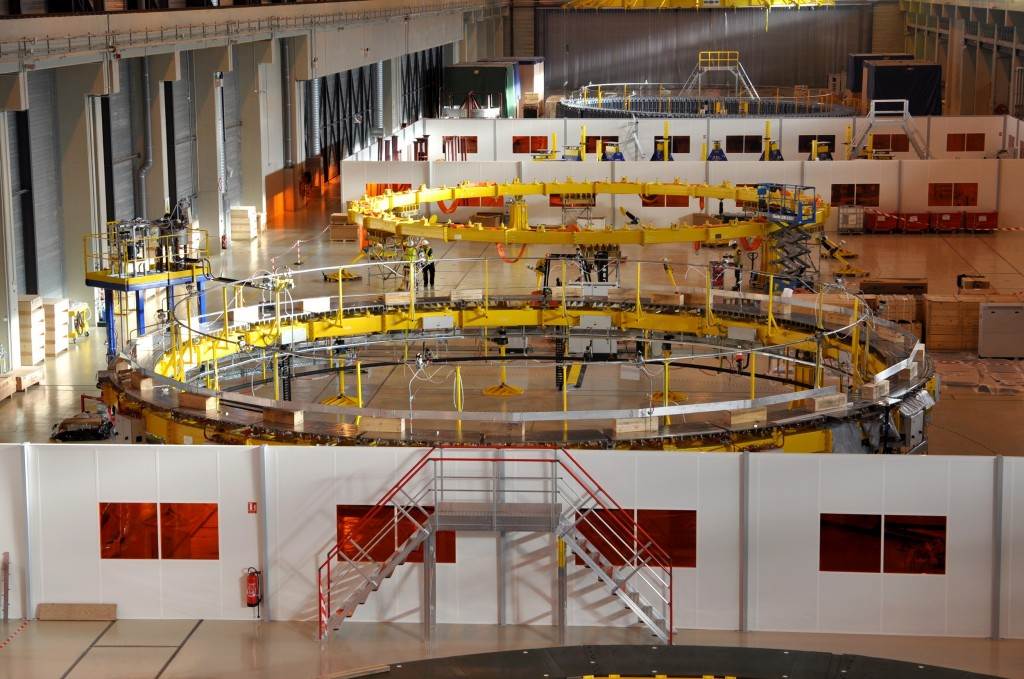
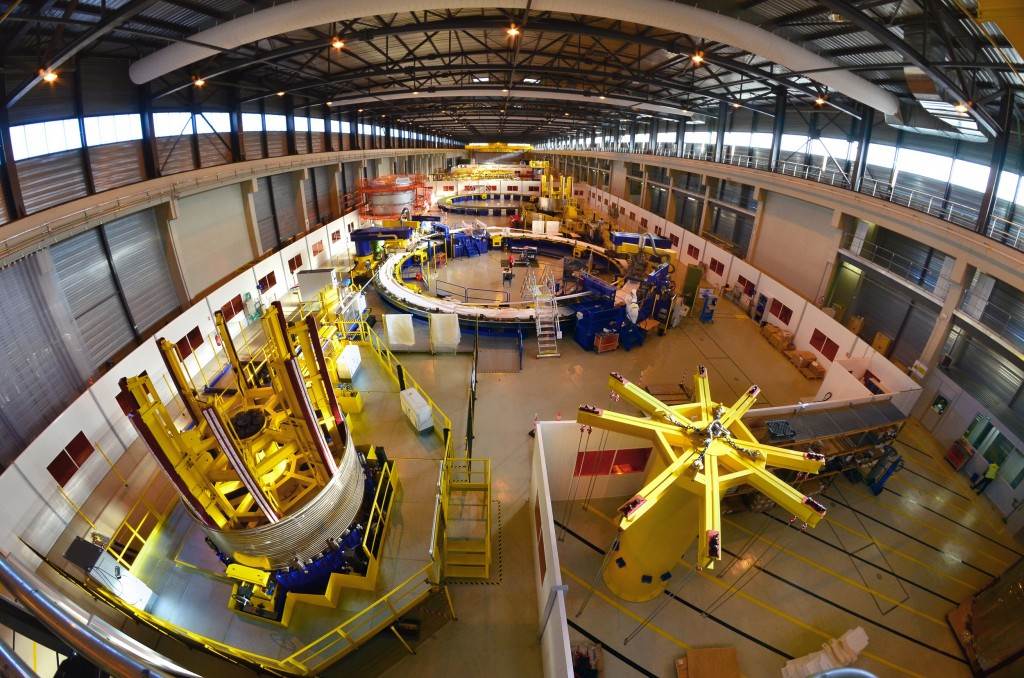
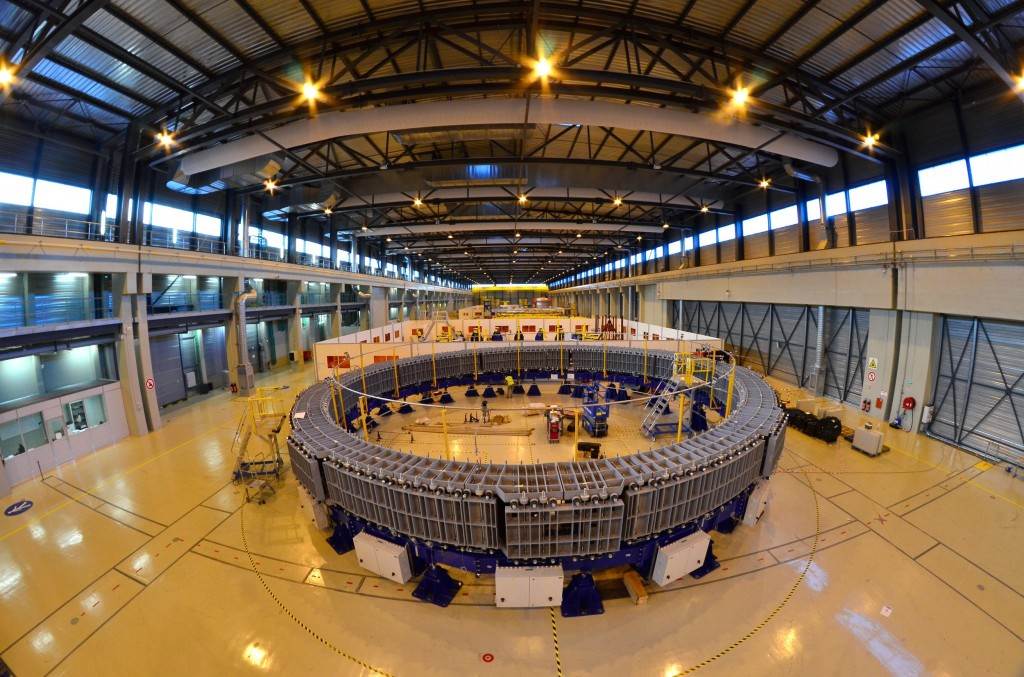
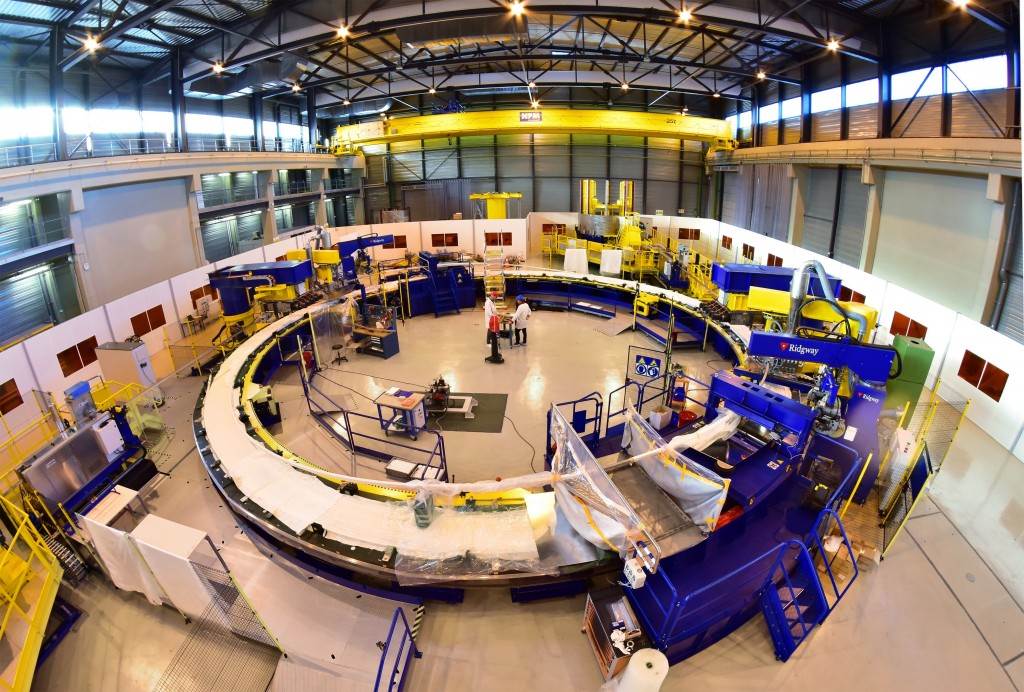
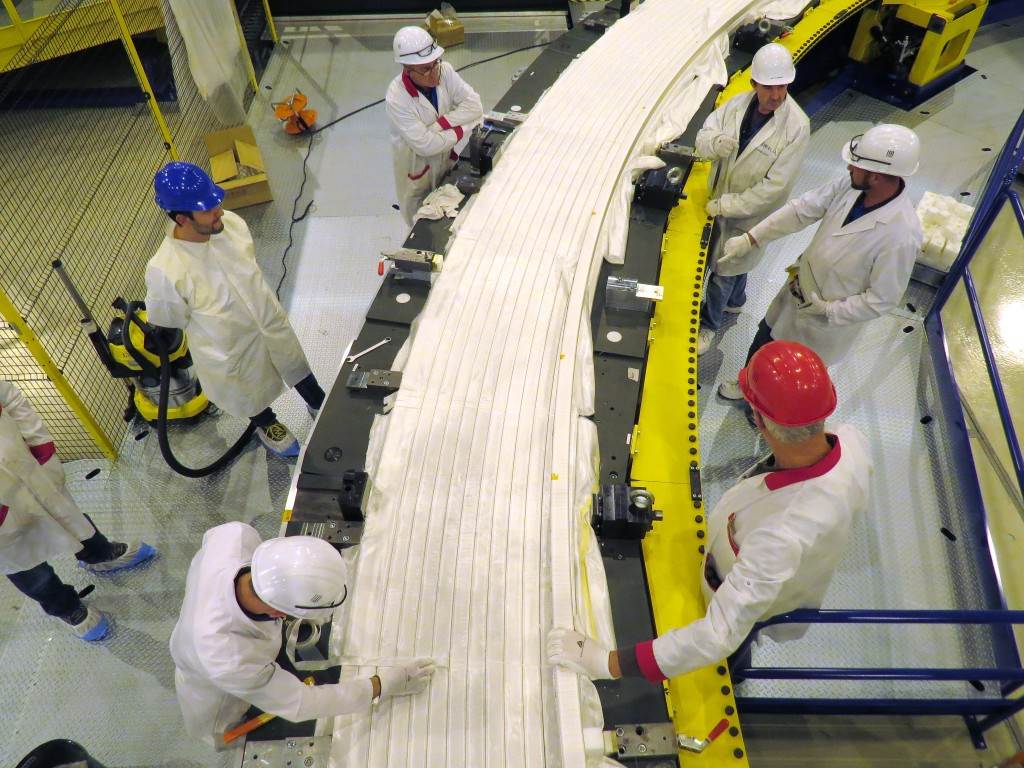
