ITER NEWSLINE
-
Central solenoid qualification coil passes milestone
US ITER
Central solenoid qualification coil passes milestone
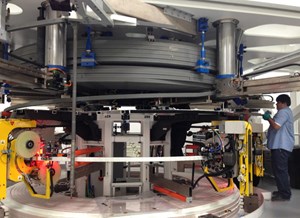
As the qualification coil is suspended from a specially designed structure, turn insulation machines applysix layers of Kapton and fiberglass tape.
Module fabrication for the "heartbeat of ITER"—the 1,000-tonne central solenoid at the centre of the ITER magnet system—is underway at the General Atomics Magnet Development Facility in Poway, California.
General Atomics finished the insulation process earlier this month for the qualification coil. This coil serves to validate final manufacturing processes prior to their application during the production of the six coil modules that make up the stacked central magnet.
Because ITER's central solenoid is subject to fault voltages up to 14,000 volts and must be tested at 30,000 volts, the successful ground insulation of the coils is a vital step in the fabrication process of the modules. The ground insulation system, consisting of 12 layers of glass and Kapton sheets, provides protection for up to 30,000 volts from other systems and components located in the ITER cryostat.
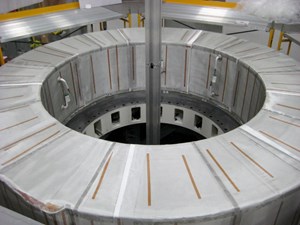
The completely insulated qualification coil, with helium inlet pipes attached on its inner surface. The qualification coil serves to validate each step in the manufacturing process.
Approximately 116 km of Kapton and fiberglass tape were used to wrap the 224 coil turns at the perimeter of the qualification coil with six successive layers. For a true production module, which is made up of 560 turns, more than double that amount—or 300 km—will be needed.
"From here, the qualification coil will be vacuum-pressure impregnated with 2,000 litres of resin, permeating the glass cloth and further insulating the coil," said John Smith, ITER program manager for General Atomics.
The epoxy resin impregnation is scheduled to be completed by late December 2016. At that stage, the demonstration coil will be nearly 80 percent through its two-year fabrication process.
"The scale of this central solenoid project is remarkable, as is the amount of engineering and fabrication work that brought us to this milestone. Watching this project continue to progress has been immensely gratifying," added Smith.
Read the General Atomics press release here.
return to the latest published articles