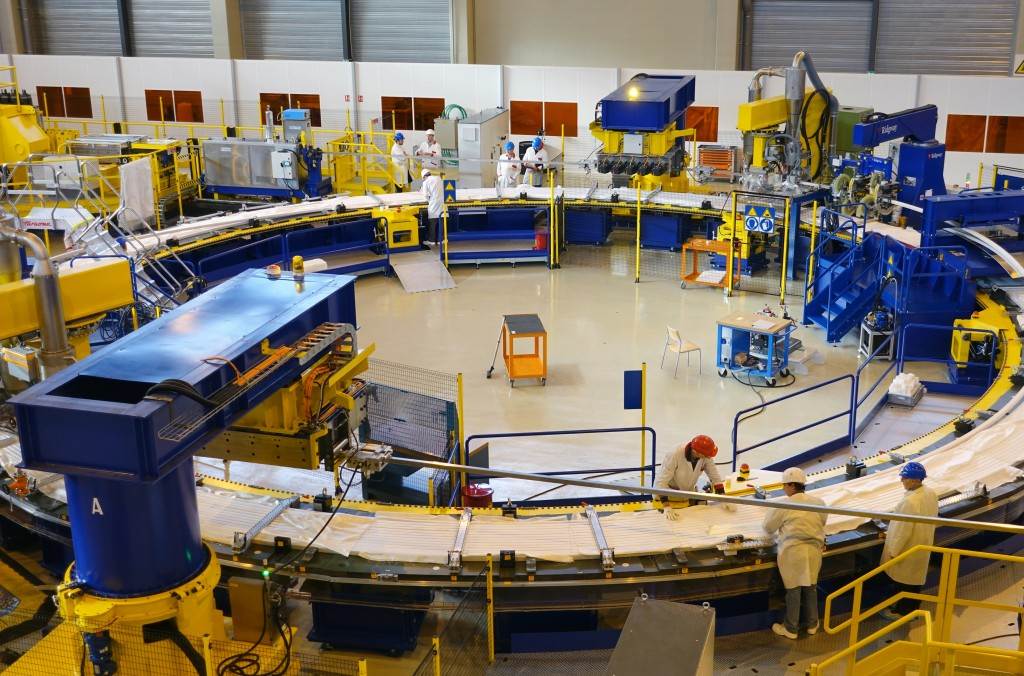
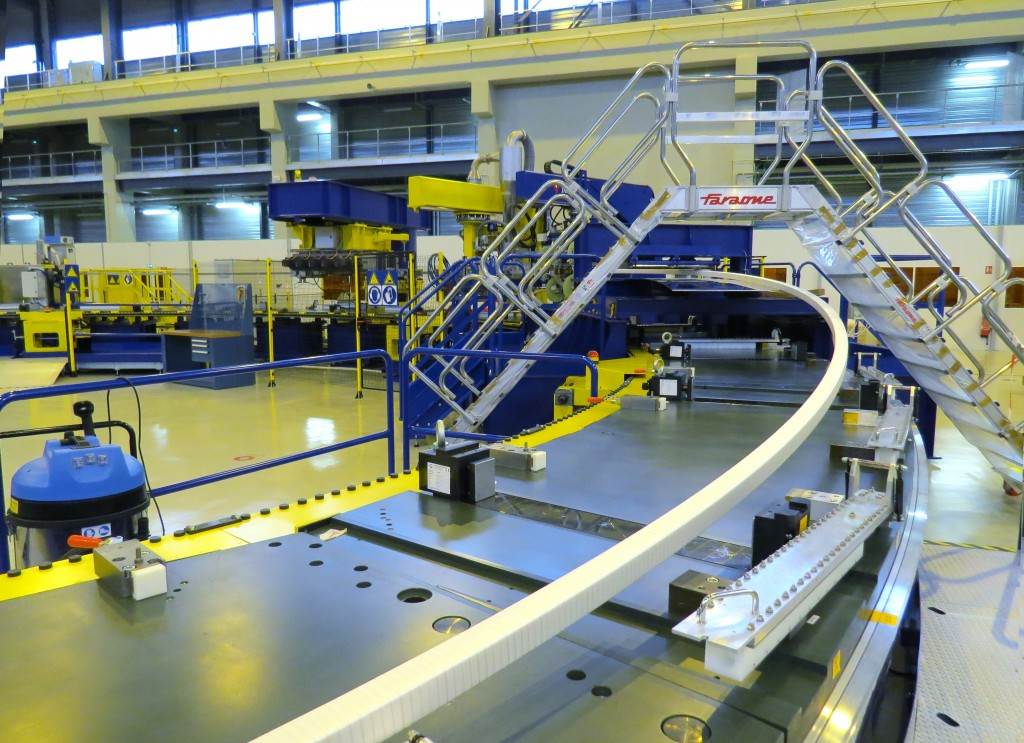
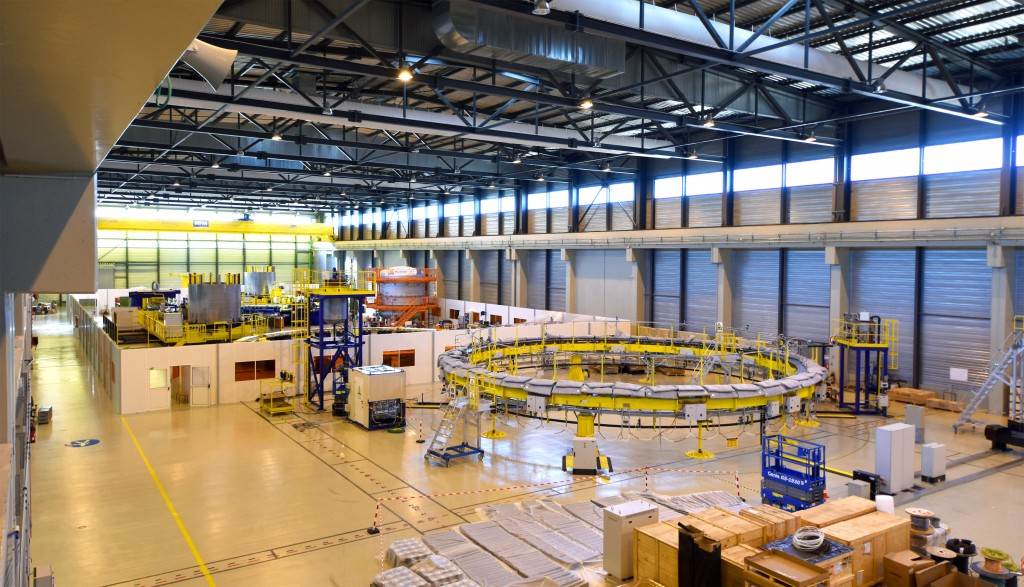
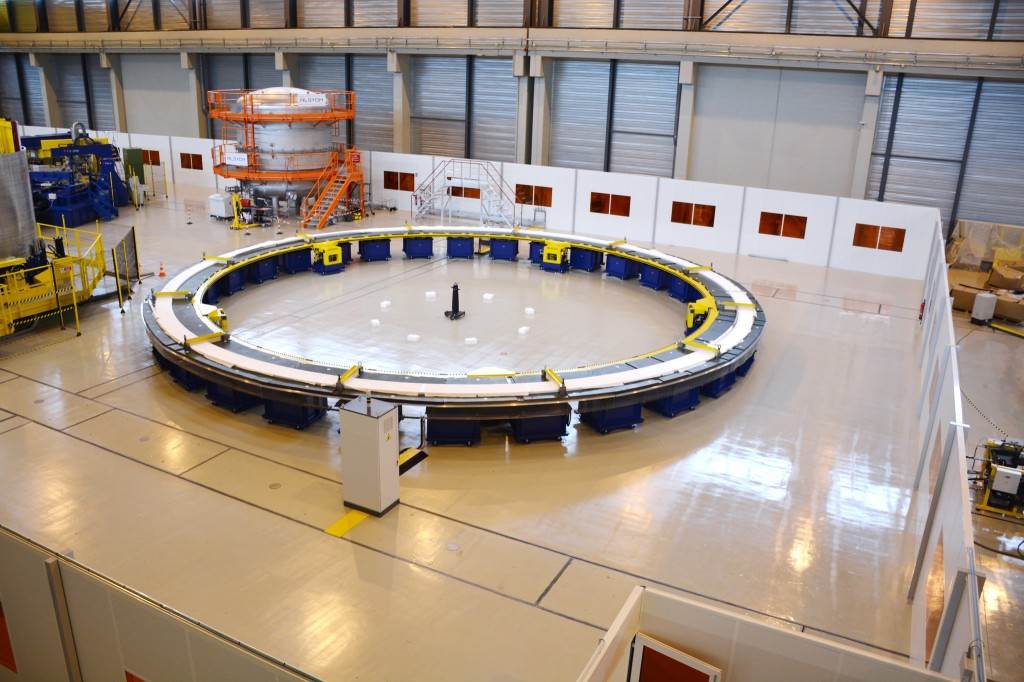
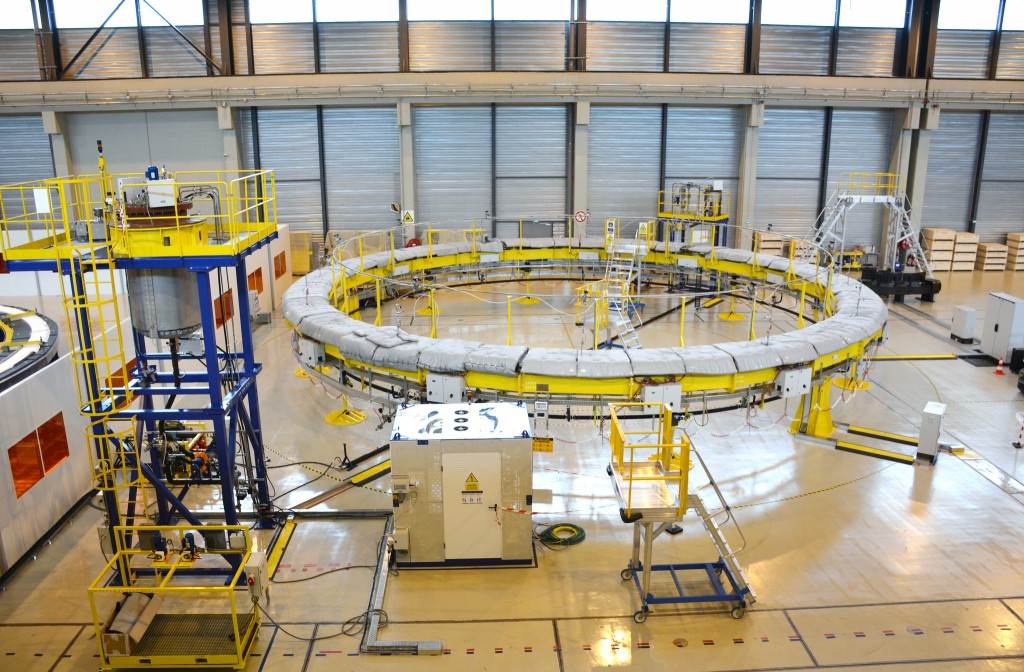
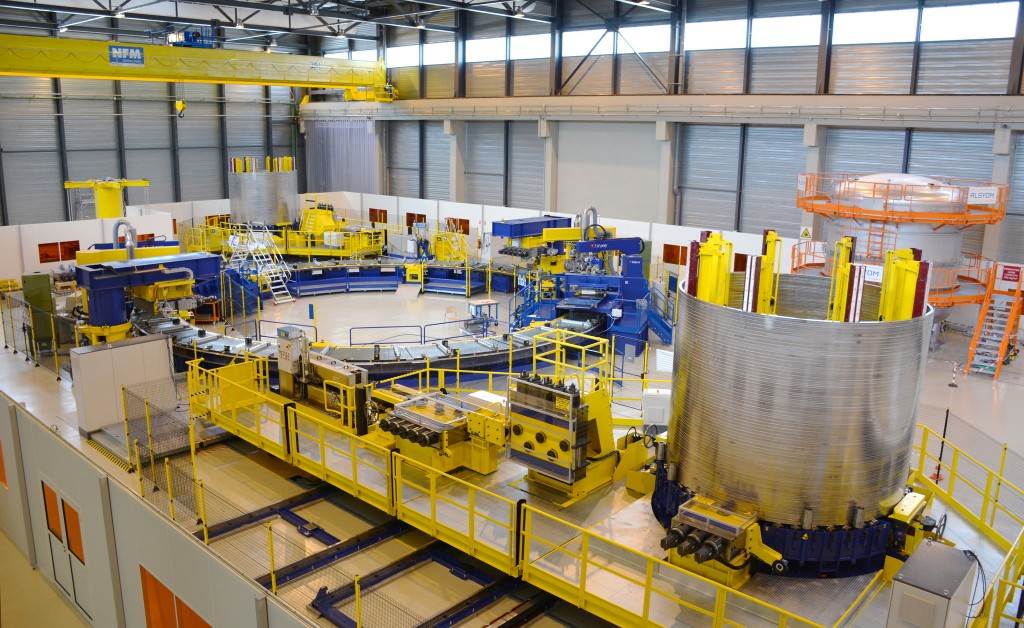
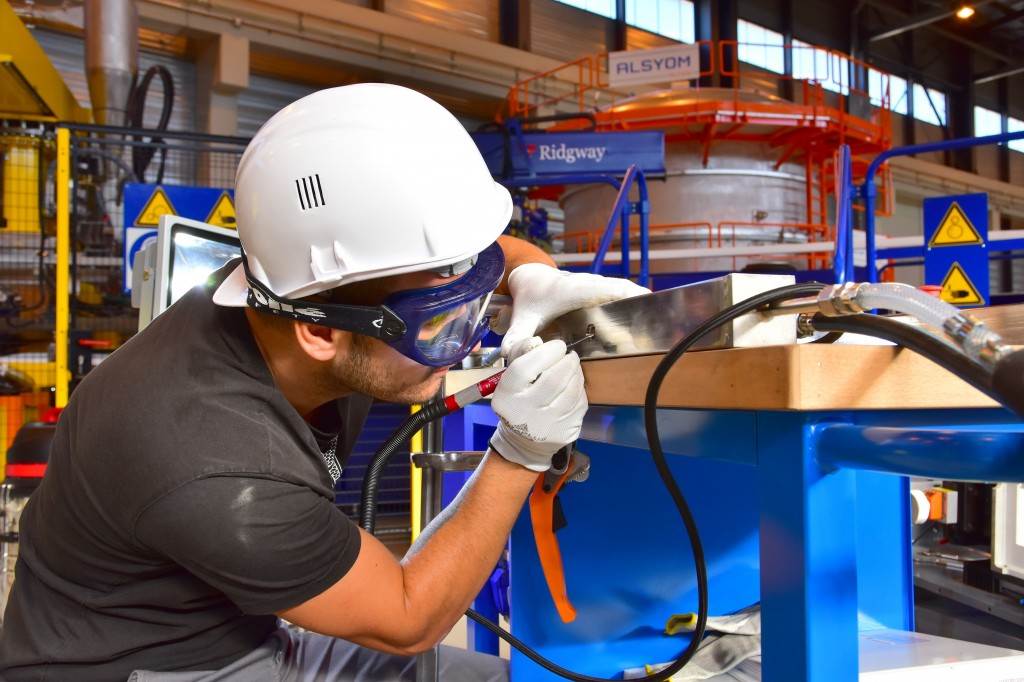
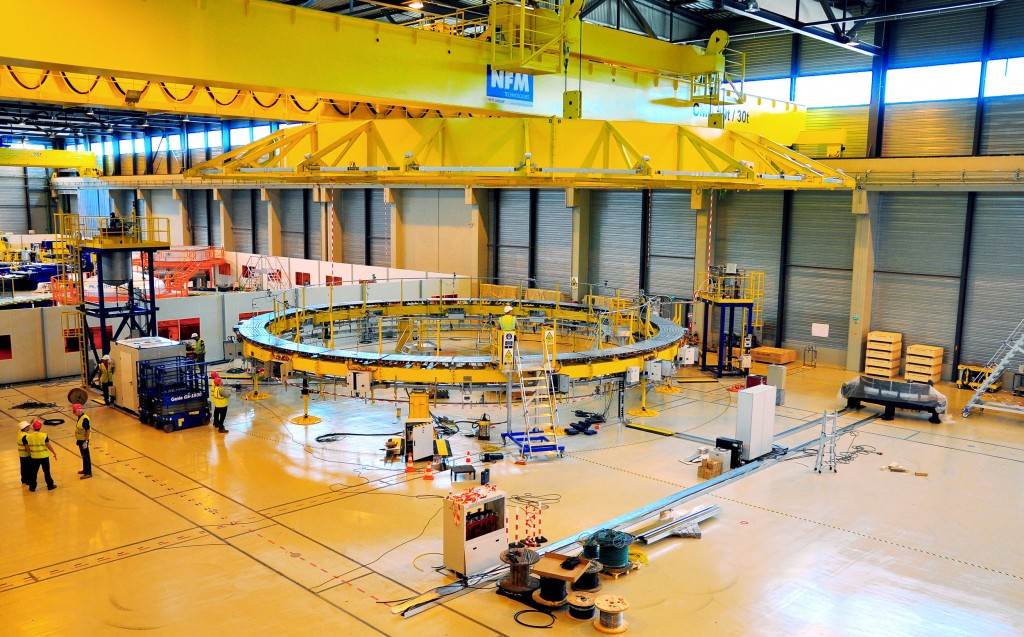
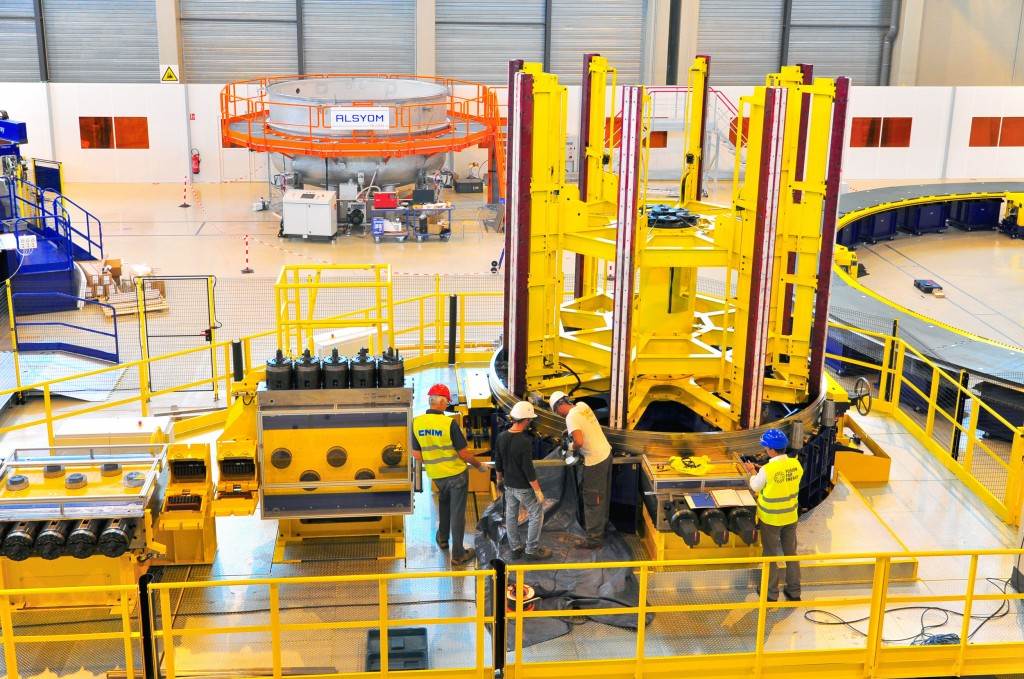
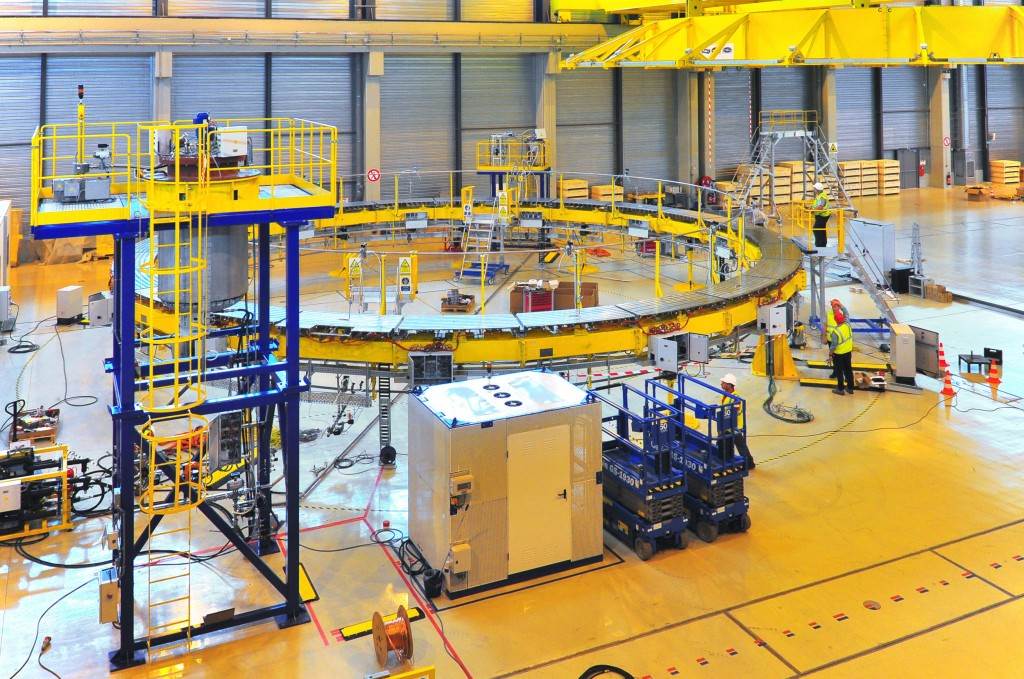
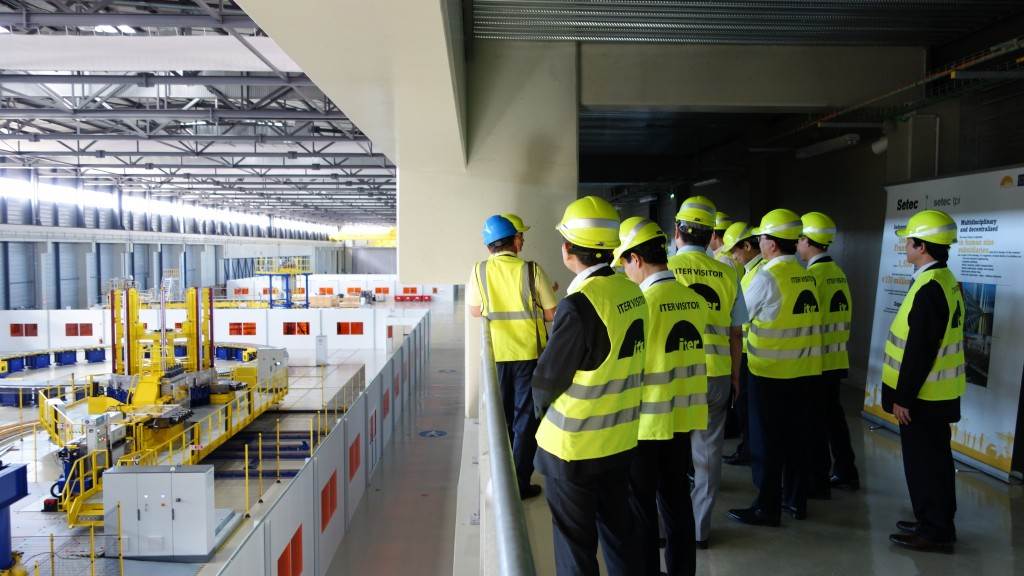
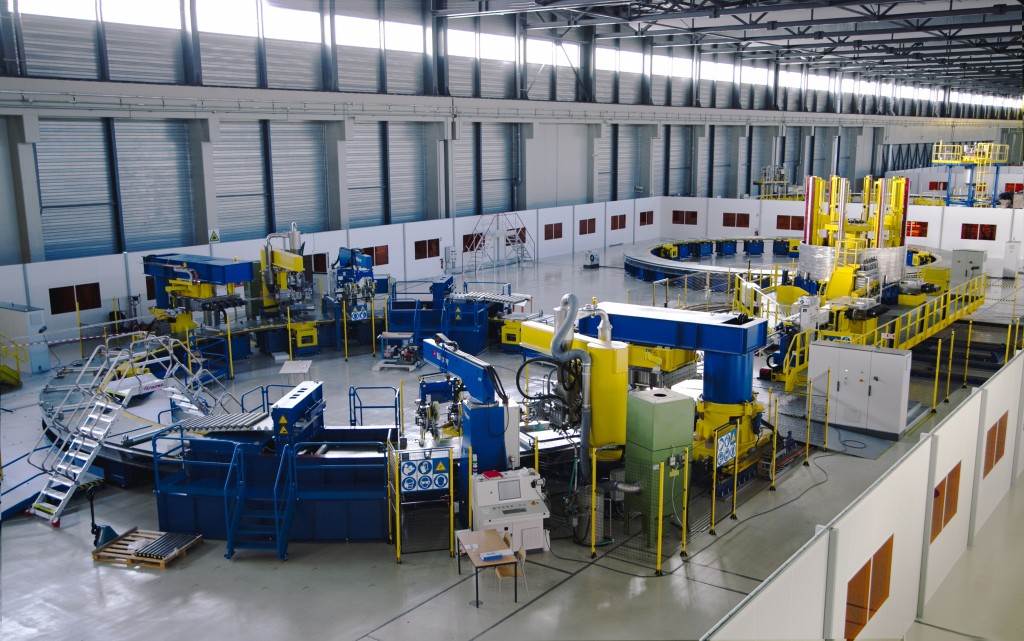
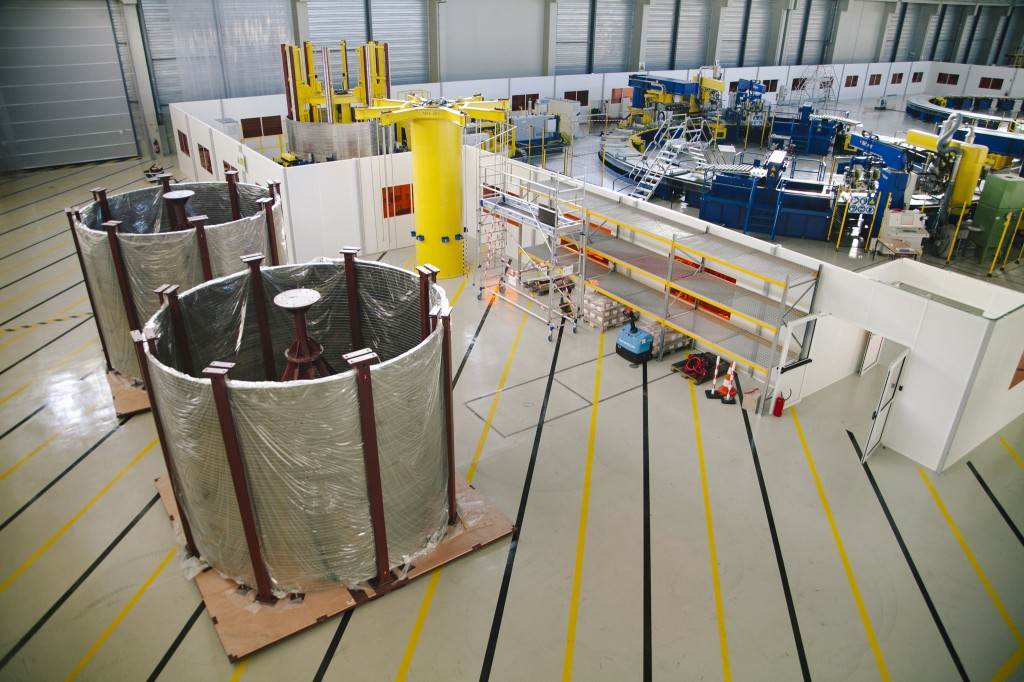
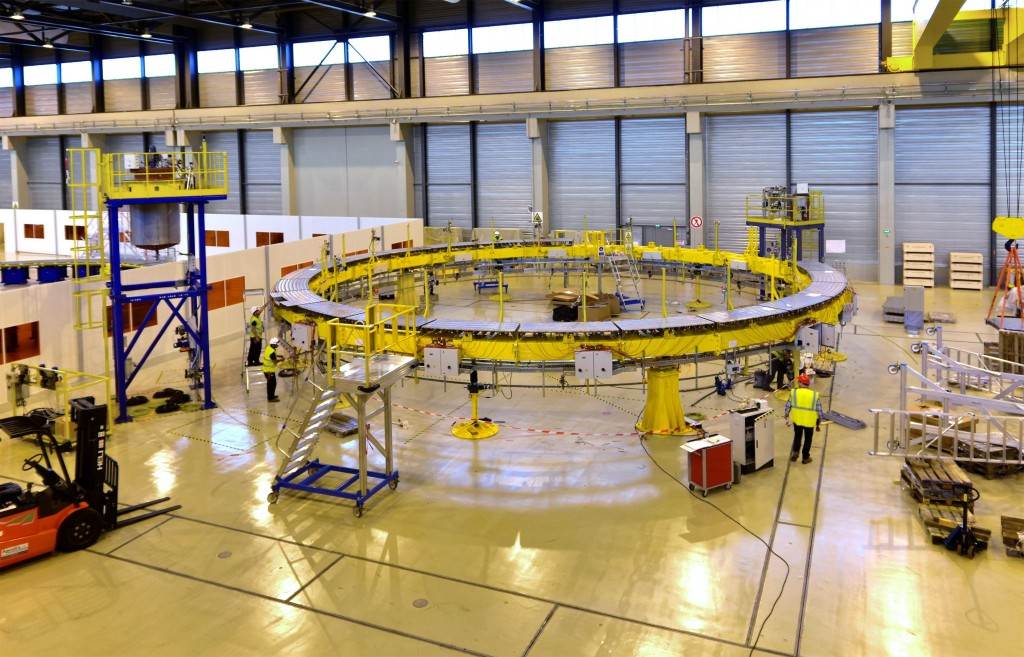
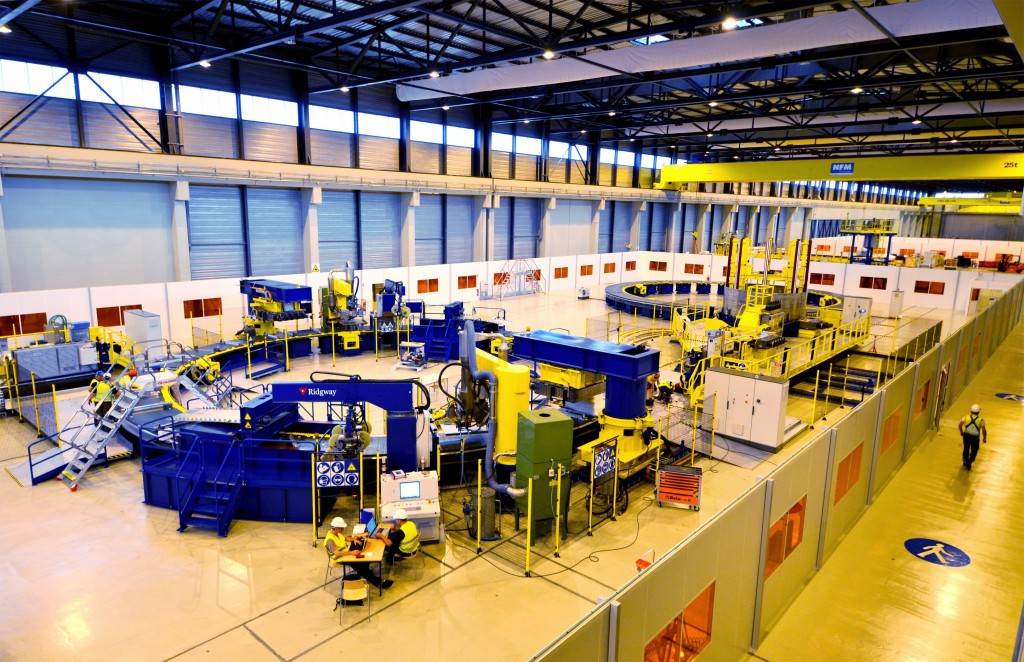
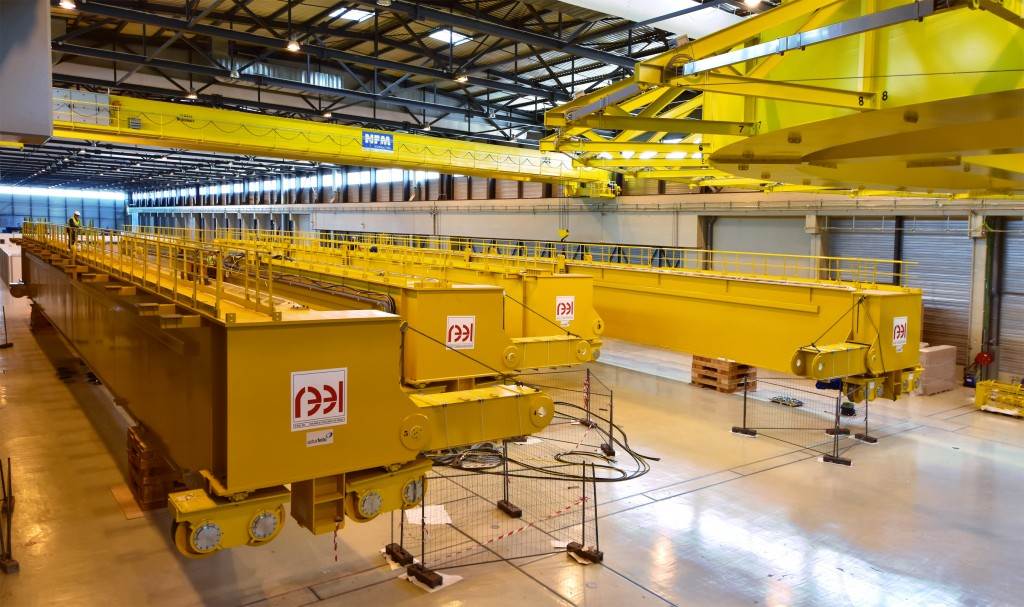
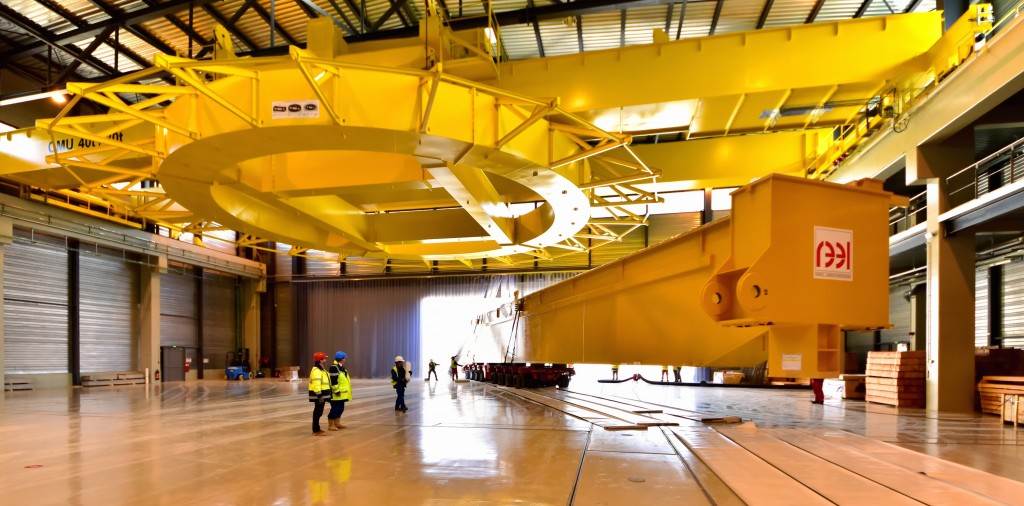
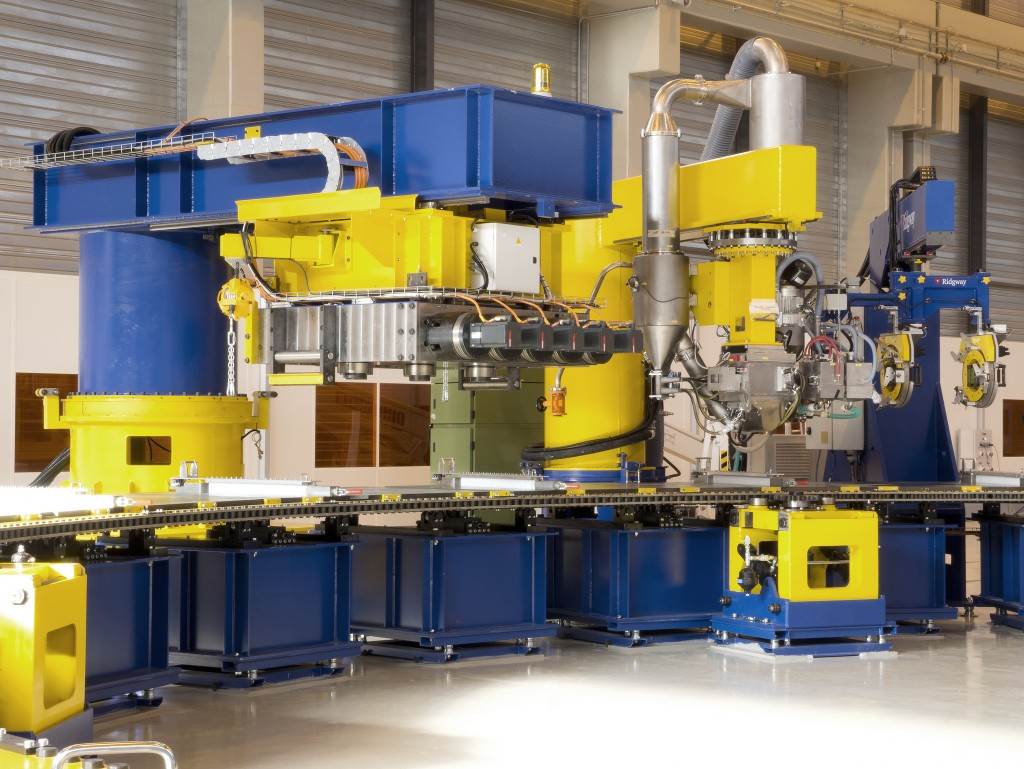
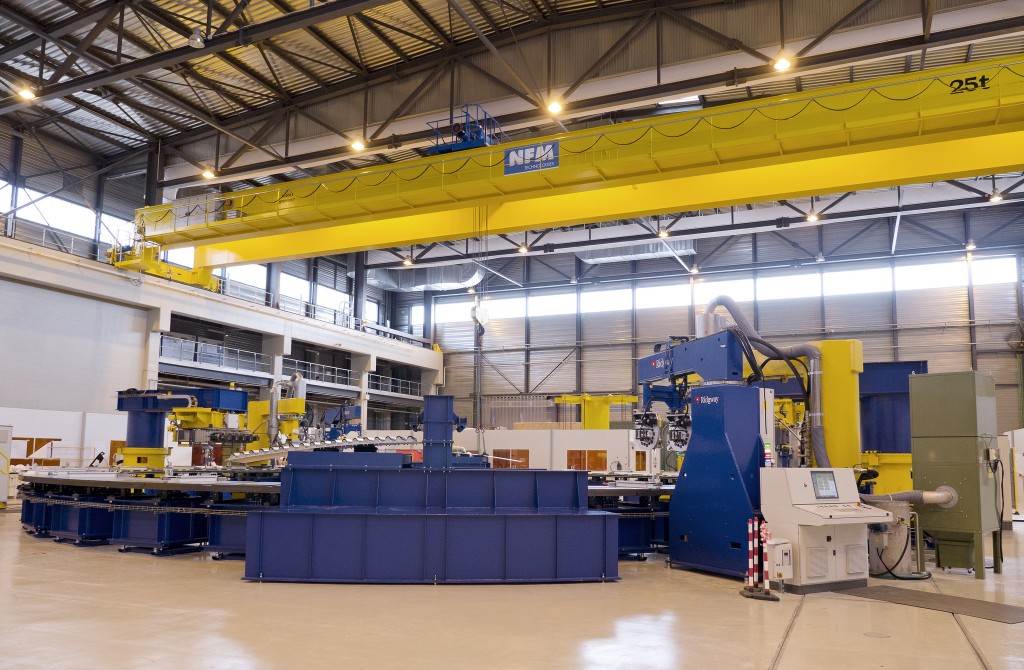
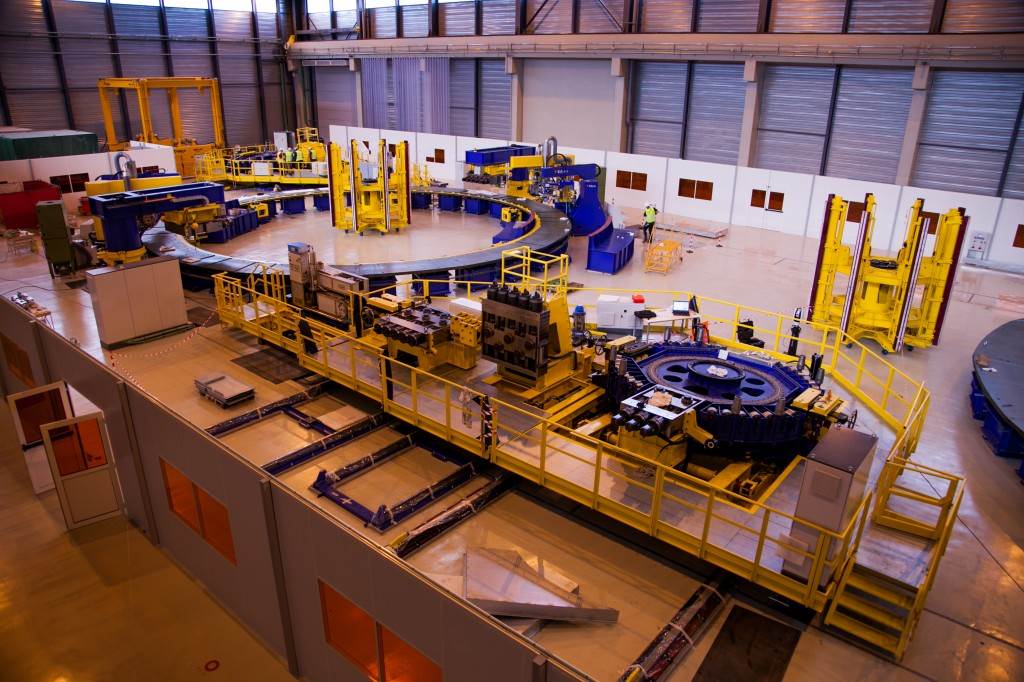
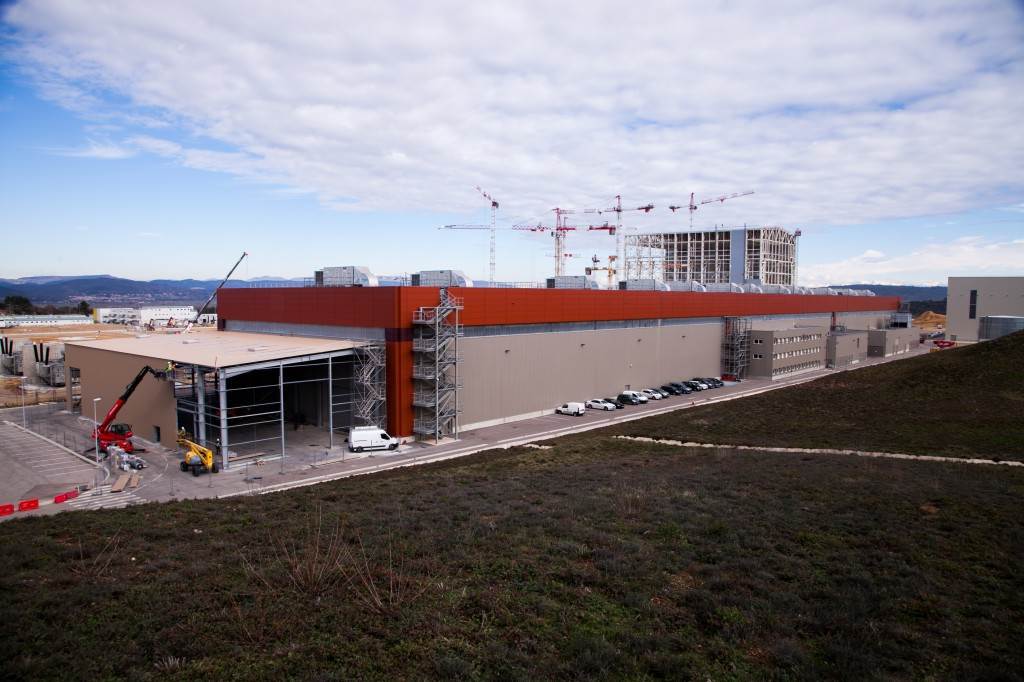
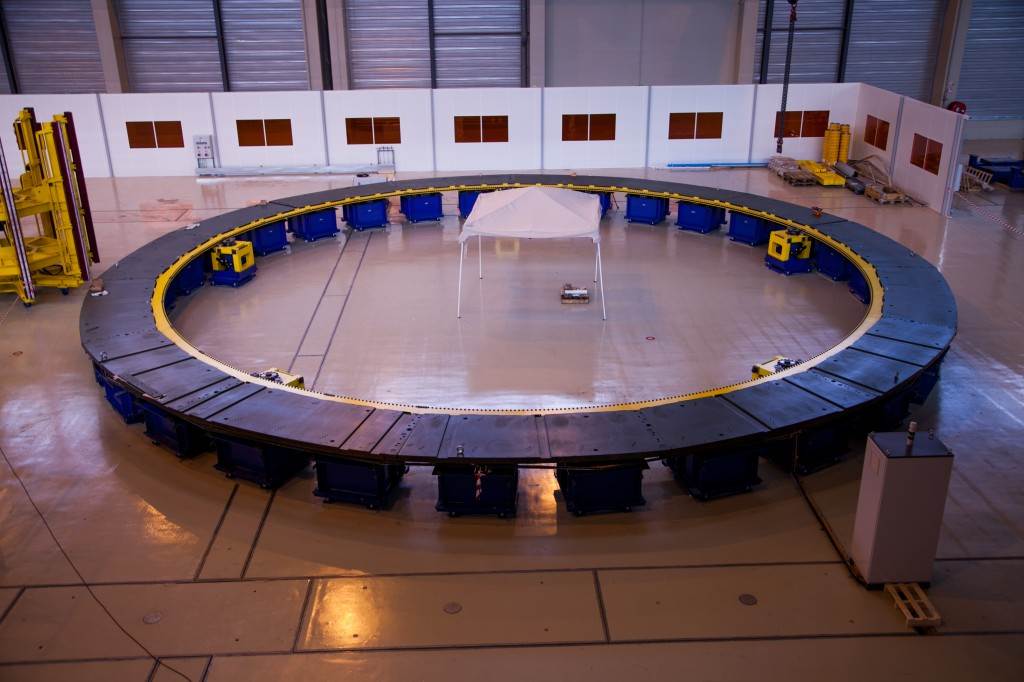
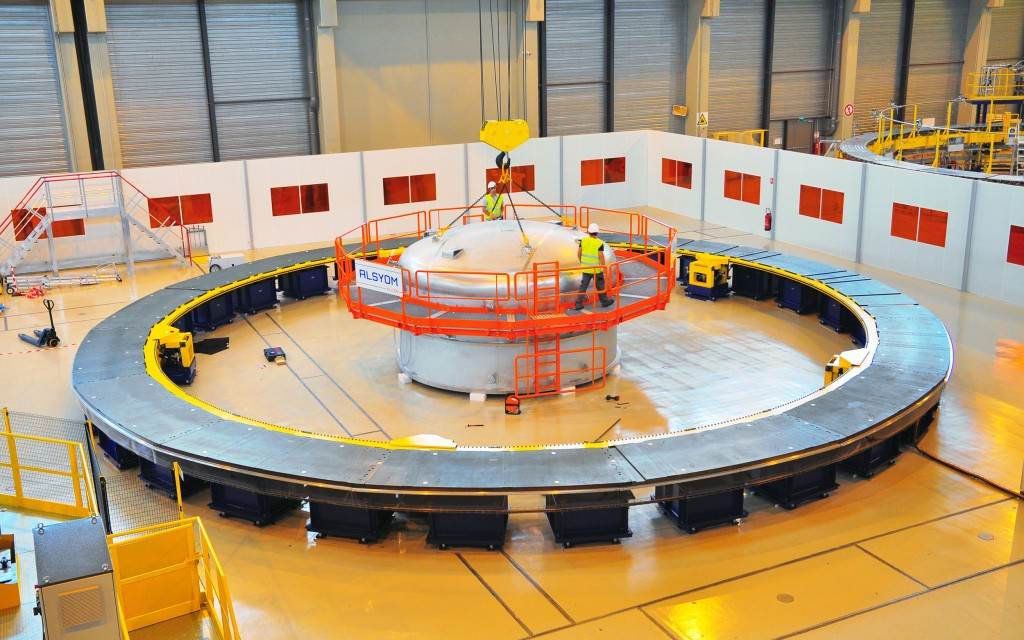
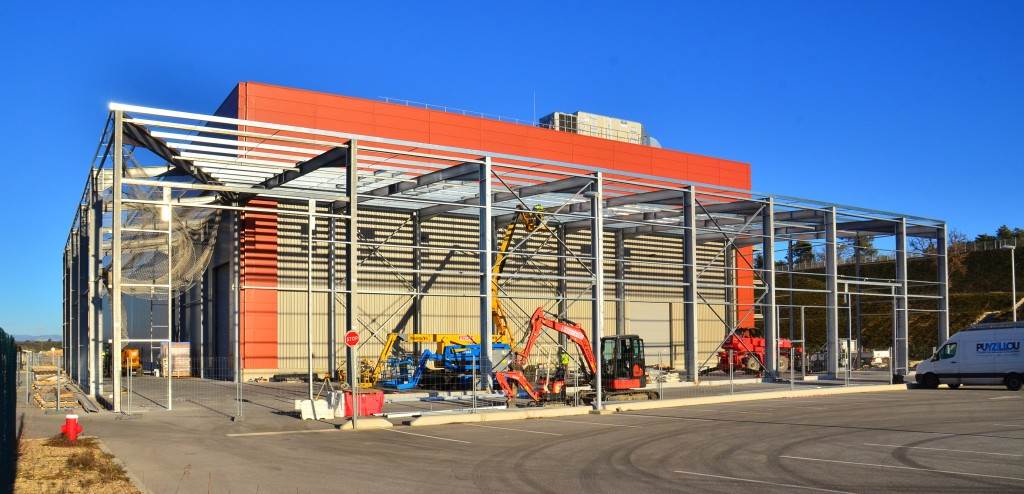
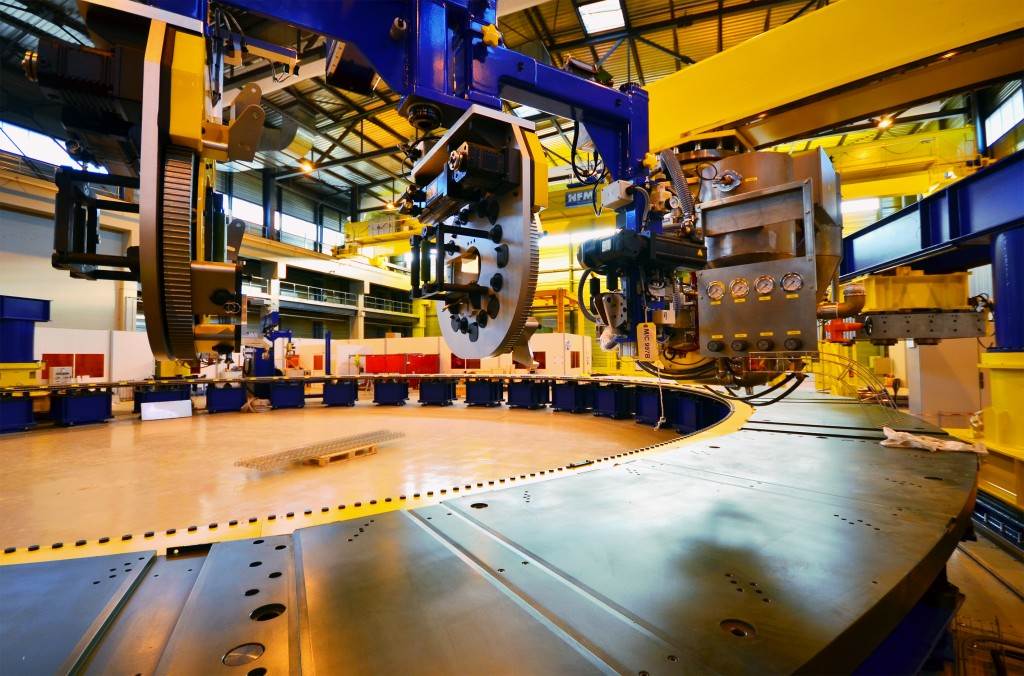
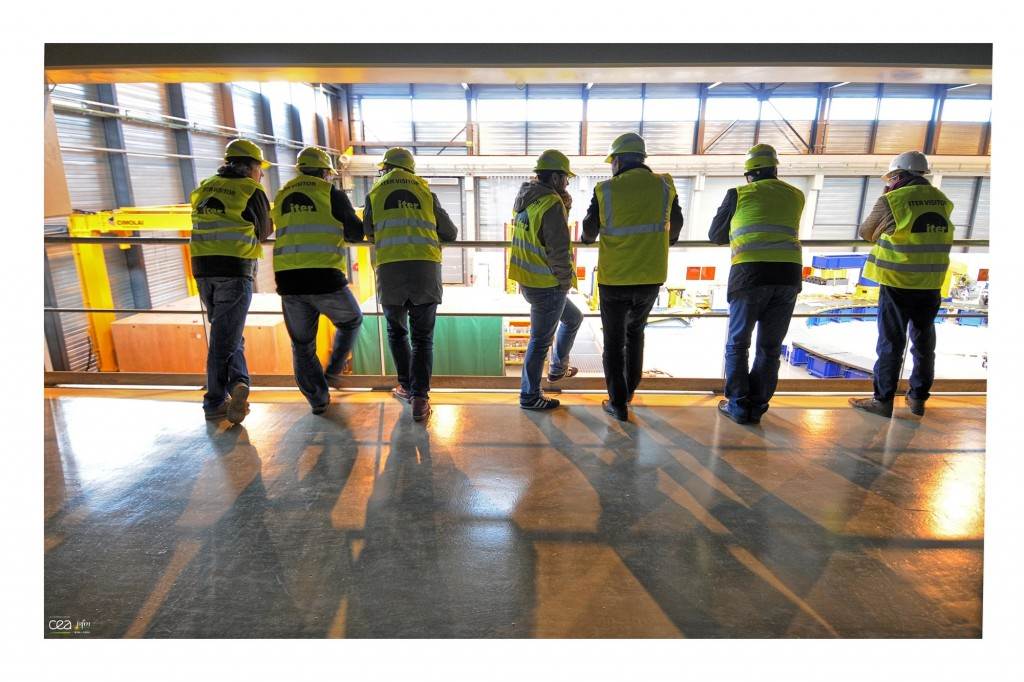
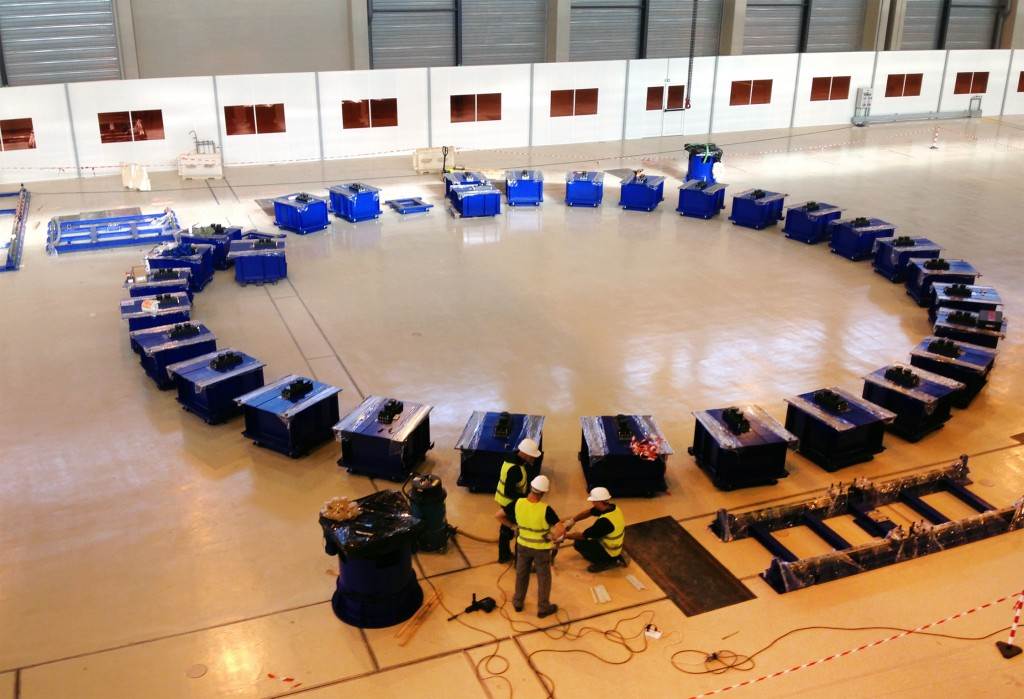
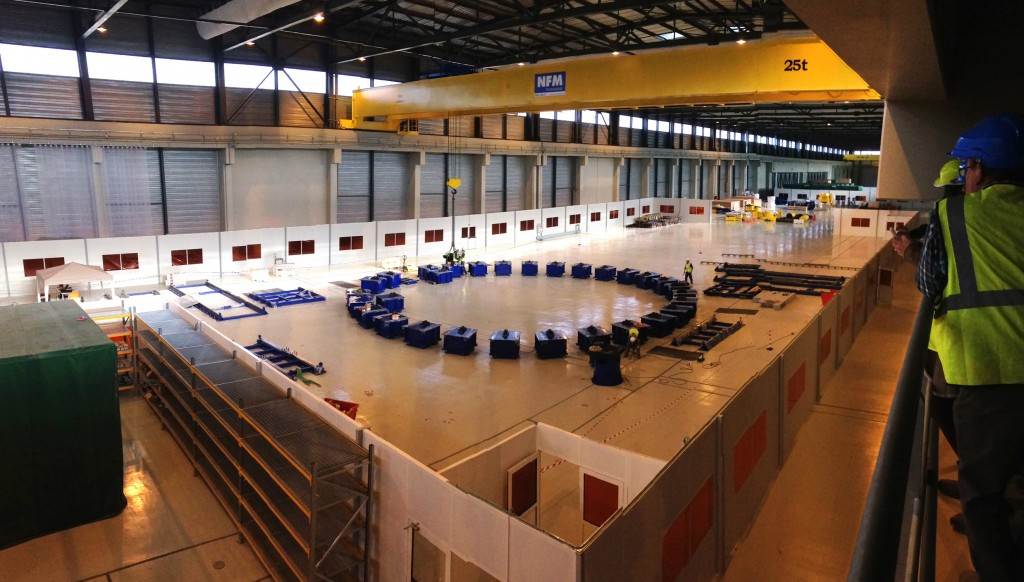
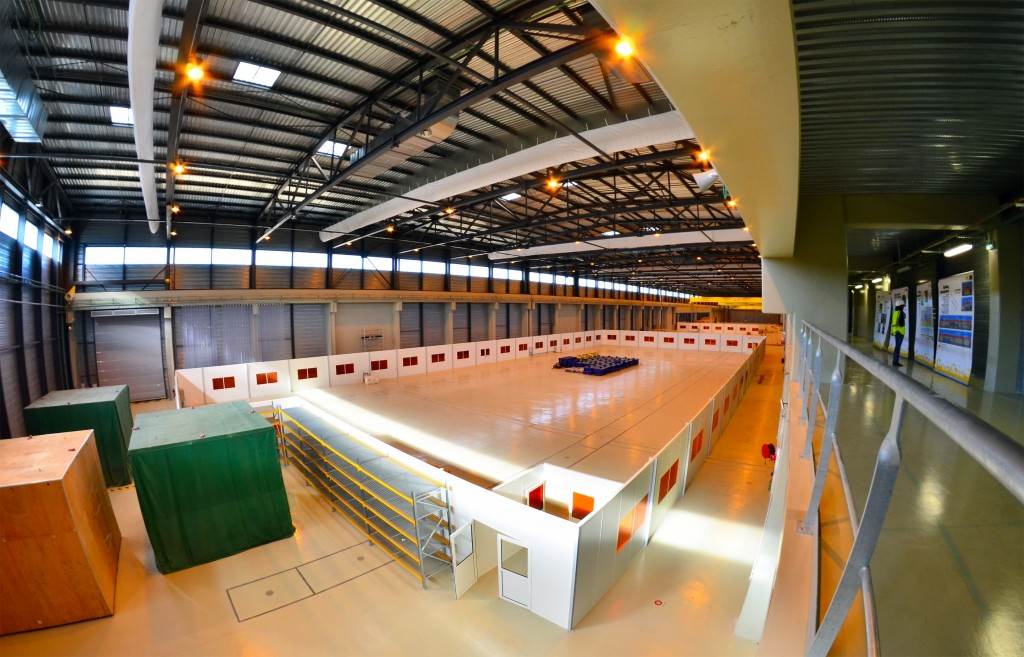
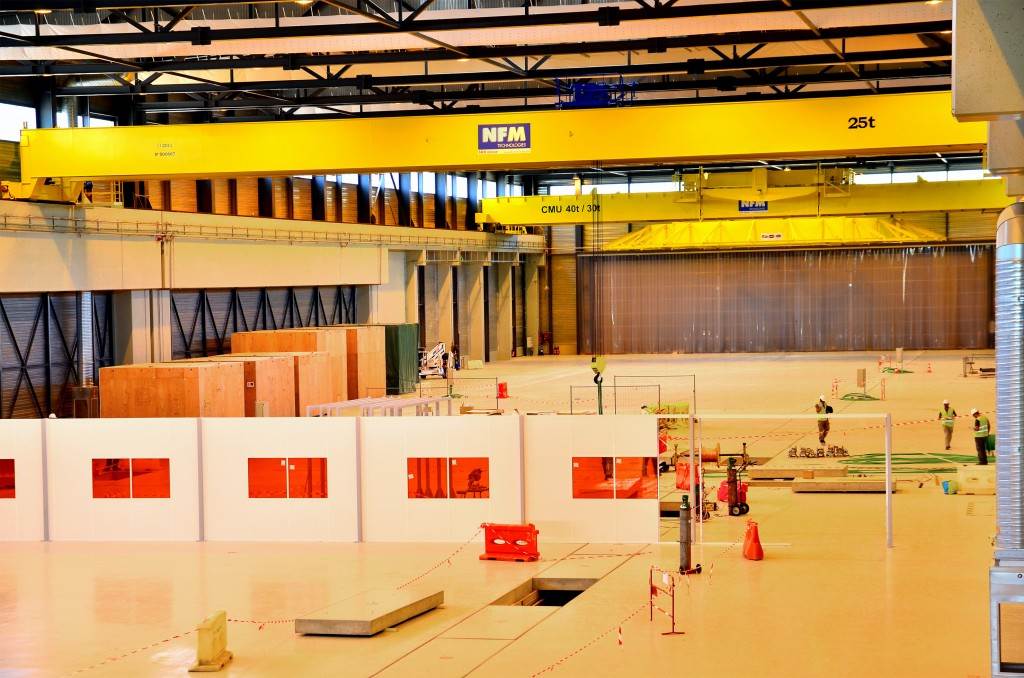
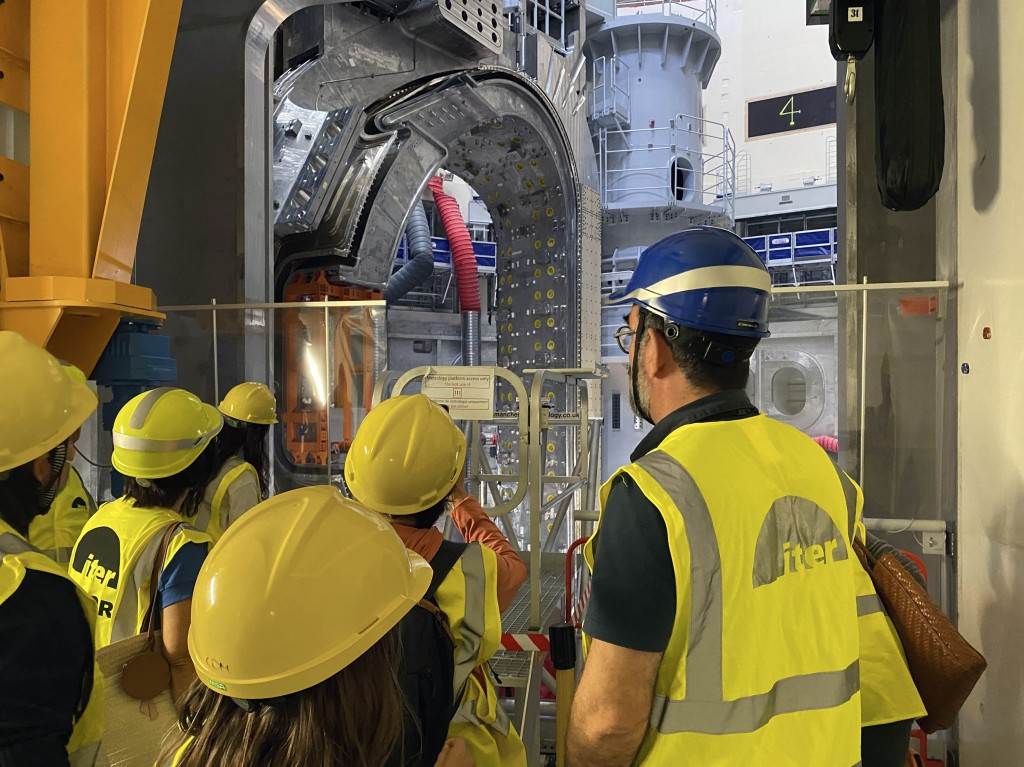
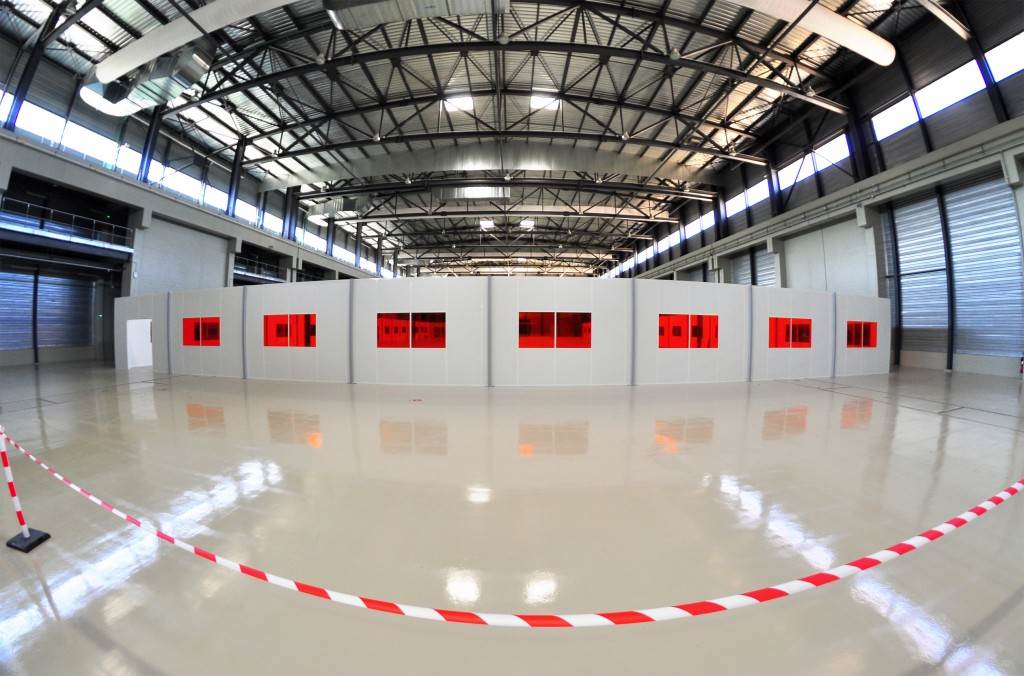